硫化体系
硫化体系PPT课件

硫化体系的热力学原理
熵变效应
热稳定性
在硫化过程中,橡胶分子链由无序状 态转变为有序的网状结构,导致熵变 效应,影响硫化反应的平衡状态。
硫化体系在高温下的热稳定性取决于 橡胶分子的热分解温度和交联键的热 稳定性。
自由能变化
硫化过程中,橡胶分子链的自由能变 化与交联密度、交联键类型等因素有 关,自由能变化会影响硫化体系的稳 定性。
硫化体系的动力学原理
硫化速率
硫化体系的动力学原理主要研究 硫化速率与反应条件的关系,如 温度、压力、促进剂种类和浓度
等。
硫化动力学模型
通过建立硫化动力学模型,可以描 述硫化过程中各阶段的反应速率常 数、活化能等参数,有助于优化硫 化工艺和提高产品质量。
促进剂的作用
在硫化过程中,促进剂可以加速硫 化反应速率,缩短硫化时间,提高 生产效率。
03 硫化体系的应用
在橡胶工业中的应用
轮胎制造
硫化体系在轮胎制造过程中起到 至关重要的作用,能够提高轮胎 的耐磨性、抗疲劳性和抗湿滑性, 从而提高轮胎的性能和使用寿命。
橡胶管和密封件
硫化体系在橡胶管和密封件的生 产中也有广泛应用,能够改善橡 胶制品的弹性和耐久性,提高产
品的质量和可靠性。
橡胶鞋和手套
硫化体系与其他技术的结合
硫化技术与纳米技术的结合
利用纳米材料的特点,如高比表面积、高活性等,与硫化体系结合,制备出具有 优异性能的橡胶复合材料。
硫化技术与智能材料的结合
将硫化技术与智能材料技术相结合,制备出具有自感知、自适应、自修复等功能 的智能橡胶材料。
硫化体系在环保方面的应用
低VOC排放
通过优化硫化体系配方,降低生产过 程中VOC(挥发性有机化合物)的排 放,减少对环境的污染。
硫化体系对天然橡胶性能的影响

硫化体系对天然橡胶性能的影响采用常规硫化体系(CV)、半有效硫化体系(SEV)和有效硫化体系(EV)制备了不同的NR(天然橡胶)硫化胶。
着重探讨了不同硫化胶的微观形貌、200%定伸强度、撕裂强度、拉伸强度、断裂伸长率和交联密度。
研究结果表明:SEV硫化胶的微观形貌相对较好,填料能均匀分散在基体中;在其他条件保持不变的前提下,当w(NOBS)=w(硫)=2.0%(相对于NR质量而言)时,相应的未老化SEV硫化胶的撕裂强度(78kN/m)相对最大;SEV硫化胶的交联密度大于CV硫化胶和EV硫化胶,并且适当增加交联密度能有效提高其综合性能,从而为开发新一代轮胎等复合材料奠定了基础。
前言天然橡胶(NR)具有拉伸强度高、抗湿滑性优和滚动阻力小等诸多特点,其硫化胶中主要包括单硫键(C—S—C)、双硫键(C—S2—C)和多硫键(C—Sx—C)等3种硫交联键型。
硫化胶的交联键长度分布和硫原子排布由下列因素决定:①促进剂和交联剂的种类及其浓度;②硫化时间和硫化温度。
硫化体系主要分为常规硫化体系(CV)、半有效硫化体系(SEV)和有效硫化体系(EV)等3种,交联键中硫原子的排布主要取决于硫含量、促进剂与硫的比率等因素;硫化初期比硫化后期具有更多的C—Sx—C(x=4或5),硫化过程中长交联键短化(直至生成单硫键)。
Rattanasom等研究结果表明:老化后硫化胶的模量增大,同时试样的断裂伸长率降低(这是由于老化过程中发生了后硫化作用,而后硫化使硫化胶的交联密度增大,从而降低了橡胶分子链的运动性)。
尽管硫化胶的力学性能与交联结构有很大的关系,但系统研究这种关系仍报道较少。
因此,本研究通过改变硫化体系、硫化剂及其比率,制得了不同性能的硫化胶,并对硫化胶的力学性能、耐热氧老化性能与交联密度的关系进行了探究。
1·试验部分1.1试验原料天然橡胶(NR),工业级(牌号为1#烟片胶),海南省农垦总公司;高耐磨炉黑,工业级(牌号N330);丙酮、正庚烷,分析纯;4,4′-二硫化二吗啉(DTDM),工业级,;2-(4-吗啉硫代)苯并噻唑(NOBS),工业级,;硫磺(S),工业级;硬脂酸(SA)、氧化锌(ZnO),工业级;2,2,4-三甲基-1,2-二氢化喹啉聚合体(RD),工业级;N-异丙基-N′-苯基对丙二胺(4010NA),工业级。
有效硫磺硫化体系

有效硫磺硫化体系有效硫磺硫化体系是指在一定条件下,硫磺与其他物质发生硫化反应,生成硫化合物的化学体系。
硫磺硫化体系在许多领域中具有重要的应用价值,例如冶金、化工、材料科学等。
本文将重点介绍有效硫磺硫化体系的定义、特性以及应用等方面内容。
一、有效硫磺硫化体系的定义和特性有效硫磺硫化体系是指在一定条件下,硫磺与其他物质发生硫化反应,生成硫化合物的化学体系。
硫磺是一种黄色固体,具有特殊的气味。
