齿轮设计计算 (2)
齿轮的设计与计算
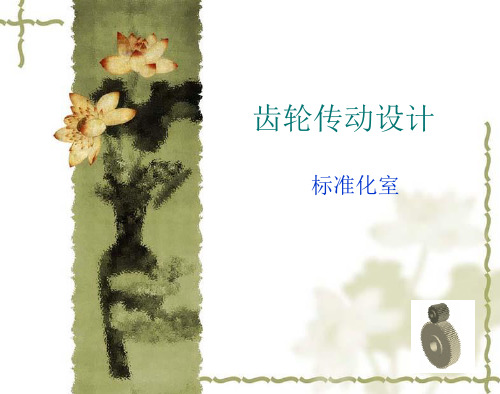
标准化室
目录
❖ §1.齿轮传动的特点及分类 ❖ §2.渐开线直齿圆柱齿轮各部分名称、基本参数和
几何尺寸 ❖ §3.变位齿轮传动和变位系数的选择 ❖ §4.渐开线直齿圆柱齿轮传动的几何计算 ❖ §5.齿轮材料及热处理
§6.渐开线直齿圆柱齿轮的强度计算 §7.圆柱齿轮精度 §8.渐开线圆柱齿轮图样上应注明的尺寸数据 §9.直齿圆锥齿轮传动 §10.齿轮结构设计 小结
m越大,p越大,轮齿的尺寸也越大,齿轮承受载荷的 能力也越高。
(8)齿顶高 齿顶圆和分度圆间的径向距离,用ha表示。 ha=ha*m ( ha*—齿顶高系数)
(9)齿根高 分度圆和齿根圆间的径向距离,用hf表示。
h f=(ha*+c*)m (c* —顶隙系数) 我国标准规定:正常齿制ha*=1 ,c*=0.25
二、齿轮的常用材料及热处理
1.锻钢 锻钢因具有强度高、韧性好、便于制造、便于热处理
等优点,大多数齿轮都用锻钢制造。
(1)软齿面齿轮:齿面硬度<350HBS,常用中碳钢和中 碳合金钢,如45钢、40Cr、35SiMn等材料,进行调质或 正火处理。这种齿轮适用于强度、精度要求不高的场合, 轮坯经过热处理后进行插齿或滚齿,生产便利、成本较低。
三、齿根弯曲疲劳强度计算 (摘自GB/T 3480-1997 渐开线圆柱齿轮承载能力计算方法)
轮齿的弯曲强度校核公式为
F
2KT1 bd1m
YFYs
2KT1 bm2 z1
YF
YS
[ F ](MPa)
将齿宽系数
d
b d
代入上式,得弯曲强度的设计公式
m
1.263
d
KT1
z12
齿轮的基本参数和计算公式

齿轮的基本参数和计算公式齿轮是一种常见的机械元件,广泛应用于机械传动系统中。
了解齿轮的基本参数和计算公式对于正确设计和选择齿轮传动具有重要的意义。
下面将详细介绍齿轮的基本参数和计算公式。
一、齿轮的基本参数1.分度圆直径(D):齿轮两侧齿槽最低点所在的圆的直径,是齿轮设计的基本参数。
2.齿数(z):齿轮上的齿的数量。
齿数一般为整数,两个齿轮的齿数比可以决定齿轮传动的速比。
3.法向模数(m):齿轮的模数,是齿轮设计中的重要参数。
可以通过齿轮的公称齿数和分度圆直径来计算。
4.齿廓圆直径(D_a):位于齿槽底部的圆的直径,决定了齿轮传动的拓扑形状。
5.齿顶圆直径(D_f):齿槽的顶部所在的圆的直径,与齿槽的接触和传力能力有关。
6.齿底圆直径(D_b):齿槽底部所在的圆的直径,与齿槽的接触和传力能力有关。
7.齿距(p):相邻齿的中心距离,是齿轮传动中两个齿轮之间的齿距参数。
8.压力角(α):相接触齿廓线与法线之间的夹角,影响着齿轮接触性能和传力能力。
二、齿轮的计算公式1.模数(m)的计算公式:m=D/z2.齿距(p)的计算公式:p=πm3.弧齿高(h_a)和压力角(α)的计算公式:h_a = m(cos(α) + cos(α - φ))其中,φ为齿顶圆角。
4.齿顶高(h_f)和压力角(α)的计算公式:h_f = m(cos(α) + cos(α + φ))其中,φ为齿顶圆角。
5.齿厚(s)的计算公式:s = m(π/2 + tan(α) - α)6.齿廓圆直径(D_a)的计算公式:D_a=D+2m7.齿顶圆直径(D_f)的计算公式:D_f = D + 2m(cos(α) + cos(α + φ))8.齿底圆直径(D_b)的计算公式:D_b = D - 2m(cos(α) + cos(α - φ))需要注意的是,上述公式中齿顶圆角(φ)是一个常量,一般情况下取20°。
三、齿轮的计算过程1.根据传动比确定主动轮的分度圆直径和齿数。
齿轮齿条设计计算公式

齿轮齿条设计计算公式齿轮和齿条是机械传动中常见的元件,用于传递动力和转速。
齿轮齿条的设计计算是设计师在进行齿轮齿条设计时所必须掌握的知识。
本文将介绍齿轮齿条设计计算的一些基本公式和原理。
一、齿轮设计计算公式1. 齿数计算公式齿数是齿轮设计中最基本的参数之一,可以通过以下公式计算:N = (π * D) / m其中,N为齿数,D为齿轮直径,m为模数。
2. 齿轮间距计算公式齿轮间距是指两个相邻齿轮之间的中心距离,可以通过以下公式计算:P = (N1 + N2) / 2 * m其中,P为齿轮间距,N1和N2分别为两个相邻齿轮的齿数,m为模数。
3. 齿轮传动比计算公式齿轮传动比是指两个相邻齿轮的转速之比,可以通过以下公式计算:i = N2 / N1其中,i为传动比,N1和N2分别为两个相邻齿轮的齿数。
