催化剂硫化
催化剂硫化的主要步骤

催化剂硫化的主要步骤催化剂硫化是制备硫化催化剂的重要工艺步骤之一。
硫化催化剂具有催化剂活性高、稳定性好等优点,广泛应用于化工领域中的各种催化反应中。
下面将介绍催化剂硫化的主要步骤。
步骤一:催化剂的选择催化剂硫化的第一步是选择合适的催化剂。
催化剂的选择应根据具体的反应要求来确定。
常见的催化剂包括金属催化剂、氧化物催化剂、酸碱催化剂等。
在选择催化剂时,需要考虑催化剂的活性、选择性、稳定性以及成本等因素。
步骤二:催化剂的预处理在催化剂硫化之前,需要对催化剂进行预处理。
预处理的目的是去除催化剂表面的杂质和不稳定物质,提高催化剂的活性和稳定性。
常见的预处理方法包括洗涤、焙烧、还原等。
步骤三:硫化剂的选择硫化剂是催化剂硫化的关键步骤。
硫化剂可以是硫化氢、硫醇、硫酸等。
根据具体的反应要求和催化剂的特性,选择合适的硫化剂进行硫化。
硫化剂的选择应考虑硫化速率、硫化效率以及对催化剂活性的影响等因素。
步骤四:硫化条件的控制硫化过程中,硫化条件的控制非常重要。
硫化温度、硫化时间、硫化压力等条件的选择应根据催化剂和硫化剂的性质来确定。
硫化温度过高或过低都会影响硫化效果,硫化时间过长或过短也会导致催化剂的质量下降。
步骤五:催化剂的活化催化剂硫化完成后,还需要对催化剂进行活化处理。
活化的目的是进一步提高催化剂的活性和稳定性。
常见的活化方法包括还原、氧化、钝化等。
活化过程中需要控制好活化剂的浓度、温度和时间等参数,以保证活化效果的良好。
步骤六:催化剂的测试和评价催化剂硫化完成后,需要对催化剂进行测试和评价。
测试的目的是评估催化剂的催化性能和稳定性。
常见的测试方法包括催化活性测试、选择性测试、寿命测试等。
评价的目的是确定催化剂的优缺点,为后续的催化反应提供依据。
催化剂硫化的主要步骤包括催化剂的选择、催化剂的预处理、硫化剂的选择、硫化条件的控制、催化剂的活化以及催化剂的测试和评价。
这些步骤的正确进行可以保证催化剂的质量和活性,从而提高催化反应的效果和产率。
加氢催化剂预硫化方案

1. 引言加氢催化剂是广泛应用于石化工业领域的关键催化剂之一。
为了提高加氢催化剂的活性和稳定性,预硫化技术被广泛应用。
本文将从预硫化的原理、影响因素以及常见的预硫化方案等方面进行探讨。
2. 预硫化的原理预硫化是指在加氢催化剂使用之前,使用硫化物溶液进行处理,使其表面形成一层硫化物膜。
这一膜可以防止催化剂表面被氧化物或其他不活性物质占据,从而提高催化剂的活性和稳定性。
预硫化的原理可以归结为两个方面:•活性金属硫化物的形成:活性金属如镍、钼等能够与硫化物反应形成硫化物,这种硫化物能够促进加氢反应的进行,提高催化剂的反应活性。
•表面硫化膜的形成:硫化物膜可以阻隔外界氧气和不活性物质的侵蚀,减少催化剂的表面被氧化的机会,提高催化剂的稳定性。
3. 预硫化的影响因素预硫化的效果受到多种因素的影响,下面列举了一些主要的影响因素:3.1 硫化剂的选择预硫化过程中使用的硫化剂对催化剂的性能起着至关重要的作用。
常用的硫化剂包括硫化氢(H2S)、二硫化碳(CS2)等。
不同的硫化剂在反应中会产生不同的硫化物,并对催化剂表面的化学状态产生影响。
3.2 预硫化温度和时间预硫化温度和时间是影响预硫化效果的关键因素。
一般来说,高温和长时间的预硫化会使硫化剂更充分地与催化剂发生反应,生成更完善的硫化物膜。
然而,过高的温度可能会导致催化剂的部分活性成分被分解或损失,因此需要根据具体情况选择合适的预硫化温度和时间。
3.3 氛围条件预硫化过程中的气氛条件也会对催化剂的预硫化效果产生影响。
一般情况下,加氢环境中的氢气浓度越高,硫化剂与催化剂的反应速度越快,硫化物膜形成的效果也越好。
4. 常见的预硫化方案4.1 H2S气体预硫化H2S气体预硫化是一种常用的预硫化方式。
预硫化过程中,将催化剂放入加热炉中,通入含有H2S气体的加硫气体。
通过控制炉内温度和气氛浓度,使硫化剂与催化剂表面反应生成硫化物。
4.2 溶液浸泡预硫化溶液浸泡预硫化是另一种常见的预硫化方式。
等温变换催化剂硫化方案

在常温常压下二硫化碳为无色透明微带芳香味的脂溶性液体,有杂质时呈黄色,普通试剂有腐败臭鸡蛋味,具有极强的挥发性、易燃性和爆炸性。
燃烧时伴有蓝色火焰并分解成二氧化碳与二氧化硫。
人吸入最低致死量为4000ppm (30 分钟)。
急性中毒时,初期兴奋、头痛,继而意识丧失、昏睡和死亡。
低浓度长期暴露时,下肢浮现多发性神经炎,伴有头痛、失眠、性欲减退和记忆力下降,脱离接触时能康复。
长期暴露会发生视网膜症和肾疾患为特征的血管损伤。
外观与性状:无色或者淡黄色透明液体,纯品有乙醚味,易挥发。
熔点:-111.9℃密度:1.26g/cm相对蒸气密度(空气=1):2.64沸点:46.2℃稳定性:稳定份子式:CS2相对份子质量:76.14饱和蒸气压(28℃时):53.32kPa燃烧热:1030.8kJ/mol临界温度:279℃临界压力:7.90MPa闪点:-30℃爆炸上限(体积分数):60.0引燃温度:90℃爆炸下限(体积分数):1.0健康危害:二硫化碳是伤害神经和血管的毒物。
急性中毒:轻度中毒有头晕、头痛、眼及鼻粘膜刺激症状;中度中毒尚有酒醉表现;重度中毒可呈短期的兴奋状态,继之浮现谵妄、昏迷、意识丧失,伴有强直性及阵挛性抽搐。
可因呼吸中枢麻痹而死亡。
严重中毒后可遗留神衰综合征,中枢和周围神经永久性伤害。
慢性中毒:表现有神经衰弱综合征,植物神经功能紊乱,多发性周围神经病,中毒性脑病。
眼底检查:视网膜微动脉瘤,动脉硬化,视神经萎缩。
危(wei)险特性:极易燃,其蒸气能与空气形成范围广阔的爆炸性混合物。
接触热、火星、火焰或者氧化剂易燃烧爆炸。
受热分解产生有毒的硫化物烟气。
与铝、锌、钾、氟、氯、叠氮化物等反应剧烈,有燃烧爆炸危(wei)险。
高速冲击、流动、激荡后可因产生静电火花放电引起燃烧爆炸。
其蒸气比空气重,能在较低处扩散到相当远的地方,遇火源会着火回燃。
