带凸缘圆筒形件的拉深
圆筒形件拉深尺寸计算和成形过程模拟

圆筒形件拉深尺寸计算和成形过程模拟摘要:在冲压生产中,拉深是广泛使用的工序。
通过拉深可获得筒形、阶梯形、锥形、球形等零件。
平板毛坯拉深成筒状开口零件时口部出现飞边卷口现象,对此进行切边设计。
关键词:筒形件;模具结构;拉深间隙Dynaform作为近年来板料成形数值模拟技术中常用的软件,可以预测成形过程中板料的破裂、起皱、回弹等,从而帮助设计人员显著减少模具开发设计时间及试模周期。
在利用该软件进行模拟分析时,应该采用理论计算和软件模拟共用,以找出合适的成形工艺。
带凸缘的圆筒形件是日常生活中常用的零件,如不锈钢的面盆、压力锅的锅盖等物品,均属于带凸缘的圆筒形件。
本文利用所给的拉深件,首先计算了拉深过程中的部分尺寸,而后在理论计算的基础上,结合Dynaform软件对零件的拉伸过程进行模拟,找出了较为合适的压边力,从而为后续拉深模具设计提供依据。
1、带凸缘圆筒形件拉深尺寸计算图1是带凸缘圆筒形件的零件图,其壁厚为2mm,材料为304不锈钢,精度为IT14级。
本文计算的拉深尺寸包括拉深毛坯的尺寸、拉深次数的计算、压边装置的使用与否以及压边力的计算。
1.1带凸缘圆筒形件毛坯尺寸的计算由图1,零件的厚度t=2mm,因此在计算毛坯尺寸时应采用中线尺寸计算。
该零件的相对直径dt/d=380/320=1.18,其中dt为凸缘直径,d为圆筒件底部直径,取修边余量δ=6mm。
由拉深毛坯尺寸的计算公式可知:根据图1,d4=380+2δ=392mm,r=6mm,d2=d+2r=332mm,H=98mm由此计算出防尘盖毛坯尺寸:1.2是否需要压边装置和拉深次数的计算本零件采用普通平面凹模拉深,毛坯不起皱条件为:t/D≥(0.09~0.17)(1-m)由图1和D可计算出:t/D=2/527=0.38%,总拉深系数m=d2/D=332/527=0.63。
因此(0.09~0.17)(1-m)=0.0333~0.0629,则t/D<(0.09~0.17)(1-m),因此该零件拉深时需使用压边圈。
带凸缘圆筒形件拉深模设计
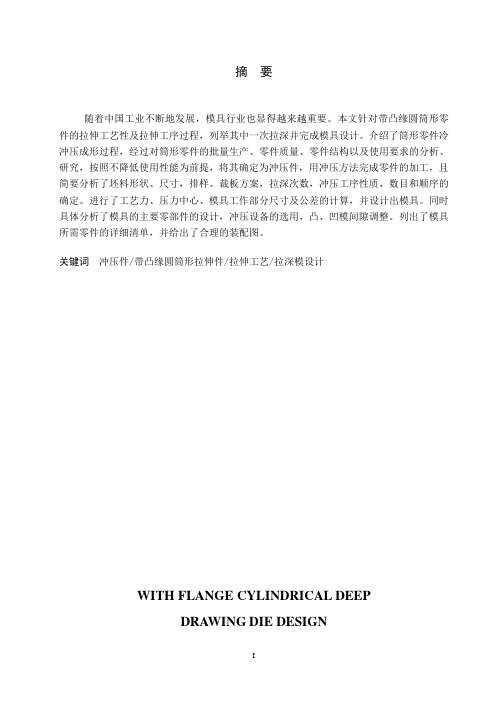
摘要随着中国工业不断地发展,模具行业也显得越来越重要。
本文针对带凸缘圆筒形零件的拉伸工艺性及拉伸工序过程,列举其中一次拉深并完成模具设计。
介绍了筒形零件冷冲压成形过程,经过对筒形零件的批量生产、零件质量、零件结构以及使用要求的分析、研究,按照不降低使用性能为前提,将其确定为冲压件,用冲压方法完成零件的加工,且简要分析了坯料形状、尺寸,排样、裁板方案,拉深次数,冲压工序性质、数目和顺序的确定。
进行了工艺力、压力中心、模具工作部分尺寸及公差的计算,并设计出模具。
同时具体分析了模具的主要零部件的设计,冲压设备的选用,凸、凹模间隙调整。
列出了模具所需零件的详细清单,并给出了合理的装配图。
关键词冲压件/带凸缘圆筒形拉伸件/拉伸工艺/拉深模设计WITH FLANGE CYLINDRICAL DEEPDRAWING DIE DESIGNABSTRACTAs China's industrial development unceasingly, the mold industry also appears more and more important. This paper belt of flange cylindrical parts stretching manufacturability and stretching process process, list one time deep drawing and complete the mold design. Cold stamping process of cylindrical parts is introduced, after mass production of the cylindrical parts, parts quality, parts structure, and use requirement analysis, research, according to not reduce the usability for the premise, to identify it for stamping parts, complete parts processing, with stamping method and the brief analysis of the blank shape, size, layout, cutting board, deep drawing, stamping process in nature, the determination of number and order. The technology force, pressure center, mold working parts dimension and tolerance of calculation, and design the mold. At the same time, concrete analysis of main components of the mold design, the selection of