对线材表面脱碳层深度变化规律的研究
加热过程中弹簧钢55SiCr表面脱碳研究
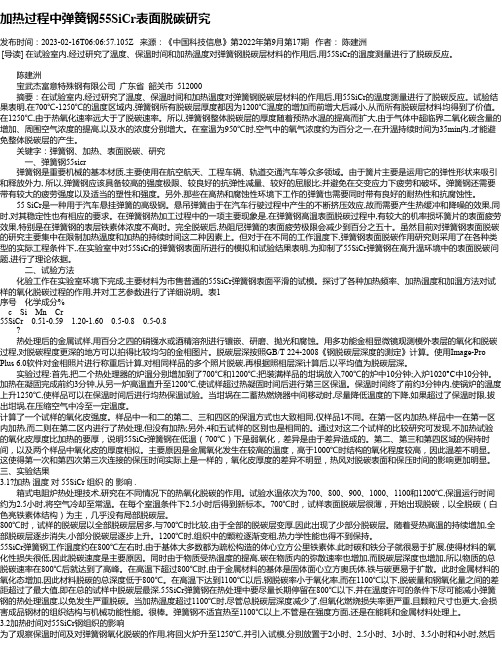
加热过程中弹簧钢55SiCr表面脱碳研究发布时间:2023-02-16T06:06:57.105Z 来源:《中国科技信息》第2022年第9月第17期作者:陈建洲[导读] 在试验室内,经过研究了温度、保温时间和加热温度对弹簧钢脱碳层材料的作用后,用55SiCr的温度测量进行了脱碳反应。
陈建洲宝武杰富意特殊钢有限公司广东省韶关市 512000摘要:在试验室内,经过研究了温度、保温时间和加热温度对弹簧钢脱碳层材料的作用后,用55SiCr的温度测量进行了脱碳反应。
试验结果表明,在700℃-1250℃的温度区域内,弹簧钢所有脱碳层厚度都因为1200℃温度的增加而前增大后减小,从而所有脱碳层材料均得到了价值。
在1250℃,由于热氧化速率远大于了脱碳速率。
所以,弹簧钢整体脱碳层的厚度随着预热水温的提高而扩大,由于气体中超临界二氧化碳含量的增加、周围空气浓度的提高,以及水的浓度分别增大。
在室温为950℃时,空气中的氧气浓度约为百分之一,在升温持续时间为35min内,才能避免整体脱碳层的产生。
关键字:弹簧钢、加热、表面脱碳、研究一、弹簧钢55sicr弹簧钢是重要机械的基本材质,主要使用在航空航天、工程车辆、轨道交通汽车等众多领域。
由于簧片主要是运用它的弹性形状来吸引和释放外力, 所以,弹簧钢应该具备较高的强度极限、较良好的抗弹性减量、较好的屈服比;并避免在交变应力下疲劳和破坏。
弹簧钢还需要带有较大的疲劳强度以及适当的塑性和强度。
另外,那些在高热和腐蚀性环境下工作的弹簧也需要同时带有良好的耐热性和抗腐蚀性。
55 SiCr是一种用于汽车悬挂弹簧的高级钢。
悬吊弹簧由于在汽车行驶过程中产生的不断挤压效应,故而需要产生热缓冲和降噪的效果,同时,对其稳定性也有相应的要求。
在弹簧钢热加工过程中的一项主要现象是,在弹簧钢高温表面脱碳过程中,有较大的机率损坏簧片的表面疲劳效果,特别是在弹簧钢的表层铁素体浓度不高时。
完全脱碳后,热阻尼弹簧的表面疲劳极限会减少到百分之五十。
高速线材生产中的产品缺陷分析
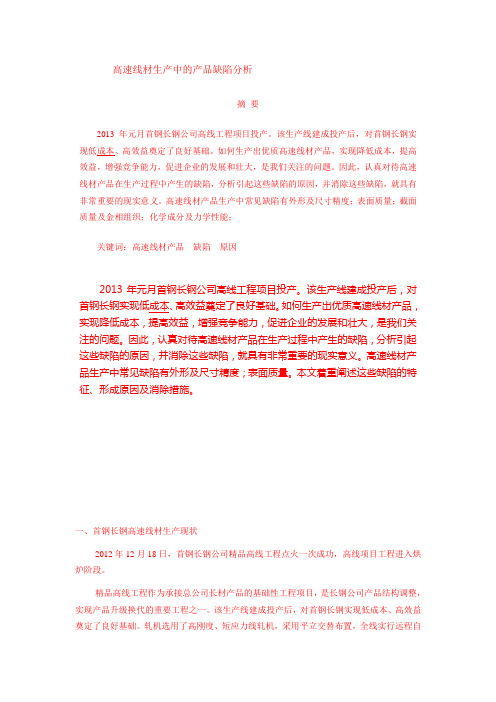
高速线材生产中的产品缺陷分析摘要2013年元月首钢长钢公司高线工程项目投产。
该生产线建成投产后,对首钢长钢实现低成本、高效益奠定了良好基础。
如何生产出优质高速线材产品,实现降低成本,提高效益,增强竞争能力,促进企业的发展和壮大,是我们关注的问题。
因此,认真对待高速线材产品在生产过程中产生的缺陷,分析引起这些缺陷的原因,并消除这些缺陷,就具有非常重要的现实意义。
高速线材产品生产中常见缺陷有外形及尺寸精度;表面质量;截面质量及金相组织;化学成分及力学性能;关键词:高速线材产品缺陷原因2013年元月首钢长钢公司高线工程项目投产。
该生产线建成投产后,对首钢长钢实现低成本、高效益奠定了良好基础。
如何生产出优质高速线材产品,实现降低成本,提高效益,增强竞争能力,促进企业的发展和壮大,是我们关注的问题。
因此,认真对待高速线材产品在生产过程中产生的缺陷,分析引起这些缺陷的原因,并消除这些缺陷,就具有非常重要的现实意义。
高速线材产品生产中常见缺陷有外形及尺寸精度;表面质量。
本文着重阐述这些缺陷的特征、形成原因及消除措施。
一、首钢长钢高速线材生产现状2012年12月18日,首钢长钢公司精品高线工程点火一次成功,高线项目工程进入烘炉阶段。
精品高线工程作为承接总公司长材产品的基础性工程项目,是长钢公司产品结构调整,实现产品升级换代的重要工程之一。
该生产线建成投产后,对首钢长钢实现低成本、高效益奠定了良好基础。
轧机选用了高刚度、短应力线轧机,采用平立交替布置,全线实行远程自动化控制,工艺装备达到了国际先进水平。
加热炉采用蓄热式高温燃烧技术,双层框架斜坡滚轮式炉底步进机械,热工自动化控制系统采用了国内先进技术,比常规加热炉节能45%。
轧机机组传动采用Siemens的SIMOREC-K全数字直流传动装置,所有传动电器均采用变频控制节能技术和无功补偿技术,节电率达35%以上,工业用水100%循环利用,实现零排放。
该工程项目于2013年元月份投产,可实现年产110万吨精品线材,主要产品品种有φ5.5—25mm全系列精品线材及中碳钢、高碳预应力钢丝及钢绞线、冷镦钢、爆破线、合金焊线等线材产品,可实现工业产值75亿元以上。
降低Ф5.5 mm LX72A盘条脱碳层深度的研究

第46卷 第5期金 属 制 品2020年10月 Vol 46 No 5MetalProductsOctober2020 doi:10.3969/j.issn.1003-4226.2020.05.009降低 5.5mmLX72A盘条脱碳层深度的研究李伟涛, 程培亮(潍坊特钢集团有限公司, 山东 潍坊 261201)摘要:为控制 5.5mmLX72A盘条的脱碳层深度不超过0.05mm,对影响脱碳层深度的因素进行研究分析并制定控制措施:加热炉均热段温度由1110~1150℃降低到1070~1110℃,炉内钢坯采用间隔布料的方式以减少加热时间,严格控制炉内空燃比。
采取控制措施后, 5.5mmLX72A盘条脱碳层深度不大于0.05mm,满足用户要求。
