催化裂化汽油在催化剂上裂化生焦的研究
催化裂化汽油催化裂解及两段催化裂化动力学模型研究的开题报告
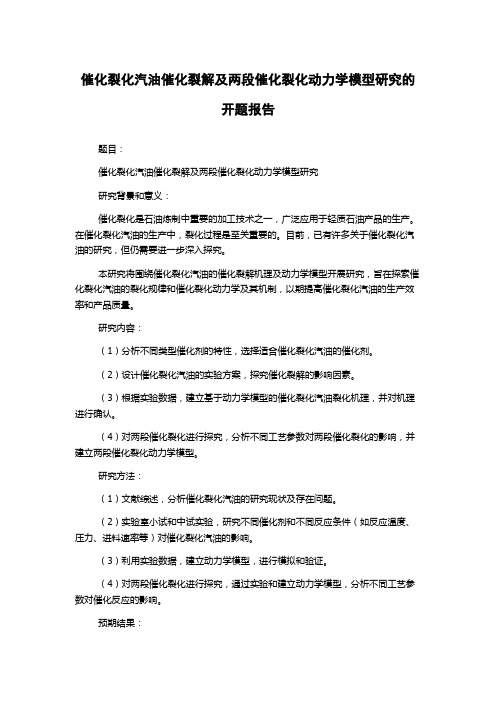
催化裂化汽油催化裂解及两段催化裂化动力学模型研究的开题报告题目:催化裂化汽油催化裂解及两段催化裂化动力学模型研究研究背景和意义:催化裂化是石油炼制中重要的加工技术之一,广泛应用于轻质石油产品的生产。
在催化裂化汽油的生产中,裂化过程是至关重要的。
目前,已有许多关于催化裂化汽油的研究,但仍需要进一步深入探究。
本研究将围绕催化裂化汽油的催化裂解机理及动力学模型开展研究,旨在探索催化裂化汽油的裂化规律和催化裂化动力学及其机制,以期提高催化裂化汽油的生产效率和产品质量。
研究内容:(1)分析不同类型催化剂的特性,选择适合催化裂化汽油的催化剂。
(2)设计催化裂化汽油的实验方案,探究催化裂解的影响因素。
(3)根据实验数据,建立基于动力学模型的催化裂化汽油裂化机理,并对机理进行确认。
(4)对两段催化裂化进行探究,分析不同工艺参数对两段催化裂化的影响,并建立两段催化裂化动力学模型。
研究方法:(1)文献综述,分析催化裂化汽油的研究现状及存在问题。
(2)实验室小试和中试实验,研究不同催化剂和不同反应条件(如反应温度、压力、进料速率等)对催化裂化汽油的影响。
(3)利用实验数据,建立动力学模型,进行模拟和验证。
(4)对两段催化裂化进行探究,通过实验和建立动力学模型,分析不同工艺参数对催化反应的影响。
预期结果:(1)确定适合催化裂化汽油的催化剂类型和工艺条件,为催化裂化汽油的生产提供科学依据。
(2)建立基于动力学模型的催化裂化汽油裂化机理,并对机理进行确认,为理解催化裂化汽油的裂化规律和机制提供科学依据。
(3)建立两段催化裂化动力学模型,有助于优化催化裂化汽油的生产工艺,提高产品质量和生产效率。
研究目标:在分析催化裂化汽油催化裂解的基础上,建立两段催化裂化汽油动力学模型,探究不同工艺参数对裂化汽油的影响,提高催化裂化汽油的生产效率和产品质量。
催化裂化油浆系统结焦原因及对策
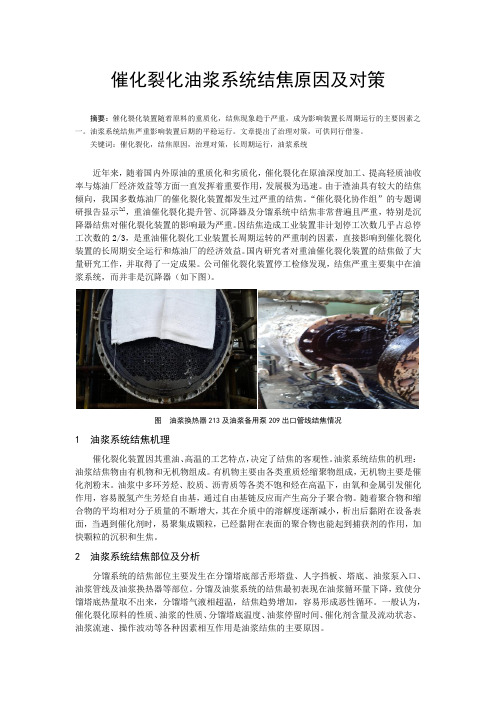
催化裂化油浆系统结焦原因及对策摘要:催化裂化装置随着原料的重质化,结焦现象趋于严重,成为影响装置长周期运行的主要因素之一。
油浆系统结焦严重影响装置后期的平稳运行。
文章提出了治理对策,可供同行借鉴。
关键词:催化裂化,结焦原因,治理对策,长周期运行,油浆系统近年来,随着国内外原油的重质化和劣质化,催化裂化在原油深度加工、提高轻质油收率与炼油厂经济效益等方面一直发挥着重要作用,发展极为迅速。
由于渣油具有较大的结焦倾向,我国多数炼油厂的催化裂化装置都发生过严重的结焦。
“催化裂化协作组”的专题调研报告显示[1],重油催化裂化提升管、沉降器及分馏系统中结焦非常普遍且严重,特别是沉降器结焦对催化裂化装置的影响最为严重。
因结焦造成工业装置非计划停工次数几乎占总停工次数的2/3,是重油催化裂化工业装置长周期运转的严重制约因素,直接影响到催化裂化装置的长周期安全运行和炼油厂的经济效益。
国内研究者对重油催化裂化装置的结焦做了大量研究工作,并取得了一定成果。
公司催化裂化装置停工检修发现,结焦严重主要集中在油浆系统,而并非是沉降器(如下图)。
图油浆换热器213及油浆备用泵209出口管线结焦情况1 油浆系统结焦机理催化裂化装置因其重油、高温的工艺特点,决定了结焦的客观性。
油浆系统结焦的机理:油浆结焦物由有机物和无机物组成。
有机物主要由各类重质烃缩聚物组成,无机物主要是催化剂粉末。
油浆中多环芳烃、胶质、沥青质等各类不饱和烃在高温下,由氧和金属引发催化作用,容易脱氢产生芳烃自由基,通过自由基链反应而产生高分子聚合物。
随着聚合物和缩合物的平均相对分子质量的不断增大,其在介质中的溶解度逐渐减小,析出后黏附在设备表面,当遇到催化剂时,易聚集成颗粒,已经黏附在表面的聚合物也能起到捕获剂的作用,加快颗粒的沉积和生焦。
2 油浆系统结焦部位及分析分馏系统的结焦部位主要发生在分馏塔底部舌形塔盘、人字挡板、塔底、油浆泵入口、油浆管线及油浆换热器等部位。
催化裂化油浆结焦原因及对策

催化裂化油浆结焦原因及对策标签:催化裂化;油浆结焦;解决对策在我国炼油厂的催化裂化过程当中,油浆系统当中产生的结焦结垢问题直接影响到了催化裂化设备的正常工作,主要是因为产生大量的结焦结垢物质,直接降低了热换器的热转化效率,同时提高了管道当中材料输送的阻力,进而造成了蜡油渣油的热转换效率降低。
系统内部产生的蒸汽量减少,同时整个反应设备在工作过程当中的能源消耗量加大,油浆当中多余的热量无法及时被排除,进而造成了整个反应系统内部的热平衡性下降,严重的情况下还直接造成油浆输送系统堵塞,进而影响到了整个生产过程的正常进行。
