钻削参数
05第五章 钻削、镗削、铰削与拉削
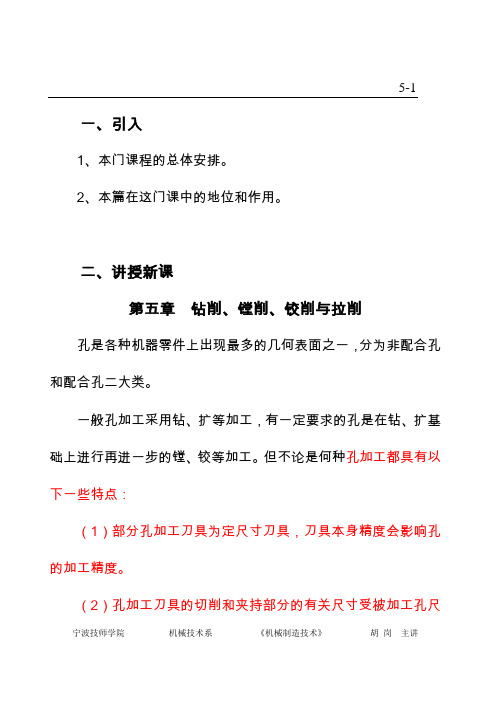
5-1一、引入1、本门课程的总体安排。
2、本篇在这门课中的地位和作用。
二、讲授新课第五章钻削、镗削、铰削与拉削孔是各种机器零件上出现最多的几何表面之一,分为非配合孔和配合孔二大类。
一般孔加工采用钻、扩等加工,有一定要求的孔是在钻、扩基础上进行再进一步的镗、铰等加工。
但不论是何种孔加工都具有以下一些特点:(1)部分孔加工刀具为定尺寸刀具,刀具本身精度会影响孔的加工精度。
(2)孔加工刀具的切削和夹持部分的有关尺寸受被加工孔尺寸的限制,会使刀具的刚性变差。
(3)孔加工时,刀具一般是封闭或半封闭状态下进行工作,对加工质量和刀具耐用度都会产生不利的影响。
宁波技师学院机械技术系《机械制造技术》胡岗主讲5-2 基于以上原因,在机械设计过程中选用孔和轴配合的公差等级时,经常把孔的公差等级定得比轴低一级。
孔加工的方法很多,常用的有钻孔、扩孔、锪孔、铰孔、镗孔、拉孔、磨孔等,还有金刚镗、珩磨、研磨、挤压及特种加工孔等方法。
其加工孔直径Φ0.01~Φ1000mm,加工精度可达到IT13~IT5,表面粗糙度Ra12.5~0.006μm;可在金属或非金属材料上加工,也可在普通材料或高硬度材料上加工。
在加工中可根据不同要求,合理进行选择最佳的加工方案,达到加工质量能符合要求。
第一节钻削加工(一)一、概述用钻头作回转运动,并使其与工件作相对轴向进给运动,在实体工件上加工孔的方法称为钻孔;在已有孔的情况下,用扩孔钻对孔径进行再扩大的加工称为扩孔;钻孔与扩孔统称为钻削。
钻削可以在各种钻床上进行,也可以在车床、铣床、镗床和组宁波技师学院机械技术系《机械制造技术》胡岗主讲5-3合机床、加工中心上进行,但大多数情况下,尤其是在大批量下生产时,主要还是在钻床上进行。
二、钻床主要用钻头在工件上加工孔的机床称为钻床。
通常以钻头的回转运动为主运动,钻头的轴向移动为进给运动。
钻床的分类:坐标镗钻床、深孔钻床、摇臂钻床、台式钻床、立式钻床、卧式钻床、铣钻床、中心孔钻床等八大类。
第九章--钻削加工

第九章钻削加工钻床是加工内孔的机床,是用钻头在实体材料上加工孔,主要用于加工外形复杂,没有对称旋转轴线的工件,如杠杆、盖板、箱体、机架等零件上的单孔或孔系。
钻孔属粗加工。
·钻削加工的工艺特点(1)钻头在半封闭的状态下进行切削的,切削量大,排屑困难。
(2)摩擦严重,产生热量多,散热困难。
(3)转速高、切削温度高,致使钻头磨损严重。
(4)挤压严重,所需切削力大,容易产生孔壁的冷作硬化。
(5)钻头细而悬伸长,加工时容易产生弯曲和振动。
(6钻孔精度低,尺寸精度为IT13~IT10,表面粗糙度Ra为12.5~6.3μm。
·钻削加工的工艺范围钻削加工的工艺范围较广,在钻床上采用不同的刀具,可以完成钻中心孔、钻孔、扩孔、铰孔、攻螺纹、锪埋头孔和锪凸台端面等,如图所示。
在钻床上钻孔精度低,但也可通过钻孔----扩孔----铰孔加工出精度要求很高的孔(IT6~IT8,表面粗糙度为1.6~0.4μm),还可以利用夹具加工有位置要求的孔系。
在钻床上加工时,工件固定不动,刀具作旋转运动(主运动)的同时沿轴向移动(进给运动)。
第一节钻床钻床的主要类型有:台式钻床、立式钻床、摇臂钻床、铣钻床和中心孔钻床等。
钻床的主参数一般为最大钻孔直径。
一、立式钻床立式钻床是钻床中应用较广的一种,其特点是主轴轴线垂直布置,且位置固定,需调整工件位置,使被加工孔中心线对准刀具的旋转中心线。
由刀具旋转实现主运动,同时沿轴向移动作进给运动。
因此,立式钻床操作不便,生产率不高。
适用于单件小批生产中加工中小型零件。
·立式钻床的传动原理主运动:单速电动机经齿轮分级变速机构传动;主轴旋转方向的变换,靠电动机正反转实现进给运动:主轴随同主轴套筒在主轴箱中作直线移动。
进给量用主轴每转一转时,主轴的轴向移动量来表示二、台钻台式钻床简称台钻,其实质上是一种加工小孔的立式钻床,结构简单小巧,使用灵活方便,适于加工小型零件上的小孔。
钻孔直径一般小于15mm。
