生产现场7大浪费、改善浪费的执行方法及改善实例
消除生产现场的七大浪费
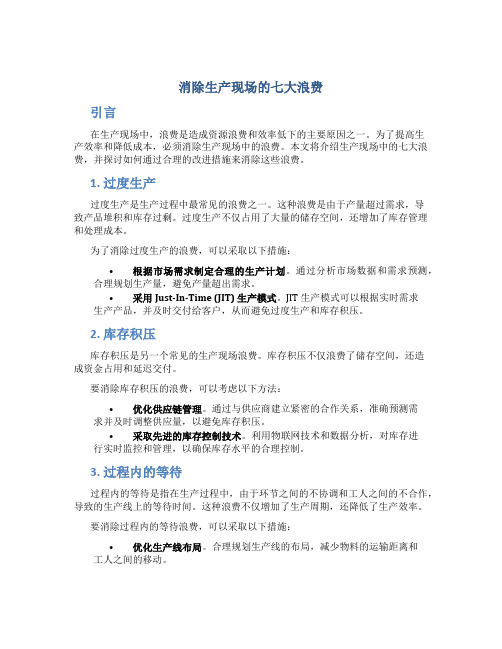
消除生产现场的七大浪费引言在生产现场中,浪费是造成资源浪费和效率低下的主要原因之一。
为了提高生产效率和降低成本,必须消除生产现场中的浪费。
本文将介绍生产现场中的七大浪费,并探讨如何通过合理的改进措施来消除这些浪费。
1. 过度生产过度生产是生产过程中最常见的浪费之一。
这种浪费是由于产量超过需求,导致产品堆积和库存过剩。
过度生产不仅占用了大量的储存空间,还增加了库存管理和处理成本。
为了消除过度生产的浪费,可以采取以下措施:•根据市场需求制定合理的生产计划。
通过分析市场数据和需求预测,合理规划生产量,避免产量超出需求。
•采用Just-In-Time (JIT) 生产模式。
JIT 生产模式可以根据实时需求生产产品,并及时交付给客户,从而避免过度生产和库存积压。
2. 库存积压库存积压是另一个常见的生产现场浪费。
库存积压不仅浪费了储存空间,还造成资金占用和延迟交付。
要消除库存积压的浪费,可以考虑以下方法:•优化供应链管理。
通过与供应商建立紧密的合作关系,准确预测需求并及时调整供应量,以避免库存积压。
•采取先进的库存控制技术。
利用物联网技术和数据分析,对库存进行实时监控和管理,以确保库存水平的合理控制。
3. 过程内的等待过程内的等待是指在生产过程中,由于环节之间的不协调和工人之间的不合作,导致的生产线上的等待时间。
这种浪费不仅增加了生产周期,还降低了生产效率。
要消除过程内的等待浪费,可以采取以下措施:•优化生产线布局。
合理规划生产线的布局,减少物料的运输距离和工人之间的移动。
•实施流程改进。
通过分析生产过程,找出瓶颈环节并进行优化,以减少等待时间。
4. 过度加工过度加工是指对产品进行不必要的加工或处理,从而浪费时间、能源和材料。
过度加工不仅增加了生产成本,还增加了生产周期。
要消除过度加工的浪费,可以考虑以下方法:•优化产品设计。
通过重新设计产品,减少不必要的加工步骤和材料使用量。
•改进工艺流程。
分析生产过程中的每个环节,找出可以简化和优化的步骤,以减少加工时间和浪费。
生产7大浪费及解决方案

生产7大浪费及解决方案大家好,今天我们聊聊生产过程中的那些浪费问题,嗯,是的,你没听错,就是浪费。
听到这个词,大家脑海里可能会浮现出各种奇怪的场景。
不过,别急着走神,我们要聊的是制造业中的浪费问题,这些浪费可是让企业流血的罪魁祸首哦。
咱们一块儿来看下去,如何搞定这些浪费,提升生产效率!1. 过多的库存1.1 库存的烦恼哎,说到库存,大家可能会觉得,哇,库存多点不是好事吗?其实不然。
库存积压就像是家里的旧物堆积,既占地方又浪费资源。
库存多了,产品可能过时,生产线也被拖慢,哎,这可真是让人头疼的事儿。
1.2 解决办法那咋办呢?第一步,咱们得搞清楚需求,精准预测,别买一堆又用不上的原材料。
还有,利用“刚性生产”这种方法,按需生产,减少库存积压,真的是“下手快,省得多”。
2. 生产过剩2.1 过剩的烦恼生产过剩嘛,就像是做饭时多煮了一大锅菜,结果吃不完,全都浪费了。
生产线上的东西做得太多,不但没卖出去,库存也得增加,造成不必要的浪费。
2.2 解决办法要解决这个问题,得合理规划生产计划。
可以采用“拉动式生产”,根据实际需求来调整生产节奏,不盲目追求产量,做到“生产有节奏,库存不超标”。
3. 过多的等待时间3.1 等待的煎熬生产过程中,机器闲置、员工等活儿等得不耐烦,这都是浪费时间的表现。
就像是排队等餐,一等就等个天荒地老,效率低得让人心烦。
3.2 解决办法要减少等待时间,就得提高生产线的流畅度。
可以引入“持续改进”的理念,优化生产流程,减少不必要的等待,让生产线像高速公路一样通畅无阻。
4. 不必要的搬运4.1 搬运的麻烦如果生产线上的东西被搬来搬去,就像是玩具被小孩乱丢乱放,费劲不说,还容易出错。
搬运不仅费时费力,还增加了损耗的风险。
4.2 解决办法减少搬运的办法就是优化工作环境,尽量把需要的工具和原材料都放在离工作位置较近的地方。
这样,就能减少不必要的搬运,真是“近水楼台先得月”了。
5. 过多的加工5.1 加工的困扰有些生产流程中,产品被多次加工,就像是在一块木板上反复雕刻,最后不仅时间耗费大,结果也未必好。
生产管理中的七大浪费

生产管理中的七大浪费引言在现代制造业中,高效的生产管理对于企业的竞争力至关重要。
然而,在生产过程中,存在着一些浪费现象,这些浪费会导致资源的过度消耗、时间的浪费以及产品质量的下降。
本文将介绍生产管理中的七大浪费,并提出相应的解决方案,以帮助企业提高生产效率和节约成本。
一、物料浪费物料浪费是指在生产过程中由于物料的错误使用或过度消耗导致的浪费现象。
