间歇生产过程安全控制分析
化工单元安全操作1-7章整理

第一章化工生产安全运行及控制1.工业生产过程操作现代工业生产过程存在的安全操作与控制问题:a)开车、停车b)工艺流程及设备间切换c)工艺运行中安全控制d)间歇生产过程操作e)生产负荷的改变f)异常状态下的紧急处理对上述运行过程按一定的顺序操作;其他要求:监视和管理整个生产过程对生产过程进行规划、调度和决策生产过程的异常现象记录,事故案例的积累以及安全操作与控制措施的总结2. 影响工业生产的安全因素原材料的组成变化产品性能与规格的变化生产过程中设备的安全可靠性装置与装置、工厂与工厂之间的关联性生产设备特性的漂移控制系统失灵3.现代工业生产过程,能量平衡接近于临界状态,一个局部的扰动,就会在整个生产过程传播开来,给安全生产带来威胁。
4.影响工业生产过程控制的因素a.从负反馈角度分析:测量的影响一些生产过程的变量很难测定技术的发展,使过去某些不可测变量变为可测变量间接测量:利用可测变量与相关模型,计算不可测量的变量b.测不准原理:任何物体的一些成对的性质,比如位置和动量,不可能对两者同时精密测定。
5.工业生产自动控制.☐为了使一个工业生产过程或一个企业良好、高效地运行,都离不开对整个生产过程物料、能源、人力等的管理、组织和运作。
要达到此目的,必须对工业生产过程的信息、数据进行及时的检测和控制。
☐生产计划、生产调度、安全稳定地生产与操作等,都离不开自动化技术。
6.企业生产过程管理与控制的递阶结构生产过程→常规控制→先进控制→优化监控→决策调度7.控制变量:需要控制的工艺变量操纵变量,扰动:造成被控变量产生不期望波动的原因。
8.工艺控制流程图,它是用自控设计的文字符号和图形符号在工艺流程图上描述生产过程自动控制的原理图。
9.间歇生产分析a间歇生产过程:将有限量的物质,按规定的加工顺序,在一个或多个加工设备中加工,以获得有限量的产品的加工过程。
如需更多的产品则必须重复整个过程。
b间歇过程由多个分批操作的间歇设备单元和半操作设备单元组成。
基于模型的多尺度间歇过程性能监控
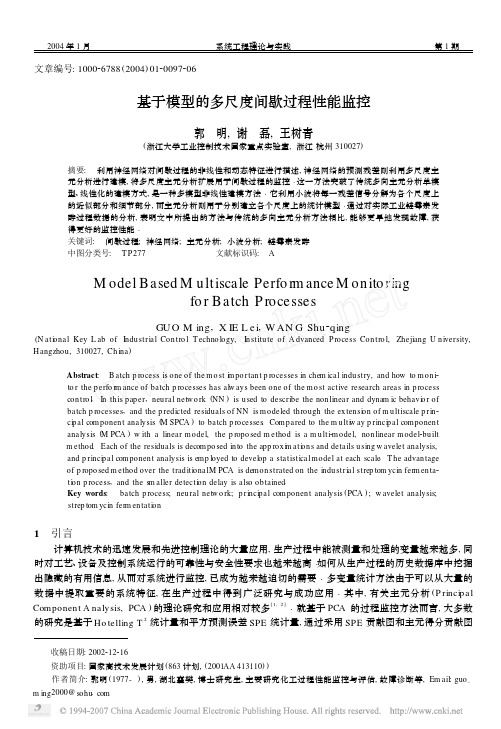
2004年1月系统工程理论与实践第1期 文章编号:100026788(2004)0120097206基于模型的多尺度间歇过程性能监控郭 明,谢 磊,王树青(浙江大学工业控制技术国家重点实验室,浙江杭州310027)摘要: 利用神经网络对间歇过程的非线性和动态特征进行描述,神经网络的预测残差则利用多尺度主元分析进行建模,将多尺度主元分析扩展用于间歇过程的监控Λ这一方法突破了传统多向主元分析单模型、线性化的建模方式,是一种多模型非线性建模方法Λ它利用小波将每一残差信号分解为各个尺度上的近似部分和细节部分,而主元分析则用于分别建立各个尺度上的统计模型Λ通过对实际工业链霉素发酵过程数据的分析,表明文中所提出的方法与传统的多向主元分析方法相比,能够更早地发现故障,获得更好的监控性能Λ关键词: 间歇过程;神经网络;主元分析;小波分析;链霉素发酵中图分类号: T P277 文献标识码: A M odel Based M u ltiscale Perfo rm ance M on ito ringfo r Batch P rocessesGU O M ing,X IE L ei,W AN G Shu2qing(N ati onal Key L ab of Indu strial Con tro l T echno logy,In stitu te of A dvanced P rocess Con tro l,Zhejiang U n iversity, H angzhou,310027,Ch ina)Abstract: Batch p rocess is one of the mo st i m po rtan t p rocesses in chem ical indu stry,and how to mon i2to r the perfo rm ance of batch p rocesses has al w ays been one of the mo st active research areas in p rocesscon tro l.In th is paper,neu ral netw o rk(NN)is u sed to describe the non linear and dynam ic behavi o r ofbatch p rocesses,and the p redicted residuals of NN is modeled th rough the ex ten si on of m u ltiscale p rin2ci pal componen t analysis(M SPCA)to batch p pared to the m u lti w ay p rinci pal componen tanalysis(M PCA)w ith a linear model,the p ropo sed m ethod is a m u lti2model,non linear model2bu iltm ethod.Each of the residuals is decompo sed in to the app rox i m ati on s and details u sing w avelet analysis,and p rinci pal componen t analysis is emp loyed to develop a statistical model at each scale.T he advan tageof p ropo sed m ethod over the traditi onalM PCA is demon strated on the indu strial strep tom ycin ferm en ta2ti on p rocess,and the s m aller detecti on delay is also ob tained.Key words: batch p rocess;neu ral netw o rk;p rinci pal componen t analysis(PCA);w avelet analysis;strep tom ycin ferm en tati on1 引言计算机技术的迅速发展和先进控制理论的大量应用,生产过程中能被测量和处理的变量越来越多,同时对工艺、设备及控制系统运行的可靠性与安全性要求也越来越高Λ如何从生产过程的历史数据库中挖掘出隐藏的有用信息,从而对系统进行监控,已成为越来越迫切的需要Λ多变量统计方法由于可以从大量的数据中提取重要的系统特征,在生产过程中得到广泛研究与成功应用Λ其中,有关主元分析(P rinci p al Com ponen t A nalysis,PCA)的理论研究和应用相对较多[1,2]Λ就基于PCA的过程监控方法而言,大多数的研究是基于Ho telling T2统计量和平方预测误差SPE统计量,通过采用SPE贡献图和主元得分贡献图收稿日期:2002212216资助项目:国家高技术发展计划(863计划,(2001AA413110)) 作者简介:郭明(1977-),男,湖北襄樊,博士研究生,主要研究化工过程性能监控与评估,故障诊断等,Em ail:guo_ m ing2000@去分离故障Λ但从本质上讲,PCA 适用于稳态线性过程,并以样本观测相互独立,不存在序列相关性为假设前提Λ但大多数的实际工业生产过程,并不满足这一假设Λ针对样本的序列相关性,文[3]提出了动态主元分析(D