转炉连铸新技术
连铸新技术
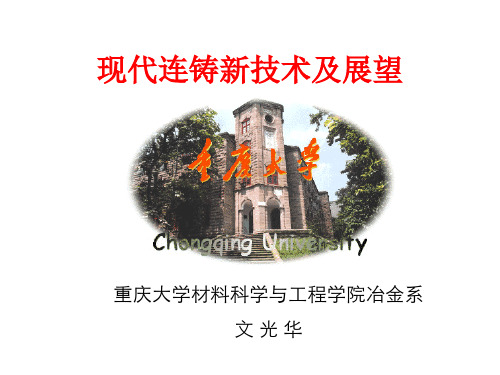
,
,
16
,
2.3
连续铸钢的生产现状
• 近几年,在我国钢铁工业大力发展的同时,连 铸生产也得到高速的增长。2002年全国连铸比 就上升到94%,粗钢产量为1.8亿吨。 2005年
估计钢产量将达 3.5 亿吨左右,占世界钢产量
,
,
、 20
3.1 高效连铸的应用
化国 最外 高方 拉坯 速铸 :机 高 效
21
3.1 高效连铸的应用
国内状况
可以说,采用高效连铸技术后,使我国钢铁工 业仅用10年时间完成了行业总体流程和生产水平的 历史性技术改造任务,步入了中后期工业国家的先 进行列。
22
3.2 高效连铸关键技术
当连铸机作业率超过了80%以上, 再要提 高连铸机产量就必须从提高拉速着手。而拉速 的提高决定于: —出结晶器均匀的坯壳厚度; —液相穴的长度; —铸坯的冷却强度。
用,低碳钢拉速达3.5m/min. ,中碳钢达2.8m/min.,高
碳钢达2.6m/min.。生产效率提高了50%,铸坯表面质量 改善,中心偏析减少。
29
板坯结晶器高效化技术
• 结晶器自动调宽技术; • 结晶器冷却优化技术(水缝、水速等); • 奥钢联最近开发的CLEVER的新型高效箱式结晶 器。该结晶器具有以下特点:箱式设计可快速更换铜板;
27
新型方坯高拉速结晶器
3 、奥地利VAI公司的钻石结晶器(DIAMOLD) 该结晶器在设计上有如下三个特点:①将结晶器长 度延长至1000mm,以延长铸坯在结晶器内的停留时间, 增加出结晶器的坯壳厚度;②采用比传统结晶器锥度大 的抛物线锥度,以保证坯壳均匀成长;③从结晶器顶部 往下300~400mm处开始,角部取消锥度以减小摩擦力, 而中部仍旧保持抛物线锥度。按照此方法设计出的结晶 器,从顶部看其内壁形状象钻石,故称作 DIAMOLD 。 数值模拟表明,该结晶器内坯壳生长稳定均匀,坯壳与 模壁间的摩擦力也小。在奥地利、美国、法国、德国及 意大利等国投入使用后,拉速大幅度提高,最高超过 5.0m/min. ,生产效率提高 20% ~ 50% ,铸坯质量明显 改善,而且铜管寿命也有所提高。 28
炼钢过程中的连铸技术改进与优化

炼钢过程中的连铸技术改进与优化随着现代工业的快速发展,钢铁行业在全球范围内扮演着重要的角色。
炼钢是制造钢材的关键过程之一,而连铸技术在炼钢过程中的应用越来越广泛。
本文将探讨炼钢过程中连铸技术的改进与优化措施,以提高钢材质量和生产效率。
一、连铸技术的基本原理与流程连铸技术是指将炼钢炉中液态钢水直接注入连铸机中,通过结晶器的作用,使其快速凝固为连续坯料。
基本上,连铸技术分为结晶器区、中间区和加热区三个部分。
结晶器区是最重要的部分,其作用是促使钢水迅速凝固形成坯料。
中间区则起到支撑坯料并保持其形状的作用,加热区则用来提供所需的坯料温度。
二、连铸技术改进的原因尽管连铸技术已经成为钢铁生产中主要的浇铸方法,但仍然存在一些问题和潜在的改进空间。
首先,连铸坯料的质量不稳定是一个重要问题。
由于熔铸过程中的各种因素,如温度、流速、结晶器形状等,坯料的结构和性能可能会出现变化。
这导致了产品的不均匀性和不稳定性。
其次,连铸过程中易产生气孔和夹杂物的问题也需要解决。
气孔和夹杂物对钢材的力学性能和外观质量有着显著影响。
此外,传统的连铸技术在能源消耗和生产效率方面也存在一些局限。
例如,冷却设备和传输系统的耗能较高,同时生产线上的工作效率较低。
因此,为了改进钢铁行业的连铸技术,提高生产效率和产品质量,钢铁企业已经采取了一系列的措施。
三、连铸技术改进与优化措施1. 结晶器改进结晶器是连铸技术中最关键的部分,对坯料质量起到决定性的作用。
通过改进结晶器的设计和材料,可以提高坯料的凝固性能和整体质量。
现代连铸技术使用先进的结晶器涂层和陶瓷材料,以减少坯料表面张力和增加热传导率。
此外,优化结晶器的几何形状和冷却系统,可以提高坯料的结晶行为和熔体流动性。
2. 连铸过程控制技术连铸过程中的温度、流速和加热条件等参数对坯料质量有着直接的影响。
通过引入先进的控制技术,如自动化控制系统和实时监测装置,可以实现对连铸过程的精细控制和优化。
自动化系统可以实时监测和调整炉温、浇注速度和结晶器温度等参数,以确保坯料的一致性和质量。
转炉炼钢连铸大型钢结构施工方案

转炉炼钢连铸大型钢结构施工方案1. 引言转炉炼钢连铸是一种将熔融钢液通过连续铸造机连续浇铸成坯料的工艺。
大型钢结构施工是工程建设中的重要环节,而转炉炼钢连铸技术在大型钢结构的制造中起着至关重要的作用。
本文将介绍转炉炼钢连铸大型钢结构施工的方案和关键技术。
2. 施工方案2.1 施工准备在进行转炉炼钢连铸大型钢结构施工之前,需要做好一系列的施工准备工作,包括:•钢材采购:根据工程需求,选择合适的钢材,保证材质符合标准要求。
•设备准备:确保连铸机和转炉设备运行正常,进行必要的检修和保养。
•施工人员培训:培训施工人员,确保他们熟悉操作流程和安全要求。
2.2 施工流程转炉炼钢连铸大型钢结构的施工流程一般包括以下几个步骤:2.2.1 准备作业在开始转炉炼钢连铸施工之前,需要对设备进行检查和调试,确保运行正常。
同时,对生产线进行清洁,准备无尘环境。
2.2.2 钢材炼制将原始钢材放入转炉中进行热炼制,控制温度、冶炼时间和成分,以确保钢材的质量。
