载货汽车动力传动系统参数优化匹配
几篇关于重型载货汽车动力匹配的文章简述

重型载货汽车传动与动力匹配一、参考文献介绍1《重型载货汽车动力传动系统参数优化匹配》作者:王铁武玉维李萍锋郑利锋王晓2《某重型汽车动力性与燃油经济性仿真与匹配优化》作者:杜子学颜溯刘记君3《重型汽车列车动力系统的优化匹配》作者:张翠平吕秀斌李萍锋胡建功4《基于发动机特性综合评价的传动系优选匹配方法》作者:刚宪约朱江苏柴山5《载货汽车动力传动系统的优化设计》作者:鲍远通范振勇6《基于CRUISE的动力传动系统匹配建模与仿真分析》作者:陈金柱张洁哈建东7《基于燃油经济性的汽车动力传动系匹配优化》作者:杜子学刘记君8《重型载货汽车动力传动系匹配研究》作者:董金松9《重型载货汽车动力传动系统匹配优化》作者:王乾峰10《新型混合动力汽车传动系统设计与工作模式耦合特性分析》作者:杨阳赵新富秦大同段志辉巩慧二、文献摘要1《重型载货汽车动力传动系统参数优化匹配》作者:王铁武玉维李萍锋郑利锋王晓针对某重型载货汽车油耗过高问题,利用仿真软件AVL-Crusie建立了整车性能仿真模型,采用MATLAB软件建立了数学分析方程,并集成到优化平台ISIGHT 软件中,对汽车动力传动系统的速比参数进行了优化设计和匹配。
在满足汽车动力性各项设计指标的前提下,该车辆驱动功率损失率降低了0.28%,6工况循环油耗降低了3.7%。
2《某重型汽车动力性与燃油经济性仿真与匹配优化》作者:杜子学颜溯刘记君根据某重型汽车的结构参数,按照动力传递路线,利用GT-DRIVE软件对该重型汽车进行了建模仿真,并分析了其动力性和燃油经济性。
仿真结果与试验结果的对比验证了该整车模型的正确性。
将此模型导入modeFRONTIER优化软件,采用多目标遗传算法对该车的传动系统参数进行优化,从优化方案中选取几种方案进行比较分析,并根据实际使用的需要确定了该车动力传动系统的最佳匹配方案。
3《重型汽车列车动力系统的优化匹配》作者:张翠平吕秀斌李萍锋胡建功利用CRUISE软件对TY4250半挂牵引车进行了建模,并对其动力性和燃油经济性进行了模拟仿真和计算分析;结合试验结果,验证了TY4250半挂牵引车CRUISE 模型的正确性。
NJ1042轻型货车发动机与传动系参数优化匹配

l 1
≥ … ≥ 止
l
(- 2 9)
为 了防止轻型货车加速过程 中出现动力传递中断 ,应保证当前梢 发动机的最高转速 n 对应的最大车速 U 一 i 一高于换人下一 档时发动机 最大转矩 点转速 I 对应 的车速 U 即: 1 T ,
一
≤ 唑 d l , ‘ — ) =,・, 1 2 ‘n
nT
( — 0 2 1)
1目 十1
23N 14 . J0 2基本参数及优化结果 汽车总质量 m= 4 0 g 4 5 k ,轮胎滚动半径 R = . 6 03 m,空气阻力系数 5 Cm . 汽车 迎 风 面积 A 34m 传 动 阻力 系 数 f002, 油 密 度 f06 4, = .4 , = .1 燃 p 07 2 g ( = .2  ̄/ 汽油 )变速器各挡速 比: c ,
1 ——预期最高车速 1 满足最大爬坡度要求 , 则有:
i ≥j
i
…
— —
( —5) 2
预期最 大爬坡度
(— 2 6)
满足加速时 间要求 , 则有:
t ≤t
t 预期加速 时间 对 于轻型货车 , 直接 挡最大动力 因数一 般为 00—0O , .5 .8 因此满足 直接挡最 大动力 因数要求 , 则有:
和燃 油经济性 。 本文以 N 14 轻型货车为研 究对象, 用数学模型和优化方法 , J0 实例验证 了在 动力性 下降很 小的条件下 , 通过 匹配优 化轻型货车的动 力系统可 以改善轻型货车的燃油经济性 。 [ 关键词 ] 传动 系 优化 发动机 动力性
1 引言 .
满足最高车速要求 , 则有:
U ≥u (— ) 2 4
在对轻 型货 车的动力系统进行 匹配优 化设计 过程中 ,当发动机和 传 动系参数确定后 , 需要对整车 的使用性 能进行 评价 , 以判断发动机与 传动系统匹配是 否合理 ; 为优化 动力系统以获得更好的综合性能提 也 供依据 , 价的合 理与否直接影 响到优 化决策。汽车的动力性 、 评 燃油经 济性 和排放性是 汽车整 车性能评价 中最重要 、 最基本的组成部分 。 根据发动机原理和汽车理论 ,汽车动力性 和燃 料经济性指标是相 互 矛盾 的, 因为动力性好 , 别是加速性和爬坡 性好 , 特 一般要求 汽车稳 定 行驶 的后备功率大 ; 但对 于燃料经济性来说 , 必然 降低发动机的负荷 率 , 而使燃料经济性变差 。从汽车使用要求来看 , 从 既不可脱离动力性 来 孤立地追求燃料经济性 , 也不能脱离经济性来 孤立 地追求动力性 , 最 佳的设计方案是 汽车 的动力性与燃料经济性之间取得最佳折衷 。 汽车动力性燃料经济性 的综合评价指标 , 该能定 量的反映汽车 应 动 力传动 系统 的匹配程度 ,能够反 映出发 动机动 力性与燃料经济性的 发挥程度 以及汽 车实 际行驶工况所对应 的发动机 工况与其理想工况的 差异。