典型事故二十一:中石油兰州石化“1.7”罐区爆炸事故
20100107中石油兰州石化发生重大爆炸事故
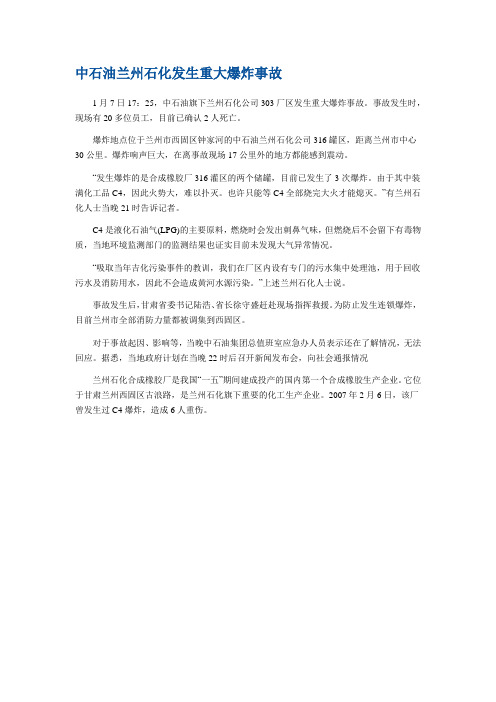
中石油兰州石化发生重大爆炸事故
1月7日17:25,中石油旗下兰州石化公司303厂区发生重大爆炸事故。
事故发生时,现场有20多位员工,目前已确认2人死亡。
爆炸地点位于兰州市西固区钟家河的中石油兰州石化公司316罐区,距离兰州市中心30公里。
爆炸响声巨大,在离事故现场17公里外的地方都能感到震动。
“发生爆炸的是合成橡胶厂316灌区的两个储罐,目前已发生了3次爆炸。
由于其中装满化工品C4,因此火势大,难以扑灭。
也许只能等C4全部烧完大火才能熄灭。
”有兰州石化人士当晚21时告诉记者。
C4是液化石油气(LPG)的主要原料,燃烧时会发出刺鼻气味,但燃烧后不会留下有毒物质,当地环境监测部门的监测结果也证实目前未发现大气异常情况。
“吸取当年吉化污染事件的教训,我们在厂区内设有专门的污水集中处理池,用于回收污水及消防用水,因此不会造成黄河水源污染。
”上述兰州石化人士说。
事故发生后,甘肃省委书记陆浩、省长徐守盛赶赴现场指挥救援。
为防止发生连锁爆炸,目前兰州市全部消防力量都被调集到西固区。
对于事故起因、影响等,当晚中石油集团总值班室应急办人员表示还在了解情况,无法回应。
据悉,当地政府计划在当晚22时后召开新闻发布会,向社会通报情况
兰州石化合成橡胶厂是我国“一五”期间建成投产的国内第一个合成橡胶生产企业。
它位于甘肃兰州西固区古浪路,是兰州石化旗下重要的化工生产企业。
2007年2月6日,该厂曾发生过C4爆炸,造成6人重伤。
兰州石化公司“2010.1.7”火灾爆炸事故
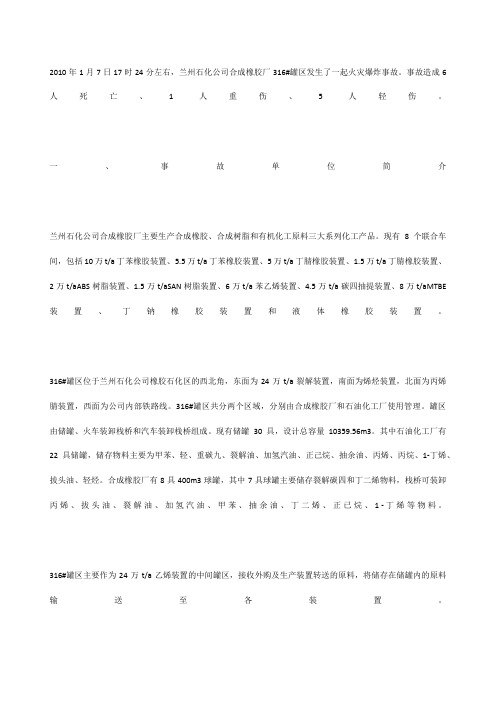
2010年1月7日17时24分左右,兰州石化公司合成橡胶厂316#罐区发生了一起火灾爆炸事故。
事故造成6人死亡、1人重伤、5人轻伤。
一、事故单位简介兰州石化公司合成橡胶厂主要生产合成橡胶、合成树脂和有机化工原料三大系列化工产品。
现有8个联合车间,包括10万t/a丁苯橡胶装置、5.5万t/a丁苯橡胶装置、5万t/a丁腈橡胶装置、1.5万t/a丁腈橡胶装置、2万t/aABS树脂装置、1.5万t/aSAN树脂装置、6万t/a苯乙烯装置、4.5万t/a碳四抽提装置、8万t/aMTBE 装置、丁钠橡胶装置和液体橡胶装置。
316#罐区位于兰州石化公司橡胶石化区的西北角,东面为24万t/a裂解装置,南面为烯烃装置,北面为丙烯腈装置,西面为公司内部铁路线。
316#罐区共分两个区域,分别由合成橡胶厂和石油化工厂使用管理。
罐区由储罐、火车装卸栈桥和汽车装卸栈桥组成。
现有储罐30具,设计总容量10359.56m3。
其中石油化工厂有22具储罐,储存物料主要为甲苯、轻、重碳九、裂解油、加氢汽油、正己烷、抽余油、丙烯、丙烷、1-丁烯、拔头油、轻烃。
合成橡胶厂有8具400m3球罐,其中7具球罐主要储存裂解碳四和丁二烯物料,栈桥可装卸丙烯、拔头油、裂解油、加氢汽油、甲苯、抽余油、丁二烯、正已烷、1-丁烯等物料。
316#罐区主要作为24万t/a乙烯装置的中间罐区,接收外购及生产装置转送的原料,将储存在储罐内的原料输送至各装置。
二、事故经过2010年1月6日零点班开始,合成橡胶厂316岗位开启P201/B泵外送R202(裂解碳四储罐)物料,同时接受来自石油化工厂烯烃装置产出的裂解碳四。
此时,其余2具碳四储罐:R201罐内储存物料291m3,R204罐检修后未储存物料。
7日15时30分,根据生产调度安排,停送R202(罐内当时有物料230m3)物料,并从烯烃装置接收裂解碳四(接收量约6吨/小时);R201物料打循环。
17时15分左右,316岗位化工三班操作工王某按班长指令到罐区检查卸车流程,准备卸丁二烯汽车槽车。
兰州石化“1·7”爆炸事故遇难者升至6人

兰州石化“1·7”爆炸事故遇难者升至6人中石油兰州石化公司昨天透露,截至目前,在事故现场已经找到6具遇难人员遗体,经确认6人均系公司职工;事故还造成1人重伤,但生命体征平稳,没有生命危险;5名轻伤人员正在恢复中。
4个着火点熄灭一个据中石油集团公司介绍,目前,现场4个着火点已有一个熄灭,剩余3个着火区域已形成稳定燃烧。
据监测,现场没有有毒气体排出,所有消防水已进入污水防控系统。
中石油已组织抢险灭火和防护工作。
一是全部切断相关物料,与周边罐隔离冷却,采取控制性燃烧措施。
二是加大消防力度,保证消防水量充足,确保消防污水全部排入缓冲池。
三是千方百计做好伤员施救,妥善安置门窗受损的20余名居民。
附近百余辆罐车转移据现场指挥部昨天介绍,316罐区6个油罐发生爆炸后,造成管线断裂,未燃爆的部分罐体物质外泄,25个液态烃储罐受到火势威胁。
现场抢救力量连续奋战,采取减压、降温持续排险。
同时,为了确保周边1000米内不发生次生连爆事故,现场指挥部紧急部署,调运8台机车,对临近爆炸现场的专用线石岗车站、颖川堡车站的6列油车,共215辆石脑油,121辆汽、煤、柴油罐车安全转移。
