采油过程中涉及到的各类废水处理方法
油田污水处理方法

油田污水处理方法引言概述:油田污水处理是保护环境和可持续发展的重要环节。
随着油田开采规模的不断扩大,油田污水处理方法的研究和应用变得尤为重要。
本文将从五个大点出发,详细阐述油田污水处理的方法和技术。
正文内容:1. 物理处理方法1.1 沉淀法:通过加入沉淀剂,使污水中的悬浮物沉淀下来,从而达到净化水质的目的。
1.2 过滤法:利用过滤器将污水中的固体颗粒物拦截下来,使水质得到净化。
1.3 离心法:利用离心机将污水中的固体颗粒物通过离心力分离出来,实现水质的净化。
1.4 吸附法:通过吸附剂吸附污水中的有机物和重金属离子,从而净化水质。
1.5 蒸发法:将污水加热蒸发,使水分蒸发掉,从而实现水质的净化。
2. 化学处理方法2.1 氧化法:利用氧化剂将有机物氧化分解,从而净化水质。
2.2 中和法:通过加入中和剂,将酸性或碱性的污水中的酸碱度调节到中性,实现水质的净化。
2.3 沉淀法:通过加入沉淀剂,使污水中的重金属离子沉淀下来,从而净化水质。
2.4 气浮法:利用气浮设备将污水中的悬浮物和油脂浮起,从而实现水质的净化。
2.5 活性炭吸附法:通过活性炭吸附有机物和重金属离子,实现水质的净化。
3. 生物处理方法3.1 好氧处理法:利用好氧微生物将有机物降解为二氧化碳和水,从而净化水质。
3.2 厌氧处理法:利用厌氧微生物将有机物降解为甲烷和二氧化碳,实现水质的净化。
3.3 植物处理法:利用水生植物吸收污水中的营养物质和重金属离子,从而净化水质。
3.4 红外辐射处理法:利用红外辐射杀灭污水中的微生物,实现水质的净化。
3.5 稳定化处理法:通过添加稳定剂,控制微生物的生长,从而净化水质。
4. 膜分离技术4.1 超滤技术:利用超滤膜将污水中的悬浮物、胶体等分离出来,实现水质的净化。
4.2 逆渗透技术:通过逆渗透膜将污水中的溶解物质和离子分离出来,从而净化水质。
4.3 微滤技术:利用微滤膜将污水中的微生物和悬浮物分离出来,实现水质的净化。
油田污水处理方法

油田污水处理方法一、引言油田是一种重要的能源开辟和生产基地,但其产生的废水也带来了严重的环境问题。
为了保护水资源和生态环境,油田污水处理成为了一个迫切的任务。
本文将介绍几种常见的油田污水处理方法,并分析其优缺点。
二、物理处理方法1. 沉淀沉淀是最常见的物理处理方法之一。
通过将污水静置一段时间,使其中的悬浮物沉淀到底部,然后将上清液体排出,从而实现固液分离。
这种方法简单易行,成本低廉,但对于一些细小的悬浮物效果不佳。
2. 过滤过滤是利用过滤介质对污水进行过滤,将其中的悬浮物截留下来。
常见的过滤介质有砂子、滤纸、滤布等。
过滤方法可以有效去除细小颗粒物,但需要定期更换过滤介质,维护成本较高。
三、化学处理方法1. 氧化法氧化法是利用氧化剂对污水中的有机物进行氧化分解的方法。
常见的氧化剂有高锰酸钾、过氧化氢等。
这种方法可以有效去除有机物,但氧化剂的选择和投加量需要根据具体情况进行调整。
2. 沉淀法沉淀法是利用化学反应使污水中的悬浮物生成沉淀,从而实现固液分离。
常见的沉淀剂有氯化铁、聚合氯化铝等。
这种方法适合于去除重金属离子和悬浮物,但对于溶解性有机物的去除效果较差。
四、生物处理方法1. 好氧生物处理好氧生物处理是利用好氧微生物对污水中的有机物进行降解的方法。
通过增加氧气供给和搅拌设备,促使微生物快速繁殖和降解有机物。
这种方法对于有机物的去除效果好,但设备投资和运行成本较高。
2. 厌氧生物处理厌氧生物处理是利用厌氧微生物对污水中的有机物进行降解的方法。
与好氧生物处理相比,厌氧生物处理不需要额外供氧设备,能耗较低。
但该方法对于一些难降解的有机物效果较差。
五、综合处理方法综合处理方法是将多种处理方法结合起来,以达到更好的处理效果。
常见的综合处理方法有物化结合法、生化结合法等。
这些方法可以充分发挥各种处理方法的优势,但设备投资和运行维护成本较高。
六、结论油田污水处理是一项重要的环境保护任务,选择合适的处理方法对于保护水资源和生态环境至关重要。
油田污水处理方法

油田污水处理方法一、引言油田污水是指在石油开采、生产和加工过程中产生的含油、含盐、含重金属等有害物质的废水。
油田污水的处理对于保护环境、维护生态平衡和可持续发展具有重要意义。
本文将介绍几种常用的油田污水处理方法,包括物理处理、化学处理和生物处理。
二、物理处理方法1. 沉淀沉淀是一种常用的物理处理方法,通过重力作用使污水中的固体颗粒沉降到底部,从而达到分离的目的。
常见的沉淀设备有沉淀池和沉淀槽。
沉淀池通过增大水流速度和减小水流面积来提高沉淀效果,而沉淀槽通过增加沉淀时间和减小流速来提高沉淀效果。
沉淀后的固体颗粒可以通过过滤等方法进一步处理。
2. 过滤过滤是一种通过介质(如砂、石英砂等)的孔隙作用将污水中的固体颗粒截留下来的物理处理方法。
过滤设备通常包括过滤器和滤布。
过滤器通过增加过滤介质的层数和减小孔隙大小来提高过滤效果,而滤布通过增加滤布的厚度和减小孔隙大小来提高过滤效果。
过滤后的污水可以进一步进行化学处理或者生物处理。
三、化学处理方法1. 氧化氧化是一种常用的化学处理方法,通过添加氧化剂(如过氧化氢、高锰酸钾等)使有机物质氧化分解成无害物质。
氧化剂的选择应根据污水中的有机物质种类和浓度来确定。
氧化剂的投加量应根据实际情况进行调整,以达到最佳处理效果。
2. 沉淀剂沉淀剂是一种通过与污水中的悬浮物或者溶解物发生化学反应形成沉淀物,从而达到分离的目的的化学处理方法。
常用的沉淀剂有氢氧化铁、氢氧化铝等。
沉淀剂的投加量应根据污水中的悬浮物或者溶解物的种类和浓度来确定。
投加沉淀剂后,应进行充分的搅拌和沉淀时间,以确保沉淀效果。
四、生物处理方法1. 厌氧处理厌氧处理是一种利用厌氧微生物降解有机物质的生物处理方法。
厌氧处理通常需要建立一个密闭的反应器,通过控制反应器内的温度、pH值和厌氧微生物的种类和数量来实现有机物质的降解。
厌氧处理的产物主要是甲烷和二氧化碳。
2. 好氧处理好氧处理是一种利用好氧微生物降解有机物质的生物处理方法。
油田污水处理方法
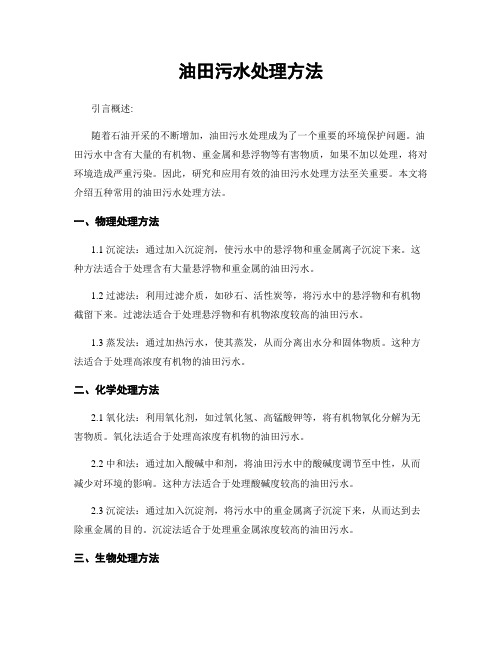
