铝合金锻造设计及制程技术应用
7075铝合金锻造工艺
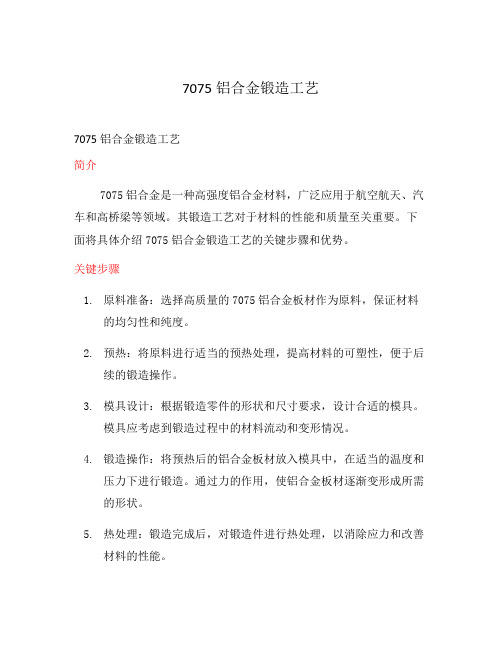
7075铝合金锻造工艺7075铝合金锻造工艺简介7075铝合金是一种高强度铝合金材料,广泛应用于航空航天、汽车和高桥梁等领域。
其锻造工艺对于材料的性能和质量至关重要。
下面将具体介绍7075铝合金锻造工艺的关键步骤和优势。
关键步骤1.原料准备:选择高质量的7075铝合金板材作为原料,保证材料的均匀性和纯度。
2.预热:将原料进行适当的预热处理,提高材料的可塑性,便于后续的锻造操作。
3.模具设计:根据锻造零件的形状和尺寸要求,设计合适的模具。
模具应考虑到锻造过程中的材料流动和变形情况。
4.锻造操作:将预热后的铝合金板材放入模具中,在适当的温度和压力下进行锻造。
通过力的作用,使铝合金板材逐渐变形成所需的形状。
5.热处理:锻造完成后,对锻造件进行热处理,以消除应力和改善材料的性能。
6.表面处理:根据实际需求,对锻造件的表面进行喷涂、抛光或阳极氧化等处理,提高其耐腐蚀性和美观度。
优势•高强度:7075铝合金具有优异的强度特性,锻造工艺能够进一步提高其强度,使其在高强度要求的领域中得到广泛应用。
•良好的可塑性:锻造过程中,铝合金板材能够充分流动和变形,便于制造复杂形状的零件。
•精确的尺寸控制:通过合理的模具设计和锻造操作,能够获得高精度和一致性的锻造件尺寸,提高产品质量。
•节约材料:锻造工艺可以最大限度地利用原料,减少浪费和成本。
结论7075铝合金锻造工艺是一种高效、精确和经济的制造方法。
它在航空航天、汽车和高桥梁等领域发挥重要作用。
通过严格控制每个步骤,可以获得高质量的7075铝合金锻造件。
工艺优化1.温度控制:在锻造过程中,合理控制锻造温度对于获得理想的锻造效果至关重要。
过高的温度可能导致过度软化或烧结,而过低的温度可能使材料难以变形。
因此,准确控制锻造温度是优化工艺的关键。
2.压力控制:合适的锻造压力可以有效促进材料流动和变形,获得所需的形状。
过高的压力可能导致过度变形或裂纹,而过低的压力可能使得零件形状不完整。
铝合金锻造设计及制程技术应用

各種鋁合金在衝擊擠出中可擠出的最小壁厚
(單位:英吋)
P.46
成形過程設計
RA=53%
RA=53%
RA=24%
•密閉式前向擠出最大 RA=70~75% 後向擠出最大RA=70~75 %;最小20~25 %
P.47
鋁扣件成形過程實體
Al1100-O
Al6061-T4
P.48
冷間鍛造模具
P.49
軸型前向擠伸標準模組
B :沖頭導引部 D :頂出部 N :補強環 D′ :成形直徑
防止沖頭偏心之導引部設計
P.55
複合擠伸沖頭
P.56
鍛粗模組結構
P.57模具補強之效果P.8實用之補強環尺寸與干涉量
P.59
模殼模仁之結合方式
P.60
內模仁之外形錐度選擇
P.61
分割模仁的設計準則
P.62
冷鍛素材退火
軟化材料使其易於成形 消除加工時所產成的內應力 調整結晶組織 均勻材質成分 延長模具壽命
• 回復及再結晶的驅動力是 變形儲能
• 冷作量大時再結晶溫度降 低
• 冷作量有一下限,低於此 則不發生在結晶
P.14
晶粒成長
P.15
晶粒組織之不良的影響
•晶粒大小會影響材料流動性 •晶粒大小會影響表面粗糙度 •晶粒粗大會降低鍛件方向性強度 •晶粒粗大易產生疲勞破壞及粒晶腐蝕 •混經使材料韌性下降 •晶粒粗大使材料塑性降低
連續鑄造生產線
直徑70㎜棒材輥製生產線
冷輥生產線
連續鑄造生產線(捲繞部份) P.28
粉末金屬合金(Powder metal alloy)
鑄錠
製成粉末
壓成塊狀
熱擠壓
浅谈对我国铝合金锻造生产工艺的应用与研究
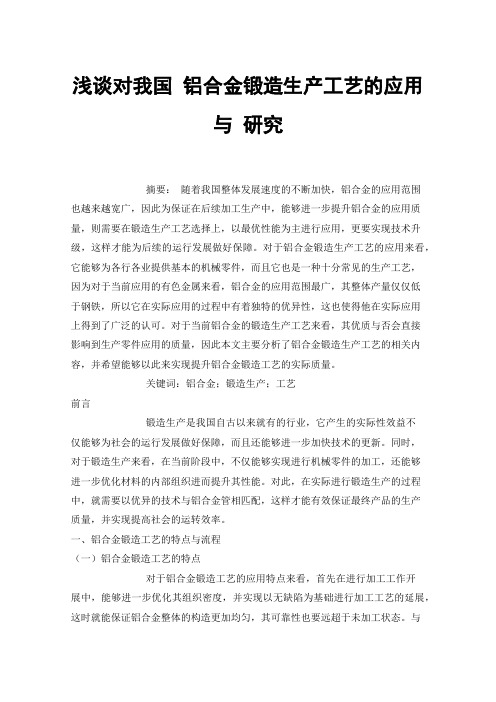
浅谈对我国铝合金锻造生产工艺的应用与研究摘要:随着我国整体发展速度的不断加快,铝合金的应用范围也越来越宽广,因此为保证在后续加工生产中,能够进一步提升铝合金的应用质量,则需要在锻造生产工艺选择上,以最优性能为主进行应用,更要实现技术升级,这样才能为后续的运行发展做好保障。
对于铝合金锻造生产工艺的应用来看,它能够为各行各业提供基本的机械零件,而且它也是一种十分常见的生产工艺,因为对于当前应用的有色金属来看,铝合金的应用范围最广,其整体产量仅仅低于钢铁,所以它在实际应用的过程中有着独特的优异性,这也使得他在实际应用上得到了广泛的认可。
对于当前铝合金的锻造生产工艺来看,其优质与否会直接影响到生产零件应用的质量,因此本文主要分析了铝合金锻造生产工艺的相关内容,并希望能够以此来实现提升铝合金锻造工艺的实际质量。
关键词:铝合金;锻造生产;工艺前言锻造生产是我国自古以来就有的行业,它产生的实际性效益不仅能够为社会的运行发展做好保障,而且还能够进一步加快技术的更新。
同时,对于锻造生产来看,在当前阶段中,不仅能够实现进行机械零件的加工,还能够进一步优化材料的内部组织进而提升其性能。
对此,在实际进行锻造生产的过程中,就需要以优异的技术与铝合金管相匹配,这样才能有效保证最终产品的生产质量,并实现提高社会的运转效率。
一、铝合金锻造工艺的特点与流程(一)铝合金锻造工艺的特点对于铝合金锻造工艺的应用特点来看,首先在进行加工工作开展中,能够进一步优化其组织密度,并实现以无缺陷为基础进行加工工艺的延展,这时就能保证铝合金整体的构造更加均匀,其可靠性也要远超于未加工状态。
