数控编程刀具材料选择
g90循环加工编程实例

g90循环加工编程实例
G90指令是数控编程中的一个固定循环指令,主要用于进行切削加工。
以下是使用G90进行加工编程的一个简单实例:
假设我们有一个简单的工件,其形状是一个圆柱体,我们想要使用G90进行加工。
1. 工件材料和工具
假设工件材料为45号钢,使用直径为10mm的刀具。
2. 程序开始
```
O1000
T1 M06 // 刀具选择
G00 G90 G40 G21 G17 G94 G80 // 设置初始条件
G54 X-75 Y-75 S500 M03 // 快速定位到起始点,并开始主轴旋转
```
3. 加工过程
```css
Z10 // 快速定位到Z=10
G1 Z-20 F100 // 以F100的速度切削到Z=-20
X-50 // 快速定位到X=-50
G1 Z-20 // 以当前Y位置切削到Z=-20
Y50 // 快速定位到Y=50
G1 Z-20 // 以当前X位置切削到Z=-20
X-75 // 快速定位到X=-75
G92 X-75 Y-75 Z20 // 使用G92设置新的Z位置为20
M30 // 程序结束
```
4. 注意事项
在使用G90进行加工时,要确保刀具路径是正确的,避免过切或未切削的
情况。
初始的G代码(例如G00、G90、G40等)通常在程序开始时设置。
刀具路径应根据工件的形状、刀具的直径和所需的加工精度进行选择。
在切削过程中,要确保主轴速度(S代码)和进给速度(F代码)是合适的。
在完成加工后,程序应适当地结束,如使用M30。
数控刀具基础知识
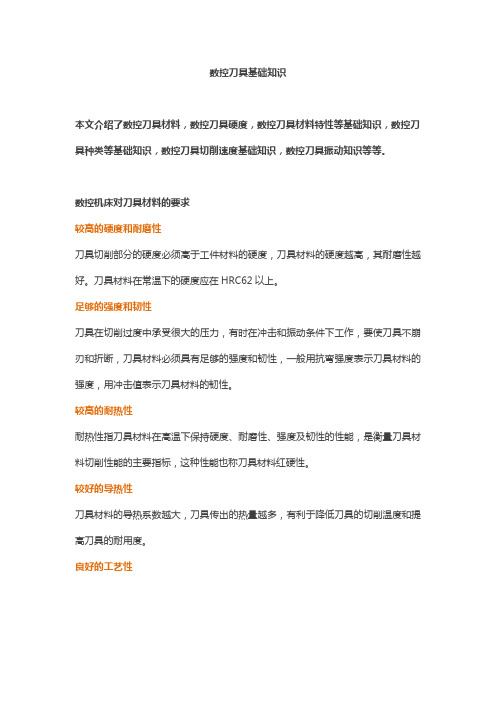
数控刀具基础知识本文介绍了数控刀具材料,数控刀具硬度,数控刀具材料特性等基础知识,数控刀具种类等基础知识,数控刀具切削速度基础知识,数控刀具振动知识等等。
数控机床对刀具材料的要求较高的硬度和耐磨性刀具切削部分的硬度必须高于工件材料的硬度,刀具材料的硬度越高,其耐磨性越好。
刀具材料在常温下的硬度应在HRC62以上。
足够的强度和韧性刀具在切削过度中承受很大的压力,有时在冲击和振动条件下工作,要使刀具不崩刃和折断,刀具材料必须具有足够的强度和韧性,一般用抗弯强度表示刀具材料的强度,用冲击值表示刀具材料的韧性。
较高的耐热性耐热性指刀具材料在高温下保持硬度、耐磨性、强度及韧性的性能,是衡量刀具材料切削性能的主要指标,这种性能也称刀具材料红硬性。
较好的导热性刀具材料的导热系数越大,刀具传出的热量越多,有利于降低刀具的切削温度和提高刀具的耐用度。
良好的工艺性为便于刀具的加工制造,要求刀具材料具有良好的工艺性能,如刀具材料的锻造、轧制、焊接、切削加工和可磨削性、热处理特性及高温塑性变形性能,对于硬质合金和陶瓷刀具材料还要求有良好的烧结与压力成形的性能。
刀具材料种类高速钢高速钢是由W、Cr、Mo等合金元素组成的合金工具钢,具有较高的热稳定性,较高的强度和韧性,并有一定的硬度和耐磨性,因而适合于加工有色金属和各种金属材料,又由于高速钢有很好的加工工艺性,适合制造复杂的成形刀具,特别是粉沬冶金高速钢,具有各向异性的机械性能,减少了淬火变形,适合于制造精密与复杂的成形刀具。
硬质合金硬质合金具有很高的硬度和耐磨性,切削性能比高速钢好,耐用度是高速钢的几倍至数十倍,但冲击韧性较差。
由于其切削性能优良,因此被广泛用作刀具材料。
切削刀具用硬质合金分类及标志涂层刀片1)CVD气相沉积法涂层涂层物质为TiC,使硬质合金刀具耐用度提高1-3倍。
涂层厚;刃口钝;利于提高速度寿命。
2)PVD物理气相沉积法涂层涂层物质为TiN、TiAlN和Ti(C,N),使硬质合金刀具耐用度提高2-10倍。
数控刀具的选择方法
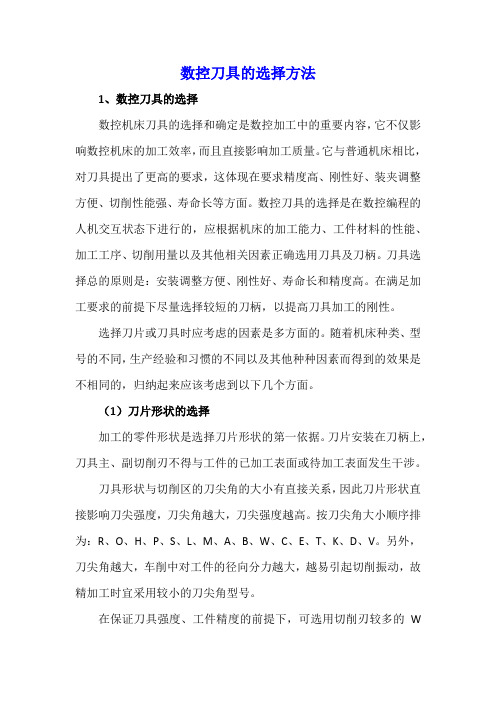
数控刀具的选择方法1、数控刀具的选择数控机床刀具的选择和确定是数控加工中的重要内容,它不仅影响数控机床的加工效率,而且直接影响加工质量。
它与普通机床相比,对刀具提出了更高的要求,这体现在要求精度高、刚性好、装夹调整方便、切削性能强、寿命长等方面。
数控刀具的选择是在数控编程的人机交互状态下进行的,应根据机床的加工能力、工件材料的性能、加工工序、切削用量以及其他相关因素正确选用刀具及刀柄。
刀具选择总的原则是:安装调整方便、刚性好、寿命长和精度高。
在满足加工要求的前提下尽量选择较短的刀柄,以提高刀具加工的刚性。
选择刀片或刀具时应考虑的因素是多方面的。
随着机床种类、型号的不同,生产经验和习惯的不同以及其他种种因素而得到的效果是不相同的,归纳起来应该考虑到以下几个方面。
(1)刀片形状的选择加工的零件形状是选择刀片形状的第一依据。
刀片安装在刀柄上,刀具主、副切削刃不得与工件的已加工表面或待加工表面发生干涉。
刀具形状与切削区的刀尖角的大小有直接关系,因此刀片形状直接影响刀尖强度,刀尖角越大,刀尖强度越高。
按刀尖角大小顺序排为:R、O、H、P、S、L、M、A、B、W、C、E、T、K、D、V。
另外,刀尖角越大,车削中对工件的径向分力越大,越易引起切削振动,故精加工时宜采用较小的刀尖角型号。
在保证刀具强度、工件精度的前提下,可选用切削刃较多的W型、T型刀片。
此外,某些刀片形状的使用范围有其专用性。
如D型、V型车削刀片一般只在仿形车削时才使用。
R型刀片在仿形、车削盘类零件(车轮)、曲面加工时采用。
(2)刀片主切削刃后角的选择当刀片后角选N型0°时,刀片可正反使用,这样可以降低刀片成本。
此时刀柄上的刀片安装面不是水平的,当刀片与刀体组合后,刀具形成正的后角,只是刃倾角为负。
由于数控机夹刀片一般都有断屑槽,故前角也为正值。
因此N型刀片被较多选用,选用时注意考虑槽形。
另外,由于该型刀具的刃倾角为负,在进行曲面加工时,刀具上切削点位置不同,且不在同一中心高上,故在进行较大的精密曲面加工时会造成误差。
数控刀具选择常用的十五条原则,选错后悔!

