基于ABAQUS的煤油介质中电火花表面强化工艺参数的研究
电火花新加工技术及其发展趋势
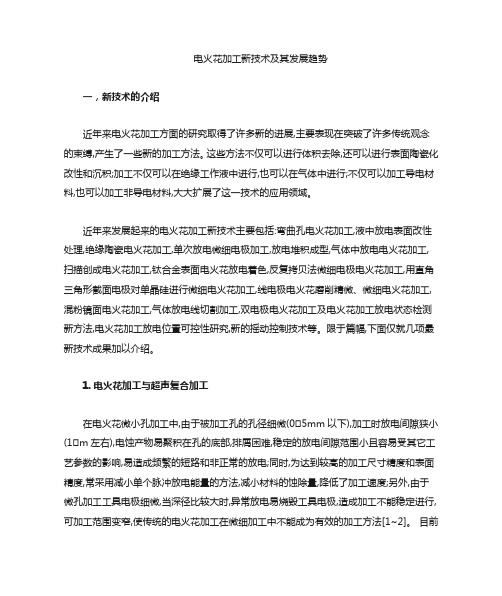
电火花加工新技术及其发展趋势一,新技术的介绍近年来电火花加工方面的研究取得了许多新的进展,主要表现在突破了许多传统观念的束缚,产生了一些新的加工方法。
这些方法不仅可以进行体积去除,还可以进行表面陶瓷化改性和沉积;加工不仅可以在绝缘工作液中进行,也可以在气体中进行;不仅可以加工导电材料,也可以加工非导电材料,大大扩展了这一技术的应用领域。
近年来发展起来的电火花加工新技术主要包括:弯曲孔电火花加工,液中放电表面改性处理,绝缘陶瓷电火花加工,单次放电微细电极加工,放电堆积成型,气体中放电电火花加工,扫描创成电火花加工,钛合金表面电火花放电着色,反复拷贝法微细电极电火花加工,用直角三角形截面电极对单晶硅进行微细电火花加工,线电极电火花磨削精微、微细电火花加工,混粉镜面电火花加工,气体放电线切割加工,双电极电火花加工及电火花加工放电状态检测新方法,电火花加工放电位置可控性研究,新的摇动控制技术等。
限于篇幅,下面仅就几项最新技术成果加以介绍。
1.电火花加工与超声复合加工在电火花微小孔加工中,由于被加工孔的孔径细微(0 5mm以下),加工时放电间隙狭小(1 m左右),电蚀产物易聚积在孔的底部,排屑困难,稳定的放电间隙范围小且容易受其它工艺参数的影响,易造成频繁的短路和非正常的放电;同时,为达到较高的加工尺寸精度和表面精度,常采用减小单个脉冲放电能量的方法,减小材料的蚀除量,降低了加工速度;另外,由于微孔加工工具电极细微,当深径比较大时,异常放电易烧毁工具电极,造成加工不能稳定进行,可加工范围变窄,使传统的电火花加工在微细加工中不能成为有效的加工方法[1~2]。
目前常采用的提高电火花加工能力的方法,如人工排气法,强迫冲液或抽液法、加速工作液循环等方法,常因加工条件或加工要求的限制而无法实现。
因此,为改善电火花加工性能,在微细加工中,采用超声电火花复合加工是非常有效的手段。
在电极上附加超声振动,就可以使电极端面频繁进入合适的放电间隙,提高火花击穿的概率;同时由于超声的空化作用和泵吸作用,可以增大被加工材料的去除量,加速工作液循环,改善间隙放电条件,从而提高被加工孔的深径比、加工稳定性、生产率和脉冲电源的利用率,并且在振幅得到良好控制的情况下,可以获得更高的加工精度。
2Cr3WMoV电火花加工表面质量的研究
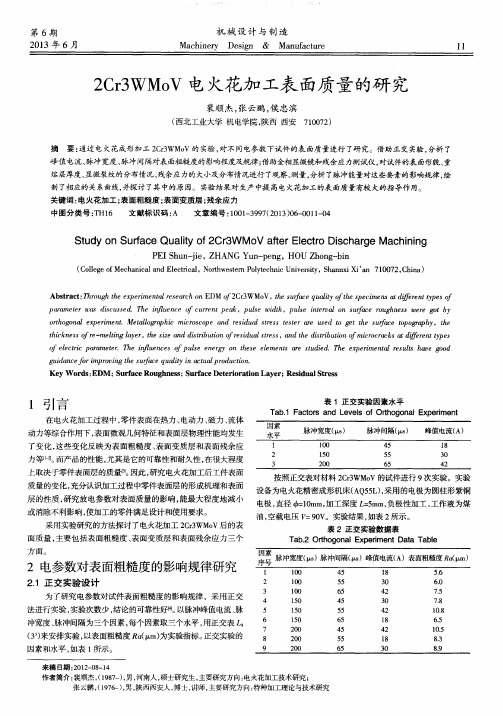
Ab s t r a c t : T h r o u g h t h e e x p e r i m e n t a l r e s e a r c h o n E D M o f2 C r 3 WMo V, t h e s u  ̄ C a c e q u li a t y ft o h e s p e c i m e n s a t d f i f e r e n t t y p e s f o p ra a et m e r 珊 d i s c u s s e d .T he i n lu f e n c e f o c u r r e n t p e a k ,p u l s e w i d t h ,p u l s e i n t e r v l a o n轧 锰e r o u g h n e s s w e r e g o t b y o r t h o g o n l a e x p e r i me n t .Me t ll a o g r a p h i c mi c r o s c o p e nd a r e s i d u l a s t r e s s t e s t e r r a e u s e d t O g e t t h e s u  ̄ a c e t o p o g r a p h y ,t h e t h i c k n e s s fr o e — m e l t i n g l a y e r , t h e s i z e a n d d i s t r i b u t i o n fr o e s i d u l a s t r e s s , nd a t h e d s i t r i b u t i o n fm o i c r o c r a c k s t a d i f f e r e n t t y p e s
浅析模具制造中的电火花加工
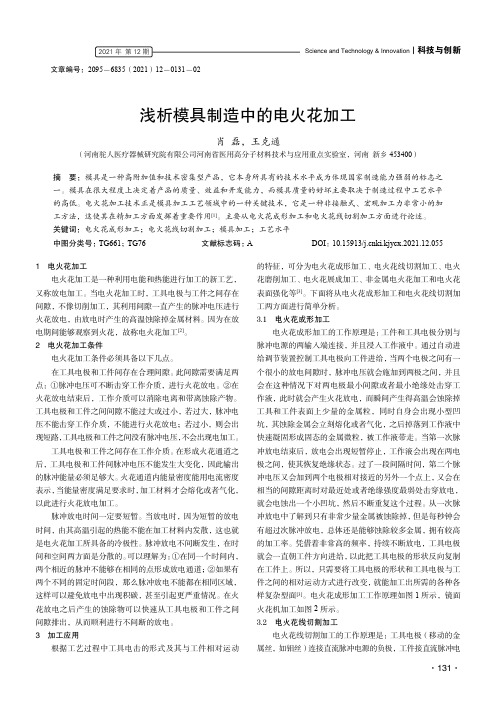
开,以期为该数据集的价值和影响力提供更多的支撑。 参考文献: [1]国家气象信息中心,湖北省气象局.QX/T 119—2010 气
象数据归档格式 地面[S].北京:气象出版社,2010. [2]国家气象信息中心.QX/T 93—2017 气象数据归档格式
影响材料放电腐蚀量(电蚀量)的因素有以下几个方面: ①电参数。通过调节各种电参数(脉冲宽度、脉冲频率和脉 冲能量等),可以改变电蚀量。如提高电流,可以加大电蚀 量。②极性效应。工具电极和工件使用相同的材料进行放电 加工,两者中一个被电蚀量一定比另外一个大,这就是极性 效应。当工具电极和工件使用不相同材料时,其极性效应更 大。③金属材料。当电参数相同时,工件材料的热学性能决 定着电蚀量,如果材料的比热容、熔点、热稳定性等越大, 其电蚀量越小。④工作液。在电火花加工中工作液被当作放 电介质,主要作用是冷却、排屑。常用的工作液具有黏度较 低、性能稳定等特点,如煤油、去离子水和乳化液等。 5.2 影响加工精度的因素
表 1 广东省审核气象历史资料专题库数据集说明信息
资料类别
资料名称
资料来源
时间和频率说明
站点范围
地面资料
广东历史审编资料 国家地面自动 气象站历史小时数据 广东历史审编资料 广东地面区域 自动气象站历史小时数据 广东历史审编资料 国家地面自动 气象站历史分钟数据
地面气象小时观测月报数据文件(A 文 件、A0 文件、A6 文件) 广东区域站地面气象小时观测月报数据 文件(DG 文件)
图 3 电火花线切割加工工作原理图
电火花线切割加工不需要单独制造电极,仅用一根电极 ·132·
第三讲__电火花加工

精密与特种加工
5)加工同样的工件,其总蚀除量少,材料利用率高,对 加工贵重金属有着重要意义。 6)线切割的缺点是不能加工盲孔类零件和阶梯成形表面。
HIGH EDUCATION PRESS
精密与特种加工