油田污水处理方法引言概述:随着石油开采的不断增加,油田污水处理成为了一个重要的环境保护问题。
油田污水中含有大量的有机物、重金属和悬浮物等有害物质,如果不加以处理,将对环境造成严重污染。
因此,研究和应用有效的油田污水处理方法至关重要。
本文将介绍五种常用的油田污水处理方法。
一、物理处理方法1.1 沉淀法:通过加入沉淀剂,使污水中的悬浮物和重金属离子沉淀下来。
这种方法适合于处理含有大量悬浮物和重金属的油田污水。
1.2 过滤法:利用过滤介质,如砂石、活性炭等,将污水中的悬浮物和有机物截留下来。
过滤法适合于处理悬浮物和有机物浓度较高的油田污水。
1.3 蒸发法:通过加热污水,使其蒸发,从而分离出水分和固体物质。
这种方法适合于处理高浓度有机物的油田污水。
二、化学处理方法2.1 氧化法:利用氧化剂,如过氧化氢、高锰酸钾等,将有机物氧化分解为无害物质。
氧化法适合于处理高浓度有机物的油田污水。
2.2 中和法:通过加入酸碱中和剂,将油田污水中的酸碱度调节至中性,从而减少对环境的影响。
这种方法适合于处理酸碱度较高的油田污水。
2.3 沉淀法:通过加入沉淀剂,将污水中的重金属离子沉淀下来,从而达到去除重金属的目的。
沉淀法适合于处理重金属浓度较高的油田污水。
三、生物处理方法3.1 好氧生物处理法:利用好氧微生物,将有机物分解为二氧化碳和水。
这种方法适合于处理低浓度有机物的油田污水。
3.2 厌氧生物处理法:利用厌氧微生物,将有机物分解为甲烷等可再利用的气体。
厌氧生物处理法适合于处理高浓度有机物的油田污水。
3.3 植物处理法:利用植物的吸收作用,将油田污水中的有机物和重金属吸收并转化为植物组织。
植物处理法适合于处理低浓度有机物和重金属的油田污水。
四、膜分离技术4.1 超滤法:利用超滤膜,将污水中的悬浮物、胶体和高份子有机物截留下来。
这种方法适合于处理悬浮物和有机物浓度较高的油田污水。
4.2 反渗透法:利用反渗透膜,将污水中的溶解性有机物、重金属离子和盐分截留下来。
油田污水处理方法
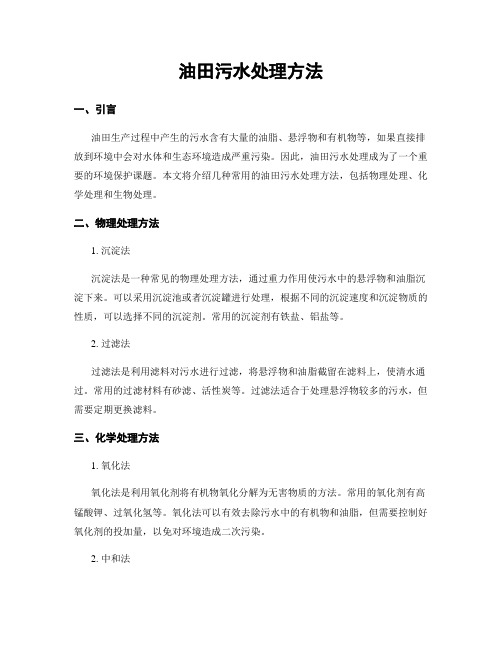
油田污水处理方法一、引言油田生产过程中产生的污水含有大量的油脂、悬浮物和有机物等,如果直接排放到环境中会对水体和生态环境造成严重污染。
因此,油田污水处理成为了一个重要的环境保护课题。
本文将介绍几种常用的油田污水处理方法,包括物理处理、化学处理和生物处理。
二、物理处理方法1. 沉淀法沉淀法是一种常见的物理处理方法,通过重力作用使污水中的悬浮物和油脂沉淀下来。
可以采用沉淀池或者沉淀罐进行处理,根据不同的沉淀速度和沉淀物质的性质,可以选择不同的沉淀剂。
常用的沉淀剂有铁盐、铝盐等。
2. 过滤法过滤法是利用滤料对污水进行过滤,将悬浮物和油脂截留在滤料上,使清水通过。
常用的过滤材料有砂滤、活性炭等。
过滤法适合于处理悬浮物较多的污水,但需要定期更换滤料。
三、化学处理方法1. 氧化法氧化法是利用氧化剂将有机物氧化分解为无害物质的方法。
常用的氧化剂有高锰酸钾、过氧化氢等。
氧化法可以有效去除污水中的有机物和油脂,但需要控制好氧化剂的投加量,以免对环境造成二次污染。
2. 中和法中和法是利用酸碱中和反应将污水中的酸性物质或者碱性物质中和至中性的方法。
常用的中和剂有氢氧化钠、氢氧化钙等。
中和法适合于处理酸性或者碱性污水,但需要控制好中和剂的投加量,以免产生过量的沉淀物。
四、生物处理方法1. 好氧生物处理法好氧生物处理法是利用好氧微生物对污水中的有机物进行降解的方法。
通过提供充足的氧气和适宜的温度、pH值等条件,促进微生物的生长和代谢活动,从而降解有机物。
好氧生物处理法具有处理效果好、投资成本低的优点。
2. 厌氧生物处理法厌氧生物处理法是利用厌氧微生物对污水中的有机物进行降解的方法。
与好氧生物处理法相比,厌氧生物处理法不需要额外供氧,适合于有机物浓度较高的污水处理。
但厌氧生物处理法处理效果受温度和pH值等条件的影响较大。
五、综合处理方法综合处理方法是将多种处理方法结合起来,以达到更好的处理效果。
常见的综合处理方法有物化处理、化生处理等。
油田污水处理方法

油田污水处理方法标题:油田污水处理方法引言概述:油田污水是指在石油开采和生产过程中产生的含有油类、气体、固体颗粒、重金属等有害物质的废水。
油田污水的处理是保护环境、维护生态平衡的重要环节。
本文将介绍几种常见的油田污水处理方法。
一、物理处理方法1.1 沉淀法:通过加入絮凝剂,使悬浮物沉降到底部,然后通过过滤或离心等方式分离出清水。
1.2 过滤法:通过过滤介质,如砂滤器、活性炭等,将悬浮物和油类颗粒截留在滤料上,得到清洁水。
1.3 蒸馏法:利用油水混合物的沸点差异,通过蒸馏过程将油类物质从水中分离出来。
二、化学处理方法2.1 氧化法:利用氧化剂如臭氧、过氧化氢等氧化有机物质,将其转化为无害物质。
2.2 中和法:通过加入中和剂如氢氧化钠、氢氧化钙等,将酸性或碱性废水中的有害物质中和成中性物质。
2.3 氧化还原法:通过改变废水中的氧化还原电位,促使有机物质氧化分解,降低其毒性。
三、生物处理方法3.1 厌氧处理:将油田污水置于无氧环境中,利用厌氧菌分解有机物质,产生沼气和二氧化碳。
3.2 好氧处理:将油田污水置于富氧环境中,利用好氧菌将有机物质氧化分解为二氧化碳和水。
3.3 植物处理:利用水生植物如莲藕、菖蒲等吸收废水中的有害物质,达到净化水质的目的。
四、膜分离技术4.1 超滤技术:利用超滤膜对废水进行过滤,将悬浮物、胶体颗粒等截留在膜上,得到清洁水。
4.2 反渗透技术:通过半透膜对废水进行过滤,将水分子从溶解物质中分离出来,得到高纯度的水。
4.3 离子交换技术:利用离子交换膜将废水中的离子物质进行交换,去除重金属等有害物质。
五、综合处理方法5.1 组合工艺:将物理、化学、生物等多种处理方法结合起来,根据废水的特性进行综合处理。
5.2 循环利用:将处理后的清洁水用于油田生产中的冷却、注水等环节,实现废水的循环利用。
5.3 持续改进:不断优化污水处理工艺,引入新技术、新设备,提高处理效率和水质达标率。
结语:通过物理、化学、生物、膜分离等多种处理方法的综合应用,可以有效地处理油田污水,减少对环境的污染,保护地下水资源,实现资源的可持续利用。