硫磺在常温下不易熔化,需要加热到119.5摄氏度才能熔化。
硫磺具有很高的燃点和燃烧温度,可以用作火药的重要成分。
有效硫磺硫化体系的特性是其反应速度较快,生成的硫化物具有稳定的化学性质。
硫磺与其他元素或化合物发生硫化反应时,常常能够生成高稳定性的硫化物。
硫化物可以作为重要的材料应用于多个领域,例如硫化铁可以用于制备磁性材料,硫化锌可以用于制备光电材料等。
1. 冶金领域在冶金领域中,有效硫磺硫化体系被广泛应用于矿石的处理和提取。
例如,在铜冶炼过程中,硫磺可以与铜矿石中的铁等杂质发生反应,生成稳定的硫化物,从而实现铜的提取和纯化。
2. 化工领域在化工领域中,有效硫磺硫化体系被用于合成有机硫化物。
有机硫化物是一类重要的有机化合物,具有广泛的应用价值。
例如,硫磺可以与烯烃类化合物发生硫化反应,生成硫代烯烃类化合物,用于合成橡胶、塑料等材料。
3. 材料科学领域在材料科学领域中,有效硫磺硫化体系被用于合成硫化物材料。
硫化物材料具有特殊的电学、光学和磁学性质,可以应用于电子器件、光电器件和磁性材料等领域。
例如,硫磺可以与金属硫化物发生硫化反应,生成稳定的硫化物材料,用于制备电子器件中的半导体材料。
三、有效硫磺硫化体系的研究进展近年来,随着科学技术的不断发展,对有效硫磺硫化体系的研究也取得了一系列重要的进展。
研究人员通过调控反应条件、改变硫磺的形态和结构等方式,提高了硫磺与其他物质发生硫化反应的效率和选择性。
研究人员还通过表面修饰、掺杂等手段,改善了硫化物材料的性能和稳定性。
3橡胶工艺学第二章橡胶的硫化体系
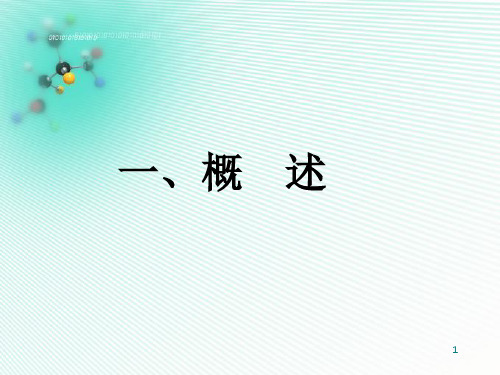
特点:
焦烧时间长,硫化速度快。 适用于合成橡胶的高温快速硫化和厚制
品的硫化。该类促进剂诱导期的长短与 和氨基相连基团的大小数量有关,基团 越大,数量越多,诱导期越长,防焦效 果越好。如DZ>NOBS>CZ。
31
Ⅲ.秋兰姆类:
ห้องสมุดไป่ตู้
结构通式为:
R' S
S
R'
N C Sx C N
R
R
R,R’为烷基,芳基或其它基团
双键 自由基 Or 离子型加成
∵硫化前后双键数目变化不大。
∴反应主要在α-H上反应,以自由基 机理为主。
7
㈡、硫化历程
第一阶段:诱导期,活性剂,促进剂,硫 黄之间相互作用,生成带有多硫促进剂侧 基的橡胶大分子。线型分子,能流动。
第二阶段:交联反应,带有多硫促进剂侧 基的橡胶大分子与橡胶大分子之间发生交 联反应,生成交联键。初期网状分子,已 不能流动。
H, D
NA-22,
CZ
NOBS,
DZ
18
按促进速度分类:
国际上习惯以促进剂M对NR的硫化速度 为标准,以比较促进剂的硫化速度。
慢速级促进剂:H,NA-22 中速级促进剂:D 准速级促进剂:M,DM,CZ,DZ,NOBS 超速级促进剂:TMTD,TMTM 超超速级促进剂:ZDMC,ZDC
英文 简称 ZDM
C ZDC
BZ
PX
基团
R,R’为甲基,M为 锌
R,R’为乙基,M为 锌
R,R’为丁基,M为 锌
R为乙基,R’为苯 基,M为锌
36
特点:
此类促进剂比秋兰姆更活泼。 过渡金属离子使橡胶的不饱和键更易
极化,硫化速度更快,属超超速级酸 性促进剂。 诱导期极短,适用于室温硫化和胶乳 制品的硫化。
2-4 各种硫黄硫化体系

高分子科学与工程学院 College of Polymer Science and Engineering
Si-69抗硫化返原的原理
Si-69析出的活性硫参与硫化反应,其形成交
联键的速率比硫黄形成交联键的速度慢,从而 使硫化胶的交联密度在较长的时间内保持动态 的常量,消除硫化返原现象。
配合特点:硫黄/促进剂/ Si-69等摩尔比。
配合特点:高硫低促:促进剂/S=(0.6~0.8)/(1.5~2.5) 硫化胶结构特点:以多硫交联键为主(70%以上) 硫化胶性能特点:硫化胶的强度和动态疲劳性能好;
耐老化性能差,硫化胶不能在高温 下长期使用。
适用场合:常温、动态情况下使用的制品。
高分子科学与工程学院 College of Polymer Science and Engineering
1) 选用耐热胶种
胶种 NR 极限硫化温度 240 胶种 CR 极限硫化温度 260
SBR
NBR
300
300
EPDM
IIR
300
300
适用于高温快速硫化的胶种为EPDM、IIR、NBR、
SBR等。
高分子科学与工程学院 College of Polymer Science and Engineering
适合大型厚制品的硫化。
