焦炉煤气DDS脱硫技术
焦炉煤气制合成气的脱硫及净化工艺技术

焦炉煤气制合成气的脱硫及净化工艺技术摘要:众所周知,中国是一个炼焦大国,在众多焦炉仓促建成之后,由于相应设施不配套,致使一些企业“焦而不化”现象层出不穷,大量的焦炉煤气被直接的燃烧排放,既是对环境的严重污染,也是对资源的极大浪费,因而也被人们称其为“点天灯”。
本文简述了焦炉煤气的一系列净化工艺,并且介绍了采用催化转化与非催化转化制取天然气的工艺流程,希望对于了解焦炉煤气净化技术有借鉴意义。
关键词:焦炉煤气;合成气;脱硫;净化工艺引言焦炉煤气作为焦炭制成过程中煤炭经过高温干馏环节所产生的气态产品,其在炼焦产品总质量中占据着15%-18%的比重,是位于焦炭产品之下的第二大炼焦产品。
据相关统计显示,我国目前焦炉煤气年产量为1331.2亿m3,除去一半用来进行燃料回收,还有665.6亿m3的焦炉煤气可以应用到其他工业领域中,但由于国内焦化产业长期以来将工作重心放于焦炭生产方面,未能对焦炉煤气回收利用充分重视,不少焦化企业处于经济因素的考虑,未能建设起相应的焦炉煤气净化回收装置,大量焦炉煤气未被回收利用,而是直接排放燃烧。
每年未被利用的焦炉煤气高达300多亿m3,经济损失高达数百亿元,在造成极大资源浪费的同时,对周边环境也造成了十分严重的污染。
对此,为了实现焦炉煤气的有效回收利用,满足当前实现绿色工业、循环经济与建设节约型社会的发展要求,本文简要对焦炉煤气净化回收工艺进行介绍,并介绍了相应的应用情况,为日后的焦化工艺提供一定的借鉴参考。
1气体组分焦炉煤气是焦炭生产过程中煤炭经高温干馏出来的气体产物,在干馏温度为550℃,焦炉煤气中有大量的H2S、COS、CS2、NH3、HCN、噻吩、硫磺、硫醚、焦油、萘、苯等化学物质。
焦炉煤气经过净化和提取回收化工产品后成为回炉煤气,回炉煤气的气体组分一般为(%,以体积百分比计):H254-59、CH423-28、CO5.5-7、CO21.5-2.5、N23-5、CnHm2-3、O20.3-0.7。
我国焦炉煤气脱硫技术现状
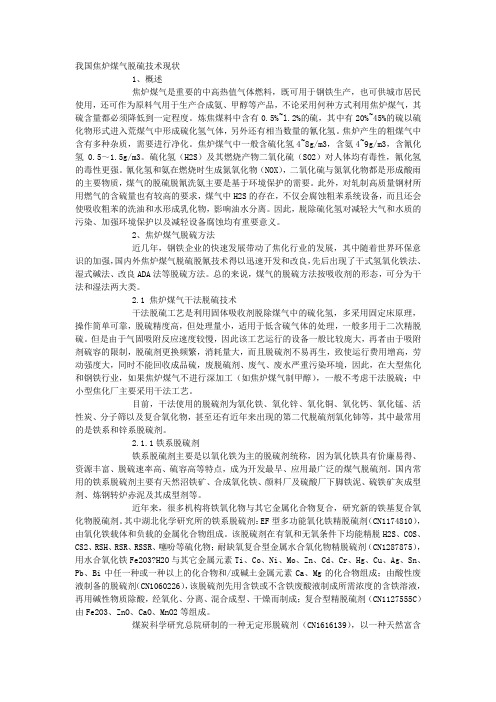
我国焦炉煤气脱硫技术现状1、概述焦炉煤气是重要的中高热值气体燃料,既可用于钢铁生产,也可供城市居民使用,还可作为原料气用于生产合成氨、甲醇等产品,不论采用何种方式利用焦炉煤气,其硫含量都必须降低到一定程度。
炼焦煤料中含有0.5%~l.2%的硫,其中有20%~45%的硫以硫化物形式进入荒煤气中形成硫化氢气体,另外还有相当数量的氰化氢。
焦炉产生的粗煤气中含有多种杂质,需要进行净化。
焦炉煤气中一般含硫化氢4~8g/m3,含氨4~9g/m3,含氰化氢0.5~1.5g/m3。
硫化氢(H2S)及其燃烧产物二氧化硫(SO2)对人体均有毒性,氰化氢的毒性更强。
氰化氢和氨在燃烧时生成氮氧化物(NOX),二氧化硫与氮氧化物都是形成酸雨的主要物质,煤气的脱硫脱氰洗氨主要是基于环境保护的需要。
此外,对轧制高质量钢材所用燃气的含硫量也有较高的要求,煤气中H2S的存在,不仅会腐蚀粗苯系统设备,而且还会使吸收粗苯的洗油和水形成乳化物,影响油水分离。
因此,脱除硫化氢对减轻大气和水质的污染、加强环境保护以及减轻设备腐蚀均有重要意义。
2、焦炉煤气脱硫方法近几年,钢铁企业的快速发展带动了焦化行业的发展,其中随着世界环保意识的加强,国内外焦炉煤气脱硫脱氰技术得以迅速开发和改良,先后出现了干式氢氧化铁法、湿式碱法、改良ADA法等脱硫方法。
总的来说,煤气的脱硫方法按吸收剂的形态,可分为干法和湿法两大类。
2.1 焦炉煤气干法脱硫技术干法脱硫工艺是利用固体吸收剂脱除煤气中的硫化氢,多采用固定床原理,操作简单可靠,脱硫精度高,但处理量小,适用于低含硫气体的处理,一般多用于二次精脱硫。
但是由于气固吸附反应速度较慢,因此该工艺运行的设备一般比较庞大,再者由于吸附剂硫容的限制,脱硫剂更换频繁,消耗量大,而且脱硫剂不易再生,致使运行费用增高,劳动强度大,同时不能回收成品硫,废脱硫剂、废气、废水严重污染环境,因此,在大型焦化和钢铁行业,如果焦炉煤气不进行深加工(如焦炉煤气制甲醇),一般不考虑干法脱硫;中小型焦化厂主要采用干法工艺。
dds催化剂脱硫新技术及工业应用
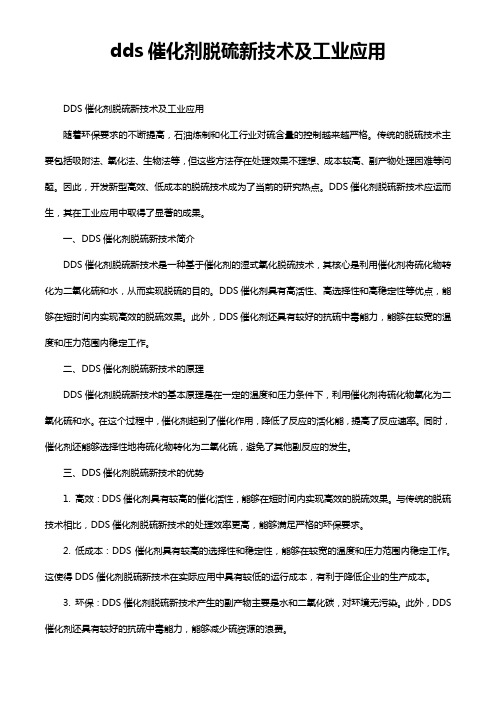
dds催化剂脱硫新技术及工业应用DDS催化剂脱硫新技术及工业应用随着环保要求的不断提高,石油炼制和化工行业对硫含量的控制越来越严格。
传统的脱硫技术主要包括吸附法、氧化法、生物法等,但这些方法存在处理效果不理想、成本较高、副产物处理困难等问题。
因此,开发新型高效、低成本的脱硫技术成为了当前的研究热点。
DDS催化剂脱硫新技术应运而生,其在工业应用中取得了显著的成果。
一、DDS催化剂脱硫新技术简介DDS催化剂脱硫新技术是一种基于催化剂的湿式氧化脱硫技术,其核心是利用催化剂将硫化物转化为二氧化硫和水,从而实现脱硫的目的。
DDS催化剂具有高活性、高选择性和高稳定性等优点,能够在短时间内实现高效的脱硫效果。
此外,DDS催化剂还具有较好的抗硫中毒能力,能够在较宽的温度和压力范围内稳定工作。
二、DDS催化剂脱硫新技术的原理DDS催化剂脱硫新技术的基本原理是在一定的温度和压力条件下,利用催化剂将硫化物氧化为二氧化硫和水。
在这个过程中,催化剂起到了催化作用,降低了反应的活化能,提高了反应速率。
同时,催化剂还能够选择性地将硫化物转化为二氧化硫,避免了其他副反应的发生。
三、DDS催化剂脱硫新技术的优势1. 高效:DDS催化剂具有较高的催化活性,能够在短时间内实现高效的脱硫效果。
与传统的脱硫技术相比,DDS催化剂脱硫新技术的处理效率更高,能够满足严格的环保要求。
2. 低成本:DDS催化剂具有较高的选择性和稳定性,能够在较宽的温度和压力范围内稳定工作。
这使得DDS催化剂脱硫新技术在实际应用中具有较低的运行成本,有利于降低企业的生产成本。
3. 环保:DDS催化剂脱硫新技术产生的副产物主要是水和二氧化碳,对环境无污染。
此外,DDS 催化剂还具有较好的抗硫中毒能力,能够减少硫资源的浪费。
4. 安全:DDS催化剂脱硫新技术采用湿式氧化法进行脱硫,避免了高温、高压等危险条件,具有较高的安全性。
四、DDS催化剂脱硫新技术的工业应用近年来,DDS催化剂脱硫新技术在石油炼制和化工行业的工业应用中取得了显著的成果。
DDS脱硫技术简介

CO2+H2O+ Na2CO32NaHCO3(由于一般气体中含有CO2)
CS2+ H2O COS + H2S
CS2+2H2O CO2+2H2S
COS + H2O CO2+ H2S
2R-SH + Fe2+Fe(R-S)2+ 2H+
3R-SH + Fe3+Fe(R-S)3+ 3H+
日常生产中只要加入三种药品:DDS催化剂、辅料、碳酸亚铁。
7、从气液吸收平衡角度讲,湿法脱硫不可能将H2S脱至1mg/m3以下,为什么DDS脱硫技术可以?