4. 齿轮模数计算公式齿轮模数是指齿轮齿数和齿轮直径之间的比值,可以通过以下公式计算:m = D / N其中,m为模数,D为齿轮直径,N为齿数。
二、齿条设计计算公式1. 齿条模数计算公式齿条模数是指齿条齿数和齿条长度之间的比值,可以通过以下公式计算:m = L / N其中,m为模数,L为齿条长度,N为齿数。
2. 齿条传动比计算公式齿条传动比是指齿条的移动距离与齿轮转动角度之间的比值,可以通过以下公式计算:i = L / (π * D)其中,i为传动比,L为齿条的移动距离,D为齿轮的直径。
3. 齿条齿数计算公式齿条齿数是指齿条上的齿数,可以通过以下公式计算:N = L / m其中,N为齿数,L为齿条长度,m为模数。
三、齿轮齿条设计计算实例假设有一对齿轮,其中一个齿轮的齿数为20,直径为40mm,另一个齿轮的齿数为40,直径为80mm,模数为2mm。
我们可以通过上述公式进行计算。
根据齿数计算公式,可得第一个齿轮的齿数为20,第二个齿轮的齿数为40。
根据齿轮间距计算公式,可得齿轮间距为(20+40)/2*2=60mm。
齿轮设计计算说明书

齿轮设计计算说明书齿轮设计计算说明书设计背景:齿轮是广泛应用于机械传动系统中的一种重要零件,常用于减速器、变速器、转向器等机械装置中。
在机械设计中,齿轮需要满足一定的强度和耐久性要求,因此需要进行齿轮设计计算。
本说明书将对齿轮设计的相关计算进行详细介绍。
设计计算:1.齿轮参数计算:1.1 齿轮模数(m)的计算公式为:m = K * (√(T_s / (Y * σ))) / (n * z)其中,K为修形系数,取值1.25;T_s为传递的扭矩;Y为齿轮面展向材料的弹性模量;σ为齿轮材料抗弯应力;n为齿轮转速(rpm);z为齿轮的齿数。
1.2 中心距(a)的计算公式为:a = ((z1 + z2) * m) / 2其中,z1和z2分别为两个齿轮的齿数。
1.3 齿轮模数(m)取值范围为0.5mm至50mm。
1.4 中心距(a)的设计范围应满足:1.4.1 当m≤3mm时,a≥2.5m。
1.4.2 当m>3mm时,a≥2.2m。
2.齿轮几何参数计算:2.1 齿高(h)的计算公式为:h = 2.25 * m2.2 齿宽(b)的计算公式为:b = 0.85 * m * z2.3 压力角(α)的计算公式为:α = cos^(-1)((a * sin(β)) / ((z1 + z2) / 2))其中,β为齿轮的压力角。
3.齿轮强度计算:3.1 计算传递的扭矩(T_s):T_s = (P * 60) / (2 * π * n)其中,P为传递的功率(kW);n为齿轮转速(rpm)。
3.2 计算齿轮面弯矩(F)的公式为:F = (T_s * K_f) / (d1 * m)其中,K_f为齿轮面弯曲系数;d1为齿轮1的基圆直径。
3.3 计算转矩系数(K_v):K_v = 1.5 * C_v * (b / m)^(0.25)其中,C_v为转矩载荷系数。
3.4 计算齿轮面张力(F_t)的公式为:F_t = (K_v * F) / b3.5 计算齿轮失效应力(σ_f)的公式为:σ_f = (F_t * K_H) / (b * m)其中,K_H为齿轮荷载分布系数。
齿轮传动的强度设计计算

1. 齿面接触疲劳强度的计算齿面接触疲劳强度的计算中,由于赫兹应力是齿面间应力的主要指标,故把赫兹应力作为齿面接触应力的计算基础,并用来评价接触强度。
齿面接触疲劳强度核算时,根据设计要求可以选择不同的计算公式。
用于总体设计和非重要齿轮计算时,可采用简化计算方法;重要齿轮校核时可采用精确计算方法。
分析计算表明,大、小齿轮的接触应力总是相等的。
齿面最大接触应力一般出现在小轮单对齿啮合区内界点、节点和大轮单对齿啮合区内界点三个特征点之一。
实际使用和实验也证明了这一规律的正确。
因此,在齿面接触疲劳强度的计算中,常采用节点的接触应力分析齿轮的接触强度。
强度条件为:大、小齿轮在节点处的计算接触应力均不大于其相应的许用接触应力,即:⑴圆柱齿轮的接触疲劳强度计算1)两圆柱体接触时的接触应力在载荷作用下,两曲面零件表面理论上为线接触或点接触,考虑到弹性变形,实际为很小的面接触。
两圆柱体接触时的接触面尺寸和接触应力可按赫兹公式计算。
两圆柱体接触,接触面为矩形(2axb),最大接触应力σHmax位于接触面宽中线处。