切削参数计算公式

切削参数计算公式切削参数计算是机械加工中非常重要的一环,它决定了整个加工过程的效率和质量。
在进行切削参数计算时,需要考虑多个因素,如切削速度、进给速度、切削深度等。
下面我们将介绍一些常用的切削参数计算公式,帮助加工人员更好地确定合适的切削参数。
1.切削速度的计算公式:切削速度是指工件表面上单位时间内被切削刀具切削的长度,通常用m/min 来表示。
切削速度的计算公式为:Vc=π×D×n其中,Vc 为切削速度,单位为m/min;D 为刀具的直径,单位为mm;n 为主轴转速,单位为r/min。
2.进给速度的计算公式:进给速度是指切削刀具在工件上运动的速度,通常用mm/r 来表示。
进给速度的计算公式为:F=f×n其中,F 为进给速度,单位为mm/r;f 为每齿进给量,单位为mm,通常由刀具制造商提供;n 为主轴转速,单位为r/min。
3.切削深度的计算公式:切削深度是指刀具切入工件内部的深度,通常用mm 来表示。
切削深度的计算公式为:ae = ft×n其中,ae 为切削深度,单位为mm;ft 为切削时每齿的切削厚度,单位为mm;n 为主轴转速,单位为r/min。
4.主轴转速的计算公式:主轴转速是指主轴每分钟旋转的圈数,通常用r/min 来表示。
主轴转速的计算公式可以根据切削速度和刀具直径来确定,公式为:n=Vc/(π×D)其中,n 为主轴转速,单位为r/min;Vc 为切削速度,单位为m/min;D 为刀具的直径,单位为mm。
5.铣削切削力的计算公式:铣削切削力是在铣削过程中刀具对工件作用的力,通常用N(牛顿)来表示。
铣削切削力的计算公式为:Ft = Kc×ae×ap×fr其中,Ft 为铣削切削力,单位为N;Kc 为切削力系数;ae 为切削深度,单位为mm;ap 为轴向进给深度,单位为mm;fr 为切削速度,单位为mm/min。
钻头切削参数表

铸钢
500~600
——
~
~
35~38
38~40
不锈钢
——
——
~
~
25~27
27~35
耐热钢
——
——
~
~
3~6
5~8
灰铸铁
——
200
~
~
40~45
45~60
干切或乳化液
合金铸铁
——
230~350
~
~
20~40
25~45
非水溶性切削油或乳化液
——
350~400
~
~
8~20
10~25
可锻铸铁
——
118
~0.90C
175~225
88~96
17
25~35
118
合金钢
~0.25C
175~225
88~98
21
25~35
118
~0.65C
175~225
88~98
15~18
25~35
118
工具钢
196
94
18
25~35
118
灰铸铁
软
120~150
~80
43~46
30~30
90~118
中硬
160~220
进给量f/(mm/r)
切削速度V/(m/min)
切削液
d/mm
5~10
11~30
5~10
11~30
工具钢
1000
1800~1900
2300
300
500
575
~
~
<
~
氟金云母陶瓷钻削参数对刀具磨损的影响

9月
氟金 云母 陶瓷钻 削参数 对刀具磨 损 的影 响米
马廉 洁 , 爱兵 于思远 .于 - ,
(. 1白城 师 范 学 院 机 电 系 , 白城 1 70 2天 津 大 学 先进 陶瓷 与加 工 技 术 教 育 部 重 点 实 验 室 , 3 00; . 天津 3 0 7 ) 0 0 2
ts e u t h w t e t o a ae i il f ce y t o t r n o l g c n i o s D r g f o o h o o i e a c e tr s l s o h o l s we rrt sman y a e td b o l mae a a d c o i o d t n . u n u r p lg pt c r mis i l n i i l e
o d acdC rm c & M c ii eh ooyo eSa d ct nM ns , i j nvrt, in n30 7 , hn ) f vne ea is A ahnn T c nlg fh t eE uai ii r Ta i U iesy Taj 00 2 C i g t t o t y nn i i a