与此同时,对于铝合金锻造工艺的应用来看,它能在加工过程中将铝合金的形状进行重塑,并以高精度为基础进行锻造,进而就能以机械加工为主来实现进行延伸,以此就能节省其成本,并且也能提高其质量。
其次,对于铝合金锻造工作开展来看,由于铝合金自身的导热性能良好,这也使得它在锻造过程中,其温度控制范围相对狭窄,且在整体工作开展时,能够以恒温技术为基础实现对其进行性能的转化,这时就能使其结构产生变化,并且能够实现以力学为基础来进行金属组织的改变,这时也能够实现通过外部锻造来提高其机械性能,进而也能实现提升其应用质量[1]。
铝合金锻造技术的研究与发展

铝合金锻造技术的研究与发展铝合金是一种轻质、高强度、耐腐蚀的材料,被广泛应用于汽车、飞机、电子、建筑等领域。
而铝合金的制造过程中,锻造技术是一种高效、节能、环保的加工方法。
在现代工业中,铝合金锻造技术越来越受到重视和广泛应用。
本文将围绕铝合金锻造技术的研究与发展,探讨其应用前景和发展方向。
一、铝合金锻造技术的优点铝合金锻造技术是将铝合金预热,然后通过压力作用加工成型。
与其他加工方式相比,铝合金锻造技术有以下优点:1.高效节能:锻造工艺中,铝合金在高温下易变形,所需压力较小,且能将铝合金加热均匀,从而缩短了制造周期。
2.高精度:铝合金锻造时,金属流动性能优良,能够使物品表面形状的精确度更高。
3.优良性能:铝合金锻造后,铝合金的力学性能和物理性能更加均匀,且具有更高的强度、韧性和防腐蚀性能。
4.环保:铝合金锻造过程中没有削减、切削和热处理,相比其他加工方式,铝合金锻造环保更佳。
二、铝合金锻造技术的应用前景1.汽车领域:铝合金锻造技术在汽车轮毂、发动机进气道等关键部件中的应用已成为趋势。
铝合金材料的轻量化,有利于提高汽车的节能环保性能。
2.电子领域:随着电子技术的不断发展,铝合金以其轻、薄、平等特性成为电子产品材料的首选。
特别是在手机、电脑等国民消费品制造中,铝合金以其轻质和优良的外观和性能,减轻了用户的使用负担。
3.航空航天领域:铝合金在航空航天领域中,具有优良的耐腐蚀性、高强度和轻量化等特点。
以美国的波音公司为例,其制造的飞机机身比以前的飞机机身轻了35%。
在航空航天领域中,铝合金锻造技术的应用前景十分广阔。
三、铝合金锻造技术的发展方向随着社会的不断发展和技术的不断进步,铝合金锻造技术也在不断地改进和发展。
1.数值模拟技术的发展:数值模拟技术已经成为铝合金锻造研究中不可或缺的一部分。
利用数值模拟技术可以精确地预测铝合金的变形、应力状况等,有助于提高锻造件的质量。
2.材料研究:铝合金锻造技术的发展需要更好的铝合金材料的支持。
热锻造铝合金
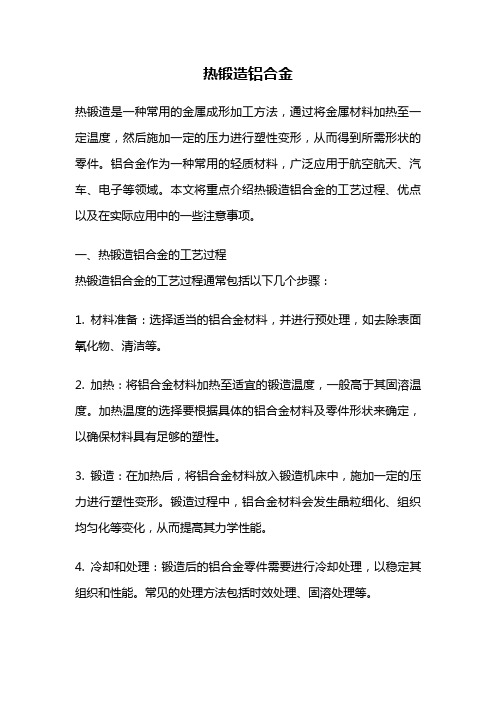
热锻造铝合金热锻造是一种常用的金属成形加工方法,通过将金属材料加热至一定温度,然后施加一定的压力进行塑性变形,从而得到所需形状的零件。
铝合金作为一种常用的轻质材料,广泛应用于航空航天、汽车、电子等领域。
本文将重点介绍热锻造铝合金的工艺过程、优点以及在实际应用中的一些注意事项。
一、热锻造铝合金的工艺过程热锻造铝合金的工艺过程通常包括以下几个步骤:1. 材料准备:选择适当的铝合金材料,并进行预处理,如去除表面氧化物、清洁等。
2. 加热:将铝合金材料加热至适宜的锻造温度,一般高于其固溶温度。
加热温度的选择要根据具体的铝合金材料及零件形状来确定,以确保材料具有足够的塑性。
3. 锻造:在加热后,将铝合金材料放入锻造机床中,施加一定的压力进行塑性变形。
锻造过程中,铝合金材料会发生晶粒细化、组织均匀化等变化,从而提高其力学性能。
4. 冷却和处理:锻造后的铝合金零件需要进行冷却处理,以稳定其组织和性能。
常见的处理方法包括时效处理、固溶处理等。
二、热锻造铝合金的优点热锻造铝合金相比其他加工方法具有以下几个优点:1. 提高材料性能:热锻造过程中,铝合金材料的晶粒细化,组织均匀化,从而提高了材料的强度、韧性等力学性能。
2. 优化零件形状:热锻造可以通过压力加工,使铝合金材料得到复杂形状的零件,满足不同领域对零件形状的需求。
3. 节约材料:热锻造可以有效利用材料,减少废料的产生,提高材料利用率。
4. 提高生产效率:热锻造具有高效、快速的特点,适用于大批量、高精度的生产需求。
三、热锻造铝合金的注意事项在热锻造铝合金过程中,需要注意以下几个问题:1. 温度控制:加热温度的选择要根据具体的铝合金材料来确定,过高或过低的温度都会影响材料的塑性和力学性能。
2. 压力控制:施加的锻造压力要适中,过大的压力会导致材料的过度变形甚至撕裂,过小的压力则无法满足零件形状的要求。
3. 冷却处理:锻造后的铝合金零件需要进行适当的冷却处理,以稳定其组织和性能。
铝合金锻造工艺技术标准

铝合金锻造工艺技术标准铝合金锻造是一种常见的金属加工方式,广泛应用于航空航天、汽车制造、机械制造等领域。
为了保证铝合金锻造的质量和安全性,需要遵循一系列的工艺技术标准。
一、原材料的选择和准备1. 原材料的选择应符合相关的标准要求,比如铝合金的成分和性能指标。
对于特殊要求的合金材料,应根据设计要求进行特殊熔炼和处理。
2. 在进行锻造前,需要对原材料进行清洁和预热处理,以确保材料的均匀性和可锻性。
二、模具设计和制造1. 根据产品的形状和尺寸要求,设计合理的模具结构,确保产品的形状和尺寸精度。