答:DDS催化剂具有特殊的结构,被DDS催化剂吸附的H2S分子即使在再生过程中没有转化为单质硫,其在溶液中也不再表现游离S2-和HS-的物化性质,因此,被DDS催化剂吸附的H2S与气相中的H2S之间不存在气液吸收平衡的问题,只有液相中极少量的游离的S2-和HS-会影响H2S的吸收。因此,可以将硫化氢脱至1 mg/m3以下。
主要目的是为了降低运行费用。由于DDS催化剂成本较高,因此价格相对也较高。加入DDS催化剂辅料、B型DDS催化剂辅料和活性碳酸亚铁后,以DDS催化剂作为“模板”,在亲硫性耗氧菌的作用下可生成DDS催化剂,从而减少DDS催化剂的加入量;另外,由于DDS催化剂对生存环境有严格要求,在亲硫性耗氧菌的作用下,加入DDS催化剂辅料、B型DDS催化剂辅料和活性碳酸亚铁后可以稳定溶液组分,给DDS催化剂的生存及保持高活性提供环境保障。
答:主要目的是为了降低运行费用。由于DDS催化剂成本较高,因此价格相对也较高。加入DDS催化剂辅料、B型DDS催化剂辅料和活性碳酸亚铁后,以DDS催化剂作为“模板”,在亲硫性耗氧菌的作用下可生成DDS催化剂,从而减少DDS催化剂的加入量;另外,由于DDS催化剂对生存环境有严格要求,在亲硫性耗氧菌的作用下,加入DDS催化剂辅料、B型DDS催化剂辅料和活性碳酸亚铁后可以稳定溶液组分,给DDS催化剂的生存及保持高活性提供环境保障。
焦炉烟气脱硫脱硝工艺流程
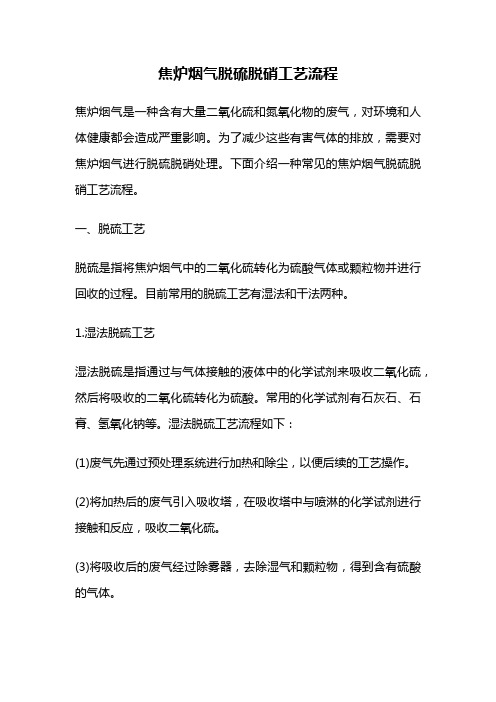
焦炉烟气脱硫脱硝工艺流程焦炉烟气是一种含有大量二氧化硫和氮氧化物的废气,对环境和人体健康都会造成严重影响。
为了减少这些有害气体的排放,需要对焦炉烟气进行脱硫脱硝处理。
下面介绍一种常见的焦炉烟气脱硫脱硝工艺流程。
一、脱硫工艺脱硫是指将焦炉烟气中的二氧化硫转化为硫酸气体或颗粒物并进行回收的过程。
目前常用的脱硫工艺有湿法和干法两种。
1.湿法脱硫工艺湿法脱硫是指通过与气体接触的液体中的化学试剂来吸收二氧化硫,然后将吸收的二氧化硫转化为硫酸。
常用的化学试剂有石灰石、石膏、氢氧化钠等。
湿法脱硫工艺流程如下:(1)废气先通过预处理系统进行加热和除尘,以便后续的工艺操作。
(2)将加热后的废气引入吸收塔,在吸收塔中与喷淋的化学试剂进行接触和反应,吸收二氧化硫。
(3)将吸收后的废气经过除雾器,去除湿气和颗粒物,得到含有硫酸的气体。
(4)最后,将含有硫酸的气体进行净化和回收,同时将剩余的废液进行处理和排放。
2.干法脱硫工艺干法脱硫是指利用固体吸收剂吸收二氧化硫,然后将吸附的硫化合物进行回收或转化为稳定的物质。
常用的固体吸收剂有活性炭、氧化铁、氧化钙等。
干法脱硫工艺流程如下:(1)废气经过预处理系统后,与喷雾的固体吸收剂进行接触和反应,吸附二氧化硫。
(2)将吸附后的固体吸收剂进行回收或转化为稳定的物质,如通过加热脱附二氧化硫。
(3)最后,将剩余的固体吸收剂进行处理和排放。
二、脱硝工艺脱硝是指将焦炉烟气中的氮氧化物转化为氮气和水的过程。
目前常用的脱硝工艺有选择性催化还原法和非选择性催化还原法两种。
1.选择性催化还原法选择性催化还原法是指将氧化剂加入焦炉烟气中,将氮氧化物转化为氮气和水。
常用的氧化剂有氨气和尿素等。
选择性催化还原法脱硝工艺流程如下:(1)预处理系统将废气进行加热和除尘。
(2)在催化剂层中,将氨气或尿素加入焦炉烟气中,氮氧化物和氨气或尿素在催化剂的作用下发生反应,生成氮气和水。
(3)最后,将剩余的氨气或尿素进行处理和回收利用。
焦炉煤气脱硫及硫回收工艺介绍及特点分析

焦炉煤气脱硫及硫回收工艺介绍及特点分析焦炉煤气脱硫是指将焦炉煤气中的硫化氢(H2S)等含硫化合物去除,以减少对环境的污染和提高能源利用效率的过程。
煤气脱硫工艺种类繁多,常见的有吸收法、吸附法、催化氧化法等。
下面将介绍吸收法和催化氧化法,并分析其特点。
吸收法是通过将焦炉煤气中的硫化氢溶于溶剂中,实现气体的物理吸收和化学吸收,从而达到脱硫的目的。
常用的溶剂有碱性溶液、有机溶剂等。
在吸收法中,气体与液体的接触方式有湿法和干法之分。
湿法吸收法是利用液体溶剂对焦炉煤气进行吸收脱硫。
具体工艺流程为:煤气首先通过一个喷淋器,将溶剂喷淋到煤气中,形成液滴;接着在吸收塔内,煤气通过液滴与溶剂的接触,硫化氢溶于溶剂中;最后,经过分离器将溶剂和硫化氢分离,溶剂再重新进入循环。
湿法吸收法具有脱硫效率高、气体处理量大、适应性广的特点。
干法吸收法是指利用固体吸附剂对焦炉煤气进行吸附脱硫。
常用的固体吸附剂有活性炭、分子筛等。
具体工艺流程为:煤气通过一个吸附器,固体吸附剂将煤气中的硫化氢吸附;当固体吸附剂饱和后,可以通过加热或换料的方式实现再生,从而循环使用。
干法吸附法具有烟气温度低、处理量大、不产生二次污染等特点。
催化氧化法是通过将焦炉煤气中的硫化氢氧化成硫酸气体,再进行后续处理。
具体工艺流程为:煤气先通过一个反应器,在催化剂的作用下,硫化氢氧化成硫酸气体;然后通过吸收塔对硫酸气体进行吸收,得到硫酸液;最后,通过蒸馏、结晶等方式使硫酸液再生。
催化氧化法具有氧化效率高、硫回收量大的特点。
总的来说,焦炉煤气脱硫及硫回收工艺的选择应根据实际情况,综合考虑效率、成本、环保等因素。
吸收法具有处理量大、脱硫效率高等特点,适用于大规模高硫煤气的处理;催化氧化法具有回收硫的优势,适用于硫回收要求较高的情况。
同时,还可以根据需求将多种脱硫工艺结合应用,以达到更好的脱硫效果。
焦炉煤气DDS脱硫技术(简装)
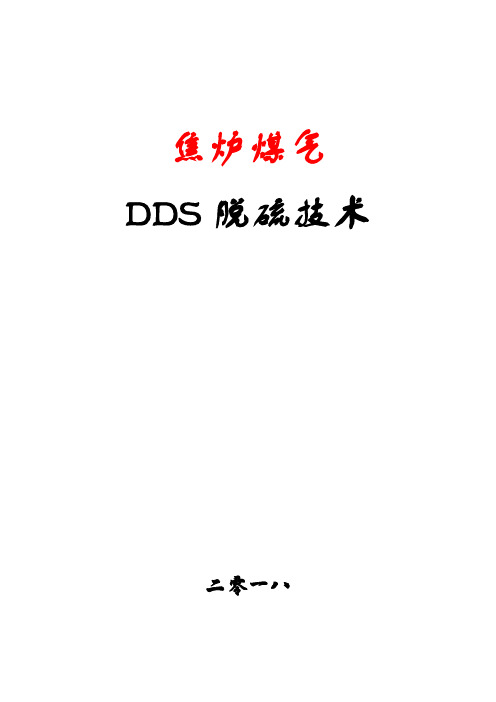
焦炉煤气DDS脱硫技术二零一八焦炉煤气DDS脱硫技术1、DDS脱硫技术简介1.1 概述DDS脱硫技术是“铁-碱溶液催化法煤气脱硫技术”的简称,是一种全新的湿法生物化学脱硫技术,用含DDS脱硫催化剂和亲硫耗氧性耐热耐碱菌及有关辅助材料的碱性溶液吸收煤气中的无机硫、有机硫、HCN和极少量的CO2,进行脱硫。
其脱硫原理和概念与传统的湿法脱硫技术有所不同。
1.2 DDS脱硫反应原理DDS脱硫剂是模仿人体正常血红蛋白的载氧性能研制出来的脱硫催化剂,它是含有铁的有机络合物的多聚合物。
DDS催化剂既能脱除无机硫又能脱除少量有机硫。
同时在吸收过程中会产生一些不溶性铁盐沉淀,好氧菌在DDS络合铁配体的协助下可以将这些不溶性铁盐瓦解,使之以活性铁离子的形式返回溶液中,保证溶液中各种形态铁离子的稳定存在。
DDS脱硫液在酚类物质与铁离子的共同催化下,用空气氧化再生,副产硫膏,再生DDS脱硫液循环使用。
其反应过程可归纳为:吸收反应、再生反应、生物降解反应。
1)吸收反应可以简单归结如下为五类反应:(1) H2S、CO2与碱及铁离子的反应。
