STRATCO硫酸烷基化工艺技术特点及影响因素分析
硫酸烷基化工艺腐蚀分析及应对措施研究

硫酸烷基化工艺腐蚀分析及应对措施研究
硫酸烷基化工艺是一种重要的化工生产方法,但同时也存在着一些腐蚀问题。
本文将分析硫酸烷基化工艺中可能存在的腐蚀问题,并提出相应的解决措施。
硫酸烷基化工艺涉及到硫酸的使用,硫酸具有很强的腐蚀性。
在生产过程中,硫酸可能会与设备和管道内壁接触,导致设备和管道的腐蚀。
硫酸还可能与其他金属离子或化合物形成酸性环境,加速设备和管道的腐蚀。
针对硫酸的腐蚀问题,可以采取以下应对措施:
1. 选择耐腐蚀材料:在设计和选择设备和管道时,应优先选择耐腐蚀材料,例如高合金钢,不锈钢等。
这些材料具有较强的抗硫酸腐蚀能力,可以有效延长设备和管道的使用寿命。
2. 强化涂层保护:在设备和管道内壁涂覆一层耐腐蚀的涂层,可以防止硫酸直接接触设备和管道的金属表面,减少腐蚀的发生。
常用的涂层材料包括聚氨酯涂层、环氧涂层等。
3. 控制工艺条件:在硫酸烷基化工艺中,通过控制工艺条件,如温度、压力和流速等参数,可以减少硫酸对设备和管道的腐蚀。
降低硫酸的浓度和温度,减少腐蚀的程度。
4. 定期维护和检修:对设备和管道进行定期的维护和检修,及时清除设备和管道内的污垢和腐蚀产物,可以减少腐蚀的发生。
定期检查设备和管道的腐蚀情况,及时更换受损的部件,保证设备和管道的正常运行。
针对硫酸烷基化工艺中的腐蚀问题,可以通过选择耐腐蚀材料、强化涂层保护、控制工艺条件和定期维护和检修等措施来解决。
这些措施可以有效降低腐蚀的发生,延长设备和管道的使用寿命,保障硫酸烷基化工艺的安全生产。
烷基化工艺的技术特点及发展状况
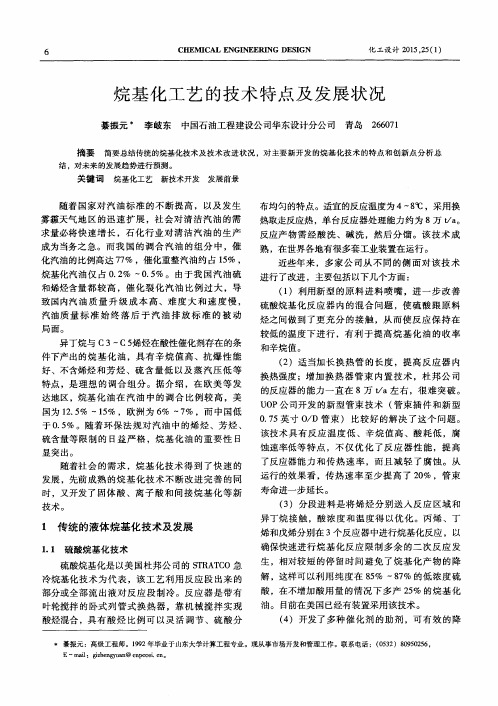
硫含 量等 限 制 的 日益 严 格 ,烷 基 化 油 的 重 要 性 日
显 突出 。
随着社 会 的 需 求 ,烷 基 化 技 术 得 到 了快 速 的
了反应器能力和传热速 率 ,而且减轻 了腐蚀 。从 运行的效果看 ,传热速率至少提高 了 2 0 % ,管束
寿命 进一 步延长 。 ( 3 ) 分段 进料 是 将 烯 烃 分别 送 人 反 应 区域 和 异 丁烷 接 触 ,酸浓 度 和 温 度 得 以优 化 。丙 烯 、丁
6
I GN
化 工设 计 2 0 1 5 , 2 5 ( 1 )
烷基 化工 艺 的技 术 特 点及 发展 状 况
綦 振元 李 岐东 中 国石 油工程 建设 公 司华东 设计 分公 司 青岛 2 6 6 0 7 1
丙烯丁1传统的液体烷基化技术及发展烯和戊烯分别在3个反应器中进行烷基化反应以11硫酸烷基化技术确保快速进行烷基化反应限制多余的二次反应发生相对较短的停留时间避免了烷基化产物的降硫酸烷基化是以美国杜邦公司的stratco急冷烷基化技术为代表该工艺利用反应段出来的解这样可以利用纯度在8587的低浓度硫部分或全部流出液对反应段制冷
烷 基化 汽 油仅 占 0 . 2 % ~ 0 . 5 % 。 由 于我 国 汽 油 硫
布均 匀 的特 点 。适 宜的反应 温度 为 4— 8 ℃ ,采用 换
热取走反应 热 ,单 台反 应器 处理 能力 约 为 8万 t / , a 。 反应 产 物 需 经 酸洗 、碱 洗 ,然 后 分 馏 。该 技 术 成 熟 ,在世 界各 地有很 多套 工业装 置在运 行 。 近些 年来 ,多 家 公 司从 不 同 的侧 面 对 该 技 术
硫酸烷基化反应器内的混合 问题 ,使硫 酸跟原料 烃之间做到了更充 分的接触 ,从而使反应保 持在
硫酸烷基化反应因素分析
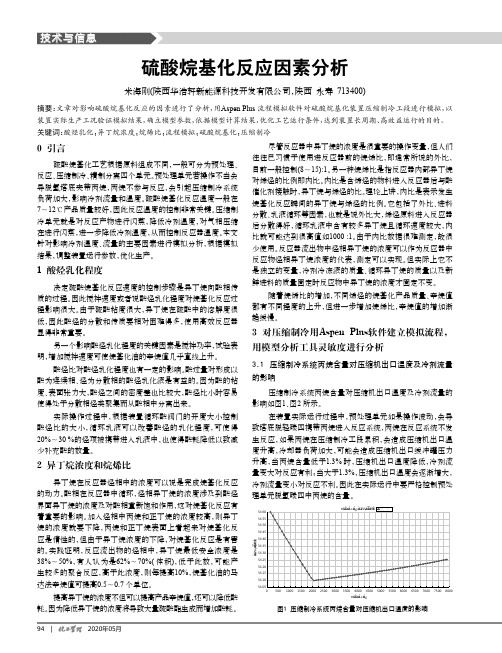
尽管反应器中异丁烷的浓度是很重要的操作变量,但人们往往已习惯于使用进反应器前的烷烯比,即通常所说的外比,目前一般控制(8~15):1。
另一种烷烯比是指反应器内部异丁烷对烯烃的比例即内比。
内比是含烯烃的物料进入反应器后与酸催化剂接触时,异丁烷与烯烃的比。
理论上讲,内比是表示发生烷基化反应瞬间的异丁烷与烯烃的比例。
它包括了外比、进料分散、乳液循环等因素,也就是说外比大,烯烃原料进入反应器后分散得好,循环乳液中含有较多异丁烷且循环速度较大,内比就可能达到很高值如1000:1。
由于内比数据很难测定,故很少使用。
反应器流出物中烃相异丁烷的浓度可以作为反应器中反应物烃相异丁烷浓度的代表,测定可以实现。
但实际上它不是独立的变量,冷剂冷冻液的质量、循环异丁烷的质量以及新鲜进料的质量固定时反应物中异丁烷的浓度才固定不变。
随着烷烯比的增加,不同烯烃的烷基化产品质量、辛烷值都有不同程度的上升,但进一步增加烷烯比,辛烷值的增加渐趋缓慢。
3 对压缩制冷用Aspen Plus软件建立模拟流程,用模型分析工具灵敏度进行分析3.1 压缩制冷系统丙烷含量对压缩机出口温度及冷剂流量的影响压缩制冷系统丙烷含量对压缩机出口温度及冷剂流量的影响如图1、图2所示。
在装置实际运行过程中,预处理单元如果操作波动,会导致塔底脱轻碳四携带丙烷进入反应系统,丙烷在反应系统不发生反应,如果丙烷在压缩制冷工段累积,会造成压缩机出口温度升高,冷却器负荷加大,可能会造成压缩机出口缓冲罐压力升高,当丙烷含量低于1.3%时,压缩机出口温度降低,冷剂流量变大对反应有利;当大于1.3%,压缩机出口温度会逐渐增大,冷剂流量变小对反应不利。
因此在实际运行中要严格控制预处理单元脱氢碳四中丙烷的含量。
图1 压缩制冷系统丙烷含量对压缩机出口温度的影响0 引言硫酸烷基化工艺根据原料组成不同,一般可分为预处理、反应、压缩制冷、精制分离四个单元。
预处理单元若操作不当会导脱氢塔底夹带丙烷,丙烷不参与反应,会引起压缩制冷系统负荷加大,影响冷剂流量和温度。
硫酸法烷基化的工艺原理和反应系统

硫酸法烷基化的工艺原理和反应系统王欢(大庆炼化公司炼油生产二部,黑龙江 大庆 163000)摘要:烷基化技术包括很多种,其中硫酸法烷基化主要指STRATCO 硫酸法烷基化技术中流出物制冷技术,此工艺技术成熟可靠,有着酸资源丰富,价格便宜,可回收,能够连续保持活性等优点。
该工艺中硫酸腐蚀性较强,设备易腐蚀,消耗酸较大,容易产生大量的酸渣,装置需要长周期运行。
文章主要探讨硫酸法烷基化的加氢硫酸法烷基化和烷基化反应原理和主要的工艺流程。