1、加工中最重要的刀具都意味着生产出现停顿。
但并不意味着每把刀具都具有同样重要的地位。
切削加工时间最长的刀具对生产周期的影响更大,任何一把刀具停止工作。
因此同等前提下,应当给予这把刀具更多关注。
此外,还应该注意加工关键部件及加工公差范围要求最严格的刀具。
另外,对切屑控制相对差的刀具,如钻头、切槽刀、螺纹加工刀具也应重点关注。
因为切屑控制不佳可引起停机。
2、与机床相匹配因此选择正确的刀具非常重要。
通常,刀具分右手刀及左手刀。
右手刀具适合于逆时针旋转(CCW机床(沿主轴方向看);左手刀具适合于顺时针旋转(CW机床。
如果你有几台车床,一些夹持左手刀具,其他左右手兼容,那么请选择左手刀具。
而对于铣削而言,人们通常倾向于选择通用性更强的刀具。
但是尽管此类刀具涵盖的加工范围更大,也令你即刻损失了刀具的刚性,增大了刀具挠曲变形,降低了切削参数,同时更容易引起加工振动。
另外,机床更换刀具的机械手对刀具的尺寸及重量也有所限制。
若你购买的主轴带内冷却通孔的机床,也请选择带内冷却通孔的刀具。
3、与被加工材料相匹配因此大多数刀具基于优化碳钢加工设计。
刀片牌号需依据被加工材料进行选择。
刀具制造商提供一系列的刀体及相配合的刀片用于加工诸如高温合金、钛合金、铝、复合材料、塑料及纯金属等非铁材料。
当你需要加工上述材料时,碳钢是机械加工中最常见的被加工材料。
请选择相匹配材质的刀具。
绝大多数品牌都有各种系列刀具,标明适合加工什么材料。
如DaElement3PP系列就主要用来加工铝合金、86P系列专门来加工不锈钢、6P系列专门来加工高硬钢。
4、刀具规格铣刀规格太大。
大规格的车刀刚性更佳;而大规格的铣刀不仅价格更高,常见的错误是所选的车刀规格太小。
且空切时间更长。
总体而言,大规格的刀具价格高于小规格刀具。
5、选择可换刀片式还是重新修磨式刀具条件允许下,遵循的原则很简单:尽量避免修磨刀具。
除了少数钻头和端面铣刀外。
尽量选择可换刀片式或可换刀头式刀具。
数控机床、刀具和夹具的选择与使用

数控刀具的选择
▪ 刀具的选择是数控加工工艺设计中的重要内容之一。刀具选择 合理是否不仅影响数控机床的加工效率,而且还直接影响加工质量。 选择刀具通常要考虑机床的加工能力、工序内容和工件材料等等因 素。
模具制造工艺学
数控机床、刀具和夹具的选择与使用
▪ 数控机床的合理使用 ▪ 1 数控机床的选用原则
▪ 目前,我国生产的数控机床有高档、中档、及经济型3个档次, 经济性数控机床的性能现已有了质的提高,而价格却只有中档数控 的几分之一至十几分之一,应可能选用。
数控机床、刀具和夹具的选择与使用
▪ 数控机床的合理使用 ▪ 2 曲面加工与坐标轴数的选择
1.3 夹具的设计和使用
▪ 对数控机床夹具设计使用的具体要求
3 夹具的设计要方便加工零件的装卸,夹具要能迅速完成零件的 定位、夹紧和拆卸过程。为此,夹具的设计要力求结构简单,整体 性能好,不得有零碎的配件和繁杂的结构。为有效缩短辅助工作时 间,保证装夹的可靠,数控机床夹具常采用气动、液压和偏心夹紧 方式夹紧工件。
切屑缠绕都会影响加工的正常进行,因此,应合理选用断屑槽的形
状、尺寸与切削用量,保证断屑的可靠。
刀柄
▪ 刀柄是加工中心必备的辅助工具,用以将刀具与机床主轴连接 起来。由于加工中心有自动交换刀具的功能,所以刀柄必须满足机 床主轴自动松开和拉紧定位的要求,且能在机械手的夹持下与搬运 下,准确地安装各种切削刀具。
1.3 夹具的设计和使用
▪ 对数控机床夹具设计使用的具体要求
2 为适应数控加工高强度、大切削量的特点,数控夹具的结构应 具备足够的强度与刚度,以避免在振动与装夹力的作用下产生变形; 要避免工件在受强力切削时位置发生错动,数控夹具对工件的夹紧 力就要大一些,为防止过大的夹紧力与较大的切削力使工件产生变 形,夹具的定位点、支撑受力点、夹紧点的选择应慎重。
数控加工工艺及编程 项目3螺纹轴加工工具刀具选择

螺纹轴加工刀具和工具选择一、车刀选择外圆车刀选择原则与短轴加工时的外圆车刀相同用90度外圆车刀,这里就不在赘述。
分析该螺纹零件。
螺纹为M12的三角外螺纹,我选择三角形外螺纹车刀,刀尖角60度。
割槽刀选用3mm宽的外割槽刀。
二、螺纹车刀特点螺纹车刀是成形刀具,其切削部分的形状应和螺纹牙型轴向剖面的形状相符合,车刀的刀尖角应该等于牙型角。
三角形螺纹的牙型角是60°,理论上三角形螺纹车刀的刀尖角也应该是60°。
但实际生产中,只有高速工具钢三角形螺纹车刀的刀尖角是60°,硬质合金三角形螺纹车刀的刀尖角则应为59°30’左右。
这是因为用硬质合金车刀高速切削时,工件材料受到较大的挤压力,会使牙型角增大约0.5°。
三、螺纹车刀种类1.高速工具钢三角形螺纹车刀(图1)的前角一般取5°~15°,粗车刀的纵向前角一般取15°左右,精车刀的前角一般取6°~10°。
2.硬质合金三角形螺纹车刀(图2)的前角和纵向前角一般都取0°,为了增加切削刃的强度,在车削较高硬度的材料时,两切削刃上可磨出负倒棱。
a)粗车到b)精车刀图1高速钢三角螺纹车刀c)焊接式d)机加式图2 硬质合金三角螺纹车刀三、刀具的刃磨三角螺纹车刀刃磨要求:①根据粗、精车的要求,刃磨出合理的前、后角。
