铁路钢桥保护涂装精编
铁路桥梁钢结构保护涂装及涂料第3部分施工组织

铁路桥梁钢结构保护涂装及涂料第3部分施工组织一、引言铁路桥梁的钢结构在长期使用过程中,容易受到大气、水分、化学物质等的侵蚀,从而导致腐蚀、疲劳断裂等问题。
为了保护钢结构的安全和延长使用寿命,需要进行保护涂装及涂料的施工。
本文将详细探讨铁路桥梁钢结构保护涂装及涂料的施工组织。
二、施工组织的目标和原则2.1 目标铁路桥梁钢结构保护涂装及涂料的施工组织的目标是确保施工质量,提高涂层的耐久性和防护性能,延长钢结构的使用寿命,减少维护成本。
2.2 原则•合理安排施工进度,确保施工质量和工期的有效控制;•严格按照设计要求和规范进行施工,确保涂层的质量和性能;•采取科学的施工方法和工艺,提高施工效率和质量;•做好施工现场的安全管理,确保施工人员的安全。
三、施工组织的内容和步骤3.1 施工准备•制定详细的施工方案和施工组织设计,明确施工任务、施工方法、施工工艺等;•确定施工人员和施工班组,组织人员培训和技术交流,提高施工人员的素质和技能;•准备施工所需的材料、设备和工具,确保施工进度和质量。
3.2 施工过程3.2.1 表面处理•清洁表面,去除油污、锈蚀等杂质,可采用喷砂、喷丸等方法;•进行表面预处理,包括除锈、除油、除尘等,确保涂层的附着力和质量。
3.2.2 底涂施工•选择适合的底涂材料,根据设计要求进行施工;•采用刷涂、喷涂等方法进行底涂施工;•控制底涂的干燥时间和厚度,确保涂层的质量和性能。
3.2.3 中涂施工•选择适合的中涂材料,根据底涂的情况进行施工;•采用刷涂、喷涂等方法进行中涂施工;•控制中涂的干燥时间和厚度,确保涂层的质量和性能。
3.2.4 面涂施工•选择适合的面涂材料,根据中涂的情况进行施工;•采用刷涂、喷涂等方法进行面涂施工;•控制面涂的干燥时间和厚度,确保涂层的质量和性能。
3.3 施工验收•对施工过程进行现场检查,确保施工质量和规范;•对涂层进行检测和测试,包括涂层厚度、附着力、硬度等;•进行施工验收,确保涂层符合设计要求和规范。
铁路钢桥涂装体系
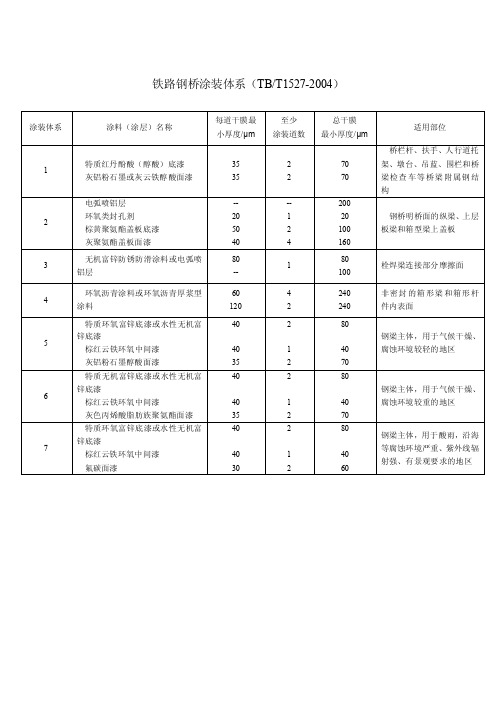
80
铝层
--
环氧沥 青涂 料或 环氧沥 青厚 浆型
60
涂料
120
特质 环氧 富锌底 漆或 水性 无机富
40
锌底漆
棕红云 铁环氧 中间漆
40
灰铝粉石 墨醇酸 面漆
35
特质 无机 富锌底 漆或 水性 无机富
40
锌底漆
棕红云 铁环氧 中间漆
40
灰色丙 烯酸脂 肪族聚 氨酯面 漆
35
特质环 氧富 锌底 漆或水 性无 机富
60
现代桥梁重防腐涂料体系
部位 钢板预处 理
钢箱梁外 部
钢箱梁内 部
涂层系统
涂料品种
车间底漆
无机硅酸 锌车间 底漆
1 环氧富锌底漆
底面防锈 2 无机硅酸辛底漆
3 金属热喷涂锌或铝
封闭漆
环氧封闭 漆
中间漆
厚浆型环 氧云铁 中间漆
丙烯酸聚 氨酯
面漆
氟碳面漆
丙烯酸聚 硅氧烷
底漆 环氧富锌底漆
1 面漆 浅色环氧厚浆型涂料
40
锌底漆
棕红云铁 环氧中 间漆
40
氟碳面漆
30
至少 涂装道数
2 2
-1 2 4
1
4 2 2
1 2 2
1 2 2
1 2
总干膜 最小厚度/ μm
70 70
200 20 100 160 80 100
适用部位
桥栏杆、扶手、人 行道托 架、墩 台、吊 蓝、围栏和 桥 梁检查 车等 桥梁 附属钢 结 构
钢桥明 桥面的 纵梁、上 层 板梁和箱 型梁上 盖板
2 底/面漆 浅色厚浆型环氧涂料
干膜厚度 15~20 80 80
桥梁隧道钢结构保护涂装技术标准

铁路桥隧建筑物大修维修钢结构保护涂装技术标准第3.2.1条钢梁、钢塔架、人行道栏杆支架等都应进行保护涂装,防止钢结构生锈。
第3.2.2条涂装前表面清理:在涂装底漆前,应将钢料表面的污泥、油垢、铁锈、旧漆皮和氧化皮彻底清除干净。
清除方法可采用喷砂、喷丸。
手工清理和溶剂擦洗。
严禁使用腐蚀性物质清理钢表面。
第3.2.3条清理等级及粗糙度要求:1. 清理等级要求根据使用的涂料品种、施工方法和构件部位的不同,涂装对钢结构表面清理等级要求如下:(1)热喷锌、铝或涂装环氧富锌底漆时,钢表面清理应达到S a3级。
