化工基础概论 第二章 非均相物系的分离
合集下载
非均相分离

三、过滤设备
过滤悬浮液的设备称为过滤机。
按照操作方式可分为间歇过滤机和连续过滤机;
按照过滤推动力产生的方式可分为压滤式、吸滤式和离心式。
1.板框压滤机 其结构如图4-3所示。
优点:结构简单,制造容易,设备紧凑,过滤面积大而占地小,操作压强高,滤饼含水少, 对各种物料的适应能力强。 缺点:间歇手工操作,劳动强度大,生产效率低
回转一周每个扇形格可依次完成过滤、洗
涤、吸干、吹松、卸饼等操作。 分配头由紧密贴合着的转动盘和固定盘 构成,转动盘装配在转鼓上一起旋转,
固定盘内侧开有长度不等的凹槽与各种不
同作用的管道相通.
操作时转动盘与固定盘相对滑动旋转,由固定盘上相连的不同作用的管道实现滤液吸出、洗
涤水吸出及空气压入的操作。即当转鼓上某些扇形格浸入料浆中时,恰与滤液吸出系统相通,进
4、滤饼的压缩性和助滤剂 (1)滤饼的压缩性
不可压缩滤饼: 颗粒有一定的刚性,挤压不变形。
滤饼
可压缩滤饼: 颗粒比较软,挤压变形,使滤饼中的流动通 道小,阻力增大。
(2)助滤剂
助滤剂—具有一定刚性的颗粒或纤维状的固体。加入助滤剂可减少可压缩滤饼的 流动阻力 助滤剂加入方法:
预涂法:用助滤剂配成悬浮液,在正式过滤前用它进行过滤,并在过滤介 质上形成一层由助滤剂组成的滤饼。
2015-2-16 非均相物系的分离 22
2015-2-16
非均相物系的分离
23
3、转鼓真空过滤机的优缺点
优点:连续操作,生产能力大,适于处理量大而容易过滤的料浆。 缺点:是附属设备较多,投资费用高,滤饼含液量高(常达30%)。由于 是真空操作,料浆温度不能过高。
2015-2-16
非均相物系的分离
非均相物系的分离全课件

非均相物系的分 离全课件
contents
目录
• 非均相物系分离概述 • 非均相物系分离原理 • 非均相物系分离技术及应用 • 非均相物系分离设备 • 非均相物系分离实验与案例分析
01
CATALOGUE
非均相物系分离概述
定义与分类
定义
非均相物系是指由固体颗粒、液体或 气体等不同相态物质组成的混合物。 分离是指将非均相物系中的各相态物 质进行分离、提纯或富集的过程。
萃取设备
总结词
利用两种不相溶溶剂的溶质分配原理,实现溶质由一种溶剂向另一种溶剂转移 的设备。
详细描述
萃取设备包括萃取塔、混合器、分液漏斗和离心萃取器等,适用于处理难以用 一般分离方法分离的混合物。通过选择合适的萃取剂,将目标物质从一种溶剂 转移到另一种溶剂中,达到分离和提纯的目的。
05
CATALOGUE
浮选分离原理
泡沫浮选
利用气泡将目的物质吸附并浮至液面形成泡沫层,从而实现 物质的分离。
沉淀浮选
将目的物质在溶液中先沉淀,再通过浮选的方法将其与其他 物质分离。
萃取分离原理
分配系数
物质在两种不混溶液体中的溶解度之比。
萃取过程
将待分离的物质加入两种不混溶液体的混合物中,经过一定时间后,利用两种液体的密度差异进行分 离。
应用
在石油、化工、制药、食品、环保等领域广泛应用,主 要用于固-液分离。
离心分离技术及应用
离心分离技术
利用离心力场的作用,使不同密度的物 质在离心场中受到不同的离心力,从而 实现物质分离的技术。
VS
应用
在化工、制药、环保、食品等领域广泛应 用,主要用于固-液分离和液-液分离。
浮选分离技术及应用
浮选分离技术
contents
目录
• 非均相物系分离概述 • 非均相物系分离原理 • 非均相物系分离技术及应用 • 非均相物系分离设备 • 非均相物系分离实验与案例分析
01
CATALOGUE
非均相物系分离概述
定义与分类
定义
非均相物系是指由固体颗粒、液体或 气体等不同相态物质组成的混合物。 分离是指将非均相物系中的各相态物 质进行分离、提纯或富集的过程。
萃取设备
总结词
利用两种不相溶溶剂的溶质分配原理,实现溶质由一种溶剂向另一种溶剂转移 的设备。
详细描述
萃取设备包括萃取塔、混合器、分液漏斗和离心萃取器等,适用于处理难以用 一般分离方法分离的混合物。通过选择合适的萃取剂,将目标物质从一种溶剂 转移到另一种溶剂中,达到分离和提纯的目的。
05
CATALOGUE
浮选分离原理
泡沫浮选
利用气泡将目的物质吸附并浮至液面形成泡沫层,从而实现 物质的分离。
沉淀浮选
将目的物质在溶液中先沉淀,再通过浮选的方法将其与其他 物质分离。
萃取分离原理
分配系数
物质在两种不混溶液体中的溶解度之比。
萃取过程
将待分离的物质加入两种不混溶液体的混合物中,经过一定时间后,利用两种液体的密度差异进行分 离。
应用
在石油、化工、制药、食品、环保等领域广泛应用,主 要用于固-液分离。
离心分离技术及应用
离心分离技术
利用离心力场的作用,使不同密度的物 质在离心场中受到不同的离心力,从而 实现物质分离的技术。
VS
应用
在化工、制药、环保、食品等领域广泛应 用,主要用于固-液分离和液-液分离。
浮选分离技术及应用
浮选分离技术
非均相物系的分离

构造简单,可直接安装在气体管道上,所以无需专门 的操作,但分离效率不高。
化工单元操作—非均相分离
2021/8/18
(二)离心沉降设备
1. 旋风分离器
工作过程
化工单元操作—非均相分离
2021/8/18
工作原理 :含尘气体以20~
30m/s的流速从进气管沿切
向进入旋风分离器,受圆筒壁
的约束旋转,做向下的螺旋运
化工单元操作—非均相分离
化工单元操作—非均相分离
2021/8/18