目前,经过一线抢险警力的全力工作,确保了未燃爆罐体的安全,燃烧罐正在稳定燃烧,但由于危险源仍未排除,消防官兵和公安干警仍在全力奋战。
事因裂解碳四罐泄漏昨天,中石油集团公司透露,由国家安监总局等相关部门组成的事故调查组已在现场全面开展工作。
经初步分析,事故是由于裂解碳四罐泄漏,致使现场可燃气体浓度达到爆炸极限,呲出的可燃气体产生静电,引发爆炸着火。
爆炸详细原因还在进一步调查中。
兰州石化向公众致歉爆炸事故引起兰州市民高度关注,并给市民情绪和生产生活带来一定的负面影响。
“发生这样的事故,无论对于企业,还是市民来说,都是十分不幸的。
作为企业,我们感到十分惭愧。
”昨天,兰州石化公司副总经理李家民在接受媒体采访时说,这次爆炸给公众造成了一定的影响,他希望通过媒体向市民表示歉意,并承诺将尽快妥善处理这次事故,接受教训,防止此类事件再次发生。
化工安全事故案例汇总

化工安全事故案例汇总目录目录 (1)第一章火灾事故案例 (4)一山东赫达股份有限公司"9.12"爆燃事故 (4)二淄博中轩生化有限公司"6.16"火灾事故 (5)三吉林化学工业公司化肥厂火灾事故 (6)四菏泽海润化工有限公司小井乡黄庄储备库11.23 爆燃事故 (7)五兴化化工公司甲醇储罐爆炸燃烧事故 (9)六制度不全操作不当引发爆燃事故“2005.9.28”燃爆事故 (11)七济南市某化工厂氮氢气压缩机放空管雷击着火事故 (12)八锅炉长期高负荷运行引发火灾事故 (13)九爆炸危险区域使用非防爆电气设备引发火灾 (15)十一起氧气管道燃爆事故 (16)十一某化工厂动火措施不完善气柜方箱着火事故 (19)十二中石油兰州石化爆炸事故 (20)第二章爆炸事故案例 (22)一安徽某化肥厂汽车槽车液氨储罐爆炸 (22)二大庆石油化工总厂2004.10.27硫磺装置酸性水罐爆炸事故分析 (23)三山东德齐龙化工集团有限公司“7.11”爆炸事故 (25)四河北省某银矿空气压缩机油气分离储气箱爆炸 (27)五某石化总厂化工一厂换热器爆炸 (28)六锅炉炉膛煤气爆炸事故案例 (29)七山东德齐龙化工集团氮氢气体泄漏爆炸事故 (31)八动火前检查欠详作业中爆炸伤人 (32)九山东博丰大地工贸有限公司“7.27”爆炸事故 (33)十山西某化工厂压力容器爆炸事故案例 (34)十一南京化工厂爆炸事故 (34)十二大连输油管道爆炸事故 (36)第三章中毒事故案例 (38)一河南濮阳中原大化集团有限责任公司“2.23”较大中毒窒息事故 (38)二莘县化肥有限责任公司“7.8”液氨泄漏事故 (39)三淄博市周村区“5.21”危化品槽罐车中毒死亡事故 (43)四山东阿斯德化工有限公司“8.6”一氧化碳中毒事故 (44)五山东滨化集团化工公司“4.15”氮气窒息事故 (45)六山东晋煤同辉化工有限公司“4.21”事故 (46)七苯中毒事故案例 (48)八制度不执行,入罐作业酿事故 (49)九某化工厂急性硫化氢中毒事故分析 (50)十二氧化硫中毒事故案例 (52)第四章国外化工安全事故案例 (55)一美国乔治亚州奥古斯塔BP-阿莫科聚合物工厂爆炸事故 (55)二美国路易斯安那州Sonat Exploration公司油气分离厂火灾爆炸事故 (57)三美国托斯科埃文炼油厂爆炸事故 (61)四日本甲醇精馏塔爆炸事故 (65)五美国环氧乙烷再蒸馏塔爆炸事故 (66)六韩国幸福公司的ABS树脂厂火灾爆炸事故 (68)七日本一合成氨装置爆炸事故 (69)八印度马弗罗炼油厂储罐区爆炸事故 (70)九墨西哥城液化石油气站火灾爆炸事故 (70)十西班牙液化丙烯罐车爆炸事故 (73)十一美国联合碳化物公司氮气窒息事故 (76)十二印度博帕尔甲基异氰酸酯泄漏事故 (79)十三日本一化工厂生产农药时焦油状废物分解泄漏事故 (83)十四塞内加尔液氨储罐发生爆炸事故 (84)第一章火灾事故案例一山东赫达股份有限公司"9.12"爆燃事故2010年9月12日,山东赫达股份有限公司发生爆燃事故,造成2人重伤,2人轻伤,直接经济损失约230余万元。
中国石油天然气股份有限公司兰州石化分公司“1·7”爆炸火灾事故
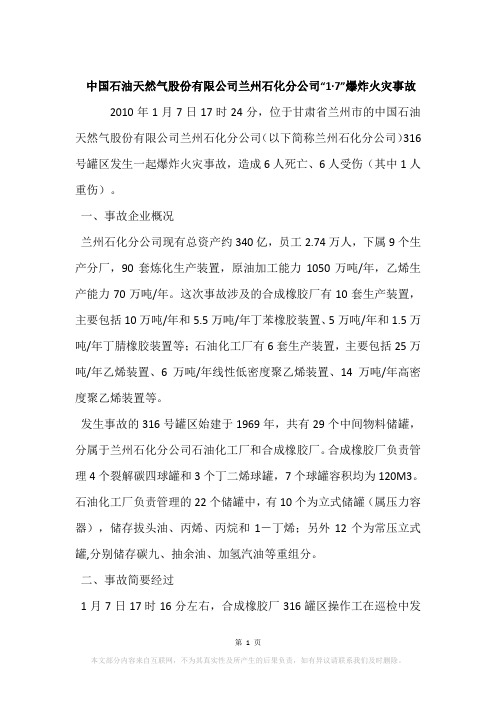
中国石油天然气股份有限公司兰州石化分公司“1·7”爆炸火灾事故2010年1月7日17时24分,位于甘肃省兰州市的中国石油天然气股份有限公司兰州石化分公司(以下简称兰州石化分公司)316号罐区发生一起爆炸火灾事故,造成6人死亡、6人受伤(其中1人重伤)。
一、事故企业概况
兰州石化分公司现有总资产约340亿,员工2.74万人,下属9个生产分厂,90套炼化生产装置,原油加工能力1050万吨/年,乙烯生产能力70万吨/年。
这次事故涉及的合成橡胶厂有10套生产装置,主要包括10万吨/年和5.5万吨/年丁苯橡胶装置、5万吨/年和1.5万吨/年丁腈橡胶装置等;石油化工厂有6套生产装置,主要包括25万吨/年乙烯装置、6万吨/年线性低密度聚乙烯装置、14万吨/年高密度聚乙烯装置等。
发生事故的316号罐区始建于1969年,共有29个中间物料储罐,分属于兰州石化分公司石油化工厂和合成橡胶厂。