燃爆危(wei)险:该品极度易燃,具刺激性。
皮肤接触:即将脱去污染的衣着,用大量流动清水冲洗至少 15 分钟,就医。
耐硫变换催化剂的硫化反应方程式

耐硫变换催化剂的硫化反应方程式
1变换催化剂的硫化反应
变换催化剂的硫化反应是一种化学反应,它通过硫来生成一种光和热敏感的产物。
这种反应常用来生产烃、醛、醚和酮等物质,例如用于制造医药和分子生物学工作的新物质。
变换催化剂的硫化反应可用以下方程式表示:
R-X + 2S → R-S-S-X
其中,R代表烃基,X代表定位基,S代表硫。
变换催化剂的硫化反应可以分为三个阶段:催化剂反应,催化剂形成,催化剂催化的产物形成。
在催化剂反应阶段,一部分被硫化的变换催化剂与原料烃发生反应,一部分变换催化剂不参与反应。
在催化剂形成阶段,未参与反应的变换催化剂与原料烃再次反应,形成活性变换催化剂。
最后,在催化剂催化的产物形成阶段,活性变换催化剂与硫反应,生成所需要的产物。
变换催化剂的硫化反应需要高温高压,除金属表面上的氧以外,反应中还有其他杂质,如不共存的轻烃物质。
所以,需要用精确的操作方法来防止反应副反应,确保硫化反应的高选择性。
总之,变换催化剂的硫化反应是一种反应,可以用来生产烃、醛、醚和酮等物质,是一种技术性的反应,需要用精确的操作方法才能得
到期望的产物。
Co - Mo 系耐硫变换催化剂的硫化处理

Co - Mo系耐硫变换催化剂的硫化处理1、硫化反应耐硫变换催化剂在使用前一般要将其活性组份的氧化态转化为硫化态,这一转化过程称之为硫化。
钴钼系耐硫催化剂的硫化反应在热力学上可用下列式子表示:CS2 + 4H2 = 2H2S + CH4 + 230. 45 kJMoO3 + H2 + 2H2S = MoS2 + 3H2O +48. 15 kJCoO + H2S = CoS + H2O + 13. 4 kJCO + 3H2 = CH4 + H2O + 214. 8 kJCO+H2O = CO2+H2 +41.19 KJ/mol2H2 +O2 =2 H2O + 241. 83 kJ上述反应均为放热反应。
常用的硫化剂有CS2和H2S两种。
其中H2S来自高硫煤气或固体硫化剂, CS2可直接加入原料气。
另外,硫氧化碳等有机硫也可作硫化剂。
2、硫化反应机理在催化剂的硫化过程中,不论采用何种硫化方法,最基本的硫化剂就是H2S。
因此只要在硫化条件下容易提供H2S的物质都可用作硫化剂。
工业上通常采用低分子量的有机硫化合物和无机的固体硫化剂。
硫化过程通常分为两个反应步骤,即硫化剂的分解和催化剂活性组分的相态转化。
(1)硫化剂的分解硫化剂的分解是指硫化剂在催化剂正常的硫化工艺条件下,硫化剂与氢气或水发生化学反应生成H2S的过程,下面是常见的几种硫化剂及其分解反应。
CS2(二硫化碳)十4H2=CH4十2H2SCOS(硫氧碳)十H2O=CO2十H2S(2)硫化对耐硫变换催化剂的作用:使催化剂中的金属组分即活性组分由氧化态变成硫化态,如MoO3变成活性物种MoS2;使催化剂中的活性组分处于最佳活性价态,以Mo为例,Mo由MoO3中Mo6+经过硫化变为活性物种MoS2。
MoO3和CoO在催化剂硫化过程中发生的化学变化表示如下:(3)硫化剂的选择从硫化剂的分解反应上看,其最终产物为H2S,理论上认为除本身的分解反应外,不会对催化剂的硫化过程造成影响。
为什么加氢催化剂使用前必须进行预硫化
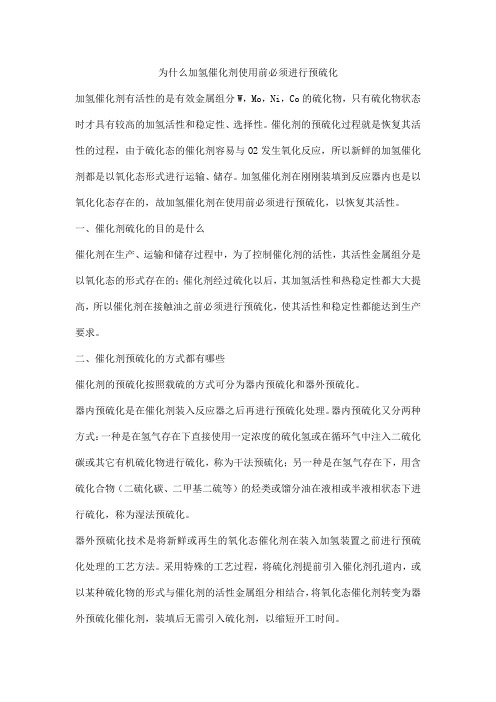
为什么加氢催化剂使用前必须进行预硫化加氢催化剂有活性的是有效金属组分W,Mo,Ni,Co的硫化物,只有硫化物状态时才具有较高的加氢活性和稳定性、选择性。
催化剂的预硫化过程就是恢复其活性的过程,由于硫化态的催化剂容易与O2发生氧化反应,所以新鲜的加氢催化剂都是以氧化态形式进行运输、储存。
加氢催化剂在刚刚装填到反应器内也是以氧化化态存在的,故加氢催化剂在使用前必须进行预硫化,以恢复其活性。
一、催化剂硫化的目的是什么催化剂在生产、运输和储存过程中,为了控制催化剂的活性,其活性金属组分是以氧化态的形式存在的;催化剂经过硫化以后,其加氢活性和热稳定性都大大提高,所以催化剂在接触油之前必须进行预硫化,使其活性和稳定性都能达到生产要求。
二、催化剂预硫化的方式都有哪些催化剂的预硫化按照载硫的方式可分为器内预硫化和器外预硫化。
器内预硫化是在催化剂装入反应器之后再进行预硫化处理。
器内预硫化又分两种方式:一种是在氢气存在下直接使用一定浓度的硫化氢或在循环气中注入二硫化碳或其它有机硫化物进行硫化,称为干法预硫化;另一种是在氢气存在下,用含硫化合物(二硫化碳、二甲基二硫等)的烃类或馏分油在液相或半液相状态下进行硫化,称为湿法预硫化。
器外预硫化技术是将新鲜或再生的氧化态催化剂在装入加氢装置之前进行预硫化处理的工艺方法。
采用特殊的工艺过程,将硫化剂提前引入催化剂孔道内,或以某种硫化物的形式与催化剂的活性金属组分相结合,将氧化态催化剂转变为器外预硫化催化剂,装填后无需引入硫化剂,以缩短开工时间。
三、常用的硫化剂都有哪些硫化剂的作用是在硫化过程中提供H2S与金属氧化物反应,为此,硫化剂的选用原则是在硫化过程中能在较低温度下分解为H2S,保证催化剂硫化的顺利进行,提高硫化效果。
经综合考虑使用效果、价格、分解温度、安全环保等因素,器内预硫化剂主要包括二硫化碳(CS2)、二甲基二硫化物(DMDS)、正丁硫醇(NBM)、二甲基硫化物(DMS)、甲硫醚等,目前,工业上普遍采用的硫化剂是CS2和DMDS。
催化剂预硫化

黑龙江安瑞佳石油化工学习资料〔催化剂预硫化方法〕气分车间2013年4月催化剂的预硫化催化剂的预硫化有两种方法:一是干法预硫化,亦称气相预硫化,即在循环氢或氢氮混合气或氢气与丙烷或氢气与丁烷混合气存在下注入硫化剂进行硫化;二是湿法预硫化,亦称液相预硫化,即在循环氢存在下以轻油等为硫化油携带硫化剂注入反应系统进行硫化。