在最近几年发展过程当中,我国炼油厂的催化裂化原材料质量都不是非常理想,外加上在加油的催化裂化技术方面一直是难以攻克的难题。
因此,催化裂化油浆结焦和结垢的问题受到了各大化工企业的广泛关注,必须要采取相应的解决措施来解决这一问题。
1.催化裂化油浆结焦问题分析1.1温度问题的影响从催化裂化的整个反应过程中可以看出,该反应过程中会受到温度的影响,在相同的催化设备当中分馏塔的底部温度越高,那么出现的结焦现象就越明显。
针对己经产生结焦问题来讲,随着温度不断提高整个反应过程的结焦问题就更加明显,就在模拟FCC油浆的结焦单元当中所得出的结论非常明显。
1.2氧含量的影响通过模拟实验分析了FCC油浆当中产生结焦单元的具体原因,通过向试管当中通入一定量的空气或者是氧气,可以看出在不同量的空气和氧气掺入的情况下,对结焦问题的影响比较明显,其中如果空气或者氧气的参与量较大,那么结焦的问题就越严重。
由此可以看出氧气含量的多少对结焦问题的影响非常明显。
1.3固体和电效应影响通过实际的生产过程可以看出,在催化裂化反应过程当中,如果增加油浆内部的沉降器和过滤器设备之后,在产生结焦和结垢的问题上有着明显的缓解。
因此,这一现象也可以得到充分的证明,从中可以得出催化裂化反应过程中油浆当中,所存在的固体杂质对结焦问题的影响比较明显。
催化裂化汽油加氢过程中结焦机理分析
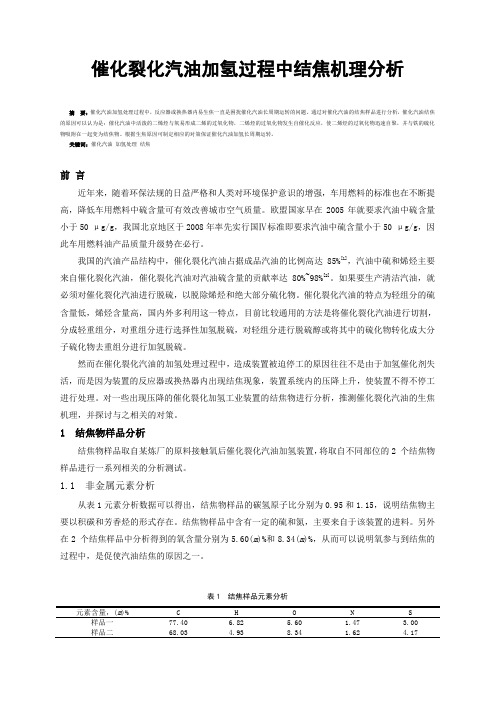
催化裂化汽油加氢过程中结焦机理分析摘要:催化汽油加氢处理过程中,反应器或换热器内易生焦一直是困扰催化汽油长周期运转的问题。
通过对催化汽油的结焦样品进行分析,催化汽油结焦的原因可以认为是:催化汽油中活泼的二烯烃与氧易形成二烯的过氧化物,二烯烃的过氧化物发生自催化反应,使二烯烃的过氧化物迅速自聚,并与铁的硫化物吸附在一起变为结焦物。
根据生焦原因可制定相应的对策保证催化汽油加氢长周期运转。
关键词:催化汽油加氢处理结焦前言近年来,随着环保法规的日益严格和人类对环境保护意识的增强,车用燃料的标准也在不断提高,降低车用燃料中硫含量可有效改善城市空气质量。
欧盟国家早在2005年就要求汽油中硫含量小于50 μg/g,我国北京地区于2008年率先实行国Ⅳ标准即要求汽油中硫含量小于50 μg/g,因此车用燃料油产品质量升级势在必行。
我国的汽油产品结构中,催化裂化汽油占据成品汽油的比例高达85%[1],汽油中硫和烯烃主要来自催化裂化汽油,催化裂化汽油对汽油硫含量的贡献率达80%~98%[2]。
如果要生产清洁汽油,就必须对催化裂化汽油进行脱硫,以脱除烯烃和绝大部分硫化物。
催化裂化汽油的特点为轻组分的硫含量低,烯烃含量高,国内外多利用这一特点,目前比较通用的方法是将催化裂化汽油进行切割,分成轻重组分,对重组分进行选择性加氢脱硫,对轻组分进行脱硫醇或将其中的硫化物转化成大分子硫化物去重组分进行加氢脱硫。
然而在催化裂化汽油的加氢处理过程中,造成装置被迫停工的原因往往不是由于加氢催化剂失活,而是因为装置的反应器或换热器内出现结焦现象,装置系统内的压降上升,使装置不得不停工进行处理。
对一些出现压降的催化裂化加氢工业装置的结焦物进行分析,推测催化裂化汽油的生焦机理,并探讨与之相关的对策。
1 结焦物样品分析结焦物样品取自某炼厂的原料接触氧后催化裂化汽油加氢装置,将取自不同部位的2 个结焦物样品进行一系列相关的分析测试。
1.1 非金属元素分析从表1元素分析数据可以得出,结焦物样品的碳氢原子比分别为0.95和1.15,说明结焦物主要以积碳和芳香烃的形式存在。
重油催化裂化结焦原因及改进措施

重油催化裂化结焦原因及改进措施重油催化裂化是润滑油加工工艺的一个重要环节,是提高润滑油的质量的关键技术。
在重油催化裂化过程中,结焦是一个常见的问题,会严重降低催化裂化的效率。
重油催化裂化结焦的原因,主要有三个方面:首先,催化剂受污染。
催化剂通常是复合物,容易受到空气、产品成分和其他物质的侵蚀、混入或碳化,受到污染时,催化剂性能会受到严重影响,从而导致结焦。
其次,催化剂不可逆变化。
重油催化裂化温度高,使重油催化剂发生不可逆变化,催化剂的性能也下降,从而导致结焦等问题。
最后,温度控制不当。
重油催化裂化的温度控制是很重要的,太高或太低的温度都会影响催化剂的功能,导致结焦。
为了解决重油催化裂化结焦问题,应采取一些有效的措施。
首先,科学选用催化剂。
重油催化裂化中使用的催化剂一般是催化剂复合物,应根据实际需要科学选择恰当的催化剂,降低催化剂受污染的可能性。
其次,采用稳定性好的催化剂。