合成橡胶厂负责管理4个裂解碳四球罐和3个丁二烯球罐,7个球罐容积均为120M3。
石油化工厂负责管理的22个储罐中,有10个为立式储罐(属压力容器),储存拔头油、丙烯、丙烷和1-丁烯;另外12个为常压立式罐,分别储存碳九、抽余油、加氢汽油等重组分。
二、事故简要经过
1月7日17时16分左右,合成橡胶厂316罐区操作工在巡检中发
第 1 页
本文部分内容来自互联网,不为其真实性及所产生的后果负责,如有异议请联系我们及时删除。
兰州“1·7”石化公司爆炸事故扑救及处置对策

3 6 区上空 。到场 后发现爆炸 冲击 波将西南 两侧的 l l罐 3
节 火 车 槽 罐 掀 翻 , 大 的 气 浪 将 炸 飞 的 贮 罐 残 片 抛 至 巨
1 0多 米 外 ,3 6罐 区 的 1 2 3号 罐 群 已 呈 猛 烈 燃 烧 态 0 l 、、
和 近 百 条 生 产 工 艺 管 线 的 安 全 , 免 了 恶 性 爆 炸 事 故 和 避 环境 污染 等 次生 灾 害 的 发 生 , 火 灾 损 失 降 到 了最 低 , 将 参 战 官 兵无 一 伤 亡 。
1 起 火罐 区 基本 情 况
势 , 向 罐 区 东 、 、 侧 的 8万 t 烯 裂 解 装 置 和 生 产 并 南 北 乙 工 艺 管 线 蔓 延 , 场情 况 万 分 危 急 。 火 1 7时 5 分 , 场 的 西 固 中 队 在 进 行 火 情 侦 查 时 , O 到 位 于 5号 罐 群 的 F 重 碳 9 罐 发 生 第 三 次 爆 炸 。根 据 火 5 储 场 情 况 , 固消 防 中 队 官 兵 在 罐 区 东 、 两 侧 各 出 1门水 西 南 炮 阻 止 火 势 蔓 延 。 兰州 石 化 公 司 消 防 支 队在 罐 区 西 北 侧
丙 烯 爆 炸 极 限 为 1 ~ 1 。 这 些 物 料 爆 炸 危 险 性 极 5 大 , 火救 援 过 程 中 , 场 先 后 发 生爆 炸 4次 、 燃 2次 。 灭 现 爆
中图 分 类 号 : 9 2 U9 8 1 X 3 ,T 9 .
文 献 标 志 码 : B
( ) 火 面 积 大 , 响 范 围广 。罐 区 、 线 一 片 火 海 , 3过 影 管
中石油兰州石化爆炸事故

In places deeper than night, there must be darker eyes than night.简单易用轻享办公(页眉可删)中石油兰州石化爆炸事故十二中石油兰州石化爆炸事故1.事故经过2010年1月7日,兰州石化公司石油化工厂316罐区发生爆炸燃烧事故,甘肃省消防总队迅速调集两个消防支队赶赴现场,会同兰州石化公司消防支队对火场实施警戒,确保现场起火的四个罐体稳定燃烧,不再发生爆炸,4个燃烧罐体经过平稳燃烧,8日凌晨一个已经熄灭,火灾现场的明火估计将于9日凌晨熄灭。
爆炸发生后,现场抢险人员在甘肃省消防总队总队长陶润仁的指挥下,再次加派人力,在现场增设水炮对罐体进行持续冷却。
8日凌晨,火场附近风力加强,气温骤然降低,喷洒在附近其他罐体上的消防水很快凝结成几十厘米长的冰凌,在外围警戒的救援人员只能蜷缩在驾驶室内,相互依偎取暖,而靠近火场的救援人员遭受猛火灼烤,穿着隔热服大汗淋漓,每次换班,从火场换下的救援人员汗水很快就结冰,然而救援人员在当晚几经冰火考验,冒着生命危险继续与大火鏖战。
截止8日凌晨3时,经过救援人员严密布控,爆炸现场的火势渐渐减弱,并再次处于稳定燃烧状态。
在救援人员的持续监控下,现场附近没有再次发生爆炸,凌晨5时许,现场四个着火点已有一个熄灭,剩余三个着火区域已形成稳定燃烧。
在8日下午,由中石油兰州石化分公司召开的新闻发布会上,相关负责人告诉记者,据监测,现场没有有毒气体排出,所有消防水已进入污水防控系统。
爆炸现场残存的易燃气体经过稳定燃烧,有可能将于今日凌晨燃烧殆尽。
事故造成5人失踪,1人重伤,5人轻伤。
受伤和失踪人员均为兰州石化公司员工。
目前,现场四个着火点已有一个熄灭,剩余三个着火区域已形成稳定燃烧。
据监测,现场没有有毒气体排出,所有消防水已进入污水防控系统。
2.事故原因(1)该公司所属兰州石化公司一厂区发生爆炸着火事故的原因,是由于罐体泄漏,致使现场可燃气体浓度达到爆炸极限,呲出的可燃气体产生静电,引发爆炸着火。
兰州石化罐区爆炸(组图)

兰州石化基地掠影(组图)2008年06月12日10:08中国石油新闻中心刘延治刘建华丁伟胡冰冯作文我要评论(0)字号:T|T兰州石化基地掠影兰州石化公司加快人才培育和新产品自主研发步伐,进一步推进操作技能人才队伍建设,提高操作人员队伍的整体素质。
兰州石化目前具备年1050万吨炼油能力,是我国西部最大的炼厂,成为保障西北、西南地区成品油供应的重要基地。
九曲黄河,宁静金城。
兰州石化公司坐落于此。
近日,西北地区首套丙烯酸及酯装置在兰州石化公司建成投产,并产出合格的丙烯酸和丙烯酸丁酯产品。
这意味着兰州石化向着“建设具有国际竞争力炼油化工基地”的目标又迈出了坚实的一步。