油田污水处理方法

油田污水处理方法一、引言油田污水是指在石油开采和生产过程中产生的含油、含盐、含有机物和重金属的废水。
由于油田污水的复杂性和高度污染性,对其进行有效处理是保护环境、实现可持续发展的重要任务。
本文将介绍几种常用的油田污水处理方法,包括物理处理、化学处理和生物处理。
二、物理处理方法1. 沉淀沉淀是一种常用的物理处理方法,通过重力作用使悬浮物和油水分离。
可以采用沉淀池或沉淀槽进行处理,将污水停留一段时间,使悬浮物沉淀到污水底部,然后将上清液排出。
这种方法适用于处理大颗粒的悬浮物和油脂。
2. 过滤过滤是利用过滤介质将悬浮物和油水分离的方法。
常用的过滤介质有砂滤器、活性炭滤器等。
将污水通过过滤介质,悬浮物和油脂被截留在过滤介质上,而清洁的水则通过滤器流出。
过滤方法适用于处理较小颗粒的悬浮物和油脂。
三、化学处理方法1. 混凝混凝是通过添加化学混凝剂使悬浮物和油水凝聚成较大的颗粒,便于沉淀和分离。
常用的混凝剂有聚合氯化铝、聚合硫酸铁等。
将混凝剂加入污水中,与悬浮物和油脂发生反应,形成絮凝物,然后通过沉淀或过滤将絮凝物分离出来。
2. 氧化氧化是利用化学氧化剂将有机物氧化为无机物的方法。
常用的氧化剂有过氧化氢、高锰酸钾等。
将氧化剂加入污水中,与有机物发生氧化反应,将有机物转化为无机物,从而达到降解有机物的目的。
四、生物处理方法1. 好氧生物处理好氧生物处理是利用好氧微生物将有机物降解为无机物的方法。
将污水通入好氧生物反应器,提供充足的氧气和适宜的温度、pH值等条件,好氧微生物将有机物分解为二氧化碳和水。
这种方法适用于有机物含量较高的油田污水。
2. 厌氧生物处理厌氧生物处理是利用厌氧微生物将有机物降解为甲烷等有机酸的方法。
将污水通入厌氧生物反应器,提供适宜的温度、pH值和缺氧条件,厌氧微生物将有机物分解为甲烷等有机酸。
这种方法适用于有机物含量较低的油田污水。
五、综合处理方法综合处理方法是将多种处理方法综合应用,以达到更好的处理效果。
油田污水处理方法
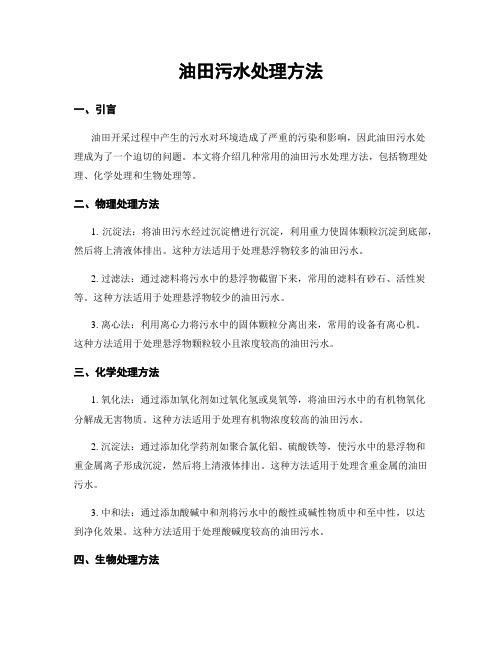
油田污水处理方法一、引言油田开采过程中产生的污水对环境造成了严重的污染和影响,因此油田污水处理成为了一个迫切的问题。
本文将介绍几种常用的油田污水处理方法,包括物理处理、化学处理和生物处理等。
二、物理处理方法1. 沉淀法:将油田污水经过沉淀槽进行沉淀,利用重力使固体颗粒沉淀到底部,然后将上清液体排出。
这种方法适用于处理悬浮物较多的油田污水。
2. 过滤法:通过滤料将污水中的悬浮物截留下来,常用的滤料有砂石、活性炭等。
这种方法适用于处理悬浮物较少的油田污水。
3. 离心法:利用离心力将污水中的固体颗粒分离出来,常用的设备有离心机。
这种方法适用于处理悬浮物颗粒较小且浓度较高的油田污水。
三、化学处理方法1. 氧化法:通过添加氧化剂如过氧化氢或臭氧等,将油田污水中的有机物氧化分解成无害物质。
这种方法适用于处理有机物浓度较高的油田污水。
2. 沉淀法:通过添加化学药剂如聚合氯化铝、硫酸铁等,使污水中的悬浮物和重金属离子形成沉淀,然后将上清液体排出。
这种方法适用于处理含重金属的油田污水。
3. 中和法:通过添加酸碱中和剂将污水中的酸性或碱性物质中和至中性,以达到净化效果。
这种方法适用于处理酸碱度较高的油田污水。
四、生物处理方法1. 好氧处理法:利用好氧微生物降解油田污水中的有机物,将其转化为二氧化碳和水。
这种方法适用于处理有机物浓度较高的油田污水。
2. 厌氧处理法:利用厌氧微生物将油田污水中的有机物转化为甲烷等可燃气体,同时产生沼气。
这种方法适用于处理有机物浓度较低的油田污水。
3. 植物处理法:利用水生植物如芦苇、菖蒲等吸收油田污水中的营养物质,同时通过植物根系的微生物降解有机物。
这种方法适用于处理有机物浓度较低且悬浮物较少的油田污水。
五、结论针对不同类型的油田污水,可以选择合适的处理方法进行处理。
物理处理方法适用于悬浮物较多或较少的污水,化学处理方法适用于有机物浓度较高或含重金属的污水,生物处理方法适用于有机物浓度较高或较低的污水。
油田污水处理

油田污水处理油田污水处理概述油田污水处理是指对产生于石油开采过程中的污水进行处理和净化的过程。
在石油开采过程中,油井产生的水含有大量的油脂、悬浮物、重金属和溶解性有机物等污染物,如果不经过处理直接排放到环境中,将对生态环境造成严重的污染。
因此,对油田污水进行处理和净化是十分必要的。
污水处理工艺机械处理机械处理是油田污水处理的第一步,它主要是通过物理方法去除污水中的悬浮物、油脂和颗粒物。
常见的机械处理方法包括:- 沉淀:利用重力作用,使污水中的固体颗粒物在污水中沉淀下来。
- 过滤:通过过滤介质,如砂石、滤纸等,过滤掉污水中的悬浮物和颗粒物。
- 离心分离:利用离心力,将污水中的悬浮物和油脂分离出来。
生化处理生化处理是指利用生物菌群对污水中的有机物进行降解和分解的过程。
在油田污水处理中,常用的生化处理方法有:- 好氧处理:通过注入氧气,利用好氧微生物对有机物进行分解和降解。
好氧处理过程中产生的废物一般是水和二氧化碳。
- 厌氧处理:不加氧气,利用厌氧微生物对有机物进行降解。
厌氧处理过程中产生的废物一般是水、甲烷和二氧化碳。
高级氧化处理高级氧化处理是指利用氧化剂(如臭氧、过氧化氢、氯等)对污水中的有机物进行降解的过程。
高级氧化处理常用于处理难降解的有机污染物。
膜分离技术膜分离技术是指利用膜对污水进行过滤和分离的过程。
常见的膜分离技术包括:- 超滤:通过超滤膜对污水进行过滤,过滤掉其中的悬浮物和胶体物质。
- 逆渗透:通过逆渗透膜对污水进行过滤,过滤掉其中的溶解性有机物、重金属、盐类等。
- 蒸发浓缩:将污水蒸发浓缩,通过膜对蒸发水进行分离,得到浓缩液和纯净水。
污水处理设备沉淀器沉淀器是用于沉淀固体颗粒物的设备。
常见的沉淀器包括:- 均质沉淀器:通过减小水流速度,使悬浮物沉淀下来。
- 沉砂池:利用水流的旋涡作用,将固体颗粒物沉淀到底部。
- 气浮池:通过注入微小气泡,使悬浮物上浮并从表面捞取。
好氧生物反应器好氧生物反应器是用于好氧生化处理的设备。
