国内化工设备制造技术发展论述
石油化工工艺设备现状及发展趋势分析
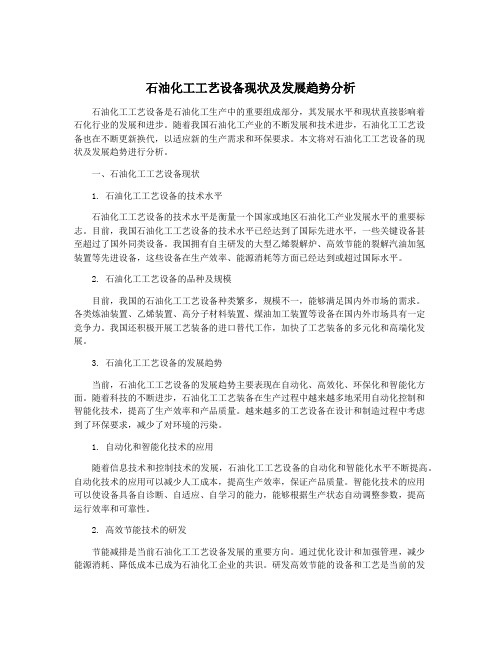
石油化工工艺设备现状及发展趋势分析石油化工工艺设备是石油化工生产中的重要组成部分,其发展水平和现状直接影响着石化行业的发展和进步。
随着我国石油化工产业的不断发展和技术进步,石油化工工艺设备也在不断更新换代,以适应新的生产需求和环保要求。
本文将对石油化工工艺设备的现状及发展趋势进行分析。
一、石油化工工艺设备现状1. 石油化工工艺设备的技术水平石油化工工艺设备的技术水平是衡量一个国家或地区石油化工产业发展水平的重要标志。
目前,我国石油化工工艺设备的技术水平已经达到了国际先进水平,一些关键设备甚至超过了国外同类设备。
我国拥有自主研发的大型乙烯裂解炉、高效节能的裂解汽油加氢装置等先进设备,这些设备在生产效率、能源消耗等方面已经达到或超过国际水平。
2. 石油化工工艺设备的品种及规模目前,我国的石油化工工艺设备种类繁多,规模不一,能够满足国内外市场的需求。
各类炼油装置、乙烯装置、高分子材料装置、煤油加工装置等设备在国内外市场具有一定竞争力。
我国还积极开展工艺装备的进口替代工作,加快了工艺装备的多元化和高端化发展。
3. 石油化工工艺设备的发展趋势当前,石油化工工艺设备的发展趋势主要表现在自动化、高效化、环保化和智能化方面。
随着科技的不断进步,石油化工工艺装备在生产过程中越来越多地采用自动化控制和智能化技术,提高了生产效率和产品质量。
越来越多的工艺设备在设计和制造过程中考虑到了环保要求,减少了对环境的污染。
1. 自动化和智能化技术的应用随着信息技术和控制技术的发展,石油化工工艺设备的自动化和智能化水平不断提高。
自动化技术的应用可以减少人工成本,提高生产效率,保证产品质量。
智能化技术的应用可以使设备具备自诊断、自适应、自学习的能力,能够根据生产状态自动调整参数,提高运行效率和可靠性。
2. 高效节能技术的研发节能减排是当前石油化工工艺设备发展的重要方向。
通过优化设计和加强管理,减少能源消耗、降低成本已成为石油化工企业的共识。
现代化工生产技术的发展现状

现代化工生产技术的发展现状随着现代化的进一步发展,化工生产技术也在不断地进行创新和改进,以适应社会和市场的需求。
新的技术手段和新的设备进入了化工生产领域,使得生产效率和质量都得到了大幅提升。
本文将就现代化工生产技术的发展现状进行探讨,包括新技术的应用、新设备的应用、生产流程的改进等方面。
一、新技术的应用1.1 人工智能技术人工智能技术是近年来化工生产领域中最引人注目的技术之一。
它可以帮助企业实现自动化生产,提高生产效率和生产质量。
通过使用人工智能技术,生产过程可以自己调节生产设备,并且可以根据物料合成情况智能调整反应参数。
目前,人工智能技术广泛应用于化工生产的各个领域,包括石油化工、金属加工、半导体制造、生物工程等。
1.2 超声波技术超声波技术是一种高效、低成本的清洗技术。
超声波振动可以形成大量的气泡,这些气泡瞬间破裂,产生高压和高温,使化学反应加速。
通过将超声波技术应用到制备化学品中,可以减少反应时间、降低反应温度、提高反应效率。
1.3 生物技术随着生物工程技术的发展,生物技术在化工生产领域越来越重要。
生物技术可以将生物质转化为有用的产品,减少首层物质的使用。
同时,生物技术可以改善产品的质量,并提高产品的市场竞争力。
二、新设备的应用2.1 压力波发生器压力波发生器是一种新型的化学设备,它可以在液体中产生高频、高能的压力波。
这些压力波可以促进化学反应的进行,加速反应过程。
在化工生产中,压力波发生器已经广泛应用于化学合成、材料制备、液体喷雾等领域。
2.2 泡沫床反应器泡沫床反应器是一种新型的化学反应器,采用泡沫床来替代传统的液态反应器。
因为泡沫床的气相和液相的界面面积很大,使得催化剂与反应物之间的接触频率增加,从而提高了反应速率和效率。
同时,泡沫床反应器的温度控制和气体互换比传统液态反应器更加稳定。
三、生产流程的改进3.1 焚化技术焚化技术是一种与传统技术相比更加环保的处理废弃物的方法。
这种技术采用高温和高压的环境,将有害物质转化为可回收的资源,同时减少有害气体的排放。
化工设备设计技术现状及发展趋势核心思路

科学论坛幸福生活指南152幸福生活指南化工设备设计技术现状及发展趋势核心思路薛保安南京中特检测研究院有限公司 江苏 南京 210000摘 要:随着我国科学技术的不断发展,我国各工业的生产模式都发生了很大的改变,不断地进行改革、发展,从只注重经济效益的思想逐渐转变为重视生态效益和经济效益的协调发展。
极大地促进了我国的社会经济发展。
本文主要了解了我国化工设备设计技术的发展现状,进而阐述了化工设备技术的发展趋势。
关键词:化工设备;设计技术;发展现状;发展趋势近年来,工厂产业已成为我国重要的经济支柱之一,创造了丰富的就业机会,为国民生活质量提升,幸福感上涨起到了积极影响。
化工设备是工厂生产的必备工具,对生产效率提升,产业发展走势有着重要影响。
因此,各个产业一定要重视化工设备技术的发展,确保企业的持续稳定发展。
一、我国化工设备设计技术的发展现状 我国的化工生产设备经历了漫长的发展,在20世纪60年代,由于生产规模的不断扩大,使化工设备的需求量不断增加,成为众多产业的必需品,化工设备的设计人员也为满足广大生产者的需要,编制了规范的工艺程序和通用设计。
到了 80 年代, 设备设计人员又从实际生产入手,优化了设备技术、材料等方面进一步加强了创新,不但提高了设备生产效率还提升了其安全性。
到了90 年代,计算机技术的普及,又一次推动了设备生产改革,再次丰富了设备使用用途,增加了其工厂使用范围。
到现在,化工设备技术已经往最高层次开始发展,逐渐向模拟设计和科学仿真方向过渡。
