型腔电火花加工精度问题
电火花加工常见的异常问题及分析
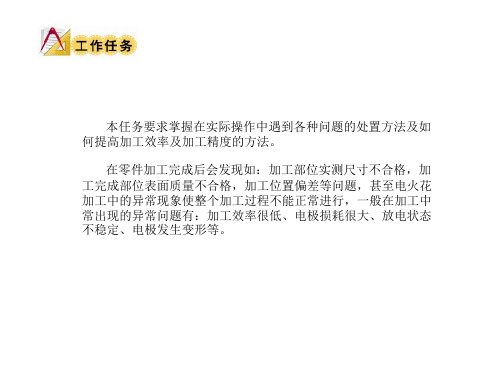
3.选用合理的电极材料.
电极材料的选取直接关系到放电加工的效果。在很大程度上,材 料的选取是否恰当,决定了放电速度、加工精度及表面粗糙度的最终 情况。应根据不同类型模具加工的实际需求,有针对性地进行电极材 料的选用。
⑴ 紫铜做电极较容易获得稳定的加工状态,可获得轮廓清晰的 型腔,表面粗糙度值低,适合低损耗的加工条件,但不适合大电流加 工,生产率不高。
3.放电状态不稳定。
放电状态不稳定这种情况是在加工过程中能够发现的 异常现象,应该及时处理,以免造成影响加工质量的后果。 放电状态不稳定时会有一系列相应表现,如火花颜色红亮, 冒白烟,声音低而闷,放电集中于一处,电流、电压表表 针不均匀急速摆动,伺服百分表指针来回摆动等。 发现这些情况时,应先考虑电参数的影响,如放电时间是 否过长,排渣高度是否不够,电流、脉冲宽度是否过大, 脉冲间隙是否过小等。其次应考虑加工部位是否存在杂物、 毛刺。再次应考虑冲油压力和方式的选用是否合理。
4.电参数调节因素的影响。
电参数调节直接关系到加工中实际火花位的大小。更改电参数 条件的各项均会影响火花间隙的大小。对火花间隙影响最明显的是 电流,随着电流的增大火花间隙也相应增大。脉冲宽度的影响也是 如此。脉冲间隙的增大会使火花间隙变小,但作用不是很明显。其 它相关参数也在间接地影响火花位的大小。因此在调节电参数时一 定要选用合理,更改电参数时要弄清楚会对加工尺寸产生的影响。
2.电极损耗很大。
电极损耗过大时会严重影响加工部位的仿形精度、尺寸精度。应 正确分析引起电极损耗很大的原因。 ⑴ 电规准中脉冲宽度是控制电极损耗的主要参数,在电极损耗大的 情况下应该考虑选用的脉冲宽度值是否太小。 ⑵ 在精度要求很高的情况下应考虑选用的电极材料能否达到低损耗 加工要求。 ⑶ 检查加工的正负极性是否接反。 ⑷ 在小电极加工时是否因为加工电流过大引起损耗过大。 ⑸ 冲油压力,流速过大也会引起电极局部损耗过大,应适当调整。
电火花加工精度的改善措施

汇报人: 2024-01-02
目录
• 电火花加工原理及精影响因 素
• 提高电火花加工精度的措施 • 新技术在电火花加工中的应用 • 电火花加工精度改善的实践与
展望
01
电火花加工原理及精度影响因 素
电火花加工原理简介
电火花加工是一种利用电火花放电产生的高温来去除材料的加工方法。在加工过 程中,工具电极和工件之间产生瞬时的高电压和高温,导致工件材料的熔化和汽 化,最终实现材料的去除。
02
减小放电间隙的方法包括优化电 参数、改进工作液循环系统和提 高电极材料质量等。
优化电极的损耗
电极的损耗会影响加工精度和表面质 量,因此优化电极的损耗是提高加工 精度的关键措施之一。
优化电极损耗的方法包括选择合适的 电极材料、减小电极截面尺寸和采用 电极修整技术等。
选用合适的加工液
加工液的选用对电火花加工精度和表面质量有重要影响。选 用合适的加工液可以减小工件表面粗糙度和提高加工精度。
案例二
在某大型模具的电火花加工中,采用 先进的数控技术,实现了高精度、高 效率的加工,提高了模具的成品率和 使用寿命。
案例三
针对某航空零件的电火花加工,通过 引入先进的误差补偿技术,有效减小 了加工误差,提高了零件的几何精度 和表面质量。
未来研究方向与展望
研究方向一
深入研究电火花加工过程的物理机制和数学模型,为进一步提高加工 精度提供理论支持。
加工参数的选择
工作液的选用
加工参数的选择对加工精度和表面质量有 很大影响,需要根据实际情况选择合适的 加工参数。
工作液的选用对电火花加工精度和表面质 量有较大影响,需要选择合适的工作液, 以保证加工精度和表面质量。
电火花加工中的加工深度和精度控制
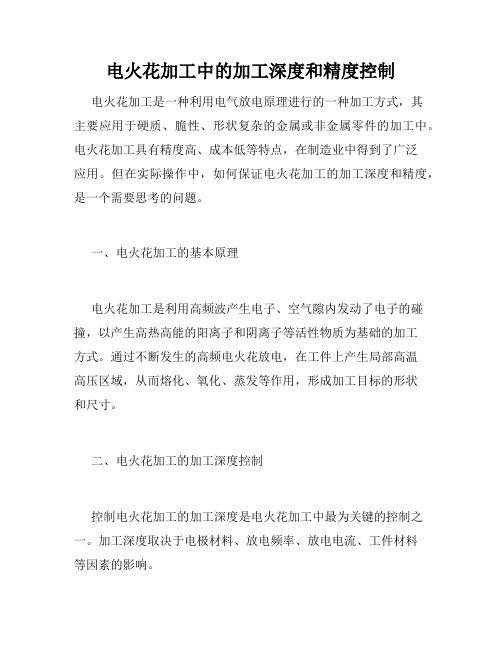
电火花加工中的加工深度和精度控制电火花加工是一种利用电气放电原理进行的一种加工方式,其主要应用于硬质、脆性、形状复杂的金属或非金属零件的加工中。
电火花加工具有精度高、成本低等特点,在制造业中得到了广泛应用。
但在实际操作中,如何保证电火花加工的加工深度和精度,是一个需要思考的问题。
一、电火花加工的基本原理电火花加工是利用高频波产生电子、空气隙内发动了电子的碰撞,以产生高热高能的阳离子和阴离子等活性物质为基础的加工方式。
通过不断发生的高频电火花放电,在工件上产生局部高温高压区域,从而熔化、氧化、蒸发等作用,形成加工目标的形状和尺寸。
二、电火花加工的加工深度控制控制电火花加工的加工深度是电火花加工中最为关键的控制之一。
加工深度取决于电极材料、放电频率、放电电流、工件材料等因素的影响。