(2) CS2、COS的水解反应。
(3) R-SH、 SH 与铁离子的反应。
(4) SO2与H2S的氧化还原反应。
(5) 少量铁离子在碱性溶液中的降解反应。
2)再生反应可以简单归结为如下三类反应:(1) NaHCO3与Na2CO3的转换过程(2) Fe3+氧化溶液中的S2-及HS-离子自身被还原为Fe2+,Fe2+再被空气中的氧及醌类物质氧化为Fe3+的反应。
(3) 醌氧化溶液中的S2-、HS-及Fe2+离子自身被还原为酚,酚再被氧化为醌的酚醌转换的过程。
3)生物降解过程的降解反应可以简单归结为如下三类反应:(1) 细菌与不溶性铁盐[Fe(OH)2、FeCO3、FeO、FeS]结合并返回到溶液中。
(2) 在DDS配体作用下瓦解不溶性铁,重新结合为DDS铁的形式。
(3) 载氧菌氧化溶液中的S2-及HS-离子。
焦炉煤气精脱硫工艺分析

焦炉煤气精脱硫工艺分析一、工艺原理:焦炉煤气中的H2S主要通过煤气中的Fegl肟羧酸盐、CaS等吸收剂进行吸收。
Fegl肟羧酸盐是一种高效的硫化物吸收剂,可在较低的温度下将煤气中的H2S和COS吸收。
而CaS则可以将煤气中的剩余H2S去除。
二、工艺流程:1.气体预处理:首先对焦炉煤气进行预处理,去除其中的悬浮颗粒物和水分,以净化煤气。
2.前骤吸收:采用Fegl肟羧酸盐作为吸收剂,通过吸收剂床将煤气中的H2S、COS等硫化物吸收。
床层中的吸收剂会与煤气中的硫化氢进行反应,生成硫化铁,并将其捕集。
3.普鲁士蓝阳极液循环:将废液中的硫化铁氧化为硫酸铁,通过循环泵送到反应床顶部,实现循环利用。
4.精脱硫:采用CaS作为吸收剂,通过床层吸收煤气中剩余的硫化氢,并将其转化为CaS。
此过程需要保持一定的温度和压力,以促使吸收反应的进行。
5.再复焦炉:将经过精脱硫的煤气送入焦炉进行再加热,以提高炉内温度。
三、工艺特点:1.高效: 采用Fegl肟羧酸盐和CaS作为吸收剂,可以高效地吸收煤气中的硫化物,使硫化氢的去除率达到90%以上,保证煤气的质量。
2.安全:精脱硫过程中对温度和压力的要求较高,可以有效地防止硫化氢的泄漏,保证了生产环境的安全。
3.循环利用:工艺中的废液通过循环泵送到反应床顶部,实现了废液中的硫化铁的循环利用,减少了废液的排放,具有较好的环保效益。
总结起来,焦炉煤气精脱硫工艺通过床层吸收剂的反应,有效地去除焦炉煤气中的硫化氢等硫化物,以保证煤气的质量达到环保要求。
该工艺具有高效、安全、循环利用等特点,在焦化行业得到广泛应用。
工艺方法——焦炉煤气脱硫技术
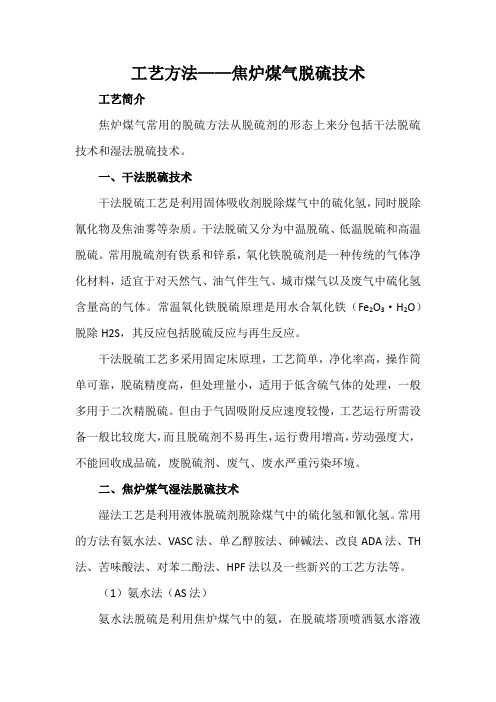
工艺方法——焦炉煤气脱硫技术工艺简介焦炉煤气常用的脱硫方法从脱硫剂的形态上来分包括干法脱硫技术和湿法脱硫技术。
一、干法脱硫技术干法脱硫工艺是利用固体吸收剂脱除煤气中的硫化氢,同时脱除氰化物及焦油雾等杂质。
干法脱硫又分为中温脱硫、低温脱硫和高温脱硫。
常用脱硫剂有铁系和锌系,氧化铁脱硫剂是一种传统的气体净化材料,适宜于对天然气、油气伴生气、城市煤气以及废气中硫化氢含量高的气体。
常温氧化铁脱硫原理是用水合氧化铁(Fe2O3·H2O)脱除H2S,其反应包括脱硫反应与再生反应。
干法脱硫工艺多采用固定床原理,工艺简单,净化率高,操作简单可靠,脱硫精度高,但处理量小,适用于低含硫气体的处理,一般多用于二次精脱硫。
但由于气固吸附反应速度较慢,工艺运行所需设备一般比较庞大,而且脱硫剂不易再生,运行费用增高,劳动强度大,不能回收成品硫,废脱硫剂、废气、废水严重污染环境。
二、焦炉煤气湿法脱硫技术湿法工艺是利用液体脱硫剂脱除煤气中的硫化氢和氰化氢。
常用的方法有氨水法、VASC法、单乙醇胺法、砷碱法、改良ADA法、TH 法、苦味酸法、对苯二酚法、HPF法以及一些新兴的工艺方法等。
(1)氨水法(AS法)氨水法脱硫是利用焦炉煤气中的氨,在脱硫塔顶喷洒氨水溶液(利用洗氨溶液)吸收煤气中H2S,富含H2S和NH3的液体经脱酸蒸氨后再循环洗氨脱硫。
在脱硫塔内发生的氨水与硫化氢的反应是:H2S+2NH3·H2O→(NH4)2S+2H2O。
AS循环脱硫工艺为粗脱硫,操作费用低,脱硫效率在90%以上,脱硫后煤气中的H2S在200-500mg·m-3。
(2)VASC法VASC法脱硫过程是洗苯塔后的煤气进入脱硫塔,塔内填充聚丙烯填料,煤气自下而上流经各填料段与碳酸钾溶液逆流接触,再经塔顶捕雾器出塔。
煤气中的大部分H2S和HCN和部分CO2被碱液吸收,碱液一般主要是Na2CO3或K2CO3溶液。
吸收了酸性气体的脱硫富液与来自再生塔底的热贫液换热后,由顶部进入再生塔再生,吸收塔、再生塔及大部分设备材质为碳钢,富液与再生塔底上升的水蒸汽接触使酸性气体解吸。
焦炉煤气脱硫技术操作规程

2、原料、产品的技术条件及质量标准2.1原料、产品技术条件入吸收塔煤气温度23~25℃入吸收塔脱硫液温度30~35℃进再生塔空气压力≥0.5MPa进导热油温度200~230℃出导热油温度180~220℃2.2产品质量标准吸收塔后煤气含H2S≤0.5g/Nm3脱硫效率≥90%3、设备一览表序号设备名称型号台数标准设备1吸收液循环泵CZ300-500Q=1200m3/hH=50m3附电机N=280kw(10KV)YKK450-4W32再生液循环泵CZ300-500Q=1200m3/hH=50m3附电机N=280kw(10kv) YKK450-4w33缓冲液泵SCZ200-400AQ=650m3/hH=50m2附电机N=132kw Y315M1-4w25滤液泵SAJK50-32-160AQ=9m3/hH=30m2附电机N=4kw YFB112M-2W26浆液泵SAJK50-32-200AQ=9m3/hH=50m2附电机N=7.5kw YFB132M-2W27放空槽自吸泵SLZ50-32-160Q=12.5m3/hH=32m1附电机N=5.5kw Y132S1-2-W18离心机LW450×1610-N2附电机N=37kw Y225S-4w29手动单轨吊Q=5t SDX-31附手拉葫芦H=11m HS5110手动单轨吊Q=5t SDX-31附手拉葫芦H=16m HS5111煤气电动闸阀DN1400 MZg44w-1.55附电动装置N=7.5kw16循环液冷却器F=70m2 BR05-1.0-70-E-12 17熔硫釜DN1200 H=5000418螺杆式空气压缩机37.8m3/min LU200-2502附主电机N=250kw 2非标设备2 19吸收塔DN6000 H=32400(其中不锈钢15526.5kg)20再生塔DN5500 H=24700(其中不锈钢9564.8kg)2 21事故槽DN9000 H=9725 VN=550m31 22缓冲槽DN7740 H=9140 VN=430m31搅拌器附电机N=15kw2 23滤液槽DN1400 H=20001 24浆液槽DN1400 H=50001 25废液槽DN3400 H=28251 26地下放空槽DN1400 L=4500 VN=6m31 27水封槽DN800 H=15001 28旋流板捕雾器DN1600 H=50002 29硫磺冷却盘1200×1200×1504 4、岗位工艺技术指标4.1温度指标入吸收塔煤气温度23~25℃入吸收塔脱硫液温度35~40℃导热油温度200~230℃导热油温度180~220℃4.2压力指标5.9认真执行周五加油制,备用设备每班盘车一次。