2. 制造模具时,应选用高质量的材料,进行精密加工和热处理,以提高模具的使用寿命和承载能力。
三、锻造工艺参数的确定1. 根据铝合金的材料性能和产品的形状要求,确定合适的锻造温度。
温度过高或过低都会影响产品的质量。
2. 确定合理的锻造速度和锻压力,以保证材料的变形均匀,并避免超过材料的弹性极限,导致裂纹和变形。
四、温度控制1. 锻造过程中需要严格控制温度,以保持材料在可变形状态。
对于大尺寸或复杂形状的产品,可以采用局部加热的方式,确保温度均匀。
2. 锻造完成后,及时对产品进行冷却处理,防止热裂纹和退火软化。
五、锻造后的处理1. 锻造完成后,对产品进行退火处理,以消除锻造过程中产生的应力和组织不均匀性。
2. 对于需要额外需求的产品,如表面处理、喷漆等,应根据设计要求进行后续处理,并确保处理质量符合相关标准。
六、质量检测和控制1. 对于铝合金锻造产品,需要进行各项质量指标的检测,如尺寸、力学性能、化学成分等,确保产品符合设计要求和标准要求。
2. 在锻造过程中,需要进行全程质量控制,及时发现和解决可能出现的质量问题,确保产品质量稳定可靠。
铝合金锻造工艺技术标准为铝合金锻造提供了指导和保障,通过遵循这些标准,可以保证铝合金锻造的质量和安全性。
同时,不断优化和改进工艺技术标准,可以提高铝合金锻造的效率和质量,满足不同行业对铝合金锻造产品的需求。
铝合金材料的加工技术及应用

铝合金材料的加工技术及应用铝合金是一种重要的材料,它具有良好的耐腐蚀性、强度高、密度低、耐热性能好等特点,因此广泛应用于航空、汽车、电子等领域。
本文将介绍铝合金材料的加工技术及其应用。
1. 铝合金加工技术铝合金的加工技术主要包括锻造、拉伸、挤压、压铸、铸造等。
其中,锻造是一种重要的铝合金成型技术,它通过将铝合金材料在高温、高压下进行变形,使其形成所需形状。
锻造的优点是能够得到优良的机械性能和高品质表面,适用于制造大型零件、奇形异状零件和高强度零件等。
拉伸是另一种常用的铝合金加工技术,它可以增强铝合金的强度和硬度,提高其抗拉性能。
通过拉伸可以制造各种规格的铝合金材料,如板材、管材、棒材等。
拉伸还可以通过冷拉、热拉等方式进行加工,以适应不同需求。
挤压是铝合金加工中常用的一种方法,它通过在挤压机中将铝合金材料加热,然后通过挤压机的模具进行挤出,达到所需的形状。
该工艺适用于制造各种规格的管材、棒材等铝合金材料,具有高效、高精度等优点。
压铸是一种将熔融状态下的铝合金材料压入模具中的工艺,通过快速冷却固化来制造各种铝合金零件。
压铸可以制造出形状复杂、尺寸规格精确的铝合金零件,适用于制造汽车零件、电子产品等。
铸造是一种将液态铝合金材料倒入模具中然后冷却凝固成型的工艺,通常用于制造大型铝合金零件。
铸造工艺可以制造各种铝合金零件,包括汽车零件、船舶零件、机械零件等。
2. 铝合金应用领域铝合金具有良好的耐腐蚀性、强度高、密度低、耐热性能好等特点,因此广泛应用于航空、汽车、电子等领域。
航空领域是铝合金的主要应用领域之一,航空器的大部分结构都是采用铝合金材料制造,如机身、机翼、起落架等。
铝合金材料的轻量化能够提高整个飞机的飞行性能和经济性。
汽车领域也是铝合金的重要应用领域之一。
铝合金材料的轻量化对于汽车的能耗和环保性能有着显著的贡献。
目前,汽车厂商普遍采用铝合金材料制造发动机盖、车门、车架等部件。
电子领域也广泛应用铝合金材料,如电脑外壳、手机外壳等都采用铝合金材料制造。
铝合金锻造典型工艺
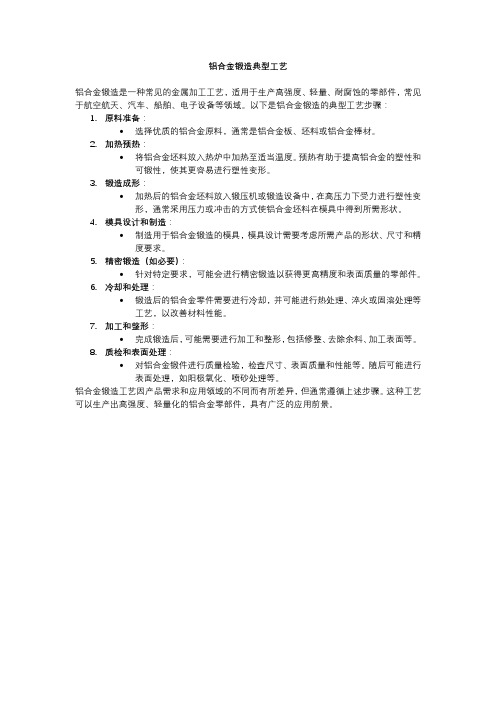
铝合金锻造典型工艺
铝合金锻造是一种常见的金属加工工艺,适用于生产高强度、轻量、耐腐蚀的零部件,常见于航空航天、汽车、船舶、电子设备等领域。
以下是铝合金锻造的典型工艺步骤:
1.原料准备:
•选择优质的铝合金原料,通常是铝合金板、坯料或铝合金棒材。
2.加热预热:
•将铝合金坯料放入热炉中加热至适当温度。
预热有助于提高铝合金的塑性和可锻性,使其更容易进行塑性变形。
3.锻造成形:
•加热后的铝合金坯料放入锻压机或锻造设备中,在高压力下受力进行塑性变形,通常采用压力或冲击的方式使铝合金坯料在模具中得到所需形状。
4.模具设计和制造:
•制造用于铝合金锻造的模具,模具设计需要考虑所需产品的形状、尺寸和精度要求。
5.精密锻造(如必要):
•针对特定要求,可能会进行精密锻造以获得更高精度和表面质量的零部件。
6.冷却和处理:
•锻造后的铝合金零件需要进行冷却,并可能进行热处理、淬火或固溶处理等工艺,以改善材料性能。
7.加工和整形:
•完成锻造后,可能需要进行加工和整形,包括修整、去除余料、加工表面等。
8.质检和表面处理:
•对铝合金锻件进行质量检验,检查尺寸、表面质量和性能等。
随后可能进行表面处理,如阳极氧化、喷砂处理等。
铝合金锻造工艺因产品需求和应用领域的不同而有所差异,但通常遵循上述步骤。
这种工艺可以生产出高强度、轻量化的铝合金零部件,具有广泛的应用前景。
浅谈锻造工艺及铝合金锻造
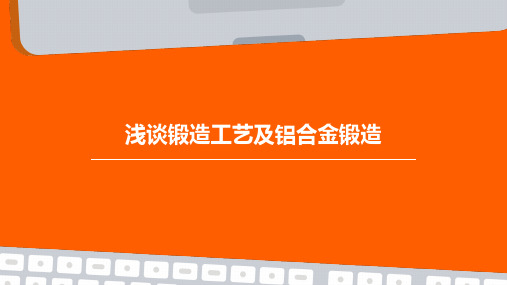
目录
• 锻造工艺概述 • 铝合金锻造的特点与优势 • 铝合金锻造的工艺流程与技术 • 铝合金锻造的质量控制与缺陷防止 • 铝合金锻造技术的发展趋势与展望
01
锻造工艺概述
锻造工艺的定义与分类
锻造工艺是指通过施加外力,使金属 坯料在高温或室温下发生塑性变形, 从而获得所需形状和性能的金属制品 的一种加工方法。根据变形温度的不 同,锻造工艺可分为热锻、温锻和冷 锻。