粗车刀前角大、后角小,精车刀则相反;②车刀的左右刀刃必须是直线,无崩刃;③刀头不歪斜,牙型半角相等;④内螺纹车刀刀尖角平分线必须与刀杆垂直;⑤内螺纹车刀后角应适当大些,一般磨有两个后角。
四、割槽刀1)高速工具钢槽刀如图3所示1)前角ϒ0:前角增大能使车刀刃口锋利,切削省力并排屑顺畅,ϒ0=5°~20°;2)主后角α0:可减少车槽刀主后刀面和工件过渡表面间的摩擦,α0=6°~8°;3)副后角α0’:可减少车槽刀两个副后刀面和工件已加工表面间的摩擦,α0'=1~3°。
提高数控机床加工效率的方法与技巧
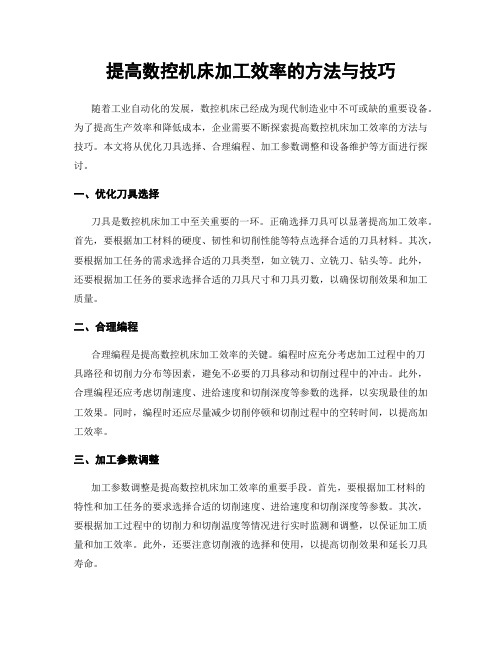
提高数控机床加工效率的方法与技巧随着工业自动化的发展,数控机床已经成为现代制造业中不可或缺的重要设备。
为了提高生产效率和降低成本,企业需要不断探索提高数控机床加工效率的方法与技巧。
本文将从优化刀具选择、合理编程、加工参数调整和设备维护等方面进行探讨。
一、优化刀具选择刀具是数控机床加工中至关重要的一环。
正确选择刀具可以显著提高加工效率。
首先,要根据加工材料的硬度、韧性和切削性能等特点选择合适的刀具材料。
其次,要根据加工任务的需求选择合适的刀具类型,如立铣刀、立铣刀、钻头等。
此外,还要根据加工任务的要求选择合适的刀具尺寸和刀具刃数,以确保切削效果和加工质量。
二、合理编程合理编程是提高数控机床加工效率的关键。
编程时应充分考虑加工过程中的刀具路径和切削力分布等因素,避免不必要的刀具移动和切削过程中的冲击。
此外,合理编程还应考虑切削速度、进给速度和切削深度等参数的选择,以实现最佳的加工效果。
同时,编程时还应尽量减少切削停顿和切削过程中的空转时间,以提高加工效率。
三、加工参数调整加工参数调整是提高数控机床加工效率的重要手段。
首先,要根据加工材料的特性和加工任务的要求选择合适的切削速度、进给速度和切削深度等参数。
其次,要根据加工过程中的切削力和切削温度等情况进行实时监测和调整,以保证加工质量和加工效率。
此外,还要注意切削液的选择和使用,以提高切削效果和延长刀具寿命。
四、设备维护设备维护是保证数控机床加工效率的重要保障。
定期对数控机床进行维护和保养,可以有效预防设备故障和延长设备寿命。
维护工作主要包括设备清洁、润滑和紧固等方面。
此外,还要定期检查和更换刀具、零部件和液压元件等,以确保设备的正常运行和高效加工。
综上所述,提高数控机床加工效率需要从多个方面进行考虑和优化。
优化刀具选择、合理编程、加工参数调整和设备维护是提高加工效率的关键。
企业应根据自身的实际情况和生产需求,采取相应的措施,不断探索和创新,以提高数控机床加工效率,提升企业的竞争力和盈利能力。
数控机床刀具选择和合理使用

数控机床刀具选择和合理使用数控加工刀具必须适应数控机床高速、高效和自动化程度高的特点,一般应包括通用刀具、通用连接刀柄及少量专用刀柄。
刀柄要联接刀具并装在机床动力头上,因此已逐渐标准化和系列化。
数控刀具的分类有多种方法。
根据刀具结构可分为:①整体式;②镶嵌式,采用焊接或机夹式联接,机夹式又可分为不转位和可转位两种;③特殊型式,如复合式刀具、减震式刀具等。
根据制造刀具所用的材料可分为:①高速钢刀具;②硬质合金刀具;③金刚石刀具;④其他材料刀具,如立方氮化硼刀具、陶瓷刀具等。
从切削工艺上可分为:①车削刀具,分外圆、内孔、螺纹、切割刀具等多种;②钻削刀具,包括钻头、铰刀、丝锥等;③镗削刀具;④铣削刀具等。
为了适应数控机床对刀具耐用、稳定、易调、可换等的要求,近几年机夹式可转位刀具得到广泛的应用,在数量上达到整个数控刀具的30%~40%,金属切除量占总数的80%~90%。
数控刀具与普通机床上所用的刀具相比,有许多不同的要求,主要有以下特点:①刚性好(尤其是粗加工刀具)、精度高、抗振及热变形小;②互换性好,便于快速换刀;③寿命高,切削性能稳定、可靠;④刀具的尺寸便于调整,以减少换刀调整时间;⑤刀具应能可靠地断屑或卷屑,以利于切屑的排除;⑥系列化、标准化,以利于编程和刀具管理。
刀具的选择是在数控编程的人机交互状态下进行的。
应根据机床的加工能力、工件材料的性能、加工工序、切削用量以及其它相关因素正确选用刀具及刀柄。
刀具选择总的原则是:安装调整方便、刚性好、耐用度和精度高。
在满足加工要求的前提下,尽量选择较短的刀柄,以提高刀具加工的刚性。
选取刀具时,要使刀具的尺寸与被加工工件的表面尺寸相适应。
生产中,平面零件周边轮廓的加工,常采用立铣刀;铣削平面时,应选硬质合金刀片铣刀;加工凸台、凹槽时,选高速钢立铣刀;加工毛坯表面或粗加工孔时,可选取镶硬质合金刀片的玉米铣刀;对一些立体型面和变斜角轮廓外形的加工,常采用球头铣刀、环形铣刀、锥形铣刀和盘形铣刀。
数控机床选用刀具及编程
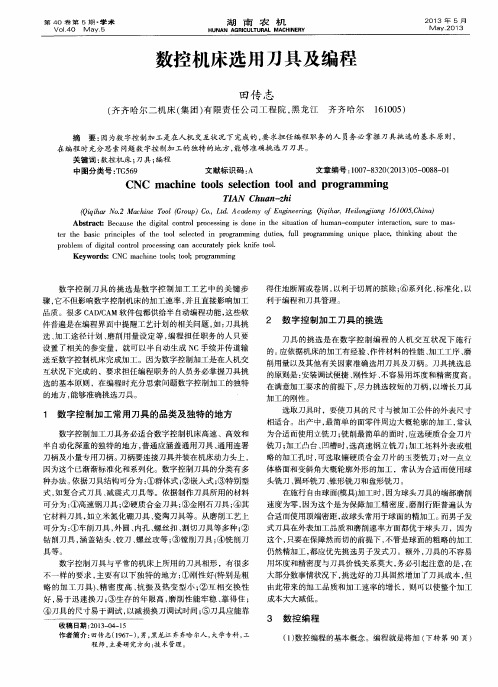
的地 方 , 能够 准 确 挑 选 刀 具 。
的。 应依据机床 的a l o有经验 、 t 作件材料的性能 、 加工工序 、 磨
p r o b l e m o f d i g i t a l c o nt r o l pr o c e s s i ng c a n a c c ur a t e l y p i c k k n i f e t o o 1 .