关键词:硫酸法烷基化;工艺原理;工艺流程中图分类号:TQ111文献标志码:A文章编号:1008-4800(2021)08-0160-02DOI:10.19900/ki.ISSN1008-4800.2021.08.077The Process Principle and Reaction System of Sulfuric Acid AlkylationWANG Huan (Daqing Refining & Chemical Company Production Department II , Daqing 163000, China)Abstract: There are many kinds of alkylation technologies, among which sulfuric acid alkylation mainly refers to the effluentrefrigeration technology in STRATCO sulfuric acid alkylation technology. This process is mature and reliable, has the advantages of rich acid resources, low price, recyclability, and continuous activity. In this process, the sulfuric acid is more corrosive, the equipment is easy to corrode, the consumption of acid is large, and it is easy to produce a large amount of acid slag, the device needs long-term operation. This paper mainly discusses the principle and main process flow of hydrosulfuric acid alkylation and alkylation reaction of sulfuric acid alkylation.Keywords: sulfuric acid alkylation; process principle; process flow0 引言伴随时代的发展,油气生产的标准越来越为严格,在石油炼制工业产业中,通过烷基化技术的运用,可以提高汽油成分中的辛烷值和抗暴性能,从而提高汽油的整体效率,满足化工产业的发展需求。
硫酸烷基化工艺腐蚀分析及应对措施研究

硫酸烷基化工艺腐蚀分析及应对措施研究硫酸烷基化工艺是工业生产中常见的一种化工生产工艺,其在石化、化肥、农药等行业有着广泛的应用。
在硫酸烷基化过程中,常常会遇到腐蚀问题,腐蚀严重影响了设备的使用寿命和生产效率。
对硫酸烷基化工艺腐蚀分析及应对措施的研究具有重要意义。
一、硫酸烷基化工艺腐蚀分析1. 腐蚀原因分析在硫酸烷基化工艺中,腐蚀主要是由于以下几个原因引起的:(1)介质腐蚀:硫酸烷基化反应中使用的介质中含有大量的硫酸、酸性离子等腐蚀性物质,这些物质可能对设备材料产生腐蚀作用。
(2)温度腐蚀:硫酸烷基化反应需要在一定的温度下进行,高温环境会加剧设备的腐蚀情况。
(1)表面腐蚀:设备表面出现腐蚀斑点、锈蚀等现象。
(2)局部腐蚀:设备的某些局部受到腐蚀,出现孔洞、腐蚀凹陷等情况。
(3)材料疲劳:长期腐蚀会导致设备材料疲劳、脆化,降低了设备的使用寿命。
针对硫酸烷基化工艺中的腐蚀问题,需要进行腐蚀评价分析,根据设备材料、反应条件等因素进行腐蚀风险评估,确定腐蚀程度和影响范围,为后续的防腐措施提供重要依据。
1. 材料选择在硫酸烷基化工艺中需要选择耐酸性能好的材料,如不锈钢、镍基合金、耐酸塑料等,以提高设备的耐腐蚀性能。
2. 表面处理对设备进行表面处理,如镀锌、喷涂耐酸涂料等,提高设备表面的抗腐蚀能力。
3. 设备设计在设备设计过程中,考虑对腐蚀性介质的隔离,减少介质对设备的腐蚀作用。
4. 防腐涂层5. 监测与维护定期对设备进行腐蚀情况的监测和维护,发现问题及时进行修复和更换,延长设备的使用寿命。
6. 新技术应用引进新技术,如防腐蚀合金材料、防腐蚀涂料等,提高设备的耐腐蚀性能。
三、结语硫酸烷基化工艺腐蚀问题是工业生产中常见的难题,为了保证生产设备的安全运行和生产效率的提高,必须加强对硫酸烷基化工艺腐蚀分析及应对措施的研究。
针对硫酸烷基化工艺中的腐蚀问题,必须做好材料选择、设备设计、防腐涂层等工作,同时加强对设备腐蚀情况的监测和维护,引进新技术应用,从源头上预防腐蚀问题的发生。
硫酸烷基化解析

----------------------- Page 1-----------------------文件编码:CHRP-104-PE-OI-0001-2011烷基化装置操作规程版本/状态:B/1分发号:中海石油炼化有限责任公司惠州炼油分公司----------------------- Page 2-----------------------2011年01月01日发布2011月01日实施编写签字表名称签字时间编写人审校人审核人----------------------- Page 3-----------------------专业会审表单位专业名称签字时间技术中技术专业心质量专业指挥中心调度专业动设备专业设备中静设备专业心仪表专业电气专业安全专业HSE中环保专业心消防专业职业卫生专业--------------------- Page 4-----------------------审核签字表中心领导签字时间技术中心经理设备中心经理HSE中心经理批准签字表公司领导签字时间总工程师目录第一章工艺技术规程3第一节设计依据第二节装置概况、特点及工艺原理第三节工艺流程说明第四节工艺指标第五节原材料指标第六节半成品、成品主要性质指标第七节公用工程(水、电、汽、风等)指标第八节主要操作条件及质量指标详见第十二节第九节原材料、公用工程消耗、能耗计算指标和节能措施.第十节物料平衡第十一节主要设备选择及工艺计算汇总第十二节生产控制化验分析第十三节装置内外关系第二章岗位操作法54第一节烷基化装置操作原则第二节预加氢系统操作法第三节烷基化反应系统操作法第四节致冷系统操作法第五节分馏系统操作法第三章岗位开停工规程86第一节开工规程第二节停工规程第四章设备操作规程164第一节大型专用设备操作规程第二节基础设备操作规程第五章事故处理191第一节事故处理原则第二节紧急停工方法第三节事故处理预案第四节事故处理预案演练规定第六章仪表控制系统操作法231第一节仪表控制系统概况及操作第二节工艺操作仪表控制回路说明第四节仪表投用、停用及注意事项第七章操作规定325第一节定期工作规定第二节操作规定第八章安全生产及环境保护330第一节安全知识第二节安全规定第三节烷基化装置防风防台措施第四节同类装置典型事故分析、处理方法及经验教训.