兰州石化公司是我国“一五”期间的156项重点工程之一,是保障西北、西南广大地区油品和化工产品供应的重要基地。
近年来,兰州石化先后建成了年70万吨乙烯改扩建工程、年40万吨芳烃抽提装置、年10万吨丁苯橡胶装置等一批重点项目,已具备千万吨炼油、70万吨乙烯生产规模,形成目前我国西部集炼油、化工、化肥生产以及机械仪表制造、工程技术、建安维修、物流仓储等生产和社会服务为一体的大型综合炼化企业。
兰州石化公司在新的发展思路上,继续深化改革,持续自主创新,着力转变发展方式和提高发展质量,切实加强安全环保和节能减排,更加注重文化建设和员工发展,实施技术进步、资源节约、员工发展、人员转移和企业文化建设五大战略,全面提升炼油化工业务的竞争能力,大力发展机械仪表制造、工程技术、建安维修、物流仓储等生产和社会服务,努力建设具有国际竞争力的炼油化工基地。
兰州石化基地掠影(组图)2008年06月12日10:08中国石油新闻中心刘延治刘建华丁伟胡冰冯作文我要评论(0)字号:T|T年70万吨乙烯改扩建工程建成投产。
催化干气、液化气脱硫装置项目建设将于6月30日建成中交,两套装置的建成将使催化干气、液化气的品质更高更环保。
兰州石化公司不断夯实管理基础,通过细化检查标准,拓宽检查内容,将集中检查与日常抽检相结合,推进岗位责任制大检查、达标创奖和五型班组创建活动。
重大危险源分级评定及管理
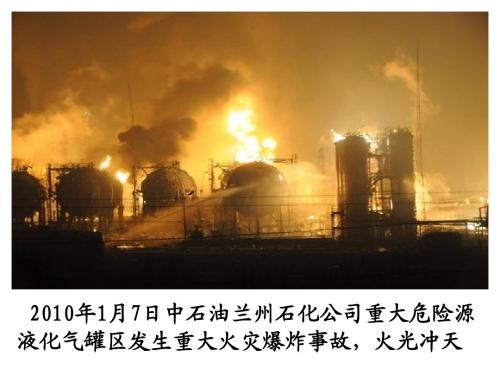
重大危险源辨识分级结果:
对上述情况1,应明确说明本项目500米范围
内构成重大危险源及装置、贮罐(区)的分
级结果; 对上述情况2, 应明确说明本项目500米范围 内构成(或不构成)重大危险源。若构成重 大危险源,应说明其分级结果。
二、危险化学品重大危险源评估 报告应细化说明的事项
。
1、明确评估检查的重点部位,细化现场检查表 内容
选择。一般包括温度、压力、液位、阀位、流量以及可 燃/有毒气体浓度、明火和音视频信号和其他危险因素 等。
库区(库) 库区(库)监测预警项目主要根据储存介质
特性、包装物和容器的结构形式和环境条件等
的不同进行选择。一般包括库区室内的温度、
湿度、烟气以及室内外的可燃/有毒气体浓度、
明火、音视频信号以及人员出入情况和其他危
必须在确定评估单元基础上,明确检查重点部位、对 涉及重大危险源的检查内容利用检查表进行检查。如 相关工艺设备的检测监控、自动化控制、仪表控制室 设置、对吸入性有毒气体构成重大危险源的设立气防 站(组)、气防站设备的合理配置、应急器材配备、 安全管理等。
。
监控项目的分类 对于储罐区(储罐)、库区(库)、生产场所三类重 大危险源,因监控对象不同,所需要的安全监控预警 参数有所不同。主要可分为: a) 储罐以及生产装置内的温度、压力、液位、流量、 阀位等可能直接引发安全事故的关键工艺参数; b) 当易燃易爆及有毒物质为气态、液态或气液两相时, 应监测现场的可燃/有毒气体浓度; c) 气温、湿度、风速、风向等环境参数; d) 音视频信号和人员出入情况; e) 明火和烟气; f) 避雷针、防静电装置的接地电阻以及供电状况。
识》中规定的临界量比值之和大于或等于1的。
CASST-QRA重大危险源区域定量风险评价软件(V2.0),
20100107兰州石化爆炸事故
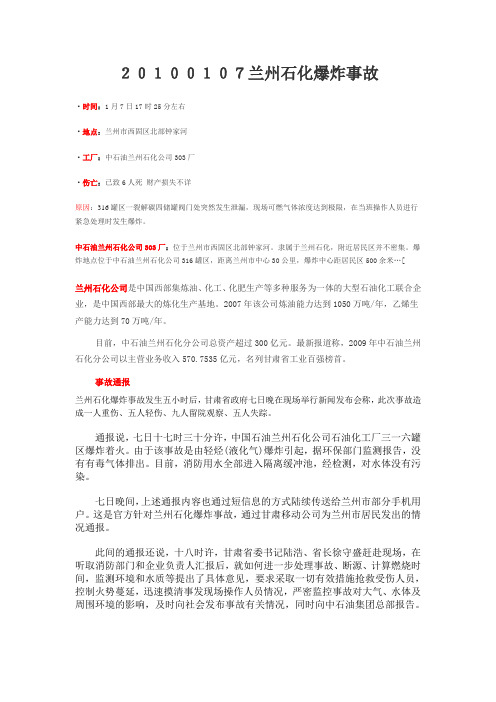
20100107兰州石化爆炸事故·时间:1月7日17时25分左右·地点:兰州市西固区北部钟家河·工厂:中石油兰州石化公司303厂·伤亡:已致6人死财产损失不详原因:316罐区一裂解碳四储罐阀门处突然发生泄漏,现场可燃气体浓度达到极限,在当班操作人员进行紧急处理时发生爆炸。
中石油兰州石化公司303厂:位于兰州市西固区北部钟家河。
隶属于兰州石化,附近居民区并不密集。
爆炸地点位于中石油兰州石化公司316罐区,距离兰州市中心30公里,爆炸中心距居民区500余米…[兰州石化公司是中国西部集炼油、化工、化肥生产等多种服务为一体的大型石油化工联合企业,是中国西部最大的炼化生产基地。
2007年该公司炼油能力达到1050万吨/年,乙烯生产能力达到70万吨/年。
目前,中石油兰州石化分公司总资产超过300亿元。
最新报道称,2009年中石油兰州石化分公司以主营业务收入570.7535亿元,名列甘肃省工业百强榜首。
事故通报兰州石化爆炸事故发生五小时后,甘肃省政府七日晚在现场举行新闻发布会称,此次事故造成一人重伤、五人轻伤、九人留院观察、五人失踪。
通报说,七日十七时三十分许,中国石油兰州石化公司石油化工厂三一六罐区爆炸着火。
由于该事故是由轻烃(液化气)爆炸引起,据环保部门监测报告,没有有毒气体排出。
目前,消防用水全部进入隔离缓冲池,经检测,对水体没有污染。
七日晚间,上述通报内容也通过短信息的方式陆续传送给兰州市部分手机用户。
这是官方针对兰州石化爆炸事故,通过甘肃移动公司为兰州市居民发出的情况通报。