重油催化裂化时,要选择温度稳定性较好的催化剂,不变性的催化剂能有效降低结焦的可能性。
再次,做好温度控制。
重油催化裂化时,温度应稳定在一定范围内,太高或太低的温度都会影响催化剂的功能,因此应做好温度控制,以保证重油催化裂化效果。
最后,改善反应条件和催化裂化技术。
采用新型催化剂和剂的组合,改善反应条件,控制反应温度和反应压力,改进催化裂化技术,进一步提高重油催化裂化的效率。
综上所述,重油催化裂化结焦的主要原因是催化剂受污染、催化剂不可逆变化以及温度控制不当。
要改善这种情况,应采取有效的措施,如科学选用催化剂、采用稳定性好的催化剂、做好温度控制、改善反应条件和催化裂化技术等。
只有真正落实这些措施,才能有效防止重油催化裂化结焦,达到质量理想。
催化裂化催化剂的研究与应用
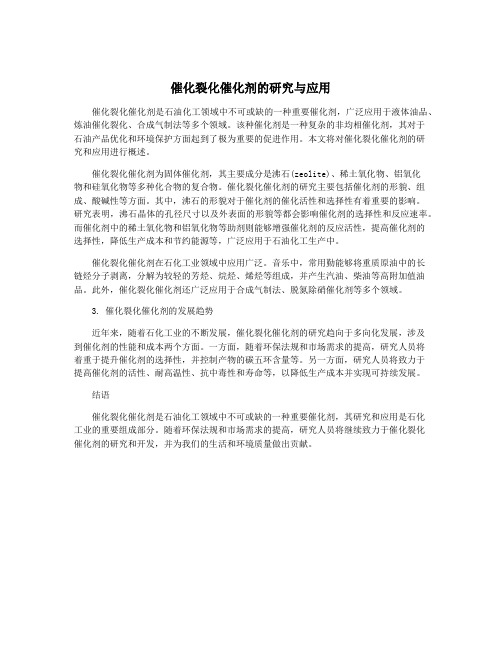
催化裂化催化剂的研究与应用催化裂化催化剂是石油化工领域中不可或缺的一种重要催化剂,广泛应用于液体油品、炼油催化裂化、合成气制法等多个领域。
该种催化剂是一种复杂的非均相催化剂,其对于石油产品优化和环境保护方面起到了极为重要的促进作用。
本文将对催化裂化催化剂的研究和应用进行概述。
催化裂化催化剂为固体催化剂,其主要成分是沸石(zeolite)、稀土氧化物、铝氧化物和硅氧化物等多种化合物的复合物。
催化裂化催化剂的研究主要包括催化剂的形貌、组成、酸碱性等方面。
其中,沸石的形貌对于催化剂的催化活性和选择性有着重要的影响。
研究表明,沸石晶体的孔径尺寸以及外表面的形貌等都会影响催化剂的选择性和反应速率。
而催化剂中的稀土氧化物和铝氧化物等助剂则能够增强催化剂的反应活性,提高催化剂的选择性,降低生产成本和节约能源等,广泛应用于石油化工生产中。
催化裂化催化剂在石化工业领域中应用广泛。
音乐中,常用勤能够将重质原油中的长链烃分子剥离,分解为较轻的芳烃、烷烃、烯烃等组成,并产生汽油、柴油等高附加值油品。
此外,催化裂化催化剂还广泛应用于合成气制法、脱氮除硝催化剂等多个领域。
3. 催化裂化催化剂的发展趋势近年来,随着石化工业的不断发展,催化裂化催化剂的研究趋向于多向化发展,涉及到催化剂的性能和成本两个方面。
一方面,随着环保法规和市场需求的提高,研究人员将着重于提升催化剂的选择性,并控制产物的碳五环含量等。
另一方面,研究人员将致力于提高催化剂的活性、耐高温性、抗中毒性和寿命等,以降低生产成本并实现可持续发展。
结语催化裂化催化剂是石油化工领域中不可或缺的一种重要催化剂,其研究和应用是石化工业的重要组成部分。
随着环保法规和市场需求的提高,研究人员将继续致力于催化裂化催化剂的研究和开发,并为我们的生活和环境质量做出贡献。
石油催化裂化

催化裂化催化剂的研究进展摘要:本文详细阐述了重油裂化催化剂、生产高辛烷值催化裂化催化剂、生产清洁燃料催化剂、增产低碳烯烃催化剂、多产液化气和柴油等催化剂的研究进展。
并对今后催化剂的发展方向进行了展望,今后催化裂化催化剂仍然是重油高效转化、增产丙烯、高温化学改性、降低汽油烯烃含量和高固含量成胶技术的方向发展。
关键词:催化裂化催化剂;研究进展;发展方向引言石油炼制的发展在很大程度上依赖于催化剂的发展,在炼油生产过程中,催化裂化装置用于将重油转化为汽油、柴油和轻气体组分,是当今炼油厂催化剂消耗量最大的炼油工艺。
国产汽油的调和组分中70%以上是催化裂化汽油,而柴油调和组分中40%来自催化裂化。
当代催化裂化面临着原料重质化,且环保方面对产品质量要求越来越严格,这对汽油的烯烃含量、芳烃含量、硫含量和氧含量提出了更高的要求。
催化剂配方一方面可根据已有的认识进行科学设计,另一面还要开发催化剂新材料和新配方。
1 催化裂化催化剂的研究现状1.1 重油催化裂化催化剂重油中含有较多的重馏分,原料分子大,在正常裂化条件下难于气化。
且还有较多的重金属和碱土金属元素,包括Fe、Ni、Cu、V、Na、Ca、Mg等,这些杂质会使催化剂中毒,导致催化剂的活性和选择性降低。
此外,重油中还有杂环化合物、胶质和沥青质,硫和氮含量较高,残炭高,碳氢比高[1]。
针对这些特点,催化剂研究者从重油裂化能力、焦炭选择性、抗重金属污染性能、抗碱氮性能方面设计重油裂化催化剂。
此外,现代重油裂化催化剂也已发展为较复杂的多功能组分的复合物。
如Grace Davison公司组合了突出的钒捕集能力、沸石分子筛良好的稳定性和基质对金属优异的钝化能力等技术,推出了新型渣油催化裂化催化剂IMPACT家族技术。
此催化剂具有良好的焦炭选择性,可改进渣油裂化,焦炭选择性提高近30%,对钒的允许度也高于常规催化剂[2]。