常见的物料浪费包括过剩的原材料处理、废弃物料的处理以及物料的过度采购等。
这会增加企业的成本,降低生产效率。
解决方案:- 优化物料采购策略,减少过多采购 - 引入物料追溯系统,提高物料使用效率 - 建立合理的废料回收机制,减少废弃物料的处理成本二、人力浪费人力浪费是指在生产过程中由于人力资源的错误分配、人员培训不足或不适当的工作设计等原因导致的浪费现象。
常见的人力浪费包括员工重复劳动、不必要的等待时间以及过度的人员调动等。
这会导致生产成本的上升和生产效率的降低。
解决方案:- 合理分配人力资源,确保每个员工都能发挥其最大的价值 - 加强员工培训,提高员工的技能水平和工作效率 - 优化工艺流程,减少员工的等待时间和重复劳动三、时间浪费时间浪费是指在生产过程中由于工艺缺陷、设备故障或生产计划不合理等原因导致的时间的浪费现象。
常见的时间浪费包括设备停机时间、生产线调整时间以及生产计划变更所引起的时间延误等。
这会导致生产效率的降低和交货期的延迟。
解决方案:- 加强设备维护和保养,减少设备故障和停机时间 - 优化生产计划,避免频繁的调整和变更 - 优化工艺流程,减少生产线调整时间和产品切换时间四、能源浪费能源浪费是指在生产过程中由于能源的不合理使用或过度消耗导致的浪费现象。
常见的能源浪费包括未关闭的电器、过度的加热和制冷以及能源的无效利用等。
这会增加企业的能源成本和环境负担。
解决方案:- 加强能源管理,确保设备的合理使用和节能措施的实施 - 定期检查和维护设备,减少能源的损耗 - 优化生产工艺和设备设计,提高能源利用率五、运输浪费运输浪费是指在物料运输过程中由于不合理的运输方式或过长的运输距离导致的浪费现象。
产品工作过程中的七大浪费及其解决方案

产品工作过程中的七大浪费及其解决方案在产品开发过程中,存在着七大浪费,也称为“七大Muda”,这些浪费会导致时间、资源和成本的浪费。
了解这些浪费并采取相应的解决方案,可以帮助产品团队提高效率和质量。
1.过度生产过度生产指的是在没有需求的情况下,过早或生产过多的产品。
这会造成库存积压、资金占用和产品过期等问题。
解决方案是通过使用“精益生产”原则,只在有需求的情况下生产所需数量的产品。
2.运输浪费运输浪费包括不必要的物料运输和产品运输。
这会增加成本、延长交货时间,并增加货物损坏的风险。
解决方案是优化物料和产品运输的路径,减少运输距离和次数,并避免不必要的中间仓储。
3.等待浪费等待浪费指的是因为制造过程中的等待而导致的时间浪费。
这可能是由于缺乏前置物料、技术故障或生产线停机等原因引起的。
解决方案是通过优化供应链管理和生产计划来减少等待时间,并确保所需的物料和资源都及时准备就绪。
4.过度加工过度加工是指在产品制造过程中超出需求的额外工作量。
这可能是因为不明确的设计要求、复杂的工艺流程或繁琐的审批程序等原因。
解决方案是通过简化产品设计、优化工艺流程和减少不必要的审批程序来减少过度加工。
5.库存浪费库存浪费是指因过量的库存而造成的资金占用、过期、变质等问题。
这可能是由于过度生产、缺乏库存管理和控制、或供应链延迟等原因导致的。
解决方案是通过精细的库存管理和控制,采取准时交付和供应链协同等方法来减少库存浪费。
6.动作浪费动作浪费指的是在制造过程中没有价值的额外运动和步骤。
如多余的物料搬运、操作过程不流畅、等待签字批准等。
解决方案是通过优化工作站布局,提供合适的工具和设备,并对操作过程进行持续改进来减少动作浪费。
7.缺陷浪费缺陷浪费是指由于制造过程中的缺陷导致的废品、返工、售后客户投诉等问题。
这可能是由于原材料质量问题、工艺流程不稳定或操作不当等原因引起的。
解决方案是通过质量控制和过程改进来减少缺陷,并提高产品质量和客户满意度。
精益生产中的七大浪费及改善方法
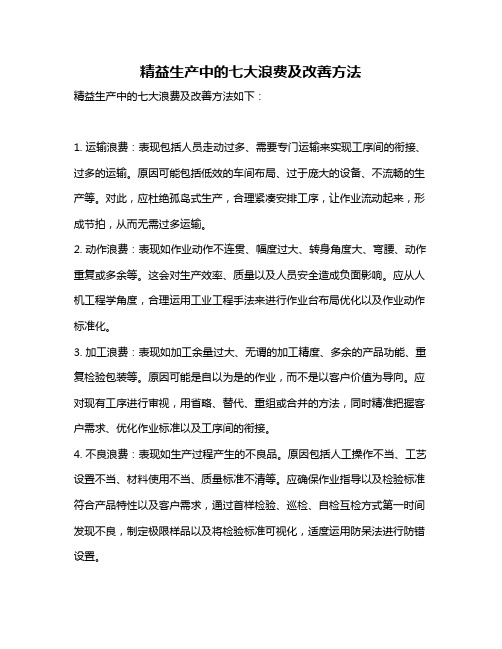
精益生产中的七大浪费及改善方法精益生产中的七大浪费及改善方法如下:1. 运输浪费:表现包括人员走动过多、需要专门运输来实现工序间的衔接、过多的运输。
原因可能包括低效的车间布局、过于庞大的设备、不流畅的生产等。
对此,应杜绝孤岛式生产,合理紧凑安排工序,让作业流动起来,形成节拍,从而无需过多运输。
2. 动作浪费:表现如作业动作不连贯、幅度过大、转身角度大、弯腰、动作重复或多余等。
这会对生产效率、质量以及人员安全造成负面影响。
应从人机工程学角度,合理运用工业工程手法来进行作业台布局优化以及作业动作标准化。
3. 加工浪费:表现如加工余量过大、无谓的加工精度、多余的产品功能、重复检验包装等。
原因可能是自以为是的作业,而不是以客户价值为导向。
应对现有工序进行审视,用省略、替代、重组或合并的方法,同时精准把握客户需求、优化作业标准以及工序间的衔接。