为此 , 本文 以能量效率作为汽车动力性和燃 油经济性综合评价指 标。 2N 14 . J 0 2轻 型 货 车 传 动 系 的 优 化 匹 配 21目标 函数 的建立 . 目 函数是使设计得 以优化 的函数 ,可以用来评价设计方案 的好 标 坏, 建立 目标 函数是整个优化设计过程中的重要 问题。 轻 型货车动力系统 匹配优化 的 目的是使 轻型货 车在保证动力性的 前 提下 , 常用行驶工况下燃 油经济性最佳 , 能满足排放性 的要 求 , 在 并 因此 , 这是一个多 目标优化 问题 。轻型货 车的动力 性 、 油经济性和排 燃 放性指标 既相互联系又相互矛盾 , 建立 目 函数 时 , 标 不能单独考虑动力 性 指标 、 燃油经济性指标或排放性指标 , 实际优 化过程中也很难达到 在 各 单 目 的最优解 。 标 一般通过构造评价函数 , 将这样 的多 目 标优化 问题 转化 为单 目标优化问题 ,然后利用单 目标优化 问题 的求 解方法求m最 优解 , 并把这种最优解 当作多 目标优化问题的最优解l 1 l 。 本文 以轻 型货车 的燃油经济作 为 目 函数 ,采用加权组合法构造 标 评 价函数 , 通过在燃油经济性评价指标 和排 放性评 价指标 中引入加权 因子 , 考虑这 两个分 目 标在综合评价指标 中相对重要程 度方 面的差 异。 由此建立轻型货车动力系统匹配优化设 计的 目标 函数 为:
某载货汽车动力传动系统匹配优化过程

1 研究背景今年由国家统计局发布的相关资料显示,到2014年止我国汽车保有量达到1.5亿辆。
短短的10年,我国民用汽车的保有量从2003年的2380万辆增长到2014年的1.5亿辆。
车辆的快速增长,带来的能源紧缺和环保问题也是非常突出的。
对于物流企业来讲,货运车辆的经济性是影响物流成本的主要因素。
为了解决节能环保问题,人们在不断尝试各种新技术来改善汽车的整车动力性和经济性。
经过汽车研发人员的努力发现车辆整车动力性和经济性除了和车辆搭载的发动机性能紧密联系,同时也取决于整车动力传动系统的合理化匹配。
国内外专家对汽车发动机和传动系统的匹配问题进行了大量的研究,并开发了像AVL-Cruise、GT-SUITE这样的仿真软件。
利用这些软件可以通过仿真技术对传动系统的参数进行优化,达到提高整车性能的目的[1]。
该文就以对某载货汽车发动机和传动系统匹配优化为例,说明使用GT-DRIVE软件进行仿真辅助设计的过程。
2 建模仿真计算分析通过市场调研分析报告可以了解到关于某一市场细分的相关信息,例如:市场中某一载货汽车存在经济性不太好的问题。
为了解决市场问题,需要对该车进行进一步调研,以便确定该车的具体设计目标(假设u x ma ≥h km /115,i max ≥%30,Q z ≤km L /24)。
然后将该车发动机和传动系统进行参数匹配优化,给出理论上最为理想的传动系各部件的传动比。
载货汽车使用优化后的传动系统参数配置就可以使得该车的经济性能有所改善。
根据仿真计算分析的重点不同使用GT-DRIVE软件建模时有三种方式,即静力学、动力学及运动学模型。
分别可以进行基本性能分析、经济性分析和排放性能分析。
该文主要讨论载货汽车的经济性,所以应该选择动力学模型,它可以对汽车的行驶工况进行模拟所以能够准确仿真。
建立模型时只要根据该载货汽车的动力传递路线,再将GT-DRIVE元件库中相关的汽车元件拖入建模区并按动力传递方向进行物理连接,便可以建立所需的仿真模型。
大吨位运输车辆传动系统匹配设计
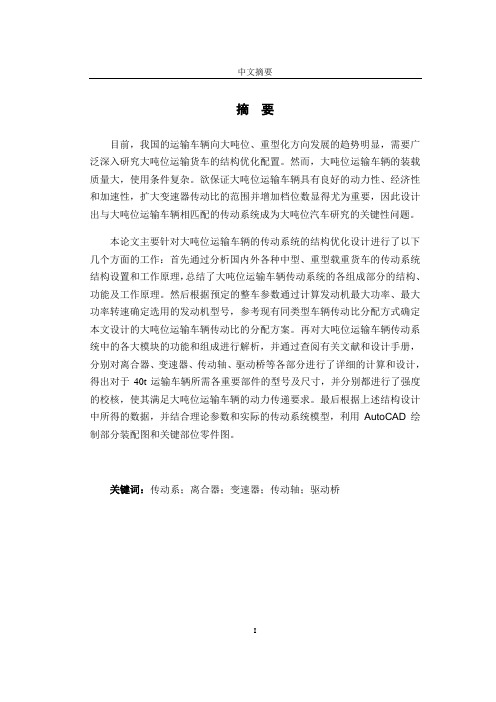
驱动桥位于汽车传动系统的末端,主要由主减速器、差速器、半轴和驱动桥壳等组成。其功用是将万向传动装置传来的发动机转矩通过主减速器、差速器、半轴等传到驱动车轮,实现降低转速、增大转矩;通过主减速器圆锥齿轮副改变转矩的传递方向;通过差速器实现两侧车轮差速作用,保证内、外侧车轮以不同转速转向。
1.3.2
在确定了传动系统方案后,下一步就是结合原始数据,展开各个模块具体结构的设计,然后结合上一步结构设计中所得的数据,用AutoCAD绘制部分零件的装配图和部分零件图。
第二章
所设计的汽车的载重量为40吨,驱动形式为发动机前置、6轮驱动,汽车的最高时速为 。
2.1
2.1.1
汽车的动力性能在很大程度上取决于发动机的功率值。发动机功率越大,动力性能就越好,粗略估计发动机功率时,可根据所要求的最大车速 来确定 ,即:
本论文主要针对大吨位运输车辆的传动系统的结构优化设计进行了以下几个方面的工作:首先通过分析国内外各种中型、重型载重货车的传动系统结构设置和工作原理,总结了大吨位运输车辆传动系统的各组成部分的结构、功能及工作原理。然后根据预定的整车参数通过计算发动机最大功率、最大功率转速确定选用的发动机型号,参考现有同类型车辆传动比分配方式确定本文设计的大吨位运输车辆传动比的分配方案。再对大吨位运输车辆传动系统中的各大模块的功能和组成进行解析,并通过查阅有关文献和设计手册,分别对离合器、变速器、传动轴、驱动桥等各部分进行了详细的计算和设计,得出对于40t运输车辆所需各重要部件的型号及尺寸,并分别都进行了强度的校核,使其满足大吨位运输车辆的动力传递要求。最后根据上述结构设计中所得的数据,并结合理论参数和实际的传动系统模型,利用AutoCAD绘制部分装配图和关键部位零件图。