(2)涂装酚醛红丹、醇酸红丹、聚氨脂底漆或维护涂装环氧宙锋及热喷锌时,钢表面清理应达到S a2.5级。
(3)箱形梁内表面涂装环氧沥青底漆时,钢表面清理应达到S a2级。
(4)人行道栏杆、扶手、托架、墩台吊篮、围栏等附属结构及铆钉头、螺栓头或局部维护涂装使用红丹底漆时,钢表面清理应达到S t3级。
2. 清理粗糙度要求(1)涂装涂料涂层时,钢表面粗糙度为R z25~60μm;选用最大粗糙度不得超过涂装体系干膜厚度的1/3。
表面粗糙度超过要求时,需加涂一道底漆。
(2)热喷锌或铝金属时,钢表面粗糙度为R z25~100μm;当表向粗糙度超过R z100μm时,涂层应至少超过轮廓峰125~150μm。
第3.2.4条钢梁连接板层之间大于0.5mm的缝隙须将缝内污垢和铁锈清除干净,在第一道底漆干燥后,用石膏腻子填塞,待腻子表面干燥后,方可继续进行涂料涂装。
小于0.5mm的缝隙可用油漆封闭。
第3.2.5条钢梁初始涂装及运营中钢梁重新涂装:1. 钢梁初始涂装如在制造厂进行,应完成底漆、中间漆和第一道面漆涂装工作(节点或拼接部位只进行喷铝或涂无机富锌漆),其余面漆涂装在桥位上进行。
2. 运营中钢梁保护涂装起泡或裂纹或脱落的面积达33%,点锈面积达5%,粉化劣化达四级时,应进行整孔重新涂装。
第3.2.6条钢梁涂装体系:1. 钢梁大面积涂装(l)钢梁大面积涂料涂装体系及最小厚度要求如表3.2.6—1。
铁路通道钢桁梁桥位涂装施工方案

铁路通道钢桁梁桥位涂装施工方案
山西中南部铁路通道钢桁梁桥位
涂装施工方案
中铁宝桥集团有限公司
04月目录
一、工程概况
1.1编制依据
依据<山西中南部铁路通道钢桁梁制造规则>、<山西中南部铁路通道钢桁梁招标文件>及相应的标准编制本涂装施工方案。
编制引用以下标准:
1.2工程范围
本工程为山西中南部铁路通道钢桁梁现场单孔架设完成后对工地焊缝及栓接点外露面进行涂装,并进行全桥现场涂层损伤处修补以及最后一道面漆涂装。
1.3山西中南部铁路通道钢桁梁涂装体系
涂装体系如下:
注:(1)高强螺栓连接部位补涂装见下表:
(2)损伤面对于未损伤至底材的区域:去油后对周边涂层实施保护,对损坏区域采用打磨机打磨;周围涂层打磨成坡度,磨出不同漆层的层面,用刷涂方法补涂相应涂层的涂料。
自检、专检各格后,报请监理验收。
二、施工前准备
2.1施工人员进场
主要工序的施工人员(打磨工、配漆工和涂装工)和管理人员(质检员、带班负责人、现场经理等)应具备相应的涂装施工技能和施工经验。
【铁路方案】某铁路通道钢桁梁桥位涂装施工方案(doc 17页)

XXXX铁路通道钢桁梁桥位涂装施工方案XX集团有限公司20XX年XX月一、工程概况1.1编制依据依据《山西中南部铁路通道钢桁梁制造规则》、《山西中南部铁路通道钢桁梁招标文件》及相应的标准编制本涂装施工方案。
编制引用以下标准:本工程为山西中南部铁路通道钢桁梁现场单孔架设完成后对工地焊缝及栓接点外露面进行涂装,并进行全桥现场涂层损伤处修补以及最后一道面漆涂装。
1.3山西中南部铁路通道钢桁梁涂装体系涂装体系如下:注:(1)高强螺栓连接部位补涂装见下表: (2)损伤面对于未损伤至底材的区域:去油后对周边涂层实施保护,对损坏区域采用打磨机打磨;周围涂层打磨成坡度,磨出不同漆层的层面,用刷涂方法补涂相应涂层的涂料。
自检、专检各格后,报请监理验收。
二、施工前准备2.1施工人员进场主要工序的施工人员(打磨工、配漆工和涂装工)和管理人员(质检员、带班负责人、现场经理等)应具备相应的涂装施工技能和施工经验。
2.2施工设备进场现场开工前,施工设备进入施工现场。
并对进场设备进行安装调试,对检测仪器或设备检查计量合格证是否过期。
涂装施工设备、机具见表2-1,涂装施工检测装置见表2-2。
涂装施工设备、机具 表2-1涂装施工检测装置表2-22.3涂装材料准备2.3.1油漆(涂料)的准备(1)油漆(涂料)的采购所有构成防护体系采购的油漆都招标文件及设计要求(2)油漆(涂料)的封装和运输所有涂料应装在密闭容器内,容器的大小应方便运输。
每个容器应在侧面贴说明书,包括用途(例如是底漆、中间漆还是面漆)、颜色、批号、生产日期和生产厂。
(3)油漆(涂料)的验收入库仓库保管员应对进库前的涂料验证其合格证/质保书,检查是否与相应的涂料实物相同,相同时方可入库(入库后及时抽样、复验,复验合格并经监理批准后,才能正式入库投入使用).否则拒绝入库,并退回供方更换。