1、电极材料电极材料的选择会对加工深度产生一定的影响,正常情况下,电极材料较软时,加工深度较小;电极较硬时,加工深度较深。
一般来说,电极材料应该尽量选用成分稳定、均匀的高温材料,如铜、银、钨等。
2、放电频率放电频率是指每秒钟反复发生的电火花放电次数,也是影响加工深度的因素之一。
放电频率越高,对工件的加工深度影响越小。
3、放电电流放电电流越大,加工深度越大。
但在实际应用中,过大的电流对电极的消耗也会变大,同时也会导致工件表面的粗糙度增加。
4、工件材料工件材料也是影响加工深度的因素之一。
一般来说,工件硬度越大,加工深度就会越小。
同时,工件的导热性能也会影响加工深度。
导热性差的工件可以通过提高工件表面温度,从而使电火花的能量有效地转移到加工目标上,提高加工深度。
三、电火花加工的加工精度控制除了加工深度的控制外,电火花加工中还需要控制其加工精度,从而保证加工质量的稳定性和一致性。
1、电极材料电极材料对加工精度的影响也非常大。
一般来说,使用高稳定性的电极能有效地保证加工精度。
2、放电电流和电压放电电流和电压的稳定控制是保证加工精度的重要手段。
电火花加工精度的改善措施
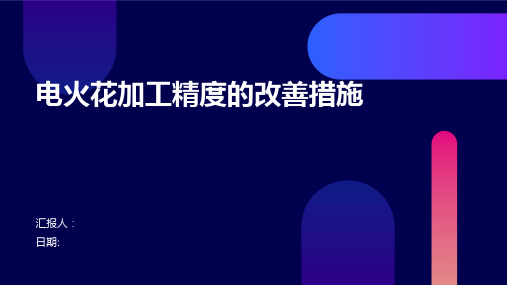
引入先进控制技术
加强工艺研究和经验积累
如模糊控制、神经网络等,实现加工过程 的实时监测和智能调整,进一步提高加工 精度和效率。
深入研究电火花加工过程中的各种影响因 素,总结和积累实践经验,不断完善和优 化加工工艺。
未来研究方向和挑战
复合加工技术研究 将电火花加工与其他加工方法相 结合,形成复合加工技术,以进 一步提高加工精度和效率。
采用高精度滚珠丝杠、直线导轨等传动元件,确保机床各轴的高精度运
动。
03
控制系统升级
采用高性能数控系统,实现加工过程的精确控制,提高加工精度和稳定
性。同时,引入先进的自适应控制算法,实时调整加工参数,以应对不
同工况下的加工需求。
04
实施措施与效果验证
改善措施的实施计划
1. 设备升级与更新
2. 优化加工工艺参数
加工能量控制
放电能量的大小和持续时间直接 影响到工件的去除速度和加工精 度。
加工精度的重要性
01
02
03
产品质量
高精度的电火花加工能确 保产品几何形状和尺寸精 度符合设计要求,提高产 品质量。
性能保障
精确的加工能减少工件表 面的损伤和残余应力,保 障产品的力学性能和稳定 性。
降低成本
提高加工精度可以减少废 品率和返工率,降低生产 成本。
。
工作液选择
选择合适的工作液,如煤油、去离 子水等,以改善放电条件,提高加 工稳定性和精度。
加工速度调整
在保证加工精度的前提下,适当提 高加工速度,以实现高效高精度电 火花加工。
增强机床精度和稳定性
01
机床结构设计优化
采用高刚度、低热变形的机床结构,减少加工过程中的振动和变形,提
电火花加工质量问题分析及对策(1)
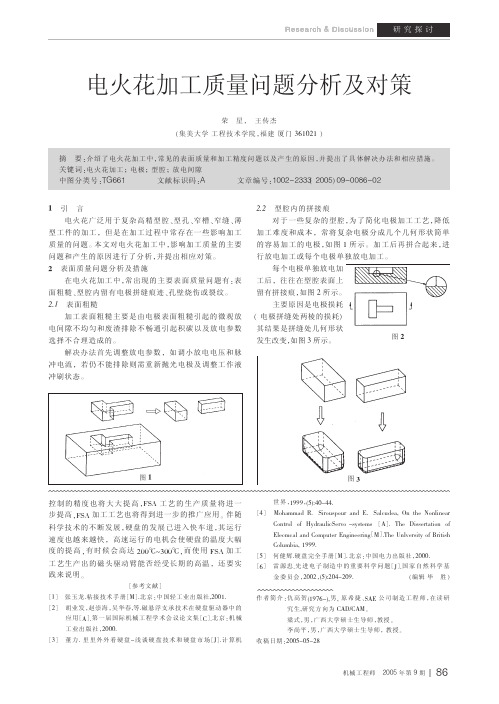
应用##$$第 一届 国际 机械 工程学 术会 议论 文集 #+$$北京%机 械 工 业 出 版 社 !$%%%’ #&$ 董 力’ 里 里 外 外 看 硬 盘%浅 谈 硬 盘 技 术 和 硬 盘 市 场 #,$’计 算 机
+4?E;4A 4G HI8;6<A:B"C;J4 3=I=EC7= ##$’ K5C L:==C;E6E:4? 4G
#2$ (4567768 9$ ":;4<=>4<; 6?8 @$ "6AB<8C6) D? E5C F4?A:?C6;
世 界 !*--- !./012%322’
!!!!!!!!!!!!!!!!!!!!!!!!!!!!!!!!!!!!!!!!!!!!!!!!!!!!!!!!!
!!!!!!!!!! 作 者 简 介 %仇 高 贺.*-TQ3S)男) 原 希 捷 ("#@ 公 司 制 造 工 程 师 !在 读 研
究生)研究方向为 +#LU+#(" 梁式!男!广西大学硕士生导师!教授" 李尚平!男!广西大学硕士生导师! 教授" 收 稿 日 期 %$%%/3%/3$V
金 委 员 会 !$%%$ !R/S1$%23$%-’
加工表面粗糙主要是由电极表面粗糙引起的微观放 电间隙不均匀和废渣排除不畅通引起积碳以及放电参数 选择不合理造成的"
解决办法首先调整放电参数! 如调小放电电压和脉 冲电流! 若仍不能排除则需重新抛光电极及调整工作液 冲刷状态"
电火花加工质量问题分析及对策
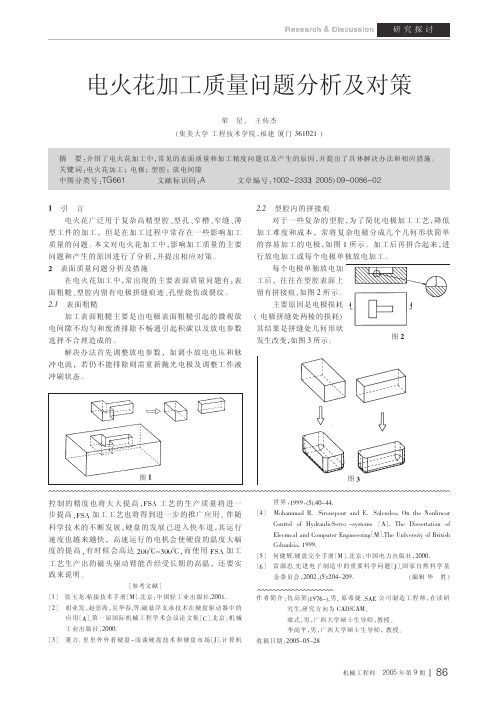
!!!!!!!!!! & #%&"’’ ! 男 ! 讲师 ! 主要从事模具设计加工 # 数控 加工 作者简介 $ 荣星
等方面的工作 " 收稿日期 $$%%*+%0+%’
!"