第五节烷基化装置易燃易爆物质的安全性质第六节本装置主要有害物质的性质第七节装置污染物主要排放部位和排放的主要污染物.第八节消防器材、设施使用方法及消防规定第九节职业卫生九章附录366 附表一主要设备明细表附表二主要设备结构图附表三装置平面分布图附表四可燃气体报警仪布置图附表五装置消防设施布置图附表六控制参数报警值附表七安全阀定压值附录八工艺流程简图附表九开工统筹图附录十停工统筹图----------------------- Page 7-----------------------惠炼16万吨/年烷基化装置操作规程第3 页共397 页第一章工艺技术规程第一节设计依据1中国海洋石油总公司惠州炼油项目管理项目组关于“惠州炼油项目基础设计工作”的委托书(2005年6月16日);2中国石化工程建设公司与中国海洋石油总公司签订的关于开展“中国海洋石油总公司惠州炼油项目基础设计”的合同和合同附件;3 DUPONT公司提供的硫酸烷基化工艺包;4中国海洋石油总公司惠州炼油项目设计统一规定;5上游MTBE、加氢裂化装置提供的原料液化气量及组成;6中国石化工程建设公司与中国海洋石油总公司召开的PFD、PID等审查会会议纪要。
硫酸烷基化工艺腐蚀分析及应对措施研究

硫酸烷基化工艺腐蚀分析及应对措施研究硫酸烷基化是一种重要的化工生产工艺,但也存在一定的腐蚀问题。
本文就硫酸烷基化工艺的腐蚀问题进行分析,并提出相应的应对措施。
1. 腐蚀症状硫酸烷基化过程中,腐蚀主要表现为设备内部的腐蚀和管道的腐蚀。
设备内部的腐蚀主要表现为反应釜内壁和底部的腐蚀,而管道的腐蚀则表现为管道内壁的腐蚀和管道连接处的腐蚀。
腐蚀症状主要包括:(1)设备内壁和底部出现磨损、毛刺和凸起。
(2)管道内壁出现腐蚀坑和凹陷,管道连接处出现漏气现象。
(3)设备和管道表面出现斑点、腐蚀颜色不同等。
2. 腐蚀原因硫酸烷基化过程中,腐蚀主要是由于以下原因所引起的:(1)化学腐蚀:硫酸极具腐蚀性,因此在硫酸烷基化过程中难免产生化学腐蚀。
(2)机械磨损:在反应釜内部,由于反应物之间的剧烈反应以及搅拌器的搅拌作用,会导致设备内部的机械磨损,从而产生腐蚀。
(3)温度和压力:硫酸烷基化需要在高温高压下进行,高温和高压会使设备产生应力变形,从而大大降低了设备的抗腐蚀能力。
3. 应对措施为了解决硫酸烷基化过程中的腐蚀问题,需要采取相应的应对措施,包括:(1)选择合适的材料:在原材料的选择上,应尽量选用耐腐蚀的材料。
例如,采用不锈钢、玻璃钢等材料制造设备和管道,这些材料可以有效提高设备和管道的耐腐蚀性能。
(2)合理的维护保养:对设备和管道进行定期的维护保养,使用防腐材料进行修补和涂层处理,有效延长设备和管道的使用寿命。
同时,应注意设备和管道的清洗,避免在清洗过程中对设备和管道造成二次损伤。
综上所述,硫酸烷基化工艺腐蚀问题的解决需要采取一系列的应对措施,包括选择合适的材料、合理的维护保养和严格控制温度和压力等。
通过这些措施,可以有效保护设备和管道,延长设备和管道的使用寿命。
STRATCO硫酸烷基化工艺技术特点及影响因素分析_厉建伦
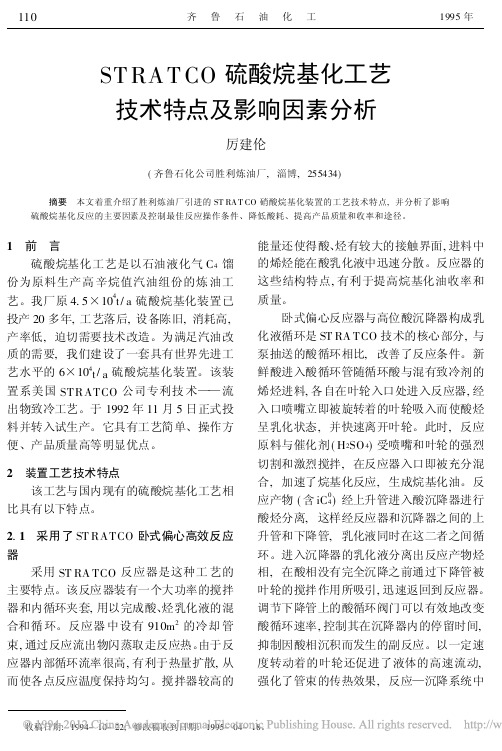
ST RA T CO 硫酸烷基化工艺技术特点及影响因素分析厉建伦(齐鲁石化公司胜利炼油厂,淄博,255434)摘要 本文着重介绍了胜利炼油厂引进的ST RAT CO 硝酸烷基化装置的工艺技术特点,并分析了影响硫酸烷基化反应的主要因素及控制最佳反应操作条件、降低酸耗、提高产品质量和收率和途径。
收稿日期:1994-10-22;修改稿收到日期:1995-04-18。
1 前 言硫酸烷基化工艺是以石油液化气C 4馏份为原料生产高辛烷值汽油组份的炼油工艺。
我厂原4.5×104t/a 硫酸烷基化装置已投产20多年,工艺落后,设备陈旧,消耗高,产率低,迫切需要技术改造。
为满足汽油改质的需要,我们建设了一套具有世界先进工艺水平的6×104t /a 硫酸烷基化装置。
该装置系美国STRATCO 公司专利技术——流出物致冷工艺。
于1992年11月5日正式投料并转入试生产。
它具有工艺简单、操作方便、产品质量高等明显优点。
2 装置工艺技术特点该工艺与国内现有的硫酸烷基化工艺相比具有以下特点。
2.1 采用了ST RATCO 卧式偏心高效反应器采用ST RA TCO 反应器是这种工艺的主要特点。
该反应器装有一个大功率的搅拌器和内循环夹套,用以完成酸、烃乳化液的混合和循环。
反应器中设有910m 2的冷却管束,通过反应流出物闪蒸取走反应热。
由于反应器内部循环流率很高,有利于热量扩散,从而使各点反应温度保持均匀。
搅拌器较高的能量还使得酸、烃有较大的接触界面,进料中的烯烃能在酸乳化液中迅速分散。
反应器的这些结构特点,有利于提高烷基化油收率和质量。
卧式偏心反应器与高位酸沉降器构成乳化液循环是ST RA TCO 技术的核心部分,与泵抽送的酸循环相比,改善了反应条件。
新鲜酸进入酸循环管随循环酸与混有致冷剂的烯烃进料,各自在叶轮入口处进入反应器,经入口喷嘴立即被旋转着的叶轮吸入而使酸烃呈乳化状态,并快速离开叶轮。
此时,反应原料与催化剂(H 2SO 4)受喷嘴和叶轮的强烈切割和激烈搅拌,在反应器入口即被充分混合,加速了烷基化反应,生成烷基化油。
硫酸烷基化工艺腐蚀分析及应对措施研究

硫酸烷基化工艺腐蚀分析及应对措施研究【摘要】本文针对硫酸烷基化工艺中常见的腐蚀问题进行了深入分析和研究,通过对腐蚀机理、影响因素及应对措施进行论述,总结了现有研究进展。
在腐蚀问题日益凸显的情况下,对腐蚀控制和预防提出了有效的解决方案。
通过本文的研究,可以更好地认识硫酸烷基化工艺中腐蚀问题的本质和特点,为相关行业提供技术支持和参考。
未来的研究方向包括进一步探索腐蚀机理、开发新型抗腐蚀材料以及提高腐蚀控制技术水平,以实现对硫酸烷基化工艺腐蚀问题的更好预防和处理。
【关键词】硫酸烷基化工艺、腐蚀、分析、应对措施、研究背景、研究意义、腐蚀机理、影响因素、常见问题、研究进展、成果总结、未来展望。
