机械加工过程中的材料理论作业整理
机械加工中的知识点总结

机械加工中的知识点总结1. 材料的选择在机械加工中,材料的选择至关重要。
常见的金属材料有铁、铜、铝、不锈钢等,而非金属材料有塑料、橡胶、木材等。
选择合适的材料可以有效提高加工效率和产品质量。
需要考虑材料的强度、硬度、耐磨性、耐腐蚀性、导热性等性能指标,同时还要考虑成本和加工性能等因素。
2. 切削理论切削是机械加工的一种常用方法,它包括车削、铣削、钻削、刨削等多种形式。
切削理论是指在切削过程中,刀具与工件之间的相互作用规律。
在切削理论中,有切削力、刀具磨损、热变形、表面质量等重要内容。
掌握切削理论可以有效提高加工效率和降低加工成本。
3. 机床的选择机床是机械加工的重要设备,它包括车床、铣床、钻床、磨床等。
不同的机床适用于不同的加工工艺,选择合适的机床可以提高加工效率和产品质量。
在选择机床时,需要考虑加工工件的形状、尺寸和材料,同时还要考虑加工精度和生产效率等因素。
4. 加工工艺机械加工的加工工艺包括粗加工和精加工两个阶段。
粗加工是指将工件的毛坯加工成近似形状的工艺过程,通常采用车削、铣削、钻削等方法。
精加工是指将粗加工后的工件进行精细加工,使其达到设计要求的工艺过程,通常采用磨削、拉削、滚削等方法。
5. 数控技术数控技术是机械加工中的一种先进技术,它通过计算机控制机床实现加工过程。
数控技术具有高精度、高效率、多样化加工等优点,广泛应用于航空、航天、汽车等高端制造领域。
掌握数控技术可以提高加工精度和生产效率。
6. 自动化生产自动化生产是指通过自动化设备和系统实现生产过程的自动化。
在机械加工中,自动化生产可以提高生产效率、降低劳动强度、保证产品质量等多方面的优势。
常见的自动化设备有自动送料机、自动上下料机、自动检测设备等。
7. 质量控制质量控制是机械加工中的重要环节,它包括工艺规程的制定、检验标准的确定、质量管理体系的建立等内容。
通过严格的质量控制可以保证产品的质量和稳定性,提高用户满意度和企业竞争力。
机械工程材料作业及思考题大全讲解

思考题
1.什么是强度?什么是硬度?硬度与耐磨性关系如何? 2.实际晶体中存在哪些晶体缺陷?它们对金属性能有什么影响? 3.试比较下列铸造条件下(其它条件相同),铸件晶粒的大小。
① 金属模浇注与砂模浇注; ② 铸成薄壁件与铸成厚壁件; ③ 高温浇注与低温浇注; ④ 浇注时采用振动与不采用振动; 4.什么是热处理?有哪些常用的热处理方法? 5.什么是晶粒度?晶粒大小对力学性能的影响如何?
W18Cr4V、GCr15、Cr12MoV
分别用20钢和45钢制造齿轮各一个,要求齿面具有高的硬度和耐
磨性,问应采用何种热处理工艺?热处理的目的是什么?热处理 后在组织和性能上有什么不同?
试卷三
试为下列工具选材,并确定热处理方式.
(1)锉刀; (2)丝锥; (3)滚动轴承; 4)自行车座簧 备选材料: 45、T8、T12、40Cr、9SiCr、 65Mn、W18Cr4V 、
11.什么是淬火临界冷却速度?
12. 两个碳质量分数为1.2%的碳钢薄试样,分别加热到 780℃和900℃,保温相同时间奥氏体化后,以大于淬火临 界冷却速度的速度冷却至室温。试分析:
① 哪个温度加热淬火后马氏体晶粒较粗大? ② 哪个温度加热淬火后马氏体碳含量较多? ③ 哪个温度加热淬火后残余奥氏体较多? ④ 哪个温度加热淬火后未溶渗碳体较多? ⑤ 你认为哪个温度加热淬火合适?为什么?
起加热到1000℃保温,当出炉后再次吊装工件时,钢丝绳发 生断裂,试分析其原因。
试卷二
简述化学热处理的基本过程。 什么是晶粒度?晶粒大小对金属的性能有何影响? 指出下列各钢的种类,并指明有下划线的数字和符号的含义 。
①40Cr ②1Cr18Ni9Ti ③GCr15 ④T12A ⑤QT600-03 ⑥9SiCr
机加工材料知识点总结

