转炉炼钢新技术(精选)
转炉炼钢工艺
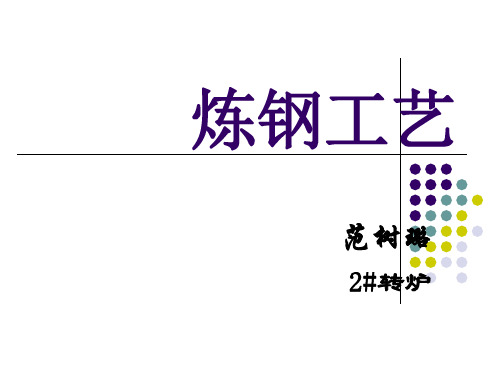
合金钢是指钢中除含有硅和锰作为合金元素或脱氧 元素外,还含有其他合金元素如铬、镍、钼、钛、钒、 铜、钨、铝、钴、铌、锆和稀土元素等,有的还含有 某些非金属元素如硼、氮等的钢。根据钢中合金元素 含量的多少,又可分为低合金钢,中合金钢和高合金 钢。一般合金元素总含量小于3%的为普通低合金钢, 总含量为3%~5%的为低合金钢,大于10%的叫高合金钢, 总含量介于3%~10%之间为中合金钢。按钢中所含有的 主要合金元素不同可分为锰钢、硅钢、硼钢、铬镍钨 钢、铬锰硅钢等。
如果钢中的氧含量较高,FeS与FeO形成的共晶体熔
点更低(940℃),更加剧了钢的“热脆”现象的发 生。 锰可在钢凝固范围内生成MnS和少量的FeS,纯MnS的 熔点为1610℃,共晶体FeS-MnS(占93.5%)的熔点
为1164℃,它们能有效的防止钢热加工过程的“热
脆”。
在 冶 炼 一 般 钢 种 时 要 求 将 [Mn] 控 制 在 0.4%-0.8%。在实际生产中还将[Mn]/[S]比作 为一个指标进行控制,因为研究发现钢中的 [Mn]/[S] 比对钢的热塑性影响很大,从低碳 钢高温下的拉伸实验结果可以发现提高 [Mn]/[S] 比 可 以 提 高 钢 的 热 延 展 性 。 一 般 [Mn]/[S]≥7时不产生热脆。
外来夹杂是指冶炼和浇铸过程中,带入钢液
中的炉渣和耐火材料以及钢液被大气氧化所
形成的氧化物。
内生夹杂包括:
脱氧时的脱氧产物; 钢液温度下降时,硫、氧、氮等杂质元素 溶解度下降而以非金属夹杂形式出现的生 成物; 凝固过程中因溶解度降低、偏析而发生反 应的产物; 固态钢相变溶解度变化生成的产物。
铝(Al)
铝是终脱氧剂,生产镇静钢时,[Al]多在0.005%0.05%,通常为0.01%-0.03%。钢中铝的加入量因氧量而异, 对高碳钢应少加些,而低碳钢则应多加,加入量一般 为:0.3-1.0kg/t钢。
转炉工艺技术

转炉工艺技术转炉工艺技术是一种炼钢方法,通过使用转炉来将生铁转化为钢材。
这种工艺技术具有高效、环保等优点,因此在现代炼钢领域得到广泛应用。
转炉工艺技术的基本原理是在转炉内加入生铁和废钢,然后通过高温熔炼的过程将其转化为合格的钢材。
转炉的炉体由耐火材料构成,能够承受高温和高压的作用。
在炉口处还设有喷口,用来喷入石灰、氧气等物质,调节反应条件。
转炉工艺技术主要有两个阶段:冶炼阶段和调温阶段。
在冶炼阶段,先将炉体加热至适宜的温度,然后加入废钢和生铁。
废钢中的杂质和含碳量会对炉内氧气的消耗产生影响,因此要根据废钢的质量和含碳量来调节氧气的喷入量。
通过废钢和生铁的熔炼,炉内的氧气会和碳发生反应,生成一定量的二氧化碳和一氧化碳,从而将炉内的过剩碳消耗掉,使得钢材的碳含量降低。
在冶炼阶段过后,需要进行调温阶段。
调温的目的是降低熔融钢液的温度,以便在下一步工艺中将其浇制成钢坯。
调温的方法主要有三种:一是通过喷吹冷风,即将冷风喷入转炉中,通过热交换来降低钢液的温度;二是通过喷吹水雾,即喷入水雾来降低炉内的温度;三是通过喷吹冷却物质,如纸浆或粉末来吸收炉内的热量。
这三种调温方法都能有效地降低钢液的温度,确保钢材的质量。
转炉工艺技术相对于其他炼钢方法有许多优点。
首先,转炉的生产效率高。
转炉冶炼的周期短,炉型大,能够一次性冶炼大量的原料,提高生产效率。
其次,转炉冶炼的过程对环境的影响小。
由于转炉工艺是在密闭的炉腔内进行,污染物的排放量较少,能够有效地防止废气和废水的污染。
此外,转炉冶炼能够利用废钢回收再利用,提高资源利用率,减少废物的产生。
总而言之,转炉工艺技术是一种高效、环保的炼钢方法。
通过合理地控制和调节冶炼条件,能够将生铁和废钢转化为合格的钢材,提高钢铁行业的生产效率和产品质量。
