界面导热粘接材料粘接工艺研究
复合材料的界面特性与粘结机制研究
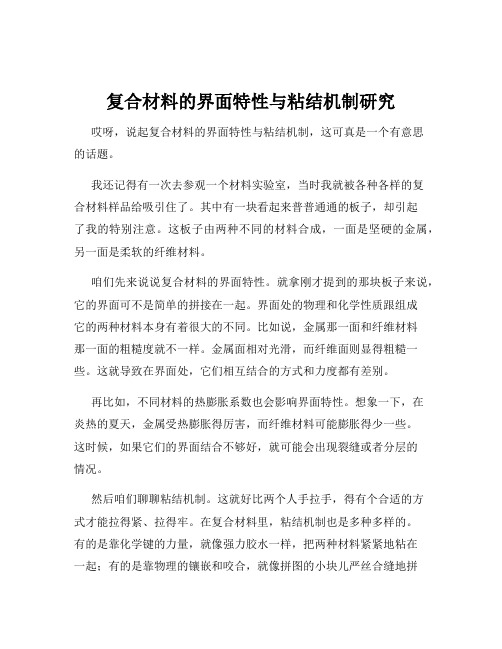
复合材料的界面特性与粘结机制研究哎呀,说起复合材料的界面特性与粘结机制,这可真是一个有意思的话题。
我还记得有一次去参观一个材料实验室,当时我就被各种各样的复合材料样品给吸引住了。
其中有一块看起来普普通通的板子,却引起了我的特别注意。
这板子由两种不同的材料合成,一面是坚硬的金属,另一面是柔软的纤维材料。
咱们先来说说复合材料的界面特性。
就拿刚才提到的那块板子来说,它的界面可不是简单的拼接在一起。
界面处的物理和化学性质跟组成它的两种材料本身有着很大的不同。
比如说,金属那一面和纤维材料那一面的粗糙度就不一样。
金属面相对光滑,而纤维面则显得粗糙一些。
这就导致在界面处,它们相互结合的方式和力度都有差别。
再比如,不同材料的热膨胀系数也会影响界面特性。
想象一下,在炎热的夏天,金属受热膨胀得厉害,而纤维材料可能膨胀得少一些。
这时候,如果它们的界面结合不够好,就可能会出现裂缝或者分层的情况。
然后咱们聊聊粘结机制。
这就好比两个人手拉手,得有个合适的方式才能拉得紧、拉得牢。
在复合材料里,粘结机制也是多种多样的。
有的是靠化学键的力量,就像强力胶水一样,把两种材料紧紧地粘在一起;有的是靠物理的镶嵌和咬合,就像拼图的小块儿严丝合缝地拼在一起;还有的是靠分子间的相互作用力,虽然这种力量相对较弱,但在一定条件下也能发挥不小的作用。
比如说,有一种复合材料是用树脂把玻璃纤维粘结起来的。
在这个过程中,树脂会渗透到玻璃纤维的缝隙里,然后经过固化,形成一个牢固的整体。
这里面树脂的选择就很关键,如果树脂的性能不好,或者在粘结过程中没有处理好温度、压力等条件,那粘结效果就会大打折扣。
还有一种情况,是在金属和陶瓷的复合材料中。
由于金属和陶瓷的性质差异很大,要实现良好的粘结就更不容易了。
这时候,往往需要对金属表面进行特殊处理,比如增加粗糙度,或者在表面镀上一层薄薄的过渡层,来提高粘结的效果。
在实际应用中,了解复合材料的界面特性和粘结机制那是太重要了。
金属基复合材料的界面粘结强度研究
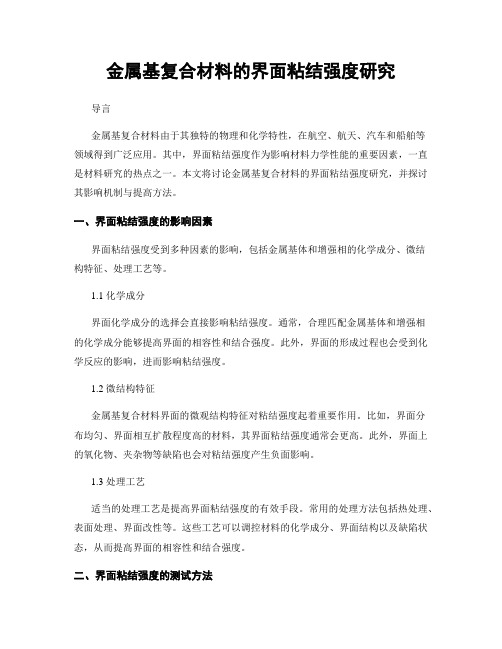
金属基复合材料的界面粘结强度研究导言金属基复合材料由于其独特的物理和化学特性,在航空、航天、汽车和船舶等领域得到广泛应用。
其中,界面粘结强度作为影响材料力学性能的重要因素,一直是材料研究的热点之一。
本文将讨论金属基复合材料的界面粘结强度研究,并探讨其影响机制与提高方法。
一、界面粘结强度的影响因素界面粘结强度受到多种因素的影响,包括金属基体和增强相的化学成分、微结构特征、处理工艺等。
1.1 化学成分界面化学成分的选择会直接影响粘结强度。
通常,合理匹配金属基体和增强相的化学成分能够提高界面的相容性和结合强度。
此外,界面的形成过程也会受到化学反应的影响,进而影响粘结强度。
1.2 微结构特征金属基复合材料界面的微观结构特征对粘结强度起着重要作用。
比如,界面分布均匀、界面相互扩散程度高的材料,其界面粘结强度通常会更高。
此外,界面上的氧化物、夹杂物等缺陷也会对粘结强度产生负面影响。
1.3 处理工艺适当的处理工艺是提高界面粘结强度的有效手段。
常用的处理方法包括热处理、表面处理、界面改性等。
这些工艺可以调控材料的化学成分、界面结构以及缺陷状态,从而提高界面的相容性和结合强度。
二、界面粘结强度的测试方法为了准确评估金属基复合材料的界面粘结强度,研究者们发展了多种测试方法。
2.1 剥离实验剥离实验是一种常用的测试界面粘结强度的方法。
通过在界面上施加剥离载荷,并测量载荷和位移之间的关系,可以得到界面的粘结强度。
2.2 拉伸实验拉伸实验是另一种测试界面粘结强度的常用方法。
将复合材料样品制成拉伸试样,施加拉力加载,并记录力和变形之间的关系,从而计算界面的粘结强度。
2.3 微观观察和力学测试利用扫描电子显微镜(SEM)和透射电子显微镜(TEM)等技术,可以观察界面微观结构和缺陷,并结合力学测试,分析界面的粘结强度。
三、提高金属基复合材料界面粘结强度的方法为了提高金属基复合材料的界面粘结强度,研究者们提出了多种方法。
3.1 优化界面化学成分通过选择合适的化学成分,可以改善金属基体和增强相之间的相容性,提高界面的结合强度。
复合材料的界面粘结强度研究
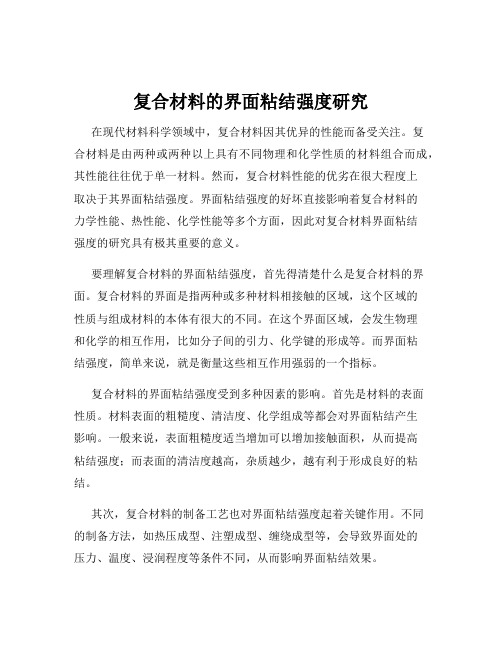
复合材料的界面粘结强度研究在现代材料科学领域中,复合材料因其优异的性能而备受关注。
复合材料是由两种或两种以上具有不同物理和化学性质的材料组合而成,其性能往往优于单一材料。
然而,复合材料性能的优劣在很大程度上取决于其界面粘结强度。
界面粘结强度的好坏直接影响着复合材料的力学性能、热性能、化学性能等多个方面,因此对复合材料界面粘结强度的研究具有极其重要的意义。
要理解复合材料的界面粘结强度,首先得清楚什么是复合材料的界面。
复合材料的界面是指两种或多种材料相接触的区域,这个区域的性质与组成材料的本体有很大的不同。
在这个界面区域,会发生物理和化学的相互作用,比如分子间的引力、化学键的形成等。
而界面粘结强度,简单来说,就是衡量这些相互作用强弱的一个指标。
复合材料的界面粘结强度受到多种因素的影响。
首先是材料的表面性质。
材料表面的粗糙度、清洁度、化学组成等都会对界面粘结产生影响。
一般来说,表面粗糙度适当增加可以增加接触面积,从而提高粘结强度;而表面的清洁度越高,杂质越少,越有利于形成良好的粘结。