铝合金的铸锭
熔炼完成后,将铝液倒入模具中,冷 却凝固后形成铝合金铸锭。铸锭的尺 寸和质量对后续锻造过程有着重要影 响。
铝合金锻造前的准备
铝合金铸锭的加热
在锻造前,需要对铝合金铸锭进行加热,使其达到适合锻造 的温度。
铝合金铸锭的清理与检查
加热前需对铸锭进行清理,去除表面杂质和氧化物,并进行 质量检查,以确保其符合锻造要求。
铝合金锻件表面形成的致密氧化膜具 有优异的耐腐蚀性,可应用于海洋工 程、化学工业和食品加工等领域。
高强度与刚性
通过锻造工艺可获得高强度和刚性的 铝合金构件,适用于航空、汽车和高 速列车等领域。
03
铝合金锻造的工艺流程 与技术
铝合金的熔炼与铸锭
铝合金的熔炼
熔炼是铝合金锻造的第一步,需要将 铝和其他合金元素加热至熔点以上, 并进行搅拌和除气处理,以确保合金 成分均匀且不含杂质。
05
铝合金锻造技术的发展 趋势与展望
提高铝合金锻件的性能与质量
优化锻造工艺参数
通过精确控制锻造温度、变形速 度等参数,提高铝合金锻件的性
能和质量。
采用新型合金材料
研发高强度、高韧性、耐腐蚀的铝 合金材料,提高锻件的综合性能。
强化组织结构控制
铝合金锻造技术在汽车工业中的应用
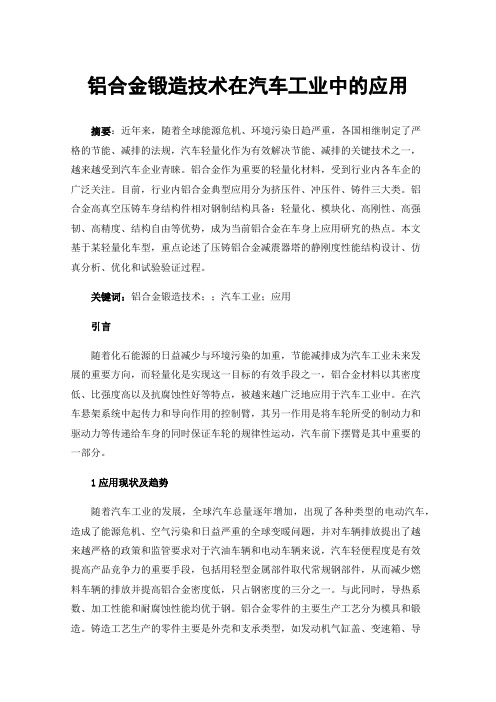
铝合金锻造技术在汽车工业中的应用摘要:近年来,随着全球能源危机、环境污染日趋严重,各国相继制定了严格的节能、减排的法规,汽车轻量化作为有效解决节能、减排的关键技术之一,越来越受到汽车企业青睐。
铝合金作为重要的轻量化材料,受到行业内各车企的广泛关注。
目前,行业内铝合金典型应用分为挤压件、冲压件、铸件三大类。
铝合金高真空压铸车身结构件相对钢制结构具备:轻量化、模块化、高刚性、高强韧、高精度、结构自由等优势,成为当前铝合金在车身上应用研究的热点。
本文基于某轻量化车型,重点论述了压铸铝合金减震器塔的静刚度性能结构设计、仿真分析、优化和试验验证过程。
关键词:铝合金锻造技术;;汽车工业;应用引言随着化石能源的日益减少与环境污染的加重,节能减排成为汽车工业未来发展的重要方向,而轻量化是实现这一目标的有效手段之一,铝合金材料以其密度低、比强度高以及抗腐蚀性好等特点,被越来越广泛地应用于汽车工业中。
在汽车悬架系统中起传力和导向作用的控制臂,其另一作用是将车轮所受的制动力和驱动力等传递给车身的同时保证车轮的规律性运动,汽车前下摆臂是其中重要的一部分。
1应用现状及趋势随着汽车工业的发展,全球汽车总量逐年增加,出现了各种类型的电动汽车,造成了能源危机、空气污染和日益严重的全球变暖问题,并对车辆排放提出了越来越严格的政策和监管要求对于汽油车辆和电动车辆来说,汽车轻便程度是有效提高产品竞争力的重要手段,包括用轻型金属部件取代常规钢部件,从而减少燃料车辆的排放并提高铝合金密度低,只占钢密度的三分之一。
与此同时,导热系数、加工性能和耐腐蚀性能均优于钢。
铝合金零件的主要生产工艺分为模具和锻造。
铸造工艺生产的零件主要是外壳和支承类型,如发动机气缸盖、变速箱、导向箱、发动机支承、转向架支承等。
;使用锻造工艺生产的零件主要是需要高机械特性的零件,如车轮、底盘悬架系统控制臂、回转截面、空调压缩机转台等。
2铝合金轻量化现如今,普通汽车中对于铝合金应用渗透效果不高,普通品牌车辆中,铝合金材料制成的各部件,转向节应用率达到左右,控制臂部分仅有。
铝合金的制作和应用
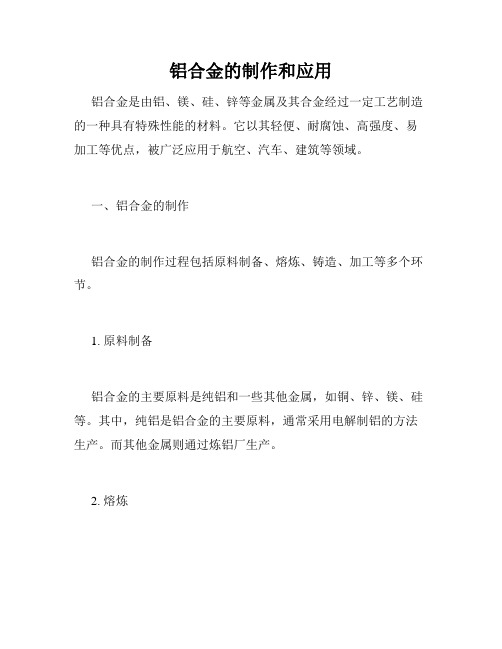
铝合金的制作和应用铝合金是由铝、镁、硅、锌等金属及其合金经过一定工艺制造的一种具有特殊性能的材料。
它以其轻便、耐腐蚀、高强度、易加工等优点,被广泛应用于航空、汽车、建筑等领域。
一、铝合金的制作铝合金的制作过程包括原料制备、熔炼、铸造、加工等多个环节。
1. 原料制备铝合金的主要原料是纯铝和一些其他金属,如铜、锌、镁、硅等。
其中,纯铝是铝合金的主要原料,通常采用电解制铝的方法生产。
而其他金属则通过炼铝厂生产。
2. 熔炼铝合金的熔炼过程一般采用电炉熔炼法或氧化铝热还原法。
其中,电炉熔炼法的优点是可以控制合金成分,制作精度高。
而氧化铝热还原法则可以制造大批量的铝合金。
3. 铸造铸造是铝合金制作中的重要环节。
铝合金的铸造方式有几种,如压铸、重力铸造、低压铸造等。
其中,压铸是最常用的铸造方式之一,可以制造出各种形状的零件,并能够达到精密加工的要求。
4. 加工铝合金的加工主要是通过机械加工、热加工等方式来实现。
机械加工主要包括切削、钻孔、搓孔等操作,常用的设备有车床、铣床、钻床等;热加工则通常用于制造大型零件,如压铸、锻造等。
二、铝合金的应用1. 航空领域因为铝合金具有轻便和耐腐蚀等特点,所以在航空领域广泛应用。
航空器的机身、发动机、座椅等很多部件都采用铝合金来制造。
2. 汽车领域铝合金在汽车领域也有很广泛的应用,主要用于车身、发动机部件、制动系统等制造。
铝合金可以有效降低汽车的重量,提高汽车的燃油经济性,并且还可以减少汽车废弃物的数量。
3. 建筑领域铝合金在建筑领域也有着很多应用,如门窗、幕墙、天窗等。
铝合金制成的门窗具有耐久性好、美观、不变形等优点。
而幕墙和天窗则可以有效地抵御风吹雨打等自然环境的侵蚀。
4. 其他领域除了上述领域,铝合金还广泛应用于计算机、手机、智能家居等电子产品,因其轻便、散热快等特点。