载货汽车的整车性能匹配分析
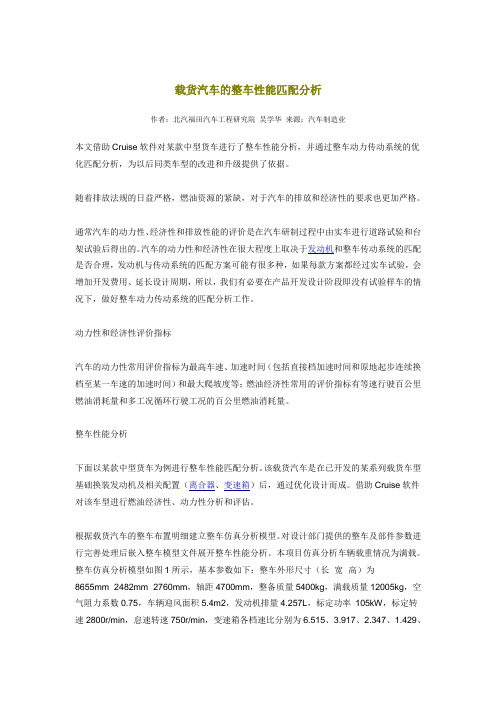
载货汽车的整车性能匹配分析作者:北汽福田汽车工程研究院吴学华来源:汽车制造业本文借助Cruise软件对某款中型货车进行了整车性能分析,并通过整车动力传动系统的优化匹配分析,为以后同类车型的改进和升级提供了依据。
随着排放法规的日益严格,燃油资源的紧缺,对于汽车的排放和经济性的要求也更加严格。
通常汽车的动力性、经济性和排放性能的评价是在汽车研制过程中由实车进行道路试验和台架试验后得出的。
汽车的动力性和经济性在很大程度上取决于发动机和整车传动系统的匹配是否合理,发动机与传动系统的匹配方案可能有很多种,如果每款方案都经过实车试验,会增加开发费用、延长设计周期,所以,我们有必要在产品开发设计阶段即没有试验样车的情况下,做好整车动力传动系统的匹配分析工作。
动力性和经济性评价指标汽车的动力性常用评价指标为最高车速、加速时间(包括直接档加速时间和原地起步连续换档至某一车速的加速时间)和最大爬坡度等;燃油经济性常用的评价指标有等速行驶百公里燃油消耗量和多工况循环行驶工况的百公里燃油消耗量。
整车性能分析下面以某款中型货车为例进行整车性能匹配分析。
该载货汽车是在已开发的某系列载货车型基础换装发动机及相关配置(离合器、变速箱)后,通过优化设计而成。
借助Cruise软件对该车型进行燃油经济性、动力性分析和评估。
根据载货汽车的整车布置明细建立整车仿真分析模型。
对设计部门提供的整车及部件参数进行完善处理后嵌入整车模型文件展开整车性能分析。
本项目仿真分析车辆载重情况为满载。
整车仿真分析模型如图1所示,基本参数如下:整车外形尺寸(长×宽×高)为8655mm×2482mm×2760mm,轴距4700mm,整备质量5400kg,满载质量12005kg,空气阻力系数0.75,车辆迎风面积5.4m2,发动机排量4.257L,标定功率105kW,标定转速2800r/min,怠速转速750r/min,变速箱各档速比分别为6.515、3.917、2.347、1.429、1.00、0.814、R6.061,主减速器速比为6.33。
汽车传动系参数的优化匹配研究(精)

汽车传动系参数的优化匹配研究课题分析:汽车的动力性、燃油经济性和排放特性是汽车的重要性能。
如何在保证汽车具有良好动力性的同时尽量降低汽车的油耗并获得良好的排放特性,是汽车界需要解决的重大问题。
传动系参数的优化匹配设计是解决该问题的主要措施之一。
汽车传动系参数的优化匹配设计是在汽车总质量、质量的轴荷分配、空阻及滚阻等量已确定的情况下,合理地设计和选择传动系参数,从而大幅提高匹配后汽车的动力性、燃油经济性和排放特性。
以往传动系统参数设计依靠大量的实验和反复测试完成,耗时长,费用高,计算机的广泛应用和新的计算方法的出现,使得以计算机模拟计算为基础的传动系设计可在新车的设计阶段就较准确地预测汽车的动力性、经济性和排放特性,经济且迅速。
目前国内围绕汽车传动系参数的设计和优化,主要在以下几个方面展开工作:①汽车传动系参数优化匹配设计评价指标的研究;②汽车传动系各部分数学模型的研究,特别是传动系各部分在非稳定工况下模型的研究;③按给定工况模式的模拟研究;④按实际路况随机模拟的研究;⑤传动系参数优化模型的研究;⑥模拟程序的开发和研究。
检索结果:所属学科:车辆工程中文关键字:汽车传动系参数匹配优化英文关键字:Power train;Optimization;Transmission system; Parameter matching;使用数据库:维普;中国期刊网;万方;Engineering village;ASME Digital Library文摘:维普:检索条件: ((题名或关键词=汽车传动系)*(题名或关键词=参数))*(题名或关键词=优化)*全部期刊*年=1989-2008汽车传动系统参数优化设计1/1【题名】汽车传动系统参数优化设计【作者】赵卫兵王俊昌【机构】安阳工学院,安阳455000【刊名】机械设计与制造.2007(6).-11-13【文摘】主要研究将优化理论引入到汽车传动系参数设计中,以实现汽车的发动机与传动系的最佳匹配,达到充分发挥汽车整体性能的目的。
汽车动力传动系统参数优化匹配方法

1机械传动汽车动力传动系统参数的优化通常包括发动机性能指标的优选,机械变速器传动比的优化和驱动桥速比的优化,以下分别阐述。
7.1汽车发动机性能指标的优选方法 在汽车设计中,发动机的初选通常有两种方法:一种是从保持预期的最高车速初步选择发动机应有功率来选择的,发动机功率应大体上等于且不小于以最高车速行驶时行驶阻力功率之和;一种是根据现有的汽车统计数据初步估计汽车比功率来确定发动机应有的功率。