uae . h a it e tr l e v l ou ltd T ewe rw dhp rmae a mo a lme( / i r v VB V)wa p l d t v laeto e ri hsts. ru h s gefco sa pi oe au t o lw a nti t T o g i l a tr e e h n
ts , s me ma h n n a a t r r i u s d s c s t o tr ,c o ig c n i o s p n l p e n o la ge h e e t o c i i g p r me e swe e d s s e u h a o lmae i c l a o l o dt n ,s i de s e d a d t o n l .T n i
基于粒子群优化算法的神经网络钻削参数优化

Ke wo d p ri l wa m ’p i z to l o ih n u a e wo k ; a a tr o tmiai n y r s: a t e s r o t c mia in a g rt m; e r n t r s p r me e p i z to l
1 引言 . } + ) )} + ) , 1= +, 1 ; () 2 其 中: 为 惯 性 权值 , 常 随进 化 代 数 从 0 w 通 . 性 递 减 至 04d 12 9线 .,= … 兑 现 代 化 生 产 来 说 ,无 论 是 数 控 机 床 ( N 、 机 械 加 工 中 心 C C) ( ) 柔 性 制 造 系统 ( MS 、 算 机 集 成 制 造 系 统 ( [ ) 工 艺 参 数 nn为 解 空 间 的 维 数 , 自变量 个 数, MC 、 F )计 CMS , , 即 d为 n维 中 的第 d维 .为 当 前进 化 t
优 化 是 一 个 至 关 重 要 的 问题 。 现 代 的 数 控 加 工 工 艺 系 统 , 果 不 搞 代 数 , l , 种 群 规模 , 对 如 i ~ SS为 =2 和 r为 分 布 于 【,] 间 的 随 机 数 . 和 C 2 O1 之 c 。 2 通 。设 定 位 移 上 限 控 制 粒 子位 移 工 艺参 数 优化 , 搞 科 学 制 定 工 艺 规程 。 从 “ 验 判 断 ” 向 “ 学 定 为 位 移 变 化 的 限 定 因子 , 常取 为 2 不 不 经 转 科 量 分析 ”则 提 高 数 控 加 工 工 艺水 平 便 难 于 实 现 , 产 效 率 的提 高受 到 不 致 过 大 。P 0 算 法 主要 计 算 步 骤 为 : ) 始 化 , 定 位 移 因 子 C c , 生 S (初 1 设 和 影 响 , 而 缺 乏 市 场 竞 争力 。 机 械加 工过 程 中 , 品 质 量 和成 本直 接 惯 性 权 值 W最 大 进 化 代 数 7 , 当前 进 化 代 数 置 为 t 定 义 空 间 从 在 产 , 舾 .将 , 在 与加 工 的 各项 参 数 有 关 , 而 加 工 参 数 的 优 化 选 择 至 关 重 要 , 接 影 中 随 机 产 生 S个 粒 子 l2 … 组 成 初 始 种 群 x t 随 机 产 生 各 粒 子 故 直 … (; ) p ( (评 )2 t( )3 响着 企 业 的效 益 。 在 现代 机 械 制 造 业 中 , 多 参 数 需 要 操 作 人 员 一 次 初 始位 移 变化 , … …p 组 成 位 移 变 化 矩 阵 Vt; ) 价 种 群 X( ; ) 许
钻削的概念

钻削的概念钻削是指用钻头进行机械加工的过程,用于在工件上制造圆孔。
它是现代制造工艺中常见的一种加工方法,广泛应用于机械制造、汽车制造、航空航天、石油勘探等领域。
钻削的基本原理是利用钻头的旋转运动和轴向推进力,将刀具与工件接触并磨削工件。
钻头通常由切削刃和刀体两部分组成,切削刃负责切削工件,刀体则负责传递动力和固定切削刃。