关键词:LX72A;盘条;脱碳层深度;加热温度;加热时间;空燃比中图分类号:TG356.4+6 文献标识码:AStudyonreducingdecarburizationdepthofdiameter5.5mmLX72AwirerodLiWeitao,ChengPeiliang(WeifangSpecialSteelGroupCo.,Ltd.,Weifang261201,China)Abstract:Tocontroldecarburizationdepthofdiameter5.5mmLX72Awirerodnotexceed0.05mm,thefactorsaffectingdecarbonizationdepthwerestudiedandanalyzedandcontrolledmeasureswereformulated.Temperatureofsoakingsectionofreheatingfurnacewasreducedfrom1110~1150℃to1070~1110℃,heatingtimeofbilletinreheatingfurnacewasreducedbyintervaldistribution,andstrictlycontroltheairfuelratioinfurnace.Aftertakingcontrolmeasures,thedecar burizationdepthofdiameter5.5mmLX72Awirerodisnotexceeding0.05mm,whichmeettheuser’srequirements.Keywords:LX72A;wirerod;decarbonizationdepth;heatingtemperature;heatingtime;airfuelratio 钢帘线是子午线轮胎的骨架材料,具有强度高、耐磨性好、弹性好及散热快的特点,是金属制品中生产难度最大的产品之一。
钢丝断裂原因分析

一、夹杂物引起断裂线材中非金属夹杂物的存在,破坏了组织的连续性,起到了一个显微裂纹的作用.当受到外力作用时,在夹杂物的顶端首先产生附加的应力集中.尤其在原奥氏体晶粒交界处出现的大块状、条状或片状碳化物,这些异常碳化物在材料冷变形时,严重地阻塞了位错的移动,致使该处产生应力集中.当应力集中达到一定大小时便会使碳化物开裂,或在碳化物与基体交界处产生裂纹.当裂纹达到失稳状态尺寸,地瞬时产生断裂.非金属夹杂物的多少是衡量帘线钢质量高低的一个重要因素.在用SEM对断口进行分析的过程中,经常发现非金属夹杂物.在典型的杯锥状断口上有时候就能发现夹杂物,SEM表明大多为三氧化二铝夹杂或其它高熔点脆性夹杂物.其避免主要是通过精炼,使夹杂物变为塑性低熔点夹杂物.脆性夹杂物是引起钢丝断裂的重要原因之一,而夹杂物引起断裂分为以下几种形势:1、夹杂物与钢基体之间界面脱开拉伸过程中,在夹杂物周围的局部加剧了应力集中;裂纹优先在与拉应力垂直的夹杂物与基体的界面产生并沿着夹杂物与钢基体界面扩展,致使夹杂物与基体界面脱开.2、夹杂物本身开裂由于脆性较矮杂物本身具有缺陷,在拉伸过程中,在缺陷处产生严重的应力集中,由于局部应力升高而导致夹杂物本身开裂.;3、混合开裂钢中非金属夹杂物的形状、分布是没有规律的,因此夹杂物在钢中引起裂纹也是随机性的,取决于夹杂物的性质、尺寸、形状与分布,对于同类型的夹杂物,由于形状、分布和受力方向不同,往往产生断裂的情况也不尽相同,有时两种断裂方式同时存在,有时两种断裂方式交替进行.4、沿两种不同类型夹杂物的相界开裂钢中经常出现几种夹杂物相共生在一起的复合夹杂物,由于各类夹杂物之间的力学性能和物理性质不同,相界结合力较弱,在拉应力作用下容易从相界开裂.二、偏析引起的钢丝断裂在一定程度上,中心偏析对钢丝拉断的危害必脆性夹杂物.因为偏析在更大程度上影响了钢丝的延伸性,从而使塑性变形不能在存在偏析的地方产生.在钢丝最初的拉拔过程中偏析导致小的裂纹的出现,等进入了最终拉拔时就导致了人字形断口<chevroncracks> 在连铸过程中减少中心偏析的途径有以下几个:1、中心偏析随着中包过热度的降低而降低,因此中包的钢液温度应该尽可能的低;2、在结晶器和二冷安装电磁搅拌.结晶器的电磁搅拌能够减少中心偏析的程度和X围.电磁搅拌同样可改善V形偏在铸坯中心的存在;3、尽可能的降低拉速,能够减轻中心偏析程度.三、马氏体组织造成拉拔脆断硬线属高碳钢,控制冷却时,若冷却时间太短,对钢材不起作用;若冷却时间太长,就容易引起脆断.在斯太尔摩控制冷却上,穿水冷却是奥氏体急速过冷阶段.它的目的是控制具有高形变能压扁的奥氏体晶粒长大和保留加工硬化的效果,为吐丝温度和后部风冷段控制做准备.轧制硬线错误的指导思想是,企图使线材表面淬成马氏体,然后通过心部自回火方式形成回火马氏体.如果这样,在高速的轧制下线材表面得不到充分自回火,难免出现马氏体残余.因为线材直径只有5.5 mm,最大也只有9mm,它的断面小,形变潜能也小,所以冷却不能过急,宜控制在0.3~0.6s,使线材表面温度始终在Ms以上<高于400℃>,以防止表面淬成马氏体.硬线的散卷风冷相当于"等温〞处理阶段,它的目的是控制钢中以索氏体为主的组织,以利于提高拉拔性能.要求组织中铁素体可能少且以块状均匀分布,而非网状析出,因而也应采用快速冷却方式.但若冷却速度过快,也会产生贝氏体或马氏体组织.尤其对于有合金元素偏析的铸坯,冷却速度达25℃/s就容易产生马氏体.因此,冷却速度宜为6~15℃/s,使奥氏体分解转变在接近CCT 曲线的鼻尖进行.对大直径线材,可选择高的初始冷却速度,因为直径增大,随体积增加的热焓量比表面所失去的热量要大,有促使先共析铁素体增加,珠光体组织长大之趋势.高碳马氏体既硬又脆,冲击吸收功很低,断后伸长率和断面收缩率几乎为零.同时,马氏体的比容比奥氏体大,当奥氏体转变为马氏体时钢的体积增大.由于马氏体转变的不均匀性,这种体积变化将引起很大的内应力,使钢发生变形,成为裂纹的根源.这样,在拉拔力或其它外力的作用下,易引起应力集中而使硬线脆断.