ynam ic PCA ),使PCA 可以扩展用于解决此类问题Λ文[4]提出非线性主元分析(N on linear PCA )用于解决变量之间存在严重非线性的问题Λ间歇过程作为一种重要的生产方式,与连续过程相比,间歇过程具有启停频繁、动态特性变化快、时序操作严格等特点Λ间歇过程的监控和故障诊断更具挑战性Λ目前间歇过程的监控方法大多是基于文[5]提出的多向主元分析(M u lti w ay PCA ,M PCA ),通过假定所有批次的生产时间相同,将间歇过程的三维数据矩阵按时间展开为二维矩阵,从而进行PCA 分解Λ但是,M PCA 仍然是一种线性模型,对于具有严重非线性的间歇生产过程,每一批次的生产时间并不相同,这一方法往往难以保证故障检测的及时性和准确性Λ本文提出一种基于模型的多尺度间歇过程监控方法,以解决间歇过程的非线性建模及故障检测问题Λ2 基于模型的多尺度建模问题2.1 模型的建立传统的基于PCA 的系统性能监控方法都是直接根据过程的测量变量y 建立相应的统计模型,由于变量之间往往存在复杂的非线性关系,导致建立的模型对故障不够灵敏,造成误报和漏报Ζ本文提出根据过程与模型的残差建立相应的模型,如图1所示Ζ图中d 为未知扰动,y s 为设定值向量,e 为过程实际输出y 与模型预测输出yδ的差值Ζ图中的模型可以是用微分方程形式描述的机理模型,也可以是用神经网络建立的黑箱模型Ζ在完全理想且无外界干扰的情况下,残差e 等于零Ζ实际上,由于各种因素的作用(如干扰、模型简化近似等),在正常操作条件下,残差e 只能是接近于零的向量,由中心极限定理,可以认为其服从正态分布Ζ当过程出现故障时,过程输出与模型预测输出的差值e 将显著增大Ζ由于过程的非线性部分已由模型所描述,残差e 对于由过程的非线性和设定值引起的变化相对不敏感,从而大大增强了故障的识别能力Ζ图1中的M SPCA 表示多尺度主元分析,这将在下面具体叙述Ζ图1 基于模型的系统性能监控示意图2.2 多尺度的PCA 性能监控传统的基于PCA 的性能监控方法都是在单一尺度上考察系统,但对于实际工业过程而言,不同的事件具有不同的时空局部特征(如不同随机干扰信号的功率谱密度函数随时间或频率而不同,各种变量的采样周期相差也较大),所以历史数据库中记录的数据实际上是不同尺度上发生事件的总和,严格讲应在不同的尺度上分别建立相应的模型Λ小波由于在时域—频域同时具有良好的局部化性质,且在不同的尺度上具有不同的分辨率,在信号的去噪、数据压缩、故障诊断等众多领域获得广泛应用Λ多尺度主元分析[6](M u ltiscale PCA ,M SPCA )是由B ak sh i 于1998年提出Λ它正是将小波分析在不同尺度上提取信号特征的能力与主元分析去除变量间相关性的能力结合起来,对系统进行监控Λ文[6]中的M SPCA 方法都是针对连续稳态过程,本文将其扩展用于间歇过程的监控Λ2.2.1 主元分析对于归一化后的数据矩阵X m ×n (m 为采样点数,n 为传感器数)的相关系数矩阵R =X T X(m -1)作奇异值分解,R =UDU T (1)89系统工程理论与实践2004年1月式中U n ×n 为酉矩阵,D 为对角矩阵,D =diag (Κi =1,…,n )Ζ其中U =[u 1,u 2,…,u n ]构成R n 空间的一组标准正交基ΖX 在基底U 各方向上的方差为Κi (i =1,2,…,n ),且满足Κ1>Κ2>…>Κn ΖU 的前k 个线性无关的向量P =[u 1,u 2,…,u k ]构成主元子空间S δ的基底,后n -k 个向量P ~=[u k +1,u k +2,…,u n ]构成残差子空间S ~的基底Ζ主元数k 可以根据某一标准来选取,通常采用的是方差累计和百分比Ζ即当k 个主元的方差贡献率大于某一事先确定的水平(常选85%)时,认为前k 个主元包含了原变量的大部分信息Ζ进一步地,数据矩阵X 可以分解为X =TP T +X ~=TP T +T ~P~T (2)式中T 和T ~分别为主元和残差得分矩阵Ζ一旦PCA 模型建立之后,对于任一时刻新采集的数据向量x ∈R n (已归一化)可以分解为x =x δ+x ~=C δx +C ~x(3)式中x δ和x ~分别为x 在子空间S δ和S ~上的投影,C δ和C ~分别为相应的投影算子矩阵,C δ=P P T ,C ~=P ~P ~T =I -C δΖPCA 通过坐标轴的旋转和正交变换消除了变量之间的相关性,并通过在主元子空间和残差子空间分别建立相应的统计模型,从而对系统进行监控Ζ具体就是建立T 2和SPE 两个统计量Ζ本文主要利用残差空间的S P E 统计量对系统进行监控Ζ其定义为SPE =‖C ~x ‖2ΦQ Α(4)式中,Q Α为SPE 统计量的控制限,在测量变量满足相互独立,服从正态分布的条件下,Q Α有如下表达式[7]:Q Α=(11+c Αh 02(2(1+(2h 0(h 0-1)(211 h 0(5)(i =6n j =k +1Κi j , i =1,2,3(6)h 0=1-(1(3 3(22(7)式中,c Α为高斯分布(1-Α)%的置信限Ζ若SPE 值小于Q Α,则认为系统处于正常操作条件;反之,则认为系统发生了异常Ζ2.2.2 小波分析小波分析是一种多分辨率分析的信号处理技术Ζ它将能量有限平方可积函数空间L 2(R )分解为一系列依次嵌套的函数子空间的和Ζ每一子空间的基底由一系列正交小波基构成Ζ该小波基函数具有如下形式:7m ,n (t )=2-m 27(2-m t -n )(8)式中,7为小波母函数,m 为尺度参数,其值决定了小波在频率空间中的位置;n 为平移参数,其值决定了小波在时域空间中的位置Ζ不同的m 和n 对应于不同的时空分辨率Ζ图2 M allat 小波分解示意图快速小波分解与重构算法由M allat 于1989年提出[8]Λ该算法将信号层层分解,每层分解的结果是将上层分解得到的低频信号进一步分解为低频(近似部分,app rox i m ati on s )和高频(细节部分,details )两部分Λ每次分解后数据量减半,时频分辨率降低一半,其分解过程见图2Λ图中c A i 和c D i 分别表示第i 级分解得到的低频部分的系数和高频部分的系数Ζ设其对应的重构信号分别A i (t )和D i (t ),则原始信号S (t )可以表达为(设分解到第L 层)S (t )=A L (t )+6j ΦL D j (t )(9)99第1期基于模型的多尺度间歇过程性能监控001系统工程理论与实践2004年1月其中,A L=6j>L D j(t)=6j>L6k∈Z c(j,k)7j,k(t),D j(t)=6k∈Z c(j,k)7j,k(t),c(j,k)为对应的小波系数Ζ即任一平方可积信号都可分解为一系列尺度上的细节信号与最粗糙尺度上的近似信号的加权和,而小波系数即为相应的权系数Ζ值得指出的是,图2中的每一层所代表的尺度不同,而不同尺度代表不同的频率范围,由于各种故障或异常工况的频率范围不同,因此不同尺度下的小波系数包含了特定的故障信息Ζ2.2.3 多尺度PCA正如前面所述,工业实际生产过程可能包括不同尺度的事件,如传感器噪声、参数漂移、操作者的误动作等,这些事件具有它们各自的时频特性Λ如传感器噪声主要位于高频部分,而参数漂移则主要位于低频部分Λ因此,实际过程的测量数据本质上是多尺度的,不同的事件出现在不同的尺度上[6]Λ传统的M PCA 方法从单一的尺度考察所有尺度上的数据,从而对某些尺度上发生事件的分辨率可能不高Λ由于不同尺度的小波变换系数包含了相对应尺度上的事件信息,因此多尺度PCA分别对各个尺度上的小波系数建立相应的PCA模型,在不同的尺度上考察事件,比传统的单尺度模型具有更高的分辨率Λ设在图1中,过程和预测模型的输出残差矩阵为E n×m,其中n为预测模型的输出变量个数,m为采集到的时间点数Ζ对每一残差变量分别进行小波分解,设分解到第L层为止Ζ那么,共可建立L+1个PCA 模型(L个细节部分的模型,和1个近似部分的模型)Ζ令X i=[c D i,1,c D i,2,…,c D i,n], i=1,2,…,L(10)X L+1=[c A L,1,c A L,2,…,c A L,n](11)式中,c D i,j表示第j个变量第i个尺度上的高频小波系数向量Ζc A L,j表示第j个变量第L个尺度上的低频小波系数向量Ζ分别对这L+1个小波系数矩阵进行主元分析,建立相应的统计模型,确定各自的SPE控制限,共得到L+1个主元模型Ζ由于信号经小波分解后得到的小波系数近似相互独立[6],也就是说,小波系数序列基本上不存在严重的自相关性.