转炉工艺技术的广泛应用,推动了钢铁行业的发展,对于国民经济和社会发展起到了重要的促进作用。
关于炼钢新技术的几点介绍
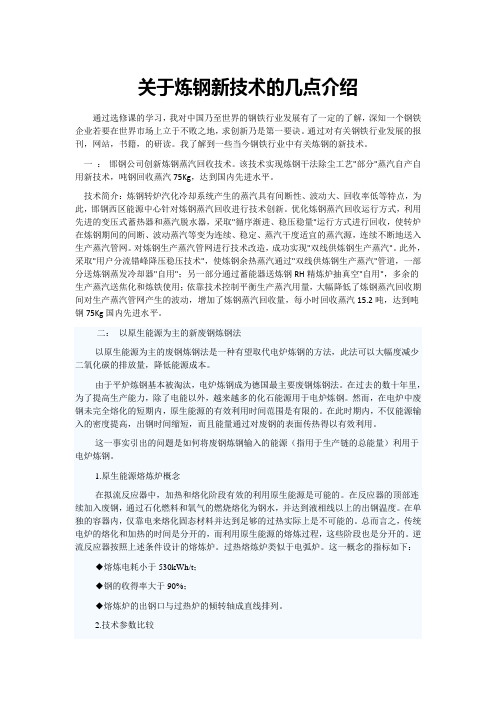
关于炼钢新技术的几点介绍通过选修课的学习,我对中国乃至世界的钢铁行业发展有了一定的了解,深知一个钢铁企业若要在世界市场上立于不败之地,求创新乃是第一要诀。
通过对有关钢铁行业发展的报刊,网站,书籍,的研读。
我了解到一些当今钢铁行业中有关炼钢的新技术。
一:邯钢公司创新炼钢蒸汽回收技术。
该技术实现炼钢干法除尘工艺"部分"蒸汽自产自用新技术,吨钢回收蒸汽75Kg,达到国内先进水平。
技术简介:炼钢转炉汽化冷却系统产生的蒸汽具有间断性、波动大、回收率低等特点,为此,邯钢西区能源中心针对炼钢蒸汽回收进行技术创新。
优化炼钢蒸汽回收运行方式,利用先进的变压式蓄热器和蒸汽脱水器,采取"循序渐进、稳压稳量"运行方式进行回收,使转炉在炼钢期间的间断、波动蒸汽等变为连续、稳定、蒸汽干度适宜的蒸汽源,连续不断地送入生产蒸汽管网。
对炼钢生产蒸汽管网进行技术改造,成功实现"双线供炼钢生产蒸汽"。
此外,采取"用户分流错峰降压稳压技术",使炼钢余热蒸汽通过"双线供炼钢生产蒸汽"管道,一部分送炼钢蒸发冷却器"自用";另一部分通过蓄能器送炼钢RH精炼炉抽真空"自用",多余的生产蒸汽送焦化和炼铁使用;依靠技术控制平衡生产蒸汽用量,大幅降低了炼钢蒸汽回收期间对生产蒸汽管网产生的波动,增加了炼钢蒸汽回收量,每小时回收蒸汽15.2吨,达到吨钢75Kg国内先进水平。
二:以原生能源为主的新废钢炼钢法以原生能源为主的废钢炼钢法是一种有望取代电炉炼钢的方法,此法可以大幅度减少二氧化碳的排放量,降低能源成本。
由于平炉炼钢基本被淘汰,电炉炼钢成为德国最主要废钢炼钢法。
在过去的数十年里,为了提高生产能力,除了电能以外,越来越多的化石能源用于电炉炼钢。
然而,在电炉中废钢未完全熔化的短期内,原生能源的有效利用时间范围是有限的。
唐钢转炉炼钢新技术
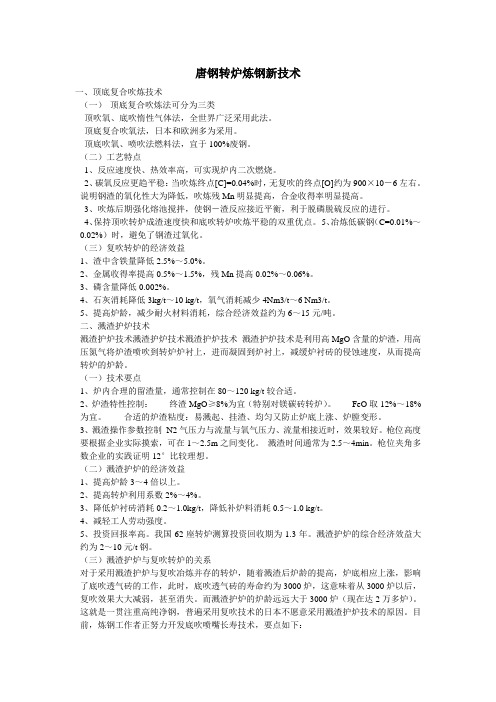
唐钢转炉炼钢新技术一、顶底复合吹炼技术(一)顶底复合吹炼法可分为三类顶吹氧、底吹惰性气体法,全世界广泛采用此法。
顶底复合吹氧法,日本和欧洲多为采用。
顶底吹氧、喷吹法燃料法,宜于100%废钢。
(二)工艺特点1、反应速度快、热效率高,可实现炉内二次燃烧。
2、碳氧反应更趋平稳:当吹炼终点[C]=0.04%时,无复吹的终点[O]约为900×10-6左右。
说明钢渣的氧化性大为降低,吹炼残Mn明显提高,合金收得率明显提高。
3、吹炼后期强化熔池搅拌,使钢-渣反应接近平衡,利于脱磷脱硫反应的进行。
4、保持顶吹转炉成渣速度快和底吹转炉吹炼平稳的双重优点。
5、冶炼低碳钢(C=0.01%~0.02%)时,避免了钢渣过氧化。
(三)复吹转炉的经济效益1、渣中含铁量降低2.5%~5.0%。
2、金属收得率提高0.5%~1.5%,残Mn提高0.02%~0.06%。
3、磷含量降低0.002%。
4、石灰消耗降低3kg/t~10 kg/t,氧气消耗减少4Nm3/t~6 Nm3/t。
5、提高炉龄,减少耐火材料消耗,综合经济效益约为6~15元/吨。
二、溅渣护炉技术溅渣护炉技术溅渣护炉技术溅渣护炉技术溅渣护炉技术是利用高MgO含量的炉渣,用高压氮气将炉渣喷吹到转炉炉衬上,进而凝固到炉衬上,减缓炉衬砖的侵蚀速度,从而提高转炉的炉龄。
(一)技术要点1、炉内合理的留渣量,通常控制在80~120 kg/t较合适。
2、炉渣特性控制:终渣MgO≥8%为宜(特别对镁碳砖转炉)。
FeO取12%~18%为宜。
合适的炉渣粘度:易溅起、挂渣、均匀又防止炉底上涨、炉膛变形。