高分子科学与工程学院 College of Polymer Science and Engineering
常用的抗硫化返原的方法
采用硫给体或有效硫化体系:对撕裂强度和耐
疲劳性有不利影响。
低温长时间硫化:生产效率下降且橡胶制品在
高温下使用时易降解。
并用具有增大模量的橡胶(如 SBR 和HVBR) 使用抗硫化返原剂:通过Diels—Alder反应形
硫黄硫化体系
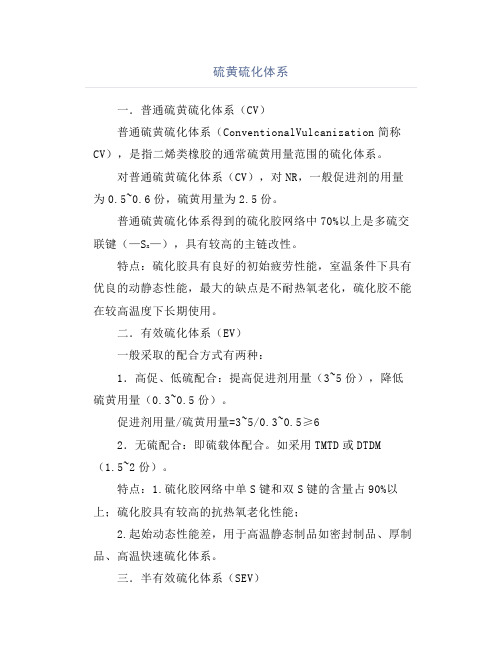
硫黄硫化体系一.普通硫黄硫化体系(CV)普通硫黄硫化体系(ConventionalVulcanization简称CV),是指二烯类橡胶的通常硫黄用量范围的硫化体系。
对普通硫黄硫化体系(CV),对NR,一般促进剂的用量为0.5~0.6份,硫黄用量为2.5份。
普通硫黄硫化体系得到的硫化胶网络中70%以上是多硫交联键(—S x—),具有较高的主链改性。
特点:硫化胶具有良好的初始疲劳性能,室温条件下具有优良的动静态性能,最大的缺点是不耐热氧老化,硫化胶不能在较高温度下长期使用。
二.有效硫化体系(EV)一般采取的配合方式有两种:1.高促、低硫配合:提高促进剂用量(3~5份),降低硫黄用量(0.3~0.5份)。
促进剂用量/硫黄用量=3~5/0.3~0.5≥62.无硫配合:即硫载体配合。
如采用TMTD或DTDM (1.5~2份)。
特点:1.硫化胶网络中单S键和双S键的含量占90%以上;硫化胶具有较高的抗热氧老化性能;2.起始动态性能差,用于高温静态制品如密封制品、厚制品、高温快速硫化体系。
三.半有效硫化体系(SEV)为了改善硫化胶的抗热氧老化和动态疲劳性能,发展了一种促进剂和硫黄的用量介于CV和EV之间的硫化体系,所得到的硫化胶既具有适量的多硫键,又有适量的单、双硫交联键,使其既具有较好的动态性能,又有中等程度的耐热氧老化性能,这样的硫化体系称为半有效硫化体系(SEV)。
用于有一定的使用温度要求的动静态制品。
一般采取的配合方式有两种:1.促进剂用量/硫用量=1.0/1.0=1(或稍大于1);2.硫与硫载体并用,促进剂用量与SEV中一致。
NR的三种硫化体系配合如表2-1所示:随着橡胶工业生产的自动化、联动化,高温快速硫化体系被广泛采用,如注射硫化、电缆的硫化等。
所谓高温硫化是指温度在180~240℃下进行的硫化。
一般硫化温度每升高10℃,硫化时间大约可缩短一半,生产效率大大提高。
1.高温硫化体系配合的原则:1).选择耐热胶种为了减少或消除硫化胶的硫化返原现象,应该选择双键含量低的橡胶。
橡胶硫化体系详解

硫化是胶料通过生胶分子间交联,形成三维网络结构,制备硫化胶的基本过程。
不同的硫化体系适用于不同的生胶。
橡胶硫化的研究一直在深入持久地进行,研究的目的主要是改进硫化胶的力学性能及其它性能,简化及完善工艺过程,降低硫化时有害物质的释放等等。
下面有针对性地简述当前使用的硫化体系。
不饱和橡胶通常使用如下几类硫化体系。
1.以硫黄,有机二硫化物及多硫化物、噻唑类、二苯胍类,氧化锌及硬脂酸为主的硫化剂。
这是最通用的硫化体系。
但所制得的硫化胶的耐热氧老化性能不高。
2.烷基酚醛树脂。
3.多卤化物(如用于聚丁二烯橡胶、丁苯橡胶及丁腈橡胶的六氯乙烷)、六氯-对二甲苯。
4.双官能试剂[如醌类、二胺类、偶氮及苯基偶氮衍生物(用于丁基橡胶及乙丙橡胶)等。
5.双马来酰亚胺,双丙烯酸酯。
两价金属的丙烯酸酯(甲基丙烯酸酯)、预聚醚丙烯酸酯。
6.用于硫化饱和橡胶的有机过氧化物。
饱和橡胶硫化不同种类的饱和橡胶时,可使用不同的硫化体系。
例如,硫化三元乙丙橡胶时,使用有机过氧化物与不饱和交联试剂,如三烯丙基异氰脲酸酯(硫化剂TAIC)。
硫化硅橡胶时也可使用有机过氧化物。
乙烯基硅橡胶硫化时可在催化剂(Pt)参与条件下进行。
含卤原子橡胶或含功能性基团的橡胶。
聚氯丁二烯橡胶、氯磺化聚乙烯及氯化丁基橡胶等是最常用的含氯橡胶。
硫化氯丁橡胶通常采用ZnO与MgO的并用物,以乙撑硫脲(NA-22)、二硫化秋兰姆、二-邻-甲苯基二胍(促进剂BG)及硫黄作硫化促进剂。
硫化氯磺化聚乙烯时可使用如下硫化体系。
1.氧化铝、氧化铅和氧化镁的并用物,以及氧化镁和季戊四醇酯,以四硫化双五甲撑秋兰姆(促进剂TRA)及促进剂DM作硫化促进剂。
2.六次甲基四胺与己二酸及癸二酸盐及氧化镁。
3.有机胺与环氧化物作用的产物。
以下体系可用于氯化丁基橡胶硫化:1.氧化锌与硬脂酸、氧化镁、秋兰姆及苯并噻唑二硫化物等的并用物;2.乙烯基二硫脲与氧化锌及氧化镁的并用物。
3.多羟基甲基酚醛树脂与氧化锌的并用物。
