钣金零件折弯工艺简析
钣金折弯方法,图文讲解四种折弯工艺!

折弯是一种对平面板件进行折叠、弯曲的工艺,它在整个加工链中紧随切割工序之后。
工件放在带有V型开口的凹模上。
楔形刀具(上刀)将工件压入V型开口中,并以这种方式将板材折弯到需要的角度。
大多数折弯件采用悬空折弯、模中折弯以及折边与压合等工艺与方法制成。
作业方式均遵循同一原理:冲芯将工件压入凹模的下模中。
因此,执行上述工艺与方法的折弯机被称为模压折弯机。
1、悬空折弯冲芯将工件压入凹模,却不将其压向模具壁。
冲芯下移期间,工件边向上弯折并形成夹角。
冲芯将工件压入凹模的深度越大,角度就越小。
此时,冲芯和凹模之间留有空隙。
悬空折弯也被称为路径依赖型工艺。
每种夹角都需要特定路径。
机床控制系统同时计算路径与相应的冲压力。
路径与冲压力取决于模具、材料与产品特性(夹角、长度)。
2、模中折弯冲芯将工件完全压入凹模,因此凹模、工件与冲芯之间不留空隙。
这种工序被称为合模。
冲芯与凹模必须精确相互贴合。
因此,每种夹角与形状都需要相应的模具组件。
工件一旦完全压入,冲芯则无法继续向下移动。
机床控制系统继续提升冲压力,直至达到规定值。
施加至工件的压力由此上升,从而呈现出冲芯与凹模的轮廓。
夹角在高压作用下逐渐稳固,几乎彻底消除回弹问题。
3、翻板折弯机床内置的折弯摆臂由C形型材构成,其上安装有下部与上部折弯模具。
折弯时C形型材向上或向下移动,或是进行小范围椭圆形运动,即翻转。
摆臂折弯机半自动化运行,以快速性与灵活性着称,即使是小批量生产也完成得毫不逊色。
此外,通过翻板折弯技术还可使用同一模具在单个部件上实现多种半径尺寸的高效折弯。
4、折边与压合板材边缘通常被完全弯折(例如盒边缘),随后折边相互平行。
成品件整体因此更加稳定或是形成边缘防护。
随后折边内通常需要挂入其他零件。
折边与压合分为两个步骤完成:首先操作员预先折好30°夹角,然后将工件重新放入并压合夹角。
如果边缘之间存在空隙,则称为折边。
压合中弯边则完全相互挤压。
折边是路径依赖型,压合却是力度依赖型。
钣金双边折弯90°的加工方法
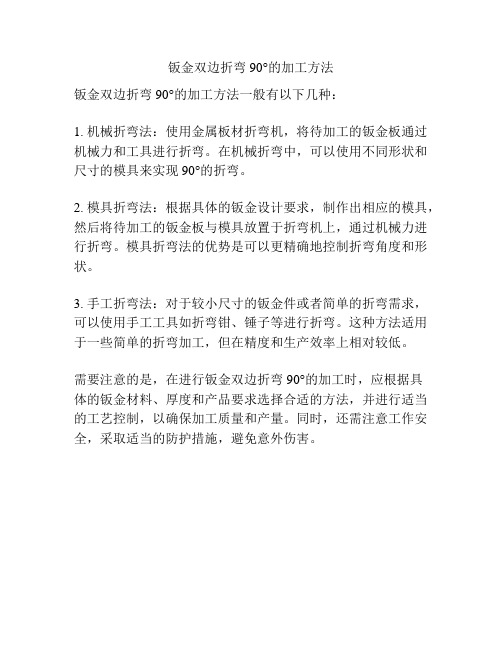
钣金双边折弯90°的加工方法
钣金双边折弯90°的加工方法一般有以下几种:
1. 机械折弯法:使用金属板材折弯机,将待加工的钣金板通过机械力和工具进行折弯。
在机械折弯中,可以使用不同形状和尺寸的模具来实现90°的折弯。
2. 模具折弯法:根据具体的钣金设计要求,制作出相应的模具,然后将待加工的钣金板与模具放置于折弯机上,通过机械力进行折弯。
模具折弯法的优势是可以更精确地控制折弯角度和形状。
3. 手工折弯法:对于较小尺寸的钣金件或者简单的折弯需求,可以使用手工工具如折弯钳、锤子等进行折弯。
这种方法适用于一些简单的折弯加工,但在精度和生产效率上相对较低。
需要注意的是,在进行钣金双边折弯90°的加工时,应根据具
体的钣金材料、厚度和产品要求选择合适的方法,并进行适当的工艺控制,以确保加工质量和产量。
同时,还需注意工作安全,采取适当的防护措施,避免意外伤害。
钣金的折弯工艺汇总(图解)

锁金的折弯工艺汇总(图解)1、什么是镀金折弯?镀金折弯是一种金属加工技术,用于将扁平的镀金件变成V形、U形或槽型。
这是一个重要且方便的制造过程,因为将一块扁平金属板弯曲成新形状比从实心工件加工v、u或通道形状或在铸造厂中铸造要便宜得多。
此外,弯曲产生的零件比例如将两片扁平金属片焊接成V形的零件更坚固。
许多类型的镀金折弯涉及使用称为制动器的机器,有时称为折弯机或镀金折叠机。
可以手动施加力,也可以使用例如液压装置施加力。
2、镀金折弯设备最重要的镀金折弯设备是制动器,它有几种不同的形式: 檐口制动器是一种简单的折弯机——也是制造业中使用最广泛的制动器一一它将一块金属板夹在一个平面上,然后通过可移动的折弯叶片的运动,使用力进行直弯或简单的折痕。
折弯机是一种使用移动冲头和相应模具的折弯机。
在此过程中,金属板被放置在模具上,并且冲头被强制移动到金属中,迫使其进入模具。
根据模具的形状,可以使用折弯机来制作V形弯、U形弯和其他形状。
箱式制动器(也称为手指制动器)是另一种折弯机,它使用一排金属“手指”来实现多个自定义折弯。
顾名思义,箱盘式制动器通常用于制作定制尺寸的盒子。
棒材折叠机是一种小型且简单的折弯机,带有一个手柄,可以夹住金属板并以单一动作弯曲它。
3、镀金折弯的种类有不同种类的镀金折弯用于以不同的方式实现不同的折弯。
其中三种折弯方法(空气折弯、打底和压印)使用折弯机,而其他折弯方法则使用各种机械。
1)空气弯曲空气弯曲是一种折弯折弯方法,在这种方法中,冲头将金属板压入模具,但不会太远以至于它接触到模具的壁。
这种方法不如其他方法准确,但它非常灵活:它可以用来制作V、U和其他形状的弯曲。
这部分是因为模具几何形状不需要完全对应于所需的镀金弯曲,因为两个表面之间没有接触。
2)打底打底是另一种折弯折弯方法。
在打底过程中,冲头将金属板完全压入模具,形成与模具内部几何形状相对应的弯曲。
它用于制作V 形弯曲。
3)冲压冲压是一种更昂贵的折弯折弯类型,其中冲头以更大的力在银金和模具中降低,从而产生永久变形而回弹很小。