计算公式为:接触面半宽:最大接触应力:•F——接触面所受到的载荷•ρ——综合曲率半径,(正号用于外接触,负号用于内接触)•E1、E2——两接触体材料的弹性模量•μ1、μ2——两接触体材料的泊松比2)齿轮啮合时的接触应力两渐开线圆柱齿轮在任意一处啮合点时接触应力状况,都可以转化为以啮合点处的曲率半径ρ1、ρ2为半径的两圆柱体的接触应力。
在整个啮合过程中的最大接触应力即为各啮合点接触应力的最大值。
节点附近处的ρ虽然不是最小值,但节点处一般只有一对轮齿啮合,点蚀也往往先在节点附近的齿根表面出现,因此,接触疲劳强度计算通常以节点为最大接触应力计算点。
参数直齿圆柱齿轮斜齿圆柱齿轮节点处的载荷为综合曲率半径为接触线的长度为,3)圆柱齿轮的接触疲劳强度将节点处的上述参数带入两圆柱体接触应力公式,并考虑各载荷系数的影响,得到:接触疲劳强度的校核公式为:接触疲劳强度的设计公式为:•KA——使用系数•KV——动载荷系数•KHβ——接触强度计算的齿向载荷分布系数•KHα——接触强度计算的齿间载荷分配系数•Ft——端面内分度圆上的名义切向力,N;•T1——端面内分度圆上的名义转矩,N.mm;•d1——小齿轮分度圆直径,mm;•b ——工作齿宽,mm,指一对齿轮中的较小齿宽;•u ——齿数比;•ψd——齿宽系数,指齿宽b和小齿轮分度圆直径的比值(ψd=b/d1)。
第二章 二级圆柱齿轮减速器的设计计算

第二章二级圆柱齿轮减速器的设计计算2.1、减速器的条件设计热处理车间清洗零件所用的传送设备上的二级圆柱齿轮减速器。
要求如下:单向运转,工作平稳,两班值工作,每班工作8小时,每年工作250日,传送带容许误差为5%,减速器小批量生产,使用年限为六年。
2.2、所选参数如下传送带所需扭矩为1500N•m传送带运行速度为0.85m/s传送带鼓轮直径为350mm2.3、方案的草图如下图2-1 传动方案草图1为带传动的效率η2为轴承的效率η3为齿轮传动效率η4为联轴器的传动效率η5为鼓轮上的传动效率η2.4、设计计算2.4.1、传动方案的拟定根据要求电机与减速器间选用V 带传动,减速器与工作机间选用联轴器传动,减速器为二级圆柱直齿齿轮减速器。
方案草图如图2.1。
2.4.2、电动机的选择1、电机类型和结构根据电源及工作机工作条件,工作平稳,单向运转,两班制工作,选用Y 型鼠笼式交流电机,卧式封闭结构。
2、电机容量 n =w Dv π100060 =60×1000×0.85/(3.14×350) =46.42r/min 卷筒所需功率P ===2×1500×0.85×1000/(1000×350)w 1000TwDTv10002=7.29kw传动装置的总效率η=ηηη2ηη124345取V 带的效率η=0.961轴承的效率η=0.982直齿圆柱齿轮的传动效率η=0.993联轴器的效率η=0.994鼓轮上的传动效率η=0.965总效率η=0.96×0.98×0.99×0.99×0.96=0.81 42则,电动机的输出功率P =P /η=7.29/0.81=9.0 Kw ed W 3、电动机额定功率 P ed由已有的标准电机可知,所选择电机的额定功率 P =11 Kw ed 4、电动机转速为便于选择电动机的转速,先推算电动机的可选范围,V 带传动常用的传动比i 范围是2~4,两级圆柱齿轮减速器传动比i ´范围是8~40,那么电动机的转速可选范围为:742.56~7425.6r/min 。
齿轮齿条设计计算公式
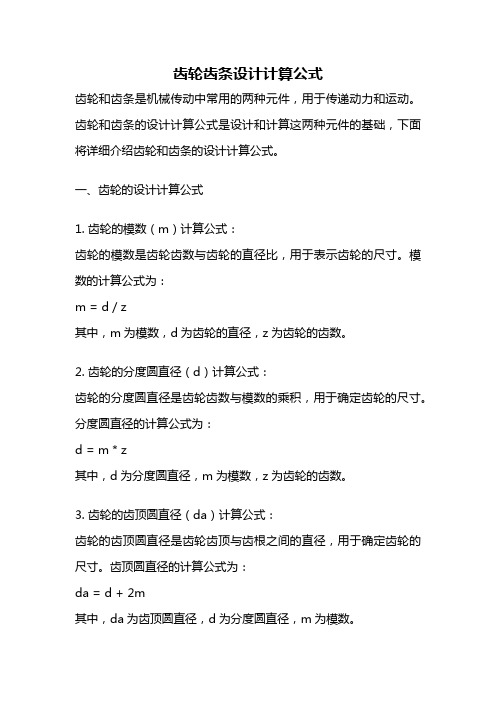
齿轮齿条设计计算公式齿轮和齿条是机械传动中常用的两种元件,用于传递动力和运动。
齿轮和齿条的设计计算公式是设计和计算这两种元件的基础,下面将详细介绍齿轮和齿条的设计计算公式。
一、齿轮的设计计算公式1. 齿轮的模数(m)计算公式:齿轮的模数是齿轮齿数与齿轮的直径比,用于表示齿轮的尺寸。
模数的计算公式为:m = d / z其中,m为模数,d为齿轮的直径,z为齿轮的齿数。
2. 齿轮的分度圆直径(d)计算公式:齿轮的分度圆直径是齿轮齿数与模数的乘积,用于确定齿轮的尺寸。
分度圆直径的计算公式为:d = m * z其中,d为分度圆直径,m为模数,z为齿轮的齿数。
3. 齿轮的齿顶圆直径(da)计算公式:齿轮的齿顶圆直径是齿轮齿顶与齿根之间的直径,用于确定齿轮的尺寸。
齿顶圆直径的计算公式为:da = d + 2m其中,da为齿顶圆直径,d为分度圆直径,m为模数。
4. 齿轮的齿根圆直径(df)计算公式:齿轮的齿根圆直径是齿轮齿根与齿顶之间的直径,用于确定齿轮的尺寸。
齿根圆直径的计算公式为:df = d - 2.2m其中,df为齿根圆直径,d为分度圆直径,m为模数。