Ke y wo r d s :C NC ma c h i n e t o o l s ; t o o l ;p r o g r a mmi n g
CNC ma c h i n e t o o l s s e l e c t i o n t o o l a n d p r o g r a mm i n g
刀_ AⅣ ( u an— z l | I l f
( Q i q i h a r N o . 2 Ma c h i n e T o o l r o u p )C o . ,L t d . A c a d e m y o f E n g i n e e r i n g ,Q i q i h a r ,H e i l o n  ̄i a n g 1 6 1 0 0 5 , C h i n a )
数字控 制刀 具 的挑 选是数 字控制 加工工 艺 中的关 键步
骤, 它不但影响数字控制机床 的加工速率 , 并且 直接影 响加工 品质。很多 C A D / C AM软件包都供 给半 自动编程功能 , 这些软
得住地断屑或卷屑 , 以利于切屑的摈 除 ; ⑥系列化 、 标准化 , 以
数控机床刀具正确选用及编程技巧

2. 控加 工 常用 刀 具 的种 类 及特 点 数
数 控加 工刀具 必 须适应 数控机 床高 速 、高效 和 自动 化程 度高 的 特 点 ,一般应 包括 通 用刀具 通用连 接 刀柄及 少量 专用 刀柄 。刀 柄
要联 接 刀具 并装在 机 床动 力头 上 , 因此 已逐 渐标 准化 和 系列化 。 21 . 数控刀具 的分 类有 多种 方法 。 a 根据 刀具结构可 分为 : . ( ) 整体式 ; 1.
( ) 镶嵌式 ,采用焊 接或机 夹式联 接 .机夹式又可 分 为不 转位 2 .
和 可转位 两 种 ;
( . 3) 特殊型 式 ,如 复合式刀 具 、减 震式刀具等 。 b 根 据 制造刀具所 用 的材料可分 为 : .
( ) 高速钢 刀具 ; 1.
( ) 硬质合金 刀具 ; 2 . ( ) 金 刚石刀具 ; 3 .
・
1 4・ 期 2 第1 数 床市 0 控机 场
维普资讯
维普资讯
维普资讯
F 术 ■技 沿 前
数控 棚 床 刀具 正确 选用
及 编 程 技 巧
文 / 福建省 湄洲湾职业 技术学 院 苏志雄 1. 言 引
目前 ,许 多 C D C M软件包都提供 自动 A /A 编程 功 能 ,这 些软 件一 般 是在 编 程界 面 中提 示 工艺规 划 的有关 问题 ,如 ,刀具选择 、加工
路径规 划、切削用量设定等 ,编程人员只要设 置 有关 的参数 ,就可 以 自动生成 N C程序并
传输 至 数控机 床完 成加 工 。 因此 ,数 控加 工 中的 刀具选 择 和切 削 用 量确 定是 在 人机 交 互状 态 下完 成 的 ,这 与 普 通机 床加 工 形成 鲜 明的对 比 ,同 时也 要 求 编 程 人 员必 须 掌握 刀具 选 择 和切 削 用量 确定 的 基 本原 则 ,在编 程 时充 分考 虑 数 控加 工 的特 点 ,能够 正确 选择 刀刃具及 切 削用 量 。
UG编程在CNC加工中的自动化刀具选择与更换

UG编程在CNC加工中的自动化刀具选择与更换自从计算机数控(CNC)技术在机床加工中的应用得到广泛推广,自动化程度和效率大幅提高。
UG编程作为一种先进的CAD/CAM软件,为CNC加工提供了强大的功能和灵活性。
在CNC加工过程中,刀具的选择和更换对于加工效果和加工质量起着关键作用。
本文将探讨UG编程在CNC加工中的自动化刀具选择与更换的方法和技巧。
一、UG编程中的刀具库管理UG编程软件提供了刀具库管理功能,允许用户根据实际需求创建和编辑刀具库。
刀具库可以包括不同类型的刀具,如铣刀、钻头、车刀等,每种刀具都有其特定的参数和几何形状。
用户可以根据工件材料、加工形式和加工要求,选择合适的刀具,并将其添加到刀具库中。
对于不同类型的刀具,在刀具库中进行详细的设置是十分重要的。
UG编程软件提供了丰富的参数设置选项,用户可以根据实际需要,设置刀具的直径、长度、刃数、剖面形状等参数。
此外,用户还可以设置刀具的材质和涂层,以提高切削效率和刀具寿命。
二、自动化刀具选择UG编程软件在刀具选择方面提供了智能化的功能,可以根据工件的几何形状和切削条件,自动选择合适的刀具。
在进行刀具选择之前,用户需要对工件进行几何建模和加工设置。
接下来,将通过以下步骤进行刀具的自动选择:1. 进行工件识别:UG编程软件可以通过模型识别功能,自动识别工件的几何形状和特征。
通过自动识别,可以根据工件的形状,确定刀具的加工轮廓和加工路径。
2. 设置切削条件:根据加工要求和工件材料,设置合适的切削条件。
切削条件包括切削速度、进给速度和切削深度等参数。
根据切削条件,UG编程软件可以自动选择适当的刀具。
3. 自动选择刀具:UG编程软件根据工件的几何形状和切削条件,从刀具库中智能选择合适的刀具。
选择的刀具应具备良好的切削性能,并确保加工效率和加工质量。
三、自动化刀具更换UG编程软件支持自动化的刀具更换功能,可以根据加工任务的需要,自动进行刀具的更换。
刀具的更换可以基于切削条件的变化、刀具磨损或者加工方案的优化等原因。
木质材料CNC数控加工刀具的选择与切削用量确定
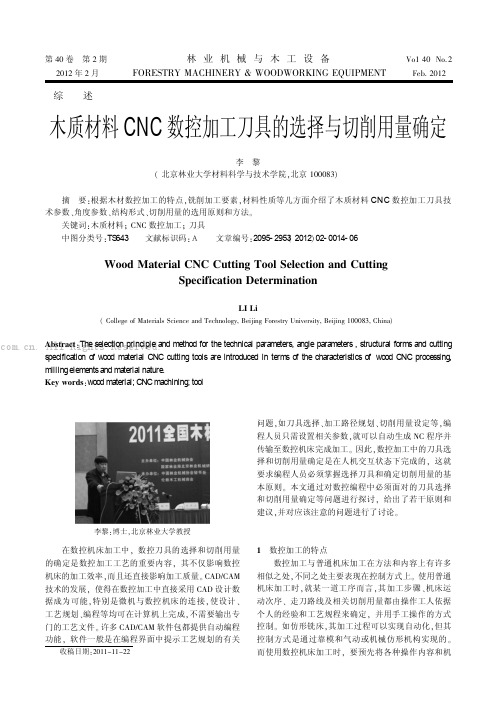
李黎:博士,北京林业大学教授木质材料CNC 数控加工刀具的选择与切削用量确定李黎(北京林业大学材料科学与技术学院,北京100083)摘要:根据木材数控加工的特点,铣削加工要素,材料性质等几方面介绍了木质材料CNC 数控加工刀具技术参数、角度参数、结构形式、切削用量的选用原则和方法。