钣金折弯知识讲解
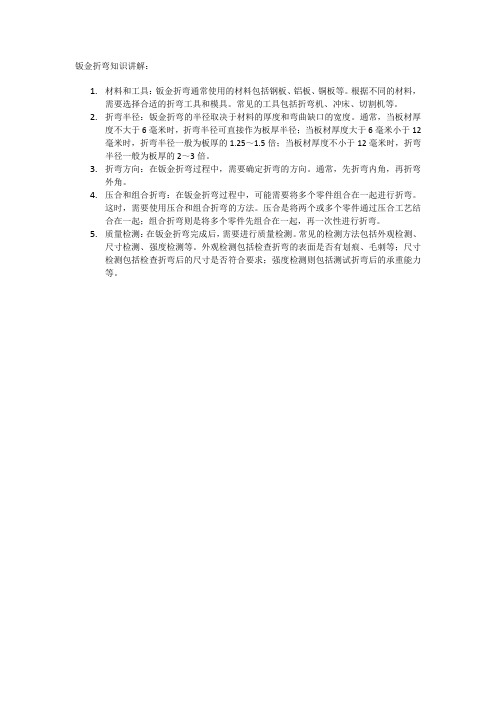
钣金折弯知识讲解:
1.材料和工具:钣金折弯通常使用的材料包括钢板、铝板、铜板等。
根据不同的材料,
需要选择合适的折弯工具和模具。
常见的工具包括折弯机、冲床、切割机等。
2.折弯半径:钣金折弯的半径取决于材料的厚度和弯曲缺口的宽度。
通常,当板材厚
度不大于6毫米时,折弯半径可直接作为板厚半径;当板材厚度大于6毫米小于12毫米时,折弯半径一般为板厚的1.25~1.5倍;当板材厚度不小于12毫米时,折弯半径一般为板厚的2~3倍。
3.折弯方向:在钣金折弯过程中,需要确定折弯的方向。
通常,先折弯内角,再折弯
外角。
4.压合和组合折弯:在钣金折弯过程中,可能需要将多个零件组合在一起进行折弯。
这时,需要使用压合和组合折弯的方法。
压合是将两个或多个零件通过压合工艺结合在一起;组合折弯则是将多个零件先组合在一起,再一次性进行折弯。
5.质量检测:在钣金折弯完成后,需要进行质量检测。
常见的检测方法包括外观检测、
尺寸检测、强度检测等。
外观检测包括检查折弯的表面是否有划痕、毛刺等;尺寸检测包括检查折弯后的尺寸是否符合要求;强度检测则包括测试折弯后的承重能力等。
产品结构设计——钣金件的折弯
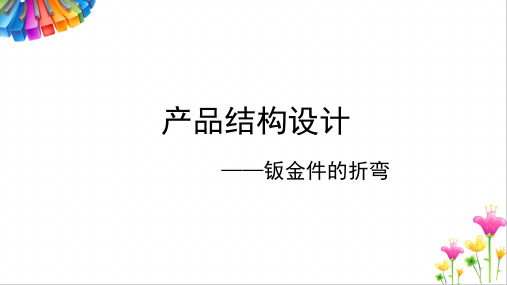
——钣金件的折弯钣金件的折弯是指在钣金件上做直边、斜边、弯曲边等形状,如将钣金弯成L形、U形、V形等。
折弯加工可采用模具折弯或专业的折弯机折弯,模具折弯一般用于外形复杂、尺寸较小、产量多的钣金产品,折弯机折弯一般用于外形复杂、尺寸较大、小批量生产的钣金产品。
设计折弯的钣金产品时要注意其独特的工艺性。
钣金件的折弯1.钣金折弯件的精度2.钣金折弯件的材料3.钣金折弯件的结构工艺性4.钣金折弯件弯曲工序的安排1.钣金弯曲件精度弯曲件的精度受坯料定位、偏移、翘曲和回弹等因素的影响,弯曲的工序数目越多,精度也越低。
一般弯曲加工,弯曲件的角度偏差见表1,弯曲件的尺寸公差见表2。
表1 弯曲件的角度偏差表2 弯曲件的直线尺寸公差2.钣金折弯件的材料弯曲件的材料如果具有足够的塑性,并且屈服强度σs小,弹性模量E大、力学性能稳定,则有利于弯曲成形和工件质量的提高。
例如软钢、软黄铜和铝等材料的弯曲成形性能好。
而脆性较大的材料,如磷青铜、铍青铜、弹簧等,则不利于弯曲成形。
3.弯曲件的结构工艺性(1)弯曲半径弯曲件的弯曲半径不能小于材料的最小弯曲半径,否则,在弯曲变形区外层表面会出现裂纹。
如果要求弯曲件的弯曲半径小于材料的最小弯曲半径时,可以参照本章第二节中有关提高弯曲极限变形程度的方法予以解决。
弯曲件的最大弯曲半径一般不加以限制,只要能控制回弹量,保证工件的精度即可。
(2)折弯件的形状弯曲件形状应该对称,弯曲半径左右一致,如果弯曲件不对称,由于板料与模具之间的摩擦阻力不均匀,坯料在弯曲过程中会产生滑动,造成偏移,如下图所示。
为了防止偏移现象的发生,应在模具上增加压料装置,或者在弯曲件上增加工艺孔定位。
(3)折弯件的直边高度弯曲件的直边高度不宜过小,否则无法保证弯曲件的直边平直,应使H> 2t,如图1所示。
如果H< 2t时,为了得到形状准确的零件,则需要在弯曲圆角处预先压槽,再弯曲,如图2所示;或者增加直边高度,弯曲后再切掉多余部分,如图1所示。
钣金折弯工艺分析
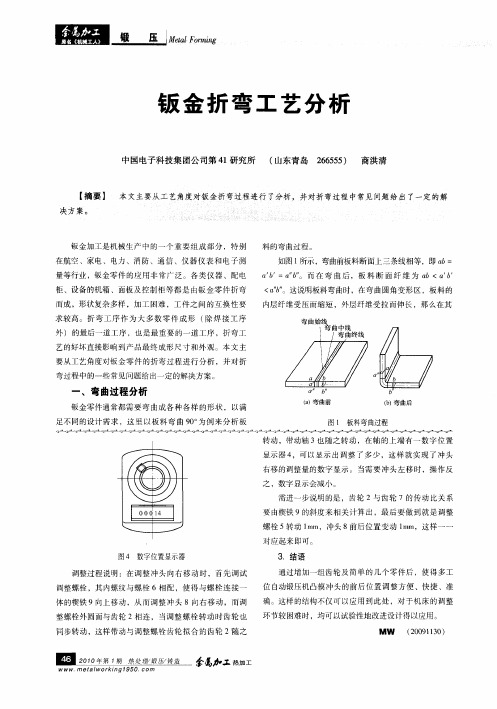
如图 1 所示 ,弯曲前板料断面上三条线相等 ,即 a b=
。6 =。 ” 而 在 弯 曲 后 ,板 料 断 面 纤 维 为 a b<。6
<o6。这说明板料弯曲时 ,在 弯曲圆角变形 区,板料 的 ””
内层纤维受压而缩短 ,外层纤 维受拉而伸长 ,那 么在其
求较 高。折 弯工 序作 为大 多数 零 件成 形 ( 除焊 接 工序
其 中,, 、, J J 。 为平 直部分长 度 ; =10 8 。一O O为 L(L
缺 口和外形 尺寸符合 预期要求 , 就需要 在折弯工 序前 这
准确计算 出零件 的展 开尺寸及各 孔位 和缺 口的位置 。计
弯曲角 ) o ;X 为中性层 系数 , 一般 < . ,该系数 随料 厚 05
及弯曲半 径 的改变而改变 。 ( ) 弯曲 9 。( 图4 的简化计算方法 。 3 0 见 )
算零件板料 的展开尺 寸 ,是根据弯 曲中性层 长度不 变的
原理进行计算的 。板料展 开长度等 于直线部 分 的长 度与 弯曲部分 中性层的长度之 和。板料 的展开尺 寸与板料 的 种类 、厚度 、弯曲半径 ,以及折 弯时 选用 的模 具槽 宽等
■■■i oi - 一压 l Fmg ■■■ r rn .■■l ■ ■_1 ■■ j ■
钣 金 折 弯 工 艺 分 析
中 国电子科技集 团公 司第 4 研究所 ( 1 山东青 岛 2 6 5 ) 商洪清 6 5 5
【 要】 本文主要从工艺角度对钣金折弯过程进行了分析 ,并对折弯过程中常见问题给 出了一定的解 摘
对应起来 即可 。
图 4 数 字位置显示器
3 结语 .