此间的通报还说,十八时许,甘肃省委书记陆浩、省长徐守盛赶赴现场,在听取消防部门和企业负责人汇报后,就如何进一步处理事故、断源、计算燃烧时间,监测环境和水质等提出了具体意见,要求采取一切有效措施抢救受伤人员,控制火势蔓延,迅速摸清事发现场操作人员情况,严密监控事故对大气、水体及周围环境的影响,及时向社会发布事故有关情况,同时向中石油集团总部报告。
兰州石化“1·7”爆燃事故原因初步查明
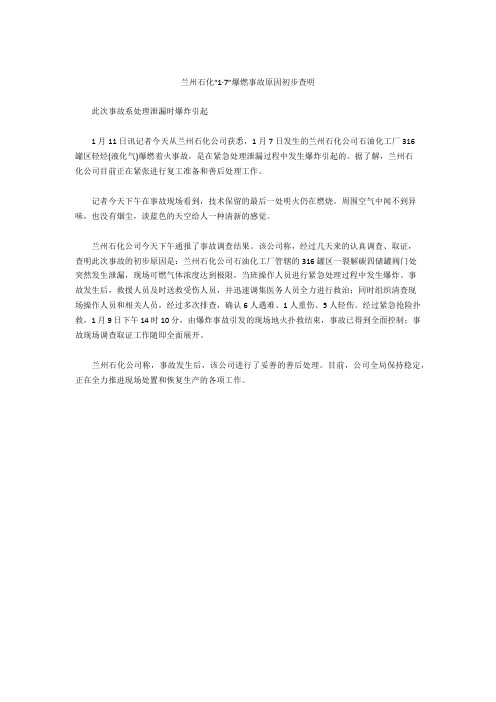
兰州石化“1·7”爆燃事故原因初步查明
此次事故系处理泄漏时爆炸引起
1月11日讯记者今天从兰州石化公司获悉,1月7日发生的兰州石化公司石油化工厂316
罐区轻烃(液化气)爆燃着火事故,是在紧急处理泄漏过程中发生爆炸引起的。
据了解,兰州石
化公司目前正在紧张进行复工准备和善后处理工作。
记者今天下午在事故现场看到,技术保留的最后一处明火仍在燃烧。
周围空气中闻不到异味,也没有烟尘,淡蓝色的天空给人一种清新的感觉。
兰州石化公司今天下午通报了事故调查结果。
该公司称,经过几天来的认真调查、取证,
查明此次事故的初步原因是:兰州石化公司石油化工厂管辖的316罐区一裂解碳四储罐阀门处
突然发生泄漏,现场可燃气体浓度达到极限,当班操作人员进行紧急处理过程中发生爆炸。
事
故发生后,救援人员及时送救受伤人员,并迅速调集医务人员全力进行救治;同时组织清查现
场操作人员和相关人员,经过多次排查,确认6人遇难、1人重伤、5人轻伤。
经过紧急抢险扑救,1月9日下午14时10分,由爆炸事故引发的现场地火扑救结束,事故已得到全面控制;事故现场调查取证工作随即全面展开。
兰州石化公司称,事故发生后,该公司进行了妥善的善后处理。
目前,公司全局保持稳定,正在全力推进现场处置和恢复生产的各项工作。
司兰州石化分公司17爆炸火灾事故的通报

国家安全监管总局关于中国石油天然气股份有限公司兰州石化分公司“1·7”爆炸火灾事故的通报安监总管三〔2010〕8号各省、自治区、直辖市及新疆生产建设兵团安全生产监督管理局,有关中央企业:2010年1月7日17时24分,位于甘肃省兰州市的中国石油天然气股份有限公司兰州石化分公司(以下简称兰州石化分公司)316号罐区发生一起爆炸火灾事故,造成6人死亡、6人受伤(其中1人重伤)。
事故发生后,国务院领导同志高度重视并作出重要批示,甘肃省省委、省政府主要负责同志和省政府分管负责同志迅速赶赴事故现场,协调指挥应急抢险工作。
国家安全监管总局局长骆琳,副局长王德学、孙华山立即对事故应急处置和处理作出部署,派员赶赴现场,指导协助事故抢险和调查处理工作。
中国石油天然气集团公司有关领导及时赶赴现场组织抢险。
为认真落实国务院领导重要批示精神,深刻吸取事故教训,举一反三,防止类似事故发生,现将事故有关情况通报如下:一、事故企业概况兰州石化分公司现有总资产约340亿,员工2.74万人,下属9个生产分厂,90套炼化生产装置,原油加工能力1050万吨/年,乙烯生产能力70万吨/年。
这次事故涉及的合成橡胶厂有10套生产装置,主要包括10万吨/年和5.5万吨/年丁苯橡胶装置、5万吨/年和1.5万吨/年丁腈橡胶装置等;石油化工厂有6套生产装置,主要包括25万吨/年乙烯装置、6万吨/年线性低密度聚乙烯装置、14万吨/年高密度聚乙烯装置等。
发生事故的316号罐区始建于1969年,共有29个中间物料储罐,分属于兰州石化分公司石油化工厂和合成橡胶厂。
合成橡胶厂负责管理4个裂解碳四球罐和3个丁二烯球罐,7个球罐容积均为120M3。
石油化工厂负责管理的22个储罐中,有10个为立式储罐(属压力容器),储存拔头油、丙烯、丙烷和1-丁烯;另外12个为常压立式罐,分别储存碳九、抽余油、加氢汽油等重组分。
二、事故简要经过1月7日17时16分左右,合成橡胶厂316罐区操作工在巡检中发现裂解碳四球罐(R202)出口管路弯头处泄漏,立即报告当班班长。
《兰州石化爆炸事故》课件

兰州石化爆炸事故是一起对兰州市造成巨大影响的灾难性事件。
事故概述
事故时间和地点
2019年8月25日,在兰州 市兰州石化公司一座化工 厂发生爆炸事故。
事故原因分析
经过调查,事故起因是由 于操作失误和设备故障导 致的化学品泄露和点火。
事故影响范围
爆炸导致周边地区严重受 损,包括人员伤亡、房屋 损毁和环境污染等。
2 危化品管理的问题与挑战
当前的危化品管理仍存在不足,需要加强相关法规和标准的建设。
3 政府、企业及公众的责任和义务
政府、企业和公众共同肩负起预防和应对事故的责任和义务。
参考文献
新闻报道和相关材料
收集兰州石化爆炸事故的新闻报道和相关材料以获取全面的信息。
网络信息和社会反响
分析事故在网络上的传播和社会的反响,了解事件对社会的影响。救援和处理情况1来自处理措施及效果2
隔离事故区域,确保人员安全,并展
开事故调查工作以防止类似事故再次
发生。
3
救援行动过程
立即启动紧急救援行动,调派消防部 队和急救人员赶赴现场。
后续处理的展望
加强化学工业安全监管,提高应急处 置能力,加强事故预警和应对机制。
事故启示
1 工业安全的重要性
事故提醒我们工业安全不能掉以轻心,必须时刻保持高度警惕。
相关法律法规和规范性文件
查阅相关法律法规和规范性文件以了解危化品管理的标准和要求。