在钻削过程中,切削刃对工件表面施加切削力,将工件上的金属材料削除,形成一个圆孔。
钻削一般分为粗钻、精钻两个过程。
粗钻时,钻削刃快速旋转,以较大的切削速度将大量金属屑削除;而精钻则是以较小的切削速度进行,用于在工件上获得更精确的孔径和表面质量。
钻削的过程涉及到几个重要的参数,包括切削速度、进给速度、切削深度和刀具选型等。
切削速度是指钻头的旋转速度,它决定了钻削的效率和切削力的大小。
进给速度是指钻头在轴向上的推进速度,它影响到切削过程中金属屑的形成和排除。
切削深度是指刀具在每一次钻削过程中进入工件的深度,它根据工件要求和刀具强度来确定。
刀具选型则是根据工件材料和形状,选择合适的钻头类型和尺寸。
钻削过程中,切削刃与工件表面的摩擦会引起热量的产生,这可能导致刀具磨损、工件变形和表面质量下降等问题。
为了解决这些问题,钻削过程中通常需要使用切削液进行冷却和润滑,以降低切削温度、延长刀具寿命、改善切削质量。
钻削的优点是加工精度高,适用于各种材料的加工,如金属、非金属、木材等。
钻削可以制造各种类型的孔,如盲孔、通孔、倒角孔等,并可进行各种类型的表面处理,如车削、镗削、铰削等。
此外,钻削还具有生产效率高、机械加工力度小、工艺稳定可靠等特点。
然而,钻削也有一些局限性。
首先,钻削只能制造圆孔,对于其他形状的孔无法实现。
其次,钻削过程中切削刃容易受到工件表面硬度不均匀、切削力不平衡等因素的影响,导致刀具磨损和加工质量下降。
此外,钻削过程中切削力较大,易产生振动和噪音,对机床和工件都会带来一定的负荷。
综上所述,钻削是一种常见的机械加工方法,具有广泛的应用领域和许多优点。
枪钻切削速度参数【一览表】
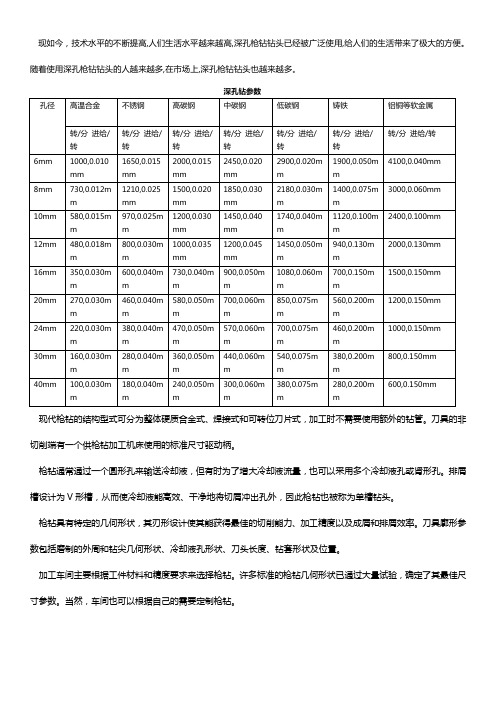
现如今,技术水平的不断提高,人们生活水平越来越高,深孔枪钻钻头已经被广泛使用,给人们的生活带来了极大的方便。
随着使用深孔枪钻钻头的人越来越多,在市场上,深孔枪钻钻头也越来越多。
现代枪钻的结构型式可分为整体硬质合金式、焊接式和可转位刀片式,加工时不需要使用额外的钻管。
刀具的非切削端有一个供枪钻加工机床使用的标准尺寸驱动柄。
枪钻通常通过一个圆形孔来输送冷却液,但有时为了增大冷却液流量,也可以采用多个冷却液孔或肾形孔。
排屑槽设计为V形槽,从而使冷却液能高效、干净地将切屑冲出孔外,因此枪钻也被称为单槽钻头。
枪钻具有特定的几何形状,其刃形设计使其能获得最佳的切削能力、加工精度以及成屑和排屑效率。
刀具廓形参数包括磨制的外周和钻尖几何形状、冷却液孔形状、刀头长度、钻套形状及位置。
加工车间主要根据工件材料和精度要求来选择枪钻。
许多标准的枪钻几何形状已通过大量试验,确定了其最佳尺寸参数。
当然,车间也可以根据自己的需要定制枪钻。
当所需孔的直径小于50-75mm,深径比(D/d)超过20:1时,最适合采用枪钻加工。
枪钻在深径比高达400:1的情况下仍能保持很高的加工精度。
该工艺可采用3种加工方式:①刀具旋转,工件固定;②工件旋转,刀具固定;③刀具与工件相互反转。
后一种方式特别适合精度要求较高的深孔加工,可以达到0.08mm/m的直线度和Ra0.2μm的表面粗糙度。
对于直径较大的孔,可以先用其他深孔钻削刀具进行钻孔,然后通过二次加工(如铰孔)进一步提高孔的圆度、直线度和表面光洁度。
性能优势与其他钻削加工方法相比,枪钻具有一些性能优势,能够降低生产成本和缩短加工时间。
如前所述,枪钻能通过一次进刀加工出精密深孔。
枪钻的钻套对孔壁具有挤光作用,也有助于提高孔壁表面光洁度,因此往往可以省略二次精加工。
当对深孔的圆度或直线度公差要求严格,或工件材料硬度较高时,枪钻加工也是首选的加工方式,因为枪钻能够达麻花钻难以企及的加工精度。
此外,枪钻的刀头磨损后可以重磨修复,从而可以大大延长刀具的使用寿命。
深孔加工参数计算方式

深孔加工参数计算方式
一、切削速度
Vc(m/min):切削速度
DC(mm):钻头直径
Π(3.14):圆周率
n(min-1):主轴转速
例:主轴转速1350min-1,钻头直径12。
求切削速度?