二、化工设备技术的发展趋势 目前,我国石化企业的发展突飞猛进,其工业总产值也升至一个新的层面,石化工业GDP 也在国民经济中不断上升,不论是在经营管理方面还是在技术革新上都朝着智能化、一体化的方向开始发展。
同时,计算机技术的发展也有了巨大的突破,在科学仿真技术、三维实体设计等方面取得了骄人的成绩,带动了各行各业的数字化改革。
所以,我国化工设备设计也也顺应时代发展,结合现代化技术朝更多元、便捷方向发展。
石油化工工艺设备现状及发展趋势分析
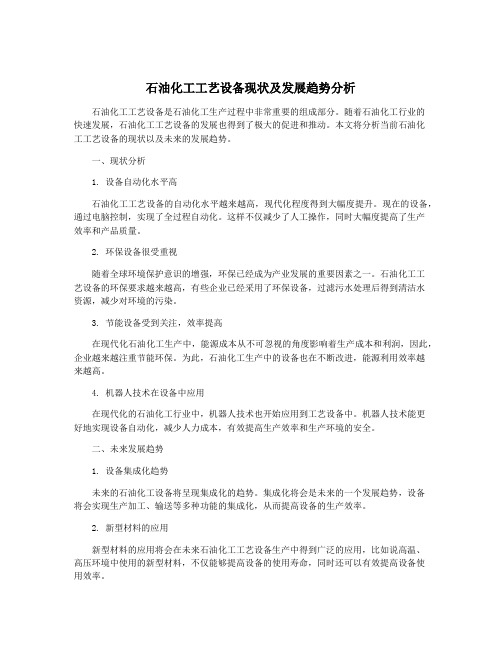
石油化工工艺设备现状及发展趋势分析石油化工工艺设备是石油化工生产过程中非常重要的组成部分。
随着石油化工行业的快速发展,石油化工工艺设备的发展也得到了极大的促进和推动。
本文将分析当前石油化工工艺设备的现状以及未来的发展趋势。
一、现状分析1. 设备自动化水平高石油化工工艺设备的自动化水平越来越高,现代化程度得到大幅度提升。
现在的设备,通过电脑控制,实现了全过程自动化。
这样不仅减少了人工操作,同时大幅度提高了生产效率和产品质量。
2. 环保设备很受重视随着全球环境保护意识的增强,环保已经成为产业发展的重要因素之一。
石油化工工艺设备的环保要求越来越高,有些企业已经采用了环保设备,过滤污水处理后得到清洁水资源,减少对环境的污染。
3. 节能设备受到关注,效率提高在现代化石油化工生产中,能源成本从不可忽视的角度影响着生产成本和利润,因此,企业越来越注重节能环保。
为此,石油化工生产中的设备也在不断改进,能源利用效率越来越高。
4. 机器人技术在设备中应用在现代化的石油化工行业中,机器人技术也开始应用到工艺设备中。
机器人技术能更好地实现设备自动化,减少人力成本,有效提高生产效率和生产环境的安全。
二、未来发展趋势1. 设备集成化趋势未来的石油化工设备将呈现集成化的趋势。
集成化将会是未来的一个发展趋势,设备将会实现生产加工、输送等多种功能的集成化,从而提高设备的生产效率。
2. 新型材料的应用新型材料的应用将会在未来石油化工工艺设备生产中得到广泛的应用,比如说高温、高压环境中使用的新型材料,不仅能够提高设备的使用寿命,同时还可以有效提高设备使用效率。
3. 智能化设备的推广智能化是未来石油化工设备的一个趋势。
智能化能够提供更好的生产效率和更佳的生产环境,同时也能够降低人员操作误差,避免生产过程中的安全事故,从而提高设备的生产效率和安全性。
4. 环保设备的发展随着全球环保意识的加强,未来的石油化工工艺设备将会更加关注环保,并且进一步提高设备的环保标准和环保技术。
浅谈化工机械工业的高新技术进展

浅谈化工机械工业的高新技术进展一、化工机械技术发展的必要性化工机械完善到何种程度在很大程度上决定着化工产品的质量和成本。
而化工机械作为化工行业生产工具,它自身的特点决定了它必须能适应高温、高压、易燃、易爆以及强腐蚀性等特殊外在条件。
而近代化学工业要求化工机械能够连续运转并且安全可靠,机械强度高,具有耐腐蚀,密封性好,高效低能等特性。
化工机械是生产化学制剂和化学制品必不可少的工具。
化工机械涉及的能量形式多,而且这些能量之间的交换和转换十分繁复,运行工况域比较宽大,操作参数非同一般,能充分适应不同产品的化学性质。
二、高新技术在化工机械中的应用1.复合材料化工机械零部件的磨损是伴随摩擦而产生的,它是两个相对运动的机械零部件表面材料在使用过程中不断分离和消耗的过程。
值得注意的是,磨损并不是机械材料自身固有的性质,它与机械的运行条件紧密相关。
准确说来,磨损与整个机械系统都有关。
影响化工机械磨损的因素主要分为工作状况、组成材料、几何形状和环境条件。
金属复合材料具有较高效率、功能繁多、成本低廉等特性,应用范围十分广泛。
我国在复合材料的开发研制方面具有一定基础。
随着社会的发展,当单一物质材料已不能满足生产、生活中的要求时,人们自然会想到通过组合两种或更多种的物质,改善材料的结构、成分来满足现实社会的各种需求,因此,复合材料的研究越来越受到人们的普遍关注。
复合材料的共同特点是综合各种组成材料的优点合而为一,使这种新材料具有多种性能。
这种材料可以依照需要的性能来选材、设计和制造。
复合材料能够制成任意形状,其优于其它材料的特点在于复合材料的性能组合性;物理性能与其它各种单质材料相匹配性;各组分间“扬长补短”性。
既弥补了之前单一材料存在的性能漏洞,又会产生组合后的新功能。
2.特种涂料及其制品随着机械化生产的发展进程的不断加速,化工机械已经作为推动生产力发展的必不可少的工具而广泛用于房地产建设行业、汽车生产加工行业、石油开采应用行业、电子电气工业等。
2024年化工设备市场发展现状
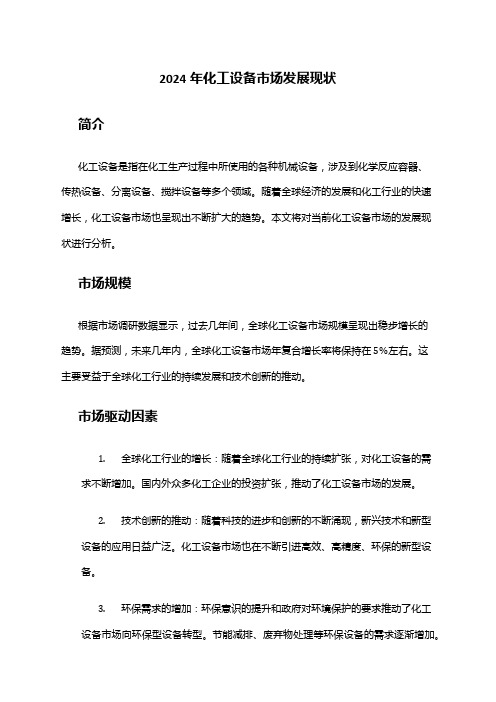
2024年化工设备市场发展现状简介化工设备是指在化工生产过程中所使用的各种机械设备,涉及到化学反应容器、传热设备、分离设备、搅拌设备等多个领域。
随着全球经济的发展和化工行业的快速增长,化工设备市场也呈现出不断扩大的趋势。
本文将对当前化工设备市场的发展现状进行分析。
市场规模根据市场调研数据显示,过去几年间,全球化工设备市场规模呈现出稳步增长的趋势。
据预测,未来几年内,全球化工设备市场年复合增长率将保持在5%左右。
这主要受益于全球化工行业的持续发展和技术创新的推动。
市场驱动因素1.全球化工行业的增长:随着全球化工行业的持续扩张,对化工设备的需求不断增加。
国内外众多化工企业的投资扩张,推动了化工设备市场的发展。
2.技术创新的推动:随着科技的进步和创新的不断涌现,新兴技术和新型设备的应用日益广泛。
化工设备市场也在不断引进高效、高精度、环保的新型设备。
3.环保需求的增加:环保意识的提升和政府对环境保护的要求推动了化工设备市场向环保型设备转型。
