焊接熔深测量方法
焊缝熔深测量方法
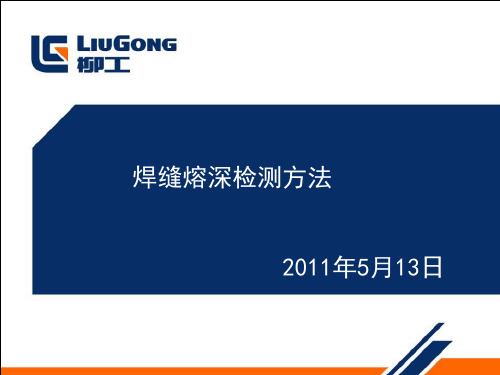
焊标题缝熔深的定义
什么叫焊接熔深:在焊接接头横截面上,母材 或前焊道焊缝熔化的深度。
a
c b 图1
焊接接头包括:焊缝(OA)、熔合区 (AB)、热影响区(BC)三部分。
熔标题深试验前准备
样件要求:1、把截取下来的焊接样 件两端磨平或铣平,表面粗糙度为 6.3um。
此课件下载可自行编辑修改,此课件供参考! 部分内容来源于网络,如有侵权请与我出两条线条(目的是便于测 量熔深的基准线)。
图2
熔标题深样件检测方法
硝酸调配:用浓度为5%的稀硝酸。
操作方法:用调试好的稀硝酸清洗焊
缝端面,使焊缝熔深清晰可见(如图
图2
2),然后用游标卡尺测量熔深大小
(如图3;1、2、3三个尺寸)。
图3
测标题量
1
2
3
结标题束
Thank you
焊接熔深检测方法
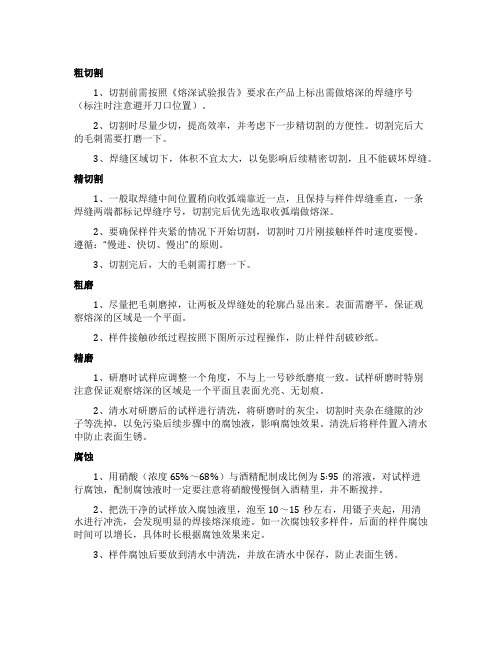
粗切割1、切割前需按照《熔深试验报告》要求在产品上标出需做熔深的焊缝序号(标注时注意避开刀口位置)。
2、切割时尽量少切,提高效率,并考虑下一步精切割的方便性。
切割完后大的毛刺需要打磨一下。
3、焊缝区域切下,体积不宜太大,以免影响后续精密切割,且不能破坏焊缝。
精切割1、一般取焊缝中间位置稍向收弧端靠近一点,且保持与样件焊缝垂直,一条焊缝两端都标记焊缝序号,切割完后优先选取收弧端做熔深。
2、要确保样件夹紧的情况下开始切割,切割时刀片刚接触样件时速度要慢。
遵循:“慢进、快切、慢出”的原则。
3、切割完后,大的毛刺需打磨一下。
粗磨1、尽量把毛刺磨掉,让两板及焊缝处的轮廓凸显出来。
表面需磨平,保证观察熔深的区域是一个平面。
2、样件接触砂纸过程按照下图所示过程操作,防止样件刮破砂纸。
精磨1、研磨时试样应调整一个角度,不与上一号砂纸磨痕一致。
试样研磨时特别注意保证观察熔深的区域是一个平面且表面光亮、无划痕。
2、清水对研磨后的试样进行清洗,将研磨时的灰尘,切割时夹杂在缝隙的沙子等洗掉,以免污染后续步骤中的腐蚀液,影响腐蚀效果。
清洗后将样件置入清水中防止表面生锈。
腐蚀1、用硝酸(浓度65%~68%)与酒精配制成比例为5∶95的溶液,对试样进行腐蚀,配制腐蚀液时一定要注意将硝酸慢慢倒入酒精里,并不断搅拌。
2、把洗干净的试样放入腐蚀液里,泡至10~15秒左右,用镊子夹起,用清水进行冲洗,会发现明显的焊接熔深痕迹。
如一次腐蚀较多样件,后面的样件腐蚀时间可以增长,具体时长根据腐蚀效果来定。
3、样件腐蚀后要放到清水中清洗,并放在清水中保存,防止表面生锈。
4、腐蚀结束后5分钟内在显微镜下观察焊缝熔深,并拍照记录。
时间过长焊缝表面会被氧化,影响熔深的判断。
拍照观察1、用显微镜对腐蚀后的试样进行观察,拍照。
拍照时,从低倍到高倍,调节焦距至图像最清晰状态,试样放平,光线不宜太暗。
所拍照片倍数应与显微镜倍数为一致。
再用测量工具对照片熔深进行测量,测量值保留在照片上进行存档。
焊接熔深测量原理
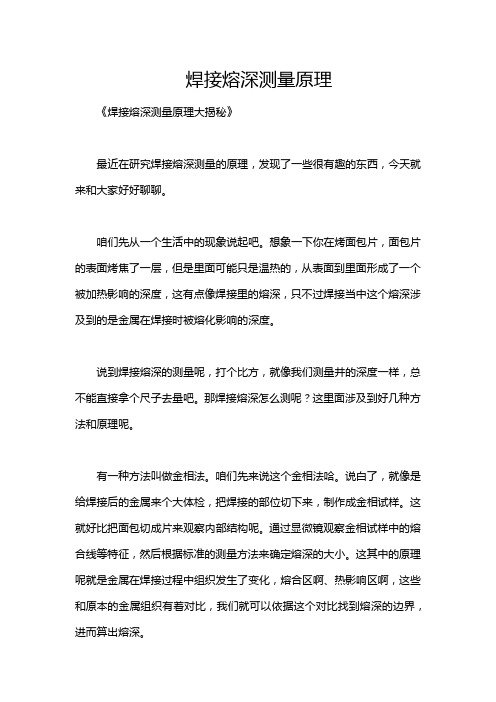
焊接熔深测量原理《焊接熔深测量原理大揭秘》最近在研究焊接熔深测量的原理,发现了一些很有趣的东西,今天就来和大家好好聊聊。
咱们先从一个生活中的现象说起吧。
想象一下你在烤面包片,面包片的表面烤焦了一层,但是里面可能只是温热的,从表面到里面形成了一个被加热影响的深度,这有点像焊接里的熔深,只不过焊接当中这个熔深涉及到的是金属在焊接时被熔化影响的深度。
说到焊接熔深的测量呢,打个比方,就像我们测量井的深度一样,总不能直接拿个尺子去量吧。
那焊接熔深怎么测呢?这里面涉及到好几种方法和原理呢。
有一种方法叫做金相法。
咱们先来说这个金相法哈。
说白了,就像是给焊接后的金属来个大体检,把焊接的部位切下来,制作成金相试样。
这就好比把面包切成片来观察内部结构呢。
通过显微镜观察金相试样中的熔合线等特征,然后根据标准的测量方法来确定熔深的大小。
这其中的原理呢就是金属在焊接过程中组织发生了变化,熔合区啊、热影响区啊,这些和原本的金属组织有着对比,我们就可以依据这个对比找到熔深的边界,进而算出熔深。
还有一种基于超声波的测量方法。
这就像医生用超声波给孕妇检查肚子里的宝宝一样。
超声波可以穿透金属,遇到焊接界面这种不同性质的区域就会反射回来,通过检测超声波往返的时间和一些复杂的换算,就能得到熔深的数值。
个人理解哈,这种方法就像是给焊接部分做了个声波造影,清晰地显示出内部的结构轮廓,从而确定熔深。