2.2.3 钢水连铸炼制好的钢水通过连铸机进行连续浇铸,形成连续坯料。
在此过程中,需要确保连铸机的运行平稳,避免产生缺陷。
2.2.4 坯料冷却将连续铸造的钢水坯料冷却,使其达到适合后续加工的温度。
2.2.5 除氧处理和去渣对钢水进行除氧处理和去渣,确保钢材中的杂质得到清除。
2.2.6 结果检查和质量保证对连铸得到的结构钢材料进行质量检查,保证其满足相关标准和要求。
2.3 安全措施在转炉炼钢连铸大型钢结构施工过程中,需采取一系列的安全措施,以保证施工人员的安全。
主要包括:•穿戴个人防护用品,如安全帽、手套、防护眼镜等。
•配备消防器材,定期进行消防演练,并确保消防设备的正常运行。
•进行施工现场的安全隐患排查,及时消除危险因素。
•培训施工人员安全知识,提高他们的安全意识。
3. 关键技术3.1 温度控制技术在转炉炼钢连铸过程中,温度的控制是非常关键的。
需要通过合适的燃烧控制和温度检测设备,确保钢水炼制温度的准确控制。
0010连铸工艺详解(图文)

连铸工艺流程介绍【导读】:转炉生产出来的钢水经过精炼炉精炼以后,需要将钢水铸造成不同类型、不同规格的钢坯。
连铸工段就是将精炼后的钢水连续铸造成钢坯的生产工序,主要设备包括回转台、中间包,结晶器、拉矫机等。
本专题将详细介绍转炉(以及电炉)炼钢生产的工艺流程,主要工艺设备的工作原理以及控制要求等信息。
由于时间的仓促和编辑水平有限,专题中难免出现遗漏或错误的地方,欢迎大家补充指正。
连铸的目的: 将钢水铸造成钢坯。
将装有精炼好钢水的钢包运至回转台,回转台转动到浇注位置后,将钢水注入中间包,中间包再由水口将钢水分配到各个结晶器中去。
结晶器是连铸机的核心设备之一,它使铸件成形并迅速凝固结晶。
拉矫机与结晶振动装置共同作用,将结晶器内的铸件拉出,经冷却、电磁搅拌后,切割成一定长度的板坯。
{连铸工艺详解连铸的生产工艺流程:将装有精炼好钢水的钢包运至回转台,回转台转动到浇注位置后,将钢水注入中间包,中间包再由水口将钢水分配到各个结晶器中去。
结晶器是连铸机的核心设备之一,它使铸件成形并迅速凝固结晶。
拉矫机与结晶振动装置共同作用,将结晶器内的铸件拉出,经冷却、电磁搅拌后,切割成一定长度的板坯。
连铸钢水的准备一、连铸钢水的温度要求:钢水温度过高的危害:①出结晶器坯壳薄,容易漏钢;②耐火材料侵蚀加快,易导致铸流失控,降低浇铸安全性;③增加非金属夹杂,影响板坯内在质量;④铸坯柱状晶发达;⑤中心偏析加重,易产生中心线裂纹。
钢水温度过低的危害:①容易发生水口堵塞,浇铸中断;②连铸表面容易产生结疱、夹渣、裂纹等缺陷;③非金属夹杂不易上浮,影响铸坯内在质量。
二、钢水在钢包中的温度控制:根据冶炼钢种严格控制出钢温度,使其在较窄的范围内变化;其次,要最大限度地减少从出钢、钢包中、钢包运送途中及进入中间包的整个过程中的温降。
实际生产中需采取在钢包内调整钢水温度的措施:1)钢包吹氩调温2)加废钢调温3)在钢包中加热钢水技术4)钢水包的保温中间包钢水温度的控制一、浇铸温度的确定浇铸温度是指中间包内的钢水温度,通常一炉钢水需在中间包内测温3次,即开浇后 5min、浇铸中期和浇铸结束前 5min,而这 3 次温度的平均值被视为平均浇铸温度。
金属冶炼中的连铸技术
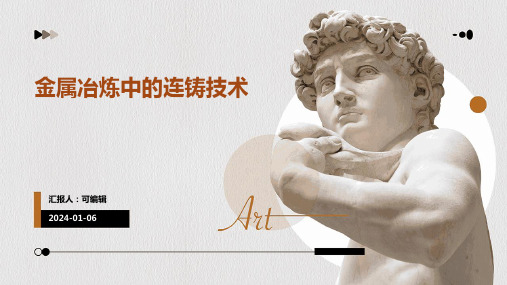
有色金属行业
其他行业
连铸技术也可用于铜、铝、锌等有色金属的生产中。
除钢铁和有色金属行业外,连铸技术还可应用于航空航天、汽车、机械制造等领域中。
03
02
01
02
CHAPTERBiblioteka 连铸技术的基本原理在连铸过程中,钢水从液态逐渐冷却凝固,形成固态铸坯。
钢水凝固
钢水在结晶器内通过与冷却水接触,将热量传递给冷却水,实现快速冷却。
金属冶炼中的连铸技术
汇报人:可编辑
2024-01-06
目录
连铸技术概述连铸技术的基本原理连铸技术的工艺流程连铸技术的优缺点分析连铸技术的应用实例
01
CHAPTER
连铸技术概述
连铸技术是一种将液态金属连续浇注到铸型中,形成一定形状和规格的铸坯或铸件的生产工艺。
定义
连铸技术具有高效、节能、环保等优点,能够提高金属的收得率和生产效率,降低生产成本,同时改善铸件的质量和性能。
传热过程
控制钢水的温度和冷却速度是连铸过程中的关键,直接影响到铸坯的质量和生产效率。
温度控制
03
CHAPTER
连铸技术的工艺流程
钢水成分控制
钢水温度调整
去除杂质
钢水搅拌
01
02
03
04
根据产品要求,对钢水成分进行严格控制,确保其化学成分符合标准。
通过加热或冷却,将钢水温度调整至适宜的浇注温度,以保证连铸过程顺利进行。
特点
连铸技术起源于19世纪中叶,当时主要用于生产玻璃和陶瓷等非金属材料。
起始阶段
20世纪初,人们开始尝试将连铸技术应用于金属材料的生产,但技术和设备尚不成熟,存在很多问题。
初步发展阶段
钢铁冶金新工艺技术目录

钢铁冶金新工艺技术目录钢铁冶金是现代工业中应用最广泛的材料之一,其技术不断发展和创新,推动了钢铁行业的高效生产和质量提升。
下面是一份钢铁冶金新工艺技术目录。
一、高炉冶炼新技术1. 高效节能热风炉技术:采用高效燃烧器和余热回收装置,提高燃烧效率和热风温度,降低燃料消耗和排放。
2. 富氧预处理技术:通过对冶炼矿石进行富氧预处理,提高还原效率和高炉产能,减少煤耗和焦耗。
3. 燃料灰渣精煤技术:通过对燃料灰渣中的可燃物质进行精煤,提高燃烧效率和热量利用率,降低煤耗和废气排放。