在初步选定发动机功率之后,还需要进一步分析计算汽车动力性和燃料经济性,最终确定发动机性能指标(如发动机最大转矩,最大转矩点转速等)。
通常在给定汽车底盘参数、整车性能要求(如最大爬坡度max i ,最高车速m ax V ,正常行驶车速下百公里油耗Q ,原地起步加速时间t 等),以及车辆经常运行工况条件下,就可以选择发动机的最大转矩T emax ,及其转矩n M ,最大功率max e P 及其转速P n ,发动机最低油耗率min e g 和发动机排量h V 。
在优选发动机时常常遇到两种情况:一种情况是有几个类型的发动机可供选择,在整车底盘参数和车辆经常行驶工况条件确定时,这属于车辆动力传动系合理匹配问题,可用汽车动力传动系统最优匹配评价指标来处理。
第二种情况是根据整车性能要求和汽车经常行驶工况条件来对发动机性能提出要求,作为发动机选型或设计的依据,而这时发动机性能是未知的。
对于计划研制或未知性能特性指标的发动机性能可看作为发动机设计参数和运行参数的函数,此时,外特性和单位小时燃油消耗率可利用表示发动机的简化模型。
优选汽车发动机参数的方法: (1) 目标函数F (x )目标函数为汽车行驶的能量效率最高。
(2) 设计变量X],,,,[max h M p e em V n n P T X(3) 约束条件1) 发动机性能指标的要求 发动机转矩适应性要求:3.1/1.1≤≤P em T T转矩适应性系数也可参考同级发动机试验值选取。
载货汽车动力传动系统参数优化匹配-25页文档资料
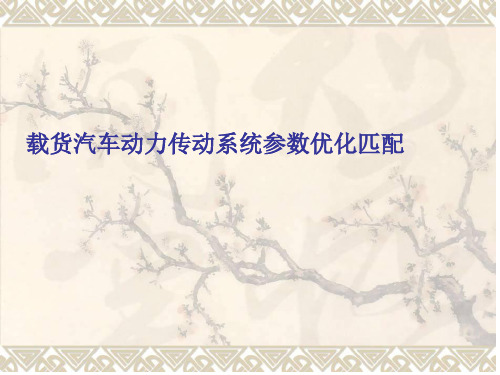
收敛
结束
2020/1/9
18
优化结果--优化前后的传动系速比
变速器档位 1 2 3 4 5 6 7 8 9 10 11 12
主减速器
2020/1/9
原车传动系速比 15.53 12.08 9.39 7.33 5.73 4.46 3.48 2.71 2.10 1.64 1.28 1 4.42
优化后传动系速比 15.5455 12.0714 9.375 7.27273 5.6452 4.381 3.40 2.639 2.048 1.591 1.261 1 4.22
19
优化结果--优化前后的汽车性能指标
指标
最高车速(km/(m/s2) 性
驱动功率损失率
40km/L等速油耗(L/100km)
经
50km/L等速油耗(L/100km)
济
60km/L等速油耗(L/100km)
性 70km/L等速油耗(L/100km)
六工况油耗(L/100km)
驱动功率损 失率f(X1)
六工况f(X2)
F(X)=ω1f(X1)+ω2 f(X2)
动力性约束及 各档速比约束
2020/1/9
16
优化系统集成
2020/1/9
17
优化组合策略
开始计算
速比设计变量 DOE实验设计
未结束
速比的修改
ASA全局搜索 未收敛
RSM 局部搜索
未收敛
任务计算
NLPQL数值优化
加 速 度 性 能
爬 坡 性 能
等 速 百 公 里
多 工 况 循 环
汽 车 能 量 利
油
油
用
耗
耗
率
2020/1/9
重型牵引车动力传动系统优化匹配
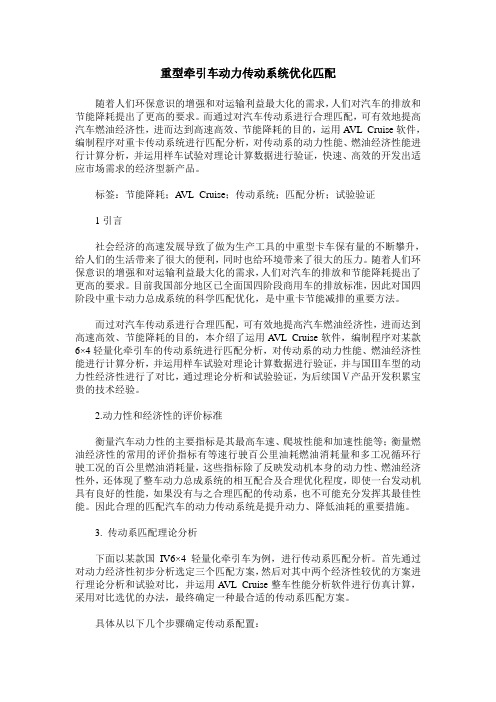
重型牵引车动力传动系统优化匹配随着人们环保意识的增强和对运输利益最大化的需求,人们对汽车的排放和节能降耗提出了更高的要求。
而通过对汽车传动系进行合理匹配,可有效地提高汽车燃油经济性,进而达到高速高效、节能降耗的目的,运用A VL_Cruise软件,编制程序对重卡传动系统进行匹配分析,对传动系的动力性能、燃油经济性能进行计算分析,并运用样车试验对理论计算数据进行验证,快速、高效的开发出适应市场需求的经济型新产品。
标签:节能降耗;A VL_Cruise;传动系统;匹配分析;试验验证1引言社会经济的高速发展导致了做为生产工具的中重型卡车保有量的不断攀升,给人们的生活带来了很大的便利,同时也给环境带来了很大的压力。
随着人们环保意识的增强和对运输利益最大化的需求,人们对汽车的排放和节能降耗提出了更高的要求。
目前我国部分地区已全面国四阶段商用车的排放标准,因此对国四阶段中重卡动力总成系统的科学匹配优化,是中重卡节能减排的重要方法。
而过对汽车传动系进行合理匹配,可有效地提高汽车燃油经济性,进而达到高速高效、节能降耗的目的,本介绍了运用A VL_Cruise软件,编制程序对某款6×4轻量化牵引车的传动系统进行匹配分析,对传动系的动力性能、燃油经济性能进行计算分析,并运用样车试验对理论计算数据进行验证,并与国Ⅲ车型的动力性经济性进行了对比,通过理论分析和试验验证,为后续国Ⅴ产品开发积累宝贵的技术经验。
2.动力性和经济性的评价标准衡量汽车动力性的主要指标是其最高车速、爬坡性能和加速性能等;衡量燃油经济性的常用的评价指标有等速行驶百公里油耗燃油消耗量和多工况循环行驶工况的百公里燃油消耗量,这些指标除了反映发动机本身的动力性、燃油经济性外,还体现了整车动力总成系统的相互配合及合理优化程度,即使一台发动机具有良好的性能,如果没有与之合理匹配的传动系,也不可能充分发挥其最佳性能。