不过老实说,我一开始也不明白为什么测量个熔深还要这么复杂多样的方法呢?后来就明白其实不同的焊接环境、焊接对象需要不同的测量准确性和方便性。
比如说,在一些精细的电子元件焊接中,对于熔深的控制和测量就要求非常精确,可能金相法就不合适了,因为它有点像破坏性的检测,切下来看那这个电子元件可能就废了,这种时候超声波法就派上用场了。
说到这里,你可能会问,是不是不同的金属对于测量熔深的原理应用有区别呢?这其实是很棒的一个问题。
不同金属的组织结构、声阻抗等性质是不同的,就像不同的材料做的容器装水的效果不同一样。
如何测量焊接后的熔深
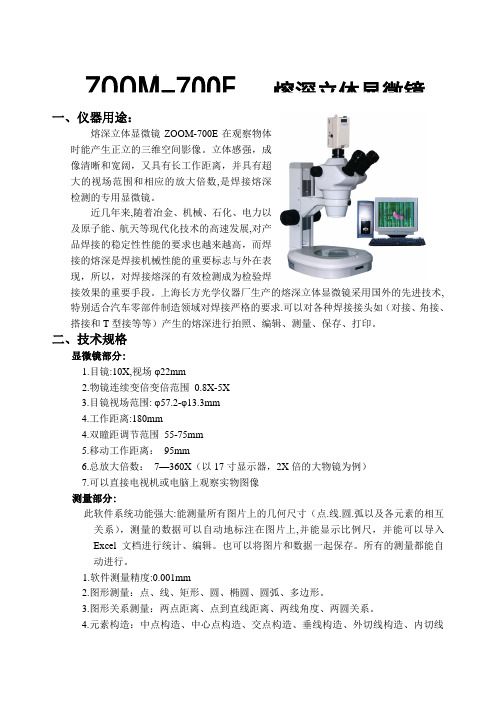
一、仪器用途:Array熔深立体显微镜ZOOM-700E在观察物体时能产生正立的三维空间影像。
立体感强,成像清晰和宽阔,又具有长工作距离,并具有超大的视场范围和相应的放大倍数,是焊接熔深检测的专用显微镜。
近几年来,随着冶金、机械、石化、电力以及原子能、航天等现代化技术的高速发展,对产品焊接的稳定性性能的要求也越来越高,而焊接的熔深是焊接机械性能的重要标志与外在表现,所以,对焊接熔深的有效检测成为检验焊接效果的重要手段。
上海长方光学仪器厂生产的熔深立体显微镜采用国外的先进技术,特别适合汽车零部件制造领域对焊接严格的要求.可以对各种焊接接头如(对接、角接、搭接和T型接等等)产生的熔深进行拍照、编辑、测量、保存、打印。
二、技术规格显微镜部分:1.目镜:10X,视场φ22mm2.物镜连续变倍变倍范围0.8X-5X3.目镜视场范围: φ57.2-φ13.3mm4.工作距离:180mm4.双瞳距调节范围55-75mm5.移动工作距离:95mm6.总放大倍数:7—360X(以17寸显示器,2X倍的大物镜为例)7.可以直接电视机或电脑上观察实物图像测量部分:此软件系统功能强大:能测量所有图片上的几何尺寸(点.线.圆.弧以及各元素的相互关系),测量的数据可以自动地标注在图片上,并能显示比例尺,并能可以导入Excel 文档进行统计、编辑。
也可以将图片和数据一起保存。
所有的测量都能自动进行。
1.软件测量精度:0.001mm2.图形测量:点、线、矩形、圆、椭圆、圆弧、多边形。
3.图形关系测量:两点距离、点到直线距离、两线角度、两圆关系。
4.元素构造:中点构造、中心点构造、交点构造、垂线构造、外切线构造、内切线构造、弦构造。
5.图形预置:点、线、矩形、圆、椭圆、圆弧。
6.图像处理:图像捕捉、图像文件打开、图像文件保存、图像打印三、参考放大倍数电脑型(ZOOM-700E ):7-360倍(以17寸显示器,2X 倍的大物镜为例)四、焊接熔深质量检测制作实例上海长方光学仪器厂开发了针对现有的行业标准(HB5282-1984 结构钢和不锈钢电阻点焊和缝焊质量检验,HB5276-1984铝合金电阻点焊和缝焊质量检验)的焊接质量检测的系统,即焊接熔深测量立体显微镜.主要针对: 航空制造,机械制造,车辆制造,锅炉及压力容器的制造及检验,石油化工,铁路,造船,电厂,电站,设备安装,大型模具,安全检测,质量监督,理化试验室等行业的焊接熔深质量检测.压力容器(空调压缩机)的焊接熔深质量检测实例. 本公司愿与此行业的技术人员共同探讨.以求共同学习进步!第一步: 切割(如图)1.用”切割机”将需要检测的焊接部位从截面切割下来.如下图红色所指第二步: 制样(如图)1. 用”抛光机”将切割下的焊接部位,先在抛光机上用金相砂纸,经过粗磨.细磨,2. 在”抛光机”多次抛光,后用相应的腐蚀液腐蚀(每种金属对应的腐蚀液不一样)3. 将抛光好的焊接部位插入橡皮泥(粉红色)中,并放在一个硬的平板上(如:小块三角板或盖玻片或硬的薄片),放入”平行机(客户选购)”,用力压,使上下两面平行.提高测量精度.抛光机第三步: 观察测量(如图)1.将做好的样品放在熔深立体显微镜2.通过计算机专用软件得到各种需要的数据.并加以分析.。
熔深检测方法
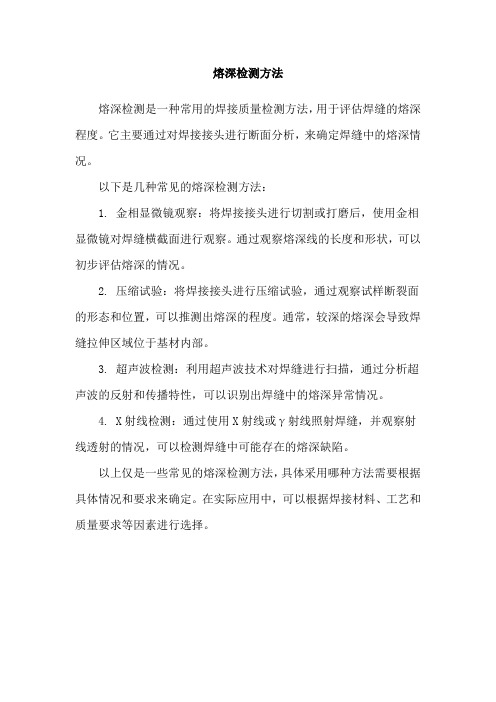
熔深检测方法
熔深检测是一种常用的焊接质量检测方法,用于评估焊缝的熔深程度。
它主要通过对焊接接头进行断面分析,来确定焊缝中的熔深情况。
以下是几种常见的熔深检测方法:
1. 金相显微镜观察:将焊接接头进行切割或打磨后,使用金相显微镜对焊缝横截面进行观察。
通过观察熔深线的长度和形状,可以初步评估熔深的情况。
2. 压缩试验:将焊接接头进行压缩试验,通过观察试样断裂面的形态和位置,可以推测出熔深的程度。
通常,较深的熔深会导致焊缝拉伸区域位于基材内部。
3. 超声波检测:利用超声波技术对焊缝进行扫描,通过分析超声波的反射和传播特性,可以识别出焊缝中的熔深异常情况。
