常减压装置新技术介绍
常减压装置新技术的应用
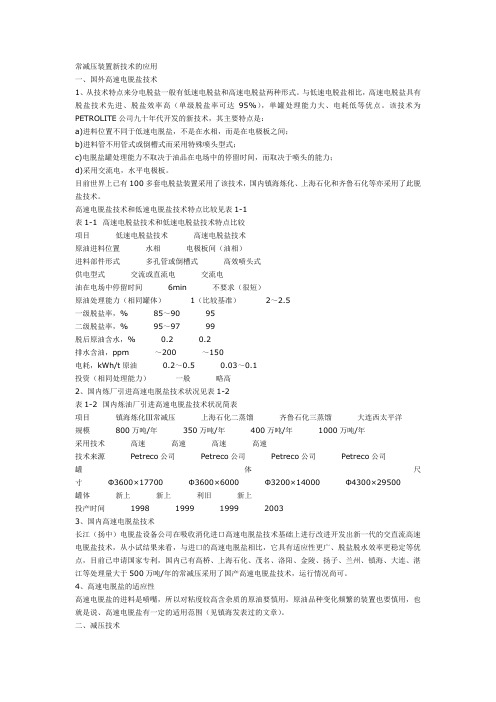
常减压装置新技术的应用一、国外高速电脱盐技术1、从技术特点来分电脱盐一般有低速电脱盐和高速电脱盐两种形式。
与低速电脱盐相比,高速电脱盐具有脱盐技术先进、脱盐效率高(单级脱盐率可达95%),单罐处理能力大、电耗低等优点。
该技术为PETROLITE公司九十年代开发的新技术,其主要特点是:a)进料位置不同于低速电脱盐,不是在水相,而是在电极板之间;b)进料管不用管式或倒槽式而采用特殊喷头型式;c)电脱盐罐处理能力不取决于油品在电场中的停留时间,而取决于喷头的能力;d)采用交流电,水平电极板。
目前世界上已有100多套电脱盐装置采用了该技术,国内镇海炼化、上海石化和齐鲁石化等亦采用了此脱盐技术。
高速电脱盐技术和低速电脱盐技术特点比较见表1-1表1-1 高速电脱盐技术和低速电脱盐技术特点比较项目低速电脱盐技术高速电脱盐技术原油进料位置水相电极板间(油相)进料部件形式多孔管或倒槽式高效喷头式供电型式交流或直流电交流电油在电场中停留时间6min 不要求(很短)原油处理能力(相同罐体)1(比较基准)2~2.5一级脱盐率,% 85~90 95二级脱盐率,% 95~97 99脱后原油含水,% 0.2 0.2排水含油,ppm ~200 ~150电耗,kWh/t原油0.2~0.5 0.03~0.1投资(相同处理能力)一般略高2、国内炼厂引进高速电脱盐技术状况见表1-2表1-2 国内炼油厂引进高速电脱盐技术状况简表项目镇海炼化Ⅲ常减压上海石化二蒸馏齐鲁石化三蒸馏大连西太平洋规模800万吨/年350万吨/年400万吨/年1000万吨/年采用技术高速高速高速高速技术来源Petreco公司Petreco公司Petreco公司Petreco公司罐体尺寸Φ3600×17700Φ3600×6000Φ3200×14000Φ4300×29500罐体新上新上利旧新上投产时间1998 1999 1999 20033、国内高速电脱盐技术长江(扬中)电脱盐设备公司在吸收消化进口高速电脱盐技术基础上进行改进开发出新一代的交直流高速电脱盐技术,从小试结果来看,与进口的高速电脱盐相比,它具有适应性更广、脱盐脱水效率更稳定等优点,目前已申请国家专利,国内已有高桥、上海石化、茂名、洛阳、金陵、扬子、兰州、镇海、大连、湛江等处理量大于500万吨/年的常减压采用了国产高速电脱盐技术,运行情况尚可。
常减压装置工艺技术和设备

节能减排
采用先进的节能技术和设 备,降低装置能耗;同时 减少污染物排放,实现绿 色生产。
设备升级改造
针对现有装置存在的问题 和不足,进行技术升级和 设备改造,提高装置处理 能力和产品质量。
03
常减压装置设备
加热炉
加热炉是常减压装置中的重要设备之 一,用于提供热能,使原油能够进行 加热和蒸馏。
加热炉的主要技术参数包括热效率、 燃料消耗和操作压力等,这些参数的 选择和优化对于提高装置效率和降低 能耗具有重要意义。
维护保养
日常保养
定期检查设备运行状态,清洁设备表面,紧固松 动部件。
定期保养
根据设备使用情况和厂家建议,进行全面的检查 、清洗、润滑和调整。
维修计划
制定维修计划,对易损件进行定期更换,对故障 设备进行修复或更换。
故障处理
01
故障识别
通过监测和检查,及时发现设备 异常现象,判断故障类型和原因 。
紧急处理
历史与发展
起源
发展趋势
常减压装置起源于20世纪初,随着石 油工业的发展而逐步完善。
未来,常减压装置将朝着提高油品质 量、降低能耗和减少污染物排放的方 向发展,同时加强与其他石油炼化工 艺的集成和优化。
技术进步
近年来,随着环保要求的提高和能源 消耗的降低,常减压装置的技术不断 进步,出现了许多新型的工艺技术和 设备。
02
03
修复与预防
对于突发故障,采取紧急措施防 止事故扩大,保障人员和设备安 全。
对故障设备进行修复或更换,分 析故障原因,采取预防措施避免 类似故障再次发生。
05
常减压装置安全与环保
安全措施
操作规程
制定和执行严格的操作规程, 确保装置在安全条件下运行。
炼油厂常减压装置节能新技术措施分析
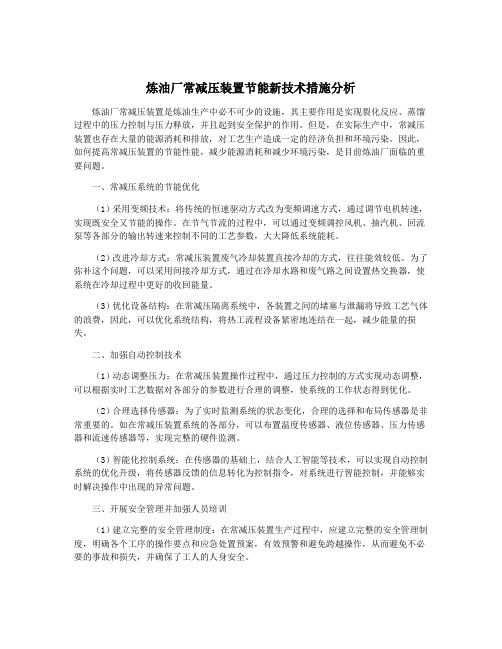
炼油厂常减压装置节能新技术措施分析炼油厂常减压装置是炼油生产中必不可少的设施,其主要作用是实现裂化反应、蒸馏过程中的压力控制与压力释放,并且起到安全保护的作用。
但是,在实际生产中,常减压装置也存在大量的能源消耗和排放,对工艺生产造成一定的经济负担和环境污染。
因此,如何提高常减压装置的节能性能,减少能源消耗和减少环境污染,是目前炼油厂面临的重要问题。
一、常减压系统的节能优化(1)采用变频技术:将传统的恒速驱动方式改为变频调速方式,通过调节电机转速,实现既安全又节能的操作。
在节气节流的过程中,可以通过变频调控风机、抽汽机、回流泵等各部分的输出转速来控制不同的工艺参数,大大降低系统能耗。
(2)改进冷却方式:常减压装置废气冷却装置直接冷却的方式,往往能效较低。
为了弥补这个问题,可以采用间接冷却方式,通过在冷却水路和废气路之间设置热交换器,使系统在冷却过程中更好的收回能量。
(3)优化设备结构:在常减压隔离系统中,各装置之间的堵塞与泄漏将导致工艺气体的浪费,因此,可以优化系统结构,将热工流程设备紧密地连结在一起,减少能量的损失。
二、加强自动控制技术(1)动态调整压力:在常减压装置操作过程中,通过压力控制的方式实现动态调整,可以根据实时工艺数据对各部分的参数进行合理的调整,使系统的工作状态得到优化。
(2)合理选择传感器:为了实时监测系统的状态变化,合理的选择和布局传感器是非常重要的。