stamping equipment, convex and concave die clearance adjustment. Lists the mould needs a detailed list of spare parts, and gives the reasonable assembly drawing.KEYWORDS stamping parts, flange cylindrical stretching, stretching, deep drawing die design process目录1 前言 (1)1.1 模具的概论 (1)1.1.1 冲压与冲模 (1)1.1.2 我国冲压现状与发展方向 (2)1.1.3 国外模具发展趋势及行业特点 (2)1.1.4 模具设计及加工技术的现状 (3)1.1.6 冲模的零部件 (4)1.2 冲压件工艺分析 (5)1.2.1 冲压加工的经济性分析 (5)1.2.2 冲压件的工艺性分析 (5)1.3 本设计要求 (6)2 工艺方案 (7)2.1 工艺性分析 (7)2.1.1 拉深件的结构与尺寸 (7)2.1.3拉深件材料 (7)2.2 设计方案的确定 (7)3 主要工艺参数计算 (8)3.1 确定排样、裁板方案 (8)3.1.1 工艺分析 (8)3.1.2 确定修边余量 (8)3.1.3 坯料直径 (8)3.1.4 排样 (9)3.1.5 压力中心的确定 (10)3.2 拉深工艺的计算 (10)3.2.1 压边 (10)3.2.2 总拉深系数 (10)3.2.3 预算拉深次数 (10)3.2.4 确定首次拉深工序件尺寸 (11)3.2.5 确定拉深次数及以后各次拉深的工序件尺寸 (12)3.2.6 第二次拉深直径和高度 (13)3.2.7 第三次拉深直径和高度 (13)3.2.8 修边 (14)3.2.9 拉深速度 (14)3.3 工艺力计算 (14)3.3.1 拉深力 (14)3.3.2 压料力 (15)3.4 压力机的选择 (16)3.4.1 初选压力机 (16)3.4.2拉深功 (16)3.4.3压力机电动机功率 (16)3.4.4功率校核 (17)4 拉深模设计 (17)4.1拉深模具结构设计 (17)4.2模具工作部分尺寸计算 (17)4.2.1 凸凹模间隙 (17)4.2.2 凸凹模圆角半径 (17)4.2.3凸凹模工作尺寸及公差 (17)4.3标准件的选取 (18)4.3.1 模架 (18)4.3.2下模座 (19)4.3.3上模座 (19)4.3.4 导柱、导套 (19)4.3.5 销钉 (19)4.3.6 螺钉 (20)4.3.7 模柄 (20)4.3.8带螺纹推杆(顶杆) (20)4.3.9 打杆 (20)4.3.10 打杆螺母 (21)4.3.11 橡胶的选取 (21)4.3.12 橡胶螺杆 (22)4.3.13 ;螺杆螺母 (22)4.3.14 模柄紧固螺钉 (22)4.4模具非标准件的设计 (22)4.4.1 拉深凸模的设计 (22)4.4.2拉深凹模的设计 (23)4.4.3 凸模固定板设计 (24)4.4.4压料圈的设计 (24)4.4.6 托板的设计 (25)5 压力机的校核 (25)6 模具装配图 (26)结束语 (27)致谢 (28)参考文献 (29)1 前言板料冲压是金属加工的一种基本方法,他用以生产各种板料零件,具有生产效率高、尺寸精度好、重量轻、成本低并易于实现机械化和自动化等特点。
带凸缘筒形件拉深工序计算

例:图示带凸缘筒形件拉深工序计算。
分析:零件具有双耳凸缘,拉深时应拉出圆形凸缘,拉深后再用冲裁方法加工出凸缘所要求的形状,并完成冲孔。
凸缘直径mm d f 806268=⨯+= 相对凸缘直径7.14680==d d f 零件属于宽凸缘拉深件,且零件高度大于直径,可采用缩小直径增加深度的拉深方法。
拉深件圆角半径较小,拉深时凸、凹模圆角取合理的数值,拉深后采用整形的方法使圆角半径达到要求。
工序件尺寸计算按零件图所标注的尺寸进行计算。
1. 确定修边余量修边余量为3mm ,则凸缘直径mm d f 862380=⨯+=2. 计算毛坯直径)2.135(13614644.360464863.44dR-dh 4d D 22t =⨯⨯-⨯⨯+=+=3. 判断能否一次拉深4. 决定实际采用的毛坯直径考虑到相对板料厚度较小,为了防止后续拉深出现拉破现象,决定首次拉深按表面积计算多拉入3%的材料,在后续拉深中再将多拉入的料返回到凸缘根部,就可防止再拉深时因凸缘区材料再流入凹模而出现拉破现象。
实际采用的毛坯直径为:mm D D 13813603.103.11=⨯==5. 计算首次拉深直径 设2.11=d d f由表查得m t =0.53,则首次拉深直径为:7313853.011=⨯=⨯=D m d t验算所选取的m t 是否合适。
6. 计算再拉深工序件的直径m 2=0.78、m 3=0.80、m 4=0.827. 确定各次拉深的圆角半径8. 计算各次工序件的高度首次按表积计算多拉入了3%的料,如果后两次拉深每次按表积计算返回到凸缘根部为1.5%的料,则后两次拉深的毛坯直径为:mm D D mmD D 1361371360015.1015.132===⨯==工序件的高度:n d p d p n fn n d r r r r d d D h n n n n 222214.0)(43.025.0-+++-=h 2=54h 3=63。