其次,复合材料的制备工艺也对界面粘结强度起着关键作用。
不同的制备方法,如热压成型、注塑成型、缠绕成型等,会导致界面处的压力、温度、浸润程度等条件不同,从而影响界面粘结效果。
再者,组成复合材料的两种或多种材料的相容性也是一个重要因素。
如果材料之间的相容性好,它们在界面处能够更好地相互扩散、渗透,形成较强的界面结合;反之,如果相容性差,界面处容易出现缺陷和应力集中,导致粘结强度降低。
为了研究复合材料的界面粘结强度,科学家们采用了各种各样的方法。
其中,微观分析技术是常用的手段之一。
通过扫描电子显微镜(SEM)、透射电子显微镜(TEM)等,可以直接观察到界面的微观结构,了解界面处的结合情况、是否存在缺陷等。
另外,力学性能测试也是评估界面粘结强度的重要方法。
比如拉伸试验、剪切试验等,可以直接测量复合材料在受力情况下的表现,从而间接反映出界面粘结强度的大小。
复合材料的界面粘结性能研究
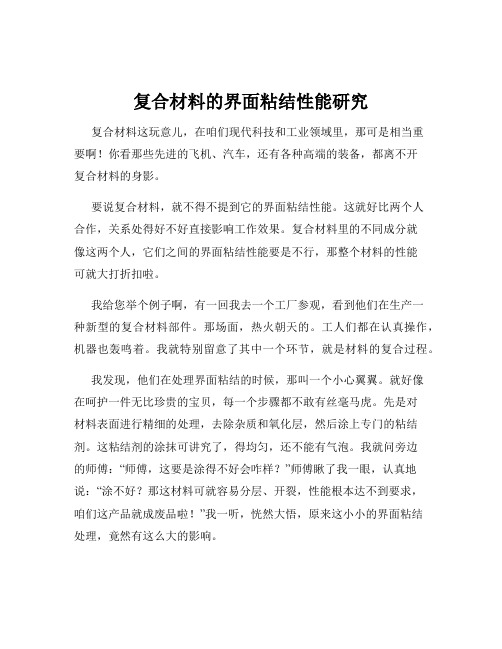
复合材料的界面粘结性能研究复合材料这玩意儿,在咱们现代科技和工业领域里,那可是相当重要啊!你看那些先进的飞机、汽车,还有各种高端的装备,都离不开复合材料的身影。
要说复合材料,就不得不提到它的界面粘结性能。
这就好比两个人合作,关系处得好不好直接影响工作效果。
复合材料里的不同成分就像这两个人,它们之间的界面粘结性能要是不行,那整个材料的性能可就大打折扣啦。
我给您举个例子啊,有一回我去一个工厂参观,看到他们在生产一种新型的复合材料部件。
那场面,热火朝天的。
工人们都在认真操作,机器也轰鸣着。
我就特别留意了其中一个环节,就是材料的复合过程。
我发现,他们在处理界面粘结的时候,那叫一个小心翼翼。
就好像在呵护一件无比珍贵的宝贝,每一个步骤都不敢有丝毫马虎。
先是对材料表面进行精细的处理,去除杂质和氧化层,然后涂上专门的粘结剂。
这粘结剂的涂抹可讲究了,得均匀,还不能有气泡。
我就问旁边的师傅:“师傅,这要是涂得不好会咋样?”师傅瞅了我一眼,认真地说:“涂不好?那这材料可就容易分层、开裂,性能根本达不到要求,咱们这产品就成废品啦!”我一听,恍然大悟,原来这小小的界面粘结处理,竟然有这么大的影响。
回到咱们说的复合材料的界面粘结性能研究。
这可是个复杂又有趣的课题。
它涉及到材料的物理、化学性质,还有加工工艺等等好多方面。
比如说,不同材料之间的相容性就很关键。
有些材料就像天生不对付的两个人,怎么都合不来,它们的界面粘结性能就很差。
而有些材料呢,一碰到一起就“亲密无间”,界面粘结性能杠杠的。
这就得靠咱们科研人员去深入研究,找出其中的规律,然后想办法让那些“不对付”的材料也能好好相处。
还有啊,温度、压力这些加工条件对界面粘结性能也有很大影响。
温度太高了,可能会把材料“烤坏”;压力太大了,又可能把材料压变形。
所以得找到那个恰到好处的平衡点,这可不容易,得经过无数次的实验和测试。
另外,材料表面的粗糙度也不能忽视。
太光滑了,粘结不牢固;太粗糙了,又会影响美观和性能。
粘接材料的加工和施工工艺

粘接材料的加工和施工工艺随着人们对高性能材料的需求越来越高,粘接材料在现代工程领域中的应用越来越广泛。
而对这类材料的加工和施工工艺的熟悉和掌握程度,将直接影响着工程质量和应用效果。
因此,本文将从加工和施工两个方面对粘接材料做一些介绍和分享。
一、粘接材料的加工工艺1.表面处理粘接材料的表面处理非常重要,它直接决定了粘接剂和基材间的附着强度。
一般来说,表面处理要根据基材和粘接材料的特性来具体选择。
例如对于金属基材,表面处理可以采用机械打磨、腐蚀处理等方式,而对于聚合物基材,表面处理则可以采用火热处理、气氛等离子体处理等方式。
2.测量和调配在进行粘接材料的加工过程中,测量和调配是一个不可忽视的环节。
正确的配比和调配能够保证粘接剂的品质和工作性能,从而在后续的工作中提高安全性和效益。
另外,对于一些颜色要求较高的粘接材料,还需要根据需要添加色母来调配颜色。
3.混合混合是将粘接剂和固化剂等配料物料混合均匀的过程。
在混合的过程中,需要严格控制各配比物料的比例和颜色等特性,以确保混合均匀且品质优良。
一般来说,混合过程可以采用手动或者机械化操作,具体的选择要根据实际需要来决定。
4.制备制备即指将混合均匀的粘接材料在特定条件下进行加热、冷却、压力等加工工艺的过程。
在制备过程中,需要对加工条件进行严格控制,以确保粘接材料获得最佳性能的同时保证生产效率。
一般来说,制备过程可以采用手工制备或者机械自动制备。
二、粘接材料的施工工艺1.涂布涂布是指将粘接材料均匀涂布在基材表面的过程。
涂布的精度和均匀性直接决定了粘接剂和基材间的附着力。
因此,在涂布的过程中,需要注意粘接剂的涂布量、厚度和布涂均匀性,同时也要控制涂布温度和湿度等环境因素对涂布质量的影响。
2.压合在涂布完成后,需要对涂布后的基材进行压合,以提高附着力和强度。
压合过程中,要注意控制压合时间和压力的大小,以保证涂布剂和基材能够紧密结合并达到最佳的粘接效果。
3.固化固化是指使涂布的粘接剂在适当的条件下发生固化反应并且形成牢固的连结的过程。
复合材料的界面粘结性能研究
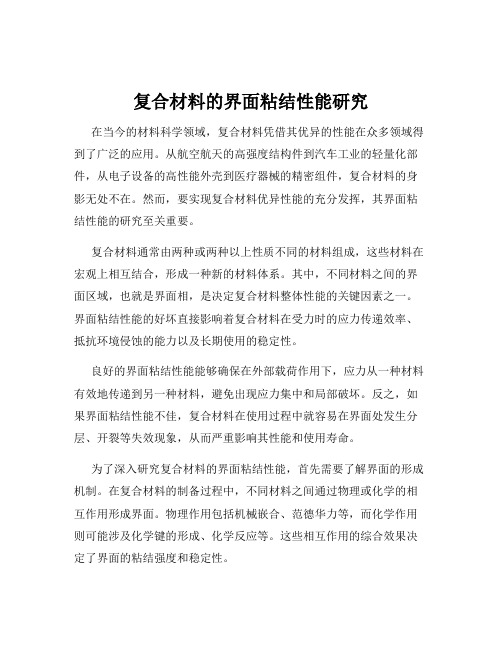
复合材料的界面粘结性能研究在当今的材料科学领域,复合材料凭借其优异的性能在众多领域得到了广泛的应用。
从航空航天的高强度结构件到汽车工业的轻量化部件,从电子设备的高性能外壳到医疗器械的精密组件,复合材料的身影无处不在。