1. 引言1.1 研究背景硫酸烷基化工艺是一种常见的化工生产方法,广泛应用于石油化工、合成染料、医药和农药等领域。
随着生产规模的不断扩大和生产条件的复杂化,硫酸烷基化工艺在实际生产中面临着严重的腐蚀问题。
在硫酸烷基化工艺中,金属设备受到硫酸和烷基物所引起的腐蚀威胁,容器、管道和阀门等设备往往存在着腐蚀的风险。
腐蚀不仅会降低设备的使用寿命,还会导致设备的安全隐患和生产事故的发生。
研究硫酸烷基化工艺腐蚀问题及应对措施具有重要意义。
通过对硫酸烷基化工艺腐蚀机理的深入分析,可以更好地了解腐蚀过程中的原理和规律,为腐蚀问题的预防和控制提供科学依据。
探讨硫酸烷基化工艺中常见的腐蚀问题及应对措施,可以有效减少生产中的腐蚀损失,提高设备的稳定性和可靠性。
对硫酸烷基化工艺腐蚀问题的研究具有重要的现实意义和应用价值。
1.2 研究意义硫酸烷基化工艺在化工生产中具有重要的应用价值,能够实现烷基化反应,提高产物的附加值。
随着工艺规模的扩大和生产条件的变化,硫酸烷基化工艺腐蚀问题逐渐凸显出来。
腐蚀问题不仅会影响设备的正常运行,还会危及生产安全,导致生产事故的发生。
研究硫酸烷基化工艺腐蚀分析及应对措施具有重要的意义。
通过对硫酸烷基化工艺腐蚀进行深入研究,可以更好地了解腐蚀机理,找出影响腐蚀的因素,提出有效的应对措施,为化工生产提供技术支撑和保障。
硫酸烷基化工艺腐蚀分析及应对措施研究

硫酸烷基化工艺腐蚀分析及应对措施研究硫酸烷基化工艺是一种在精细化学品生产中广泛使用的化学反应过程,但随着工艺的推广应用,其腐蚀问题日益显著。
针对硫酸烷基化工艺的腐蚀问题,本文进行了相关分析并提出了相应的应对措施。
硫酸烷基化反应过程中存在着许多影响腐蚀的因素,如进料质量、反应温度、反应物浓度、气体流量、反应容器材质等。
其中,温度是影响腐蚀的最主要因素。
反应温度高于170℃时,硫酸烷基化反应会产生大量的硫酸酰烷基,硫酸酰烷基能形成极具腐蚀性的硫酸。
此外,硫酸烷基化反应中的反应物也会影响腐蚀性。
含有醇类反应物的硫酸烷基化反应会产生较高浓度的氯化氢,而氯化氢对不锈钢等材质很容易产生腐蚀作用。
此外,不同反应物的比例也会对腐蚀性产生影响,比如甲苯与氯化硫酸反应的比例过高,会使腐蚀速度加快。
针对硫酸烷基化工艺的腐蚀问题,我们可以从以下方面采取应对措施:1、选择合适材质在硫酸烷基化反应中,由于反应物的不同组合会导致生成的化学物质不同,其对材质的腐蚀程度也不同。
因此,在选择精细化学品生产中的反应容器时,应根据化学反应类型与条件来选用适应性良好的材质,如碳钢、316L不锈钢、锆合金等。
2、控制反应温度反应温度是影响硫酸烷基化反应腐蚀的最主要因素。
降低反应温度可以减少产生的硫酸酰烷基浓度,进而减缓腐蚀的速度。
因此,在生产过程中应控制反应温度在170℃以下。
同时,将硫酸酰烷基排放到处理设备中,在排放前进行稀释也可以减轻腐蚀问题。
3、加入缓蚀剂在反应中加入适当的缓蚀剂,能起到减缓、抑制腐蚀的作用。
常用的缓蚀剂有咪唑类缓蚀剂和卡宾类缓蚀剂等。
4、加强清洗与维护及时清洗反应容器、保养设备,以及设立检测系统进行监测,都能帮助尽早发现、处理反应容器内壁存在的腐蚀问题。
此外,设立防腐涂层也是一种有效的预防措施。
5、规范生产操作生产操作的规范化,能最大程度地避免人为因素引发的安全事故。
在硫酸烷基化反应中,要求合格的操作技术员、表明化学物质的标识、采用个人防护措施等,也有助于减少潜在风险。
硫酸烷基化工艺腐蚀分析及应对措施研究

硫酸烷基化工艺腐蚀分析及应对措施研究硫酸烷基化工艺是一种重要的有机合成工艺,在某些化工行业中得到广泛应用。
这种工艺在实际应用中容易出现腐蚀问题,特别是对于设备和管道,导致设备寿命缩短、工作效率下降以及生产安全风险增加。
对硫酸烷基化工艺的腐蚀进行分析和研究,并采取相应的应对措施,对于提高工艺的稳定性和安全性具有重要意义。
对硫酸烷基化工艺的腐蚀进行分析。
硫酸烷基化过程中常用的反应物是硫酸和烷基化剂,这些反应物具有一定的腐蚀性。
在硫酸溶液中,一些金属如铁、铜、镍等容易发生腐蚀反应,导致设备和管道的金属材料受损。
硫酸的酸性也使得设备和管道的非金属材料受到侵蚀,例如橡胶密封件、塑料管道等。
腐蚀是硫酸烷基化工艺中无法忽视的一个重要问题。
针对硫酸烷基化工艺的腐蚀问题,可以采取如下的应对措施:1.材料选择:选择具有良好耐腐蚀性的材料用于设备和管道的制作,例如不锈钢、玻璃钢、聚丙烯等。
避免选用容易受腐蚀的金属材料。
2.涂层保护:在金属表面涂覆一层抗腐蚀涂层,如橡胶、聚酯等材料的涂层,可以起到防腐蚀的作用。
涂层的选择应根据具体的工艺条件和腐蚀介质进行合理选择。
3.防腐措施:加入适量的缓蚀剂或者缓蚀剂体系,如硝酸铜、碳酸钠等,可以减少腐蚀速率,提高设备和管道的抗腐蚀性能。
定期进行设备和管道的维修和检测,及时发现和处理腐蚀问题。
4.工艺改进:通过改进硫酸烷基化工艺,减少腐蚀介质的作用时间和浓度,可以降低腐蚀风险。
优化反应条件、改变反应器结构等,可以减少腐蚀反应的发生。
需要强调的是,腐蚀分析和应对措施的研究是一个多方面的工作,需要综合考虑工艺条件、设备材料、腐蚀介质等因素的影响。
只有在腐蚀分析的基础上制定出科学合理的防腐措施,才能提高硫酸烷基化工艺的安全性和可靠性,保障生产过程的顺利进行。
硫酸烷基化工艺腐蚀分析及应对措施研究

硫酸烷基化工艺腐蚀分析及应对措施研究硫酸烷基化是一种重要的化工工艺,在石化、制药、农药等领域都有广泛应用。
由于硫酸烷基化过程中存在的腐蚀问题,工艺的稳定性和安全性可能会受到威胁。
对硫酸烷基化工艺的腐蚀问题进行分析并采取相应的应对措施是非常必要的。
硫酸烷基化工艺涉及到硫酸与烷烃反应生成亚硫酸盐的过程。
在该过程中,腐蚀主要由以下两方面导致。
由于反应过程中产生的亚硫酸盐具有腐蚀性,会对设备和管道内壁产生腐蚀。
亚硫酸盐在酸性条件下易于氧化为硫酸,硫酸是一种强酸,具有很强的腐蚀性。
在硫酸烷基化过程中,设备和管道的材料选择非常重要。
一般而言,不锈钢等高耐腐蚀材料是比较常用的选择。
可以通过在设备和管道内部进行涂层处理,增加腐蚀抵抗能力。
还可以定期进行腐蚀监测,及时修复或更换受损的设备和管道,以保障工艺的稳定性和安全性。
在硫酸烷基化过程中,反应温度较高,会导致设备和管道的金属材料受热腐蚀。
高温环境下,金属材料容易发生氧化、蒸发、颗粒剥离等现象,从而降低了设备和管道的使用寿命,甚至引发安全事故。
为了解决这个问题,可以采取降温措施,如在设备和管道周围设置隔热层、增加冷却剂的流速、调整反应温度等。