4. X射线检测:通过使用X射线或γ射线照射焊缝,并观察射线透射的情况,可以检测焊缝中可能存在的熔深缺陷。
以上仅是一些常见的熔深检测方法,具体采用哪种方法需要根据具体情况和要求来确定。
在实际应用中,可以根据焊接材料、工艺和质量要求等因素进行选择。
焊缝熔深度测量(ss 0501-2005) .

焊缝熔深度测量(SS 0501-2005)是一项关于焊接质量的工业标准,它规定了焊缝熔深测量的方法和要求。
根据SS 0501-2005,焊缝熔深是指焊接过程中,熔化金属到达母材表面或形成熔池时的深度。
具体测量方法可根据标准规定进行操作:在焊接完成冷却后,用卡尺测量焊缝表面至母材表面的距离。
需要注意的是,在测量过程中,应确保测量面平整、无氧化物等杂质,以保证测量的准确性。
此外,SS 0501-2005还规定了其他一些要求,如测量位置的选择、重复测量、记录和报告等。
这些要求旨在确保测量数据的可靠性和可重复性,从而更好地评估焊缝质量。
总的来说,焊缝熔深度测量是一项重要的质量控制手段,对于保证焊接质量具有重要意义。
执行此项标准有助于提高焊接过程的稳定性和可靠性,从而降低生产成本和减少潜在的焊接缺陷。
激光焊熔深测量方法

激光焊熔深测量方法嘿,咱今儿就来聊聊激光焊熔深测量方法这档子事儿!你知道不,这激光焊啊,那可是个厉害的玩意儿,在好多领域都大显身手呢!可这熔深要是测不准,那不就麻烦啦!就好比你要去一个地方,却不知道走多远才到,心里没底呀!那怎么测量这熔深呢?咱先来说说最简单直接的办法,那就是切片法!就跟切蛋糕似的,把焊接好的物件给切开来,然后直接观察测量熔深。
这办法直观吧,就像你能清楚看到蛋糕里有多少奶油一样。
但这也有缺点呀,这一切开,物件不就毁了嘛,要是贵重的东西,那可就心疼咯!还有一种叫金相法,听着是不是挺高大上的。
它就像是给焊接部位拍个特别的照片,通过观察这个照片来了解熔深情况。
这可比切片法温柔多了,不会把东西给弄坏。
不过呢,这也得技术好才行,不然拍出来的“照片”不清楚,那可就白忙活啦!然后呢,还有超声检测法。
这就好像是用声波去探索焊接内部的秘密。
声波在里面传播,根据反馈回来的信息,就能知道熔深啦。
这多神奇呀,就像有双看不见的眼睛在里面探测一样。
你想想,要是没有这些测量方法,那激光焊不就像没头苍蝇一样乱撞啦?那可不行呀!咱得把这熔深给弄清楚,才能保证焊接的质量呀!这不就跟你走路得知道方向一样重要嘛!每种测量方法都有它的优点和缺点,就像人一样,没有十全十美的呀!切片法直接但毁东西,金相法温柔但得技术好,超声检测法神奇但也不是万能的。
咱得根据具体情况来选择合适的方法,这可不能马虎!要是选错了方法,那后果可不堪设想呀!就好比你要去一个地方,选错了路,那不是越走越远嘛!所以呀,可得好好琢磨琢磨,选个最合适的。
咱再回过头来想想,这激光焊熔深测量方法多重要呀!没有它们,那些高科技产品、那些大工程怎么能顺利完成呢?这可都是幕后的大功臣呀!所以说呀,咱可别小瞧了这些测量方法,它们可是保证质量的关键呢!以后再看到激光焊,你就会想到这些测量方法,就知道它们有多重要啦!你说是不是这个理儿呢?。
熔深检测方法
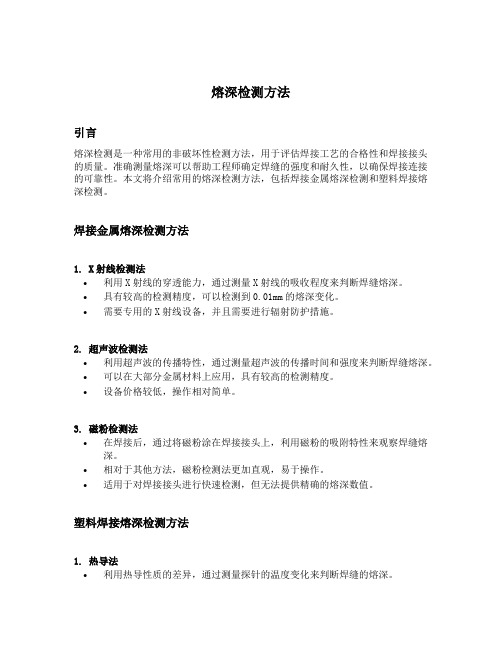
熔深检测方法引言熔深检测是一种常用的非破坏性检测方法,用于评估焊接工艺的合格性和焊接接头的质量。
准确测量熔深可以帮助工程师确定焊缝的强度和耐久性,以确保焊接连接的可靠性。
本文将介绍常用的熔深检测方法,包括焊接金属熔深检测和塑料焊接熔深检测。
焊接金属熔深检测方法1. X射线检测法•利用X射线的穿透能力,通过测量X射线的吸收程度来判断焊缝熔深。
•具有较高的检测精度,可以检测到0.01mm的熔深变化。
•需要专用的X射线设备,并且需要进行辐射防护措施。
2. 超声波检测法•利用超声波的传播特性,通过测量超声波的传播时间和强度来判断焊缝熔深。
•可以在大部分金属材料上应用,具有较高的检测精度。
•设备价格较低,操作相对简单。
3. 磁粉检测法•在焊接后,通过将磁粉涂在焊接接头上,利用磁粉的吸附特性来观察焊缝熔深。
•相对于其他方法,磁粉检测法更加直观,易于操作。
•适用于对焊接接头进行快速检测,但无法提供精确的熔深数值。
塑料焊接熔深检测方法1. 热导法•利用热导性质的差异,通过测量探针的温度变化来判断焊缝的熔深。
•可以在塑料材料中应用,具有较高的检测精度。
•需要专用的温度测量设备,并且需要对材料进行加热。
2. 落体法•将标准密度的小球放置在塑料焊缝上,并测量小球的沉入深度来判断熔深。
•操作简单,不需要特殊设备。