节能减排、废弃物处理等环保设备的需求逐渐增加。
4.区域经济发展不平衡:全球化工设备市场受到各区域经济发展的不平衡影响,市场需求呈现出一定的分化趋势。
发展中国家市场潜力巨大,而成熟市场则呈现出一定的饱和状态。
市场前景1.化工设备行业竞争激烈:随着市场规模的增大,化工设备行业竞争也日益激烈。
企业需要通过技术创新、产品优势等方面来提升竞争力。
2.智能化和自动化趋势:随着信息技术的快速发展,化工设备市场也在朝着智能化和自动化方向发展。
智能化设备和自动化生产线的应用正在成为市场的新趋势。
3.产业结构调整:在市场竞争的压力下,化工设备行业将面临一系列的结构调整。
专业化、特色化的产品将受到市场的追捧。
4.地区市场的差异化:由于区域经济的差异,不同地区的化工设备市场呈现出差异化的特点。
企业需根据市场需求,制定相应的市场拓展策略。
总结化工设备市场在全球范围内呈现出持续增长的趋势。
市场规模扩大、技术创新和环保要求的推动,将为化工设备行业带来新的机遇和挑战。
试论化工机械制造自动化技术的应用与发展
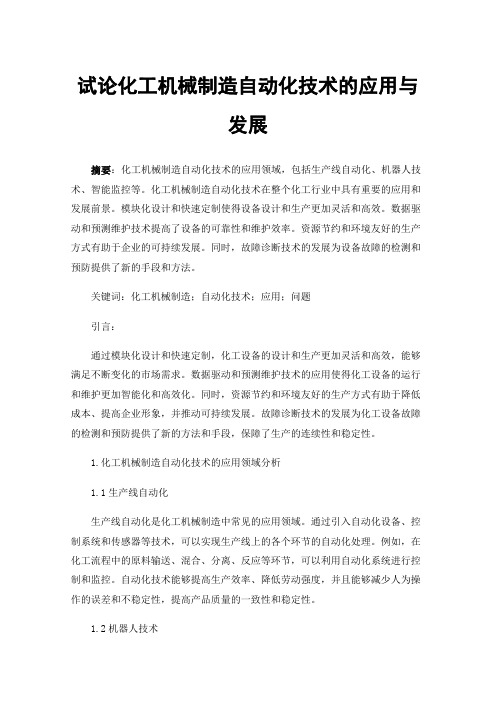
试论化工机械制造自动化技术的应用与发展摘要:化工机械制造自动化技术的应用领域,包括生产线自动化、机器人技术、智能监控等。
化工机械制造自动化技术在整个化工行业中具有重要的应用和发展前景。
模块化设计和快速定制使得设备设计和生产更加灵活和高效。
数据驱动和预测维护技术提高了设备的可靠性和维护效率。
资源节约和环境友好的生产方式有助于企业的可持续发展。
同时,故障诊断技术的发展为设备故障的检测和预防提供了新的手段和方法。
关键词:化工机械制造;自动化技术;应用;问题引言:通过模块化设计和快速定制,化工设备的设计和生产更加灵活和高效,能够满足不断变化的市场需求。
数据驱动和预测维护技术的应用使得化工设备的运行和维护更加智能化和高效化。
同时,资源节约和环境友好的生产方式有助于降低成本、提高企业形象,并推动可持续发展。
故障诊断技术的发展为化工设备故障的检测和预防提供了新的方法和手段,保障了生产的连续性和稳定性。
1.化工机械制造自动化技术的应用领域分析1.1生产线自动化生产线自动化是化工机械制造中常见的应用领域。
通过引入自动化设备、控制系统和传感器等技术,可以实现生产线上的各个环节的自动化处理。
例如,在化工流程中的原料输送、混合、分离、反应等环节,可以利用自动化系统进行控制和监控。
自动化技术能够提高生产效率、降低劳动强度,并且能够减少人为操作的误差和不稳定性,提高产品质量的一致性和稳定性。
1.2机器人技术机器人技术在化工机械制造中的应用也越来越广泛。
机器人具有高度的灵活性和精准的操作能力,能够承担起化工流程中的复杂、重复和危险的工作。
例如,在化工实验室中,机器人可以用于配料、混合、样品分析等操作,提高实验的稳定性和准确性。
此外,在制造过程中的装配、检测和包装等环节,机器人的应用也可以提高生产效率和品质控制。
1.3智能监控智能监控技术通过传感器和数据采集系统,对化工设备和生产过程进行实时监测和分析,以实现生产的智能化与优化。
2023年化工装备行业市场发展现状
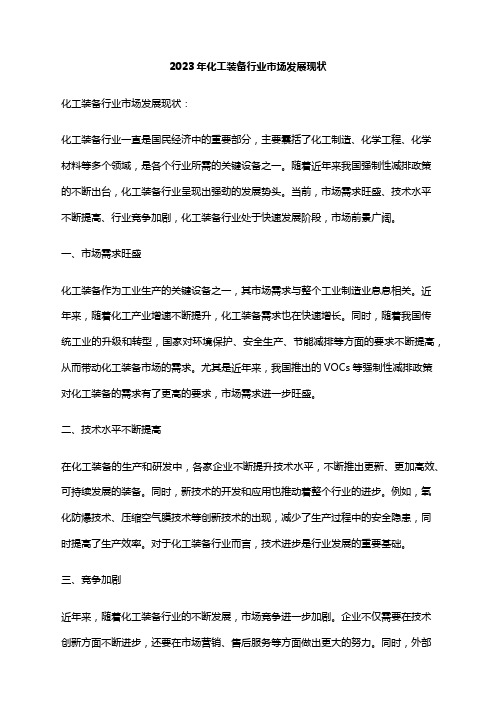
2023年化工装备行业市场发展现状化工装备行业市场发展现状:化工装备行业一直是国民经济中的重要部分,主要囊括了化工制造、化学工程、化学材料等多个领域,是各个行业所需的关键设备之一。
随着近年来我国强制性减排政策的不断出台,化工装备行业呈现出强劲的发展势头。
当前,市场需求旺盛、技术水平不断提高、行业竞争加剧,化工装备行业处于快速发展阶段,市场前景广阔。
一、市场需求旺盛化工装备作为工业生产的关键设备之一,其市场需求与整个工业制造业息息相关。
近年来,随着化工产业增速不断提升,化工装备需求也在快速增长。
同时,随着我国传统工业的升级和转型,国家对环境保护、安全生产、节能减排等方面的要求不断提高,从而带动化工装备市场的需求。
尤其是近年来,我国推出的VOCs等强制性减排政策对化工装备的需求有了更高的要求,市场需求进一步旺盛。
二、技术水平不断提高在化工装备的生产和研发中,各家企业不断提升技术水平,不断推出更新、更加高效、可持续发展的装备。
同时,新技术的开发和应用也推动着整个行业的进步。
例如,氧化防爆技术、压缩空气膜技术等创新技术的出现,减少了生产过程中的安全隐患,同时提高了生产效率。
对于化工装备行业而言,技术进步是行业发展的重要基础。
三、竞争加剧近年来,随着化工装备行业的不断发展,市场竞争进一步加剧。
企业不仅需要在技术创新方面不断进步,还要在市场营销、售后服务等方面做出更大的努力。
同时,外部环境也在不断变化,劳动力成本上升、原材料价格波动、政策环境的变化等因素都会对企业经营带来一定的挑战。
因此,企业需要强化自身竞争能力,不断寻求创新、突破发展难题。
总之,随着我国经济的不断发展和产业结构的不断升级,化工装备行业面临着前所未有的机遇与挑战。
企业需要充分把握市场机遇,不断提升技术水平,不断拓展国内外市场,积极因应各种挑战,通过创新发展,取得更为辉煌的业绩。
化工装备技术发展趋势

化工装备技术发展趋势先进的石化生产工艺过程要靠先进的石化装备来实现。
因此,石化生产技术开发要与装备技术开发并重。
本文对几种典型的石化专用和通用设备的技术现状与趋势进行了介绍。
我国化工装备经过20多年的努力,取得重大技术研制成果。
其中的催化裂化、加氢精制、聚乙烯等主要生产装置所需的关键装备,已达到了国际先进水平。