合理设计设备和管道的结构,选择耐高温材料,也可以有效减少热腐蚀的发生。
为了进一步提高硫酸烷基化工艺的稳定性和安全性,还可以采取以下措施:1. 设备和管道的定期维护和保养,及时发现并处理可能存在的腐蚀问题。
2. 强化操作人员的培训和安全意识,确保他们对工艺过程的理解和控制。
3. 加强设备和管道的监测,通过温度、压力、流量等参数的实时监控,及时发现异常情况并采取措施。
4. 对离子膜进行合理选择和保养,防止其受腐蚀。
硫酸烷基化工艺的腐蚀问题是一个需要重视并解决的难题。
通过合理选择材料、加强设备和管道的维护、控制反应温度、加强操作人员培训等措施,可以有效降低腐蚀的发生,提高工艺的稳定性和安全性。
硫酸烷基化工艺腐蚀分析及应对措施研究
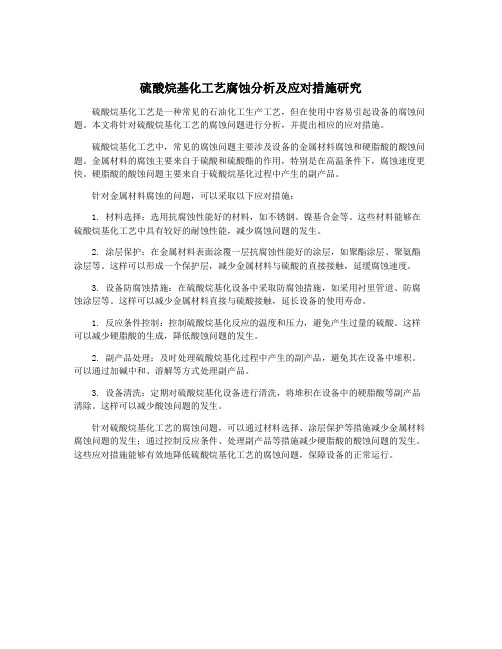
硫酸烷基化工艺腐蚀分析及应对措施研究硫酸烷基化工艺是一种常见的石油化工生产工艺,但在使用中容易引起设备的腐蚀问题。
本文将针对硫酸烷基化工艺的腐蚀问题进行分析,并提出相应的应对措施。
硫酸烷基化工艺中,常见的腐蚀问题主要涉及设备的金属材料腐蚀和硬脂酸的酸蚀问题。
金属材料的腐蚀主要来自于硫酸和硫酸酯的作用,特别是在高温条件下,腐蚀速度更快。
硬脂酸的酸蚀问题主要来自于硫酸烷基化过程中产生的副产品。
针对金属材料腐蚀的问题,可以采取以下应对措施:1. 材料选择:选用抗腐蚀性能好的材料,如不锈钢、镍基合金等。
这些材料能够在硫酸烷基化工艺中具有较好的耐蚀性能,减少腐蚀问题的发生。
2. 涂层保护:在金属材料表面涂覆一层抗腐蚀性能好的涂层,如聚酯涂层、聚氨酯涂层等。
这样可以形成一个保护层,减少金属材料与硫酸的直接接触,延缓腐蚀速度。
3. 设备防腐蚀措施:在硫酸烷基化设备中采取防腐蚀措施,如采用衬里管道、防腐蚀涂层等。
这样可以减少金属材料直接与硫酸接触,延长设备的使用寿命。
1. 反应条件控制:控制硫酸烷基化反应的温度和压力,避免产生过量的硫酸。
这样可以减少硬脂酸的生成,降低酸蚀问题的发生。
2. 副产品处理:及时处理硫酸烷基化过程中产生的副产品,避免其在设备中堆积。
可以通过加碱中和、溶解等方式处理副产品。
3. 设备清洗:定期对硫酸烷基化设备进行清洗,将堆积在设备中的硬脂酸等副产品清除。
这样可以减少酸蚀问题的发生。
针对硫酸烷基化工艺的腐蚀问题,可以通过材料选择、涂层保护等措施减少金属材料腐蚀问题的发生;通过控制反应条件、处理副产品等措施减少硬脂酸的酸蚀问题的发生。
这些应对措施能够有效地降低硫酸烷基化工艺的腐蚀问题,保障设备的正常运行。
硫酸法烷基化装置腐蚀影响因素分析及防护措施

硫酸法烷基化装置腐蚀影响因素分析及防护措施摘要:在硫酸法烷基化装置运行过程中,硫酸会对装置造成较为严重的腐蚀影响。
做好腐蚀问题的防护是确保装置安全运行的关键。
基于此,文章对硫酸法烷基化装置的易腐蚀部位进行了分析,以及分析了影响装置腐蚀的相关因素,最后对装置的腐蚀防护措施进行了有效探讨,以提高烷基化装置的安全生产运行效果。
关键词:硫酸法;烷基化装置;腐蚀;影响;措施一、硫酸法烷基化装置易腐蚀部位(一)反应部位在装置运行过程中,反应器、酸烃聚结分离器、闪蒸罐等相关的设备、容器会受到硫酸的影响而产生均匀、轻微的腐蚀,在容器的器壁、底部都能够观察到浮锈,以及有液体流经留下的轻微流痕。
(二)反应化学处理部位装置中进行酸洗的筒体腐蚀痕迹较轻,但是内部的合金填料会受到较为严重的腐蚀,即便是没有穿孔的位置也只剩薄薄的一层。
同时,碱洗罐注入位置也会遭到严重腐蚀,尤其是在注入点的液体流态较为复杂,在中和反应时也会形成水分偏析现象,运行一段时间后也会由于内部沟槽冲蚀发生管线腐蚀泄漏。
即使是碱洗罐上封头在其内表面也会出现氧化腐蚀现象。
(三)分馏部位在装置的分馏过程中,脱异丁烷冷却位置会出现集中腐蚀,反应产物即便是经过酸洗、碱洗、水洗也不能完全去除脂类杂质,在反应塔的高温环境下会分解形成二氧化硫与水融合形成亚硫酸,进而对分馏塔造成腐蚀。
尤其是塔顶水冷器的腐蚀更为明显,管束腐蚀较为均匀。
以及在塔底的反应物中烷基硫酸盐与硫酸脂受高温分解、聚合,导致管束出现沉淀物堆积形成腐蚀。
(四)制冷压缩部位制冷压缩设备材质主要为碳钢,闪蒸气相夹带酸的影响会使得冷剂空冷器管束出现酸腐蚀,形成与脱异丁烷塔顶空冷管束一样的腐蚀问题。
(五)浓硫酸储罐部位酸储与输送设备以碳钢为主要材质,运行基本平稳,但是在新酸泵出口管线弯头位置会发生腐蚀问题,包括废酸泵出口管线也会腐蚀变薄、泄漏。
尤其是在夏季管线温度可达40摄氏度,泵口温度升高与发生湍流,会手打硫酸腐蚀问题进一步加重。
硫酸烷基化工艺腐蚀分析及应对措施研究
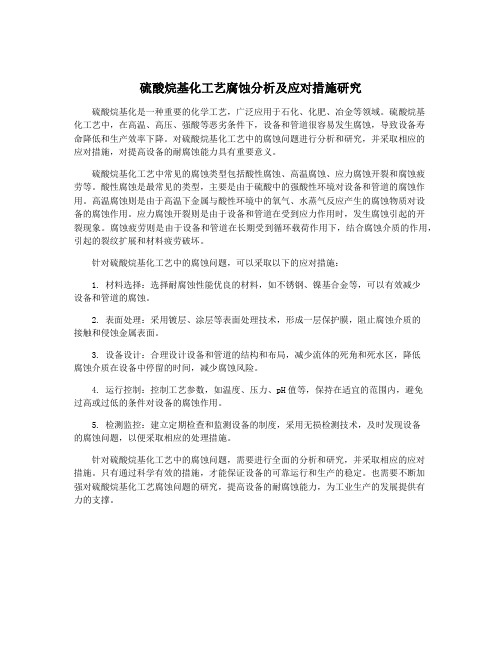
硫酸烷基化工艺腐蚀分析及应对措施研究硫酸烷基化是一种重要的化学工艺,广泛应用于石化、化肥、冶金等领域。
硫酸烷基化工艺中,在高温、高压、强酸等恶劣条件下,设备和管道很容易发生腐蚀,导致设备寿命降低和生产效率下降。
对硫酸烷基化工艺中的腐蚀问题进行分析和研究,并采取相应的应对措施,对提高设备的耐腐蚀能力具有重要意义。
硫酸烷基化工艺中常见的腐蚀类型包括酸性腐蚀、高温腐蚀、应力腐蚀开裂和腐蚀疲劳等。
酸性腐蚀是最常见的类型,主要是由于硫酸中的强酸性环境对设备和管道的腐蚀作用。
高温腐蚀则是由于高温下金属与酸性环境中的氧气、水蒸气反应产生的腐蚀物质对设备的腐蚀作用。
应力腐蚀开裂则是由于设备和管道在受到应力作用时,发生腐蚀引起的开裂现象。
腐蚀疲劳则是由于设备和管道在长期受到循环载荷作用下,结合腐蚀介质的作用,引起的裂纹扩展和材料疲劳破坏。
针对硫酸烷基化工艺中的腐蚀问题,可以采取以下的应对措施:1. 材料选择:选择耐腐蚀性能优良的材料,如不锈钢、镍基合金等,可以有效减少设备和管道的腐蚀。
2. 表面处理:采用镀层、涂层等表面处理技术,形成一层保护膜,阻止腐蚀介质的接触和侵蚀金属表面。
3. 设备设计:合理设计设备和管道的结构和布局,减少流体的死角和死水区,降低腐蚀介质在设备中停留的时间,减少腐蚀风险。
4. 运行控制:控制工艺参数,如温度、压力、pH值等,保持在适宜的范围内,避免过高或过低的条件对设备的腐蚀作用。
5. 检测监控:建立定期检查和监测设备的制度,采用无损检测技术,及时发现设备的腐蚀问题,以便采取相应的处理措施。
针对硫酸烷基化工艺中的腐蚀问题,需要进行全面的分析和研究,并采取相应的应对措施。