然而,要实现复合材料优异性能的充分发挥,其界面粘结性能的研究至关重要。
复合材料通常由两种或两种以上性质不同的材料组成,这些材料在宏观上相互结合,形成一种新的材料体系。
其中,不同材料之间的界面区域,也就是界面相,是决定复合材料整体性能的关键因素之一。
界面粘结性能的好坏直接影响着复合材料在受力时的应力传递效率、抵抗环境侵蚀的能力以及长期使用的稳定性。
良好的界面粘结性能能够确保在外部载荷作用下,应力从一种材料有效地传递到另一种材料,避免出现应力集中和局部破坏。
反之,如果界面粘结性能不佳,复合材料在使用过程中就容易在界面处发生分层、开裂等失效现象,从而严重影响其性能和使用寿命。
为了深入研究复合材料的界面粘结性能,首先需要了解界面的形成机制。
在复合材料的制备过程中,不同材料之间通过物理或化学的相互作用形成界面。
物理作用包括机械嵌合、范德华力等,而化学作用则可能涉及化学键的形成、化学反应等。
这些相互作用的综合效果决定了界面的粘结强度和稳定性。
目前,研究复合材料界面粘结性能的方法多种多样。
其中,微观分析技术如扫描电子显微镜(SEM)、透射电子显微镜(TEM)等可以帮助我们直观地观察界面的微观结构,包括界面的形貌、粗糙度、相分布等。
通过这些观察,我们能够了解界面的物理结合情况,并推测其对粘结性能的影响。
此外,力学性能测试也是评估界面粘结性能的重要手段。
常见的测试方法有拉伸试验、剪切试验、弯曲试验等。
通过这些试验,可以获得复合材料的强度、模量、断裂伸长率等力学性能参数,从而间接反映界面的粘结强度。
同时,化学分析方法如 X 射线光电子能谱(XPS)、傅里叶变换红外光谱(FTIR)等可以用于检测界面处的化学组成和化学键的变化,进而揭示界面的化学结合机制。
材料的界面粘结性能研究
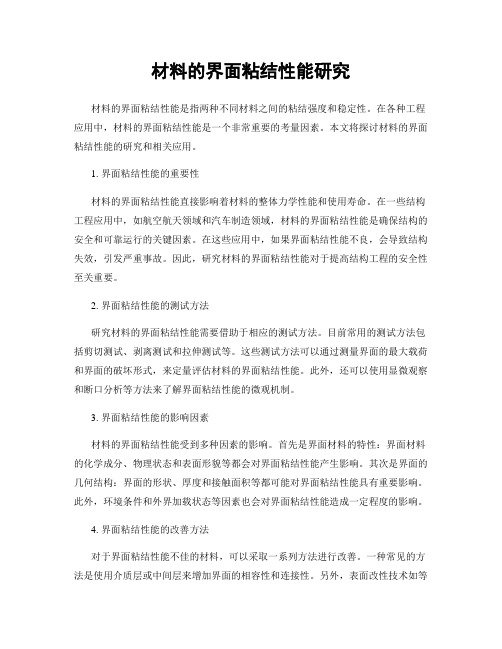
材料的界面粘结性能研究材料的界面粘结性能是指两种不同材料之间的粘结强度和稳定性。
在各种工程应用中,材料的界面粘结性能是一个非常重要的考量因素。
本文将探讨材料的界面粘结性能的研究和相关应用。
1. 界面粘结性能的重要性材料的界面粘结性能直接影响着材料的整体力学性能和使用寿命。
在一些结构工程应用中,如航空航天领域和汽车制造领域,材料的界面粘结性能是确保结构的安全和可靠运行的关键因素。
在这些应用中,如果界面粘结性能不良,会导致结构失效,引发严重事故。
因此,研究材料的界面粘结性能对于提高结构工程的安全性至关重要。
2. 界面粘结性能的测试方法研究材料的界面粘结性能需要借助于相应的测试方法。
目前常用的测试方法包括剪切测试、剥离测试和拉伸测试等。
这些测试方法可以通过测量界面的最大载荷和界面的破坏形式,来定量评估材料的界面粘结性能。
此外,还可以使用显微观察和断口分析等方法来了解界面粘结性能的微观机制。
3. 界面粘结性能的影响因素材料的界面粘结性能受到多种因素的影响。
首先是界面材料的特性:界面材料的化学成分、物理状态和表面形貌等都会对界面粘结性能产生影响。
其次是界面的几何结构:界面的形状、厚度和接触面积等都可能对界面粘结性能具有重要影响。
此外,环境条件和外界加载状态等因素也会对界面粘结性能造成一定程度的影响。
4. 界面粘结性能的改善方法对于界面粘结性能不佳的材料,可以采取一系列方法进行改善。
一种常见的方法是使用介质层或中间层来增加界面的相容性和连接性。
另外,表面改性技术如等离子体处理、化学修饰和功能化涂层等也可以提高界面的粘结性能。
此外,通过优化材料配方和制备工艺等方法也可以改善界面的粘结性能。
5. 界面粘结性能在实际应用中的案例材料的界面粘结性能在实际应用中有广泛的应用。
在航空航天领域,界面粘结性能的研究和改善对于降低飞机结构的自重和提高飞行安全有重要意义。
在汽车制造领域,界面粘结性能的研究可用于提高汽车车身的强度和刚度,同时降低车辆的噪音和振动。
粘接材料的生产流程和工艺创新

粘接材料的生产流程和工艺创新粘接材料是一种能够将两个或两个以上的材料黏合在一起的材料。
它们被广泛应用于建筑、汽车、飞机、船舶和家居等领域,为现代工业的发展和进步做出了巨大的贡献。
本文将介绍粘接材料的生产流程和工艺创新。
1.生产流程粘接材料的生产流程主要分为三个步骤:原料准备、生产加工和包装贮存。
1.1 原料准备粘接剂的原料包括树脂、硬化剂、填充剂以及其他添加剂。
其中,树脂是基础,填充剂和添加剂是辅助材料。
硬化剂是重要的配合剂,用于使树脂成为固态结构。
1.2 生产加工生产加工主要包括混合、搅拌、调整、分切、包裹等步骤。
混合是将树脂、硬化剂、填充剂和其他添加剂按照一定比例混合在一起,形成流体状物质。
搅拌是使其混合均匀,调整是针对不同工艺和要求进行调整。
分切是将混合好的材料进行定量切割。
包裹是将切好的材料包装存放至适宜的环境条件下。
1.3 包装贮存包装是将粘接材料按照规定量进行分装、包装并标识各种信息。
贮存是应该存放在低温、干燥的仓库中,有利于保持粘接材料的性能,延长使用寿命。
2.工艺创新粘接材料的工艺创新主要包括生产工艺、优化设计以及特殊功能材料开发等方面。
2.1 生产工艺在生产过程中,采用更加高效的混合、搅拌、分切和包裹工艺,使得粘接材料的准确度和稳定性得到提高。
如混合工艺中引入新型混合机和控制系统,可以实现材料的自动化生产和精准控制。
搅拌工艺中,采用新型搅拌器和各种加热方式能够大大提高产品质量和生产效能。
分切和包装方面,采用分选机、包装机等自动化设备,大大提高材料的质量和生产效率。