5. 齿轮的齿宽(b)计算公式:齿轮的齿宽是齿轮齿根与齿顶之间的宽度,用于确定齿轮的尺寸。
齿宽的计算公式为:b = m * zc其中,b为齿宽,m为模数,zc为齿轮齿数系数。
二、齿条的设计计算公式1. 齿条的模数(m)计算公式:齿条的模数是齿条齿数与齿条的厚度比,用于表示齿条的尺寸。
模数的计算公式为:m = t / z其中,m为模数,t为齿条的厚度,z为齿条的齿数。
2. 齿条的分度圆直径(d)计算公式:齿条的分度圆直径是齿条齿数与模数的乘积,用于确定齿条的尺寸。
分度圆直径的计算公式为:d = m * z其中,d为分度圆直径,m为模数,z为齿条的齿数。
3. 齿条的基圆直径(db)计算公式:齿条的基圆直径是齿条齿槽底部的直径,用于确定齿条的尺寸。
基圆直径的计算公式为:db = d - 2m其中,db为基圆直径,d为分度圆直径,m为模数。
齿轮(设计手册)(二)

齿轮设计的一般准则(二)引言:在齿轮系统设计中,遵循一般准则是确保齿轮传动系统的性能和可靠性的重要因素之一。
本文将深入探讨齿轮设计的一般准则,包括齿轮的噪音控制、材料选择、润滑和冷却、加工和装配以及齿轮系统的测试与验证,以帮助工程师和设计师在实际项目中确保齿轮系统的高效运行。
正文:1. 齿轮的噪音控制- 通过减小齿轮的齿距、模数和齿数来降低齿轮传动的噪音水平。
- 采用切向位移齿形设计和优化齿轮的螺旋角度等方法来减少齿轮系统的噪音产生。
- 使用噪音阻尼材料和减振机构来有效降低齿轮传动系统的振动和噪音。
2. 材料选择- 根据齿轮传动系统的工作条件和负载要求选择合适的齿轮材料,如钢、铸铁、铝合金等。
- 注意齿轮材料的硬度、强度、韧性和耐磨性等性能指标,以确保齿轮系统的寿命和可靠性。
- 在特殊工况下,考虑使用表面处理、热处理等工艺来增强齿轮材料的性能。
3. 润滑和冷却- 在齿轮设计中充分考虑润滑系统,使用合适的润滑剂来降低齿轮系统的摩擦和磨损。
- 设计合理的冷却系统来控制齿轮温度,避免齿轮因温度过高而变形或退化。
- 考虑使用外部润滑和冷却装置来优化齿轮系统的工作环境。
4. 加工和装配- 采用先进的齿轮加工方法,如磨削、滚齿等,以保证齿轮的几何精度和表面质量。
- 控制齿轮的安装间隙和啮合间隙,确保齿轮传动的相对位置和啮合质量。
- 定期检查齿轮的磨损和损伤,及时维护和更换损坏的齿轮零件。
5. 齿轮系统的测试与验证- 进行静态和动态测试,检测齿轮系统的工作性能和可靠性。
- 使用合适的测试设备和方法来评估齿轮系统的噪音、振动、温升和负载能力等指标。
- 结合测试和模拟分析的结果,对齿轮系统进行优化和改进。
总结:在齿轮设计中,我们需要注意噪音控制、材料选择、润滑和冷却、加工和装配以及系统的测试与验证。
遵循这些一般准则,可以提高齿轮传动系统的性能和可靠性,确保其高效运行。
齿轮设计师和工程师应密切关注齿轮系统的设计和制造过程,不断追求技术创新和工艺改进,以满足不同应用领域的需求。
齿轮传动设计2

2、一对斜齿圆柱齿轮的传动的正确啮合条件为
m n1 = m n 2 = m n
α n1 = α n 2 = α β1 = ±β 2
α t1= α t2,但不是标准值。
n
端面模数和端面压力角也分别相等,即mt1=mt2,
3、几何尺寸计算。 由于斜齿轮在端面上相当于直齿轮,故斜齿 轮的几何尺寸计算,只需将端面参数代入直齿轮 的尺寸计算公式即可。 分度圆直径: d=mz=mnz/cosβ 齿顶圆直径: da=d+2mn 齿根圆直径: df=d-2.5mn 标准中心距: a=(d1+d2)/2=(z1+z2)mn/2/cosβ
2. 斜齿轮不发生根切的最少齿数 可由其当量齿轮的最少齿 数 求得,即
z min = zv min cos β
3
9、13 斜齿圆柱齿轮传动的强度计算 、
一、受力分析(图9-31)。 斜齿圆柱齿轮轮齿上的法向力 可分解为圆周力Ft、 径向力Fr和轴向力Fa,其大小分别为
圆周力 径向力 轴相力
Ft Fr
1. 计算依据:一对齿轮啮合传动时,轮齿在任一点的 接触可看作是曲率半径为ρ1 和ρ2 及宽度为b的两个圆 柱体相互接触。由弹性力学的赫兹公式可知,齿面 最大接触应力为
FE σ H = 0.418 bρ
由于节点P处同时啮合的齿对数少,两齿廓相对滑 动速度小,不易形成油膜,摩擦力大,故点蚀常发生 在节点附近,所以,通常以节点P处计算齿轮的接触应 力。
9、11 直齿圆柱齿轮轮齿的弯曲疲劳强度计算
1. 2. 计算依据:轮齿可视为悬臂梁,齿根危险截面,可用切 线法确定,为简化计算,假定全部载荷 都作用于齿顶。 计算公式:齿根弯曲疲劳强度的计算公式为