只有通过科学有效的措施,才能保证设备的可靠运行和生产的稳定。
也需要不断加强对硫酸烷基化工艺腐蚀问题的研究,提高设备的耐腐蚀能力,为工业生产的发展提供有力的支撑。
硫酸法烷基化产品质量影响因素及优化措施分析

硫酸法烷基化产品质量影响因素及优化措施分析摘要:硫酸法烷基化产品的质量会受到多种因素的影响,特别是对于硫酸法烷基化装置所生产的烷基化油,这种产品的辛烷值较高,硫含量较低,具有无烯烃、无芳烃、不含氧等特点,是汽油的最理想成分之一。
因此通过调整烷基化原料的组成,去除其中杂质的含量,确保生产设备的安全稳定运行就必须加强对于影响生产质量的因素分析,提升产品质量。
关键词:硫酸法烷基化产品;原料成分;因素分析引言:烷基化油的拂程很宽,顺应了当前新配方汽油的发展需求,如果只是使用烷基化油代替MTBE,就会导致原本的部分异构化物很难成为汽油的调和组分。
然而现在通过减小雷德蒸汽压的方式能够有效促进调和,因此就如何提升烷基化装置的生产效率以及生产稳定性,降低整个装置的运行成本成为当前生产中急剧待解的问题。
1硫酸法烷基化简介硫酸法烷基化是一种物制冷技术,这种技术已经有了较长时间的发展,艺术整体较为成熟,有很多工业企业都是以此技术为基础的生产装置。
我国是在上个世纪80年代引入的硫酸烷基化装置采用该技术进行生产,硫酸烷基化的主要优点是酸资源较为丰富,技术应用价格便宜,生产成本低,而且在回收的过程中因为硫酸烷基化的产品活性较高,可以让整个装置运行周期变得更长。
但是由于硫酸会腐蚀生产设备,硫酸法烷基化工艺的消耗酸会较大,而且会产生大量的污染物导致周围环境受到污染。
因此需要建立废酸再生装置来保证生产过程的环保性,由于生产而污染环境[1]。
2 原料对产品质量影响2.1原料各组分(1)丙烷及正丁烷这两种物质在玩机化反应过程中不会参加反应,因为这两种物质都属于惰性组分。
如果其含量过高会降低异丁烷进入酸相的速度,进而导致整个反应过程受到影响,使得烯烃在烷基化反应中发生自聚反应。
(2)丁烯在生产的过程中C8组分含量高,其中特别是2,2,4-三甲基戊烷的含量是最高的,并且由于异丁烯的活性是高于正丁烯的活性,催化剂的作用下容易发生自身聚合,从而溶解在酸相中,形成一种新的ASO酸性油。
硫酸烷基化工艺腐蚀分析及应对措施研究

硫酸烷基化工艺腐蚀分析及应对措施研究硫酸烷基化工艺是一种广泛应用于石油化工行业的重要技术。
由于硫酸具有很强的腐蚀性,对于硫酸烷基化设备的腐蚀问题一直是工艺研究和应用的难点之一。
本文将对硫酸烷基化工艺的腐蚀问题进行分析,并提出相应的应对措施。
我们需要了解硫酸烷基化工艺中可能存在的腐蚀问题。
硫酸本身是一种强酸,具有很强的腐蚀性,可以腐蚀大部分金属和非金属材料。
在硫酸烷基化工艺中,硫酸会与烷基化原料和反应产物产生直接接触,导致设备表面腐蚀。
硫酸烷基化反应中常常伴随着高温和高压的条件,进一步加剧了设备的腐蚀问题。
接下来,我们需要分析硫酸烷基化设备的腐蚀机理。
硫酸可以通过两种主要的腐蚀机理对设备进行腐蚀,即酸腐蚀和氧化腐蚀。
酸腐蚀是指硫酸直接与设备表面的金属发生反应,形成金属离子和硫酸盐,同时释放出氢气。
氧化腐蚀是指硫酸中存在的氧气参与腐蚀反应,形成金属氧化物。
针对硫酸烷基化设备腐蚀问题,我们可以采取以下应对措施:1. 材料选择:选择抗硫酸腐蚀性能优良的材料作为设备的构建材料。
常见的抗硫酸腐蚀材料有不锈钢、镍基合金等。
根据不同的工艺条件,可以使用涂层材料或陶瓷材料进行保护。
2. 设备设计:设计合理的设备结构和附属设备,减少硫酸接触表面积和腐蚀程度。
可以采用短管道、可拆卸的衬里等方式。
3. 操作控制:严格控制工艺操作参数,如温度、浓度、压力等,避免过高或过低的条件对设备造成腐蚀。
定期进行设备检修,及时清理设备内部的硫酸结垢和腐蚀产物。
4. 表面处理:对设备表面进行防腐处理,如采用表面镀锌、喷涂防腐漆等方式,形成一层保护膜,阻止硫酸对设备表面的直接腐蚀。
硫酸烷基化工艺的腐蚀问题是一个复杂而严重的技术难题。
通过合理的材料选择、设备设计、操作控制和表面处理等措施,可以有效地减少硫酸对设备的腐蚀,延长设备的使用寿命,提高生产效率和安全性。
对于硫酸烷基化设备的腐蚀问题还需要进一步的研究和探索,以不断改进和优化工艺。
硫酸法烷基化工艺技术探析
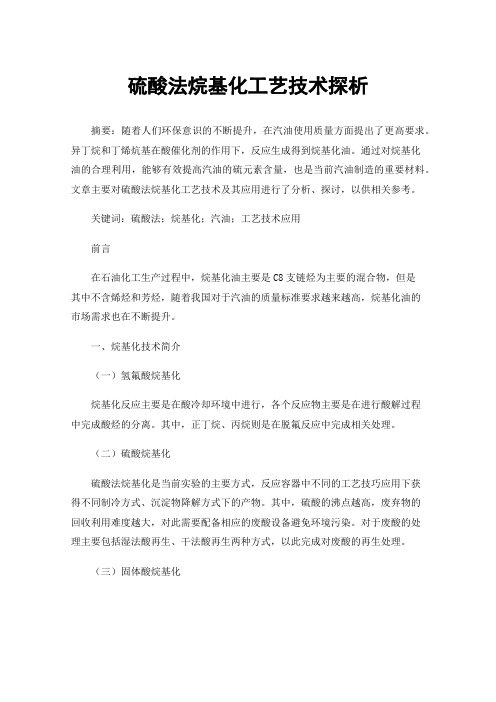
硫酸法烷基化工艺技术探析摘要:随着人们环保意识的不断提升,在汽油使用质量方面提出了更高要求。
异丁烷和丁烯炕基在酸催化剂的作用下,反应生成得到烷基化油。
通过对烷基化油的合理利用,能够有效提高汽油的硫元素含量,也是当前汽油制造的重要材料。
文章主要对硫酸法烷基化工艺技术及其应用进行了分析、探讨,以供相关参考。
关键词:硫酸法;烷基化;汽油;工艺技术应用前言在石油化工生产过程中,烷基化油主要是C8支链烃为主要的混合物,但是其中不含烯烃和芳烃,随着我国对于汽油的质量标准要求越来越高,烷基化油的市场需求也在不断提升。
一、烷基化技术简介(一)氢氟酸烷基化烷基化反应主要是在酸冷却环境中进行,各个反应物主要是在进行酸解过程中完成酸烃的分离。
其中,正丁烷、丙烷则是在脱氟反应中完成相关处理。
(二)硫酸烷基化硫酸法烷基化是当前实验的主要方式,反应容器中不同的工艺技巧应用下获得不同制冷方式、沉淀物降解方式下的产物。
其中,硫酸的沸点越高,废弃物的回收利用难度越大,对此需要配备相应的废酸设备避免环境污染。
对于废酸的处理主要包括湿法酸再生、干法酸再生两种方式,以此完成对废酸的再生处理。
(三)固体酸烷基化在进行固体酸烷基化过程中,主要是借助烷基化、催化反应来进行相关工艺的操作,使得反应物和催化剂分析。
这一反应过程对于设备的要求较低,并且不会出现酸泄漏问题,操作优势较为明显。
(四)离子液烷基化主要是借助对混合碳四原料的合理利用在离子液催化剂的作用下完成异丁烷与烯烃的反应,进而获得烷基化油。
这种类型的烷基化油的辛烷值较高,且不含烯烃、芳烃,敏感度也较小,与其他化合物具备较好的调和性,挥发性、清洁性能都较为明显,是汽油生产过程中最为理想的原料,在实际生产中也主要依靠烷基化技术进行生产设备的基础安装。
二、烷基化工艺(一)CDALKY工艺的应用主要是通过加热碳四混合料分离原材料,再在反应器中与异丁烷进行融合混合,最后在反应器顶端中进行分离反应,进而顺利进入压缩机内部。
硫酸烷基化工艺腐蚀分析及应对措施研究