关键词:木质材料;CNC 数控加工;刀具中图分类号:TS 643文献标识码:A文章编号:2095-2953(2012)02-0014-06Wood Material CNC Cutting Tool Selection and CuttingSpecification DeterminationLI Li(College of Materials Science and Technology,Beijing Forestry University,Beijing 100083,China )Abstract :The s e le ction principle a nd m e tho d fo r the te chnica l pa ra m e te rs ,a ngle pa ra m e te rs ,s tructura l fo rm s and cutting s pecifica tio n o f w o o d m a te ria l CNC cutting to o ls a re introduce d in te rm s o f the cha racte ris tics o f wo o d C NC pro ce s s ing ,m illingele m e ntsand m a te ria l na ture .Key words :wo o d m a te ria l;CNC m a chining ;to ol在数控机床加工中,数控刀具的选择和切削用量的确定是数控加工工艺的重要内容,其不仅影响数控机床的加工效率,而且还直接影响加工质量。
数控车床编程实例
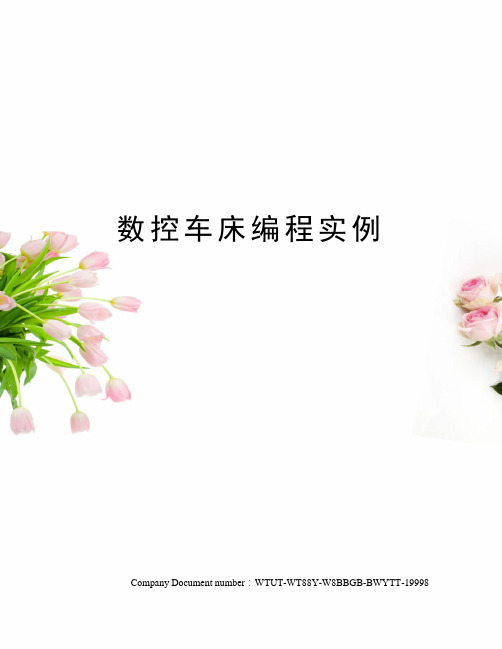
数控车床编程实例Company Document number:WTUT-WT88Y-W8BBGB-BWYTT-19998如图2-16所示工件,毛坯为φ45㎜×120㎜棒材,材料为45钢,数控车削端面、外圆。
1.根据零件图样要求、毛坯情况,确定工艺方案及加工路线1)对短轴类零件,轴心线为工艺基准,用三爪自定心卡盘夹持φ45外圆,使工件伸出卡盘80㎜,一次装夹完成粗精加工。
2)工步顺序①粗车端面及φ40㎜外圆,留1㎜精车余量。
②精车φ40㎜外圆到尺寸。
2.选择机床设备根据零件图样要求,选用经济型数控车床即可达到要求。
故选用CK0630型数控卧式车床。
3.选择刀具根据加工要求,选用两把刀具,T01为90°粗车刀,T03为90°精车刀。
同时把两把刀在自动换刀刀架上安装好,且都对好刀,把它们的刀偏值输入相应的刀具参数中。
4.确定切削用量切削用量的具体数值应根据该机床性能、相关的手册并结合实际经验确定,详见加工程序。
5.确定工件坐标系、对刀点和换刀点确定以工件右端面与轴心线的交点O为工件原点,建立XOZ工件坐标系,如前页图2-16所示。
采用手动试切对刀方法(操作与前面介绍的数控车床对刀方法基本相同)把点O作为对刀点。
换刀点设置在工件坐标系下X55、Z20处。
6.编写程序(以CK0630车床为例)按该机床规定的指令代码和程序段格式,把加工零件的全部工艺过程编写成程序清单。
该工件的加工程序如下:N0010 G59 X0 Z100 ;设置工件原点N0020 G90N0030 G92 X55 Z20 ;设置换刀点N0040 M03 S600N0050 M06 T01 ;取1号90°偏刀,粗车N0060 G00 X46 Z0N0070 G01 X0 Z0N0080 G00 X0 Z1N0090 G00 X41 Z1N0100 G01 X41 Z-64 F80 ;粗车φ40㎜外圆,留1㎜精车余量N0110 G28N0120 G29 ;回换刀点N0130 M06 T03 ;取3号90°偏刀,精车N0140 G00 X40 Z1N0150 M03 S1000N0160 G01 X40 Z-64 F40 ;精车φ40㎜外圆到尺寸N0170 G00 X55 Z20N0180 M05N0190 M02如图2-17所示变速手柄轴,毛坯为φ25㎜×100㎜棒材,材料为45钢,完成数控车削。
数控机床刀具的选择

第二章数控机床刀具的选择机械加工自动化生产可分为以自动生产线为代表的刚性专用化自动生产和以数控机床为主的柔性通用化自动生产。
就刀具而言,在刚性专用化自动生产中,是以提高刀具专用复合化程度来获得最佳经济效益的。
而在柔性自动化生产中,为适应随机多变加工零件的需求,尽可能通过提高刀具及其工具系统的标准化、系列化和模块化程度来获得最佳经济效益。
本章简述对数控刀具的特殊要求:车削类、镗铣类数控刀具系统;刀具预调、磨损与破损的自动监测。
2.1 对数控刀具的要求刀具的选择是数控加工工艺中的重要内容之一,它不仅影响机床的加上效率,而是直接影响加上质量。
编程时,选择刀具通常要考虑机床的加工能力、工序内容、工件材料等多方面的因素。
以数控机床为主的柔性自动化加工是按预先编好的程序指令自动地进行加工。
应适应加工品种多、批量小的要求,刀具除应具备普通机床用刀具应有的性能外,还应满足下列要求:1)刀具切削性能应稳定可靠,避免刀具过早地损坏,而造成频繁地停机。
由于刀具和工件材料性能的分散性,以及刀具制造工艺和工作条件控制不言,有相当一部分刀具的切削性能远低于平均性能,使刀具切削性能稳定可靠性差。
因此必须严格控制刀具材料的质量,严格贯彻刀具制造工艺,特别是热处理和刃磨工序。
严格检查刀具质量,确保刀具切削性能稳定可靠。
2)刀具寿命应有较高的寿命。
应选用切削性能好、耐磨性高的涂层刀片以及合理地选择切削用量。
3)保证可靠地断屑、卷屑和排屑。
加工时,应不产生紊乱的带状切屑,缠绕在刀具、工件上;不易断屑的刀具应保证切屑顺利的卷曲和排出;避免形成细碎的切屑;精加工是切屑不划伤已加工表面;切屑流出时不妨碍切削液浇注。
为了确保可靠地断屑、卷屑和排屑,可采取一下措施:合理选用可转位刀片的断屑槽槽形;合理地调整切削用量;在刀体中设置切削液通道,将切削液直接输送至切削区,有助于清除切屑;利用高压切削液强迫断屑。
4)能快速地换刀或自动换刀。
5)能迅速、精确地调整刀具尺寸。
数控机床如何正确选用刀具及编程

王 旭
(江 汉 大 学 文 理 学 院 机 建 学 部
湖北
武汉
4 0 5) 3 0 6