二、非均相物系分离在化工生产中的应用 ① 满足后序生产工艺的要求 ② 回收有价值的物质 ③ 分离非均相混合物,得到所要求的产品 ④ 使某些单元操作正常、高效地进行 ⑤ 减少环境污染,保证生产安全
化工单元操作—非均相分离
2021/8/18
不良反应
1.轻度反应 发热、恶心呕吐、面色苍白、局限性 荨麻疹。
旋液分离器可用于悬浮液的增稠、 固体颗粒的分级等。
化工单元操作—非均相分离
2021/8/18
二、过滤设备
(一)板框压滤机
通过直接给悬浮液加压,迫使其穿过过滤介质来实 现过滤的目的。
1.结构 板框压滤机由交替排列的滤板、滤框与夹于板框之间 的滤布叠合组装压紧而成。板框数视工艺要求在机座长度 范围内可灵活调节。组装后,在板框的四角位置形成连通 的流道,由机头上的阀门控制悬浮液、滤液及洗液的进出。
麻疹。
• 中度反应 频繁恶心、呕吐、泛发性荨麻疹、血压
偏低、面部及声门水肿、呼吸困难、寒战高热、头 痛及胸腹部不适等。
• 严重反应 血压急骤下降、晕厥、出现意识障碍、
急性肺水肿,心率失常以至心跳、呼吸骤停。
化工单元操作—非均相分离
2021/8/18
化工单元操作—非均相分离
2021/8/18
(二)离心沉降设备
1. 旋风分离器
工作过程
化工单元操作—非均相分离
2021/8/18
工作原理 :含尘气体以20~
30m/s的流速从进气管沿切
向进入旋风分离器,受圆筒壁
的约束旋转,做向下的螺旋运
化工单元操作—非均相分离
化工单元操作—非均相分离
2021/8/18
二、非均相物系分离在化工生产中的应用 ① 满足后序生产工艺的要求 ② 回收有价值的物质 ③ 分离非均相混合物,得到所要求的产品 ④ 使某些单元操作正常、高效地进行 ⑤ 减少环境污染,保证生产安全
化工单元操作—非均相分离
2021/8/18
不良反应
1.轻度反应 发热、恶心呕吐、面色苍白、局限性 荨麻疹。
旋液分离器可用于悬浮液的增稠、 固体颗粒的分级等。
化工单元操作—非均相分离
2021/8/18
二、过滤设备
(一)板框压滤机
通过直接给悬浮液加压,迫使其穿过过滤介质来实 现过滤的目的。
1.结构 板框压滤机由交替排列的滤板、滤框与夹于板框之间 的滤布叠合组装压紧而成。板框数视工艺要求在机座长度 范围内可灵活调节。组装后,在板框的四角位置形成连通 的流道,由机头上的阀门控制悬浮液、滤液及洗液的进出。
麻疹。
• 中度反应 频繁恶心、呕吐、泛发性荨麻疹、血压
偏低、面部及声门水肿、呼吸困难、寒战高热、头 痛及胸腹部不适等。
• 严重反应 血压急骤下降、晕厥、出现意识障碍、
急性肺水肿,心率失常以至心跳、呼吸骤停。
化工单元操作—非均相分离
2021/8/18
2 非均相混合物的分离

第三节 沉降分离
在外力场作用下,利用分散相和连续相之间的密度差,使 之发生相对运动而实现非均相混合物分离的操作称为沉降
分离。
重力沉降(分离较大颗粒,如选矿)
根据外力场不同:
离心沉降(分离较小颗粒,如气体除尘)
根据颗粒是否受到其他颗粒或器壁的影响: 自由沉降:容器壁和其它颗粒不影响沉降速度; 干扰沉降:实际颗粒的沉降。
包围着分散相物质且处于连续状 态的流体 如:气态非均相物系中的气体,
液态非均相物系中的连续液体
二、非均相物系的分离方法
1.非均相物系的分离依据
分散质与分散介质之间物性的差异,如密度,颗粒粒径等。
2.分离方法——机械法
使分散质与分散介质之间发生相对运动实现分离。
机械 分散相和连续相 分离
发生相对运动的方式
大的悬浮液的分离。 这种设备具有结构简单,可连续操作且增稠物浓度较
均匀等优点,其缺点是设备庞大、占地面积大、分离 效率较低等。
学习重力沉降时应注意以下几个问题:
(1) 沉降速度:是当颗粒在流体中沉降时所受到的重力与浮力和阻力
之和为零时,颗粒作匀速运动时的速度,其值与流体物性、颗粒的密 度、颗粒直径及流体流动型态等因素有关,沉降速度不是操作特性, 而是一综合特性。
反之。气体的粘度随着温度升高而增大,故温度高的气体较温度低的 气体除尘困难。
二、离心沉降
离心沉降:依靠惯性离心力的作用而实现的沉降过程 。 适于分离两相密度差较小,颗粒粒度较细的非均相物系。
惯性离心力场与重力场的区别
重力场
离心力场
力场强度 方向
重力加速度g
ut2/R
指向地心
沿旋转半径从中心指向外周
流体——颗粒相对运动的三种情况:
非均相物系的分离及固体流态化课件
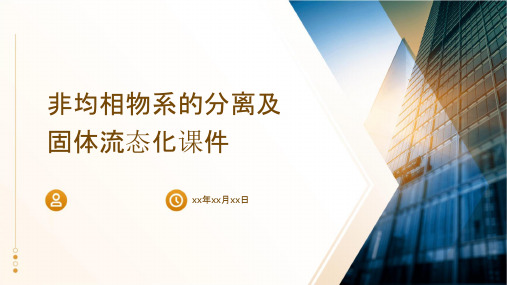
详细描述
离心分离法适用于颗粒较大、密度差较大的固-液或固-固非均相物系的分离。通过离心机的高速旋转,产生强大 的离心力场,使颗粒在离心场中受到较大的离心力而向外运动,最终实现固-液或固-固两相的分离。
浮选分离法
总结词
利用气泡吸附颗粒并上浮,实现固-液或固-固非均相物系的分离。
详细描述
浮选分离法适用于颗粒较小、密度接近于水的非均相物系的分离。通过向非均相物系中通入气泡,气 泡与颗粒相互作用,将颗粒吸附并带到液面上,从而实现固-液或固-固两相的分离。常用的浮选剂有 起泡剂、捕收剂等。
状态。
应用
广泛应用于气力输送、流化床 反应器等领域。
优点
操作简单,适用于大规模生产。
缺点
能耗较高,对颗粒大小和密度 有一定要求。
机械搅拌法
原理
通过机械搅拌装置,使固体颗 粒在搅拌桨的作用下形成流态
化状态。
应用
适用于实验室和小规模生产。
优点
设备简单,易于实现。
