Lummu公司烷基化工艺简介
烷基化生产工艺

烷基化生产工艺烷基化是一种将烯烃和烃基化合物的同时产生烷基化产物的化学反应。
烷基化生产工艺的目标是高效、经济地生产烷基化产物。
本文将介绍一个典型的烷基化生产工艺,并讨论其优缺点。
典型的烷基化生产工艺可以分为以下几个步骤:烃基化剂与烯烃的混合、反应器反应、产物分离和纯化、废物处理。
首先,烃基化剂和烯烃按照一定的比例混合在一起。
烃基化剂通常是含有烃基的化合物,如甲醇、醇类化合物等。
烯烃则是通过石化工艺生产的,如乙烯、异丁烯等。
烃基化剂和烯烃的混合可以通过加热、搅拌等方式进行。
接下来,混合物被进入反应器进行反应。
反应器通常是高压高温的容器,可以提供充分的反应条件。
在反应过程中,烃基化剂与烯烃发生加成反应,生成烷基化产物。
反应时间和反应温度需要根据具体情况进行调节,以达到最佳的反应效果。
反应完成后,产物需要经过分离和纯化的步骤。
这通常包括蒸馏、结晶、萃取等过程,以去除杂质和提高产物的纯度。
分离和纯化过程需要精确控制操作条件,以确保产物的质量符合要求。
最后,废物需要进行处理。
废物处理包括废水、废气和固体废物的处理。
废水可以通过物理和化学方法进行处理,以去除有害物质。
废气可以通过吸附、吸收、氧化等方式进行处理,以达到排放标准。
固体废物可以通过焚烧、填埋等方式进行处理。
废物处理需要符合环保要求,确保对环境没有负面影响。
总结起来,烷基化生产工艺包括烃基化剂和烯烃的混合、反应器反应、产物分离和纯化、废物处理等步骤。
该工艺能够高效、经济地生产烷基化产物,但同时也需要进行废物处理,以保护环境。
烷基化装置工艺技术方案比选2014

4 结 论 ( 1 ) 从装置投资、 操作费用方面来看, 若将废 酸处理装置投资、 操作费用考虑在内, 氢氟酸法烷 基化技术占有明显优势。 2 ) 从原料适应性及产品质量方面来看, 两 ( 种技术相当。 3 ) 从安全环保角度来看, 两种技术所用的 ( 催化剂均属于有毒化学品, 但氢氟酸属于剧毒化 学品, 对人体安全及环境危害更严重。目前硫酸 法烷基化装置配套的废酸再生处理技术已成功解 决了硫酸法所带来的废酸处理困难的问题, 硫酸 法烷基化更有优势。 ( 4 ) 从当 前 工 业 应 用 业 绩 来 看, 2 0 0 0 —2 0 1 0 年硫酸法与氢氟酸法专利授权比较结果是硫酸法 占烷基化技术的 9 6 %, 而氢氟酸法占 4 %, 硫酸法 烷基化占有绝对优势。
。
0套烷基化装置大都建于 2 0世纪 8 0 国内 2 年代末期, 其中硫酸法烷基化 8套, 氢氟酸烷基化 1 2套, 总处理能力仅 1 . 4M t / a 。由于安全环保问 0 1 0年投产的中海 题, 多数装置处于停工状态。2 油惠州炼油厂烷基化装置采用杜邦公司硫酸法烷 . 1 6M t / a , 是目前国内技术最 基化技术, 规模为 0 先进, 加工能力最大的烷基化装置。表 1~ 2分别 为该装置烷基化反应进料( 选择性加氢后) 及烷 基化油质量的分析数据。
表6 硫酸法与氢氟酸法总体比较 T a b l e 6 O v e r a l l c o m p a r i s o no f H S O n dH F 2 4a
项 目 装置投资 操作费用 安全环保 产品质量 原料适应类性 注: √表示有利。 √ √ √ √ √ 硫酸法( 含废酸处理) 氢氟酸法 √ √
理装置, 而这一难题目前已得到解决。 氢氟酸法烷基化装置具有常温下反应无需制 冷系统的优点, 但是催化剂氢氟酸具有强腐蚀性 及毒性, 在装置选材上要高于硫酸法烷基化装置, 部分材质需采用蒙乃尔合金, 而且对环境的影响 也大于硫酸法烷基化。 与硫酸法和氢氟酸法相比,固体酸烷基化技 术先进, 基本解决了在生产高辛烷值汽油调合组 分过程中产生的环境污染问题, 是既环保又安全 的一种工艺。固体酸烷基化技术能提供更好的原 料灵活性, 降低催化剂消耗, 并且改善产品质量, 代表了烷基化技术的未来发展方向, 但目前尚无 工业化应用。 2 烷基化工业应用
苯乙烯

年产78万吨苯乙烯工艺设计摘要以年产78万吨苯乙烯为生产目标,采用乙烯与苯烃化反应得到乙苯,再由乙苯脱氢制得苯乙烯的工艺方法,对整个工段进行工艺设计和设备选型。