因此,对小波系数建模同时可以较好的克服传统PCA建模中的序列相关性问题Λ由于小波变换仍是正交变换,文[6]已经证明了原始测量数据空间经小波变换后保持不变,且具有相同的载荷基向量Λ因此,各个尺度上的PCA模型并不会改变变量之间的相互关系Λ文献[6]将M SPCA用于连续稳态过程的监控,获得比传统PCA更好的结果Λ本文则通过建立过程的动态模型,通,将M SPCA扩展用于间歇过程的监控Λ3 链霉素间歇发酵过程的监控链霉素发酵过程机理比较复杂,过程变量多,难以建立精确的数学模型,现有的经验模型只适用于发酵过程的某些阶段,文[9]通过规则基模式识别系统以及多元线性回归建立了链霉素的发酵模型,取得较好的结果Λ但该模型仅涉及产物浓度的预测,为了便于对系统进行监控,还需对系统中的一些关键变量进行预测Λ工业上链霉素发酵过程测量变量有:发酵时间、PH值、氮源浓度、碳源浓度、效价、粘度、罐温、罐压、空气流量等Λ这些变量对链霉素菌体生长和产物合成都有一定影响Λ但是这些变量是相互关联的,它们各自对最后产物合成所作的贡献是不一样的Λ从工艺实际角度出发,影响链霉素产率最重要的因素为碳浓度和碳氮浓度比Λ本文利用B P网络建立碳浓度、碳氮浓度比及效价这三个变量的预测模型Λ对于链霉素发酵这一具有严重非线性的系统,为了减少训练次数并易于实现起见,采用多输入单输出(M u lti p le Inp u t and Single O u tp u t,M ISO)的神经网络作为预测模型Λ就本例而言,共建立三个M ISO神经网络预测模型Λ对于具有多个输出变量的非线性系统而言,训练多个M ISO神经网络比训练单个多输入多输出(M u l2 ti p le Inp u t and M u lti p le O u tp u t,M I M O)神经网络要容易得多,且收敛更快,输出变量越多,这种优势越明显Λ链霉素的工业发酵过程约持续200-300个小时,生产上每4小时取样一次Λ在生成训练样本时,先对数据以半小时为间隔进行三次样条插值,并对测量数据引入高斯白噪声,通过插值可以得到较小时间间隔的数据以扩充样本集,使样本集具有较广泛的覆盖面[10]Λ选择正常工况下的15批报表数据按上述方法组成训练样本集,另取3批不同的报表数据组成检验样本集,以考察网络的泛化能力如何Λ网络输入为发酵时间;当前时刻的PH 值;当前时刻的碳源浓度;当前时刻的碳氮浓度比;当前时刻的效价;当前时刻的粘度;当前时刻的罐温;当前时刻的空气流量Λ网络的输出分别为下一时刻的碳源浓度,下一时刻的碳氮浓度比和下一时刻的效价Λ隐含层选Sigm o id 函数,输出层选线性函数Λ建立的三个神经网络的结构经交叉检验后,确定其输入层节点数,隐含层节点数,输出层节点数依次为{8,13,1},{8,13,1},{8,10,1}Λ网络学习过程采用反向传播—随机趋向算法[10]Λ图3为用训练好的神经网络对验证集中某一批次报表数据的验证结果Λ图中的变量均已经标准化,即化为0与1之间的值Λ图中,—表示神经网络计算值,×表示碳浓度的实际测量值,○表示碳氮浓度比的实际值,△表示产物效价的实际值Λ在建立了神经网络的预测模型之后,另取10批正常工况下的批次报表数据,用上述神经网络对上述三个变量进行预测,预测误差进行多尺度PCA 建模Λ其中,小波基选择D aubech ies 小波基函数Λ图3 BP 神经网络的验证结果下面,考察该方法的故障识别能力,并将其与多向主元分析(M PCA )进行比较Λ设从150小时开始,氮源浓度突然增加,偏离正常均值10%Λ图4为在三个尺度上的SPE 变化趋势图Λ图中的横线代表由(5)式计算得到的95%的控制限Λ其中,图4(A )为第3个尺度上的近似部分(A pp rox i m ati on )的监控结果,可以看出,从150小时开始,SPE 值已经显著地高出控制限Λ图4(B -D )为在各尺度上小波细节部分的PCA 监控结果Λ由于氮源浓度的突然增高,属于高频范围发生的事件,因此,图4(B )可以清晰地检测到这一事件的发生Λ这一尺度上细节部分的PCA 模型对于突发事件的启始与结束能够比较灵敏得检测到,而对事件发生的过程则不敏感Λ图4(C )和(D )中,除150小时左右外,其它时间点上也有若干尖峰信号超出了95%的控制限,这是由于一些变量的局部高频扰动引起的Λ这两个尺度上的尖峰信号往往代表着快速突变波动信号的发生Λ如在本例中,空气流量的频繁波动事件可以在这两个尺度上检测到Λ图4 三个尺度上的多尺度主元分析SPE 监控图图5是用训练神经网络的15批报表数据采用多向主元分析(M PCA )的方法建立相应的统计模型,并对同一故障批次数据进行监控的结果Λ从图中可以看出,M PCA 的方法在180小时之后才检验出故障,并且其SPE 值在95%的控制限上下来回波动Λ可见,M SPCA 比M PCA 能够更早地预报故障的发生,其灵敏度也要更高Λ传统的M PCA 方法对于变量均值的较小变化是不灵敏的Λ图6是采用前面训练的神经网络模型,对间歇过程与神经网络模型输出的误差E 进行传统主元分析得到的结果Λ正如前文所述,由于神经网络模型在很大程度上消除了间歇过程的严重非线性和动态特征,101第1期基于模型的多尺度间歇过程性能监控因此,误差信号对于过程变量的突然变化应该更为灵敏Λ图6也证实了这一点,160小时已检测出故障,其检测能力也要优于M PCA方法Λ从图4-图6可以看出,基于模型的多尺度PCA的故障识别能力要高于基于模型的PCA方法,而后者又要高于M PCA方法Λ图5 多向主元分析SPE监控图图6 基于模型的主元分析SPE监控图4 结论间歇生产过程是一种重要的的生产方式,如何对其性能进行监控一直是控制领域研究的热点之一Λ传统的多向主元分析(M PCA)方法通过将三维数据矩阵按时间展开为二维矩阵,从而进行PCA分解Λ本质上讲,它仍然是一种线性建模的方法Λ本文提出一种基于模型的多尺度建模方法,采用B P神经网络建立关键变量的预测模型,并对预测残差进行多尺度建模Λ由于神经网络很大程度上消除了过程的非线性和动态特征,其预测残差对于过程的故障具有更高的灵敏度Λ而对于实际工业过程而言,许多事件发生在不同的尺度上,(如每一变量的采样速率不同,频谱范围也不同),对每一尺度分别建立PCA模型,要比单一尺度的PCA模型能够更好的预报和重构故障,这是一种基于多模型的系统监控方法Λ值得注意的是,本文所采用的方法都是基于数据驱动的,而其中的预测模型也可以用基于机理的微分方程或规则推理系统来描述,即本文提出的框架也可以集成过程的先验知识,这有助于更好的识别故障发生的原因Λ事实上,对残差进行分析也可以提供控制器控制效果的一些信息,从而对控制器的性能进行评价,这是今后进一步的研究方向Λ参考文献:[1] M acGrego r J F,Kou rti T.Statistical p rocess con tro l of m u ltivariate p rocesses[J].Con tro l Engineering P ractice,1995,3(3):403-404.