2.2 优化设计优化设计是从材料本身的性能和应用需求出发,采用高精度的分析模型和新型的材料制备方法,实现材料的多功能化和更加广泛的应用。
如开始采用的材料模型存在诸多不足,而现在使用的模型可以更加真实、精确地描述材料的力学、物理性质。
基于这些分析模型,研究人员可以进行多种方法的改进设计,得到更加新颖、高性能的粘接材料。
此外,还可以通过特殊加工方法和添加剂来实现材料的特殊功能化,比如防火、耐高温、抗辐射等等。
导热绝缘胶粘剂的研究进展及其在金属基板上的应用

覆铜板 C L C
导 热绝缘胶粘剂 的研 究进展及 其在
金属基板上 的应 用
Pa er d : - 3 p Co e S 0 8
韩志慧
刘传 超
( 北省化 学研 究 院 ,湖北 武 汉 407 ) 湖 30 4
范 和 平
( 华烁科技股份有限公司,湖北 武汉 407 ) 304
e f c so ol e e i n h r a on u tvi le r ic s d. fe t fp ym rr sn a d t e m lc d c i t f l ra e d s use Ther c n e e r h p og e so e m a yi e e tr s a c r r s ft r l h
元 器 件 的 正 常工 作 ,严 重 时 甚 至 会 使 电子元 器 件 失
效 。统 计 资料 表 明n,电子 元 器件 温度 每 升 高2℃ , ]
信 息 产 品 需 求 的 大 幅度 增 长 ,有 力 地 促 进 了 电子 信
息 产业 的 发展 。 而作 为 电子 信 息 产 业 基ቤተ መጻሕፍቲ ባይዱ础 的 电子 元
摘 要
文章 简单介绍 了导热绝缘胶粘剂 的导热原理 ,重点分析 了导热绝缘胶粘剂 中最主要的
两类组 分一一高分子树脂和导热填料的影响及其最新研 究进展 ,概 述 了该类胶 粘剂在 金 属基板 上的应 用情况,并对 导热绝缘胶 粘剂的发展 前景 进行 了展 望。
关键词 导热 ;绝缘 ;胶粘剂 ;金属基板 中图分类号 :T 4 N 1 文献标识码 :A 文章编号 :1 0 — 0 6( 0 0 — 0 9 0 909 21 0 1】 4 0 0 — 8
复合材料界面的粘结强度研究
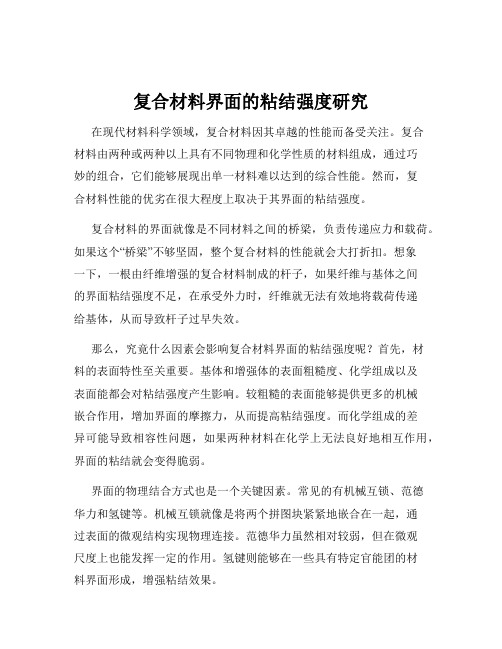
复合材料界面的粘结强度研究在现代材料科学领域,复合材料因其卓越的性能而备受关注。
复合材料由两种或两种以上具有不同物理和化学性质的材料组成,通过巧妙的组合,它们能够展现出单一材料难以达到的综合性能。
然而,复合材料性能的优劣在很大程度上取决于其界面的粘结强度。
复合材料的界面就像是不同材料之间的桥梁,负责传递应力和载荷。
如果这个“桥梁”不够坚固,整个复合材料的性能就会大打折扣。
想象一下,一根由纤维增强的复合材料制成的杆子,如果纤维与基体之间的界面粘结强度不足,在承受外力时,纤维就无法有效地将载荷传递给基体,从而导致杆子过早失效。
那么,究竟什么因素会影响复合材料界面的粘结强度呢?首先,材料的表面特性至关重要。
基体和增强体的表面粗糙度、化学组成以及表面能都会对粘结强度产生影响。
较粗糙的表面能够提供更多的机械嵌合作用,增加界面的摩擦力,从而提高粘结强度。
而化学组成的差异可能导致相容性问题,如果两种材料在化学上无法良好地相互作用,界面的粘结就会变得脆弱。
界面的物理结合方式也是一个关键因素。
常见的有机械互锁、范德华力和氢键等。
机械互锁就像是将两个拼图块紧紧地嵌合在一起,通过表面的微观结构实现物理连接。
范德华力虽然相对较弱,但在微观尺度上也能发挥一定的作用。
氢键则能够在一些具有特定官能团的材料界面形成,增强粘结效果。
化学结合在提高粘结强度方面也具有不可忽视的作用。
通过在界面处发生化学反应,形成化学键,如共价键、离子键等,可以显著增强材料之间的结合力。
例如,在某些复合材料的制备过程中,可以对增强体进行表面处理,引入能与基体发生反应的官能团,从而实现更牢固的界面粘结。
制备工艺同样对复合材料界面的粘结强度有着深远的影响。
不同的加工方法会导致材料的组织结构和性能差异。
以复合材料的成型工艺为例,注塑成型、模压成型和缠绕成型等方法所产生的温度、压力和冷却速率等条件各不相同,这些都会直接影响界面的粘结质量。
为了准确评估复合材料界面的粘结强度,科学家们开发了一系列的测试方法。
导热胶粘剂材料的制备及其热传导性能研究
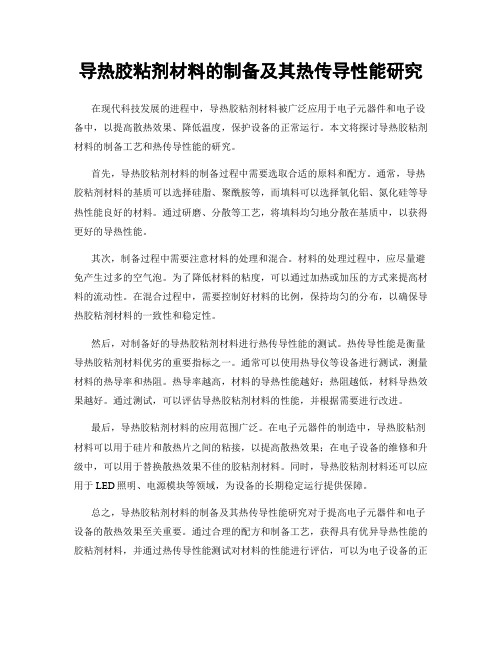
导热胶粘剂材料的制备及其热传导性能研究在现代科技发展的进程中,导热胶粘剂材料被广泛应用于电子元器件和电子设备中,以提高散热效果、降低温度,保护设备的正常运行。
本文将探讨导热胶粘剂材料的制备工艺和热传导性能的研究。
首先,导热胶粘剂材料的制备过程中需要选取合适的原料和配方。
通常,导热胶粘剂材料的基质可以选择硅脂、聚酰胺等,而填料可以选择氧化铝、氮化硅等导热性能良好的材料。
通过研磨、分散等工艺,将填料均匀地分散在基质中,以获得更好的导热性能。
其次,制备过程中需要注意材料的处理和混合。
材料的处理过程中,应尽量避免产生过多的空气泡。
为了降低材料的粘度,可以通过加热或加压的方式来提高材料的流动性。
在混合过程中,需要控制好材料的比例,保持均匀的分布,以确保导热胶粘剂材料的一致性和稳定性。
然后,对制备好的导热胶粘剂材料进行热传导性能的测试。
热传导性能是衡量导热胶粘剂材料优劣的重要指标之一。