如在常减压装置系统的各部分,可以布置温度传感器、液位传感器、压力传感器和流速传感器等,实现完整的硬件监测。
(3)智能化控制系统:在传感器的基础上,结合人工智能等技术,可以实现自动控制系统的优化升级,将传感器反馈的信息转化为控制指令,对系统进行智能控制,并能够实时解决操作中出现的异常问题。
三、开展安全管理并加强人员培训(1)建立完整的安全管理制度:在常减压装置生产过程中,应建立完整的安全管理制度,明确各个工序的操作要点和应急处置预案,有效预警和避免跨越操作,从而避免不必要的事故和损失,并确保了工人的人身安全。
炼油厂常减压装置节能新技术措施分析

炼油厂常减压装置节能新技术措施分析炼油厂常减压装置是常见的管路减压装置之一,其主要作用是在高压管路上降低压力,从而保证设备的安全运行。
为了进一步提高炼油厂的节能效果,新技术措施被引入到常减压装置的设计和应用中。
首先,节能措施实现的第一步是优化常减压装置的结构。
新技术方案可以通过改进常减压装置的结构,将不必要的压力丢失降到最低。
例如,在设计和制造过程中优化了喷嘴和叶片的设计和加工方式,从而减少了水流冲程和风量,降低了能耗和运行噪音,同时还提高了装置的稳定性和可靠性。
其次,新技术可通过利用重力势能实现常减压装置的能量回收。
通过在常减压装置的出口处安装涡轮,以收集燃料的剩余能量,将其转换为可再生能源进行回收,从而实现能量的再循环利用。
变压器也可以帮助降低随机干扰因素的存在,使每个输出恒定,从而提高整个系统的可靠性和稳定性。
第三,我们可以利用现代化的自动控制技术来优化常减压装置的操作和维护,确保能源和成本的最优化。
通过安装传感器和自动化监测器,可以实时监控流量、压力等运行数据,并将此数据传回集中控制系统以进行实时监控。
这可以确保常减压装置的稳定运行,并及时发现任何异常或故障。
同时,通过控制系统中的反馈机制,可以根据实时监测数据自动调整操作参数,优化装置的运行效率。
最后,我们还可以使用新技术来减少对燃料的依赖,从而实现燃料的节约和使用的可持续性。
例如,通过采用尽可能高效的燃烧方式和燃烧后的废气处理,可以最大限度地减少有害气体和颗粒物的排放,减少对自然资源的消耗。
同时,使用可再生能源,如太阳能和风能,也有助于减少燃料消耗和碳足迹。
综上所述,通过使用先进的技术手段,常减压装置节能成为一个可行的可持续方案。
通过减少能源消耗,实现能源回收和再利用,并利用自动化控制技术优化运行效率,可以确保炼油厂的可持续生产和环境可持续性。
炼油厂常减压装置节能新技术措施分析

炼油厂常减压装置节能新技术措施分析炼油厂是石油加工行业的重要组成部分,常减压装置是炼油厂中的核心设备之一。
随着能源消耗和环保问题日益受到关注,炼油厂常减压装置的节能技术也变得尤为重要。
本文将就炼油厂常减压装置节能新技术措施进行详细的分析,以期为炼油厂的节能降耗工作提供参考和借鉴。
一、炼油厂常减压装置的节能问题炼油厂中的常减压装置是用于将高压气体减压至低压,并分离出液体成分的装置。
在这一过程中,常减压装置需要消耗大量的能源,尤其是在高压气体减压的过程中,会产生大量的余热。
如何有效利用这些余热,提高能源利用率,成为了炼油厂常减压装置需要解决的节能问题。
二、常减压装置节能新技术措施1. 余热回收技术在常减压装置的使用过程中,会产生大量的余热,传统做法是将这些余热散发到环境中。
而通过余热回收技术,可以将这些余热有效地回收利用,用于加热水或者预热原料等环节,从而减少能源消耗。
现在市场上已经出现了许多余热回收设备,如热交换器、蒸汽再生装置等,可以帮助炼油厂进行余热回收,提高能源利用效率。
2. 热风循环技术炼油厂常减压装置的加热过程需要大量的热风,传统做法是直接排放到大气中,造成能源的浪费。
而采用热风循环技术,可以将已经加热过的热风再利用,从而减少能源消耗。
这种技术需要依靠一定的回收设备和系统,可以有效地提高能源利用率,减少能源消耗。
3. 高效节能设备高效节能设备的使用是节能技术的重要组成部分。
采用高效的温度控制装置、节能换热器等设备,可以在不影响设备正常运行的前提下,减少能源消耗。
目前,市场上已经有很多高效节能设备可供选择,炼油厂可以根据自身的情况选择合适的设备,提高设备的能源利用效率。
4. 远程监控和智能化控制技术通过远程监控和智能化控制技术,可以对炼油厂的常减压装置进行实时监测和控制,从而提高设备的运行效率,降低能源消耗。
智能化控制技术可以通过精准的控制和调节,降低设备运行的能源消耗。
远程监控技术可以让工作人员对设备的运行情况进行实时监测,及时发现问题并加以处理,提高设备的稳定运行和节能效果。
炼油常减压装置特点及节能新技术

炼油常减压装置特点及节能新技术摘要:常减压装置能够回收余热、降低过剩空气系数,本文对如何控制常减压装置的能耗展开研究,分析常减压装置的特性,然后分析当前可以采取的技术措施。
通过研究帮助工厂解决常减压装置的运行能耗问题,提升综合效益。
关键词:常减压装置;特点;技术;应用引言:现代炼油厂为了保证工作的顺利进行,会使用常减压装置开展工作。
但是常减压装置同样有耗能较大的问题,为了保证生产的顺利进行,需要使用有效的技术,控制常减压装置的能耗。
1炼油常减压装置特性分析1.1加强烟气余热回收使用常减压装置能够回收炼油厂的烟气余热,常减压装置的余热回收系统会包括高温段空气预热器、低温段空气预热器两种装置,在高温段使用了高效的导热元件是,低温段使用双向板翅预热器[1]。
通过使用这些装置,常减压装置能够有效控制烟气余热所导致的露点腐蚀问题,控制烟气温度在130℃的安全范围以内。
通过使用常减压装置,其中的余热回收系统可以有效利用炼油系统的余热,解决温度浪费问题,并降低炼油系统的能耗临。