•适用于对塑料焊接接头进行初步的质量评估。
3. 激光检测法•利用激光的穿透能力,通过测量激光的反射信号来判断塑料焊缝的熔深。
•可以对焊接贴合度进行快速检测,具有较高的检测精度。
•需要专用的激光设备,并且需要进行激光辐射防护。
总结熔深检测方法是评估焊接工艺质量的重要手段,对于确保焊接接头的可靠性至关重要。
本文介绍了常用的焊接金属熔深检测方法和塑料焊接熔深检测方法。
对于金属焊接,X射线检测法、超声波检测法和磁粉检测法是常用的方法。
对于塑料焊接,热导法、落体法和激光检测法是常用的方法。
不同的方法在检测精度、设备要求和操作难度上有所差异,工程师可以根据具体情况选择适合的方法来进行熔深检测。
熔深检测作业指导书
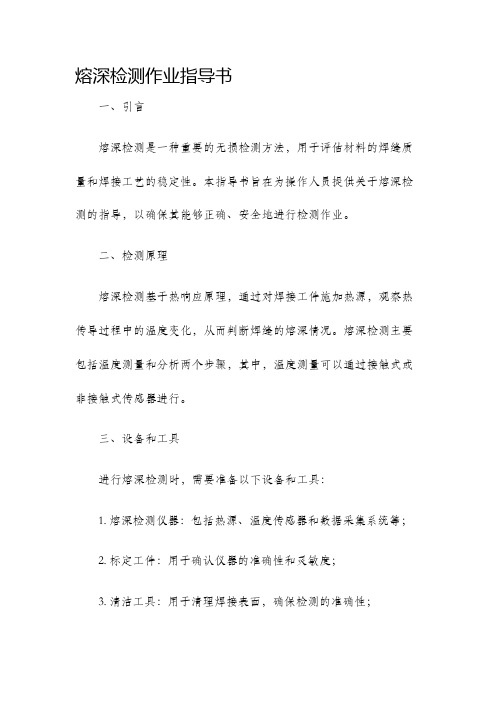
熔深检测作业指导书一、引言熔深检测是一种重要的无损检测方法,用于评估材料的焊缝质量和焊接工艺的稳定性。
本指导书旨在为操作人员提供关于熔深检测的指导,以确保其能够正确、安全地进行检测作业。
二、检测原理熔深检测基于热响应原理,通过对焊接工件施加热源,观察热传导过程中的温度变化,从而判断焊缝的熔深情况。
熔深检测主要包括温度测量和分析两个步骤,其中,温度测量可以通过接触式或非接触式传感器进行。
三、设备和工具进行熔深检测时,需要准备以下设备和工具:1. 熔深检测仪器:包括热源、温度传感器和数据采集系统等;2. 标定工件:用于确认仪器的准确性和灵敏度;3. 清洁工具:用于清理焊接表面,确保检测的准确性;4. 个人防护装备:包括防护手套、护目镜等,确保操作安全。
四、检测步骤1. 准备工作:清理焊接表面,确保无杂质和脏污;2. 设备连接:将温度传感器连接至数据采集系统,并确认仪器的工作状态;3. 标定检测仪器:使用标定工件对仪器进行校准,确保其准确性;4. 设定检测参数:根据焊接材料的类型和要求,设置热源功率、检测时间等参数;5. 进行检测:点亮热源,开始进行熔深检测;6. 数据采集与分析:通过数据采集系统记录热传导过程中的温度变化,并进行数据分析;7. 检测结果评估:根据热传导曲线、温度变化等数据,评估焊缝的熔深情况;8. 结果记录与报告:将检测结果记录在作业报告中,并编写相关报告。
五、安全注意事项1. 在使用热源时,避免直接触摸以防烫伤;2. 在操作过程中要佩戴个人防护装备,确保操作人员的人身安全;3. 确保工作场所通风良好,以避免有害气体积聚;4. 操作仪器时应严格按照操作手册和安全规范进行,以避免意外事故的发生;5. 在操作结束后,及时关闭热源并清理现场。
六、常见问题与解决方法1. 仪器无法启动:检查电源和连接是否正常,确保设备已连接至电源;2. 仪器测量结果不准确:检查温度传感器是否正确连接,尝试重新校准仪器;3. 温度传感器损坏:检查温度传感器的状况,如有损坏应及时更换;4. 检测结果不一致:检查操作步骤是否正确,是否存在干扰因素。
电阻焊熔深
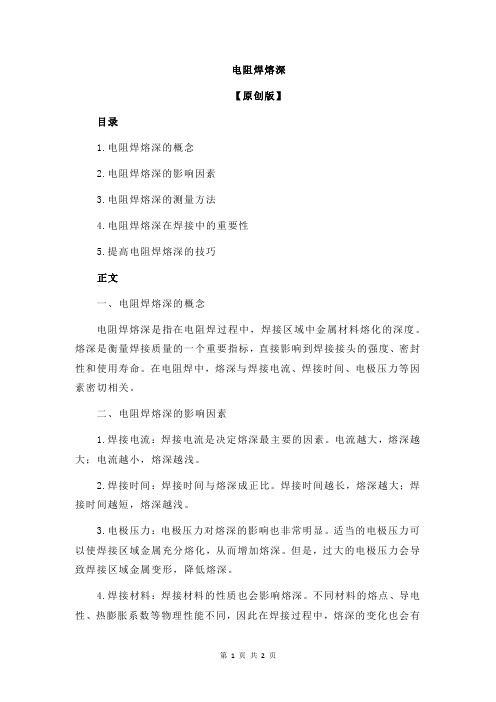
电阻焊熔深【原创版】目录1.电阻焊熔深的概念2.电阻焊熔深的影响因素3.电阻焊熔深的测量方法4.电阻焊熔深在焊接中的重要性5.提高电阻焊熔深的技巧正文一、电阻焊熔深的概念电阻焊熔深是指在电阻焊过程中,焊接区域中金属材料熔化的深度。
熔深是衡量焊接质量的一个重要指标,直接影响到焊接接头的强度、密封性和使用寿命。
在电阻焊中,熔深与焊接电流、焊接时间、电极压力等因素密切相关。
二、电阻焊熔深的影响因素1.焊接电流:焊接电流是决定熔深最主要的因素。
电流越大,熔深越大;电流越小,熔深越浅。
2.焊接时间:焊接时间与熔深成正比。
焊接时间越长,熔深越大;焊接时间越短,熔深越浅。
3.电极压力:电极压力对熔深的影响也非常明显。
适当的电极压力可以使焊接区域金属充分熔化,从而增加熔深。
但是,过大的电极压力会导致焊接区域金属变形,降低熔深。
4.焊接材料:焊接材料的性质也会影响熔深。
不同材料的熔点、导电性、热膨胀系数等物理性能不同,因此在焊接过程中,熔深的变化也会有所不同。
5.焊接方法:不同的焊接方法对熔深的影响也不同。
例如,点焊和缝焊的熔深就有很大差别。
三、电阻焊熔深的测量方法电阻焊熔深的测量方法主要有以下几种:1.磁性法:利用磁性探头测量焊接区域的磁性,从而推算出熔深的大小。
2.电容法:通过测量焊接区域的电容变化,间接测量熔深的大小。
3.X 射线法:利用 X 射线穿透焊接区域,根据射线吸收程度判断熔深。
4.金属贴片法:将标准厚度的金属贴片放置在焊接区域,通过比较贴片厚度与熔深关系,判断熔深大小。
四、电阻焊熔深在焊接中的重要性电阻焊熔深是衡量焊接质量的重要指标。