油田污水处理方法
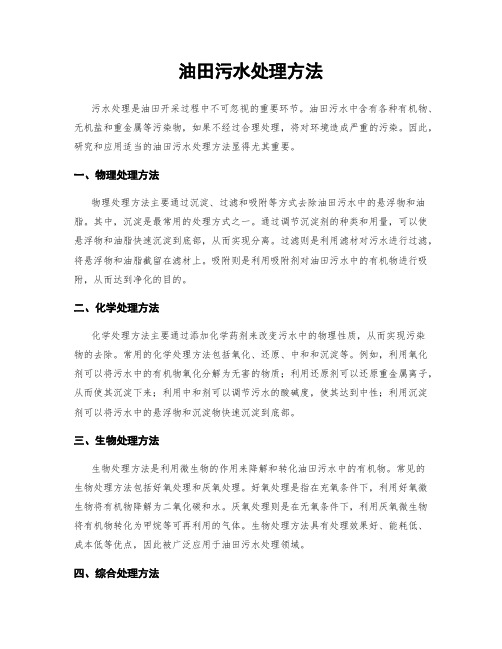
油田污水处理方法污水处理是油田开采过程中不可忽视的重要环节。
油田污水中含有各种有机物、无机盐和重金属等污染物,如果不经过合理处理,将对环境造成严重的污染。
因此,研究和应用适当的油田污水处理方法显得尤其重要。
一、物理处理方法物理处理方法主要通过沉淀、过滤和吸附等方式去除油田污水中的悬浮物和油脂。
其中,沉淀是最常用的处理方式之一。
通过调节沉淀剂的种类和用量,可以使悬浮物和油脂快速沉淀到底部,从而实现分离。
过滤则是利用滤材对污水进行过滤,将悬浮物和油脂截留在滤材上。
吸附则是利用吸附剂对油田污水中的有机物进行吸附,从而达到净化的目的。
二、化学处理方法化学处理方法主要通过添加化学药剂来改变污水中的物理性质,从而实现污染物的去除。
常用的化学处理方法包括氧化、还原、中和和沉淀等。
例如,利用氧化剂可以将污水中的有机物氧化分解为无害的物质;利用还原剂可以还原重金属离子,从而使其沉淀下来;利用中和剂可以调节污水的酸碱度,使其达到中性;利用沉淀剂可以将污水中的悬浮物和沉淀物快速沉淀到底部。
三、生物处理方法生物处理方法是利用微生物的作用来降解和转化油田污水中的有机物。
常见的生物处理方法包括好氧处理和厌氧处理。
好氧处理是指在充氧条件下,利用好氧微生物将有机物降解为二氧化碳和水。
厌氧处理则是在无氧条件下,利用厌氧微生物将有机物转化为甲烷等可再利用的气体。
生物处理方法具有处理效果好、能耗低、成本低等优点,因此被广泛应用于油田污水处理领域。
四、综合处理方法综合处理方法是将多种处理方法相结合,以达到更好的处理效果。
例如,物化处理和生物处理的结合,可以充分发挥各自的优势,提高处理效率。
此外,还可以结合膜分离技术、电化学技术等先进技术,进一步提高油田污水处理的效果。
综上所述,油田污水处理方法包括物理处理、化学处理、生物处理和综合处理等多种方法。
根据不同的污染物和处理要求,可以选择适当的处理方法进行处理。
在实际应用中,还需要考虑到处理成本、处理效率、环境影响等因素,综合选择最佳的处理方案。
油田污水处理方法
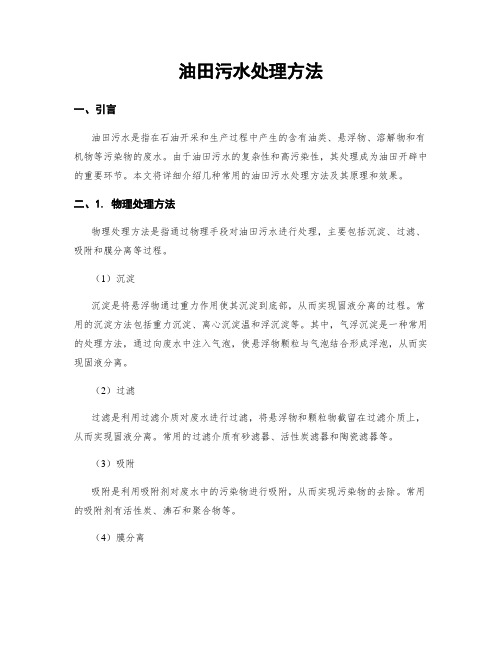
油田污水处理方法一、引言油田污水是指在石油开采和生产过程中产生的含有油类、悬浮物、溶解物和有机物等污染物的废水。
由于油田污水的复杂性和高污染性,其处理成为油田开辟中的重要环节。
本文将详细介绍几种常用的油田污水处理方法及其原理和效果。
二、1. 物理处理方法物理处理方法是指通过物理手段对油田污水进行处理,主要包括沉淀、过滤、吸附和膜分离等过程。
(1)沉淀沉淀是将悬浮物通过重力作用使其沉淀到底部,从而实现固液分离的过程。
常用的沉淀方法包括重力沉淀、离心沉淀温和浮沉淀等。
其中,气浮沉淀是一种常用的处理方法,通过向废水中注入气泡,使悬浮物颗粒与气泡结合形成浮泡,从而实现固液分离。
(2)过滤过滤是利用过滤介质对废水进行过滤,将悬浮物和颗粒物截留在过滤介质上,从而实现固液分离。
常用的过滤介质有砂滤器、活性炭滤器和陶瓷滤器等。
(3)吸附吸附是利用吸附剂对废水中的污染物进行吸附,从而实现污染物的去除。
常用的吸附剂有活性炭、沸石和聚合物等。
(4)膜分离膜分离是利用特殊的膜材料对废水进行分离和过滤,常用的膜分离方法有微滤、超滤、纳滤和反渗透等。
膜分离方法具有高效、节能、无二次污染等优点,广泛应用于油田污水处理中。
2. 化学处理方法化学处理方法是指通过化学反应对油田污水中的污染物进行去除或者转化的方法,常用的化学处理方法有氧化、还原、沉淀和中和等。
(1)氧化氧化是指通过氧化剂对废水中的有机物进行氧化反应,将其转化为无害的物质。
常用的氧化剂有过氧化氢、高锰酸钾和臭氧等。
(2)还原还原是指通过还原剂对废水中的氧化物进行还原反应,将其转化为无害的物质。
常用的还原剂有亚硫酸盐和二氧化硫等。
(3)沉淀沉淀是指通过添加沉淀剂使废水中的溶解物和悬浮物发生沉淀反应,从而实现固液分离。
常用的沉淀剂有氢氧化铁、氯化铁和聚合氯化铝等。
(4)中和中和是指通过添加酸碱中和剂,将废水中的酸性或者碱性物质中和至中性,从而达到废水的中和处理。
常用的中和剂有氢氧化钠、氢氧化钙和石灰等。
油田污水处理方法
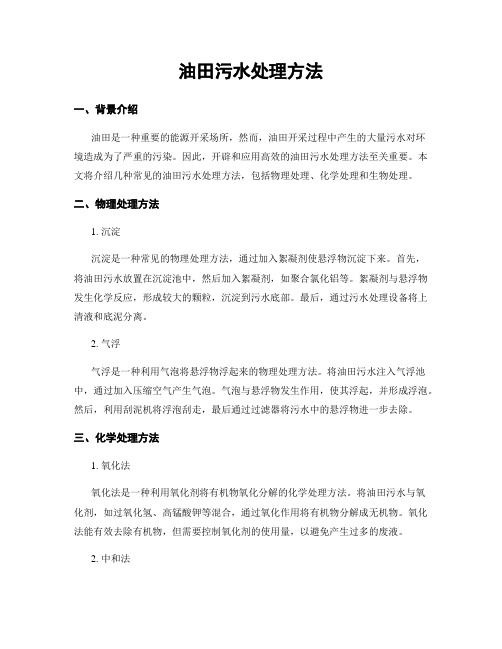
油田污水处理方法一、背景介绍油田是一种重要的能源开采场所,然而,油田开采过程中产生的大量污水对环境造成为了严重的污染。
因此,开辟和应用高效的油田污水处理方法至关重要。
本文将介绍几种常见的油田污水处理方法,包括物理处理、化学处理和生物处理。
二、物理处理方法1. 沉淀沉淀是一种常见的物理处理方法,通过加入絮凝剂使悬浮物沉淀下来。
首先,将油田污水放置在沉淀池中,然后加入絮凝剂,如聚合氯化铝等。
絮凝剂与悬浮物发生化学反应,形成较大的颗粒,沉淀到污水底部。
最后,通过污水处理设备将上清液和底泥分离。
2. 气浮气浮是一种利用气泡将悬浮物浮起来的物理处理方法。
将油田污水注入气浮池中,通过加入压缩空气产生气泡。
气泡与悬浮物发生作用,使其浮起,并形成浮泡。
然后,利用刮泥机将浮泡刮走,最后通过过滤器将污水中的悬浮物进一步去除。
三、化学处理方法1. 氧化法氧化法是一种利用氧化剂将有机物氧化分解的化学处理方法。
将油田污水与氧化剂,如过氧化氢、高锰酸钾等混合,通过氧化作用将有机物分解成无机物。
氧化法能有效去除有机物,但需要控制氧化剂的使用量,以避免产生过多的废液。
2. 中和法中和法是一种利用酸碱中和反应将酸性或者碱性污水中的酸碱度调整到中性的化学处理方法。
将油田酸性或者碱性污水与相应的中和剂混合,使其酸碱度逐渐接近中性。
中和法不仅能调整酸碱度,还能使污水中的金属离子沉淀下来,进一步净化水质。
四、生物处理方法1. 好氧生物处理好氧生物处理是一种利用好氧微生物将有机物降解为无机物的生物处理方法。
将油田污水送入好氧生物反应器中,通过加入适宜的氧气和微生物,使有机物被微生物降解为二氧化碳和水。
好氧生物处理能够高效去除有机物,但需要控制反应器中的氧气供应和微生物的生长条件。