凸缘圆筒形工件的拉深设计要点

凸缘圆筒形工件的拉深设计要点凸缘圆筒形工件的拉深设计要点:设计确定拉深模具结构时为充分保证制件的质量及尺寸的精度,凸缘圆筒形工件拉深设计注意点:拉深高度应计算准确,且在模具结构上要留有安全余量,以便工件稍高时仍能适应拉深凸模上必须设有出气孔,并注意出气孔不能被工件抱住面而失去作用3)有凸缘拉深件的高度取决于上模行程,模具中药设计限程器,以便于模具调整4)对于形状复杂,须经多次拉深的零件,需先做拉深模,经试压确定合适的毛坯形状和尺寸再做落料模,并在拉深模上按已定形的毛坯,设计安装定位装置。
5)弹性压料设备必须有限位器,防止压料力过大6)模具结构及材料要和制件批量适应7)模架和模具零件,要尽量是使用标准化8)放入和取出制件必须方便安全2、有凸缘圆筒形件的拉深方法及工艺计算有凸缘筒形件的拉深原理与一般圆筒形件是相同的,但由于带有凸缘,其拉深方法及计算与一般筒形件有一定差别。
1)有凸缘拉深件可以看成是一般筒形件在拉深未结束时的半成品,即只将毛坯外径拉深到等于法兰边直径d时的拉深过程就结束。
因此其变形力的压力状态和变形特点与筒形件相同。
2)根据凸缘的相对直径有凸缘筒形件可分为:窄凸缘筒形件和宽凸缘筒形件3、宽凸缘筒形件的工艺计算要点1)毛坯尺寸的技术,毛坯尺寸的计算仍按等面积原理进行,其中要考虑修边余量:根据拉深系数的定义,宽凸缘件总拉深系数仍可表示为:2)判断工件是否一次拉成,这只须比较工件实际所需的总拉深系数和h/d与凸缘件第一次拉深系数和极限拉深系数的相对高度即可。
M总>M1,当h/d4、拉深凸模和凹模的间隙拉深模间隙是指单面间隙,间隙的大小对拉深力,拉深件的质量,拉深模的寿命都有影响,若c值大时,凸缘区变厚的材料通过间隙时,校正和变形的阻力增加,与模具表面的摩擦,磨损严重,使拉深力增加,零件变薄,甚至拉破,模具寿命降低。
间隙小时得到的零件侧壁平直而光滑,质量好,精度较高。
间隙过大时,对毛坯的校直和挤压作用减小,拉深力降低,模具的寿命提高,但零件的质量变差,冲出的零件侧壁不直。
5 带凸缘筒形件的拉深
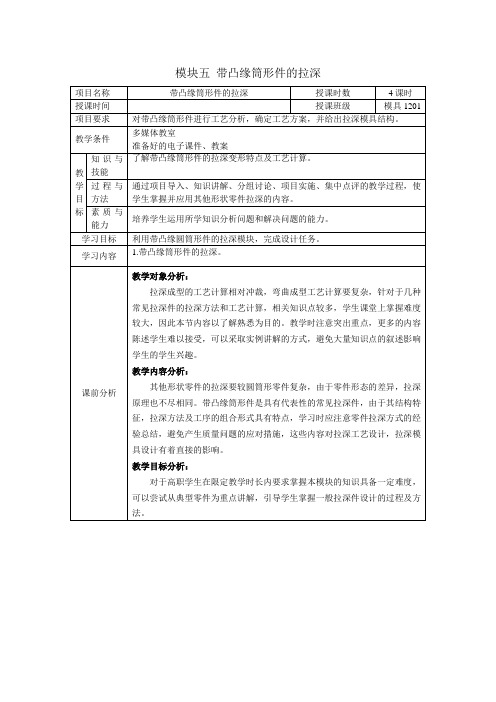
模块五带凸缘筒形件的拉深
一、项目导入(10分钟)
可采用拉深成型工序完成的零件的形态多种多样,通过本章节的学习,同学们已经掌握了圆筒形拉深件的拉深工艺及模具设计,那么除圆筒形拉深件以外,其他形态拉深件的成型方式是怎么样的呢?在本模块中将介绍典型的带凸缘筒形件的拉深工艺。
知识讲解(90分钟)。
4.5 带凸缘筒形件拉深
有凸缘筒形件的拉深变形原理与一般圆筒形件是相同的,但由于带有凸缘(图4-43),其拉深方法及计算方法与一般圆筒形件有一定的差别。
1.有凸缘圆筒形件一次成形拉深极限
有凸缘圆筒形件的拉深过程和无凸缘圆筒形件相比,其区别仅在于前者将毛坯拉深至某一时刻,达到了零件所要求的凸缘直径d t 时拉深结束;而不是将凸缘变形区的材料全部拉入凹模内。
所以,从变形区的应力和应变状态看两者是相同的。
图4-43有凸缘圆形件与坯料图图4-44拉深时凸缘尺寸的变化
图 4-46宽凸缘零件的拉深方法
分钟)
对右图中的带凸缘筒形件进行拉深工艺分析?确定拉深件的工艺方案,完成工艺计算?
查表得工件第一次拉深的最大相对高度
m
查表得第一次拉深时的拉深系数
1
推杆; 12-推板;13-紧固螺钉; 14-紧固螺栓; 15-空心垫板; 16-压边圈;螺母; 18-下模座 压边力的计算: 22
1[(2)]4
Y A F D d r P π=-+
查表。
计算得:
22
[152(7229.6)]334.8,40.8()0.8(15280)29.6
A KN D d t π=-+⨯⨯==-=-⨯=其中r
6)压力机吨位的选择
203.934.8238.7KN F F >+=+=压拉。
有凸缘筒形件拉深设计说明书

J I A N G S U U N I V E R S I T Y本科毕业论文有凸缘筒形件成型工艺与工装设计The process planning of the drawing of the tube-shaped flangepart.学院名称:材料学院专业班级:材料成型052学生姓名:秦亚飞指导教师姓名:刘忠德指导教师职称:教授2009年 5 月目录摘要 (1)引言 (1)第一章有凸缘筒形件拉深工艺分析 (1)§1.1 零件冲压工艺分析 (1)§1.2 拟定工艺方案 (1)1.2.1 冲压工序分析 (1)1.2.2判断拉深次数 (2)1.2.3判断是否需要压边力 (2)1.2.4确定各次拉深系数 (2)1.2.5确定各次拉深圆角半径 (3)1.2.6计算拉深高度 (3)1.2.7拟定工序图 (3)1.2.8拟定工艺方案 (3)§1.3 毛坯尺寸及排样设计 (4)1.3.1毛坯尺寸设计 (4)1.3.2排样设计 (4)第二章通过压力计算初选压力机 (5)§2.1 落料力的计算 (5)§2.2 正拉深相关力的计算 (5)2.2.1拉深力的计算 (5)§2.3 反拉深相关力的计算 (6)2.3.1 拉深力的计算 (6)2.3.2压边力的计算 (6)§2.4 压力机的选择 (6)2.4.1公称压力的计算 (6)2.4.2选择压力机 (6)第三章模具工作部分尺寸计算 (7)§3.1正拉深部分 (7)§3.2反拉深部分 (8)第四章模具结构设计 (9)§4.1复合模 (9)4.1.1 复合模的特点 (9)4.1.2 最小壁厚 (9)§4.2复合模正装与倒装的比较 (10)§4.3模具结构选择 (13)第五章模具主要零部件设计 (15)§5.1 正拉深凸、凹模的设计 (15)5.1.1模壁厚的计算 (15)5.1.2高度的确定 (15)5.1.3强度的校核 (15)5.1.4最大长度校核 (15)5.1.5结构形式 (15)§5.2 凸模的设计 (16)5.2.1长度的计算 (16)5.2.2强度的校核 (16)5.2.3最大长度校核 (16)5.2.4固定形式 (16)5.2.5结构形式 (16)§5.3落料凹模的设计 (17)5.3.1模壁厚的计算 (17)5.3.2刃壁高度 (17)5.3.3模具高度计 (17)5.3.4固定形式 (17)5.3.5结构形式 (17)§5.4落料凸模的设计 (18)5.4.1壁厚的计算 (18)5.4.2高度的计算 (18)5.4.3外缘直径D的计算 (18)5.4.4结构形式 (18)§5.5卸料板的设计 (19)5.5.1直径的计算 (19)5.5.2厚度的计算 (19)§5.6导料板的设计 (19)5.6.1直径的计算 (19)5.6.2厚度的计算 (19)§5.7压料装置的设计 (19)5.7.1结构形式 (19)5.7.2橡胶的设计 (20)§5.8顶料装置的设计 (20)第六章压力机校核及模具安装 (21)§6.1压力机的的选用 (21)§6.2 模具安装 (21)设计小结 (22)致谢 (23)参考文献 (24)有凸缘筒形件拉深工艺分析及工装设计专业班级:材料成型052 学生姓名:秦亚飞指导教师:刘忠德职称:教授摘要:有凸缘筒形件被广泛用在很多领域和场合,例如发动机端盖等。
圆筒件的拉深系数

若某相邻两阶梯直径比值dn/dn-1小于相应圆筒 形件的极限拉深系数时,则由直径dn-1到dn按 凸缘件的拉深办法,其拉深顺序由小阶梯到大 阶梯依次拉深。
若mΣ>m(极限拉深系数),则该零件只 需拉深一次,否则必须多次拉深。
多次拉深时,拉深次数的确定:
取首次拉深系数为m1,则m1=d1/D,故d1=m1D 取第二次拉深系数为m2,则m2=d2/d1
故d2=m2d1=m1m2D … 第n次拉深时,工作直径则为:dn=m1m2m3……mnD 因而mΣ=m1m2m3…mn
工序图:
二、有凸有凸缘圆筒形件的拉深将毛坯拉深至某一时刻 达到零件所要求的凸缘直径dt时不再拉深。
毛坯直径为 :D d2t1 4d1h1 3.44d1r
当圆角半径rd=rp=r时,第一次拉深 系数为 :
m1
d1 D
1
d t1 d1
2
h1 4
d1
3.44 r d1
对于中小型零件(d t<200mm), 采用减小圆筒形部分直径、增加 高度来达到,而圆角半径rp和rd 在整个变形过程中基本保持不变。
用此方法制成的零件,表面质量较差, 容易在筒壁部分和凸缘上残留有中间工 序中形成的圆角部分弯曲和厚度的局部 变化的痕迹,所以最后要加一道整形工 序。
2.改变圆角半径并减小圆筒形直径
当工件的相对拉深高度h/d>h1/d1时,则该 工件就不能用一道工序拉深出来,而需 要两次或多次才能拉出。
以后各次拉深的拉深系数为mn=dn/dn-1。
(二)窄凸缘圆筒形件拉深
对 dt / d 1.11.4 之间的凸缘件称为窄凸缘件。
这类零件因凸缘很小,可以当作一般圆筒形件 进行拉深,只在倒数第二道工序时才拉出凸缘 或拉成具有锥形的凸缘,而最后通过校正工序 压成水平凸缘。
课程设计带凸缘筒形件首次拉深的拉深模设计
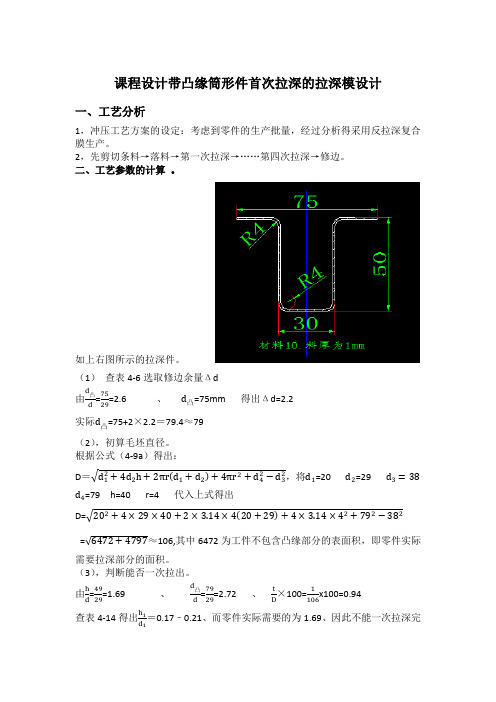
课程设计带凸缘筒形件首次拉深的拉深模设计一、工艺分析1,冲压工艺方案的设定:考虑到零件的生产批量,经过分析得采用反拉深复合膜生产。
2,先剪切条料→落料→第一次拉深→……第四次拉深→修边。
二、工艺参数的计算 。
如上右图所示的拉深件。
(1) 查表4-6选取修边余量Δd 由d 凸d=7529=2.6 、 d 凸=75mm 得出Δd=2.2实际d 凸=75+2×2.2=79.4≈79 (2),初算毛坯直径。
根据公式(4-9a )得出:D =√d 12+4d 2h +2πr (d 1+d 2)+4πr 2+d 42−d 32,将d 1=20 d 2=29 d 3=38d 4=79 h=40 r=4 代入上式得出D=√202+4×29×40+2×3.14×4(20+29)+4×3.14×42+792−382 =√6472+4797≈106,其中6472为工件不包含凸缘部分的表面积,即零件实际需要拉深部分的面积。
(3),判断能否一次拉出。
由h d =4929=1.69 、d 凸d=7929=2.72 、 t D ×100=1106x100=0.94查表4-14得出h1d 1=0.17﹣0.21、而零件实际需要的为1.69、因此不能一次拉深完成。
(4),计算拉深次数及各工序的拉深直径。
,因此需要用试凑法计算利用表4-14来进行计算,但由于有两个未知数m和d td1拉深直径。
下面用逼近法来确定第一的拉深直径。
的值为由于实际拉深系数应该比极限拉伸系数稍大,才符合要求,所以上表中d td11.5、1.6、1.7的不合适。