DDS脱硫技术简介

1、简述
简单的说
铁—碱溶液催化法气体脱碳脱硫脱氰方法 发明DDS催化剂
细菌
生化铁——碱溶液催化法气体脱硫方法 DDS脱硫技术
2、铁
3、
简单地说,
我们将加入了
4、生化铁——碱溶液催化法气体脱硫方法(专利申请号:02130605.2;公开号:1398659)
结合生物制药的研究,魏博士考虑能否在溶液中加入某种能够分解铁盐沉淀的细菌,使生成的铁盐沉淀在细菌的作用下分解,然后再把铁释放回溶液中。在以后的日子里,寻找这种细菌就成了魏博士研究工作的主要内容。经过大量的试验和筛选,最终找到了一种细菌具有这种功能。将这种细菌加入“铁——碱溶液”中,不但解决了溶液稳定性差的问题,而且脱硫效果也有明显的提高。将加了细菌的“铁——碱溶液”脱硫法称为“生化铁——碱脱硫法”,为方便起见,也叫“DDS脱硫法”。“DDS脱硫法”不但延承了络合铁法脱硫效率高的优点,而且克服了络合铁法不稳定的缺点,使运行成本大幅度降低。因此,DDS催化剂和细菌是“DDS脱硫技术”的两大核心技术。如何保证DDS催化剂及其相应的菌类处于最佳活性状态是本技术的关键所在。
SO2+2H2SH2O +3S
Fe2++2OH-Fe(OH)2
Fe3++3OH-Fe(OH)3
以上反应中CS2,COS,R-SH,SH分别是二硫化碳,硫氧化碳,硫醇和硫酚,它们属于挥发性有机硫类化合物。
以上吸收反应可以简单归结为如下五类反应:
(1)、H2S、CO2与碱及铁离子的反应。
(2)、CS2、COS的水解反应。
4Fe2++ O2+ 2H2O 4Fe3++ 4OH-
煤气脱硫

煤气脱硫鼓入空气,用空气进行氧化再生并析出单指硫。
大量的硫泡沫在再生塔内生成,并浮于塔顶扩大部分。
由此利用位差自流入硫泡沫槽,经澄清分层,清夜返回循环槽,硫泡沫放至真空过滤机进行过滤,成为硫膏。
硫膏经处理制得硫磺产品。
再生塔内的液体自下流到脱硫塔顶部循环使用。
要求溶液的pH值在8.5~9.1之间,pH值若小于8.5会导致反应速度太慢,太高会增加副反应,使碱耗增大,同时硫析出速度加快,易造成堵塔。
图3—9 脱硫过程示意图1—吸收塔;2—再生塔;3—循环槽湿法脱硫常用的方法如下:(1)FRC法FRC法由日本开发研制,利用焦炉煤气中的氨,在催化剂苦味酸的作用下脱除H2S,利用多硫化铵脱除HCN。
其装置是由吸收塔和再生塔组成,前者用以吸收粗煤气中的硫化氢,后者用以硫化氢氧化和催化剂再生。
将煤气用弗玛克斯液洗涤,所含硫化氢被洗涤液吸收后,脱硫即可完成,其吸收反应为:NH3+H2S=NH4HS。
将吸收污液送入再生塔,使之与空气接触,氧化硫化氢的同时再生催化剂,然后送回吸收塔顶循环,循环液中悬浮再生的固体硫磺,用离心机分离回收。
该工艺脱硫效率高达99%以上、脱氰效率为93%,煤气经吸收塔后,H2S可降到20mg/m3,HCN可降到100mg/m3。
催化剂苦味酸耗量少且便宜易得,操作费用低;再生率高,新空气用量少、废气含氧量低,无二次污染。
但因苦味酸是爆炸危险品,运输存储困难,且工艺流程长、占地多、投资大等因素,其使用受到一定限制。
(2) HPF法HPF法是国内自行开发的以氨为碱源、HPF为复合催化剂的湿式液相催化氧化脱硫脱氰工艺,主要由脱硫和再生两部分组成。
该法也是以煤气中的氨为碱源,脱硫液在吸收了煤气中H2S后,在复合催化剂HPF作用下氧化再生,最终H2S转化为单体硫得以除去,脱硫液循环使用,生成的硫泡沫放人熔硫釜,经间歇熔硫、冷却成型后外售。
HPF催化剂活性高、流动性好,不仅对脱硫脱氰过程起催化作用,而且对再生过程也有催化作用,脱硫脱氰效率高。
科技成果——DDS烟道气除尘脱硫脱硝技术
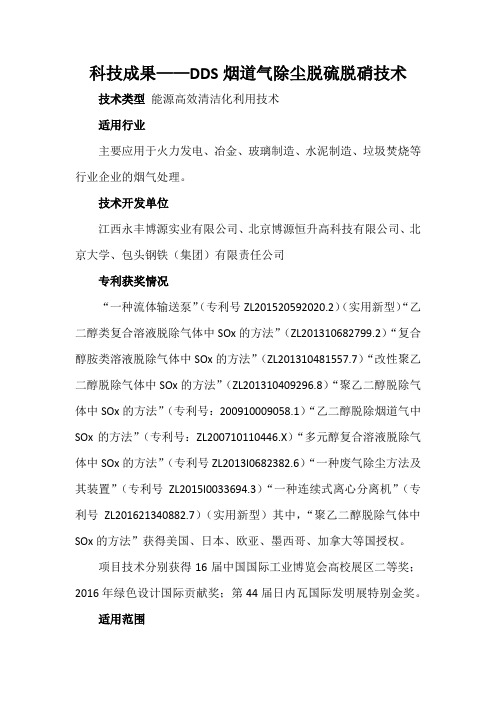
科技成果——DDS烟道气除尘脱硫脱硝技术技术类型能源高效清洁化利用技术适用行业主要应用于火力发电、冶金、玻璃制造、水泥制造、垃圾焚烧等行业企业的烟气处理。
技术开发单位江西永丰博源实业有限公司、北京博源恒升高科技有限公司、北京大学、包头钢铁(集团)有限责任公司专利获奖情况“一种流体输送泵”(专利号ZL201520592020.2)(实用新型)“乙二醇类复合溶液脱除气体中SOx的方法”(ZL201310682799.2)“复合醇胺类溶液脱除气体中SOx的方法”(ZL201310481557.7)“改性聚乙二醇脱除气体中SOx的方法”(ZL201310409296.8)“聚乙二醇脱除气体中SOx的方法”(专利号:200910009058.1)“乙二醇脱除烟道气中SOx的方法”(专利号:ZL200710110446.X)“多元醇复合溶液脱除气体中SOx的方法”(专利号ZL2013I0682382.6)“一种废气除尘方法及其装置”(专利号ZL2015I0033694.3)“一种连续式离心分离机”(专利号ZL201621340882.7)(实用新型)其中,“聚乙二醇脱除气体中SOx的方法”获得美国、日本、欧亚、墨西哥、加拿大等国授权。
项目技术分别获得16届中国国际工业博览会高校展区二等奖;2016年绿色设计国际贡献奖;第44届日内瓦国际发明展特别金奖。
适用范围适用于火电、钢铁、水泥、玻璃、冶炼、陶瓷、化工、建材和垃圾焚烧等废气的除尘、脱硫和脱硝。
可以是除尘、脱硫、脱硝一体化全套装置,也可投资单项功能设备。
本技术可适合SO2含量大于10%的烟道气脱硫,为硫含量大于3%的原煤、高硫含量的重油、煤焦油和石油焦等劣质燃料开拓了广阔的应用前景;本技术脱除各种有机物的能力显著,也为垃圾焚烧尾气的治理带来了便利。
成果简介DDS烟道气除尘、脱硫、脱硝技术是一种拥有完全自主知识产权的烟道气综合治理创新技术,该技术逐级将烟气中灰尘、HF、HCl、二噁英、多环芳烃等有机物、重金属、SO2、NO X等有害成分从烟道气中分离出来,实现烟气最终的洁净排放;脱硫液封闭全循环;同时,将分离出来的有害物质富集起来,转化成高度纯液体SO2和NO X或硝酸盐副产品,并利用辅助余热回收系统将烟气中的多余热量富集起来,实现系统热平衡。