机加工材料知识点总结一、机加工材料介绍机加工材料是指在机械加工过程中用来切削、研磨、焊接以及其他工艺操作的原料。
它们的性能直接影响着加工的效率和加工零件的质量。
不同的材料在机加工过程中的性能也不同,因此工程师需要了解不同材料的特性,并选择合适的材料来满足具体加工需求。
机加工材料主要分为金属材料、非金属材料和复合材料三大类。
金属材料是一类具有金属元素组成的材料,通常具有良好的导电性、导热性和机械性能。
主要包括钢、铁、铜、铝、镁、镍、钛等。
金属材料在机加工中广泛应用,因为它们具有较好的机加工性能、刚性和耐磨性。
非金属材料主要包括塑料、橡胶、陶瓷、玻璃等材料。
它们通常具有较好的耐化学性和耐磨性,但机加工性能较差。
非金属材料在一些特殊的机加工场合也有一定的应用。
复合材料是一种将不同材料通过成型加工而成的新型材料,通常具有多种材料的优点。
例如碳纤维复合材料,具有较好的强度和刚度,而且比重轻,适用于制造轻量化零件。
复合材料在航空航天、汽车、船舶等领域有着广泛的应用。
二、金属材料1. 钢钢是一种铁和碳的合金,通常含有少量其他元素形成合金钢。
钢的硬度、强度和塑性可以根据不同的成分来调整,因此钢材广泛应用于机床、建筑、汽车、船舶等领域。
2. 铁铁是一种常见的金属材料,具有良好的导电性和导热性。
在机加工中,铁的硬度较低,切削性能较好,适用于一些易加工的零件。
3. 铜铜是一种良好的导电性材料,常用于制造电气零件和导热器件。
在机加工中,铜的软度较大,易切削,但刀具磨损较快。
4. 铝铝是一种轻金属,在机加工中广泛应用。
它的比重轻、强度高、导热性好,适用于制造航空零件和汽车零件。
5. 镁镁是一种轻质金属,具有良好的机加工性能,适用于制造航空零件和航天零件。
6. 镍镍是一种具有抗腐蚀性和高温强度的合金材料,广泛应用于化工、航空航天等领域。
7. 钛钛是一种具有轻量化、高强度和耐腐蚀性的金属材料,适用于航空航天、船舶等高端领域。
机械工程材料作业整理
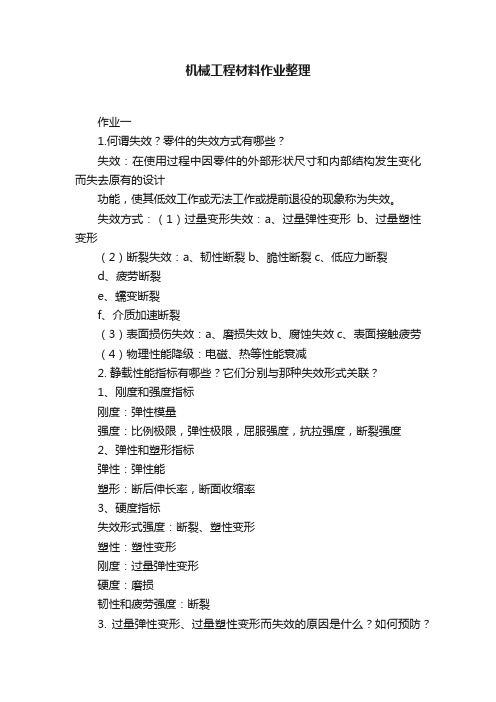
机械工程材料作业整理作业一1.何谓失效?零件的失效方式有哪些?失效:在使用过程中因零件的外部形状尺寸和内部结构发生变化而失去原有的设计功能,使其低效工作或无法工作或提前退役的现象称为失效。
失效方式:(1)过量变形失效:a、过量弹性变形b、过量塑性变形(2)断裂失效:a、韧性断裂b、脆性断裂c、低应力断裂d、疲劳断裂e、蠕变断裂f、介质加速断裂(3)表面损伤失效:a、磨损失效b、腐蚀失效c、表面接触疲劳(4)物理性能降级:电磁、热等性能衰减2. 静载性能指标有哪些?它们分别与那种失效形式关联?1、刚度和强度指标刚度:弹性模量强度:比例极限,弹性极限,屈服强度,抗拉强度,断裂强度2、弹性和塑形指标弹性:弹性能塑形:断后伸长率,断面收缩率3、硬度指标失效形式强度:断裂、塑性变形塑性:塑性变形刚度:过量弹性变形硬度:磨损韧性和疲劳强度:断裂3. 过量弹性变形、过量塑性变形而失效的原因是什么?如何预防?失效的责任主要在于设计者的考虑不周、计算错误或选材不当,故防止措施主要应从设计方面考虑。
过量弹性变形产生变形的主要原因是材料刚度不够。
预防途径:1.选择合适的材料或结构2.确定适当的匹配尺寸3.采用减少变形影响的转接件,比如在系统中采用软管等柔性构件,可显著减少弹性变形的有害影响。
过量塑性变形产生变形的主要原因是材料的弹性极限,屈服强度不够。
预防途径:1.降低实际应力:降低工作应力;减少残余应力;降低应力集中。
2.提高材料的屈服强度:通过合金化、热处理等方法。
4. 何谓冲击韧性?如何根据冲击韧性来判断材料的低温脆性倾向?冲击韧性是指材料在冲击载荷作用下吸收塑性变形功和断裂功的能力,即反映材料承受外来冲击负荷而不断裂的抵抗能力。
冲击韧性指标的实际意义在于揭示材料的变脆倾向。
材料的冲击吸收功随温度降低而降低,当温度低于韧脆转变温度时,材料由韧性状态变为脆性状态的现象,称为低温脆性。
从试样结果看(参见沈莲《机械工程材料》第三版P10图1-4)冲击韧性高的材料的低温脆性倾向小。
材料加工知识总结

材料加工知识总结第一章铸造工艺基础§1 液态合金的充型充型: 液态合金填充铸型的过程.充型能力: 液态合金充满铸型型腔,获得形状完整,轮廓清晰的铸件的能力充型能力不足:易产生: 浇不足: 不能得到完整的零件.冷隔:没完整融合缝隙或凹坑, 机械性能下降.一合金的流动性液态金属本身的流动性----合金流动性1 流动性对铸件质量影响1) 流动性好,易于浇出轮廓清晰,薄而复杂的铸件.2) 流动性好,有利于液态金属中的非金属夹杂物和气体上浮,排除.3) 流动性好,易于对液态金属在凝固中产生的收缩进行补缩.2 测定流动性的方法:以螺旋形试件的长度来测定: 如灰口铁:浇铸温度1300℃试件长1800mm.铸钢: 1600℃100mm3 影响流动性的因素主要是化学成分:1) 纯金属流动性好:一定温度下结晶,凝固层表面平滑,对液流阻力小2) 共晶成分流动性好:恒温凝固,固体层表面光滑,且熔点低,过热度大.3) 非共晶成分流动性差: 结晶在一定温度范围内进行,初生数枝状晶阻碍液流二浇注条件1 浇注温度: t↑ 合金粘度下降,过热度高. 合金在铸件中保持流动的时间长,∴t↑ 提高充型能力. 但过高,易产生缩孔,粘砂,气孔等,故不宜过高2 充型压力:液态合金在流动方向上所受的压力↑ 充型能力↑如砂形铸造---直浇道,静压力. 压力铸造,离心铸造等充型压力高.三铸型条件1 铸型结构:若不合理,如壁厚小, 直浇口低, 浇口小等充↓2 铸型导热能力:导热↑ 金属降温快,充↓如金属型3 铸型温度: t↑ 充↑如金属型预热4 铸型中气体: 排气能力↑ 充↑ 减少气体来源,提高透气性, 少量气体在铸型与金属液之间形成一层气膜,减少流动阻力,有利于充型.§2 铸件的凝固和收缩铸件的凝固过程如果没有合理的控制,铸件易产生缩孔,缩松一铸件的凝固1 凝固方式:铸件凝固过程中,其断面上一般分为三个区: 1—固相区2—凝固区3—液相区对凝固区影响较大的是凝固区的宽窄,依此划分凝固方式.1) 逐层凝固:纯金属,共晶成分合金在凝固过程中没有凝固区,断面液,固两相由一条界限清楚分开,随温度下降,固相层不断增加,液相层不断减少,直达中心.2) 糊状凝固合金结晶温度范围很宽,在凝固某段时间内,铸件表面不存在固体层,凝固区贯穿整个断面,先糊状,后固化.故---3) 中间凝固2 影响铸件凝固方式的因素1) 合金的结晶温度范围范围小: 凝固区窄,愈倾向于逐层凝固如: 砂型铸造, 低碳钢逐层凝固, 高碳钢糊状凝固2) 铸件的温度梯度合金结晶温度范围一定时,凝固区宽度取决于铸件内外层的温度梯度.温度梯度愈小,凝固区愈宽.(内外温差大,冷却快,凝固区窄)二合金的收缩液态合金从浇注温度至凝固冷却到室温的过程中,体积和尺寸减少的现象---.是铸件许多缺陷(缩孔,缩松,裂纹,变形,残余应力)产生的基本原因.1 收缩的几个阶段1) 液态收缩: 从金属液浇入铸型到开始凝固之前. 液态收缩减少的体积与浇注温度质开始凝固的温度的温差成正比.2) 凝固收缩: 从凝固开始到凝固完毕. 同一类合金,凝固温度范围大者,凝固体积收缩率大.如: 35钢,体积收缩率3.0%, 45钢 4.3%3) 固态收缩: 凝固以后到常温. 固态收缩影响铸件尺寸,故用线收缩表示.2 影响收缩的因素1) 化学成分: 铸铁中促进石墨形成的元素增加,收缩减少. 如: 灰口铁C, Si↑,收↓,S↑ 收↑.因石墨比容大,体积膨胀,抵销部分凝固收缩.2) 浇注温度: 温度↑ 液态收缩↑3) 铸件结构与铸型条件铸件在铸型中收缩会受铸型和型芯的阻碍.实际收缩小于自由收缩.∴铸型要有好的退让性.3 缩孔形成在铸件最后凝固的地方出现一些空洞,集中—缩孔. 纯金属,共晶成分易产生缩孔*产生缩孔的基本原因: 铸件在凝固冷却期间,金属的液态及凝固受缩之和远远大于固态收缩.4 影响缩孔容积的因素(补充)1) 液态收缩,凝固收缩↑ 缩孔容积↑2) 凝固期间,固态收缩↑,缩孔容积↓3) 浇注速度↓缩孔容积↓4) 浇注速度↑液态收缩↑ 易产生缩孔5 缩松的形成由于铸件最后凝固区域的收缩未能得到补足,或者,因合金呈糊状凝固,被树枝状晶体分隔开的小液体区难以得到补缩所至.1) 宏观缩松肉眼可见,往往出现在缩孔附近,或铸件截面的中心.非共晶成分,结晶范围愈宽,愈易形成缩松.2) 微观缩松凝固过程中,晶粒之间形成微小孔洞---凝固区,先形成的枝晶把金属液分割成许多微小孤立部分,冷凝时收缩,形成晶间微小孔洞. 凝固区愈宽,愈易形成微观缩松,对铸件危害不大,故不列为缺陷,但对气密性,机械性能等要求较高的铸件,则必须设法减少.(先凝固的收缩比后凝固的小,因后凝固的有液,凝,固三个收缩,先凝固的有凝,固二个收缩区----这也是形成微观缩松的基本原因.与缩孔形成基本原因类似)6 缩孔,缩松的防止办法基本原则:制定合理工艺—补缩, 缩松转化成缩孔.顺序凝固: 冒口—补缩同时凝固: 冷铁—厚处. 减小热应力,但心部缩松,故用于收缩小的合金.易于产生变形和裂纹.∴主要用于凝固收缩大,结晶间隔小的合金.l 非共晶成分合金,先结晶树枝晶,阻碍金属流动,冒口作用甚小.l 对于结晶温度范围甚宽的合金,由于倾向于糊状凝固,结晶开始之后,发达的树枝状骨状布满整个截面,使冒口补缩道路受阻,因而难避免显微缩松的产生.显然,选用近共晶成分和结晶范围较窄的合金生产铸件是适宜的.§3 铸造内应力,变形和裂纹凝固之后的继续冷却过程中,其固态收缩若受到阻碍,铸件内部就发生内应力,内应力是铸件产生变形和裂纹的基本原因.(有时相变膨胀受阻,负收缩)一内应力形成1 热应力:铸件厚度不均,冷速不同,收缩不一致产生.塑性状态: 金属在高于再结晶温度以上的固态冷却阶段,受力变形,产生加工硬化,同时发生的再结晶降硬化抵消,内应力自行消失.(简单说,处于屈服状态,受力—变形无应力)弹性状态:低于再结晶温度,外力作用下,金属发生弹性变形,变形后应力继续存在.举例: a) 凝固开始,粗细处都为塑性状态,无内应力∵两杆冷速不同,细杆快,收缩大,∵受粗杆限制,不能自由收缩,相对被拉长,粗杆相对被压缩,结果两杆等量收缩.b) 细杆冷速大,先进如弹性阶段,而粗杆仍为塑性阶段,随细杆收缩发生塑性收缩,无应力.c) 细杆收缩先停止,粗杆继续收缩,压迫细杆,而细杆又阻止粗杆的收缩,至室温, 粗杆受拉应力(+),(-)由此可见,各部分的温差越大,热应力也越大,冷却较慢的部分形成拉应力,冷却较快的部分形成压应力.预防方法: 1 壁厚均匀 2 同时凝固—薄处设浇口,厚处放冷铁优点: 省冒口,省工,省料缺点: 心部易出现缩孔或缩松,应用于灰铁锡青铜,因灰铁缩孔、缩松倾向小,锡青铜糊状凝固,用顺序凝固也难以有效地消除其显微缩松。
机械工程材料作业答案