因此合理的匹配汽车的动力传动系统是提升动力、降低油耗的重要措施。
基于AVLCRUISE的某小型货车动力传动系统优化匹配

提高车辆动力性和经济性 降低排放和噪声 优化传动系统效率和可靠性 确保与发动机和底盘的匹配协调
方案目标:提高动力性和经济性,降低排放
方案内容:基于AVL CRUISE进行动力传动系统参数优化,包括发动机、变速器和底盘 等部件
实施步骤:a.建立模型并进行初步分析;b.进行多目标优化设计;c.优化结果验证与评 估;d.方案实施与测试
可进行动力传动系统优化匹配和性 能预测
添加标题
添加标题
支持多种车型和发动机类型
添加标题
添加标题
用户界面友好,易于操作和使用
发动机:提供动力,决定车辆性能 变速器:调节车速,改善驾驶体验 传动轴:传递动力,实现车辆行驶 差速器:控制转向,提高操控稳定性
动力性能不足,加速性和爬坡能力差 燃油经济性差,油耗高 传动效率低,动力损失大 维护成本高,维修不便
XX,a click to unlimited possibilities
汇报人:XX
01
02
03
04
05
06
AVL CRUISE是一款汽车仿真 软件
AVL CRUISE支持多种车型和 动力系统
AVL CRUISE可以模拟车辆的 动力性能和排放性能
AVL CRUISE广泛应用于汽车 行业
车辆动力传动系统仿真软件
提高了车辆的动力性和燃油经济性
优化了传动系统的性能,提高了驾 驶舒适性
添加标题
添加标题
减少了排放,提高了环保性能
添加标题
添加标题
实现了更高效的能量利用,提高了 续航里程
评估方法:通过对比优化前后的动力传动系统性能参数,如功率、扭矩、油耗等, 以及实车试验验证
评估结论:优化后的动力传动系统在性能参数上有所提升,实车试验验证效果良 好,能够提高车辆的动力性和经济性
纯电动厢式物流车动力系统参数匹配与优化
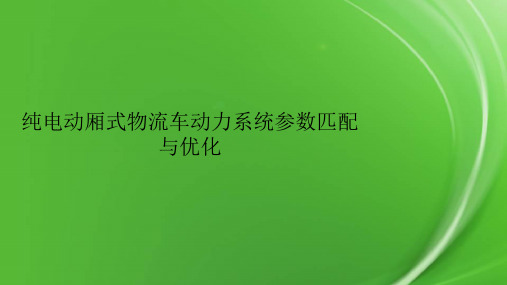
基于ISIGHT/CRUISE集成优化平台,对纯电动厢式物流车传动系 参数进行优化。在满足整车动力性的基础上,尽可能的使整车经 济性达到最优。
5)样车进行试验分析。根据匹配的动力系统参数试制样车,并进 行动力性和经济性试验。
通过对比仿真结果和试验结果,虽略有差异,但均满足各项性能 指标要求,验证了ISIGHT/CRUISE集成优化模型的准确性。本文 对纯电动厢式物流车动力系统参数进行了匹配和优化,同时通过 样车试验验证了匹配优化结果的准确性,为以后该类车型的研发 提供了参考。
纯电动厢式物流车动力系统参数匹配 与优化
汽车的诞生给人类出行带来了便利,同时也造成了环境的破坏以 及能源短缺等问题。在此背景下,纯电动汽车因具有节能环保等 优点成为了未来汽车的发展方向。
然而纯电动汽车续驶里程短、充电速度慢等问题仍没有得到充 分的解决,在某种程度上阻碍了纯电动汽车的普及。因此,在现 有的动力电池技术条件下,如何合理的匹配优化动力系统参数, 提高车辆的续驶里程,是本文研究的重点工作。
具体有如下几个方面:1)理论研究。首先对纯电动厢式物流车进 行了驱动理论分析,同时针对整车的动力性、经济性进行了理论 研究,为动力系统参数匹配提供了理论依据。
2)பைடு நூலகம்车动力系统参数匹配。根据纯电动厢式物流车的整车参数 和性能指标,对动力传动系统参数进行了匹配。
根据最高车速、加速性能和最大爬坡度指标要求,计算出了驱动 电机的峰值功率、额定功率、峰值转速、额定转速、峰值转矩 和额定转矩。根据续驶里程指标要求,计算出了动力电池的标称 电压和标称容量。
根据最高车速、最大爬坡度和附着性能等要求,计算出了传动系 速比。同时根据挡数计算公式,最终采用两挡变速机构。
3)整车模型的建立与性能仿真计算。基于CRUISE仿真软件建立 了整车模型,其重点介绍了驱动电机和动力电池数学模型的建立。
货车传动系统匹配与总体设计
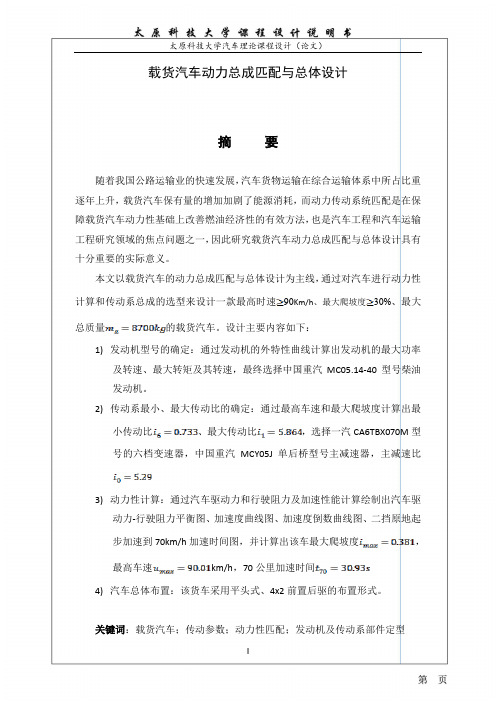
载货汽车动力总成匹配与总体设计摘要随着我国公路运输业的快速发展,汽车货物运输在综合运输体系中所占比重逐年上升,载货汽车保有量的增加加剧了能源消耗,而动力传动系统匹配是在保障载货汽车动力性基础上改善燃油经济性的有效方法,也是汽车工程和汽车运输工程研究领域的焦点问题之一,因此研究载货汽车动力总成匹配与总体设计具有十分重要的实际意义。
本文以载货汽车的动力总成匹配与总体设计为主线,通过对汽车进行动力性计算和传动系总成的选型来设计一款最高时速90Km/h、最大爬坡度30%、最大总质量的载货汽车。
设计主要内容如下:1)发动机型号的确定:通过发动机的外特性曲线计算出发动机的最大功率及转速、最大转矩及其转速,最终选择中国重汽MC05.14-40型号柴油发动机。
2)传动系最小、最大传动比的确定:通过最高车速和最大爬坡度计算出最小传动比、最大传动比,选择一汽CA6TBX070M型号的六档变速器,中国重汽MCY05J单后桥型号主减速器,主减速比3)动力性计算:通过汽车驱动力和行驶阻力及加速性能计算绘制出汽车驱动力-行驶阻力平衡图、加速度曲线图、加速度倒数曲线图、二挡原地起步加速到70km/h加速时间图,并计算出该车最大爬坡度,最高车速km/h,70公里加速时间4)汽车总体布置:该货车采用平头式、4x2前置后驱的布置形式。