校核公式
齿轮的设计计算过程
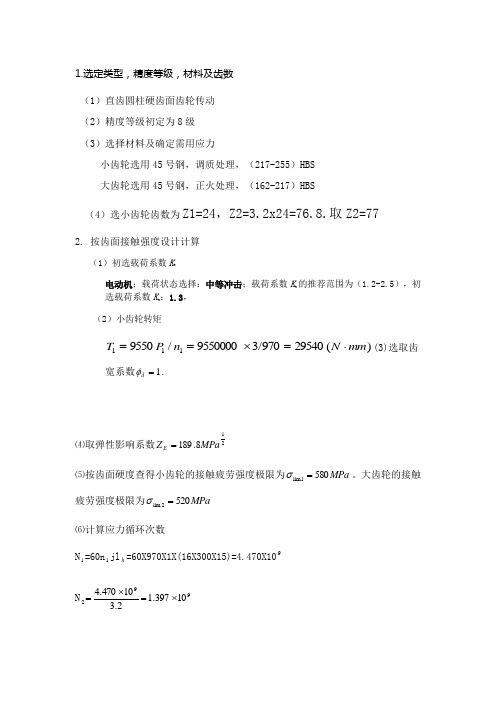
1.选定类型,精度等级,材料及齿数 (1)直齿圆柱硬齿面齿轮传动 (2)精度等级初定为8级 (3)选择材料及确定需用应力小齿轮选用45号钢,调质处理,(217-255)HBS 大齿轮选用45号钢,正火处理,(162-217)HBS (4)选小齿轮齿数为Z1=24,Z2=3.2x24=76.8.取Z2=772. 按齿面接触强度设计计算(1)初选载荷系数K t电动机;载荷状态选择:中等冲击;载荷系数K t 的推荐范围为(1.2-2.5),初选载荷系数K t :1.3, (2)小齿轮转矩)(29540/97039550000/9550111mm N n P T ⋅=⨯==(3)选取齿宽系数1=d φ.⑷取弹性影响系数218.189MPa Z E =⑸按齿面硬度查得小齿轮的接触疲劳强度极限为MPa 5801lim =σ。
大齿轮的接触疲劳强度极限为MPa 5202lim =σ ⑹计算应力循环次数N 1=60n 1jl h =60X970X1X(16X300X15)=4.470X109N 99210397.12.310470.4⨯=⨯=⑺取接触疲劳寿命系数K .89.0,88.021==HN HN K⑻计算接触疲劳许用应力 取失效概率为1%,安全系数S=1[]a HN H MP MPa SK 4.5105709.01lim 11=⨯==σσ[]a HN H MP MPa SK 8.46253095.02lim 22=⨯==σσ⑼按齿面接触强度设计计算 ①试算小齿轮分度圆直径mm Z u u T K d H E d t t 248.56)8.4628.189(2.32.4110954.28.132.2)][(132.23243211=⨯⨯⨯=+〉σφ②计算齿轮圆周转速v 并选择齿轮精度 s m n d V t /48.2100060970248.5610006011=⨯⨯⨯=⨯=ππ③计算齿轮宽度bmm d b t d 248.56248.5611=⨯=⨯=φ④计算齿轮宽度b 与齿高h 之比 模数 mm mm Z d m t 033.22272.44111===齿高 mm mm m h 574.4033.225.225.21=⨯==67.10=hb⑤计算载荷系数根据v=2.27m/s 。
齿轮传动的设计计算

齿轮传动的设计计算
齿轮传动的设计计算通常涉及以下几个方面:
1. 齿轮尺寸计算:首先需要确定主动轮和从动轮的模数(齿轮的模数是齿轮齿数与齿轮直径的比值),根据传动比和齿数关系,计算主动轮和从动轮的齿数。
然后根据齿轮的模数和齿数,计算出齿轮的分度圆直径、齿顶圆直径和齿根圆直径。
2. 传动比计算:根据所需的输入转速和输出转速,计算传动比。
传动比可以通过齿轮齿数之比来确定。
3. 齿轮强度计算:根据传动功率和转速,计算齿轮的弯曲强度和接触强度。
弯曲强度是指齿轮在承受力矩时的抗弯能力,接触强度是指齿轮齿面在传递力矩时的抗磨损能力。
根据齿轮材料的强度参数和几何参数,使用相应的公式计算弯曲强度和接触强度,并与所需的传动功率和转速进行比较,确保齿轮能够满足设计要求。
4. 齿轮齿形计算:根据齿轮的模数、齿数和压力角,计算齿轮的齿形。
齿形计算包括计算齿顶高度、齿根高度、齿根圆曲率半径等参数。
通过合理选择这些参数,可以确保齿轮传动的平稳运行和高效传动。
5. 齿轮轴的计算:根据齿轮的传动功率和转速,计算齿轮轴的强度。
齿轮轴的强度计算涉及到材料的抗弯强度和抗剪强度,并考虑到齿轮轴的几何参数。
以上是齿轮传动设计计算的一般步骤,具体的计算方法和公式可能会根据不同的设计要求和标准有所差异。
在实际的工程设计中,通
常需要参考相关的齿轮设计手册或使用专业的齿轮设计软件来完成计算。
结构设计齿轮有关计算

齿轮数据计算一般减速器对传动尺寸无特殊限制,可采用软齿面传动。
小齿轮选用45钢调质,齿面平均硬度240HBS ,大齿轮选用45钢正火,齿面平均硬度200HBS 。
这是闭式软齿面齿轮传动,故可先按接触疲劳强度设计,再校核其弯曲疲劳强度。