机械工程师
!""# 年第 ! 期
何健辉 ’ 硬盘完全手册 #( $’ 北京 % 中国电力出版社 !$%%%’ 雷 源 忠 ’ 先 进 电 子 制 造 中 的 重 要 科 学 问 题 # , $’ 国 家 自 然 科 学 基 金委员会 !$%%$ !R/S1$%23$%-’ & 编辑 毕 胜’
!!!!!!!!!!
作 者 简 介 % 仇 高 贺 .*-TQ3S) 男 ) 原 希 捷 ("#@ 公 司 制 造 工 程 师 ! 在 读 研 究生 ) 研究方向为 +#LU+#( " 梁式 ! 男 ! 广西大学硕士生导师 ! 教授 " 李尚平 ! 男 ! 广西大学硕士生导师 ! 教授 " 收稿日期 %$%%/3%/3$V
# 参考文献 $ ## $ #$ $ 张玉龙 ’ 粘接技术手册 #( $’ 北京 % 中国轻工业出版社 )$%%*$ 胡业发 ! 赵崇海 ! 吴华春 ) 等 $ 磁悬浮支承技术在硬 盘驱 动器 中的 应用 ## $$ 第 一届 国际 机械 工程学 术会 议论 文集 #+ $$ 北京 % 机 械 工业出版社 !$%%%’ #& $ 董 力 ’ 里 里 外 外 看 硬 盘 % 浅 谈 硬 盘 技 术 和 硬 盘 市 场 #, $’ 计 算 机 #/ $ #Q $
图#
"
表面质量问题分析及措施 在电火花加工中 ! 常出现的主要表面质量问题有 % 表
电火花加工技术在模具加工中精度问题分析及对策
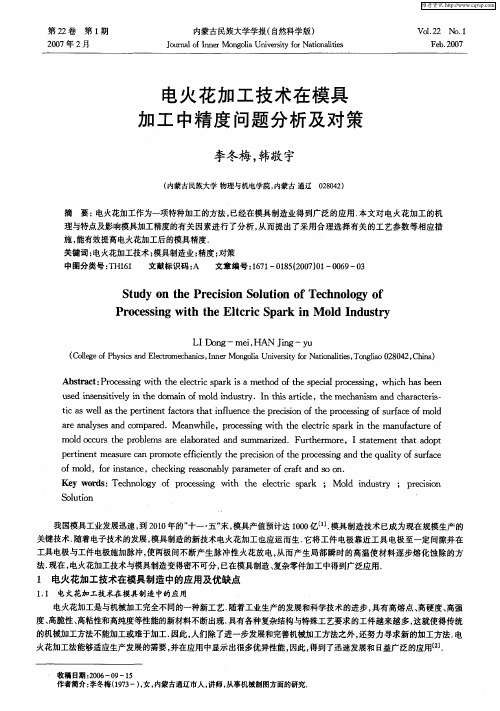
20 0 7年 2月
电火 花加 工 技 术在 模具 加 工中精度 问题分析及对策
李冬梅 , 韩敬宇
( 内蒙古民族大学 物理 与机电学院 , 内蒙古 通辽 084) 202
摘
要 :电火花加工作为一项特种加工 的方法 , 已经在模具制造业得 到广泛 的应用 . 本文对 电火 花加工 的机
理与特点及影 响模具加工精度 的有关 因素进行 了分析 , 从而提 出了采用 合理选择 有关 的工艺参 数等相应措 施, 能有效提高电火花加工后的模具 精度 .
电火花加工是 与机械加工完全不 同的一种新工艺 . 随着工业生产的发展和科学技术 的进步 , 具有高熔点 、 高硬度、 高强
度、 高脆性、 高粘性和高纯度等性能的新材料不断出现. 具有各种复杂结构与特殊工艺要求的工件越来越多, 这就使得传统 的机械加工方法不能加工或难于加工. 因此, 人们除了进一步发展和完善机械加工方法之外, 还努力寻求新的加工方法. 电
工具电极与工件电极施加脉冲, 使两极间不断产生脉冲性火花放电, 从而产生局部瞬时的高温使材料逐步熔化蚀除的方
法 . , 花加工技术与模具制造 变得密不可分 , 现在 电火 已在模具制造 、 复杂零件加工 中 到广泛应用 . 得
1 电火花加工技术在模具制造中的应用及优缺点
11 电火花加工技术在模 具制造 中的应用 .