针对设计要求对整个工艺流程进行物料衡算,热量衡算,然后根据物料平衡分别对烃化反应塔,乙苯分离塔,乙苯精馏塔,乙苯/苯乙烯塔,苯乙烯精馏塔,乙苯回收塔的进料量,塔顶、塔底出料量进行物料衡算。
根据热力学定律,对各设备进行热量衡算,并根据设计要求,对设备理论上进行了尺寸计算及选择。
使设备满足设计要求,达到所需要的工艺条件。
本着理论联系实际的精神。
本文对整个工艺流程及车间生产进行了经济技术分析,其中包括各部件的材质、用料量的选择的经济评价、设备投机及投资回收期的计算。
一、原料及产品概述1. 原料概述生产苯乙烯的原料是乙烯和苯。
(1).性质乙烯是无色,稍有气味的气体。
分子式C2H4,相对分子量28。
不溶于水,微溶于乙醇、酮、苯,溶于醚,溶于四氯化碳等有机溶剂。
易燃易爆,具有较强的麻醉作用,吸入高浓度乙烯可立即引起意识丧失。
能发生氧化、加成、聚合反应等化学反应。
苯在常温下为无色、有甜味的透明液体,并具有强烈的芳香气味。
分子式C6H6,相对分子量78。
难溶于水,易溶于有机溶剂,本身也可作为有机溶剂。
可燃,有毒,是一种致癌物质。
能发生氧化、取代、加成反应等化学反应。
(2).用途乙烯是合成纤维、合成橡胶、合成塑料(聚乙烯及聚氯乙烯)、合成乙醇的基本化工原料,也用于制造氯乙烯、苯乙烯、环氧乙烷、醋酸、乙醛、乙醇和炸药等。
苯主要用于合成苯乙烯,聚酰胺树脂(环己烷),苯酚,氯化苯,硝基苯,烷基苯,顺酐,农用化学品,其它医药、轻工及橡胶制品业等。
另外也是一种重要的有机溶剂。
2 产品概述生产产品为纯度大于99.7%的苯乙烯。
(1)性质苯乙烯(SM)是无色、有特殊香气的油状液体。
分子式C8H10,相对分子量104。
难溶于水,能溶于甲醇、乙醇及乙醚等溶剂中。
有毒,空气中允许浓度为0.1mg/L。
lumms硫酸法烷基化

C4xH8x+2
H2SO4 + CxHy (ASO) 2H2O + SO2 + CxHy-2
A World of Solutions
10
Sulfuric Acid Alkylation Fundamentals 硫酸法烷基化基本原理
A World of Solutions
Sulfuric Acid Alkylation Chemistry 硫酸法烷基化化学反应机理
Alkylation Reactions
������2 ������������4
2 i-C4H10 + C5H10 2 C8H18 CxH2x+2
������2 ������������4 ������2 ������������4
C8H18 + C5H12
C7H16 + C9H20 CyH2y + Cx-yH2(x-y)+2
– Contaminants, i.e. Butadiene, Mercaptans, Oxygenates 杂质,如丁二烯,硫醇,氧化物
10
California CaRFG3 加州标准
Euro 5 欧五
Sulfur, ppm 硫 Olefins, % 烯烃 Aromatics, % 芳烃 O + A, % 烯烃+芳烃 Benzene, % 苯 RVP, kPa Winter/Summer 蒸汽压 冬季/夏季 Effective 生效日期
Boiling Point, oF
Reference: Mr. Bill Piel, Tier Associates, USA
烷基化技术

烷基化技术异丁烷和烯烃在酸催化剂的作用下反应生成的烷基化油,其辛烷值高、敏感性(研究法辛烷值与马打法辛烷值之差)小,不含硫、芳烃、烯烃,具有理想的挥发性和清洁的燃烧性,是航空汽油和车用汽油的理想调和组分。
烷基化工艺能充分利用炼厂气体资源的优点,而且,随着环保要求越来越高,因此烷基化工艺是炼油厂中应用最广、最受重视的一种气体加工过程。
一、反应机理烯烃与异丁烷的烷基化反应是复杂的,有简单的加成反应,还有各种副反应。
1、加成反应正碳反应机理:烯烃与催化剂的质子生成一个带正电荷的烃离子异丁烷+异丁烯→三甲基戊烷异丁烷+2-丁烯→三甲基戊烷异丁烷+1-丁烯→二甲基己烷2、异构化反应1-丁烯→2-丁烯异丁烷+2-丁烯→三甲基戊烷三甲基戊烷的辛烷值(RON 100~109)二、对原料的要求1、杂质的含量无论硫酸法烷基化或氢氟酸烷基化,酸耗在操作费用中占有很大比重。
在硫酸法中,反应器中硫酸的浓度是保证烷基化油质量的重要因素。
在氢氟酸法中,酸的含水量是影响设备腐蚀和能否长周期安全运行的关键。