电火花线切割加工是在电火花加工基础上发展起来的一种加 工工艺(简称 WEDM )。其工具电极为金属丝(钼丝或铜丝), 在金属丝与工件间施加脉冲电压,利用脉冲放电对工件进行切 割加工,因而也称线切割。 1.电火花线切割加工的原理 电火花线切割加工的电蚀原理与电火花加工的原理相同, 其加工原理如图所示。 电火花线切割加工的基本设备是数控电火花切割机,它由 床身部分、坐标工作台部分(一般均采用十字和滚动导轨、滚 动丝杠)、走丝机构和锥度切割装置等主要部件组成。
提高加工速度途径
1)提高脉冲频率: 缩小脉冲停歇时间或压窄脉冲 宽度。 2)增加单个脉冲能量: 加大脉冲电流或增加脉冲 宽度,但会影响表面质量和加工精度,通常只用于 粗、半精加工之中。 3)提高工艺参数 :如合理选用电极材料、工作液 及放电参数,改善工作液循环过滤方式等,来有效 地提高脉冲利用率,以达到提高工艺参数的目的。 4)正确选择工件的极性: 窄脉冲加工选用正极性 加工(工件接脉冲电源的正极),而采用宽脉冲加 工时,采用负极性加工(工件接电源的负极)。
HIGH EDUCATION PRESS
精密与特种加工
(2) 表面变质层
放电痕剖面显示的表面变质层
HIGH EDUCATION PRESS
精密与特种加工
(3) 表面力学性能 应力:电火花加工后的工件表面易形成残余应 力,且大多为拉应力。 硬度:一般来说,电火花加工表面最外层的硬 度比较高,耐磨性好。 耐疲劳性能:采用回火、喷丸处理来降低残余 应力或者使残余拉应力转变为压应力。
2011年《电加工与模具》总目次

基 于 R 2 4的 电火 花 线 切 割 加 工 数 控 系 统 解 释 器 的 S7 设计与实现 ……… 陈成细, 学程 , 奚 徐 辉 , ( —8 等 2 )
杨晓冬 , 滕
庆( 6—7 )
一
76 一
信 息 ・ 态 动
基 于 IA总线 的电火花线切割机床接 口电路 的设计及研究 S
… … … … … … … …
第 十 二 届 中 国 国 际 机 床 展 览会 特种 加 工 机 床评 述 … … … …
… … … …
郭艳 玲 , 凯 译 , 宗生 , ( —2 ) 姜 辛 等 6 9
C MT 2 1 I 0 1特 种 加 工 机 床 评 述 专 家 组 ( —1 3 )
… … … … … … … … … …
《 电加工与 模具 21 年第6 》 01 期
重 掺 杂 硅 微 球 的脉 冲放 电法 制备 研 究 … … … … … … … … …
… … … … … … … …
钟孟辉 , 烈恩 , 郭 沈
川 ( —1 ) 2 2
一
洪
捐, 汪
炜 , 海娣 , ( —1 ) 冯 等 4 9
… … … … … … … … … …
李
龙, 叶
军 , 红 敏 , ( ~2 ) 朱 等 2 3
陈娟 烈 , 轧
刚, 常延 晓 ( 4—3 ) 0
毛 细 管 电 极 电液 束 加 工 微 小 孔试 验 研 究 … … … … … … … …
… … … … … … … …
有 限 元逆 算 法 在 汽 车 覆 盖 件 数 值 模 拟 成形 中 的 应用 … … …
… … … … … … … … … … … … … … … … …
课题一--电火花技术简要介绍

课题一电火花技术简要介绍一、电火花简介电火花技术,又称放电加工,日本叫法是Electrical Discharge Machining,简称EDM,苏联称电蚀加工,Electroerosion Machining,指利用两极间的脉冲放电产生的电腐蚀现象,对材料进行加工的方法。
电火花与机械加工的区别:机械加工是通过机床部件的相对运动,用比工件硬的刀具切除工件上多余的部分,来得到成品零件的;而电火花加工,工具与工件并不接触,靠工具和工件之间不断的脉冲性火花放电,产生局部的瞬间高温,把金属材料蚀除掉。
电火花腐蚀的主要原因是什么?火花放电时火花通道中瞬间产生大量的热,达到很高的温度,足以使任何金属材料局部熔化、气化而蚀除,形成放电凹坑,从而将金属材料腐蚀掉。
二、电火花的历史在插头或电器开关触点开、闭时,往往会产生火花而把接触表面烧毛,腐蚀成粗糙不平的凹坑而逐渐损坏,人们不断地避免这种有害的电腐蚀。
1940年,苏联学者拉扎连科夫妇开始研究发明电火花加工,之后随着脉冲电源和控制系统的改进,而迅速发展起来。
最初使用的脉冲电源是简单的电阻-电容回路。
50年代初,改进为电阻-电感-电容等回路。
同时,还采用脉冲发电机之类的所谓长脉冲电源,使蚀除效率提高,工具电极相对损耗降低。
随后又出现了大功率电子管、闸流管等高频脉冲电源,使在同样表面粗糙度条件下的生产率得以提高。
60年代中期,出现了晶体管和可控硅脉冲电源,提高了能源利用效率和降低了工具电极损耗,并扩大了粗精加工的可调范围。
到70年代,出现了高低压复合脉冲、多回路脉冲、等幅脉冲和可调波形脉冲等电源,在加工表面粗糙度、加工精度和降低工具电极损耗等方面又有了新的进展。
在控制系统方面,从最初简单地保持放电间隙,控制工具电极的进退,逐步发展到利用微型计算机,对电参数和非电参数等各种因素进行适时控制。
三、有害的火花放电转化为有用的加工技术的条件图1 电加工的示意图1、使工具电极和工件被加工表面之间保持一定的放电间隙,几微米-几百微米,不能间隙太小或太大,应具备工具电极的自动进给和调节装置。
第十章-模具表面强化技术

*
表面化学热处理技术
二、渗氮(氮化)
(一)气体渗氮
表2 部分模具钢的气体渗氮工艺规范
牌号
处理 方法
渗氮工艺规范
渗氮层 深度/mm
表面硬度
阶段
渗氮温度/℃
时间/h
氨分解率/%
30CrMnSiA
一段
—
500±5
25~30
20~30
0.2~0.3
(一)气体渗氮
(1) 经过渗氮后钢表面形成一层极硬的合金氮化物,渗氮层的硬度一般可达到68~72HRC,不需要再经过淬火便具有很高的表面硬度和耐磨层,而且还可以保持到600~650℃而不明显下降。
(2) 渗氮后钢的疲劳极限可提高15%~35%。这是由于渗氮层的体积增大,使工件表面产生了残余压应力。
(3) 渗氮后的钢具有很高的抗腐蚀能力。
>58HRC
Cr12MoV
760~800HV
*
表面化学热处理技术
二、渗氮(氮化)
(二)离子渗氮
离子渗氮有如下特点:
(1) 渗氮速度快,生产周期短。
(2) 渗氮层质量高。
(3) 工件的变形小。
(4) 对材料的适应性强。
氮碳共渗
提高硬度、耐磨性、抗粘附性、抗蚀性、耐热疲劳性
冷挤模、拉深模、挤压模穿孔针
渗硼
具有极好的表面硬度、耐磨性、抗粘附性、抗氧化性、热硬性、良好的抗蚀性
挤压模、拉深模
碳氮硼三元共渗
提高硬度、强度、耐磨性、耐疲劳性、抗蚀性
挤压模、冲头针尖
盐浴覆层 (TD处理)
提高硬度、耐磨性、耐热疲劳性、抗蚀性、抗粘附性、抗氧化性
基于ABAQUS的激光冲击金属表面强化