用电火花加工时其加工精度受机床夹具电极放电参数放电环境等诸多因素影响仅电极而言其尺寸精度和相对于型腔的位置精度直接影响放电型腔的尺寸精度如果设计电极时只考虑电极的尺寸精度而忽略电极在型腔加工中的位置精度和校正电极的基准势必造成型腔尺寸误差和位置误差因此设计加工电极时不仅要考虑电极的尺寸精度还要考虑电极放电时的位置精度以及确定电极在xyz三轴方向校正基准以便在电火花加工前校正电极的正确位置和状态否则直接影响放电后型腔的形状和尺寸
数控电火花成型加工质量问题分析及对策
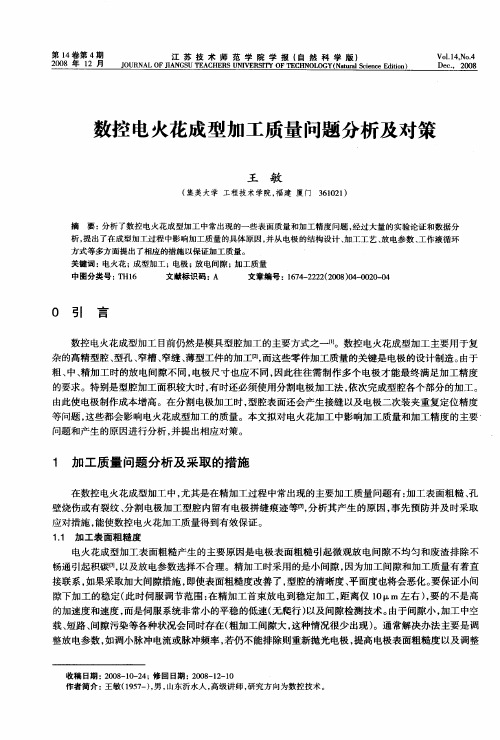
拼合 电极或每个电极单独放电加工后 , 往往在型腔表面上留有拼接痕迹 , 如图 2 所示。 拼接痕迹产生
的主要 原因是 电极损耗 ( 电极 拼缝处 两棱 的损耗 ) 电极 损耗是 由于 在加工过 程 中 , 电发 生在 电极端 部 。 放 前沿尖 角处 , 电流密度 较大 , 放电集 中度高 。严重 的 电极 损耗 现象会 造成 电极 拼缝处 几何形 状发 生改 变 , 如图 3 示。 所 电极 拼缝处 的这种几 何形状 的改 变 , 即电极拼缝 处两棱 的损耗 , 将直 接导致 该处 的放 电间隙
1薯哿 删 4 耄 R
N科 al 然 (r O Yt L 学a ON G u
。
V1o D,0 0.8 eN 12 c0 .. .4 4
数控 电火花成型 加工质量 问题 分析及对策
王 敏
( 集美大学 工程技术学院, 福建 厦 f 6 0 1 - j 12 ) 3
摘
要: 分析了数控电火花成 型加工 中常出现 的一些表面质量和加工精度问题 , 过大量 的实验论证 和数据分 经
整放 电参数 , 如调小脉冲电流或脉冲频率 , 若仍不能排除则重新抛光 电极 , 提高电极表面粗糙度以及调整
收稿 日期 : 0 8 1— 4 修 回 日期 : 0 8 1— 0 20一0 2 ; 20 — 2 1
作者简介 : 王敏( 9 7 )男 , 15 一 , 山东沂水人 , 高级讲师 , 研究方向为数控技术 。
明显增大, 使得加工过程 中该处金属无法被加工到, 最终造成拼缝处的放电加工表面上留有不规则的凸 起痕迹。采取的措施为: 在设计和加工电极时将两电极的结合部分重合 12 m左右拼接,  ̄r a 如图 4 所示 。
接联系 , 如果采取加大间隙措施 , 即使表面粗糙度改善了, 型腔的清晰度 、 平面度也将会恶化。 要保证小间
电火花机的加工不准是什么原因呢?

电火花机的加工不准是什么原因呢?电火花机加工中伴随有一系列派生现象,通过加工过程中的外在表现,可以了解加工的稳定性,发觉加工的异常放电状态。
正常加工中,察看到的火花颜色通常为蓝白色夹火红颜色,火花细小均匀。
加工液面冒无烟小气泡,听到的火花声音清脆、连续。
机床的电流、电压表呈有规律的摇摆,伺服百分表匀速进给。
加工中每次放电时间、抬刀动作有规律的持续。
电火花机深度检测值呈稳定的递进。
反之,加工中放电集中于一处,火花颜色偏红亮,液面冒白烟大气泡,火花爆炸声音低、沉闷,电流、电压表指针急剧摇摆,伺服机构急剧跳动的放电不稳定现象可判定是电弧放电的可能,这种现象常使电极、工件结炭、烧伤。
我们在使用电火花机时显现加工不准是什么原因呢?又该如何解决?一起来看看吧!1、机械故障:刀架转动不到位、刀架未锁紧、传动带打滑、转动间隙大、丝杠质量等机械故障也是引起加工尺寸偏差的紧要原因。
2、外界干扰或脉冲丢失:针对外界干扰而导致的加工尺寸不准。
可考虑从以下几方面检查、处理:四周是否存在较大干扰源,如大型的电机、大功率的变频系统、焊接机械等,让这些设备短时间停止工作后再查看情况是否有改观;检查电柜中的线缆布线,将动力电缆和掌控信号电缆尽量分开走线;掌控信号电缆是否采纳双绞屏蔽电缆、屏蔽层是否正确连接?机床接地是否有效,牢靠?3、参数调整不当:目前设备型号浩繁,不同厂家生产的数控机床的结构、所用材料也不相同。
因此,不同机械设备的惯量、刚性、负载大小、稳定性也不尽相同。
4、工艺机操作:在用户现场必需对用户的每一步操作、加工的每一道工序等进行认真查看,找出问题所在。
5、进行回零位置不准:在加工零件时,假如发觉加工尺寸存在偏差,且偏差的尺寸恰好为丝杠导程时,很大可能是由于进行回零位置不准的原因造成。
影响电火花成形加工质量的因素

影响电火花成形加工质量的因素影响加工质量的原因是多方面的,大致与电极材料的选择、电极制造、电极装夹找正、加工规准的选择、操作工艺是否恰当等有关。
要防止产生废品,应注意下列各点。
1.1正确选择电极材料在型腔加工中,石墨是常用的电极材料,但由于石墨的品种很多,不是所有的石墨材料都可作为电加工的电极材料,应该使用电加工专用的高强度、高密度、高纯度的特种石墨。
紫铜电极常用于精密的中、小型型腔加工。
在使用铸造或锻造制造的紫铜坯料做电极时,材质的疏松、夹层或砂眼,会使电极表面本身有缺陷、粗糙和损耗不均匀,使加工表面不理想。
1.2制造电极时正确控制电极的缩放尺寸制造电极是电火花加工的第一步,根据图纸要求,缩放电极尺寸是顺利完成加工的关键。
缩放的尺寸要根据所决定的放电间隙再加上一定的比例常数而定。
一般宁肯取理论间隙的正差,即电极的标称尺寸要偏“小”一些,也就是“宁小勿大”。
若放电间隙留小了,电极做“大”了,使实际的加工尺寸超差,则造成不可修废品。
如电极略微偏“小”,在尺寸上留有调整的余地,经过平动调节或稍加配研,可最终保证图纸的尺寸要求。
在型孔加工中无论是制造阶梯电极,还是用直接加工电极,由于最终要控制凸凹模具的配合间隙,因此对电极缩放尺寸的要求是十分严格的,一般应控制在±0.01mm。
1.3把好电极装夹和工件找正的第一关在校正完水平与垂直,最后紧固时,往往会使电极发生错位、移动,加工时造成废品。
因此,紧固后还要不厌其烦地再找正检查一下,甚至在加工开始进行了少量进给后,还需要停机再查看一下是否正确无误。
因为电火花加工开始阶段是很重要的一个环节,也是需要操作者最精心的时候。
由于电极装夹不紧,在加工中松动,或找正误差过大,是造成废品的一个原因。
电极或辅助夹具的微小松动,会给加工深度带来误差。
有时在多次重复加工中,加工条件相同,但深度误差分散性很大,往往也是电极松动造成的。