摘 要 : 控 刀 具 的 选 择 和 切 削 用 量 的 确 定 是 数 控 加 工 工 艺 中 的 重 要 内 容 , 它 不 仅 影 响 数 控 机 床 的加 工 效 率 , 而 且 直 接 影 响加 数 工 质 量 。CAD/ CAM技 术 的 发 展 , 得 在 数控加 工 中直 接利 用c D的设 计 数 据 成 为 可 能 ,特 别 是 DNc系统 微 机 与 数 控 机 床 的 联 接 ,使 使 A
主要有 以下 特点 :
I ,许多C / AM软件 包都 提供 自动编程 功能 ,这些软 件一 3前 AD C
般 是 在 编 程 界 面 中 提 示 下 艺 规 划 的 有 关 问 题 ,如 ,刀 具 选 择 、加 _ _ [ 路径 规划 、切削 用量设 定等 ,编 程人员 只要 设置 了有关 的参 数 ,就 可 以 自动 生 成 NC 序 并 传 输 至 数 控 机 床 完 成 加 工 。 程 因 此 , 数 控 加 T 中 的 刀 具 选 择 和 切 削 用 量 确 定 是 在 人 机 交 互 状 态下完 成 的 ,这 与普通 机床加 工形 成鲜 明 的对 比 ,同时也要 求 编程 人 员 必 须 掌 握 刀 具 选 择 和 切 削 用 量 确 定 的 基 本 原 则 ,在 编 程 时 充 分 考 虑 数 控 加 L的 特 点 , 能 够 正 确 选 择 刀 刃 具 及 切 削 用 量 。 数 控 加 工 刀 具 的 选 择 刀具 的选择 是在数 控编程 的人 机交 互状 态下进 行 的 。应 根据 机 床 的加 工能 力 、J 件材 料 的性 能 、加1 工序 、切 削用量 以及 其 它相 二
数控加工工艺——第五章 数控加工刀具的选择
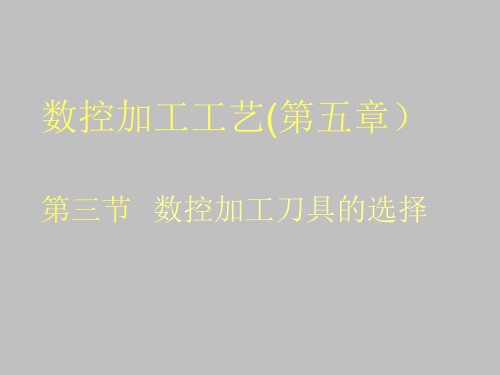
第三节 数控加工刀具的选择
第三节 数控加工刀具的选择
一、选择数控加工刀具应考虑的因素
选择数控加工刀片或刀具应考虑的因素是多方面的, 如机床的种类、型号、被加工的材料等,大致可归纳为以 下几点。
(1)被加工材料及性能。
(2)切削工艺的类别。
(3)被加工工件的几何形状、零件精度和加工余量等因 素。
扩孔直径较小或中等时,选用高速钢整体式扩孔;扩 20
第三节 数控加工刀具的选择
三、数控铣削刀具的选择
1.铣刀的类型 (1) 面铣刀。 如图5-6所示
图5-6 面铣刀
第三节 数控加工刀具的选择
硬质合金面铣刀按刀片和刀齿的安装方式不同,可分 为整体式、机夹-焊接式和可转位式3种(图5-7)。
图5-7硬质合金面铣刀
第三节 数控加工刀具的选择
(2) 立铣刀。立铣刀是数控机床上用得最多的一种 铣刀,其结构如图5-8所示。
第三节 数控加工刀具的选择
图5-15 直柄浅孔钻
第三节 数控加工刀具的选择
1-工件;2-钻套;3-外钻管;4-喷嘴;5-内钻管;6-钻头 图5-15 直柄浅孔钻
第三节 数控加工刀具的选择
2.扩孔刀具的选择
扩孔钻是主要的扩孔刀具,用于扩大孔径并提高孔的 加工精度。
扩孔钻的结构形式有高速钢整体式(图5-17(a))、镶 齿套式(图5-17(b))及硬质合金可转位式(图5-17(c)) 等。
可转位面铣刀分粗齿、细齿和密齿3种。粗车铣 刀一般用于粗铣钢件;粗铣带断续表面的铸件或平 稳条件下铣削钢件时,可选用细齿铣刀;而密齿铣 刀一般用于薄壁铸件的加工。
第三节 数控加工刀具的选择
由于铣削时有冲击,面铣刀的前角一般比车刀略小。 前角的数值主要根据刀具材料与工件材料来选择,其具 体数值可参见表5-2。
数控刀具选型及应用

• 薄壁零件
• 一般加工的首选
• 多个刃口最强壮
• 装夹不牢固的替零件 • 长悬深减小振动
• 一般加工
• 需要形成90°角的零件 • 切屑薄,能提高效率 • 切屑很薄,加工耐热合金
的首选
铣削公式
铣削公式
铣削计算
• 面铣刀直径80mm, 6个刀片刃口 ,若刀片的 切削速为150m/min, 问主轴的转速是多少? 如果每齿进刀量为fz=0.2mm/z, 问机床的工作 台进刀量是多少?
断屑槽的参数直 接影响到切削的 卷曲和折断,目 前刀片的断屑槽 形式较多,各种 断屑槽刀片的使 用情况不尽相同, 选用时一般参照 具体的产品样本
切削范围
代 号
断屑槽 形状
特点
精加工切削 FH
•精加工专用断屑槽
轻切削 SH 中切削 MV
•适合用于小切深,大进给 •大的前角刃口锋利
•适用于仿形向上切削加工 •正角刀棱锋利
走刀路线
• + 切削速度控制 - ve • + 高速铣加工 • + 高进给 • + 高效率 • + 刀片寿命 • + 安全
• – 刀片中心负荷大 • – 减小进给 • – 减小刀具寿命 • – 机械撞刀 • – 形状误差 • – 更长的程序和加工时间
走刀路线
走刀路线
走刀路线
不同主偏角铣刀的切削力不同
➢数控刀具的基本特点 ➢数控刀具的材料及牌号 ➢车削刀具的选择及应用 ➢铣削刀具的选择及应用 ➢工具系统选择
数控刀具的基本特征
数控加工刀具必须适应数控机床高速、高效和自动化程度高的特 点,一般应包括通用刀具、通用连接刀柄及少量专用刀柄。刀柄要联 接刀具并装在机床动力头上,因此已逐渐标准化和系列化。数控刀具 的分类有多种方法。
数控编程刀具材料和选择原则
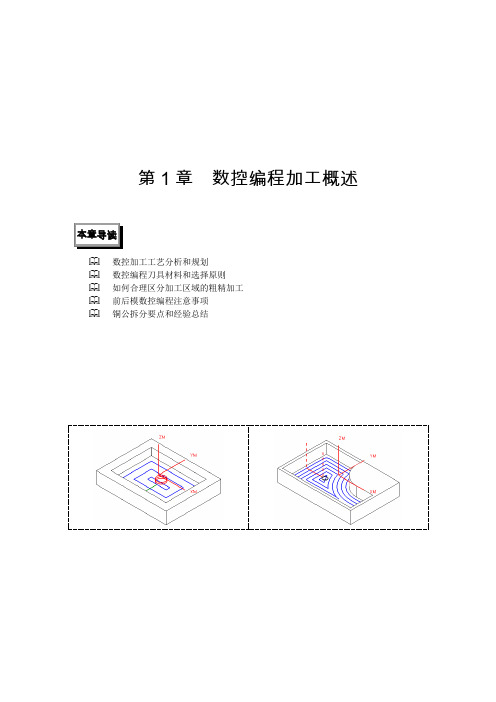
第1章 数控编程加工概述数控加工工艺分析和规划数控编程刀具材料和选择原则如何合理区分加工区域的粗精加工前后模数控编程注意事项铜公拆分要点和经验总结·2·精通中文版UG NX6数控编程与加工1.1 数控加工工艺合理确定数控加工工艺对实现优质、高效和经济的数控加工具有极为重要的作用。
数控加工工艺问题的处理与普通加工工艺基本相同,在设计零件的数控加工工艺时,首先要遵循普通加工工艺的基本原则和方法,同时还必须考虑数控加工本身的特点和零件编程要求。
1.1.1 加工工艺过程和特殊要求1.加工工艺过程数控加工工艺过程是利用切削刀具在数控机床上直接改变加工对象的形状、尺寸、表面位置、表面状态等,使其成为成品或半成品的过程。
2.加工工艺的特殊要求(1)由于数控机床较普通机床的刚度高,所配的刀具也较好,因而在同等情况下,所采用的切削用量通常比普通机床大,加工效率也较高。