因为当d t的值取1.4的时候,实际拉深系数与极限拉深系数接近。
故初定第一次d1拉深直径d1=56.因以后各次拉深,按表4-8选取。
故查表4-8选取以后各次的拉深系数为当m2=0.77时d2=d1×m2=56×0.77=43mm当m2=0.79时d3=d2×m3=43×0.79=34mm当m3=0.81时d4=d3×m4=34×0.81=27mm<29mm因此以上各次拉程度分配不合理,需要进行如下调整。
第六章拉深(5—7)
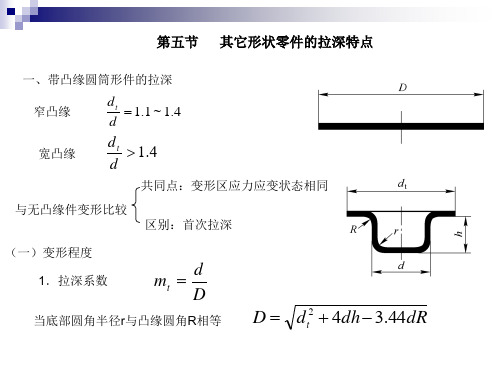
②变形情况:直边流入凹模的速度>圆角部分
∴直边对圆角的变形有带动作用,因此,可减少圆角的拉应力σL。 ③直边与圆角相互影响程度决定于r/B和H/B r/B↓→ 直边对圆角变形影响↑ H/B↑→ 直边对圆角变形影响↑
(二)盒形件毛坯形状与尺寸的确定 1、一次拉深成形的低盒形件坯料 作图法: (1)直边——按弯曲变形
不能用来作为判断依据
m
d d D 2d
2.三种成形方法
(1)
t 3% D
可不用压料圈,但行程终了要整形,
(2)
t 0.5% ~ 3% 采用压料装置拉深 D t 3% D
采用压料筋或反拉深方法
(3)
1. 带直壁 h (0.1 ~ 0.2)d 或带凸缘球形件 dt d (0.2 ~ 0.3)d 有利于球面成形(防皱) 2. 高度小于 r 的浅球形件 问题----------起皱、坯料偏移、回弹 (1)
di mi d i 1
(i=2,3,4…n)
以后各次拉深系数——其值与凸缘宽度及外形尺寸无关,可 查表5-11,与无凸缘拉深相同。
(二)拉深方法
1.小凸缘圆筒件拉深
前几道按无凸缘拉深→最后两道拉为带锥形凸缘件→再整形成平面凸缘。
2.宽凸缘圆筒件拉深方法
表面质量较差,需最后增加整形 工序,适用于薄、深、中小件 (dt<200mm)
查表5-14
ri——各次拉深后工序件口部圆角半径
(2)相对高度 当 r rd 也可用H/r表示 首次拉深查表5-13
拉深系数m大于表5-12或相对高度H/r小于表5-13可一次拉深成形。
(四)盒形件多工序的拉深方法及工序件尺寸的确定 盒形件多次拉深的变形特点: (与筒形件多次拉深不同;与盒形件首次拉深不同)
拉深工艺及拉深模设计

拉深工艺及拉深模设计本章内容简介:本章在分析拉深变形过程及拉深件质量影响因素的基础上,介绍拉深工艺计算、工艺方案制定和拉深模设计。
涉及拉深变形过程分析、拉深件质量分析、圆筒形件的工艺计算、其它形状零件的拉深变形特点、拉深工艺性分析与工艺方案确定、拉深模典型结构、拉深模工作零件设计、拉深辅助工序等。
学习目的与要求:1.了解拉深变形规律、掌握拉深变形程度的表示;2.掌握影响拉深件质量的因素;3.掌握拉深工艺性分析。
重点:1. 拉深变形特点及拉深变形程度的表示;2.影响拉深件质量的因素;3.拉深工艺性分析。
难点:1.拉深变形规律及拉深变形特点;2.拉深件质量分析;3.拉深件工艺分析。
拉深:利用拉深模将一定形状的平面坯料或空心件制成开口空心件的冲压工序。
拉深工艺可以在普通的单动压力机上进行,也可在专用的双动、三动拉深压力机或液压机上进行。
拉深件的种类很多,按变形力学特点可以分为四种基本类型,如图5-1所示。
图5-1 拉深件示意图5.1 拉深变形过程分析5.1.1 拉深变形过程及特点图5-2所示为圆筒形件的拉深过程。
直径为D、厚度为t的圆形毛坯经过拉深模拉深,得到具有外径为d、高度为h的开口圆筒形工件。
图5-2 圆筒形件的拉深1.在拉深过程中,坯料的中心部分成为筒形件的底部,基本不变形,是不变形区,坯料的凸缘部分(即D-d的环形部分)是主要变形区。
拉深过程实质上就是将坯料的凸缘部分材料逐渐转移到筒壁的过程。
2.在转移过程中,凸缘部分材料由于拉深力的作用,径向产生拉应力,切向产生压应力。
在和的共同作用下,凸缘部分金属材料产生塑性变形,其“多余的三角形”材料沿径向伸长,切向压缩,且不断被拉入凹模中变为筒壁,成为圆筒形开口空心件。
3.圆筒形件拉深的变形程度,通常以筒形件直径d与坯料直径D的比值来表示,即m=d/D(5-1)其中m称为拉深系数,m越小,拉深变形程度越大;相反,m越大,拉深变形程度就越小。
5.1.2 拉深过程中坯料内的应力与应变状态拉深过程是一个复杂的塑性变形过程,其变形区比较大,金属流动大,拉深过程中容易发生凸缘变形区的起皱和传力区的拉裂而使工件报废。
宽凸缘圆筒形拉伸件级进模具设计实例

宽凸缘圆筒形拉伸件级进模具设计实例定义:——凸缘的相对直径( d p包含修边余量)——相对拉伸高度(全部数据均取中性层数值)带凸缘圆筒形件拉伸一般分为两类:第一种:窄凸缘= 1.1 ~1.4第二种:宽凸缘> 1.4计算宽凸缘圆筒形件工序尺寸原则:1.在第一次拉伸时,就拉成部件所要求的凸缘直径,而在此后的各次拉伸中,凸缘直径保持不变。
2.为保证拉伸时凸缘不参加变形,宽凸缘拉伸件初次拉入凹模的资料应比部件最后拉伸部分实质所需资料3%-10%(按面积计算,拉伸次数多去上限,拉伸次数少去下限),这些剩余资料在此后各次拉深中逐次将1.5%-3%的资料挤回到凸缘部分,使凸缘增厚防止拉裂。
这对资料厚度小于0.5mm的拉伸件成效更明显。