加工过程中夹具发热,也会使电极松动。
电火花加工精度改善措施

加工方法对比如下图
改善前后定位、加工方法对比
改 善 前
改 善 后
改善前:工件直接在磁台上定位,加工完成后再拆下测量 确认。如NG再上机重新采用千分表校正、基准球分中、加工,
加工方法对比
改善前:工件直接在磁台上定位,加工完成
后再拆下测量确认。
改善后:细小工件增加装夹辅助装置,通
过采用日本制JAM牌超微精密平口钳装夹后,在
确认。从这三方面详细论述了如何提高电火花加工精度、工艺流
程化,为公司带来的直接应用效益。
公司现状使用的数控机床均为日本高速高精度加工机,其机床相 关信息如下表2-1、图2-1所示:
机床型号 制造商
加工中心 机
V22
牧野
电火花加 工机
AQ35L
沙迪克
慢走丝线 割机
FA10PS-A
三菱
磨床 NN515-S 长岛
产地 日本 泰国 日本 中国
行程(㎜) 类型
320*280* 300
高速机
350*250* 250
高速机
350*250* 220
高精机
350*150* 250
高精机
机床加工 精度(㎜) ±0.002
±0.005
±0.005
±0.001
主要加工机图片
我们主要利用上述几款机床进行
模具相关工件的加工,用Nikon高度仪、
对位置也存在偏差。
机床的几何误差:工件的加工精度很大程度上取决于机床的精度。
包括机床的制造误差、安装误差、和磨损引起的误差。在加工过程中这
些误差会直接反映到工件上去,影响加工精度。通常的理解是,使用机
床进行加工,加工精度无法超越机床本身精度。
工艺系统的几何误差是指机床、夹具、刀具和工件的原始误差。
影响电火花加工精度的因素

影响电火花加工精度的因素影响电火花加工精度的主要因素有: 放电间隙的全都性, 工具电极的损耗及其稳定性. 电火加工时, 工具电极与工件之间存在着肯定的放电间隙, 假如加工过程中放电间隙保持不变, 则可以通过修正工具电极的尺寸放电间隙进行补偿, 以获得较高的加工精度. 然而放电间隙的大小实际上是变化的, 影响着加工精度.除了保持间隙能否全都性外, 间隙大小对加工精度也有影响, 尤其是对简单外形的加工表面, 棱角部位电场强度分布不均, 间隙越大, 影响越严峻. 因此, 为了削减加工误差, 应采纳较少的加工规准, 缩小放电间隙, 这样不但能提高仿形精度, 而且放电间隙愈小, 可能产生的间隙变化量也愈小; 另外,, 还必需尽可能使加工过程稳定. 电参数对放电间隙的影响也特别显著, 精加工的放电间隙一般只有0.01mm, 而粗加工时则为0.5mm 左右.工具电极的损耗对尺寸精度和外形精度都有影响. 电火花穿孔加工时, 电极可以贯穿型孔而补偿电极损耗, 型腔加工时则无法采纳这一方法, 精密型腔加工时可以采纳更换电极的方法.影响电火花加工外形精度的因素还有“ 二次放电”, 二次放电是指已加工表面上由于电蚀产物等的介入而再次进行的非必要的放电, 它使加工深度方向产生斜度和加工棱角棱边变顿.电火花加工时, 工具的尖角或凹角很难精确的复制在工件上, 这是由于当工具为凹角时, 工件上对应的尖角处放电蚀除的概率大,简单患病腐蚀而成为圆角. 当工具为尖角时, 一则由于放电间隙的等距性, 工件上只能加工出以尖角顶点为圆心, 放电间隙s 为半径的圆弧; 而则工具上的尖角本身因尖端放电蚀除的概率大而损耗成圆角. 采纳高频窄脉宽精加工, 放电间隙小, 圆角半径可以明显削减, 因而提高了仿形精度, 可以获得圆角半径小于0.01mm 的尖棱, 这对于加工精密小模数齿轮等冲模是很重要的.目前, 电火花加工的精度可达0.01-0.05mm, 在精密光整加工时可小于0.05mm.。
数控电火花加工常见问题解决办法!

数控电火花加工常见问题的解决办法!在工作中,电火花加工经常会遇到一些常见问题,那么如何解决呢?看完本文相信您就都懂了!1、加工效率低1)起始放电加工效率低-----电极尺寸缩放量(火花位)要大,自动编程才能选出更大电流的条件号。
型腔要尽可能进行预铣加工。
2)程序中间的放电加工段效率低-----各段条件之间的余量过多,可以适当减少各段之间的加工余量。
3)程序最后的精细放电加工段效率低-----使用定时加工功能来有效控制精加工时间(需要设定加工时间)。
4)面积输入过小-----系统以面积作为限制门槛,即使电极尺寸缩放量再大,由于面积太小,也不会产生大的放电条件。
此类情况,可以适当人为增大输入的面积值。
5)应用类型选择不正确-----比如实际是大型腔的加工而选择了“微细”应用类型。
6)加工优先权-----选择低损耗优先权则效率低,选择高效率优先权则速度快,损耗偏大。
7)放电、抬刀组合不合理-----根据加工状态,调整抬刀高度、放电时间与之匹配。
8)优化参数-----减少脉冲间隙P,加大伺服基准COMP。
9)改进工艺-----使用石墨电极,大幅度提升整体生产效率。
2、电极损耗大1)使用参数不当-----应使用优先权为低损耗的加工参数。
小电极可选用微细加工应用类型。
2)放电条件号太强-----对于尖小电极,不能使用大电流加工。
3)放电能量太小,加工效率低下导致电极长时间的放电而损耗-----如果电极损耗大的同时伴随加工速度太慢的情况,请提高加工效率。
4)电极材料不好-----使用纯度高的紫铜,或者使用损耗更低的洛铜甚至是铜钨合金作为电极材料。
5)脉冲宽度太小-----加大条件号中的脉冲宽度T,可以显著降低电极损耗。
6)脉冲波形-----使用低损耗,带有斜度的放电波形模式。
3、分中不准确,位置偏差1)使用传统的“电极碰工件进行分中”的方法,由于分中属于面接触,电极与工件之间存在的诸多因素都会影响分中精度-----推荐使用“基准球点对点进行分中”的定方法。
电火花加工精度的改善措施
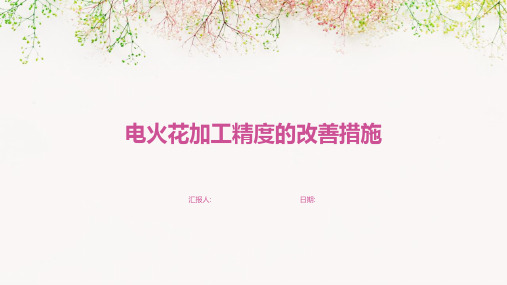
根据加工需求设置合理的补偿参数 ,如放电间隙补偿、电极丝半径补 偿等,以修正加工过程中的误差, 提高加工精度。
04
工艺参数对加工精度的影响
电火花加工参数对加工精度的影响
脉宽
脉宽的增加会导致加工速度提高,但同时也会导 致电极损耗增加,影响加工精度。
脉冲间隔