丁基橡胶硫化体系

丁基橡胶硫化体系摘要:1.丁基橡胶硫化体系的概述2.丁基橡胶硫化体系的组成3.丁基橡胶硫化体系的作用4.丁基橡胶硫化体系的发展趋势正文:一、丁基橡胶硫化体系的概述丁基橡胶硫化体系是指在制备丁基橡胶过程中,通过加入硫化剂和其他辅助材料,使丁基橡胶具有良好的韧性、强度、耐磨性和耐高温性能的一种技术。
硫化体系对于丁基橡胶的性能至关重要,直接影响到丁基橡胶制品的使用寿命和可靠性。
二、丁基橡胶硫化体系的组成丁基橡胶硫化体系主要由以下几部分组成:1.丁基橡胶:丁基橡胶是一种合成橡胶,具有优良的耐热性、耐老化性和耐化学品性能。
2.硫化剂:硫化剂是丁基橡胶硫化体系中最关键的部分,它能够使丁基橡胶分子间产生交联,提高橡胶的韧性和强度。
常用的硫化剂有硫磺、加速剂和促进剂等。
3.填充剂:填充剂可以改善丁基橡胶的加工性能和制品的性能,如增加硬度、耐磨性和耐高温性能等。
常用的填充剂有碳黑、硅烷等。
4.增塑剂:增塑剂能够提高丁基橡胶的柔韧性和可塑性,使其更容易加工成各种形状。
常用的增塑剂有酯类、醚类等。
5.防老剂:防老剂能够延缓丁基橡胶制品的老化过程,延长使用寿命。
常用的防老剂有抗氧化剂、紫外线吸收剂等。
三、丁基橡胶硫化体系的作用丁基橡胶硫化体系的主要作用有以下几点:1.提高丁基橡胶的韧性和强度:通过硫化剂的作用,使丁基橡胶分子间产生交联,形成稳定的三维结构,从而提高韧性和强度。
2.改善丁基橡胶的加工性能:通过添加填充剂、增塑剂等辅助材料,改善丁基橡胶的加工性能,使其更容易加工成各种形状和尺寸的制品。
3.提高丁基橡胶制品的耐热性、耐磨性和耐老化性:通过选择合适的硫化剂、填充剂等材料,提高丁基橡胶制品在使用过程中的耐热性、耐磨性和耐老化性。
四、丁基橡胶硫化体系的发展趋势随着科技的不断发展,丁基橡胶硫化体系也在不断改进和优化,主要发展趋势有以下几点:1.硫化剂的环保化:随着人们对环境保护意识的增强,硫化剂的环保化成为丁基橡胶硫化体系发展的重要方向,如采用无硫硫化剂或低硫硫化剂等。
第二章硫化体系

促 进 剂
硫黄
促 进 剂 多 硫 化 物
橡胶
橡 胶 大 分 子 多 硫
分解
大 分 子 自 由 基
橡胶
交 联 反
活 化 剂
活 性 中 间 体
化
或
物
离
子
RSxSX
பைடு நூலகம்
应
交 联 键 重 排 裂 解 主 链 改 性
网 络 稳 定 的 硫 化 胶
诱导期
交联反应期 网络形成期
四、硫化曲线(curing curve)
第二节、硫化体系助剂
一、硫化剂(curing agent)
硫化剂:又称交联剂,是指能够将橡胶线型大分子交联成网状
结构的一类物质。
作用:进行交联反应,使橡胶线型分子网络化。是配方中不可
缺少的最重要的配合剂。
主要硫化剂:
制法 硫铁矿煅烧,得硫块再粉碎
1、硫黄 硫黄粉
(最常用)
石油尾气分离出H2S,氧化再还原
《橡胶工艺学》精品课程多媒体教程
第二章 硫化体系 (Chapter 2: curing system)
8学时
本章主要内容
1 硫化曲线及硫化特性参数 2 硫化体系配合剂 3 各种硫化体系配合、结构及性能 4 硫化胶结构与性能的关系
本章要求
掌握硫化体系的选取方法
掌握硫化、焦烧、喷霜、 返原、焦烧时间、工艺正 硫化时间的概念
操作焦烧时间(processing scorch time):胶料在加工过 程中由于热积累效应所消耗的焦烧时间;
剩余焦烧时间(surplus scorch time):胶料在模具内保持 流动的时间。
操作焦烧时间长,剩余焦烧时间就短,在装模期间容易焦烧, 给成品带来质量缺陷。因此,希望剩余焦烧时间长一些,产品加 工安全。
第2章 硫化体系-2

高分子科学与工程学院 College of Polymer Science and Engineering
②热硫化(crosslink)阶段
硫化反应逐渐产生网络结构,使橡胶的弹性和拉伸强度急剧上 升。 该段斜率的大小代表硫化反应速度的快慢,主要与促进剂的品 种、用量和硫化温度有关。 促进剂活性越高、用量越大、温度越高,硫化速度也越快。
二战以前,以噻唑类为主。 20世纪70年代,发现了次磺酰胺类促进剂。 未来促进剂的发展方向是“一剂多能”,即兼备
硫化剂、活性剂、促进剂、防焦剂及对环境无污 染的特点。
高分子科学与工程学院 College of Polymer Science and Engineering
促进剂的发展历史
(three-dimensional network)