四、严重脱碳层造成拉拔脆断线材的脱碳层直接影响着硬线的拉拔,对高碳硬线来说,严重的脱碳层好像一个缺口,不但承受面积小,应力增大,而且由于突然缩颈,容易引起应力集中导致拉丝脆断.通过脱碳层深度超标而使硬线脆断的试样断口观察和试样金相分析,发现有裂纹和组织两个重要特征.第一,硬线表面均存在白色长条,其中平行地分布着横裂纹,有的横裂纹已深入基体.因此,硬线的断线是由于它表层长条区内的横裂纹扩展而引起的.白色长条区是全脱碳形成的铁素体组织,它是组织中的薄弱环节.第二,硬线组织不是所要求的以索氏体为主的组织,而是网状铁素体和粗片状珠光体.网状铁素体的存在会导致抗拉强度下降,拉拔时承受变形能力差;粗片状珠光体的存在也会导致硬线塑韧性与拉拔能力的降低.这两种组织是由于加热温度过高、加热时间过长,钢的相变温度偏高,过冷度小而析出的,是脱碳的前沿产物.此外,硬线随拉拔变形程度的加大,加工硬化程度也增大,网状铁素体和粗片珠光体的存在又增加硬线的脆性.当硬线拉拔时,由于脱碳层产生横裂纹,而邻近网状铁素体和粗片状珠光体又不能有效地阻止裂纹的扩展,且受到拉拔、收盘的扭绞力共同作用,部分硬线即刻脆断.因此,铸坯加热温度愈高,加热时间愈长,炉内漏气或其他不正常因素愈多,脱碳会愈严重,从部分脱碳到全脱碳,使钢失去更多的碳.为了防止脱碳,应严格执行规章制度,对不同钢号和规格钢坯与时调整加热温度,提高工作的责任感.从控制脱碳优化氧化铁皮的角度考虑,炉内应保持一定氧化气氛,可形成薄的氧化铁皮,阻止钢坯表面继续脱碳.在预热段应缓慢加热<至850℃,2h>,并有合适的保温.钢坯在850℃~105 0℃时,由于脱碳有向抛物线顶点发展的趋势,应严格控制加热时间不超过30min,并要尽理缩短均热段保温时间.五、其它非冶金原因关于钢丝拉拔时的断丝,1984年ZeevZimerman和RoverJ.Henry 对此作了探讨.他们对钢帘线用钢丝在水箱拉丝机上拉拔时断口用SE M进行分析,观察到拉拔断口大部分成杯锥状.并指出,钢丝拉拔时,表面层金属比心部金属变形大,这引起表面层金属沿长度方向受压应力而中心部分受拉应力,当此拉应力过大时致使在中心部位产生中心破裂,即形成V型裂纹或人字形裂纹.并认为这种V型裂纹是拉拔断丝成为大量杯锥状断口的原因.虽然ZeevZimerman和RovertJ.Herry对此研究得很详细,但是未能考虑后面工序中的捻制断丝问题,未能指出两种杯锥状断口的内在联系.1981年,EddyG.Demeyere在研究高低碳钢的夹杂物对钢丝拉拔时的可加工性能和机械性能的影响时,曾指出,在钢丝拉拔到Φ0.25mm过程中,很少或根本没有发现由于夹杂物引起的断丝更令人惊奇的是,即使50µm大的零星存在的夹杂物也未能造成拉拔断丝,而主要是由于表面缺陷或过在造成的断丝.他说,这种情况与帘线捻制时不同,由于在捻制时钢丝受到扭转变形,则夹杂物的影响就显得中大.显然,EddyG.Demeyere试图从夹杂物角度出发同时考虑帘线钢用钢丝的拉拔断丝和年至断丝问题,但在该文中,他对这两种断丝之间内在联系的探讨仅此而已,未能进行深入研究.因此,钢丝表面缺陷、内部夹杂物、热处理工艺、拉拔工艺都可能导致钢丝质量不合理,从而在拉拔过程中断裂.。
脱碳层检测标准(一)

脱碳层检测标准(一)
脱碳层检测标准
介绍
•脱碳层是金属材料经过高温加热后,表面的碳元素被氧化、还原等反应脱去形成的一层低碳金属组织。
•脱碳层影响材料的机械性能和化学性能,因此脱碳层检测标准的制定非常重要。
目的
•确保产品质量,保证材料性能和使用寿命。
标准一:脱碳层检测的方法
•火花光谱法:通过电极放电时产生的火花光谱来分析材料中的元素成分及脱碳层的深度。
•金相显微镜法:观察材料的组织结构,脱碳层的宽度和深度可以通过特定的显微镜放大倍数来确定。
•硬度计法:利用硬度计测试材料的硬度,脱碳层会导致硬度值的降低。
标准二:脱碳层检测的要求
•确定脱碳层的宽度和深度,同时要求在给定材料和工艺条件下,脱碳层的厚度应符合规定的数值范围。
•材料的力学性能如抗拉强度、硬度等不应受到脱碳层的影响,即脱碳层的形成不应对材料的力学性能产生负面影响。
•检测结果应具有可重复性和准确性,确保不同实验室、不同设备之间的检测结果一致。
标准三:脱碳层检测的限制
•不同材料的脱碳层深度和宽度可能会有差异,需要根据具体材料的特性确定合理的范围。
•检测方法的精度和准确性直接影响着脱碳层检测结果的可信度,需要进行定期校准和质量控制。
结论
•脱碳层检测标准的制定和执行对于确保材料的质量和使用寿命具有重要意义。
•通过采用多种检测方法,确保脱碳层的宽度和深度符合要求,并注意检测结果的精度和准确性,可以有效提高产品的质量和可靠性。
以上是关于脱碳层检测标准的相关内容,希望对读者有所帮助。
脱碳层深度测定方法(一)
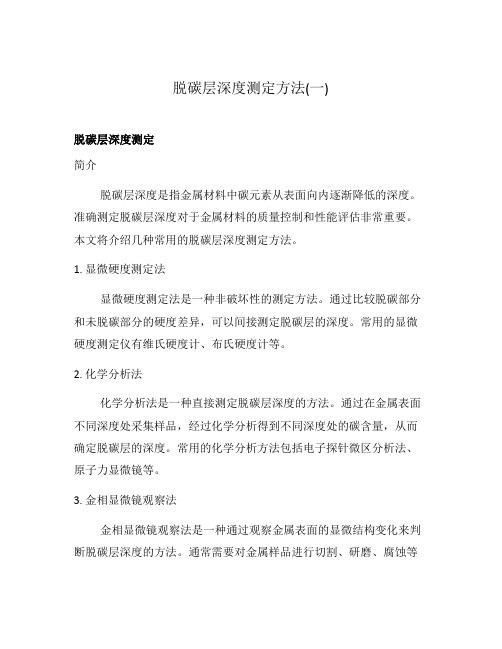
脱碳层深度测定方法(一)脱碳层深度测定简介脱碳层深度是指金属材料中碳元素从表面向内逐渐降低的深度。
准确测定脱碳层深度对于金属材料的质量控制和性能评估非常重要。
本文将介绍几种常用的脱碳层深度测定方法。
1. 显微硬度测定法显微硬度测定法是一种非破坏性的测定方法。
通过比较脱碳部分和未脱碳部分的硬度差异,可以间接测定脱碳层的深度。
常用的显微硬度测定仪有维氏硬度计、布氏硬度计等。
2. 化学分析法化学分析法是一种直接测定脱碳层深度的方法。
通过在金属表面不同深度处采集样品,经过化学分析得到不同深度处的碳含量,从而确定脱碳层的深度。
常用的化学分析方法包括电子探针微区分析法、原子力显微镜等。
3. 金相显微镜观察法金相显微镜观察法是一种通过观察金属表面的显微结构变化来判断脱碳层深度的方法。