3、溅渣操作参数控制N2气压力与流量与氧气压力、流量相接近时,效果较好。
枪位高度要根据企业实际摸索,可在1~2.5m之间变化。
溅渣时间通常为2.5~4min。
枪位夹角多数企业的实践证明12°比较理想。
(二)溅渣护炉的经济效益1、提高炉龄3~4倍以上。
2、提高转炉利用系数2%~4%。
转炉炼钢工艺

转炉炼钢工艺转炉炼钢工艺绪论1、转炉炼钢法的分类转炉是以铁水为主要原料的现代炼钢方法。
该种炼钢炉由圆台型炉帽、圆柱型炉身和球缺型炉底组成。
炉身设有可绕之旋转的耳轴,以满足装料和出钢、倒渣操作,故而得名。
酸性空气底吹转炉——贝塞麦炉〔英国1856年〕空气转炉{ 碱性空气底吹转炉——托马斯炉〔德国1878年〕碱性空气侧吹转炉〔中国1952年〕转炉{ 氧气顶吹转炉——LD〔奥地利1952年〕氧气转炉{ 氧气底吹转炉——OBM〔德国1967年〕顶底复吹转炉〔法国1975年〕2、氧气顶吹转炉炼钢法简介(1) 诞生的布景及简称现代炼钢出产首先是一个氧化精炼过程,最初的贝氏炉和托马斯炉之所以采用空气吹炼正是操纵此中的氧。
二次世界大战以后,工业制氧机在美国问世,使操纵纯氧炼钢成为可能,但本来的底吹方式炉底及喷枪极易烧坏。
美国联合碳化物公司于1947年在尝试室进行氧气顶吹转炉的尝试并获成功,定名为BOF。
奥地利闻之即派有关专家前往参不雅学习,回来后于1949年在2吨的转炉长进行半工业性尝试并获成功,1952年、1953年30吨氧气顶吹转炉别离在Linz和Donawitz建成投产,故常简称LD。
1967年12月德国与加拿大合作缔造了氧气底吹转炉,使用双层套管喷嘴并通以气态碳氢化合物进行冷却。
1975年法国研发了顶底复吹转炉,综合了LD和OBM的长处,77年在世界年会上颁发。
(2) 氧气顶吹转炉的特点1〕长处氧气顶吹转炉一经问世就显示出了极大的优越性,世界各国竟相开展,目前成为最主要的炼钢法。
其长处主要暗示在:〔1〕熔炼速度快,出产率高〔一炉钢只需20分钟〕;〔2〕热效率高,冶炼中不需外来热源,且可配用10%~30%的废钢;〔3〕钢的品种多,质量好〔上下碳钢都能炼,S、P、H、N、O及夹杂含量低〕;〔4〕便于开展综合操纵和实现出产过程计算机控制。
2〕错误谬误当然,LD尚存在一些问题,如吹损较高〔10%,〕、所炼钢种仍受必然限制〔冶炼含大量难熔元素和易氧化元素的高合金钢有必然的困难〕等。
转炉高效炼钢技术创新
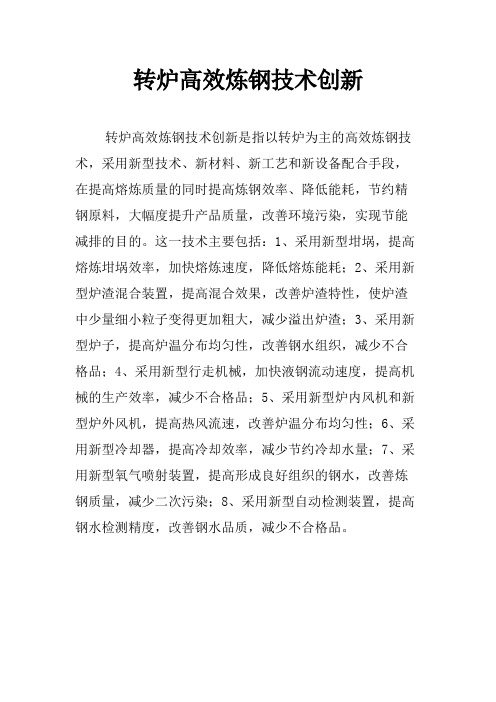
转炉高效炼钢技术创新
转炉高效炼钢技术创新是指以转炉为主的高效炼钢技术,采用新型技术、新材料、新工艺和新设备配合手段,在提高熔炼质量的同时提高炼钢效率、降低能耗,节约精钢原料,大幅度提升产品质量,改善环境污染,实现节能减排的目的。
这一技术主要包括:1、采用新型坩埚,提高熔炼坩埚效率,加快熔炼速度,降低熔炼能耗;2、采用新型炉渣混合装置,提高混合效果,改善炉渣特性,使炉渣中少量细小粒子变得更加粗大,减少溢出炉渣;3、采用新型炉子,提高炉温分布均匀性,改善钢水组织,减少不合格品;4、采用新型行走机械,加快液钢流动速度,提高机械的生产效率,减少不合格品;5、采用新型炉内风机和新型炉外风机,提高热风流速,改善炉温分布均匀性;6、采用新型冷却器,提高冷却效率,减少节约冷却水量;7、采用新型氧气喷射装置,提高形成良好组织的钢水,改善炼钢质量,减少二次污染;8、采用新型自动检测装置,提高钢水检测精度,改善钢水品质,减少不合格品。
浅析大型转炉设备新技术
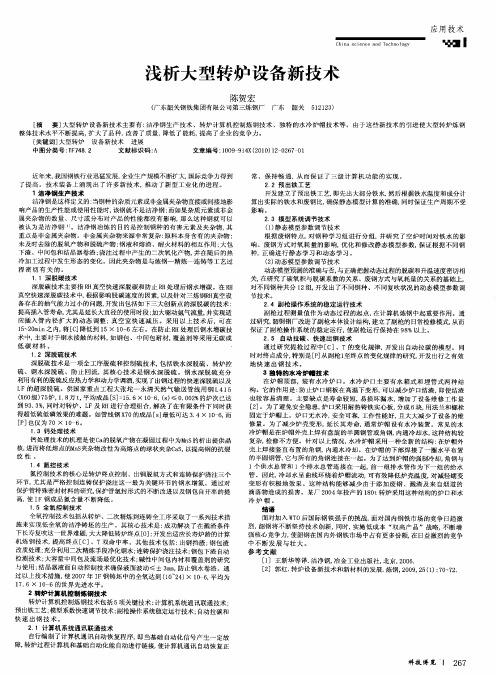