催化剂硫化的基本原理催化剂硫化是基于硫化剂〔CS2或二甲基二硫DMDS〕临氢分解生成的H2S,将催化剂活性金属氧化态转化为相应的硫化态的反应。
干法硫化反应:用氢气作载体,硫化氢为硫化剂。
MoO3 + 2H2S + H2MoS2 + 3H2O9CoO + 8H2S + H2Co9S8 + 9H2O3NiO + 2H2S + H2Ni3S2 + 3H2O湿法硫化反应:用氢气作载体,CS2为硫化剂。
CS2 + 4H22H2S + CH4MoO3 + CS2 + 5H2MoS2 + 3H2O + CH4MoO3 + CS2 + 3H2 MoS2 + 3H2O + C9CoO + 4CS2 + 17H2Co9S8 + 9H2O + CH49CoO + 4CS2 + 9H2Co9S8 + 9H2O + 4C3NiO + 2CS2 + 5H2Ni3S2 + 3H2O + CH4基于上述硫化反应式和加氢催化剂的装量及相关金属含量可估算出催化剂硫化剂的理论需要量。
其硫化剂的备用量〔采购量〕一般按催化剂硫化理论需硫量的倍考虑即可。
硫化剂和硫化油的选择实际上催化剂硫化时是H2S在起作用,所以所选用的硫化剂在临氢和催化剂存在的条件下,能在较低反应温度下分解生成H2S,以有利于催化剂硫化的顺利进行,提高硫化效果,同时硫化剂中的硫含量应较高,以减少硫化剂的用量,防止其它元素对硫化过程的不利影响,另外硫化剂价格廉价、毒性小、使用安全。
常用硫化剂的理化性质见表4。
表4 常用硫化剂的理化性质催化剂湿法硫化时需要硫化油,硫化油一般采用含链烷烃的直馏煤油或轻柴油,其指标见表5。
催化剂硫化反应方程式

催化剂硫化反应方程式在化学领域中,硫化反应是一个复杂而又重要的过程,它关乎着许多产品的制造与材料的形成。
而在这一过程中,催化剂扮演着不可或缺的角色。
那么,硫化反应的方程式是什么?催化剂又是如何发挥其作用的呢?让我们一起走进这一神奇的化学世界。
硫化反应方程式通常可以表示为:$$R-SH+X-S-Y\rightarrow R-S-X+Y-S-H$$其中,$R-SH$代表硫醇,$X-S-Y$则是二硫化物或二芳基。
这个反应的关键在于将有机分子中的硫-硫键转化为更稳定的碳-硫键。
而催化剂的作用就在于降低这个反应的活化能,使得反应更容易进行。
催化剂在硫化反应中的具体作用机制相当复杂,涉及到电子转移、键的断裂与形成等多个方面。
简单来说,催化剂能够"锁定"硫醇和二硫化物中的特定化学键,从而促使它们更有效地结合,形成新的碳-硫键。
这一过程不仅提高了反应速率,还优化了产物的结构与性能。
值得一提的是,催化剂的选择对硫化反应的影响至关重要。
不同的催化剂会对反应速率、产物纯度以及副产物的生成产生显著影响。
因此,在工业生产中,科研人员需经过反复试验与优化,找到最适合特定硫化反应的催化剂。
除了基本的硫化反应外,科学家们还致力于研发新型的催化体系,以适应各种复杂的硫化过程和特殊的产物需求。
这些研究不仅有助于提高生产效率和产品质量,还有助于推动硫化学和催化科学的发展。
在深入理解硫化反应和催化剂作用的基础上,我们可以更好地应对现实中的挑战和问题。
例如,通过优化催化剂和反应条件,可以降低生产成本、减少环境污染;通过研发新型催化体系,可以满足特殊材料和产品的需求;通过深入探索硫化反应的机理,可以为相关领域的研究提供新的思路和方法。
总的来说,硫化反应方程式揭示了催化剂在化学世界中的神奇作用。
通过研究催化剂如何影响硫化反应,我们不仅可以优化生产过程、提高产品质量,还可以推动相关学科的发展。
未来,随着科学技术的不断进步,我们期待在硫化反应和催化剂研究方面取得更多突破性的成果。
催化剂预硫化过程中的注意事项是什么
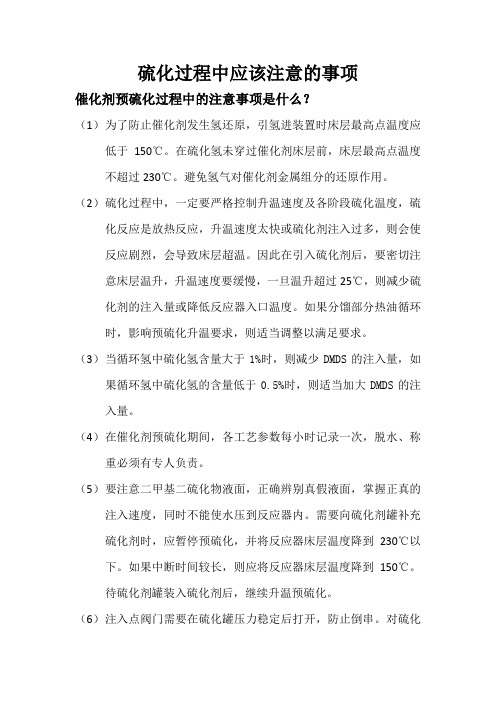
硫化过程中应该注意的事项催化剂预硫化过程中的注意事项是什么?(1)为了防止催化剂发生氢还原,引氢进装置时床层最高点温度应低于150℃。
在硫化氢未穿过催化剂床层前,床层最高点温度不超过230℃。
避免氢气对催化剂金属组分的还原作用。
(2)硫化过程中,一定要严格控制升温速度及各阶段硫化温度,硫化反应是放热反应,升温速度太快或硫化剂注入过多,则会使反应剧烈,会导致床层超温。
因此在引入硫化剂后,要密切注意床层温升,升温速度要缓慢,一旦温升超过25℃,则减少硫化剂的注入量或降低反应器入口温度。
如果分馏部分热油循环时,影响预硫化升温要求,则适当调整以满足要求。
(3)当循环氢中硫化氢含量大于1%时,则减少DMDS的注入量,如果循环氢中硫化氢的含量低于0.5%时,则适当加大DMDS的注入量。
(4)在催化剂预硫化期间,各工艺参数每小时记录一次,脱水、称重必须有专人负责。
(5)要注意二甲基二硫化物液面,正确辨别真假液面,掌握正真的注入速度,同时不能使水压到反应器内。
需要向硫化剂罐补充硫化剂时,应暂停预硫化,并将反应器床层温度降到230℃以下。
如果中断时间较长,则应将反应器床层温度降到150℃。
待硫化剂罐装入硫化剂后,继续升温预硫化。
(6)注入点阀门需要在硫化罐压力稳定后打开,防止倒串。
对硫化管线要在投用前用氮气吹扫干净。
冷高分脱水过程特别注意硫化氢中毒的预防措施,水包中的水不要一次性排完。
预硫化的终止的标志是什么?(1)反应器出入口气体露点差在3℃以内。
(2)反应器出入口气体的硫化氢浓度相同。
(3)高分无水生成。
(4)床层没有温升。
为什么新催化剂升温至150℃以前,要严格控制10-15℃/h 的温升速度?在催化剂床层从常温开始升温时,分两个阶段,常温至150℃和150-250℃。
新催化剂温度小于150℃时属于从催化剂微孔向外脱水阶段,在此阶段升温速度太快,水汽化量大,易破坏催化剂微孔,严重时导致催化剂破损,造成床层压降过大,缩短开工周期。
催化剂硫化剂
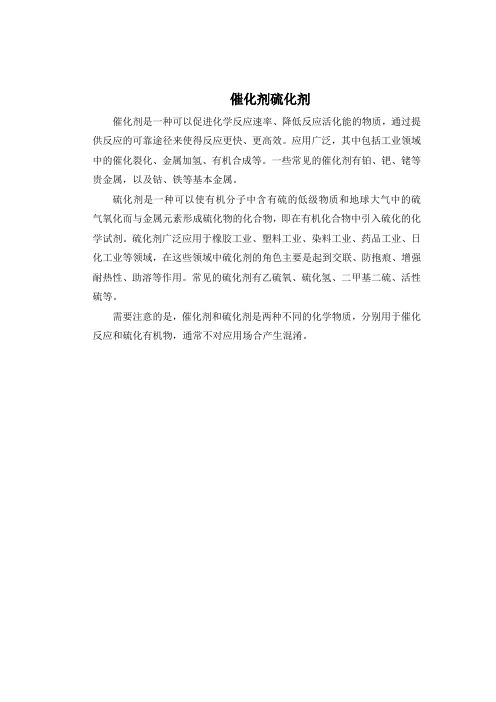
催化剂硫化剂