设计步骤如下:计 算 与 说 明主 要 结 果1.按齿面接触疲劳强度设计 (1)许用接触应力极限应力38087.0lim +=HBS H σ(表3-4) MPa H 5891lim =σMPa H 5542lim =σ安全系数 取 1=H S许用接触应力 []H H H S limσσ=取[]1H σ、[]2H σ中较小者代入计算公式[]MPa H 5891=σ []MPa H 5542=σ(2)计算小齿轮分度圆直径小齿轮转矩 mm N n P T ·990221055.91055.96161⨯⨯=⨯=mmN T ·1012.251⨯=齿宽系数 单级减速器中齿轮相对轴承对称布置,由表3-7取 1=d ψ载荷系数 工作平稳,软齿面齿轮,取 5.1=K节点区域系数 标准直齿圆柱齿轮传动 5.2=H Z弹性系数 由表3-5MPa Z E 8.189=小齿轮计算直径 []312112⎪⎭⎫ ⎝⎛+⎪⎪⎭⎫ ⎝⎛≥i i KT Z Z d d H HE ψσm m76.8821211012.25.125545.28.189352=+⨯⨯⨯⨯⨯⎪⎭⎫ ⎝⎛⨯=2.确定几何尺寸齿数 取361=z 36222⨯==iz z722=z计 算 与 说 明 主 要 结 果 模数 mm mm z d m 47.23676.8811===,由表3-2取标准模数mm m 5.2=分度圆直径 mm mz d 365.211⨯==mm mz d 725.222⨯==mm d 901= mm d 1802=中心距 ()()mm d d a 18090212121+=+=mm a 135=齿宽 mm mm d b d 909011=⨯==ψ取b b =2mm b b 10~51+=mm b 902= mm b 951=3.校核齿根疲劳强度 (1)许用齿根应力极限应力2757.0lim +=HBS F σ(表3-4) MPa F 4431lim =σ MPa F 4152lim =σ安全系数 取1=F S .4许用齿根应力[]FF FS limσσ=[]MPa F 3161=σ []MPa F 2962=σ(2)验算齿根应力复合齿形系数 由表3-6,经线性差值06.41=FS Y 99.32=FS Y齿根应力 MPa Y m bd KT FS F 5.2909006.41012.25.12251111⨯⨯⨯⨯⨯⨯==σMPa Y Y FS FS F F 06.499.31191212⨯==σσMPa F 1191=σ MPa F 1172=σ由于[]11F F σσ<,[]22F F σσ<,故弯曲疲劳强度足够。
齿轮各部分计算公式

齿轮各部分计算公式
齿轮是一种常见的机械传动装置,由于其结构复杂,设计计算也相对繁琐。
下面将介绍齿轮各部分的计算公式,包括齿数计算、模数计算、齿廓曲线计算等。
一、齿数计算公式:
齿数是齿轮设计中最基本的参数之一、一般情况下,要求输入齿轮中心距、模数和齿数,通过计算可以得到另一个齿轮的齿数。
1.齿数计算公式:
n=(πd)/m
其中,n为齿数,d为齿轮的规定直径,m为模数。
2.齿轮中心距计算公式:
a=m(z1+z2)/2
其中,a为齿轮中心距,m为模数,z1、z2为两个齿轮的齿数。
二、模数计算公式:
模数是齿轮设计中重要的参数之一,是决定齿轮尺寸的关键。
1.模数计算公式:
m=d/z
其中,m为模数,d为齿轮的规定直径,z为齿数。
三、齿廓曲线计算公式:
齿廓曲线是描述齿轮齿形的曲线,常用的齿廓曲线有圆弧、渐开线等。
1.圆弧齿廓曲线计算公式:
y = r - (r' + r' tanα)
其中,y为齿廓偏差,r为齿轮基圆半径,r'为齿轮分度圆半径,α
为压力角。
2.渐开线齿廓曲线计算公式:
x = (r + r α) cosθ + m tanθ - m tanα
其中,x为齿廓偏差,r为齿轮基圆半径,α为压力角,θ为齿廓角。
以上仅是齿轮计算中的一部分公式,实际的齿轮设计计算还需要考虑
到材料强度、结构刚度等因素。
此外,齿轮的传动特性、工作精度也需要
在设计时进行综合考虑。
齿轮轴
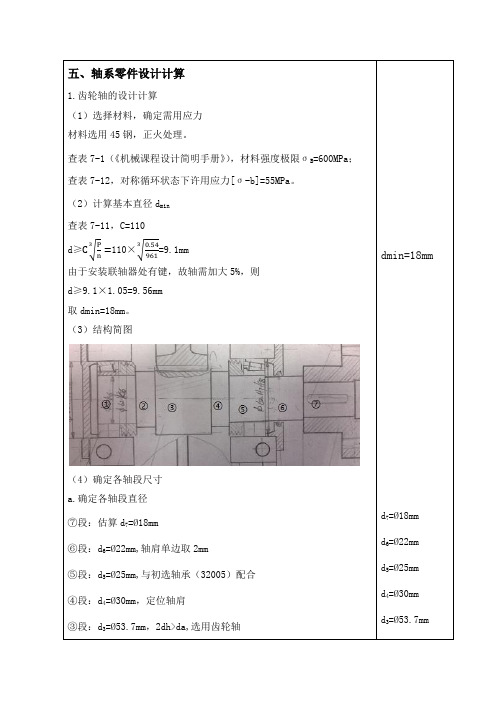
⑦段:l7=30,与联轴器配合长度
总轴长 L=l1+l2+l3+l4+l5+l6+l7=184mm
轴承间距 LAB=97mm
联轴器距离右端轴承
LBC=58.5mm
(5)按弯扭组合强度校核轴的强度
①受力分析,如图(a)
轴上扭矩T=5.4N﹒m
齿轮上圆周力 Ft=2T/d3=2×5.4×103/49.7=217.3N
(2)通气器
减速器工作时,由于箱体内部温度升高,气体膨胀,压力增大,使得箱体内外压力不等。为使箱体内受热膨胀的气体自由排出,以保持箱体内外压力平衡,不致使润滑油沿分箱面或轴伸件密封处向外渗漏,需在箱体顶部或直接在窥视孔盖上设置通气器。针对该箱体在窥视孔盖上设置通气器,并选用简单式通气器尺寸M20×1.5.