因此对原料的水和会直接或间接导致酸耗增加和稀释酸的杂质需严格限制。
2、对烷烯比的要求原料中的烷/烯是指进装置原料中异丁烷与烯烃的摩尔比。
一般来说在烷基化反应中,异丁烷与烯烃是等分子反应,但由于少量的异丁烷不可避免地随正丁烷及烷基化油带出装置,因此要求进装置原料中异丁烷分子略多于烯烃分子。
一般要求烷烯比(体积)不小于1.05。
三、硫酸法烷基化1、工艺流程压缩机→分离罐→丙烷↑酸沉降罐→闪蒸罐→酸碱洗→分馏塔→正丁烷酸→↓↑↓原料→缓冲罐→脱水罐→反应器烷基化油2、操作条件3、技术经济指标斯特拉科技术的指标4、废酸回收废酸回收涉及改善环境保护和降低成本,是硫酸法烷基化装置的重要配套设施。
国外目前较大的装置多采用焚烧再生法回收废酸,在高温下生成SO2,再将SO2进一步氧化制取硫酸。
烷基化装置工艺流程概述
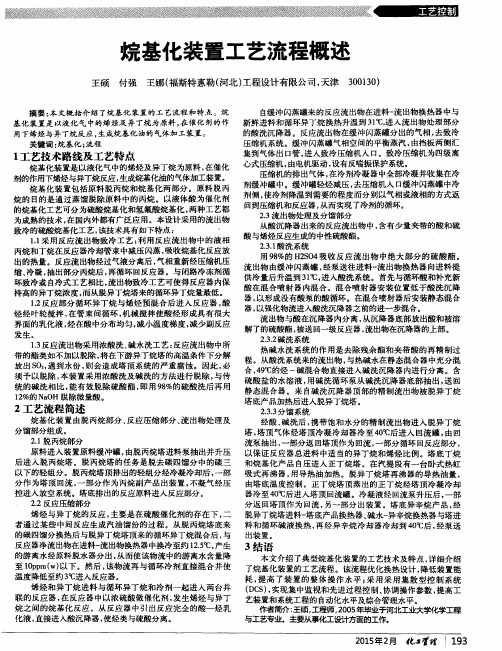
烷基化装置工艺流程概述
王硕 付强 王娜( 福斯特惠勒 ( 河北) 工程设计有限公司, 天津 3 0 0 1 3 0 )
摘要: 本 文概 括介 绍 了烷 基化装 置的 工艺流程 和特 点。烷 自 缓 冲 闪蒸罐来 的反应 流 出物 在进料一 流 出物 换热 器中与 1 ℃, 进 入 流出物 处理 部分 基化 装置是 以液化 气 中的烯烃及 异 丁烷 为原料 , 在 催化 剂的作 新鲜 进料 和循 环异 丁烷换 热升 温到 3 的酸 洗沉 降器 。反 应流 出物在缓 冲 闪蒸 罐分 出的气相 , 去 致冷 用下烯烃与异 丁烷 反应 , 生成烷基化 油的 气体加 工装置 。 压缩 机系统 。缓 冲闪蒸 罐气相 空间的平 衡蒸 汽 , 由挡板 两侧汇 关键词 : 烷基化 ; 流程 集 到气体 出 口管 , 进 入致冷 压缩机 入 口。致冷压缩 机为 四级离 1 工艺技术路线及工艺特点 心式 压缩机 , 由电机 驱动 , 设 有反喘振 保护系统 。 烷基 化装 置是 以液化 气 中的烯烃 及异丁烷 为原 料 , 在催化 压缩机 的排 出气体 , 在冷剂冷 凝器 中全部 冷凝并 收集在 冷 剂的作用 下烯烃 与异丁烷反应 , 生成烷基化 油的气体加 工装 置。 剂 缓冲罐 中 。缓 冲罐轻 烃减压 , 去 压缩机 入 口 缓 冲 闪蒸罐 中冷 烷 基化 装置 包括 原料 脱 丙烷 和烷 基化两 部 分 。原料 脱 丙 剂侧 , 使冷 剂降温 到需要 的程 度而分 别以气相 或液相 的方式 返 烷 的 目的是通 过蒸 馏 脱除原 料 中的 丙烷 。以 液体 酸为 催化 剂 回到压缩机和 反应器 , 从而实 现 了冷剂 的循 环 。 的烷基化 工艺 可分为 硫酸烷 基化和 氢氟酸烷 基化 , 两 种工艺都 2 . 3流 出物处 理及分馏部 分 为成 熟的技 术 , 在 国内外都有广 泛应 用。本设 计采用 的流 出物 从酸 沉 降器 出来 的反应 流 出物 中, 含有 少量夹 带的酸 和硫 致冷的硫 酸烷基化 工艺 , 该技术具有如 下特点 : ’ 酸与烯烃 反应生成 的中性硫酸酯 。 1 . 1 采用 反应 流 出物致 冷 工艺 : 利 用反 应流 出物 中的液 相 2 _ 3 . 1 酸洗 系统 丙烷 和丁烷 在反应 器冷却 管束 中减压 闪蒸 , 吸收烷 基化反 应放 用9 8 %的 H 2 S 0 4 吸收反应流出物中绝大部分的硫酸酯。 出的 热量 。反应流 出物经 过气液 分离后 , 气相重新 经压缩 机压 流 出物 由缓 冲闪 蒸罐 , 经泵送 往进 料一 流 出物 换 热 器向进 料提 缩、 冷凝, 抽 出部 分丙烷 后 , 再循环 回反应 器 。与 闭路冷 冻剂循 供冷 量后升 温到 3 1 ℃, 进入酸 洗 系统 。首先 与循 环酸和补 充新 环致 冷或 自冷式 工艺相 比 , 流出物致 冷工 艺可使 得反应 器内保 酸在 混 合喷 射器 内混 合 。混 合喷射 器安 装位 置低 于 酸洗 沉 降 持高 的异丁烷浓 度 , 而 从脱异丁烷 塔来的循环 异丁烷量最低 。 器, 以形成没有酸泵的酸循环。在混合喷射器后安装静态混合 1 . 2 反应 部 分循 环 异丁烷 与 烯烃 预混 合 后进 入 反应 器 , 酸 器, 以 强化物流进入 酸洗沉降 器之前的进一 步混合 。 