2. 厌氧生物处理厌氧生物处理是一种利用厌氧微生物将有机物降解为甲烷等产物的生物处理方法。
将油田污水送入厌氧生物反应器中,通过提供适宜的温度和厌氧条件,使有机物被微生物降解为甲烷等产物。
油田污水处理方法

油田污水处理方法一、引言油田污水是指在石油开采和生产过程中产生的含油、含盐和其他污染物的废水。
由于油田污水的复杂性和对环境的潜在危害,有效的油田污水处理方法对于保护环境和可持续发展至关重要。
本文将介绍几种常见的油田污水处理方法,包括物理处理、化学处理和生物处理。
二、物理处理方法1. 沉淀沉淀是一种常见的物理处理方法,通过重力作用将悬浮物和油脂从污水中分离出来。
常用的沉淀设备包括沉淀池和沉淀罐。
沉淀池通过增加沉淀时间和减少流速来促进悬浮物的沉淀,而沉淀罐则通过引入气泡来提高悬浮物的沉降速度。
2. 过滤过滤是另一种常见的物理处理方法,通过过滤介质将悬浮物和油脂从污水中截留。
常用的过滤介质包括砂滤器、活性炭和纤维滤料。
过滤器的选择应根据悬浮物和油脂的粒径和浓度来确定。
3. 离心分离离心分离是利用离心力将悬浮物和油脂从污水中分离出来的物理处理方法。
离心分离器通过旋转运动产生的离心力将重质物质分离出来,从而实现油水分离。
三、化学处理方法1. 混凝混凝是一种常见的化学处理方法,通过添加混凝剂将悬浮物和油脂凝结成较大的颗粒,便于后续的沉淀或者过滤。
常用的混凝剂包括铝盐和铁盐。
混凝剂的选择应根据污水的性质和所需的处理效果来确定。
2. 氧化氧化是一种将有机物氧化为无机物的化学处理方法,可有效降解油田污水中的有机污染物。
常用的氧化剂包括过氧化氢、高锰酸盐和臭氧。
氧化剂的选择应根据有机污染物的种类和浓度来确定。
3. 中和中和是通过添加酸、碱或者中和剂将酸性或者碱性废水中的酸碱度调整到中性的化学处理方法。
中和可使废水的pH值接近中性,有利于后续的生物处理或者其他处理过程。
四、生物处理方法1. 厌氧消化厌氧消化是一种利用微生物在无氧条件下降解有机物的生物处理方法。
通过将油田污水引入厌氧消化池中,微生物将有机物转化为甲烷等可燃气体和沉淀物,达到净化污水的目的。
2. 好氧处理好氧处理是一种利用氧气和好氧微生物降解有机物的生物处理方法。
油田污水处理方法

油田污水处理方法污水处理是油田开辟过程中的重要环节,它涉及到对产生的废水进行处理,以确保环境的安全和可持续发展。
本文将详细介绍油田污水处理的标准格式,包括处理方法、设备和技术。
1. 污水处理方法1.1. 机械化处理方法机械化处理方法是油田污水处理的基本方法之一。
它包括沉淀、过滤、气浮和离心等过程。
首先,通过沉淀将污水中的固体物质沉淀下来,然后通过过滤去除悬浮物,再通过气浮去除溶解气体,最后通过离心去除弱小颗粒。
1.2. 生物处理方法生物处理方法是一种利用微生物降解有机物质的方法。
常见的生物处理方法包括好氧处理和厌氧处理。
好氧处理利用氧气供给微生物进行降解,而厌氧处理则在缺氧条件下进行。
这些方法可以有效地去除油田污水中的有机物质,减少对环境的影响。
1.3. 化学处理方法化学处理方法是利用化学物质对污水进行处理的方法。
常见的化学处理方法包括氧化、还原和沉淀等。
通过添加适量的化学药剂,可以有效地去除油田污水中的有机物质和重金属离子。
2. 污水处理设备2.1. 沉淀池沉淀池是油田污水处理中常用的设备之一。
它通过重力作用将污水中的固体物质沉淀下来,从而实现初步的固液分离。
2.2. 过滤器过滤器用于去除污水中的悬浮物。
它通过过滤介质(如砂、石英砂等)将悬浮物截留下来,从而实现固液分离。
2.3. 气浮机气浮机是一种利用气泡将污水中的悬浮物浮起来并从上部移除的设备。
它通过给污水注入气体,使气泡与悬浮物发生作用力,从而实现固液分离。
2.4. 生物反应器生物反应器是用于生物处理方法的设备。
它提供了一个适宜的环境,使微生物能够进行降解有机物质的活动。
2.5. 化学加药系统化学加药系统用于化学处理方法。
它可以自动控制药剂的投加量,确保处理效果的稳定和可靠。
3. 污水处理技术3.1. 膜分离技术膜分离技术是一种通过半透膜将污水中的溶质和溶剂分离的技术。
常见的膜分离技术包括超滤、纳滤和反渗透等。
这些技术可以有效地去除油田污水中的有机物质和溶解物质。
油田污水处理方法
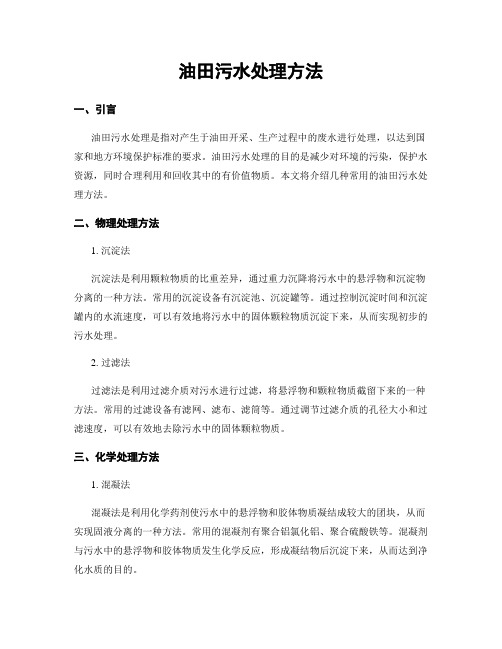
油田污水处理方法一、引言油田污水处理是指对产生于油田开采、生产过程中的废水进行处理,以达到国家和地方环境保护标准的要求。
油田污水处理的目的是减少对环境的污染,保护水资源,同时合理利用和回收其中的有价值物质。
本文将介绍几种常用的油田污水处理方法。
二、物理处理方法1. 沉淀法沉淀法是利用颗粒物质的比重差异,通过重力沉降将污水中的悬浮物和沉淀物分离的一种方法。
常用的沉淀设备有沉淀池、沉淀罐等。
通过控制沉淀时间和沉淀罐内的水流速度,可以有效地将污水中的固体颗粒物质沉淀下来,从而实现初步的污水处理。
2. 过滤法过滤法是利用过滤介质对污水进行过滤,将悬浮物和颗粒物质截留下来的一种方法。
常用的过滤设备有滤网、滤布、滤筒等。
通过调节过滤介质的孔径大小和过滤速度,可以有效地去除污水中的固体颗粒物质。
三、化学处理方法1. 混凝法混凝法是利用化学药剂使污水中的悬浮物和胶体物质凝结成较大的团块,从而实现固液分离的一种方法。
常用的混凝剂有聚合铝氯化铝、聚合硫酸铁等。
混凝剂与污水中的悬浮物和胶体物质发生化学反应,形成凝结物后沉淀下来,从而达到净化水质的目的。
2. 氧化法氧化法是通过氧化剂对污水中的有机物进行氧化分解的一种方法。
常用的氧化剂有臭氧、过氧化氢等。
氧化剂与污水中的有机物发生氧化反应,将其分解为无机物或者较易分解的有机物,从而达到净化水质的效果。
四、生物处理方法生物处理方法是利用微生物对污水中的有机物进行降解和转化的一种方法。
常用的生物处理设备有活性污泥法、生物膜法等。
1. 活性污泥法活性污泥法是利用活性污泥中的微生物对污水中的有机物进行降解和转化的一种方法。
污水经过曝气槽进行曝气,使污水中的有机物被微生物吸附和降解,然后通过沉淀池将污泥与水分离。
分离后的污泥可以经过进一步处理或者回收利用。
2. 生物膜法生物膜法是利用生物膜中的微生物对污水中的有机物进行降解和转化的一种方法。