第一章材料的结构与金属的结晶1.解释下列名词:变质处理P28;细晶强化P14;固溶强化P17。
5.为什么单晶体具有各向异性P12,而多晶体在一般情况下不显示各向异性P13?答:因为单晶体内部的原子都按同一规律同一位向排列,即晶格位向完全一致。
而在多晶体的金属中,每个晶粒相当于一个单晶体,具有各项异性,但各个晶粒在整块金属中的空间位向是任意的,整个晶体各个方向上的性能则是大量位向各不相同的晶粒性能的均值。
6.在实际金属中存在哪几种晶体缺陷P13?它们对力学性能有何影响P14?答:点缺陷、线缺陷、面缺陷。
缺陷的存在对金属的力学性能、物理性能和化学性能以及塑性变形、扩散、相变等许多过程都有重要影响。
7.金属结晶的基本规律是什么P25?铸造(或工业)生产中采用哪些措施细化晶粒?举例说明。
P27~P28答:金属结晶过程是个形核、长大的过程。
(1)增大过冷度。
降低金属液的浇筑温度、采用金属模、水冷模、连续浇筑等。
(2)变质处理。
向铝合金中加入钛、锆、硼;在铸铁液中加入硅钙合金等。
(3)振动和搅拌。
如机械振动、超声波振动、电磁搅拌等。
第二章金属的塑性变形与再结晶1.解释下列名词:加工硬化P40;再结晶P43;纤维组织P38。
2.指出下列名词的主要区别:重结晶、再结晶P43答:再结晶转变前后的晶格类型没有发生变化,故称为再结晶;而重结晶时晶格类型发生了变化。
另外,再结晶是对冷塑性变形的金属而言,只有经过冷塑性变形的金属才会发生再结晶,没有经过冷塑性变形的金属不存在再结晶的问题。
5.为什么常温下晶粒越细小,不仅强度、硬度越高,而且塑性、韧性也越好?P38答:晶粒愈细,单位体积内晶粒数就愈多,变形是同样的变形量可分散到更多的晶粒中发生,以产生比较均匀的变形,这样因局部应力集中而引起材料开裂的几率较小,使材料在断裂前就有可能承受较大的塑性变形,得到较大的伸长率和具有较高的冲击载荷抗力。
6.用冷拔铜丝制作导线,冷拔后应如何处理?为什么?P42答:应该利用回复过程对冷拔铜丝进行低温退火。
机械产品加工应知应会理论试题(含答案)