通过增加一组齿轮及 简单 的几 个零件后 ,使 得多工
钣金折弯方法汇总
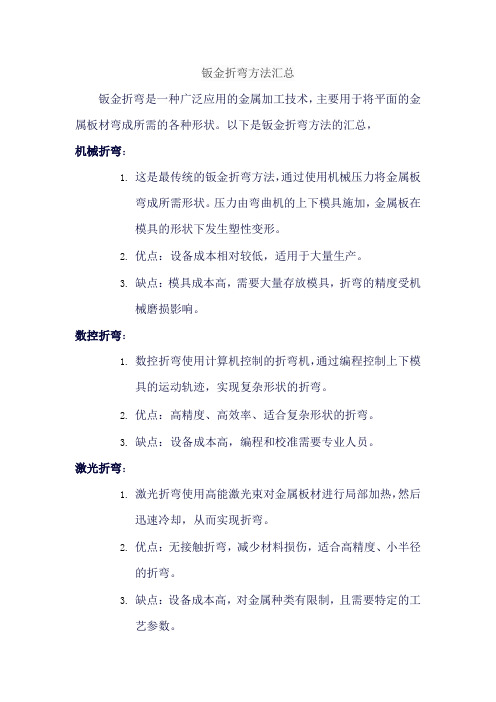
钣金折弯方法汇总钣金折弯是一种广泛应用的金属加工技术,主要用于将平面的金属板材弯成所需的各种形状。
以下是钣金折弯方法的汇总,机械折弯:1.这是最传统的钣金折弯方法,通过使用机械压力将金属板弯成所需形状。
压力由弯曲机的上下模具施加,金属板在模具的形状下发生塑性变形。
2.优点:设备成本相对较低,适用于大量生产。
3.缺点:模具成本高,需要大量存放模具,折弯的精度受机械磨损影响。
数控折弯:1.数控折弯使用计算机控制的折弯机,通过编程控制上下模具的运动轨迹,实现复杂形状的折弯。
2.优点:高精度、高效率、适合复杂形状的折弯。
3.缺点:设备成本高,编程和校准需要专业人员。
激光折弯:1.激光折弯使用高能激光束对金属板材进行局部加热,然后迅速冷却,从而实现折弯。
2.优点:无接触折弯,减少材料损伤,适合高精度、小半径的折弯。
3.缺点:设备成本高,对金属种类有限制,且需要特定的工艺参数。
液压折弯:1.液压折弯使用液体压力对金属板进行弯曲,通常需要一个可移动的弯曲冲头和固定模具。
2.优点:适用于大型和重型材料的折弯。
3.缺点:设备成本高,且对工作环境有特殊要求。
折弯成形一体机:1.这是一种将折弯和成形工艺结合在一起的方法,使用一台机器完成金属板的弯曲和成形。
2.优点:减少生产流程,提高效率。
3.缺点:设备成本和维护成本较高。
柔性折弯:1.柔性折弯使用柔性材料(如柔性金属带或塑料)作为模具,通过加热或弯曲使金属板与之贴合。
2.优点:模具成本低,适合快速原型制作和小批量生产。
3.缺点:精度和效率相对较低。
电化学折弯:1.电化学折弯利用电解的方法对金属板进行局部溶解,通过控制溶解过程实现弯曲。
2.优点:无机械应力,适用于薄片材料。
3.缺点:设备成本高,对工作环境有特殊要求,且加工时间较长。
超声波折弯:1.超声波折弯利用高频振动使金属板发生局部塑性变形,从而实现弯曲。
2.优点:适用于小型零件和高精度折弯。
3.缺点:设备成本高,对材料和工艺参数有特定要求。
钣金件折弯工艺研究分析

钣金件折弯工艺研究分析【摘要】随着计算机辅助工艺规划主流的形成,钣金件折弯工艺的优化也随之得到了迅速的发展,同时也成为打破国外垄断突破口的关键。
本文主要是由钣金件折弯工艺的发展进行展开,根据自主研发的钣金件折弯工艺优化系统中的功能进行介绍,分别是三维绘制和弯曲工序等功能。
同时主要对钣金件折弯工艺的优化方法进行了深入的研究,以此对国内的钣金件折弯工艺进行了指导和总结。
【关键词】钣金件;折弯工艺;优化方法;研究钣金件折弯工艺中应用广泛的是通用性较好的折弯成形的模具,其工艺简单且应用范围广。
过去的人工折弯程序不仅效率低下,质量也远远不如钣金件折弯工艺所生产的钣金件。
随着折弯机的发展,人们对其自动化要求不断提高,所以在科技进步下,钣金件折弯工艺自动生成的技术在不断的前进中。
提高国产设备性能指标,打破国外垄断的局面,使此技术得到广泛的应用。
1.国内外钣金件折弯工艺的现状数控折弯机在数控技术的发展一直受到大家的瞩目,这是由于数控折弯机精度高,质量好,大大减轻了工人的劳动力,所以受到了大家的欢迎,并且得到了广泛的应用。
钣金件就是利用模具,通过机床将展开的材料按要求弯曲一定的程度,其顺序和工具的选择都是一个优化选择的过程。
故国内外针对这个问题进行着不断的研究。
1.1国外钣金件折弯工艺现状由于产品种类的多样化和环境的复杂性,导致折弯加工的工艺过程非常复杂。
实际上,折弯工艺的优化过程就是一个寻求最优化的过程,但是由于其排序的规模巨大,环境中复杂因素较多,所以寻求最优的过程也变成一个极为复杂的智能过程。
这点国外经常运用启发式规则来减少搜索的空间,避免盲目的搜索。
S.K.Ong和L-J.De.Ⅵ将模糊理论的思想应用在钣金工件折弯的工艺中,来解决各个工序的操作顺序问题,通过对每个弯曲程度的赋值,来设定模糊矩阵,以此利用模糊矩阵得到优化顺序的方案。
还有采用two-page算法来确定工序的顺序和工具的选择,是通过避免碰撞来寻求可行方案,并以最低代价寻到最优的弯曲顺序。
钣金件的折弯工艺

钣金件的折弯工艺钣金的折弯,是指改变板材或板件角度的加工。
如将板材弯成V形,U形等。
一般情况下,钣金折弯有两种方法:一种方法是模具折弯,用于结构比较复杂,体积较小、大批量加工的钣金结构;另一种是折弯机折弯,用于加工结构尺寸比较大的或产量不是太大的钣金结构。
目前公司产品的折弯主要采用折弯机加工。
这两种折弯方式有各自的原理,特点以及适用性。
模具折弯:对于年加工量在5000件以上,零件尺寸不是太大的结构件(一般情况为300X300),加工厂家一般考虑开冲压模具加工。
常用折弯模具常用折弯模具,如图1-17所示:为了延长模具的寿命,零件设计时,尽可能采用圆角。
图1-17 专用的成形模具过小的弯边高度,即使用折弯模具也不利于成形,一般弯边高度L≥3t(包括壁厚)。
台阶的加工处理办法一些高度较低的钣金Z形台阶折弯,加工厂家往往采用简易模具在冲床或者油压机上加工,批量不大也可在折弯机上用段差模加工,如图1-18所示。
但是,其高度H不能太高,一般应该在(0~1.0)t ,如果高度为(1.0~4.0)t,要根据实际情况考虑使用加卸料结构的模具形式。