催化剂是一种可以促进化学反应速率、降低反应活化能的物质,通过提供反应的可靠途径来使得反应更快、更高效。
应用广泛,其中包括工业领域中的催化裂化、金属加氢、有机合成等。
一些常见的催化剂有铂、钯、铑等贵金属,以及钴、铁等基本金属。
硫化剂是一种可以使有机分子中含有硫的低级物质和地球大气中的硫气氧化而与金属元素形成硫化物的化合物,即在有机化合物中引入硫化的化学试剂。
硫化剂广泛应用于橡胶工业、塑料工业、染料工业、药品工业、日化工业等领域,在这些领域中硫化剂的角色主要是起到交联、防抱痕、增强耐热性、助溶等作用。
常见的硫化剂有乙硫氧、硫化氢、二甲基二硫、活性硫等。
需要注意的是,催化剂和硫化剂是两种不同的化学物质,分别用于催化反应和硫化有机物,通常不对应用场合产生混淆。
关于催化剂的预硫化

关于催化剂的预硫化1.苯加氢装置所用催化剂为两种:预反应催化剂(M8-21,NiMo 4.90吨;NiO:4%, MoO3:14%)和主反应催化剂(M8-12,CoMo 11.9吨; CoO:3.3%, MoO3:14%),预计催化剂运转周期为3年,总寿命约为6年。
2.催化剂的作用●在预反应器内进行如下反应:⑴炔烃等不饱和物的加成转化反应:CnH2n-2+H2NiMo CnH2nC6H5C2H3+H2NiMo C6H5C2H5⑵含硫化合物的加氢脱硫反应:CS2+4H2NiMo CH4+2H2S●在主反应器进行如下反应:⑴烯烃的加成反应C n H2n+H2CoMo C n H2N+2⑵加氢脱硫反应C4H4S(噻吩)+4H2CoMo C4H10+H2S⑶加氢脱氮反应C6H7N+H2CoMo C6H14+NH3⑷加氢脱氧反应C6H6O+H2CoMo C6H6+H2O⑸副反应、芳香烃氢化反应C6H6+3H2CoMo C6H123.催化剂预硫化的目的本装置所用原始催化剂的主要成分为金属钴、镍、钼的氧化物,对粗苯中杂质的加氢并不具备催化作用,需将其变为硫化态,方具有活性。
4.催化剂硫化的反应机理催化剂硫化所用硫化剂为DMDS(二甲基二硫),其在标准条件下为液体,恶臭,剧毒。
在催化剂硫化条件下,其被气化,并与氢气反应:CH3-S-S-CH3+ 3H2= 2 H2S + 2CH4反应生成的硫化氢再与金属钴、镍、钼的氧化物进行反应:H2S + CoO =Co S + H2OH2S + NiO =NiS + H2O2H2S + H2 + MoO3=MoS2 + 3H2O5.催化剂预硫化的过程⑴加氢系统的冷循环和升温加氢系统气密试验合格后,通过点燃H6101提高R6102的温度,通过循环,提到整个加氢系统的温度并应达到以下条件:V-6103 PIC-6171 2.4MPaR6101 TI-6151 159℃TI-6153 149℃H6101 TI-6161 145℃TI-6162A 244℃PICA-6167 开度16%R6102 TICA-6164 242℃TI-6167A 235℃E6104A TI-6145 65℃E TI-6144 63℃⑵B.T(总硫<1.0ppm)加入以上条件以达到主反应器预硫化的条件,但预反的温度比较低,不利于所需加入的DMDS的气化,为此必须提高与反应器的温度。
变换催化剂硫化的原理

变换催化剂硫化的原理嘿,你知道变换催化剂硫化是咋回事不?这可是个超级神奇的过程呢!变换催化剂,那家伙,就像是化学反应中的超级英雄。
而硫化呢,就像是给这位超级英雄赋予特殊能力的神秘仪式。
咱先说说变换催化剂是干啥的。
它就像是一个神奇的魔法师,能把一种物质变成另一种物质。
在工业生产中,它的作用可大了去了。
它能让那些原本没啥用的气体,变成有用的宝贝。
比如说,能把一氧化碳变成二氧化碳,这可不是一般的厉害吧!那硫化又是咋回事呢?硫化就像是给这个魔法师穿上了一件魔法铠甲。
这件铠甲可不是随便就能穿上的,得有一套特殊的方法。
硫化的过程,就像是一场精心策划的魔法表演。
首先,得把催化剂准备好,就像魔法师要准备好自己的魔杖一样。
然后,把含有硫的物质加进去,这就像是给魔杖注入魔法力量。
接着,在一定的温度和压力下,让它们发生反应。
这个反应可不像普通的化学反应那么简单哦!它就像是一场神秘的魔法仪式,充满了各种奇妙的变化。
你想想看,这就好比是在打造一把绝世宝剑。
先要选好材料,然后经过高温煅烧、淬火等一系列复杂的工序,才能打造出一把锋利无比的宝剑。
变换催化剂硫化也是一样,要经过一系列精心设计的步骤,才能让催化剂发挥出最大的作用。
在硫化的过程中,催化剂的表面会发生很多变化。
那些原本平平无奇的表面,会变得充满活力,就像被施了魔法一样。
硫会和催化剂中的金属元素结合,形成一种特殊的化合物。
这种化合物就像是魔法铠甲上的符文,赋予了催化剂强大的力量。
硫化后的催化剂,就像是脱胎换骨了一样。
它的性能会大大提高,能够更好地完成自己的使命。
它可以在更恶劣的环境下工作,也可以更高效地进行化学反应。
你说,这变换催化剂硫化是不是很神奇呢?它就像是一个隐藏在工业生产背后的魔法,默默地为我们的生活带来便利。
没有它,我们的生活可就没那么精彩了。
所以说,变换催化剂硫化是一个非常重要的过程。
它让那些看似普通的催化剂变得与众不同,为工业生产带来了巨大的贡献。
我们应该好好研究这个过程,让它发挥出更大的作用。
方案十三(催化剂硫化方案)
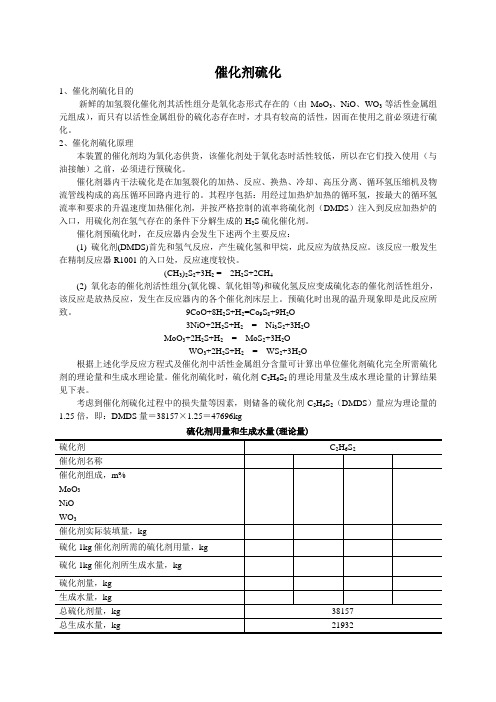
催化剂硫化1、催化剂硫化目的新鲜的加氢裂化催化剂其活性组分是氧化态形式存在的(由MoO3、NiO、WO3等活性金属组元组成),而只有以活性金属组份的硫化态存在时,才具有较高的活性,因而在使用之前必须进行硫化。
2、催化剂硫化原理本装置的催化剂均为氧化态供货,该催化剂处于氧化态时活性较低,所以在它们投入使用(与油接触)之前,必须进行预硫化。
催化剂器内干法硫化是在加氢裂化的加热、反应、换热、冷却、高压分离、循环氢压缩机及物流管线构成的高压循环回路内进行的。