烃 经 叶轮搅 拌 , 在 管束 间循 环 , 机 械搅拌 使 酸烃 形成 具有 很大 流 出物 与酸在 沉降 器内分 离 , 从 沉 降器底部 放出酸 和被溶 界 面的乳 化液 , 烃 在酸 中分 布均 匀 , 减 小温 度梯度 , 减 少副反应 解了的硫酸酯 , 被送 回一级反 应器 , 流出物在沉 降器的上部 。 发生 。 2 . 3 . 2 碱 洗系统 1 - 3 反应 流 出物 采用 浓酸洗 、 碱 水洗 工艺 : 反应 流 出物 中所 热碱 水 洗系 统的 作用 是去 除 残余 酯和 夹带 酸 的再精 制过 带的酯 类如 不加 以 脱除 , 将在下 游异丁 烷塔 的高温条 件下分 解 程 。从 酸洗 系统来的 流 出物 , 与热碱水 在静态 混合 器中充分 混 放出s ( ) 2 , 遇 到水份 , 则会 造成 塔顶 系统 的严 重腐蚀 。因此 , 必 合, 4 9  ̄ C 的烃 一碱混 合物 直接 进入碱 洗沉 降器 内进行分 离 。含 须予 以脱 除 , 本 装 置采用 浓酸 洗及 碱洗 的方 法进 行 脱除 , 与 传 硫酸盐的水溶液 , 用碱洗循环泵从碱洗沉降器底部抽出, 送回 统 的碱 洗相 比 , 能 有效 脱除 硫酸 酯 , 即用 9 8 %的硫 酸洗 后再 用 静态 混 合器 。来 自碱洗 沉 降器 顶部 的精 制流 出物 被脱 异丁 烷 1 2 %的 N a O H脱除 微量酸 。 塔底产 品加 热后进入 脱异丁烷塔 。 2 工艺流程简述 2 - 3 - 3 分馏 系统 烷 基化 装 置 由脱丙烷 部 分 、 反 应压 缩部分 、 流 出物 处理 及 经酸、 碱 洗后 , 携 带 饱和 水分 的精 制流 出物 进 入脱 异丁 烷 分馏部分 组成 。 塔, 塔顶气体经塔顶冷凝冷却器冷至4 0  ̄ C 后进入 回流罐 , 由回 2 . 1 脱 丙烷 部分 流泵 抽 出, 一部 分返 回塔顶作为 回流 , 一部 分循 环 回反应 部分 , 原料 进入 装 置原 料缓 冲罐 , 由脱 丙烷塔 进料泵 抽 出并 升压 以保 证 反应 器总 进料 中适 当的 异丁烷 和 烯烃 比例 。塔 底丁 烷 后 进入 脱丙 烷塔 。脱 丙烷 塔 的任务 是 脱去碳 四馏 分 中的 碳三 和烷 基化 产 品 自压进 入正 丁烷 塔 。在汽 提 段有一 台 卧式 热虹 以 下的轻组 分 。脱丙烷塔 顶排 出的轻组分 经冷 凝冷却后 , 一部 吸式 再 沸器 , 用 导热 油加 热 。脱异 丁烷 塔再 沸 器的导 热 油量 , 分 作为 塔顶 回流 , 一部 分作 为丙烷 副 产品 出装 置 , 不凝 气 经压 由塔 底温 度 控制 。正 丁烷 塔顶 蒸 出的正 丁烷 经塔 顶冷 凝 冷却 控进 入放空 系统 。塔底排 出的反应原料 进入反应部分 。 器冷 至 4 0 q C 后进入塔 顶 回流罐 。冷凝液 经 回流 泵升压 后 , 一部 2 . 2 反 应压缩部分 分返 回塔 顶 作为 回流 , 另一 部分 出装 置 。塔 底 异辛烷 产 品 , 经 烯烃 与异 丁烷 的反 应 , 主 要是 在硫 酸催 化剂 的 存在 下 , 二 脱异 丁烷塔进 料一 塔 底产 品换 热器 、 碱水 一 异辛烷 换热 器与塔进 者通 过 某些 中间反应 生成 汽 油馏份 的过 程 。从脱 丙烷 塔 底来 料和 循 环碱 液换 热 , 再 经异 辛烷 冷 却器 冷却到 4 0 ℃后 , 经 泵送 的碳 四馏分 换热后 与脱异 丁烷塔 顶来 的循 环异 丁烷混 合后 , 与 出装 置。 反应 器净流 出物 在进料一 流出物换热 器中换冷 至约 1 2 . 5  ̄ C , 产生 3结语 的游 离水 经原料 脱水器分 出 , 从而使 该物流 中的游 离水含 量降 本文介 绍了典 型烷基 化装 置的工艺 技术及 特点 , 详细 介绍 至1 0 p p m( w) 以下 。然 后 , 该 物流 再 与循 环冷 剂直 接混 合 并使 了烷 基化 装置的 工艺流程 。该 流程优 化换热设 计 , 降低 装置能 温度 降低至 约 3 ℃进 入反应器 。 耗, 提 高 了装 置 的 整 体操 作水 平 ; 采 用 采 用 集 散 型控 制 系统 烯烃 和异 丁烷 进料 与循 环 异丁 烷和 冷剂 一起 进 入两 台并 ( D C S ) , 实现 集 中监 视和 先进 过程控 制 、 协调 操作 参数 , 提 高 工 联 的反 应 器 , 在 反应 器中 以浓硫 酸做 催化 剂 , 发 生烯 烃与 异丁 艺装 置和 系统 工程的 自 动化 水平及综合 管理水平 。 烷 之 间的烷 基化 反应 。从 反应 器 中 引出反应 完 全的 酸一 烃乳 作者 简介 : 王硕 , 工程 师 , 2 0 0 5 年 毕业于 河 北工 业大 学化 学工 程 化液, 直接 进入酸沉 降器 , 使烃类与硫酸 分离 。 与工 艺 专业 。主要 从事 化 工设 计方 面的 工作 。