(4)涂料的存放和保存期涂料应存放在专用库房内,库房应防止漏水,有安全、灭火设施;并视需要提供隔热、加热和通风手段保持漆料的合适温度;除非另有说明,在生产厂家建议的贮存期内,没有使用的涂料应予废弃,不得用于永久性工程。
桥梁隧道钢结构保护涂装技术标准

铁路桥隧建筑物大修维修钢结构保护涂装技术标准第3.2.1条钢梁、钢塔架、人行道栏杆支架等都应进行保护涂装,防止钢结构生锈。
第3.2.2条涂装前表面清理:在涂装底漆前,应将钢料表面的污泥、油垢、铁锈、旧漆皮和氧化皮彻底清除干净。
清除方法可采用喷砂、喷丸。
手工清理和溶剂擦洗。
严禁使用腐蚀性物质清理钢表面。
第3.2.3条清理等级及粗糙度要求:1. 清理等级要求根据使用的涂料品种、施工方法和构件部位的不同,涂装对钢结构表面清理等级要求如下:(1)热喷锌、铝或涂装环氧富锌底漆时,钢表面清理应达到S a3级。
(2)涂装酚醛红丹、醇酸红丹、聚氨脂底漆或维护涂装环氧宙锋及热喷锌时,钢表面清理应达到S a2.5级。
(3)箱形梁内表面涂装环氧沥青底漆时,钢表面清理应达到S a2级。
(4)人行道栏杆、扶手、托架、墩台吊篮、围栏等附属结构及铆钉头、螺栓头或局部维护涂装使用红丹底漆时,钢表面清理应达到S t3级。
2. 清理粗糙度要求(1)涂装涂料涂层时,钢表面粗糙度为R z25~60μm;选用最大粗糙度不得超过涂装体系干膜厚度的1/3。
表面粗糙度超过要求时,需加涂一道底漆。
(2)热喷锌或铝金属时,钢表面粗糙度为R z25~100μm;当表向粗糙度超过R z100μm时,涂层应至少超过轮廓峰125~150μm。
第3.2.4条钢梁连接板层之间大于0.5mm的缝隙须将缝内污垢和铁锈清除干净,在第一道底漆干燥后,用石膏腻子填塞,待腻子表面干燥后,方可继续进行涂料涂装。
小于0.5mm的缝隙可用油漆封闭。
第3.2.5条钢梁初始涂装及运营中钢梁重新涂装:1. 钢梁初始涂装如在制造厂进行,应完成底漆、中间漆和第一道面漆涂装工作(节点或拼接部位只进行喷铝或涂无机富锌漆),其余面漆涂装在桥位上进行。
2. 运营中钢梁保护涂装起泡或裂纹或脱落的面积达33%,点锈面积达5%,粉化劣化达四级时,应进行整孔重新涂装。
第3.2.6条钢梁涂装体系:1. 钢梁大面积涂装(l)钢梁大面积涂料涂装体系及最小厚度要求如表3.2.6—1。
《铁路钢桥保护涂装及涂料供货技术条件》等29项技术标准目录(国铁集团 2019.12版)

TB/T
2883.8—1998
15号车钩钩舌
S曲面
校对样板
26
Q/CR
741.11—2019
机车车辆部件检修量具 第11部分:16型和17型车钩检修量具
TB/T
3464—2016
机车车辆车钩缓冲装置计量器具16型和17型车钩检修
量具
27
Q/CR
8
Q/CR
734.1—2019
铁路混凝土用骨料碱活性试验方法化学法
TB/T
2922.2—1998
铁路混凝土用骨料碱活性试验方法化学法
9
Q/CR
734.2—2019
铁路混凝土用骨料碱活性试验方法
砂浆棒法
TB/T
2922.3—1998
铁路混凝土用骨料碱活性试验方法
砂浆棒法
10
Q/CR 735—2019
道镐
741.12—2019
机车车辆部件检修量具 第12部分:承载鞍检修用计量
器具
TB/T
2884.2—2006
铁道货车承载鞍专用计量
器具 第2部分:承载鞍检修用计量器具
28
Q/CR
741.13—2019
机车车辆部件检修量具:第13部分:铁道货车心盘及磨耗盘检修用
量具
TB/T
3198.2—2008
铁道货车心盘及磨耗盘专用量具 第2部分:心盘及磨耗盘检修用
21
Q/CR
741.6—2019
机车车辆部件检修量具 第6部分:15型车车钩综合检查样板
TB/T
2883.4—1998
15号车钩综合
检查样板
22
关于铁路钢梁桥保护涂装的分析