我国近几年开发的重油转化催化剂有北京石油化工科学研究院的Orbit系列、MLC系列及兰州石化公司开发的LB-5,这些催化剂都具有较强的重油转换能力及抗重金属污染能力。
催化裂化装置生焦量大的主要因素及措施

69能源环保与安全一、原因分析扬子石化2.0Mt/a催化裂化装置由4月初240 t/h下降至目前225t/h左右(5月6日上午约为235t/h),造成装置负荷下降的主要原因是生焦量大,再生烧焦负荷超高致使烟机入口温度达到698℃控制指标。
(再生器烧焦负荷一直处于满负荷状态,烧焦量约为22t/h。
)⑴原料影响。
原料油中残碳和胶质含量一直处于较高水平,胶质约为13%远高于设计值≤8.4%;另外700℃馏出量含量较低,对于目前反应温度(527℃),喷嘴进料处汽化温度约在585℃,原料油700℃以上组分难以汽化,加上此部分“重组分”多为大分子稠环芳烃附着在催化剂表面,造成装置生焦量较大。
此外,在原料本身氢含量不足12.3%的基础上,原料中重金属造成严重脱氢反应,直接表现为干气中氢含量达到43%(v),氢组分的损失直接造成生焦量增加。
若将干气中氢含量由45%(v)降至35%(v),则可以降低由于脱氢缩合生成的焦炭3.94t。
⑵终止剂量。
目前沉降器顶温度有缓慢下降趋势,由4月初496℃下降至目前490℃,因此稍微降低了终止剂量注入量。
从图1可以看出,终止剂量由10t/h下降至目前7t/h,延长了二反停留时间,造成生焦量有所上升。
⑶氢转移能力。
从油浆性质可以看出,其密度及残碳自4月份以来达到最高点,表明反应深度较高,一般油浆密度不超过1125kg/m3为宜。
过大的反应深度在二反停留时间过长的情况下必然造成氢转移过剩。
催化裂化装置生焦量大的主要因素及措施周校蕾 中国石化扬子石油化工有限公司炼油厂【摘 要】分析了扬子石化2.0Mt/a催化裂化装置生焦量大的原因,并提出优化改进措施。
【关键词】生焦量;原料性质;氢转移能力;终止剂量;剂油比(4)一般认为,剂油比提高,生焦量会上升。
主要是剂油比提高后,增加了反应时问,提高转化率,提高了焦炭产率,循环催化剂夹带的可汽提焦量升高,导致总焦量增加。
但在实际操作中,在一定范围内提高剂油比,总产焦且并无增加。
催化裂化增产汽油的分析与探讨

催化裂化增产汽油的分析与探讨摘要:随着经济的快速发展,汽油的消耗量大幅度增加,为了提高汽油的产量,降低汽油供应的巨大压力,优化加工流程对提高汽油产量具有十分重要的意义。
本文主要从催化裂化增产汽油的潜力入手,从四个方面对影响催化裂化汽油产率的因素进行分析,即原料油的性质、催化剂性质、反应温度以及原料油的预热温度。
关键词:催化裂化汽油分析随着我国经济的迅速发展,汽车数量的日益增加,汽油的消耗量也承受着前所未有的压力。
企业为了增加汽油的产量,一般采用催化裂化技术,一些企业还采用短流程的加工方法,直接把催化裂化汽油当做商品油有进行出厂,取得了特别好的经济效益。
这种短流程的加工方法,以催化装置为核心,也成为了炼油企业的重要加工流程。
经济的发展使人们的综合素质大幅度提高,人们开始注重自身的生活环境,环保意识增强。
人们对于汽车尾气的排放问题、汽油中硫的含量问题日益关注,这也使汽油质量新标准顺利得到实施,新汽油标准不仅对于汽油中硫含量进行了严格的控制,而且对车用汽油中苯含量和芳烃以及烯烃也提出了更合适的量化质量指标,这就降低了汽油池中催化裂化汽油的比例。
在巨大的市场需求的条件下,我国对催化裂化技术进行了探索和研究,对于改变产品结构来提高汽油产率,降低汽油供应的巨大压力具有十分重要的意义。
一、催化裂化增产汽油的潜力中国的催化裂化装置与国外相比具有很大的差距,根据调查数据,可以看出中国催化裂化增产汽油还具有十分大的发展空间。
2008年的调查数据显示,中国50套催化裂化装置平均产率只有39%,而欧美国家和亚洲的一些发达国家的催化裂化汽油产率的平均水平已经超过了45%,而中国超过45%的仅仅只有几套。
数据显示中国最高的催化裂化产率为48%,而欧美国家为57%,欧美国家的催化裂化汽油产率远高于中国。
因此,可以看出,中国的催化裂化装置相对于欧美其他国家来说,相对落后,国家要重视催化裂化技术的研究开发,提高汽油产率,缩小与欧美国家的差距,发挥巨大的发展空间。
重油MIP催化裂化反应系统结焦原因与防焦措施探讨

图 2 沉降器内的结焦状况
2. 5 CSC 粗旋内壁
CSC 内壁生成了一层类似于保护膜的硬焦,并有明显的“冲 刷”痕迹。这种焦非常坚硬,一般不易脱落,且达到一定厚度后 冲刷与结焦速度 达 到 平 衡,不 会 继 续 增 长。在 正 常 平 稳 生 产 过 程中不会造成危害,但是由于 CSC 设计的小环蒸汽出口设计在 旋分下料锥形段 内 壁 上,结 焦 使 小 环 蒸 汽 出 口 分 布 板 上 的 孔 几 乎完全堵死,影响了 CSC 的汽提分离效果。要防止小环蒸汽进 入升气管的分布板不被结焦堵塞,一定要注意保证 CSC 小环蒸 汽的畅通及一定的流量。