烷基化流程简述
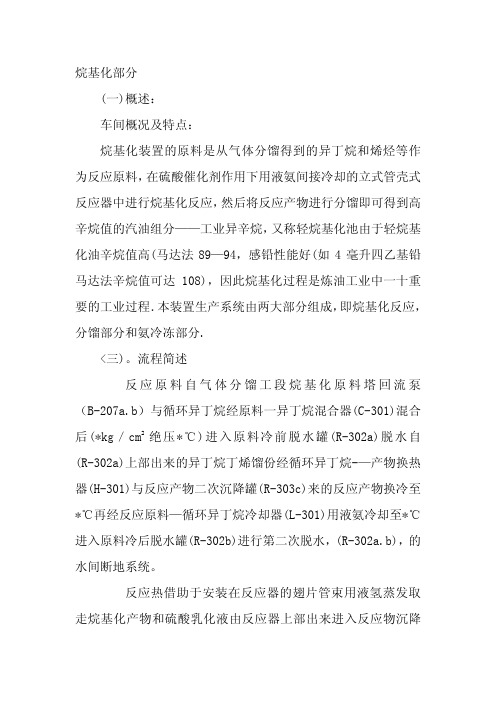
烷基化部分(一)概述:车间概况及特点:烷基化装置的原料是从气体分馏得到的异丁烷和烯烃等作为反应原料,在硫酸催化剂作用下用液氨间接冷却的立式管壳式反应器中进行烷基化反应,然后将反应产物进行分馏即可得到高辛烷值的汽油组分——工业异辛烷,又称轻烷基化池由于轻烷基化油辛烷值高(马达法89—94,感铅性能好(如4毫升四乙基铅马达法辛烷值可达108),因此烷基化过程是炼油工业中一十重要的工业过程.本装置生产系统由两大部分组成,即烷基化反应,分馏部分和氨冷冻部分.<三)。
流程简述反应原料自气体分馏工段烷基化原料塔回流泵(B-207a.b)与循环异丁烷经原料一异丁烷混合器(C-301)混合后(*kg/cm2绝压*℃)进入原料冷前脱水罐(R-302a)脱水自(R-302a)上部出来的异丁烷丁烯馏份经循环异丁烷-—产物换热器(H-301)与反应产物二次沉降罐(R-303c)来的反应产物换冷至*℃再经反应原料—循环异丁烷冷却器(L-301)用液氨冷却至*℃进入原料冷后脱水罐(R-302b)进行第二次脱水,(R-302a.b),的水间断地系统。
反应热借助于安装在反应器的翅片管束用液氢蒸发取走烷基化产物和硫酸乳化液由反应器上部出来进入反应物沉降罐(R-303a.b)沉降分离,分离出来的硫酸循环使用.反应产物由(R-303a.b)部出来进入反应物二次沉降罐(R-303c) 进行二次沉降分离,(R-303c)上部出来的反应产物经(H—301),与循环异丁烷换热后,经产物碱洗混合器.(C302)与碱液混合进入反应产物碱洗罐(R-305),自(R-305)顶出来经产物水洗混合器(C-303)与*~*℃温水混合后进入反应产物水洗罐(R-306)水洗后反应产物进入(T-301)进科缓冲罐(R-307)当*%的硫酸降至*%以下时,不再使用,由(R-302a.b)压入废酸沉降罐(R-304)沉降分离出来的废硫酸经循环硫酸泵送入废酸贮罐(R-324),用汽车槽车送往奎屯硫酸厂处理。
危险工艺之烷基化工艺参数

反应类型
放热反应
重点监控单元
烷基化反应釜
工艺简介
把烷基引入有机化合物分子中的碳、氮、氧等原子上的反应称为烷基化反应。涉及烷基化反应的工艺过程为烷基化工艺,可分为C-烷基化反应、 N-烷基化反应、 O-烷基化反应等。
工艺危险特点
(1)反应介质具有燃爆危险性;
(2)烷基化催化剂具有自燃危险性,遇水剧烈反应,放出大量热量,容易引起火灾甚至爆炸;
(3)烷基化反应都是在加热条件下进行,原料、催化剂、烷基化剂等加料次序颠倒、加料速度过快或者搅拌中断停止等异常现象容易引起局部剧烈反应,造成跑料,引发火灾或爆炸事故。
典型工艺
(1) C-烷基化反应
乙烯、丙烯以及长链α-烯烃,制备乙苯、异丙苯和高级烷基苯;
苯系物与氯代高级烷烃在催化剂作用下制备高级烷基苯;
重点监控工艺参数
烷基化反应釜内温度和压力;烷基化反应釜内搅拌速率;反应物料的流量及配比等。
安全控制的基本要求
反应物料的紧急切断系统;紧急冷却系统;安全泄放系统;可燃和有毒气体检测报警装置等。
宜采用的控制方式
将烷基化反应釜内温度和压力与釜内搅拌、烷基化物料流量、烷基化反应釜夹套冷却水进水阀形成联锁关系,当烷基化反应釜内温度超标或搅拌系统发生故障时自动停止加料并紧急停车。
对甲苯胺与硫酸二甲酯制备N,N-二甲基对甲苯胺;
环氧乙烷与苯胺制备N-(β-羟乙基)苯胺;
氨或脂肪胺和环氧乙烷制备乙醇胺类化合物;
苯胺与丙烯腈反应制备N-(β-氰乙基)苯胺等。
(3) O-烷基化反应
对苯二酚、氢氧化钠水溶液和氯甲烷制备对苯二甲醚;
硫酸二甲酯与苯酚制备苯甲醚;
高级脂肪醇或烷基酚与环氧乙烷加成生成聚醚类产物等。
烷基化技术及其工业应用研究