兰州石化爆炸

•安全是我们的生命!
• 我们的穿戴安全吗? • 我们的操作安全吗? • 我们的指令安全吗?
7
中石油兰州石化工厂爆炸事故
1
中石油兰州石化工厂爆炸事故
2
中石油兰州石化工厂爆炸事故
3
中石油兰州石化工厂爆炸事故
4
中石油兰州石化工厂爆炸事故
5
中石油兰州石化工厂爆炸事故
事故初步结果
2010年1月7日17时30分,兰州石化公司石油化工厂316罐区发生爆炸着火事故。 22时40分,甘肃省政府在现场举行新闻发布会称,此次事故造成事故造成5人失踪,1 人重伤,5人轻伤,9人留院观察。据环保部门监测报告,没有有毒气体排出。目前,消 防用水全部进入隔离缓冲池,经检测,对水体没有污染。兰州石化公司负责人介绍, 发生爆炸着火的罐区是个轻质油的罐区,主要是液化气、轻烃等物质,是和家庭液化 气类似的组分。据《21世纪经济报道》,此次发生爆炸的合成橡胶厂316灌区的两个 储罐装满化工品C4。C4是液化石油气(LPG)的主要原料,燃烧时会发出刺鼻气味,但燃 烧后不会留下有毒物质。 爆炸地点位于兰州市西固区钟家河的中石油兰州石化公司316罐区,距离兰州市 中心30公里。爆炸响声巨大,在离事故现场17公里外的地方都能感到震动。
1、事故是由于罐体泄露而引起,因此现场操作人员必须按照相关 规定做好巡检,尽早发现隐患,中控员要高度集中精神,注意 中控的各项报警参数。 2、设备保养维护工作要落实到个人并执行做好,保证设备以良好 的状态进行工作,杜绝一切隐患。 3、员工要打醒十二分精神,时刻牢记安全,安全工作关系每一个 人
安全是什么?
中石油公布兰州石化工厂爆炸事故初步调查结果 : 中国石油天然气集团公司 (8日)早晨发布消息说,经初步分析,该公司所属兰州 石化公司一厂区发生爆炸着火事故的原因,是由于罐体泄漏,致使现场可燃气体浓度 达到爆炸极限,呲出的可燃气体产生静电,引发爆炸着火。
典型事故二十一:中石油兰州石化“1.7”罐区爆炸事故

典型事故二十一:中石油兰州石化“1.7”罐区爆炸事故一、事故调查分析(一)事故概要1、事故简介2010年1月7日17时24分,兰州石化公司316#罐区发生火灾、爆炸事故,事故共造成6人死亡、1人重伤、5人轻伤,未造成次生事故和环境污染。
2、事故原因(1)直接原因设备缺陷。
由于316#罐区R202球罐出料管弯头母材焊缝热影响区存在组织缺陷,致使该弯头局部脆性开裂,导致碳四物料大量泄漏,泄漏汽化后的碳四物料蔓延至罐区东北侧丙烯腈装置焚烧炉,遇焚烧炉明火引燃爆炸。
(2)间接原因①特种设备安全监督管理不到位Ⅰ、未按规程规定对事故管线进行定期检验没有按照国家质监总局2003年6月试行的《在用工业管道定期检验规程》规定,对在用工业管道进行全面定期检验,致使R202球罐出料管线母材存在的组织缺陷未被发现和整改。
Ⅱ、未按规定落实事故管线更换计划2007年3月,经检验发现R203、R206、R207球罐底部进出物料管线腐蚀严重、壁厚减薄,定为4级,企业下达了R201、R202、R203、R204球罐底部进出物料管线更换计划。
实际仅更换了R201球罐底部进出物料管线,R202、R203、R204球罐底部进出物料管线一直未更换。
②设备管理人员没有认真履行设备管理职责设备管理部门和有关管理人员,没有按照规定要求对碳四车间R202等球罐进出物料管线进行全面检测检验,在R202球罐管线更换计划下达后,又没有履行监督落实职责,致使事故隐患长期存在并最终导致事故发生。
③安全应急处置设施不完善316#罐区自1986年建成投运以来,未按照《石油化工企业设计防火规范》(GB50160-2008)规定,对储罐进出物料管道设置自动联锁切断装置,致使事故状态下无法紧急切断泄漏源,导致泄漏扩大并引发事故。
(二)基本情况1、兰州石化公司基本情况兰州石化公司拥有原油加工能力1050万吨/年、乙烯生产能力70万吨/年、化肥生产能力52万吨/年、合成树脂生产能力124.5万吨/年、合成橡胶生产能力17.5万吨/年、炼油催化裂化剂生产能力5万吨/年。
- 1、下载文档前请自行甄别文档内容的完整性,平台不提供额外的编辑、内容补充、找答案等附加服务。
- 2、"仅部分预览"的文档,不可在线预览部分如存在完整性等问题,可反馈申请退款(可完整预览的文档不适用该条件!)。
- 3、如文档侵犯您的权益,请联系客服反馈,我们会尽快为您处理(人工客服工作时间:9:00-18:30)。
典型事故二十一:中石油兰州石化“1.7”罐区爆炸事故一、事故调查分析(一)事故概要1、事故简介2010年1月7日17时24分,兰州石化公司316#罐区发生火灾、爆炸事故,事故共造成6人死亡、1人重伤、5人轻伤,未造成次生事故和环境污染。
2、事故原因(1)直接原因设备缺陷。
由于316#罐区R202球罐出料管弯头母材焊缝热影响区存在组织缺陷,致使该弯头局部脆性开裂,导致碳四物料大量泄漏,泄漏汽化后的碳四物料蔓延至罐区东北侧丙烯腈装置焚烧炉,遇焚烧炉明火引燃爆炸。