其程序包括:用经过加热炉加热的循环氢,按最大的循环氢流率和要求的升温速度加热催化剂,并按严格控制的流率将硫化剂(DMDS)注入到反应加热炉的入口,用硫化剂在氢气存在的条件下分解生成的H2S硫化催化剂。
催化剂预硫化时,在反应器内会发生下述两个主要反应:(1) 硫化剂(DMDS)首先和氢气反应,产生硫化氢和甲烷,此反应为放热反应。
该反应一般发生在精制反应器R1001的入口处,反应速度较快。
(CH3)2S2+3H2 = 2H2S+2CH4(2) 氧化态的催化剂活性组分(氧化镍、氧化钼等)和硫化氢反应变成硫化态的催化剂活性组分,该反应是放热反应,发生在反应器内的各个催化剂床层上。
预硫化时出现的温升现象即是此反应所致。
9CoO+8H2S+H2=Co9S8+9H2O3NiO+2H2S+H2 = Ni3S2+3H2OMoO3+2H2S+H2= MoS2+3H2OWO3+2H2S+H2= WS2+3H2O根据上述化学反应方程式及催化剂中活性金属组分含量可计算出单位催化剂硫化完全所需硫化剂的理论量和生成水理论量。
催化剂硫化时,硫化剂C2H6S2的理论用量及生成水理论量的计算结果见下表。
考虑到催化剂硫化过程中的损失量等因素,则储备的硫化剂C2H6S2(DMDS)量应为理论量的1.25倍,即:DMDS量=38157×1.25=47696kg硫化剂用量和生成水量(理论量)硫化过程中还可能有不希望发生的副反应:氧化态的催化剂活性组分(氧化镍、氧化钼、氧化钨)被氢气还原,生成金属单质和水,这会极大损害催化剂的活性。
催化剂预硫化生成的水
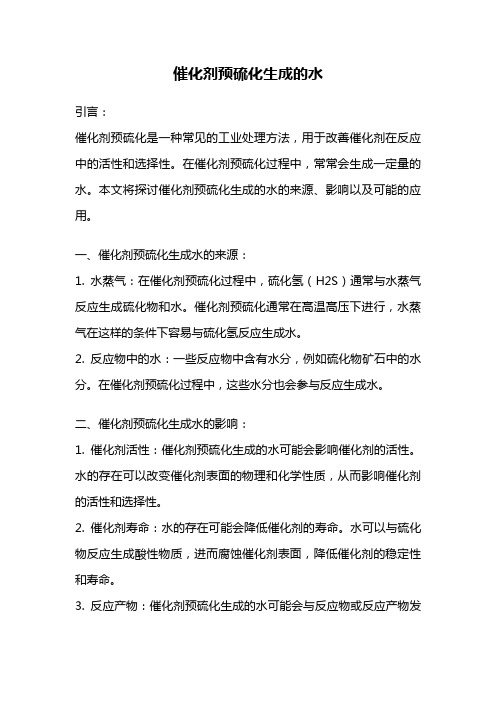
催化剂预硫化生成的水引言:催化剂预硫化是一种常见的工业处理方法,用于改善催化剂在反应中的活性和选择性。
在催化剂预硫化过程中,常常会生成一定量的水。
本文将探讨催化剂预硫化生成的水的来源、影响以及可能的应用。
一、催化剂预硫化生成水的来源:1. 水蒸气:在催化剂预硫化过程中,硫化氢(H2S)通常与水蒸气反应生成硫化物和水。
催化剂预硫化通常在高温高压下进行,水蒸气在这样的条件下容易与硫化氢反应生成水。
2. 反应物中的水:一些反应物中含有水分,例如硫化物矿石中的水分。
在催化剂预硫化过程中,这些水分也会参与反应生成水。
二、催化剂预硫化生成水的影响:1. 催化剂活性:催化剂预硫化生成的水可能会影响催化剂的活性。
水的存在可以改变催化剂表面的物理和化学性质,从而影响催化剂的活性和选择性。
2. 催化剂寿命:水的存在可能会降低催化剂的寿命。
水可以与硫化物反应生成酸性物质,进而腐蚀催化剂表面,降低催化剂的稳定性和寿命。
3. 反应产物:催化剂预硫化生成的水可能会与反应物或反应产物发生反应,改变反应的产物分布和产率。
三、催化剂预硫化生成水的应用:1. 催化剂再生:在催化剂使用一段时间后,可以通过再生来恢复其活性。
水可以作为再生过程中的溶剂,帮助去除催化剂表面的污染物,从而提高催化剂的再生效果。
2. 活性组分制备:催化剂预硫化生成的水可以用于制备活性组分。
水中的氧气可以与硫化物反应生成氧化物,并作为活性组分的前体物质。
结论:催化剂预硫化生成的水主要来源于水蒸气和反应物中的水分。
这些水可能会影响催化剂的活性、寿命和反应产物。
然而,催化剂预硫化生成的水也可以被应用于催化剂再生和活性组分制备等领域。
因此,在催化剂预硫化过程中,对生成的水进行合理的利用和处理,可以提高催化剂的性能和效果。
催化剂硫化温度

催化剂硫化温度催化剂硫化温度是指在催化反应中,催化剂对硫化反应的温度敏感性。
催化剂硫化温度的研究对于提高催化剂的活性和选择性,优化反应条件,改善催化剂的使用寿命具有重要意义。
本文将就催化剂硫化温度的相关概念、影响因素、研究方法以及应用前景进行综述,以期为相关领域的研究和应用提供参考。
一、概念及意义催化剂硫化温度是指在硫化反应过程中,催化剂表面吸附的硫化物的形成温度。
硫化反应是一种重要的离子反应,它通常发生在高温下。
硫化温度的高低直接影响着硫化反应的进行速率、催化剂的活性和选择性,因此硫化温度是催化剂研究中十分重要的参数。
通过调节催化剂的硫化温度,可以提高催化反应的效率,改善反应条件,从而提高催化剂的使用寿命。
硫化反应是工业上广泛应用的一种反应,它在石油化工、化肥、有机合成等领域均有重要的应用。
研究催化剂硫化温度对于优化工业生产过程具有重要意义。
通过降低硫化温度,可以减少反应能耗,提高反应速率,降低催化剂的失活速率,降低生产成本。
因此,研究催化剂硫化温度对于工业生产具有重要的应用前景。
二、影响因素催化剂硫化温度的大小受到多种因素的影响。
主要包括催化剂的成分、结构、表面性质,硫化剂的性质,反应条件等。
以下将对这些因素进行详细介绍。
1.催化剂的成分催化剂的成分对硫化温度有着重要的影响。
在硫化反应中,催化剂通常是含有过渡金属的氧化物或硫化物。
过渡金属的种类、含量、结构对催化剂的硫化温度有着重要的影响。
一般来说,过渡金属的氧化态越高,硫化温度越低。
例如,对于镍催化剂来说,氧化态越高,硫化温度越低。
此外,催化剂的晶体结构、粒径、导电性等也会对硫化温度产生影响。
因此,在设计催化剂时,需要考虑催化剂成分对硫化温度的影响。
2.催化剂的表面性质催化剂的表面性质对硫化温度有着重要的影响。
表面活性位点的形成、分布、性质对硫化温度起着决定性的作用。
一般来说,表面活性位点的形成能力越强,硫化温度越低。
此外,催化剂的表面结构、形貌、晶面、形态等也会对硫化温度产生影响。
钒催化剂硫化饱和说明

钒催化剂硫化饱和说明
钒催化剂硫化饱和描述的是一种催化反应过程。
在硫化饱和反应中,钒催化剂充当催化剂,加速硫化反应的进行。
催化剂是一种可以改变反应速率但本身不参与反应的物质。
在钒催化剂的存在下,硫化饱和反应可以更快地发生。
硫化饱和指的是将硫原子(S)添加到有机化合物的双键或三键上,使其形成硫化物键,从而饱和化合物的不饱和度。
钒催化剂在硫化饱和中发挥的作用可能是通过多种机制实现的。