缺点
搅拌桨的转速和形状对流态化 效果影响较大,不适合大规模
固体流态化的基本原理
固体流态化的定义
固体流态化
在流体作用下,使固定床层固体颗粒 呈现类似流体状态的过程。
固体流态化技术
利用固体流态化技术,实现非均相物 系的分离和固体颗粒的连续输送、分 离、混合、反应等操作。
固体流态化的分类
根据操作条件
分为自然流态化和强制流 态化。
根据颗粒性质
分为散式流态化和聚式流 态化。
工业应用中的问题与对策
问题
在工业应用中,非均相物系分离及固 体流态化技术面临着操作复杂、能耗 高、稳定性差等问题。
对策
针对这些问题,工业界采取了一系列 对策,如引入自动化控制系统、优化 操作参数、采用新型分离技术等,以 提高操作的简便性、降低能耗和提高 稳定性。
离心分离法适用于颗粒较大、密度差较大的固-液或固-固非均相物系的分离。通过离心机的高速旋转,产生强大 的离心力场,使颗粒在离心场中受到较大的离心力而向外运动,最终实现固-液或固-固两相的分离。
浮选分离法
总结词
利用气泡吸附颗粒并上浮,实现固-液或固-固非均相物系的分离。
详细描述
浮选分离法适用于颗粒较小、密度接近于水的非均相物系的分离。通过向非均相物系中通入气泡,气 泡与颗粒相互作用,将颗粒吸附并带到液面上,从而实现固-液或固-固两相的分离。常用的浮选剂有 起泡剂、捕收剂等。
状态。
应用
广泛应用于气力输送、流化床 反应器等领域。
优点
操作简单,适用于大规模生产。
缺点
能耗较高,对颗粒大小和密度 有一定要求。
机械搅拌法
原理
通过机械搅拌装置,使固体颗 粒在搅拌桨的作用下形成流态
化状态。
应用
适用于实验室和小规模生产。
优点
设备简单,易于实现。
缺点
搅拌桨的转速和形状对流态化 效果影响较大,不适合大规模
固体流态化的基本原理
固体流态化的定义
固体流态化
在流体作用下,使固定床层固体颗粒 呈现类似流体状态的过程。
固体流态化技术
利用固体流态化技术,实现非均相物 系的分离和固体颗粒的连续输送、分 离、混合、反应等操作。
固体流态化的分类
根据操作条件
分为自然流态化和强制流 态化。
根据颗粒性质
分为散式流态化和聚式流 态化。
工业应用中的问题与对策
问题
在工业应用中,非均相物系分离及固 体流态化技术面临着操作复杂、能耗 高、稳定性差等问题。
对策
针对这些问题,工业界采取了一系列 对策,如引入自动化控制系统、优化 操作参数、采用新型分离技术等,以 提高操作的简便性、降低能耗和提高 稳定性。
第二章非均相物系的分离

图3-2 Ret 关系曲线
一、沉降速度
对球形颗粒 Ret关系曲线大致可分为三个
区域:
104 Ret 1 为层流区或斯托克斯(Stokes)定律区 24
Ret
ut
d
2 (s 18
)g
ut
4gd(s ) 3
一、沉降速度
1 Ret 103 为过渡区或艾仑(Allen)定律区
标准筛:有不同的系列, 常用泰勒标准筛。 筛号(目数):每英寸长度 筛网上的筛孔数目
二、颗粒群的特性
2. 颗粒的平均直径 粒群的平均直径计算式为
d
1 xi
di
第3章 非均相物系的分离
3.2 颗粒及颗粒床层的特性 3.2.1 颗粒的特性 3.2.2 颗粒床层的特性
3.2.2 颗粒床层的特性
第3章 非均相物系的分离和固体流态化
3.3 沉降分离 3.3.1 重力沉降
一、沉降速度
4.沉降速度的计算 (1)试差法
假设沉降属 于某一流型
计算沉 降速度
核算
Ret
一、沉降速度
(2)摩擦数群法
ut
4gd(s ) 3
4ds g
3ut2
Re t2
d 2ut2 2 2
一、沉降速度
(2)摩擦数群法
18.5
Ret0.6
ut 0.27
d
(s
)g
Ret0.6
一、沉降速度
103 Ret 2105 为湍流区或牛顿(Newton)定律区
0.44
ut 1.74
d(s )g
一、沉降速度
3.影响沉降速度的因素 自由沉降
沉降过程中,任一颗粒的沉降不因其他颗 粒的存在而受到干扰。 干扰沉降
非均相物系的分离.课件
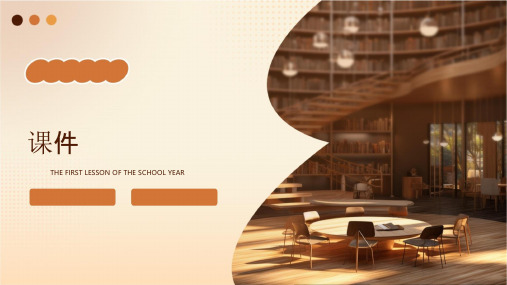
治理等。
01
非均相物系的分离 方法
沉降分离法
总结词
利用颗粒在重力场中的自然下落 实现分离
详细描述
根据颗粒的密度和粒径差异,使 不同组分在沉降过程中分层,从 而实现分离。适用于颗粒密度差 异较大的体系。
过滤分离法
总结词
通过过滤介质截留颗粒实现分离
详细描述
利用过滤介质(如滤布、滤纸等)的孔径大小,将颗粒截留在介质表面或内部,从而实现非均相物系的分离。适 用于颗粒粒径大于过滤介质孔径的体系。
03
分离高度
分离高度影响颗粒在流体 中的运动路径和时间,较 高的分离高度有助于颗粒 的沉降和分离。
分离压力
在某些非均相物系分离过 程中,压力的变化会影响 流体的物理性质和流动状 态,从而影响分离效果。
分离速度
提高分离速度可以增加颗 粒与流体的接触频率和碰 撞机会,有助于提高分离 效率。
01
非均相物系分离过 程的设计与优化
流体的性 质
流体粘度
流体温度
流体的粘度越大,颗粒在流体中的运 动阻力越大,沉降速度减慢,分离效 果降低。
温度影响流体的粘度和密度,进而影 响颗粒在流体中的运动和分离效果。
流体密度
流体的密度与颗粒密度之间的差异影 响颗粒的沉降速度,流体密度与颗粒 密度相差越大,越有利于颗粒的沉降。
操作条件
01
02
浮选分离法
总结词
利用颗粒的浮力性质实现分离
详细描述