通常需要对金属样品进行切割、研磨、腐蚀等处理,然后在金相显微镜下观察脱碳层的深度和形态。
该方法操作简单,但需要一定的经验和技术。
4. X射线衍射法X射线衍射法是一种通过测定材料中的晶格结构变化来确定脱碳层深度的方法。
通过测量X射线在不同深度处的衍射图样,可以分析出脱碳层的厚度和组织结构的变化。
X射线衍射法有较高的分辨率和灵敏度,但需要专业的设备和技术支持。
5. 磁学方法磁学方法是一种利用磁性测量来判断脱碳层深度的方法。
通过测量不同深度处的磁性特征,可以确定脱碳层的厚度和性质。
磁学方法操作简单,但对于非磁性材料不适用。
以上是几种常见的脱碳层深度测定方法,每种方法都有其优缺点。
在实际应用时,需要根据具体情况选择合适的方法进行测定。
对于不同材料和应用要求,可以综合运用多种方法来提高测定的准确性和可靠性。
注:本文仅供参考,具体操作时请遵循相关的标准和规范。
6. 激光扫描法激光扫描法是一种利用激光扫描测量脱碳层深度的方法。
通过激光的反射和折射特性,扫描金属表面,可以得到表面的形貌和高程数据,从而间接测定脱碳层的深度。
激光扫描法具有非接触、高精度、高效率的优点,适用于各种金属材料的测量。
总脱碳层深度定义

总脱碳层深度是指材料在退火或高温回火过程中,其表面或内部由于碳元素扩散迁移所导致的含碳量降低的程度。
这个概念在金属材料中非常重要,因为它涉及到材料的性能、组织和使用效果。
首先,脱碳层深度的影响因素主要包括材料的成分、温度和时间。
在高温环境下,金属材料中的碳元素会随着温度的升高而更容易迁移,这会导致材料的含碳量降低。
此外,材料的成分也会影响脱碳层的深度,一般来说,低碳合金的脱碳层深度较小,而高碳合金的脱碳层深度较大。
在实际应用中,总脱碳层深度对材料的使用效果有着重要的影响。
例如,在铸造铝合金生产中,如果脱碳层深度较大,会导致材料的强度和硬度降低,影响其使用效果。
同时,过深的脱碳层深度还可能导致材料出现脆性断裂,从而降低其安全性。
因此,控制脱碳层深度是保证材料性能和使用效果的重要措施之一。
对于不同的材料和加工工艺,控制脱碳层深度的方法也不尽相同。
例如,对于钢铁材料,可以通过控制加热温度和时间来减少脱碳层深度;对于铸造铝合金,可以通过控制熔炼过程和铸造工艺来减少脱碳层深度。
此外,在材料表面涂覆一层保护层或者采用真空冶炼等先进工艺技术也可以有效地控制脱碳层深度。
总的来说,总脱碳层深度是一个非常重要的概念,它涉及到材料的性能、组织和使用效果。
通过了解脱碳层深度的影响因素和实际应用中的控制方法,我们可以更好地利用材料,提高其性能和使用效果,同时也能够更好地保障其安全性和可靠性。
然而,脱碳层深度并不是衡量材料质量或性能的唯一指标。
在实际应用中,我们还需要考虑其他因素,如材料的强度、硬度、韧性、耐腐蚀性等。
因此,我们需要综合考虑各种因素,选择最适合实际需求的材料和加工工艺。
总之,总脱碳层深度是一个重要的概念,它涉及到材料的性能和使用效果。
通过深入了解其影响因素和控制方法,我们可以更好地利用材料,提高其性能和使用效果,同时也能够更好地保障其安全性和可靠性。
iso 3887-2023 钢的脱碳层测定方法

钢的脱碳层测定方法一、金相法金相法是通过观察钢的表面脱碳层在金相显微镜下的组织形态,以确定脱碳层的深度。
该方法要求样品制备规范,操作复杂度较低,但对于操作人员的经验要求较高。
二、硬度法硬度法是通过测量钢的表面硬度和深度,推算出脱碳层的深度。
硬度法操作简便,但对于不同成分的钢,其对应关系有一定的差异,需要进行校准。
三、腐蚀法腐蚀法是通过化学或电化学方法对钢表面进行处理,使其表面形成一层腐蚀膜,然后通过观察腐蚀膜的厚度来确定脱碳层的深度。
该方法精度较高,但操作过程较为繁琐,且对实验条件要求较高。
四、宏观观察法宏观观察法是通过肉眼或低倍显微镜观察钢表面的颜色、光泽等宏观特征,结合经验判断脱碳层的深度。
该方法简单易行,但精度较低,且受观察者的主观因素影响较大。
五、扫描电镜法扫描电镜法是通过扫描电镜观察钢表面的微观形貌,结合能谱分析确定脱碳层的元素分布和深度。
该方法精度高,但设备昂贵,操作复杂度较高。
六、俄歇电子能谱法俄歇电子能谱法是通过俄歇电子能谱仪测量钢表面元素的俄歇跃迁能量,结合已知的元素浓度和能量关系,计算脱碳层的深度。
该方法精度高,但对样品的要求较高,且设备昂贵。
七、X射线能谱法X射线能谱法是通过X射线能谱仪测量钢表面元素的特征X射线能量,结合已知的元素浓度和能量关系,计算脱碳层的深度。
该方法精度高,但对样品的要求较高,且设备昂贵。
八、化学分析法化学分析法是通过化学溶解钢样品,使用滴定、光谱等手段测量溶解液中各元素的浓度,结合已知的元素分布和浓度关系,计算脱碳层的深度。
该方法精度高,但对样品的要求较高,且操作复杂度较高。
九、厚度测量法厚度测量法是通过精密测量设备,如千分尺、测厚仪等,直接测量脱碳层的厚度。
这种方法简单直接,精度较高,但需要使用精密的测量设备,且对于较厚的脱碳层可能存在一定的误差。
十、X射线衍射法X射线衍射法是通过X射线衍射仪对钢表面进行衍射分析,根据衍射峰的强度和位置变化,推算出脱碳层的厚度。
钢的脱碳层深度

钢的脱碳层深度钢的脱碳层深度一、什么是脱碳层脱碳层是指钢铁中碳浓度低于表面和深度较浅处的标准含碳量的组织。
在淬火和回火过程中,会因为碳在钢中的扩散而形成脱碳层,并在表面形成显微硬度大、强度高的硬皮。
二、脱碳层深度的测试方法1.金相法金相法是通过金相显微镜观察钢铁组织来测定脱碳层深度,并且可以直观地看到脱碳层的形态和大小。
但是,该方法对检验人员的经验和操作技能要求较高。
2.化学分析法化学分析法是针对不同材料测定脱碳深度的方法,广泛应用于工业生产中。