1. 硫化的本质:交联-crosslink (线形→体型) 2. 物理作用:分子间作用力、结晶区、聚集相形成的, 高温下消失。 3. 化学作用:高温下不消失,外力作用下发生断裂。
高分子科学与工程学院 College of Polymer Science and Engineering
高分子科学与工程学院 College of Polymer Science and Engineering
喷霜(blooming)
喷霜:又名喷出,指混炼胶或硫化胶中的配合剂
在橡胶中的溶解度超过其饱和溶解度而迁移到 橡胶表面的现象。
有时这种喷出物呈霜状结晶物,习惯上称为喷
霜。
较多见的喷霜物是硫(溶解度低)。
高分子科学与工程学院 College of Polymer Science and Engineering
170℃ 160℃ 150℃
第2章 硫化体系02

硫黄的品种 粉末硫黄 不溶性硫黄 喷霜 硫黄的裂解和活性 纯硫黄硫化胶的结构
高分子科学与工程学院 College of Polymer Science and Engineering
一.硫黄的品种
硫黄有结晶性和非结晶性两种,常用的一般为结晶性硫黄。 硫黄有结晶性和非结晶性两种,常用的一般为结晶性硫黄。 1.粉末硫黄(powder sulfur) .粉末硫黄 在自然界中主要以硫八环的形式存在。 在自然界中主要以硫八环的形式存在。 硫八环的形式存在 在混炼胶中容易喷霜 影响粘合性能。 喷霜, 在混炼胶中容易喷霜,影响粘合性能。 2.不溶性硫黄 .不溶性硫黄(insoluble sulfur) 不溶于二硫化碳; 不溶于二硫化碳; 硫的均聚物,聚合硫; 硫的均聚物,聚合硫; 混炼胶不易喷霜,胶料的粘合性能好, 混炼胶不易喷霜,胶料的粘合性能好,是钢丝子午线轮胎 及其它橡胶复合制品的首选硫化剂。 及其它橡胶复合制品的首选硫化剂。 不溶性硫黄在热、化学物质(尤其是胺) 不溶性硫黄在热、化学物质(尤其是胺)的作用下容易转 化为可溶性硫黄。 化为可溶性硫黄。
高分子科学与工程学院 College of Polymer Science and Engineering
二.各种促进剂的结构与作用特性 各种促进剂的结构与作用特性
噻唑类 次磺酰胺类 秋兰姆类 二硫代氨基甲酸盐类 胍类 硫脲类 醛胺类
高分子科学与工程学院 College of Polymer Science and Engineering
高分子科学与工程学院 College of Polymer Science and Engineering
喷霜的危害
影响外观质量,尤其是生活用橡胶制品; 影响外观质量,尤其是生活用橡胶制品; 降低制品表面的粘着性, 降低制品表面的粘着性,影响胶料半成品的 贴合成型。 贴合成型。
橡胶中dcp硫化体系的作用_解释说明以及概述

橡胶中dcp硫化体系的作用解释说明以及概述1. 引言1.1 概述橡胶作为一种重要的材料,在工程和日常生活中有广泛的应用。
为了提高橡胶的性能和满足特定需求,研究人员一直在寻找适当的添加剂和新的硫化体系。
dcp (二苯基二异丙基氧化锆)硫化体系是近年来在橡胶领域中受到广泛关注的一种。
它被证明可以有效改善橡胶的物理性能、耐热性和耐老化性等方面。
1.2 文章结构本文将对橡胶中dcp硫化体系的作用进行详细解释和说明。
首先,我们将简要介绍dcp硫化体系的基本原理和作用机理。
然后,我们将论述该硫化体系在橡胶材料中的具体应用,并分析其对橡胶物理性能改善的影响。
最后,我们将探讨该硫化体系对橡胶耐热性、耐老化性等方面的影响,并总结其在橡胶领域中的作用和意义。
1.3 目的本文旨在全面了解并解释橡胶中dcp硫化体系的作用,并阐述其在橡胶领域中的应用前景和发展方向。
通过对该硫化体系的深入研究,我们可以更好地理解它对橡胶性能的影响,为橡胶工业提供技术支持和指导。
同时,通过展望未来的研究方向和应用前景,我们可以为相关领域的科学家和工程师提供一些建议和启示。
2. 橡胶中dcp硫化体系的作用2.1 dcp硫化体系简介橡胶是一种重要的弹性材料,用于制造各种制品,例如轮胎、密封件和鞋底等。
而硫化是橡胶加工中常用的一种方法,其中dcp(二氧化二己基三苯基膦硫酸钼)是一种广泛使用的硫化剂。
dcp硫化体系由dcp硫化剂及其辅助物质组成,能够在适当的温度和时间下促使橡胶分子间形成交联结构,从而提高橡胶制品的物理性能。
2.2 dcp硫化体系的作用机制dcp硫化剂在橡胶中起到催化剂的作用。
它能够通过与橡胶中的双键进行反应,将双键之间形成交联结构。
当dcp加入到橡胶中后,在适当的温度下发生热分解,生成自由基,并与橡胶中存在的双键进行反应。