一种可能的机制是钒催化剂与硫化物反应形成活性中间体,然后该中间体与有机化合物发生反应。
这种反应可以发生在低温下,并且具有高选择性和高效率。
钒催化剂硫化饱和的应用范围广泛,包括石油化工、有机合成和环境保护等领域。
它可以用于饱和烃类化合物、脂肪酸、多烯烃和其他不饱和有机化合物的转化。
通过硫化饱和反应,可以改善化合物的稳定性、降低毒性或改善化学性质。
钒催化剂在硫化饱和中发挥重要作用,加速反应速率,使有机化合物发生硫化反应,转化为相应的硫化物,以实现饱和化合物的形成。
催化剂硫化的作用

催化剂硫化的作用
催化剂硫化的作用是在化学反应中加速速率,提高反应的选择性和效率。
催化剂硫化通常通过在催化剂表面形成硫化物来实现。
以下是催化剂硫化的一些常见作用:
1. 去除有毒物质:催化剂硫化可以将一些有毒物质转化为无毒或低毒的形式。
例如,硫化镍可以将有毒的有机硫化物转化为无毒的硫化物。
2. 催化氧化还原反应:催化剂硫化可以在氧化还原反应中加速电子转移过程,从而增加反应速率。
例如,硫化铁在醇的氧化反应中起到了催化剂的作用。
3. 选择性催化:催化剂硫化可以调控化学反应中的选择性,使反应产生特定的产物。
例如,硫化钴在氧化还原反应中可以选择性地催化底物的氧化或还原。
4. 提高反应效率:催化剂硫化可以降低活化能,使反应在较低的温度和压力下进行,从而提高反应的效率。
例如,硫化铂可以催化汽车尾气中的氮氧化物的转化,使其在较低温度下发生。
总而言之,催化剂硫化可以改变化学反应的速率、选择性和效率,从而在很多工业和实验室应用中起到重要作用。
催化剂硫化的作用

催化剂硫化的作用
催化剂硫化是一种常见的催化剂制备方法,其主要作用是通过硫化反应将催化剂中的金属组分与硫元素结合,形成具有一定稳定性和活性的硫化物催化剂。
在催化剂硫化过程中,金属组分与硫元素之间发生化学反应,形成金属硫化物催化剂。
这种催化剂具有以下优点:
1. 提高催化剂的稳定性:金属硫化物催化剂具有较高的稳定性,不易被氧化、还原等反应破坏,能够在高温、高压等恶劣条件下保持较高的催化活性。
2. 提高催化剂的活性:金属硫化物催化剂具有较好的电子结构和表面性质,能够提高催化剂的活性,使其在催化反应中具有更好的催化性能。
3. 降低催化剂成本:相比于贵金属催化剂,金属硫化物催化剂的制备成本较低,能够降低催化剂的生产成本,提高催化剂的经济效益。
总之,催化剂硫化是一种常用的催化剂制备方法,通过将催化剂中的金属组分与硫元素结合,可以制备出具有较高稳定性和活性的硫化物催化剂,具有广泛的应用前景。
- 1、下载文档前请自行甄别文档内容的完整性,平台不提供额外的编辑、内容补充、找答案等附加服务。
- 2、"仅部分预览"的文档,不可在线预览部分如存在完整性等问题,可反馈申请退款(可完整预览的文档不适用该条件!)。
- 3、如文档侵犯您的权益,请联系客服反馈,我们会尽快为您处理(人工客服工作时间:9:00-18:30)。
催化剂硫化1.催化剂硫化的目的和原理1.1硫化目的:在一定的温度和硫化氢分压下,把催化剂的活性组分(氧化镍、氧化钼等)由活性低的氧化态变成活性稳定的硫化态,提高催化剂活性和稳定性,延长催化剂寿命。
虽然加氢催化剂在使用氧化态形式开工后,也会因较弱的加氢活性促使一部分原料中的硫化物发生加氢脱硫反应,生成硫化氢,继而使催化剂金属组分从氧化态转化为硫化态,但这种转化是在催化剂长时间与高温氢气接触、并且有大量结焦的情况下进行,催化剂的活性金属组分在转化为硫化态之前,有一部分可能被氢还原,这种氢还原或已经沉积有炭的金属组分很难再被硫化,从而使催化剂处于低的加氢活性,并带来短的寿命。
因此,加氢催化剂在接触原料油之前,必须先将催化剂活性金属组分的氧化态用硫化剂将其转化为硫化态,即进行催化剂预硫化。
本装置催化剂硫化方式采用湿法硫化。
1.2 预硫化原理:预硫化时,硫化反应极其复杂。
在反应器内会发生两个主要反应:(1)硫化剂(DMDS)和氢气反应,产生硫化氢和甲烷,反应会放出热量。
预硫化时该反应一般在反应器入口发生,反应速度较快。
反应方程式:CS2+4H2→CH4+2H2S(2)氧化态的催化剂活性组分(氧化镍、氧化钼等)和硫化氢反应变成硫化态的催化剂活性组分,反应会放出热量。
预硫化时该反应发生在各个床层。
反应方程式:M O O3+2H2S+H2→M O S2+3H2O3N i O3+2H2S+H2→NiS2+3H2O(3)副反应:在有氢气存在、无硫化氢的条件下,氧化态的催化剂活性组分(氧化镍、氧化钼等)被氢气还原,生成金属镍、钼和水,导致催化剂活性损失。
温度越高(大于230℃),反应越严重;在循环气中的硫化氢含量过高时,会生成金属的多硫化物,降低了催化剂活性,易造成产品腐蚀不合格。
2. 催化剂硫化应具备的条件(1)反应系统催化剂干燥、高压气密结束,紧急泄压和急冷氢试验问题整改完。
(2)分馏系统热油运运转正常,具备接收生成油条件。
(3)高压注水等其他系统试运正常。
(4)新氢系统具备正常供氢条件。
(5)注硫系统试运正常,DMDS装罐。
(6)通知化验及其他相关单位,做好催化剂预硫化的配合工作。
(7)仪表、DCS及SIS联锁系统调试合格,工艺联锁已全部投用。
(8)预硫化所需化工原材料和有关物品准备齐全,其中硫化剂:DMDS77t,硫化油:直馏柴油(氮含量<100 g/g、干点<350℃、含水量<0.01%)2000t(8)所有操作人员经过硫化培训,气防安全考试合格上岗,包括硫化氢的防毒防护知识,正压式呼吸器及各类放毒面罩的正确佩戴。
(9)预硫化前工艺具备条件:反应系统压力维持15.4MPa,反应器入口温度175℃恒温。
严格控制反应加热炉和各床层温度,保证反应器床层任意一点温度不大于180℃,防止催化剂被氢气还原。
反应系统循环氢压缩机全量循环,循环氢纯度大于85%。
(10)按附表准备好化工原材料和有关物品。