污水通过生物膜,微生物在膜上形成生物膜,对污水中的有机物进行降解,然后通过分离装置将水与污泥分离。
石油厂污水处理方法

石油厂污水处理方法石油工业是全球经济中重要的一部分,然而,石油生产和加工过程中产生的大量废水带来了严重的环境问题。
因此,石油厂污水的处理成为了迫切需要解决的问题。
本文将介绍一些常见的石油厂污水处理方法。
1. 沉淀法沉淀法是一种常见的污水处理方法,可用来处理石油厂的废水,在处理过程中主要是利用重力将悬浮物和污染物沉淀下来。
首先,通过物理或化学方法将悬浮物凝聚成较大的颗粒,并使用沉淀池将颗粒沉淀下来。
这种方法可以有效地去除悬浮物和一些重金属离子,但对于难以沉淀的污染物效果有限。
2. 生物处理法生物处理法是一种使用微生物来分解并转化废水中有机物的方法。
这种方法通过在生物反应器中培养特定类型的微生物,使其通过生物降解的过程将有机物分解为水和二氧化碳。
这种方法可以高效地去除废水中的有机物,但对于一些难以分解的物质,如石油中的烃类化合物,效果有限。
3. 活性炭吸附法活性炭吸附法是一种常见的物理吸附方法,通过将废水通过活性炭床,活性炭表面的微孔和孔道能够吸附废水中的有机物和一些溶解的污染物。
这种方法可以高效去除废水中的有机物和一些小分子离子,但对于大分子物质的吸附效果有限。
4. 膜技术膜技术是一种基于膜分离的废水处理方法,通过在膜表面形成过滤层,将废水中的溶解物和悬浮物通过膜的选择性阻挡。
常见的膜技术包括纳滤、超滤、反渗透等。
这些膜技术可以高效地去除废水中的溶解物和大部分悬浮物,但对于一些微小颗粒的去除效果较差。
5. 高级氧化处理法高级氧化过程是一种利用氧化剂将有机物氧化分解的方法,可有效去除废水中的有机物和一些难以分解的物质。
常用的高级氧化剂包括过氧化氢、臭氧和紫外线辐射等。
这种方法对于石油厂的废水处理效果良好,但是成本较高。
在实际应用中,通常需要综合运用多种污水处理方法来处理石油厂的废水,以达到更好的处理效果。
此外,应根据石油厂废水的具体情况进行合理的工艺设计和控制,保证处理效率和减少对环境的影响。
总结起来,石油厂污水处理方法应包括沉淀法、生物处理法、活性炭吸附法、膜技术和高级氧化处理法等。
油田污水处理方法

油田污水处理方法一、引言油田污水是指在石油开采和生产过程中产生的含油废水和含有各种有机和无机污染物的废水。
这些废水的排放对环境造成严重污染,因此需要采取有效的处理方法进行处理。
本文将介绍几种常用的油田污水处理方法,包括物理方法、化学方法和生物方法。
二、物理方法1. 沉淀法沉淀法是通过调节油田污水的pH值,加入适量的沉淀剂,使污水中的悬浮物和重金属离子沉淀下来。
常用的沉淀剂有铁盐、铝盐等。
沉淀后的污泥可以通过过滤、离心等方法进行固液分离。
2. 滤过法滤过法是将油田污水通过滤料进行过滤,将悬浮物和颗粒物截留在滤料上,从而实现固液分离。
常用的滤料有砂石、活性炭等。
滤过后的污水可以进一步进行处理或者直接排放。
3. 蒸发法蒸发法是将油田污水加热,使其中的水分蒸发掉,从而实现浓缩和固体化处理。
蒸发后的固体可以进行焚烧或填埋处理,而蒸发后的水分可以进行进一步处理或者回收利用。
三、化学方法1. 氧化法氧化法是通过加入氧化剂,如过氧化氢、高锰酸钾等,将油田污水中的有机物氧化为无机物,从而降低水中有机物的浓度。
氧化后的废水可以通过沉淀、过滤等方法进行固液分离。
2. 吸附法吸附法是通过加入吸附剂,如活性炭、沸石等,将油田污水中的有机物吸附到吸附剂表面,从而实现有机物的去除。
吸附后的吸附剂可以进行再生利用,而吸附后的废水可以进行进一步处理或者直接排放。
3. 中和法中和法是通过加入中和剂,如氢氧化钠、氢氧化钙等,将油田污水中的酸性物质中和为中性或碱性,从而降低废水的酸碱度。
中和后的废水可以通过沉淀、过滤等方法进行固液分离。
四、生物方法1. 好氧生物处理法好氧生物处理法是利用好氧微生物将油田污水中的有机物降解为无机物,从而实现废水的处理。
好氧微生物需要充足的氧气供应,因此需要提供充足的曝气设备。
好氧生物处理法适用于有机物浓度较低的油田污水。
2. 厌氧生物处理法厌氧生物处理法是利用厌氧微生物将油田污水中的有机物降解为无机物,从而实现废水的处理。
油田污水处理方法

油田污水处理方法
油田污水处理方法包括以下几种:
1. 沉淀-过滤:通过沉淀和过滤的方式去除污水中的固体颗粒物,其中沉淀是指将污水静置一段时间,使悬浮物沉淀到底部,然后将上清液体从上部分离开。
过滤是通过过滤介质(如砂、碳等)将污水中的固体颗粒物截留下来。
2. 段落油-溶解气浮:这是一种常用的油田污水处理方法,通过将污水中的油脂进行段落油(或称油-溶解)处理,使其转化为微小的油-溶解颗粒,然后利用溶解气浮设备将其浮出水面并去除。
3. 活性炭吸附:活性炭吸附是一种常用的去除污水中有机污染物的方法。
通过将活性炭投加到污水中,有机污染物会被活性炭吸附,从而达到净化水质的目的。
4. 生物处理:生物处理是利用微生物将有机物、氨氮等污染物降解为无毒或低毒物质的方法。
常见的生物处理方法包括活性污泥法、固定化生物膜法、厌氧处理法等。
5. 离子交换:离子交换是利用离子交换树脂将污水中的阳离子或阴离子进行吸附并交换,从而去除污水中的有害物质。
常见的应用是通过离子交换树脂将污水中的重金属去除。
6. 高级氧化:高级氧化是利用氧化剂(如臭氧、过氧化氢等)在一定条件下对污水进行氧化反应,可将有机物质降解为低分子化合物或水和二氧化碳。
这种方法对难降解的有机污染物有较好的处理效果。
油田污水处理..简版

油田污水处理..油田污水处理在油田开采过程中,会产生大量的污水,主要来自于注水、沉降池、进水处理、压裂流法以及油气回收等环节。
这些废水中含有各种有机和无机物质,对环境造成严重污染。
因此,油田污水处理是一个非常重要的问题,需要采取适当的措施来净化和处理油田污水。
油田污水处理方法1. 物理处理方法物理处理方法是指通过物理手段将污水中的固体颗粒和悬浮物分离出来,以达到净化水质的目的。
常见的物理处理方法包括沉淀、过滤、离心等。
- 沉淀:利用重力作用使固体颗粒在污水中沉降,通过沉淀池将固体颗粒分离出来。