常、 保 持畅 通 , 而 保 证 了三 级 计 算 机 功 能 的实 现 。 从 2 2预 出铁 工艺 开发 建立 了预 出铁 工艺, 即先 出大 部分 铁水, 然后 根据 铁水温 度和 成分 计 算 出实 际 的铁 水和 废钢 比, 确保 静态 模型 计算 的准 确, 同时 保证 生产周 期不 受 影响。 2 3 模 型系 统调 节技 术 . () 态模 型参 数调 节技 术 1静 根 据 废钢 特 点, 对钢 种 学 习组 进行 分 组, 并研 究 了空 炉 时问 对铁 水 的影 响 、废 钢 方 式对 氧 耗量 的影 响 , 化 和修 改静 态 模 型参 数, 证根 据 不 同钢 优 保 种,正确 进 行静 态 学 习和 动 态学 习 。 () 态模 型参数 调节 技术 2动 动态 模型预 测 的准 确与 否, 与正确 把握动 态过程 的脱碳 和升温 速度密切 相 关, 在研 究 了碳氧积 与 脱碳 系数 的关系 、废钢 方式 与氧 耗量 的关 系的基 础上 。 对 不 同钢种 共分 1 组 , 2 开发 出 了不 同钢 种 、不 同复吹 状况 的动 态模 型参数 调 节 技术 。 2 4 副枪操 作 系统 的稳 定运行 技术 . 副枪 过程 测量 值 作为 动态 过程 的起 点 , 在计 算机 炼钢 中起重 要作 用 。通 过研 究I 韶钢钢 厂改进 了副枪 本体设 计结构 , 建立 了副 枪的 日常检修 模式, 从而 保 证 了副枪 操作 系 统 的稳定 运行 , 副 枪运 行保 持在 9 %以上 。 使 8 2 5 自动拉碳 、快速 出钢 技 术 . 通 过 研究 提枪 过 程 中 [ ] C 、T的变 化规 律 , 发 出 自动拉 碳 的模 型 。 同 开 时对 终点 成分, 特别 是 [] 副枪 1 终点 的变 化规律 的研 究, P从 至 开发 出行之 有效 地快速出钢技术 。
转炉炼钢的冶炼原理

转炉炼钢的冶炼原理
转炉炼钢法:这种炼钢法使用的氧化剂是氧气。
把空气鼓入熔融的生铁里,使杂质硅、锰等氧化。
在氧化的过程中放出大量的热量(含1%的硅可使生铁的温度升高200摄氏度),可使炉内达到足够高的温度。
因此转炉炼钢不需要另外使用燃料。
转炉炼钢是在转炉里进行。
转炉的外形就像个梨,内壁有耐火砖,炉侧有许多小孔(风口),压缩空气从这些小孔里吹炉内,又叫做侧吹转炉。
开始时,转炉处于水平,向内注入1300摄氏度的液态生铁,并加入一定量的生石灰,然后鼓入空气并转动转炉使它直立起来。
这时液态生铁表面剧烈的反应,使铁、硅、锰氧化(FeO,SiO2 , MnO,) 生成炉渣,利用熔化的钢铁和炉渣的对流作用,使反应遍及整个炉内。
几分钟后,当钢液中只剩下少量的硅与锰时,碳开始氧化,生成一氧化碳(放热)使钢液剧烈沸腾。
炉口由于溢出的一氧化炭的燃烧而出现巨大的火焰。
最后,磷也发生氧化并进一步生成磷酸亚铁。
磷酸亚铁再跟生石灰反应生成稳定的磷酸钙和硫化钙,一起成为炉渣。
转炉负能炼钢与煤气回收技术(三篇)
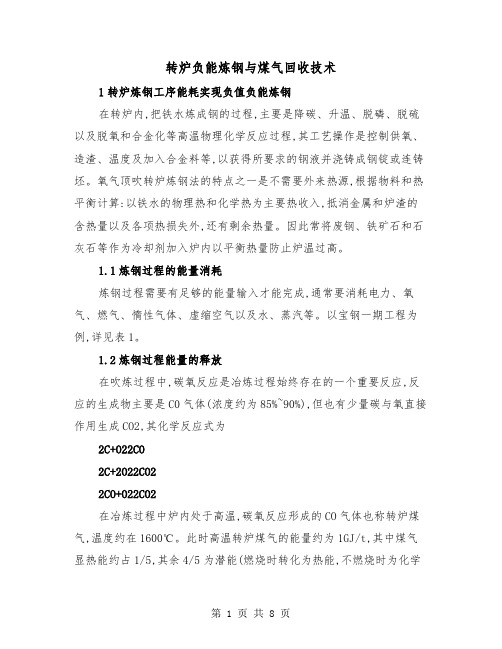
转炉负能炼钢与煤气回收技术1转炉炼钢工序能耗实现负值负能炼钢在转炉内,把铁水炼成钢的过程,主要是降碳、升温、脱磷、脱硫以及脱氧和合金化等高温物理化学反应过程,其工艺操作是控制供氧、造渣、温度及加入合金料等,以获得所要求的钢液并浇铸成钢锭或连铸坯。
氧气顶吹转炉炼钢法的特点之一是不需要外来热源,根据物料和热平衡计算:以铁水的物理热和化学热为主要热收入,抵消金属和炉渣的含热量以及各项热损失外,还有剩余热量。
因此常将废钢、铁矿石和石灰石等作为冷却剂加入炉内以平衡热量防止炉温过高。
1.1炼钢过程的能量消耗炼钢过程需要有足够的能量输入才能完成,通常要消耗电力、氧气、燃气、惰性气体、虚缩空气以及水、蒸汽等。
以宝钢一期工程为例,详见表1。