焦炉煤气DDS脱硫技术介绍
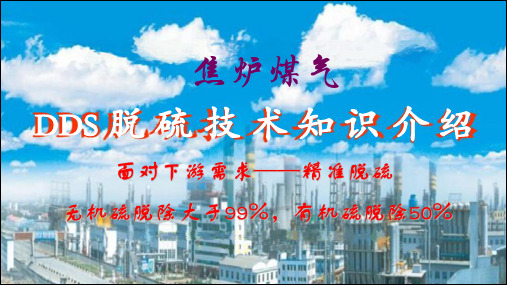
焦炉煤气DDS 脱 硫 技 术 知识介绍脱硫效果好、精度高,无机硫脱除率99%以上,有机硫脱除率可达到50%,视含硫状况与业主需求,通过多级脱硫,S降至1mg/Nm3以下。
可将气体中的H2对于焦炉煤气脱硫而言,减少精脱硫投资,减轻后续烟道气脱硫负荷。
降低二次污染的处理难度。
利于高老厂脱硫效率,不达标厂在不增加设备投资情况下达到煤气脱硫要求指标。
例如:阳煤集团平原化工有限公司:全厂8套常压脱脱、加压脱硫系统P=0.8MPa,气量约4×76000Nm3/h;常压系统进口3000 ~ 5000mg/m3;出口≤50 mg/m3加压系统进口300 ~ 500 mg/m3;出口≤1.7 mg/m3安徽泉盛化工有限公司:33万t合成氨变脱共1套系统P=2.5MPa,气量约175000Nm3/h;变脱进口120 ~ 260 mg/m3,出口≤1 mg/m31碱源碳酸钠碳酸钠相同栲胶、PDS、8889检修时间10堵塔程度11副盐生成量节能和运行焦炉气中含有苯、萘、酚、焦油以及HCN等有害物质,对脱硫催化剂影响较大,致使很多催化剂很难适应这种工况,即使勉强应用,也会造成系统脱硫效率抵、副盐高,溶液外排量大,环境污染严重等问题。
焦炉气中的酚、苯类等有机物含量较高,而DDS 催化剂辅料为多酚类,它们在物质结构及性能上有相近之处,因此,酚、苯类的存在对发挥 DDS 催化剂的性能有推进作用,不会产生副作用。
焦炉气含CO较低,约为半水煤气的三分之2的吸收,有利于一,可降低脱硫溶液对CO2溶液PH值的稳定,从而提高脱硫效率。
采用改良 ADA 湿法脱硫的企业,脱硫溶液中的ADA、V 2O 5对 DDS 催化剂没有副作用,且其适当的含量具有激活 DDS 催化剂活性的作用。
(更换DDS时的优点)由于 DDS 催化剂分子结构的特殊性,可减少溶液中副盐 Na 2S 2O 3、Na2SO 4的生成量,稳定溶液的物理、化学性能。
煤化工技术专业《16种脱硫工艺技术以及实际应用情况详解9》
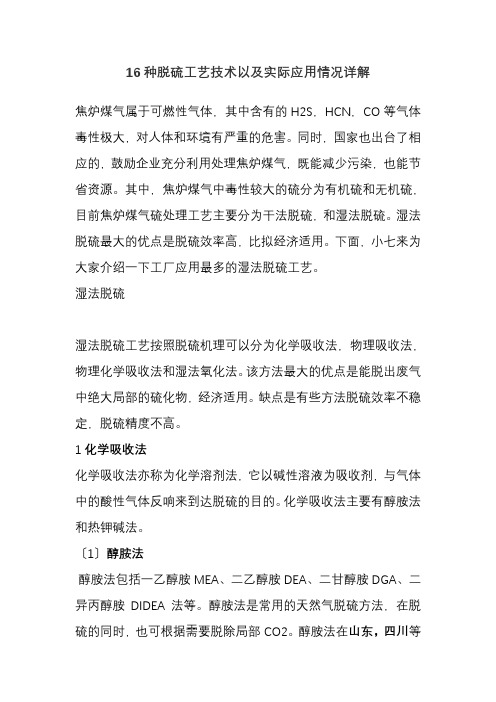
16种脱硫工艺技术以及实际应用情况详解焦炉煤气属于可燃性气体,其中含有的H2S,HCN,CO等气体毒性极大,对人体和环境有严重的危害。
同时,国家也出台了相应的,鼓励企业充分利用处理焦炉煤气,既能减少污染,也能节省资源。
其中,焦炉煤气中毒性较大的硫分为有机硫和无机硫,目前焦炉煤气硫处理工艺主要分为干法脱硫,和湿法脱硫。
湿法脱硫最大的优点是脱硫效率高,比拟经济适用。
下面,小七来为大家介绍一下工厂应用最多的湿法脱硫工艺。
湿法脱硫湿法脱硫工艺按照脱硫机理可以分为化学吸收法,物理吸收法,物理化学吸收法和湿法氧化法。
该方法最大的优点是能脱出废气中绝大局部的硫化物,经济适用。
缺点是有些方法脱硫效率不稳定,脱硫精度不高。
1化学吸收法化学吸收法亦称为化学溶剂法,它以碱性溶液为吸收剂,与气体中的酸性气体反响来到达脱硫的目的。
化学吸收法主要有醇胺法和热钾碱法。
〔1〕醇胺法醇胺法包括一乙醇胺MEA、二乙醇胺DEA、二甘醇胺DGA、二异丙醇胺DIDEA法等。
醇胺法是常用的天然气脱硫方法,在脱硫的同时,也可根据需要脱除局部CO2。
醇胺法在山东,四川等工厂有广泛的应用。
2021年,永坪炼油厂改用醇胺法脱硫,脱硫效果及产品质量均得到提高。
〔2〕热钾碱法催化热钾碱法工艺图热碱钾法采用的是较高浓度的碳酸钾水溶液做吸收剂,可以直接吸收煤气中的硫化氢和氰化氢。
该方法吸收酸气速率慢,效率低,已逐渐被催化热钾碱法取代。
催化热钾碱法就是在碳酸钾溶液里参加一定量的催化剂,加快反响速率。
真空碳酸钾法工艺流程真空碳酸钾法是利用碳酸钾溶液直接吸收酸性气体,脱硫装置在粗苯回收后面,位于焦炉煤气工艺流程末端。
该工艺开始是由德国引进而来的,使用该方法脱硫脱氰后的酸性气体,既可以采用克劳斯法生产元素硫,也可以使用接触法生产硫酸。
之后,中野焦耐公司在吸收国内外真空碳酸钾先进技术及生产实践的根底上,与高等院校合作开发了具有自主产权的新工艺,已在宝钢股份化工公司梅山分公司,陕西焦化,邯郸新区焦化厂等工厂得到应用。
工艺方法——焦炉煤气脱硫技术

工艺方法——焦炉煤气脱硫技术工艺简介焦炉煤气是炼焦过程的副产品,是H2、CH4、CO2、CO等气体组成的混合物,焦炉煤气的产率和构成取决于炼焦用煤的质量及炼焦过程操作条件。
焦炉煤气是一种高热值煤气,可作燃料使用,也可用作化工产品的重要原料,如合成氨、甲醇等。
焦炉煤气无论是作燃料,还是作生产原料,使用前需进行净化处理,以脱除煤气中H2S及HCN 等,满足环保和生产要求。
焦炉煤气脱硫工艺可分为干法脱硫工艺和湿法脱硫工艺2大类。
一、干法脱硫工艺干法脱硫工艺是指使用固体脱硫剂,在固定床层中进行H2S的物理或化学吸附、吸收与化学反应。
干法脱硫技术主要包括活性炭系、铁系、锌系、铜系、锰系及钙系等脱硫剂。
干法脱硫效率高,生产成本低,但脱硫剂需要定期更换,劳动强度大,同时失效的脱硫剂需进行处理。
因此,干法脱硫工艺主要用于湿法脱硫后的精脱硫。
二、湿法脱硫工艺湿法脱硫工艺是指利用液体形式的脱硫剂脱除煤气中的H2S和HCN。
按溶液的吸收和再生性质又分为湿式吸收法,包括物理吸收法、化学吸收法和物理-化学吸收法以及湿式氧化法。
湿法脱硫具有焦炉煤气处理量大、脱硫效率高等特点,在国内焦炉煤气脱硫中较为常用。
1、湿式吸收法湿式吸收法是以单乙醇胺、碳酸盐及氨溶液等不同的碱源作吸收液,吸收焦炉煤气中的H2S和HCN,吸收液在一定操作条件下经解吸释放出H2S等酸性气体,借助制酸工艺或克劳斯工艺,将酸性气体转化生成硫酸或硫磺产品。
湿式吸收法包括真空碳酸盐法、氨硫联合洗涤法及单乙醇胺法。
(1)真空碳酸盐法真空碳酸盐法脱硫工艺是—种物理—化学吸收方法,溶液中起吸收作用的是碳酸钠(或碳酸钾)。
焦炉煤气与吸收液逆流进行传质并发生反应,HCN、H2S及CO2被吸收液吸。
吸收了H2S的等酸性气体的溶液循环到再生塔,在一定操作条件下,H2S等酸性气体析出,实现吸收液的再生。
酸性气体经克劳斯法生成硫磺或经Topsoe法生成浓硫酸。
该工艺特点如下:脱硫剂单一,脱硫效率可达99%;产品质量好,硫磺纯度可达99.7%;采用真空解吸,操作温度低,为50-60℃,可有效利用循环氨水余热。
DDS脱硫技术的基本原理