Key words: MIP; FCC; coking; countermeasures
焦炭作为催化裂 化 反 应 产 物 之 一,在 催 化 剂 上 生 焦 是 必 然 的,正常的生焦 是 两 器 热 平 衡 的 热 量 保 证。但 是 在 反 应 器 壁 等 位置上结焦却会 给 带 装 置 的 平 稳 运 行 带 来 极 大 的 安 全 隐 患,据 报道,每年都有大量的催化装置因结焦问题而非计划停工,给生 产带来极大的经济损失[1]。
2. 6 单旋的料腿
清焦前发现六个单旋的料腿有 4 个几乎结焦堵死,其余 2 个下料孔径也已 缩 得 很 小。从 现 场 割 下 来 的 料 内 的 焦 料 看,主 要成粒状物粘附在内壁。这种情况主要是由于绝大部分的催化 剂与油气在 CSC 粗旋中得到了较高的分离,在单旋中只有少量 的催化剂与大量的油气,因此,下料腿得不到很好的“冲刷”,同 时由于温差与温降,此时温度大约在 480 ~ 510 ℃ 。在此温度 下,烃类以热裂化反应为主,且热裂化反应速度较大。热裂化反 应产生不饱和的 热 裂 化 产 物 二 烯 烃,二 烯 烃 很 易 与 稠 环 芳 烃 聚
催化裂化催化剂的研究与应用

催化裂化催化剂的研究与应用催化裂化是石油加工中主要的重要工艺之一,利用催化剂使长链烯烃在适当的压力和温度条件下发生裂化反应,生成短链烯烃和芳烃。
催化裂化催化剂的研究与应用是提高催化裂化转化率和选择性,改善催化裂化产品质量的关键。
催化裂化催化剂的研究主要集中在两个方面:一是提高裂化活性和选择性;二是提高催化剂的稳定性和寿命。
为了提高催化剂的裂化活性和选择性,研究人员主要从以下几个方面进行优化。
首先是调节催化剂的酸碱性质。
催化裂化反应是一个酸碱催化反应,催化剂表面的酸碱性质直接影响反应速率和选择性。
通过改变催化剂组分、载体、孔结构和酸碱度等方法来调节催化剂的酸碱性质,可以有效提高催化裂化反应的效果。
其次是设计合适的催化剂孔道结构。
催化剂的孔道结构直接影响反应物分子在催化剂内的扩散和反应活性中心的利用率。
通过合理设计催化剂孔道结构,可以增加反应物分子在催化剂内的停留时间,提高反应活性中心的利用率,从而提高催化裂化反应的转化率和选择性。
研究人员还从催化剂组分、活性中心、金属添加剂等方面入手进行改进,进一步提高催化裂化反应的效果。
催化裂化催化剂的研究与应用在石油加工中具有重要的意义。
一方面,催化裂化技术可以提高原油转化率,降低原油中硫、氮等有害元素的含量,提高产品质量和附加值,降低环境污染。
催化裂化催化剂的研究与应用可以为石油工业提供更高效、更环保的生产工艺,促进石油工业的可持续发展。
催化裂化催化剂的研究与应用是提高石油加工效率和产品质量的重要手段。
通过优化催化剂的裂化活性、选择性、稳定性和寿命等方面,可以提高催化裂化反应的效果,实现石油加工的可持续发展。
催化裂化汽油催化裂解反应规律研究的开题报告
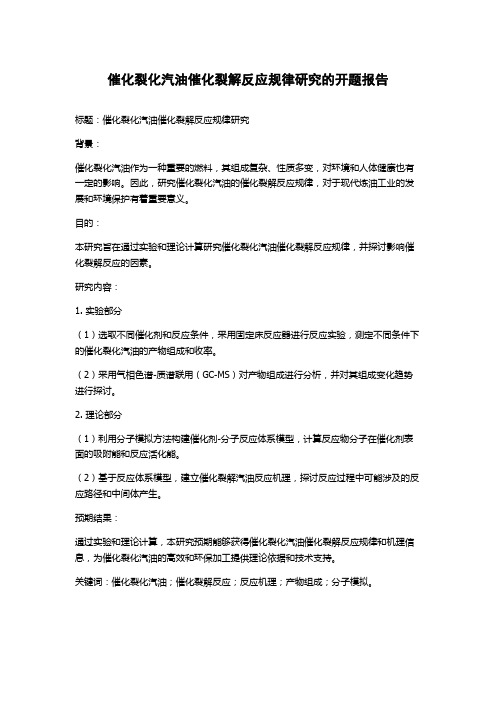
催化裂化汽油催化裂解反应规律研究的开题报告
标题:催化裂化汽油催化裂解反应规律研究
背景:
催化裂化汽油作为一种重要的燃料,其组成复杂、性质多变,对环境和人体健康也有一定的影响。
因此,研究催化裂化汽油的催化裂解反应规律,对于现代炼油工业的发展和环境保护有着重要意义。
目的:
本研究旨在通过实验和理论计算研究催化裂化汽油催化裂解反应规律,并探讨影响催化裂解反应的因素。
研究内容:
1. 实验部分
(1)选取不同催化剂和反应条件,采用固定床反应器进行反应实验,测定不同条件下的催化裂化汽油的产物组成和收率。
(2)采用气相色谱-质谱联用(GC-MS)对产物组成进行分析,并对其组成变化趋势进行探讨。
2. 理论部分
(1)利用分子模拟方法构建催化剂-分子反应体系模型,计算反应物分子在催化剂表面的吸附能和反应活化能。
(2)基于反应体系模型,建立催化裂解汽油反应机理,探讨反应过程中可能涉及的反应路径和中间体产生。
预期结果:
通过实验和理论计算,本研究预期能够获得催化裂化汽油催化裂解反应规律和机理信息,为催化裂化汽油的高效和环保加工提供理论依据和技术支持。
关键词:催化裂化汽油;催化裂解反应;反应机理;产物组成;分子模拟。
催化裂解待生催化剂上焦炭的构成研究
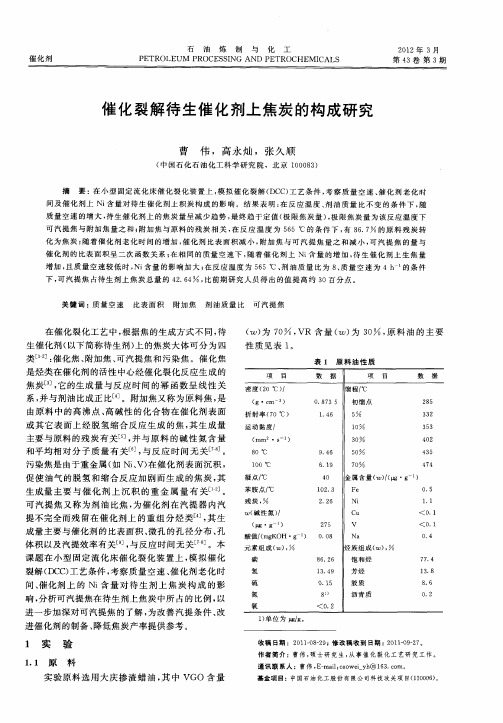
氮
氧
8) 1
< 02 .