脉冲间隔的增加可以减少电极损耗,提高加工精 度,但也会导致加工速度降低。
100%
加工参数优化
通过试验和优化选择最佳的电极 加工参数,如脉冲宽度、脉冲间 隔、加工速度等。
80%
制造环境控制
保持恒温、恒湿、防震等加工环 境,减少环境因素对电极制造精 度的影响。
电极精度检测及修正方法
光学显微镜检测
使用光学显微镜对电极进行尺 寸和形状检测,观察电极表面 质量。
激光扫描检测
采用激光扫描技术对电极进行 快速、高精度的三维检测。
数控系统的编程能力
优化数控系统的编程,通过高级编程语言和自动化编程软件提高加 工精度和效率。
伺服控制系统的精度控制
伺服控制系统的选择
01
选择具有高精度、快速响应的伺服控制系统,以确保加工过程
中的精确控制。
位置反馈系统
02
采用高分辨率的位置反馈系统,提高加工精度的同时还能监控
加工过程中的误差,及时调整加工参数。
电火花修正
对于加工过程中出现的电极损 耗或变形,采用电火花修正方 法对电极进行修复。
03
数控系统及伺服控制精度
数控系统对加工精度的影响
数控系统的类型和性能
选择适合电火花加工的数控系统,如具有高精度插补、曲面加工 等功能的数控系统。
数控系统的稳定性
评估数控系统的稳定性,选择稳定性高的产品,以避免加工过程中 因系统故障而影响加工精度。
[整理版]电火花问加工题目解答
![[整理版]电火花问加工题目解答](https://img.taocdn.com/s3/m/c5349698d5d8d15abe23482fb4daa58da0111c1f.png)
1型腔模电火花加工时选择电规准的原则是什么?答:电规准的正确选择和转换,是实现低损耗、提高生产率、保证型腔加工精度和经济效益的重要环节。
一般选用宽脉冲(电极损耗ti>400us)、大峰值电流,用负极性进行粗加工;选用脉冲宽度ti=20~400us,用比粗加工小的电流密度进行中规准加工。
精加工时常采用窄的脉冲宽度(电极损耗ti<20us)和小的峰值电流进行加工。
2电解液在电解加工过程中的作用?答:1作为导电解质传递电流;2在电场作用下进行电化学反应,使阳极溶解能顺利有控制的进行;3及时地把加工间隙内产生的电解产物及热量带走,起更新与冷却作用。
3数控电火花线切割加工适合加工那些零件?答:1加工模具适合于各种形状的冲模2加工电火花成型加工用的电极3加工零件及直接切割试制新品。
4特种加工的特点是什么?答:1不是主要靠机械加工,而是主要用其它的能量(电、化学、光、声、热)去除材料2工具硬度可以低于被加工材料的硬度3加工过程中工具和工件之间不存在显著的切削力。
1电铸加工工艺的主要特点,主要用于什么类型零件的加工?答:特点:1制精度很高,可获得尺寸和形状精度要求高、花纹细致。
复杂的型腔。
2可用一个标准母模复制出多个形状一致的型腔或电铸电极,适应性广泛。
3使用设备简单、操作容易、铸成后不需热处理等。
4电铸加工速度慢、周期长、成本高。
类型:1复制精细的表面轮廓花纹,如唱片模,工艺美术品模、纸币、邮票的印刷版2复制注塑用的模具、电火花型腔加工用的电极工具。
3制造复杂、高精度的空心零件和薄壁零件,如波导管等。
4制造表面粗糙度标准样块、反光镜、表盘导形孔喷嘴等特殊零件。
2特种加工带来的变革并举例?答:1提高了材料的可加工性。
是材料的加工范围变得更广,可以加工硬质合金、超硬材料和特殊材料。
例如,对电火花、线切割加工而言,淬火钢比为淬火钢更易加工。
2改变了零件的典型工艺路线。
例如,电火花线切割加工等必须先淬火后加工。
精密模具型腔电火花加工要点!

精密模具型腔电火花加工要点!随着现代模具制造水平不断的发展,对模具制造的要求也越来越高。
许多模具制造企业的制造对象也放到了精密模具。
对于型腔模具的制造,电火花加工一直是一种比较精密的加工方法。
虽然现在可以利用高速加工中心加工型腔模具中一些精密部位,但是型腔模具中深窄小型腔,沟槽拐角,形状特殊复杂等许多地方必须由电火花加工完成,下面对电火花加工精密型腔模要点进行阐述。
电火花加工精密型腔模具的精度表现在尺寸精度、仿形精度、表面质量等 B 个方面。
加工精密型腔模具,应正确分析其各部位尺寸要求,灵活控制不同地方的尺寸精度,应特别重视那些尺寸要求高的部位,精密型腔模具中的重要尺寸公差可达±2-3μm,可见其尺寸要求的严格性。
仿形精度要求亦高,型腔应清角,棱角清楚。
表面粗糙度值均匀,并达到预定表面精糙度值,一般要求Ra值很小,甚至要求镜面加工,另外电火花加工部位表面变质层的厚度要很小。
加工精密型腔模具的要点(1)先进的精密放电设备是保证加工精度的前提。
现代模具企业使用的电火花机床一般都是数显和数控的,机床本身的精度对加工精度起着重要影响。
机床结构的力学性能,主轴和工作台的各种几何精度、数显和数控的精度都不可以忽视。
机床的加工性能尤为重要。
精密电火花加工机床加工放电稳定,火花间隙小,电极损耗小,加工速度相对快,表面质量高。
此类机床使用起来也有很多优越性,如果我们进行电极与工件的碰边时,它会产生微放电,有利于将细微杂质清除,提高定位精度,机床的积炭监控调节系统可以防止积炭,自动调节放电状态等,最先进的EFE 电火花机床可以实现五轴数控联动,并带有电极库,可以自动更换电极工具,只需事先调整好电极工具和编制好相应的程序便能自动完成加工任务。
精密的型腔模具的电火花加工必须由精密电火花机床来完成,那些传统老式的放电机床将会被淘汰。
(2)宜采用多电极加工法。
这里指的多电极加工方法是根据一个型腔在粗、半精、精加工中放电间隙不同的特点采用几个相应尺寸缩放量的电极完成一个型腔的粗、半精、精加工。
概述塑料注射模型腔的电火花成形加工情况

概述塑料注射模型腔的电火花成形加工情况注塑模(塑料注射模)的型腔多是盲孔,用一般机械加工方法难以加工出来,这时就要考虑使用电火花成形加工。
概述塑料注射模型腔的电火花成形加工情况注塑模(塑料注射模)的型腔多是盲孔,用一般机械加工方法难以加工出来,这时就要考虑使用电火花成形加工。
(1)型腔电火花成形加工的特点①型腔的加工余量一般较大,尤其是在不预加工的情况下,蚀除的金属量更多,因此,对电源的首要要求是:提高生产率和降低损耗。