二、转炉冶炼新技术1. 高效氧枪技术:采用高效氧枪和透氧技术,提高氧枪吹氧效率和转炉熔化过程中的氧气利用率,降低氧气消耗和炉渣中的氧化铁含量。
2. 喷吹粉煤技术:通过将粉煤喷吹到转炉中,在燃烧过程中释放高热值的挥发分,提高炉内温度和燃烧效率,减少焦耗和燃料消耗。
3. 渣液脱锰技术:通过添加适量的石灰和石膏等物质,控制转炉渣中的碱度和碳酸锰含量,降低转炉渣锰损失和锰冶炼成本。
三、连铸新技术1. 水模连铸技术:采用水模铸坯,提高结晶器冷却效果和铸坯的表面质量,降低铸坯变形和裂损率,提高铸坯质量和连铸效率。
2. 轧辊调整技术:通过轧辊调整系统自动化控制,实现辊型调整和轧件形状控制,提高轧件尺寸精度和表面质量,降低轧制能耗和加工成本。
3. 涂层技术:在连铸过程中,对铸坯和轧件表面进行涂层处理,减少表面氧化、脱碳和损伤,提高产品质量和附加值。
四、高温热处理新技术1. 连续退火技术:采用连续退火设备,对钢材进行高温退火处理,实现均匀结构和优良性能,提高钢材的塑性和韧性。
2. 淬火技术:采用先进的淬火设备和工艺,快速冷却钢材,形成细小、均匀的马氏体组织,提高钢材的硬度和耐磨性。
3. 氮化处理技术:通过将钢材置于含氮气氛中,在高温下进行氮化处理,提高钢材的表面硬度和耐腐蚀性。
五、环保技术1. 高效除尘技术:采用先进的除尘设备和技术,减少钢铁冶炼过程中的烟尘和废气排放,改善环境污染问题。
金属冶炼过程中的连铸技术

中大型钢厂由于规模较大,连铸技术 主要用于生产大型钢材和特殊钢材, 如大型矩形坯、板坯、方坯等。
中大型钢厂的连铸技术应用中,通常 采用先进的连铸工艺流程,如电磁搅 拌、结晶器振动、动态二冷等,以提 高产品质量和降低能耗。
中大型钢厂的连铸机通常采用多流形 式,以提高生产效率和降低成本。
不锈钢冶炼的连铸技术应用
06
连铸技术的应用实例
小型钢厂的连铸技术应用
小型钢厂由于规模较小,连铸技 术主要用于生产小型钢坯和钢材 ,如小型圆钢、小型矩形坯等。
由于设备规模较小,连铸机通常 采用单流或双流形式,便于维护
和操作。
小型钢厂的连铸技术应用中,通 常采用传统的连铸工艺流程,如 钢水注入、结晶器冷却、二次冷
却等。
中大型钢厂的连铸技术应用
板坯连铸技术主要用于生产薄板和钢板,广泛应用于汽车、船舶、建筑、家电等 领域。
板坯连铸技术的优点包括高精度、高质量、高效率等,是现代金属板材制造的重 要技术之一。
圆坯连铸技术
圆坯连铸技术主要用于生产圆形的钢坯,主要应用于石油、 化工、电力等领域。
圆坯连铸技术的优点包括高效率、低成本、节能环保等,是 现代圆形结构件制造的重要技术之一。
智能化与自动化
智能化
随着人工智能和大数据技术的应用,连铸技术正朝着智能化方向发展。通过建立智能化监控系统,实 时监测生产过程,对异常情况自动预警和处理,提高生产安全性和稳定性。
自动化
自动化是提高连铸生产效率和产品质量的重要手段。通过自动化设备、机器人和自动化控制系统,实 现连铸生产过程的自动化操作,减少人工干预,提高生产效率。
05
连铸技术的发展趋势
高效化与节能化
高效化
随着技术的不断进步,连铸技术正朝着提高生产效率和降低能耗的方向发展。 通过优化工艺参数、改进设备结构和采用先进的控制技术,实现连铸生产的高 效化,提高铸坯质量和产量。
炼钢与连铸若干新技术
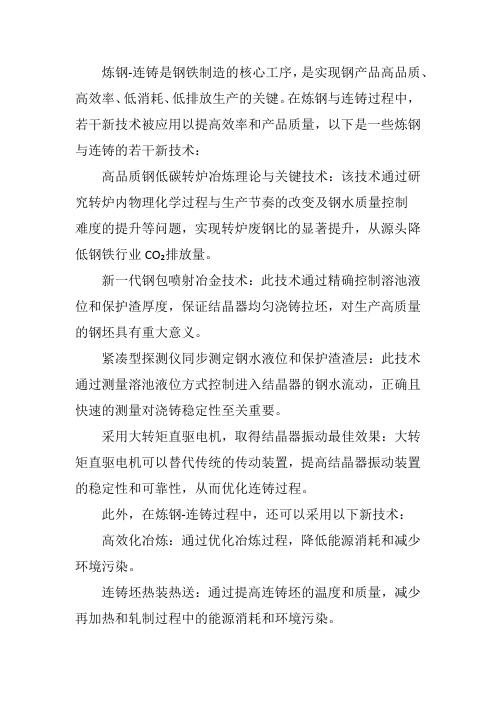
炼钢-连铸是钢铁制造的核心工序,是实现钢产品高品质、高效率、低消耗、低排放生产的关键。
在炼钢与连铸过程中,若干新技术被应用以提高效率和产品质量,以下是一些炼钢与连铸的若干新技术:高品质钢低碳转炉冶炼理论与关键技术:该技术通过研究转炉内物理化学过程与生产节奏的改变及钢水质量控制难度的提升等问题,实现转炉废钢比的显著提升,从源头降低钢铁行业CO₂排放量。
新一代钢包喷射冶金技术:此技术通过精确控制溶池液位和保护渣厚度,保证结晶器均匀浇铸拉坯,对生产高质量的钢坯具有重大意义。
紧凑型探测仪同步测定钢水液位和保护渣渣层:此技术通过测量溶池液位方式控制进入结晶器的钢水流动,正确且快速的测量对浇铸稳定性至关重要。
采用大转矩直驱电机,取得结晶器振动最佳效果:大转矩直驱电机可以替代传统的传动装置,提高结晶器振动装置的稳定性和可靠性,从而优化连铸过程。
此外,在炼钢-连铸过程中,还可以采用以下新技术:高效化冶炼:通过优化冶炼过程,降低能源消耗和减少环境污染。
连铸坯热装热送:通过提高连铸坯的温度和质量,减少再加热和轧制过程中的能源消耗和环境污染。
近终形化生产:通过采用先进的工艺和技术,生产更小断面的连铸坯,提高成材率和生产效率。
精确控制结晶器液面和保护渣厚度:通过精确控制结晶器液面和保护渣厚度,提高连铸坯的质量和稳定性。
电磁搅拌技术:通过采用电磁搅拌技术,改善连铸坯的凝固过程,提高产品质量和生产效率。
自动化的物流系统:通过采用先进的物流系统和技术,实现生产过程中物料的自动化运输和跟踪管理,提高生产效率和产品质量。
高效节能的轧制技术:通过采用高效节能的轧制技术,降低轧钢过程中的能源消耗和提高产品质量。
环保型轧制工艺:通过采用环保型轧制工艺和技术,减少轧钢过程中的环境污染和资源浪费。
集成化工艺控制技术:通过采用集成化工艺控制技术,将炼钢、连铸和轧制等工艺过程进行优化和控制,提高生产效率和产品质量。