关键词: 脱硫 脱硫技术 本技术是用含好氧菌、酚类物质和含铁离子的碱性物质的水溶液(以下简称为“DDS 脱硫液”),吸收气体中的有机硫、无机硫,同时,在吸收过程中也会产生一些不溶性铁盐 沉淀,好氧菌在 DDS 络合配体的协助下,可以将这些不溶性铁盐瓦解,使之以活性铁离子 的形式返回溶液中,保证溶液中各种形态铁离子稳定存在,DDS 脱硫液在酚类物质与铁离 子的共同催化下,用空气氧化再生,副产硫磺,再生 DDS 脱硫液全循环使用。当气体和 DDS 脱硫液接触时,发生如下吸收反应(为了方便起见,在以下的反应式中,我们仅用 Fe、Fe2、 Fe3分别表示零价型 DDS 催化剂、二价型 DDS 催化剂和三价型 DDS 催化剂;用 DDS 表示 DDS 络合铁的配体、酚类物质仅用对苯二酚表示、好氧菌用⊙表示)。气体和 DDS 脱硫液接触时, 发生如下吸收反应:CO2 H2O Na2CO32NaHCO3CS2 H2OCOS H2SCOS H2OCO2 H2S2R-SH Fe2Fe(R-S)2 2H 3R-SH Fe3Fe(R-S)3 3H 2SH Fe2Fe(S)2 2H 3SH Fe3Fe(S)3 3H H2S Na2CO3NaHS NaHCO3H2S Fe2FeS 2H 3H2S 2Fe3Fe2S3 6H CO2 Fe2H2OFeCO3 2H 3CO2 Fe33H2OFe2(CO3)3 6H SO2 2H2SH2O 3SFe22OH-Fe(OH)2Fe33OH-Fe(OH)3⊙ FeCO3⊙-FeO CO2⊙ Fe2(CO3)3⊙-Fe2O3 3CO2⊙ FeS⊙-FeS⊙ Fe2S3⊙-Fe2S3⊙ Fe(OH)2⊙-Fe(OH)2⊙ Fe(OH)3⊙-Fe(OH)3以上反应中 CS2,COS,R-SH,SH 分别是二硫化碳,硫氧化碳,硫醇和硫酚,它们属于挥发性有机硫类化合物。吸收了硫和 二氧化碳的含铁离子的碱性物质水溶液(即“DDS 脱硫液”),以下简称为“富液”。“富 液”在酚类物质与铁离子的共同催化下,用空气氧化再生,再生反应如下:2NaHCO3Na2CO3 H2O CO24Fe2O2 2H2O4Fe34OH-2HOOH O2OO 2H2OS2- OO 2H2OHOOH 2OH- S2Fe2OO 2H2OHOOH 2Fe32OH-S22Fe32Fe2S 经空气氧化再生,“富液”转变成“贫液”,“贫液”再循环使用。由于在吸收 和再生过程中会产生氢氧化铁、氢氧化亚铁、氧化铁、氧化亚铁、硫化铁和硫化亚铁等不 溶性铁盐,在 DDS 络合配体的协助下,好氧菌可以将生成的不溶性铁盐瓦解,使之返回 DDS 脱硫液中,保证溶液中各种形态铁离子稳定存在,其作用过程如下:⊙ FeCO3⊙-FeO CO2⊙ Fe2(CO3)3⊙-Fe2O3 3CO2⊙ FeS⊙-FeS⊙ Fe2S3⊙-Fe2S3⊙ Fe(OH)2⊙-Fe(OH)2⊙ Fe(OH)3⊙-Fe(OH)3⊙-FeO DDS⊙-O DDS-Fe2⊙-Fe2O3 2DDS⊙-3O 2DDS-Fe3⊙-FeS DDS⊙-S DDS-Fe2⊙-Fe2S3 2DDS⊙-3S 2DDS-Fe3⊙-Fe(OH)2 DDS⊙-O DDS-Fe2H2O⊙-Fe(OH)3 DDS OH-⊙-2O DDS-Fe32H2O⊙-O ⊙-S H2O2⊙ 2OH- S⊙-2O 2⊙-S 2H2O3⊙ 4OH- 2S⊙-3O ⊙-3S 3H2O2⊙ 6OH- 6SDDS-Fe2DDS Fe2DDS-Fe3DDS Fe3从以上反应式中可以看出,增大溶液中碳酸 亚铁含量,可以减少和防止 DDS 催化剂分解,这就是为什么要向脱硫液中加入适量的碳酸 亚铁的原因。由于“DDS 脱硫液”进入系统后,首先会在所有设备内壁形成一层非常致密 的氧化物保护膜;再者,DDS 脱硫液中含有较高浓度的二价铁离子和三价铁离子,从化学 反应动力学和热力学及化学反应平衡理论角度来看,可以有效降低单质铁被氧化成二价铁 离子或三价铁离子的反应速度,即减缓溶液对设备的腐蚀速度,延长设备的使用寿命。
梅山钢铁焦炉煤气DDS生物脱硫技术的应用研究
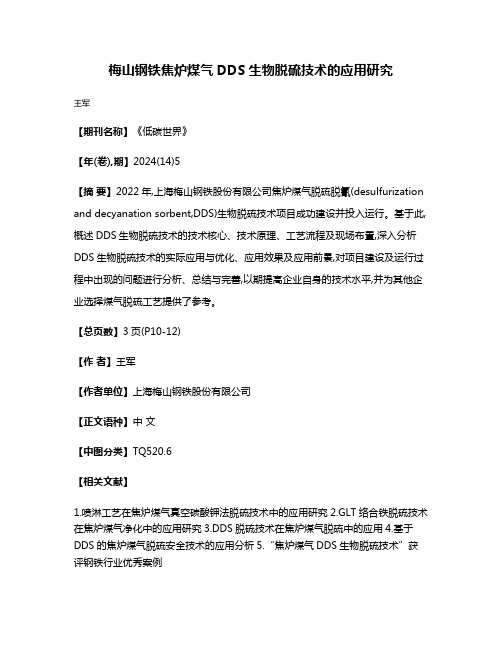
梅山钢铁焦炉煤气DDS生物脱硫技术的应用研究
王军
【期刊名称】《低碳世界》
【年(卷),期】2024(14)5
【摘要】2022年,上海梅山钢铁股份有限公司焦炉煤气脱硫脱氰(desulfurization and decyanation sorbent,DDS)生物脱硫技术项目成功建设并投入运行。
基于此,概述DDS生物脱硫技术的技术核心、技术原理、工艺流程及现场布置,深入分析DDS生物脱硫技术的实际应用与优化、应用效果及应用前景,对项目建设及运行过程中出现的问题进行分析、总结与完善,以期提高企业自身的技术水平,并为其他企业选择煤气脱硫工艺提供了参考。
【总页数】3页(P10-12)
【作者】王军
【作者单位】上海梅山钢铁股份有限公司
【正文语种】中文
【中图分类】TQ520.6
【相关文献】
1.喷淋工艺在焦炉煤气真空碳酸钾法脱硫技术中的应用研究
2.GLT络合铁脱硫技术在焦炉煤气净化中的应用研究
3.DDS脱硫技术在焦炉煤气脱硫中的应用
4.基于DDS的焦炉煤气脱硫安全技术的应用分析
5.“焦炉煤气DDS生物脱硫技术”获评钢铁行业优秀案例
因版权原因,仅展示原文概要,查看原文内容请购买。
科技成果——DDS烟道气除尘脱硫脱硝技术

科技成果——DDS烟道气除尘脱硫脱硝技术技术开发单位北京博源恒升高科技有限公司、北京泓龙环保有限公司、江西永丰博源实业有限公司、北京大学适用行业火电、钢铁、冶金、陶瓷、建材、化工、垃圾焚烧等适用范围烟道气除尘(含脱除PM粒子、二噁英、多环芳烃、部分VOCs 和部分重金属)、脱硫(脱除SO X)和脱硝(脱除NO X)等。
成果简介DDS烟道气除尘脱硫脱硝技术是首先除尘,再进行脱硫,最后进行脱硝,三个过程可以相互独立,也可以合并在一起。
每个过程介绍如下:除尘:DDS除尘液是根据相似相溶原理设计的一种无毒、无害的含大分子的液体;在除尘塔中,DDS除尘液和烟道气直接接触,将烟道气中的灰尘(含PM粒子)及HCl、HF、二噁英、多环芳烃、部分VOCs和重金属等捕捉,然后经再生分离出所捕捉的有害物质,再生分离后的DDS除尘液循环使用,同时将烟道气的温度降至40℃以下,并回收余热,副产水蒸汽,实现节能环保。
脱硫:DDS脱硫液是含DDS脱硫剂的乙二醇或聚乙二醇溶液。
在脱硫塔中,DDS脱硫液和除尘后的低温烟道气直接接触,吸收烟道气中的SO2,吸收了SO2的DDS脱硫液在再生塔中,在90-130℃下,经蒸汽气提再生,并释放出SO2,再生后的DDS脱硫液循环使用;再生释放出的SO2经提浓后转化成纯度大于99%的SO2副产品,实现变废为宝。
脱硝:在脱硝塔中,脱硫后的烟道气和自由基氧混合,烟道气中的NO被氧化成NO2。