这种模具台阶高度可以通过加垫片进行调整,所以,高度H是任意调节的,但是,也有一个缺点,就是长度L尺寸不易保证,竖边的垂直度不易保证。
如果高度H尺寸很大,就要考虑在折弯机上折弯。
图1-18 Z形台阶折弯折弯机折弯折弯机分普通折弯机和数控折弯机两种。
由于精度要求较高,折弯形状不规则,通信设备的钣金折弯一般用数控折弯机折弯,其基本原理就是利用折弯机的折弯刀(上模)、V形槽(下模),对钣金件进行折弯和成形。
优点:装夹方便,定位准确,加工速度快;缺点:压力小,只能加工简单的成形,效率较低。
成形基本原理成形基本原理如图1-19所示:图1-19 成形基本原理折弯刀(上模)折弯刀的形式如图1-20所示,加工时主要是根据工件的形状需要选用,一般加工厂家的折弯刀形状较多,特别是专业化程度很高的厂家,为了加工各种复杂的折弯,定做很多形状、规格的折弯刀。
浅析钣金件折弯工艺

浅析钣金件折弯工艺发布时间:2023-01-03T05:39:59.731Z 来源:《当代电力文化》2023年17期作者:熊夫亮1 许涛2 [导读] 钣金应用越来越广,折弯及展开造型是钣金设计的关键技术之一,本文分析总结了钣金折弯件工艺中的尺寸计算、折弯机模具选择及钣金折弯工艺参数相关内容。
熊夫亮1 许涛2(徐州海伦哲专用车辆股份有限公司江苏徐州 221003)摘要:钣金应用越来越广,折弯及展开造型是钣金设计的关键技术之一,本文分析总结了钣金折弯件工艺中的尺寸计算、折弯机模具选择及钣金折弯工艺参数相关内容。
关键词:钣金折弯、模具、弯曲引言钣金是机械零件中的一个重要的组成部分,钣金是针对金属薄板来说的一种综合冷加工工艺,钣金零件是由金属板料经冲压、折弯加工制造而成,一般是厚度均匀的板材,主要用于轻工、航天、汽车、电器等领域。
钣金零件具有一个重要的共同特性,无论其形状多复杂,其开始均为一块平板,经过复杂的冲压、折弯加工制造而成。
为了提升钣金件的精度,就需要非常准确的钣金件展开造型,以便钣金件的下料,因此钣金件的展开及折弯是钣金工艺中十分重要的内容。
一、钣金折弯中的计算:1. 板料展开长度计算折弯展开长度由于折弯操作产生弯曲的展开长度,其长度L=L1+L2+L0,L1、L2为直边长度,L0是中性层圆弧的弧长,折弯系数一般有折弯系数表、系数值、中性层系数三种表示方法,本文采用中性层系数。
我们需要找到中性层的位移值xt,这个数值是板材的厚度乘以中性层系数x,而x的值又被叫做折弯K因子,我们可以通过查表获得,知道了位移值就知道了中性层圆弧的半径R,根据折弯角度a的大小就能计算出中性层弧长L0,再加上直边L1、L2就是工件的展开尺寸。
其中:P为折弯工艺力,单位t;为板材厚度,单位mm;B为板材宽度,单位mm;V为下模槽口宽度,单位mm;Rm为典型抗拉强度,单位MPa。
折弯吨位因为折弯机型号、折弯模具的不同而不同,大多数会有吨位限制名牌粘接在折弯机侧面,折弯吨位也能够通过数控模拟系统进行模拟。
钣金折弯工艺技术方案

钣金折弯工艺技术方案钣金折弯工艺技术方案钣金折弯工艺是一种将金属板材通过折弯工序加工成所需形状的加工工艺。
下面是一份钣金折弯工艺技术方案。
1. 设计方案:根据客户提供的图纸或样品,设计产品的折弯计划和加工工序。
确定所需的折弯角度和折弯方向。
2. 材料准备:根据图纸确定所需材料,并进行材料的采购和准备工作。
材料常用的有钢板、铝板等。
3. 材料切割:根据设计方案和所需尺寸,将材料切割成所需的大小。
4. 折弯工序:在折弯机上进行折弯工序。
根据设计方案的要求,将材料放置在折弯机上,通过折弯机的上下模具施加压力,使材料折弯成所需的形状。
5. 折弯角度控制:使用数控折弯机或手动测量工具来控制折弯角度的准确度。
根据设计方案中所需的折弯角度,调整折弯机的参数,确保折弯角度的准确性。
6. 折弯顺序控制:根据设计方案确定折弯的顺序,特别是对于复杂形状的产品。
折弯顺序的确定可以避免材料的变形和折弯过程中的错误。
7. 补偿计算:在进行折弯工序时,需要根据材料的弹性变形进行补偿计算。
通过调整折弯机的参数和折弯顺序,可以减小折弯过程中的材料变形。
8. 完成产品:完成折弯工序后,需要进行打磨、焊接和表面处理等后续工艺。
确保产品的质量和外观完整。
9. 质量检验:进行产品的质量检验,确保产品符合设计要求。
质量检验可以包括外观检查、尺寸检测和功能测试等。
10. 成品包装:按照客户要求进行产品包装,以确保产品在运输和使用过程中不受损坏。
以上是一份钣金折弯工艺技术方案的基本内容。
在实际操作过程中,需要根据具体的产品和工艺要求进行调整和改进。
通过科学的工艺流程和精确的操作控制,可以提高产品的质量和生产效率。
钣金折弯分析报告范文

钣金折弯分析报告范文钣金折弯分析报告一、背景介绍钣金折弯是一种将金属板材折弯成所需的形状的加工方法。
在钣金加工中,折弯是常见的工艺之一,广泛应用于各个行业领域。
通过折弯,可以使平板变成角度、曲线等形状,满足不同需求。
二、折弯分析1. 材料选择:根据需要折弯的材料种类、厚度、弯曲角度等要求,选择合适的钣金材料。
常见的材料有不锈钢、铝合金、碳钢等。
材料的性能、强度、耐蚀性等特性需要根据具体需求进行考虑。
2. 设计图纸:根据产品的设计要求,制作详细的图纸。
图纸中需要标注折弯线、弯曲角度、折弯区域等关键参数。
同时,需要考虑到折弯后的尺寸和形状是否满足设计需求。