沥青 质
02 .
进催 化剂 的制备 、 降低 焦炭产率 提供参考 。
1 单 位 为 / 。 ) g
1 实 验
1 I 原 料 .
收稿 日期 :2 1 -82 ;修 改 稿 收 到 日期 : 0 10 —7 0 10—9 2 1—92 。
作 者 简 介 :曹伟 , 士 研 究 生 , 事催 化 裂量 空 速 比表 面 积 附 加 焦 剂 油 质 量 比 可 汽 提 焦 质
在催化 裂化工艺 中 , 根据焦 的生成方式不 同, 待
( 为 7 % , R 含 量 ( 为 3 , 料 油 的 主 要 叫) O V 叫) O 原 性 质 见 表 1 。
表 I 原 料 油 性质
摘
要 : 小 型 固定 流 化 床 催 化 裂 化 装 置 上 , 拟 催 化 裂 解 ( C ) 艺 条 件 , 察 质 量 空 速 、 化 剂 老 化 时 在 模 D C工 考 催
间及 催 化 剂上 Ni 量 对 待 生 催 化 剂 上 积 炭 构 成 的 影 响 。结 果 表 明 : 反 应 温 度 、 油 质 量 比不 变 的 条 件 下 , 含 在 剂 随 质 量 空 速 的增 大 , 生 催 化 剂 上 的焦 炭 量 呈 减 少 趋 势 , 终 趋 于定 值 ( 限 焦 炭 量 ) 极 限 焦 炭 量 为 该 反 应 温 度 下 待 最 极 , 可 汽 提 焦 与 附加 焦 量之 和 ; 加 焦 与 原 料 的残 炭 相 关 , 反 应 温 度 为 5 5℃ 的 条 件 下 , 8. 的 原 料 残 炭 转 附 在 6 有 67 化 为 焦 炭 ; 着催 化 剂 老 化 时 间 的 增 加 , 化 剂 比表 面 积 减 小 , 随 催 附加 焦 与 可 汽 提 焦 量 之 和 减 小 , 汽 提 焦 的量 与 可 催 化 剂 的 比表 面 积 呈 二 次 函数 关 系 ; 相 同 的质 量 空 速 下 , 着催 化 剂 上 Ni 量 的 增 加 , 生 催 化 剂 上 生 焦 量 在 随 含 待 增 加 , 质 量 空速 较低 时 , 含 量 的 影 响 加 大 ; 反 应 温度 为 5 5℃ 、 油 质 量 比为 8 质 量 空 速 为 4h 的条 件 且 Ni 在 6 剂 、 下 , 汽 提 焦 占待 生 剂 上 焦 炭 总 量 的 4 . 4 , 可 2 6 比前 期 研 究 人 员 得 出 的值 提 高 约 3 O百 分 点 。
重油催化裂化装置结焦原因分析及抑制措施

重油催化裂化装置结焦原因分析及抑制措施摘要:随着重油催化裂化装置的不断改造,结焦问题已经成为制约该装置长周期、安全、稳定运行的重要因素之一。
对于重油催化裂化装置结焦问题的研究,为提高该装置的工艺水平、保证装置长周期运行具有重要的意义。
本文在介绍我国重油催化裂化装置结焦情况及对其原因分析基础上,对结焦抑制技术进行了阐述,并结合实际情况提出了一些建议。
希望能够在今后重油催化裂化装置结焦抑制工作中有所帮助。
关键词:重油催化裂化;沉降器;雾化蒸汽;结焦;原因引言某企业制造的一种新型的重油催化裂化设备,是近年来投入应用的一种新型的设备,其设备的结构采用了同轴向的布局,整个设备的整体高约57 m,并采用了器内再生烧焦的形式。
由于旋风分离机的出风口没有横向隔断,所以沉淀机的上方通常都设置了防焦气。
该管道的总长度约为44米,并配有适当数量的喷头。
现实中在装置正常生产的时候,所产生的焦量一般是近10%的给料量。
在一定的条件下,由于各种因素的影响,可能会产生凝块,对设备造成极大危害。
一、我国重油催化裂化装置结焦情况我国重油催化裂化装置大多是在70年代开始设计,经过多年的生产运行,目前已有很多重油催化裂化装置采用了重叠式两段再生、蒸汽吹扫和回炼油抽提等工艺技术,但操作中不可避免的会出现结焦问题,结焦严重时可导致催化剂活性降低、装置停工、产品收率降低、产品质量下降、甚至产生恶性事故等,因此也成为影响催化裂化装置长周期运行的一个重要因素。
结焦对催化裂化装置的危害主要有以下几方面:一是再生操作中大量焦炭燃烧引起再生器温度超高从而使催化剂床层温度升高;二是使催化剂床层温度分布不均;三是容易造成碳堆积,若烧炭量小于积碳量,再生剂含碳量过高进入反应器后,反应原料不能充分反应从而使油气附着在催化剂表面造成恶性循环引发恶性事故;四是引起催化剂再生器结垢和堵塞;五是引起催化剂床层密度降低、减压塔压力升高,当减压塔压力升高到一定程度时,会导致减压塔顶出现积蜡现象,从而降低减压塔顶循环液中的回流比。