减少了我国对化工装备进口的依赖度,降低了建设投资和生产成本,对促进石化工业发展起到重要的作用,同国外相比,我国化工装备还有不少差距,主要是化工生产技术进步与设备技术开发脱节,重大设备的软件技术开发差距较大:设备技术开发跟不上工艺技术发展的速度,重工艺、轻设备的现象存在;基本上停留在模仿开发的地步,开发具有自主知识产权的专有技术的能力弱;设备开发还不能做到专业化、系列化;设备设计和制造水平、设备质量和可靠性还有待进一步提高。
随着化工工艺的进步和发展,对化工装备提出了更高要求。
必须加大装备的开发力度,掌握装备的核心技术,形成一批具有自主知识产权的装备,做到性能先进、质量可靠、高效节能、经济安全,满足化学工业的发展需求。
一.石化专用设备石化专用设备主要包括反应设备、塔器、换热设备、工业炉、储运设备和专用机械等。
反应设备反应器:是进行化学反应过程的“心脏”设备。
其发展趋势各不一样,国际上向着由经验放大走向数学模拟放大,实现大型化、高效化、结构简单化、操作自动化,研究方法趋向综合化方向发展。
催化裂化反应器:国的制造技术基本上达到了国际先进水平,广泛应用于各个炼油厂。
加氢反应器:国外著名的制造商有日本制钢所和神户制钢所等。
国正在为煤化工研制的锻焊加氢反应器外径5500mm,壁厚340mm,重量2040吨,是世界上最重的加氢反应器,其差距是我国创新能力差。
连续重整四重叠反应器:美国UOP专利技术使得该反应器具有反应效率高、节省能源、占地面积小、节省投资等优点。
国已经掌握了其设计制造技术,件安装指标完全达到UOP技术提出的要求。
现代化工生产专用设备制造的新发展趋势分析
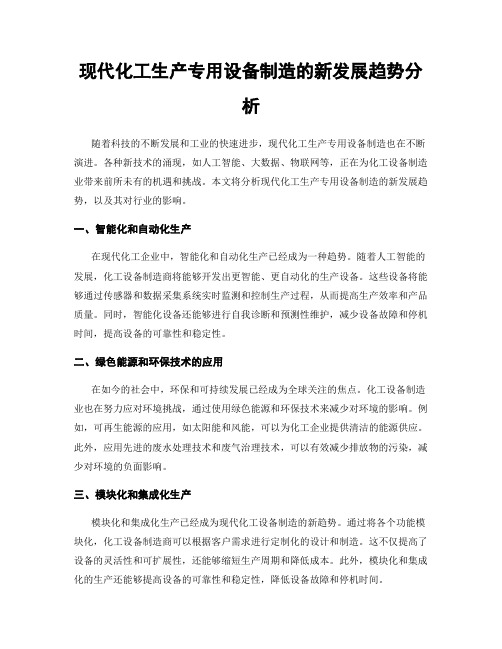
现代化工生产专用设备制造的新发展趋势分析随着科技的不断发展和工业的快速进步,现代化工生产专用设备制造也在不断演进。
各种新技术的涌现,如人工智能、大数据、物联网等,正在为化工设备制造业带来前所未有的机遇和挑战。
本文将分析现代化工生产专用设备制造的新发展趋势,以及其对行业的影响。
一、智能化和自动化生产在现代化工企业中,智能化和自动化生产已经成为一种趋势。
随着人工智能的发展,化工设备制造商将能够开发出更智能、更自动化的生产设备。
这些设备将能够通过传感器和数据采集系统实时监测和控制生产过程,从而提高生产效率和产品质量。
同时,智能化设备还能够进行自我诊断和预测性维护,减少设备故障和停机时间,提高设备的可靠性和稳定性。
二、绿色能源和环保技术的应用在如今的社会中,环保和可持续发展已经成为全球关注的焦点。
化工设备制造业也在努力应对环境挑战,通过使用绿色能源和环保技术来减少对环境的影响。
例如,可再生能源的应用,如太阳能和风能,可以为化工企业提供清洁的能源供应。
此外,应用先进的废水处理技术和废气治理技术,可以有效减少排放物的污染,减少对环境的负面影响。
三、模块化和集成化生产模块化和集成化生产已经成为现代化工设备制造的新趋势。
通过将各个功能模块化,化工设备制造商可以根据客户需求进行定制化的设计和制造。
这不仅提高了设备的灵活性和可扩展性,还能够缩短生产周期和降低成本。
此外,模块化和集成化的生产还能够提高设备的可靠性和稳定性,降低设备故障和停机时间。
四、数字化和虚拟化技术的应用数字化和虚拟化技术的应用也在化工设备制造业中发挥越来越重要的作用。
通过使用大数据分析和建模仿真技术,化工设备制造商可以进行精确的工艺设计和优化,实现合理的资源配置和能源消耗。
此外,虚拟现实和增强现实技术可以提供更直观、更真实的设备操作和维护培训,提高操作人员的技能和效率。
五、全球化合作和信息共享化工设备制造业越来越意识到全球化合作和信息共享的重要性。
我国化工机械制造技术工艺的发展现状与趋势探究

我国化工机械制造技术工艺的发展现状与趋势探究摘要:化工机械制造技术工艺的发展,应该与自动化技术、新型材料、绿色环保技术等相结合,从而不断地优化产品质量,调整产业结构,增强产品的核心竞争力。
本文主要介绍化工机械制造技术工艺的特点、发展现状与存在不足以及未来的发展趋势。
关键词:化工机械;制造技术;现代工艺;环保化工机械制造技术关系到化工工艺的优化、产品质量的提高,因此受到行业人员的广泛重视。
由于化工行业往往涉及到易燃易爆、高温高压、有毒有害等介质,一旦化工设备发生泄漏、爆炸等问题,就会造成严重后果,导致环境的污染或者危害到人民生命财产安全,因此有必要不断改进化工机械制造技术工艺,采用新型材料,制造出耐腐蚀,耐高压等优良品质的化工设备,确保化工生产的高效、安全和环保。
1.现代化工机械制造技术工艺的特点从化工机械制造技术的发展历程可以将化工机械制造技术工艺的特点分为以下几点:(1)系统性。
机械制造技术是一个融合了计算机技术、自动化技术、新材料技术和现代管理技术的系统性工程。
它还涉及到产品设计、产品制造和市场营销等各个方面。
众多技术的融合使得化工机械制造过程更加系统和专业,并保证生产过程正常有序进行。
(2)先进性。
现代化工机械制造技术工艺的先进性主要表现为高效、优质和低能耗。
高效是指运用自动化技术,使整个生产制造过程在人机一体化中进行,从而缩短了产品生产周期,提高生产效率;高效是指生产出来的化工机械产品质量高、性能好、零部件尺寸精准。
低能耗是指现代化工机械制造技术要求减少材料的浪费,降低对环境的污染,并通过模拟化技术提高产品一次合格率来有效降低废品的产生。
1.2我国化工机械制造技术工艺的发展现状及存在的问题(1)新型材料的应用及存在的不足。
由于化工机械制造需要适应腐蚀、易燃等恶劣条件下的生产和应用,许多老材料已经无法满足生产需求,人们开始研究和使用大量的新型材料投入到化工机械制造业之中。
新型材料虽然存在高成本的问题,然而从行业长远发展角度来看,却非常有利于提高化工机械产品整体的质量性能,优化技术工艺,进而增强提高企业的竞争力。
浅论我国化工设备技术的发展
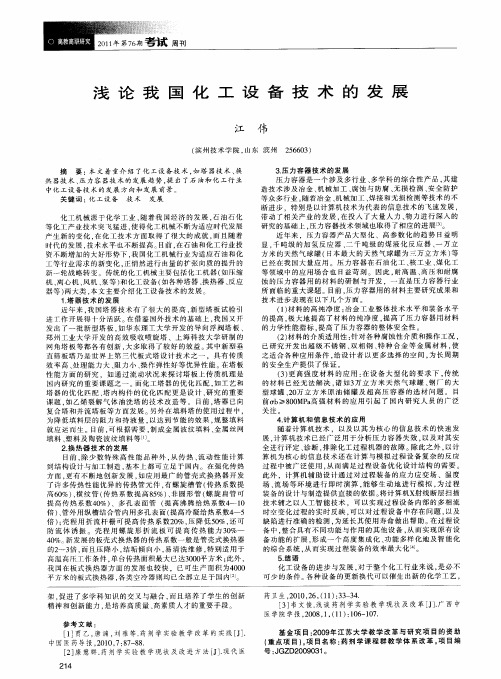
3 压 力 容 器技 术 的 发 展 .