这些自由基会引发链式反应,将相邻分子连接起来形成交联网状结构,从而增加了橡胶材料的强度和硬度。
此外,dcp硫化剂还可以通过氧化作用,将部分橡胶链上的疏松结构形成更为紧密的网络结构,从而提高橡胶制品的耐磨性、耐油性和耐老化性。
有效硫磺硫化体系

有效硫磺硫化体系有效硫磺硫化体系是指在一定的条件下,硫磺和其他物质发生反应生成硫化物的化学反应体系。
硫磺是一种常见的元素,其具有较高的反应活性和广泛的应用领域。
本文将对有效硫磺硫化体系进行探讨,并介绍其在冶金、化工、医药等领域的应用。
在冶金领域,有效硫磺硫化体系被广泛应用于矿石的硫化浸出过程。
硫磺可以与金属矿石中的硫化物发生反应,生成相应的硫化金属。
例如,在铜矿的浸出过程中,可以使用硫磺与铜矿中的硫化铜反应,生成硫化铜,从而实现铜的提取。
这种反应具有高效、低成本、易操作等优点,因此得到了广泛的应用。
在化工领域,有效硫磺硫化体系可以用于合成有机硫化物。
硫磺可以与醇、酚、胺等有机物反应,生成相应的硫化物。
这些硫化物具有较高的稳定性和活性,在橡胶、塑料、染料等领域有着重要的应用。
例如,通过硫磺与乙醇反应,可以合成乙硫化物,用于橡胶的硫化改性。
这种方法具有简单、高效、环保等特点,因此在化工生产中得到了广泛应用。
在医药领域,有效硫磺硫化体系被用于制备硫化药物。
硫磺可以与一些有机化合物反应,生成硫化药物。
这些硫化药物具有一定的药理活性,可以用于治疗一些疾病。
例如,硫磺与二苯胺反应,可以得到硫化二苯胺,该化合物具有抗菌、抗炎等作用,常用于皮肤病的治疗。
这种制备方法简单、高效,因此在医药领域得到了广泛应用。
总结起来,有效硫磺硫化体系是一种重要的化学反应体系,具有广泛的应用领域。
在冶金、化工、医药等领域,通过硫磺与其他物质的反应,可以合成硫化物、有机硫化物、硫化药物等。
这些产物具有重要的应用价值,为相关行业的发展提供了有力的支持。
随着科学技术的不断进步,对有效硫磺硫化体系的研究将会更加深入,其应用领域也将不断拓展。
EPDM硫化体系

性,喷霜就会减轻或不喷霜,如配方A促进剂BZ使用多达 1 5 份仍不喷霜,从结
构上看,TMTD比TRA更易造成EPDM硫化胶喷霜,配方 7 快速喷霜能说
明这一点;喷霜还会由促进剂间相互作用引起,如配方 6,各种促进剂用量都不算
大,但硫化胶却喷霜。总而言之,喷霜首先由配合剂结构决定,与胶料不相容的配
合剂易喷霜;其次,配合剂间的相互作用既可以减少也可能加剧喷霜;再者,胶料
炼胶抗焦烧而且硫化速度快。使用了DM,CZ的配方 8,9,10,11,12 有较长的
t10,配方 10,12 相比,不需要很多CZ即可达到延长t10 的目的,一般情况下 0
5 份DM或CZ就足够了,配方 10,11 可以证明;若超速或超超速的促进剂用量
比较大时,应适当增加DM或CZ的用量,如配方 3 的t10 就较小;DM与CZ
很容易造成喷霜。配方 12 使用了 5 7 份的促进剂,仅硫化特性比较好,而物理机
械性能并不十分突出。ZBPD为新型的进口EPDM专用促进剂,与市场上常
用的EG-3(数种超速促进剂复合物)一样有硫化速度快、交联密度大、不易喷
霜等特点,但某些物理机械性能不佳。ZBPD可能是一种相对分子量很大的促
进剂,它需要较高用量才有较好的效果。对比配方 9,10,有效硫含量相同时,用 0 .1
作用机理又有所不同,配方设计时应加以区分。仅从物理机械性能来看,配方
2,3,10,11 硫化胶的拉伸强度大,撕裂强度高,拉断伸长率高,拉断永久变形低,
综合性能好。
2. 3 各硫化体系对EPDM硫化胶喷霜的影响/VwhX W
配方 5,7 硫化结束后立即喷霜,配方C,D在室温、阴凉处搁置两天后
喷霜,配方D喷霜很轻微,配方 6,9 经加速喷霜实验后才喷霜。配方 9,10 的主要
- 1、下载文档前请自行甄别文档内容的完整性,平台不提供额外的编辑、内容补充、找答案等附加服务。
- 2、"仅部分预览"的文档,不可在线预览部分如存在完整性等问题,可反馈申请退款(可完整预览的文档不适用该条件!)。
- 3、如文档侵犯您的权益,请联系客服反馈,我们会尽快为您处理(人工客服工作时间:9:00-18:30)。
压缩变形
耐老化性 溶解性 自粘性 电性能 适用温度范围 致密性 耐磨性 耐介质性 硬度
大
差 溶解 有 相同 狭 低 低 差 低
小
好 溶胀 无 相同 广 高 高 好 高
二、硫化发展历史