目前一般使用冷凝技术进行烟气的低温余热回收,可以有效提升热炉的热反应效率。
1.2减少过剩空气炼油厂工作中,如果剩余的空气系数比较小,加热炉内部的燃烧就会缺少足够的空气,很难满足加热炼油的要求,不仅会造成工作效率降低,还会释放出比较多的废物,对环境造成比较严重的损害。
但是如果盲目提升空气系数,过剩的空气就会将炉内多余的热量带走,同样会导致炼油设备热强度不能达标的问题,还会严重影响系统的热传递效率,也会缩短锅炉的使用寿命,以及造成空气污染。
为了解决上述问题,在目前的炼油工作中会使用常减压设备将空气系数控制在合理的范围内。
工作人员在点燃火嘴含氧量会比较高,常减压设备也会同时对气压进行调节,让设备的火焰能始终处于燃烧的状态下,并保证锅炉温度保持正常,工作人员通过随时控制常减压设备可以进行工作方式的调节,让炉内的空气系数保持最佳的运行状态。
1.3能源消耗大在目前的炼油厂生产中,常减压设备的装置会占据比较大的能源消耗,普遍超过了30%,在很多炼油厂重,常减压设备已经成为了最为主要的生产成本要素。
炼油厂常减压装置节能新技术措施分析

炼油厂常减压装置节能新技术措施分析炼油厂常减压装置通常用于将高压油气逐级减压到低压状态,以满足生产过程中不同工艺环节的需要。
常减压系统的节能是炼油厂实现节约能源和减少污染物排放的一项重要任务。
以下是炼油厂常减压装置节能新技术措施分析。
1. 减少阀门误差在常减压系统中,阀门是一个关键组成部分。
为减少能源浪费和功率损失,应对阀门进行耐用性和精度的检查。
如果阀门开度超过额定值,减压损失会增加,对整个系统的能源效率影响很大。
因此,优化常减压系统的阀门管理可以提高设备的可靠性和减少能源浪费。
2. 使用先进的减压装置在炼油厂常减压装置中,使用高效的先进减压装置可以大量减少能源的消耗。
例如,采用气体液体增压装置将高压气体转化为高压液体,再通过进入容器自然膨胀来实现自发减压。
这种方法可最大限度地降低能耗,从而有效地提高设施的能效。
3. 应用计算机辅助设计可以使用计算机辅助设计来优化炼油厂常减压装置的设计和操作,以最大程度地提高其节能效率。
通过计算机模拟和仿真,可以提前发现常减压系统中可能存在的问题,及时进行调整。
同时,可以利用计算机技术提高生产过程的自动化程度,并优化设备的维护和运营。
这些措施都可以提高能源的效率,减少污染物的产生。
4. 合理利用余热在炼油厂中,余热回收是一项非常有利的节能措施。
通过在常减压系统中收集和再利用余热,可以显著降低设备的能源消耗和运营成本。
例如,可以将冷凝水回收,用于减少冷却水的消耗。
另外,也可以利用蒸汽余热,提高设备的产能和运行效率。
这些方法都可以有效地提高能源利用效率,并减少环境污染。
综上所述,常减压系统节能新技术措施分析可得出,通过优化阀门管理、使用先进装置、应用计算机辅助设计、合理利用余热等措施,可以有效地提高炼油厂常减压装置的能效,减少能源浪费和污染物排放,从而降低企业成本,提高经济效益和社会效益。
炼油常减压装置中减压塔技术优化范本(2篇)
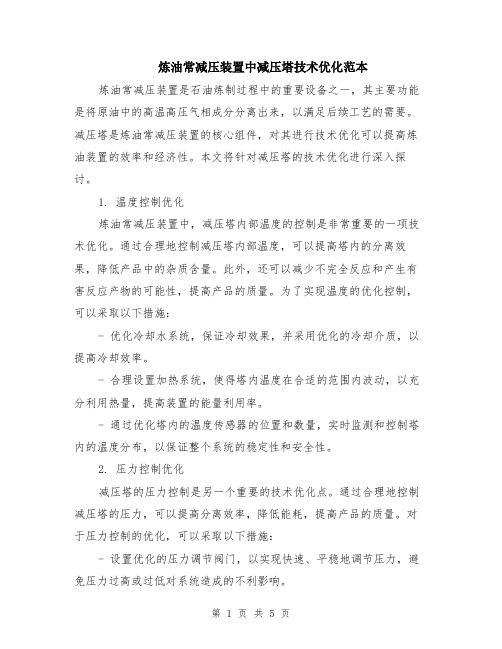
炼油常减压装置中减压塔技术优化范本炼油常减压装置是石油炼制过程中的重要设备之一,其主要功能是将原油中的高温高压气相成分分离出来,以满足后续工艺的需要。
减压塔是炼油常减压装置的核心组件,对其进行技术优化可以提高炼油装置的效率和经济性。
本文将针对减压塔的技术优化进行深入探讨。
1. 温度控制优化炼油常减压装置中,减压塔内部温度的控制是非常重要的一项技术优化。
通过合理地控制减压塔内部温度,可以提高塔内的分离效果,降低产品中的杂质含量。
此外,还可以减少不完全反应和产生有害反应产物的可能性,提高产品的质量。
为了实现温度的优化控制,可以采取以下措施:- 优化冷却水系统,保证冷却效果,并采用优化的冷却介质,以提高冷却效率。
- 合理设置加热系统,使得塔内温度在合适的范围内波动,以充分利用热量,提高装置的能量利用率。
- 通过优化塔内的温度传感器的位置和数量,实时监测和控制塔内的温度分布,以保证整个系统的稳定性和安全性。
2. 压力控制优化减压塔的压力控制是另一个重要的技术优化点。
通过合理地控制减压塔的压力,可以提高分离效率,降低能耗,提高产品的质量。
对于压力控制的优化,可以采取以下措施:- 设置优化的压力调节阀门,以实现快速、平稳地调节压力,避免压力过高或过低对系统造成的不利影响。
- 通过设置合理的压力传感器和控制系统,实时监测和控制减压塔内的压力,以保证整个系统的稳定性和安全性。
- 利用模拟仿真方法,对减压塔的压力控制进行优化,找到最佳的压力控制策略,并对系统进行调优。
3. 流体动力学优化炼油常减压装置中的减压塔是一个典型的多相流动系统,其流体动力学行为对系统的稳定性和分离效率有着重要影响。
对减压塔的流体动力学进行优化,可以提高减压塔的性能。
以下是一些流体动力学优化的措施:- 优化静态混合分离器的设计,使气液两相在分离器内充分混合,以提高分离效果。
- 通过合理设置横隔板、直隔板和填料层,优化塔内的流动分布,减小气液的相互干扰,提高分离效率。
炼油厂常减压装置节能新技术措施分析

炼油厂常减压装置节能新技术措施分析石油炼制工艺中,常减压装置是一个非常重要的环节。
它主要用于将原油中的各种烃类分离出来,通过降低管道中的压力来使原油蒸发,从而实现烃类的分离。
在常减压装置的运行中,能源消耗是一个非常重要的问题,因此寻找并应用节能的新技术措施非常有必要。
一、热能回收利用技术炼油过程中,常减压装置中产生了大量的废热。
传统上,这些废热会直接排放到大气中。