机械产品加工应知应会理论试题(含答案)一、选择题(每题5分,共25分)1. 以下哪种材料属于塑性材料?()A. 碳钢B. 工具钢C. 铝合金D. 黄铜答案:C2. 在机械加工过程中,以下哪种方式不属于切削运动?()A. 铣削B. 磨削C. 拉伸D. 钻孔答案:C3. 以下哪种加工方式不属于金属切削加工?()A. 车削B. 铣削C. 电火花加工D. 热处理答案:D4. 以下哪种公差属于位置公差?()A. 尺寸公差B. 形状公差C. 表面粗糙度公差D. 圆度公差答案:D5. 在机械加工过程中,以下哪种方式可以提高加工精度?()A. 提高加工速度B. 降低加工速度C. 提高加工温度D. 降低加工温度答案:B二、填空题(每题5分,共25分)1. 机械加工过程中,切削力主要包括____、____和____三个分力。
答案:主切削力、轴向力、径向力2. 以下哪种加工方式属于精密加工?()A. 车削B. 铣削C. 电火花加工D. 热处理答案:C3. 以下哪种方式可以提高机床的生产效率?()A. 提高加工速度B. 降低加工速度C. 提高加工温度D. 降低加工温度答案:A4. 以下哪种材料属于脆性材料?()A. 碳钢B. 工具钢C. 铝合金D. 黄铜答案:D5. 以下哪种公差属于形状公差?()A. 尺寸公差B. 形状公差C. 表面粗糙度公差D. 圆度公差答案:B三、判断题(每题5分,共25分)1. 机械加工过程中,切削力对加工精度有较大影响。
()答案:正确2. 提高加工速度可以提高机床的生产效率。
()答案:正确3. 塑性材料在加工过程中容易产生变形。
()答案:正确4. 钻孔加工属于塑性加工。
()答案:错误5. 表面粗糙度公差是指零件表面粗糙度的允许范围。
()答案:正确四、简答题(每题10分,共30分)1. 请简要说明机械加工过程中切削力对加工的影响。
答案:切削力对加工的影响主要包括以下几点:(1)切削力会导致工件产生变形,影响加工精度;(2)切削力会使刀具产生磨损,降低加工质量;(3)切削力会影响机床的加工稳定性,甚至可能导致机床损坏。
机械工程材料_习题集答案

作业01 力学性能 参考答案一、下列情况分别是因为哪一个力学性能指标达不到要求?1. 紧固螺栓使用后发生塑性变形。
( 屈服强度 )2. 齿轮正常负荷条件下工作中发生断裂。
( 疲劳强度 )3. 汽车紧急刹车时,发动机曲轴发生断裂。
( 冲击韧度 )4. 不锈钢圆板冲压加工成圆柱杯的过程中发生裂纹。
( 塑性 )5. 齿轮工作在寿命期内发生严重磨损。
( 硬度 )二、下列现象与哪一个力学性能有关?1. 铜比低碳钢容易被锯割。
( 硬度 )2. 锯条易被折断,而铁丝不易折断。
( 塑性 )p151-4 甲、乙、丙、丁四种材料的硬度分别为45HRC 、90HRB 、800HV 、240HBS ,试比较这四种材料硬度的高低。
答: 45HRC →HV : 90HRB →HB : 183901307300HRB 1307300HB ≈-=-=所以,800HV >45HRC >240HBS >90HRB作业02a 金属结构与结晶 参考答案一、判断题( × )1. 凡是由液体凝固成固体的过程都是结晶过程。
( × )2. 室温下,金属晶粒越细,则强度越高、塑性越低。
二、选择题( b )1. 金属结晶时,冷却速度越快,其实际结晶温度将:a. 越高b. 越低c. 越接近理论结晶温度( b )2. 为细化晶粒,可采用:a. 快速浇注b. 加变质剂c. 以砂型代金属型(c )3. 晶体中的位错属于:a. 体缺陷b. 面缺陷c. 线缺陷d. 点缺陷三、填空题1. 晶体与非晶体结构上的最根本的区别是,晶体内原子排列是:(有规则、周期性的)。
2. γ-Fe的一个晶胞原子数=(4 )。
3. α-Fe、Al、Cu、Ni、V、Mg、Zn各属何种晶体结构:体心立方:(α-Fe、V );面心立方:(Al、Cu、Ni );密排六方:(Mg、Zn )4. 实际金属晶体中存在:(点、线、面)三种缺陷,引起晶格(畸变)。
5. 结晶过程是靠两个密切联系的基本过程来实现的,它们是:(形核)和(晶核长大)。
材料加工整理资料(1)

材料加工原理第一章1.凝固过程中,热阻包括:液态金属的热阻,已凝固金属的热阻,中间层的热阻以及铸型的热阻等。
1.1凝固过程中传热的方式与特点基本传热方式有三种:传导、对流和辐射。
四种典型的热交换情况:a,铸型热阻起决定作用;b,中间层热阻起决定作用c,金属凝固层热阻起决定作用;d,进到户凝固层热阻和铸型热阻共同起决定作用影响金属凝固温度场的因素1)凝固金属的性质;2)铸型的性质3)浇注条件;4)铸件结构。
1.2 金属凝固过程中,起断面一般呈现三个区域:固相区、凝固区、液相区1.2.3 凝固方式:根据液固两相区的宽度可分:逐层凝固、体积凝固(糊状凝固)、中间凝固影响凝固方式的因素1)合金的结晶温度范围:取决于铸件材料。
2)铸件的温度梯度:是调节凝固方式的重要因素。
1.4 最典型的铸件晶粒组织由三个晶区组成:表面细晶区、内部柱状晶区、中心等轴晶区P29(1)表面细晶区:表面细晶区的大小与浇注温度、铸型温度、铸型导热能力、合金的生核能力以及合金成分有关。
细晶区的形成关键在于造成大量生核的条件,除了晶体脱落及其增殖作用外,有效质点的存在也能增加此区的生核,促进细晶区的形成。
(2)内部柱状晶区:它是表面层区晶体向内单向延伸生长的结果。
(3)中心等轴晶区1.4.2等轴晶组织的获得:原则是使液态金属中不断地产生新晶核,以阻止柱状晶的生长。
细化的方法:a,降低浇注温度b、孕育处理:加入孕育剂,促进液态金属内部形核从而获得细等轴晶(非自发形核作用、溶质偏析作用)c、动力学细化:方法,浇注过程控制技术、铸型振动、超声波振动、液相搅拌、提高冷却速度1.4.3 凝固缺陷:偏析、气孔和非金属夹杂物、缩孔与缩松第二章(一道计算题)第三章粉末冶金是冶金学的一个分支,是制取金属粉末或以金属粉末为原料,经过成型和烧结,制造各种金属或金属—非金属材料和制品的工艺过程。
它主要包括粉末制备、成型、烧结、后处理等基本工序。
3.2.1粉体的制备方法:a粉碎法:由粗颗粒粉碎获得细粉的方法。
第1章 机械工程材料作业