因此,选择切削用量时要充分考虑这些特点。
(2)由于数控机床复合化程度越来越高,因此,工序相对集中是现代数控加工工艺的特点,明显表现为工序数目少,工序内容多,并且由于在数控机床上尽可能安排较复杂的工序,所以数控加工的工序内容要比普通机床加工的工序内容复杂。
(3)由于数控机床加工的零件比较复杂,因此在确定装夹方式和夹具时,要特别注意刀具与夹具、工件的干涉问题。
1.1.2 加工工艺分析和规划加工工艺分析和规划主要从加工对象及加工区域规划、加工路线规划和加工方式规划3方面考虑。
1.加工区域规划加工区域规划是将加工对象分成不同的加工区域,分别采用不同的加工工艺和加工方式进行加工,目的是提高加工效率和质量。
常见的需要进行分区域加工的情况有以下几种。
❑加工表面形状差异较大,需要分区加工。
如加工表面由水平面和自由曲面组成。
显然,对于这两种类型可采用不同的加工方式以提高加工效率和质量,即对水平面部分采用平底刀加工,刀轨的行间距可超过刀具半径,一般为刀具直径的60%~75%,以提高加工效率。
- 1、下载文档前请自行甄别文档内容的完整性,平台不提供额外的编辑、内容补充、找答案等附加服务。
- 2、"仅部分预览"的文档,不可在线预览部分如存在完整性等问题,可反馈申请退款(可完整预览的文档不适用该条件!)。
- 3、如文档侵犯您的权益,请联系客服反馈,我们会尽快为您处理(人工客服工作时间:9:00-18:30)。
第1章数控编程加工概述本章导读数控加工工艺分析和规划数控编程刀具材料和选择原则如何合理区分加工区域的粗精加工前后模数控编程注意事项铜公拆分要点和经验总结1 / 11.1 数控加工工艺合理确定数控加工工艺对实现优质、高效和经济的数控加工具有极为重要的作用。
数控加工工艺问题的处理与普通加工工艺基本相同,在设计零件的数控加工工艺时,首先要遵循普通加工工艺的基本原则和方法,同时还必须考虑数控加工本身的特点和零件编程要求。
1.1.1 加工工艺过程和特殊要求1.加工工艺过程数控加工工艺过程是利用切削刀具在数控机床上直接改变加工对象的形状、尺寸、表面位置、表面状态等,使其成为成品或半成品的过程。
2.加工工艺的特殊要求(1)由于数控机床较普通机床的刚度高,所配的刀具也较好,因而在同等情况下,所采用的切削用量通常比普通机床大,加工效率也较高。
因此,选择切削用量时要充分考虑这些特点。
(2)由于数控机床复合化程度越来越高,因此,工序相对集中是现代数控加工工艺的特点,明显表现为工序数目少,工序内容多,并且由于在数控机床上尽可能安排较复杂的工序,所以数控加工的工序内容要比普通机床加工的工序内容复杂。
(3)由于数控机床加工的零件比较复杂,因此在确定装夹方式和夹具时,要特别注意刀具与夹具、工件的干涉问题。
1.1.2 加工工艺分析和规划加工工艺分析和规划主要从加工对象及加工区域规划、加工路线规划和加工方式规划3方面考虑。
1.加工区域规划加工区域规划是将加工对象分成不同的加工区域,分别采用不同的加工工艺和加工方式进行加工,目的是提高加工效率和质量。
常见的需要进行分区域加工的情况有以下几种。
❑加工表面形状差异较大,需要分区加工。
如加工表面由水平面和自由曲面组成。
显然,对于这两种类型可采用不同的加工方式以提高加工效率和质量,即对水平面部分采用平底刀加工,刀轨的行间距可超过刀具半径,一般为刀具直径的60%~75%,以提高加工效率。
而对曲面部分应使用球刀加工,行间距一般为0.08~0.2mm,以保证表面光洁度。
❑加工表面不同区域尺寸差异较大,需要分区加工。
如对较为宽阔的型腔可采用较大的刀具进行加工,以提高加工效率,而对于较小的型腔或转角区域使用大尺寸刀具不能进行彻底加工,应采用较小刀具以确保加工到位。
❑加工表面要求精度和表面粗糙度差异较大时,需要分区加工。
如对于同一表面的配合部位要求精度较高,需要以较小的步距进行加工,而对于其他精度和光洁度要求较低的表面可以以较大的步距加工以提高效率。
❑为有效控制加工残余高度,针对曲面的变化采用不同的刀轨形式和行间距进行分区加工。
2.加工路线规划在数控工艺路线设计时,首先要考虑加工顺序的安排,加工顺序的安排应根据零件的结构和毛坯状况,以及定位安装与夹紧的需要来考虑,重点是保证定位夹紧时工件的刚性和利于保证加工精度。
加工顺序安排一般应按下列原则进行。
❑上道工序的加工不能影响下道工序的定位与夹紧,要综合考虑。
❑加工工序应由粗加工到精加工逐步进行,加工余量由大到小。
❑先进行内腔加工工序,后进行外形加工工序。
❑尽可能采用相同定位、夹紧方式或同一把刀具加工的工序连接进行,以减少重复定位次数、换刀次数与挪动压板次数。
❑在同一次安装中进行的多道工序,应先安排对工件刚性破坏较小的工序。
另外,数控加工的工艺路线设计还要考虑数控加工工序与普通工序的衔接,数控加工的工艺路线设计常常仅是几道数控加工工艺过程,而不是指毛坯到成品的整个工艺过程。
由于数控加工工序常常穿插于零件加工工艺过程中,因此在工艺路线设计中一定要全面,瞻前顾后,使之与整个工艺过程协调吻合。
如果衔接得不好就容易产生矛盾,最好的解决办法是建立下一个工序向上一工序提出工艺要求的机制,如要不要留加工余量,留多少,定位面与定位孔的精度要求及形位公差,对校形工序的技术要求,对毛坯的热处理状态要求等。
目的是达到相互能满足加工需要,且质量及技术要求明确,交接验收有依据。
3.加工方式规划加工方式规划是实施加工工艺路线的细节设计。
主要内容如下。
❑刀具选择:为不同的加工区域、加工工序选择合适的刀具,刀具的正确选择对加工质量和效率有较大的影响。
❑刀轨形式选择:针对不同的加工区域、加工类型、加工工序选择合理的刀轨形式,以确保加工的质量和效率。
❑误差控制:确定与编程有关的误差环节和误差控制参数,保证数控编程精度和实际加工精度。
❑残余高度的控制:根据刀具参数、加工表面质量确定合理的刀轨行间距,在保证加工表面质量的前提下,可以提高加工效率。
❑切削工艺控制:切削工艺包括了切削用量控制(包括切削深度、刀具进给速度、主轴旋转方向和转速控制等)、加工余量控制、进退刀控制、冷却控制等诸多内容,是影响加工精度、表面质量和加工损耗的重要因素。