凸缘圆筒形件拉伸工序计算步骤:1.选定修边余量(查表 1)2.估算毛培直径3.算出x100 和,查表2第一次拉深同意的最大相对高度之值,而后与部件的相对高度相比,看可否一次拉成。
若≤可一次拉出,若>多次拉深,是算各工序尺寸。
4.表 3 第一次拉深系数 m1,表 4 此后各工序拉深系数 m2、m3、m4⋯⋯,并算各工序拉深直径,得出拉深次数。
5.整各工序拉深系数。
计算实例1.产品件简化凸直径: d p=74.9拉挺直径:d=43.15拉伸高度:H=19.5资料厚度:t=1 2.修边余量表1凸拉深件修余量凸尺寸 dp相凸尺寸 dp/d≤1.5> 1.5 ~2>2~2.5>2.5 ~325 1.6 1.4 1.21 50 2.52 1.8 1.6 100 3.53 2.5 2.2 150 4.3 3.63 2.5 2005 4.2 3.5 2.7 250 5.5 4.6 3.8 2.8 3006543相对凸缘尺寸:=74/43.15 =1.71 ;依据上边的表格 ( 表1) 1.5< =1.71<2 ;50<dp=74 <1004<100则,带凸缘的拉伸件修边余量:2~3,取值 3则,带凸缘的拉伸件修边余量:d=3 mm3.睁开依据成型前后中性层的面积不变原理使用 UG丈量出拉深件中性层面积 7379.0492 mm2 (不介绍使用公式计算,个人感觉一般计算得数偏大,故本文省略公式)则,睁开尺寸 D== 96.95 ≈ 97 mm睁开直径: D=97凸缘直径:d凸 =80.9拉挺直径: d=43.15拉伸高度: H=19.5资料厚度: t=1修边余量:d=34.拉深系数确立表 2带凸缘拉深件的初次拉深系数凸缘相对直资料相对厚度x100径 dp/d1≤0.2>0.2 ~0.5>0.5 ~0.1>1~1.5>1.5≤1.10.640.620.60.580.55> 1.1 ~1.30.600.590.580.560.53> 1.3 ~1.50.570.560.550.530.51> 1.5 ~1.80.530.520.510.500.49>1.8 ~ 20.470.460.450.440.43表3 带凸缘拉深件的初次拉深最大相对高度h1/d1凸缘相对直资料相对厚度x100径 dp/d1≤0.2>0.2 ~0.5>0.5 ~0.1>1~1.5>1.5≤1.10.450.500.570.650.75> 1.1 ~1.30.400.450.500.560.65> 1.3 ~1.50.350.400.450.500.58> 1.5 ~1.80.290.340.370.420.48>1.8 ~ 20.250.290.320.360.42表 4带凸缘拉深件的此后各次拉深系数凸缘相对直资料相对厚度x100径dp/d1≤0.2>0.2 ~0.5>0.5 ~0.1>1~1.5>1.5 m20.800.790.780.760.75m30.820.810.800.790.78m40.850.830.820.810.80m50.870.860.850.840.82(1)考证可否一次达成拉伸资料相对厚度: t/D=1/97 ×100=1.03 ≈1凸缘相对直径: dp/d=80.9/43.15=1.87总的拉伸系数: M=d/D=43.15/97=0.45依据上表(附表 2): 0.5< t/D≤1;1.8< dp/d <2则有工艺切口的初次最小拉伸系数M1=M依据上表(附表 3)有工艺切口的初次拉伸最大相对高度: h/d=19.5/43.15=0.45>0.32 因此,依据 M1=M 和 h/d=0.45>0.32 , 判断一次拉伸不可以成功,需要多步拉伸。
有凸缘圆筒形拉深件起皱和拉裂的原因及控制方法

[】 郑 家贤. 2 冲压模具设计实用手册【 . : M】 北京 机械工业出版社 ,
2 7. 0O
Re s n n n r l eh d fCy i d ia a g a o sa d Co t o t o so l rc l M n Fl n e
W rn l g a d De p Dr wi gPa t r cu i g i k i n e a n r sF a t rn n
Ab t a t T r u h f l e e r h c i c lv l med t fp rsp o e sn n e e a se l a t so ti e . i ep o l msi e t s r c : h o g ed r s a c ,rt a o u a ao a t r c s i g a d g n r a s mb y p rsi b a n d W t t r b e n i i i l h h d —
3 控制起皱开裂的工艺方法 1 有效压料 。在单动压力机上 冲压时 , ) 模具的压
边必须借助弹性元件 。目前 的弹性元件有橡胶垫 、 弹 簧或气压装置 。气压装置提供的压力可以认为是基本 不变的 ; 而橡胶垫提供 的压力随行程的增加而迅速增 加, 容易在拉深后期使拉伸件破裂 ; 弹簧次之 ; 因此 , 弹 性 元 件 的选 择 , 量用 气压 装置 , 尽 以减 少 拉伸 件 的
HAN n h n Ru — o g ’
(. o be p ies ye n ut o, d T iun0 0 0 ; .h nin ut n gmet c olT i a 3 0 2 C ia 1 D u lHapn s T r d s y . , aya 30 6 2 S ax Id syMaae n Sh o, a u n 0 1, hn) I rC h r y 0