第1章 机械工程材料 作业1.常见的金属晶格类型有哪些?说明其特征。
答:常见的金属晶格类型有三种:(1)体心立方晶格。
它的晶胞是一个立方体,在立方晶胞的八个顶点和中心各有一个原子。
(2)面心立方晶格。
它的晶胞是一个立方体,在立方晶胞的八个顶点和六个面的中心各有一个原子。
(3)密排六方晶格。
它的晶胞是六棱柱体,在棱柱体的十二个棱角上,上下两个面的中心各有一个原子。
2.何谓过冷度?它与冷却速度有何关系?它对铸件晶粒大小有何影响?比较普通铸铁件表层和心部晶粒的大小。
答:在极其缓慢的冷却条件下测得的结晶温度称为理论结晶温度T 0,在实际冷却条件下测得的洁净温度称为实际洁净温度T 1,T 1 总是低于T 0,T 0 与T 1之差称为过冷度。
金属液体的冷却速度越大,T 1就越低,△T 也就越大。
增加过冷度能使晶核形成速度大于长大速度,使晶核数量相对增多,可起到细化晶粒的目的.普通铸铁件表层结晶温度低,心部结晶温度高,所以表层的晶粒小于心部的晶粒.3. 何谓金属的同素异构转变?试写出纯铁的同素异构转变过程。
答:一些金属在固态下的晶体结构随温度发生变化的现象称为同素异构转变。
纯铁的同素异构转变如下:密排六方晶格面心立方晶格体心立方晶格FeFeFeL C C -−−→−-−−→−-→αγδ0091213944.试述固溶强化和细化强化的原理。
答:固熔强化:在一种固熔体的晶格中熔入了另一种元素的原子,必然会造成晶格的畸变,晶格畸变必然导致合金的强度、硬度升高。
这种溶质原子使固溶体的强度和硬度升高的现象称为固溶强化。
固溶强化是强化金属材料的重要途径之一。
细化强化:由于多晶粒是由许多不同的晶核长成的晶粒所组成的,因此晶粒的大小会对金属力学性能产生很大的影响。
一般情况下,金属晶粒越细,金属的强度越高,塑性、韧性越好。
细化强化是通过采取细化晶粒的措施来提高金属材料的硬度和强度.通常采用增加过冷度、进行孕育处理和金属的同素异构转变等措施。
机械制造复习材料

机械制造复习材料随着机械制造行业的发展以及应用范围的扩大,作为机械制造从业者的我们更加需要掌握丰富的知识体系,以满足市场需求和产品质量的要求,因此复习材料变得尤为重要。
本文针对机械制造行业的复习材料进行总结和归纳,旨在为从业者提供一些有益的参考。
一、母材及其加工(1)母材的分类不同工件的加工需要不同的母材,因此母材的分类需要清晰。
分金属母材与非金属母材;金属母材可分铸造坯、锻造坯、轧制坯、铸锭坯、特殊生产方法制成的大尺寸坯料等;非金属母材可分为陶瓷、塑料、复合材料等。
(2)母材的表面母材表面处理对工件的加工精度和质量有很大影响,因此需要不同的加工方法,包括:铣磨、车削、研磨、光面加工等。
二、常用量具及其测量方法测量是机械制造过程中不可或缺的一部分。
了解常用的量具及其测量方法可以帮助我们更好的确认工件的尺寸和形状。
(1)常用量具螺距计、千分尺、游标卡尺、内径卡尺、高度规、放大显微镜等。
(2)测量方法直接测量法、间接测量法、比较测量法、平均值法等。
三、机械加工工艺及其分析机械加工是制造过程中的重要工序。
了解不同的机械加工工艺及其分析可以帮助我们优化工艺流程,提高工件的质量和效率。
(1)铣削工艺铣削是通过刀具的旋转和工件的向下移动来加工工件的方法。
了解铣削的工艺流程以及参数有助于提高加工精度和效率。
(2)车削工艺车削是工件围绕轴心旋转,利用切削刀进行加工的方法。
对切削刀的选择、工艺参数的设定以及处理方式等的掌握有助于提高工件的面质和精度。
(3)钻削工艺钻削是工件固定,利用钻头进行加工的方式。
了解适当的轴向力、进给速度和切削速度等参数有助于保证工件质量和安全性。
(4)车铣复合加工车铣复合加工是同时采用铣削和车削工艺进行加工的方式,有助于提高工件的加工精度和表面质量。
四、切削力及其研究(1)切削力的定义切削力是指在切削过程中,削屑对刀具产生的静力负荷。
了解切削力的大小和变化对机械加工工艺的控制和优化具有重要意义。
机械加工中级理论1000题

机械加工中级理论1000题
1. 问题描述
本文档提供了1000个机械加工中级理论问题的集合。
这些问题覆盖了机械加工的各个方面,包括加工工艺、工具选用、加工表面质量、尺寸公差等内容。
每个问题都有一个简洁明确的描述,并附带有四个备选答案。
请在每个问题后给出您认为最正确的答案。
本文档的目的是帮助读者巩固和扩展机械加工方面的理论知识。
2. 使用说明
- 每个问题后都有四个备选答案(A、B、C、D),请在每个问题的答案选项中选择一个最合适的答案。
- 您可以逐题回答,也可以先浏览整个文档后再选择您想回答的问题。
- 在每个问题后都留有足够的空间供您标记答案。
3. 目标
通过回答这1000个机械加工中级理论问题,您将能够:
- 加深对机械加工理论知识的理解和掌握;
- 熟悉常见的机械加工术语和概念;
- 检验自己在机械加工中级理论方面的知识掌握程度。
4. 注意事项
- 本文档中的问题和答案均为作者根据自身经验和知识整理而成,不保证所有答案都是唯一正确的。
读者在回答问题时请根据自己的判断选择答案,如有疑问可进行进一步的自学或请教相关专业人士。
- 答案标准可能因个人见解不同而有所差异,读者应理性对待答案并以扩展知识为主要目标。
现在,请开始解答机械加工中级理论的1000个问题!祝您好运!。
机械工程材料作业2和答案