通常可以使用热导仪等设备进行测试,测量材料的热导率和热阻。
热导率越高,材料的导热性能越好;热阻越低,材料导热效果越好。
通过测试,可以评估导热胶粘剂材料的性能,并根据需要进行改进。
最后,导热胶粘剂材料的应用范围广泛。
在电子元器件的制造中,导热胶粘剂材料可以用于硅片和散热片之间的粘接,以提高散热效果;在电子设备的维修和升级中,可以用于替换散热效果不佳的胶粘剂材料。
同时,导热胶粘剂材料还可以应用于LED照明、电源模块等领域,为设备的长期稳定运行提供保障。
总之,导热胶粘剂材料的制备及其热传导性能研究对于提高电子元器件和电子设备的散热效果至关重要。
通过合理的配方和制备工艺,获得具有优异导热性能的胶粘剂材料,并通过热传导性能测试对材料的性能进行评估,可以为电子设备的正常运行提供保障。
未来,我们可以进一步研究材料的导热机制和改进方法,以不断提升导热胶粘剂材料的性能,满足不同领域的需求。
复合材料的界面粘接与增韧研究

复合材料的界面粘接与增韧研究复合材料在现代制造业中扮演着重要的角色,它们结合了不同材料的优点,具有出色的力学性能和广泛的应用领域。
然而,复合材料的界面粘接和增韧是一个持续的挑战,直接影响着其性能和可靠性。
界面粘接是指两个或多个不同材料的接触面之间形成的粘结区域。
在复合材料中,界面粘接是将复合材料的各个组件牢固地粘结在一起的关键。
一个强大的界面粘接能够有效地传递力学载荷,并能够抵抗外界环境的侵蚀。
而一个弱化的界面粘接则容易引起界面失效,导致材料损坏。
为了提高复合材料的界面粘接性能,研究人员进行了大量的研究和实践。
其中一个关键的研究方向是表面改性技术。
通过在复合材料表面引入适当的功能化化合物或添加剂,可以增强界面粘接效果。
例如,使用表面处理剂可以提高纤维增强复合材料中纤维与矩阵的粘接强度。
此外,也可以使用聚合物、金属或陶瓷等材料作为界面层,强化界面的结合力。
除了改善界面粘接外,增韧是另一个需要解决的问题。
复合材料主要由纤维增强材料和矩阵材料组成,纤维起到增加材料强度的作用,而矩阵则起到传递载荷和保护纤维的作用。
然而,界面粘接的弱点容易导致纤维在界面处脱粘,导致复合材料的脆性断裂。
因此,研究人员致力于开发各种增韧技术,以提高复合材料的韧性和抗冲击性能。
其中一种增韧技术是纳米填料增韧。
通过在界面处引入纳米颗粒,可以增加界面的接触面积和摩擦力,从而提高界面的粘结效果。
此外,纳米填料还可以平均分散在复合材料中,形成纳米尺度的网络结构,增加材料的韧性。
例如,研究人员发现,在碳纤维增强复合材料中添加适量的纳米氧化铝填料可以显著提高材料的断裂韧性和冲击强度。
另一种增韧技术是多尺度增韧。
这种技术通过在复合材料中引入不同尺度的增韧结构,从而增加其抗拉强度和韧性。
例如,可以在纤维增强复合材料中引入微尺度的纳米纤维或纳米管,以改善其界面粘接和层间结合强度。
此外,也可以在复合材料中引入宏观尺度的增韧结构,如纤维增强层或裂纹桥梁,以增加材料的抗裂性能。
导热性粘接片、其制造方法以及使用该导热性粘接片的电子器件[发明专利]
![导热性粘接片、其制造方法以及使用该导热性粘接片的电子器件[发明专利]](https://img.taocdn.com/s3/m/0d530a2e5fbfc77da369b1a2.png)
专利名称:导热性粘接片、其制造方法以及使用该导热性粘接片的电子器件
专利类型:发明专利
发明人:加藤邦久,森田亘,武藤豪志
申请号:CN201480050736.8
申请日:20140924
公开号:CN105531837A
公开日:
20160427
专利内容由知识产权出版社提供
摘要:本发明提供一种导热性粘接片、其制造方法、以及使用了该导热性粘接片的电子器件,通过将所述导热性粘接片叠层在电子器件上,能够高效地放出热,并且能够选择性地在特定方向上放出热,从而对该电子器件内部赋予充分的温差。
本发明的导热性粘接片包含基材和粘接剂层,所述基材包含高导热部和低导热部,在该基材的一面叠层粘接剂层,并且,该基材的另一面由该低导热部的与该粘接剂层相接的面相反侧的面及该高导热部的与该粘接剂层相接的面相反侧的面构成,或者该高导热部和该低导热部的至少任一个构成了该基材的厚度的一部分。
本发明还提供上述导热性粘接片的制造方法、以及使用了该导热性粘接片的电子器件。
申请人:琳得科株式会社
地址:日本东京都
国籍:JP
代理机构:北京市柳沈律师事务所
代理人:王利波
更多信息请下载全文后查看。
界面导热粘接材料粘接工艺研究
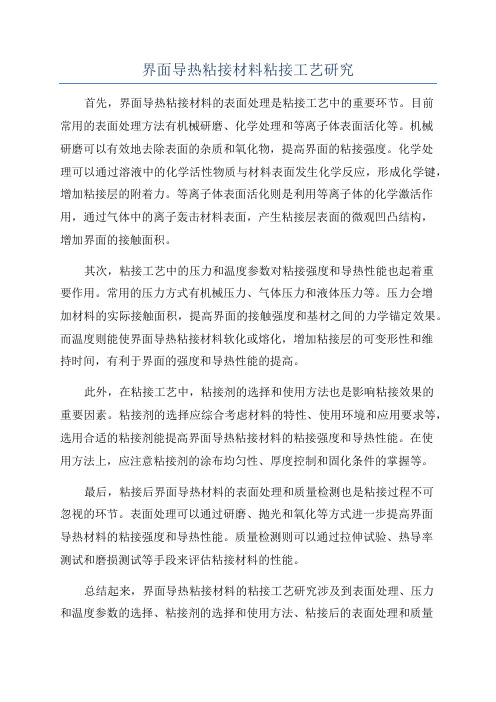
界面导热粘接材料粘接工艺研究首先,界面导热粘接材料的表面处理是粘接工艺中的重要环节。
目前常用的表面处理方法有机械研磨、化学处理和等离子体表面活化等。
机械研磨可以有效地去除表面的杂质和氧化物,提高界面的粘接强度。
化学处理可以通过溶液中的化学活性物质与材料表面发生化学反应,形成化学键,增加粘接层的附着力。
等离子体表面活化则是利用等离子体的化学激活作用,通过气体中的离子轰击材料表面,产生粘接层表面的微观凹凸结构,增加界面的接触面积。
其次,粘接工艺中的压力和温度参数对粘接强度和导热性能也起着重要作用。
常用的压力方式有机械压力、气体压力和液体压力等。
压力会增加材料的实际接触面积,提高界面的接触强度和基材之间的力学锚定效果。
而温度则能使界面导热粘接材料软化或熔化,增加粘接层的可变形性和维持时间,有利于界面的强度和导热性能的提高。
此外,在粘接工艺中,粘接剂的选择和使用方法也是影响粘接效果的重要因素。