通过该方法可以更准确地测定脱碳层的深度。
3.触针法触针法是一种快速简便的测定脱碳深度的方法,并且能够得到较为准确的结果。
但是,该方法对针头大小和形状的精确要求较高。
三、影响脱碳层深度的因素1. 钢的成分不同的钢材在生产中采用的合金元素和含量不同,对其脱碳层深度会产生不同的影响。
2. 淬火温度和时间淬火温度高、时间长会导致脱碳层变厚,反之脱碳层变薄。
3. 钢材表面加工钢材表面的机械加工、化学处理等都会对脱碳层深度产生影响。
四、如何控制脱碳层深度1. 降低淬火温度和时间为了控制脱碳层深度,在淬火过程中可以降低温度和时间,避免脱碳层过厚。
2. 选择合适的钢材不同合金元素和含量的钢材对应的脱碳层深度不同,选择合适的钢材可以有效控制脱碳层深度。
3. 加强钢材处理钢材生产过程中加强钢材的表面处理是控制脱碳层深度的重要手段之一。
总的来说,脱碳层深度是影响钢铁性能的重要因素之一。
通过科学的检测方法和合理的控制手段,可以有效地控制脱碳层深度,保证钢铁的品质和使用寿命。
金属材料脱碳层深度试验测试
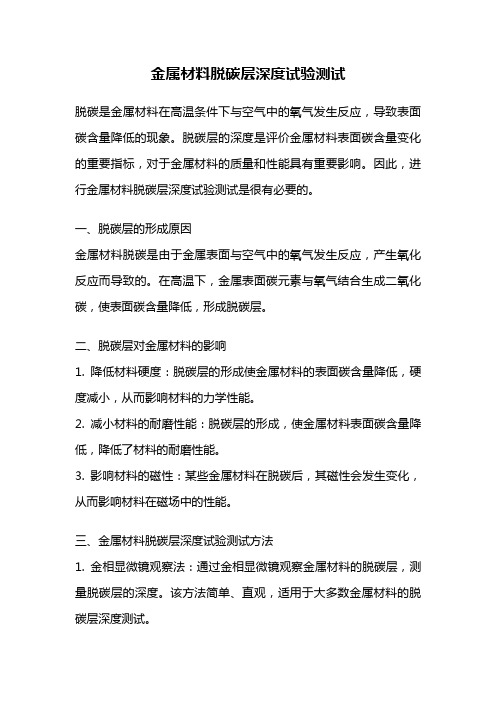
金属材料脱碳层深度试验测试脱碳是金属材料在高温条件下与空气中的氧气发生反应,导致表面碳含量降低的现象。
脱碳层的深度是评价金属材料表面碳含量变化的重要指标,对于金属材料的质量和性能具有重要影响。
因此,进行金属材料脱碳层深度试验测试是很有必要的。
一、脱碳层的形成原因金属材料脱碳是由于金属表面与空气中的氧气发生反应,产生氧化反应而导致的。
在高温下,金属表面碳元素与氧气结合生成二氧化碳,使表面碳含量降低,形成脱碳层。
二、脱碳层对金属材料的影响1. 降低材料硬度:脱碳层的形成使金属材料的表面碳含量降低,硬度减小,从而影响材料的力学性能。
2. 减小材料的耐磨性能:脱碳层的形成,使金属材料表面碳含量降低,降低了材料的耐磨性能。
3. 影响材料的磁性:某些金属材料在脱碳后,其磁性会发生变化,从而影响材料在磁场中的性能。
三、金属材料脱碳层深度试验测试方法1. 金相显微镜观察法:通过金相显微镜观察金属材料的脱碳层,测量脱碳层的深度。
该方法简单、直观,适用于大多数金属材料的脱碳层深度测试。
2. 超声波测厚仪法:利用超声波测厚仪对金属材料进行测试,测量脱碳层的厚度。
该方法无需破坏样品,测试速度快,适用于不同形状和尺寸的金属材料。
3. X射线衍射法:利用X射线衍射仪测量金属材料的脱碳层深度。
该方法具有高精度、无损伤等特点,适用于对脱碳层深度要求较高的金属材料。
四、脱碳层深度试验测试的注意事项1. 样品制备:样品制备要保证表面平整、无杂质,以确保测试结果的准确性。
2. 测试环境:测试环境应保持稳定的温度和湿度,以避免外界因素对测试结果的影响。
3. 测试仪器校准:使用前要对测试仪器进行校准,确保测试结果的准确性和可靠性。
4. 多次测试取平均值:为了提高测量结果的准确性,可以进行多次测试并取平均值。
五、金属材料脱碳层深度试验测试的应用金属材料脱碳层深度试验测试广泛应用于金属材料加工、制造、材料研究等领域。
通过脱碳层深度的测试,可以评估金属材料的质量和性能,指导金属材料的选用和加工工艺的优化。
热处理表面脱碳层深度

热处理表面脱碳层深度我们来了解一下什么是表面脱碳。
表面脱碳是指金属材料在加热和冷却过程中,表面碳含量减少的现象。
一般来说,金属材料的表面碳含量较高,而内部含碳量较低。
在加热过程中,由于碳的活性较高,容易被氧化,从而导致表面碳含量减少,形成表面脱碳层。
那么,热处理过程中的表面脱碳层深度受到哪些因素的影响呢?首先是加热温度。
加热温度是影响表面脱碳层深度的主要因素之一。
一般来说,加热温度越高,表面脱碳层深度越大。
这是因为高温下,碳元素更容易与氧气发生反应,从而加剧表面脱碳现象。
其次是加热时间。
加热时间也会对表面脱碳层深度产生影响。
加热时间越长,表面脱碳层深度越大。
这是因为长时间的加热会使金属材料中的碳元素与氧气反应的时间更充足,从而加剧了表面脱碳现象。
金属材料的成分也会对表面脱碳层深度产生影响。
一般来说,含碳量较高的金属材料,其表面脱碳层深度较大。
这是因为含碳量较高的金属材料,其表面碳含量也较高,容易被氧气氧化而形成表面脱碳层。
除了以上因素外,还有一些其他因素也会对表面脱碳层深度产生影响,如冷却速度、环境气氛等。
冷却速度越快,表面脱碳层深度越小。
环境气氛中的氧气浓度越高,表面脱碳层深度也越大。
为了减小表面脱碳层的深度,可以采取一些措施。
首先是控制加热温度和时间,避免过高的温度和过长的时间。
其次是采用保护气氛或真空热处理,减少氧气的接触。
此外,还可以选择含碳量较低的金属材料,从根本上减少表面脱碳层的深度。
热处理过程中的表面脱碳层深度是受到多种因素影响的。
加热温度、加热时间、金属材料成分、冷却速度和环境气氛等因素都会对表面脱碳层的形成产生影响。
为了减小表面脱碳层的深度,可以采取相应的措施。
通过合理的热处理工艺,可以控制表面脱碳层的深度,从而获得理想的金属材料性能和表面质量。
中高碳钢脱碳控制技术研究

( o rh n ieM a a e n e a t n ) C mp e e s n g me t p rme t v D