关于铁路钢梁桥保护涂装的分析发布时间:2021-01-29T08:59:04.610Z 来源:《基层建设》2020年第27期作者:赵岩[导读] 摘要:在当今时代的发展背景之下,铁路桥梁拥有着极高的现实性作用,而整体铁路桥梁在构建过程中,军需采取相应的防腐蚀材料对其进行有效的保护,我国铁路桥梁在构建过程中所拥有的耐腐蚀技术,在具体的应用过程中正处于逐步完善的现实状态,基于上述角度,文章对整体铁路桥梁保护涂装所用的重要性以及相应的保护质量影响因素进行了详细的分析,同时对具体的保护涂装采取措施进行有效的探讨,希望能够为同行提供有效的现实性参考。
中国铁路北京局集团有限公司承德工务段河北承德 067000摘要:在当今时代的发展背景之下,铁路桥梁拥有着极高的现实性作用,而整体铁路桥梁在构建过程中,军需采取相应的防腐蚀材料对其进行有效的保护,我国铁路桥梁在构建过程中所拥有的耐腐蚀技术,在具体的应用过程中正处于逐步完善的现实状态,基于上述角度,文章对整体铁路桥梁保护涂装所用的重要性以及相应的保护质量影响因素进行了详细的分析,同时对具体的保护涂装采取措施进行有效的探讨,希望能够为同行提供有效的现实性参考。
关键词:铁路;桥梁保护;涂装应用探讨 1对铁路桥梁保护涂装所拥有的重要性进行分析在具体的应用过程中,由于钢结构自身拥有着较为优质的均匀材质性,并且其自身的力学性能相对较好,在具体的处理过程中其自身的结构断面相对较小,同时其自动相对较轻,并且相应的综合跨越能力较高,在具体大跨度桥梁的构建过程中往往会充分的对钢结构予以有效的应用,同时相应的钢结构构件在具体应用过程中将会充分的应用于各类工业化生产当中,在具体的生产过程中,会对工程预设以及相应的工程拼装架设进行有效的应用,在整体施工中其自身的攻击相对较短,并且其应用效率较高,同时如若相应的钢结构与以损坏同样可以进行有效的加固,因此,在我国的铁路建设过程中,当对大跨度桥梁进行构建过程中往往会采取钢桥梁,而铁路钢桥梁在具体的应用过程中往往会常年暴露在室外环境之内,会受到大气、海水等诸多环境所存在的有害物质的侵蚀,致使其各个部件产生一定程度的现实腐蚀钢结构,在腐蚀过程中,如果遭受相应的腐蚀,将导致整体钢梁杆件的断面被削弱,并且整体钢结构的连接出现松弛,使整体钢结构的综合承受能力无法得到有效的构建,使整体钢结构自身的应用寿命大幅度降低,使整体钢结构在运用过程中的使用功能受到了严重的削弱,由此使车辆及行人的安全受到了严重的威胁,因此,需要充分的对相应的钢结构及相应的附属结构件进行有效效出装保护,防止钢机构在应用过程中出现生锈变形的诸多现实性问题。
浙江沿海钢结构桥梁防腐保护与涂装

浙江交通职业技术学院学报,第21卷第1期,2020年3月Journal of Zhejiang Institute of CommunicationsVol.21No.l,Mar.2020浙江沿海钢结构桥梁防腐保护与涂装马旭涛(浙江公路水运工程咨询有限责任公司,杭州310000)摘要:对浙江沿海主要钢结构桥梁的防腐涂装应用情况进行了文献调研和实地调研,结果表明现有主体工程的防腐涂层防护体系基本达到设计防护要求,主要存在问题是面漆的耐候性以及桥面系钢构件普遍锈蚀问题,并从设计、施工、养护和管理角度提出了钢结构桥梁防腐涂装的提升改进建议,最后展望了未来的长效防腐涂装材料发展方向。
关键词:钢结构桥梁;防腐涂装;涂层体系中图分类号:U448.36文献标识码:A doi:10.3969/j.issn.1671-234X.2020.01.006文章编号:1671-234X(2020)01-0025-061钢结构桥梁防腐涂装概述钢结构桥梁具有强度高、韧性好、制作方便、施工速度快等优点,已广泛应用于铁路、公路及人行天桥。
由于钢结构长期暴露在自然环境中,同时承受着交变荷载,会受到环境介质的腐蚀,特别是在一些环境恶劣的地区,往往会造成钢结构的严重腐蚀⑴,影响桥梁的外观和耐久性。
在钢结构设计建造时,根据自身结构特点和环境条件采用相应的防腐措施,并合理考虑后期的涂层养护,才能确保桥梁的耐久性。
2钢结构桥梁防腐措施常用的桥梁钢结构件防腐蚀措施主要分为两类:一类是机械隔离措施,即采用惰性材料包覆在钢结构表面,隔离水、氧气等腐蚀介质以达到防腐目的,如涂料涂装;另一类是根据电化学腐蚀原理,人为提高钢结构构件的电位,使其处于电位较高的一极,从而达到保护目的,如牺牲阳极保护阴极法。
热浸镀、电弧喷涂为机械屏蔽和阴极保护联合作用。
钢结构桥梁的涂装通常是由具有耐腐蚀、耐候性和施工性能好的底漆、中间漆和面漆组成的综合防腐蚀体系。