预硫化期间所需化工原材料和物品表3. 催化剂硫化注意事项(1)为防止催化剂发生氢还原,引氢进装置前反应器床层最高温度应低于175℃。
避免高温氢气对催化剂金属组份的还原。
(2)硫化过程中,应严格控制加热炉出口温度,避免温度大幅波动;(3)在200℃前,DMDS的注入速度不宜过快,以免累积在反应器床层中发生集中分解放热;(4)200℃以前,应严格控制升温速率不大于给定值;(5)为避免高温氢气对催化剂金属组份的还原作用,循环氢中H2S含量未被检出或浓度小于0.3%时,反应器内床层温度不得超过230℃。
(6)硫化期间,正常情况下不用冷氢,但冷氢阀必须处于随时可用状态。
硫化过程中应严密观察反应器各床层温度的变化。
若单个催化剂床层温升达到10℃,立即投用冷氢控制床层温度,并停止升温;若单个催化剂床层温升达到20℃以上,且呈快速上升趋势,则停炉熄火,并立即启动紧急放空系统(0.7MPa/min)。
(7)硫化期间如发生故障而中止了硫化,重新开始时必须恢复到中止前的状态进行。
(8)硫化过程中必须作好分析、检测、计量结果的记录。
认真记录好DMDS实际注入量、高分水生成量。
在预硫化期间,各工艺参数每小时记录一次,脱水、计量必须有专人负责。
(9)在整个硫化过程及升温过程中,要保证反应系统循环氢纯度大于85%,硫化氢的浓度不大于2%,不低于0.1%(V)。
若硫化氢过高,可通过减少DMDS的注入量来调节;若氢纯度低于85%,通废氢排放和补充新氢来维持。
记录排放循环氢量和补入新氢量。
(10)在催化剂预硫化阶段,维持高分压力在15.4MPa。
为了避免大量硫化氢从高分尾气中跑损,在循环气氢纯度大于85%的情况下,不排放高分废氢。
预硫化过程中大部分时间系统又处在升温过程中,在不耗氢的情况下系统压力会升高,而催化剂预硫化所耗氢气量较少,因此预硫化期间的耗氢量远低于正常生产期间的耗氢量,新氢的补充量较小。
因此,在高分不排废氢的情况下,要调整好补充氢压缩机向系统的注入量。
(11)预硫化期间循环氢中的硫化氢浓度较高,硫化生成水中含有大量的硫化氢,在高分切水时,水中溶解的硫化氢因减压而逸出。
硫化氢对人体有较大的危害,在空气中的卫生允许浓度仅为0.010毫克/升。
因此,硫化期间巡检、切水必须两人以上,要戴好防毒面具,携带H2S监测仪。
特别是高分切水人员,一人操作,一人监护,严防硫化氢中毒。
(12)催化剂预硫化的好坏直接影响到催化剂的活性和稳定性,而严格升温程序、控制DMDS的注入量、保持注硫泵的平稳运转是催化剂预硫化操作的关键。
因此应临时设置注硫岗位,做到每半小时一次检查、调整和记录注硫量。
(13)催化剂预硫化结束后,尽快统计预硫化操作过程中的各种工艺参数,特别是注硫量、出水量、循环氢中硫化氢浓度、水中硫浓度、新氢补充量、尾气排放量等数据,通过对数据的分析,判断催化剂的预硫化效果是否符合工艺要求。
关于催化剂的上硫情况,参照预硫化硫平衡表格进行核算。
4.催化剂硫化步骤4.1反应系统进油润湿,建立反应-分馏系统循环4.1.1反应系统进油前工艺条件确认(M)-确认冷高分压力控制15.4MPa(M)-确认反应器入口温度175℃(M)-反应系统氢气循环,循环氢纯度大于85%(M)-确认循环氢压缩机运转正常,循环氢流量240000Nm3/h(M)-确认低氮油主要指标符合要求(M)-分馏热油循环正常4.1.2原料系统收低氮油[P]-改通原料系统引油流程,投用相应液位控制阀、界位控制阀[M]-通知罐区送开工低氮油,装置准备收油;通知罐区装置准备外送尾油和污油[I]-低氮油进装置后,通过开工低氮油流控阀控制系统进料,经S101,至V101 。
[P]-V101液位至70%时,启动P101,低氮油经E106、E107、FI102至V102[I ]-控制V101液位60%,压力0.2MPa4.1.3反应器进油预湿[P]-V102液位至70%时,启动P102,向反应器进料润湿,控制进料量75t/h(正常设计值的30%左右)[I ]-控制V102液位60%,压力0.2MPa[I ]-监控反应器温升,随着预湿油与催化剂的接触反应,会由于吸附碳烃化合物而放热出现温升,必要时,用冷氢维持反应器床层温度不大于175℃。
[I]-如吸附热温波超过40℃,停止进料量并降低炉出口温度[I]-待吸附热温波通过后,控制反应器入口温度175℃[I]-当吸附温波顺利通过催化剂床层后,以≯60t/h速度提反应器进料量至满负荷255t/h,进行催化剂预湿[I]-保持满负荷进料及最大循环氢流量4小时,以在催化剂颗粒上建立理想的薄膜流动(由于尾油泵量较小,需等分馏系统操作条件满足后,柴油、航煤、轻重石脑油有足够产生量,能够外送才可提量至满负荷,否则分馏系统塔、容器易超液位)[I]- V103液位至10%时,打开底部连锁切断阀,液位至30%时,通过控制阀缓慢向V104减油,至50%时,控制阀投自动。
[I]-A101出口温度超过50℃,投用A101风机, 控制V105温度50℃[I]- V105液位至10%时,打开底部连锁切断阀,液位至30%时,通过控制阀缓慢向V106减油,至50%时,控制阀投自动。
[I]-为防止反应产生的水在热高分底及热低分底聚集,尽量保证进热高分的原料油温度高一些[I]-V105界位至液位至30%时,通过控制阀缓慢向污水系统排放,至50%时,控制阀投自动。
[I]-V105界位至液位至30%时,通过控制阀缓慢向污水系统排放,至50%时,控制阀投自动。
4.1.4建立反应-分馏系统循环[I]- V104液位至70%,向T201减油,控制液位60%[I]-A102出口温度超过50℃,投用A101风机,控制V106温度50℃[I]- V106液位至70%,向T201减油,控制液位60%[P]- V104向T201减油后,打开尾油出装置阀门,关闭分馏短循环线阀门,外甩尾油4小时[P]-外甩尾油4小时后,采尾油样分析,检测其中的明水及颗粒杂质含量情况,若质量合格,以50t/h速度降低反应进料量至153t/h(60%负荷),改通尾油至V102循环,关闭尾油出装置控制阀,建立装置内反应-分馏长循环。