低生焦催化裂化技术
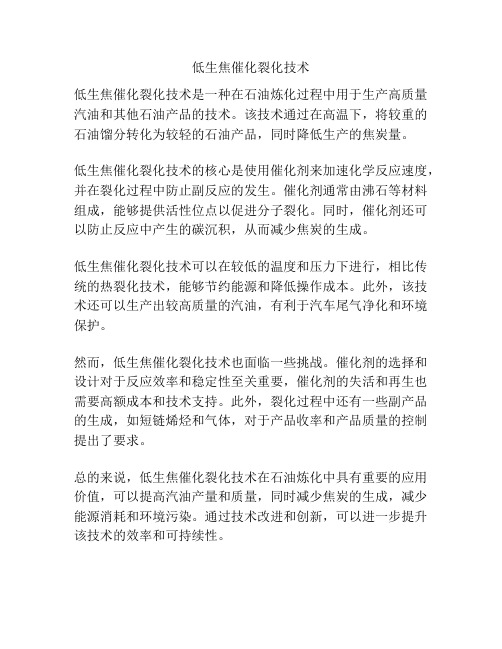
低生焦催化裂化技术
低生焦催化裂化技术是一种在石油炼化过程中用于生产高质量汽油和其他石油产品的技术。
该技术通过在高温下,将较重的石油馏分转化为较轻的石油产品,同时降低生产的焦炭量。
低生焦催化裂化技术的核心是使用催化剂来加速化学反应速度,并在裂化过程中防止副反应的发生。
催化剂通常由沸石等材料组成,能够提供活性位点以促进分子裂化。
同时,催化剂还可以防止反应中产生的碳沉积,从而减少焦炭的生成。
低生焦催化裂化技术可以在较低的温度和压力下进行,相比传统的热裂化技术,能够节约能源和降低操作成本。
此外,该技术还可以生产出较高质量的汽油,有利于汽车尾气净化和环境保护。
然而,低生焦催化裂化技术也面临一些挑战。
催化剂的选择和设计对于反应效率和稳定性至关重要,催化剂的失活和再生也需要高额成本和技术支持。
此外,裂化过程中还有一些副产品的生成,如短链烯烃和气体,对于产品收率和产品质量的控制提出了要求。
总的来说,低生焦催化裂化技术在石油炼化中具有重要的应用价值,可以提高汽油产量和质量,同时减少焦炭的生成,减少能源消耗和环境污染。
通过技术改进和创新,可以进一步提升该技术的效率和可持续性。
催化裂化装置结焦原因分析及对策研究
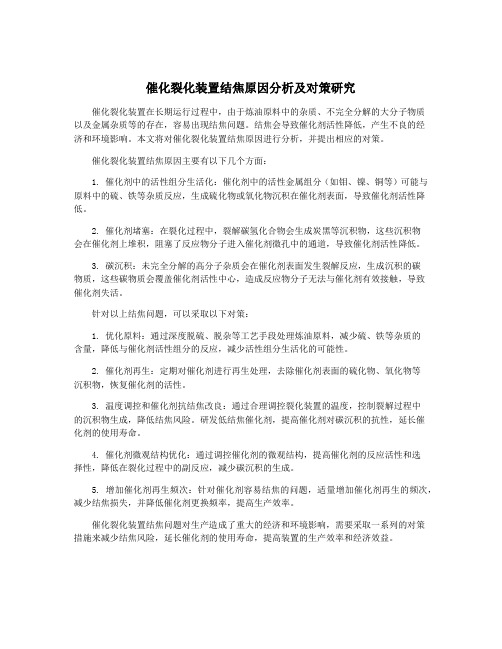
催化裂化装置结焦原因分析及对策研究催化裂化装置在长期运行过程中,由于炼油原料中的杂质、不完全分解的大分子物质以及金属杂质等的存在,容易出现结焦问题。
结焦会导致催化剂活性降低,产生不良的经济和环境影响。
本文将对催化裂化装置结焦原因进行分析,并提出相应的对策。
催化裂化装置结焦原因主要有以下几个方面:1. 催化剂中的活性组分生活化:催化剂中的活性金属组分(如钼、镍、铜等)可能与原料中的硫、铁等杂质反应,生成硫化物或氧化物沉积在催化剂表面,导致催化剂活性降低。
2. 催化剂堵塞:在裂化过程中,裂解碳氢化合物会生成炭黑等沉积物,这些沉积物会在催化剂上堆积,阻塞了反应物分子进入催化剂微孔中的通道,导致催化剂活性降低。
3. 碳沉积:未完全分解的高分子杂质会在催化剂表面发生裂解反应,生成沉积的碳物质,这些碳物质会覆盖催化剂活性中心,造成反应物分子无法与催化剂有效接触,导致催化剂失活。
针对以上结焦问题,可以采取以下对策:1. 优化原料:通过深度脱硫、脱杂等工艺手段处理炼油原料,减少硫、铁等杂质的含量,降低与催化剂活性组分的反应,减少活性组分生活化的可能性。
2. 催化剂再生:定期对催化剂进行再生处理,去除催化剂表面的硫化物、氧化物等沉积物,恢复催化剂的活性。
3. 温度调控和催化剂抗结焦改良:通过合理调控裂化装置的温度,控制裂解过程中的沉积物生成,降低结焦风险。
研发低结焦催化剂,提高催化剂对碳沉积的抗性,延长催化剂的使用寿命。
4. 催化剂微观结构优化:通过调控催化剂的微观结构,提高催化剂的反应活性和选择性,降低在裂化过程中的副反应,减少碳沉积的生成。
5. 增加催化剂再生频次:针对催化剂容易结焦的问题,适量增加催化剂再生的频次,减少结焦损失,并降低催化剂更换频率,提高生产效率。
催化裂化装置结焦问题对生产造成了重大的经济和环境影响,需要采取一系列的对策措施来减少结焦风险,延长催化剂的使用寿命,提高装置的生产效率和经济效益。
重油催化裂化结焦原因及改进措施

重油催化裂化结焦原因及改进措施重油催化裂化结焦,也被称为下游结焦,是指重油在催化裂化过程中的一种现象,它的出现会给裂化过程带来很多不便,使裂化效果受到一定的影响,因此重油催化裂化结焦的定量与质量是催化裂化产品质量的关键因素。
结焦的主要原因是催化剂不均匀的分布。
当反应催化剂在重油催化裂化剂中的分布不均匀时,部分反应区域的催化剂不足,从而导致反应产物积累,进而形成结焦物。
此外,反应条件不合理也是造成结焦的重要原因,包括反应温度过高或者反应温度不稳定,反应压力过高、反应压力不稳定,反应液体的层数、反应时间过长等等。
另外,重油催化裂化结焦还可能是由于原料重油中夹带的杂质或者水分、油类离子过高等原因造成的。
在重油中,各种杂质如烃、氧化物、含碳水等不易被催化裂化,如果温度和压力条件不合适,就可能形成结焦物。
另外,当重油中含碳水离子过高时,它们会结合形成结焦物,也会对裂化过程造成影响。
二、改进措施(1)优化催化剂的使用。