②由于型腔的形状多较复杂,电极损耗引起其尺寸的变化会直接影响型腔的精度,而电极向工件的进给却受到限制,其损耗不能像电火花穿孔那样可通过电极进给获得补偿,因此要求电极的损耗应越小越好。
③型腔属于盲孔加工,其电蚀产物的排除较为困难,尤其是在型腔加工时更甚,因此在工艺上必须采用冲油或抽油式来实现排屑。
④在加工过程中,由于工艺的需要,为了侧面精加工、控制加工精度、更换或修整电极等的需要,机床应备有相应的附件(2)型腔电火花成形加工的方法①单电极平动加工。
这是采用一个电极来完成型腔的粗、中、精加工。
首先采用粗规准加工,然后利用平动头沿型腔侧面进行“仿形”加工,按照粗、中、精的顺序逐渐改变电规准。
并依次加大电极的平动量,来完成整个型腔的加工。
此法只用一个电极加工,操作简单,但难以获得高精度的型腔。
它的应用十分广泛。
②多电极更换加工。
这是采用多个电极依次更换来加工同一个型腔,每个电极加工时必须把上一规准的放电痕迹去掉。
一般用两个电极分别进行粗、精加工即可。
若型腔精度要求高,可采用更多电极进行加工。
此法加工精度高,尤适于有尖角、窄缝多的型腔加工,但它需要多个精度高的电极,机床的定位精度要求高,多用于精密型腔的加工。
③分解电极加工。
对于型腔形状比较复杂的,可把型腔分成几部分,主型腔和副型腔分别采用不同电极,先加工主型腔,再用副型腔电极加工尖角、窄缝等处。
此法加工,可根据主、副型腔不同的加工条件,选择不同的加工规准,可保证质量和提高速度。
电火花成型机加工精度受影响原因简析

电火花成型机加工精度受影响原因简析
成型机主轴头是电火花成型机床的一个关键部件,在结构上由伺服进给机构(步进电动机、直流电动机或交流伺服电动机作进给驱动)、导向和防扭机构、辅助机构三部分组成。
用以控制工件与工具电极之间的放电间隙。
主轴头的好坏直接影响加工的工艺指标,如生产率、几何精度以及表面粗糙度,因此对主轴头有如下要求:
1)有一定的轴向和侧向刚度及精度;
2)有足够的进给和回升速度;
3)主轴运动的直线性和防扭转性能好;
4)灵敏度要高,无爬行现象;
5)具备合理的承载电极质量的能力。
电火花加工机床成形加工时,主轴头最重要的附件是平动头,它是实现单电极型腔电火花加工所必备的工艺装备。
在加工大间隙冲模和零件上的异形孔时,平动头经常得到应用。
平动头包括两部分,一是由电动机驱动的偏心机构,二是平动轨迹保持机构。
通过偏心机构和平动轨迹保持机构,平动头将伺服电动机的旋转运动转化成工具电极上每一个质点都在水平面内围绕其原始位置做平面圆周平移运动(如图4.2.2所示),各个小圆的外包络线就形成加工表面,小圆的圆周半径(即平动量Δ),通过平动头偏心量来调节可由零逐步扩大,S 为放电间隙。
采用平动头加工的特点是:用一个工具电极就能由粗至精直接加工出工件(由粗加工转至精加工时,放电规准、放电间隙要减小),在加工过程中,工具电极的轴线偏移工件的轴线,这样,除了处于放电区域的部分外,在其他地方工具电极与工件之间的间隙都大于放电间隙,这有利于电蚀产物的排出,提高加工稳定性,但由于有平动轨迹半径的存在,因此,无法加工出有清角直角的型腔。
- 1、下载文档前请自行甄别文档内容的完整性,平台不提供额外的编辑、内容补充、找答案等附加服务。
- 2、"仅部分预览"的文档,不可在线预览部分如存在完整性等问题,可反馈申请退款(可完整预览的文档不适用该条件!)。
- 3、如文档侵犯您的权益,请联系客服反馈,我们会尽快为您处理(人工客服工作时间:9:00-18:30)。
三、型腔电火花加工精度问题
加工精度主要包括“仿形”精度和尺寸两个方面。所谓
“仿形”精度,是指电加工后的型腔与加工前工具电极几何形 状的相似程度。 影响“仿形”精度的因素有: 1.使用平动头造成的几何形状失真,如很难加工出清角,尖角变圆等。 2.工具电极损耗及“反粘”现象的影响。 3.电极装夹校正装置的精度和平动头、主轴头的精度以及刚性影响。 4.规准选择转换不当,造成电极损耗增大。
㈠平动头工作原理
电火花粗加工时的火花间隙比中加工的要大,而中加工的火花间隙 比精加工的又要大一些。当用一个电极进行粗加工,将工件的大部分余 量蚀除掉后,其底面和侧壁四周的表面粗糙度很差,为了将其修光,就 得改变规准逐档进行修整。由于后档规准的放电间隙比前档小,对工件 底面可通过主轴进给进行修光,而四周侧壁就无法修光了。平动头就是 为解决修光侧壁和提高其尺寸精度而设计的
㈡
平动头结构
利用偏心机构将伺服电动机的旋转运动通过平动轨迹保持 机构,转化成电极上每一个质点都能围绕其原始位置在水平面内 作平面小圆周运动,许多小圆的外包络线就形成加工表面。其运 动半径即平动量,通过调节可由零逐步扩大,以补偿粗、中、精 加工的火花放电间隙之差,从而达到修光型腔的目的。其中每个 质点运动轨迹的半径就称为平动量。
一、工艺准备
一、加工方法及平动量选择 选用单电极平动法进行电火花成型加工,为保证侧面棱角清晰(R<0.3 mm),其平动量应小,取δ ≤0.25 mm。
二、工具电极材料、结构尺寸、缩放量的确定
㈠ 电极材料选用锻造过的紫铜,以保证电极加工质量以及加工表面粗 糙度。 ㈡ 电极结构与尺寸确定。 ① 电极水平尺寸单边缩放量取b=0.25 mm,根据相关计算式可知,平 动量δ 0=0.25-δ 精<0.25 mm。 ② 由于电极尺寸缩放量较小,用于基本成型的粗加工电规准参数不宜 太大。对应的型腔主体20 mm深度与R7 mm搭子的型腔6 mm度的电极长度之 差不是14 mm,而是(20-6)×(1+1%)=14.14 mm。尽管精修时也有损耗,但 由于两部分精修量—样,故不会影响二者深度之差。
一、型腔的电火花加工方法
型腔的电火花成型加工主要有: ㈠ 单电极平动法。 ㈡ 多电极更换法。 ㈢ 分解电极法
二、数控成形机床的平动加工
平动加工方式可分为自由平动和伺服平动。自由平动即一边向 下加工,一边平动,可分为5种平动方式(○、□、◇、×、+)。伺 服平动即加工到深度后再平动,可分为圆形和二维矢量两种方式。如 图所示,为常用平动头。
㈢ 电极制造。电极可以用机械加工的方法制造,但因有两 个半圆的搭子,一般都用线切割加工,主要工序如下: ① 备料; ② 刨削上下面; ③ 画线; ④ 加工M8×8的螺孔; ⑤ 按水平尺寸用线切割加工; ⑥ 按图示方向前后转动90°,用线切割加工两个半圆及主 体部分长度; ⑦ 钳工修整。