熔深不足会导致焊接接头强度不足、密封性差,容易发生漏气、漏水等问题;熔深过大则容易导致焊接变形、脆化等问题。
因此,在焊接过程中,合理控制熔深是非常重要的。
五、提高电阻焊熔深的技巧1.选择合适的焊接电流和时间:根据焊接材料的性质和厚度,选择合适的焊接电流和时间,以保证焊接区域的金属充分熔化。
氩弧焊熔深
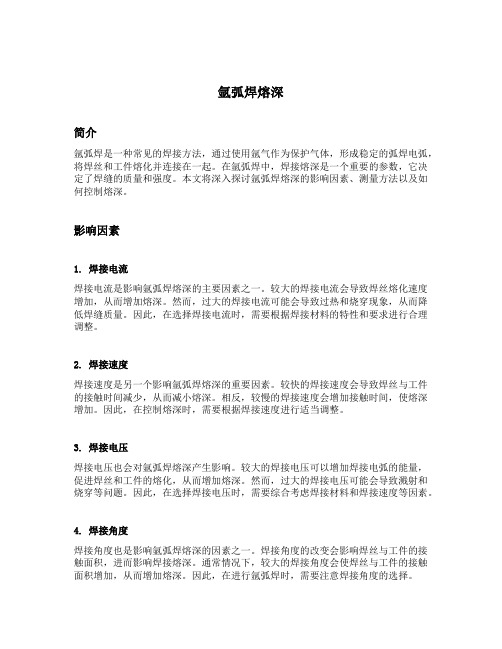
氩弧焊熔深简介氩弧焊是一种常见的焊接方法,通过使用氩气作为保护气体,形成稳定的弧焊电弧,将焊丝和工件熔化并连接在一起。
在氩弧焊中,焊接熔深是一个重要的参数,它决定了焊缝的质量和强度。
本文将深入探讨氩弧焊熔深的影响因素、测量方法以及如何控制熔深。
影响因素1. 焊接电流焊接电流是影响氩弧焊熔深的主要因素之一。
较大的焊接电流会导致焊丝熔化速度增加,从而增加熔深。
然而,过大的焊接电流可能会导致过热和烧穿现象,从而降低焊缝质量。
因此,在选择焊接电流时,需要根据焊接材料的特性和要求进行合理调整。
2. 焊接速度焊接速度是另一个影响氩弧焊熔深的重要因素。
较快的焊接速度会导致焊丝与工件的接触时间减少,从而减小熔深。
相反,较慢的焊接速度会增加接触时间,使熔深增加。
因此,在控制熔深时,需要根据焊接速度进行适当调整。
3. 焊接电压焊接电压也会对氩弧焊熔深产生影响。
较大的焊接电压可以增加焊接电弧的能量,促进焊丝和工件的熔化,从而增加熔深。
然而,过大的焊接电压可能会导致溅射和烧穿等问题。
因此,在选择焊接电压时,需要综合考虑焊接材料和焊接速度等因素。
4. 焊接角度焊接角度也是影响氩弧焊熔深的因素之一。
焊接角度的改变会影响焊丝与工件的接触面积,进而影响焊接熔深。
通常情况下,较大的焊接角度会使焊丝与工件的接触面积增加,从而增加熔深。
因此,在进行氩弧焊时,需要注意焊接角度的选择。
测量方法1. 切割测量法切割测量法是一种常用的测量氩弧焊熔深的方法。
该方法通过切割焊缝,然后使用显微镜或显微硬度计等工具测量焊缝的深度。
切割测量法可以获得较为准确的焊缝熔深数据,但对焊接工艺和设备要求较高。
2. 非接触测量法非接触测量法是一种无需破坏焊缝的测量方法。
该方法使用激光或光学传感器等设备对焊缝进行扫描和测量,从而得到焊缝的熔深数据。
非接触测量法操作简便,速度快,但对设备和环境的要求较高。
3. 热电偶测量法热电偶测量法是一种通过焊接过程中测量焊丝表面温度来间接推断熔深的方法。
DB13_T2770-2018焊接熔深检测方法
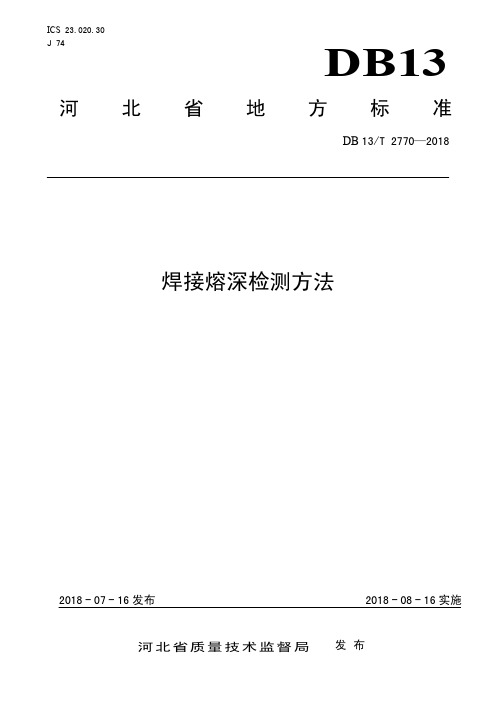
ICS23.020.30J 74 DB13 河北省地方标准DB 13/T 2770—2018焊接熔深检测方法2018-07-16发布2018-08-16实施前言本标准按照GB/T 1.1-2009给出的规则起草。
本标准由保定市质量技术监督局提出。
本标准起草单位:长城汽车股份有限公司、保定市计量测试所。
本标准主要起草人:齐元波、高红、王志苗、梁辉、张伟、曹立辉、姚焕朝、陈宇、张云飞。
焊接熔深检测方法1 范围本标准规定了焊接熔深的术语和定义、检测内容及表示符号、试样准备、检测方法、试验报告。
本标准适用于汽车钢铁结构件熔化焊接后焊接熔深检测。
2 规范性引用文件下列文件对于本文件的应用是必不可少的。
凡是注日期的引用文件,仅注日期的版本适用于本文件。
凡是不注日期的引用文件,其最新版本(包括所有的修改单)适用于本文件。
GB/T 3375 焊接术语GB/T 13298-2015 金属显微组织检验方法3 术语和定义GB/T 3375中界定的及下列术语和定义适用于本文件。
3.1熔化起始线 starting line of melting焊接接头横截面上,母材熔化前的轮廓线,如图1所示。
1—母材t1的熔化起始线; 2—母材t2的熔化起始线图1 熔化起始线4 检测内容及表示符号本标准根据熔化焊接后,焊接接头处焊缝金相组织与母材及热影响区金相组织不同,用特定的溶剂浸蚀后,焊缝与热影响区会出现明显的熔化线。
经体视显微镜放大后,测量焊接熔深、焊缝厚度。
焊接熔深检测内容及表示符号见表1。
DB13/T 2770—2018表1 检测内容及表示符号5 试样准备5.1 试样选取为保证试验的有效性,选取的试样应客观全面的代表被检测的材料,应包含焊缝、热影响区和母材。
5.2 试样截取试样可用砂轮切割、电火花线切割、火焰切割、机加工(车、铣、刨、磨)、手锯以及剪切等方法截取,同时应避免截取方法对组织的影响(如变形、过热等)。
在后续制样过程中,可用合适的方法去除截取操作引起的影响,保留正常组织。