[P]-轻重石脑油、航煤、柴油根据塔、容器液位情况,通过轻污油线外送[P]-原料系统根据情况外补低氮油,以维持塔、容器的正常液位。
(因循环油泵量有限,需装置外开工低氮油连续进料,才能保证反应器有足够进料)[I]-系统各部位压力均按正常指标控制:V101压力0.2MPa、V102压力0.2MPa、 V105压力15.4MPa、 V106压力2.6MPa 、T201压力0. 75MPa、V202压力0. 5MPa、T202压力0.08MPa、T205压力1.3MPa、T206压力3.1MPa T208压力0.13MPa、 T209压力0.45MPa[I]-分馏系统温度控制:F201出口温度300℃、F202出口温度280℃,各塔顶温度按设计指标控制[I]-F202以15℃/h速度升温,控制其出口温度250℃(M)-确认催化剂充分预湿,尾油样分析合格,装置内反应-分馏长循环正常,准备进行催化剂硫化4.2脱硫系统投用4.2.1贫氨液系统投用(M)-确认贫氨液系统气密合格、氮气置换合格[P]-关闭贫氨液系统所有低点排凝阀、高点放空阀、蒸汽扫线阀[P]-投用加热器E219、E210循环水[P]-投用V208、V209安全阀和仪表[P]-投用V208、V209顶压控,并控制压力0.2MPa[P]-改通好贫氨液进贫氨液缓冲罐流程:装置外贫液液控阀 E219壳 V208液控阀 E220壳 V209[ I ] —联系罐区送贫氨液[ I ] —通过调节V208液控阀开度,控制V208液位60%,等待向T210系统送氨液[ I ] —通过调节V209液控阀开度,控制V208液位60%,等待向T207、T211系统送氨液4.2.2干气脱硫塔(T210)系统投用(M)-确认T209系统运行正常(M)-确认T210系统气密合格、氮气置换合格[P]-关闭T210系统所有低点排凝阀、高点放空阀、氮气、蒸汽扫线阀[P]-投用水冷器E221循环水[P]-投用T210、V210安全阀和仪表[P]-关闭T210、V210底液控上、下游阀门及副线阀门[P]-改通T210气体运行流程:T210 E221壳V210 V210压控放空[P]-投用V210顶压控,压力控制0.45MPa[P]-将T209气体改至去T210,关闭T209气体去放空线阀门,关闭T210跨线阀门(M)-确认T210系统气体流程运行正常,压力稳定[P]-投用T210贫液流控阀,启动P217,向T210送氨液,通过贫液流控阀控制流量6t/h [I]-T210液位至30%,投用T210液位控制阀,控制液位70%,将富氨液排至富氨液系统[ I ] —V210液位至30%,投用V210液位控制阀,控制液位50%[P]-系统运行稳定后,采干气样分析,分析合格,将干气由去放空系统改去干气管网系统4.2.3液化气脱硫抽提塔(T207)系统投用(M)-确认T206系统运行正常(M)-确认T207系统气密合格、氮气置换合格[P]-关闭T207系统所有低点排凝阀、高点放空阀、氮气、蒸汽扫线阀[P]-投用水冷器E212循环水[P]-投用T207、V206安全阀和仪表[P]-关闭T207、V206底液控上、下游阀门及副线阀门[P]-改通T207气体运行流程:T207 V206E212壳T207压控放空[P]-投用T207顶压控,压力控制1.9MPa[P]-打开T206含硫液化气入T207阀门,关闭T207跨线阀门(M)-确认T207系统气体流程运行正常,压力稳定[P]-投用T207贫液流控阀,启动P218,向T207送氨液,通过贫液流控阀控制流量3t/h [I]-T207液位至30%,投用T207液位控制阀,控制液位70%,将富氨液排至富氨液系统[ I ] —V206液位至30%,投用V206液位控制阀,控制液位50%,将富氨液排至富氨液系统[P]-系统运行稳定后,采液化气样分析,分析合格,将液化气由去放空系统改去液化气管网系统4.2.4低分气脱硫塔(T211)系统投用(M)-确认V106系统运行正常(M)-确认T211系统气密合格、氮气置换合格[P]-关闭T211系统所有低点排凝阀、高点放空阀、氮气、蒸汽扫线阀[P]-投用水冷器E222循环水[P]-投用T211、V211安全阀和仪表[P]-关闭T211、V211底液控上、下游阀门及副线阀门[P]-改通T211气体运行流程:T211 E222壳V211 V211压控放空[P]-投用V211顶压控,压力控制2. 5MPa[P]-将V106气体改至去T211,关闭V106气体去放空线阀门,关闭T211跨线阀门(M)-确认T211系统气体流程运行正常,压力稳定[P]-投用T211贫液流控阀,(若P218未运行,应启动),向T211送氨液,通过贫液流控阀控制流量5 t/h[I]-T211液位至30%,投用T211液位控制阀,控制液位70%,将富氨液排至富氨液系统[ I ] —V211液位至30%,投用V211液位控制阀,控制液位50%[P]-系统运行稳定后,采低分样分析,分析合格,将低分气由去放空系统改去制氢PSA 4.2.5富氨液系统投用(M)-确认富氨液系统气密合格、氮气置换合格[I]-控制V309压力0.2 MPa[I]-联系罐区富氨液准备外送[P]-打开富胺液出装置阀门[ I ]-监控V309液位见涨,确认脱硫系统已向V309排富胺液[P]-V309液位至60%,启动P308,向装置外送富氨液,通过V309液控阀控制V309液位50%4.3建立硫化剂自身循环[P]-投用V312安全阀、液位计、顶部氮封[P]-将DMDS桶内硫化剂通过P309送至V312,至液位80%(M)-确认其他DMDS桶内硫化剂可根据需要随时加注[P]-改通DMDS系统的自身循环流程:V312 →P310→DMDS返回线→V312[P]-启动P310,建立DMDS系统的自身循环[M]-调整泵的运行情况,确认整个系统无问题,等待向反应系统注硫。