压 力容 器 是 一 个 涉 及 多 行 业 、 学 科 的 综 合 性 产 品 , 建 多 其 造 技 术 涉 及 冶金 、 械 加 工 、 蚀 与 防腐 、 损 检 测 、 全 防护 机 腐 无 安 等 众 多行 业 。 随着 冶 金 、 械 加工 、 机 焊接 和 无 损 检测 等 技 术 的不
等 领域 中 腐 高 蚀 的压 力容 器 用 的材 料 的研 制 与 开 发 ,一 直 是 压 力 容 器 行 业 所 面 临 的重 大 课 题 。目前 , 力容 器 用 的材 料 主 要 研究 成 果 和 压
技 术 进 步表 现 在 以下 几 个 方 面 。 () 料的高纯净度 : 1材 冶金 工业 整 体 技 术 水 平 和装 备 水 平 的提 高 . 大 地 提 高 了 材 料 的 纯 净 度 , 高 了压 力 容 器 用 材 料 极 提 的力 学 性 能 指标 . 高 了压 力 容 器 的 整 体 安 全性 。 提 () 料 的介 质 适 用 性 : 2材 针对 各 种 腐 蚀性 介 质 和 操作 工 况 , 已研 究 开 发 出 超 级 不 锈 钢 、 相 钢 、 种 合 金 等 金 属 材 料 , 双 特 使 之 适 合 各 种 应 用 条 件 , 设 计 者 以更 多 选 择 的空 间 , 长周 期 给 为 的安 全 生 产 提 供 了保 证 。 ( ) 高 强 度 材 料 的 应 用 : 设 备 大 型 化 的要 求 下 , 统 3更 在 传 的材 料 已 经 无 法 解 决 , 如 3 立 方 米 天 然 气 球 罐 、 厂 的 大 诸 万 钢 型球 罐 、0 立方 米 原 油 储 罐 及 超 高 压 容 器 的 选 材 问题 。 目 2万 前 o ≥80 a 强 材 料 的 应 用 引 起 了 国 内 研 究 人 员 的 广 泛 - b 0 MP 高 关 注。 4 计 算 机和 信 息 技 术 的 应 用 .
我国石油化工设备制造行业基本情况及发展环境分析

我国石油化工设备制造行业基本情况及发展环境分析概述我国石油化工设备制造行业作为支撑石油化工产业发展的关键环节之一,具有重要的战略地位和经济价值。
该行业的发展情况和环境对我国石油化工产业的发展具有重要影响。
本文将对我国石油化工设备制造行业的基本情况和发展环境进行分析。
基本情况分析行业规模我国石油化工设备制造行业自20世纪80年代开始发展,目前已经形成了一定规模。
该行业涵盖了石油炼制设备、化工装备、气体设备等多个细分领域。
在全国范围内,设有多家重点石油化工设备制造企业,这些企业在技术实力和市场份额上具备竞争优势。
技术水平我国石油化工设备制造行业在技术水平方面有较大的进步。
通过引进消化吸收再创新,我国的石油化工设备制造技术已经取得了重要突破。
尤其是在高端设备制造领域,我国已经具备了一定的自主研发和制造能力。
然而,与国际先进水平相比,我国石油化工设备制造行业仍存在差距,需要进一步加强技术研发和创新能力。
市场需求随着我国石油化工产业的快速发展,对石油化工设备的需求也在不断增加。
市场对于设备质量、性能和环保要求越来越高,这对石油化工设备制造行业提出了新的挑战和机遇。
同时,我国石油化工设备制造行业还面临国际市场竞争的压力,需要加强市场开拓和品牌建设。
发展环境分析政策环境我国政府对石油化工设备制造行业的支持力度逐渐加大。
一系列政策措施的出台,为该行业的发展提供了有利条件。
例如,通过鼓励技术创新和支持企业发展等政策,促进了石油化工设备制造行业的良性发展。
市场环境石油化工设备制造行业市场需求增加,但也面临诸多挑战。
一方面,行业市场竞争激烈,企业间利润空间逐渐减小。
另一方面,国际市场对石油化工设备的需求存在不确定性,需要企业灵活应对和适应市场变化。
技术环境随着科技的不断进步,石油化工设备制造行业面临着技术更新换代的压力。
新技术的应用将极大改变行业竞争格局,需要企业加强技术创新和人才培养,以保持竞争力。
结论我国石油化工设备制造行业在基本情况和发展环境方面存在一定的机遇和挑战。
化工设备安全生产的创新与发展
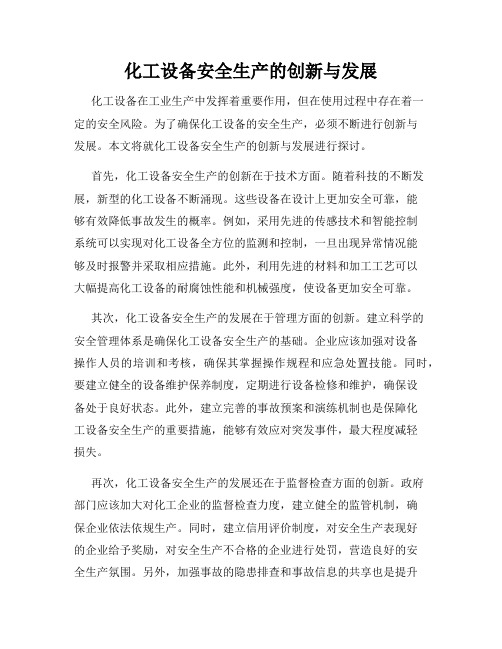
化工设备安全生产的创新与发展化工设备在工业生产中发挥着重要作用,但在使用过程中存在着一定的安全风险。
为了确保化工设备的安全生产,必须不断进行创新与发展。
本文将就化工设备安全生产的创新与发展进行探讨。
首先,化工设备安全生产的创新在于技术方面。
随着科技的不断发展,新型的化工设备不断涌现。
这些设备在设计上更加安全可靠,能够有效降低事故发生的概率。
例如,采用先进的传感技术和智能控制系统可以实现对化工设备全方位的监测和控制,一旦出现异常情况能够及时报警并采取相应措施。
此外,利用先进的材料和加工工艺可以大幅提高化工设备的耐腐蚀性能和机械强度,使设备更加安全可靠。
其次,化工设备安全生产的发展在于管理方面的创新。
建立科学的安全管理体系是确保化工设备安全生产的基础。
企业应该加强对设备操作人员的培训和考核,确保其掌握操作规程和应急处置技能。
同时,要建立健全的设备维护保养制度,定期进行设备检修和维护,确保设备处于良好状态。
此外,建立完善的事故预案和演练机制也是保障化工设备安全生产的重要措施,能够有效应对突发事件,最大程度减轻损失。
再次,化工设备安全生产的发展还在于监督检查方面的创新。
政府部门应该加大对化工企业的监督检查力度,建立健全的监管机制,确保企业依法依规生产。
同时,建立信用评价制度,对安全生产表现好的企业给予奖励,对安全生产不合格的企业进行处罚,营造良好的安全生产氛围。
另外,加强事故的隐患排查和事故信息的共享也是提升化工设备安全生产水平的关键,能够及时发现和解决问题,防患于未然。
综上所述,化工设备安全生产的创新与发展是一个系统工程,需要技术、管理、监督检查等多方面的配合。
只有不断推动技术创新,加强管理制度建设,完善监督机制,才能够有效提升化工设备的安全生产水平,保障人民生命财产安全。
希望相关部门和企业能够共同努力,共同推动化工设备安全生产的创新与发展,为我国的化工产业发展贡献力量。
现代化工机械技术发展回顾与展望分析