焊接熔深标准及测量方法

焊接熔深标准及测量方法
焊接熔深那可是超级重要的!咱先说说啥是焊接熔深标准吧。
就好比盖房子得有个结实的地基,焊接也得有个标准的熔深,不然那能行吗?不同的焊接工艺和材料,熔深标准可不一样哦!那怎么测量焊接熔深呢?嘿,这就有讲究了。
可以用金相分析法呀,把焊接件切开,磨平,然后在显微镜下观察,就像医生给病人做检查一样,看得清清楚楚。
这过程可得小心,万一弄不好,不就白忙活了?还有超声波检测法,就像给焊接件做个“B 超”,能探测到内部的情况。
那在测量的时候有啥注意事项呢?首先,操作得规范,不然得出的结果能准吗?其次,设备得靠谱呀,要是设备不好使,那不是瞎耽误工夫?
焊接过程中的安全性和稳定性那也是重中之重啊!要是不安全,那不得吓死人?就像开车不系安全带,多危险呀!焊接的时候得注意防火、防爆,这可不是闹着玩的。
稳定性也很关键,要是不稳定,焊接出来的东西能行吗?就像走钢丝的人摇摇晃晃,那不得掉下来?
焊接熔深的应用场景那可多了去了。
汽车制造、航空航天、建筑工程等等,到处都有焊接的身影。
为啥要用焊接熔深标准呢?因为这样能保证焊接质量呀!就像做饭得掌握好火候,不然能好吃吗?焊接熔深标准的优势也很明显,能提高焊接的强度和可靠性,减少出现问题的概率。
这不是好事吗?
给你举个实际案例吧。
有个汽车制造企业,在生产过程中严格按照焊接熔深标准进行操作,结果生产出来的汽车质量那叫一个棒!不仅结实耐用,而且安全性高。
这就是焊接熔深标准的实际应用效果呀!
我的观点结论就是,焊接熔深标准和测量方法非常重要,大家一定要重视起来,这样才能保证焊接质量,让我们的生活更加安全可靠。
焊接熔深显微镜检测

焊接熔深显微镜检测焊缝熔深是指在焊接接头横截面上,母材或前道焊缝熔化的深度。
焊缝熔深显微镜适用于测量金属焊接熔深。
检验方法根据对产品是否造成损伤可分为破坏性检验和无损探伤两类。
焊接熔深检测效果图熔深显微镜软件中的焊接熔深(1)焊缝熔深显微镜外观检验焊接接头的外观检验主要是发现焊缝表面的缺陷和尺寸上的偏差。
(2)焊缝熔深显微镜致密性检验贮存液体或气体的焊接容器,其焊缝的不致密缺陷,如贯穿性的裂纹、气孔、夹渣、未焊透和疏松组织等,可用致密性试验来发现。
测量焊接溶深的显微镜致密性检验方法有:煤油试验、载水试验、水冲试验等。
苏州南光电子科技有限公司的熔深检测显微镜操作的一般步骤:一、取样(切割机):采用金相试样切割机切割下包含待检测部位的试样,熔深检测显微镜待检试样二、镶嵌(金相试样镶嵌机或者冷镶嵌):对于微小试样,超薄试样等,为了保护焊接区域的稳定和可靠性,避免制样过程中造成的变形和冲击,通过镶嵌固化的方式,获得标准规格的尺寸,如Φ30x15mm,并使得后续的手持,或者自动磨抛称为可能。
镶嵌分为热镶嵌和冷镶嵌的方式:1、热镶嵌:利用金相试样镶嵌机加热加压的方式,使得试样在树脂中固化,时间短无污染,固化强度高;2、冷镶嵌:镶嵌粉和固化剂共同融合在模具或者夹具中,凝固后获得固化的试样,特别适合不能加热加压的材料,或者是需要控制方向,分析特定部位的试样。
三、研磨、预磨、抛光等:抛光机及磨抛机等:研磨:表面质量特别差的,采用砂轮机,砂轮片,砂轮盘等进行粗处理,预磨:采用粗细不同目数砂纸,分别进行粗磨、精磨等处理,抛光:采用抛光织物(带胶抛光丝绒,精抛绒等)+金刚石喷雾抛光剂等进行粗抛和精抛工作,四、腐蚀:为了焊接区域各部分有明显的显示,多数熔深要进行腐蚀处理,从而使得熔深的部位凸显出来;五、焊接熔深显微镜的选择,观察和分析:熔深检测显微镜检测效果图根据熔深区域的形貌尺寸,选择合适倍率的显微镜,进行观察,图像输出,熔深分析等,并实现熔深分析报告的输出;。
焊接熔深测量方法

a.避开起弧、收弧位置 焊缝长度>150mm时,建议熔深测量切2段,位置分别在:起弧后的1/3处和收弧前的1/3处。
b.焊缝1/3处切断
C.焊疤长度<20mm时,在焊疤中间位置切断
10/21/2019
Author: Add Name Disclosure or duplication without consent is prohibited
Author: Add Name Disclosure or duplication without consent is prohibited
7
弧焊熔深测量方法
T型接头 搭接接头(t1≤1.5mm) 搭接接头(t1>1.5mm)
10/21/2019
熔深要求
0.1 * t1 ≤ Pd ≤ t2 a ≥ 0.7 * tmin z ≥ tmin h ≤ 0.2 * t1 g < 0.5 * tmin ≤ 1mm