要想有效的解决重油催化裂化结焦的问题,首先要保证催化剂的分布均匀,可以采用多种方法,如加入悬浮剂等,以改善催化剂的可利用性,使催化剂均匀地分布在反应液中,从而提高反应效率。
(2)优化反应条件。
反应条件的优化是降低结焦率的重要措施。
反应温度和反应压力不能过高,应当根据重油类型和反应条件来选择合适的反应温度和反应压力,保证反应稳定。
另外,反应时间也不能过长,否则反应产物容易积累,形成结焦物。
(3)改善原料重油质量。
原料重油中存在的杂质和水分都会影响重油催化裂化的效果,要想获得较好的催化裂化效果,首先应该提高原料重油的质量,如选择质量较好的原料重油,做好原料重油的净化和精制等,以提高催化裂化效果。
三、结论重油催化裂化结焦是指重油在催化裂化过程中出现的现象,它的出现会给裂化过程带来一定的影响,常见的原因有:催化剂分布不均匀、反应条件不合理、原料重油中夹带的杂质或者水分、油类离子过高等。
改善重油催化裂化结焦的措施有:优化催化剂的使用、优化反应条件、改善原料重油质量等。
重油催化裂化反应工艺研究

重油催化裂化反应工艺研究摘要:近年来,随着我国社会技术的高速发展,我国在石油的炼油工业里也面临着对应的催化裂化的问题,而人们也在通过不断的研究和探索对相关技术进行革新和完善;此次就重油催化裂化反应工艺进行研究和分析。
关键词:炼油工业;重油催化裂化反应工艺;研究引言:在现实的炼油工业中,对重质原料进行加工的方式就包含催化裂化这一工艺技术。
而随着原油质量的增加和市场对相关轻质油现实需求的提高,如何对现有的重油进行高质量、高效率的轻原油产品生产和供货保障,也受到社会大众的关注。
而重油催化裂化工艺在一定程度上也是对重油轻质化的重要手段。
1、我国目前重油催化裂化工艺情况和问题当前,我国重油催化裂化生产能力已占全世界FCC生产能力的四分之一。
而我国在实现探索和应用的过程中,已具备100Mt/a以上的催化裂化加工能力。
同时,相关开展重油催化裂化的反应装置也有一百三十套左右,这里超过九成的对重油的渣油加工炼油从上世纪八十年代末的百分之十八到九十年代的百分之四十三左右。
在此之中,我国的技术研究人员也对现今的重油催化裂化工艺技术进行了相关的扩展。
文章在现实的工艺分析中,也是通过现实重油催化裂化反应工艺在依据我国石油化工科学研究院(RIPP)的相关研发技术进行以重质油为原料,利用现有的催化裂化装置在进行最小化的改造后,使其设备的运行能在日常使用的催化裂化装置中同时增加液化气和柴油的产量,同时大幅降低在实际石油炼化过程中烯烃含量的比例。
即在MGD工艺应用中,在增加液化气和柴油对应的应用占比百分点时,对其管反应器汽油反应区、重质油反应区、轻质油反应区和总反应深度控制区四个反应区进行实时的监控,也是有效提升工作效率的关键[1]。
但受到重油原料和常规进料性质的不同,这里主要有硫和氮等杂原子;钒、铁、铜等金属含量;胶质和沥青质含量及沸点组分成分超过现实的工艺指标标准,也是导致后期生产出来的轻质油无法达到出厂的数据指标。
而在现实进行重油催化裂化工艺的有效技术开展,也许从以上方面进行问题疑难的解决,即减少焦炭产出率和气体(如:氢气)的产出率;减少原料中重金属对催化剂的污染,也是保障出油产量和装置热平衡的正常运转前提。
催化剂组成及性能对焦化蜡油催化裂化影响的研究
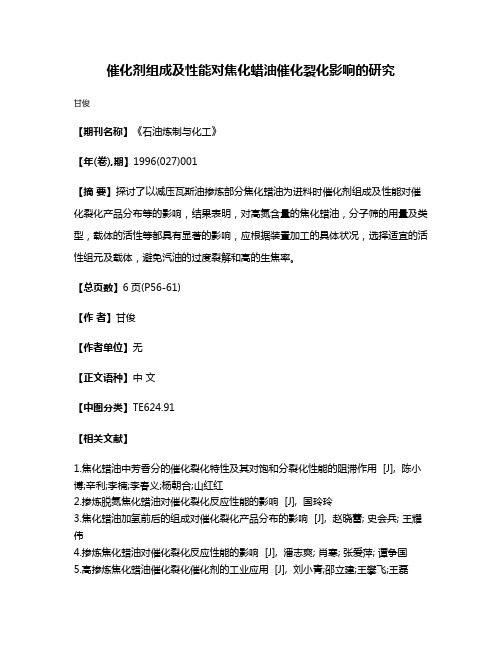
催化剂组成及性能对焦化蜡油催化裂化影响的研究
甘俊
【期刊名称】《石油炼制与化工》
【年(卷),期】1996(027)001
【摘要】探讨了以减压瓦斯油掺炼部分焦化蜡油为进料时催化剂组成及性能对催化裂化产品分布等的影响,结果表明,对高氮含量的焦化蜡油,分子筛的用量及类型,载体的活性等都具有显著的影响,应根据装置加工的具体状况,选择适宜的活性组元及载体,避免汽油的过度裂解和高的生焦率。
【总页数】6页(P56-61)
【作者】甘俊
【作者单位】无
【正文语种】中文
【中图分类】TE624.91
【相关文献】
1.焦化蜡油中芳香分的催化裂化特性及其对饱和分裂化性能的阻滞作用 [J], 陈小博;辛利;李楠;李春义;杨朝合;山红红
2.掺炼脱氮焦化蜡油对催化裂化反应性能的影响 [J], 国玲玲
3.焦化蜡油加氢前后的组成对催化裂化产品分布的影响 [J], 赵晓蕾; 史会兵; 王耀伟
4.掺炼焦化蜡油对催化裂化反应性能的影响 [J], 潘志爽; 肖寒; 张爱萍; 谭争国
5.高掺炼焦化蜡油催化裂化催化剂的工业应用 [J], 刘小青;邵立建;王攀飞;王磊
因版权原因,仅展示原文概要,查看原文内容请购买。