- 过滤:通过滤料或滤网将污水中的固体颗粒拦截下来,达到分离的效果。
- 离心:利用离心力将污水中的悬浮物分离出来,常用于处理高浓度的污水。
2. 化学处理方法化学处理方法是指通过添加化学药剂来改变污水中的物理性质和化学性质,从而分离和去除污染物。
常见的化学处理方法包括沉淀法、氧化法、中和法等。
- 沉淀法:通过添加沉淀剂使污水中的悬浮物和溶解物发生沉淀,从而达到净化水质的目的。
- 氧化法:通过添加氧化剂将污水中的有机物氧化分解为无机物,进而降低水中的有机物含量。
- 中和法:通过添加中和剂对酸性或碱性废水进行中和处理,使其达到中性或接近中性。
3. 生物处理方法生物处理方法是指利用微生物的作用来降解和去除污染物,通过生物反应器将有机物转化为无机物,从而净化水质。
生物处理方法包括生物滤池、活性污泥法、生物膜法等。
- 生物滤池:利用生物滤材对污水中的有机物进行降解和吸附,通过生物滤材层的作用将有机物去除。
- 活性污泥法:利用活性污泥对污水中的有机物进行降解和吸附,并通过氧化、还原等反应将有机物转化为无机物。
- 生物膜法:利用生物膜对污水中的有机物进行吸附和降解,通过生物膜层的作用将有机物去除。
油田污水处理设备为了实现高效、稳定的油田污水处理,需要使用一系列的处理设备。
常用的油田污水处理设备包括:- 沉淀池:用于进行物理悬浮物的沉淀和分离。
- 1、下载文档前请自行甄别文档内容的完整性,平台不提供额外的编辑、内容补充、找答案等附加服务。
- 2、"仅部分预览"的文档,不可在线预览部分如存在完整性等问题,可反馈申请退款(可完整预览的文档不适用该条件!)。
- 3、如文档侵犯您的权益,请联系客服反馈,我们会尽快为您处理(人工客服工作时间:9:00-18:30)。
油田相关污水处理调研目录一、油田污水处理现状 (2)1.1油田污水产生以及特性 (2)1.2油田相关污水的大致去向 (2)二、油田采出水 (3)2.1采出水主要特点 (3)2.2采出液废水处理工艺 (3)2.2.1物理方法 (4)2.2.2化学法 (5)2.2.3生物处理法 (5)2.3油田回注水处理 (5)2.3.1常规油田回注处理工艺 (5)2.3.2稠油回注水处理工艺 (5)2.3.3聚合物驱采出水处理工艺 (6)2.4采出水外排处理工艺 (6)2.5采出水治理涉及到的设备 (7)三、废弃钻井液特征以及处理工艺 (8)3.1钻井液特征 (8)3.2废钻井液处理技术研究 (8)3.2.1电化学技术 (9)3.2.2热蒸馏法 (9)3.2.3溶剂萃取法 (9)3.2.4废弃钻井液转化为水泥浆技术(MTC)技术 (9)3.2.5超临界流体提取技术(SFE) (10)3.2.6化学破乳法 (10)3.2.7微生物处理技术 (11)3.3工业化处理实验 (11)四、压裂返排液的处理 (13)4.1压裂返排液的特征 (13)4.2压裂返排液的处理工艺 (13)4.3应用实例 (13)五、小结 (14)5.1油田污水处理方法对比分析 (14)5.2展望 (15)一、油田污水处理现状1.1油田污水产生以及特性在油田生产过程中,广义上油田含油污水主要有几个来源:油田采出水、钻井相关废水、以及其他类型的废水。
我国各油田基本都采用注水开发方式,即注入高压水保持油层压力,驱动原油从油井开采出来。
经过一段时间注水后,注入水将伴随原油被开采出来,即采出水。
稠油油田开发是从油井向地层注入高压水蒸汽,注入一段时间后水蒸气将稠油减粘,原油与水蒸汽冷凝水混合在一起从油井采出,这种水也称为采出水。
随着油田原油含水率的不断上升,油田采出水成为油田含油污水的主要来源。
因此,狭义的油田含油污水主要指油田采出水。
钻井污水成分复杂,主要包括钻井液、洗井液压裂返排液等。
其它类型污水主要包括含油污泥堆放场所产生的渗滤水、洗涤设备的产生的污水、油田地表径流雨水、生活污水以及事故性泄露和排放引起的污水等等。
1.2油田相关污水的大致去向油田相关污水情况如下表:本调研主要从油田采出水以及钻井相关废水展开技术调研。
二、油田采出水2.1采出水主要特点油田采出水是各油层的产出液经原油脱水工艺处理后的脱出水。
它包括油层中原有的地层水及注入到油井的注入水。
油田采出水成分复杂,而且不同油区采出水的成分也有很大差别。
由于采出水在地下时与高温高压的油层接触,溶进了盐类、原油、悬浮物、有害气体、有机物等,采出原油经脱水工艺处理时,还要加入破乳剂和漂白剂。
因而,油田采出水中一般含有一定量的原油,无机离子,硫化物,有机酚,氰,细菌,固体颗粒以及水站原油处理中所投加的破乳剂,絮凝剂和杀菌剂等化学药剂。
既无法达到采出水回注地层的水质要求,也不能满足排放水质指标。
聚合物的普遍采用使得油田采出水的处理难度大大加大,因为它使油珠的表面电荷结构更加复杂化,形成水一油一水相互结合的多重结构。
由于原油产地地质条件、原油性质、注水性质以及原油集输和初加工的整个工艺不尽相同,各油田含油污水水质有较大的差异。
特点有下面几点:(1)污水废液热量高,温度高。
大部分废液温度在20~70℃左右,多数为40℃左右,倘若直接外排会造成环境热污染。
(2)污油占比大。
以分散油及悬浮油为主,高达80%,剩下的则含有一部分的乳化性油和溶解于其中得污油形式组成,通常情况下含油量为1000mg/L,更有甚者达到3000~5000mg/L。
(3)矿化度高。
多种夹杂在地层中的矿物质盐离子会在污水从油井内部被采出的过程中溶解在污水中,,如以离子形式存在的钾等大量金属阳离子,和以硫酸根为主的各类阴离子等,矿化度通常情况下不低于2000mg/L,但会有少量的会高达105mg/L。
(4)含有相应程度的悬浮物。
分别是大量泥沙、各种盐类性的腐蚀产物、胶质、等种类众多的杂质。
(5)含有不同种类的有机物质存在。
这主要是由于原油本身的组成成分中包含有各种不同类型的有机物以及在整个开采过程中使用的各种化学添加剂,造成的直接结果就是油田污水中化学需氧量COD 的含量(Chemical Oxygen Demand)会相应变高,从而为微生物的生长创造有利条件。
(6)细菌含量高。