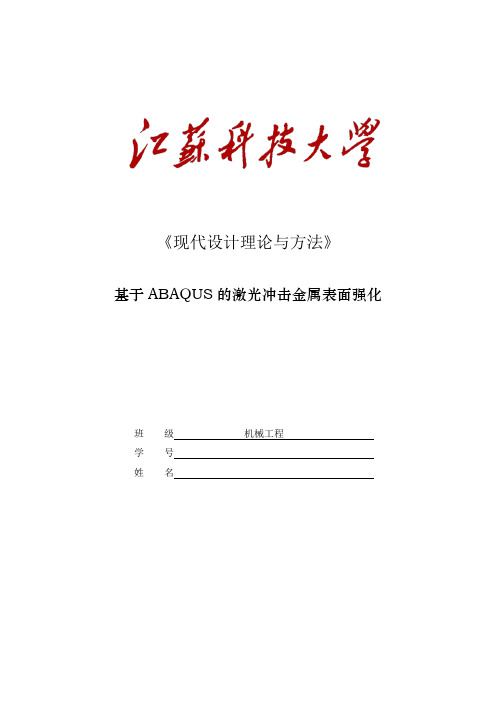
《现代设计理论与方法》基于ABAQUS的激光冲击金属表面强化班级机械工程学号姓名基于ABAQUS的激光冲击金属表面强化一、激光冲击金属表面强化的国内外现状金属材料的失效形式主要是于材料表面的疲劳、腐蚀和磨损,所以材料表面的结构和性能直接影响着材料的综合性能。
激光冲击强化是利用短脉冲( 一般在5 0s n以内)、高功率密度的激光通过透明约束层,作用于金属表面所涂覆或帖附的吸收层上,吸收层吸收激光能量后迅速气化。
形成稠密的高温、高压等离子体,该等离子体继续吸收激光能量后急剧升温膨胀,然后爆炸形成高强度冲击波作用于金属表面。
当冲击波的峰值压力超过材料的动态屈服强度时,材料发生塑性变形并在表层产生平行于材料表面的拉应力。
激光作用结束后,由于冲区域周围材料的反作用,其力学效应表现为材料表面获得较高的残余压应力。
激光冲击的研究可以追溯到1963年,White首先发现了激光诱发冲击波现象[5l,这一发现为激光冲击技术的应用拉开了序幕。
目前激光冲击强化在美国已历经三十多年的发展,技术逐渐成熟。
2000年以来,高能激光冲击强化技术研究水平有了新突破,应用领域有了新的拓展,其中一些成果受到世人瞩目。
利弗莫尔(livemore)实验室在YMP研究计划中进行了304不锈钢的耐腐蚀实验,证实激光冲击后的不锈钢试样耐腐蚀性能获得了极大提高。
高能束激光冲击技术可用于核废料储存容器焊缝的处理,以及改善核反应器的安全性与可靠性,延长反应器零件的工作时间,从而使沸水反应器和压力水反应器具有更长的服役时间和更低的运行成本。
日本东芝为了将激光冲击处理技术用于核反应堆中型芯零件和焊接构件焊缝的强化,专门设计了激光冲击伸缩强化头,可深入内壁实施强化。
我国对激光冲击处理技术的研究始于上世纪90年代。
中国科技大学、华中科技大学、南京航空航天大学等单位在这方面已做了大量的基础研究,但还没有工化应用。
1991年我国高功率(109w/cm2)激光装置通过鉴定,激光冲击强化的研究才真正开始。
《现代制造技术》思考题
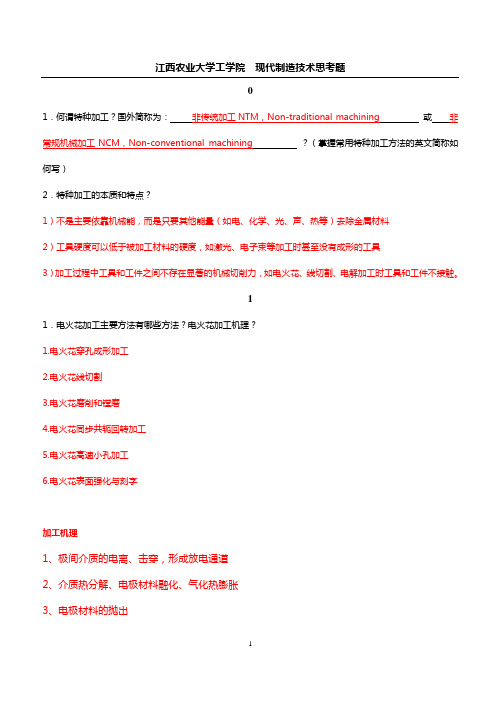
1.何谓特种加工?国外简称为:非传统加工NTM,Non-traditional machining或非常规机械加工NCM,Non-conventional machining?(掌握常用特种加工方法的英文简称如何写)2.特种加工的本质和特点?1)不是主要依靠机械能,而是只要其他能量(如电、化学、光、声、热等)去除金属材料2)工具硬度可以低于被加工材料的硬度,如激光、电子束等加工时甚至没有成形的工具3)加工过程中工具和工件之间不存在显著的机械切削力,如电火花、线切割、电解加工时工具和工件不接触。
11.电火花加工主要方法有哪些方法?电火花加工机理?1.电火花穿孔成形加工2.电火花线切割3.电火花磨削和镗磨4.电火花同步共轭回转加工5.电火花高速小孔加工6.电火花表面强化与刻字加工机理1、极间介质的电离、击穿,形成放电通道2、介质热分解、电极材料融化、气化热膨胀3、电极材料的抛出14、极间介质的消电离2.何谓电火花加工的极性效应?正极性加工和负极性加工各自适用于什么场合?加工中如何利用极性效应来提高加工效率降低工具损耗?~在电火花加工过程中,由于正、负极性不同而彼此电蚀量不一样的现象叫做极性效应。
~一般粗加工用负极性加工,精加工用正极性加工~一般在短脉冲精加工时采用正极性加工(即工件接电源正极),而在长脉冲粗加工时则采用负极性加工。
3.电火花加工的工作液有哪些作用?粗、精加工如何选择工作液有哪些作用?1)形成火花击穿放电通道,并在放电结束后迅速恢复间隙的绝缘状态2)对放电通道产生压缩作用3)帮助电蚀产物的抛出和排除4)对工具、工件产生冷却作用工作液的选择粗加工:介电性能、粘度较大的全损耗系统用油(即机油),且这种油燃点较高,大能量加工时着火燃烧的可能性小。
精加工:粘度小、流动性好、渗透性好的煤油作为工作液。
因为精加工时放电间隙比较小,排屑比较困难。
4.电火花加工的工艺范围如何?1)可以使用硬度不高的紫铜或石墨作工具电极,去加工任何硬,脆,韧,软和高熔点的导电材料;2)加工时工件与工具不接触,无切削力,因此适用加工薄壁,窄槽,低刚度及微细精密的零件;3)可以加工任何形状特殊,结构复杂的工件24)脉冲电源的参数可以任意调节,能在同一台机床上进行粗加工,半精加工或精加工。
特种加工(章 (2)

第2章 电火花加工
图2-1 电火花加工原理示意图
第2章 电火花加工
图2-2 放电间隙状况示意图 (a)放电间隙状况;(b)放电后的表面
第2章 电火花加工
2.2.2 电火花加工的形成条件 利用电火花加工方法对材料进行加工应具备以下条件: (1)作为工具和工件的两极之间要有一定的距离(通常
为数微米到数百微米),并且在加工过程中能维持这一距离。 (2)两极之间应充入介质。对导电材料进行尺寸加工时,
第2章 电火花加工
2.1.2 (1)适合于任何难切削导电材料的加工。由于加工中材料
的去除是靠放电时的电热作用实现的,因此材料的可加工性主 要取决于材料的导电性及其热学特性,如熔点、沸点、比热容、 导热系数、电阻率等,而几乎与其力学性能(硬度、强度等)无 关。这样可以突破传统切削加工对刀具的限制,可以实现用软 的工具加工硬韧的工件,甚至可以加工超硬材料。目前,电极 材料多采用紫铜或石墨,因此工具电极较容易加工。
(5)脉冲放电需要不断地多次进行,并且每次脉冲放电 在时间上和空间上是分散的、不重复的。即每次脉冲放电一般 不在同一点进行,避免发生局部烧伤。
(6)脉冲放电后的电蚀产物能及时排运至放电间隙之外, 使重复性脉冲放电顺利进行。
第2章 电火花加工
2.2.3 电火花加工的机理 火花放电时,电极表面的金属材料究竟是怎样被蚀除下来
第2章 电火花加工
电火花加工在各行业的应用主要表现在: (1)可直接加工各种金属及其合金材料、特殊的热敏感 材料、半导体和非导体材料。 (2)可加工各种形状复杂的型孔和型腔工件,包括圆孔、 方孔、多边形孔、异形孔、曲线孔、螺纹孔、微孔等。 (3)可加工深孔等型孔工件及各种型面的型腔工件。 (4)可进行各种工件与材料的切割,包括材料的切断, 特殊结构工件的切断,切割微细窄缝及微细窄缝组成的工件, 如金属栅网、异型孔喷丝板、激光器件等。
基于电火花加工方法的硅强化45钢工艺的研究
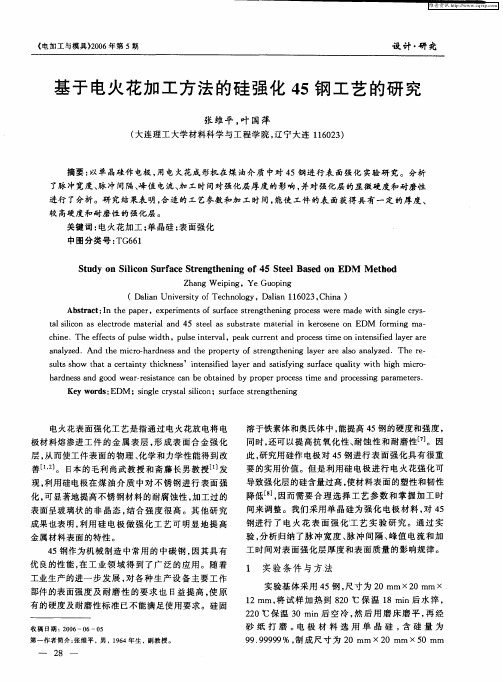
电火 花表面 强化 工艺 是指通 过 电火花放 电将 电 极材 料熔渗进 工 件 的金 属 表 层 , 成 表 面合 金 强化 形