海洋大气环境下的金属钢结构防腐涂料体系主要采用防锈底漆(金属喷涂或富锌底漆)、中间封闭漆以及以耐紫外线老化为主要功能的面漆的配套体系。
铁路钢桥保护涂装1527-2004

TB中华人民共和国铁道行业标准TB/T 1527-2004代替TB/T 1527-1995铁路钢桥保护涂装The protection coating of railway steel bridges again corrosion2004-01-30发布2004-08-01实施中华人民共和国铁道部发布前言本标准是对TB/T 1527-1995进行修订。
本标准与原标准相比主要变化如下:——本标准编写规则按GB/T 1.1-2000。
——本标准对原标准中涂装体系作了较大的改动,增加了新的涂装体系。
——本标准采用电弧喷涂金属涂装,取代了原标准中的热喷涂金属涂装。
——本标准栓焊梁摩擦面喷涂采用电弧喷铝和喷涂无机富锌防锈防滑涂料两种工艺,取代了原标准中的热喷铝工艺。
本标准自实施之日起,同时代替TB/T1527-1995。
本标准的附录A、附录B、附录C、附录D和附录E都是资料性附录。
本标准由铁道部标准计量研究所提出并归口。
本标准起草单位:铁道科学研究院金属及化学研究所、铁道部标准计量研究所、中铁山桥集团有限公司、廊坊红黄蓝化工(集团)公司本标准主要起草人:杜存山、李雪春、许金生、姜涛。
本标准于1984年12月14日首次发布,本次修订为第二次。
铁路钢桥保护涂装1 范围本标准规定了铁路钢桥保护涂装技术要求、试验方法和检验规则。
本标准适用于钢桥的初始涂装和钢桥涂膜劣化后的重新涂装和维护性涂装,也适用于桥梁的其它附属钢结构初始涂装、重新涂装和维护性涂装。
2规范性引用文件下列文件中的条款通过本标准的引用而成为本标准的条款。
凡是注日期的引用文件,其随后所有的修改单(不包括勘误的内容)或修订版均不适用于本标准,然而,鼓励根据本标准达成协议的各方研究是否使用这些文件的最新版本。
凡是不注日期的引用文件,其最新版本适用于本标准。
GB/T 470-1997 锌锭GB/T 1763-1979 漆膜耐化学试剂性测定法GB/T 1765-1979 测定耐湿热、耐盐雾、耐侯性(人工加速)的漆膜制备法GB/T 3190-1996 变形铝及铝合金化学成分GB/T 4956-1985 磁性金属基体上非磁性覆盖层厚度测量磁性方法GB/T 5210-1985 涂层附着力的测定法拉开法GB/T 6060.5-1988 表面粗糙度比较样块抛(喷)丸、喷砂加工表面GB 6514 涂装作业安全规程涂漆工艺安全及其通风净化GB 7692 涂装作业安全规程涂漆前处理工艺安全及其通风净化GB/T 8923-1988 涂装前钢材表面锈蚀等级和除锈等级GB/T 9286-1998 色漆和清漆漆膜的划格试验GB/T 9793-1997 金属和其他无机覆盖层热喷涂锌、铝及其合金GB/T 11373-1989 热喷涂金属件表面预处理通则GB/T 11374-1989 热喷涂涂层厚度的无损测量方法GB 11375 金属和其他无机覆盖层热喷涂操作安全GB/T 13452.2-1992 色漆和清漆漆膜厚度的测定GB/T 14522-1993 机械工业产品用塑料、涂料、橡胶材料人工气候加速试验方法TB/T 2137-1990 铁路钢桥栓接板面抗滑移系数试验方法TB/T 2486-1994 铁路钢梁涂膜劣化评定TB/T 2772-1997 铁路钢桥用防锈底漆供货技术条件TB/T 2773-1997 铁路钢桥用面漆、中间漆供货技术条件YB/T 5149-1993 铸钢丸YB/T 5150-1993 铸钢砂3 技术要求3.1钢梁的初始涂装和重新涂装3.1.1涂装前表面清理3.1.1.1涂装前钢表面除锈等级要求3.1.1.1.1 电弧喷涂锌、铝或涂装富锌防锈底漆时,钢表面清理应达到GB/T 8923-1988规定的Sa3级,外观相当GB/T 8923-1988规定的ASa3、BSa3、CSa3。
铁路钢桥各部位防腐蚀的分类及涂装

铁路钢桥各部位防腐蚀的分类及涂装铁路钢梁防腐涂装体系目前一直延用我国户外气候类型的区域分布图,分为干燥地区、潮湿地区、恶劣地区。
其寒冷、寒温、暖温、干热区域的内陆区为干燥地区;亚湿热、温热区域为潮湿地区;含有盐雾的沿海地区、含有二氧化硫的大气污染地区或风砂地区为恶劣地区。