[2] D un ia R,Q in S J.Sub space app roach to m u ltidi m en si onal fau lt iden tificati on and recon structi on[J].A I ChE Jou r2nal,1998,44(8):1813-1831.[3] Ku W,Sto ret R H,Geo rgak is C.D istu rbance detecti on and iso lati on by dynam ic p rinci pal componen t analysis[J].Chemom etrics and In tell L ab Syst.,1995,30:179-196.[4] Dong D,M c A voy T J.Batch track ing via non linear p rinci pal componen t analysis[J].A I ChE Jou rnal,1996,42(8):2199-2208.[5] N om iko s P,M acGrego r J F.M on ito ring batch p rocesses u sing m u lti w ay p rinci pal componen t analysis[J].A I ChEJou rnal,1994,40(8):1361-1375.[6] Bak sh i B R.M u ltiscale PCA w ith app licati on to m u ltivariate statistical p rocess mon ito ring[J].A I ChE Jou rnal,1998,44(7):1596-1610.[7] Jack son J E.(1991).A U ser’s Gu ide to P rinci pal Componen ts[M].N ew Yo rk:W iley2In terscience,1991.[8] M allet S G.A theo ry fo r m u ltireso lu ti on signal decompo siti on:the w avelet rep resen tati on[J].IEEE T ran s PatternA nalM ach ine In telligence,1989,11(7):674-693.[9] 陈元青,陈琦,王树青.多元统计分析方法在链霉素发酵中的应用[J].生物工程学报,1999,15(3):368-372.[10] 王树青.生化反应过程模型化及计算机控制[M].杭州:浙江大学出版社,1998.201系统工程理论与实践2004年1月。
香精香料生产的安全性分析

香精香料生产的安全性分析左晶晶【摘要】香精香料应用于人类生活的方方面面.阐述了香精香料的制备及其主要危险性,提出了提高香精香料生产安全性的对策措施.【期刊名称】《安徽化工》【年(卷),期】2015(041)003【总页数】4页(P62-64,67)【关键词】香精香料;制备;生产安全性【作者】左晶晶【作者单位】安徽省化工研究院,安徽合肥230041【正文语种】中文【中图分类】TQ651 引言香精香料与人们的生活水平和质量的提高息息相关。
从世界范围来看,近年来香精香料工业的增长速度一直高于其它工业的平均增长速度[1]。
在我国,随着经济的发展和人们生活水平的提高,对香精香料的需求量也越来越大。
香料是能被嗅出香气或尝出香味的物质。
香精是一种由人工调配出来的含有几种、十几种乃至几十种香料的混合物,或由发酵、酶解、热反应等方法制得的含有多种香料的混合物[2]。
根据有香物质的来源,香料分为天然香料和合成香料。
香精按其用途分为日用香精、食用香精和其它香精。
目前,我国可生产各类香料约1000种,其中天然香料140余种。
2 香精香料的制备工艺香精香料的制备方法主要有四种:物理制备法、化学合成法、生物技术制备法和应用产品的调配及生产[3]。
2.1 物理制备法物理制备法即通过压榨、蒸馏、萃取、浓缩、层析芳香植物的叶、花、根、籽、皮等,得到天然香精香料(精油、萃取物、油树脂、浸膏等)[4],如肉桂精油可经分子蒸馏制备。
2.2 化学合成法目前化学合成法制备香料的种类较多,反应机理复杂,其基本反应类型为氨基酸和还原糖的加热反应[5]。
目前,热加工食品的香味多来源于氨基酸和羰基化合物的热反应[4],如脯氨酸、半胱氨酸和核糖加热反应可生成肉汤香味料;谷氨酸和葡萄糖加热反应可生成巧克力香味料;精氨酸、赖氨酸、天冬氨酸与葡萄糖加热反应可生成咖啡香味料等[6]。
以佳乐麝香生产为例,其合成原理如下:图1 佳乐麝香合成原理其工艺流程如下:①将一定量的α-甲基苯乙烯和催化剂加入五甲基茚满合成釜中,保持釜内温度50℃左右,滴加异戊烯反应。
某原料药厂间歇精馏装置工艺安全自控设计
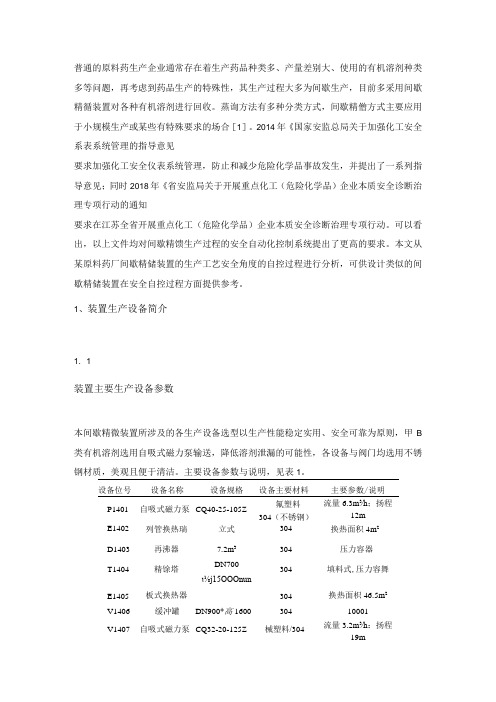
普通的原料药生产企业通常存在着生产药品种类多、产量差别大、使用的有机溶剂种类多等问题,再考虑到药品生产的特殊性,其生产过程大多为间歇生产,目前多采用间歇精循装置对各种有机溶剂进行回收。
蒸询方法有多种分类方式,间歇精僧方式主要应用于小规模生产或某些有特殊要求的场合[1]。
2014年《国家安监总局关于加强化工安全系表系统管理的指导意见要求加强化工安全仪表系统管理,防止和减少危险化学品事故发生,并提出了一系列指导意见;同时2018年《省安监局关于开展重点化工(危险化学品)企业本质安全诊断治理专项行动的通知要求在江苏全省开展重点化工(危险化学品)企业本质安全诊断治理专项行动。
可以看出,以上文件均对间歇精馈生产过程的安全自动化控制系统提出了更高的要求。
本文从某原料药厂间歇精储装置的生产工艺安全角度的自控过程进行分析,可供设计类似的间歇精储装置在安全自控过程方面提供参考。
1、装置生产设备简介1. 1装置主要生产设备参数本间歇精微装置所涉及的各生产设备选型以生产性能稳定实用、安全可靠为原则,甲B 类有机溶剂选用自吸式磁力泵输送,降低溶剂泄漏的可能性,各设备与阀门均选用不锈钢材质,美观且便于清洁。
主要设备参数与说明,见表1。
设备位号 设备名称 设备规格 设备主要材料主要参数/说明 P1401 自吸式磁力泵 CQ40-25-105Z 氟塑料304(不锈钢)流量6.3m 3∕h ;扬程12m E1402 列管换热瑞 立式 304换热面积4m 2 D1403 再沸器 7.2m 3 304压力容器 T1404 精馀塔 DN700 304填料式,压力容舞 E1405 板式换热器 ι⅛j15OOOnun 304换热面枳46.5m 2 V1406 缓冲罐 DN900*高1600 30410001 V1407 自吸式磁力泵 CQ32-20-125Z械塑料/304 流量3.2m 3∕h :扬程19mE1408列管换热器立式304换热面枳4m2 E1409丙河接收罐卧式3043OOO1P1410自吸式磁力泵CQ40-25-105氟塑料/304流量20m3∕h;扬程16m制药工艺与装哥表1主要生产设备参数与说明1.2装置主要生产设备说明原料药生产过程中待回收的丙酮溶剂,根据现行GB50160《石油化工企业设计防火规范的火灾危险性分类为甲B类液体。
化工生产过程HAZOP安全评价技术
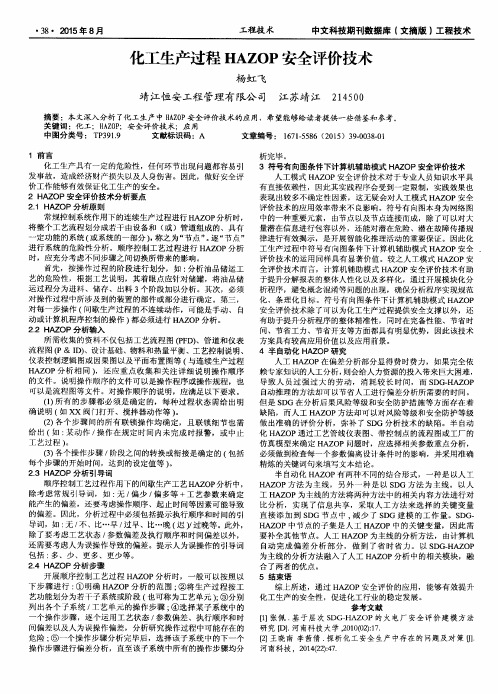
化 工生产具有一定的危险性 ,任何环节 出现 问题都容易引 发事故 ,造 成经 济财产损 失以及人 身伤 害。因此 ,做好安全评 价 工作 能够有 效保证化工 生产 的安全 。 2 H A Z OP安全评价技术分析要点