此外,在制造运动器材、火车、船舶、灯具等方面也有着广泛的应用。
总之,铝合金具有轻便、易加工和高强度等优点,成为现代工业中不可或缺的一种材料。
铝合金锻造工艺流程
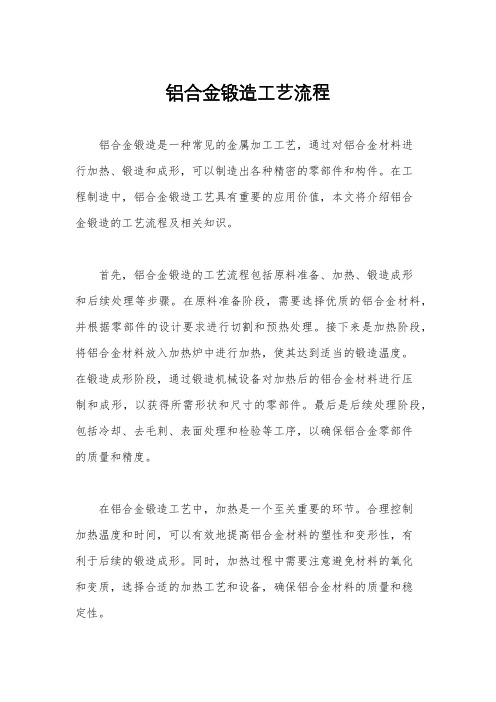
铝合金锻造工艺流程铝合金锻造是一种常见的金属加工工艺,通过对铝合金材料进行加热、锻造和成形,可以制造出各种精密的零部件和构件。
在工程制造中,铝合金锻造工艺具有重要的应用价值,本文将介绍铝合金锻造的工艺流程及相关知识。
首先,铝合金锻造的工艺流程包括原料准备、加热、锻造成形和后续处理等步骤。
在原料准备阶段,需要选择优质的铝合金材料,并根据零部件的设计要求进行切割和预热处理。
接下来是加热阶段,将铝合金材料放入加热炉中进行加热,使其达到适当的锻造温度。
在锻造成形阶段,通过锻造机械设备对加热后的铝合金材料进行压制和成形,以获得所需形状和尺寸的零部件。
最后是后续处理阶段,包括冷却、去毛刺、表面处理和检验等工序,以确保铝合金零部件的质量和精度。
在铝合金锻造工艺中,加热是一个至关重要的环节。
合理控制加热温度和时间,可以有效地提高铝合金材料的塑性和变形性,有利于后续的锻造成形。
同时,加热过程中需要注意避免材料的氧化和变质,选择合适的加热工艺和设备,确保铝合金材料的质量和稳定性。
在锻造成形阶段,需要根据零部件的设计要求和几何形状,选择合适的模具和工艺参数。
通过锻造机械设备施加压力,使加热后的铝合金材料发生塑性变形,最终获得所需形状和尺寸的零部件。
在这个过程中,需要注意控制锻造温度、压力和速度,以避免材料的裂纹和变形,确保零部件的质量和精度。
在后续处理阶段,冷却是非常重要的一环。
合理的冷却工艺可以有效地提高铝合金零部件的强度和硬度,减少内部应力和变形,提高零部件的整体性能。
同时,去毛刺和表面处理可以提高零部件的表面质量和外观效果,增强其耐腐蚀性和耐磨性,延长使用寿命。
最后,通过严格的检验和测试,可以确保铝合金零部件的质量和可靠性,满足工程制造的要求。
综上所述,铝合金锻造工艺流程包括原料准备、加热、锻造成形和后续处理等步骤,每个环节都至关重要。
合理控制加热温度和时间,选择合适的模具和工艺参数,以及严格的后续处理和检验,都是确保铝合金零部件质量的关键。
铝合金制造技术的发展及应用

铝合金制造技术的发展及应用引言铝合金工业是现代经济建设、科技进步和国防事业中的重要组成部分。
铝加工技术是铝合金产业发展的核心和支撑,对于提高铝合金产品的质量、性能和利用效率具有重要意义。
本文将围绕铝合金制造技术的发展及应用进行分析与探讨。
第一章铝合金制造技术的发展1.1 传统铝合金加工技术传统的铝合金加工技术主要是铸造、锻造、压力加工等。
其中铸造是最早出现的铝合金加工方式,也是应用最为广泛的一种。
锻造是通过对金属进行机械加工,使金属发生塑性变形而获得所需形状和尺寸的一种方法。
压力加工是指利用机械设备对材料进行拉伸和压缩,改变原材料的形状、尺寸和性质的工艺。
1.2 新型铝合金加工技术新型铝合金加工技术主要包括精密锻造技术、热挤压技术、高速加工技术、表面处理技术以及3D打印技术等。
其中,精密锻造技术具有精密成形、高质量以及节约材料的特点,适用于生产高精度、高强度和高质量的铝合金零部件。
热挤压技术是一种通过挤压变形来实现大型、精密铝合金产品加工的新型技术,具有高精度、高质量、高效率以及省材料等优点。
高速加工技术是利用高速旋转切削工具对材料进行加工,该技术具有高效率、高精度、高表面质量等优点。
表面处理技术是通过表面处理方法对铝合金进行改性,增加铝合金耐腐蚀性、抗磨损性、光泽度等性能,具有广泛应用前景。
3D打印技术是一种新型的制造技术,通过对精细的三维模型进行逐层制造,实现高精度、高可靠性和高质量的铝合金制品。
第二章铝合金制造技术的应用2.1 航空航天领域铝合金在航空航天领域得到广泛应用,如飞机结构、机翼、机身、航空发动机等铝合金部件,都采用了高强度、高韧性和轻量化的铝合金材料。
随着航空航天技术的不断发展,铝合金技术也不断升级和创新,制造技术越来越精湛,质量越来越高,性能越来越稳定。
2.2 汽车制造领域在汽车制造领域,铝合金应用也日益广泛,尤其是高端汽车和新能源汽车领域。
铝合金车身具有轻量化、抗冲击、耐用、节油等优点,能够有效提升汽车的性能和安全性能,提高汽车的能效和可靠性。
铝合金锻造技术

铝合金锻造技术
铝合金锻造技术是一种高效、高精度的金属成形加工技术,广泛应用于航空、汽车、船舶、电子、建筑等领域。
铝合金锻造技术具有以下优点:
1.高精度:铝合金锻造技术可以制造出高精度、高质量的零部件,尤其适用于制造高精度的航空零部件。
2.高效率:铝合金锻造技术可以大幅提高生产效率,缩短生产周期,降低生产成本。
3.高强度:铝合金锻造技术可以制造出高强度、高硬度的零部件,具有优异的机械性能和耐腐蚀性能。
4.节能环保:铝合金锻造技术可以减少能源消耗,降低环境污染,符合可持续发展的要求。
铝合金锻造技术主要分为以下几种:
1.自由锻造:自由锻造是指在锻造过程中不使用模具,直接将铝合金材料加热至一定温度,然后通过锤击或压力使其变形成型。
自由锻造适
用于制造大型、复杂的铝合金零部件。
2.模锻:模锻是指在锻造过程中使用模具,将铝合金材料加热至一定温度,然后通过模具施加压力使其变形成型。
模锻适用于制造中小型、精密的铝合金零部件。
3.轧制锻造:轧制锻造是指将铝合金材料通过轧制机进行加工,使其变形成型。