这些新技术的应用可以显著提高炼钢-连铸生产的效率和产品质量,同时降低能源消耗和环境污染。
炼钢与连铸若干新技术
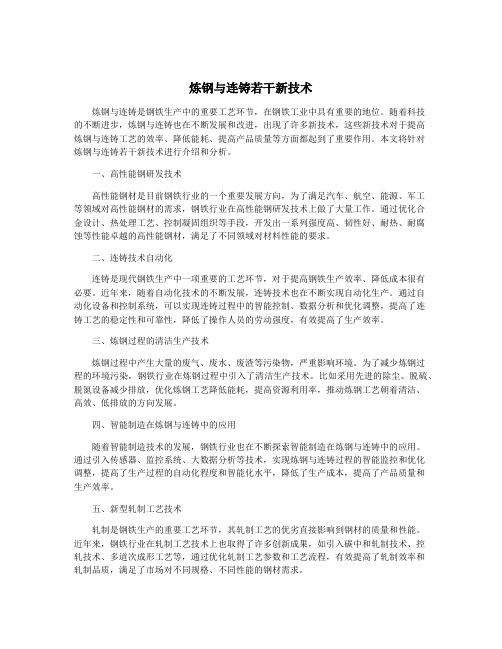
炼钢与连铸若干新技术炼钢与连铸是钢铁生产中的重要工艺环节,在钢铁工业中具有重要的地位。
随着科技的不断进步,炼钢与连铸也在不断发展和改进,出现了许多新技术,这些新技术对于提高炼钢与连铸工艺的效率、降低能耗、提高产品质量等方面都起到了重要作用。
本文将针对炼钢与连铸若干新技术进行介绍和分析。
一、高性能钢研发技术高性能钢材是目前钢铁行业的一个重要发展方向,为了满足汽车、航空、能源、军工等领域对高性能钢材的需求,钢铁行业在高性能钢研发技术上做了大量工作。
通过优化合金设计、热处理工艺、控制凝固组织等手段,开发出一系列强度高、韧性好、耐热、耐腐蚀等性能卓越的高性能钢材,满足了不同领域对材料性能的要求。
二、连铸技术自动化连铸是现代钢铁生产中一项重要的工艺环节,对于提高钢铁生产效率、降低成本很有必要。
近年来,随着自动化技术的不断发展,连铸技术也在不断实现自动化生产。
通过自动化设备和控制系统,可以实现连铸过程中的智能控制、数据分析和优化调整,提高了连铸工艺的稳定性和可靠性,降低了操作人员的劳动强度,有效提高了生产效率。
三、炼钢过程的清洁生产技术炼钢过程中产生大量的废气、废水、废渣等污染物,严重影响环境。
为了减少炼钢过程的环境污染,钢铁行业在炼钢过程中引入了清洁生产技术。
比如采用先进的除尘、脱硫、脱氮设备减少排放,优化炼钢工艺降低能耗,提高资源利用率,推动炼钢工艺朝着清洁、高效、低排放的方向发展。
四、智能制造在炼钢与连铸中的应用随着智能制造技术的发展,钢铁行业也在不断探索智能制造在炼钢与连铸中的应用。
通过引入传感器、监控系统、大数据分析等技术,实现炼钢与连铸过程的智能监控和优化调整,提高了生产过程的自动化程度和智能化水平,降低了生产成本,提高了产品质量和生产效率。
五、新型轧制工艺技术轧制是钢铁生产的重要工艺环节,其轧制工艺的优劣直接影响到钢材的质量和性能。
近年来,钢铁行业在轧制工艺技术上也取得了许多创新成果,如引入碳中和轧制技术、控轧技术、多道次成形工艺等,通过优化轧制工艺参数和工艺流程,有效提高了轧制效率和轧制品质,满足了市场对不同规格、不同性能的钢材需求。
炼钢与连铸若干新技术

炼钢与连铸若干新技术炼钢与连铸作为钢铁生产的重要环节,关系着钢铁质量、生产效率以及能源消耗。
近年来,随着科学技术的不断发展,炼钢与连铸领域出现了许多新技术,这些新技术在提高产品质量、降低生产成本等方面发挥着重要作用。
本文将介绍一些关于炼钢与连铸的若干新技术。
一、炼钢新技术1. 超高炉渣碱度炼钢技术传统炼钢过程中,高炉渣的碱度一般在1.5以上,导致了炼钢中的碱度冶炼难度大。
超高炉渣碱度炼钢技术通过增加炉渣碱度,提高炼钢过程中的碱度,使得钢水中的夹杂物得以吸附和浮渣,从而有效提高了钢水的质量,降低了夹杂物含量。
2. 高炉富氧燃烧技术传统的高炉燃烧采用煤气、焦炭等作为还原剂,而高炉富氧燃烧技术则采用富氧燃烧,使得炉顶煤气中氧分压大大提高,煤气焚烧效率显著提高,从而有效减少了炼钢过程中的二氧化碳排放,降低了生产成本。
3. 高效矿石还原技术传统的炼钢制程中,矿石还原效率低,而高效矿石还原技术采用高效还原剂和改良还原工艺,可以明显提高还原效率,减少资源的浪费,降低生产成本。
二、连铸新技术1. 动态软浇铸技术动态软浇铸技术是指在连铸过程中,通过实时数据分析,调整结晶器冷却水的流速和温度,实现钢坯凝固过程中的动态调控,确保钢坯结晶组织的均匀性和合格率。
2. 连铸直齿轮技术传统连铸转辊采用辊凹槽结构,而连铸直齿轮技术则采用直齿轮结构,使得连铸转辊的传动机构更加紧凑、稳定、可靠,最大限度地减小了设备的占地面积,提高了生产效率。
3. 连铸在线水平矫直技术传统的连铸坯的矫直需要通过离线操作进行,而连铸在线水平矫直技术则采用在线连铸坯的自动矫直设备,实现了连铸坯的在线矫直,提高了生产效率,降低了生产成本。
以上所提到的炼钢与连铸的新技术只是其中的一部分,随着科学技术的不断进步,相关新技术也在不断涌现。
这些新技术的应用,将进一步推动炼钢与连铸领域的发展,为钢铁行业的持续发展注入新的活力。
转炉精炼及连铸作用

转炉精炼及连铸作用转炉精炼和连铸是钢铁生产中的两个重要工艺环节,它们的作用分别是进行炼钢和铸造。
转炉精炼是钢铁生产中的一种重要工艺,它主要用于炼钢。
转炉精炼的原理是通过高温下将废钢、生铁和其他合金材料等物料放入转炉中进行冶炼,然后通过吹氧等工艺将钢水中的杂质和不良元素除去,从而得到高质量的钢材。
转炉精炼的过程分为炉膛预热、初始处理、主处理和终处理四个阶段。
在炉膛预热阶段,转炉内的炉料和孔隙被预先加热,以保证转炉正常运行。
初始处理阶段是将废钢和生铁放入转炉中,通过高温反应使其熔化和混合。
主处理阶段是将氧气吹入炉内,通过氧气与钢水的反应,氧化和除去钢水中的杂质和不良元素。
终处理阶段是通过加入合金材料,调整钢水中的成分和性能,从而使得钢水达到所需的质量标准。
转炉精炼的主要作用有以下几个方面:首先,转炉精炼可以有效去除钢水中的杂质。
使用吹氧等工艺将废钢和生铁等炉料加热和熔化,使得污染物与氧气发生反应并氧化,从而将杂质除去,这样可以大大提高钢材的纯度和质量。
其次,转炉精炼可以调整钢水的成分和性能。