3. 折弯模具选择:根据折弯图纸的要求,选择合适的折弯模具。
折弯模具的选择与材料的特性、折弯角度、折弯曲线等因素有关。
模具的准确、稳定、耐用等特性需满足折弯要求。
4. 折弯工艺参数设定:根据具体的材料和折弯要求,设定合适的折弯参数。
包括折弯力度、折弯速度、夹紧力等参数。
这些参数的设定需要通过试验和经验进行确定。
同时,需要经常进行监测和调整,以保证折弯质量。
5. 折弯过程控制:在折弯过程中,需要注意控制折弯角度、折弯线、折弯位置等参数的精确度。
通过合理的控制和调整,确保折弯后的尺寸和形状的精度。
6. 折弯质量检测:折弯完成后,需要对折弯件进行质量检测。
主要检测折弯尺寸误差、折弯角度、表面质量等指标。
检测结果与设计要求进行对比,评估折弯质量的合格性。
三、问题分析1. 折弯过程中可能出现的问题:折弯过程中可能出现的问题包括折弯角度不准确、折弯线不平整、折弯位置偏差等。
这些问题可能导致折弯件尺寸和形状的偏差,影响产品的质量。
2. 造成问题的原因:问题可能由材料、模具、折弯参数设定、折弯工艺控制等方面引起。
例如,材料的性能、强度不满足折弯要求;折弯模具的选择和使用不当;折弯参数设定不准确等。
3. 解决措施:针对问题的原因,采取相应的解决措施。
例如,对于材料问题,可以选择合适的材料,提高材料的质量;对于模具问题,可以选择合适的模具,定期检查和维护模具的状态;对于折弯参数设定问题,可以通过试验和经验进行优化等。
钣金折弯工艺的意义与作用
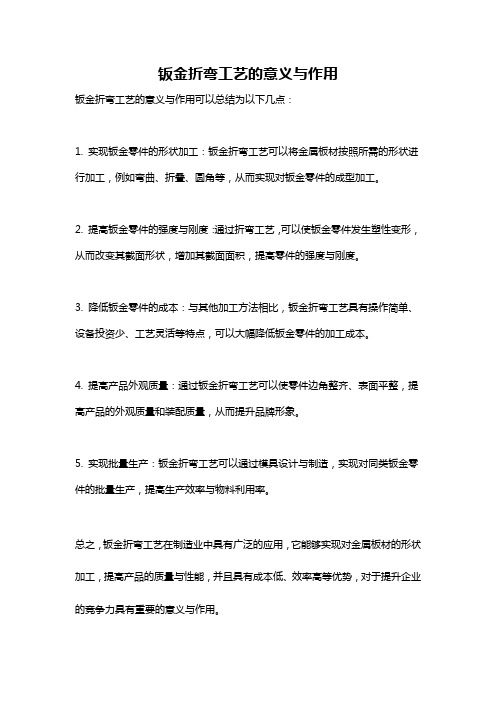
钣金折弯工艺的意义与作用
钣金折弯工艺的意义与作用可以总结为以下几点:
1. 实现钣金零件的形状加工:钣金折弯工艺可以将金属板材按照所需的形状进行加工,例如弯曲、折叠、圆角等,从而实现对钣金零件的成型加工。
2. 提高钣金零件的强度与刚度:通过折弯工艺,可以使钣金零件发生塑性变形,从而改变其截面形状,增加其截面面积,提高零件的强度与刚度。
3. 降低钣金零件的成本:与其他加工方法相比,钣金折弯工艺具有操作简单、设备投资少、工艺灵活等特点,可以大幅降低钣金零件的加工成本。
4. 提高产品外观质量:通过钣金折弯工艺可以使零件边角整齐、表面平整,提高产品的外观质量和装配质量,从而提升品牌形象。
5. 实现批量生产:钣金折弯工艺可以通过模具设计与制造,实现对同类钣金零件的批量生产,提高生产效率与物料利用率。
总之,钣金折弯工艺在制造业中具有广泛的应用,它能够实现对金属板材的形状加工,提高产品的质量与性能,并且具有成本低、效率高等优势,对于提升企业的竞争力具有重要的意义与作用。
钣金加工折弯工艺及解决办法汇总!

钣金加工折弯工艺及解决办法汇总!来源网络转载众多,如有侵权请联系我们!问题一:折弯边不平直,尺寸不稳定原因:1、设计工艺没有安排压线或预折弯2、材料压料力不够3、凸凹模圆角磨损不对称或折弯受力不均匀4、高度尺寸太小解决办法:1、设计压线或预折弯工艺2、增加压料力3、凸凹模间隙均匀、圆角抛光4、高度尺寸不能小于最小极限尺寸问题二:工件折弯后外表面擦伤原因:1、原材料表面不光滑2、凸模弯曲半径太小3、弯曲间隙太小解决办法:1、提高凸凹模的光洁度2、增大凸模弯曲半径3、调整弯曲间隙问题三:弯曲角有裂缝原因:1、弯曲内半径太小2、材料纹向与弯曲线平行3、毛坯的毛刺一面向外4、金属可塑性差解决办法:1、加大凸模弯曲半径2、改变落料排样3、毛刺改在制件内圆角4、退火或采用软性材料问题四:弯曲引起孔变形原因:采用弹压弯曲并以孔定位时弯臂外侧由于凹模表面和制件外表面摩擦而受拉,使定位孔变形。
解决办法:1、采用形弯曲2、加大顶料板压力3、在顶料板上加麻点格纹,以增大摩擦力防止制件在弯曲时滑移问题五:弯曲表面挤压料变薄原因:1、凹模圆角太小2、凸凹模间隙过小解决办法:1、增大凹模圆角半径2、修正凸凹模间隙问题六:制件端面鼓起或不平原因:1、弯曲时材料外表面在圆周方向受拉产生收缩变形,内表面在圆周方向受压产生伸长变形,因而沿弯曲方向出现挠曲端面产生鼓起现象。
解决办法:1、制件在冲压最后阶段凸凹模应有足够压力2、做出与制件外圆角相应的凹模圆角半径3、增加工序完善问题七:凹形件底部不平原因:1、材料本身不平整2、顶板和材料接触面积小或顶料力不够3、凹模内无顶料装置解决办法:1、校平材料2、调整顶料装置,增加顶料力3、增加顶料装置或校正4、加整形工序问题八:弯曲后两边对向的两孔轴心错移原因:材料回弹改变弯曲角度使中心线错移解决办法:1、增加校正工序2、改进弯曲模结构减小材料回弹问题九:弯曲后不能保证孔位置尺寸精度原因:1、制件展开尺寸不对2、材料回弹引起3、定位不稳定解决办法:1、准确计算毛坯尺寸2、增加校正工序或改进弯曲模成型结构3、改变工艺加工方法或增加工艺定位问题十:弯曲线与两孔中心联机不平行原因:弯曲高度小于最小弯曲极限高度时弯曲部位出现外胀现象解决办法:1、增加折弯件高度尺寸2、改进折弯件工艺方法问题十一:弯曲后宽度方向变形,被弯曲部位在宽度方向出现弓形挠度原因:由于制件宽度方向的拉深和收缩量不一致产生扭转和挠度解决办法:1、增加弯曲压力2、增加校正工序3、保证材料纹向与弯曲方向有一定角度问题十二:带切口的制件向下挠曲原因:切口使两直边向左右张开,制件底部出现挠度解决办法:1、改进制件结构2、切口处增加工艺留量,使切口连接起来,弯曲后再将工艺留量切去。