轧制锻造适用于制造薄板、薄壁管等铝合金材料。
4.等静压锻造:等静压锻造是指在锻造过程中使用等静压机,将铝合金材料加热至一定温度,然后通过等静压机施加压力使其变形成型。
等静压锻造适用于制造高精度、高质量的铝合金零部件。
总之,铝合金锻造技术是一种高效、高精度、高强度、节能环保的金属成形加工技术,具有广泛的应用前景。
随着科技的不断发展,铝合金锻造技术将会越来越成熟,为各行各业的发展提供更加优质的零部件。
铝合金锻压生产技术及锻件研发应用前景

Doors&Windows 摘
交通运输
其一
目前
4
锻造制坯这一工序相当关键粗
锻造成形的关键性工序之一就是模锻
克里弗兰锻造厂为了提升产品内部质量
(下转第165页)
应用与实践
Doors &Windows
需要使用到荧光渗透检测法采取锻造法制作铝合金汽车车轮目前参考文献20193175177(上接第163页)
备消防器材本项目工程原则上不安排夜间施工4防爆泄压板属于轻质脆性材料防爆泄压板泄压时呈块状及粉末状在项目方案设计时防爆泄压外墙以及外饰面的涂料总重量不超过防爆泄压板耐候性好根据建筑物的防火等级防爆泄压外墙系统中中部为空腔填充保温材料防爆泄压系统作为成熟的外墙系统防爆泄压屋面所用材料均为工厂作成型防爆泄压外墙表面非常平整众所周知应用与实践。
铝合金锻造工艺流程

铝合金锻造工艺流程铝合金是一种具有轻质、高强度和耐腐蚀性能的材料,常用于航空航天、汽车、铁路等行业。
铝合金锻造是指通过对铝合金进行热锻加工,使其达到所需的形状和性能。
本文将介绍铝合金锻造的工艺流程。
1. 原材料准备:首先需要准备合适的铝合金材料。
根据具体应用要求,选用合适的铝合金材料,如AL6061、AL7075等。
同时,对原材料进行检验,确保其符合质量要求。
2. 加热:将铝合金材料放入加热炉中进行加热。
加热温度根据具体材料和加工要求而定,通常控制在480℃~520℃之间。
加热时间也因铝合金的不同而有所差异,一般需要较长时间确保材料达到均匀的加热效果。
3. 锤击:在加热后,将铝合金材料从炉中取出,放在锻造台上。
使用大锤或锻造机械对材料进行打击,使其产生塑性变形。
通过锤击,铝合金材料的晶粒结构得到改善,同时也减少了内部缺陷。
4. 针对性锻造:根据铝合金材料的种类和形状要求,进行针对性的锻造加工。
常见的锻造方法包括自由锻造、垫片锻造、拉锤锻造等。
通过不同的锻造方式,可以使铝合金材料获得不同的形状和性能。
5. 退火处理:铝合金材料经过锻造后,晶粒结构变得致密,内部应力也有所积累。
为了消除这些应力,提高材料的强度和塑性,需要进行退火处理。
将铝合金材料放入退火炉中进行加热,并控制在适当的温度和时间下进行保温。
然后缓慢冷却,使材料得到均匀的组织结构。
6. 表面处理:铝合金材料经过锻造和退火处理后,可能会有一些表面缺陷,如氧化皮、气孔等。
为了提高材料的质量和外观,需要进行表面处理。
常见的表面处理方法包括拋光、抛光、喷砂等。
7. 检验和修整:对锻造完成的铝合金材料进行检验,确保其满足设计要求。
常见的检验方法包括外观检查、尺寸检查、化学成分分析等。
如果发现缺陷或尺寸不符合要求,需要进行修整。
8. 成品加工:将经过锻造的铝合金材料进行必要的机械加工,如切割、冲压、钻孔等。
根据具体应用需求,对成品进行加工,确定最终的形状和尺寸。
铝合金锻造工艺流程

铝合金锻造工艺流程铝合金锻造是一种常见的金属加工工艺,可以用于生产各种类型的铝合金零件。
下面将介绍铝合金锻造的基本工艺流程和相关要点。
一、准备工作1. 选择合适的锻造设备:根据待锻造的铝合金零件的尺寸和形状,选择适当的锻造设备,例如液压锻造机、气动锤等。
2. 准备原材料:选用合适的铝合金材料,确保其化学成分和物理性能满足要求。
二、模具准备1. 设计和制造模具:根据零件的形状和尺寸等要求,设计制造相应的模具。
模具通常由上模和下模组成,用于容纳和成型铝合金材料。
三、热处理1. 加热铝合金材料:将铝合金材料加热至适当的温度,一般为铝合金的固溶温度范围,以提高材料的塑性和可锻性。
2. 精确控制温度:根据铝合金材料的类型和要求,精确控制加热温度,并保持温度恒定。
四、锻造加工1. 将铝合金材料放入模具中:将预热的铝合金材料放入模具中,确保材料与模具表面充分接触。
2. 锤击或液压锻压:根据选择的锻造设备类型,使用相应的工艺手段对铝合金材料进行锤击或液压锻压,使其形成预定的形状和尺寸。
3. 重复锤击或液压加工:根据需要,可以重复进行多次锤击或液压加工,逐渐接近目标形状和尺寸。
五、冷却和退火1. 冷却锻造件:在锻造过程中,锻造件可能会产生较高的温度,需要将其逐渐冷却至室温,以提高材料的硬度和强度。
2. 退火处理:对于某些铝合金材料,在锻造后需要进行退火处理,以消除应力和改善材料的韧性和可加工性。
六、表面处理1. 修整和切割:将锻造好的零件进行修整和切割,以去除不必要的余料和表面不平整处,使其符合要求的形状和尺寸。
2. 清洁和除氧处理:清洁表面杂质和氧化物,可以采用化学清洗或电解清洗等方法,以便后续的加工和表面处理。
3. 表面处理:根据要求,可以进行表面处理,例如喷涂、阳极氧化、镀层等,以提高零件的耐腐蚀性和美观性。
以上就是铝合金锻造的基本工艺流程和相关要点。
铝合金锻造可以通过控制锻造工艺参数和选用合适的设备和模具,生产出各种形状和尺寸的铝合金零件,具有高强度、耐腐蚀、轻质等优点,在航空、汽车、机械制造等领域有广泛应用。