关键词:载货汽车;传动参数;动力性匹配;发动机及传动系部件定型目录摘要 (I)课程设计任务书 (1)1设计题目 (1)2性能参数要求 (1)3具体设计任务 (1)4参考文献 (1)第1章整体主要目标参数的初步确定 (2)1.1.发动机的选择 (2)1.1.1.发动机最大功率及转速的确定 (2)1.1.2.发动机最大转矩及转速的确定 (3)1.2轮胎的选择 (4)1.3.传动系最小传动比的确定 (5)1.4传动系最大传动比确定 (5)第2章传动系各总成选型 (6)2.1发动机选型 (6)2.2离合器的选型 (7)2.3变速器的选型 (7)2.4传动轴选型 (8)2.5驱动桥的选型 (8)2.5.1驱动桥结构形式和布置形式的选择 (8)2.5.2主减速器结构形式 (8)2.5.3驱动桥的选型 (8)第3章整车性能计算 (9)3.1汽车动力性能计算 (9)3.1.1发动机外特性曲线 (9)3.1.2汽车驱动力和行驶阻力 (10)3.1.3动力特性因数 (12)3.1.4最大爬坡度及附着率 (13)3.2汽车加速性能计算 (14)3.3汽车功率平衡计算 (18)第4章发动机与传动系部件的确定 (21)4.1发动机与传动系部件确定 (21)4.2总体布置图 (21)第5章设计总结 (22)5.1全文工作总结 (22)5.2设计心得体会 (22)参考文献 (23)课程设计任务书课程设计任务书1设计题目载货汽车动力总成匹配与总体设计2性能参数要求根据给定的参数,设计一辆最高速度、最大爬坡度的载货汽车表0-1 设计参数表额定装载质量(kg)最大总质量(Kg)比功率(Kw/t)比转矩(Nm/t)学号5000 8700 20 47 203具体设计任务1)查阅相关资料,分析设计题目,进行发动机、离合器、变速箱传动轴、驱动桥以及车轮的选型设计。
EQ1091载货汽车动力系统参数匹配与正交优化
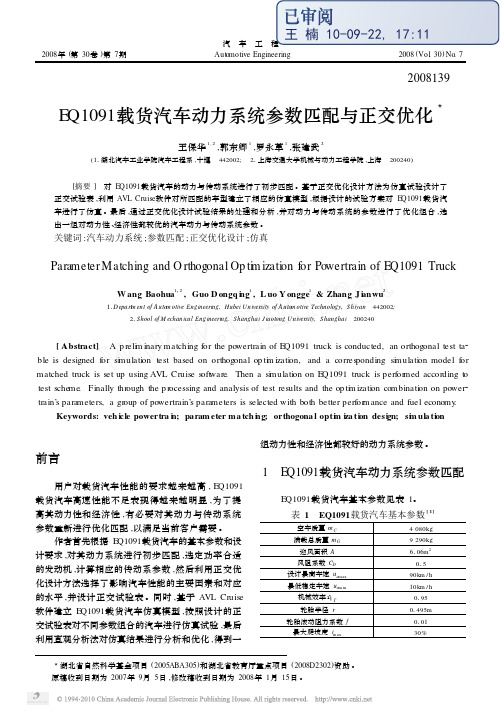
4 080kg 9 290kg 6106m2
015 90km / h 10km / h
0195 01495m源自轮胎滚动阻力系数 f0101
最大爬坡度 imax
30%
3 湖北省自然科学基金项目 (2005ABA305)和湖北省教育厅重点项目 (2008D2302)资助 。 原稿收到日期为 2007年 9月 5日 ,修改稿收到日期为 2008年 1月 15日 。
最大转矩 Te. max /N ·m 415 ( 1 400 r/m in时 ) 550 ( 1 800 r/m in时 )
怠速转速 nm in / r·m in - 1
500
800
最高转速 ne. max / r·m in - 1
3 000
2 500
时 ,变速器 1挡变速比 ig1必须满足
ig1
≥mG g ( fco sαmax + sinαmax ) η Te. max i0 T
11113 发动机型号选择
根据初步确定的发动机功率和目前市场上发动
机现有产品 ,可选择 EQ61002Ⅰ汽油机和某型 4 缸 柴油机 ,其基本参数见表 2。
表 2 EQ61002Ⅰ和某型 4缸柴油机基本参数
名 称
EQ61002Ⅰ
某型 4缸柴油机
最大功率 Pe. max / kW
125 ( 3 000 r/m in时 ) 110 ( 2 200 r/m in时 )
发动机有 2种选择 : EQ61002Ⅰ汽油机和某型 4 缸柴油机 ,并以此作为 2 个水平 。发动机水平数见 表 4。
表 4 发动机 (因素 A )水平数确定
水平 1
水平 2
发动机
EQ 6100 2Ⅰ汽油机
重型载货汽车动力传动系统参数优化匹配
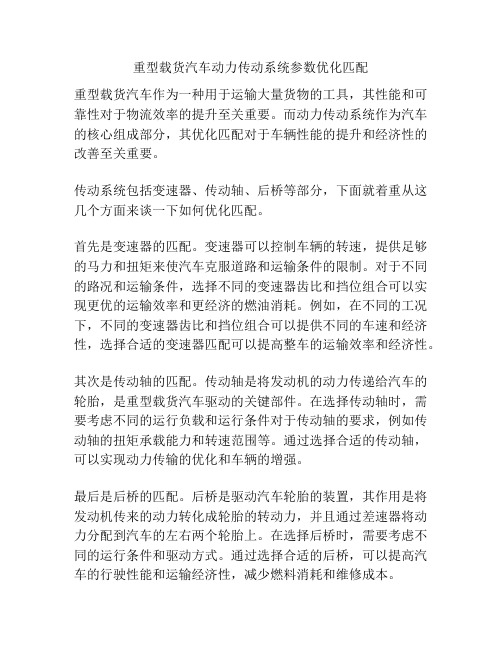
重型载货汽车动力传动系统参数优化匹配重型载货汽车作为一种用于运输大量货物的工具,其性能和可靠性对于物流效率的提升至关重要。
而动力传动系统作为汽车的核心组成部分,其优化匹配对于车辆性能的提升和经济性的改善至关重要。
传动系统包括变速器、传动轴、后桥等部分,下面就着重从这几个方面来谈一下如何优化匹配。
首先是变速器的匹配。
变速器可以控制车辆的转速,提供足够的马力和扭矩来使汽车克服道路和运输条件的限制。
对于不同的路况和运输条件,选择不同的变速器齿比和挡位组合可以实现更优的运输效率和更经济的燃油消耗。
例如,在不同的工况下,不同的变速器齿比和挡位组合可以提供不同的车速和经济性,选择合适的变速器匹配可以提高整车的运输效率和经济性。
其次是传动轴的匹配。
传动轴是将发动机的动力传递给汽车的轮胎,是重型载货汽车驱动的关键部件。
在选择传动轴时,需要考虑不同的运行负载和运行条件对于传动轴的要求,例如传动轴的扭矩承载能力和转速范围等。
通过选择合适的传动轴,可以实现动力传输的优化和车辆的增强。
最后是后桥的匹配。