Ab ta t T i p p ri t d c s t ef co s efci g d c r u iai n o ih c r o t e ier d s r c :h s a e r u e h a tr f t e a b rz t f g a b n se l r o .T s s h me i ma e n o e n o h w e t c e s d b s d o cu lp o u t n a e n a ta r d ci .T e r s l h w t a ed c r u i t n c n b e r a e y4 , f m 0 t 8 [m a d o h e u t s o t h e a b r a i a e d c e s d b 5 p r 6 o 0 x n s h t z o m o
~
8 m, 到 4 m 以 下 , 化 铁 皮 厚 度 从 1 0t 降 x 5t x 氧 4~1 m, 8 降到 8 m 以 下。
关 键词 : 铁素体脱碳 帘线钢 中高碳钢 氧化铁皮
S ud n De a b ia i n Co r lo e u nd H i h Ca bo S e l t y o c r urz to nt o fM di m a g r n t e
现象 ; 对于弹簧钢而言 , 表面 脱碳会降低 弹簧 的疲劳 极 限, . m 的 脱 碳 深 度 就 会 使 疲 劳 极 限 下 降 0 1m 5% , 0 工具钢 、 轴承 钢的表 面脱 碳层 如不 清 除干净 ,
将使工具钢 、 轴承钢表面层硬度和耐磨 性降低 , 淬火
EN 10221
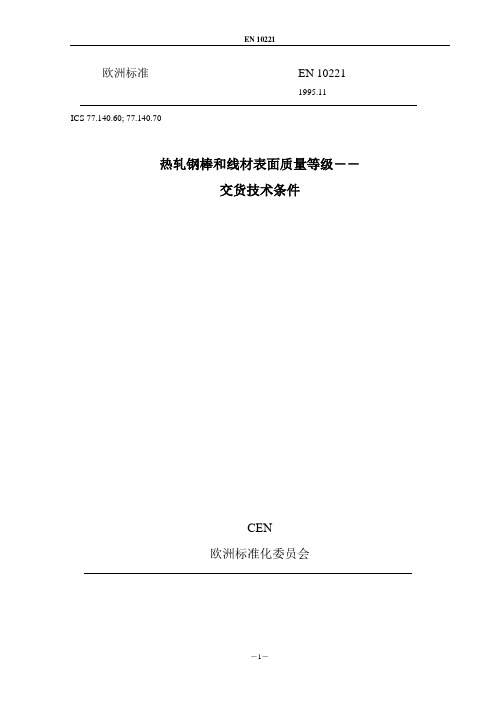
欧洲标准EN 102211995.11ICS 77.140.60; 77.140.70热轧钢棒和线材表面质量等级――交货技术条件CEN欧洲标准化委员会目录1 范围2 规范性引用文件3 定义4 要求4.1 一般要求4.2 订货内容4.3 标记5 试验5.1 一般要求5.2 试验方法6 修补前言本欧洲标准由技术委员会ECISS/TC15“钢丝-盘条-质量、尺寸、允许偏差和专用试验”(秘书处:意大利)和技术委员会ECISS/TC23“热处理钢、合金钢和易切削钢-质量”(秘书处:德国)组成的联合工作组起草。
本欧洲标准代替:Pr EN10163-4 热轧钢产品表面质量交货要求—第4部分:圆钢和线材。
本欧洲标准应用国家标准的形式最晚于1996年5月以同样文本公布或签发,并同时废除与之相矛盾的国家标准。
按照CEN/CENELEC的内部章程,下列国家有义务执行此欧洲标准:奥地利、比利时、丹麦、芬兰、法国、德国、希腊、冰岛、爱尔兰、意大利、卢森堡、荷兰、挪威、葡萄牙、西班牙、瑞典、瑞士和英国。
1 范围1.1 本欧洲标准规定了公称直径在5 mm≤dN≤150mm的热轧圆钢和线材的表面质量要求。
1.2 由供需双方协商同意,本欧洲标准也适用于方钢、六角钢和八角钢。
1.3本欧洲标准主要适用于工程用钢,但经同意也适用于一般结构钢或工具钢。
1.4本欧洲标准不包括对表面脱碳层允许深度的任何要求。
2 规范性引用文件本欧洲标准在条文中适当处引用了其它文件中的条款。
这些文件有注日期或不注日期的,名称如后。
凡注日期的引用文件,其随后所有的修改单或修订本仅当包含在本标准中时才适用于本标准。
凡未注日期的引用文件,其最新版本适用于本标准。
PrEN 10079 钢产品定义ISO 7800 金属材料—线材—简单扭转试验3定义以下定义适用于本欧洲标准:3.1交货批除非订货合同中或在相应的产品标准中另有规定,交货批是指由同一牌号、同一直径规格、同一表面质量要求、并同一时间交货的钢材数量。
GBT 224-2019《钢的脱碳层深度测定法》中金相法之缺陷
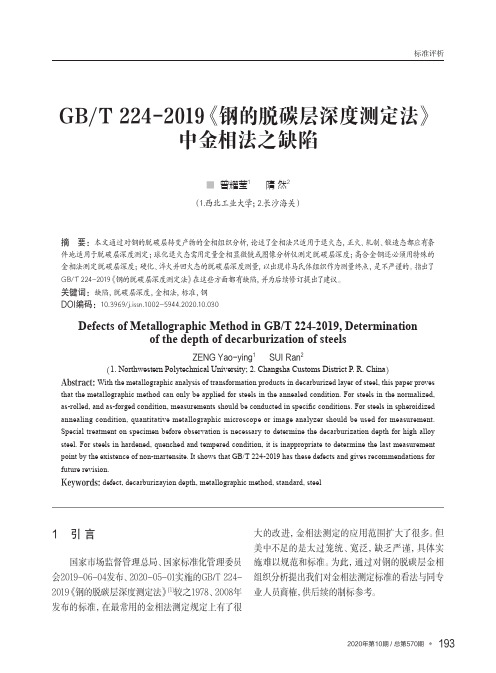
GB/T 224-2019《钢的脱碳层深度测定法》中金相法之缺陷■ 曾耀莹1 隋 然2(1.西北工业大学;2.长沙海关)摘 要:本文通过对钢的脱碳层转变产物的金相组织分析,论述了金相法只适用于退火态,正火、轧制、锻造态都应有条件地适用于脱碳层深度测定;球化退火态需用定量金相显微镜或图像分析仪测定脱碳层深度;高合金钢还必须用特殊的金相法测定脱碳层深度;硬化、淬火并回火态的脱碳层深度测量,以出现非马氏体组织作为测量终点,是不严谨的。
指出了GB/T 224-2019《钢的脱碳层深度测定法》在这些方面都有缺陷,并为后续修订提出了建议。
关键词:缺陷,脱碳层深度,金相法,标准,钢DOI编码:10.3969/j.issn.1002-5944.2020.10.030Defects of Metallographic Method in GB/T 224-2019, Determinationof the depth of decarburization of steelsZENG Yao-ying1 SUI Ran2(1. Northwestern Polytechnical University; 2. Changsha Customs District P. R. China)Abstract: With the metallographic analysis of transformation products in decarburized layer of steel, this paper proves that the metallographic method can only be applied for steels in the annealed condition. For steels in the normalized, as-rolled, and as-forged condition, measurements should be conducted in specific conditions. For steels in spheroidized annealing