硫酸烷基化工艺腐蚀分析及应对措施研究硫酸烷基化是一种重要的有机合成反应,广泛应用于化工和医药领域。
然而,使用硫酸进行烷基化反应时,往往存在腐蚀问题,对设备和安全产生一定的影响。
本文结合实际生产中的案例,对硫酸烷基化工艺的腐蚀问题进行分析,并提出相应的应对措施。
一、腐蚀原因分析烷基化反应中出现的腐蚀问题主要来自于以下方面:1.硫酸本身具有强酸性,在高温下对金属设备具有腐蚀作用。
2.烷基化反应的原料、中间体和产物中可能存在对设备具有腐蚀作用的化学物质,如硫醇、烷基溴化物和烷基硫醇等。
3.烷基化反应中产生的副产物如硫酸缩水甘油醚等,可能对设备具有腐蚀作用。
二、应对措施1.选择合适的反应器材料。
选用耐酸、耐腐蚀的材料,如不锈钢、玻璃钢等。
应避免使用烷基化反应前处理中使用不锈钢材料。
2.对设备进行防腐处理。
表面涂覆防酸材料或进行防酸涂层处理可有效避免硫酸对设备的腐蚀作用。
同时,进行定期维修和保养,及时更换老化的设备和耗损严重的构件。
3.采用节流泄压装置。
烷基化反应中,由于反应过程中产生的气体量较大,如采用传统的泄压装置,可能会造成大量的物料和反应废气泄漏,而增加环境污染和安全事故的风险。
采用节流泄压装置,可有效降低废气排放,同时更能保障设备的安全稳定运行。
4.加强储罐管理。
硫酸烷基化反应中,应对储罐进行定期检查,及时处理罐底沉淀和壁面污垢。
针对容积较大的储罐,应实行分段喷淋、定时螺旋搅拌等措施,保持反应物的均匀混合,避免死角和积存的沉淀物。
5.加强现场安全操作。
进行硫酸烷基化反应时,应制定详细的操作规程,定期开展安全培训和演练,建立安全意识。
现场操作人员应佩戴防护设备,避免直接接触反应液体,同时应对设备及时进行维护和检查。
三、结论在硫酸烷基化反应过程中,腐蚀问题是无法避免的,但通过选用适当的材料及技术手段,可以降低腐蚀作用,避免设备出现损坏,并减少环境污染和安全事故的风险。
因此,合理选择设备和储罐材料,采取适当的安全防护措施,加强设备维护管理,能够有效降低硫酸烷基化反应中的腐蚀作用,保障设备安全稳定运行。
- 1、下载文档前请自行甄别文档内容的完整性,平台不提供额外的编辑、内容补充、找答案等附加服务。
- 2、"仅部分预览"的文档,不可在线预览部分如存在完整性等问题,可反馈申请退款(可完整预览的文档不适用该条件!)。
- 3、如文档侵犯您的权益,请联系客服反馈,我们会尽快为您处理(人工客服工作时间:9:00-18:30)。
page 2
பைடு நூலகம்
, 硫酸的 粘度会随之增加, 不利于烯烃分子向酸相的 扩散与酸烃乳化液的生成, 烯 烃之间迭合的 副反应也会随之增加, 影响烷基化油的收率 和质量, 而且还会增加搅 拌机的动力消耗。 如 果反应温度过高, 虽然有助于均匀酸烃乳化 液的生成, 但也加 剧了副反应。 当反应温度上 升到 15~ 20℃时, 烯烃聚合成胶状物, 导致 酸耗急剧 增加, 烷基化油质量和收率下降。 因 此, 理想的反应温度应控制在 4 10℃。 ~ 312 异丁烷浓度 因此, 在硫酸烷基化反应中, 较高的异丁烷 浓度不仅有利于烯烃进入酸相参加 反应, 还 抑制了副反应。 图 1 为反应流出物中异丁烷 浓度与烷基化油辛烷值关系 图。 它表明烷基 化油辛烷值随反应流出物中异丁烷浓度的增 加而递增。 流出物中 异丁烷浓度的提高, 可 通过调节循环异丁烷量和纯度来实现。 但异 丁烷浓度过高, 会增大动力消耗。 实际生产 中, 反应进料中异丁烷与烯烃比率为 8 10 ~ ∶1, 反 应流出物中异丁烷在烃相中的体积含 量为 62%~ 70% , 此时反应效果最佳, 又不 致 增加动力消耗。 异丁烷浓度一般以反应器进料中异丁烷 与烯烃比率和反应流出物中异丁烷含量来表 示。 提高异丁烷浓度能减少副反应 和降低酸 耗, 提高产品的辛烷值和产率。 根据以上烷基化反应式, 其化学平衡常 数 为: 〔 8H 18 〕 C 〔 4H 10 〕〔 4H 8 〕 C C 当温度、 压力一定时, K 为恒值 。 在烷 基化反应过程中, 反应温度、压力保持恒定, K= 图 1 异丁烷浓度与辛烷值关系图 烯烃进料也稳定。 按化学平衡移动的原理, 增 大异丁烷浓度, 化学平衡向右移 动, 有利于 烷基化主反应的进行。 因此, 只有保持较高 的异丁烷浓度, 才有利于烷 基化油的生成。 生产中以保持较高的异丁烷浓度来扩大 异丁烷与酸相的接触面, 使 烯烃分子充分均 匀扩散到异丁烷分子中。 如果异丁烷不足, 烯 烃分散不均匀, 在硫 酸的催化作用下, 烯烃 之间发生聚合反应生成二聚体。 二聚体继续 与烯烃聚合生成 三聚体等多聚物, 形成大分 子的烷烃, 降低了产品的质量和收率; 而且 由于烯烃不 能在酸和异丁烷形成的相中均匀 分散, 硫酸与烯烃加成生成酸性的硫酸氢乙 酯和中 性的硫酸二乙酯, 增加了硫酸的消耗。 系统中正丁烷的累积, 对异丁烷纯度影 响很大, 从而影响烷基化油的质量和收 率。 正 丁烷在烷基化反应中不参与化学反应, 它是 异丁烷的稀释剂, 降低了异丁烷 纯度。 正丁烷 随循环异丁烷进入反应器, 和异丁烷一起共 图 2 正丁烷浓度与干点关系 第 2 期 齐 鲁 石 油 化 工 113 同与硫酸和烯烃接触, 减少了烯烃同硫酸和 异丁烷相接触的机会, 使一些烯烃 进行迭合 反应, 而不与异丁烷反应, 降低了烷基化油 的质量和收率。 由于正丁烷的 存在降低了反 应流出物中异丁烷含量。 图 2 为反应流出物 中正丁烷含量对烷基化 油干点影响的关系 图。 为降低流出物中正丁烷含量, 必须从分 馏塔的正丁烷侧线抽 出除去不参与化学反应 的正丁烷, 才能实现生产条件的优化。 313 酸浓度与酸烃比 酸耗太高, 我们控制反应酸浓度 90% 左右。 酸烃比是烷基化反应中的一个重要 参 数, 它直接影响着烷基化反应效果的好坏。 酸 烃比为酸循环量与烃的总进料比值 , 它表示 烷基化过程中酸与烃的分散状态。 若酸烃体 积比> 1, 则反应器内酸为连 续相, 烃为分散 相, 烃分散到硫酸中, 形成酸包油状态; 若 酸烃比< 1, 则反应器内 烃为连续相, 酸为分 散相, 形成油包酸, 此时反应效果变差, 使 反应器中烯烃占优 势, 缺乏足够的异丁烷, 从 而促进烯烃聚合。 理论上酸过量有利于提高 产品质量, 但生产中由于反应温度较低, 酸 粘度较大, 过量酸需消耗大量能量, 因此生 产上一 般控制酸烃比为 111∶1 左右。 4 结束语 硫酸浓度的高低, 对烷基化油质量和收