粘接剂的选择应综合考虑材料的特性、使用环境和应用要求等,选用合适的粘接剂能提高界面导热粘接材料的粘接强度和导热性能。
在使用方法上,应注意粘接剂的涂布均匀性、厚度控制和固化条件的掌握等。
最后,粘接后界面导热材料的表面处理和质量检测也是粘接过程不可忽视的环节。
表面处理可以通过研磨、抛光和氧化等方式进一步提高界面导热材料的粘接强度和导热性能。
质量检测则可以通过拉伸试验、热导率测试和磨损测试等手段来评估粘接材料的性能。
总结起来,界面导热粘接材料的粘接工艺研究涉及到表面处理、压力和温度参数的选择、粘接剂的选择和使用方法、粘接后的表面处理和质量检测等多个方面。
只有充分理解和掌握这些关键环节,才能实现界面导热粘接材料的最佳粘接效果,提高其粘接强度和导热性能,满足不同领域的应用需求。
单组份导热粘接胶的粘接基材
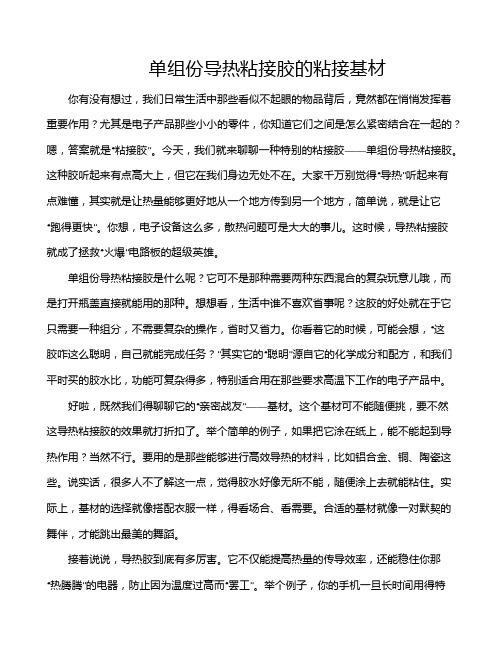
单组份导热粘接胶的粘接基材你有没有想过,我们日常生活中那些看似不起眼的物品背后,竟然都在悄悄发挥着重要作用?尤其是电子产品那些小小的零件,你知道它们之间是怎么紧密结合在一起的?嗯,答案就是“粘接胶”。
今天,我们就来聊聊一种特别的粘接胶——单组份导热粘接胶。
这种胶听起来有点高大上,但它在我们身边无处不在。
大家千万别觉得“导热”听起来有点难懂,其实就是让热量能够更好地从一个地方传到另一个地方,简单说,就是让它“跑得更快”。
你想,电子设备这么多,散热问题可是大大的事儿。
这时候,导热粘接胶就成了拯救“火爆”电路板的超级英雄。
单组份导热粘接胶是什么呢?它可不是那种需要两种东西混合的复杂玩意儿哦,而是打开瓶盖直接就能用的那种。
想想看,生活中谁不喜欢省事呢?这胶的好处就在于它只需要一种组分,不需要复杂的操作,省时又省力。
你看着它的时候,可能会想,“这胶咋这么聪明,自己就能完成任务?”其实它的“聪明”源自它的化学成分和配方,和我们平时买的胶水比,功能可复杂得多,特别适合用在那些要求高温下工作的电子产品中。
好啦,既然我们得聊聊它的“亲密战友”——基材。
这个基材可不能随便挑,要不然这导热粘接胶的效果就打折扣了。
举个简单的例子,如果把它涂在纸上,能不能起到导热作用?当然不行。
要用的是那些能够进行高效导热的材料,比如铝合金、铜、陶瓷这些。
说实话,很多人不了解这一点,觉得胶水好像无所不能,随便涂上去就能粘住。
实际上,基材的选择就像搭配衣服一样,得看场合、看需要。
合适的基材就像一对默契的舞伴,才能跳出最美的舞蹈。
接着说说,导热胶到底有多厉害。
它不仅能提高热量的传导效率,还能稳住你那“热腾腾”的电器,防止因为温度过高而“罢工”。
举个例子,你的手机一旦长时间用得特别热,就很容易影响性能,甚至死机。
而这些导热胶就像是为手机装上了一个“小空调”,帮助它散热,避免一热就“中暑”。
它们的主要功能就是让设备在长时间高温环境下依旧能保持稳定的运行。
金属粘接界面的研究与优化
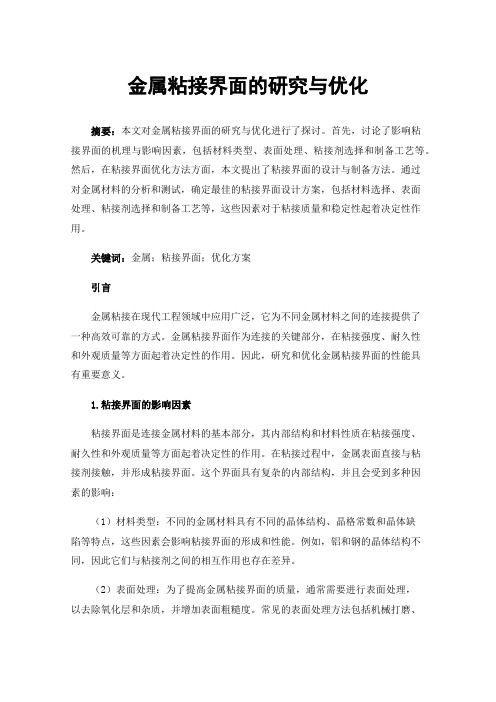
金属粘接界面的研究与优化摘要:本文对金属粘接界面的研究与优化进行了探讨。
首先,讨论了影响粘接界面的机理与影响因素,包括材料类型、表面处理、粘接剂选择和制备工艺等。
然后,在粘接界面优化方法方面,本文提出了粘接界面的设计与制备方法。
通过对金属材料的分析和测试,确定最佳的粘接界面设计方案,包括材料选择、表面处理、粘接剂选择和制备工艺等,这些因素对于粘接质量和稳定性起着决定性作用。
关键词:金属;粘接界面;优化方案引言金属粘接在现代工程领域中应用广泛,它为不同金属材料之间的连接提供了一种高效可靠的方式。
金属粘接界面作为连接的关键部分,在粘接强度、耐久性和外观质量等方面起着决定性的作用。
因此,研究和优化金属粘接界面的性能具有重要意义。
1.粘接界面的影响因素粘接界面是连接金属材料的基本部分,其内部结构和材料性质在粘接强度、耐久性和外观质量等方面起着决定性的作用。
在粘接过程中,金属表面直接与粘接剂接触,并形成粘接界面。
这个界面具有复杂的内部结构,并且会受到多种因素的影响:(1)材料类型:不同的金属材料具有不同的晶体结构、晶格常数和晶体缺陷等特点,这些因素会影响粘接界面的形成和性能。
例如,铝和钢的晶体结构不同,因此它们与粘接剂之间的相互作用也存在差异。
(2)表面处理:为了提高金属粘接界面的质量,通常需要进行表面处理,以去除氧化层和杂质,并增加表面粗糙度。
常见的表面处理方法包括机械打磨、酸洗和喷砂等。
通过表面处理,可以提高金属表面与粘接剂之间的接触面积和粘接性能。
(3)粘接剂选择:粘接剂是连接金属材料的关键环节,不同类型的粘接剂具有不同的结构和性质。
常见的金属粘接剂包括胶黏剂、焊接材料和填充物等。
选择合适的粘接剂要考虑粘接界面的化学相容性、黏附强度和温度稳定性等因素。
(4)制备工艺:金属粘接的制备工艺会直接影响粘接界面的质量和性能。
包括涂覆粘接剂、加热和压力施加等步骤。
适当的制备工艺可以确保粘接剂在界面上均匀分布,并实现良好的粘接质量[1]。
- 1、下载文档前请自行甄别文档内容的完整性,平台不提供额外的编辑、内容补充、找答案等附加服务。
- 2、"仅部分预览"的文档,不可在线预览部分如存在完整性等问题,可反馈申请退款(可完整预览的文档不适用该条件!)。
- 3、如文档侵犯您的权益,请联系客服反馈,我们会尽快为您处理(人工客服工作时间:9:00-18:30)。