1839年,Goodyear发明硫化。硫化体系组成:S 1844年,发现无机促进剂碱式碳酸铅、碱金属氧化物 等 硫化体系组成:S+无机促进剂,使用半个世 纪。 1906年,发现有机促进剂苯胺。 1921年,发现ZnO有活化作用,取代碱金属氧化物。 1926年,发现硬脂酸(SA)能提高ZnO的活化作用。 之后,有机促进剂品种不断更新,促进速度越来越快。 经过100多年的发展,逐步形成了不同的硫磺硫化体 系,如CV、SEV、EV体系等。1978年出现EC(平衡) 体系。 后发现,硫化剂除硫磺外,还有其他品种如过氧化物、 树脂、有机胺、金属氧化物等也可以使橡胶硫化,开 发了非硫硫化体系。
3、按促进速度分类: 以促进剂M对NR的促进速度为标准进行比较。 硫脲类 慢速促进剂 醛胺类 中速促进剂 胍类 噻唑类 二硫代磷酸盐类 次磺酰胺类
促 进 剂
准速促进剂
超速促进剂
超超速促进剂
秋兰姆类
二硫代氨基甲酸盐类 黄原酸盐类
焦烧
焦烧是 一 种超前硫化行为,即在硫化前 的各项工序 ( 炼胶、胶料存放、挤出、 压延、成型)中出现的提前硫化现象, 故也可称为早期硫化。
用硫磺硫化的SBR、
d以后部分,相当于硫化反 应中网络形成的后期,存在 现这一现象。 交联键的重排、交联键和链 曲线下降,网络裂解所 段的热裂解反应。不同的胶 致,NR的普通硫磺硫化 料,表现不同。 是最典型的例子。 NBR、EPDM等都会出
焦烧阶段:操作焦烧A1+剩余焦烧A2,硫化历程图,一般从A2开始。
加强炼胶及后续工序中对胶料的冷却措施,主要通
四 硫化促进剂
促进剂:凡是加入胶料后能够加快硫化反应速度,缩短硫化 时间,降低硫化温度的物质都称为硫化促进剂。
(一)促进剂分类
1、按化学结构分类:
噻唑类: M、DM、MZ
二硫代磷酸盐类:TP、ZDT、ZBTP 秋兰姆类:TMTM、TMTD、TETD、TRA、TBzTD 二硫代氨基甲酸盐类:ZDC(EZ)、BZ、ZDMC(PZ)、PX 黄原酸盐类:ZIX(已基本淘汰) 次磺酰胺类:AZ、CZ、DZ、NOBS、NS、MDB、DIBS
3.硫黄 由于它具有不溶于橡胶的特点,因此在胶料中 不易产生早期硫化和喷硫现象,无损于胶料的 粘性,从而可剔除涂浆工艺,节省汽油、清洁 环境。在硫化温度下,不溶性硫黄转变为通常 的硫黄以发挥它对橡胶的硫化作用。一般用于 特别重要的制品,如钢丝轮胎等。
喷硫产生的原因及解决办法
原因:当在混炼操作中加入硫黄时,因混炼温 度过高或混炼不均匀,硫黄在胶料中或局部 胶料中会有较多的溶解。在混炼胶停放时, 由于胶料中或局部胶料中的硫黄溶解量超过 其在室温下的饱和溶解极限或过饱和溶解极 限,就会从胶料中结晶析出,造成喷硫现象。 此外,由于硫黄配合量不当或严重欠硫,也 会造成制品喷硫。 解决办法:硫黄宜在尽可能低的温度下混入, 在胶料中配用再生胶;加硫黄之前先加入某 些软化剂,使用槽法炭黑;硫黄和硒并用等 均能减少喷硫现象,而采用不溶性硫黄是消 除喷硫的最可靠方法。
交联重排、裂解、主链改性 硫化胶
促进剂
诱 导 期 阶 段
活化剂 硫磺
第三阶段:网络形成阶段
此阶段的前期交联反应
促进剂多硫化合物 橡胶 橡胶分子链的多硫化合物 分解 自由基(或离子) 橡胶
已趋完成,初始形成的
交联键发生短化、重排
交联 反应 阶段
交联反应
网络 形成 阶段
和裂解反应,最后网络
趋于稳定,获得性能稳
(3)平坦硫化阶段
cd段,相当于网络形成的前期,这时交联反应已 基本完成,继而发生交联键的重排、裂解等反应。 交联、裂解同时存在,达到平衡,出现平坦区,对 应平坦硫化时间,其长短取决于胶料配方,主要是促 进剂和防老剂。
胶料具有最佳综合性能,在该区选取正硫化时间
4、过硫化阶段
曲线继续上升,结构化作 用所致,通常非硫磺硫化 的SBR、NBR、CR、 EPM等都可能出现这种现 象 保持较长平坦期,通常
硫化体系
硫化基本概念 硫化发展历史 硫化剂 硫化促进剂 硫化活性剂 防焦剂 抗返还剂
1.硫化的定义 硫化是指橡胶的线性大分子链通过化学交联而构成 三维网状结构的化学变化过程
2、橡胶硫化前后的性能变化 橡胶硫化后,其绝大数物理机械性能和化学性 能发生了变化表1-1 硫化前后橡胶物理机械性 能和化学性能的变化
硫脲类:NA-22、DETU 醛胺类:H、AC 胍类:D(DOPG)、DOTG
2、按酸碱性分类:
噻唑类 二硫代磷酸盐类 秋兰姆类 二硫代氨基甲酸盐类 黄原酸盐类 中性促进剂(N)
酸性促进剂(A) 促 进 剂
次磺酰胺类
硫脲类 醛胺类 胍类
碱性促进剂(B)