通过向混合物中通入气体形成气泡,使颗粒粘附在气泡上浮至液面,从而实现分离。适用于密度小于 水的颗粒。
电泳分离法
总结词
利用电场力对颗粒的分离作用实现分 离
详细描述
在电场作用下,颗粒因带电性质的不 同而受到不同的电场力作用,从而实 现分离。电泳分离法可实现连续操作, 具有较高的分离效率。
01
非均相物系的分离 方法
沉降分离法
总结词
利用颗粒在重力场中的自然下落 实现分离
详细描述
根据颗粒的密度和粒径差异,使 不同组分在沉降过程中分层,从 而实现分离。适用于颗粒密度差 异较大的体系。
过滤分离法
总结词
通过过滤介质截留颗粒实现分离
详细描述
利用过滤介质(如滤布、滤纸等)的孔径大小,将颗粒截留在介质表面或内部,从而实现非均相物系的分离。适 用于颗粒粒径大于过滤介质孔径的体系。
03
分离高度
分离高度影响颗粒在流体 中的运动路径和时间,较 高的分离高度有助于颗粒 的沉降和分离。
分离压力
在某些非均相物系分离过 程中,压力的变化会影响 流体的物理性质和流动状 态,从而影响分离效果。
分离速度
提高分离速度可以增加颗 粒与流体的接触频率和碰 撞机会,有助于提高分离 效率。
01
非均相物系分离过 程的设计与优化
流体的性 质
流体粘度
流体温度
流体的粘度越大,颗粒在流体中的运 动阻力越大,沉降速度减慢,分离效 果降低。
温度影响流体的粘度和密度,进而影 响颗粒在流体中的运动和分离效果。
流体密度
流体的密度与颗粒密度之间的差异影 响颗粒的沉降速度,流体密度与颗粒 密度相差越大,越有利于颗粒的沉降。
操作条件
01
02
浮选分离法
总结词
利用颗粒的浮力性质实现分离
详细描述
通过向混合物中通入气体形成气泡,使颗粒粘附在气泡上浮至液面,从而实现分离。适用于密度小于 水的颗粒。
电泳分离法
总结词
利用电场力对颗粒的分离作用实现分 离
详细描述
在电场作用下,颗粒因带电性质的不 同而受到不同的电场力作用,从而实 现分离。电泳分离法可实现连续操作, 具有较高的分离效率。
第二章 非均相物系的分离

高的悬浊液。 颗粒的体积 分数大于1%。
第四节 过滤操作与设备
2.深层过滤 过滤时悬浮液中的颗粒沉积在床层内部 的孔道壁面上,而不形成滤饼。
深层过滤:适于处理固体 含量较少的悬浮液。
固相体积分率小于1%。
第四节 过滤操作与设备
二、过滤介质: 使流体透过而截留固体的可渗透性材料。
1.过滤介质的特性
非均相物系分离
第一节 概述
均相混合物:物质各处物理、化学性 1.混合物 质相同且无相界面;
非均相混合物:有两种相态(有明显的
相界面,物系各处性质不均匀) 气-固物系:含尘气体; 2.非均相混合物 液-液物系:乳浊液; 液-固物系:悬浮液;
第一节 概述
连续相(分散介质); 分散相(分散物质)
思考:悬浮液、乳浊液及含尘 气体的连续相和分散相?
颗粒的沉降过程分为两个阶段
加速阶段:u=0,Fd=0,a=amax
u↑,fd↑,a↓
等速阶段:u=ut 时,Fd=Fg-Fb , a=0
3 2 u 2 t d (s ) d 6 4 2 4d (s )g ut 3
为阻力系数
第二节 重力沉降与设备
2 gdP P ut 18
(2)过渡区
1 gdP.6 P ut 0.153 0.43 0.6
1 1.4
(3)湍流区
ut 1.74 d P P g
注:计算时沉降速度ut时,可使用试差法。
第二节 重力沉降与设备
第二节 重力沉降与设备
2.连续沉降槽(澄清器,增稠器,浓缩器)
(1)结构 (2)适用于大流量、 低浓度的悬浮液的分
离,如污水处理。
化工原理非均相物系分离全PPT课件

直径的
次方成正比;在湍流区,颗粒的沉降
速度与颗粒直径的
次方成正比。
第24页/共131页
【例】采用降尘室回收常压炉气中所含球形固体颗粒。 降尘室底面积为10㎡,宽和高均为2m。操作条件下气 体密度为0.75kg/m3,粘度为2.610-5Pas,颗粒密度为 3000 kg/m3。降尘室的生产能力为3m3/s。试求: (1)理论上可完全回收的最小颗粒直径; (2)粒径为40 m的颗粒的回收百分率; (3)如将降尘室改为多层以完全回收10m的颗粒, 在原降尘室内需设置多少层水平隔板及板间距。
第41页/共131页
1)临界粒径 定义:理论上在旋风分离器中能被完全分离下来 的最小颗粒。 计算公式的推导:
第42页/共131页
假设: (1)气流严格按螺旋形路线作等速运动,其切向
速度等于进口气速ui;
(2)颗粒向器壁沉降时,必须穿过厚度等于进气 宽度B的气流层,方能达到器壁而被分离; (3)颗粒的流动类型为滞流。
第31页/共131页
1、离心沉降速度
流体作圆周运动时,形成惯性离心力场。当颗
粒 度
在 ur
距中 。
心r
A
处
旋转时
ur C
,
其
切向速度uT,径向速 惯性离心力场强度:
r1
u uT
uT2/r
r
r2 B
轨迹:
逐渐扩大的螺旋线
颗粒在旋转流体中的运动
第32页/共131页
dp,p的球形颗粒受力分析:
离心力
Fc
p
g
4
d p2
u 2
2
ma
m
du
d
当a
du
d
0时, u
化工原理课件非均相物系分离

吸附热
物理吸附过程中放出的热量较小,接近于相应 气体的液化热。
可逆性
物理吸附在一定条件下是可逆的,即被吸附的物质在一定条件下可以解吸。
化学吸附
吸附热
化学吸附过程中放出的热量较大,接近于化 学反应热。
吸附力
化学吸附涉及电子的转移或共有,形成化学 键。