例如,在太阳能领域,高效太阳能电池板、太阳能热水器等得到了广泛应用;在风能领域,风力发电机、风力泵等得到了广泛应用;在水能领域,高效水轮机、水力发电设备等得到了广泛应用。
案例四:化工机械技术在新能源领域的应用
06
总结与展望
技术进步
现代化工机械技术已经取得了显著的进步,包括新型材料的应用、高精度加工技术的普及以及自动化和智能化的发展。这些进步提高了设备的性能和效率,同时也改善了生产过程的安全性和环保性。
案例细节
例如,在废水处理方面,高效膜过滤技术、生物反应器技术等得到了广泛应用;在废气治理方面,活性炭吸附技术、催化燃烧技术等得到了广泛应用;在固废处理方面,压滤机、干燥设备等得到了广泛应用。
案例二:化工机械技术在环保领域的应用
技术应用
数字化与智能化化工机械技术的应用主要集中在设备的自动化、智能化和远程控制方面。例如,利用传感器和执行器实现设备的自动化控制,利用PLC和DCS系统实现设备的智能化控制,利用物联网和云计算技术实现设备的远程监控和控制等。
案例细节
例如,在石油领域,新型抽油机、高效油气分离技术和设备等得到了广泛应用;在化工领域,新型反应器、高效传热和分离设备等得到了广泛应用。
案例一:新型化工机械技术的研发与应用
技术应用
化工机械技术在环保领域的应用主要集中在废水处理、废气治理、固废处理等方面。例如,利用高效分离技术和设备进行废水处理,利用新型反应器和催化剂进行废气治理,利用新型压滤机和干燥设备进行固废处理等。
对现代化工机械技术发展的总结与评价
持续创新
化工机械技术的持续创新是推动其发展的关键因素。这包括新材料、新工艺、新技术的不断涌现,以及在设计和制造过程中的持续改进。这种创新有助于提高生产效率、降低成本并满足不断变化的市场需求。
国内外石油化工设备产业发展形势研究
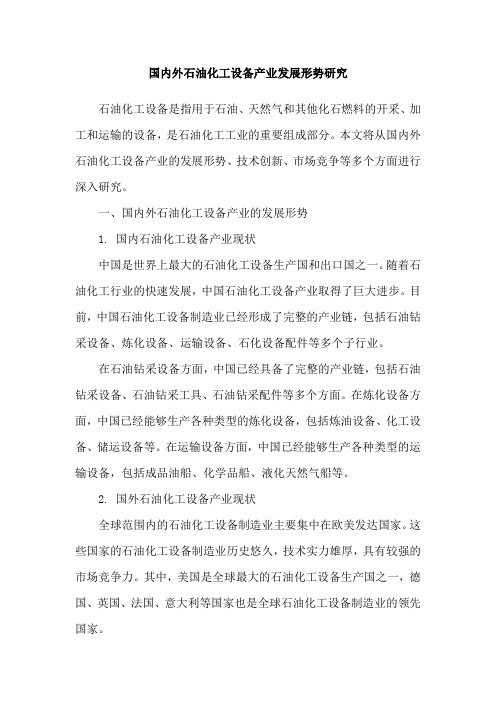
国内外石油化工设备产业发展形势研究石油化工设备是指用于石油、天然气和其他化石燃料的开采、加工和运输的设备,是石油化工工业的重要组成部分。
本文将从国内外石油化工设备产业的发展形势、技术创新、市场竞争等多个方面进行深入研究。
一、国内外石油化工设备产业的发展形势1. 国内石油化工设备产业现状中国是世界上最大的石油化工设备生产国和出口国之一。
随着石油化工行业的快速发展,中国石油化工设备产业取得了巨大进步。
目前,中国石油化工设备制造业已经形成了完整的产业链,包括石油钻采设备、炼化设备、运输设备、石化设备配件等多个子行业。
在石油钻采设备方面,中国已经具备了完整的产业链,包括石油钻采设备、石油钻采工具、石油钻采配件等多个方面。
在炼化设备方面,中国已经能够生产各种类型的炼化设备,包括炼油设备、化工设备、储运设备等。
在运输设备方面,中国已经能够生产各种类型的运输设备,包括成品油船、化学品船、液化天然气船等。
2. 国外石油化工设备产业现状全球范围内的石油化工设备制造业主要集中在欧美发达国家。
这些国家的石油化工设备制造业历史悠久,技术实力雄厚,具有较强的市场竞争力。
其中,美国是全球最大的石油化工设备生产国之一,德国、英国、法国、意大利等国家也是全球石油化工设备制造业的领先国家。
二、技术创新1. 液压系统液压系统是石油化工设备的关键核心技术之一。
当前,欧美发达国家的石油化工设备制造商已经成功地应用了液压系统的最新技术,包括高压、高效率、节能、智能化等方面。
2. 机器人技术机器人技术是当前石油化工设备制造业的热门话题之一。
先进的机器人技术可以帮助石油化工设备制造商提高生产效率、降低生产成本、提高产品质量。
三、市场竞争1. 国内市场竞争在国内石油化工设备市场中,中国本土的石油化工设备制造商与欧美日的制造商竞争。
化工机械制造技术的发展趋势【论文】
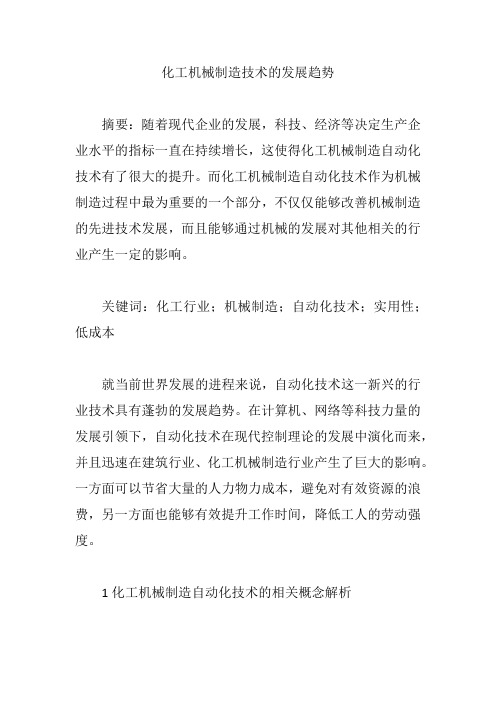
化工机械制造技术的发展趋势摘要:随着现代企业的发展,科技、经济等决定生产企业水平的指标一直在持续增长,这使得化工机械制造自动化技术有了很大的提升。
而化工机械制造自动化技术作为机械制造过程中最为重要的一个部分,不仅仅能够改善机械制造的先进技术发展,而且能够通过机械的发展对其他相关的行业产生一定的影响。
关键词:化工行业;机械制造;自动化技术;实用性;低成本就当前世界发展的进程来说,自动化技术这一新兴的行业技术具有蓬勃的发展趋势。
在计算机、网络等科技力量的发展引领下,自动化技术在现代控制理论的发展中演化而来,并且迅速在建筑行业、化工机械制造行业产生了巨大的影响。
一方面可以节省大量的人力物力成本,避免对有效资源的浪费,另一方面也能够有效提升工作时间,降低工人的劳动强度。
1化工机械制造自动化技术的相关概念解析1.1化工机械制造自动化技术的基本内涵所谓化工机械制造自动化技术,是一门能够集中化工行业所必须要的相关步骤而采取的科学技术化问题,旨在解决其在机械产品的设计理念表达、加工制作手法研究、产品从最初的生产到销售、使用过程、后期维修这一整体流程中的相关技术问题[1]。
化工机械制造自动化技术的发展,也为社会工业制造的进程起到了一定的推进作用,但是也会面临一些相关的技术难题。
因此,需要从事该行业的技术人员能够有效了解化工机械制造自动化技术的特性,结合实际工作中的情况,做出相应的应急措施,以减少资源的浪费和人力的损失[2]。
1.2化工机械制造自动化技术的特征研究1.2.1一体化技术的表现形式由于自动化技术的发展一直保持低成本、高效率的发展特性,通常将各个化工机械技术与其他问题相结合进行讨论,实现一体化发展的基本形式。
并借助国外科学合理的化工机械制造自动化技术,结合我国的实际情况,将多方融合在一起进行较为系统的发展促进。
1.2.2系统性的融合化工机械制造自动化技术自身的工作流程极其复杂,包含机械的设计、生产、销售、使用、后期维修等多个环节[3]。
化工机械设计制造的特点、优势和发展趋势
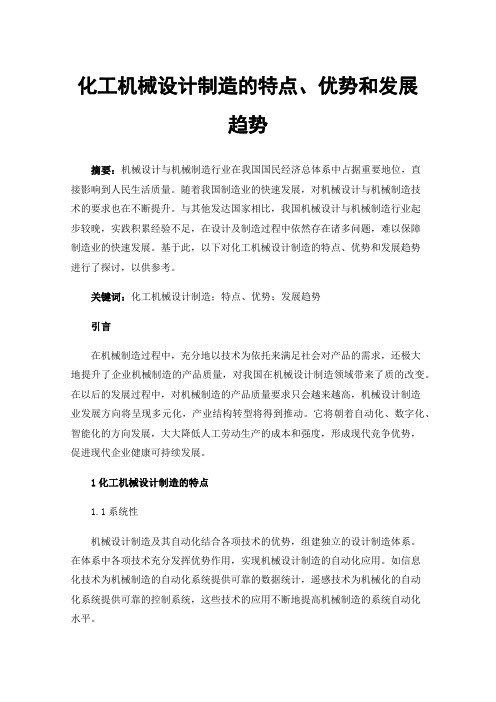
化工机械设计制造的特点、优势和发展趋势摘要:机械设计与机械制造行业在我国国民经济总体系中占据重要地位,直接影响到人民生活质量。
随着我国制造业的快速发展,对机械设计与机械制造技术的要求也在不断提升。