摘要 : 以单 晶硅作 电板 , 用电 火花 成形机 在煤 油介 质 中对 4 5钢进 行 表 面强化 实验研 究。 分析
了脉 冲 宽度 、 冲 间隔 、 脉 峰值 电流 、 工 时间对强化 层 厚度 的影 响 , 对 强化 层 的显微硬 度 和 耐磨性 加 并
进行 了分析 。研 究 结果表 明 , 适 的工 艺参数 和加 工 时 间, 合 能使 工件 的表 面获得 具 有 一 定 的厚 度 、
维普资讯
< 电加工与模具)06 20 年第 5 期
设 计 ・ 究 研
基 于 电火 花 加 工 方法 的硅 强化 4 5钢 工 艺 的研 究
张 维 平 , 国 萍 叶
( 大连理 工 大学材料 科学 与工 程学 院 , 宁大 连 1 6 2 ) 辽 1 0 3
层, 从而使 工件表 面 的物理 、 化学 和力 学性能 得到 改 善[. 。 1本 的毛利 尚武 教授 和 斋藤 长男 教 授 [ 发 2 5 】 】
现, 利用硅 电极在 煤 油 介 质 中对 不 锈 钢进 行 表 材料表 面 的塑性和韧性 使 降低 [ 因而需 要 合理 选 择 工 艺 参 数 和掌 握 加工 时 引, 间来 调整 。我们 采用 单 晶硅 为 强化 电极 材料 , 4 对 5 钢进行 了 电火 花 表 面 强 化 艺 实 验 研 究 。通 过 实 工 验 , 析归 纳 了脉 冲 宽度 、 冲 间隔 、 值 电流 和加 分 脉 峰
煤油流量对HVOF_喷涂FeCrMoSi-Ti3SiC2_涂层高温摩擦磨损性能的影响
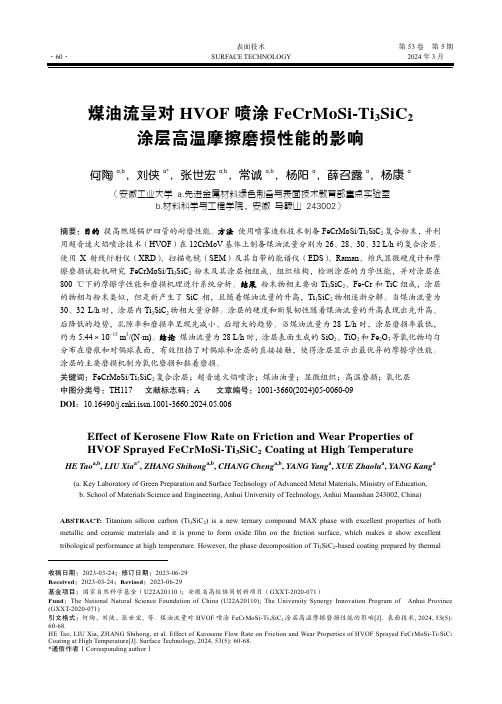
表面技术第53卷第5期煤油流量对HVOF喷涂FeCrMoSi-Ti3SiC2涂层高温摩擦磨损性能的影响何陶a,b,刘侠a*,张世宏a,b,常诚a,b,杨阳a,薛召露a,杨康a(安徽工业大学 a.先进金属材料绿色制备与表面技术教育部重点实验室b.材料科学与工程学院,安徽 马鞍山 243002)摘要:目的提高燃煤锅炉四管的耐磨性能。
方法使用喷雾造粒技术制备FeCrMoSi/Ti3SiC2复合粉末,并利用超音速火焰喷涂技术(HVOF)在12CrMoV基体上制备煤油流量分别为26、28、30、32 L/h的复合涂层。
使用X射线衍射仪(XRD)、扫描电镜(SEM)及其自带的能谱仪(EDS)、Raman、维氏显微硬度计和摩擦磨损试验机研究FeCrMoSi/Ti3SiC2粉末及其涂层相组成、组织结构,检测涂层的力学性能,并对涂层在800 ℃下的摩擦学性能和磨损机理进行系统分析。
结果粉末物相主要由Ti3SiC2、Fe-Cr和TiC组成,涂层的物相与粉末类似,但是新产生了SiC相,且随着煤油流量的升高,Ti3SiC2物相逐渐分解。
当煤油流量为30、32 L/h时,涂层内Ti3SiC2物相大量分解。
涂层的硬度和断裂韧性随着煤油流量的升高表现出先升高、后降低的趋势,孔隙率和磨损率呈现先减小、后增大的趋势。
当煤油流量为28 L/h时,涂层磨损率最低,约为5.44 ⨯ 10-15 m3/(N·m)。
结论煤油流量为28 L/h时,涂层表面生成的SiO2、TiO2和Fe2O3等氧化物均匀分布在磨痕和对偶球表面,有效阻挡了对偶球和涂层的直接接触,使得涂层显示出最优异的摩擦学性能。
涂层的主要磨损机制为氧化磨损和黏着磨损。
关键词:FeCrMoSi/Ti3SiC2复合涂层;超音速火焰喷涂;煤油油量;显微组织;高温磨损;氧化层中图分类号:TH117 文献标志码:A 文章编号:1001-3660(2024)05-0060-09DOI:10.16490/ki.issn.1001-3660.2024.05.006Effect of Kerosene Flow Rate on Friction and Wear Properties ofHVOF Sprayed FeCrMoSi-Ti3SiC2 Coating at High Temperature HE Tao a,b, LIU Xia a*, ZHANG Shihong a,b, CHANG Cheng a,b, YANG Yang a, XUE Zhaolu a, YANG Kang a(a. Key Laboratory of Green Preparation and Surface Technology of Advanced Metal Materials, Ministry of Education,b. School of Materials Science and Engineering, Anhui University of Technology, Anhui Maanshan 243002, China)ABSTRACT: Titanium silicon carbon (Ti3SiC2) is a new ternary compound MAX phase with excellent properties of both metallic and ceramic materials and it is prone to form oxide film on the friction surface, which makes it show excellent tribological performance at high temperature. However, the phase decomposition of Ti3SiC2-based coating prepared by thermal收稿日期:2023-03-24;修订日期:2023-06-29Received:2023-03-24;Revised:2023-06-29基金项目:国家自然科学基金(U22A20110);安徽省高校协同创新项目(GXXT-2020-071)Fund:The National Natural Science Foundation of China (U22A20110); The University Synergy Innovation Program of Anhui Province (GXXT-2020-071)引文格式:何陶,刘侠,张世宏, 等. 煤油流量对HVOF喷涂FeCrMoSi-Ti3SiC2涂层高温摩擦磨损性能的影响[J]. 表面技术, 2024, 53(5): 60-68.HE Tao, LIU Xia, ZHANG Shihong, et al. Effect of Kerosene Flow Rate on Friction and Wear Properties of HVOF Sprayed FeCrMoSi-Ti3SiC2 Coating at High Temperature[J]. Surface Technology, 2024, 53(5): 60-68.