不可逆性
化学吸附通常是不可逆的,需要特定的条件 才能解吸。
06
其他分离方法
电泳分离
电泳分离原理
利用物质在电场作用下的电泳行为差异进行分离。
电泳设备
主要包括电泳槽、电极、电源和检测系统等。
电泳分离应用
广泛应用于生物大分子如蛋白质、核酸的分离纯化,也可用于小 分子和离子的分离。
膜分离技术
膜分离原理
利用膜的选择透过性,使混合物中的不同组分在 膜两侧产生浓度差,从而实现分离。
05
吸附分离
吸附分离原理
吸附作用
利用吸附剂对混合物中各组分的选择性吸附作用,使 混合物得以分离。
吸附平衡
在一定温度和压力下,混合物中的各组分在吸附剂上 的吸附量达到平衡。
吸附等温线
描述在一定温度下,吸附量与混合物组成之间的关系 曲线。
物理吸附
吸附力
物理吸附主要依靠分子间作用力(范德华力) 进行吸附。
化工原理课件非均相物系分离
汇报人:XX
目录
• 非均相物系概述 • 沉降分离 • 过滤分离 • 萃取分离 • 吸附分离 • 其他分离方法
01
非均相物系概述
定义与分类
定义
非均相物系是指物系内部存在两种或 两种以上不同相态的物质,且这些物 质之间具有明显的界面。
分类
根据相态的不同,非均相物系可分为 液-固、气-固、气-液等类型。
非均相物系的分离全PPT课件
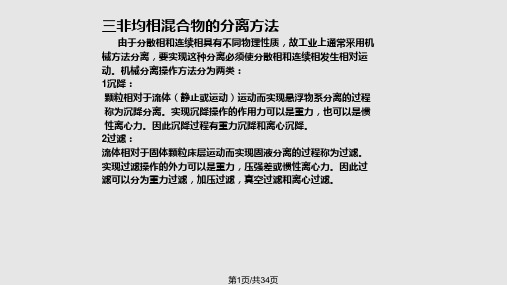
FD 3d pu
当流速较高时,Stokes定律不成立。因此, 对一般流动条件下的球形颗粒及其其他形状的颗粒, FD的数值尚需通过实验解决。
第14页/共34页
(2)曳力(阻力)系数
对球形颗粒,
用因次分析并整理后可得:
FD = F (dp , u, , )
FD
AP
1 2
u 2
Re P
d p u
三非均相混合物的分离方法
由于分散相和连续相具有不同物理性质,故工业上通常采用机 械方法分离,要实现这种分离必须使分散相和连续相发生相对运 动。机械分离操作方法分为两类: 1沉降: 颗粒相对于流体(静止或运动)运动而实现悬浮物系分离的过程 称为沉降分离。实现沉降操作的作用力可以是重力,也可以是惯 性离心力。因此沉降过程有重力沉降和离心沉降。 2过滤: 流体相对于固体颗粒床层运动而实现固液分离的过程称为过滤。 实现过滤操作的外力可以是重力,压强差或惯性离心力。因此过 滤可以分为重力过滤,加压过滤,真空过滤和离心过滤。
降分离过程。
的1000倍,当F然g 大大加快沉
第26页/共34页
2离心沉降设备
旋风分离器是利用离心沉降原理从气流中分离出颗粒的设备。如图所示,上部为圆筒 形、下部为圆锥形;含尘气体从圆筒上侧的矩形进气管以切线方向进入,藉此来获得器内 的旋转运动。气体在器内按螺旋形路线向器底旋转,到达底部后折而向上,成为内层的上 旋的气流,称为气芯,然后从顶部的中央排气管排出。气体中所夹带的尘粒在随气流旋转 的过程中,由于密度较大,受离心力的作用逐渐沉降到器壁,碰到器壁后落下,滑向出灰
aS S
v 1
,
(所3以)床层自由截面积分率A。
* 此式是近似的,在忽略床层中固
颗空A粒0隙 流 床相率动 层与互截 截面 面床积 积层 床自层由截面截积面A-床颗积层粒分截所面占率积的之A平均间截有面积何A关P 1系 A?AP 假设床层颗粒是均匀堆积(即认为
当流速较高时,Stokes定律不成立。因此, 对一般流动条件下的球形颗粒及其其他形状的颗粒, FD的数值尚需通过实验解决。
第14页/共34页
(2)曳力(阻力)系数
对球形颗粒,
用因次分析并整理后可得:
FD = F (dp , u, , )
FD
AP
1 2
u 2
Re P
d p u
三非均相混合物的分离方法
由于分散相和连续相具有不同物理性质,故工业上通常采用机 械方法分离,要实现这种分离必须使分散相和连续相发生相对运 动。机械分离操作方法分为两类: 1沉降: 颗粒相对于流体(静止或运动)运动而实现悬浮物系分离的过程 称为沉降分离。实现沉降操作的作用力可以是重力,也可以是惯 性离心力。因此沉降过程有重力沉降和离心沉降。 2过滤: 流体相对于固体颗粒床层运动而实现固液分离的过程称为过滤。 实现过滤操作的外力可以是重力,压强差或惯性离心力。因此过 滤可以分为重力过滤,加压过滤,真空过滤和离心过滤。
降分离过程。
的1000倍,当F然g 大大加快沉
第26页/共34页
2离心沉降设备
旋风分离器是利用离心沉降原理从气流中分离出颗粒的设备。如图所示,上部为圆筒 形、下部为圆锥形;含尘气体从圆筒上侧的矩形进气管以切线方向进入,藉此来获得器内 的旋转运动。气体在器内按螺旋形路线向器底旋转,到达底部后折而向上,成为内层的上 旋的气流,称为气芯,然后从顶部的中央排气管排出。气体中所夹带的尘粒在随气流旋转 的过程中,由于密度较大,受离心力的作用逐渐沉降到器壁,碰到器壁后落下,滑向出灰
aS S
v 1
,
(所3以)床层自由截面积分率A。
* 此式是近似的,在忽略床层中固
颗空A粒0隙 流 床相率动 层与互截 截面 面床积 积层 床自层由截面截积面A-床颗积层粒分截所面占率积的之A平均间截有面积何A关P 1系 A?AP 假设床层颗粒是均匀堆积(即认为
化工单元操作非均相物系的分离

澄清液体
普通要求:连续沉降槽、过滤机; 澄清要求高:深层过滤;
内蒙古化工职业学院
分离要求; 悬浮液特性; 操作条件; 过滤设备的类型; 过滤的推动力 重力、离心力和压强差。 加压过滤和真空过滤;恒速过滤与恒压过滤;