与其他发达国家相比,我国机械设计与机械制造行业起步较晚,实践积累经验不足,在设计及制造过程中依然存在诸多问题,难以保障制造业的快速发展。
基于此,以下对化工机械设计制造的特点、优势和发展趋势进行了探讨,以供参考。
关键词:化工机械设计制造;特点、优势;发展趋势引言在机械制造过程中,充分地以技术为依托来满足社会对产品的需求,还极大地提升了企业机械制造的产品质量,对我国在机械设计制造领域带来了质的改变。
在以后的发展过程中,对机械制造的产品质量要求只会越来越高,机械设计制造业发展方向将呈现多元化,产业结构转型将得到推动。
它将朝着自动化、数字化、智能化的方向发展,大大降低人工劳动生产的成本和强度,形成现代竞争优势,促进现代企业健康可持续发展。
1化工机械设计制造的特点1.1系统性机械设计制造及其自动化结合各项技术的优势,组建独立的设计制造体系。
在体系中各项技术充分发挥优势作用,实现机械设计制造的自动化应用。
如信息化技术为机械制造的自动化系统提供可靠的数据统计,遥感技术为机械化的自动化系统提供可靠的控制系统,这些技术的应用不断地提高机械制造的系统自动化水平。
1.2实用性及人性化特点机械设计制造及其自动化能够面向化工企业进行机械设备的定制化服务,并从中达到机械应用范围的延伸,促使化工企业工作运行得到效率上的提升,这样就可以有效满足化工企业对于运行标准的贴合。
此外,机械制造就是为了能够满足市场需求,在传统的化工企业中,机械制造往往单一运转,然而在自动化的融合后,化工机械制造自动化运行更具人性化的特点,运行过程中更加流畅,开始注重了其性能的调整,人性化的设计特点,让化工企业的机械制造在整体运行环节上更为便捷,制造力迅速提升。
- 1、下载文档前请自行甄别文档内容的完整性,平台不提供额外的编辑、内容补充、找答案等附加服务。
- 2、"仅部分预览"的文档,不可在线预览部分如存在完整性等问题,可反馈申请退款(可完整预览的文档不适用该条件!)。
- 3、如文档侵犯您的权益,请联系客服反馈,我们会尽快为您处理(人工客服工作时间:9:00-18:30)。
设备制造工艺学国内化工设备制造技术发展论述余乐装备0901 200906080127 成涛装备0901 200906080128目录一.化工设备制造技术工艺的发展历程 (3)二.现代化工设备制造技术与工艺的发展现状 (6)三.现代化工设备制造技术与工艺的发展方向 (7)四.结语 (8)参考文献 (9)摘要:在化工设备制造行业发展的过程中,加大创新力度,优化化工设备制造的生产工艺和生产技术,能够有效地提升化工设备制造的企业的市场竞争力,促进我国化工设备制造行业的快速发展。
文章介绍了化工设备制造技术工艺的发展历程与发展现状,并对化工机械制造行业的发展趋势进行了简要的分析。
关键词:化工机械制造;技术;工艺;发展一.化工设备制造技术工艺的发展历程我国石油炼制工业一直走自主发展的道路,因而,带动了炼油技术装备的发展。
一些高难度设备,如加氢裂化和加氢精制装置用的加氢反应器、高压换热器、高压空冷器;催化裂化和延迟焦化装置用的主风机、富氧压缩机、高效旋风分离器、外取热器、烟机以及重要的流程泵等都能制造。
曾几何时,我国制造的小型化肥、中型化肥设备遍布全国各地,解决了当时对化肥的急需。
这些化肥设备,由于其技术经济指标已落后,逐渐被大型化肥设备淘汰。
以乙烯裂解决为代表的石油化工工业,虽然其设备目前国内尚无成套供应的能力,依赖进口的局面没有得到根本扭转。
但是,近些年来,由于用户主管部门和设备主管部门坚持不懈地努力,石油化工关键设备研制取得重大进展。
我国化工设备行业生产的装备仍不能很好地满足炼油、化工行业高速发展的需要,特别是石化行业对先进的大型石油化工装置的需求。
国内在成套及产品设计、制造方面与国外先进水平还有一定差距,化工设备仍在大量进口,行业未能分享我国大量建设大型炼油厂、石化厂、化工厂急需设备的大好时期,化工设备进出口总体仍呈巨额逆差状态,行业的处境还相当困难。
通用机械以泵、阀为首不合格产品屡屡曝光,优质高新产品正走出国门占领国际市场,工业用锅炉趋向节能化,环保、安全逐渐成为此类机械发展主流。
仪器仪表在国债与政策的支持下,不但产值产量迅速增长,而且新技术、新品种也层出不穷。
非金属设备在保持原有竞争能力的同时,不断完善自我。
大型设备项目建设工作欣欣向荣,小型项目因重复建设、浪费资源等原因纷纷落马。
随着市场的发展,高耗能大污染的电解铝、水泥等行业的小型项目建设将受到一定限制,而化工重点设备项目正趋向高新化,整个化工设备行业正向大型化、集团化、高新技术化方向发展。
我国的石油化工设备制造业经过20余年的自行研制、引进吸收国外先进技术,尤其是经过一批国家重大技术装备——大型合成氨、大型尿素和大型乙烯裂解及其后处理关键设备的研制的洗礼,我国石油化工设备制造行业有了飞跃发展。
目前我国主要石化装备制造企业已经拥有较好技术和装备,某些大型石油化工、化肥、无机化工装备的制造技术达到较高水平,也生产出一些不亚于世界同类产品水平的设备。
一般的塔器、容器、加热器、换热设备等国内设计、制造较为成熟,与国际水平差距不大。
尤其是一批国家重大技术装备—大型合成氨、大型尿素和大型乙烯裂解及其后处理关键设备的研制胜利,使我国石油化工设备制造行业有了飞跃发展。
乙烯裂解炉及其急冷锅炉、30万吨/年乙烯裂解三机(裂解气压缩机、丙烯压缩机、乙烯压缩机)各种低温泵、压力达7.8MPa板翅式换热器(冷箱)大型乙烯球罐、聚丙烯反应器、大型双螺杆造粒机组等相继研制成功。
据2010年资料显示,国内已可以制造500万吨/年以上炼油厂成套设备、800万吨/年常减压蒸馏装置、200万吨/年以上重油催化裂化装置、150万吨/年加氢裂化装置、200万吨/年渣油加氢脱硫装置、100万吨/年延迟焦化装置等。
一些高难度设备,目前。
如加氢裂化和加氢精制装置用的加氢反应器、高压换热器、高压空冷器,加氢和重整装置用的离心式循环氢压缩机、50吨及80吨活塞力的往复式新氢压缩机;催化裂化和延迟焦化装置用的主风机、富氧压缩机、高效旋风分离器、外取热器、烟机以及重要的流程泵等都能制造。
以30万吨/年合成氨、52万吨/年尿素为代表的大型化肥装置的设备,包括关键设备直径2.8米的合成塔、CO2汽提塔、原料气压缩机、氨压缩机、合成气压缩机、CO2压缩机等也都已研制成功。