5
焊缝金相测量顺序指导书
目的:
指导试验操作人员按照顺序测量焊缝金相数据,防止出现测量数据的遗漏。
搭接焊缝测量顺序:
T型焊缝测量顺序:
10/21/2019
Author: Add Name Disclosure or duplication without consent is prohibited
6
使用软件内的测量工具,参照《焊缝金相测量顺序指导书》的要求 对焊缝断面图中相关位置进行逐步测量。 焊缝断面金相数据测量完成后,点检软件下方的“采集图像”按钮, 选择“另存为”功能。
在子菜单上部位置选择图片保存目录,图片保存规则“JPG”格式 进行保存。
10/21/2019
Author: Add Name Disclosure or duplication without consent is prohibited
激光焊接熔深检测原理解析
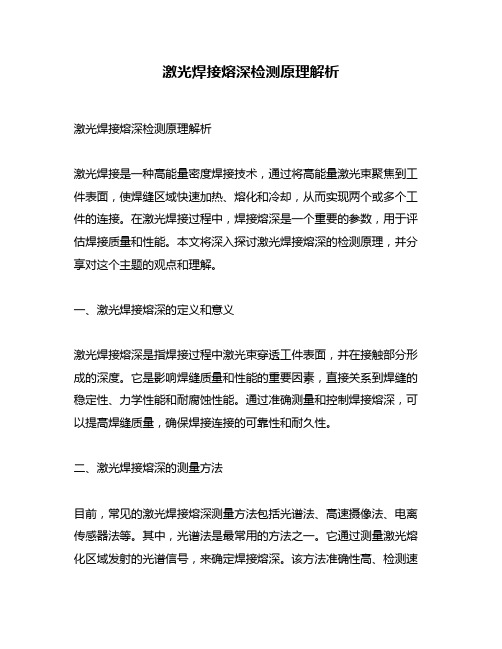
激光焊接熔深检测原理解析激光焊接熔深检测原理解析激光焊接是一种高能量密度焊接技术,通过将高能量激光束聚焦到工件表面,使焊缝区域快速加热、熔化和冷却,从而实现两个或多个工件的连接。
在激光焊接过程中,焊接熔深是一个重要的参数,用于评估焊接质量和性能。
本文将深入探讨激光焊接熔深的检测原理,并分享对这个主题的观点和理解。
一、激光焊接熔深的定义和意义激光焊接熔深是指焊接过程中激光束穿透工件表面,并在接触部分形成的深度。
它是影响焊缝质量和性能的重要因素,直接关系到焊缝的稳定性、力学性能和耐腐蚀性能。
通过准确测量和控制焊接熔深,可以提高焊缝质量,确保焊接连接的可靠性和耐久性。
二、激光焊接熔深的测量方法目前,常见的激光焊接熔深测量方法包括光谱法、高速摄像法、电离传感器法等。
其中,光谱法是最常用的方法之一。
它通过测量激光熔化区域发射的光谱信号,来确定焊接熔深。
该方法准确性高、检测速度快,适用于复杂形状和大尺寸工件的熔深测量。
三、激光焊接熔深的影响因素激光焊接熔深受多种因素的影响,包括激光功率、焊接速度、焊缝几何形状、工件材料等。
其中,激光功率和焊接速度是两个主要影响因素。
增加激光功率和降低焊接速度,会使焊接熔深增大;反之,会使焊接熔深减小。
此外,焊缝几何形状和工件材料也对焊接熔深产生影响,需根据实际情况进行综合考虑和调整。
四、激光焊接熔深控制的重要性激光焊接熔深的控制是确保焊接连接质量的重要环节。
过大的焊接熔深会导致热影响区变大,从而可能引入应力集中和裂纹产生的风险;而过小的焊接熔深则会导致焊缝连接强度降低。
因此,通过合理调整焊接参数以达到预设的熔深范围,是实现良好焊接连接的关键。
总结回顾:激光焊接熔深是评估焊接质量和性能的重要参数,通过准确测量和控制焊接熔深,可以提高焊缝质量和焊接连接的可靠性。
常用的激光焊接熔深测量方法包括光谱法、高速摄像法和电离传感器法等,其中光谱法是最常用的方法。
激光焊接熔深受多种因素的影响,包括激光功率、焊接速度、焊缝几何形状、工件材料等。
焊接熔深测量方法

焊接熔深测量方法
1. 药水配制
1.1 硝酸5毫升(分析纯)+自来水或者是纯净水100毫升
1.2 淆硝酸毫升+自来水或者是纯净水100毫升。
2. 准备原材料开始焊接:
2.1 随钢板的厚度决定焊丝直径大小,钢板
3.0mm以上的用焊丝直径 1.2-2.0mm,钢板 3.0mm以下的用焊丝直径1.0-0.8mm(注意:针对焊接样品要做好一对一的标识,并记录好相应的焊接工艺参数,如电流、电压、气压、电阻等)
3. 样品切开方法:
3.1 注意让开焊接起伏点和收伏点,找到焊点不怎么饱满的地方,竖切或斜切,切开后表面不能有粗糙不平整,如有粗糙不平整,表面需要打磨抛光,表面粗糙度为Ra6.3等冷却。
4. 准备开始测试焊接熔深:
4.1 当样品放入容器中浸泡2-8分钟,(搅拌或不搅拌自定义)用肉眼判断切开面焊点是否清晰,如清晰可见就马上用气枪吹干,若不清晰就浸泡到清晰后在用气枪吹干,这样就不会生锈有利于保存。
5. 开始测量方法:
5.1 测量工具、直尺、测量焊高、熔深(注:熔深分别有两种1.名义熔深 2 实际熔深)
5.2测量
5.2 目测观察是否有未焊透、焊缝装配不良、咬边不良等。
- 1、下载文档前请自行甄别文档内容的完整性,平台不提供额外的编辑、内容补充、找答案等附加服务。
- 2、"仅部分预览"的文档,不可在线预览部分如存在完整性等问题,可反馈申请退款(可完整预览的文档不适用该条件!)。
- 3、如文档侵犯您的权益,请联系客服反馈,我们会尽快为您处理(人工客服工作时间:9:00-18:30)。
6/26/2020
.