通过添加合金材料,可以改变钢水中的元素含量和比例,从而调整钢水的硬度、耐腐蚀性和焊接性能等,满足不同用途和要求的钢材的生产需求。
此外,转炉精炼还可以提高钢铁生产的效率。
废钢和生铁等废料可以被重新回收和利用,减少材料的浪费。
同时,转炉精炼的工艺可以自动化和连续化,提高生产效率和生产能力。
连铸是制造钢材的另一种重要工艺,它将转炉精炼后的钢水倒入连续铸造机中,通过连续结晶和拉拔过程,将钢水凝固成坯料,进一步加工成钢材。
连铸的作用主要有以下几个方面:首先,连铸可以提高钢材的质量和一致性。
通过连续铸造机的结晶和拉拔过程,钢水在坯料的形成过程中得到均匀的结晶和固化,避免了传统浇铸中因为冷却速度不均匀而产生的孔洞、夹杂物等缺陷,从而得到更加均匀和致密的钢材。
其次,连铸可以提高钢材的形状和尺寸精度。
通过控制连铸工艺参数,可以实现对坯料形状和尺寸的精确控制,使得钢材的外形和尺寸满足客户的要求,减少后续加工的量和成本,提高钢材的生产效率。
转炉-连铸新技术
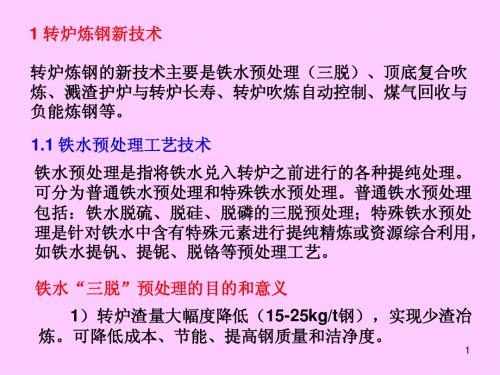
21
22
23
初炼炉—精炼炉—连铸生产能力匹配 转炉因生产周期短、节奏快、适宜选用RH;电炉冶炼周期较 长, 可选用VD。 提高炉外精炼比 针对目前多数钢厂增设了炉外精炼设备后使用率不高的 问题,因此对非真空精炼的LF炉、CAS-OB炉设备日历作业率 应>90%,真空精炼设备的RH、VD等设备作业率应>60%。而 整个炼钢厂炉外精炼比应>95%,当然应注意钢种适路、生产 节奏匹配,设备维修和生产成本。 2.2.2 炉外精炼设备的配套条件
VD脱碳能力弱(受钢包净高度的限制),具备一定的钢渣精炼 功能,适宜生产重轨、轴承、齿轮等气体含量和夹杂物要求严 格的优质钢种。
20
RH脱碳能力强,适宜大量生产超低碳钢、IF钢 VOD、AOD等专门用于生产不锈钢。 此外,经常采用不同功能 的精炼炉组合使用,如 CAS-RH,LF-RH LF-VD, AOD-VOD。
复吹转炉的经济效益
渣中含铁量降低2.5~5.0%; 金属收得率提高0.5~1.5%,残Mn 提高0.02%~0.06%; 磷含量降低0.002%。
7
石灰消耗降低3-10kg/t, 氧气消耗减少4NM3/t~6NM3/t; 提高炉龄,减少耐火材料消耗,综合经济效益约为6~15元/吨。 1.3 溅渣护炉技术
15
提高转炉作业率,宝钢转炉作业率从1995年到1998年提高 4.96个百分点,工序能耗降低2.97 kgce。 降低动力和燃料消耗。
16
2 炉外精炼 炉外精炼是指在电弧炉、转炉之外的钢包内完成对钢水 的精炼提纯任务(AOD炉不是在钢包内进行),故又可将电弧 炉、转炉成为初炼炉。精炼炉始于电弧炉外的钢包精炼炉,20 世纪90年代推广于氧气顶吹转炉的钢包精炼炉。 近20年工业发达国家要求提高钢材的纯净度改善钢材的 性能,例如:为提高轴承钢的疲劳寿命,要求控制钢中 T[O]≤5×10-6;为保证深冲钢的深冲性,要求控制钢中 C+N≤50×10-6;为提高输油管抗H2S腐蚀能力,要求控制钢中 [S]≤5×10-6等。大量生产这些高附加值纯净钢仅依靠电弧炉、 转炉是非常困难的。因此,炉外精炼工艺与装备迅速普及推广。 在日本、欧洲先进的钢铁生产国家,炉外精炼比超过90%,其中 真空精炼比超过50%,有些钢厂已达到100%。目前我国的钢 铁企业已基本装备了各种不同类型的精炼炉。
转炉炼钢流程优化和技术创新

项目名称:转炉炼钢流程优化和技术创新一转炉制动化炼钢1 项目的提出及意义随着经济的发展,对钢的性能提出了更高的要求,为了满足生产出高纯净度、高质量品种的需要,采用自动化炼钢技术已成为现代化炼钢的重要保证。
转炉炼钢自动化技术是利用副枪检测出转炉吹炼过程某一点的温度、含碳量,通过模型进行动态调整,达到准确控制吹炼终点碳和温度的目的。
按照新钢公司建设成具有现代化炼钢技术的钢铁企业的指示精神,为实现科学炼钢,达到稳定操作、降低消耗、提高质量、满足新钢生产精品板材的需要,决定在210t转炉增设副枪及自动化炼钢系统。
并成立了专人负责的副枪工程师站,工程师站的技术人员查阅了副枪及自动化炼钢有关技术资料,调研了国内武钢、宝钢等单位引进的副枪炼钢情况,经过多次专题讨论研究和比较,认为:由于与国外的条件不同,武钢副枪及自动代炼钢系统,经多年改进和软件二次开发,使用效果好。
我公司与武钢冶炼条件相近,新钢与武钢合作开发,走国内自主集成创新之路,提高应用效果,尽快实现自动化炼钢的目标,为实现副枪及自动炼钢国产化创出一条新路。
2项目的主要内容主要研究内容有如下几点:(1)炼钢工艺模型自适应研究,根据新钢条件选择确定炼钢模型编程思路与方法,确定钢种冶炼方式、熔剂系数、边界条件、温度校正系数等主要工艺参数;(2)优化计算机炼钢的吹炼模式(枪位曲线、顶吹供氧及复吹模式、根据氧步的加料方式等),进行转炉终点控制及低磷吹炼模式研究;(3)修改一级机氧枪HMI画面和相关PLC程序,建立吹炼阶段各类信号的准确采集与传输,实现按氧步控制吹炼模式;(4)修改辅料加料PLC程序,建立根据氧步控制的配料单、一级计算机自动加料控制模式和自动控制模式;(5)进行炼钢静态、动态二级模型编程及改进,实现转炉二级系统与炼钢MES及其他相关的二级、一级系统间的数据交换。
(6)强化原材料管理,对废钢进行分类。
强化计量管理,建立和完善计量和校验管理制度,以及制定相关工艺过程操作岗位作业指导书。