(2)间接原因①特种设备安全监督管理不到位Ⅰ、未按规程规定对事故管线进行定期检验没有按照国家质监总局2003年6月试行的《在用工业管道定期检验规程》规定,对在用工业管道进行全面定期检验,致使R202球罐出料管线母材存在的组织缺陷未被发现和整改。
Ⅱ、未按规定落实事故管线更换计划2007年3月,经检验发现R203、R206、R207球罐底部进出物料管线腐蚀严重、壁厚减薄,定为4级,企业下达了R201、R202、R203、R204球罐底部进出物料管线更换计划。
实际仅更换了R201球罐底部进出物料管线,R202、R203、R204球罐底部进出物料管线一直未更换。
②设备管理人员没有认真履行设备管理职责设备管理部门和有关管理人员,没有按照规定要求对碳四车间R202等球罐进出物料管线进行全面检测检验,在R202球罐管线更换计划下达后,又没有履行监督落实职责,致使事故隐患长期存在并最终导致事故发生。
③安全应急处置设施不完善316#罐区自1986年建成投运以来,未按照《石油化工企业设计防火规范》(GB50160-2008)规定,对储罐进出物料管道设置自动联锁切断装置,致使事故状态下无法紧急切断泄漏源,导致泄漏扩大并引发事故。
(二)基本情况1、兰州石化公司基本情况兰州石化公司拥有原油加工能力1050万吨/年、乙烯生产能力70万吨/年、化肥生产能力52万吨/年、合成树脂生产能力124.5万吨/年、合成橡胶生产能力17.5万吨/年、炼油催化裂化剂生产能力5万吨/年。
2、兰州石化公司合成橡胶厂基本情况兰州石化公司合成橡胶厂是兰州石化公司的二级单位,主要生产合成橡胶、合成树脂和有机化工原料三大系列化工产品。
现有八个联合车间,有10万吨/年丁苯橡胶装置、5.5万吨/年丁苯橡胶装置、5万吨/年丁腈橡胶装置、1.5万吨/年丁腈橡胶装置、2万吨/年ABS树脂装置、1.5万吨/年SAN树脂装置、6万吨/年苯乙烯装置、4.5万吨/年碳四抽提装置、8万吨/年MTBE装置、丁钠橡胶装置和液体橡胶装置。
3、316#罐区基本情况兰州石化公司316#罐区位于兰州石化公司西厂区,属生产过程中的中间罐区,主要承担石油化工厂烯烃联合车间、树脂厂、合成橡胶厂、乙烯厂相关上下游生产装置及黄河北罐区石脑油、拔头油、三苯、丁二烯、碳四及其烷烃类物料的储存、供给、装卸和转输任务。
共有各类储罐29个,分为3个罐区,其中碳四、丁二烯罐区由合成橡胶厂管理,拔头油罐区、常压罐区由石油化工厂管理。
兰州石化公司合成橡胶厂碳四、丁二烯罐区建成于1986年,共有7个400m3球罐,总容积2800m3,现储存物料有丁二烯、裂解碳四,其中R201、R202、R203、R204储存裂解碳四,R205、R206、R207储存丁二烯。
该罐区由储罐、泵房、4#火车装卸栈桥和汽车装卸站台组成,4#火车装卸栈桥共9个货位,其中第4#、第9#货位可进行汽车装卸,总装卸能力为6万吨/年。
兰州石化公司石油化工厂拔头油罐区、常压罐区建成于1970年。
共有各类物料储罐22个,总容积7858m3。
拔头油罐区有10个120m3储罐,总容积1200m3。
常压罐区有储罐12个,1000m3储罐2个、700m3储罐5个、500m3储罐1个、400m3储罐1个、86m3储罐3个,总容积6658m3。
其中拔头油罐区F1/A、F1/B、F1/C、F1/D储存拔头油,F2/A、F2/B、F2/C储存丙烯,F3/A、F3/B 储存丙烷,F4储存1-丁烯。
常压罐区F5储存重碳九,F6、F14储存抽余油,F7储存加氢汽油,F8/A储存甲苯,F9/A储存二甲苯,F10储存裂解油,F8/B 为清污分流罐,F8/C、F12储存轻碳九,F9/B储存二甲苯,F11储存正己烷。
该罐区由储罐、3#火车装卸栈桥和汽车装卸站台组成。
合成橡胶厂碳四、丁二烯罐区东侧为常压罐区,西南侧为拔头油罐区。
(三)事故发生时间序列(四)事故损失情况爆炸产生的冲击波造成合成橡胶厂碳四、丁二烯罐区操作工丁某死于操作室南侧铁路专用线站台上,当班班长孙某、操作工马某、谢某死于操作室附近,石油化工厂常压罐区与抽余油罐区外出检查的当班操作工杨某死于操作室西南方向铁路专用线两节罐车中间,扈某死于铁路专用线南侧距铁路槽车1米处。
同时造成碳四、丁二烯罐区球罐底部部分管线断裂,F1/C、F1/D拔头油罐气相管线断裂,球罐区西侧F2/A丙烯罐、F3/A丙烷罐顶部液位计法兰根部开裂泄漏着火燃烧,部分铁路槽车移位。
爆炸产生的冲击波造成常压罐区内部分管线断裂,罐内物料外泄,在防火堤内形成燃烧,先后引燃相邻F8/A甲苯罐、F5重碳九罐、F10裂解油罐、F6抽余油罐,并使其临近管线变形断裂,物料外泄燃烧,在围堤内形成较大火势。
辐射热使罐内压力、温度迅速升高,造成F6抽余油罐罐顶抛出至F7加氢汽油罐底部,F5重碳九罐罐顶向东北方向抛出落在冷却车间旁,F8/A甲苯罐罐顶向西南方向抛出落在铁路栈桥旁,F10裂解油罐罐顶抛出击中石油化工厂操作室附近管廊、栈桥,造成部分管线断裂,并落在操作室大门旁。
爆炸产生的冲击波造成316#-R201(碳四贮罐)、316#-R202(碳四贮罐)、316#-R205(丁二烯贮罐)、316#-R206(丁二烯贮罐)四个球罐底部大部分管线断裂,球罐内的可燃物料大量外泄,剧烈燃烧。