page 3
率有直接影响。酸浓度为 95%~ 96% 时最为 适宜, 在此浓度下, 硫酸的催化作 用最佳, 最 有利于烷基化主反应的进行, 烷基化油的质 量和收率都较高; 低浓度酸 将促进副反应, 增 加酸耗并降低烷基化油辛烷值。 因为较低的 硫酸浓度会使硫酸的 催化作用变差, 使部分 烯烃和硫酸作用生成硫酸酯。 硫酸酯溶于硫 酸中, 又降低了 硫酸浓度, 导致了酸耗急剧增 加, 并且降低了烷基化油产率; 另一方面, 较 低的硫 酸浓度, 使烯烃聚合的副反应加剧, 增 加了产品中的重质组分, 降低了烷基化油辛 烷值。 当酸浓度由 94% 降到 89% 时, 烷基化 油的马达法辛烷值可降低 118 个单位 , 烷基 化油的干点可由 189℃上升到 204℃。 当硫酸 浓度低于 88% 时, 硫酸迅速 被稀释, 此时无 论向系统内补加多少新酸, 酸浓度都会无可 逆转地变稀。 为保证烷 基化油质量, 又不致使 综上所述, 该工艺由于采用了先进的反 应器并进行了取热方式、 酸循环等方面的改 进, 改善了反应操作条件, 抑制了 烷基化副反 应的发生, 提高了烷基化油质量和收率, 其产 品质量、 收率、 酸耗等 各项指标均优于传统的 硫酸烷基化工艺; 所以, STRA TCO 硫酸烷 基化流出物致冷工 艺比较先进, 操作平稳, 反 应系统操作方便, 分馏系统操作弹性大, 大大 提高了生 产中的自动化程度, 降低了职工劳 动强度; 而且由于流出物精制过程和原料脱 水工 艺的改进, 降低了酸耗, 提高了产品收 率。 对循环水系统排放阀的改进 水是人类赖以生存的宝贵资源。 合理用水、 节约 用水对保持生态平衡, 提高企业经济效 益有着重要的 意义。 齐鲁石化公司第二化肥厂循环水排放阀, 在正常生产中, 大都处于关闭 状态。 现在在用 的排放阀, 因远离设备、 管道, 在冬季若不将这些阀打开防冻, 则 一旦阀门冻裂, 就会影响 到装置的安全生产; 若将这些阀门打开防冻, 又会浪费大量 的水。 几年来, 作者根据现场实 践, 自制了一种简单、紧凑的排放阀, 焊接在尿素 水冷设备、管道上。这种排放阀紧靠设备、 管道 ( 30mm ) , 冬季勿需打开防冻, 省 去了防冻检查, 还节约了大量的水。 循环水系统的排放阀石化系统有成千上万个, 若 将所有的循环水排放阀进行改进, 冬季 ( 齐鲁石化公司第二化肥厂 王 功) 防冻期 间的节水量是相当可观的。 1
page 1
齐 鲁 石 油 化 工 111 的酸循环借助上升管和下降管中物流的比重 差自然循环。 烷基化反应过程由反 应物自烃相向酸相 的传质所控制。 在硫酸法烷基化过程中, 由于 硫酸催化剂的高粘 度、 高密度、 高表面张力和 异丁烷在硫酸中的低溶解性, 突出了该工艺 过程的化 学反应与分子扩散的矛盾, 微观混 合状态直接影响着反应产物的选择性和收 率, 因 此对酸烃混合的要求非常严格。 在反 应过程中, 不互溶的酸烃 ( 反应物) 应充分 混合, 以稀释烯烃防止局部浓度过高, 并尽 量扩大异丁烷与酸相的接触面, 抑制烷基 化 副反应的产生。 反应完毕后, 酸烃 ( 反应产 物) 沉降物应快速分离, 以保持酸 烃两相中 异丁烷浓度, 卧式偏心反应器的结构的循环 系统, 使酸烃两相混合分布均 匀, 并且混合 比例可调, 较好地满足了硫酸烷基化反应对 酸烃两相接触的技术要求 。 在卧式偏心反应器中, 酸烃两相间保持 着反复地剧烈接触, 形成一个较大的相接 触 面, 增加了异丁烷向酸催化剂的传质区域, 使 酸相内反应消耗了的异丁烷能得到 及时补 充。 酸烃混合均匀以及在沉降器中酸烃两相 的快速分离, 抑制了副反应的发 生。 反应放 出的热量被反应器内的管束及时取走, 这样 可控制一个较低的反应温度 , 且分布均匀。 所 有这些条件, 保障了产品烷基化油的质量, 并 实现高收率和低能 耗。 212 采用反应流出物致冷工艺 分子比。 流出物致冷工艺使反应器内保持最 高的异丁烷浓度, 在搅拌器的搅拌 作用下, 提 高了管束的传热效果, 使整个反应器内温度 保持均匀, 有利于烷基化主 反应的进行。 213 反应流出物采用浓硫酸洗及碱水洗 214 分馏系统采用单塔产品分馏 正常生产中, 反应部分来的反应流出物 夹带少量酸及烯烃与硫酸反应生成的硫 酸 酯。 这些酯类如不加以脱除, 将在下游的脱 异丁烷塔分解放出 SO 2 ( 在高温条 件下) , 遇 到水分, 则会严重腐蚀设备, 并导致脱异丁 烷塔的重沸器结垢。 STRA TCO 工艺对反应流出物采用浓 酸洗及碱水洗的精制流程, 同时在这些设备 中设置了 静电沉降器。 这种精制流程同我厂 前套烷基化装置的碱洗、 水洗工艺相比, 能 更 有效地脱除引起下游系统腐蚀和结垢的硫 酸酯。 反应流出物首先与新酸混合进入酸 洗静 电沉降器。 硫酸酯属于极性分子, 硫酸属于 极性溶剂。 极性分子溶于极性溶 剂中, 吸收 了反应产物中绝大部分硫酸酯的浓硫酸从沉 降器底部连续排出进入反应 器。 硫酸酯是反 应的中间产物, 进入反应器后又继续参与烷 基化反应, 提高了烷基 化油收率。 经酸洗沉 降后的反应流出物携带极微量的硫酸酯和硫 酸进入碱洗电沉降 器。 电沉降器的作用在于 使极微小的极性颗粒凝聚沉降。 经酸洗、 碱 水洗的反应 流出物较好地脱除了硫酸酯, 避 免了对下游设备的腐蚀。 反应流出物致冷是 STRA TCO 工艺的 另一特点。 反应流出物中液相异丁烷的一部 分 ( 包括丙烷和正丁烷) 在反应 器冷却管束 中降压闪蒸, 吸收烷基化反应热量, 以达到 控制反应温度的目的。 反应 流出物在闪蒸罐 中气液分离后, 气相进入致冷压缩机, 经压 缩机压缩、 冷凝后再循 环回反应器。 致冷剂 进入反应器使反应器内异丁烷的量增加了约 一倍, 提高了反应 器内循环异丁烷与烯烃的 由于采用了先进的反应器且连续排出 90% 浓度的废酸, 使产品质量得到了控制 , 反 应过程中不生成重质油, 故可使产品在一个 塔中完成轻组分 ( 异丁烷) 和重组 分 ( 烷基化 油) 的分离。 实际生产中, 只要反应条件控制 适当, 烷基化油的干点 基本上在 190 200℃。 ~ 3 反应影响因素分析 311 反应温度 112 齐 鲁 石 油 化 工 1995 年 烷基化反应的基本反应式为: C 4H 10 + C 4H 8 H 2SO 4 C 8H 18 + Q 该反应是放热反应。 降低温度, 有利于烷 基化油的生成。但如温度低于 4℃时