钣金折弯压筋的加工工艺

钣金折弯压筋加工工艺一、材料准备在进行钣金折弯加工前,首先需要准备合适的材料。
材料应具备以下特性:.强度高:为了确保钣金件在折弯过程中不发生变形,应选择强度高的材料。
.塑性好:塑性好的材料在折弯过程中不易开裂,能够保证钣金件的平整度。
.厚度适中:厚度过薄会导致折弯后强度降低,厚度过厚则会导致折弯困难。
根据实际需要,可以选择不同规格和材质的钢材、铝合金等材料。
二、模具设计模具设计是钣金折弯加工中的重要环节。
根据钣金件的实际形状和尺寸,设计适合的模具。
以下是模具设计的主要步骤:.分析图纸:了解钣金件的设计要求,包括形状、尺寸、角度等。
.确定折弯线:确定钣金件的折弯线,包括折弯角度、半径等。
.设计模具:根据钣金件的要求和折弯线的确定,设计适合的模具。
.模具制作:根据设计图纸制作模具,确保模具的精度和硬度。
三、折弯工艺在模具准备好后,可以进行钣金件的折弯加工。
以下是折弯工艺的主要步骤:.上料:将准备好的钣金件放入模具中。
.定位:确保钣金件在模具中的位置准确,避免在折弯过程中发生位移。
.折弯:通过压机或折弯机进行折弯加工,按照预先设计的折弯线进行折弯。
.检查:在折弯完成后,检查钣金件的形状、尺寸是否符合设计要求。
四、压筋工艺压筋工艺是钣金加工中的一种常用技术,用于增加钣金件的强度和美观度。
以下是压筋工艺的主要步骤:.模具设计:根据需要压筋的部位和形状,设计适合的模具。
.上料:将准备好的钣金件放入模具中。
.定位:确保钣金件在模具中的位置准确,避免在压筋过程中发生位移。
.压筋:通过压机或专用压筋设备进行压筋加工,使钣金件表面形成所需的筋条。
.检查:在压筋完成后,检查钣金件的形状、尺寸是否符合设计要求。
五、冲孔工艺在钣金加工中,冲孔工艺是常用的加工方法之一。
以下是冲孔工艺的主要步骤:.模具设计:根据需要冲孔的部位和形状,设计适合的模具。
.上料:将准备好的钣金件放入模具中。
.定位:确保钣金件在模具中的位置准确,避免在冲孔过程中发生位移。
钣金零件全自动连续折弯工艺的研究
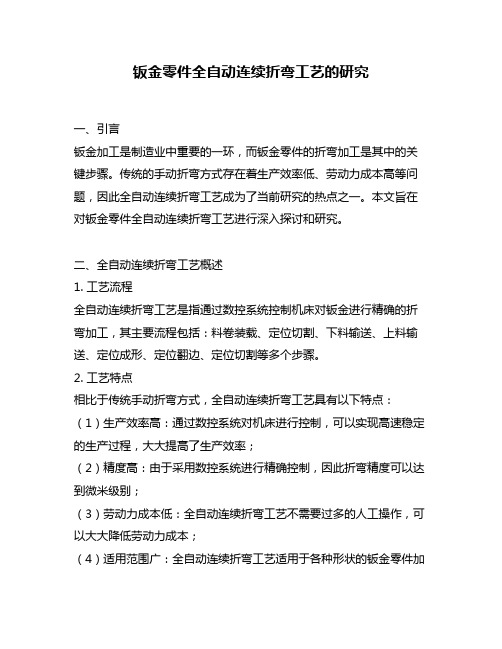
钣金零件全自动连续折弯工艺的研究一、引言钣金加工是制造业中重要的一环,而钣金零件的折弯加工是其中的关键步骤。
传统的手动折弯方式存在着生产效率低、劳动力成本高等问题,因此全自动连续折弯工艺成为了当前研究的热点之一。
本文旨在对钣金零件全自动连续折弯工艺进行深入探讨和研究。
二、全自动连续折弯工艺概述1. 工艺流程全自动连续折弯工艺是指通过数控系统控制机床对钣金进行精确的折弯加工,其主要流程包括:料卷装载、定位切割、下料输送、上料输送、定位成形、定位翻边、定位切割等多个步骤。
2. 工艺特点相比于传统手动折弯方式,全自动连续折弯工艺具有以下特点:(1)生产效率高:通过数控系统对机床进行控制,可以实现高速稳定的生产过程,大大提高了生产效率;(2)精度高:由于采用数控系统进行精确控制,因此折弯精度可以达到微米级别;(3)劳动力成本低:全自动连续折弯工艺不需要过多的人工操作,可以大大降低劳动力成本;(4)适用范围广:全自动连续折弯工艺适用于各种形状的钣金零件加工。
三、全自动连续折弯工艺的关键技术1. 机床选型机床是全自动连续折弯工艺中最为重要的设备之一。
目前市面上主要有两种类型的机床:电液伺服和液压式。
电液伺服机床具有响应速度快、精度高等优点,但价格相对较高;液压式机床则价格相对较低,但响应速度较慢。
在选择时需要根据生产需求和经济实际情况进行权衡。
2. 数控系统数控系统是全自动连续折弯工艺中另一个重要组成部分。
数控系统可以通过编程实现对机床的精确控制,从而保证了加工精度和生产效率。
目前市场上主流的数控系统有西门子、三菱、广数等多种,需要根据实际需求进行选择。
3. 夹具设计夹具是全自动连续折弯工艺中的重要组成部分。
夹具的设计需要考虑到钣金零件的形状、尺寸等因素,并通过数控系统进行精确控制。
合理的夹具设计可以提高生产效率和加工精度。
4. 刀模制作刀模是全自动连续折弯工艺中的关键零部件之一。
刀模的质量直接影响到加工精度和生产效率。
钣金工艺知识分享-折弯工艺
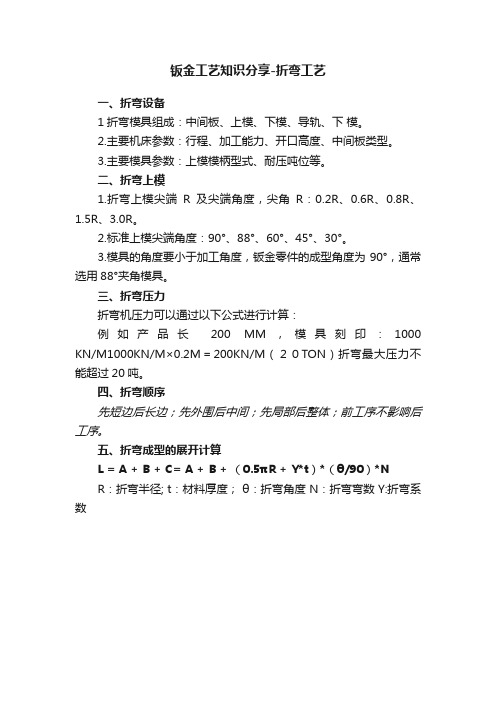
钣金工艺知识分享-折弯工艺
一、折弯设备
1折弯模具组成:中间板、上模、下模、导轨、下模。
2.主要机床参数:行程、加工能力、开口高度、中间板类型。
3.主要模具参数:上模模柄型式、耐压吨位等。
二、折弯上模
1.折弯上模尖端R及尖端角度,尖角R:0.2R、0.6R、0.8R、
1.5R、3.0R。
2.标准上模尖端角度:90°、88°、60°、45°、30°。
3.模具的角度要小于加工角度,钣金零件的成型角度为90°,通常选用88°夹角模具。
三、折弯压力
折弯机压力可以通过以下公式进行计算:
例如产品长200 MM,模具刻印:1000 KN/M1000KN/M×0.2M=200KN/M(20TON)折弯最大压力不能超过20吨。
四、折弯顺序
先短边后长边;先外围后中间;先局部后整体;前工序不影响后工序。
五、折弯成型的展开计算
L = A + B + C= A + B + (0.5πR + Y*t)*(θ/90)*N
R:折弯半径; t:材料厚度;θ:折弯角度 N:折弯弯数 Y:折弯系数。
钣金的折弯成形过程,涨知识!