铝合金锻造工艺及其在航空制造中的应用
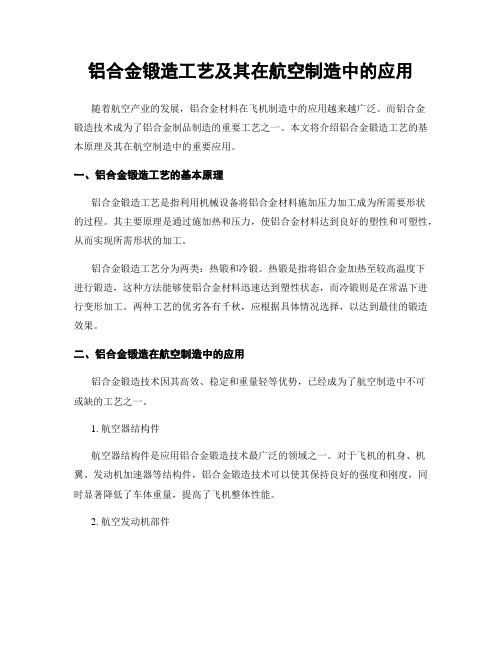
铝合金锻造工艺及其在航空制造中的应用随着航空产业的发展,铝合金材料在飞机制造中的应用越来越广泛。
而铝合金锻造技术成为了铝合金制品制造的重要工艺之一。
本文将介绍铝合金锻造工艺的基本原理及其在航空制造中的重要应用。
一、铝合金锻造工艺的基本原理铝合金锻造工艺是指利用机械设备将铝合金材料施加压力加工成为所需要形状的过程。
其主要原理是通过施加热和压力,使铝合金材料达到良好的塑性和可塑性,从而实现所需形状的加工。
铝合金锻造工艺分为两类:热锻和冷锻。
热锻是指将铝合金加热至较高温度下进行锻造,这种方法能够使铝合金材料迅速达到塑性状态,而冷锻则是在常温下进行变形加工。
两种工艺的优劣各有千秋,应根据具体情况选择,以达到最佳的锻造效果。
二、铝合金锻造在航空制造中的应用铝合金锻造技术因其高效、稳定和重量轻等优势,已经成为了航空制造中不可或缺的工艺之一。
1. 航空器结构件航空器结构件是应用铝合金锻造技术最广泛的领域之一。
对于飞机的机身、机翼、发动机加速器等结构件,铝合金锻造技术可以使其保持良好的强度和刚度,同时显著降低了车体重量,提高了飞机整体性能。
2. 航空发动机部件铝合金锻造技术的另一个主要应用领域是航空发动机部件。
通过铝合金锻造技术,可制造出具有更高强度和更长使用寿命的涡轮叶片、涡轮盘、轴承和连接器等关键部件。
这些部件的制造质量对飞机的安全和可靠性有着极大的影响。
3. 航空器外壳和内饰除了机身和结构件以外,铝合金锻造技术还被广泛应用于飞机外壳和内饰的制造中。
在外壳的制造中,铝合金锻造技术可以实现更高的制造精度和表面光滑度,使得外壳的装配更加紧密和完整。
在内饰的制造中,铝合金锻造技术可以实现更加复杂的形状和设计,让内饰更加美观和精细。
三、总结铝合金锻造技术已经成为了航空制造中不可或缺的一项工艺。
在铝合金锻造技术的不断拓展和进步的背景下,我们将会看到更加先进、精细的铝合金锻造技术的出现,这将进一步推动航空制造的发展,为民众提供更加高质量、安全和快捷的空中旅行服务。
- 1、下载文档前请自行甄别文档内容的完整性,平台不提供额外的编辑、内容补充、找答案等附加服务。
- 2、"仅部分预览"的文档,不可在线预览部分如存在完整性等问题,可反馈申请退款(可完整预览的文档不适用该条件!)。
- 3、如文档侵犯您的权益,请联系客服反馈,我们会尽快为您处理(人工客服工作时间:9:00-18:30)。
(μm)
P.21
三、鋁合金用素材之種類及特性
鑄錠 粉末金屬合金
擠製材 抽製材
輥軋材
鍛造素材一般的要求:
表面不可有刮痕:刮痕深度超過0.2~0.5mm會影響鍛件品質 表面不可有粗晶 表面不可有介金屬顆粒(如-AlFeSi針狀行晶出物)剝落後產生的坑洞
P.41
兩端同時前後向擠出設計重點(續)
P.42
同一端同時前後向擠出設計重點
P.43
不好的設計例子
未抱持
有抱持,但衝 頭強度不足
P.44
一般冷鍛件的尺寸公差(單位:英吋)
P.45
各種鋁合金在衝擊擠出中可擠出的最小壁厚
(單位:英吋)
P.46
成形過程設計
•密閉式前向擠出最大 RA=70~75% 後向擠出最大RA=70~75 %;最小20~25 % RA=53% RA=53% RA=24%
P.35
Al 7075-T42端壓試驗
端壓前胚料尺寸:Φ 30mm*30mm
端壓後高度:11.5mm 壓扁率:61.7%
產生裂紋
端壓後高度:11.25mm 壓扁率:62.5%
P.36
前向擠出設計準則
P.37
後向擠出設計準則
P.38
後向擠出沖頭壓力
P.39
冷鍛複合成形方式
P.40
兩端同時前後向擠出設計重點
點缺陷:空孔
面缺陷:晶界
線缺陷:差排
P.12
加工硬化原理
晶界
晶格 扭曲
差排堆積
P.13
鋁合金鍛造之冶金觀點
回復 再結晶 精粒成長
• 回復:減少晶格變形(殘 留應力消除)及晶格缺陷 (空孔、差排、次晶界), 晶粒形狀不發生變化 • 再結晶:產生新的晶粒 • 晶粒成長:以介面向外移 動的方式,吞併周圍的基 體,使晶逐漸長大
材料 鈦合金
密度 降伏強度/密度 4.5 13~27
鎂合金
鋁合金 特殊鋼 碳 鋼
1.8
2.8 7.8 7.8
7.1~11
11 6.4~15 3.5~7.6
銅合金
8.6
2.3以上
P.4
鋁合金具有良好熱傳導性、導電率
導電度高,僅次於銀、銅居第三位,同一重量時純鋁之導電度為銅的 2倍。 鋁合金的熱導量率大約是銅的50-60%,是低碳鋼的四倍。
成形性溫度
P.31
三、鋁合金之冷間鍛造
切斷面品質 重量誤差<1%
消除加工硬 化現象
切斷
端壓
退火
潤滑
鍛造
熱 處 理
切削
表面 處理
檢驗 及出 貨
P.32
冷間鍛造的優點
低材料損失 提升強度 節省資源 高晶密度
P.33
冷間鍛造的基本成型方式
P.34
基本冷鍛成形法則
鋁端壓細長比超過:1.8(兩端移動自由);3.2 (兩端固定)則必須做錐形 預成形,否則會挫屈
複合擠伸沖頭
P.56
鍛粗模組結構
P.57
模具補強之效果
P.58
實用之補強環尺寸與干涉量
P.59
模殼模仁之結合方式
P.60
內模仁之外形錐度選擇
P.61
分割模仁的設計準則
P.62
冷鍛素材退火