*通信作者(Corresponding author)第53卷第5期何陶,等:煤油流量对HVOF喷涂FeCrMoSi-Ti3SiC2涂层高温摩擦磨损性能的影响·61·spraying technology is easy to occur, which affects its performance and restricts its wide application in high temperature protection filed. The work aims to individually granulate Ti3SiC2 powder by spray granulation technique, and then investigate the effect of different kerosene flow rates on the coating phase structure and tribological properties at high temperature.Ti3SiC2 particles were ground by a vertical planetary ball mill and mixed with quantitative deionized water and binder to obtain Ti3SiC2 water-based slurry, and then spherical Ti3SiC2 powder was prepared by spray granulation technique. The 12CrMoV matrix square sample with the size of 20 mm × 20 mm × 5 mm was prepared by electric discharge wire cutting mechanism. Before spraying experiment, the matrix sample was roughened by sand blasting and cleaned by ultrasonic with alcohol. The composite coatings with kerosene flow rates of 26 L/h, 28 L/h, 30 L/h and 32 L/h were prepared on 12CrMoV matrix by supersonic flame spraying (HVOF) technology. The phase composition, microstructure of powder and coating were investigated with X-ray diffractometer (XRD), scanning electron microscope (SEM), energy spectrometer (EDS) and Raman spectrum. Vickers microhardness tester and high temperature friction wear testing machine were applied to test the mechanical properties and the tribological properties. Finally, the wear mechanism of the coating at 800 ℃ was analyzed.The results indicated that the powder phase was mainly composed of Ti3SiC2, Fe-Cr and TiC. The coating phase was similar to that of the powder, but a new SiC phase appeared. With the increase of kerosene flow, the Ti3SiC2 phase was gradually decomposed. When the kerosene flow was 30 L/h and 32 L/h, the Ti3SiC2 phase in the coating was decomposed a lot. The average microhardness of K-26, K-28, K-30 and K-32 coatings was 359HV0.3, 528HV0.3, 548HV0.3 and 485HV0.3, the fracture toughness was 3.75, 3.94, 4.65 and 3.95 MPa·m1/2, and the mean friction coefficient was 0.48, 0.45, 0.59 and 0.52, respectively. The hardness, fracture toughness and average friction coefficient of the four coatings all increased firstly and then decreased with the increase of kerosene flow. The porosity of coatings K-26, K-28, K-30 and K-32 was 1.03, 0.44, 0.31 and1.62, and the wear rates was 6.17⨯10-15, 5.44⨯10-15, 8.62⨯10-15 and 6.79⨯10-15 m3/(N·m), respectively. The porosity and wearrate of the four coatings decreased firstly and then increased with the increase of kerosene flow. In summary, when the kerosene flow rate was 28 L/h, the coating had higher MAX content, higher hardness and lower porosity, which ultimately resulted in the lowest coefficient of friction and wear