答:将π=3.14,DC=12,n=1350代人公式
据此,得出切削速度为50.9m/min
二、主轴进给量
vf(mm/min):主轴(Z轴)进给速度
fr(mm/rev):每转进给量
n(min-1):主轴转速
例:每转进给量为0.2mm/rev,转速为1350min-1,求主轴进给速度
答:代人公式得
由此得出主轴每分钟进给量为270mm/min。
三、孔加工时间
Tc(min):加工时间
n(min-1):主轴转速
d(mm):钻孔深
fr(mm/rev):每转进给量
i:孔数
例:在SCM440钢上钻Φ15,深30mm的孔。
切削速度为50m/min,每转进给量为0.15 mm/rev,求钻削时间?
答:主轴转速
得11.3秒,即可完成钻削。
枪钻加工原理及参数分析

枪钻加工原理及参数分析摘要:在金属深孔加工中,排屑及刀具寿命一直是难题,枪钻作为深孔加工的刀具之一,其切削刃参数及断屑排屑能力是影响枪钻使用寿命的主要因素。
本文通过对硬质合金枪钻钻头部分受力、断屑机理以及切削液供给的分析,提出合理的参数,改善枪钻切削条件。
关键词:枪钻断屑切削液枪钻加工系统由深孔钻机、硬质合金枪钻和高压冷却系统组成。
加工时,硬质合金枪钻通过工件自身导孔或导套进入工件,由于枪钻的独特结构,在钻削时能自导向,减少震动。
由于具有高压内冷却系统,枪钻能够连续进给且具有较高的切削速度,无需中途退刀排屑。
冷却液通过内通道到达切削部位,并将切屑带出v形排屑槽,同时能对刀具冷却并在工件切削表面形成润滑膜,降低刀具磨损。
本文主要分析外排屑枪钻的加工参数选择,其适用于加工φ2~φ20mm、长径比大于100、表面粗糙度ra12.5~3.2μm、精度it10~it8级的深孔。
1、硬质合金枪钻的结构硬质合金枪钻由钻头、钻杆、钻杆三部分组成(图1),钻头通常分为整体硬质合金、硬质合金镶片式、切削刃部分焊接cbn刀片整体硬质合金三种系列;钻头有单圆孔、双圆孔和肾形孔三种形式的冷却孔;钻头部分有小倒角,使钻杆外径小于钻头外径0.05~1mm,防止切削时摩擦已加工孔壁。
钻杆一般采用低碳或者低合金无缝钢管轧制成110~120°的v形槽,要求钻杆有足够的强度在小变形下提供钻削所需的扭矩;同时钻杆的有足够的韧性,以便吸收高速旋转所产生的震动。
2、硬质合金枪钻切削原理2.1.1钻头参数枪钻钻头的几何参数如图2所示。
其中α1为外角、α2为内角、α3α4分别为外刃第一、二后角、α5为钻尖后角、α6为内刃后角、α7与α2差值为油隙角、l为外刃宽度、d为钻头外径。
2.1.2受力分析枪钻钻头受力分析图如图3所示。
图3中f1为外刃法相力、f2为内刃法相力、fy1为外刃径向力、fy2为内刃径向力、fx1为外刃轴向力、fx2为内刃轴向力。
钻头切削参数表

14~25
90~118
可锻铸 铁
112~126
~71
27~37
20~30
90~118
球墨铸 铁
190~225
~98
18
14~25
90~118
塑料
30
15~25
118
硬橡胶
30~90
10~20
90~118
(2
加工材料
拉强度抗(T
b/MPa
硬度HBS
进给量f/(mm/r)切削速度V/(m/min)
硬橡胶
30~60
热固性树 脂
60~90
塑料
30~60
玻璃
手进
玻璃纤维 复合材料
198
钻孔切削用量的选
(1)咼速钢钻头钻削不同材料的切削用量
加工
材料
硬度
切削速
度V/(m/
mi n)
钻头直径d/mm
钻头 螺旋 角
/(°)
钻尖角/(°)
布氏
HBS
洛氏
HRB
<3
3~6
6~13
13~19
19~25
进给量f/(mm/r)
铝及铝合
金
45~105
~62
105
32~42
90~118
铝及铝合金
高加 工性
~0.9
0C
175~225
88~96
17
25~35
118
合金钢
~0.25
C
175~225
88~98
21
25~35
118
〜0.65
C
175~225
88~98
15~18ቤተ መጻሕፍቲ ባይዱ
任务-(7)-知识六-孔加工基础知识-添加划线加涂蓝油
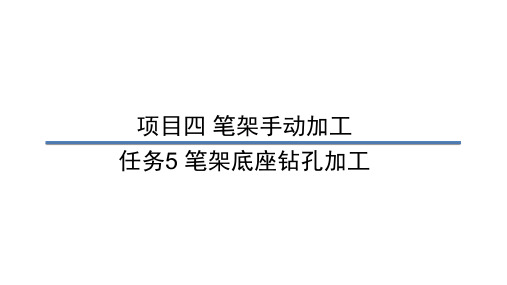