軟化材料使其易於成形 消除加工時所產成的內應力 調整結晶組織 均勻材質成分 延長模具壽命
C L
以沖頭成形型直徑 • 平面直徑
dP
為基準
• 成形面斜角 2 160 o ~ 170 o • 成形部長度
d f d P [ 2 R ( 0.2 ~ 0.3 )d P ]
• 沖頭R角
l 0.3 ~ 0.7 d P
R
• 釋放斜角 4o ~ 5o
R 0.05 ~ 0.1 d P
P.25
擠型材缺點-表面組織粗大
擠形材表面因與模具表面摩擦生熱,造成晶粒成長,使表面結晶粗大
P.26
擠形材與鍛材之金相比較
Direct Forge
Extruded
表面粗晶,鍛造時容易造成鍛件表面微裂或產生橘皮缺陷。
P.27
擠形材與鍛材之金相比較
組織均勻晶粒較細 但價格較為昂貴
連續鑄造生產線
以冰晶石(Na3AlF6)為熔劑加熱 熔融電解而得鋁(純度99.5%)
Hoopes三層式電解槽行電 解精鍊,得99.99%純鋁
P.10
鋁合金結晶構造
鋁為FCC結晶構造有四個不相平行的滑動面及三個最 密堆積方向,共有12個滑動系統
P.11
塑性變形的微觀機構
• 理論的破壞強度為:σ b=E/10 • 實際材料的破壞強度為:σ b=E/20 ~ E/100 • 差異原因:空孔、差排及微裂縫的存在
P.22
鑄錠材
粒界有溶質偏析,鍛造時容易脆裂
鑄錠在鍛造之前,需先經過均質 化處理
200X
100X
200X
100X
P.23
擠型材
組織不均勻 表面結晶粗大 頭尾料易夾入氧化物等 雜質
P.24
擠型材缺點-組織不均勻
鋁鑄錠擠製前也需先經過均質處理,消除鑄造產生之偏析組織
鑄錠原料
均質處理
鑽油平台若減少1噸重量,則海面下400呎 (約122m) 之支撐結構件可節省6噸重量。其他領域有直昇機升 降平台、伸縮鋁橋、樓梯間塔層、電纜線架等。
P.3
鋁合金高比強度特性(降伏強度/密度)
相同體積材料(Mg、Al 、鋼)時,承受荷重之彎曲性能比較
密度:Steel(7.9)> Ti(4.5) >Al(2.8) >Mg(1.8) 相對比強度:Ti> Mg> Al> Steel
Al 熱傳導係數(W/mk) 96
Mg 72
Ti 16 室溫;Mg(AZ91D);Al(A380);Ti(純 Ti)
P.5
鋁合金無毒特性
鋁品因具有高防腐性、質輕與薄等特點,常用於飲料、藥品、香煙等 包裝材。 全球80%飲料罐是鋁製品,北美洲每天消耗2.9億個,其中1.75億個被 回收再利用。1998年歐洲飲料罐約需325億個,鋁罐市場佔有率約52%。 鋁罐發展趨向薄肉化,肉厚由1976年的0.4mm降至1998年的0.26mm以下。 在先進科技研發下,鋁罐重已減少30%。
P.47
鋁扣件成形過程實體
Al1100-O
Al6061-T4
P.48
冷間鍛造模具
P.49
軸型前向擠伸標準模組
P.50
管型前向擠伸標準模組
P.51
後向擠伸標準模組
模組設計主要考慮重點:
1、主要成形元件形狀設計
2、成形元件之固緊方式 3、成形壓力之分散 4、母模承受高壓負荷之補強 5、頂出空間之考量 6、工件脫料之設計 7、上下成形元件之定位與調整方式
直徑70㎜棒材輥製生產線
冷輥生產線
連續鑄造生產線(捲繞部份)
P.28
粉末金屬合金(Powder metal alloy)
鑄錠 製成粉末 壓成塊狀
熱擠壓
切成塊狀
P.29
粉末金屬合金與一般鋁合金的抗拉強度比較
粉末金屬合金
汽缸用鍛造合金
P.30
成形溫度與成形性的關係
成形性 一般鋁合金金材
汽缸粉末冶金材
P.65
鋁合金冷鍛使用的潤滑劑
•黏度越高越好
P.66
三、鋁合金之熱間鍛造
下料 加熱 預成形
剪緣
粗形鍛造
加熱
• 混晶( duplex grain structure):同一鍛件內 晶粒大小相差懸殊 材料韌性下降
• 鍛件表面晶粒大小懸殊
電鍍後色澤不同
P.16
鋁合金7075素材的表面粗晶造成的鍛造後 的”橘皮orange peel”現象
在扭曲的表面上 明顯的有大量的 微裂縫存在
P.17
粗晶造成鋁合金強度的下降
材料 1050 1100
2014
退火溫度,℃ 340 340
340
硬度(HB) 23 23
47
2017
3003 5056 6061 6063
340
413 340 340 340
45
28 65 30 30
一般冷鍛用鋁合金退火溫度與硬度
P.63
鋁合金冷鍛之潤滑皮膜處理工程
P.64
各種磷酸鹽皮膜之摩擦係數
⑪
⑧ ⑥
① ②
⑤ ④
⑳ ③
⑦
⑨ ⑩
8、模具元件幾何精度之要求
9、成形過程之定位抱持設計
⑫ ⑬ ⑭
10、整體模座之定位與防止偏心設計
11、模座與機台空間之搭配 12、安裝與維修方便性之考量
⑯
⑮
⑰ ⑱ ⑲
P.52
後向擠伸沖頭安裝方式
不理想
理想方式
可行方式
確實壓緊
間隙0.1 ~ 0.2mm
P.53
後向擠伸沖頭
P.7
鋁合金可回收特性
生產初生鋁錠消耗能源約 13.0~15.18 kwh/kg,再生鋁錠僅約其5%(0.759 kwh/kg )
生產初生鋁錠之冶煉技術已較1950年大為精 進,目前所需電能減少約33% 生產粗鋼消耗能源約5.23kwh/kg,廢鋼回收再 生所需消耗能源一般約可低於粗鋼消耗能源之 40%(2.09kwh/kg),但若以電爐法則僅約其 13%(0.679kwh/kg) 「不活性陽極與活性陰極精鍊鋁技術」研發 成功,可減少鋁合金生產成本1/3
P.6
鋁合金加工特性
鑄造加工