电子工艺技术Electronics Process Technology201958年1月第40卷第1期【编者按】SMT无疑是电子组装技术的核心,然而,波峰焊、返修、清洗、敷形涂覆和胶材应用等也是电子组装技术不可或缺的重要工艺技术,普遍应用于军用及航空电子产品、通讯产品、汽车电子以及医疗电子等高可靠性产品的研发与生产。
这些工艺技术在一般的工厂往往不被重视,因而也很少有比较深入的研究。
鉴于此,本年度将重点介绍波峰焊、返修、清洗、敷形涂覆和胶材应用等工艺技术的常见问题及解决方案。
电子组装疑难工艺问题解析doi: 10.14176/j.issn.1001-3474.2019.01.017作者简介:黄祥彬(1975- ),男,毕业于四川大学,主要从事电子装联工艺材料的应用研究工作。
摘 要:在电子装联过程中,高功率器件需要粘接散热器进行散热。
通过设计一系列的粘接工艺实验,对粘接散热器工艺的影响因素进行分析。
实验结果表明:粘接剂本身的内聚强度、散热器/芯片的表面处理和润湿性能以及工艺操作规范性是影响散热器粘接可靠性的三个主要因素。
关键词:界面导热粘接材料;高功率器件;粘接;散热器;电子组装中图分类号:TN605 文献标识码:A 文章编号:1001-3474(2019)01-0058-05Abstract: The high power devices need to be bonded to radiator for heat dissipation in the process of electronic assembly. The factors influencing the bonding performance of radiator were analyzed based on designing a series of bonding process experiments. The experimental results show that the three main factors affecting the reliability of the radiator bonding are cohesive strength of the adhesives, surface treatment and wettability of the radiator/die, and standardization of operation.Key Words: thermal conductive adhesive; high power device; bonding performance; radiator; electronic assembly Document Code: A Article ID: 1001-3474 (2019) 01-0058-05界面导热粘接材料粘接工艺研究Bonding Technology of Thermal Conductive Adhesive at Interface黄祥彬,王玉,钟章HUANG Xiangbin, WANG Yu, ZHONG Zhang(中兴通讯股份有限公司,广东 深圳 518052)( Zhongxing Telecommunication Equipment Corporation, Shenzhen 518052, China )在电子组件(PCBA)中,部分高功率器件需要通过散热器进行散热[1]。
散热器的安装方式主要有两类:机械紧固和胶黏剂粘结。
由于粘接组件内的应力传递与传统的机械紧固(如:铆接、焊接、过盈连接和螺栓连接)相比,应力分布更均匀,而且粘接的组件结构更加紧凑、强度更高和成本更低,因而获得广泛应用,如图1所示。
芯片与散热器之间使用界面导热粘接材料作为传热和粘接的介质,业界常用的导热粘接材料是Loctite384/7387,前者为导热胶,后者为固化促进剂,两者配合使用,起散热和粘接作用。
但是,采用胶黏剂进行粘结也存在一个问题,就是如果粘结工艺或设计不当,在应用中有可第40卷第1期59能发生散热器脱落的问题。
与粘接剂、被粘接物的成分以及伴随着润湿、固化过程所发生的物理化学现象有关。
如果从宏观上分析,可以简单地把界面层直接看成是粘接剂相和被粘接材料相的结合面。
这样,界面上的作用力就直接决定了两相层间的粘接强度。
目前一般认为界面上的作用力有三类:1)静力,如“投锚”作用所形成的机械嵌合力以及摩擦力等。
理论上,静力可以达到数个MPa的强度;2)界面分子间的作用力,即粘接剂与被粘接物相互接近至0.3~0.5 nm时,由伦敦色散、偶极与氢键等作用而产生的力,分子间力可以达到100~1 000 MPa的结合强度;3)化学键力,即当粘接剂分子与被粘接物分子相互接近至0.1~0.3 nm时,由于发生化学反应而形成化学键,其结合强度理论上可以达到1 000~10 000 MPa。
因此,牢固粘接的前提是被粘物表面能被液态粘接剂充分地润湿。
这样,如果得到了理想的粘接,界面的粘附强度将是十分可观的。
然而,以下几个因素决定了实际的粘附强度达不到理想值:1)以上三种力在一个粘接体系内可能同时存在,但是所起的作用随情况而变。
一般认为,分子间力是产生粘附力的最普遍的原因,是粘接力的最主要来源,它对界面粘附强度的贡献比较大。
在各种产生粘接力的因素中,只有分子间作用力普遍存在于所有粘接体系中,其他作用仅在特殊情况下成为粘接力的来源。
要使界面粘附强度具备抗介质的腐蚀能力,还必须引入必要的化学键。
2)粘接过程分子间接触不良造成粘接界面上留有微孔缺陷等,减少了粘接界面的面积并引起应力集中,促使界面早期破坏。