为了更好地节能减排,可以采用热能回收利用技术,将这些废热进行回收利用。
具体的方法有两种:1.余热回收:常减压装置中产生的废热可以用于加热其他生产环节所需的介质。
可以将废热用于加热炼油厂内的其他装置,或者用于加热其他生产过程中需要的水,从而达到节能的目的。
2.发电回收:常减压装置中的废热可以用于发电。
通过将废热转化为蒸汽,再通过蒸汽发电机转化为电能,从而实现能量的回收利用。
二、节能控制技术常减压装置的节能措施还可以从控制方面入手。
通过合理的控制装置的运行,可以达到节能减排的目的。
具体措施如下:1.优化操作参数:通过对装置的操作参数进行优化调整,可以减少能耗,提高经济效益。
控制蒸汽的流量和压力,控制再沸器的进出口温度等。
2.自动化控制:引入自动化控制系统,实现对常减压装置的自动化控制和监测,可以降低人工干预的程度,减少能源的浪费。
三、改进设备结构和设计常减压装置的结构和设计也可以进行改进,从而达到节能的目的。
具体改进措施如下:1.改进节流装置:优化节流装置的结构参数和材料选择,减小阻力,降低能耗。
2.改善换热器传热效果:通过改进换热器的结构和设计,提高传热效率,降低能量损耗。
3.优化常减压装置的结构:通过优化常减压装置的结构,减小内部压力损失,降低能源的消耗。
炼油厂常减压装置的节能新技术主要包括热能回收利用技术、节能控制技术和改进设备结构和设计。
通过应用这些新技术措施,可以有效地降低能源消耗,提高能源利用效率,达到节能减排的目的。
常减压装置先进控制关键技术分析

常减压装置先进控制关键技术分析摘要]:常减压装置在原油加工处于首要位置,同时在其过程中也是加工规模最大的工艺装置。
自动化技术在石油化工企业生产过程应用越来越广泛,先进控制已成为石油化工企业提高产品质量和扩大生产的重要手段。
本文在分析了常减压装置的控制方案相关技术,介绍鲁棒多变量预估控制原理,并研究了常压塔控制器的功能设计。
中国论文网 h[关键词]:炼油厂,常减压装置,先进控制,结束改革目前,石油化工企业对市场和生产环境的变化都表现出十分敏感的特性,以期获得最大的经济效益。
世界各国的经验表明,先进控制技术是提高企业的经济效益、降低生产成本、提高其在国际市场中的创新力、应变力、适应力和综合竞争力的主要技术手段之一。
常减压装置的主要任务是将原油分离成合格的产品或中间产品,是原油加工中重要的组成部分。
本文就炼油厂中的常减压装置的先进控制技术的一些关键技术进行分析。
1常减压装置的工艺简介常减压装置是炼油厂进行原油提炼的第一道工序,它的作用是从原油中提炼出各种燃料、润滑油、化工原料等产品。
其基本原理主要是利用加热、分馏等物理方法分割不同沸点范围的汽油,柴油、溶剂油、航空煤油和重油等二次加工原料和产品。
其特点是加工方法简单、成本低。
因此,在保证产品质量的前提下,其一次拔出率的高低将直接影响到炼油厂的整体经济效益。
常减压装置主要由原油电脱盐系统、原油换热系统、原油精馏系统和产品冷凝、冷却系统等几部分组成,其核心为原油精馏系统。
生产上利用原油中各组分的沸点不同,将原油加热到一定温度,送入常压精馏塔,在塔的进料段进行一次汽化。
汽化后,气相部分上升至塔的精馏段,液相部分下降至塔的提馏段,是此装置工艺原理。
2常减压装置先进控制关键技术分析2.1常减压装置的控制方案常减压装置控制系统的应用目的是平稳工艺操作,保证产品产量和质量。
要达到此目的就必须保证装置的物料、气液相和热量的三大平衡。
(1)常规控制方案常规控制方案是在经典控制理论的基础上形成的,在实际生产过程中,一般的常规控制回路主要由测量单元、以PID为基础建立的常规调节器、调节阀、检测元件和工艺对象等几部分组成。
炼油厂常减压装置节能新技术措施分析

炼油厂常减压装置节能新技术措施分析炼油厂常减压装置是炼油过程中的重要设备,用于将高压煤气减压到适宜的压力,使其能够进一步处理或储存。
在常减压装置的运行过程中,能源的消耗是不可避免的。
近年来,随着节能减排的要求日益提高,炼油厂常减压装置的节能措施也得到了广泛关注。
本文将分析一些常见的节能技术措施。
1. 建立管道网络能量回收系统:炼油厂常减压装置常常会产生大量的高温高压煤气,在其减压过程中释放出的压力能够被利用,通过建立管道网络能量回收系统来回收这部分能量。
通过适当地安装换热器或利用工艺热能来加热水等方式,将这些煤气的能量回收利用,提高能源利用效率,降低能源消耗。
2. 优化工艺参数:通过对常减压装置的工艺参数进行优化,可以有效地减少能源的消耗。
调整减压装置的进气温度和压力,使其达到最佳操作状态,并降低不必要的能量损失。
还可以通过合理设计常减压装置的结构,减少压力降低过程中的能量损耗。
通过使用先进的机械设备和控制系统,可以实现常减压装置的节能效果。
3. 安装尾气回收装置:常减压装置在减压过程中会产生大量的尾气,其中包含可燃物质。
通过安装尾气回收装置,可以将这些可燃物质进行回收利用,降低能源消耗。
可以将尾气通过分离技术将其中的烃类气体分离出来,用于其他工艺或燃料。
4. 优化设备运行方式:通过优化常减压装置的运行方式,降低能源消耗。
可以通过合理安排装置的运行周期和设定操作参数,减少设备的空载运行时间,减少能源的浪费。
还可以根据实际生产情况,调整设备的启停次数和运行负荷,提高设备的能效。
5. 定期维护和检修:保证常减压装置的正常运行状态,对设备进行定期维护和检修,及时清洗和更换损坏部件,确保设备的高效运行。
定期的维护和检修可以有效地减少设备的故障和停机时间,降低能源的浪费。
炼油厂常减压装置的节能技术措施是提高能源利用效率和降低能源消耗的关键。