后桥是驱动汽车轮胎的装置,其作用是将发动机传来的动力转化成轮胎的转动力,并且通过差速器将动力分配到汽车的左右两个轮胎上。
在选择后桥时,需要考虑不同的运行条件和驱动方式。
通过选择合适的后桥,可以提高汽车的行驶性能和运输经济性,减少燃料消耗和维修成本。
在重型载货汽车动力传动系统的参数优化匹配过程中,需要综合考虑车辆的负载能力、行驶条件以及发动机的功率和扭矩要求,对变速器、传动轴和后桥进行综合匹配,实现最优化的整车性能和经济性。
在车辆的使用过程中,需要根据实际情况进行调整和维护,以保证汽车的稳定性、可靠性和经济性。
在重型载货汽车的动力传动系统中,除了变速器、传动轴和后桥之外,还有液压传动系统、制动系统和转向系统等部分也需要注意优化匹配。
液压传动系统的匹配需要根据车辆的工作负载和运行环境进行优化,选择合适的液压泵和排量、压力等参数,以保证动力传输的效率和可靠性。
重型载货汽车动力传动系统匹配优化.
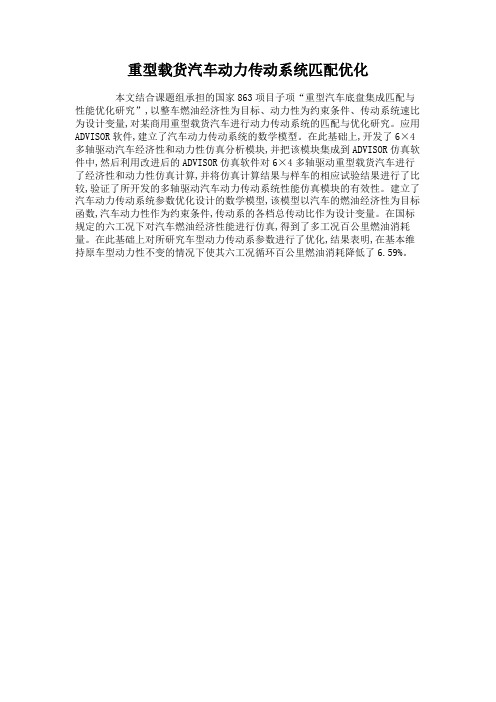
重型载货汽车动力传动系统匹配优化
本文结合课题组承担的国家863项目子项“重型汽车底盘集成匹配与性能优化研究”,以整车燃油经济性为目标、动力性为约束条件、传动系统速比为设计变量,对某商用重型载货汽车进行动力传动系统的匹配与优化研究。
应用ADVISOR软件,建立了汽车动力传动系统的数学模型。
在此基础上,开发了6×4多轴驱动汽车经济性和动力性仿真分析模块,并把该模块集成到ADVISOR仿真软件中,然后利用改进后的ADVISOR仿真软件对6×4多轴驱动重型载货汽车进行了经济性和动力性仿真计算,并将仿真计算结果与样车的相应试验结果进行了比较,验证了所开发的多轴驱动汽车动力传动系统性能仿真模块的有效性。
建立了汽车动力传动系统参数优化设计的数学模型,该模型以汽车的燃油经济性为目标函数,汽车动力性作为约束条件,传动系的各档总传动比作为设计变量。
在国标规定的六工况下对汽车燃油经济性能进行仿真,得到了多工况百公里燃油消耗量。
在此基础上对所研究车型动力传动系参数进行了优化,结果表明,在基本维持原车型动力性不变的情况下使其六工况循环百公里燃油消耗降低了6.59%。
汽车动力传动系统参数优化匹配方法

机械传动汽车动力传动系统参数的优化通常包括发动机性能指标的优选,机械变速器传动比的优化和驱动桥速比的优化,以下分别阐述。
7.1汽车发动机性能指标的优选方法 在汽车设计中,发动机的初选通常有两种方法:一种是从保持预期的最高车速初步选择发动机应有功率来选择的,发动机功率应大体上等于且不小于以最高车速行驶时行驶阻力功率之和;一种是根据现有的汽车统计数据初步估计汽车比功率来确定发动机应有的功率。
在初步选定发动机功率之后,还需要进一步分析计算汽车动力性和燃料经济性,最终确定发动机性能指标(如发动机最大转矩,最大转矩点转速等)。
通常在给定汽车底盘参数、整车性能要求(如最大爬坡度max i ,最高车速max V ,正常行驶车速下百公里油耗Q ,原地起步加速时间t 等),以及车辆经常运行工况条件下,就可以选择发动机的最大转矩T emax ,及其转矩n M ,最大功率max e P 及其转速P n ,发动机最低油耗率min e g 和发动机排量h V 。
在优选发动机时常常遇到两种情况:一种情况是有几个类型的发动机可供选择,在整车底盘参数和车辆经常行驶工况条件确定时,这属于车辆动力传动系合理匹配问题,可用汽车动力传动系统最优匹配评价指标来处理。
第二种情况是根据整车性能要求和汽车经常行驶工况条件来对发动机性能提出要求,作为发动机选型或设计的依据,而这时发动机性能是未知的。
对于计划研制或未知性能特性指标的发动机性能可看作为发动机设计参数和运行参数的函数,此时,外特性和单位小时燃油消耗率可利用表示发动机的简化模型。
优选汽车发动机参数的方法: (1) 目标函数F (x )目标函数为汽车行驶的能量效率最高。
(2) 设计变量X],,,,[max h M p e em V n n P T X(3) 约束条件1) 发动机性能指标的要求 发动机转矩适应性要求:3.1/1.1≤≤P em T T转矩适应性系数也可参考同级发动机试验值选取。
- 1、下载文档前请自行甄别文档内容的完整性,平台不提供额外的编辑、内容补充、找答案等附加服务。
- 2、"仅部分预览"的文档,不可在线预览部分如存在完整性等问题,可反馈申请退款(可完整预览的文档不适用该条件!)。
- 3、如文档侵犯您的权益,请联系客服反馈,我们会尽快为您处理(人工客服工作时间:9:00-18:30)。
设
计
约束条件
变速器与主减速速比
驱动功率损 失率f(X1)
六工况f(X2)
F(X)=ω1f(X1)+ω2 f(X2)
动力性约束及 各档速比约束
2020/9/10
16
优化系统集成
2020/9/10
17
优化组合策略
开始计算
速比设计变量 DOE实验设计
未结束
速比的修敛
任务计算
NLPQL数值优化
收敛
结束
2020/9/10
18
优化结果--优化前后的传动系速比
变速器档位 1 2 3 4 5 6 7 8 9 10 11 12
主减速器