4. 不良浪费:表现如生产过程产生的不良品。
原因包括人工操作不当、工艺设置不当、材料使用不当、质量标准不清等。
应确保作业指导以及检验标准符合产品特性以及客户需求,通过首样检验、巡检、自检互检方式第一时间发现不良,制定极限样品以及将检验标准可视化,适度运用防呆法进行防错设置。
5. 等待浪费:表现如人员(以及设备)在等待,或者有时忙、有时闲的不均衡现象。
原因如生产线品种切换、工作量少、时常缺料、设备闲置等。
应实施生产均衡化,快速换模技术的运用,全员生产性防护,多技能工,消除不良浪费,提升供应商水准。
6. 过量生产:这是常被视为最大的浪费。
其结果导致库存、资金的占用以及潜在的报废风险。
应形成一个流、节拍化生产。
“一个流生产”是指从毛坯投入成品产出的整个制造加工过程,零件始终处于不停滞、不堆积、不超越的状态。
每道工序加工完一个制件后立即流到下一工序;工序间的在制品数量不超过前工序的装夹数量。
零件的运动不间断、不超越、不落地。
只有合格的产品才允许往下一道工序流。
节拍化生产要求是需求节拍与生产节拍平衡。
生产管理7大浪费
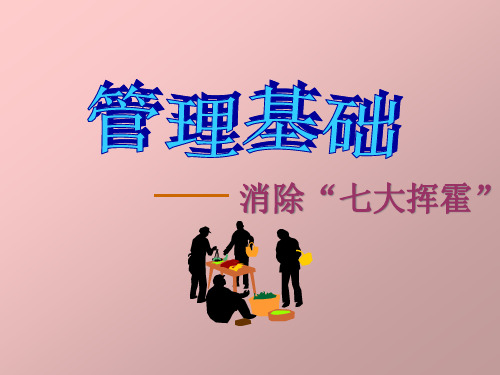
对策:
•库存意识旳改革 •U型设备配置 •均衡化生产 •生产流程调整顺畅 •看板管理旳落实 •迅速换线换模 •生产计划安排考虑库存 消化
注意:
•库存是万恶之源 •管理点数削减降低安全库存 •消除生产风险降低安全库存
6.动作旳挥霍
额外动作旳挥霍
不必要旳动作、无附加价值旳动作,及较慢旳动作
体现形式:
•工作时旳换手作业 •未倒角之产品造成不易装配旳挥霍 •小零件组合时,握持压住旳挥霍 •动作顺序不当造成动作反复旳挥霍 •寻找旳挥霍
•不良品存在库房内待修 •设备能力不足所造成旳安全库存 •换线时间太长造成次大批量生产旳挥霍 •采购过多旳物料变库存
库存是万恶旳根源
5.库存旳挥霍
过多旳库存会造成旳挥霍:
•产生不必要旳搬运、堆积、放置、找寻、防 护处理等挥霍旳动作 •使先进先出旳作业困难 •损败北息及管理费用 •物品之价值会减低,变成呆滞品 •占用厂房、造成多出旳工作场合、仓库建设 投资旳挥霍 •造成无形旳挥霍
无法确保可卖出旳产品做了太多
体现形式:
是挥霍旳源头
•物流阻塞 •库存、在制品增长 •产品积压造成不良发生 •资金回转率低 •材料、零件过早取得 •影响计划弹性及生产系统旳适应能力
适
时
J旳
I T
生
生 产
产
方
式
1.制造过多旳挥霍
制造过多是一种挥霍旳原因:
•只是提前用掉了费用(材料费、人工费)而已,并
无其他好处
对策:
•采用均衡化生产 •制品别配置—一种流生产 •防误措施 •自动化及设备保养加强 •实施目视管理 •加强进料控制
注意:
•自动化不要闲置人员 •供需及时化 •作管理点数削减
八大浪费与改善方法案例
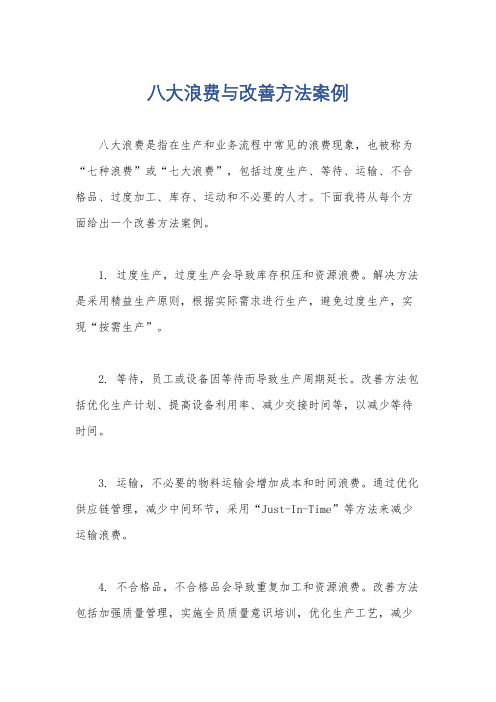
八大浪费与改善方法案例八大浪费是指在生产和业务流程中常见的浪费现象,也被称为“七种浪费”或“七大浪费”,包括过度生产、等待、运输、不合格品、过度加工、库存、运动和不必要的人才。
下面我将从每个方面给出一个改善方法案例。
1. 过度生产,过度生产会导致库存积压和资源浪费。
解决方法是采用精益生产原则,根据实际需求进行生产,避免过度生产,实现“按需生产”。
2. 等待,员工或设备因等待而导致生产周期延长。
改善方法包括优化生产计划、提高设备利用率、减少交接时间等,以减少等待时间。
3. 运输,不必要的物料运输会增加成本和时间浪费。
通过优化供应链管理,减少中间环节,采用“Just-In-Time”等方法来减少运输浪费。
4. 不合格品,不合格品会导致重复加工和资源浪费。
改善方法包括加强质量管理,实施全员质量意识培训,优化生产工艺,减少不合格品产生。
5. 过度加工,指超出产品要求的加工步骤,增加了成本和时间。
改善方法是重新评估生产流程,简化加工步骤,精简生产工艺。
6. 库存,过多的库存会增加资金占用和风险。
采用精益库存管理,通过精确预测和准确订单管理来降低库存水平,避免过多库存。
7. 运动,指员工不必要的移动或动作,增加了生产时间和疲劳。
改善方法包括优化工作站布局,减少不必要的移动,提高工作效率。
8. 不必要的人才,指员工的潜力未得到充分利用。
改善方法包括进行员工技能培训,激励员工提出改进建议,充分发挥员工的潜力。
通过以上改善方法案例,可以有效地减少八大浪费,提高生产效率,降低成本,增强企业竞争力。
同时,这些改善方法也体现了精益生产和持续改进的理念,对于企业的可持续发展具有重要意义。
生产过程中的七大浪费
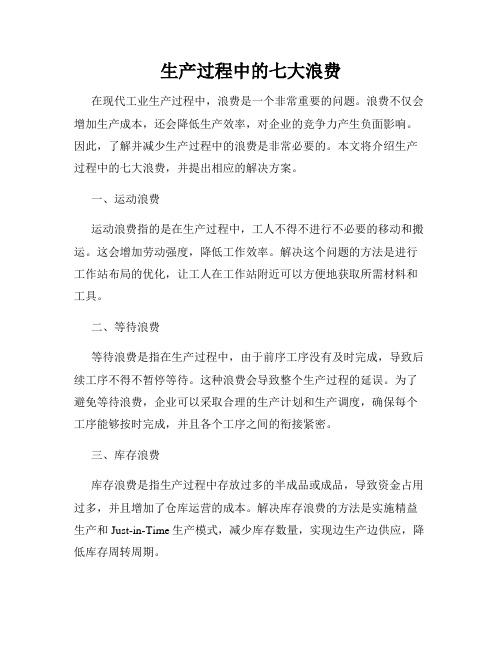