转炉CSP连铸工艺配置开发技术
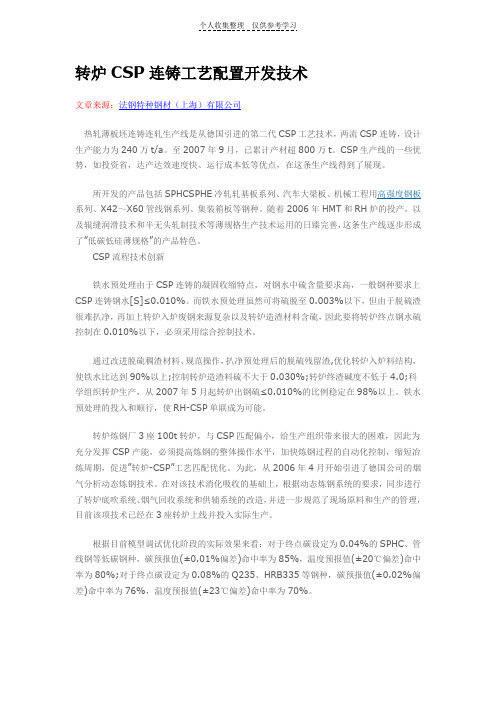
转炉CSP连铸工艺配置开发技术文章来源:法钢特种钢材(上海)有限公司热轧薄板坯连铸连轧生产线是从德国引进的第二代CSP工艺技术,两流CSP连铸,设计生产能力为240万t/a。
至2007年9月,已累计产材超800万t。
CSP生产线的一些优势,如投资省,达产达效速度快、运行成本低等优点,在这条生产线得到了展现。
所开发的产品包括SPHCSPHE冷轧轧基板系列、汽车大梁板、机械工程用高强度钢板系列、X42~X60管线钢系列、集装箱板等钢种。
随着2006年HMT和RH炉的投产,以及辊缝润滑技术和半无头轧制技术等薄规格生产技术运用的日臻完善,这条生产线逐步形成了”低碳低硅薄规格”的产品特色。
CSP流程技术创新铁水预处理由于CSP连铸的凝固收缩特点,对钢水中硫含量要求高,一般钢种要求上CSP连铸钢水[S]≤0.010%。
而铁水预处理虽然可将硫脱至0.003%以下,但由于脱硫渣很难扒净,再加上转炉入炉废钢来源复杂以及转炉造渣材料含硫,因此要将转炉终点钢水硫控制在0.010%以下,必须采用综合控制技术。
通过改进脱硫稠渣材料、规范操作,扒净预处理后的脱硫残留渣,优化转炉入炉料结构,使铁水比达到90%以上;控制转炉造渣料硫不大于0.030%;转炉终渣碱度不低于4.0;科学组织转炉生产,从2007年5月起转炉出钢硫≤0.010%的比例稳定在98%以上。
铁水预处理的投入和顺行,使RH-CSP单联成为可能。
转炉炼钢厂3座100t转炉,与CSP匹配偏小,给生产组织带来很大的困难,因此为充分发挥CSP产能,必须提高炼钢的整体操作水平,加快炼钢过程的自动化控制,缩短冶炼周期,促进”转炉-CSP”工艺匹配优化。
为此,从2006年4月开始引进了德国公司的烟气分析动态炼钢技术。
在对该技术消化吸收的基础上,根据动态炼钢系统的要求,同步进行了转炉底吹系统、烟气回收系统和供辅系统的改造,并进一步规范了现场原料和生产的管理,目前该项技术已经在3座转炉上线并投入实际生产。
转炉精炼及连铸工艺
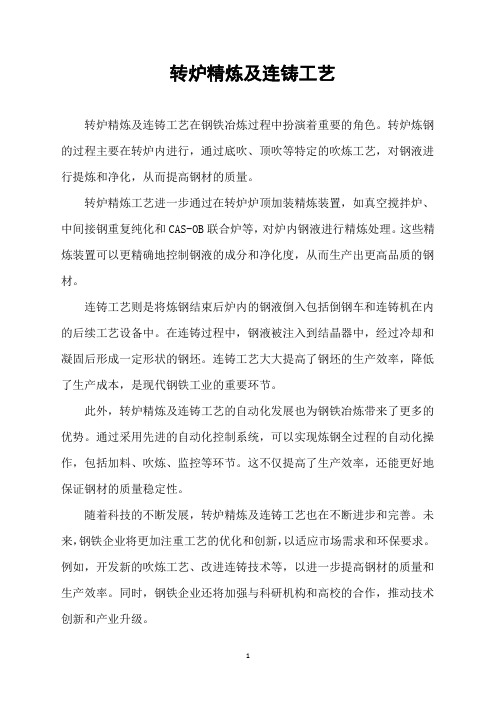
转炉精炼及连铸工艺
转炉精炼及连铸工艺在钢铁冶炼过程中扮演着重要的角色。
转炉炼钢的过程主要在转炉内进行,通过底吹、顶吹等特定的吹炼工艺,对钢液进行提炼和净化,从而提高钢材的质量。
转炉精炼工艺进一步通过在转炉炉顶加装精炼装置,如真空搅拌炉、中间接钢重复纯化和CAS-OB联合炉等,对炉内钢液进行精炼处理。
这些精炼装置可以更精确地控制钢液的成分和净化度,从而生产出更高品质的钢材。
连铸工艺则是将炼钢结束后炉内的钢液倒入包括倒钢车和连铸机在内的后续工艺设备中。
在连铸过程中,钢液被注入到结晶器中,经过冷却和凝固后形成一定形状的钢坯。
连铸工艺大大提高了钢坯的生产效率,降低了生产成本,是现代钢铁工业的重要环节。
此外,转炉精炼及连铸工艺的自动化发展也为钢铁冶炼带来了更多的优势。
通过采用先进的自动化控制系统,可以实现炼钢全过程的自动化操作,包括加料、吹炼、监控等环节。
这不仅提高了生产效率,还能更好地保证钢材的质量稳定性。
随着科技的不断发展,转炉精炼及连铸工艺也在不断进步和完善。
未来,钢铁企业将更加注重工艺的优化和创新,以适应市场需求和环保要求。
例如,开发新的吹炼工艺、改进连铸技术等,以进一步提高钢材的质量和生产效率。
同时,钢铁企业还将加强与科研机构和高校的合作,推动技术创新和产业升级。
1。
转炉-精炼-连铸过程

• 转炉炼钢 • 精炼过程 • 连铸过程 • 转炉-精炼-连铸过程中的质量控制 • 转炉-精炼-连铸过程的应用实例
01
转炉炼钢
转炉炼钢的原理
01
转炉炼钢的原理是利用铁水中的 杂质与氧气、铁矿石等发生化学 反应,去除铁水中的杂质,提高 钢的纯度。
02
在转炉炼钢过程中,通过加入铁 矿石、石灰石、白云石等原料, 调整钢的成分,控制钢的碳含量 、硫含量、磷含量等关键指标。
铝业
在铝业生产中,转炉-精炼-连铸工艺 被广泛应用于铝锭的生产,提高了产 品质量和成品率,降低了生产成本。
铜业
在铜业生产中,转炉-精炼-连铸工艺 被用于生产高纯度阴极铜,提高了产 品的导电性和耐腐蚀性。
应用实例的效果和影响
提高产品质量
通过采用转炉-精炼-连铸工艺, 企业能够生产出高质量的产品, 满足市场需求,提高产品竞争力。
降低生产成本
该工艺能够降低能耗和原材料消耗, 减少生产过程中的污染物排放,从 而降低生产成本。
促进产业升级
随着技术的不断进步和应用范围的 扩大,转炉-精炼-连铸工艺的应用 将促进相关产业的升级和转型。
THANKS
感谢观看
精炼的效果和影响因素
01
02
03
04
成分控制
精炼过程能够精确控制钢水成 分,确保钢材性能的稳定性和
可靠性。
夹杂物变性
通过精炼过程控制夹杂物的形 态和分布,有助于提高钢材的
韧性和强度。
温度控制
精炼过程中温度的稳定控制对 于钢水纯净度和连铸过程的顺
利实施具有重要影响。
操作参数
精炼过程中的吹氩流量、真空 度、加入合金的种类和数量等
根据产品要求,通过添加合金元素调整钢 水成分,以满足不同用途和性能需求。
转炉连铸工艺操作规程

转炉工艺操作规程1、兑铁水操作1.1确认生产条件具备,炉口周围无人员逗留或通过,炉内无残存液态钢渣及氧化性强的残渣;关闭主控室防爆门。