2 . 1 H A Z OP分析 原 则
常规控 制系统作用下的连续 生产过程进行 HA ZO P分析时, 将整个 工艺流程划分 成若干 由设备和 ( 或 )管道组成 的、具有 定功 能的系统 ( 或系统的一部 分 ) , 称之为 “ 节点 ” 。 逐“ 节点” 进 行系统的危险性分析 。顺序控 制工艺过程进行 H AZ OP分析 时,应 充分考虑 不同步骤之 间切换所带来 的影响 。 首先,按操作过 程的阶段进行划分 ,如 : 分析油品储运工 艺的危 险性,根据工艺说明,其着 眼点应针对储罐 ,将油 品储 运 过程 分 为 进料 、储 存 、 出料 3 个 阶段 加 以 分析 。其 次 ,必 须 对操作 过程 中所涉及 到的装置 的部件或 部分进行确定 。第三 , 对 每一步操作 ( 间歇 生产 过程的不连续动作 ,可 能是手动 、 自 动 或计 算机程序控 制的操 作 ) 都必须进行 H A Z OP分析 。 2 . 2 H A Z OP分 析 输入 所需收集 的资料不仅包括 工艺流程 图 ( P F D ) 、管道和仪表 流程 图 ( P& I D ) 、设计基础 、物料和热量平衡 、工艺控制说明、 仪表控 制逻辑 图或 因果 图以及平面布 置图等 ( 与连续生产过程 H AZ O P分析 相 同 ) ,还应重 点收集 和关注 详细 说明操作 顺序 的文件 。说明操 作顺 序的文件 可以是操作程序或操作规程 ,也 町以是流程 图等 文件 。对操作顺序 的说 明,应满足 以下要求 。 ( 1 ) 所 有 的步骤 都必须 是确定 的,每种过程 状态 需给 出明 确 说明 ( 如X X 阀 门打 开 、搅 拌 器 动 作 等 1 。 ( 2 ) 各 个步骤 间的所有 联锁操 作均确定 ,且联锁细 节也需 给 ( 如: 某动作 / 操 作在规定 时间 内未完 成时报警 ,或 中止
间歇生产进程安全控制分析
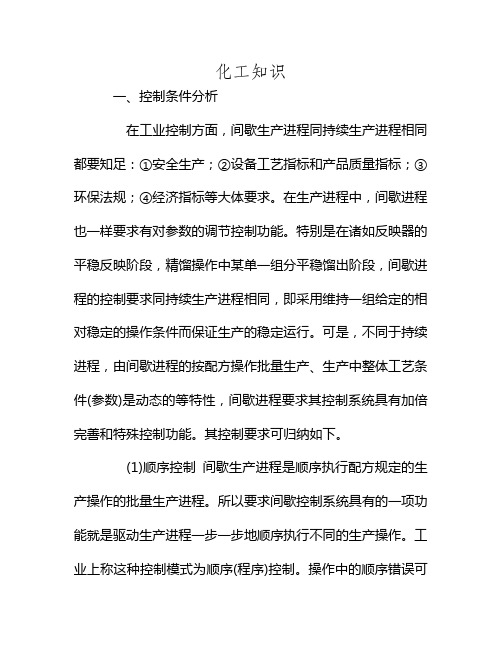
化工知识一、控制条件分析在工业控制方面,间歇生产进程同持续生产进程相同都要知足:①安全生产;②设备工艺指标和产品质量指标;③环保法规;④经济指标等大体要求。
在生产进程中,间歇进程也一样要求有对参数的调节控制功能。
特别是在诸如反映器的平稳反映阶段,精馏操作中某单一组分平稳馏出阶段,间歇进程的控制要求同持续生产进程相同,即采用维持一组给定的相对稳定的操作条件而保证生产的稳定运行。
可是,不同于持续进程,由间歇进程的按配方操作批量生产、生产中整体工艺条件(参数)是动态的等特性,间歇进程要求其控制系统具有加倍完善和特殊控制功能。
其控制要求可归纳如下。
(1)顺序控制间歇生产进程是顺序执行配方规定的生产操作的批量生产进程。
所以要求间歇控制系统具有的一项功能就是驱动生产进程一步一步地顺序执行不同的生产操作。
工业上称这种控制模式为顺序(程序)控制。
操作中的顺序错误可能致使危险物的生成乃至直接就会发生事故。
按照各步间的转换条件,顺序控制又可分为时间驱动、事件驱动和混合驱动三种顺序控制方式。
第一种是按照操作配方规定的时间段、时间点转换操作步骤,如产品的保温固化时间等。
第二种是按照被控对象的操作状态或偶发事件等转换操作步骤,如反映器加(卸)料结束、间歇式精馏的二馏出组分转换的判断等。
而更多的是第三种驱动方式,即同时依据时间和操作状态做出判断,如反映中二次反映的加料、反映中止剂的投放等。
(2)离散控制间歇生产进程中大量地利用位式控制元件,如泵、位式阀门、冰机和紧缩机等,这些设备的控制信号,和顺序操作状态标志和时间等大量信号均是离散的开关量和数字信号。
这些离散信号的传输和处置是间歇进程控制的重要环节。
(3)调节控制前面已经提到,在间歇生产进程中也一样要应用与持续生产进程控制相同的控制方式和回路来控制温度,压力、流量等工艺参数。
可是,由于间歇生产进程中的各类工艺参数是动态的,随着生产的进行,被控变量的设定值,乃至被控变量将会产生转变,控制器的参数值也可能需要进行从头整定。
生产车间安全措施分析
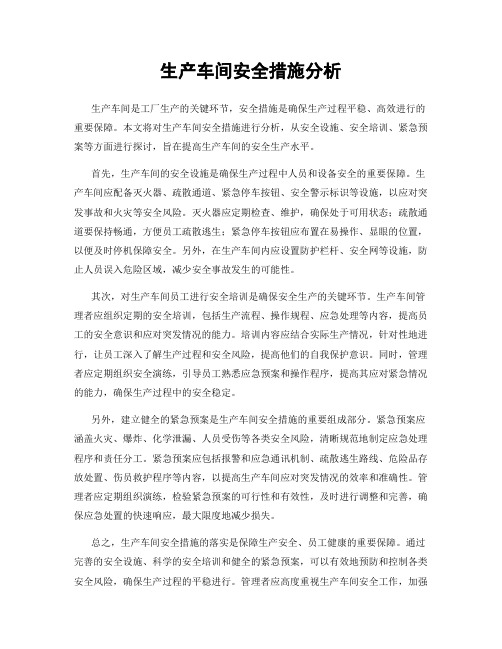
生产车间安全措施分析生产车间是工厂生产的关键环节,安全措施是确保生产过程平稳、高效进行的重要保障。
本文将对生产车间安全措施进行分析,从安全设施、安全培训、紧急预案等方面进行探讨,旨在提高生产车间的安全生产水平。
首先,生产车间的安全设施是确保生产过程中人员和设备安全的重要保障。
生产车间应配备灭火器、疏散通道、紧急停车按钮、安全警示标识等设施,以应对突发事故和火灾等安全风险。
灭火器应定期检查、维护,确保处于可用状态;疏散通道要保持畅通,方便员工疏散逃生;紧急停车按钮应布置在易操作、显眼的位置,以便及时停机保障安全。
另外,在生产车间内应设置防护栏杆、安全网等设施,防止人员误入危险区域,减少安全事故发生的可能性。
其次,对生产车间员工进行安全培训是确保安全生产的关键环节。
生产车间管理者应组织定期的安全培训,包括生产流程、操作规程、应急处理等内容,提高员工的安全意识和应对突发情况的能力。
培训内容应结合实际生产情况,针对性地进行,让员工深入了解生产过程和安全风险,提高他们的自我保护意识。
同时,管理者应定期组织安全演练,引导员工熟悉应急预案和操作程序,提高其应对紧急情况的能力,确保生产过程中的安全稳定。
另外,建立健全的紧急预案是生产车间安全措施的重要组成部分。
紧急预案应涵盖火灾、爆炸、化学泄漏、人员受伤等各类安全风险,清晰规范地制定应急处理程序和责任分工。
紧急预案应包括报警和应急通讯机制、疏散逃生路线、危险品存放处置、伤员救护程序等内容,以提高生产车间应对突发情况的效率和准确性。
管理者应定期组织演练,检验紧急预案的可行性和有效性,及时进行调整和完善,确保应急处置的快速响应,最大限度地减少损失。
总之,生产车间安全措施的落实是保障生产安全、员工健康的重要保障。
通过完善的安全设施、科学的安全培训和健全的紧急预案,可以有效地预防和控制各类安全风险,确保生产过程的平稳进行。
管理者应高度重视生产车间安全工作,加强管理和监督,提高员工的安全意识,切实保障生产车间的安全生产环境,实现生产效率与员工安全的双赢。
间歇生产过程控制与安全
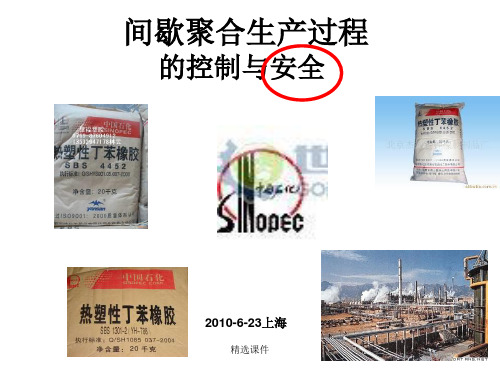
• 第四,针对中国市场特点,循序渐进开拓市场。一方面,可以按照从 工厂设备层到网络层,从硬件到软件,从安全单元到安全系统的路线 进行安全方案的应用。毕竟在中国,中小型企业占据大多数。
• 用户使用达到SIL3等级的逻辑解算器,而对于传感器和终 端设备执行机构如何设置缺乏考虑.是无法保证整体SIS系 统成为一个SIL3系统.
SIL装置=SIL传感器+SIL逻辑解算器+SIL执行机构 (+软件) 整个SIS系统的安全完整性水平SIL,是由其构成的三个单元
中最低的SIL等级所决定.这是石化企业生产装置中使用 SIS系统时,必需关切的问题.
或选用PLC实施。
• 此类技术投资较小。
精选课件
15
( 2)适合使用冗余PLC 和"小型专业ESD系统"
• 这类装置一般在同类装置中属中型装置, 需要安全联锁保护的I/O点数中等(数十点 到几百点),对系统可用度要求和安全度 要求兼顾的场合。
• 此类技术投资中等。
精选课件
16
(3)适合于专业ESD系统
指导各地对涉及危险化工工艺的生产装置进行自动化改造,
国家安全监管总局组织编制了
《首批重点监管的危险化工工艺目录》和
《首批重点监管的危险化工工艺安全控制要求、
重点监控参数及推荐的控制方案》
,现予公布.