通过合理的工艺和设备优化、安装能量回收系统和尾气回收装置、优化设备运行方式以及定期维护和检修等措施,可以有效地降低能源消耗,提高能源利用效率,实现炼油厂的可持续发展。
2024年炼油常减压装置中减压塔技术优化

2024年炼油常减压装置中减压塔技术优化减压塔是炼油常用的一种设备,用于降低石油产品中的压力和温度,将过热蒸汽或气体转化为液体。
随着炼油工艺的不断发展和炼油设备的不断升级,减压塔的技术也需要不断优化,以提高效率、降低能耗和减少对环境的影响。
2024年炼油常减压装置中减压塔技术优化主要包括以下几个方面:材料选择、结构设计、流动动力学分析、操作参数优化、节能降耗与环保措施等。
一、材料选择减压塔材料的选择直接影响到其使用寿命和安全性能。
2024年,炼油常减压装置中的减压塔可以采用更先进的高强度、高温抗腐蚀材料,如高温合金、镍基合金等。
这些材料具有良好的抗腐蚀性能和高温稳定性,可以有效延长减压塔的使用寿命,并提高设备的安全性。
二、结构设计减压塔的结构设计要考虑到流体动力学和传热性能等因素。
优化的设计可以提高减压塔的传质传热效率,并降低能耗。
结构设计需要考虑到流体的流动状态、流速和压降等参数,通过合理的结构设计可以减小流体的阻力和压降,提高减压塔的流动动力学性能。
三、流动动力学分析流动动力学分析是减压塔优化设计的关键环节。
减压塔内流体的流动状态对传质传热效率和能耗有着直接影响。
可以通过数值模拟等方法,研究减压塔内流体的流动规律,优化设计减压塔的内部结构和分布组件等,改善流体的分布和流动状态,提高传热效率,降低能耗。
四、操作参数优化优化减压塔的操作参数,可以提高减压塔的工艺效率和能源利用率。
操作参数优化主要包括进料压力、温度、流速等参数的优化。
合理的操作参数可以提高减压塔的转化率和产品质量,降低能耗和生产成本。
通过优化操作参数,可以实现能耗和产量的双重优化。
五、节能降耗与环保措施炼油常减压装置中减压塔的技术优化还需要考虑到节能降耗和环保问题。
可以采用一些节能措施,如余热回收、换热器优化设计等,降低能耗。
同时,还可以采用一些环保措施,如废气处理、废水处理等,减少对环境的影响。
技术优化的目标是在提高效率的同时,降低能耗和对环境的影响。
炼油常减压装置特点及节能新技术
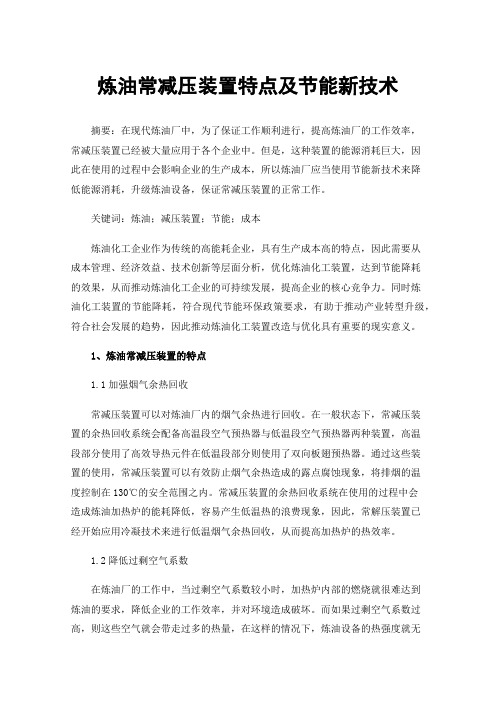
炼油常减压装置特点及节能新技术摘要:在现代炼油厂中,为了保证工作顺利进行,提高炼油厂的工作效率,常减压装置已经被大量应用于各个企业中。
但是,这种装置的能源消耗巨大,因此在使用的过程中会影响企业的生产成本,所以炼油厂应当使用节能新技术来降低能源消耗,升级炼油设备,保证常减压装置的正常工作。
关键词:炼油;减压装置;节能;成本炼油化工企业作为传统的高能耗企业,具有生产成本高的特点,因此需要从成本管理、经济效益、技术创新等层面分析,优化炼油化工装置,达到节能降耗的效果,从而推动炼油化工企业的可持续发展,提高企业的核心竞争力。
同时炼油化工装置的节能降耗,符合现代节能环保政策要求,有助于推动产业转型升级,符合社会发展的趋势,因此推动炼油化工装置改造与优化具有重要的现实意义。
1、炼油常减压装置的特点1.1加强烟气余热回收常减压装置可以对炼油厂内的烟气余热进行回收。
在一般状态下,常减压装置的余热回收系统会配备高温段空气预热器与低温段空气预热器两种装置,高温段部分使用了高效导热元件在低温段部分则使用了双向板翅预热器。
通过这些装置的使用,常减压装置可以有效防止烟气余热造成的露点腐蚀现象,将排烟的温度控制在130℃的安全范围之内。
常减压装置的余热回收系统在使用的过程中会造成炼油加热炉的能耗降低,容易产生低温热的浪费现象,因此,常解压装置已经开始应用冷凝技术来进行低温烟气余热回收,从而提高加热炉的热效率。
1.2降低过剩空气系数在炼油厂的工作中,当过剩空气系数较小时,加热炉内部的燃烧就很难达到炼油的要求,降低企业的工作效率,并对环境造成破坏。
而如果过剩空气系数过高,则这些空气就会带走过多的热量,在这样的情况下,炼油设备的热强度就无法达标,影响传热效率,并且容易缩短炉管的使用寿命,并污染空气。
在炼油厂的实际工作中,常减压设备的使用可以降低过剩空气系数,使空气系数控制在规定范围之内。
工作人员在点燃火嘴时含氧量会提高,而常减压设备则会进行适当调节气压,使设备中的火焰即保持在始终燃烧的状态,又能保证炉温的正常,工作人员通过随时操控常减压设备进行调节工作,可以使空气系数始终保持在最佳状态。
炼油厂常减压装置节能新技术措施分析

炼油厂常减压装置节能新技术措施分析炼油厂常减压装置是炼油过程中重要的装置之一,它主要用于将高温高压的油气降压并冷却,以保证炼油过程的安全性和稳定性。
常减压装置的运行消耗大量的能源,造成能源浪费和环境污染,因此需要采取节能措施来降低能源消耗。
1. 优化常减压装置的结构:通过改变常减压装置的结构设计,减少局部压降,提高设备的能效。
可以采用多级联合减压的形式,将原来的单级减压改为多级减压,减少单级减压过程中的能量损失。
2. 提高常减压装置的传热效率:常减压装置中的传热过程是能源消耗的重要环节。
可以采用增加传热面积的方法,如增加传热管束数量或采用表面增强传热技术,提高传热效率,减少能源消耗。
3. 优化常减压装置的操作方式:通过优化常减压装置的操作方式,减少能源的消耗。
可以采用变压降操作策略,根据炼油过程中油气的压力变化,调整减压装置的压降,以最低的能量消耗实现安全的减压。
4. 应用先进的控制技术:采用现代化的控制系统和自动化技术,实现常减压装置的精细化控制和优化操作。
通过精确控制常减压装置的压力、温度等参数,提高设备的运行效率,减少能源浪费。
5. 温度回收利用技术:常减压装置中的冷凝器常常需要大量的冷却水,造成能源的浪费。