机械工程材料作业(2)一,填空题1,在Fe-Fe3C相图中,共晶点的含碳量为(4.3% ),共析点的含碳量为( 0.77% )。
2.低温莱氏体是(珠光体)和(共晶渗碳体)组成的机械混合物。
3.金属结晶的过程包括形核和长大两个过程。
4.晶核的形成包括自发形核和非自发形核两种形式。
5.晶核的长大包括树枝状生长和平面生长两种形式。
6.金属铸锭的宏观组织是由三个晶区组成,由外向内分别是细等轴晶区柱状晶区、和中心等轴晶区。
7..铸锭的缺陷包括缩孔和缩松、气孔、非金属夹杂物、和成分偏析8.焊缝的组织是铸态组织柱状晶。
9.焊接接头是由焊缝和热影响区构成。
10.冷变形后金属在加热中,随温度的升高或加热时间的延长,其组织和性能一般经历回复、再结晶和晶粒长大三个阶段的变化。
11..细化晶粒的方法包括增大过冷度、加入形核剂和机械方法。
12改善和提高工程材料性能的主要途径有热处理、合金化和材料改性。
13.预先热处理常用的工艺方法有退火、正火、调质。
14.根据钢中的高低分为(写出含碳量):高碳钢(≥0.6%)、中碳钢(0.25~0.60%)和低碳钢(≤0.25%)。
二,术语解释1.正火将钢加热到Ac3或Accm以上30~500c,保温一段时间,随后取出置于静止空气中冷却。
2.调质对钢材作淬火+高温回火处理,称为调质处理3.淬火将钢加热到AC3以上30~50度,保温一段时间,随后用大于临界冷却速度的方法进行冷却,以获得马氏体组织的热处理方法。
4.回火将淬火后的工件加热至低于A1的某一温度,保温一段时间,然后冷却至室温的工艺。
5.淬透性钢在淬火后获得淬硬层深度大小的能力,即获得马氏体多少的能力。
6.表面淬火仅对工件表面做淬火处理的热处理工艺7.表面形变强化将冷变形强化用于提高金属材料的表面性能,成为提高工件疲劳强度、延长使用寿命的工艺措施8.表面涂覆将材料的表面用其他金属或者非金属涂覆后,可赋予零件表面强烈的光和热的反射性、表面着色装饰性、耐磨、耐腐蚀及其他电、磁功能之效果9.渗碳钢经渗碳、淬火、和低温回火后使用的结构钢10.调制刚经调质处理后使用的结构钢11.弹簧钢用于制造各种弹簧和弹性元件的专用结构钢12.枝晶偏析先结晶的枝干含熔点高组元较多,而后结晶的组元较少,这种现象成为枝晶偏析13.弹性变形外力去除后变形能完全恢复三,选择题1.在铁-碳合金中,当含碳量超过(B)以后,钢的硬度虽然在继续增加,但强度却在明显下降。
(整理)工程材料作业--学飞版
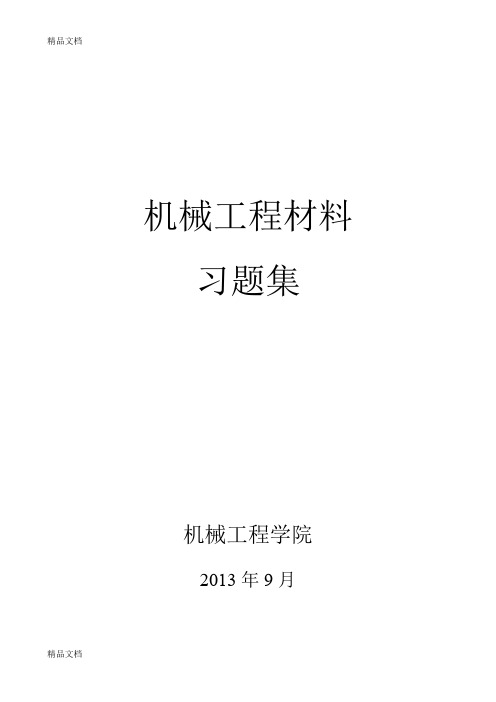
机械工程材料习题集机械工程学院2013年9月1-1现有一碳钢制支架刚性不足,采用以下三种方法中的哪种方法可有效解决此问题?为什么?①改用合金钢;②进行热处理改性强化;③改变该支架的截面与结构形状尺寸。
答:选③,改变该支架的截面与结构形状尺寸。
因为金属材料的刚度决定于基体金属的性质,当基体金属确定时,难于通过合金化、热处理、冷热加工等方法使之改变。
1-2对自行车座位弹簧进行设计和选材,应涉及到材料的哪些主要性能指标?答:强度、弹性、疲劳极限。
1-3在有关工件的图样中,出现了以下几种硬度技术条件的标注方法,用这种标注是否正确?为什么?(1)HBS250~300 (2)600~650HBS (3)5~10HRC (4)HRC70~75(5)HV800~850 (6)800~850H VHBS表示用淬火钢球去测试布氏硬度,由于淬火钢球很难达到很高的硬度值,因此在测试很高硬度时淬火钢球本身会变形,HBS的测量上限是450。
HBW是硬质合金钢球,由于硬质合金钢球比淬火钢球硬度高很多,HBW国标上说明测量上限是650,而布氏硬度计用的是球压头,在不同施压力下压入工件时其压入角在不断的变化,因此各种压头和试验力下得到的硬度值严格是不能直接比较的; HRC:洛氏标尺HRC的测量范围是20-70HRC.1-4 甲、乙、丙、丁四种材料的硬度分别为45HRC、90HRB、800HV、240HBS,试比较这四种材料硬度的高低。
1-5当某一材料的断裂韧度KIC=62MPa·m1/2,材料中裂纹的长度2a=5.7mm时,需加多大的应力会使裂纹失稳扩展而导致断裂?1-6 选择题1.拉伸试验时,试样拉断前能承受的最大拉应力称为材料的(B)A.屈服点B.抗拉强度C.弹性极限2.测定淬火钢件的硬度,一般常选用(B)来测试。
A.布氏硬度计B.洛氏硬度计C.维氏硬度计3.进行疲劳试验时,试样承受的载荷为(C)A.静载荷B.冲击载荷C.循环载荷4.洛氏硬度C标尺所用的压头是(B)A.淬火钢球B.金刚石圆锥体C硬质合金球5.金属抵抗永久变形和断裂的能力,称为(C)A.硬度B.塑性C.强度6.金属的(B )越好,则其锻造性能越好。
机械加工中的材料去除理论研究

机械加工中的材料去除理论研究随着工业的发展和科技的进步,机械加工在制造业中扮演着重要的角色。
机械加工的过程包括材料去除,也就是通过切削、磨削、抛光等方式,将原材料加工成所需形状和尺寸的零件。
在机械加工中,材料去除理论是研究和指导机械加工过程的基础,其重要性不可忽视。
材料去除理论研究的核心是切削力和切削过程,这是实现高效、精确机械加工的关键。
切削力是指在切削过程中作用在切削工具和工件之间的力。
切削力的大小和方向直接影响到切削过程中材料的去除情况,因此需要对切削力进行准确的预测和控制。
根据材料去除理论研究的成果,工程师可以选择合适的切削工艺参数,优化加工路径,提高加工效率和质量。
材料去除理论的研究不仅涉及到切削力,还包括切削热、切削振动等相关问题。
切削热是在切削过程中由于摩擦和塑性变形引起的热量。
切削热的积累会导致刀具和工件的热变形,甚至使切削刃快速磨损,影响加工质量和工具寿命。
因此,研究切削热与切削参数、刀具材料等的关系,对于提高机械加工的稳定性和可靠性至关重要。
此外,材料去除理论研究还包括切削振动的分析与控制。
切削振动是指在切削过程中切削力和切削系统的共振引起的不稳定运动。
切削振动会导致加工表面粗糙、工具损伤,甚至引起操作人员的身体不适。
因此,通过研究切削振动的机理和控制方法,可以改善机械加工的稳定性和质量。
机械加工中的材料去除理论研究不仅包括实验研究,还有理论模型的建立和仿真分析。
利用先进的数值模拟技术,可以对切削过程中的各种因素进行模拟和优化。
通过建立物理模型和数学模型,可以探究切削力、切削热、切削振动等的规律,并为实际加工过程的优化和改进提供指导。
此外,材料去除理论研究还包括新材料和新工艺的探索。
随着科学技术的不断进步,新的材料和新的工艺不断涌现,对于机械加工而言,如何高效去除这些新材料成为一个新的研究方向。
通过对材料力学行为、切削机理和刀具材料等方面的研究,可以为新材料的机械加工提供理论和技术支持。
《机械加工基础(56(8))》--车辆1101-3班学生复习之用
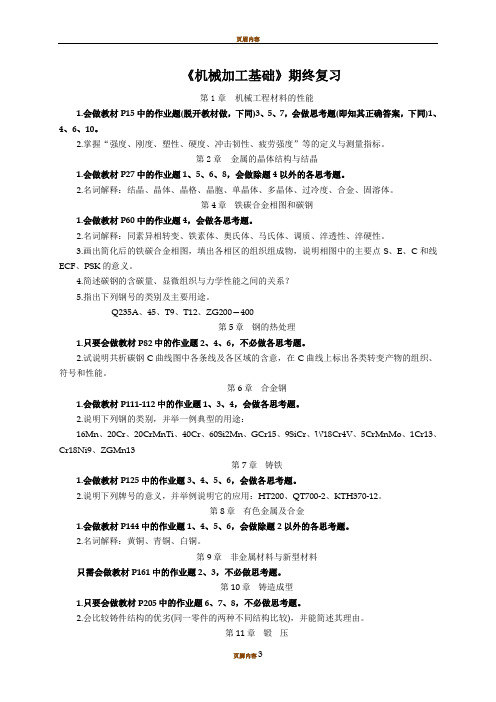
《机械加工基础》期终复习第1章机械工程材料的性能1.会做教材P15中的作业题(脱开教材做,下同)3、5、7,会做思考题(即知其正确答案,下同)1、4、6、10。
2.掌握“强度、刚度、塑性、硬度、冲击韧性、疲劳强度”等的定义与测量指标。
第2章金属的晶体结构与结晶1.会做教材P27中的作业题1、5、6、8,会做除题4以外的各思考题。
2.名词解释:结晶、晶体、晶格、晶胞、单晶体、多晶体、过冷度、合金、固溶体。
第4章铁碳合金相图和碳钢1.会做教材P60中的作业题4,会做各思考题。
2.名词解释:同素异相转变、铁素体、奥氏体、马氏体、调质、淬透性、淬硬性。
3.画出简化后的铁碳合金相图,填出各相区的组织组成物,说明相图中的主要点S、E、C和线ECF、PSK的意义。
4.简述碳钢的含碳量、显微组织与力学性能之间的关系?5.指出下列钢号的类别及主要用途。
Q235A、45、T9、T12、ZG200—400第5章钢的热处理1.只要会做教材P82中的作业题2、4、6,不必做各思考题。
2.试说明共析碳钢C曲线图中各条线及各区域的含意,在C曲线上标出各类转变产物的组织、符号和性能。
第6章合金钢1.会做教材P111-112中的作业题1、3、4,会做各思考题。
2.说明下列钢的类别,并举一例典型的用途:16Mn、20Cr、20CrMnTi、40Cr、60Si2Mn、GCr15、9SiCr、W18Cr4V、5CrMnMo、1Cr13、Cr18Ni9、ZGMn13第7章铸铁1.会做教材P125中的作业题3、4、5、6,会做各思考题。
2.说明下列牌号的意义,并举例说明它的应用:HT200、QT700-2、KTH370-12。
第8章有色金属及合金1.会做教材P144中的作业题1、4、5、6,会做除题2以外的各思考题。
2.名词解释:黄铜、青铜、白铜。
第9章非金属材料与新型材料只需会做教材P161中的作业题2、3,不必做思考题。
第10章铸造成型1.只要会做教材P205中的作业题6、7、8,不必做思考题。
机械工程材料结课作业