酸性促进剂:本身显酸性,或与H2S反应生成酸性物质的促进剂。 碱性促进剂:本身显碱性,或与H2S反应生成碱性物质的促进剂。 中性促进剂:本身显中性,或与H2S反应生成酸性和碱性物质的促进剂。
产生焦烧现象的原因:
(1)配方设计不当,硫化体系配置失衡,硫化剂、促进剂 用量超常。 (2)对某些需要塑炼的胶种,塑炼未达要求,可塑性太 低,胶质过硬,导致炼胶时急剧升温。炼胶机或其它 辊筒装置(如返炼机、压延机)辊温太高,冷却不够, 也可能导致现场焦烧。 (3)混炼胶卸料时出片太厚,散热不佳,或未经冷却,即仓 促堆积存放,加上库房通风不良、气温过高等因素,造 成热量积累,这样也会引发焦烧。 (4)胶料存放过程中管理不善,在剩余焦烧时间用尽之
2.含促进剂、硫磺的橡胶硫化历程:
促进剂
诱 导 期 阶 段
活化剂 硫磺
第一阶段:诱导阶段
先是硫磺、活化剂、促进 剂相互作用,使活化剂在 胶料中溶解度增加,活化 促进剂,使促进剂与硫磺 之间反应生成一种活性更 大的中间产物;然后进一 步引发橡胶分子链产生可 交联的橡胶大分子自由基。
促进剂多硫化合物 橡胶 橡胶分子链的多硫化合物 分解 自由基(或离子) 橡胶
硫黄硫化体系、有效、半有效硫化体系
传统硫化体系 (CV)也称普通(常规)硫化体系。是 指目前生产中常采用的常硫量(硫黄用量2~3 份)的硫黄—促进剂—活性剂体系。此体系硫 化胶的拉伸强度高,耐磨性和抗疲劳龟裂性好, 但耐热老化性能差。 这种硫化体系成本低,性能尚能满足一般制品的 要求,而且加工安全性较好,不易发生焦烧。 有效硫化体系(EV)这种硫化体系有两种,一种是 低用量的硫黄(0.3~0.5份)+高用量的促进剂 (3.0~5.0份);另一种是不用硫黄而采用高用量 的高效硫载体作为硫化剂,例如二硫化四甲基 秋兰姆(TMTD)3~3.5份或N,DTDM1.5~3份 等,为增加体系活性,也可与促进剂配合使用。
交联 反应 阶段
交联反应
网络 形成 阶段
交联重排、裂解、主链改性 硫化胶
促进剂
诱 导 期 阶 段
活化剂 硫磺
第二阶段:交联反应阶段
可交联的自由基或
促进剂多硫化合物 橡胶 橡胶分子链的多硫化合物 分解 自由基(或离子) 橡胶
离子与橡胶分子链
产生反应,生成交 联键。
交联 反应 阶段
交联反应
网络 形成 阶段
后,仍堆放不用,出现自然焦烧。
焦烧的危害:
加工困难;影响产品的物理 性能及外表面 光洁平整度;甚至会导致产 品接头处断开 等情况。
预防焦烧的方法:
胶料的设计要适宜、合理,如促进剂尽可能采取多 种并用方式,或者采用次磺酰胺类。 为适应高温、高压、高速炼胶工艺,在配方中还可 配用适量(0.3~0.5份) 的防焦剂。
三 硫化剂
1.硫化剂定义:在一定条件下,能使橡胶发生硫化 (交联)的化学物质统称为硫化剂(或交联剂)。 2.硫化剂的种类 2.1硫黄硫化体系 硫、硒、碲(硫黄硫化体系) 含硫化合物 2.2 非硫黄硫化体系 过氧化物 醌类和马来酰亚胺 树脂类化合物 金属氧化物 有机胺类硫化剂 其他类型硫化剂
3.硫黄 普通硫黄是将硫黄块粉碎筛选而得。其粒子平 均直径15~20μm,熔点114—118℃,相对密 度1.96~2.07在橡胶中的溶解度随温度的升高 而增大,当温度降低时则呈过饱和状态,过量 的硫黄会析出胶料表面形成结晶,这种现象叫 做喷硫。 不溶性硫黄 是将硫黄粉加热至沸腾(444.6℃), 倾于冷水中急冷而得的透明、无定形链状结构 的弹性硫黄。亦可将过热硫黄蒸气用惰性气体 稀释,喷在冷水雾中冷却至90℃以下制得,或 将硫黄块溶于氨中立即喷雾干燥获得。因大部 分(65~95%)不溶于二硫化碳,故称不溶性硫 黄。
交联重排、裂解、主链改性 硫化胶
定的硫化胶。
3.硫化历程图
根据硫化历程分析,可分四个阶段,即焦烧阶段、热硫化阶段、平坦硫 化阶段和过硫化阶段。
(1) 焦烧阶段
ab段,相当于硫化反应中的诱导期,对应焦烧时
间。焦烧时间的长短是由胶料配方所决定的,其中 主要受促进剂的影响,胶料在操作过程中的受热历 程也是一个重要影响因素。
热硫化阶段:交联反应,斜率表征热硫化速度。
硫化平坦阶段:交联、重排、裂解等动态平衡阶段,长度表征材料的 热稳定性 过硫化阶段:过交联和过裂解阶段,形状表征橡胶种类和硫化类型。
Байду номын сангаас
理想的橡胶硫化曲线
较为理想的橡胶硫化曲线应满足下列条件: (1)硫化诱导期要足够长.充分保证生产加工的安全性; (2)硫化速度要快,提高生产效率,降低能耗; (3)硫化平坦期要长。 要实现上述条件,必须正确选择硫化条件和硫化体系。目前比 较理想的是迟效性的次磺酰胺类促进剂的硫化体系。理想的硫化 曲线如下图所示。