2020/9/10
原车传动系速比 15.53 12.08 9.39 7.33 5.73 4.46 3.48 2.71 2.10 1.64 1.28 1 4.42
2020/9/10
10
列车模型
2020/9/10
11
列车仿真结果——经济性
2020/9/10
12
列车仿真结果——动力性
2020/9/10
13
参数敏感分析
2020/9/10
14
参数敏感分析
传动效率>总质量>空气阻力系数>滚动阻力系数
2020/9/10
15
传动系统参数优化
设计变量
参
数
优
化
目标函数
挡
计
规
算
律
最最 大高 爬车 坡速 度
等多 速工 百况 公燃 里油 油经 耗济
性
7
牵引汽车模型
2020/9/10
8
模型的验证
实验项目
初速50km/h滑行距离(m)
动 最高车速(km/h)
力 性 能
直接档最低稳定车速 (km/h)
经 等速 30 km/h
济 行驶 性 燃料 能 消耗
量
40 km/h 50 km/h 60 km/h
优化后传动系速比 15.5455 12.0714 9.375 7.27273 5.6452 4.381 3.40 2.639 2.048 1.591 1.261 1 4.22
19
优化结果--优化前后的汽车性能指标
指标
最高车速(km/h)
动
最大爬坡度(%)
力
最大加速度(m/s2) 性
驱动功率损失率
40km/L等速油耗(L/100km)
经
50km/L等速油耗(L/100km)
济
60km/L等速油耗(L/100km)
性 70km/L等速油耗(L/100km)
六工况油耗(L/100km)
2020/9/10
优化前 91.349 32.87
2.22 0.8557 30.78
32.81
35.20 38.32 39.22
优化后 95.68 31.06 2.15 0.8533 30.68
通TY4250载货汽车的优化结果对比可知,该 优化方案能够达到良好的优化效果。因此本 文所阐述的优化匹配理论和采用的优化技术 策略是有效的,可以应用到今后的整车开发 中,为整车性能的改善提供了可能途径。
2020/9/10
21
进一步工作
利用计算机仿真技术对汽车性能模拟仿真是可行的, 但是这个过程需要大量的计算准备工作。由于任务的 多样性、互异性,该工作变得十分艰巨。因此如何积 累、建立一个内容翔实、丰富的专家数据库成为一个 亟待解决的问题。
32.8
35.07 37.84 37.77
变化率 4.74% -5.51% -3.15% -0.28% -0.32%
-0.003%
-0.36% -1.25% -3.7%
20
总结
采用加权合成的双目标函数作为综合最优匹 配,采用试验设计加各种组合的优化策略 , 是本文的创新点。对比优化前后:驱动功率 损失率比原车降低了0.28%,六工况循环油耗 比原车降低了3.7%,达到了提高燃油经济性 的目的。
2020/9/10
22
攻读硕士期间发表的论文
2020/9/10
23
请各位老师批评指导!
2020/9/10
24
2020/9/10
4
研究内容
提出了载货汽车动力性、燃油经济性的评价 指标体系
建立整车性能数学模型 仿真分析载货汽车的传动系统,并对载货汽
车主要结构参数进行敏感性分析 动力传动系统参数优化匹配
2020/9/10
5
整车动力性与燃油经济性评价指标
评价指标
动力性
经济性
综合评价指标
最 高 车 速
加 速 度 性 能
载货汽车动力传动系统参数优化匹配
2020/9/10
1
目录
➢ 研究背景与目的 ➢ 主要研究内容 ➢ 结果与分析 ➢ 总结 ➢ 致谢
2020/9/10
2
课题背景
2020/9/10
3
研究目的
合理匹配汽车动力传动系统提高汽车运 输效率,降低燃油消耗
通过载货汽车动力传动系统参数优化匹 配研究,为在载货汽车的动力传动系统 的改善提供了可能的途径
汽车实际行驶工况是一个复杂的人-车-环境三者相互 作用的随机过程,使得汽车传动系统匹配变成了一个 复杂的工作,如何充分考虑不同评估专家的评价值、 不同评价指标、以及目标市场指数等诸多因素的影响, 还有待今后作进一步的研究。目前提出的模糊综合评 判系统,充分考虑了上面的诸多因素,但其操作的复 杂性、以及评价结果的合理性还待进一步的研究。
L/100km 70 km/h
2020/9/10
技术要求 仿真结果
≥800 ≥90
≤30
1142.68 91.35
28.15
15.25 18.79 21.07 23.54 26.69
实验结 果
803.1 91.8 29.8
19.9 20.8 22.0 24.9 28.2
9
模型验证--等速百公里油耗
爬 坡 性 能
等 速 百 公 里
多 工 况 循 环
汽 车 能 量 利
油
油
用
耗
耗
率
2020/9/10
驱 动 功 率 损 失 率
6
整车数学模型的建立
数学模型
发动机模型
换挡规律 动力计算模型 经济性模型
外
万最
特
有佳
性
特动
数
性力
学
数换
模
学挡
型
模规
型律
2020/9/10
最 各及
佳 档动
经 驱力
济 动因
换 力数