机械工程材料结课作业材料是人类用来制作各种产品的物质,世界万物都是有材料组成的。
机械工程材料是用于制造各种机械零件、构件的材料和机械制造过程中所应用的工艺材料。
机械工程材料的涉及面很广,但常按化学组成分为金属材料、高分子材料、陶瓷材料、复合材料四大类。
但对于机械工业生产中,应用最广的还是金属材料。
金属材料的发展距今已有几千年的历史,在日益发展的当今社会已经成为了一种不可或缺的材料,不论是在何种领域,都可以看到金属材料的身影。
机械制造中,大多数的机械零件或构件都是用金属材料制成的,因而,研究机械工程材料也就是研究金属材料的过程。
通过对金属材料的力学性能、晶体结构、结晶、以及相图的分析从而让我们进一步了解了金属的结构、组织、组成方式等。
研究机械工程材料,相图分析是必不可少的,通过对相图的分析,我们可以更好的了解金属的成因,金属的结构,金属的结晶过程,以及形成各种金属所需要的条件,在什么样的情况下可以形成什么样的金属组织。
金属材料的应用中,钢铁的应用是非常普遍的,其基本元素是铁和碳两个基本元素,统称铁碳合金。
铁碳合金的基本相主要有铁素体、奥氏体、渗碳体等。
根据铁-渗碳体相图分析,可将铁碳合金分为工业纯铁、钢和白口铸铁三大类。
其中铁碳合金的结晶过程中,又可得到共析钢、亚共析钢、过共析钢、共晶白口铸铁、亚共晶白口铸铁、过共晶白口铸铁等组织结构。
由于铁碳合金的成分、组织的不同,其使用性能便产生了差异,如含碳量对碳钢的力学影响,当钢中碳含量小于0.9%时,随着钢种含碳量的增加,钢的强度、硬度呈直线上升,而塑性、韧性不断下降;当钢中含碳量大于0.9%时,应渗碳体网的存在,不仅是钢的韧性、塑性进一步降低,而且强度也明显下降。
而且,含碳量的不同,还会再成金属的锻造性能、可锻性和焊接性、可加工性都发生改变。
在机械制造工业中,钢的热处理占有十分重要的地位,它不仅消除毛坯中的缺陷,改善工艺性能,还能显著提高钢的力学性能,充分发挥钢材的潜力,提高工件的使用性能和使用寿命。
机加工理论含题综述