烷基化技术及其工业应用研究烷基化技术是一种重要的有机合成技术,广泛应用于石油化工、精细化工等领域。
烷基化技术可以将一个分子中的氢原子替换为烷基基团,从而改变分子结构和性质,为化学工业提供了丰富的原料和方法。
本文将介绍烷基化技术的原理、工艺条件,以及其在工业生产中的应用研究。
一、烷基化技术的原理烷基化是一种将烷基基团引入到分子中的反应,通常是通过碳-碳键或者碳-氢键的断裂来实现。
烷基化反应一般是在催化剂的作用下进行的,常见的催化剂包括氯化铝、氟化铝等。
烷基化反应的一般机理包括:烷基自由基的产生、烷基自由基与底物分子的反应、烷基自由基的重组等步骤。
烷基化反应的选择性、活性和收率等性能与催化剂的种类、反应条件、底物结构等因素密切相关。
1. 反应温度:烷基化反应一般在较高的温度下进行,通常在100-300摄氏度之间。
温度过低会影响反应的速率和选择性,而温度过高则可能导致副反应的发生和产物的烷基化失活等现象。
2. 反应压力:烷基化反应的压力一般在常压至数十大气压之间,通常选择适当的压力可以提高反应速率和反应选择性。
3. 催化剂选择:不同的烷基化反应需要不同的催化剂,常见的催化剂包括氯化铝、氟化铝、氧化铝等。
催化剂的选择对反应的速率、选择性、活性等性能有着重要的影响。
4. 底物选择:底物的结构和性质对烷基化反应的进行也有着重要的影响。
通常来说,分子内含有易于被烷基化的碳-氢键的底物更容易进行烷基化反应。
5. 反应溶剂:反应溶剂的选择对反应速率和选择性有着重要的影响。
常用的反应溶剂包括烷烃、芳烃、醚类、醇类等。
烷基化技术在工业生产中有着广泛的应用,主要包括以下几个方面:1. 烷烃烷基化:烷烃烷基化是烷基化技术的一个重要应用方向。
它可以将低碳烷烴如甲烷、乙烷等转化为高碳烷烴如丙烷、丁烷等,为石油化工生产提供了丰富的原料。
2. 芳烃烷基化:芳烃烷基化是将芳烃分子中的一个或多个氢原子替换为烷基基团的反应。
它可以制备出一系列的芳基烷烃,这些产物在合成染料、香精香料、医药中间体等领域有着广泛的应用。
化工工艺学 烷基化

1. 化学反应
异丁烷与烯烃的化学反应可表述如下:
副反应有裂解、叠合、异构化、歧化和缩聚等, 生成众多的低沸点和高沸点副产物。↓副反应, 常使异丁烷大大过量。
2. 催化剂 (1) 硫酸
用作烷基化催化剂的硫酸浓度为86%~96%(w)。 硫酸浓度不能太低,以保证反应的顺利进行。硫酸
浓度太高,会促使烯烃氧化。同时,在浓酸中烷/ 烯比严重失调,副反应激烈,副产物增多。 为↑酸烃的接触面,在反应器内需使催化剂与作用 物处于良好的乳化状态,并适当↑酸烃比以↑烷基化 产物的收率和质量。
分子结合重又形成水合氢离子。
由上述机理,反应物和产物在酸膜中的扩散速 度、催化剂表面的酸浓度、反应物的浓度以及 反应温度都会对反应速度产生明显影响。动力 学试验表明,反应速度对乙烯分压是一级,而 水蒸气的分压的正面影响与乙烯相同,负面影 响是使催化剂表面酸浓度(即酸强度)↓,↓反应 速度,因此合适的水蒸气分压由实验确定。
三、乙烯水合制乙醇
1. 生产方法评述 (1) 硫酸水合法
第一步是乙烯与硫酸反应生成烷基硫酸酯 ,第 二步是烷基硫酸酯通直接蒸气加热水解蒸出醇, 硫酸浓度被稀释至50%左右。
提纯费用大,污染严重,副反应多,原料消耗 高。
(2) 直接水合法
乙烯单程转化率在5%左右,选择性94%~95%, 优点是不存在治理大量废酸问题,环境污染也比硫 酸水合法小得多。缺点是转化率低,绝大多数乙烯 需循环使用。
5-3 烷基化
利用取代反应或加成反应,在有机化合 物分子中的氮、氧、碳、硅、硫、金属 等原子上引入烷基或芳烃基的反应。
烷基化剂:烯烃、卤代烷烃、卤代芳烃、 硫酸烷酯、饱和醇
一、由异丁烷和烯烃合成烷基化汽油
烷基化
热烷基化 催化烷基化
硫酸法烷基化工艺进展

烷基化油是 一种 高辛烷值 、抗爆 性能好 、蒸汽压低 、不含 烯烃 、芳烃 、硫含量低 的烷烃混 合物 ,是一 种理想 的汽 油调和 组 分 。
当今世界环境污染 日益严 重 ,环境保护 普遍受 到各 国的重 视 。无论 国外还在 国内,随着汽 车保有量 的增加 ,汽车排放 尾 气对空气 的污染 日趋严重 ,迫 切需要 汽油升级 换代 。因此 ,烷 基 化工艺 日益受到重视 J。
H 3 y Байду номын сангаас(1, )
n H c— ::