condition, quantitative metallographic microscope or image analyzer should be used for measurement. Special treatment on specimen before observation is necessary to determine the decarburization depth for high alloy steel. For steels in hardened, quenched and tempered condition, it is inappropriate to determine the last measurement point by the existence of non-martensite. It shows that GB/T 224-2019 has these defects and gives recommendations for future revision.Keywords: defect, decarburizayion depth, metallographic method, standard, steel标准评析1 引 言国家市场监督管理总局、国家标准化管理委员会2019-06-04发布、2020-05-01实施的GB/T 224-2019《钢的脱碳层深度测定法》[1]较之1978、2008年发布的标准,在最常用的金相法测定规定上有了很大的改进,金相法测定的应用范围扩大了很多。
20crmnti渗碳硬度随深度变化曲线

大家好,今天我要和大家共享的主题是20crmnti渗碳硬度随深度变化曲线。
这是一个非常具体的主题,需要我们深入了解20crmnti的渗碳硬度曲线在不同深度下的变化情况。
下面,我将按照从简到繁、由浅入深的方式来探讨这个主题,以便让我们能更深入地理解。
让我们简单了解一下20crmnti。
20crmnti是一种优质合金钢,主要成分是铁、碳、锰、铬和钛。
它具有较高的强度和硬度,并且具有良好的韧性和耐磨性,因此被广泛应用于工程机械和汽车制造等领域。
而20crmnti的渗碳硬度随深度变化曲线,则是对这种合金钢在渗碳处理后硬度随深度变化的一种曲线描述。
在20crmnti的渗碳处理中,通常会采用气体渗碳、浸碳等方法,通过在一定气氛或介质中进行加热处理,使得材料表面形成高碳化物层,以增加材料的表面硬度和耐磨性。
而20crmnti渗碳硬度随深度变化曲线,就是描述了在这种处理过程中,20crmnti材料表面硬度和深度之间的关系。
随着渗碳时间的增加,20crmnti材料表面硬度会不断增加,形成一个硬度深度曲线。
曲线的起始部分代表着表面的硬度增加,随后随着深度的增加,硬度会逐渐下降,最终趋于稳定。
这种曲线反映了20crmnti材料在渗碳处理后的硬度变化规律,对于工程机械和汽车制造等领域的零部件来说,具有重要的意义。
结合个人观点和理解,我认为20crmnti渗碳硬度随深度变化曲线的研究对材料表面改性和性能提升具有重要意义。
通过深入研究20crmnti 材料的渗碳处理,可以更好地了解材料的表面硬度变化规律,为工程实践中的零部件制造和设计提供重要的参考依据。
这也为工程材料的性能改善和优化提供了重要的技术支持。
总结回顾一下,我们对20crmnti渗碳硬度随深度变化曲线进行了全面的评估和探讨。
首先简要介绍了20crmnti材料和渗碳处理的基本情况,然后详细描述了渗碳处理后20crmnti材料表面硬度随深度变化的曲线特点,最后结合个人观点和理解,指出了这一研究对工程实践的重要意义。
60Si2Mn弹簧钢表面脱碳的研究

第3期 No. 3
金属制品 steei Wire Products
2005 年 6 月 June 2005
60Si2mn 弹簧钢表面脱碳的研究
蔡海燕 张忠铧 张 弛
( 宝山钢铁股份有限公司 201900)
摘 要 研究加热条件、冷却速度对 60si2mn 弹簧钢线材表面脱碳的影响。结果表明,弹簧钢轧前加热和轧后冷 却过程均会导致表面脱碳。降低加热温度和炉内残氧量、缩短在炉时间、提高轧后两相区冷却速度可明显降低钢 的表面脱碳。 关键词 60si2mn;弹簧钢;加热条件;冷却速度;脱碳 中图分类号 Tg142. 41
60Si2Mn弹簧钢表面脱碳的研究
作者: 作者单位: 刊名:
英文刊名: 年,卷(期): 被引用次数:
蔡海燕, 张忠铧, 张弛, Cai Haiyan, Zhang Zhonghua, Zhang Chi 宝山钢铁股份有限公司,201900
金属制品 STEEL WIRE PRODUCTS 2005,31(3) 13次
um-free SteeIs for Suspension CoiI Sprin[g J]. Paper 800479 presented at SAE congress and exposition. Detroit,1982. 2
( 收稿日期:2005 - 04 - 04)
面脱碳相应增加。不同冷却速度和冷却介质试验结 果表明,60Si2mn 钢的 ! ! " 两相区转变温度为 800 ~ 650 C ,在此温度区间随冷却速度的增加,钢的脱 碳层尤其是铁素体脱碳减小,且冷速达到 15 C / min 时,表面没有产生铁素体全脱碳,这说明钢的脱碳不
图 5 冷却速度对表面铁素体脱碳的影响
脱碳层深度测定方法
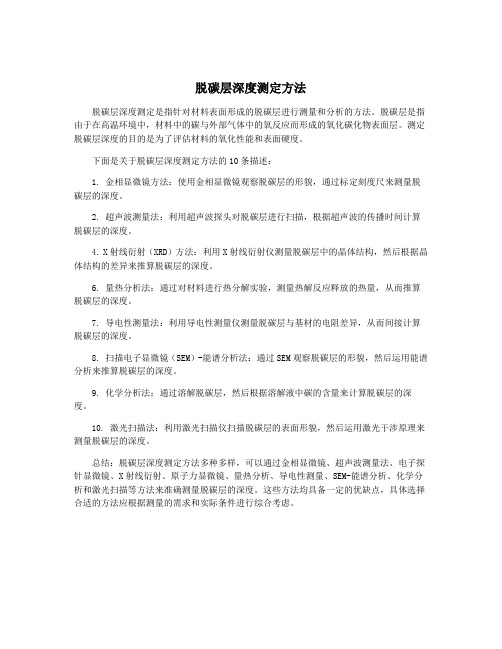
脱碳层深度测定方法
脱碳层深度测定是指针对材料表面形成的脱碳层进行测量和分析的方法。