1.2将炉子摇至兑铁水位置;1.3指挥天车将铁水包运至炉前,缓慢落下主钩,距地面约1000mm-1500mm左右时将副钩落下,挂入包环内:1.4指挥天车吊运铁水包至炉口正上方位置,小流试兑,并调整兑铁位置准确无误;1.5指挥天车提升副钩正常兑铁;1.6摇炉工根据铁流位置,准确调整炉口角度,防止铁水抛洒炉口以外;1.7兑铁完毕,指挥天车先移出炉口位置,落下副钩后方能离开;1.8注意事项:1.8.1指挥人员应站在炉口侧面,严禁站在正对炉口位置;1.8.2站位附近要有退路;能让天车司机、摇炉工清楚看见指挥手势;1.8.3指挥人员应全力观注铁流情况及火焰情况,如有异常应及时采取有效措施,防止出现意外事故;1.8.4铁水包不能碰撞、接触炉口或其它设备;1.8.5严禁将铁渣兑入转炉.2.加废钢操作2.1确认废钢中不含封闭容器、易燃易爆品等其它禁品,炉口正前方无人员逗留或通过;2.2指挥摇炉工将炉子摇至加废钢位置;2.3指挥天车将废钢斗运至炉口正中位置;指挥天车移动大、小车,将废钢斗伸进炉口;2.4指挥天车提升副钩将废钢倒入炉内;2.5废钢加完后,指挥天车移动大、小车,将废钢斗移开炉口位置;2.6指挥天车下落副钩,使废钢斗出口上倾150后,方能离开炉台;2.7炉子摇至零位,加废钢操作结束。
2.8注意事项:2.8.1废钢潮湿时,应先加废钢,后兑铁水,且加完废钢后应前后摇炉两次;2.8.2加废钢时,如遇废钢搭桥或卡死,可指挥天车将副钩稍稍下降,再提起将废钢倒入炉内;2.8.3严禁废钢斗碰撞或接触炉口;2.8.4严禁用废钢斗撞击炉口粘结物;2.8.5指挥天车站位情况同兑铁水操作。
3.供氧操作3.1确认供氧系统正常、氧枪供气已切换为氧气、装入量在要求范围、各氮封正常、转炉已摇至吹炼位置;3.2所有联锁正常;3.3降枪点火后开始正常吹炼;3.4采用分阶段定压,恒压变枪操作,保证初期渣早化,过程渣化透,中后期防止返干;后期工作氧压0.9Mpa保证脱碳完全及均匀成分温度。
连铸工艺技术
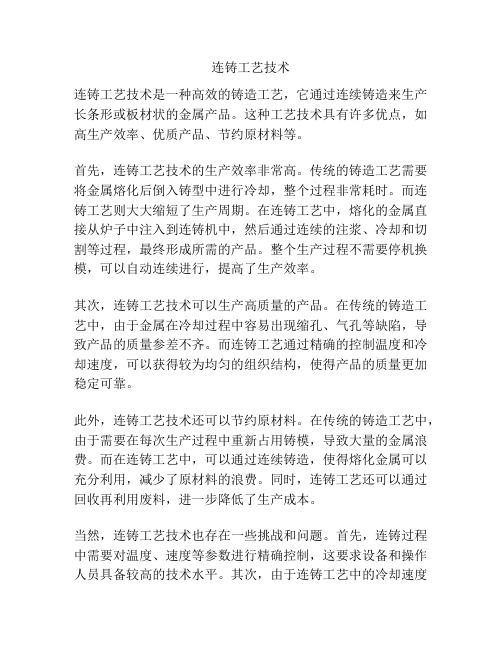
连铸工艺技术连铸工艺技术是一种高效的铸造工艺,它通过连续铸造来生产长条形或板材状的金属产品。
这种工艺技术具有许多优点,如高生产效率、优质产品、节约原材料等。
首先,连铸工艺技术的生产效率非常高。
传统的铸造工艺需要将金属熔化后倒入铸型中进行冷却,整个过程非常耗时。
而连铸工艺则大大缩短了生产周期。
在连铸工艺中,熔化的金属直接从炉子中注入到连铸机中,然后通过连续的注浆、冷却和切割等过程,最终形成所需的产品。
整个生产过程不需要停机换模,可以自动连续进行,提高了生产效率。
其次,连铸工艺技术可以生产高质量的产品。
在传统的铸造工艺中,由于金属在冷却过程中容易出现缩孔、气孔等缺陷,导致产品的质量参差不齐。
而连铸工艺通过精确的控制温度和冷却速度,可以获得较为均匀的组织结构,使得产品的质量更加稳定可靠。
此外,连铸工艺技术还可以节约原材料。
在传统的铸造工艺中,由于需要在每次生产过程中重新占用铸模,导致大量的金属浪费。
而在连铸工艺中,可以通过连续铸造,使得熔化金属可以充分利用,减少了原材料的浪费。
同时,连铸工艺还可以通过回收再利用废料,进一步降低了生产成本。
当然,连铸工艺技术也存在一些挑战和问题。
首先,连铸过程中需要对温度、速度等参数进行精确控制,这要求设备和操作人员具备较高的技术水平。
其次,由于连铸工艺中的冷却速度较快,可能导致金属材料的内应力过大,从而影响产品的机械性能。
因此,在连铸工艺中需要采取相应的措施来改善产品的内应力。
综上所述,连铸工艺技术是一种高效、高质量的铸造工艺,它通过连续铸造来生产金属产品。
连铸工艺具有高生产效率、优质产品、节约原材料等优点,但也存在一些挑战和问题。
随着科技的不断进步和工艺的不断改进,连铸工艺技术有望在金属制造领域中得到更广泛的应用。
- 1、下载文档前请自行甄别文档内容的完整性,平台不提供额外的编辑、内容补充、找答案等附加服务。
- 2、"仅部分预览"的文档,不可在线预览部分如存在完整性等问题,可反馈申请退款(可完整预览的文档不适用该条件!)。
- 3、如文档侵犯您的权益,请联系客服反馈,我们会尽快为您处理(人工客服工作时间:9:00-18:30)。
➢炉内合理的留渣量,通常控制在80~120kg/t 较合适; ➢炉渣特性控制:
终渣MgO≥8%为宜(特别对镁碳砖转炉); FeO12~18%为宜; 合适的炉渣粘度:易溅起、挂渣均匀。
7
溅渣操作参数控制
氮气压力与流量与氧气压力和 流量相接近时,效果较 好。 枪位高度要根据企业实际摸索,可在1~2.5m之间变化。 溅渣时间通常为2.5~4min,枪位夹角多数企业的实践证明 12°比较理想。
1)铁水脱硫预处理的工艺方法
1
投掷法—将脱硫剂投入铁水中。 喷吹法—将脱硫剂喷入铁水中。 搅拌法(KR法)—将通过中空机械搅拌器向铁水内加入脱硫 剂,搅拌脱硫。
2
2)铁水脱硫剂的选择 元素的脱硫能力由高到低依次为:CaC2、NaO2、Mg、BaO、 CaO、MnO、MgO。 工业中常用的脱硫剂有:CaO系、CaO+CaC2系、CaC2、 CaO+Mg系、Mg系。几种脱硫剂的特点见表2。
溅渣护炉的经济效益