生产过程中的七大浪费在现代工业生产过程中,浪费是一个非常重要的问题。
浪费不仅会增加生产成本,还会降低生产效率,对企业的竞争力产生负面影响。
因此,了解并减少生产过程中的浪费是非常必要的。
本文将介绍生产过程中的七大浪费,并提出相应的解决方案。
一、运动浪费运动浪费指的是在生产过程中,工人不得不进行不必要的移动和搬运。
这会增加劳动强度,降低工作效率。
解决这个问题的方法是进行工作站布局的优化,让工人在工作站附近可以方便地获取所需材料和工具。
二、等待浪费等待浪费是指在生产过程中,由于前序工序没有及时完成,导致后续工序不得不暂停等待。
这种浪费会导致整个生产过程的延误。
为了避免等待浪费,企业可以采取合理的生产计划和生产调度,确保每个工序能够按时完成,并且各个工序之间的衔接紧密。
三、库存浪费库存浪费是指生产过程中存放过多的半成品或成品,导致资金占用过多,并且增加了仓库运营的成本。
解决库存浪费的方法是实施精益生产和Just-in-Time生产模式,减少库存数量,实现边生产边供应,降低库存周转周期。
四、过度加工浪费过度加工浪费是指在生产过程中对产品进行不必要的加工和处理,从而增加了生产成本和工作量。
企业可以通过优化工艺流程,合理设计产品结构,避免对产品进行过度加工,实现资源最大化利用,降低成本。
五、运输浪费运输浪费是指在物料或产品在生产过程中进行运输时,由于路线不合理或者没有合理利用运输设备,导致时间和资源的浪费。
企业可以进行运输路线的优化,规划合理的物料运输方案,提高运输效率,降低浪费。
六、瑕疵浪费瑕疵浪费是指在生产过程中由于工艺不合理或者设备故障等原因导致产品出现瑕疵,无法正常出货。
为了减少瑕疵浪费,企业应该进行质量管理,加强检验和监控环节,确保产品达到质量标准,减少废品的产生。
七、不必要的运动浪费不必要的运动浪费是指在生产过程中,工人进行同一动作时反复不断的浪费。
为了减少不必要的运动浪费,企业可以培训工人,提高工人的操作技能和效率,减少工人的错误操作和反复动作,提高整体生产效率。
制造业精益生产之如何消除七大浪费

制造业精益生产之如何消除七大浪费在制造业中,浪费是一种常见的现象。
浪费的存在会导致资源的浪费、生产效率的降低以及产品质量的下降。
为了提高生产效率和降低成本,制造业采用了精益生产的方法来消除浪费。
本文将介绍精益生产中的七大浪费,并提供相应的解决方法。
1. 运输浪费运输浪费是指在生产过程中,产品或物料不必要地被运输到不同的地点,导致时间和资源的浪费。
为了消除运输浪费,可以采取以下措施:•将设备和工作站布置得更合理,减少运输距离;•优化物料管理和存储,使物料更容易获取;•使用自动化设备来替代手动搬运,减少人力资源浪费。
2. 库存浪费库存浪费是指过多的库存导致的资源浪费。
过多的库存不仅需要占用大量的存储空间,还容易导致过期或损坏。
为了消除库存浪费,可以采取以下措施:•通过精确的需求预测,减少库存量;•优化供应链和物料配送,降低供应时间;•使用先进的ERP系统和自动化仓储设备来管理库存。
3. 动作浪费动作浪费是指在生产过程中,工人做了不必要的动作,导致时间和能源的浪费。
为了消除动作浪费,可以采取以下措施:•优化工作流程和工作布局,减少不必要的移动;•培训员工,提高工作技能和效率;•使用工具和设备来代替人力操作,减少体力劳动。
4. 等待浪费等待浪费是指在生产过程中,由于前一工序没有及时完成,导致后一工序无法开始工作,从而造成时间和资源的浪费。
为了消除等待浪费,可以采取以下措施:•控制每个工序的生产时间,减少延误;•提高设备和工具的稼动率,减少停机和故障;•优化生产计划和调度,确保工序之间的无缝衔接。
5. 生产过程中的缺陷浪费生产过程中的缺陷浪费是指生产出来的产品存在缺陷,需要修复或重新生产,从而造成时间和资源的浪费。
为了消除缺陷浪费,可以采取以下措施:•实施全面质量管理,从源头控制质量;•培训员工,提高生产技能和质量意识;•使用现代化的生产设备和工具,提高产品质量。
6. 过度生产浪费过度生产浪费是指超过需求生产产品,导致存货过多和资源浪费。
生产过程中的七大浪费
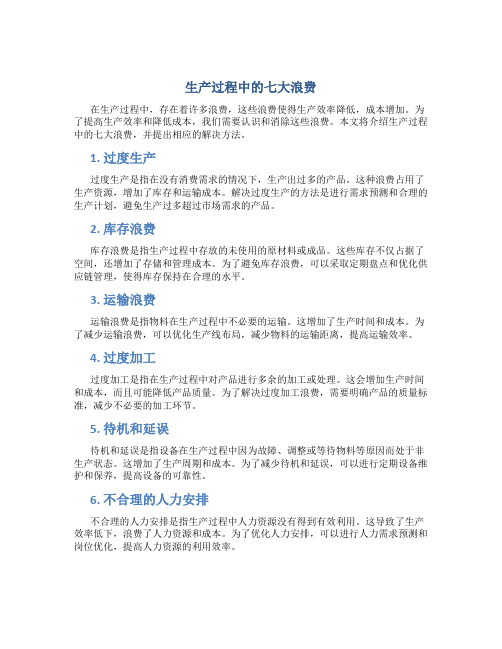
生产过程中的七大浪费在生产过程中,存在着许多浪费,这些浪费使得生产效率降低,成本增加。
为了提高生产效率和降低成本,我们需要认识和消除这些浪费。
本文将介绍生产过程中的七大浪费,并提出相应的解决方法。
1. 过度生产过度生产是指在没有消费需求的情况下,生产出过多的产品。
这种浪费占用了生产资源,增加了库存和运输成本。
解决过度生产的方法是进行需求预测和合理的生产计划,避免生产过多超过市场需求的产品。
2. 库存浪费库存浪费是指生产过程中存放的未使用的原材料或成品。