内蒙古化工职业学院
(1)处理量 (2)生产能力:单位时间内得到的滤液的体积, m3滤液/h; (3)生产率G:单位时间、单位面积内过滤出的干 固体质量,kg干固体/(m2.s); (4)过滤面积A (5)悬浮液固相浓度c:单位体积悬浮液中含有的 固体颗粒的总体积。
可压缩滤饼: 助滤剂 滤饼 不可压缩滤饼 6、滤饼的洗涤 例题:P112。
5、滤饼的可压缩性
#2022
内蒙古化工职业学院
1、过滤的基本方程 流动模型:液体在圆管内的层(滞)流流动。 哈根·泊谡叶公式: (1)空隙率ε:单位体积床层中的空隙体积, m3/m3; (2)滤液的流速:
内蒙古化工职业学院
内蒙古化工职业学院
3、过滤离心机
种类:三足式、卧式刮刀卸料式、离心卸料 式等; 操作过程:过滤、洗涤、甩干、卸料、洗网 操作特点: 操作时间可随意控制,分离1μm以上的颗粒,生产能力大,但不易保持颗粒形状的完整。
内蒙古化工职业学院
第三节 分离设备的选择
降尘室:50 μm以上;用于含尘气体的预分离;
内蒙古化工职业学院
三、离心沉降设备
旋风分离器 是判断旋风分离器分离效率高低的重要依据。 临界粒径: 5-75μm的粒子。 特点:结构简单, 价格低廉, 性能稳定;
内蒙古化工职业学院
2、旋液分离器
旋风分离器相比,旋液分离器的特点是(1)形状细长,直径小,圆锥部分长,以利于颗粒的分离;(2)中心经常有一个处于负压的气柱,有利于提高分离效果。旋液分离器中颗粒沿壁面高速运动,磨损严重,一般采用耐磨材料制造。
非均相物系分离
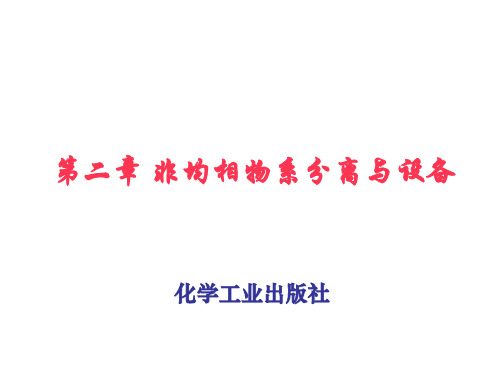
ut = 0.27× d(ρs ρ )g
ρ
Ret0.6
艾仑公式
湍流区
ut =1.74×
d(ρs ρ )g
ρ
牛顿公式
(二)降尘室生产能力 设进入降尘室的气体流量为V )。降尘室高为 设进入降尘室的气体流量为 s(m3/s)。降尘室高为 )。降尘室高为H 长为L,宽为B,单位为m。 ,长为 ,宽为 ,单位为 。颗粒随气流在降尘室中一 边以速度u在水平方向运动 同时还有向下的沉降速度u 边以速度 在水平方向运动 。同时还有向下的沉降速度 t 。 含尘气体在降尘室中的停留时间τ为
三、其他常见的气-固分离法 其他常见的气 固分离法 (一)袋滤器 袋滤器是依靠含尘气流通过过滤介质来实现气-固分 袋滤器是依靠含尘气流通过过滤介质来实现气 固分 离的净化设备。袋滤器可除去1m以下的尘粒,常用作最 离的净化设备。袋滤器可除去 以下的尘粒, 以下的尘粒 后一级的除尘设备。 后一级的除尘设备。 袋滤器的型式有多种,含尘气体可由滤袋内向外过滤, 袋滤器的型式有多种,含尘气体可由滤袋内向外过滤, 也可以由外向内过滤。脉冲袋滤器结构示意图。 也可以由外向内过滤。脉冲袋滤器结构示意图。 (二)湿法除尘器 湿法除尘是依靠亲水性的尘粒与水、水滴或其他液体 湿法除尘是依靠亲水性的尘粒与水、 相互接触、碰撞,使尘粒粘附或凝聚, 相互接触、碰撞,使尘粒粘附或凝聚,从而与气体分离的 操作。 操作。 1.喷淋式除尘器。 .喷淋式除尘器。 2.鼓泡式除尘器。 .鼓泡式除尘器。 3.填料式除尘器 。 . 4.文丘里除尘器。 .文丘里除尘器。
Vs ≤ BLut
降尘室的生产能力只取决于降尘室的底面积BL和颗粒 降尘室的生产能力只取决于降尘室的底面积 和颗粒 的沉降速度u 与降尘室的高度无关。因此, 的沉降速度 t,与降尘室的高度无关。因此,降尘室一般 设计成扁平形状,或设置多层水平隔板成多层降尘室。 设计成扁平形状,或设置多层水平隔板成多层降尘室。
ρ
Ret0.6
艾仑公式
湍流区
ut =1.74×
d(ρs ρ )g
ρ
牛顿公式
(二)降尘室生产能力 设进入降尘室的气体流量为V )。降尘室高为 设进入降尘室的气体流量为 s(m3/s)。降尘室高为 )。降尘室高为H 长为L,宽为B,单位为m。 ,长为 ,宽为 ,单位为 。颗粒随气流在降尘室中一 边以速度u在水平方向运动 同时还有向下的沉降速度u 边以速度 在水平方向运动 。同时还有向下的沉降速度 t 。 含尘气体在降尘室中的停留时间τ为
三、其他常见的气-固分离法 其他常见的气 固分离法 (一)袋滤器 袋滤器是依靠含尘气流通过过滤介质来实现气-固分 袋滤器是依靠含尘气流通过过滤介质来实现气 固分 离的净化设备。袋滤器可除去1m以下的尘粒,常用作最 离的净化设备。袋滤器可除去 以下的尘粒, 以下的尘粒 后一级的除尘设备。 后一级的除尘设备。 袋滤器的型式有多种,含尘气体可由滤袋内向外过滤, 袋滤器的型式有多种,含尘气体可由滤袋内向外过滤, 也可以由外向内过滤。脉冲袋滤器结构示意图。 也可以由外向内过滤。脉冲袋滤器结构示意图。 (二)湿法除尘器 湿法除尘是依靠亲水性的尘粒与水、水滴或其他液体 湿法除尘是依靠亲水性的尘粒与水、 相互接触、碰撞,使尘粒粘附或凝聚, 相互接触、碰撞,使尘粒粘附或凝聚,从而与气体分离的 操作。 操作。 1.喷淋式除尘器。 .喷淋式除尘器。 2.鼓泡式除尘器。 .鼓泡式除尘器。 3.填料式除尘器 。 . 4.文丘里除尘器。 .文丘里除尘器。
Vs ≤ BLut
降尘室的生产能力只取决于降尘室的底面积BL和颗粒 降尘室的生产能力只取决于降尘室的底面积 和颗粒 的沉降速度u 与降尘室的高度无关。因此, 的沉降速度 t,与降尘室的高度无关。因此,降尘室一般 设计成扁平形状,或设置多层水平隔板成多层降尘室。 设计成扁平形状,或设置多层水平隔板成多层降尘室。