C!!—H— 3吒c H + + (cH c+ +— —— — H c一 —e Ce— — H 2Cm
H 3
c++一一cH
但川
卜 叫
一 卜 “ 卜
1.3 链 终止
1 烷 基 化 反 应 机 理
烷基化反应是指各种 丁烯与异 丁烷发生 反应 ,主要 的反 应
Abstract:The development of alkylation process was introduced. The latest progress in the solid acid and liquid acid alkylation process is reviewed,solid acid alkylation process is still in the test stage of experiment as a result of the fast
关 键 词 :烷基化 ;工艺 ;进 展
中 图分 类 号 :TE624
文献 标志 码 :A
文章编 号 :1001—9677(2016)013—0029—03
烷基化工艺流程简介

烷基化工艺流程简介
烷基化工艺是从烃类中分离出一种或多种烷烃的工艺过程。
它以烷烃为原料,在催化剂作用下生成烷基化油,或由烷基化油、烷基碳数不同的产物组成的混合碳氢化合物,从而生产出性能优良、用途广泛的烷基油产品。
它可以用于生产汽油、柴油和石脑油等,也可作为化工原料。
目前,它在工业上应用最广,因而得到了极大的发展。
烷基化工艺流程简图
(1)原料气(C)进入反应器与催化剂作用,生成烷烃和
相应的烷基化合物。
当反应温度达到200~300℃时,原料气中
的碳原子上的氢原子被烷基所取代。
因此,在此温度范围内原料气中碳原子上的氢原子几乎全部被取代而形成烷基化合物。
在催化剂作用下,烷基化合物之间通过相互加成、断裂和重排反应而生成烷基油和相应的产物。
(2)进入催化剂床层的反应产物气体一部分沿床层上升至
顶部冷却、冷凝,另一部分与催化剂作用形成烷基化合物。
由于反应器内温度较高,气体中的部分碳氢化合物在高温下气化,而另一部分则继续与催化剂作用。
—— 1 —1 —。
烷基化汽油工艺学习烷基化汽油工艺介绍
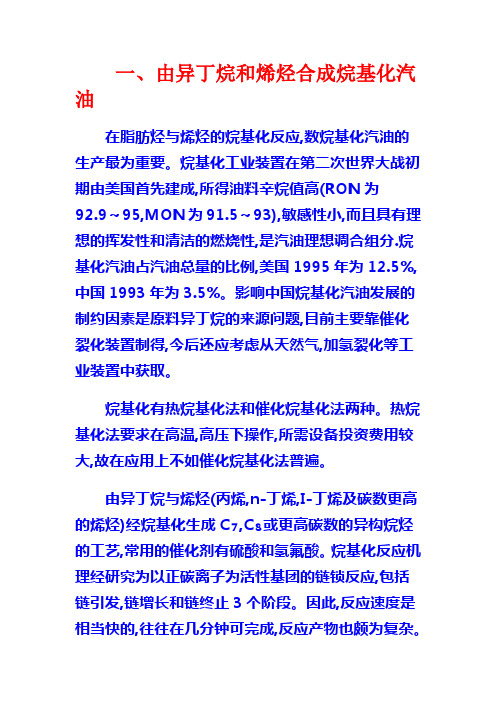
一、由异丁烷和烯烃合成烷基化汽油在脂肪烃与烯烃的烷基化反应,数烷基化汽油的生产最为重要。
烷基化工业装置在第二次世界大战初期由美国首先建成,所得油料辛烷值高(RON为92.9~95,MON为91.5~93),敏感性小,而且具有理想的挥发性和清洁的燃烧性,是汽油理想调合组分.烷基化汽油占汽油总量的比例,美国1995年为12.5%,中国1993年为3.5%。
影响中国烷基化汽油发展的制约因素是原料异丁烷的来源问题,目前主要靠催化裂化装置制得,今后还应考虑从天然气,加氢裂化等工业装置中获取。
烷基化有热烷基化法和催化烷基化法两种。
热烷基化法要求在高温,高压下操作,所需设备投资费用较大,故在应用上不如催化烷基化法普遍。
由异丁烷与烯烃(丙烯,n-丁烯,I-丁烯及碳数更高的烯烃)经烷基化生成C7,C8或更高碳数的异构烷烃的工艺,常用的催化剂有硫酸和氢氟酸。
烷基化反应机理经研究为以正碳离子为活性基团的链锁反应,包括链引发,链增长和链终止3个阶段。
因此,反应速度是相当快的,往往在几分钟可完成,反应产物也颇为复杂。
1.化学反应异丁烷与烯烃的化学反应可表述如下.在反应条件下,硫酸或氢氟酸不能催化异丁烷和乙烯的烷基化反应.异丁烷与丙烯反应主要生成2,3-二甲基戊烷(RON为91):异丁烷与1-丁烯反应时,首先1-丁烯异构化生成2-丁烯,然后再进行烷基化反应。
主要生成2,2,4-甲基戊烷,2,3,4-三甲基戊烷和2,3,3-三甲基戊烷(RON为100~106):[HJ*3]异丁烷与异丁烯反应生成RON为100的2,2,4-三甲基戊烷(即异辛烷):除上述主反应外,还能发生裂解、叠合、异构化、歧化和缩聚等副反应,生成众多的低沸点和高沸点副产物。
为了抑制副反应,常需要使异丁烷大大过量,在氢氟酸法中,异丁烷与烯烃的摩尔比为8~15∶1,硫酸法中摩尔比为4~12∶1。
2.催化剂常用硫酸或氢氟酸作催化剂(1)硫酸用作烷基化催化剂的硫酸浓度为86%~96%(w)。
烷基化工艺概述