1.2炼钢过程能量的释放在吹炼过程中,碳氧反应是冶炼过程始终存在的一个重要反应,反应的生成物主要是C0气体(浓度约为85%~90%),但也有少量碳与氧直接作用生成CO2,其化学反应式为2C+O22CO2C+2O22CO22CO+O22CO2在冶炼过程中炉内处于高温,碳氧反应形成的CO气体也称转炉煤气,温度约在1600℃。
此时高温转炉煤气的能量约为1GJ/t,其中煤气显热能约占1/5,其余4/5为潜能(燃烧时转化为热能,不燃烧时为化学能),这就是转炉冶炼过程中释放出的主要能量。
因此,转炉煤气回收利用是炼钢节能降耗的重要途径。
氧气顶吹转炉炼钢过程自台量平衡见图1。
1.3炼钢工序能耗实现负值分析炼钢工序能耗是按生产出每吨合格产品(钢锭或连铸坯)所用的各种能量之和扣除相应回收的能量(标煤)进行计算的。
消耗能量回收能量时,耗能为正值消耗能量-回收能量=0时(称零能炼钢)消耗能量回收能量时,耗能为负值(称负能炼钢)1.4实现负能炼钢是可能的转炉炼钢过程中释放出的能量是以高温煤气为载体,若以热能加以度量分析,具体表现为潜热占83.6%,显热占16.4%,详见图3。
显然,煤气所拥有的能量占总热量中的绝大部分。
炼钢方法
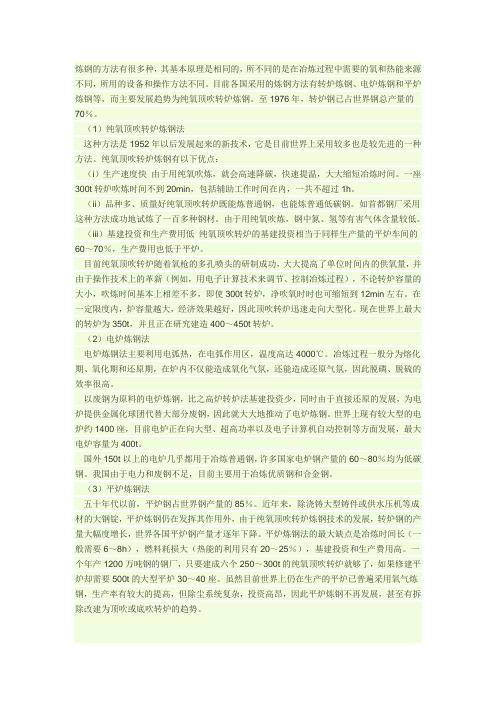
炼钢的方法有很多种,其基本原理是相同的,所不同的是在冶炼过程中需要的氧和热能来源不同,所用的设备和操作方法不同。
目前各国采用的炼钢方法有转炉炼钢、电炉炼钢和平炉炼钢等,而主要发展趋势为纯氧顶吹转炉炼钢。
至1976年,转炉钢已占世界钢总产量的70%。
(1)纯氧顶吹转炉炼钢法这种方法是1952年以后发展起来的新技术,它是目前世界上采用较多也是较先进的一种方法。
纯氧顶吹转炉炼钢有以下优点:(i)生产速度快由于用纯氧吹炼,就会高速降碳,快速提温,大大缩短冶炼时间。
一座300t转炉吹炼时间不到20min,包括辅助工作时间在内,一共不超过1h。
(ii)品种多、质量好纯氧顶吹转炉既能炼普通钢,也能炼普通低碳钢。
如首都钢厂采用这种方法成功地试炼了一百多种钢材。
由于用纯氧吹炼,钢中氮、氢等有害气体含量较低。
(iii)基建投资和生产费用低纯氧顶吹转炉的基建投资相当于同样生产量的平炉车间的60~70%,生产费用也低于平炉。
目前纯氧顶吹转炉随着氧枪的多孔喷头的研制成功,大大提高了单位时间内的供氧量,并由于操作技术上的革新(例如,用电子计算技术来调节、控制冶炼过程),不论转炉容量的大小,吹炼时间基本上相差不多,即使300t转炉,净吹氧时时也可缩短到12min左右。
在一定限度内,炉容量越大,经济效果越好,因此顶吹转炉迅速走向大型化。
现在世界上最大的转炉为350t,并且正在研究建造400~450t转炉。
(2)电炉炼钢法电炉炼钢法主要利用电弧热,在电弧作用区,温度高达4000℃。
冶炼过程一般分为熔化期、氧化期和还原期,在炉内不仅能造成氧化气氛,还能造成还原气氛,因此脱磷、脱硫的效率很高。
以废钢为原料的电炉炼钢,比之高炉转炉法基建投资少,同时由于直接还原的发展,为电炉提供金属化球团代替大部分废钢,因此就大大地推动了电炉炼钢。
世界上现有较大型的电炉约1400座,目前电炉正在向大型、超高功率以及电子计算机自动控制等方面发展,最大电炉容量为400t。
转炉炼钢新工艺、新技术介绍

转炉炼钢新工艺、新技术介绍
1. 全新工艺:
(1)结合电磁加热与旋流燃烧法,开发新型高混镍炼钢车间;
(2)利用ELIM全熔混熔法结合智能化高温处理技术,开发新的低Nb、Ti、V 低碳钢车间;
(3)将现代化技术与新型转炉及冶炼设备相结合,提高转炉炼钢工艺稳定性和质量水平。
2. 新技术:
(1)引入新鲜管理思想,通过严格控制热处理技术,满足不同用户需求;
(2)应用优化转炉流体动力学计算和智能调节技术,调节炉内温度和化学成份,提高厚度均匀性;
(3)应用智能温度场控制技术,利用计算机模拟和实时检测炉内温度的分布,控制炉温的变化趋势,以提高钢材的出炉精度。