➢提高炉龄3~4 倍以上; ➢提高转炉利用系数2~4%; ➢降低炉衬砖消耗0.2~1.0kg/t。 降低补炉料消耗0.5~1.0kg/t; ➢减轻工人劳动强度; ➢投资回报率高。我国63座转炉测算投资回收期为1.3年。 溅 渣护炉的综合经济效益大约为2~10年/吨钢。
8
溅渣护炉与复吹转炉的关系
脱硅。
1.2 顶底复合吹炼技术 顶底复合吹炼法可分为两类
✓ 顶吹氧、底吹惰性气体法,全世界广泛采用此法。 ✓ 顶底复合吹氧法,日本和欧洲多为采用。
工艺特点
✓反应速度快,热效率高,可实现炉内二次燃烧。
5
✓ 碳氧反应更趋平衡。当吹炼终点[C]=0.04复吹的终点[O]约 为900ppm,而进行复吹的炉次则为550ppm左右, 说明钢渣 的氧化性大为降低。吹炼终点残Mn明显提高,合金收得率明 显提高%
✓吹炼后期强化熔池搅拌,使钢-渣反应接近平衡,利于脱磷 脱硫反应的进行。
✓保持顶吹转炉成渣速度快和底吹转炉吹炼平稳的双重优点。
✓冶炼低碳钢(C=0.01-0.02%)时,避免了钢渣过氧化。
复吹转炉的经济效益
➢渣中含铁量降低2.5~5.0%; ➢金属收得率提高0.5~1.5%,残Mn 提高0.02%~0.06%; ➢磷含量降低0.002%。
对于采用溅渣护炉与复吹冶炼并存的转炉,随着溅渣后 炉龄的提高,炉底相应上涨,影响了底吹透气砖的工作。此时, 底吹透气砖的寿命约为3000 炉,这意味着从2000炉以后,复 吹效果大大减弱,甚至消失。 而溅渣护炉的炉龄远远大于 2000炉(现在达2万多炉),这就是一贯注重高纯净钢,普遍 采用复吹技术的日本不愿t, 氧气消耗减少4NM3/t~6NM3/t; ➢提高炉龄,减少耐火材料消耗,综合经济效益约为6~15元/吨。
1.3 溅渣护炉技术
溅渣护炉技术是利用高MgO 含量的炉渣,用高压氮气将炉渣喷 吹到转炉炉衬上,进而凝固到炉衬上,减缓炉衬砖的侵蚀速度,从 而提高转炉的炉龄。
2)脱碳速度加快、终点控制容易、氧效率提高、提高生产率。 3)锰的回收率提高,可进行锰矿熔融还原,降低成本。 4)转炉煤气成分稳定,煤气回收控制更加容易,以利实现转 炉负能炼钢、节能、降成本。 5)有利于扩大品种(高碳、高锰钢系列)。
铁水脱硫工艺技术
铁水脱硫法是指在铁水罐、铁水包、混铁车中进行脱硫。 在高炉、炉外精炼炉和转炉内每脱除1kg硫的成本分别是 铁水脱硫法的2.6倍、6.1倍、16.9倍。铁水脱硫法的成本低效 率高。
10
烟气分析:
根据炉气变化情况动态计算脱碳速率和钢水C含量,特别在吹炼末期 炉内[C][O]反应趋于平衡后,动态计算、校正熔池温度,准确预报吹炼末 期熔池的碳、温度值,根据动态计算、预报的终点[C]、T并结合转炉烟气 变化曲线确定吹炼终点并自动提枪结束吹炼,实现转炉不倒炉直接出钢自 动化炼钢技术。
静态控制
依据初始条件、铁水重量、成分、温度、废钢重量、
分类)。要求的终点目标(终点温度,化学成分)以及参
考炉次的参考数据,计算出本炉次的氧耗量,确定各种副原料
的加入量和吹炼过程氧枪的高度。静态控制包括三个模型:氧
量模型,枪位模型和副原料模型。这样可基本命中终点的含碳
量和温度目标。
动态控制
当转炉供氧量达到氧耗量的85%左右时,降低吹氧流量,副枪
开始测温、定碳,并把测得的温度值及碳含量送入过程计算机。
过程计算机则计算出达到目标温度和目标碳含量所需补吹的氧
量及冷却剂加入量,并以副枪测到的实际值作为初值,以后每
吹4秒的氧气量,启动一次动态计算,预测熔池内温度和目标
碳含量。当温度和碳含量都进入目标范围时,发出停吹命令,
终点C和温度T的命中率可达80以上。
11
全自动控制
在静态、动态控制基础上,通过对炉渣的在线检测,控制喷溅, 并全面预报终点C、P、S、T,实现闭环控制。 全自动控制效果: ➢提高终点碳含量控制精度:低碳钢±0.015%, 中碳钢±0.02%, 高碳钢±0.05%,温度±10℃; ➢实现对终点S、P、Mn含量的准确预报,精度为S ±0.009%, ➢P ± 0.001%,Mn ± 0.09; ➢后吹率从60%下降到32%(中高碳钢); ➢喷溅率从29%下降到5.4%; ➢停氧到出钢时间从8.5缩到2.5min; ➢铁收得率提高0.49%,石灰消耗减少3kg/t; ➢炉龄提高30%。
目前,炼钢工作者正努力开发底吹喷嘴长寿技术,要点 如下:
➢利用底吹喷嘴前蘑菇头的生长和控制技术,实现喷嘴长寿化; ➢炉役前期,利用粘渣、挂渣和溅渣迅速在喷嘴前端生成透气 蘑菇头,避免喷嘴烧损; ➢炉役中后期注意控制蘑菇头高度,防止堵塞; ➢对堵塞喷嘴采用复通技术。
9
1.4 转炉炼钢自动控制技术
转炉吹炼自动控制分为三个阶段:
3)在氧化条件下,脱磷反应是阳极反应([P]→P5++5e) ,脱硫反应是阴极反应([S]+2e→S2-),所以铁水间同时脱 磷脱硫是可行的,只是需采用较大脱硫能力的熔剂。
4
铁水脱硅工艺技术 1)脱硅是脱磷的必要条件。换言之。铁水须先脱硅,然
后再同时脱磷脱硫,脱硅易于减少转炉石灰用量和渣量。 2)铁水脱硅可在高炉的铁水沟连续进行,也可在铁水罐
3
铁水脱磷工艺技术 1)铁水脱磷可在四种容器中进行:混铁车同时脱硫脱磷、
铁水罐同时脱硫脱磷、铁水包同时脱硫脱磷、转炉铁水脱磷。 2)铁水预处理脱磷反应温度低,热力学条件好,易于脱
磷。铁水中C、Si含量高,提高了铁水磷的活度,有利于脱磷。 由于铁水预处理脱磷具备良好的化学热力学条件,渣钢间
磷的分配系数是炼钢脱磷的5-10倍,因而渣量小,可以控制较 低的渣中FeO含量,脱磷成本低。