刷子或铁钩清除。 5. 不准在旋转的刀具下,翻转、卡压和测量工件。手不准触摸旋转
的刀具。
• 轮盘式:松开主轴箱夹紧手柄,转动手轮即可实现主轴箱升降,到 所需的位置后锁紧主轴箱夹紧手柄即可。
台式钻床的操作
手摇升降台式钻床(右)
轮盘升降台式钻床(左)
台式钻床的操作
• 3、台式钻床转速的调节
• 钻床的主轴动力来源于主轴箱背后的电动机,电动机靠皮带传动, 带动主轴做回转运动。电动机与主轴上各自安装有一个塔式皮带轮, 调整不同层级的皮带轮,即可调整主轴的转速。
CONTENTS
目 录
1 台式钻床的操作 2 钻头 3 锪孔 4 工件装夹工具 5 钻孔的冷却和润滑 6 钻削操作步骤 7 钻削操作注意事项
钻削操作步骤
• 1. 划线 • 2. 打样冲
1
2
3
4
• 3. 装夹工件
• 4. 安装麻花钻
• 5. 调整机床转速
• 6. 试钻 • 7. 钻削
5
6
7
8
• 8. 倒角
• 台式钻床的主轴上安装有钻夹头,钻夹头常见有普通钻夹 头与自紧钻夹头。
• 普通钻夹头钻头的安装:旋转钻夹头外壳使有钻头柄能足 够放入夹心内,确定钻头处于中心位置,然后旋转钻夹头 外壳,并使用钥匙锁紧钻夹头,使钻头紧固于钻夹头内。 卸载钻头时,使用钥匙反向松开钻夹头即可。
• 自紧钻夹头钻头的安装:相比于普通钻夹头,自紧钻夹头 操作更简单,仅需转动钻夹头外壳,放入钻头,转动钻夹 头外壳手动锁紧,锁紧时不需要借助钥匙等辅助器具即可 牢固锁紧。
CONTENTS
目 录
钻头切削参数表

60
15~40
118
低加工性
~124
10~70
20
0~25
118
镁及镁合金
50~90
~52
45~120
25~35
118
锌合金
80~100
41~62
75
32~42
118
碳钢
~0.25C
125~175
71~88
24
25~35
118
~0.50C
175~225
88~98
20
25~35
118
~0.90C
切削速度V/(m/min)
切削液
d/mm
5~10
11~30
5~10
11~30
工具钢
1000
1800~1900
2300
300
500
575
~
~
<
~
~
<
35~408~11<640~4511~14
7~10
非水溶性
切削油
镍铬钢
1000
1400
300
420
~
~
~
~
35~40
15~20
40~45
20~25
铸钢
500~600
14~25
90~118
可锻铸铁
112~126
~71
27~37
20~30
90~118
球墨铸铁
190~225
~98
18
14~25
90~118
塑 料
—
—
30
15~25
118
硬橡胶
钻头切削参数表

铝及铝合金
高加工性
~124
10~70
60
0.08
0.15
0.25
0.40
0.48
15~40
118
低加工性
~124
10~70
20
0.08
0.15
0.25
0.40
0.48
0~25
118
镁及镁合金
50~90
~52
45~120
0.08
0.15
0.25
0.40
0.48
25~35
118
锌合金
80~100
38~40
不锈钢
——
——
0.08~0.12
0.12~0.2
25~27
27~35
耐热钢
——
——
0.01~0.05
0.05~0.1
3ቤተ መጻሕፍቲ ባይዱ6
5~8
灰铸铁
——
200
0.2~0.3
0.3~0.5
40~45
45~60
干切或乳化液
合金铸铁
——
230~350
0.03~0.07
0.05~0.1
20~40
25~45
非水溶性切削油或乳化液
0.13
0.20
0.26
0.32
20~30
90~118
球墨铸铁
190~225
~98
18
0.08
0.13
0.20
0.26
0.32
14~25
90~118
塑 料
—
—
30
0.08
0.13
0.20
0.26
- 1、下载文档前请自行甄别文档内容的完整性,平台不提供额外的编辑、内容补充、找答案等附加服务。
- 2、"仅部分预览"的文档,不可在线预览部分如存在完整性等问题,可反馈申请退款(可完整预览的文档不适用该条件!)。
- 3、如文档侵犯您的权益,请联系客服反馈,我们会尽快为您处理(人工客服工作时间:9:00-18:30)。