可以采用温度回收利用技术,将冷凝器排出的高温水回收利用,用于其他工艺环节或生活热水供应,减少能源消耗。
6. 应用节能设备和材料:选择高效节能的设备和材料,如高效换热器、高效节能电机等,减少能源的消耗,提高设备的能效。
在炼油厂常减压装置的节能措施分析中,可以从结构优化、传热效率提高、操作方式优化、控制技术应用、温度回收利用技术以及应用节能设备和材料等多个方面入手,共同促进常减压装置的节能改造,降低能源消耗,提高炼油过程的能效。
常减压装置工艺技术和设备
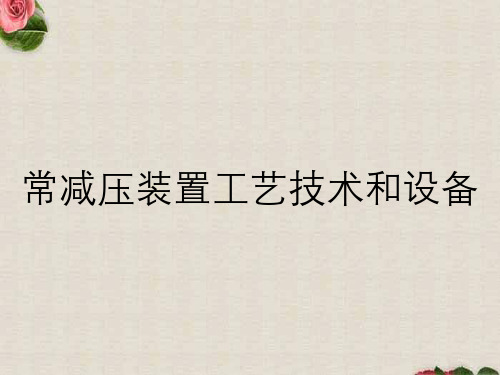
恩氏蒸馏:
IP
常顶~常三
线、
减一
线为
5%
ASTM D86 (V)
减二、三 线、
洗涤油、 减压
10% 30% 50%
渣油为
70%
ASTM D11 60 (V)
90%
95%
EP
石脑油 0.75 11.66 -19.5
14.9 22.7 87 108.7 117.9
139.5 149.6 157
常一 线油 0.7989 11.77 140
三、原料和产品
2、原油的馏分组成 原油是由各种类型的烃类和非烃类化合物所组成的复
杂混合物,其分子量从几十到几千,因而其沸点范围 也很宽,从常温到500℃以上。在对原油进行研究和加 工利用之前,要采用分馏的方法将其按沸点的高低分 割成若干部分(即馏分),每个馏分的沸点范围简称 为馏程或沸程。 馏分并不代表石油产品,只是从沸程上看有可能作为 生产汽油、煤油、柴油、润滑油的原料,它们往往需 要经过适当加工才能生产出符合相应的质量规格要求 的产品。
另外,初常顶气经过轻烃回收吸收、稳定、脱硫后还 可以生产液化石油气或者直接作为乙烯裂解气体炉原 料。
常减压装置工艺技术和设备
三、原料和产品
产品名称
技术指标
常顶油
ASTM D86 EP≯170℃
常一线
ASTM D86 EP≯280℃
比重(20℃), 0.775~0.830
冰点
≯- 47℃
常二线
不控制
350~500℃ 26.0 27.5 29.9 23.2 28.9 21.2 35.4 24.8 24.6 28.0
国内外几种常减压原油的8 47.4 33.5 32.3 29.7 65.6 40.3 33.1 24.8 56.0
炼油厂常减压装置节能新技术措施分析

炼油厂常减压装置节能新技术措施分析随着人们对环保意识的增强与能源需求的不断增长,炼油厂面临着更加严峻的限制和挑战。
炼油厂常减压装置是炼油生产过程中不可或缺的组成部分,其能够将高温高压的气体或液体通过降压降温方式进行减压处理,并回收可再利用的能源,达到节能减排的目的。
如何在炼油厂常减压装置中实现节能减排,已经成为了炼油厂技术优化与环保提升的重要研究方向。
1.换热器技术在炼油厂常减压装置的流程中,高温高压气体或液体需要进行降温降压处理,此时通过换热器技术对流体进行处理可以实现节能效果。
通过热交换技术,节约能源的同时,还可以回收处理过后的流体,以保证对环境的影响尽量降至最低。
因此,炼油厂常减压装置中采用高效换热器进行换热处理,是一种节约能源的有效方式。
2.调节阀技术调节阀技术是一种在炼油厂常减压装置中广泛应用的技术。
该技术可以通过使用自动化调节阀来实现流体在管道中的精准控制,避免因管道压力过高而导致流体泄漏、损耗等问题,并最大化地减少材料消耗,降低生产成本。
同时,这种技术还可以通过对流体流量的控制来调节压力和温度,以达到最佳处理效果。
3.节流装置技术针对传统炼油常减压装置中温降和能量回收的问题,节流装置技术可以通过对流体进行节流控制和细部调节,实现能量高效回收和降温处理,避免了传统装置中能量的低效利用和浪费现象。
同时,该技术还可以大幅度减少计算误差和排放污染物的风险,减小对人类健康和环境的危害。
二、常减压装置节能效果与优势常减压装置的节能效果是显著的。
在实际生产过程中,高端节能设备采用换热器、调节阀和节流装置等新技术,并完善控制设备,不仅有助于提高生产效率,并且还能充分回收能源,避免能源流失、物质浪费。
它的节能优势主要包括以下方面:1.可回收的能源,实现节约使用;2.流体的回收再利用,减少污染物排放;3.优化布局设计,降低压缩机运行压力;4.提高加热器、换热器的使用效率,达到高效节能效果。
在今后的工业发展过程中,常减压装置的可持续性发展将成为关注的重点。
常减压蒸馏新技术阐述

常减压蒸馏新技术阐述常压蒸馏和减压蒸馏习惯上合称常减压蒸馏,常减压蒸馏基本属物理过程,主要包括原油脱盐脱水、常压蒸馏、减压蒸馏三个环节。
常减压蒸馏技术是石油生产过程中必不可少的一道工序,但是随着石油开采种类的不断增加以及设备使用年限的不断增加,常减压蒸馏装置可能会出现不同程度的腐蚀问题,这不仅会降低石油提炼的效率,也容易引起不同程度的安全事故。
为了从根本上杜绝这种问题,就一定要防止常减压蒸馏设备发生腐蚀现象,为石油提炼工作提供安全保障。
1 常减压蒸馏装置发生腐蚀的主要原因原油的主要组成元素为碳、氢、硫、氮、氧。
含碳量为83.0%~87.0%;氢含量为11.0%~14.0%;硫含量为0.05%~8.0%,氧含量为0.05%~2.0%,氮含量为0.02%~2.0%。
虽然硫、氮、氧等元素的含量较低,但是仍具有较强的腐蚀作用。
经验表明,导致常减压蒸馏装置出现腐蚀现象的原因主要包括两方面:第一,在常压塔顶位置、减压塔顶位置,这些部位存在冷凝系统,也包括一部分挥发线,因此此部位的温度一般比较低,在提炼石油的过程中,原油中存在一定的氯盐、硫化物等,这些物质受热之后会成为硫化氢以及氯化氢,此时经过低温部位就会冷凝成为稀盐酸,因此发生腐蚀的可能性比较高。