左端轴向力Fa1=11.77N
校核受力的大的轴承
当量载荷P=XFr+YFa=0.4×39.55+1.68×68.87=131.52N
b)验算轴承寿命根据式(13-5)
Lh= = =9.99×108h
寿命要求
L=16×365×8=46720h
Lh>>L,故轴承满足设计要求
3.键连接强度校核计算
①类型选择
(3)加强肋厚 m=Z=5mm
(4)地脚螺钉直径 d=12mm
(5)地脚螺钉数目 n=10
(6)底座距离箱体壁的距离C1+C2=12+15=27mm
2.箱体附件的选择
(1)窥视孔及窥视孔盖
窥视孔用于检查传动零件的啮合、润滑及轮齿损坏情况,并兼作注油孔,可向减速器箱体内注入润滑油。窥视孔应设置在减速器箱盖上方的适当位置,且应有足够的尺寸,以便直接进行观察和手能伸入箱体内进行操作。平时窥视孔用窥视孔盖盖住,窥视孔盖常用螺钉将其固定在箱盖上。
机械设计-齿轮的几何参数和基本尺寸的计算

名称
代号
应用公式
小齿轮(mm)
大齿轮(mm)
分度圆直径
d
d=mz
1 =10×20=200
2 =10×32=320
齿顶圆直径
da
da=m(z+2)
da1=10×(20+2)=220
da2=10×(32+2)=340
齿根圆直径
df
df= m(z-2.5)
作用线方向)之间所夹锐角,也用α表示。
齿轮的几何参数和基本尺寸的计算
渐开线标准直齿圆柱齿轮的基本参数
m=4 z=16
m=2 z=16
2.齿数z
一个齿轮的轮齿总数。
3.模数m
齿距p除以圆周率π所得的商,即m= p /π。
模数已经标准化。
齿数相等的齿轮,模数越大,齿轮尺寸就越大,
m=1 z=16
轮齿也越大,承载能力越强。
pb=pcosα=πmcosα
标准中心距
a
a=(d1+d2)/2=m(z1+z2)/2
齿顶高
ha
ha=ha*m=m
齿数比
u
u=z2/z1
齿轮的几何参数和基本尺寸的计算
外啮合标准直齿圆柱齿轮的几何尺寸计算
例:有一对相啮合的标准直齿圆柱齿轮,齿数z1 =20, z2 =32,模数m=10。试计算其分度圆直径d、齿顶
齿顶高,即应留有一定的径向间隙,称为顶隙,用
c表示。
对于标准齿轮,规定c=c*m。c*称为顶隙系数。
我国标准规定:正常齿c*=0.25。
齿轮的几何参数和基本尺寸的计算
外啮合标准直齿圆柱齿轮的几何尺寸计算
齿轮设计公式

分度圆直径
计算项目及内容
主要结果
中心距
齿轮宽度
小齿轮齿宽加宽 ,即
取 ,大齿轮
5.齿轮强度校核
(1)齿面接触疲劳强度校核
为节省篇幅,仅给出计算结果:
, , , , , , , ,所以
满足要求
(2)齿根弯曲疲劳强度校核
, , , , , , , , , ,所以
满足要求。
主要设计结论
齿数 , ,模数 ,压力角 ,中心距 ,齿宽 , 。小齿轮选用40Cr(调质),大齿轮选用45(调质)。齿轮按7级精度设计。
按齿根弯曲疲劳强度设计1试算模数1确定各参数试选k计算弯曲疲劳强度用重合度系数ydv2609dm1629mm计算项目及内容主要结果计算y查得齿形系数y查得应力修正系数y查得小齿轮和大齿轮的齿根弯曲疲劳极限分别为flim1500mpa查得弯曲疲劳寿命系数kfn1085取弯曲疲劳安全系数s14yy因为大齿轮的yfay试算模数m2调整齿轮模数1数据准备圆周速度vdv齿宽bb宽高比bhbym计算项目及内容主要结果2计算实际载荷系数k查得kfk由此查得k由表104用插值法查得kh1414结合b则载荷系数为k所以m由于齿轮模数m的大小主要取决于弯曲疲劳强度所决定的承载能力而齿面接触疲劳强度所决定的承载能力仅与齿轮直径有关可取由弯曲疲劳强度算得的模数并就近圆整为标准值m125mm按接触疲劳强度算得的分度圆直径d139084mm所以取z132为使大小齿轮齿数互为质数经调整得zz几何尺寸计算分度圆直径dd中心距a齿轮宽度b小齿轮齿宽加宽510b取b150mmm1098mmzz计算项目及内容主要结果调整中心距后的强度校核采用变位法调整中心距为90mm计算变位系数和计算啮合角齿数和变位系数和中心距变动系数和齿顶高降低系数zxyy查得分配变位系数x1008齿面接触疲劳强度校核为节省篇幅仅给出计算结果
- 1、下载文档前请自行甄别文档内容的完整性,平台不提供额外的编辑、内容补充、找答案等附加服务。
- 2、"仅部分预览"的文档,不可在线预览部分如存在完整性等问题,可反馈申请退款(可完整预览的文档不适用该条件!)。
- 3、如文档侵犯您的权益,请联系客服反馈,我们会尽快为您处理(人工客服工作时间:9:00-18:30)。
16 小齿轮的许用接触应力 17 大齿轮的许用接触应力 18 19
MPa MPa MPa mm mm/s mm mm mm mm mm 度 mm mm mm mm mm
许用接触应力 分度圆直径
[σ ]H
dt1 V Kv d1 mn a β d1 d2 b2 b1