精选课件
2
有关事项通知如下
一、化工企业要按照《首批重点监管的危险 化工工艺目录》、《首批重点监管的危险 化工工艺安全控制要求、重点监控参数及 推荐的控制方案》要求,对照本企业采用 的危险化工工艺及其特点,确定重点监控 的工艺参数,装备和完善自动控制系统, 大型和高度危险化工装置要按照推荐的控 制方案装备紧急停车系统。今后,采用危 险化工工艺的新建生产装置原则上要由甲 级资质化工设计单位进行设计。
生产安全控制措施

生产安全控制措施生产安全控制措施是企业在生产经营过程中为确保员工和设备的安全而采取的一系列管理和技术手段。
针对不同行业和生产环境,企业需要制定相应的安全控制措施来保障生产过程的顺利进行和人员安全。
首先,企业应建立健全的安全管理体系,明确责任人员,制定安全生产制度和规范,加强安全生产宣传教育,提高员工安全意识和应急处理能力。
同时,进行定期的安全生产培训,确保员工了解生产过程中可能存在的危险因素及相应的应对措施。
其次,在生产过程中,企业需要通过购置符合国家标准和要求的设备和工具,并定期进行设备检修和维护,确保设备的正常运行和安全性。
此外,建立完善的设备维护台账,及时记录设备运行状况,便于监测设备的安全性和合规性。
另外,加强现场管理是保障生产安全的关键措施之一。
企业应设立专门的安全管理部门负责监督和管理生产现场,加强对工艺流程、物料存储、消防设施等方面的监控和检查。
同时,建立健全的隐患排查制度,定期进行安全检查和隐患整改,确保生产现场的安全。
此外,企业还需要加强供应链管理,确保从供应商到生产环节的物料质量和安全性。
建立合格供应商名录,对供应商进行资质审核和监管,避免由于原材料质量问题导致的安全事故。
最后,企业需要做好应急预案和演练工作,及时处置各类突发事件,减小事故损失。
建立应急预案,明确责任分工和应急处置程序,定期组织应急演练,提高员工应急处理的能力和反应速度。
总的来说,生产安全控制措施是企业保障生产过程安全的重要手段,通过建立健全的管理体系,加强现场管理,做好设备维护和供应链管理等工作,可以有效降低生产安全风险,确保员工和设备的安全,维护企业的可持续发展。
企业应当认真履行自身的社会责任,确保生产安全,为员工提供一个安全、健康的工作环境。
生产时的危险控制范文

生产时的危险控制范文在生产过程中,危险是无处不在的。
为了确保工人的生命安全和生产活动的顺利进行,有效的危险控制措施至关重要。
本文将就生产时的危险控制进行详细阐述。
首先,要确保工作场所的安全环境。
企业应落实科学的布局规划和防护设施。
例如,在化工企业中,要对易燃、易爆、有毒、有害等物品进行合理分类仓储,并采取相应的防火、防爆、通风等措施,以减少火灾、爆炸和中毒等意外事故的发生。
其次,严格要求工人佩戴个人防护装备。
根据不同的生产环境和危险程度,工人应佩戴符合国家标准的个人防护装备,如安全帽、防护眼镜、耳塞、防护手套等。
同时,企业应定期检测和维修这些装备,确保其正常使用和防护效果。
另外,要定期进行安全培训。
企业应每年进行至少一次的安全培训,向工人普及安全知识,培养他们的安全意识和应急处理能力。
培训内容应涵盖常见的事故类型、危险源辨识、正确使用个人防护装备等方面,以确保工人在工作中能够及时应对和处理各种危险情况。
此外,要建立完善的应急预案。
应急预案是应对突发事件的重要依据。
企业应明确不同紧急情况下的处置程序和责任分工,并进行定期的演练和评估。
预案涵盖的内容包括应急报警、灭火、疏散、救护等,以便在危险事件发生时能够迅速有效地采取措施,最大限度地减少损失和伤亡。
还应加强对危险源的监控和检测。
企业应采用先进的监测设备,对危险源进行实时监控,确保及时发现和处理隐患。
例如,在化工企业中,应定期检测和监控环境空气中的有害物质浓度,以及管道、设备等的泄漏情况,确保生产过程中不会产生对工人和环境的严重威胁。
最后,要加强对工人安全意识的培养。
企业应注重培养和提高工人的安全责任感和意识。
可以通过举办安全知识竞赛、发布安全通报、组织安全交流会等方式,提高工人对危险的认识和预防能力。
同时,要重视员工的心理健康,建立健全的心理辅导体系,及时帮助员工化解压力和焦虑情绪,保持工作积极动力。
总之,生产过程中的危险控制是企业安全生产的核心任务。
常见十种安全评价方法
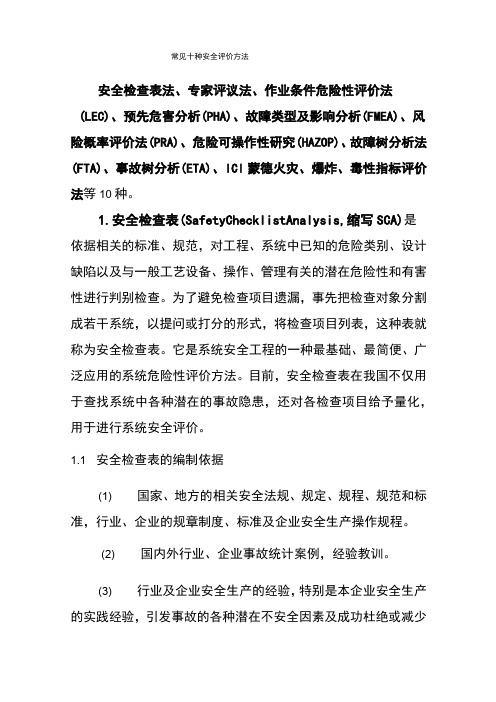
常见十种安全评价方法安全检查表法、专家评议法、作业条件危险性评价法(LEC)、预先危害分析(PHA)、故障类型及影响分析(FMEA)、风险概率评价法(PRA)、危险可操作性研究(HAZOP)、故障树分析法(FTA)、事故树分析(ETA)、ICI蒙德火灾、爆炸、毒性指标评价法等10种。
1.安全检查表(SafetyChecklistAnalysis,缩写SCA)是依据相关的标准、规范,对工程、系统中已知的危险类别、设计缺陷以及与一般工艺设备、操作、管理有关的潜在危险性和有害性进行判别检查。
为了避免检查项目遗漏,事先把检查对象分割成若干系统,以提问或打分的形式,将检查项目列表,这种表就称为安全检查表。
它是系统安全工程的一种最基础、最简便、广泛应用的系统危险性评价方法。
目前,安全检查表在我国不仅用于查找系统中各种潜在的事故隐患,还对各检查项目给予量化,用于进行系统安全评价。
1.1安全检查表的编制依据(1)国家、地方的相关安全法规、规定、规程、规范和标准,行业、企业的规章制度、标准及企业安全生产操作规程。
(2)国内外行业、企业事故统计案例,经验教训。
(3)行业及企业安全生产的经验,特别是本企业安全生产的实践经验,引发事故的各种潜在不安全因素及成功杜绝或减少事故发生的成功经验。
(4)系统安全分析的结果,即是为防止重大事故的发生而采用事故树分析方法,对系统迸行分析得出能导致引发事故的各种不安全因素的基本事件,作为防止事故控制点源列入检查表。
1.2安全检查表编制步骤要编制一个符合客观实际、能全面识别、分析系统危险性的安全检查表,首先要建立一个编制小组,其成员应包括熟悉系统各方面的专业人员。
其主要步骤有:(1)熟悉系统包括系统的结构、功能、工艺流程、主要设备、操作条件、布置和已有的安全消防设施。
(2)搜集资料搜集有关的安全法规、标准、制度及本系统过去发生过事故的资料,作为编制安全检查表的重要依据。
(3)划分单元按功能或结构将系统划分成若干个子系统或单元,逐个分析潜在的危险因素。
安全生产过程控制要点范文
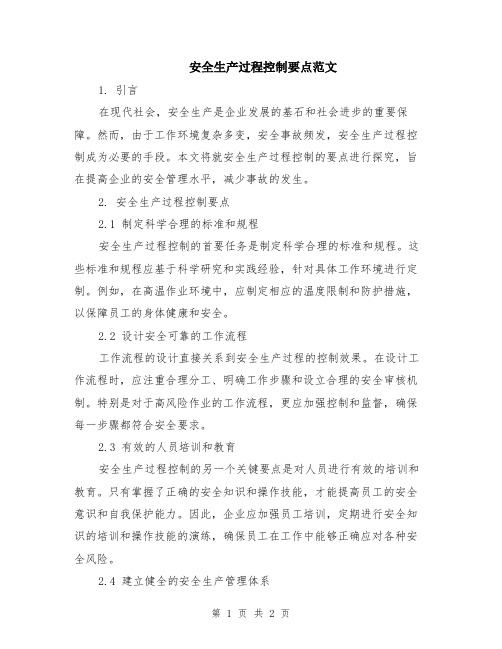
安全生产过程控制要点范文1. 引言在现代社会,安全生产是企业发展的基石和社会进步的重要保障。
然而,由于工作环境复杂多变,安全事故频发,安全生产过程控制成为必要的手段。
本文将就安全生产过程控制的要点进行探究,旨在提高企业的安全管理水平,减少事故的发生。
2. 安全生产过程控制要点2.1 制定科学合理的标准和规程安全生产过程控制的首要任务是制定科学合理的标准和规程。
这些标准和规程应基于科学研究和实践经验,针对具体工作环境进行定制。
例如,在高温作业环境中,应制定相应的温度限制和防护措施,以保障员工的身体健康和安全。
2.2 设计安全可靠的工作流程工作流程的设计直接关系到安全生产过程的控制效果。
在设计工作流程时,应注重合理分工、明确工作步骤和设立合理的安全审核机制。
特别是对于高风险作业的工作流程,更应加强控制和监督,确保每一步骤都符合安全要求。
2.3 有效的人员培训和教育安全生产过程控制的另一个关键要点是对人员进行有效的培训和教育。