燃烧产生大量的辐射热造成316#-R202(碳四贮罐)、316#-R204(碳四贮罐)、316#-R205(丁二烯贮罐)温度过高、罐内压力过大,三个球罐先后爆裂。
燃烧产生的辐射热使F1/D拔头油罐罐内油气受热后压力升高,气相空间增大,引发爆炸,造成F1/D拔头油罐罐体撕裂,并使撕裂的罐体向西北方向抛出约82m,撞击到罐区西北侧铁路罐车后落在铁路罐车旁,撞击力造成部分铁路罐车移位倾斜;同时,爆炸冲击波造成F1/C拔头油罐向南倾倒。
碳四泄漏量增大无风图1碳四向西北方向扩散焚烧炉位于图示支架东南约20m处碳四向西北方向扩散无风图2焚烧炉附近起火瞬间图3火焰向周边蔓延图4316#罐区爆炸(摄像头剧烈抖动造成影像模糊)316#-R202罐顶部有一长度约3m,宽度大于1m的横向韧性裂口,裂口在母材上扩展;316#-R205面向316#-R202一侧顶部有一爆裂口,底部有明显的黑色过火痕迹,但受热明显较316#-R201和316#-R204要轻。
底部部分管线断裂,316#-R204(碳四贮罐)裂口尺寸为550×1800mm。
爆炸产生的冲击波同时使石油化工厂F1/C、D(拔头油罐)气相管线断裂。
由于F1/D拔头油的储存量较少,罐内油气受热后发生爆炸,巨大的爆炸力将罐体撕裂并使罐体向西北方向飞出约82m,撞击西北侧环形道路基自备铁路枕木、编组的铁路罐车后落在铁路上。
冲击力造成部分铁路罐车移位、倾斜。
冲击波使石油化工厂罐体倾倒。
F1/D(拔头油罐)爆炸,泄漏的物料燃烧产生大量高温辐射热造成其西侧丙烯、丙烷罐区中的F2/A(丙烯罐)、F3/A(丙烷罐)上部液位计法兰根部泄漏着火,并形成稳定燃烧。
碳四、丁二烯蔓延至常压罐区,常压罐区内同时发生着火爆炸,冲击波使其中部分罐区管线断裂,罐内物料外泄。
碳四罐区爆炸后飞出的设备残骸击中F6(抽余油罐,储存物料283吨)罐体中部,造成F6罐内物料外泄燃烧,持续的燃烧使浮盘烧毁,罐内物料燃烧膨胀,使罐顶飞出至F7底部,在隔堤内形成池火蔓延。
强大的辐射热先后引起相邻的F8/A(甲苯罐)、F5(重碳罐)、F10(裂解油罐)燃烧,造成飞出的F5罐顶击中栈桥、合成橡胶厂316#操作室附近管廊,并将部分管线拉断。
使管线中物料直接排放并燃烧。
其强大的辐射热使邻近的管线变形断裂,直接排放的物料在罐区地沟、泵房进出线汇集燃烧,形成较大的火势。
由于消防队的及时进入并采取冷却保护、隔离,316#罐区的其他设备才免于燃烧爆炸。
(五)事故原因分析技术组通过仔细分析事故发生全过程的视频资料、电话录音、事故当事人的笔录、事故现场勘察情况和316#-R202球罐1#出口管线失效分析结论,反复核查事故证据,查找事故区域的碳四泄漏点和事故点火源。
1、事故区域内的设备及管道勘察316#-R201球罐:支柱部分防火层脱落,支柱、拉杆等受热变形,球罐保温层脱落,梯子、平台和喷淋管线等附件脱落,部分接管断裂。
球罐向316#-R202方向倾斜,球罐本体无显著变形,罐体未开裂。
316#-R201A放水槽:罐体基本完好,无过火痕迹,保温层脱落,罐体向北位移0.3m ,连接管道变形、断裂,支腿受热变形。
316#-R202球罐:支柱隔热层完全脱落,支柱受热变形,罐体坍塌,球罐保温层脱落,梯子、平台和喷淋管线等附件脱落。
罐顶部有一长度约3m ,宽度大于1m 的横向韧性裂口,裂口在母材上扩展。
支柱受热,严重变形。
罐底部及其接管严重受热变形、有严重氧化痕迹。
个别接管部分表面无氧化痕迹或氧化较轻,出料口接管弯头开裂。
316#-R203球罐:罐体基本完好,支柱基本完好,球罐保温层脱落,梯子、平台和喷淋管线等附件脱落,面向316#-R202一侧有明显的黑色过火痕迹。
316#-R204球罐:球罐支柱基本完好,球罐保温层脱落,梯子、平台和喷淋管线等附件脱落。
面向316#-R202一侧有明显的黑色过火痕迹,下部球壳板出现一处韧性裂口,长度约1800mm ,最大宽度550mm 。
进口接管弯头部位一处韧性裂口(80×40mm )。
底部管线受热严重、断裂,表面严重氧化。
图5 316#-R202球罐底部接管316#-R205球罐:支柱基本完好,球罐保温层脱落,梯子、平台和喷淋管线等附件脱落,罐体面向316#-R202一侧和底部有明显的黑色过火痕迹,但受热明物料出口管(1#)表面无氧化痕迹 物料进口管(3#)严重受热变形物料出口管(2#) 表面无氧化痕迹显较316#-R201和316#-R204要轻,且上部球壳板出现一处韧性裂口,底部部分管线断裂。
316#-R207球罐:罐体面向316#-R202一侧有明显的过火痕迹。
上述事故现象表明:(1)泄漏在事故区域的碳四遇“火”燃烧后,火焰最后集中在316#-R202球罐进行燃烧;(2)燃烧产生强大的辐射热使316#-R201、R202、R204、R205球罐存在不同程度的过火;(3)与316#-R202相邻的316#-R201、R204、R205球罐由于受到辐射热的加热分别表现为:316#-R201球罐3根支柱(面向316#-R202侧)受热强度降低,由于不堪重负,3根支柱失稳。