Zv1 Zv2
[σ ]H1 [σ ]H2
由p146,图8.28查得 60n1aLh
n1 / i
390.00 84.00 30.00 1.01 1.06 1.00 575.70 413.40 413.40
MPa 107次 107次
寿命系数 寿命系数 安全系数
由p147,图8.29查得 由p147,图8.29查得 由p147,表8.7查得 Z N 1 H lim1 / SH
3
2K A KVt K K T1 u 1 Z E Z H Z Z d u H
dt1n1 /(60 1000)
由p131,图8.7查得
dt1 3 KV / KVt
2
46.36 3.50 1.17 45.97 1.80 2.75 89.29 120.00 #NUM! #NUM! #NUM! #NUM! #NUM! 85.00 #NUM! #NUM! 2.69 2.18 1.59 1.77 0.70
结果 5.17 1440.00 3.63 2.00 8.00 45 236 45 190 8 34287.15 25
单位 kW r/min
班制 年
HBS HBS 级 Nmm
大齿轮齿数 传动比 螺旋角 齿宽系数 端面重合度
Z2 i β Фd
ε
α
圆整 误差 由p144,表8.6查得
4 5 6 7 8
90.75 70 2.80 -22.87% 不合格 12.00 1.10 1.70 1.86 1.00 1.20 1.11 1.20 189.80 2.46 0.76 0.99 570.00 MPa
mn z1 / cos mn z2 / cos
大齿轮宽度 小齿轮宽度
小齿轮当量齿数 大齿轮当量齿数
小齿轮的齿形系数 大齿轮的齿形系数
小齿轮的应力修正系数 大齿轮的应力修正系数
d d1 圆整
b 2 (5 ~ 10 )
z1 / cos3 z2 / cos3
5齿根弯曲疲劳强度校核
1 2 3 4 5
Flim2
寿命系数 寿命系数 安全系数
YN1 YN2 SF
[σ ]F1 [σ ]F2
12 小齿轮的许用弯曲应力 13 大齿轮的许用弯曲应力 14
弯曲应力 弯曲应力
σ σ
F1
2KT1 /(bmn d1 )YF1Ys1Y Y 2KT1 /(bmn d1 )YF 2Ys 2Y Y
15
F2
动载系数
齿向载荷分布系数 齿间载荷分布系数
Kvt Kβ Kα ZE
弹性系数
节点区域系数 ZH 重合度系数 Zε 螺旋角系数 Zβ
Hlim1
小齿轮的接触疲劳极限应力 σ
10
大齿轮的接触疲劳极限应力 σ
Hlim2
11 小齿轮应力循环次数 12 大齿轮应力循环次数 13 14 15
N1 N2 ZN1 ZN2 SH
YF1 YF2 Ys1 Ys2 Yε
由p139,图8.19查得 由p139,图8.19查得 由p139,图8.20查得 由p139,图8.20查得 由p140,图8.21查得
重合度系数
6 7 8 9 10 11
螺旋角系数
Yβ
Flim1
由p143,图8.26查得 由p146,图8.28查得 由p148,图8.28查得 由p147,图8.30查得 由p147,图8.30查得 由p147,表8.7查得
YN 1 F lim1 / SF YN 2 F lim2 / SF
0.98 220.00 170.00 1.00 1.00 1.25 176.00 136.00 #NUM! #NUM! #NUM! #NUM! MPa MPa MPa MPa MPa MPa
小齿轮的弯曲疲劳极限应力 σ 大齿轮的弯曲疲劳极限应力 σ
20 小齿轮运动速度 21
动载系数
22 修正分度圆直径
4齿轮参数计算
1 2 3 4 5 6 7 8 9
模数 中心距 螺旋角
小齿轮分度圆直径 大齿轮分度圆直径
d1 cos / Z1 由p124,表8.1查得 d1 (i 1) /(2cos ) 圆整 arccos mn ( z1 z2 ) / 2a
齿轮传动设计
参数 计算项目 公式 已知: 1 额定功率 P 2 n1 转速 3 传动比 i 4 工作条件 载荷平稳、大批量生产 5 工作时间 t 6 使用期限 1选择齿轮的材料、热处理方式和精度等级 1 小齿轮材料 2 小齿轮热处理 调质 3 大齿轮材料 4 大齿轮热处理 正火 5 传动精度等级 2初步确定主要参数 1 小齿轮传递转矩 T1 9.55 106 P1 / n1 2 小齿轮齿数 Z1 3
MPa
1.88 3.2(1/ Z1 1/ Z2 ) cos
0.318d Z1 tan
轴面重合度 ε β 3齿面接触疲劳强度设计 1 KA 使用系数
2 3 4 5 6 7 8 9
由p130,表8.3查得 试选 由p132,图8.11查得 由p133,表8.4查得 由p136,表8.5查得 由p136,图8.14查得 由p136,图8.15查得 由p142,图8.24查得 由p146,图8.28查得