带凸缘筒形件的拉深工艺数值模拟及模具设计
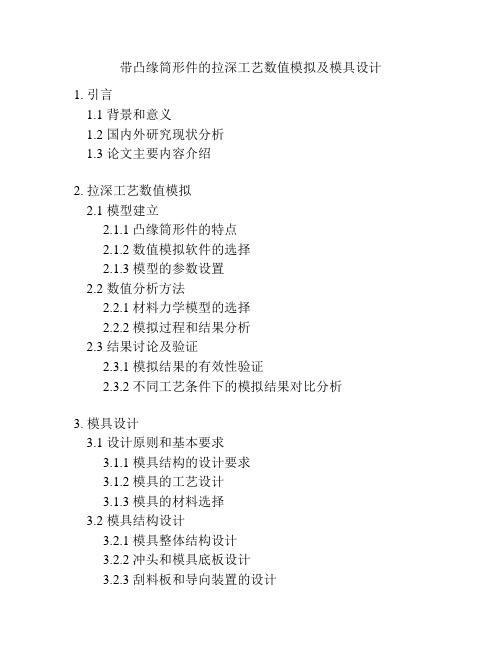
带凸缘筒形件的拉深工艺数值模拟及模具设计1. 引言1.1 背景和意义1.2 国内外研究现状分析1.3 论文主要内容介绍2. 拉深工艺数值模拟2.1 模型建立2.1.1 凸缘筒形件的特点2.1.2 数值模拟软件的选择2.1.3 模型的参数设置2.2 数值分析方法2.2.1 材料力学模型的选择2.2.2 模拟过程和结果分析2.3 结果讨论及验证2.3.1 模拟结果的有效性验证2.3.2 不同工艺条件下的模拟结果对比分析3. 模具设计3.1 设计原则和基本要求3.1.1 模具结构的设计要求3.1.2 模具的工艺设计3.1.3 模具的材料选择3.2 模具结构设计3.2.1 模具整体结构设计3.2.2 冲头和模具底板设计3.2.3 刮料板和导向装置的设计3.3 模具制造和调试3.3.1 模具加工和安装3.3.2 模具调试和性能评估4. 实验研究和结果分析4.1 实验方法和测量设备4.1.1 拉深实验环境的设计和控制4.1.2 测量设备及数据处理方法4.2 实验结果分析4.2.1 几何形状和尺寸的测量分析4.2.2 材料不均匀性和成形缺陷的分析4.3 实验结果的应用分析4.3.1 与数值模拟结果的对比分析4.3.2 工艺参数优化和工艺评估5. 结论和展望5.1 结论总结5.1.1 数值模拟和实验验证的一致性5.1.2 模具设计和制造的可行性和性能5.2 研究贡献和局限性5.2.1 研究对凸缘筒形件成形工艺的深入理解5.2.2 可能存在的方法和技术局限性5.3 展望和其他建议5.3.1 表现不足和未来研究方向5.3.2 对相关工业应用和发展的影响和建议第一章引言1.1 背景和意义凸缘筒形件是工业生产的重要组成部分,广泛应用于汽车、军工、机械等领域。
其具有良好的密封性、强度和刚性等特点,被广泛用于汽车发动机缸体、液压缸体、气缸套等部件的加工制造。
拉深是凸缘筒形件成形过程中的重要工艺之一,通过在凸缘部位形成逐渐变浅的锥形结构实现凸缘部位的成形。
8、带凸缘筒形件拉深模设计与制造 2解读
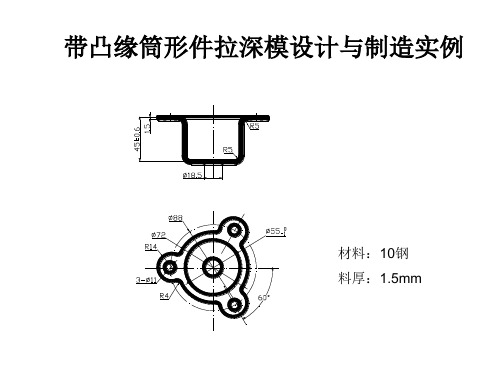
DT (DA Z min ) 0 .95 0.132) 0 .8180 T (156 0.030 mm 156 0.030 mm
h1 35.80 0.415 ,可查得当凸缘相 d1 86.35
t 1.5 100 100 0.96 时, D 157
,坯料相对厚度
第一次拉深允许的相对高度为 的m1是合理的。
h1 0.45 ~ 0.53 0.415 d1
,所以预定
(6)计算以后各次拉深的工序件直径 查得以后各次拉深极限拉深系数分别为[ m2]=0.76, [ m3]=0.79,则拉深后筒形件直径分别为
带凸缘筒形件拉深模设计与制造实例
材料:10钢 料厚:1.5mm
一、工艺性分析
1.材料分析 10钢为优质碳素结构钢,属于深拉深级别钢,具有良好的拉深成形 性能。 2. 结构分析 零件为一形状较复杂的有凸缘筒形件,且凸缘形状为异形。若拉深坯 料直接制备成凸缘的形状,则拉深成形时坯料受力不均匀,零件形状与 精度势必得不到保证,因此,拉深时坯料形状应为圆形,拉深结束后由 切边工序保证凸缘外形。零件凸缘上有3个孔,为了保证孔的精度,其 加工也放在拉深结束后冲裁。对于零件上的底孔则选择在冲压成形结束 后钻孔加工,因为拉深件成型后具有一定的高度,采用冲孔的方法凸模 的长度较长,不利于保证模具寿命。此外,零件底部圆角半径与口部圆 角半径均为R5,满足拉深件底部圆角半径大于一倍料厚、口部圆角半径 大于两倍料厚的要求。 3. 精度分析 零件上只有高度和拉深件直径两个尺寸标注公差,经查表其精度等级 都在IT14级以下,所以普通拉深即可达到零件的精度要求。
F
(2)确定坯料尺寸 查得有凸缘筒形件坯料计算公式为
D d F 4dh 3.44rd 1222 4 56.5 45 3.44 5.75 56.5mm 154.7mm 155mm
带凸缘筒形件的拉深 PPT

带凸缘筒形件的拉深
带凸缘圆筒形件的拉深看上去很简单,好像是拉深无 凸缘圆筒形件的中间状态。但当其各部分尺寸关系不同 时,拉深中要解决的问题是不同的,拉深方法也不相同。 当拉深件凸缘为非圆形时,在拉深过程中仍需拉出圆形 的凸缘,最后在用切边或其它冲压加工方法完成工件所 需的形状。
当r=R时,坯料的直径为
所以
由上式可以看出,带凸缘圆筒形件的拉深系数取决 于下列三组有关尺寸的相对比值;凸缘的相对直径dt/d; 零件的相对高度H/d,相对圆角半径R/d,其中以dt/d影 响最大;H/d次之,R/d影响较小。
带凸缘筒形件的拉深
3.带凸缘圆筒形件的拉深系数 带凸缘圆筒形件首次拉深的极限拉深系数见表4-16
带凸缘圆筒形件拉深与无凸缘圆筒形件拉深的最大 区别在于首次拉深,现结合实例说明其工序尺寸计算程 序。
项目实施
工件名称:带凸缘外壳
生产mm
项目任务: 1.对右图中的带凸缘筒形件进行拉深工艺分析? 2.确定拉深件的工艺方案,完成工艺计算? 3.完成拉深模具总体设计,初选压力机设备?