按这三种地区制定的相应的涂装体系无疑是正确的。
在这三种自然气候以外还应充分注意钢梁在各使用部位不同功能对防腐涂装的要求。
因为部位不同所接触腐蚀介质不同,其腐蚀速度相差很大。
钢桥各部位的分类及对防腐蚀的要求铁路钢桥类型可分为桁梁和板梁。
板梁分为上承板梁和下承扳梁如下图所示:腐蚀环境下的钢结构主要指钢梁钢轨以下部位。
如下承桁梁的下弦杆、纵梁、横梁等;上承板梁的所有部位。
从防腐要求来看,主要分两大部位,即腐蚀环境下的钢结构和普通环境下的钢结构。
主要腐蚀物的来源有客车上自由排放的各种污物、污水,通过轨道污染所有下面的钢结构;再者是货车运行中飘落的各种粉尘,如煤粉尘、含酸或碱性货物的粉尘等。
受腐蚀最严重的部位是桥枕下的纵梁上盖板顶面与上承板梁的上翼缘顶面。
其次是雨水和阳光紫外线的侵蚀。
普通环境下的钢结构主要指钢梁钢轨以上部位的钢结构,如下承桁梁的上弦杆、竖杆、斜杆、上平联等。
这些部位的腐蚀介质主要是雨水的侵蚀、阳光紫外线的照射等。
钢梁箱型杆件内部的腐蚀条件:箱型杆在钢梁的上弦和下弦都有存在。
由于是内部可以不区分腐蚀环境和一般环境的条件之分。
箱型杆内部的腐蚀介质是大气中潮湿气体的侵入。
因此阴暗潮湿是腐蚀的主要根源。
高强螺栓连接的栓接点:钢梁高强螺栓的栓接点不允许有上下贯穿的缝隙存在,也就是说在板缝之间不能有流锈水的现象存在,因此栓节点的腐蚀主要是雨水产生的缝隙绣蚀,必须用高质量的油漆将板缝保护好,以防栓节点的锈蚀。
纵梁上盖板顶面与板梁上翼缘顶面(放桥枕面):该面是全桥腐蚀最严重的地方,也是最难处理的地方。
该处主要是行车时桥枕震动磨擦对涂层的破坏以及列车下落的各种污物的侵蚀,要求涂层有耐磨性。
- 1、下载文档前请自行甄别文档内容的完整性,平台不提供额外的编辑、内容补充、找答案等附加服务。
- 2、"仅部分预览"的文档,不可在线预览部分如存在完整性等问题,可反馈申请退款(可完整预览的文档不适用该条件!)。
- 3、如文档侵犯您的权益,请联系客服反馈,我们会尽快为您处理(人工客服工作时间:9:00-18:30)。
TB中华人民共和国铁道行业标准TB/T 1527-2004代替TB/T 1527-1995 铁路钢桥保护涂装The protection coating of railway steel bridges again corrosion 2004-01-30发布2004-08-01实施中华人民共和国铁道部发布前言本标准是对TB/T 1527-1995进行修订。
本标准与原标准相比主要变化如下:——本标准编写规则按GB/T 。
——本标准对原标准中涂装体系作了较大的改动,增加了新的涂装体系。
——本标准采用电弧喷涂金属涂装,取代了原标准中的热喷涂金属涂装。
——本标准栓焊梁摩擦面喷涂采用电弧喷铝和喷涂无机富锌防锈防滑涂料两种工艺,取代了原标准中的热喷铝工艺。
本标准自实施之日起,同时代替TB/T1527-1995。
本标准的附录A、附录B、附录C、附录D和附录E都是资料性附录。
本标准由铁道部标准计量研究所提出并归口。
本标准起草单位:铁道科学研究院金属及化学研究所、铁道部标准计量研究所、中铁山桥集团有限公司、廊坊红黄蓝化工(集团)公司本标准主要起草人:杜存山、李雪春、许金生、姜涛。
本标准于1984年12月14日首次发布,本次修订为第二次。
铁路钢桥保护涂装1 范围本标准规定了铁路钢桥保护涂装技术要求、试验方法和检验规则。
本标准适用于钢桥的初始涂装和钢桥涂膜劣化后的重新涂装和维护性涂装,也适用于桥梁的其它附属钢结构初始涂装、重新涂装和维护性涂装。
2规范性引用文件下列文件中的条款通过本标准的引用而成为本标准的条款。
凡是注日期的引用文件,其随后所有的修改单(不包括勘误的内容)或修订版均不适用于本标准,然而,鼓励根据本标准达成协议的各方研究是否使用这些文件的最新版本。
凡是不注日期的引用文件,其最新版本适用于本标准。