rate.The K-28 coating retains a high content of MAX phase, and the oxides such as SiO2, TiO2 and Fe2O3 generated on the surface are evenly distributed on the surface of the wear scars and dual ball, effectively blocking the direct contact between the dual ball and the coating, which makes the coating show the most excellent tribological performance.KEY WORDS: FeCrMoSi/Ti3SiC2 composite coating; supersonic flame spraying; kerosene flow rate; microstructure; high temperature friction and wear; oxide layer目前我国发电方式仍以火力发电为主,但电站燃煤锅炉的高温防护问题一直是长期困扰行业的技术难题。
电火花加工科技论文

论文题目:电火花加工技术专业:机械设计制造及其自动化姓名: 王洪月电火花加工论文【摘要】电火花加工又称为放电加工(Electrical Discharge Machining,简称为EDM),是一种直接利用电能和热能进行加工的新工艺。
电火花加工技术作为特种加工领域的一门重要技术,本文从电火花加工的发展历程、基本原理、特点、加工规律、新技术进展等五方面入手加以论述。
【关键词】电火花加工的发展历程、基本原理、特点、规律、技术进展。
一、电火花加工技术的发展历程电火花加工是利用两极见脉冲放电时产生的电腐蚀现象,对材料进行加工的方法。
早在十九世纪,人们就发现了电器开光的触点开闭时,以为放电,使接触部位烧蚀,造成接触面的损坏。
这种放电引起的电极烧蚀现象叫做电腐蚀。
起初,电腐蚀被认为是有害的,为减少和避免这种有害的电腐蚀,人们一直在研究电副食产生的原因和防止的办法。
当人们掌握了它的规律之后,便创造条件,转害为益,把电腐蚀用于生产中。
研究结果表明,当两极产生放电的过程中,放电通道瞬时产生大量的热,足以使电极材料表面局部熔化或汽化,并在一定条件下,熔化或汽化的部分能抛离电极表面,形成放电腐蚀的坑穴。
二十世纪四十年代初,人们进一步认识到,在液体介质中进行重复性脉冲放电时,能够对导电材料进行尺寸加工,因此,创立了“电火花加工法”。
电火花加工技术作为特种加工领域的重要技术之一,最早应用于二战时期折断丝锥取出时的加工。
随着人类进入信息化时代,电加工技术取得了突飞猛进的发展,可控性更高,数字化程度更好。
在中国电火花加工技术起步稍晚。
根据中国的国情,实现电火花加工技术的原始创新是很困难的,只能采取引进消化吸收再创新的策略,因为这套系统集成了很多学科领域的知识,如计算机的软硬件、微电子、数控、电力半导体、机械技术、电气技术等,是多方面、多学科集成的产品,是比较复杂的高科技产品。
国内现在显然还没有一个能够独立进行原始创新的团队,因此注定要经历一个长时间痛苦的积淀过程,所以我认为中国的电火花技术创新之路别无选择。
电火花成形加工
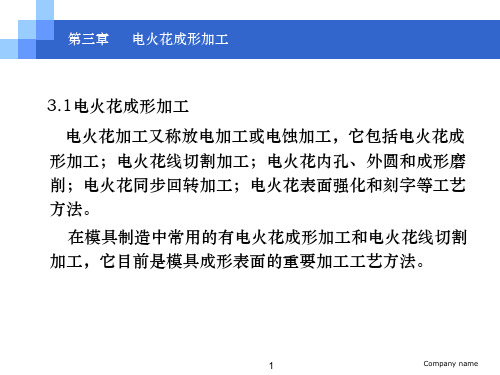
Company name
第三章 模具成形表面的特种加工 3.1 电火花成形加工
(二)电火花成形加工的机理 (2)能量的转换和传递
□ 能量的转换
两极间的介质一旦被击穿,电源就通过放电通道瞬时释 放能量,把电能转换为热能、动能、磁能、光能、声能和 电磁波辐射能等。 传递给电极上的能量是产生材料腐蚀的原因。
3.电火花加工的机理 (1) 液体介质电离、击穿和通道形成 (2) 能量的转换和传递 (3) 电蚀屑的抛出 (4) 间隙介质的消电离 放电结束,放电通道中的带电粒子复合为中性粒子, 电蚀产物及气泡的排除,介质恢复绝缘强度。
22
Company name
第三章 模具成形表面的特种加工 3.1 电火花成形加工
18
Company name
上节内容复习
这些熔化或汽化的金属在冷却为金属小颗粒(电蚀屑),然后被工 作液迅速冲离工作区,使电极和工件表面形成一个个微小的凹坑,同 时放电过程中,电压又随之迅速降为零,介质绝缘性能恢复,等待下 一次放电。 如此反复,电极不断下降,工件不断被蚀除,最后就在工件上复制 出了电极形状型腔内形,达到成形加工的目的。 电火花加工就是不断放电腐蚀金属的过程。
7
Company name
第三章 模具成形表面的特种加工 3.1 电火花成形加工
电火花成形加工必须采用脉冲电源
脉冲宽度 加到工件和工具电极上放电间隙两端电压脉冲持续时间 t 称 为脉冲宽度。脉冲宽度 t 应小于0.OOls 。 脉冲间隔 相邻两个电压脉冲间隔时间 t0称为脉冲间隔。 0 脉冲周期 脉冲宽度t和脉冲间隔t0之和称为脉冲周期T T=t+t0。 峰值电压 工件和工具电极间隙开路时电极间的最高电压ui称为峰 值电压,它等于电源的直流电压。 峰值电流 工件和工具电极间隙火花放电时脉冲电流瞬间的最大值i称 为峰值电流,它是影响加工速度和表面粗糙度的重要参数。 直流脉冲电源
第五单元电火花加工-05电参数设定

所需的热量。
电参数设定
3、工作液对加工速率的影响
• 绝缘性高、密度大、粘性大的工作液,有利于 压缩放电通道,提高放电电流强度,强化电蚀 产物的抛出效应。
• 粘度大不利于电蚀产物的排出,影响正常放电。 采用粘度小、流动性好、渗透性好的煤油或电 火花加工专用油。
模具制造技术
电参数设定
空载电压 峰值电流 脉冲宽度 脉冲间隔
电规准
电火花加工所使用的 一组电参数。
电参数设定
• 在电火花加工过程中,单个脉冲的蚀除量与单个 脉冲能量在一定范围内成正比关系:
Vi = K W
Vi —单个脉冲蚀除量 W—单个脉冲能量 K —工艺系数
电参数设定
加工速率公式
VV =60 f Vi λ
对于脉间宽度,粗加工时一般取脉冲宽度的1/5 ~ 1/10, 精加工时取脉冲宽度的2-5倍。
电参数设定
影响加工速度的其他因素
1.极性效应对加工速率的影响
1)极性效应:在电火花加工过程中,无论是正极还是负极,都 会受到不同程度的电蚀,即使是相同材料,正负电极的电蚀量 也是不同的。这种由于正负极性不同而电蚀量不一样的现象叫 做极性效应。 2)正极性加工:把工件接脉冲电源正极时的加工。 3)负极性加工:把工件接脉冲电源负极时的加工。