❑安全控制:包括安全高度、避让区域等涉及加工安全的控制因素。
工艺分析规划是数控编程中较为灵活的部分,受到机床、刀具、加工对象(几何特征、材料等)等多种因素的影响。
从某种程度上可以认为工艺分析规划基本上是加工经验的体现,因此要求编程人员在工作中不断总结和积累经验,使工艺分析和规划更符合其实际工件的需要。
4.工件装夹注意事项在确定定位基准与夹紧方案时应注意下列3点。
❑力求设计、工艺与编程计算的基准统一。
❑尽量减少装夹次数,尽可能做到一次定位后就能加工出全部待加工表面,避免采用占机人工调整方案。
❑夹具要开畅,其定位、夹紧机构不能影响加工中的走刀(如产生碰撞),碰到此类情况时,可采用用虎钳或加底板抽螺丝的方式装夹。
5.对刀点的确定对刀点可以设在被加工零件上,但注意对刀点必须是基准位或已精加工过的部位,有时在第一道工序后对刀点被加工毁坏,会导致第二道工序和之后的对刀点无从查找,因此在第一道工序对刀时注意要在与定位基准有相对固定尺寸关系的地方设立一个相对对刀位置,这样可以根据它们之间的相对位置关系找回原对刀点。
这个相对对刀位置通常设在机床工作台或夹具上。
选择原则如下。
❑找正容易。
❑编程方便。
❑对刀误差小。
❑加工时检查方便、可靠。
1.2 数控编程刀具数控刀具选择和切削用量确定是数控加工工艺中的重要一环,它不仅影响数控机床的加工效率,而且直接影响加工质量。
数控加工的刀具选择和切削用量确定是在人机交互状态下完成,这与普通机床加工形成鲜明的对比,同时也要求编程人员必须掌握刀具选择和切削用量确定的基本原则,在编程时充分考虑数控加工特点,能够正确选择刀具及切削用量。
1.2.1 数控刀具形状(1)平底刀:也叫平刀或端铣刀,如图1-1(a)所示,主要用于开粗、平面光刀、外形光刀和清角。
(2)圆鼻刀:也叫牛鼻刀,如图1-1(b)所示,主要用于开粗、平面光刀和外形光刀,常加工硬度较高的材料,如718、738和S136等。
常用圆鼻刀的刀角半径为R0.2~R1。
(3)球头刀:也叫球刀或R刀,如图1-1(c)所示,主要用于曲面光刀或流道加工,不对平面开粗或光刀。
(4)飞刀:如图1-1(d)所示,主要用于大面积的开粗、平面光刀和陡峭面光刀等。
常用飞刀有φ30R5、φ20R4、φ16R0.8/R0.4和φ12R0.4。
平底刀(a)圆鼻刀(b)球头刀(c)飞刀(d)图1-1 刀具形状1.2.2 数控刀具直径和长度选择(1)大工件尽量使用大直径的刀具,以提高刀具的加工效率和刚性。
曲面光刀和清角时,根据参考曲面凹陷和拐角处的最小半径值选择刀具。
开粗先采用大直径刀具,以提高效率,再采用小直径刀具进行二次开粗,二次开粗的目的是清除上一步开粗的残余料。
(2)在保证刀具刚性的前提下,刀具装夹长度依曲面形状和深度来确定,一般比加工范围高出2mm,防止出现刀具与工件相互干涉。
(3)选择小直径刀具要注意切削刃(刃长)长度。
直径小于φ6时,刀具切削刃的直径与刀柄直径不一致,一般刀柄直径为φ6,切削刃与刀柄之间形成锥形过渡,加工区域狭窄、深度较大时,可能出现刀柄与工件干涉。
1.2.3 数控刀具要求数控铣床能兼作粗精铣削,因此粗铣时,要选强度高、耐用度好的刀具,以满足粗铣时大吃刀量、大进给量的要求。
精铣时,要选精度高、耐用度好的刀具,以保证加工精度的要求。
此外,为减少换刀时间和方便对刀,应尽可能采用机夹刀和机夹刀片。
夹紧刀片的方式要选择得比较合理,刀片最好选择涂层硬质合金刀片。
以下几点罗列了对选择数控刀具的要求。
(1)要有较高的切削效率。
(2)要有较高的精度和重复定位精度。
(3)要有较高的可靠性和耐用度。
(4)实现刀具尺寸的预调和快速换刀。
(5)具有完善的模块式工具系统。
(6)建立完备的刀具管理系统。
(7)要有在线监控及尺寸补偿系统。
1.2.4 数控刀具特点(1)刚性好(尤其是粗加工刀具)、精度高、抗振及热变形小。
(2)互换性好,便于快速换刀。
(3)寿命高,切削性能稳定、可靠。
(4)刀具尺寸便于调整以减少换刀时间。
(5)能断屑和卷屑,利于切屑排除。
(6)系列化、标准化,有利于编程和刀具管理。
1.2.5 数控刀具材料刀具的选择是根据零件材料种类、硬度,以及加工表面粗糙度要求和加工余量等已知条件来决定刀片的几何结构(如刀尖圆角)、进给量、切削速度和刀片牌号等。
数控刀具材料有高速钢(分为W系列高速钢和Mo系列高速钢)、硬质合金(分为钨钴类、钨钛钴类和钨钛钽(铌)钴类)、陶瓷(纯氧化铝类(白色陶瓷)和TiC添加类(黑色陶瓷))、立方碳化硼和聚晶金刚石。
一般工厂使用最多的就是高速钢(白钢刀)和硬质合金刀具,与其他几类刀具相比,价格相对比较便宜。
❑高速钢刀具:刀刃锋利,易磨损,价格便宜,主要用于加工材料硬度较底的工件,如45#、铜公或外形光刀等。
❑硬质合金刀具:硬而脆,耐高温,主要用于加工硬度较高的工件,如前模、后模、镶件、行位或斜顶等。
硬质合金刀具需较高转速加工,否则容易崩刀。
而且加工效率和质量比高速钢刀具好。
1.2.6 数控刀具选择原则(1)根据被加工零件的表面形状选择刀具:若零件表面较平坦,可使用平底刀或飞刀进行加工;若零件表面凹凸不平,应使用球刀进行加工,以免切伤工件。
(2)根据从大到小的原则选择刀具:刀具直径越大,所能切削到的毛坯材料范围越广,加工效率越高。
(3)根据曲面曲率大小选择刀具:通常针对圆角或拐角位置的加工,圆角位越小选用的刀具直径越小,且通常圆角位的加工选用球刀。
(4)根据粗、精加工选择刀具:粗加工时强调获得最快的开粗过程,则刀具的选用偏向于大直径的平底刀或飞刀。
精加工强调获得好的表面质量,此时应选用相应小直径的平底刀(飞刀)或球刀。
1.2.7 数控刀具选择刀具的选择是数控加工工艺中重要内容之一。
选择刀具通常要考虑机床的加工性能、工序内容和工件材料等因素。
选取刀具时,要使刀具的尺寸和形状相适应。
刀具选择应考虑的主要因素如下。
(1)被加工工件的材料和性能,如金属、非金属,其硬度、刚度、塑性、韧性及耐磨性等。