GB/T 470-1997 锌锭GB/T 1763-1979 漆膜耐化学试剂性测定法GB/T 1765-1979 测定耐湿热、耐盐雾、耐侯性(人工加速)的漆膜制备法GB/T 3190-1996 变形铝及铝合金化学成分GB/T 4956-1985 磁性金属基体上非磁性覆盖层厚度测量磁性方法GB/T 5210-1985 涂层附着力的测定法拉开法GB/T 表面粗糙度比较样块抛(喷)丸、喷砂加工表面GB 6514 涂装作业安全规程涂漆工艺安全及其通风净化GB 7692 涂装作业安全规程涂漆前处理工艺安全及其通风净化GB/T 8923-1988 涂装前钢材表面锈蚀等级和除锈等级GB/T 9286-1998 色漆和清漆漆膜的划格试验GB/T 9793-1997 金属和其他无机覆盖层热喷涂锌、铝及其合金GB/T 11373-1989 热喷涂金属件表面预处理通则GB/T 11374-1989 热喷涂涂层厚度的无损测量方法GB 11375 金属和其他无机覆盖层热喷涂操作安全GB/T 色漆和清漆漆膜厚度的测定GB/T 14522-1993 机械工业产品用塑料、涂料、橡胶材料人工气候加速试验方法TB/T 2137-1990 铁路钢桥栓接板面抗滑移系数试验方法TB/T 2486-1994 铁路钢梁涂膜劣化评定TB/T 2772-1997 铁路钢桥用防锈底漆供货技术条件TB/T 2773-1997 铁路钢桥用面漆、中间漆供货技术条件YB/T 5149-1993 铸钢丸YB/T 5150-1993 铸钢砂3 技术要求钢梁的初始涂装和重新涂装3.1.1涂装前表面清理3.1.1.1涂装前钢表面除锈等级要求3.1.1. 电弧喷涂锌、铝或涂装富锌防锈底漆时,钢表面清理应达到GB/T 8923-1988规定的Sa3级,外观相当GB/T 8923-1988规定的ASa3、BSa3、CSa3。
3.1.1.涂装红丹醇酸、红丹酚醛或聚氨酯底漆,钢表面清理应达到GB/T 8923-1988规定的级,外观相当该标准规定的、、、。
3.1.1.桥栏杆、扶手、人行道托架、墩台吊篮等桥梁附属钢结构涂装红丹防锈底漆,箱形梁内表面涂装环氧沥青涂料时,钢表面清理应达到GB/T 8923-1988规定的Sa2级,外观相当该标准规定的BSa2、CSa2、DSa2。
附属钢结构的光圆钢涂装红丹防锈底漆时,钢表面清理应达到GB/T 8923-1988规定的St3级,外观相当该标准规定的BSt3、CSt3、DSt3。
3.1.1.2 涂装前钢表面粗糙度要求3.1.1.涂装涂料涂层时,钢表面粗糙度规定为Rz25μm~60μm,即符合GB/T 规定的粗糙度样块为Ra6.3μm和Ra12.5μm之间的粗糙度要求。
3.1.1.电弧喷涂锌或铝金属时,钢表面粗糙度规定为Rz50μm~100μm,即符合GB/T 规定的粗糙度样块为Ra12.5μm和Ra25.0μm之间的粗糙度要求。
3.1.1. 磨料粒度和表面粗糙度的关系,可参照附录A(资料性附录)。
3.1.1. 涂装涂料涂层时,选用最大粗糙度不超过涂装体系干膜厚度的1/3,表面粗糙度超过规定时需加涂一道底漆;喷涂锌铝涂层时,如果粗糙度超过Rz100μm时,涂层应超过轮廓峰125μm。
3.1.1.3 钢表面清理用磨料钢表面清理用磨料应使用符合YB/T 5149-1993和YB/T 5150-1993标准规定的钢丸、钢砂,或应使用无盐份和无沾污的石英砂。
3.1.2钢梁的涂料涂装3.1.2.1钢梁涂装体系见表1。
表1 钢梁涂装体系3.1.2.2初始涂装时,钢梁制造厂应完成全部底漆(中间漆)和第一道面漆涂装。
3.1.2.3对于距离水面较近的钢梁底面(包括桁梁下弦杆、纵横梁底面,下承板梁主梁和上承板、箱梁底面)、跨越受污染的河流的钢梁底部应增加涂装底漆一道、中间漆一道。
3.1.3钢梁的电弧喷涂金属涂装3.1.3.1电弧喷铝用铝丝材质应采用GB/T 3190-1996中LF2,含铝量为%以上;3.1.3.2电弧喷锌用锌丝材质应符合GB/T 470-1997的规定,含锌量不低于%;3.1.3.3 金属涂层采用环氧类封孔剂进行封孔时,封孔层厚度无要求,涂覆的封孔剂至不被吸收为止;封孔后应加涂相应的配套涂料。
3.1.4 栓焊梁螺栓连接部分摩擦面涂装3.1.4.1采用电弧喷涂铝,涂层厚度为150μm±50μm或采用无机富锌防锈防滑涂料,涂层厚度为120μm±40μm。
涂层的抗滑移系数不小于。
3.1.4.2 杆件栓接点外露的铝表面、无机富锌防锈防滑涂料表面与涂料涂层搭接处应涂装特制环氧富锌防锈底漆。