转炉炼钢安全技术(二篇)

转炉炼钢安全技术(1)准备工作转炉炼钢开炉前的准备工作非常重要, 稍有忽视就可能酿成重大人身事故。
吹炼时, 发现烟罩漏水, 应马上停吹, 关闭中压水阀门, 检修焊接, 直至不漏水为止。
检查管道与阀门时, 要有监护和检查二人同时进行, 严禁吸烟, 周围不得有明火, 防止漏氧燃烧。
在氧气管道周围, 不准堆放易燃易爆和油污物。
炉盖上面焊有水箱, 转炉倒炉时, 钢水不能碰水冷炉口, 以免引起事故。
冶炼过程中如发现水冷炉口漏水, 应立即停吹, 派二人检查进水阀门并修复。
(2)冶炼过程的安全①兑铁水后吹第一炉钢时, 温度要升高, 吹炼时间要长, 这样可避免发生塌炉。
尽管如此, 新开炉子倒渣出钢时, 周围人员还应让开, 因为这时炉体尚不稳定, 烧结不牢固, 而炉内气流非常激烈, 炉内渣子易喷出炉外, 造成炉衬剥落, 严重时可能塌炉。
②装料前应将炉内残钢残渣倒掉。
装料时先装废钢和铁矿石, 后装适当温度的铁水。
加入的废钢原料要仔细清理, 不能把带炸药的废武器, 盛有水、冰、雪的容器加入炉内。
发现废旧炮弹不许乱拆乱动, 应及时交有关部门处理。
③在冶炼过程中, 炉长和摇炉工要密切注意火焰的变化, 当吹到终点火焰还不下降, 周围有烟雾上升时, 应提前检查。
发现喷枪渗水时, 应迅速调换喷枪, 如果继续吹炼, 喷头大量漏水, 会造成严重的爆炸事故。
④发生喷溅时, 火星冲出氮(或蒸汽)封口, 可将氧气皮管烧坏,造成设备事故, 如果渣子不化而又采取高枪位的不正常操作, 造成连续性的剧烈大喷溅, 危害更大。
还有一种是动炉倒渣大喷溅, 爆炸威力大, 往往会炸坏摇炉房的仪器设备、灼伤人员。
出现这种大喷溅的原因是渣子氧化性过高、氧气截止阀失效, 漏氧时间过长等, 因而渣子表面氧量高, 炉子倾动时, 产生大量泡沫喷出炉口。
⑤发生跑钢事故时, 首先应搞清跑钢部位, 以便采取措施。
窜钢时应从速调整化学成分, 快速出炉, 以免发生设备和人身事故。
转炉炼钢原理及工艺介绍
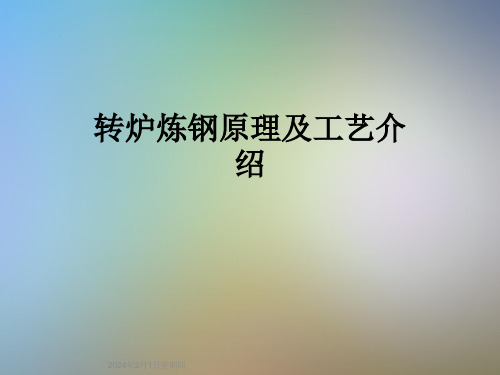
锰的氧化反应有三种情况:
(1)锰与气相中的氧直接作用
[Mn]+ 1/2{O2}=(MnO)
(2)锰与溶于金属中的氧作用
[Mn]+ [O2] =(MnO)
(3)锰的氧化与还原
3)锰与炉渣中氧化亚铁作用
[Mn]+(FeO)=(MnO)+ [Fe]
第三个反应在炉渣——金属界面上迸行,是锰氧化的主要反应。
锰的氧化还原与硅的氧化还原相比有以下基本特点:
1)在冶炼初期锰和硅一样被迅速大量氧化,但锰的氧化程度要低些
,这是由于硅与氧的结合能力大于锰与氧的结合能力;
2)MnO为弱碱性氧化物,在碱性渣中( MnO)大部分呈自由状态存
在。因此,在一定条件下可以被还原。由于锰的氧化反应是放热反应,故
温度升高有利于锰的还原。所以在生产实践中冶炼后期熔池中会出现回锰
1)在某一温度下,几种元素同时和氧相遇时,位置低的元素先氧化。如1500℃ 时,氧化顺序为Al、Si、C、V、Mn。
2)位置低的元素可将位置高的氧化物还原。炼钢过程中脱氧就是利用Al、Si等 元素将FeO还原。
3)CO的分解压曲线的斜率与其它氧化物的不同,它与Si、Mn、V等的氧化物分 解与压CO曲分线解有压一曲交线点相,交此点点对所应对的应温的度温为度15称30为℃氧,化当转t>化15温30度℃。时例,如Si,先S于iOC2被分氧解化压;曲当线 t<1530℃时,则C先于Si被氧化。1530℃即为Si、C的氧化转化温度。
• 所谓炼钢,就是通过冶炼降低生铁中的 碳和去除有害杂质,在根据对钢性能的要求 加入适量的合金元素,使其成为具有高的强 度、韧性或其他特殊性能的钢。
•二、炼钢基本原理
• 因此,炼钢的基本任务可归纳为:
转炉炼钢新技术