第二,常减压蒸馏装置的高温位置也是腐蚀问题的高发位置,在高温的作用下,原油中的硫化氢以及其他类型的硫化物质与金属的反应更加强烈,比较明显的是有高温部位的环烷酸腐蚀。
一般以原油的酸值判断环烷酸的含量,原油的酸值大于0.5mgKOH/g时,就能引起设备的腐蚀,酸值大于1.0mgKOH/g为高酸值原油。
环烷酸的腐蚀能力和温度关系密切,220℃以下,环烷酸基本不发生腐蚀,以后随温度的升高而增加,270℃~280℃达到酸沸点,腐蚀最为强烈,温度再升高腐蚀速率下降;温度达到350℃~400℃时,由于FeS膜高温融解,腐蚀重新加剧;400℃以上石油酸分解,腐蚀减弱,基本没有腐蚀。
炼油厂常减压装置节能新技术措施分析

炼油厂常减压装置节能新技术措施分析炼油厂常减压装置是石油化工生产中的重要设备,用于对裂化汽油、重油等石油产品进行降压处理,以满足生产和加工的需要。
在炼油厂常减压装置的操作过程中,能耗问题一直是一个亟待解决的难题,炼油厂常减压装置的节能新技术措施显得十分重要。
本文将对炼油厂常减压装置的节能新技术措施进行深入分析,以期为炼油厂的节能工作提供有益的参考。
一、加强装置的热力系统优化在炼油厂常减压装置的运行过程中,热力系统是一个非常重要的方面。
热力系统的效率直接关系到能源的利用程度,加强装置的热力系统优化是一个非常重要的节能技术措施。
在优化热力系统方面,可以采取以下措施:1. 合理设计热力系统结构合理设计热力系统的结构,包括进料、出料、介质循环等部分,以确保热能传递的高效率和稳定性。
2. 优化换热设备优化换热设备的设计和工艺,采用高效、节能的换热器,提高换热效率,减少能源损耗。
3. 提高热力系统的控制精度提高热力系统的控制精度,采用先进的自动控制技术,实现热力系统的智能化运行,减少人为干预,提高能源利用效率。
二、采用先进的节能设备在炼油厂常减压装置的操作过程中,各种设备都会消耗大量的能源,采用先进的节能设备是一个非常重要的节能新技术措施。
在采用先进的节能设备方面,可以从以下几个方面进行改进:1. 采用高效的压缩机采用高效的压缩机设备,能够有效地提高设备的压缩效率,减少能源损耗。
1. 优化操作参数通过优化操作参数,调整装置的运行方式,提高系统的整体效率,减少能源损耗。
2. 改进产品分离工艺改进炼油厂常减压装置的产品分离工艺,提高产品的分离效率,减少能源消耗。
3. 加强系统的监控与管理加强系统的监控与管理,实施全面的巡检和检修,及时发现并解决设备运行中存在的问题,确保系统的稳定运行。
四、提高员工的技术水平1. 开展技术培训开展特色化的技术培训,提高员工的技术水平,使其能够更好地掌握先进的节能技术知识和应用技能。
炼油厂常减压装置节能新技术措施
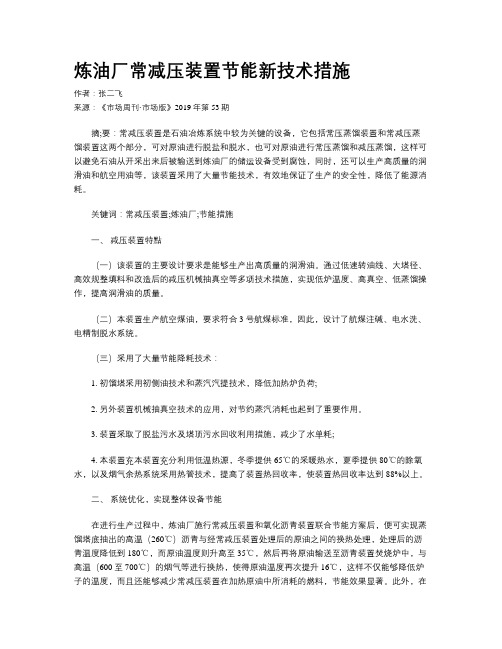
炼油厂常减压装置节能新技术措施作者:张二飞来源:《市场周刊·市场版》2019年第53期摘;要:常减压装置是石油冶炼系统中较为关键的设备,它包括常压蒸馏装置和常减压蒸馏装置这两个部分,可对原油进行脱盐和脱水,也可对原油进行常压蒸馏和减压蒸馏,这样可以避免石油从开采出来后被输送到炼油厂的储运设备受到腐蚀,同时,还可以生产高质量的润滑油和航空用油等,该装置采用了大量节能技术,有效地保证了生产的安全性,降低了能源消耗。
关键词:常减压装置;炼油厂;节能措施一、减压装置特點(一)该装置的主要设计要求是能够生产出高质量的润滑油。
通过低速转油线、大塔径、高效规整填料和改造后的减压机械抽真空等多项技术措施,实现低炉温度、高真空、低蒸馏操作,提高润滑油的质量。
(二)本装置生产航空煤油,要求符合3号航煤标准,因此,设计了航煤注碱、电水洗、电精制脱水系统。
(三)采用了大量节能降耗技术:1. 初馏塔采用初侧油技术和蒸汽汽提技术,降低加热炉负荷;2. 另外装置机械抽真空技术的应用,对节约蒸汽消耗也起到了重要作用。
3. 装置采取了脱盐污水及塔顶污水回收利用措施,减少了水单耗;4. 本装置充本装置充分利用低温热源,冬季提供65℃的采暖热水,夏季提供80℃的除氧水,以及烟气余热系统采用热管技术,提高了装置热回收率,使装置热回收率达到88%以上。
二、系统优化,实现整体设备节能在进行生产过程中,炼油厂施行常减压装置和氧化沥青装置联合节能方案后,便可实现蒸馏塔底抽出的高温(260℃)沥青与经常减压装置处理后的原油之间的换热处理,处理后的沥青温度降低到180℃,而原油温度则升高至35℃,然后再将原油输送至沥青装置焚烧炉中,与高温(600至700℃)的烟气等进行换热,使得原油温度再次提升16℃,这样不仅能够降低炉子的温度,而且还能够减少常减压装置在加热原油中所消耗的燃料,节能效果显著。
此外,在沥青、加氢裂化、催化裂化等设备之后,加入渣油热供料偶记常减压蜡油,可降低下游装置的供应温度,降低冷却液负荷,同时降低下游装置进料升温的加热负荷,减少能源消耗。
- 1、下载文档前请自行甄别文档内容的完整性,平台不提供额外的编辑、内容补充、找答案等附加服务。
- 2、"仅部分预览"的文档,不可在线预览部分如存在完整性等问题,可反馈申请退款(可完整预览的文档不适用该条件!)。
- 3、如文档侵犯您的权益,请联系客服反馈,我们会尽快为您处理(人工客服工作时间:9:00-18:30)。
1.7 塔内件
近年来常减压蒸馏系统的主要进步在于新 型或改进塔内部的开发。其发展方向是首先实现 汽液混合(操作条件甚至远在液泛点以上)然后 用辅助设施实现汽液相分离。这样可以大大提高 处理量,脱除以前不能超过液泛点的制约。采用 这一理念,各塔器内部构件供应商相继推出了一 系列专利新产品,据称新型塔板可以提高能力 30%~50%或更多。
常减压装置新技术介绍