典型应用 • 小直径 • 紧密或精密公差孔
• 比深孔短
铜焊刀尖,硬质合金钻头,Coromant Delta,是对于 CoroDrill Delta-C的补充选择。可重新磨削。
典型应用
作为对于较大直径整体硬质合金的补充或当加 工稳定性不良时 – 钻头的钢制刀体能够提供 韧性
G
H
I
E5
材料
刀柄/机床
信息/索引
当使用可转位刀片钻头CoroDrill 880钻通孔时,在钻头钻出时形成一个在高速下可能弹 出的圆片。建议 – 封闭卡盘或机床。
刀柄/机床
H
旋转止动块必须用于旋转钻头。带有切屑的冷却液可能导致狭窄的座卡滞、壳体旋转和供液管围
绕壳体被拉动 – 可能导致严重的事故。如果旋转插头有一段时间没有使用,在启动机床主轴之
0.02
铣削
E
CoroDrill 880
0.03
钻削
F
钻头跳动和对准对于成功钻削极为重要。
刀具跳动
最小刀具跳动对于成功钻削是必要的。 跳动不应超过图中的数值,对准必须平行,以便得到: • 紧密的孔公差和直线度 • 良好的表面光洁度 • 一致长的刀具寿命 参见非回转钻削,第E 42页。
0.02
镗削
G 安全防护措施 – 危险点
工方法。同一切削刀具和适配器可用于不同的用途和机床。这使得对于整个机床车间 可以通过一个刀具系统标准化。 适用于CoroDrill Delta-C的高精度夹头为CoroGrip和HydroGrip。参见刀具夹紧/机 床,第G章。
C
机密
CoroGrip®
HydroGrip®
螺纹切削
D
CoroDrill Delta C
镗削
• 保养
定期更换刀片夹紧螺钉。在更换刀片之前清洁刀尖座。使用扭距扳手和二硫
G
化钼润滑剂。在重磨整体式/焊接硬质合金钻头之前不要超过最大磨损量。参
见第E 65页。
刀柄/机床
H
材料
I
E8
信息/索引
钻削定义
A 钻削 – 应用指南
普通车削
50% × vc 最大
vc = 0
vc 最大
B
切断与切槽
钻削生产率与穿透率vf密切相关。
机密
A 钻削 – 应用指南
普通车削
B
切断与切槽
C
螺纹切削
D
铣削
E
钻削
Namnlöst-1 1
F
镗削
方法选择 可以考虑三个不同方面以确定最佳的方法和刀具加工方案。
1. 孔尺寸和质量
2. 零件材料、形状和数量G刀柄/机床H材料
3. 机床参数
I
E3
信息/索引
切断与切槽
普通车削
A 钻削 – 应用指南
初始考虑
前,检查并确认刀柄在壳体中旋转。
材料
I
E6
信息/索引
切削液 q
机密
A 钻削 – 应用指南
普通车削
p
排屑、冷却和润滑是切削液的主要功能。这影响孔质量和刀具寿命。
应该在钻尖处测量最小容量,并且可以使用秒表和桶检查。
B
冷却液箱的容积应该比泵每分钟供给的冷却液容量大5-10倍。冷却液压力在泵
和钻头之间下降。要检查压力对于水平钻削是否足够,从钻头出来的冷却液流
Coromant Delta®
E 56 E 60 E 62
材质信息 E 66
E1
普通车削
A 钻削 – 介绍 B
机密
切断与切槽
C
螺纹切削
D
铣削
E
钻削
介绍
F 大多数孔用钻削刀具加工:整体硬质合金、可转位刀片
或焊接硬质合金:因为钻削是生产率最高的孔加工方
趋势
法。
机床和机加工方法
高技术CoroDrill刀具允许通过一次操作进行钻削,不用 • 更高的主轴转速 – 这就是为什么使用整体硬质合金钻头而不使
vf = fn x n
vc =
π x Dc x n 1 000
fn = fz
可转位刀片钻头 – 一个中心刀片和一个周边刀片
C
中心刀片从切削速度零工作至50%的vc最大值,周边刀片从50% 的vc最大值直至vc最大值。中心刀片形成锥形切屑,而周边刀片形 成类似于使用大切削深度在内圆车削中形成的切屑。
螺纹切削
钻削
F
镗削
3. 机床 对于钻孔,要考虑某些重要的机床性能:
G • 稳定性、功率、扭矩,特别是对于较大的钻头
• 排屑方法如下改善: - 水平主轴 - 内部冷却液供应 - 非回转钻头
• 主轴转速(rpm)对于小直径是否足够?
H • 冷却液容量对于大直径钻头是否足够?
• 冷却液压力对于小直径钻头是否足够?