这些库存不仅占据了空间,还增加了存储和管理成本。
为了避免库存浪费,可以采取定期盘点和优化供应链管理,使得库存保持在合理的水平。
3. 运输浪费运输浪费是指物料在生产过程中不必要的运输。
这增加了生产时间和成本。
为了减少运输浪费,可以优化生产线布局,减少物料的运输距离,提高运输效率。
4. 过度加工过度加工是指在生产过程中对产品进行多余的加工或处理。
这会增加生产时间和成本,而且可能降低产品质量。
为了解决过度加工浪费,需要明确产品的质量标准,减少不必要的加工环节。
5. 待机和延误待机和延误是指设备在生产过程中因为故障、调整或等待物料等原因而处于非生产状态。
这增加了生产周期和成本。
为了减少待机和延误,可以进行定期设备维护和保养,提高设备的可靠性。
6. 不合理的人力安排不合理的人力安排是指生产过程中人力资源没有得到有效利用。
这导致了生产效率低下,浪费了人力资源和成本。
为了优化人力安排,可以进行人力需求预测和岗位优化,提高人力资源的利用效率。
7. 缺乏质量控制缺乏质量控制是指生产过程中未能及时发现和解决产品质量问题。
这会导致产品退货和重新生产,增加了生产成本和时间。
为了解决缺乏质量控制的问题,可以建立完善的质量管理体系,进行质量检查和追溯。
以上是生产过程中的七大浪费及其解决方法。
通过认识和消除这些浪费,我们可以提高生产效率和质量,降低成本,实现可持续发展。
希望本文对于您理解和改善生产过程中的浪费问题有所帮助。
七大浪费案例
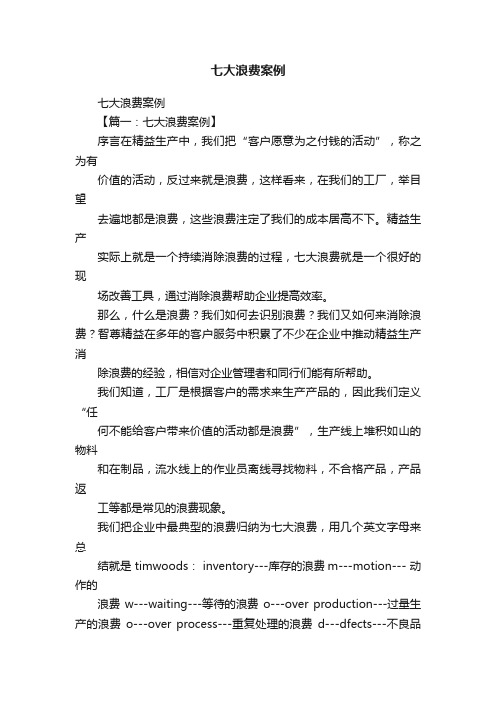
七大浪费案例七大浪费案例【篇一:七大浪费案例】序言在精益生产中,我们把“客户愿意为之付钱的活动”,称之为有价值的活动,反过来就是浪费,这样看来,在我们的工厂,举目望去遍地都是浪费,这些浪费注定了我们的成本居高不下。
精益生产实际上就是一个持续消除浪费的过程,七大浪费就是一个很好的现场改善工具,通过消除浪费帮助企业提高效率。
那么,什么是浪费?我们如何去识别浪费?我们又如何来消除浪费?智尊精益在多年的客户服务中积累了不少在企业中推动精益生产消除浪费的经验,相信对企业管理者和同行们能有所帮助。
我们知道,工厂是根据客户的需求来生产产品的,因此我们定义“任何不能给客户带来价值的活动都是浪费”,生产线上堆积如山的物料和在制品,流水线上的作业员离线寻找物料,不合格产品,产品返工等都是常见的浪费现象。
我们把企业中最典型的浪费归纳为七大浪费,用几个英文字母来总结就是 timwoods: inventory---库存的浪费m---motion--- 动作的浪费 w---waiting---等待的浪费o---over production---过量生产的浪费o---over process---重复处理的浪费d---dfects---不良品的浪费transportation 搬运的浪费指流程中因两点间距离远而造成的搬运、走动等浪费包括人的浪费和机器的浪费。
搬运本身是一种无附加价值的动作,若分解开来又分为:放置,堆积,移动,整列等动作浪费。
我们在企业中经常看到这样的搬运动作:从机械化车间到操作工位以上搬运需要我们用人或者机器来完成,它们带给企业怎样的浪费呢?显而易见,拿起、放下会造成取放过程中时间的浪费,在反复搬运中会造成我们等待和在制品库存的浪费,堆积物料和在制品会造成我们面积和空间的浪费transportation 要消除搬运的浪费,我们必须知道是什么原因导致搬运的发生:设计的兼容性:业务扩充新增工序或设备,设备或物料变换不适合,前景不明未作整体规划。
生产7大浪费及解决方案

生产7大浪费及解决方案哎呀,今天咱们聊聊一个很严肃的话题:生产7大浪费及解决方案。
别看这是一个正经八百的话题,咱们还是可以把它讲得轻松幽默一点,让大家在愉快的氛围中学到知识。
咱们来了解一下什么是生产7大浪费。
生产7大浪费是指生产过程中的以下七种资源浪费现象:1. 过剩生产:就是生产出来的东西太多,卖不掉,最后变成废品。
这就像是买了一堆衣服,结果发现根本穿不完,只能扔进衣柜里当摆设。
2. 库存积压:就是生产的物品卖不出去,堆积在仓库里。
这就像是买了一堆零食,结果吃不完,只能放在冰箱里慢慢变质。
3. 运输浪费:就是生产出来的物品需要运输到其他地方,但是运输过程中可能会损坏。
这就像是买了一盒蛋糕,结果运输途中碎了,只能眼睁睁看着它破碎。
4. 等待浪费:就是在生产过程中,因为某些原因导致生产速度变慢,需要等待。
这就像是约了朋友逛街,结果等了半天还没出发。
5. 加工浪费:就是在生产过程中,对物品进行重复加工,但是并没有提高效率。
这就像是做了一道菜,结果又炒了一遍,还加了很多调料。
6. 决策失误浪费:就是在生产过程中,因为决策错误导致资源浪费。
这就像是开了一家餐厅,结果菜单上的菜都不受欢迎。