1-上模座;2-凹模;3-凸模 ;4推件板;5-打杆;6-模柄 ;7-紧固螺钉M10;
3.带凸缘圆筒形件的拉深系数
带凸缘筒件的拉深系数为:
mt = d/D
式中 mt——带凸缘圆筒形件拉深系数;
D——拉深件筒形部分的直径
d——坯料直径
当拉深件底部圆角半径r与凸缘处圆角半径R相等,当r=R时, 坯料的直径为
带凸缘筒形件的拉深
3.带凸缘圆筒形件的拉深系数 当拉深件底部圆角半径r与凸缘处圆角半径R相等,
表4-16 带凸缘圆筒形件首次拉深的极限拉深系数
带凸缘筒形件的拉深
3.带凸缘圆筒形件的拉深系数 首次拉深可能达到的相对高度见表4-17
- 1、下载文档前请自行甄别文档内容的完整性,平台不提供额外的编辑、内容补充、找答案等附加服务。
- 2、"仅部分预览"的文档,不可在线预览部分如存在完整性等问题,可反馈申请退款(可完整预览的文档不适用该条件!)。
- 3、如文档侵犯您的权益,请联系客服反馈,我们会尽快为您处理(人工客服工作时间:9:00-18:30)。
带凸缘圆筒形件的拉深
带凸缘圆筒形件
带凸缘圆筒形件的拉深
1.1 窄凸缘圆筒形件的拉深
窄凸缘圆筒形件第一种拉深方法
带凸缘圆筒形件的拉深
1.1 窄凸缘圆筒形件的拉深
窄凸缘圆筒形件第二种拉深方法
带凸缘圆筒形件的拉深
1.2 宽凸缘圆筒形件的拉深
当 r凸 = r凹 = r 时,宽凸缘圆筒形件毛坯直径 D 为:
根据拉深系数的定义,宽凸缘圆筒形件的拉深系数为:
带凸缘圆筒形件的拉深
1.2 宽凸缘圆筒形件的拉深
宽凸缘圆筒形件的尺寸
带凸缘圆筒形件的拉深
1.2 宽凸缘圆筒形件的拉深
毛坯尺寸的 计算
判断工件是 否一次拉深
成形
凸缘件多次 拉深成形
原则
带凸缘圆筒形件的拉深
1.2 宽凸缘圆筒形件的拉深
这种工件通常采用 减小筒部直径、增加筒部 高度来达到最终尺寸。圆 角半径在整个拉深过程中 基本不变。
8)根据表4-5选取以后各次拉深系数 m2、m3、…、mn,并预算出 各工序的拉深直径 d2=m2d1、d3=m3d2、…、dn=mndn-1。 若 dn<d,按式(4-2)放大 K 值,于是各次拉深直径为:
d2 = m2d1K、d3 = m3d2 K、…、dn = mndn-1 K。
带凸缘圆筒形件的拉深
时,可一次拉成。否则需要多次拉成。 4)根据表4-8选取 m1,计算 d1=m1D。初选第1次拉深的相对凸 缘直径为 dt/d1=1.1,若 m1 选的不合理,选 dt/d1=1.2、1.3…,直 到 m1 选择合理为止。 5)按照式(4-3)、式(4-4)计算第1次拉深模的凹、凸模圆角 半径。 6)根据宽凸缘圆筒件的拉深原则来修正毛坯直径D,并计算首次 拉深半成品高度 h1 为:
这类工件的高度在 第1次拉深时就基本形成, 以后各道拉深中使高度 基本保持不变,通过减 少凸、凹模圆角半
径逐渐缩小筒部直径 来拉深成形工件。
带凸缘圆筒形件的拉深
1.2 宽凸缘圆筒形件的拉深
宽 凸 缘 圆 筒 形 件 及 毛 坯 图
带凸缘圆筒形件的拉深
1.2 宽凸缘圆筒形件的拉深
1)选定修边余量δ。 2)预算毛坯直径 D。 3)根据表4-7中的 h1/d1 判断是否一次拉深成形。当 h/d ≤ h1/d1
带凸缘圆筒形件的拉深
1.2 宽凸缘圆筒形件的拉深
h1
0.25 d1
( D12
d
2 t
)
0.43(r1
R1 )
0.14 d1
(r12
R12
)
(4-8)
7)根据表4-7中 h1/d1,验证 m1是否合适。若计算得到的 h1/d1 小
于或等于表中的 h1/d1 值,说明m1选择合适,否则按步骤(4)
重新调整。
1.2 宽凸缘圆筒形件的拉深
9)确定以后各次拉深模的凸、凹模圆角半径。 10)根据宽凸缘圆筒形件的拉深原则,计算以后各次拉深的假设 毛坯直径Dn,计算各次拉深高度hn
hn
0.25 dn
( Dn2
d
2 t
)
0.43(rn
Rn )
0.14 dn
(rn2
Rn2 )
(4-9)
11)绘出工序图。
冲压工艺与模具设计