5
焊缝金相测量顺序指导书
目的:
指导试验操作人员按照顺序测量焊缝金相数据,防止出现测量数据的遗漏。
搭接焊缝测量顺序:
T型焊缝测量顺序:
6/26/2020
.
6
电阻焊熔深测量方法
二层点焊
三层点焊
凸焊
熔深要求 0.4*t1 ≤ p1 ≤ 0.8*t1 0.4*t2 ≤ p2 ≤ 0.8*t2
磨抛注意事项
a.操作时佩戴好防护眼镜,以免飞溅伤人 b.操作时手与砂纸保持适当距离,以免磨伤手指
6/26/2020
.
4
熔接断面测量
先开启体视镜光源开关,通过亮度调整光源亮度。 再开启电脑主机以及显示器,等待设备启动。
点击电脑桌面“LAS V4.12”图标运行程序
点击软件上的“采集”图标,并将腐蚀好的试样放在固定的橡皮泥 上,将固定好的试样摆在显微镜的物镜下方。
b.焊缝1/3处切断
C.焊疤长度<20mm时,在焊疤中间位置切断
6/26/2020
.
3
断面抛光打磨
将金相砂纸摆放在抛磨盘上,并压牢(根据需要选择砂纸的粗细逐 一进行) 点击洒水器开关,开启冷却水 调整抛磨机转速,最快转速700RPM,建议转度300~500 Rpm之间
调整完成后,点击旋转启动键,抛磨盘开始转动。(根据操作习惯设 置逆时针或顺时针转动) 单手持试样,需要把抛磨面轻轻放在抛磨砂纸上,一定紧握试样, 试验接触砂纸后,可增大压力,增大试样与砂纸之间的摩擦力。 在抛磨过程中,可在砂纸为半圆来回摩擦,在抛磨一段时间后,试 样未到达平整要求,可改变力度和方向
其他要求
s>1.5mm时需要通过相关车身和制造工程部 门一致的认可
内部孔洞的数量不能超过2个,最大偏差应小 于tmin的30%
镀锌钢板间隙: 无填充材料时: g=0.25*tmin≤0.3mm 有填充材料时: g=0.5*tmin≤0.5mm
非镀锌钢板间隙: g≤0.1mm
.
9
调整焦距确保图片清晰,并进行测量焊缝厚度、焊脚尺寸、熔深等焊缝 熔接数据,保存好测量后的图片和数据。
数据整理,完成试验报告;并把试验结果通知相关QE。如不合格项需要调试 后再次切片确认,直到合格为止。注意要做好原始数据记录
.
2
焊缝横切断面
将试样放置在夹具中央,根据切割片位置调整待切片位置,然后将夹具 夹紧推杆推到位。 将切割机外罩关闭,确认侧面的安全防护传感器完全闭合。
按下绿色的开机按钮,等待3~5S,待电机运转稳定后才能进行下一步操 作
电机运转稳定后,右手把持进刀手柄,慢慢进刀开始切割
切割完成后,按下红色“关机按钮”,等待2~5S后,打开防护罩,取出 切割好的试样。
切片注意事项
a.避开起弧、收弧位置 焊缝长度>150mm时,建议熔深测量切2段,位置分别在:起弧后的1/3处和收弧前的1/3处。
用等离子切割机切割每条焊缝,把切割好的焊缝试样按编号顺序放入 容器内。
把焊缝试样在物理切割机上进行切断,取有效的焊缝横截面流下一工序。注 意选择试样焊缝有效位置切割
把需检测的焊缝断面在抛光打磨机上进行研磨平整光滑。
用排笔把腐蚀液轻轻擦拭在打磨后的焊缝断面上,经过5~10秒腐蚀好的 焊缝断面放在体视镜下放大观察
.
其他要求 单个气孔范围: t1≤1.5mm时,d≤0.4*tmin; t1>1.5mm时,d≤1.5mm 熔透凸出≤1.1*t1
8
激光焊熔深测量方法
穿透焊缝
6/26/2020
熔深要求
p ≥ 0.3 * t2 s ≥ 0.9 * tmin h1 ≤ 0.5 * ttop h2 ≤ 0.3 * t2 + 0.2mm
微调固定好的试样在物镜下的位置,直至软件内显示出需要观测的 试样位置为止。
微调体视显微镜的焦距以及光源亮度,直到软件显示的图片清晰反 应焊缝断面后点击“采集图像”。调焦时注意不要使物镜碰到试样, 以免划伤物镜
使用软件内的测量工具,参照《焊缝金相测量顺序指导书》的要求 对焊缝断面图中相关位置进行逐步测量。 焊缝断面金相数据测量完成后,点检软件下方的“采集图像”按钮, 选择“另存为”功能。
熔深要求
0.1 * t1 ≤ Pd ≤ t2 a ≥ 0.7 * tmin z ≥ tmin h ≤ 0.2 * t1 g < 0.5 * tmin ≤ 1mm R ≤ 70°
熔深要求
0.1 * t1 ≤ Pd ≤ t2 a ≥ 0.7 * tmin z ≥ tmin h ≤ 0.2 * t1 g < 0.5 * tmin ≤ 1mm
焊接熔深 测量方法
June 26, 2020
金相制样流程
试验品取样 焊缝编号 焊缝拆解
焊缝横切断面 断面抛光打磨
试样浸蚀 熔接断面测量 数据整理反馈并保存
6/26/2020
生产现场根据频次抽取试验零件,并送往金相试验室,确认检查零件外观合 格
根据零件图纸或样件对应焊缝编号,对零件每条焊缝标记编求 0.3*t1 ≤ p1 ≤ 0.8*t1 p2 = t2 0.3*t3 ≤ p3 ≤ 0.8*t3
熔深要求 0.3*hp≤p≤0.5*hp
6/26/2020
.
7
弧焊熔深测量方法
T型接头 搭接接头(t1≤1.5mm) 搭接接头(t1>1.5mm)
6/26/2020
熔深要求
0.1 * t1 ≤ Pd ≤ t2 a ≥ 0.7 * tmin z ≥ tmin h ≤ 0.2 * t1 g < 0.5 * tmin ≤ 1mm