VV :加工速率,mm3/min; Vi :单个脉冲放电的蚀除量,mm3; f :放电频率,s-1; λ: 有效脉冲利用率,%。
电火花的加工速率,正比于脉冲放电频率和单个间电压U、放电电 流I和脉冲宽度ti。
单个脉冲能量与脉冲电流幅值Ii和脉冲宽度 ti成正比。
电参数设定
加工极性选择
• 采用短脉冲时(ti<20μs): 选择正极性加工——工件接阳极(正极)。
电火花加工的优势

电火花加工的发展、特点及应用摘要:电火花加工是与机械加工完全不同的一种新工艺。
随着工业生产的发展和科学技术的进步,具有高熔点、高硬度、高强度、高脆性,高粘性和高纯度等性能的新材料不断出现。
具有各种复杂结构与特殊工艺要求的工件越来越多,这就使得传统的机械加工方法不能加工或难于加工。
因此,人们除了进一步发展和完善机械加工法之外,还努力寻求新的加工方法。
电火花加工法能够适应生产发展的需要,并在应用中显示出很多优异性能,因此,得到了迅速发展和日益广泛的应用。
关键字:电火花加工的发展史;优势与局限;难加工材料;应用;The development of electric spark machining, characteristics andapplicationsAbstract:Electrical discharge machining is and mechancal processing completely different is a new technology. With the development of the industrial production and the progress of science and technology, has the high melting point, high hardness, high strength, high brittleness, high viscosity and high purity properties of the new material appear constantly. With all kinds of complicated structure and special process requirements of the workpiece is more and more, this makes the traditional mechanical processing method can't processing or difficult to machining. Therefore, people in addition to further develop and perfect mechanical processing method, but also to seek for the new processing method. Electrical discharge machining method can adapt to the needs of the development of production, and in the application of shows a lot of excellent performance, therefore, obtained the rapid development and wide application.Key words: The history of the development of the EDM;superiority and limitations;Difficult to machine materials;Application1.引言:电火花加工是利用浸在工作液中的两极间脉冲放电时产生的电蚀作用蚀除导电材料的特种加工方法,又称放电加工或电蚀加工,英文简称EDM。
电火花表面强化技术

2
电火花加工的条件
▪ 使工具电极和工件被加工表面之间保持一定的间隙 (几um到几百um)。间隙过大,极间电压不能击 穿极间介质,不会产生电火花;间隙过小,容易形 成短路接触,也不能产生火花放电。必须有工具电 极的自动进给和调节装置
▪ 火花放电必须是瞬时的脉冲放电,放电产生的热量 来不及传导扩散到其余部分,否则像电弧放电那样 会使表面烧伤而无法采用脉冲电源
▪ 火花放电必须在有一定绝缘性能的液体介质中进行 (煤油,去离子水等),液体介质还能把放电过程 产生的金属小屑、炭黑等电蚀产物从放电间隙中悬 浮出来,对电极表面有较好的冷却作用。
▪ 工具电极材料的转移:工具电极的材料接触转移到 工件金属熔融表面,一些金属合金元素(W/Ti/Cr) 迅速扩散在金属的表面层。
5
3
金属电火花表面强化
▪ 通过电火花放电的作用把一种导电材料涂敷 熔渗到另一种导电材料的表面,从而改变后 者的表面物理、化学性能。
▪ 例如把硬质合金等材料涂敷在用碳素钢制成 的各类模具、刀具、量具及机械零件表面, 可以提高其表面硬度(HV1100~1200,相当于 HRC70~72)
4
电火花表面强化的物理化学过程
▪ 超高速淬火:电火花放电使工件表面极小面积的金 属被加热到高温,熔化或部分气化,而放电时间很 短暂,被加热的金属周围有大量的冷金属,冷速很 快。
▪ 渗氮;放电区域内温度很高,空气中的氮分子呈原 子状态,与熔化的金属中的一些元素形成氮化物 (氮化铁、氮化铬等)
▪ 渗碳:石墨电极或周围介质的碳元素,溶解在加热 而熔化的铁中,形成金属碳化物(碳化铁、碳化铬)
电火花表面强化技术及其应用

电火花表面强化技术及其应用摘要: 电火花表面强化技术是一种具有独特优势的材料表面技术,其在机械零件表面改性和表面修复等方面具有广阔的应用前景。
介绍了电火花表面强化技术的基本原理和工艺特点,阐述了电火花表面强化技术的发展概况,分析了该技术在机械零部件修复、模具强化等方面的实际工程应用,指出了该技术今后的研究方向和发展趋势。
关键词: 电火花表面强化表面改性修复(一)电火花表面强化技术的基本原理与特点电火花表面强化技术的基本原理是储能电源通过电极以10 ~2000Hz 的频率在电极与零部件之间产生火花放电,在10-6~10-5( s) 内电极与零部件接触的部位即达到5000 ~10000℃的高温,使该区域的局部材料熔化、气化或等离子体化,将电极材料高速过渡并扩散到工作表面,形成冶金结合型牢固强化层。
研究表明,强化层主要由白亮层、扩散区和热影响区构成,涂层组织较细密,具有较高硬度及较好的耐高温性、耐腐蚀性和耐磨性。
电火花表面强化技术能有效地改善零部件表面的物理、化学和机械性能,包括硬度、导热和导电性能等,与常规表面强化工艺相比较,具有以下优点。