主要内容
1、国外蒸馏装置技术现状及发展趋势 2、国内蒸馏装置技术现状
1. 国外蒸馏装置技术现状及发展趋势
1.1 单套蒸馏装置的能力
随着炼厂规模的扩大,单套蒸馏装置的加工规 模也日益大型化。美国ExxonMobil公司贝汤炼油厂 的一套蒸馏装置规模为1300x104t/a常压塔直径9.75 米。
1.3减压渣油的切割点温度和总拔出率
对于不同的原油,减压拔出率的要求和意义是 完全不同的。对于低硫低金属石蜡基原油的燃料型 常减压装置,由于其减压渣油可以全部进入重油催 化裂化装置加工,因此不必追求减压拔出率,甚至 可以不需要减压蒸馏,全部常压渣油都可以直接进 入重油催化裂化装置。对于生产润滑油的常减压装 置,减压拔出率应根据对润滑油的粘度要求和丙烷 脱沥青装置的情况来决定减压拔出率。对于生产道 路沥青的常减压装置,减压拔出率应根据沥青的生 产要求而定。
近几年来,国外蒸馏装置工艺又有了新的 进展。法国的ELF和Technip公司共同开发了一 种次分馏技术,主要将汽,煤,柴油等各种产 品逐渐进行分离,从而降低工艺总用能,可以 降低能耗30%左右。
壳牌石油公司提出的整体蒸馏装置(Shell Bulk Distillation Unit),将原油蒸馏装置,加氢脱硫装置, 高真空减压蒸馏装置和减粘装置作为一个整体加以 优化。整体分馏装置将原油分为:常压渣油,含蜡 馏分油,中间馏分油和石脑油组分。常压部分分出 常压渣油,中间馏分和石脑油以下的馏分。中间馏 分在加氢分馏脱硫塔中分离为煤油,轻,重柴油, 常压渣油进入高真空减压蒸馏,分馏出的蜡油作为 催化裂化装置和加氢裂化装置的原料。整体整流装 置可以节省投资的30%左右。
1.5换热和节能
常减压装置的换热网络系统是石油化工装置中最 复杂的热交换系统之一。它的热物流主要是常压塔和 减压塔的各侧线产品,有时还会有其他装置的热物流 (例如,催化裂化装置的油浆等),一般热物流的数 目在十个以上;它的冷物流是需要加工的原油,闪底 油和重沸器所需的热源以及预热水和发生蒸汽用水。 换热网络设计的好坏直接影响到装置的能耗水平和冷 换设备的选用,其意义十分重大。
但是,对于硫含量高,金属含量高的原油来说,
减压拔出率的意义就完全不同了。硫含量高,金属 含量高的减压渣油,很难用催化裂化装置加工,这 种渣油一般只能用溶剂脱沥青或焦化的方法。如果 进入催化裂化装置,则需进行渣油加氢预处理,而 渣油加氢装置的投资和操作费用都很高。在这种情 况下,减压拔出率和拔出的馏分质量对全厂的经济 效益就会有重大的影响。拔出的蜡油,可以作为加 氢裂化装置的原料,即使作为催化裂化装置的原料, 其加氢预处理的投资和操作费用也要比渣油加氢低 得多。
1.2 产品分离精度
典型的产品分馏精度一般为: 石脑油与煤油的脱空度ASTM D86(5-95%) 13℃ 煤油和轻柴油的脱空度ASTM D86(5-95%) 8℃ 轻柴油和重柴油的脱空度ASTM D86(5-95%) -20℃ 轻柴油和重柴油的脱空度ASTM D1160(5-95%) 5℃
具体经济脱空度根据实际生产情况要求来定。
换热网络设计研究近三十年来一直是热量
利用系统工程学科中最活跃的研究领域。七十 年代,换热网络设计方法主要是启发探试法。 Linnhoff等人提出了“窄点”的概念和“窄点 技术”合成换热网络,该技术以其较强的系统 性特别是实用性而最为引人注目。换热网络设 计大多以窄点为分界点,分别将换热网络分为 两部分进行设计,最后合并为一个完整的换热 网络。
国外公司追求整体经济效益的最大化,而不
片面追求换热终温的最大化。对于加工含硫原油 的蒸馏装置,由于原油含硫较高,温度大于 240℃的换热器将使用价格较高、抗腐蚀性能较 好的钢材,过低的“窄点”温差将带来换热面积 的大幅度增加,使换热器的投资大幅度增加。 ExxonMobil公司选定的“窄点”温差要使换热 器投资回报率达到20%以上。对于加工含硫原 油的蒸馏装置,原油的换热终温一般不超过 280℃。
常减压蒸馏装置是炼厂的能耗大户,国外公 司非常注意节能降耗,但不追求过低的能耗指标, 节能降耗是在保证产品质量和产品收率的前提下 进行的,以使装置经济效益最大化。
1.6 电脱盐
以Petrolite和Howe-Beaket二公司的专 利技术较为先进。Howe-Beaket技术主要 为低速脱盐。Petrolite已在低速脱盐的基 础上开发出了高速电脱盐。
提高减压拔出率的关键是减压塔高真空,填料
塔以及减压塔进料段的设计。美国约122个大型减 压塔中,有40座采用了高效填料,欧洲和日本也有 22座,韩国以常压拔头为主的蒸馏塔几乎全部使用 了高效十年代,国外开发了“干式”减压蒸馏技术, 其 特点是在塔和炉内不注入水蒸气,通过塔顶采用三级 抽真空系统,使减压塔的进料段和炉出口获得较高的 真空度,在较低的操作温度下获得相同的拔出率。 “干 式”减压蒸馏技术可大幅度降低装置能耗,但是由于 不 吹水蒸气,使得减压蜡油产品质量较差,减压渣油中 含有较多的蜡油组分。针对“干式”减压的缺点,国 外发 展了“微湿式”减压蒸馏技术,在减压塔和减压炉管 内注 入少量水蒸气(注入量比“湿式”减压少),塔顶采
2. 国内蒸馏技术现状
2.1 装置规模
我国蒸馏装置与国外蒸馏装置相比主要是 装置规模小,运行负荷低,运行周期短。近几年, 我国在常减压装置大型化设计,施工,生产技术 管理等方面也取得了重大技术进展。1999年10 月在镇海炼化股份公司建成投产了800x104t/a的 常减压蒸馏装置,2001年5月改造为我国第一套 加工能力为1000x104t/a的常减压蒸馏装置并开 车一次成功,这标志着我国常减压大型化技术已 经走向成熟。