7. 设备故障浪费:就是生产过程中设备出现故障,导致生产停滞。
这就像是开了一个工厂,结果机器突然坏了,整个生产线都停了下来。
了解了这些浪费现象之后,咱们再来谈谈解决方案。
解决这些问题的方法有很多,下面我给大家分享几个简单易懂的方法:1. 过剩生产:可以通过市场调查,了解消费者的需求,合理安排生产计划。
这样就不会出现买多了卖不掉的情况了。
2. 库存积压:可以通过促销活动,比如打折、满减等方式,刺激消费者购买。
这样就可以加快销售速度,减少库存积压。
3. 运输浪费:可以通过改进运输方式,提高运输效率。
比如使用冷藏车、快递等快速物流方式,确保货物在运输过程中不会受损。
4. 等待浪费:可以通过优化生产流程,提高生产效率。
这样就可以缩短等待时间,让消费者更快地拿到产品。
精益生产之七大浪费及5S管理
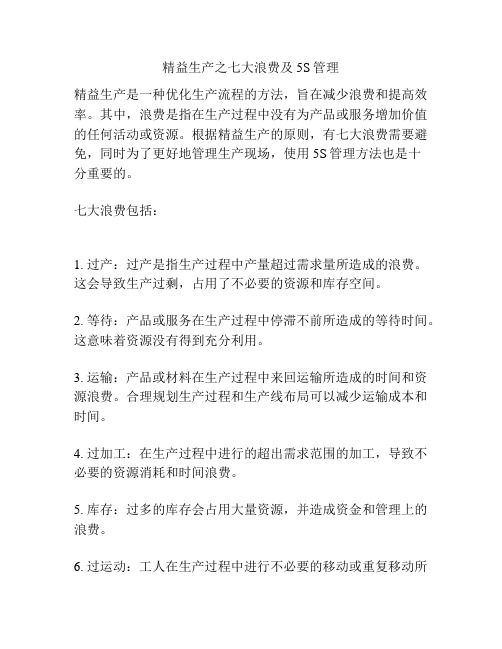
精益生产之七大浪费及5S管理精益生产是一种优化生产流程的方法,旨在减少浪费和提高效率。
其中,浪费是指在生产过程中没有为产品或服务增加价值的任何活动或资源。
根据精益生产的原则,有七大浪费需要避免,同时为了更好地管理生产现场,使用5S管理方法也是十分重要的。
七大浪费包括:1. 过产:过产是指生产过程中产量超过需求量所造成的浪费。
这会导致生产过剩,占用了不必要的资源和库存空间。
2. 等待:产品或服务在生产过程中停滞不前所造成的等待时间。
这意味着资源没有得到充分利用。
3. 运输:产品或材料在生产过程中来回运输所造成的时间和资源浪费。
合理规划生产过程和生产线布局可以减少运输成本和时间。
4. 过加工:在生产过程中进行的超出需求范围的加工,导致不必要的资源消耗和时间浪费。
5. 库存:过多的库存会占用大量资源,并造成资金和管理上的浪费。
6. 过运动:工人在生产过程中进行不必要的移动或重复移动所造成的浪费。
此外,工作场所的布局也可能导致不必要的运动。
7. 失效:产品或设备因为质量问题或故障导致不能正常使用所带来的浪费。
这包括废品、次品和修理等。
为了管理生产现场,5S管理方法可以帮助提高工作效率和质量。
5S分别代表整理、整顿、清扫、清洁和遵守。
1. 整理:整理工作场地,确定需要的物品和设备并清除不需要的物品。
2. 整顿:确定合理的工作流程和布局,确保工作区域的物品和设备放置得井井有条。
3. 清扫:保持工作区域的清洁和整洁,确保工作环境安全和舒适。
4. 清洁:定期进行清洁工作,包括设备和机器的保养和维护,以确保其正常运行。
5. 遵守:遵守标准和规定,执行工作流程,并及时纠正和改进。
精益生产的目标是通过减少浪费和提高效率来提供更高质量的产品和服务。
而5S管理方法可以帮助企业管理生产现场,提高工作效率和质量。
通过合理应用这些原则和方法,企业可以提升竞争力,并更好地满足客户需求。
精益生产的目标是通过减少浪费和提高效率来提供更高质量的产品和服务。
精益生产七大浪费的实例
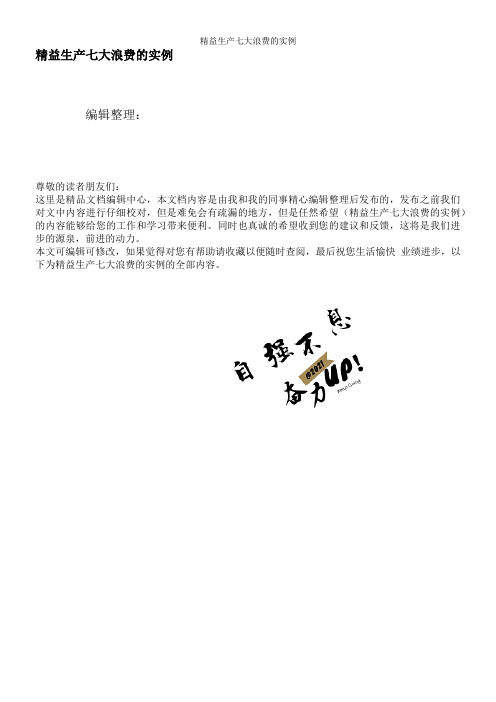
精益生产七大浪费的实例编辑整理:尊敬的读者朋友们:这里是精品文档编辑中心,本文档内容是由我和我的同事精心编辑整理后发布的,发布之前我们对文中内容进行仔细校对,但是难免会有疏漏的地方,但是任然希望(精益生产七大浪费的实例)的内容能够给您的工作和学习带来便利。
同时也真诚的希望收到您的建议和反馈,这将是我们进步的源泉,前进的动力。
本文可编辑可修改,如果觉得对您有帮助请收藏以便随时查阅,最后祝您生活愉快业绩进步,以下为精益生产七大浪费的实例的全部内容。
精益生产七大浪费的实例七种浪费第一种:等待的浪费主要因素表现为:作业不平衡,安排作业不当、待料、品质不良等.第二种:搬运的浪费主要因素表现为:车间布置采用批量生产,依工作站为区别的集中的水平式布置所致。
(也就是分工艺流程批量生产),无流线生产的观念。
第三种:不良品的浪费主要因素表现为:工序生产无标准确认或有标准确认未对照标准作业,管理不严密、松懈所导致。
第四种:动作的浪费主要因素表现为:生产场地不规划,生产模式设计不周全,生产动作不规范统一。
第五种:加工的浪费主要因素表现为:制造过程中作业加工程序动作不优化,可省略、替代、重组或合并的未及时检查。
第六种:库存的浪费主要因素表现为:管理者为了自身的工作方便或本区域生产量化控制一次性批量下单生产,而不结合主生产计划需求流线生产所导致局部大批量库存。
库存的损害表现有:(1):产生不必要的搬运、堆积、放置、防护处理、找寻等浪费.(2):使先进先出的作业困难。
(3):损失利息及管理费用。
(4):物品的价值会减低,变成呆滞品。
(5):占用厂房空间,造成多余的工场、仓库建设投资的浪费.(6):没有管理的紧张感,阻碍改进.(7):设备能力及人员需求的误判。