( 1) 电火花强化是在空气中进行,不需要特殊、复杂的处理装置和设备。
配套装置简单、灵活,投资和运行费用低,强化工艺环保。
( 2) 热输入量小,放电时间很短,放电端点的面积小,放电的热作用只发生在零部件表面的微小区域内,被强化零部件基体不产生退火或热变形。
( 3) 不受零部件形状限制,可以对平面或曲面形状零部件强化; 对需修复局部、有少量损伤、焊接性差以及淬火状态工件的修复更具优势。
( 4) 强化层是电极和零部件材料在放电时的瞬间高温高压条件下重新合金化形成的新合金层,结合非常牢固,不易发生剥落。
( 5) 强化层厚度、表面粗糙度与脉冲电源的电气参数以及强化时间等有关,控制相对简单。
电火花强化处理后可作为最终工序,加工余量少。
( 6) 电极材料来源广,耗量小,容易实现异种材料强化层,同时可以根据强化目的选择电极材料。
- 1、下载文档前请自行甄别文档内容的完整性,平台不提供额外的编辑、内容补充、找答案等附加服务。
- 2、"仅部分预览"的文档,不可在线预览部分如存在完整性等问题,可反馈申请退款(可完整预览的文档不适用该条件!)。
- 3、如文档侵犯您的权益,请联系客服反馈,我们会尽快为您处理(人工客服工作时间:9:00-18:30)。
织结构 、 性能测 试 和设 备研 制等方 面 , 已有较 多的研 究 成果 , 对 电火 花强 化 过程 中火 花放 电 的温度 场 但
属 的表 面进行 强化 。 已知 峰值 电流和脉 宽在单 脉 冲
面强化的 热传 导模 型 。在 此基 础上 , 用 A A 利 B QUS有 限元 分析 系统 , 拟 了煤 油介 质 中电 火花 表 模
面强化 的单脉 冲瞬 态温度场 , 究 了电流 增 大对 温度 场的影响 , 对单脉 冲条件 下的 工具 电极和 工 研 并 件在 不 同峰 值 电流 下的温度 场进行 数值模 拟 , 测 了电火花表 面 强化的 X 艺参数 。 预 - 关键词 :电火花 表面强 化 ; 温度 场 ; 艺参 数 ; B 工 A AQU S
S n c a , h n n u , n u j o gXi o Z a gJa h a Do gCh n h i i e (S a d n iest Jn n2 0 6 , ia) h n o g Unv ri a 5 0 Chn y,i 1
Ab t a t s r c :By s lc i g pr p rh a —o c d la d t e t e ma o n a y c n to n ime e ee tn o e e ts ure mo e n h h r lb u d r o diin a d da tr
A BAO U S
电火花 表面 强化工艺 是利用 高 能量密度 的脉 冲 放 电对 工件表 面进 行 强 化处 理 , 过 脉 冲火 花 放 电 通 作用将 电极材料 熔 渗 进金 属 工 件 的表 层 , 成 合金 形 化的表 面强化层 , 而使 工 件 的物 理化 学 和 力 学性 从 能得到 改善… 。 电火花表 面强化 工艺具有 可处 理 复 杂 零 件 、 化 层 硬 度 适 当 、 产 成 本 低 等 诸 多 优 硬 生 点 。工件经 电火 花 表 面强 化 后 , 强化 层 与 基 体 材
tr r rdce t esweep e itd wi FEM to n h meh d a dABAQUS sfwae ot r .
Ke wo d y r s: ee tia dic r e u f c modfc to lc rc l s ha g s r a e iia in;t e ma fed;p o e sn p r me e s h r l il rc sig a a tr ;
中 图分 类 号 : G 6 T 61 文献 标识码 : A 文 章 编 号 :0 9—2 9 2 1 ) l 0 6 5 10 7 X( 0 1o 一0 0 —0
Ree r h o h r c sig P r mee so sa c n te P o esn a a tr fEDC i r sn sd o AQUS n Keo e eBae n AB
料 的结 合 非 常 牢 固 , 会 发 生 剥 落 , 件 不 会 退 火 和 不 工
特 性 研 究 较 少 。 由 于 放 电 过 程 是 一 个 相 当复 杂主要 是 以热能 的形 式熔 放 化、 汽化 工件 和工 具 电极 材 料 , 有温 升 快 、 度 高 具 温 的特点 , 因此采 用实 验 方 法很 难 获 得 放 电过 程 中温 度场 的分 布 。本文 利用有 限元数 值模 拟方法 对 电火 花表 面强化 单 脉 冲 瞬态 温 度 场 特 性 进 行 了仿 真分 析, 为进 一步 优化 强化 工 艺 提供 理 论 依据 和 扩 大该
o s h r e c nn 1 a he t c d c in m o e f ED M u f c fdic a g ha e , a on u to d lo s ra e modfc to n iia in i Ke o e a u l, r s ne w s b i t b s d o h c het a se h r a il fsn l le wa nay e a e n w ih t r n intt e m lfed o i g epus s a l z d. Th h r a il ft o lc e t e m lfed o o l e — e t o n o k e ewa n lz d w ih d fe e u r nt nd rsn e p lea hep o e sn a a e r de a d w r pic sa a y e t if r ntc r e su e igl u s nd t r c s i g p r m —
工艺 的应用 领域提供 条件 。
变形 。强化后 微观 形貌如 图 1 示 。 所
电 火 花 表 面 强 化 技 术 在 强 化 机 理 、 化 层 的 组 强
煤 油 中的 电火 花 表 面 强化 主 要 是 通 过 S 工具 i 电极在 z轴 方 向进 给 , 接利 用 高 密度 电能 量 在金 直
《 Jr与模具}01 电}a u 2 1 年第 1 期
设 计 ・ 究 研
基于 A A B QUS的 煤 油 介 质 中 电火 花 表 面 强 化 工 艺 参 数 的 研 究
宋 夕超 , 张建 华 , 董春 杰
(山东大学 机械 工程学 院 , 山东 济南 2 0 6 5 0 1)
摘要 : 选取合 适的 热源模 型 、 边界条件 和放 电通 道 半径 公 式等 , 立 了煤 油介 质 中电 火花 表 热 建