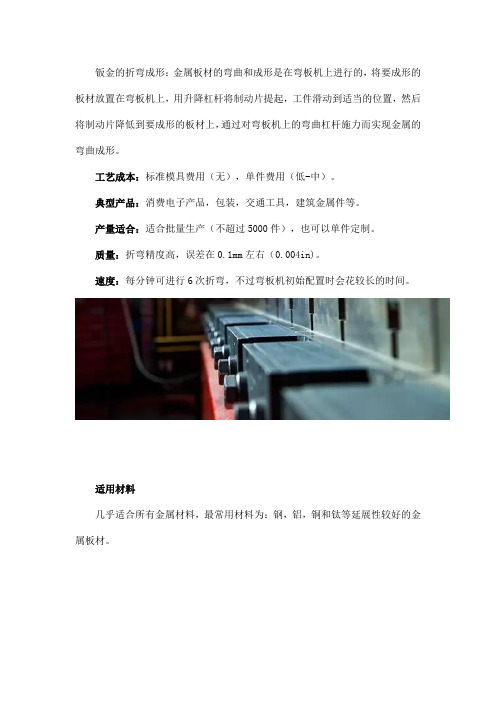
钣金的折弯成形:金属板材的弯曲和成形是在弯板机上进行的,将要成形的板材放置在弯板机上,用升降杠杆将制动片提起,工件滑动到适当的位置,然后将制动片降低到要成形的板材上,通过对弯板机上的弯曲杠杆施力而实现金属的弯曲成形。
工艺成本:标准模具费用(无),单件费用(低-中)。
典型产品:消费电子产品,包装,交通工具,建筑金属件等。
产量适合:适合批量生产(不超过5000件),也可以单件定制。
质量:折弯精度高,误差在0.1mm左右(0.004in)。
速度:每分钟可进行6次折弯,不过弯板机初始配置时会花较长的时间。
适用材料
几乎适合所有金属材料,最常用材料为:钢,铝,铜和钛等延展性较好的金属板材。
设计考虑因素
1.单件折弯长度最长可达16m(52ft)。
2.金属折弯的路径只能是直线。
3.可延展材料的折弯内侧圆角半径是板材厚度的1倍,硬材料的折弯内侧圆角半径是板材厚度的3倍。
4.如果金属板材没有经过热处理,折弯的厚度最厚可达50mm(2in)。
工艺过程详解
冲头由液压缸驱动(提供竖直的压力),而压力大小由4个因素决定:折弯长度,板材厚度,延展力和折弯半径。
步骤1:将准备好的钣金件放置于硬质模具上。
步骤2:冲头由液压缸驱动,向下压迫钣金件折弯成型,每一次折弯只需要几秒钟,全程由电脑控制。
钣金折弯的形状由冲头型号和硬质模具型号决定,分为标准模具和非标模具。
钣金折弯工艺介绍

钣金折弯工艺介绍钣金折弯工艺是一种常见的金属加工方法,用于将金属板材折弯成所需的形状和角度。
它在许多工业领域中都有广泛的应用,包括汽车制造、航空航天、电子设备等。
本文将介绍钣金折弯工艺的基本原理、工艺流程和常见的折弯方法。
一、基本原理钣金折弯工艺利用机械力将金属板材按照所需的角度弯曲。
在折弯过程中,金属板材的外层受到拉伸力,内层受到压缩力。
通过合理的控制力度和角度,可以使金属板材保持一定的强度和稳定性,同时实现所需的形状和角度。
二、工艺流程钣金折弯工艺的一般流程包括设计、材料准备、模具制作、加工和检验等步骤。
1. 设计:根据产品的要求,设计出需要折弯的金属板材的尺寸、形状和角度。
2. 材料准备:根据设计要求,选择合适的金属板材,并进行切割、去毛刺等处理,以保证板材的质量和表面光滑度。
3. 模具制作:根据设计图纸,制作适用于折弯的模具,包括上模、下模和弯边模等。
4. 加工:将准备好的金属板材放置在折弯机的工作台上,根据设计要求调整机器参数,将模具安装到机床上,进行折弯加工。
操作人员需要根据需要调整机器的压力和角度,保证折弯的精度和质量。
5. 检验:对折弯后的产品进行检验,包括尺寸、角度、外观等方面。
如果有不合格的地方,需要进行修正或重新加工。
三、常见的折弯方法钣金折弯工艺有多种方法,常见的包括V型折弯、U型折弯和Z型折弯。
1. V型折弯:V型折弯是通过将模具上的上模和下模夹紧金属板材,在板材两侧施加力量,使金属板材弯曲成V形。
这种折弯方法适用于金属板材较薄的情况,可以获得较小的弯曲半径。
2. U型折弯:U型折弯是通过将模具上的上模和下模夹紧金属板材,在板材两侧施加力量,使金属板材弯曲成U形。
这种折弯方法适用于金属板材较厚的情况,可以获得较大的弯曲半径。
3. Z型折弯:Z型折弯是通过将模具上的上模和下模夹紧金属板材,在板材两侧施加力量,使金属板材弯曲成Z形。
这种折弯方法适用于需要多次折弯的情况,可以获得更复杂的形状和角度。
- 1、下载文档前请自行甄别文档内容的完整性,平台不提供额外的编辑、内容补充、找答案等附加服务。
- 2、"仅部分预览"的文档,不可在线预览部分如存在完整性等问题,可反馈申请退款(可完整预览的文档不适用该条件!)。
- 3、如文档侵犯您的权益,请联系客服反馈,我们会尽快为您处理(人工客服工作时间:9:00-18:30)。
当孔在折弯变形区内时, 采用的切 口形式示例如图 3 。
作者 简介 : 刘丽琴 (9 5 ) 女 , 17 一 , 辽宁辽阳人 , 工程师 , 本科学历 , 研究方 向: 机械制造。 7 0
《 装备制造技术)0 2 2 1 年第 5 期
一
() 2 过小 的直边高度。 如果设计需要弯曲件的直 种综合冷加工工艺 , 其显著的特征 , 就是 同一零件 边高度 h≤2 则首先要加大弯边高度 , t 弯好后 再加 厚度一致 。本文简述了钣金折弯加工方式所要注意 工 到需 要 尺寸 ; 者在 弯 曲变形 区 内加工 浅 槽 后 , 或 再
( 表示料 参 考 文 献 :
厚 )如果使用 5 1 , , 则折弯系数也要相应加大, 如 [] 2 肖黎明. 钣金结构设计 与加工工 艺分 析【 . M】北京 : 机械 工业 果使用 5 + V, T l 则折弯系数也要相应减小 。
出版社 ,0 2 2 1.