塔顶馏出物经冷凝器冷凝后进入塔顶回流罐。冷凝液经泵抽出,部分顶回流,另一部分经冷却器冷却至40℃送出装置。塔底烷基化油经泵抽出,两次换热,再冷却至40℃送出装置。
流出物精制和产品分馏部分
目的是脱除酸脂(99.2%的硫酸+12%的NaOH)。
换热后的反应流出物进入酸洗系统,与酸在酸洗混合器内进行混合后,进入流出物酸洗罐,绝大部分酸脂被吸收。流出物烃类和酸在酸洗罐中分离,烃类流出物酸含量低于10ppm,酸则连续进入反应器作为催化剂使用。
酸洗后的流出物与循环碱液在流出物碱洗混合器中混合后,进入碱洗罐脱除微量酸,进入流出物水洗罐含硫酸钠和亚硫酸盐的碱水经泵从罐底抽出换热后送回混合器入口循环使用。
反应部分
烯烃与异丁烷的烷基化反应,主要是在酸催化剂的作用下,二者通过中间反应生成汽油馏分的过程。
C4馏分与脱异丁烷塔来的循环异丁烷混合经换冷至11℃,经脱水器脱除游离水(10ppm)后与闪蒸罐来的循环冷剂直接混合,温降至3℃分两路进入烷基化反应器。反应完全的酸-烃乳化液经一上升管直接进入酸沉降器,分出的酸液循下降管返回反应器重新使用,90%浓度废酸排至废酸脱烃罐,从酸沉降器分出的烃相流经反应器内的取热管束部分汽化,汽-液混合物进入闪蒸罐。净反应流出物经泵抽出经换热、加热至约31℃去流出物精制和产品分பைடு நூலகம்部分继续处理。循环冷剂经泵抽出送至反应进料线与原料C4直接混合,从闪蒸罐气相空间出来的烃类气体至制冷压缩机。
- 1、下载文档前请自行甄别文档内容的完整性,平台不提供额外的编辑、内容补充、找答案等附加服务。
- 2、"仅部分预览"的文档,不可在线预览部分如存在完整性等问题,可反馈申请退款(可完整预览的文档不适用该条件!)。
- 3、如文档侵犯您的权益,请联系客服反馈,我们会尽快为您处理(人工客服工作时间:9:00-18:30)。
Lummu公司烷基化工艺
烷基化装置是以液化气中的烯烃及异丁烷为原料,在催化剂的作用下烯烃与异丁烷反应,生成烷基化油的气体加工装置。
原料加氢精制的目的是通过加氢脱除原料中的丁二烯。
因为丁二烯是烷基化反应中主要的有害杂质,在烷基化反应过程中,丁二烯会生成多支链的聚合物,使烷基化油干点升高,酸耗加大。
脱除原料中的丁二烯采用选择性加氢技术,该技术已在国内多套烷基化装置上应用,为国内成熟技术。
由于气分装置所提供的未反应碳四馏分中烷烯比不足,需补充部分异丁烷,因此引入部分MEK装置混合丁烷及部分混合碳四,进行选择性加氢,加氢后的碳四馏分混合进入分馏塔,分离出满足烷基化要求的碳四馏分。
以液体酸为催化剂的烷基化工艺可分为硫酸烷基化和氢氟酸烷基化,两种工艺都为成熟的技术,在国内外都有广泛应用。
本装置采用的是LUMMUS公司的硫酸烷基化工艺,该技术具有如下特点:
1)CDALKY低温硫酸法烷基化在-4℃操作,低温操作可以比在传统烷基化工艺更低的烷烯比(I:O)下操作,脱异丁烷塔再沸器的能耗会显著地降低。
采用反应流出物自致冷工艺:利用反应流出物中的液相丙烷和丁烷在反应器中填料段减压闪蒸,吸收烷基化反应放出的热量。
反应流出物经过气液分离后,气相重新经压缩机压缩、冷凝,抽出部分丙烷后,再循环回反应器。
流出物自致冷工艺可使得反应器内保持高的异丁烷浓度,而从脱异丁烷塔来的循环异丁烷量最低。
2)与传统硫酸法烷基化相比,CDALKY低温硫酸法烷基化工艺采用两台专用立式的、可放大的反应器即可生产60万吨烷基化油,立式反应器通过去除机械搅拌设施和反应器流出物的后处理,大大提高了装置的在线率和可靠性。
反应器不采用机械搅拌,摆脱了低温下酸乳液粘度高的限制,因此,可在-4℃下操作,CDALKY的低温操作抑制了副反应,提高了C8选择性,使得最终产品辛烷值更高、更优质。
3)反应流出物不采用浓酸洗、碱水洗工艺:CDALKY工艺反应流出物处理段由一级聚结器、二级聚结器和补充聚结器组成,HC聚结器和LC聚结器分别配有各自的聚结系统。
不需要碱水洗涤系统(设备和相应的罐、泵和混合器都不需要了)。
4)本工艺采用脱异丁烷塔和脱正丁烷塔双塔分馏流程来分离烷基化油、异丁烷和正丁烷。
异丁烷返回反应器,由于不需要碱水对反应流出物进行洗涤,因此,CDALKY整个分馏段是干式的。
没有水存在,腐蚀基本被杜绝,从而显著地减少设备维修费用、减少了计划外停车几率。
5)CDALKY反应器的台数减少使得占地面积远小于使用多台卧式反应器传统硫酸法烷基化装置,占地面积小势必意味着配管、管廊等基建费用的减少。