只有掌握了正确的安全知识和操作技能,才能提高员工的安全意识和自我保护能力。
因此,企业应加强员工培训,定期进行安全知识的培训和操作技能的演练,确保员工在工作中能够正确应对各种安全风险。
2.4 建立健全的安全生产管理体系安全生产过程控制需要建立健全的安全生产管理体系。
这包括制定安全生产制度和规章制度,明确各级安全责任人的职责和权限,建立安全生产部门,并进行定期的安全检查和隐患排查,及时采取安全措施,防范事故的发生。
2.5 引入先进的安全技术和装备在安全生产过程控制中,引入先进的安全技术和装备是提高控制效果的重要手段。
例如,可以使用可视化监控系统、智能传感器等技术,实时监测作业场所的安全状况,及时发现并解决存在的安全隐患。
3. 结论安全生产过程控制是企业实现安全生产的核心环节。
通过制定科学合理的标准和规程,设计安全可靠的工作流程,进行有效的人员培训和教育,建立健全的安全生产管理体系,引入先进的安全技术和装备等要点,可以有效提高企业安全生产的水平,减少事故的发生。
安全生产与运行操作(三篇)

安全生产与运行操作安全生产及运行操作是指在工作过程中,采取一定的技术和管理措施,确保员工的人身安全和财产安全。
它是企业生产经营的基本要求之一,也是提高企业效益的关键手段。
下面将分别从安全生产和运行操作两个方面来探讨。
一、安全生产1、制定安全生产管理制度企业应制定完善的安全生产管理制度,包括安全责任制、安全生产规章制度、安全生产操作规程等,明确工作流程和安全责任,确保生产过程中的安全。
2、开展安全培训企业要定期开展安全培训,提高员工的安全意识和安全操作技能,使员工能够正确使用工作设备、防止事故发生、有效应对突发事件。
3、建立危险源辨识与评估体系企业要建立危险源辨识与评估体系,对生产现场存在的潜在危险源进行识别和评估,并采取相应措施控制风险,确保员工安全。
4、加强安全设施建设企业要加强安全设施建设,如消防设施、监控设备等,以预防火灾和其他事故的发生,并保障员工生命安全。
5、加强安全检查与隐患排查企业要加强对生产设备、工作环境的安全检查,及时发现和排除安全隐患,确保生产过程中的安全。
二、运行操作安全1、遵守规章制度员工在工作过程中要遵守企业的规章制度,保持良好的工作纪律,注意个人安全和他人安全。
2、正确使用工具和设备员工要正确使用工作工具和设备,按照操作规程进行操作,避免因操作不当引发事故。
3、个人防护用具员工在进行有风险的操作或工作环境中,要正确佩戴个人防护用具,避免受伤。
4、化学品和危险品的操作对于涉及化学品和危险品的操作,员工要严格遵守相关操作规程,正确使用防护设施,避免事故发生。
5、安全堆放物品员工要注意把杂物进行清理、分类堆放,避免杂乱堆放导致意外伤害。
6、应急预案在突发事件发生时,员工要快速、冷静地采取应急措施,按照预案进行应对,保证自身和他人的生命安全。
综上所述,安全生产与运行操作是企业生产经营过程中非常重要的环节。
企业要制定完善的安全生产管理制度,开展安全培训,建立危险源辨识与评估体系,加强安全设施建设和安全检查,员工要遵守规章制度,正确使用工具和设备,佩戴个人防护用具,遵守化学品和危险品操作规程,安全堆放物品,掌握应急预案等。
间歇操作名词解释
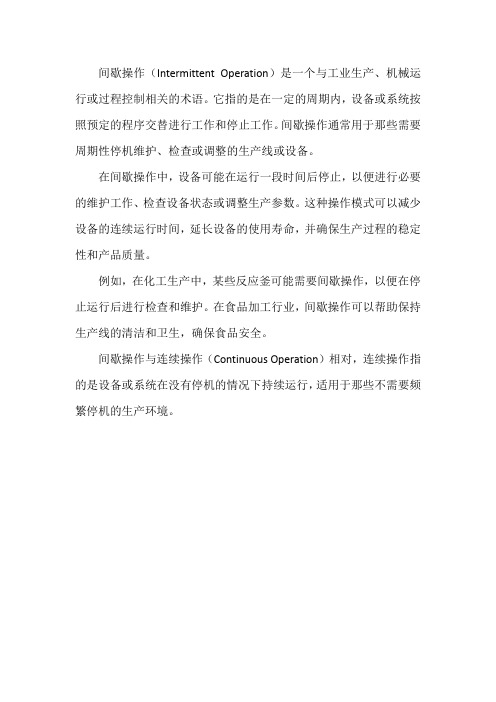
间歇操作(Intermittent Operation)是一个与工业生产、机械运行或过程控制相关的术语。
它指的是在一定的周期内,设备或系统按照预定的程序交替进行工作和停止工作。
间歇操作通常用于那些需要周期性停机维护、检查或调整的生产线或设备。
在间歇操作中,设备可能在运行一段时间后停止,以便进行必要的维护工作、检查设备状态或调整生产参数。
这种操作模式可以减少设备的连续运行时间,延长设备的使用寿命,并确保生产过程的稳定性和产品质量。
例如,在化工生产中,某些反应釜可能需要间歇操作,以便在停止运行后进行检查和维护。
在食品加工行业,间歇操作可以帮助保持生产线的清洁和卫生,确保食品安全。
间歇操作与连续操作(Continuous Operation)相对,连续操作指的是设备或系统在没有停机的情况下持续运行,适用于那些不需要频繁停机的生产环境。
浅谈化工生产过程运行安全控制
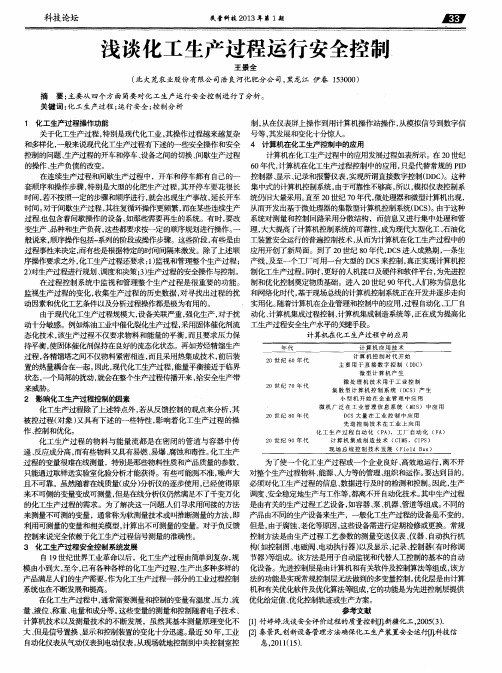
2 0世 纪 9 0年 代 计算 机集 成制 造技 术 ( C I M S, C I P S) 化工生产过程的物料与能量流都是 在密闭的管道 与容器 中传 现 场总 线控 制技术 发展 ( F i e1 d BI I S ) 递、 反应成分高 , 而有些物料又具有易燃 、 易爆、 腐蚀和毒胜。 化工生产 过程的变量很难在线测量 ,特别是那些物料 f 生 质和产品质量的参数 , 为 了使一个化工生产过程或一个企业 良好 、 高效地运行 , 离不开 只能通过取样送实验室化验分析才能获得。有些可能测不准 , 噪声大 对整个生产过程物料 、 能源 、 人力等的管理 、 组织和运作。 要达到 目的, 数据进行及时的检测和控制。 因此, 生产 且不可靠。虽然随着在线质量( 成分 ) 分析仪的逐步使用 , 已经使得原 必须对化工生产过程的信息、
持平衡 , 使 固体催化剂保持在良好的流态化状态。再如芳烃精馏生产 过程 , 各精馏塔之间不仅物料紧密相连, 而且采用热集成技术 , 前后装 置的热量耦合在—起。 因此 , 现代化工生产过程, 能量平衡接近于临界 状态 , 一个局部的扰动, 就会在整个生产过程传播开来 , 给安全生产带 来威胁。 2 影响化工生产过程控制的因素 化工生产过程除了上述特点外 , 若从反馈控制 的观 点来分析, 其 被控过程( 对象 ) 又具有下述的一些特 陛, 影响着化工生产过程的操
制, 从在仪表屏上操作到用计算机操作站操作 , 从模拟信号到数字信
关于化工生产过程 , 特别是现代化工业 , 其操作过程越来越复杂 号等, 其发展和变化十分 晾人。 和多样化, 一般来说现代化工生产过程有下述的一些安全操作和安全 4 计算机在化工生产控制中的应用 控制的问题 、 生产过程的开车和停车 、 设备之间的切换、 间歇生产过程 计算机在化工生产过程中的应用发展过程如表所示。在 2 0 世纪 的操作、 生产负债的改变。 6 0年代 , 计算机在化工生产过程控制中的应用 , 只是代替常规的 P I D 在连续生产过程和间歇生产过程中,开车和停车都有 自己的一 控制器 、 显示 、 记录和报警仪表 , 实现所谓直接数字控制( D D C ) 。这种 套J l 顶 序和操作步骤, 特别是大型的化肥生产过程 , 其开停车要花很长 集中式的计算机控制系统, 由于可靠性不够高, 所以, 模拟仪表控制系 时间 , 若不按照一定的步骤和顺序进行, 就会出现生产事故 , 延长开车 统仍旧大量采用。 直至 2 0 世纪 7 0 年代 , 微处理器和微型计算机出现 , 时间。 对于间歇生产过程 , 其往复循环操作更频繁 , 而在某些连续生产 从而开发出基于微处理器的集散型计算机控制系统( D C S ) 。由于这种 过程地 包含着间歇操作的设备 , 如那些需要再生的系统 。有时 , 要改 系统对测量和控制 回路采用分散结构 ,而信息又进行集 中处理和管 变生产、 品种和生产负荷 , 这些都要求按一定的顺序规划进行操作。 一 理 , 大大提高了计算机控制系统的可靠 陛, 成为现代大型化工、 石油化 般说来, 顺序操作包括一 系列的阶段或操作步骤。这些阶段, 有些是由 工装置安全运行的普遍控制技术, 从而为计算机在化工生产过程中的 过程事性来决定 , 而有些是根据特定 的时间间隔来激发。除了上述顺 应用开创了新局面。到了 2 0世纪 8 0年代, D C S 进入成熟期 , 一条生 序操作要求之外 , 化工生产过程还要求 : 1 ) 监视和管理整个生产过程 ; 产线 , 及至—个工厂可用一台大型的 D C S 来控制 , 真正实现计算机控 2 ) 对生产过程进行规划 、 调度和决策 ; 3 ) 生产过程的安全操作与控制。 制化工生产过程。 同时, 更好的人机接 口及硬件和软件平台 , 为先进控 在过程控制系统中监视和管理整个生产过程是很重要的功能。 制和优化控制奠定物质基础。进入 2 0世纪 9 0 年代, 人们称为信息化 监视生产过程的变化 , 收集生产过程的历史数据 , 对寻找出过程 的扰 和网络化时代 , 基于现场总线的计算机控制系统正在开发并逐步走向 实用化。 随着计算机在企业管理和控制中的应用 , 过程 自动化、 工厂 自 动因素和优化工艺条件 以及分析过程操作都是极为有用的。