第七种:制造过多(早)的浪费主要因素表现为:管理者认为制造过多与过早能够提高效率或减少产能的损失和平衡车间生产力.制造过多(早)的损害表现有:(1):提早用掉费用(材料费、人工费),不能创造利润。
精益生产之如何消除七大浪费

过多的库存会隐藏的问题点:
☆没有管理的紧张感,阻碍进一步的改善 ☆设备能力及人员需求的误判 ☆对场地需求的判断错误 ☆产品品质变差的可能性 ☆容易出现呆滞物料
☆何谓浪费 ☆浪费的种类
☆“七大浪费”介绍
☆消除浪费的做法
☆浪费的实例
何谓浪费:
不产生任何附加价值的动作、方法、 行为和计划。
用不同的评判标准去判断一个 动作、行为、方法或计划时,所得 到的浪费程度都会不同。
现场活动包括“有附加价值的”和“没有附加价值的”活动,那些 不产生附加价值的活动应坚决予以消除。
精益生产之如何消除七大浪费
引言
竞争力提升
品质提升 合理化成本降低 形象提升
改善 消除浪费 标准化 现场5S
动作改善、作业流程改善、物流改善、设 备模具夹具改善、品质改善、管理改善等
七大浪费、三无工程等
动作标准化、作业流程标准化、操作流程 标准化、包装运输标准化等
整理、整顿、清扫、清洁、素养等
目 录
☆☆运消用 除四生大产经风济险原,则降低安全库存产品的飞边太多,如果 制造过多是一种浪费的通原因过:修整模具能够使修边更 现象、申诉内容、发生容次数易、5,W2则H处可置内节容 省人力
7 不良所造成的库存,半成品所造成的库存,制造
过多所造成的库存
大浪费
材料、零件、组合件等物品的停滞状态,包括库存及在制品
表现形式:
☆不良品存在库房内待修 ☆设备能力不足所造成的安全库存 ☆换线时间太长,造成大批量生产的浪费 ☆采购过多的物料,成为库存
库存是万恶的根源
过多的库存会造成的浪费:
7大浪费
☆产生不必要的搬运、堆积、放置、寻找、防护处理等浪费的动作 ☆使先进先出的作业困难 ☆损失利息及管理费用 ☆物品之价值会减低,变成呆滞品 ☆占用厂房、造成多余的工作场所、仓库建设 的浪费 ☆造成无形的浪费
八大浪费改善案例

八大浪费改善案例
八大浪费是精益生产中经常提到的概念,包括不良、修理的浪费,过分加工的浪费,动作的浪费,搬运的浪费,库存的浪费,制造过多过早的浪费,等待的浪费和管理的浪费。
以下是一些针对这些浪费的改善案例:
1. 不良、修理的浪费:某公司通过实施严格的质量控制体系,提高首次合格率,减少了不良品和需要返工的产品的数量。
2. 过分加工的浪费:某制造企业通过重新评估生产流程,优化了切割和打磨等工艺步骤,减少了不必要的加工工作,提高了生产效率。
3. 动作的浪费:某装配线引入了更为合理的物料摆放和输送方式,减少了工人的动作量,提高了工作效率。
4. 搬运的浪费:某工厂优化了物料配送流程,减少了中间环节和运输距离,降低了搬运成本。
5. 库存的浪费:某公司引入了实时库存管理系统,实现了库存的精准控制,减少了库存积压和浪费。
6. 制造过多过早的浪费:某生产车间引入了准时制生产方式,严格按照客户需求进行生产和排程,避免了过度生产和过早生产的问题。
7. 等待的浪费:某生产线引入了多能工制度,通过交叉培训和任务分配,减少了人员等待时间,提高了生产效率。
8. 管理的浪费:某企业通过引入先进的生产管理软件,简化了管理流程,提高了管理效率。
这些案例都是通过深入分析和优化生产和管理流程,消除了八大浪费中的一些问题点,提高了效率并降低了成本。
在实际操作中,需要针对企业具体情况制定相应的改善方案。
消除生产现场的七大浪费
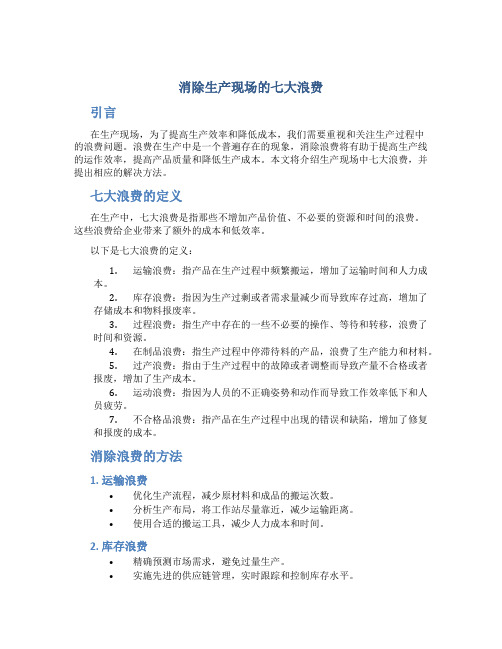
消除生产现场的七大浪费引言在生产现场,为了提高生产效率和降低成本,我们需要重视和关注生产过程中的浪费问题。
浪费在生产中是一个普遍存在的现象,消除浪费将有助于提高生产线的运作效率,提高产品质量和降低生产成本。
本文将介绍生产现场中七大浪费,并提出相应的解决方法。
七大浪费的定义在生产中,七大浪费是指那些不增加产品价值、不必要的资源和时间的浪费。
这些浪费给企业带来了额外的成本和低效率。
以下是七大浪费的定义:1.运输浪费:指产品在生产过程中频繁搬运,增加了运输时间和人力成本。
2.库存浪费:指因为生产过剩或者需求量减少而导致库存过高,增加了存储成本和物料报废率。
3.过程浪费:指生产中存在的一些不必要的操作、等待和转移,浪费了时间和资源。
4.在制品浪费:指生产过程中停滞待料的产品,浪费了生产能力和材料。
5.过产浪费:指由于生产过程中的故障或者调整而导致产量不合格或者报废,增加了生产成本。
6.运动浪费:指因为人员的不正确姿势和动作而导致工作效率低下和人员疲劳。
7.不合格品浪费:指产品在生产过程中出现的错误和缺陷,增加了修复和报废的成本。