不应有向下超过至少30 cm的下降。
切断与切槽
Dc
C
切削液供给中的压力直径关系(压力为红色,直径为黄 色,容量为蓝色)
螺纹切削
• 可溶机油(乳化液)应该总是带有EP(极压)添加剂,并且机油和水的混合比应该在 5-15%之间,以得到最佳的刀具寿命。不锈钢和耐热合金材料中的钻削得益于高混合液。
• 高压力冷却液(~70 bar)改善长切屑材料中的排屑和刀具寿命,例如不锈钢。
检查钻头的切除量。
D
• 干净机油改善润滑并且在钻削不锈钢时有好处。
• 可以使用雾状切削液或最小润滑,特别是在铝合金中。
铣削
• 干钻削可以在短切屑材料和孔深度直至3倍直径的情况下进行,特别是在水平应用中, 但刀具寿命将降低。
注意:干钻削绝对不推荐用于不锈钢材料(ISO M和S),并且绝对不推荐使用焊接硬质 合金钻头,即Coromant Delta。
D
整体式和焊接硬质合金钻头从中心到周边的两个切削刃。
铣削
vc = 0
Namnlöst-1 1
50% × vc 最大
孔深
vc 最大 fn = 2 x fz
2009-08-31 09:29:34
E
背锥 整体式或焊接硬质合金钻头在其外径稍加研 磨成Namnl一öst-1 定1 锥度,以提供间隙防止钻头卡滞在 孔中。
E
最好使用内部冷却液供应,以免切屑堵塞,并应在孔深度为3 x Dc时使用。外部冷却液 供应在短切屑材料中可以接受,并且可以帮助避免切屑瘤。必须正确引导冷却液喷嘴,
如图所示。
总是优先考虑内部冷却液供应。
钻削
F
镗削
如果使用外部冷却液,确保正确引导冷 却液。
G
刀柄/机床
切屑控制
切屑形成和排屑是钻削中的重要事项。它取决于工件材料、钻头/刀片 槽型选择、冷却液压力/容量、切削参数。
切屑堵塞可能导致钻头径向移动并影响孔质量、钻头寿命和可靠性, 或钻头/刀片断屑槽。
参见第E 15页。
更厚和更硬 的切屑
转速
H
由于更低的摩 擦而更开阔
材料
进给量
I
E7
信息/索引
A 钻削 – 应用指南
切削参数
普通车削
线速度影响 – vc (m/min) 切削速度 – 主要参数,以及材料硬度,影响刀
具寿命和功率消耗。速度越高产生的温度越高,并增加后刀面磨损。
典型应用 • 中等和大直径孔 • 中等公差要求
• 需要“平”底的盲孔
• 插钻或镗孔加工
灵活性, 小批量生产
E
F
钻削
镗削
整体硬质合金钻头,CoroDrill Delta-C,在较低切 削速度下加工,但是与可转位钻头相比具有更大的每 转进给量。相对可转位刀片钻头的主要优点是可以得 到更紧密的孔公差。可重新磨削。
C • 影响进给力Ff (N),当状况不稳定时要考虑。
• 影响功率Pc (kW)和扭矩Mc (Nm)。
fn (mm/r)
螺纹切削
D
当钻削薄/弱零件时,每转进给量(fn)应该保持 低。
铣削
E 如何得到良好的孔质量
• 排屑 确保排屑令人满意。切屑堵塞影响孔质量和可靠性/刀具寿命。钻头/刀片槽 型和切削参数是关键的。参见第E 15页。
非腐蚀性材料。
刀柄/机床
H
材料
I
E2
信息/索引
应用指南
孔加工方法
钻削 普通钻削– 山特维克可乐满公司具有宽范围的钻头选择,覆盖从0.30到110 mm的直 径范围。孔深度高达15 x Dc。参见第E 10页。 阶梯/倒角钻削– 使用优化的阶梯/倒角钻头或通过刀具路径编程使用标准刀具加 工。参见第E 24页。 其他方法– 径向调节、镗孔、螺旋插补、插钻、套孔和堆钻。参见第E30页。 镗孔和铰削 镗孔被定义为扩大现有孔或改善其质量的方法。现有加工直径范围很大的粗加工和精 加工刀具。多刃铰刀是用于孔精加工的高生产率刀具。参见镗孔,第F章。 铣削 可以使用螺旋铣刀或圆弧插补铣刀代替钻头或镗削刀具。在下列情况下,该方法生产 率低,但是可以作为备选方案: • 机床功率受限和/或没有可用冷却液 • 通过钻削难以断屑/排屑 • 需要绝对平坦的底孔 • 刀库中空间有限 参见铣削,第D章。 深孔钻削 山特维克可乐满公司具有大范围的单管钻头和喷吸钻头及枪钻,钻削深度可以达到大 约150 x Dc。有关深孔钻削,参见主目录和应用指南,C-1202:1。
刀柄/机床
材料
I
E4
信息/索引
方法选择 – 示例
要加工的孔: 钻削和镗孔
阶梯钻削
优点 • 简单的标准刀具 • 相对灵活
缺点 • 两把刀具、适配器和基本刀柄 • 需要两个刀具位置
优点 • 简单的定制刀具 • 加工孔的快速方法
缺点 • 需要更大的功率和稳定性 • 灵活性较低
机密
A 钻削 – 应用指南
普通车削