3)固化时,由于界面存在的残余热应力和粘接剂的收缩应力也使得界面强度有所损失。
因此,为了得到良好的粘附强度,就需要从粘接剂配方设计(引入必要的化学键、改善粘接剂固化时的收缩应力和热应力等)到粘接工艺的实现上(保证良好的润湿,以形成洁净的两相亲密结合的界面等)进行有效控制。
3 粘接破坏机理粘接体系的破坏类型包括被粘接物破坏、界面层(主要是胶层)的内聚破坏、界面破坏和混合破坏等类型。
3.1 粘接体系从评价粘接体系的角度考虑,被粘接物如果发生破坏就说明粘接本身具有足够高的强度,因此一般都力争出现这种情况。
内聚破坏和界面破坏则应图1 粘接方式安装的散热器1 粘接工艺采用胶粘结安装散热器,通常的操作步骤如图2所示。
导热胶解冻 清洁工装 手涂促进剂 手工刷胶静置30 min以上 手贴研磨 检查胶厚图2 散热器粘贴工艺流程2 粘接机理粘接作用发生在粘接剂相和被粘接相相互接触的界面层上,其实质是材料表面的重新结合,这一点与焊接相类似[2]。
粘接剂固化后,粘接结构(一般称为粘接接头)按材料组成的分布梯度可以划分为五层,如图3所示。
图3 粘接结构示意图被粘物体胶黏剂粘接界面层被粘物体粘接过程是一个复杂的物理、化学过程。
粘接力的产生,不仅取决于胶黏剂和被粘物表面的结构与状态,而且和粘接过程的工艺条件密切相关。
粘接界面层是形成粘接体系的主要结构,与粘接强度直接相关。
界面层的形成与液态粘接剂对被粘材料的润湿有关。
通过润湿,液态粘接剂与固体表面亲密结合并形成“纯净”的液-固两相界面。
随着粘接剂的固化,两相界面也就发生了具有一定强度的结合。
关于界面层的厚度、组织或化学结构,黄祥彬,等:界面导热粘接材料粘接工艺研究2019电子工艺技术Electronics Process Technology年1月60尽力避免。
内聚破坏主要是粘接剂的内聚强度不足的结果,需要重新选择粘接剂或更改配方设计。
界面破坏则是粘接剂的润湿性较差或表面处理、工艺实施不当造成的。
混合破坏一般能表示一个较好的粘接效果,这时粘接强度主要由粘附强度和粘接剂的内聚强度决定。
由于界面层与其两侧的材质的不确定性,使得外力作用下的应力分布也呈现了不连续的复杂情况。
当局部应力超过局部强度以后,破坏可能首先在界面层或粘接剂中发生,然后向另一方扩展,最终导致混合破坏。
可以看出,粘接强度同时受到界面粘附强度以及各材料自身内聚强度的影响。
3.2 表面能研究高分子材料表面能是了解其粘合机理的基础。
无论是从热力学理论出发提出的粘接功,还是反应材料润湿能力的接触角以及与材料粘合有关的扩散、键合和机械作用等理论,都与液固两相及其界面的表面能(表面张力)有关。
当材料的表面能足够大时,与合适的胶水一起形成的粘接强度就大。
一般表面能达到35 N/m及以上的材料属于容易粘接的,如玻璃、铜和铝等,表面能为35 N/m以下的材料属于不好粘接的,如尼龙和橡胶等。
对于不好粘接的材料,对所需的胶黏剂要求比较严格,才能最终达到粘接强度高的效果。
因此,选用不同的胶黏剂时可以根据材质的不同而制定各阶梯的用胶要求。
部分材料的表面能见表1。
释放出自由基的速度较加热时快,自由基数量也更多,所以一般使用促进剂固化会时速度更快,固化的完整程度也会更高。
384固化反应类似甲基丙烯酸酯的反应。
5 散热器粘接工艺实验方案从粘接剂的内聚强度、芯片/散热器的表面处理与润湿性能和工艺操作规范性等三方面设计散热器的粘接工艺实验[3]。
实验共8个,见表2。
表1 部分材料的表面能材料表面能σ/(N·m -1)聚四氟乙烯(PTFE/Teflon)18~20聚丙烯(PP)29~31尼龙(polyundecanamide)33丙烯酸树脂(acrylic film)35镀锡铁35铜44铝45铁,碳钢46聚碳酸酯(PC)46聚氨脂(PU)434 Loctite384/7387导热粘接材料的主要组成和固化机理384是一款丙烯酸酯类导热结构胶,使用促进剂加速固化,实际操作中需增加散热器的研磨动作,以使导热胶和促进剂混合充分,促进导热胶固化。
使用促进剂固化时,促进剂一般是氨类物质,在与过氧化物固化剂接触时会使过氧化物反应释放出自由基,自由基再与树脂单体反应形成三维交联结构。
由于促进剂与过氧化物反应相对剧烈,所以序号实验名称实验条件设置实验目的1384/315导热胶的对比实验与Loctite315胶对比同行有使用Loctite315胶,同我司胶水性能比较2不同刮胶厚度剪切强度对比实验0.1~1.0 mm以上厚度验证胶水厚度及点状缺失的影响3粘接面积大小与粘接强度关系的实验粘接面积分25.40×12.70 mm 2与12.70×6.35 mm 2两种对比粘接面积大小与粘接强度的关系4散热器研磨、加压块、研磨加压块实验研磨0~5圈,加3×2×2 cm 3铁压块验证研磨圈数、加压块对粘接力的影响5促进剂刷涂时间及刷涂量实验促进剂不刷涂,刷涂后放置时间0~24 h验证促进剂刷涂对粘接力的影响6导热胶解冻与存储时间实验胶水的存储和解冻时间不同验证解冻与存储时间对粘接力的影响7阳极氧化与镀镍散热器对比实验阳极氧化和镀镍铝片验证散热器常见表面处理对粘接力的影响8导热胶被铁锈等异物污染实验导热胶刷涂后加铁锈验证铁锈等异物对粘接力的影响表2 散热器粘接工艺实验实验1~8均采用阳极氧化处理的标准铝片,实验2~8均使用384/7387导热胶,粘接面积25.4 mm×12.7 mm,测试方法参照ASTM D1002-10和国标《GB/T 7124-2008 胶粘剂拉伸剪切强度的测定》,只测试剪切力。