㈣ 镶块坯料加工。 ① 按尺寸需要备料; ② 刨削六面体; ③ 热处理(调质)达38~40HRC; ④ 磨削镶块六个面。 ㈤ 电极与镶块的装夹与定位。 ① 用M8的螺钉固定电极,并装夹在主轴头的夹具上。然而用千分表(或百 分表)以电极上端面和侧面为基准,校正电极与工件表面的垂直度,并使其X、 Y轴与工作台X、Y移动方向一致。 ② 镶块一般用平口钳夹紧,并校正其X、Y轴,使其与工作台X、Y移动方向 一致。 ③ 定位,即保证电极与镶块的中心线完全重合。用数控电火花成型机床加 工时,可利用机床自动找中心功能准确定位。
影响尺寸精度的因素有: 1.操作者选用的电规准与电极缩小量不匹配,以致加工完成以 后,使尺寸精度超差。 2.在加工深型腔时,二次放电机会较多,使加工间隙增大,以 致侧面不能修光,或者即使能修光,也超出了图纸尺寸。 3.冲油管的放置和导线的架设存在问题。导线与油管产生阻力, 使平动头不能正常进行平面圆周运动。 4.电极制造误差。 5.主轴头、平动头、深度测量装置等机械误差。
五、影响模具型腔表面质量的“波纹”问题
用平动头修光侧面的型腔,在底部圆弧或斜面处易出现“细丝”及鱼 鳞状的凸起,这就是“波纹”。“波纹”问题将严重影响模具加工的表面质 量,一般“波纹”产生的原因如下: 1.电极材料的影响。如在用石墨做电极时,由于石墨材料颗粒粗、组织疏 松、强度差,会引起粗加工后电极表面产生严重剥落现象,因为电火花加工 是精确“仿形”加工,故在电火花加工中石墨电极表面剥落现象经过平动修 整后会反映到工件上,即产生了“波纹”。 2.中、粗加工电极损耗大。由于粗加工后电极表面粗糙度值很大,中、精 加工时电极损耗较大,故在加工过程中工件上粗加工的表面不平度会反拷到 电极上,电极表面产生的高低不平又反映到工件上,最终就产生了所谓的 “波纹”。 3.冲油、排屑的影响。电加工时,若冲油孔开设得不合理,排屑情况不良, 则蚀除物会堆积在底部转角处,这样也会助长“波纹”的产生。
第一篇 电火花成型加工
模块二 电火花成形机床加工
任务3 模具型腔的电火花成形加工
1.本任务要求利用单电极平动成形加工方法,通过自动编程,进行模具型腔 的电火花成形加工。 2.了解模具型腔电极的设计加工制造。 3.通过实际操作掌握单电极平动成形加工方法。
如图所示,注射模镶块,材料为40Cr,硬度为38~40HRC, 加工表面粗糙度Ra为0.8 μ m,要求型腔侧面棱角清晰,圆角半径 R<0.25 mm。 模具型腔复杂程度一般,但尺寸公差比较严格。加工采用 电火花加工型腔一次成型。为保证模具型腔尺寸的精度,重点要解决 电极的尺寸精度、电极装夹定位及校正等精度问题,模具所要求的型 腔尺寸精度和表面粗糙度可运用平动方法逐步扩大轨迹来保证。但平 动头的仿形精度要好,回零精度不应超过0.02mm。
四、型腔电火花加工粗糙度问题
电火花加工型腔模,有时型腔表面会出现尺寸到位,但修不光的现象。 造成这种现象的原因有以下几方面: 1.电极对工作台的垂直度没校正好,使电极的一个侧面成了倒斜度,这 样相对应模具侧面的上部分就会修不光。 2.主轴进给时,出现扭曲现象,影响了模具侧表面的修光。 3.在加工开始前,平动头没有调到零位,以致到了预定的偏心量时,有 一面无法修出。 4.各挡规准转换过快,或者跳规准进行修整,使端面或侧面留下粗加工 的麻点痕迹,无法再修光。 5.电极或工件没有装夹牢固,在加工过程中出现错位移动,影响模具侧 面粗糙度的修整。 6.平动量调节过大,加工过程出现大量碰撞短路,使主轴不断上下往返, 造成有的面修出,有的面修不出。
4.电极运动方式的影响。“波纹”的产生并不是平动加 工引起的,相反,平动运动能有利于底面“波纹”的消除, 但它对不同角度的斜度或曲面“波纹”仅有不同程度的减 少,却无法消除。这是因为平动加工时,电极与工件有一 个相对错开位置,加工底面错位量大,加工斜面或圆弧错 位量小,因而导致两种不同的加工效果。 波纹”的产生既影响了工件表面粗糙度,又降低了 加工精度,为此,在实际加工中应尽量设法减小或消除 “波纹”。
㈥ 电火花成型加工。所选用的电规准和平动量及其转换过程如表23-1所示。(先高效低损耗电规准进行粗加工——依次改变电规准, 加大平动量——最后使用的电极加工规准小,损耗量小)
表2-3-1 电规准转换与平动量分配
序号 1 2 3 4 5 6 7 脉冲宽 脉冲电流 度/μs 幅值/A 350 210 130 70 20 6 2 30 18 12 9 6 3 1 平均加工 电流/A 14 8 6 4 2 1.5 0.5 表面粗糙度 Ra/μm 10 7 5 3 2 1.3 0.6 单边平动 量/mm 0 0.1 0.17 0.21 0.23 0.245 0.25 端面进给 量/mm 19.90 0.12 0.07 0.05 0.03 0.02 0.01 1. 型腔深度为 20 mm,考虑 1%损 耗, 端面总进给量为 20.2 mm 2. 型腔加工表面 粗糙度 Ra 为 0.6 μm 3. 用 Z 轴数控电 火花成型机床加工 备 注
㈢
平动头作用
1.机械式平动头能够补偿加工中电极的损耗,可使用单个电极 完成粗加工到精加工转换的过程。 2.机械式平动头有扩孔作用,当工件要求偏小时,设定所需平 动量加工,满足工件加工要求。 3.机械式平动头对工件光洁度有明显效果,特别是工件型腔侧 边犹为明显。 4.机械式平动头可对螺纹孔放电加工 5.数控平动头能够作多种循迹及侧向加工,包含圆形循迹、方 形循迹、正方形侧向、圆周任意角度等分连续、任意角度对称、 任意角度侧向。极大的提升了ZNC电火花的作用。 精密数控平动头与火花机相连,可改变平动量和侧壁修整量控制 放电侧边间隙。并在平动结束时能够自动停止加工。
ቤተ መጻሕፍቲ ባይዱ
1.有关单工具电极直接成型法的叙述中,不正确的是( )。 A) 需要重复装夹 B) 不需要平动头 C) 加工精度不高 D) 表面质量很好 2.下列各项中对电火花加工精度影响最小的是( )。 A) 放电间隙 B) 加工斜度 C) 工具电极损耗 D) 工具电极直径 3.型腔的电火花加工方法有哪些?