主要是因为油田现场所排污液自身温度很适宜与生长,在20~70℃左右,并且污水中含有各种有机物,在这种情况下给细菌的生长提供了适宜的生存条件,才会造成污水中有比如硫酸还原菌、铁细菌、腐生菌等的大量存在,有些污水中细菌含量甚至高达106个/mL,由于这些细菌的存在,会造成水体自身流动性的降低、并且会造成对所接触装置的腐蚀,还会引起输油管线的堵塞。
前面简单阐述了油田污水的来源,根据现阶段,油气田开采现状状,在我国大部分的石油企业中,开采工作基本已经到达了后期,随着石油的开采,含水量也在不断的增加,导致油田采出液逐渐增加。
2.2采出液废水处理工艺国内采出水的处理工艺,油田采出水经过处理后主要用于回注。
总体来说多数采用三段处理工艺即除油一混凝沉降(或气浮)一过滤,再辅以缓蚀、阻垢、杀菌处理后即可用于回注。
用于油田回注水时,此时对回注水水质有着严格的要求,一般执行企业标准SY/T5329-2012对污水中的含油量、悬浮固体、SRB等多项指标要进行严格的控制,防止其对地层产生伤害。
但是目前采出水还无法完全回注到地层,外排量在增加。
外排采出水的COD值偏高,特别是对于稠油污水、聚合物采出水、高含盐采出水、达标排放率就更低。
工艺过程中研究的主要方法有物理方法、化学方法以及生物方法。
2.2.1物理方法物理处理法的重点是去除废水中的矿物质和大部分固体悬浮物、油类等。
物理处理法包括重力分离、过滤、离心分离、粗粒化和蒸发等方法。
(1)重力分离技术依靠油水比重差进行重力分离是油田采出水治理的关键。
从油水分离的试验结果看,沉淀时间越长,从水中分离浮油的效果越好。
自然沉降除油罐、重力沉降罐平流式隔油池和斜板式隔油池作为采出水治理的基本手段,己被各油田广泛使用。
(2)离心分离离心分离是使装有废水的容器高速旋转,形成离心力场,因颗粒和污水的质量不同,受到的离心力也不同。
质量大的受到较大离心力作用被甩向外侧,质量小的废水则留在内侧,各自通过不同的出口排出,达到分离污染物的目的。
液一液水力旋流器是用于油田采出水处理系统的新型设备,它具有体积小、重量轻、分离性能好、运行安全可靠等优点。
目前在世界各地的油田。
(3)粗粒化法粗粒化法,又称聚结,是分离含油废水中分散油的物理化学方法。
在运行中,用填充粗粒化材料的床层改善含油废水的分离性能。
采用粗粒化的方法具有设备简单、投资少、粗粒化材料使用周期较长、不需用电和外加添加剂等优点。
目前常用的粗粒化材料除了石英砂、无烟煤、蛇纹石、陶粒等四种材料外,树脂也是近年新开发的一种粗粒化滤料。
树脂经过表面活性剂处理之后,不仅具有亲油性,而且具有反复可用性。
粗粒化设备能去除大于的20um 的油粒,同时该方法也可去除乳化油。
(4)过滤精细过滤技术采出水经过沉降、水力旋流等前处理后,大部分悬浮物及油已被去除,但其中悬浮物指标仍不能满足回注标准,因此采出水必须进行过滤。
近年来,随着纤维材料的应用和发展,以纤维材料为滤料发展起来的深床高精度纤维球过滤器,在食品、制药、酿造等工业领域应用较多。
其滤料纤维细密,过滤时可以形成上大下小的理想滤料空隙分布,纳污能力大,去除悬浮物的效果高于石英砂、核桃壳滤料,而且反洗时不会出现滤料流失的现象。
(5)膜过滤法膜过滤法是在近20多年迅速发展起来的分离技术。
国内外己经大量开发了超滤膜技术处理油田采出水的工艺。
与传统污水处理方法存在着一定的差异,使用这种技术的时候,通常情况下,不需要破乳过程,另一方面,分离时,能够将浓缩液焚烧掉,这个环节没有含油污泥形成,操作简单,并且分离效果好。
但是这种技术中用到的膜污染严重,对其进行清洗比较困难,成本相对较高,因此需要预处理来减少含污量,从而减轻后续膜处理的设备负担。
除了预处理与设计高性能的膜组件,还可把膜处理和其它技术(例如电化学法)组合,这样可以有效的提高处理效果,并可以在很大程度上减小成本。
2.2.2化学法油田采出水的化学处理方法主要用于处理废水中不能单独用物理方法或生物方法去除的一部分胶体和溶解性物质,特别是采出水中的乳化油。
所采用的化学处理方法主要有混凝沉淀、化学氧化和中和法。
先阶段研究的化学氧化法较为新的技术为臭氧氧化、超临界水氧化技术。
2.2.3生物处理法目前国内普遍采用A/O法,即先厌氧后好氧的方法进行处理。
序批间歇式活性污泥法(SBR)是融厌氧、好氧为一体的处理方法,因此在研究中用的较普遍。
2.3油田回注水处理2.3.1常规油田回注处理工艺常规油田回注水处理工艺对于中、高渗透油层回注的含油废水,大部分油田都采用“三段式”常规处理工艺极:自然沉降一混凝一过滤。
对于中、低渗透油层的含油废水,一般选用“三段式”加“精细过滤”工艺。
2.3.2稠油回注水处理工艺稠油采出水特点一般有:悬浮物含量高、水温高、油水密度差小、粘滞性大、成分复杂多变。
稠油废水经过处理后一部分用于回注,一部分还需再经过深度处理用于热采锅炉的给水。
稠油回注水处理工艺2.3.3聚合物驱采出水处理工艺随着聚合物驱的加大使用,使含油废水处理起来更加困难。
常规的“二级沉淀”和“二级过滤”处理工艺已经满足不了出水水质的要求了。
我国对于含聚废水的处理主要用于回注,因此处理该类废水的技术主要集中在除油和除聚合物两方面。
而大庆油田开发的横向流除油器能够去除含聚废水中的油类,具有很高的推广价值。
大庆油田采出水横向处理工艺2.4采出水外排处理工艺随着国民经济的不断提高,环境保护越来越受到重视,对污水排放指标要求也越来越高。
采出液在回注一部分的同时,有部分处理后采取外排的形式。
涸洲岛处理厂的污水处理就是采用生化处理来去除水中有机物的,污水处理采用流程如下图。
常用的采出水外排工艺:可采用SBR法、水解酸化一接触氧化法等,对水中难于被生物降解的有机物,可采取化学沉淀法去除。
处理流程如下:该流程中要根据水质情况来选择是否要采用一级或两级及生化处理和化学沉淀。
对于不能用生化处理的污水,应采用物化方法进行处理,物化方法有化学沉淀、活性炭吸附、光催化氧化等方法等。
2.5采出水治理涉及到的设备近些年来国外开发了一些新的用于采出水处理设备。
(l)净化采出水装置,该装置实际上是一种密闭的浮选箱。
该浮选箱有4个浮选室,各个浮选室都有一个气体布管,处理过的采出水分为两层,下层为清水上层为浮油,浮油收集于储油箱内。
(2)浮选柱,浮选装置在侧部采用布气技术,能分离含油废水中的细小悬浮物和油滴。