继续在自由基氧的作用下,NO2与碱性物质水溶液(如NaOH或KOH水溶液等)接触,生成硝酸盐溶液,达到脱硝目的。
硝酸盐溶液经浓缩、结晶,获得纯度大于99%的硝酸盐(如NaNO3或KNO3等)副产品,实现变废为宝。
技术效果脱除烟道气中的灰尘、二氧化硫和氮氧化物效率高,可以实现超低排放。
从工业源头消除大气污染,减轻甚至消除灰霾现象,无二次污染。
彻底脱除烟道气中二氧化硫和氮氧化物,并副产纯二氧化硫和硝酸盐产品,实现变废为宝。
焦炉煤气脱硫工艺技术

焦炉煤气脱硫工艺技术焦炉煤气脱硫工艺技术是指通过一系列的物理、化学或生物方法,去除焦炉煤气中的硫化氢(H2S)等有害物质,以保护环境和提高煤气利用效率的技术过程。
目前常用的焦炉煤气脱硫工艺有干法脱硫和湿法脱硫两种。
干法脱硫是指通过吸附剂吸附H2S等硫化物,然后进行再生处理,脱除硫化物而实现脱硫的过程。
常用的吸附剂有氧化铁、铁磁性煤气净化剂和锰增强剂。
在焦炉煤气脱硫的工艺中,需要优化吸附剂的选择和技术参数,以提高脱硫效率和经济性。
湿法脱硫是将焦炉煤气先与一定流量的洗涤液接触,使H2S等硫化物溶解到液体中,然后通过氧化、沉淀、吸附等方法将硫化物转化为硫酸根离子或其他形式,最后得到脱硫后的煤气。
湿法脱硫常用的洗涤液有氨碱溶液、碱性液体和氧化剂溶液等。
湿法脱硫技术具有脱硫彻底、操作简便等优点,但是存在液体回收、处理和废水排放等问题。
在实际应用中,干法脱硫常用于小型焦炉,工艺简单、成本较低,但不能完全脱除H2S;湿法脱硫则适用于大型焦炉,能有效去除H2S,但其液相处理和废水处理是一个挑战。
近年来,为了提高焦炉煤气脱硫效率和降低环境污染,一些新兴的煤气脱硫技术被广泛关注和研究。
比如,生物脱硫技术是利用硫氧化细菌、硫还原细菌等微生物对焦炉煤气中的硫化氢进行吸附、处理和转化的一种脱硫方法。
生物脱硫技术具有脱硫效率高、废水低、处理成本低等优点,但需要解决微生物耐受性、稳定性和生长条件等问题。
除了上述的脱硫技术外,目前还有很多新的煤气脱硫工艺正在不断涌现,如气体膜分离技术、超声波脱硫技术等。
这些新技术通过提高脱硫效率、降低能耗和废物产生,为未来焦炉煤气脱硫提供了更好的选择。
总之,焦炉煤气的脱硫工艺技术对于环境保护和碳资源利用具有重要意义。
通过不断创新和研发,我们将能够开发出更加高效、环保和经济的焦炉煤气脱硫技术,为可持续发展做出更大的贡献。
- 1、下载文档前请自行甄别文档内容的完整性,平台不提供额外的编辑、内容补充、找答案等附加服务。
- 2、"仅部分预览"的文档,不可在线预览部分如存在完整性等问题,可反馈申请退款(可完整预览的文档不适用该条件!)。
- 3、如文档侵犯您的权益,请联系客服反馈,我们会尽快为您处理(人工客服工作时间:9:00-18:30)。
目录1、DDS脱硫技术简介1.1 概述1.2 DDS脱硫反应原理1.3 工艺流程简介2、DDS脱硫剂2.1 主要组分及作用2.2 DDS脱硫溶液2.3 加入四种药品的原因3、DDS脱硫过程中的注意事项3.1 加药过程中需要注意的问题3.2 DDS脱硫的再生时间和溶液的PH值3.3 细菌疲劳3.4 细菌数量3.5 副反应问题4、DDS脱硫技术操控指标及效果4.1 操控指标4.2 脱硫效果5、原料投入及运行成本分析5.1 原料投入分析5.2 运行成本分析附DDS脱硫操作焦炉煤气DDS脱硫技术1、DDS脱硫技术简介1.1 概述DDS脱硫技术是“生化铁—碱溶液催化法气体脱硫方法”的简称,是一种全新的湿法生物化学脱硫技术,用含DDS脱硫催化剂和亲硫耗氧性耐热耐碱菌及有关辅助材料的碱性溶液吸收煤气中的无机硫、有机硫和极少量的二氧化碳,进行脱硫。
其脱硫原理和概念与传统的湿法脱硫技术有所不同。
1.2 DDS脱硫反应原理DDS脱硫剂是模仿人体正常血红蛋白的载氧性能研制出来的脱硫催化剂,它是含有铁的有机络合物的多聚合物。
DDS催化剂既能脱除无机硫又能脱除少量有机硫。
同时在吸收过程中会产生一些不溶性铁盐沉淀,好氧菌在DDS络合铁配体的协助下可以将这些不溶性铁盐瓦解,使之以活性铁离子的形式返回溶液中,保证溶液中各种形态铁离子的稳定存在。
DDS脱硫液在酚类物质与铁离子的共同催化下,用空气氧化再生,副产硫膏,再生DDS脱硫液循环使用。
由于DDS脱硫液进入系统后,首先会在所有设备内壁形成一层非常致密的氧化物保护膜,再者DDS脱硫液中含有较高浓度的Fe2+和Fe3+,可以有效降低单质铁被氧化成 Fe2+和Fe3+,即减缓溶液对设备的腐蚀速度,延长设备的使用寿命。
当DDS溶液和气体接触时,吸收气体中的无机硫、有机硫和二氧化碳.并转化为“富液”。
“富液”是吸收了S 、H2S和CO2的含DDS催化剂(的Na2CO3)的水溶液。
吸收反应可以简单归结如下为五类反应:(1) H2S、CO2与碱及DDS铁离子的反应。
(2) CS2、COS的水解反应。
(3) R-SH、 SH 与DDS铁离子的反应。
(4) SO2与H2S的氧化还原反应。
(5) 少量DDS铁离子在碱性溶液中的降解反应。
通常情况下,“富液”经减压和加热后,溶解于其中的CO2逸出,再通入空气,在 DDS催化剂的催化作用下,“富液”中的 S2-被氧化成S,并以泡沫形式浮出,DDS溶液得以再生,再生后的DDS溶液循环使用。
再生反应可以简单归结为如下三类反应:(1) NaHCO3与Na2CO3的转换过程(2) DDS-Fe3+氧化溶液中的S2-及HS-离子自身被还原为DDS-Fe2+,DDS-Fe2+再被空气中的氧及醌类物质氧化为DDS-Fe3+的反应。
(3) 醌氧化溶液中的S2-、HS-及DDS-Fe2+离子自身被还原为酚,酚再被氧化为醌的酚醌转换的过程。
由于在吸收和再生过程中会产生Fe(OH)3、Fe(OH)2、Fe2O3、FeO、Fe2S3和FeS等不溶性铁盐,在DDS络合铁配体的协助下,好氧菌可以将生成的不溶性铁盐瓦解,使之返回DDS脱硫液中,保证溶液中各种形态铁离子的稳定存在,增大溶液中FeCO3的含量可以减少和防止DDS 催化剂的分解。
生物降解过程的降解反应可以简单归结为如下三类反应:(1) 细菌与不溶性铁盐[氢氧化(亚)铁、碳酸(亚)铁、氧化(亚)铁、硫化(亚)铁]结合并返回到溶液中。
(2) 在DDS配体作用下瓦解不溶性铁,重新结合为DDS铁的形式。
(3) 载氧菌氧化溶液中的S2-及HS-离子。
1.3 工艺流程简介来自上一工序的煤气进入预冷塔,将煤气温度降至30~35℃进入脱硫塔,在脱硫塔填料层中与脱硫液逆流接触,煤气中的H2S被溶液吸收后进入气液分离器,气液分离后的煤气进入下一道工序。
吸收了H2S的“富液”经脱硫循环泵进入再生塔,在催化剂的作用下经空气氧化再生后,“富液”转化为“贫液”,“贫液”经贫液泵打入脱硫塔,(对于高塔再生“贫液”经液位调节器进入脱硫塔)如此循环使用。