工艺过程安全风险分析生产运行

设置物料规定
定期进行工艺培训、自动化控制操作规程培训
配备防护手套、防静电工作服
发生工艺事故立即调整工艺参数
3
4
15
2
橙
5
压力控制
进气量过大、进气量过小、G303压力调节不稳。
容器爆炸、火灾、其他伤害
设置压力高低报警、联锁
制定操作规程、人员岗位责任制及考核规定
处置
1
DCS控制
UPS不工作、数据传输不正确、机柜和卡件运行不正常、设施漏电
触电、其他伤害
配备UPS电源、设置自动化设施故障报警
制定自动化操作规程、加强人员劳动纪律管理
定期进行工艺培训、自动化控制操作规程培训
配备防护手套、防静电工作服
1.发生人身伤害事故立即进行救援
2.发生工艺事故立即调整工艺参数
3.发生触电事故立即切断电源,对人员进行救护
3.发生设备损坏事故立即切断设备电源
1
4
4
4
蓝
3
进料控制
进料不稳、计量泵运行不正常、
火灾、机械伤害、其他伤害
设置物料流量自动化控制
制定操作规程、人员岗位责任制及考核规定
定期进行工艺培训、自动化控制操作规程培训
配备防护手套、防静电工作服
发生工艺事故立即调整工艺参数
2
5
10
3
黄
4
回流控制
回流偏小沸T401蒸馏塔、回流过大温度不稳定、设备运行不正常
定期进行工艺培训、自动化控制操作规程培训
配备防护手套、防静电工作服
1.发生工艺事故立即调整工艺参数
2.发生爆炸:启动现场处置方案;
2
4
8
4
蓝
- 1、下载文档前请自行甄别文档内容的完整性,平台不提供额外的编辑、内容补充、找答案等附加服务。
- 2、"仅部分预览"的文档,不可在线预览部分如存在完整性等问题,可反馈申请退款(可完整预览的文档不适用该条件!)。
- 3、如文档侵犯您的权益,请联系客服反馈,我们会尽快为您处理(人工客服工作时间:9:00-18:30)。
间歇生产过程安全控制分析一、控制条件分析
在工业控制方面,间歇生产过程同连续生产过程相同都要满足:①安全生产;②设备工艺指标和产品质量指标;③环保法规;④经
济指标等基本要求。
在生产过程中,间歇过程也同样要求有对参数
的调节控制功能。
特别是在诸如反应器的平稳反应阶段,精馏操作
中某单一组分平稳馏出阶段,间歇过程的控制要求同连续生产过程
相同,即采用保持一组给定的相对稳定的操作条件而保证生产的稳
定运行。
但是,不同于连续过程,由间歇过程的按配方操作批量生产、生产中整体工艺条件(参数)是动态的等特性,间歇过程要求其
控制系统具备更加完善和特殊控制功能。
其控制要求可概括如下。
(1)顺序控制间歇生产过程是顺序执行配方规定的生产操作的批
量生产过程。
所以要求间歇控制系统具有的一项功能就是驱动生产
过程一步一步地顺序执行不同的生产操作。
工业上称这种控制模式
为顺序(程序)控制。
操作中的顺序错误可能导致危险物的生成甚至
直接就会发生事故。
根据各步间的转换条件,顺序控制又可分为时
间驱动、事件驱动和混合驱动三种顺序控制方式。
第一种是根据操
作配方规定的时间段、时间点转换操作步骤,如产品的保温固化时
间等。
第二种是根据被控对象的操作状态或偶发事件等转换操作步骤,如反应器加(卸)料结束、间歇式精馏的二馏出组分转换的判断
等。
而更多的是第三种驱动方式,即同时依据时间和操作状态做出
判断,如反应中二次反应的加料、反应中止剂的投放等。
(2)离散控制间歇生产过程中大量地使用位式控制元件,如泵、
位式阀门、冰机和压缩机等,这些设备的控制信号,以及顺序操作
状态标志和时间等大量信号均是离散的开关量和数字信号。
这些离
散信号的传输和处理是间歇过程控制的重要环节。
(3)调节控制前面已经提到,在间歇生产过程中也同样要应用与
连续生产过程控制相同的控制方法和回路来控制温度,压力、流量
等工艺参数。
但是,由于间歇生产过程中的各种工艺参数是动态的,随着生产的进行,被控变量的设定值,甚至被控变量将会产生变化,控制器的参数值也可能需要进行重新整定。
所以,在间歇生产过程
中常常要求控制回路具有“重组”和“重整”的功能。
(4)人—机接口在间歇生产过程中,操作工人的干预是正常操作
的一部分,在生产中起到十分重要的作用。
往往是一个关键的操作
是由操作工人操纵控制系统启动的,而不是由控制系统自动触发。
如反应物料的加入、中止剂的加入、产品的导出等多数是由人工判
断和启动的。
即在间歇生产过程中,操作工人一定要了解过程的运
行状态和进程。
因此,设计一个人—机接口的友好界面,便于操作
人员掌握生产的动态信息和人为地控制生产的进行是决定间歇安全
控制系统成败的一个关键。
二、间歇控制模型
(1)过程不执行任何控制任务,描述间歇过程本身特点。
如系统各单元的尺寸、功能、连接特点及原料、产品的物理化学性能等。
(2)过程I/O现场的传感器产生描述过程现状的模拟和数字信号。
如热电偶等测量元件模拟信号输出,限位开关、电机启停的开关信号,涡轮流量计的脉冲信号,智能变送器的数字信号等。
而现场的执行器接受控制系统的输出信号,执行操作指令。
(3)联锁过程控制中的联锁包括安全联锁和过程联锁。
安全联锁是一个保护人员、设备安全的控制系统。
这一系统应是不受其他控制回路或控制信号影响的相对独立的控制系统。
过程联锁的功能是保证过程系统按配方规定的顺序实施加工生产,避免产生误动作而影响生产进行和产品质量。
(4)调节控制/离散控制实施对过程系统的实时控制。
这里有三种控制形式:手动控制,基本的调节控制/离散控制和复杂的调节控制/离散控制。
手动控制主要用于操作人员对间歇过程的干预,替代自控系统以手动方式进行间歇生产的操作。
基本的调节控制/离散控制形式应用于实现各控制回路和控制自动操作,按配方要求控制过程变量。
而复杂调节控制/离散控制则通过组合多个控制回路和控制器构成串级,前馈和智能控制等先进控制系统,具有协调间歇过程各单元设备和实现设备优化操作的功能。
(5)顺序控制其作用是保证间歇生产过程按计划时间(状态)和顺序进入不同的操作工序,并与其他控制子系统一同完成配方规定的
生产任务。
它的功能主要包括判断过程时间、过程状态,适时发出转换指令并更换应用控制软件、修正必要的状态和操作参数等。
由图1—10可知,间歇控制模型除了上面介绍的有关过程的几部分外,还将包括批量生产管理,配方管理,生产调度等部分。
它们的主要功能是:根据生产计划选择并确定最优的生产调度方案,协调各间歇(批量)生产的顺序、时间、
设备连接等关系;根据过程控制配方调配生产所需资源,协调安排共享资源的使用方式;采集和管理生产数据,监视生产过程。