钢梁组装后,栓接点外露的铝涂层应按条规定进行涂装。
栓接点螺栓、螺栓头处涂装特制环氧富锌防锈底漆,涂装前螺栓应除油,螺母和垫片应水洗清除皂化膜。
钢梁维护性涂装3.2.1铁路钢梁涂膜劣化类型按TB/T 2486-1994判定。
3.2.2劣化类型为3级粉化时,应清除涂层表面污渍,用细砂纸除去粉化物,然后覆盖2道相应面漆。
3.2.3 当旧涂层未锈蚀,劣化类型为2~3级起泡、裂纹或脱落时,用手动工具或动力工具清理损坏的区域周围疏松的涂层,并延伸至未损坏的涂层区域50mm~80mm坡口,局部涂相应底漆和面漆。
如要保持涂层表面一致,可在局部涂面漆后,全部再覆盖面漆。
3.2.4当旧涂层锈蚀,劣化类型为2~3级生锈时,应清除松散的涂层,直到良好结合的涂层区域为止,旧涂层表面清理应达到PSt31)级,未损坏的涂层区域边缘按条要求处理,然后局部涂装相应防锈底漆和相应中间漆、面漆。
如要保持涂层表面一致,可在局部涂面漆后,全部再覆盖面漆。
3.2.5当旧喷锌或铝涂层发生锈蚀劣化类型为2~3级生锈时,应除去松动的锌或铝涂层和涂料涂层直到良好结合的锌或铝涂层区域为止,钢表面锈蚀清理应达到级。
对于未损坏的涂料和锌或铝涂层区域边缘按条要求处理。
对于电弧喷锌或铝涂层清理部位,也可改涂特制环氧富锌防锈底漆2道,然后涂装相应中间漆和面漆。
涂层质量要求3.3.1涂料涂层表面平整均匀,不允许有剥落、起泡、裂纹、气孔,允许有不影响防护性能的轻微桔皮、流挂、刷痕和少量杂质。
3.3.2 金属涂层表面均匀一致,不允许有起皮、鼓泡、大熔滴、松散粒子、裂纹、掉块,允许有不影响防护性能的轻微结疤、起皱。
3.3.3整个涂装体系涂层间附着力按GB/T 9286-1998规定作划格试验,附着力不低于一级。
3.3.4锌、铝涂层对钢基材附着力按GB/T 9793-1997规定,采用切格试验法时,试验结束后,方格内的涂层不得与基体剥离;采用拉力试验法时,附着力不低于。
涂装作业环境和涂装间隔时间要求3.4.1电弧喷涂锌、铝涂层时作业环境要求与电弧喷涂作业的间隔时间要求,按GB/T 11373-1989规定。
3.4.2 钢结构表面清理后应在4h内完成涂装锌、铝涂层,电弧喷涂锌或铝完成后应立即覆盖封孔剂。
既有线利用列车运行间隔施工时,覆盖封孔剂或涂层前,应对锌或铝涂层表面作清洁处理。
1)PSt3:被清理的表面油漆涂层部分应粘附牢固完好无损,其它部分应无可见的油脂和污物,无粘附不牢的氧化皮、铁锈、油漆涂层和异物,金属基底要有金属光泽。
3.4.3涂装涂料时作业环境要求:水性无机富锌防锈底漆、酚醛漆、醇酸漆、聚氨酯漆、氟碳面漆不允许在气温5℃以下施工,环氧类漆不允许在10℃以下施工;不允许在相对湿度80%以上,雨天、雾天或风沙场合施工。
3.4.4涂装涂料涂层需在上一道涂层实干后,方可涂装下一道漆,底漆、中间漆最长暴露时间不超过7天,两道面漆间隔若超过7天时需用细砂纸打磨成细微毛面。
3.4.5水性无机富锌防锈底漆和氟碳面漆的施工参照附录B的规定进行。
涂装施工安全3.5.1 手工和动力工具除锈、喷射除锈和清除旧涂层等涂装前处理工艺安全,按GB 7692规定进行。
3.5.2涂漆工艺中如贮存、涂料调制、涂装、干燥等劳动安全卫生技术要求按GB 6514规定进行,按该标准规定划出涂漆区、火灾危险区、电气防爆区。
3.5.3 锌、铝喷涂设备的安全操作、操作人员的安全保证和通风保健要求,按GB 11375规定。
4 试验方法表面清理等级检验按GB/T 8923-1988规定除锈等级目视评定方法进行,注意磨料不同造成的外观上差别。
表面粗糙度检验4.2.1表面粗糙度可采用GB/T 规定的比较样块进行粗糙度目视和触觉评定。
4.2.2 表面粗糙度可用触针式表面轮廓仪测量。
4.2.3 测量峰谷深度可用指针式千分尺。
涂层表面质量检查方法采用目视法涂层厚度的检测方法4.4.1涂料涂层干膜厚度和湿膜厚度测量,按GB/T 规定进行。
4.4.2 涂料涂层厚度测量时,以钢梁杆件为一测量单元,在特大杆件表面上以10m2为一测量单元,每个测量单元至少应选取三处基准表面,每一基准表面测量五点,其测量分布如图1,取其算术平均值。
4.4.3锌、铝涂层厚度测量方法按GB/T 4956-1985规定,测点位置按GB/T 11374-1989规定进行。