氧化后的单质硫以泡沫的形式从再生槽中浮选出来去(压滤)熔硫。
其工艺流程图见图1。
2、DDS脱硫剂简单地说,DDS催化剂的结构,主要由“氧柱”和“铁柱”组成,两者之间的间距是8~20A°这么近的距离很容易将吸附在其表面的粒子产生静电吸附而发生化学反应,同时“铁柱”将硫化物分解的能量迅速传递,使氧化还原反应进行很快。
T101预冷塔T102脱硫塔T103脱硫塔T104再生塔 R101换热器R101换热器 R103熔硫釜 P101预冷循环泵 P102液下泵P103脱硫循环泵 P104碱泵 P105硫泡沫泵 V101反应槽V102液封槽V103地下槽 V104液封槽 V105反应槽 V106液封槽V107反应槽V108液位调节器 V109加药装置 V110空气缓冲罐V111碱液槽V112泡沫槽BK101板框压滤机图1 DDS煤气脱硫工艺流程图(高塔再生)2.1主要组分及作用DDS催化剂,DDS催化剂辅料, B型DDS催化剂辅料和活性FeCO3。
DDS催化剂: DDS铁、细菌的芽孢以及细菌生存所必需的一些物质。
催化剂辅料:多元酚类物质,细菌营养物质。
B型辅料:铁的无机、有机化合物(络合物)细菌培养基物质和活性载氧体。
活性FeCO3:分子结构比较蓬松,给催化剂提供反应空间,在辅料、B辅及好氧菌的作用下,生成一种类似DDS铁的物质。
2.2 DDS脱硫溶液DDS溶液是由DDS催化剂、DDS催化剂辅料、Na2CO3 (或氨水)和水组成。
以Na2CO3(或氨水)为碱源制备的脱硫液作为缓冲溶液,配以DDS 催化剂、DDS催化剂辅料,控制Na2CO3(或氨水)的加入量。
药品的补入,尤其是辅料的加入,不可进行大幅度的加减量,以免引起溶液成分大幅度波动,造成脱硫液成分的恶化。
提高PH值,不宜单纯依靠加碱来增加总碱度 (碱量增加造成副盐增加,对再生系统影响比较大),而应通过调节NaHC03/Na2CO3比值来控制总碱度。
尽量控制低比值,做到稀液脱硫。
DDS脱硫溶液组分的稳定对整个系统的长周期稳定运行至关重要。
因为刚开始DDS脱硫效果特别好,煤气H2S几乎检测不到或很低,往往短期内不按要求进行加药,脱硫效果也很好。
但是运行时间一长,溶液组分发生变化,脱硫效果会变差。
配料时应根据脱硫效果及H2S的变化情况对所加脱硫剂的数量给予适当的调整。
2.3加入四种药品的原因主要目的是为了降低运行费用。
由于DDS催化剂成本较高,因此价格相对也较高。
加入DDS催化剂辅料、B型DDS催化剂辅料和活性碳酸亚铁后,以DDS 催化剂作为“模板”,在亲硫性耗氧菌的作用下可生成DDS催化剂,从而减少DDS催化剂的加入量;另外,由于DDS催化剂对生存环境有严格要求,在亲硫性耗氧菌的作用下,加入DDS 催化剂辅料、B 型DDS催化剂辅料和活性碳酸亚铁后可以稳定溶液组分,给DDS催化剂的生存及保持高活性提供环境保障。
3、DDS脱硫过程中注意事项DDS脱硫技术中的一大核心技术就是生物物质—细菌,正是由于细菌的参与使得DDS脱硫技术具有生化反应的特点。
在脱硫的过程中除了无机反应和有机反应外,还存在细菌的繁殖、生长、成熟和死亡等过程。
DDS脱硫技术较之其它的脱硫方法对日常生产管理的要求更为严格,凡是能引起细菌数量减少、细菌中毒死亡和细菌疲劳的做法都是不允许的。
大量溶液损失是造成细菌数量减少的主要原因,虽然每天都补充DDS催化剂,但 DDS催化剂中只有细菌的芽孢,要使其成长为具有活性的细菌需要一定的时间,而随脱硫液损失掉的大部分细菌却是具有活性的成熟细菌。
细菌中毒或死亡的原因主要是细菌的生存环境遭到破坏。
重金属离子 (如 Co,Ni,Pb,Hg等)或其它杀菌物质的加入、操作条件的恶化等都可能引起细菌中毒甚至死亡。
因此,最好不要往脱硫液中加入其它类型的脱硫催化剂。
细菌疲劳现象的直接原因是细菌的负载能力降低而且又长时问处于超负荷工作状态,从而最终疲惫失去脱硫能力。
这时,脱硫效率会大幅度下降,整个脱硫和再生过程主要以无机或有机反应为主,生化反应基本停止。
3.1加药过程中需要注意的问题加料过程中最忌讳将DDS催化剂和活性FeCO3加热后加入脱硫液中,因为加热后会使DDS催化剂和活性FeCO3的分子结构遭到破坏。
所以,应将DDS催化剂和活性FeCO3用脱硫液混合均匀后,直接加入反应槽。
在反应槽中活化反应以后,DDS 催化剂转型稳定,活性FeCO3、DDS催化剂辅料和B型辅料形成稳定的“共同体”,此后,对DDS 脱硫液加热时,DDS催化剂和活性FeCO3就不会被破坏。
但是,DDS催化剂辅料和B型DDS催化剂辅料需要加热溶解后送入反应槽。
3.2 DDS脱硫的再生时间和溶液PH值DDS脱硫技术最关键的过程是再生过程,再生最佳停留时间为25min左右,最小停留时间也应大于10min。
溶液的PH值一般为8.2~9.0,其中最佳为8.8。
主要是在这个PH值下DDS催化剂的活性最好,脱硫效果最佳,此外在此条件下,其它辅料合成DDS催化剂的反应也比较活跃。
3.3细菌疲劳DDS脱硫技术是一种生物化学技术,在脱硫和再生过程中除了无机反应和有机反应外,还存在细菌的繁殖、生长、成熟、死亡的过程。
因此DDS脱硫技术具有明显的生物特点,细菌疲劳就是生物特性其中之一。
造成溶液生物疲劳的直接原因是细菌负载能力降低,而且又处于超负荷工作状态,从而最终疲惫失去脱硫能力。
此时脱硫效率会大幅下降,溶液中不溶性铁盐含量增大,整个脱硫和再生过程主要以无机或有机反应为主,生化反应基本停止。
造成溶液生物疲劳的根本原因有:1)溶液配制初期(转型期)没有按照操作规程加药,加药量少,或转型期操作条件控制不严格,导致形成的脱硫液负载能力低,没有打好基础。
2)正常生产过程中加药量少或不加药。
3)使用过程中长时间负荷过大,如煤气量、进口H2S严重超过设计指标。
4)再生反应不完全,溶液长时间处于欠再生状态。
5)细菌数量少,活性低。
一旦出现细菌疲劳现象仅加大催化剂投入量往往无济于事,唯一的办法是降低负荷,给细菌必要的休息时间,使之慢慢恢复活力。
因此加强日常管理,严格执行操作规程是防止细菌疲劳的最有效办法。
3.4细菌数量大量溶液损失是造成细菌减少的主要原因,虽然日常生产中每天补充催化剂,但催化剂中只有细菌芽胞,要使其成长为具有活性的细菌需一定时间,而随脱硫液损失的大部分细菌是具有活性的成熟细菌,因此日常生产中一定要避免带液和跑液现象的发生。
其次重金属离子(如Co、Ni、Pb、Hg等离子)、各种杂质或杀菌物质的加入、操作条件的恶化等都可以引起细菌中毒甚至死亡,因此最好不要往脱流液中加入其它物质,生产过程中也要避免各种杂质进入系统。