[】 1 王爱珍 . 钣金加工技术【 . M]北京 : 械工业 出版社 ,0 8 机 20.
10t . 2 0l .
弯 曲半 径是指 弯 曲件 的 内侧半 径 ,是材料 的 t
壁厚 。
鼻 日 圈
tm ( m) sTr) (II rr
s= H s 15t r . +
2 弯 曲件 的直边 高度
f ( mm)
≤ 2 5 S2 > 2 > 5 5 2—O > 0 5
d sg h e t a t . e in s e tmea p rs l
Ke r s s e t t l b n ; r c s - u ; a a tr y wo d : h e a ; e d p o e s c t p r mee me
71
E up n Ma ua t n e h oo y No5, 0 2 q i me t n f er g T c n lg . 2 1 i
f 、,、 、_ ,、 、 ^ ^
{- -装 { 3艺与3
钣金零件折弯工艺简析
刘丽琴 。 娟娟 唐
( 中国电子科技集团公司第二研究所 , 山西 太原 00 2 ) 3 04
表 1 常用材料最 小弯曲半径参考表
序号
1
●
图 2 特殊情况下的直边高度要求
材 料
0 l Ni 、 C l Ni l r 8 iT 、 2 Cr 8 9 I r 8 9、 C l N 9 i T
最小弯 曲半径
O4t .
3 折弯件上的孔边距
孔边距是指先 冲孔后折弯 ,孔的位置应处 于弯 曲变形 区外 , 避免弯曲时孔会产生变形 。
摘 要 : 过对折 弯加 工过程 中影响加 工准确度 的 因素进行 了研 究分析 , 通 概括 总结普遍 适用的折弯工 艺要 求 。 以便 在设 计过程 中能更加有效、 合理 的设计钣金零件。
关键 词 : ; 钣金 折弯 ; 工艺切 1; : 参数 2
中图分类号 : H1 1 T 6 文献标识码 : B 文章编号 :6 2 5 5 ( 0 2 0 — 0 0 0 1 7 — 4 X 2 1 )5 0 7 - 2
smm) (
s 2t r + s 2 5t r . + s 3t. 4 r
() 1 弯曲件 的直边高度不宜太小 , 最小高度要求
为 : >2t见 图 1) h ( 。
—叶
4 局部弯 曲的工艺切 口
() 1 当孔位于折弯变形区内 , 所采取 的切 口形式 。
图 1 弯 曲件的直边高度最小值
5 折床 的加工工艺参数
钣金件 的设计者 ,仅停 留在简单的需求设计 上是远 折弯展开计算时 ,会根据需要对展开尺寸进行 远不够 的,只有充分 了解并掌握钣金零件在加工过 才能设计 出结构合理 、 加 数值补偿 , 也就是通常所说的折弯系数 。 但针对不同 程 中所要考虑 的工艺问题 , 易行的高品质钣金零件。 的折弯下模 , 折弯系数也会有相应的改变 , 这样计算 工简单、 出来 的展开尺寸才能更精准。 折床使用的下模 形槽通常为 5
表 2 折弯件上 的孔边距
2 3
4
I、0Q 3 、 25 5 2 、 2 5 Q 3 A、 2 、0 Q 5 53 、 25
1 r 3 H6 Cl 、 2
0 .t 5 06 .l
O 8t .
5 6
4 5 5、 0 6 Mn 6 S Mn C l Ni 、 C l Ni- S 3 1 5 0 i 1 r T 7 1 rT 7 y US 0
Ab t c : h sa t l r u h fl e af e d n r c s co sif e cn r c s i g a c r c n l ss g n r l s r t T i ri et o g d d i h l n i gp o e sf tr l n i gp o e sn c u a ya ay i, e e al a c h o n b a n u y i s mme p t eb n i g p o e sr q i me t S a e d sg r c s a a e mo e e e t e a d r a o a l s u d u e d n r c s e u r h e n , Ot t n t e in p e st t n b r f ci n e s n b e h i h o h c v
图 3 切 口形 式 示 例
() 2 带斜边 的折弯边 , 避开变形 区。如图 4 应
所示 。
变形 区域
下 。 广
() a
r
() b () c
臼
口
变域 形目 区
正
图 5 弯 曲件 标 注 示例
错
图 4 带斜边的折弯边应避开变形区
7 结束语
总而言之 , 钣金折弯技术是一 门综合技术 , 作为
的工 艺要 求 。
钣金是针对金属薄板 ( 厚度通常在 6 m以下 ) m
折弯( 如图 2所示 )后者处理方法 比较适用 于较厚 , 板材 。
V
- e
1 折弯件 的最小 弯 曲半径
弯 曲零件的结构设计 ,应避免过小的弯曲圆角 半径 , 以避免材料的拉伸应力造成的材料断裂 。常用 材 料 的最 小弯 曲半 径 参见 表 1 。
—
…
6 标注弯 曲件相关尺寸 时 , 考虑 工艺性 要
I 弯线 l 曲 匝j垂r一
( a) ( b)
如图 5 所示 , a先 冲孔后折弯 , 尺寸精度容 ()
易保证 , 加工方便 ;
( ) ()如果尺寸 精度要求高 , b和 e , 则需要先折 弯后加工孔 , 加工麻烦。
Sh e t l a s B n ig Pr c s ay i e t Me a n e d n o e sAn l s P s
LU L- i T N a-un I iqn,A GJ n ja u ( hn l t nc eh o g ru op rt nS cn eerhIstt,a un0 0 2 ,hn ) C iaEe r i T c n l yG o pC roai eo dR sac tue i a 3 0 4C ia co s o o ni Ty