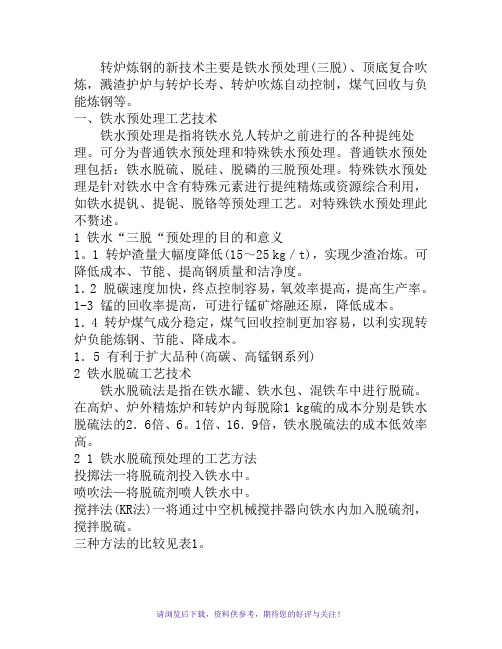
转炉炼钢的新技术主要是铁水预处理(三脱)、顶底复合吹炼,溅渣护炉与转炉长寿、转炉吹炼自动控制,煤气回收与负能炼钢等。
一、铁水预处理工艺技术铁水预处理是指将铁水兑人转炉之前进行的各种提纯处理。
可分为普通铁水预处理和特殊铁水预处理。
普通铁水预处理包括:铁水脱硫、脱硅、脱磷的三脱预处理。
特殊铁水预处理是针对铁水中含有特殊元素进行提纯精炼或资源综合利用,如铁水提钒、提铌、脱铬等预处理工艺。
对特殊铁水预处理此不赘述。
1 铁水“三脱“预处理的目的和意义1。
1 转炉渣量大幅度降低(15~25 kg/t),实现少渣冶炼。
可降低成本、节能、提高钢质量和洁净度。
1.2 脱碳速度加快,终点控制容易,氧效率提高,提高生产率。
1-3 锰的回收率提高,可进行锰矿熔融还原,降低成本。
1.4 转炉煤气成分稳定,煤气回收控制更加容易,以利实现转炉负能炼钢、节能、降成本。
1.5 有利于扩大品种(高碳、高锰钢系列)2 铁水脱硫工艺技术铁水脱硫法是指在铁水罐、铁水包、混铁车中进行脱硫。
在高炉、炉外精炼炉和转炉内每脱除1 kg硫的成本分别是铁水脱硫法的2.6倍、6。
1倍、16.9倍,铁水脱硫法的成本低效率高。
2 1 铁水脱硫预处理的工艺方法投掷法一将脱硫剂投入铁水中。
喷吹法—将脱硫剂喷人铁水中。
搅拌法(KR法)一将通过中空机械搅拌器向铁水内加入脱硫剂,搅拌脱硫。
三种方法的比较见表1。
2。
2 铁水脱硫剂的选择元素的脱硫能力,由高到低依次为:CaC 、NaO 、Mg、BaO、CaO、MnO MgO工业中常用的脱硫剂有:CaO系、CaO+CaC 系、CaC 、CaO+Mg 系、Mg系。
几种脱硫剂的特点见表2。
3 铁水脱磷工艺技术3。
1 铁水脱磷可在四种容器中进行:混铁车同时脱硫脱磷;铁水罐同时脱硫脱磷;铁水包同时脱硫脱磷;转炉铁水脱磷。
3。
2 铁水预处理脱磷反应温度低(1 300℃~1 350℃),热力学条件好,易于脱磷。
铁水中c、si含量高,提高了铁水磷的活度,有利于脱磷。
转炉炼钢工艺(主要是热平衡计算)
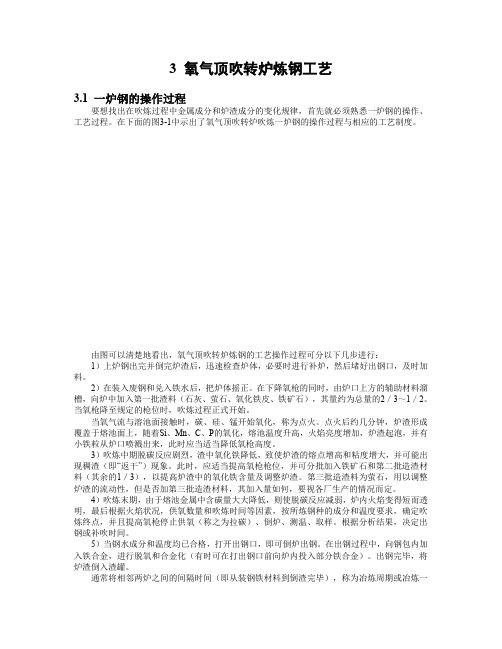
3 氧气顶吹转炉炼钢工艺3.1 一炉钢的操作过程要想找出在吹炼过程中金属成分和炉渣成分的变化规律,首先就必须熟悉一炉钢的操作、工艺过程。
在下面的图3-1中示出了氧气顶吹转炉吹炼一炉钢的操作过程与相应的工艺制度。
由图可以清楚地看出,氧气顶吹转炉炼钢的工艺操作过程可分以下几步进行:1)上炉钢出完并倒完炉渣后,迅速检查炉体,必要时进行补炉,然后堵好出钢口,及时加料。
2)在装入废钢和兑入铁水后,把炉体摇正。
在下降氧枪的同时,由炉口上方的辅助材料溜槽,向炉中加入第一批渣料(石灰、萤石、氧化铁皮、铁矿石),其量约为总量的2/3~1/2。
当氧枪降至规定的枪位时,吹炼过程正式开始。
当氧气流与溶池面接触时,碳、硅、锰开始氧化,称为点火。
点火后约几分钟,炉渣形成覆盖于熔池面上,随着Si、Mn、C、P的氧化,熔池温度升高,火焰亮度增加,炉渣起泡,并有小铁粒从炉口喷溅出来,此时应当适当降低氧枪高度。
3)吹炼中期脱碳反应剧烈,渣中氧化铁降低,致使炉渣的熔点增高和粘度增大,并可能出现稠渣(即“返干”)现象。
此时,应适当提高氧枪枪位,并可分批加入铁矿石和第二批造渣材料(其余的1/3),以提高炉渣中的氧化铁含量及调整炉渣。
第三批造渣料为萤石,用以调整炉渣的流动性,但是否加第三批造渣材料,其加入量如何,要视各厂生产的情况而定。
4)吹炼末期,由于熔池金属中含碳量大大降低,则使脱碳反应减弱,炉内火焰变得短而透明,最后根据火焰状况,供氧数量和吹炼时间等因素,按所炼钢种的成分和温度要求,确定吹炼终点,并且提高氧枪停止供氧(称之为拉碳)、倒炉、测温、取样。