- 1、下载文档前请自行甄别文档内容的完整性,平台不提供额外的编辑、内容补充、找答案等附加服务。
- 2、"仅部分预览"的文档,不可在线预览部分如存在完整性等问题,可反馈申请退款(可完整预览的文档不适用该条件!)。
- 3、如文档侵犯您的权益,请联系客服反馈,我们会尽快为您处理(人工客服工作时间:9:00-18:30)。
2.3.2过滤设备
1、板框压滤机
2、叶滤机 3、转鼓真空过滤机 4、离心过滤机
1、板框压滤机
板框压滤机是由许多块滤板和滤框交替排列组装而成,如图 2-11(a)所示。滤 板和滤框的构造如图 2-11(b)所示。滤板具有棱状的表面,形成了许多沟槽的 通道,板与框之间隔有滤布,装合时用压紧装置将一组板与框压紧。压紧后, 滤框与其两侧的滤板所形成的空间便构成了一个过滤空间。由于一台板框压滤 机由若干块板和框组成,故有数个过滤空间。每一块滤板和滤框的角上皆有孔, 当板、框叠合后即形成料液和洗涤液的通道。 过滤时,悬浮液在压力作用下经料液通道进入滤框内,滤液通过,滤渣被滞留 覆盖在滤板上,过滤结束后,松开板框,取出滤渣,再将滤板、滤框和滤布洗 净后重新装合,即可进行下次过滤。
2、旋液分离器
如使大直径微粒从底流中排出,小直径微粒从溢流中排出的操作,称为分级, 还可以通过对底流量与溢流量之比的调节,控制两部分中微粒大小的范围。 旋液分离器的直径与长度之比通常比较小,这样有利于增大分离作用力,同时 增大了液流的行程,从而延长了停留时间,锥形段的斜度一般为 10~20o。由于 旋液分离器较重力沉降设备构造简单,无运动部分,占地面积小,处理能力大, 设备费用低,有利于实现工艺连续化、自动化,故近年来在工业生产上应用日 广,旋液分离器往往是很多个串联起来使用,它可以从液流中分出直径为几 μm 的小微粒,通常是作为分级设备来使用,由于圆筒直径小(常见的范围是 50~300mm) ,液体进口速度大(可达到 10m/s) ,故流体阻力很大,磨损也较严 重。
4、离心过滤机
当待分离的悬浮液中固体颗粒较大,且含量也较多时,可在过滤式离心机中进 行分离,如图 2-15 所示。这种离心机的转鼓壁上开有若干小孔,若固体颗粒较 大时,可在转鼓的内壁上覆盖一层金属网作为过滤介质,若颗粒较小时,可在 金属网上再盖上一层滤布。悬浮液加在高速旋转的转鼓内,悬浮液中的液体受 到离心力的作用穿过滤布及转鼓上的小孔流出,而固体颗粒则被截留在转鼓内, 即完成了两相的分离任务。与过滤相比,离心过滤不仅过滤速率快、时间短, 而且所得的滤饼含液量较少。
②碟式离心机
碟式离心机的转鼓内装有许多倒锥形碟片,碟片直径一般为 0.2~8m,碟片数约 为 50~100 片。两个碟片间的间隙很小,一般为 0.25~1.25mm。各碟片在两个相 同位置上都开有小孔,当各碟片迭起时,可形成几个通道。转鼓的转速一般为 4700~8500r/min。此种离心机可用作分离或澄清两种情况。 如图 2-10 所示,料液从顶部中心管 1 加入离心机内,流到底部后再上升,经各 碟片小孔形成的孔道,使料液在各碟片间分布或若干薄液层。 分离乳浊液时,在离心力作用下重液靠近碟片的内侧,并沿径向往外移动,最 后从重液出口 3 流出;轻液沿碟片外侧向中央移动,由轻液出口 4 流出。分离 悬浮液时,固体颗粒向碟片的内侧沉降,并沿碟片下滑,沉积于转鼓的周边, 当累积至一定量时,停机卸出。 这种离心机由于沉降距离很小,沉降面积较大,故分离效果较好。
1、板框压滤机
但很多过滤操作要求在卸渣前对滤渣进行洗涤,用于这种情况的过滤机的滤板有两种,一 种是板上开有洗涤液通道的, 称为洗涤板, 另一种是板上没有洗涤液通道的, 称为过滤板。 滤液通过滤布沿滤板上的棱状表面流下,汇集于滤板下部,经旋塞放出。滤渣则被截留在 滤框内。当操作一段时间后,滤渣充满滤框时,若滤渣不需洗涤,则可放松压紧装 滤板和滤框可用金属、塑料或木柴制造,一般均为正方形。滤板通常比滤框簿。过滤的操 作压力一般为 294~981kPa。 板框过滤机的优点是:结构简单、操作容易、故障少、保养方便;单位过滤面积占地少, 过滤面积选择范围宽;过滤压力较高、滤渣的含水率低,便于用耐腐蚀材料制造;对物料 的适应性强。 它的主要缺点是:操作不能连续自动,劳动强度大。它适用于过滤粘度大、微粒细、固体 含量低的难过滤悬浮液,也比较适用于多品种、小规模的生产情况。 近年来研制成多种自动操作的板框过滤机,使过滤效率和劳动强度都得到很大地改善。
第二章 非均相物系的分离与设备
2.1常见非均相物系的分离方法及应用
• 非均相物系是指物系中存在着两相或更多的相, 就含有两相的非均相物系而言其中一相为分散物 质或称为分散内相,以细微的分散状态存在。包 围在分散物质各个粒子的周围的另一相称为连续 相。根据连续相的物理状态不同,非均相物系可 分为两类:一、当连续相为气体时称为气态非均 相物系,如含尘气体和含雾气体;二、当连续相 为液体时称为液态非均相物系,例如悬浮液、乳 浊液以及含有气泡的液体,即泡沫液等。
2.3液-固分离
2.3.1沉降设备
2.3.2过滤设备 2.3.3湿式除尘设备 2.3.4静电除尘器
2.3.1沉降设备
1沉降器
2旋液分离器 3沉降式离心机
1沉降器