脱碳层是指由于在高温环境中,材料中的碳与外部气体中的氧反应而形成的氧化碳化物表面层。
测定脱碳层深度的目的是为了评估材料的氧化性能和表面硬度。
下面是关于脱碳层深度测定方法的10条描述:
1. 金相显微镜方法:使用金相显微镜观察脱碳层的形貌,通过标定刻度尺来测量脱碳层的深度。
2. 超声波测量法:利用超声波探头对脱碳层进行扫描,根据超声波的传播时间计算脱碳层的深度。
4. X射线衍射(XRD)方法:利用X射线衍射仪测量脱碳层中的晶体结构,然后根据晶体结构的差异来推算脱碳层的深度。
6. 量热分析法:通过对材料进行热分解实验,测量热解反应释放的热量,从而推算脱碳层的深度。
7. 导电性测量法:利用导电性测量仪测量脱碳层与基材的电阻差异,从而间接计算脱碳层的深度。
8. 扫描电子显微镜(SEM)-能谱分析法:通过SEM观察脱碳层的形貌,然后运用能谱分析来推算脱碳层的深度。
9. 化学分析法:通过溶解脱碳层,然后根据溶解液中碳的含量来计算脱碳层的深度。
10. 激光扫描法:利用激光扫描仪扫描脱碳层的表面形貌,然后运用激光干涉原理来测量脱碳层的深度。
总结:脱碳层深度测定方法多种多样,可以通过金相显微镜、超声波测量法、电子探针显微镜、X射线衍射、原子力显微镜、量热分析、导电性测量、SEM-能谱分析、化学分析和激光扫描等方法来准确测量脱碳层的深度。
这些方法均具备一定的优缺点,具体选择合适的方法应根据测量的需求和实际条件进行综合考虑。
- 1、下载文档前请自行甄别文档内容的完整性,平台不提供额外的编辑、内容补充、找答案等附加服务。
- 2、"仅部分预览"的文档,不可在线预览部分如存在完整性等问题,可反馈申请退款(可完整预览的文档不适用该条件!)。
- 3、如文档侵犯您的权益,请联系客服反馈,我们会尽快为您处理(人工客服工作时间:9:00-18:30)。
万方数据
怎第174期
同样道理,只要知道各道次轧件尺寸。
可以根据(1)式来计算其脱碳层深度。
如果某逆晴卿轧件直径为loomm,由式(1)可得,线材的脱碳层深度为0.5679mm。
4线材表面脱碳层深度变化规律的研究
由式(1)中的关系,也可以看作钢坯表面1.045mm深度的脱碳层随着轧制其深度的变化情况。
但是,在实际工作中常常是希望将成品线材表面脱碳层深度控制在一定深度以下,以保证线材冷镦时不发生开裂。
由于线材裂纹深度变化规律和脱碳层是相同的,所以将(1)中的直线关系可以用来计算成品线材对钢坯缺陷深度要求。
推导可得:
日=1.07+日I一0.005928币(2)式中,忙钢坯表面缺陷深度,mm;
日.——成品表面缺陷深度,mm;
中——线材成品直径。
mm。
I上接第5l页)
3.2间接张力控制
间接张力控制同单一速度控制的方式基本控制系统大致相同,不同处是在速度调节器后增加正负转矩限幅功能,实现转矩限幅控制,通常转矩控置在10%左右。
但这种控制方式会在高速运行时或快速的升降速时易造成热张辊前失张的情况。
为了解决这个问题,采用在热张辊前几个炉辊。
根据实际情况把18静一21撑炉辊的转矩限幅设定要比其他炉辊转矩限幅要小些,根据经验数据转矩控制在6%一8%左右。
间接张力控制方式在实际生产中,基本解决了单一速度控制方式对钢带质量的影响问题。
但这种方式因固定了所有辊的转矩。
而因各辊性能不一及炉辊运行时负载摩擦转矩不同,在起停车及升降速时会造成某些炉辊出力不足使钢带表面划伤和轻微打折的情况,炉内张力波动较大,制约了生产线的高速运行和薄带的生产。
鉴于以上原因,采用了下面的第三种方式。
3.3在D啪p特性下的速度控制
这种控制方式和单一速度控制方式l一样为速度控制,但不同处是在速度调节器前引入了Scale
26
一般认为,线材表面脱碳层深度不大于O.030mm时,就可以保证冷镦时不开裂,利用(2)可得表2中的数据。
表2保证冷镦合格时要求的钢坯脱碳层深度mm直径最大深度直径最大深度
101.0107216O.97515
14O.987Ol200.95l14
30O.89216
5结论
(1)经过研究得到了轧制中线材脱碳层深度的变化规律,要保证冷镦不开裂小规格线材允许的钢坯裂纹深度要大一些。
(2)对邢钢目前的线材产品来说,要保证所有产品冷镦性能的稳定,钢坯表面脱碳层深度必须控制在O.9衄以下。
Droop形成负反馈,实现转矩弱化的目的。
此控制系统仍然加入转矩限幅环节,但限幅值设定较大基本在70%左右。
Droop的引入解决了启动转矩不足的问题,同时也降低了加减速时转矩过大的问题,而且根据各辊机械性能的不同转矩也随之变化。
由此可见这种控制方式在炉辊控制方式方面解决了前两种方式的难题,并在实际生产中也得到了验证,解决了我厂因生产薄带时炉内打折、划伤等问题。
4结论
通过对三种连续热镀锌生产线退火炉炉辊控制方式在实际中的应用对比,最终采用了在Droop特性下工作的速度控制方式。
这种控制方式在中冶恒通冷轧技术有限公司5}}镀铝锌硅生产线得到使用。
快速的升降速使炉辊转矩得到很好的控制。
炉内张力平稳;改进了起停车时炉辊转矩较小的难题,使带钢擦伤的情况得到解决。
生产线高速运转时(速度在170In/min),炉辊转矩调节良好,提高了生产线的产能。
万方数据
对线材表面脱碳层深度变化规律的研究
作者:郑永瑞, 李庆彦, 张素萍, 韩伟旗, 李兵, 曹瑞春, Zheng Yongrui, Li Qingyan , Zhang Suping, Han Weiqi, Li Bing, Cao Ruichun
作者单位:邢台钢铁公司,技术中心,河北,邢台,054027
刊名:
河北冶金
英文刊名:HEBEI METALLURGY
年,卷(期):2009(6)
本文链接:/Periodical_hbyj200906008.aspx。