根据分析结果,决定出钢或补吹时间。
5)当钢水成分和温度均已合格,打开出钢口,即可倒炉出钢。
在出钢过程中,向钢包内加入铁合金,进行脱氧和合金化(有时可在打出钢口前向炉内投入部分铁合金)。
出钢完毕,将炉渣倒入渣罐。
通常将相邻两炉之间的间隔时间(即从装钢铁材料到倒渣完毕),称为冶炼周期或冶炼一炉钢的时间。
转炉炼钢新工艺、新技术介绍
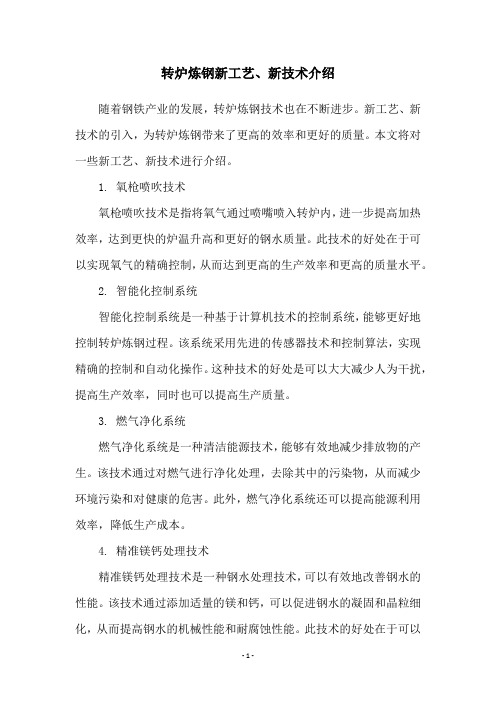
转炉炼钢新工艺、新技术介绍
随着钢铁产业的发展,转炉炼钢技术也在不断进步。
新工艺、新技术的引入,为转炉炼钢带来了更高的效率和更好的质量。
本文将对一些新工艺、新技术进行介绍。
1. 氧枪喷吹技术
氧枪喷吹技术是指将氧气通过喷嘴喷入转炉内,进一步提高加热效率,达到更快的炉温升高和更好的钢水质量。
此技术的好处在于可以实现氧气的精确控制,从而达到更高的生产效率和更高的质量水平。
2. 智能化控制系统
智能化控制系统是一种基于计算机技术的控制系统,能够更好地控制转炉炼钢过程。
该系统采用先进的传感器技术和控制算法,实现精确的控制和自动化操作。
这种技术的好处是可以大大减少人为干扰,提高生产效率,同时也可以提高生产质量。
3. 燃气净化系统
燃气净化系统是一种清洁能源技术,能够有效地减少排放物的产生。
该技术通过对燃气进行净化处理,去除其中的污染物,从而减少环境污染和对健康的危害。
此外,燃气净化系统还可以提高能源利用效率,降低生产成本。
4. 精准镁钙处理技术
精准镁钙处理技术是一种钢水处理技术,可以有效地改善钢水的性能。
该技术通过添加适量的镁和钙,可以促进钢水的凝固和晶粒细化,从而提高钢水的机械性能和耐腐蚀性能。
此技术的好处在于可以
满足不同品种钢的要求,提高钢水质量水平。
转炉炼钢原理及工艺介绍

转炉炼钢原理及工艺介绍引言转炉炼钢是一种常用的钢铁生产工艺,具有高效、灵活、环保等特点。
本文将介绍转炉炼钢的原理及工艺流程。
一、转炉炼钢原理转炉炼钢是通过在高温下将生铁与废钢等原料进行反应,去除杂质,调整合金成分来生产钢铁。
其原理基于以下几个重要的化学反应步骤:1.氧化反应:在高温下,将生铁中的杂质氧化为气体或溶于渣中。
主要的氧化反应有:Fe+C+O2=FeO+CO、Mn+C+O2=MnO+CO等。
2.还原反应:在氧化反应的基础上,通过还原剂(如脱氧剂)来还原产生的氧化物。
主要还原反应有:FeO+CO=Fe+CO2、MnO+CO=Mn+CO2等。
3.合金化反应:在还原反应的基础上,通过加入适量合金元素来调整合金成分。
合金化反应可以通过添加合金块、废钢等方式实现。
通过以上化学反应的组合,转炉炼钢可以控制合金成分、去除杂质、调整温度等,从而得到符合要求的钢铁产品。
二、转炉炼钢工艺介绍转炉炼钢的工艺可以分为以下几个主要步骤:1.预处理:生铁、废钢等原料经过破碎、除尘等处理后,进入转炉炉前料斗。
2.加料:原料从炉前料斗通过螺旋输送机被输送至转炉炉缸中。
3.预热:将炉缸中的原料进行预热,以提高反应效果。
4.吹炼:将炉底引入的高纯氧吹入炉缸中,通过氧化反应和还原反应去除杂质、调整合金成分。
5.加料:在吹炼过程中,适量添加合金块、废钢等调整合金成分。
6.测温:通过测温仪器监测和调节炉内温度。
7.出渣:通过倾炉装置将产生的渣浆从转炉中排出。
8.抽炉:将炉内得到的钢液通过倾炉装置倾出,并进行钢液处理(如脱氧、出气、精炼等)9.浇铸:将经过处理的钢液进行浇铸,得到需要的钢铁产品。
三、转炉炼钢的优势转炉炼钢工艺具有以下几个优势:1.高效:转炉炼钢的操作灵活,能够快速调整合金成分和生产规格,生产效率高。
2.资源利用:转炉炼钢可以利用废钢等再生资源,减少资源浪费。
3.环保:转炉炼钢排放的烟尘、废气等污染物可以通过环保设施进行处理,达到环保要求。