沉降器是处理悬浮液的重力沉降设备,沉降器可分为:间歇式、半连续式和连 续式三种。 在化工生产和环保部门广泛使用的是连续式沉降槽 (又称增稠器) 如图 2-6 所示。 连续沉降槽是一个底部略具圆锥形的不深的圆槽。槽内装有转速为 0.025~0.5r/min 的耙集桨,桨上固定有钢耙。液体连续地沿送液槽从上方中央进 入,浓稠的沉淀沉降到器底,并被耙慢慢地集聚于器底中心,然后经排出管, 用泵连续地排出。澄清液经上口周缘的溢流槽连续排出。 沉降槽适于处理固体微粒不太小,浓度不高,但处理量较大的悬浮液。 沉降槽的优点是结构简单、操作结处理量大且增稠物的浓度均匀。缺点是设备 庞大,占地面积大、分离效率较低等。
2.2.2旋风分离器
1、旋风分离器的构造和操作原理
2、旋风分离器的选用
1、旋风分离器的构造和操作原理
A D D D D D H1 2 D H 2 2 D S D2 B D1 4 2 4 2 8
图 2-4 为一标准型旋风分离器构造示意图,以圆筒直径 D 表示其它部分的比例 尺寸。旋风分离器的主体上部为圆筒形,下部为一圆锥形底,锥底下部有排灰 口,圆筒形上部装有顶盖,侧面装一与圆筒相切的矩形截面进气管,圆筒的上 部中央处装一排气口。 含尘气体由圆筒上侧面的矩形进气管以切线方向进入,由于圆筒器壁的约束作 用,含尘气体只能在圆筒内和排气管之间的环状空间内向下作螺旋运动,如图 2-5 中实线所示。在旋转过程中,含尘气体中的颗粒在离心力的作用下被甩向器 壁,与器壁撞击后,因本身失去能量而沿器壁落至锥形底后由排灰口排出。经 过一定程度净化后的气体(因不可能将全部尘粒除掉)从圆锥底部自下而上作 旋转运动到排气管中排出,如图 2-5 中虚线所示。
2、叶滤机
叶滤机主要由一个垂直放置或水平放置的密闭圆柱滤槽和由许多滤叶组成,如 图 2-12 所示为一垂直加压过滤机
如图 2-13 和图 2-14 所示为一台转鼓真空过滤机的外形图和操作简图。 过滤机的 主要部分包括转鼓、滤浆槽、搅拌槽、搅拌器和分配头。转鼓长度和直径之比 约为 1/2~2。转鼓里一般有 10~30 个彼此独立的扇形小滤室,在小滤室的圆弧 形外壁上,装着覆以滤布的排水筛板,这样便形成了圆柱形过滤面。每个小滤 室都有管路通向分配头,使小滤室有时与真空源相通,有时与压缩空气源相通。 运转时浸没于滤浆中的过滤面积约占全部面积的 30%~40%。 每旋转一周, 过滤 面积的任一部分,都顺次经历过滤、洗涤、吸干、吹松、卸渣等阶段。因此, 每旋转一周,对任何一部分表面来说,都经历了一个操作循环,而任何瞬间, 对整个转鼓来说,其各部分表面都分别进行着不同阶段的操作。
2、旋液分离器
旋液分离器是利用离心沉降的原理从悬浮液中分离颗粒的设备。其结构和操作 原理与旋风分离器的大体相同,设备主要由圆筒和圆锥两部分构成,如图 2-7 所示。旋液分离器不能将固体微粒与液体介质完全分开,悬浮液经入口管由切 向进入圆筒,向下作螺旋形运动,固体微粒受离心力的作用被甩向器壁,并随 旋流降到锥底的出口,由底部排出的稠厚液称为底流,清液或只含有很细微粒 的液体,则形成螺旋上升的内旋流,由器壁的溢流管排出,称为溢流;由于离 心力的作用,在内层旋流中心还有一个处于负压的空气蕊.;旋液分离器的底部 出口是打开的,调节此口的开度,可以调节底流量与溢流量的比例,从而可使 几乎全部或仅使一部分微粒从底流中排出,使全部微粒从底流中排出并得到稠 厚浆液的操作,称为增稠;
2、旋风分离器的选用
旋风分离器由于其具有结构简单、制造方便、分离效率高,可处理高温气体等 优点,故在工业生产中广泛应用。为满足各种不同含尘物系的分离要求,已设 计和制造了多种型式的旋风分离器供选用。 我国生产的旋风分离器型号有 CLT、CLT/A、CLP/A、CLP/B 及扩散式等。上述 代号中 C 表示除尘器,L 表示离心式,A、B 为产品类别等,其详细尺寸及主要 性能可查有关资料及手册。选用旋风分离器的型式及主要尺寸的依据是:含尘 气体的性质、气体的处理量(主要指体积流量) 、要求的分离效率及其允许的压 力损失等。通常选用旋风分离器时应在高效率和低阻力之间进行权衡。 旋风分离器用以分离粒径为 5~200μm 的尘粒较为适宜。 大于 200μm 的颗粒应先 在降尘室中除去,以免旋风分离器磨损严重。小于 5μm 的颗粒,应在袋滤器或 湿式除尘器中捕集。
2、净化分散介质以获取纯净的气体或液体。
•
3、环境保护的需要 •
2.2气-固分离
2.2.1降尘室
2.2.2旋风分离器
2.2.1降尘室
降尘室是借重力沉降来分离气固非均相物系的设备。在重力场中,借连续相和分散相的密度差异使两 相得以分离。例如空气中的尘粒因受重力作用而降到地面,从而使尘粒从空气中分离出来。 最简单的设备形式有降尘气道如图 2-1 所示。降尘气道具有相当大的横截面积和一定的长度。当含尘 气体进入气道后,其流通面积增大,流速降低,使得灰尘在气体离开气道以前,有足够的停留时间沉 到室底而被除去。 图 2-2 为降尘室的示意图,含尘气体由气体入口进入降尘室后,气体中的尘粒一方面随着气流在水平 方向流动,其速度与气流速度 u 相同,另一方面在重力作用下以沉降速度在垂直方向向下运动。只要 含尘气体从降尘室入口到出口所需的停留时间等于或大于尘粒从降尘室的顶部沉降到底部所需的沉降 时间,尘粒即可被分离出来(即尘粒沉降在降尘室内不被带走) 。 降尘室的生产能力仅与其沉降速度 ut 和降尘室的沉降面积 A 有关,而与降尘室的高度无关。因此也可 将降尘室做成多层,如图 2-3 所示称为多层降尘室。室内以隔板均匀分成若干层,隔板间距为 40~100mm。