消除浪费的方法1. 运输浪费•优化生产流程,减少原材料和成品的搬运次数。
•分析生产布局,将工作站尽量靠近,减少运输距离。
•使用合适的搬运工具,减少人力成本和时间。
2. 库存浪费•精确预测市场需求,避免过量生产。
•实施先进的供应链管理,实时跟踪和控制库存水平。
•追求生产柔性,减少产品变化带来的库存压力。
3. 过程浪费•优化工艺流程,消除不必要的操作和等待时间。
•采用合理的生产排程,最大程度地减少转移时间。
•培训员工,提高员工的技能水平,减少操作失误。
4. 在制品浪费•优化物料供应链,确保物料及时供应。
•设立及时报警机制,及时发现停工待料情况。
•引入自动化设备,提高生产效率和稳定性。
5. 过产浪费•定期检查和维护设备,减少设备故障的发生。
•加强员工培训,提高员工的技能水平和故障排除能力。
- 1、下载文档前请自行甄别文档内容的完整性,平台不提供额外的编辑、内容补充、找答案等附加服务。
- 2、"仅部分预览"的文档,不可在线预览部分如存在完整性等问题,可反馈申请退款(可完整预览的文档不适用该条件!)。
- 3、如文档侵犯您的权益,请联系客服反馈,我们会尽快为您处理(人工客服工作时间:9:00-18:30)。
作业现场的7大浪费
生产现场发生的浪费有捡取掉在地上的部件或其他物品的行为、临时组装行为、踩到产品或零件的行为、绞线的行为、临时决定或插入的行为、临时存放行为、物品摆放不整齐、抬起和放下的行为、坐下和站起行为等,生产现场的浪费具体可分为7类,如下所述。
⑥ 第1种:生产过多的浪费 即不必要的产品在不必要的时间段,生产的数量超过需要量的生产行为为第一种浪费。
⑥ 第2种:库存的浪费 放在生产车间的材料、零件、装
配件等物品,工程与工程之间的在制品也都属于库存的浪费。
库存和在制品如“毒品”一样,最初就不能开始,一旦开始就很容易养成习惯,习惯成自然,很难戒掉。
发生一些小问题也就不会太在意。
⑥ 第3种:搬运的浪费
不必要的搬运、物品的移动、保管、容器更换,长距离搬运等都
过多生产
过多生产
库存
属于搬运的浪费。
抬、放、搬、堆,都属于没有任何附加值的不必要的劳动。
⑥第4种:制作不良的浪费
材料不良、加工不良、检查不良、
索赔、再作业、修整等不良工程形成的
浪费。
不良是产生额外的工作,废弃和
减少利益的元凶。
出现不良就要添加人手管理,人工成本也随之增加。
⑥第5种:加工的浪费
不必要的工序或工序管理不善导致需要追加修正作业所产生加工浪费。
现在所做的工作确实是必要的吗?不能一次性完成吗?
⑥第6种:动作的浪费
不必要的动作,或没有附加值的工作以及慢吞吞的行动都是行为浪费。
为什么要执行
这项作业材料不良
再次不良
第7种:等待的浪费
材料、作业、搬运、检查等方面的等
待,或者因为有空闲时间呆着什么都不
做,监视作业等等待浪费。
等待机器作业
结束也属于等待浪费。
另外,工厂现场浪费又可划分为与人相关的浪费(如迟到多、缺勤者多等)和与物品相关的浪费(如材料不良、设备故障较多等)。
工厂需加以识别区分,革新人员可分析总结根据各类浪费的特点,提出改善措施,达成及时、针对性、有效改善这些浪费的目的。
改善浪费的执行方法
1.改善浪费的执行
改善浪费的方法措施如下表1-3所示。
改善浪费的措施
改善浪
费
执行说明
改善的
原则◎考虑人的合适性,如眼睛判别能力、手的移动方法等◎业务分工合理性,综合考虑进度、难度,追求质量与数量的平衡
2.实行动作经济原则——消除浪费
“动作经济原则”又称“省工原则”,是使作业以最少的“工”的投入,产生最有效率的效果,从而达成作业目的。
动作经济原则经许多专家学者研究整理而成,熟悉运用其对有效安排作业动作、提高作业效率、减少浪费等起到很大帮助。
动作经济原则包括4大基本原则和人、工具设备、环境布置等3个方面的16大原则,工厂革新活动中可根据作业特性进行运用,具
体如图1-12所示。
图1-12 动作经济的20大原则
作业现场浪费改善实例
现场的消除浪费不只是个很大的主题,
也是一些细小的主题合起
4项基本原则
◎ 减少动作数量 ◎ 追求动作平衡 ◎ 缩短动作移动距离 ◎ 使动作保持轻松自然的节奏
关于环境布置方面的原则 ◎ 适当位置的原则 ◎ 安全可靠的原则 ◎ 照明通风的原则 ◎ 高度适当的原则
关于人体动作方面的原则 ◎ 双手并用的原则 ◎ 对称反向的原则 ◎ 排除合并的原则 ◎ 降低动作等级的原则 ◎ 减少动作限制的原则 ◎ 避免动作突变的原则 ◎ 保持轻松节奏的原则
◎ 利用惯性的原则 ◎ 手脚并用的原则 关于工具设备方面的原则 ◎ 利用工具的原则
◎ 工具万能化原则(工具组合) ◎ 易于操纵的原则
来给工厂带来巨大成果。
下面是能对现场消除浪费能提供帮助的实例,供读者参考。