化工设备制造技术在我国化工行业的发展过程当中占据了重要的地位,现代化的化工设备能够帮助化工生产实现设备与工艺的优化。
因此,化工设备的制造技术与工艺长期以来都受到了人们的重视,尤其是压力容器的制造工艺,更是占据了举重要地位。
作为特殊的承压设施,压力容器在实际应用中,会面对复杂的使用环境和操作方式,处理的介质也常常具有易燃、甚至有毒等特点,一旦设备出现问题,便会产生严重的后果,给国家及人民的生命财产带来威胁。
因此,在压力容器制造技术的发展过程中,不断地改进压力容器的制造工艺,提高容器耐压性、密闭性、抗腐蚀性等多种性能便成为了研究的重点。
我国石化装备发展历程可总结为以下三点:1、初始阶段举步维艰上世纪70年代,我国只有数量不多的中小型炼油厂,还没有真正意义上的石化厂。
当时国内只有少数几个化工机械厂能够制造这些中小型炼油厂所用的一般设备,一些重大关键设备全部依赖进口。
1976年北京燕山石化30万吨/年乙烯项目建成投产,石化工业开始发展。
到80年代初,又先后建设了南京扬子、上海金山、山东齐鲁、黑龙江大庆等4套30万吨/年乙烯项目,至此,我国才有了真正意义上的石化工业,但乙烯装备几乎是成套进口。
1983年,国务院下达《关于抓紧研制重大技术装备的决定》(简称决定),指出依靠自己技术的同时,要积极引进国外先进技术,并力争把最核心的关键技术掌握在自己手里。
其中30万吨/年乙烯成套设备被列入国家十个重大装备研制项目之一,中石化集团为此还成立了重大装备自主制造办公室。
从1984年开始,陆续对涵盖炼油、化工、化纤和化肥主要装置的关键设备自主制造可行性进行了调查研究,又对全国可以承担石化重大装置研制的制造企业进行了大规模调研,确定了一批有能力的研制单位。
由于对炼油生产工艺及装备比较熟悉,对装备大型化的攻关、研制相对于乙烯装置而言要容易些。
为了给乙烯装备自主制造奠定基础,中石化决定先对炼油成套设备中的催化裂化、催化重整、加氢精制、加氢裂化装置的关键设备组织攻关。
在研制工作中制造企业看到了自己在设备设计和制造上同国外先进水平的差距,纷纷引进技术软件、加工装备、检验技术,或同国外合作来提高自己的研发水平,攻克了一个个难关,使不少重大关键设备开始立足国内。
到目前为止,炼油装置主要生产工艺及设备已自主制造,设备自主制造率按投资计算已达95%,除DCS系统和个别泵阀外基本不再进口。
2、上世纪末全面突破进入90年代初,第一批引进的乙烯项目需要进行改造和扩建,国内对乙烯生产工艺及其设备有了较深的了解,乙烯装备的自主制造也实质性地开始了。
1993年国家批准了燕山45万吨/年乙烯改造工程,国家和中石化集团要求改造工程28个月、28亿元不能突破。
如果改造的技术和装备还是成套从国外引进,投资肯定降不下来,最后中石化集团决定乙烯裂解工艺和主要设备仍然从国外引进,14万吨/年聚乙烯工艺和主要设备实行自主制造。
一些关键设备的研制成功,给石化重大装备自主制造树立了信心。
1997年大庆48万吨/年乙烯工程进行改造,中国石化集团决定对乙烯装置"三机"中的裂解气压缩机和丙烯压缩机实现自主制造。
当时的石化集团副总经理王基铭经过调查研究,力排众议,坚决支持乙烯"三机"自主制造,并表示主动承担风险。
裂解气压缩机和丙烯压缩机自1999年研制成功并投产以来,各项工艺性能都达到了设计要求,满足了生产工艺的需要。
为我国乙烯大型化建设提供了先进实用的装备,打破了国外垄断,打开了乙烯关键设备自主制造的禁区。
从1999年开始,中石化集团陆续对燕山、扬子、上海、齐鲁、茂名乙烯进行第二轮改造,规模由45万吨/年改造到70万~80万吨/年。
中石化集团经过多次慎重研究,决定在这轮乙烯改造中,重大装备的自主制造要比以前有所前进,不能后退。
尽管反对自主制造的人很多,但乙烯重大装备自主制造的步伐不会放慢。
3、硕果累累石化重大装备自主制造经过20年的努力,在"七五"期间对6个课题310台套设备实现自主制造,"八五"期间35个攻关课题的研制成果应用于生产,"九五"期间有30个攻关课题研制成果应用于生产。
据不完全统计,从"七五"到"九五"期间依托石化工程建设和技术改造项目研制和推广应用的自主制造重大设备达927台,与同期引进设备相比节约投资达43亿元。
"十五"期间,石化重大装备自主制造虽然遇到很大的困难,但也有不少重大装备研制成功,如大型PTA装置的结晶器、钛管换热器、回转干燥器;20万吨/年苯乙烯装置脱氢反应器;20万吨/年聚丙烯装置环管反应器和大型迷宫压缩机、20万吨/年聚酯装置酯化反应器和缩聚反应器、30万吨/年化肥装置大型汽化炉、4.8万等级空分装置工艺设计及其设备自主制造等,使石化重大装备自主制造上了一个新台阶。
目前还有一些重大装备研制工作正在进行,如60万吨/年乙烯装置裂解气压缩机、30万吨/年聚丙烯环管反应器、干燥器、40万吨/年PVC装置氯化反应器等。
到目前为止,正式立项研制成功并推广应用的重大装备2000多台,与同期进口相比节约投资达52亿元。
现在炼油设备自主制造率按投资计算已达到95%左右,化工设备自主制造率已达到70%左右,一批重大装备研制成果达到或接近国际先进水平。
化工设备大致发展历程如下图所示:二.现代化工设备制造技术与工艺的发展现状千万吨级炼厂和百万吨级的乙烯厂等一批大型石油化工工程项目陆续开工或投产,为炼油化工设备带来了巨大的市场需求,中国炼油化工设备行业发展前景广阔。
近年来,我国炼油化工设备行业无论在生产规模和产业结构,还是产品开发和国产化成果方面都取得了较好的成绩。
据统计,2011年中国炼油化工设备行业实现销售收入616.26 亿元,同比增长25.07%;实现利润总额42.91亿元,同比增长11.23%。
(图1-1)随着先进技术与工艺不断引入到化工设备生产过程中,使得化工设备的制造技术有了长足的进步。
以压力容器的制造为例,为了提高压力容器的性质,保证压力容器在生产过程中的安全性,压力容器的生产过程被科学的分为七个部分,从而有效地保证了压力容器的质量,很好地体现了化工设备制造技术的发展现状。
首先,现代化工设备制造技术工艺对新材料的应用,有效地提高了机械的性能,保障了化工设备的使用质量,提高了化工设备对环境的使用能力,确保了化工设备的使用安全。