机加工理论复习资料一填空1. 切削用量包含切削速度 , 吃刀深度和进给量。
2. 副偏角是平面与背叛进给运动方向之间的夹角,在基面内丈量。
3. 滚珠丝杠螺母的长处是:传动效率高,动作敏捷,传动时没有轴向空隙,磨损小,精度保持性好。
4. 装刀时一定使修光刃与进给方向平行,且修光刃长度一定大于进给量。
5. 极限偏差与实质偏差能够是正当,负值或许是零。
公差是一个不等于零的数,而且没有负值。
6. 公差带是公差带图中,由代表上下偏差的两条直线所限制的地区。
7. 孔的尺寸减去相当合的轴的尺寸所得代数差为正当时,称为空隙;为负值时称为过盈。
8. 最大过盈是孔的最小极限尺寸减去轴的最大极限尺寸所得的代数差。
它也等于孔的下偏差减轴的上偏差所得的代数差。
9. 断屑槽的形状有直线型和圆弧型。
10. 用两顶尖装夹工件的特色是装夹精度高,但刚性差,不合用装夹重型工件。
11. 死顶尖的长处是:刚性好,安心正确。
12. 精车刀的前角和后角都应取大些,而粗车刀的前角和后角都应去小些。
13. 精车中碳钢台阶轴,硬质合金刀片牌号为 YT30 ,其主偏角为 90 度,后来角为 8°-12°。
14. 偏刀一般是指主偏角为 90°的车刀。
15. 从床头向尾座方向车削的偏刀称为左偏刀。
16. 用左偏刀车削端面时,因为是用主切削刃进行切削,因此车出的表面粗拙度值比较渺小。
17. 磨削时所产生的振动有逼迫振动和自激振动。
18. 用左偏刀车端面,合用于车削铸件和锻件等工件的大端面。
19. 在砂轮主切削刃上磨凹槽可起到减振和导向的作用。
20. 一般一般部件都用直沟槽,要求较高需要磨削外圆和端面的部件常采纳 45°沟槽和圆弧沟槽。
21. 砂轮主要的展转精度是指主轴前端的径向圆跳动和轴向窜动,它直接影响工件表面的加工精度。
22. 切削刀的后角角度一般为 6° -8°,副后角的角度一般为 1° -2 °,副偏角的角度一般为 1° -1 ° 30’。
- 1、下载文档前请自行甄别文档内容的完整性,平台不提供额外的编辑、内容补充、找答案等附加服务。
- 2、"仅部分预览"的文档,不可在线预览部分如存在完整性等问题,可反馈申请退款(可完整预览的文档不适用该条件!)。
- 3、如文档侵犯您的权益,请联系客服反馈,我们会尽快为您处理(人工客服工作时间:9:00-18:30)。
机械加工过程中的材料理论作业整理第一次课1. 如何划分切削过程的三个变形区?解答:对塑性金属进行切削时,切屑的形成过程就是切削层金属的变形过程。
塑形金属切削过程中切屑的形成过程有三个变形区:1、第一变形区(剪切滑移);2、第二变形区(纤维化);3、第三变形区(纤维化与加工硬化)。
第一变形区:变形量最大。
第二变形区:切屑形成后与前刀面之间存在压力,所以沿前刀面流出时有很大摩擦,所以切屑底层又一次塑性变形。
第三变形区:已加工表面与后刀面的接触区域。
这三个变形区汇集在切削刃附近,应力比较集中,而且复杂,金属的被切削层在此处于工件基体分离,变成切屑,一小部分留在加工表面上。
第一变形区(近切削刃处切削层内产生的塑性变形区)金属的剪切滑移变形切削层受刀具的作用,经过第一变形区的塑性变形后形成切屑。
切削层受刀具前刀面与切削刃的挤压作用,使近切削刃处的金属先产生弹性变形,继而塑性变形,并同时使金属晶格产生滑移。
第二变形区(与前刀面接触的切屑层产生的变形区)内金属的挤压磨擦变形经过第一变形区后,形成的切屑要沿前刀面方向排出,还必须克服刀具前刀面对切屑挤压而产生的摩擦力。
此时将产生挤压摩擦变形。
第三变形区(近切削刃处已加工表面内产生的变形区)金属的挤压磨擦变形已加工表面受到切削刃钝圆部分和后刀面的挤压摩擦,造成纤维化和加工硬化。
◆ 2. 切削过程中加工表面热过程的特点?解答:切削金属时,被切削的金属在刀具的作用下,发生弹性和塑性变形而耗功,以及由于切屑剪切变形所作的功和刀具前面、后面摩擦所作的功都转变为热,这种热叫切削热。
使用切削液时,刀具、工件和切屑上的切削热主要由切削液带走;不用切削液时,切削热主要由切屑、工件和刀具带走或传出。
切削热的来源又三个变形区产生弹性变形功、塑性变形功所转化的热量Q变;切削与刀具摩擦功、工件与刀具摩擦功所转化的热量Q摩所组成。
产生的热量再传散到切屑Q屑、工件Q工、刀具Q刀、和介质Q介中。
3. 结合本人所从事的机械加工方面的研究和生产工作,分析加工过程中的力、热、塑变,以及组织、性能变化。
第二次课◆ 1. 在立方晶系中画出以[001]为晶带轴的所有晶面。
解答:晶带轴[uvw]与该晶带的晶面(hkl)之间存在以下关系:hu+kv+lw=0;将晶带轴[001]带入,h*0+k*0+l*1=0,当l=0时对任何h,k取值均能满足上式故晶带轴[001]的所有晶带面的晶面指数一般形式为(hk0)。
2. 归纳总结三种典型的晶体结构的晶体学特征。
(材料科学基础课本和笔记)3. 若将一位错线的正向定义为原来的反向,此位错的柏氏矢量是否改变?位错的类型性质是否变化?4. 位错一般分为哪两种,各有何特征?5. 位错的运动形式有哪些?解答:位错的运动方式有两种最基本形式,即滑移和攀移。
一位错的滑移位错沿着滑移面的移动称为滑移。
位错在滑移面上滑动引起滑移面上下的晶体发生相对运动,而晶体本身不发生体积变化称为保守运动。
这又包括刃位错的滑移、螺位错的滑移、混合型位错的滑移。
二位错的攀移刃型位错除可以在滑移面上滑移外,还可在垂直滑移面的方向上运动即发生攀移。
攀移的实质是多余半原子面的伸长或缩短。
攀移与滑移不同,攀移时伴随物质的迁移,需要空位的扩散,需要热激话,比滑移需要更大能量。
低温攀移较困难,高温时易攀移。
攀移通常会引起体积的变化,故属非保守运动。
6. 试述大角度晶界和小角度晶界的区别。
(材料科学基础课本和笔记)解答:小角度晶界取向差θ小于10~15度,可以看作由一系列位错所组成。
大角度晶界两侧晶粒的取向差较大,但过渡区很窄,原子排列不规则,很难用位错模型来描述。
第三次课1. 什么是滑移带?解答:将一个表面抛光的单晶体进行一定的塑性变形后,在光学显微镜下观察,发现抛光表面有许多平行的线条,成为滑移带。
每条滑移带由许多聚集在一起的相互平行的滑移线组成,这些滑移线实际上是晶体表面产生的小台阶。
2. 晶界对室温及高温变形过程有何影响?解答:晶界----阻碍位错运动----a.强度升高b.位错塞积----应力集中------塑性下降。
由于室温情况下,晶界强而晶粒本身弱,晶界在室温下阻碍位错滑移,而高温情况下,晶界弱而晶粒强,故除了晶粒内滑移,相邻两个晶粒还会沿着晶界发生相对滑移,此称为晶界滑动。
3. 塑性变形对组织、性能有何影响?解答:一.组织:a.塑性变形---晶粒延形变方向拉长-----纤维组织;b.塑性变形-----位错密度增加-----不均匀分布-----位错胞(胞壁高密度位错、胞内位错很少)c.变形织构:(丝织构和板织构)各向异性二.残余应力和点阵畸变三.性能:a加工硬化b.其他物理化学性能变化:密度、热导率下降;化学活性增加,加快腐蚀速度;导磁率、导电率和电阻温度系数下降;电阻率上升。
组织:(1)晶粒发生变形。
发生塑性变形后,晶粒沿形变方向被拉长或被压扁。
(2)亚结构形成。
发生较大变形时,由于位错的密度增大和发生交互作用,大量位错堆积在局部区域,使晶粒内产生亚晶粒。
(3)形变织构产生。
当塑性变形发生到70%以上时,由于晶粒发生转动,使各晶粒的位向趋于一致,形成特殊的择优取向,这种有序化的结构叫做形变织构。
性能:(1)形变强化。
发生塑性变形,随着形变的增大,金属的强度和硬度显著提高,塑性和韧性明显下降。
(2)产生各向异性。
由于纤维组织和形变织构的形成,使金属的性能产生各向异性。
(3)物理化学性能变化。
塑像变形可影响金属的物理化学性能,如使电阻增大,耐腐蚀性降低。
(4)产生残余内应力。
由于金属在发生塑性变形时,金属内部变形不均匀,位错,空位等晶体缺陷增多,金属内部会产生残余内应力。
4. 回复过程中,组织、性能有何变化?解答:将冷变形的金属加热到0.5Tm的温度进行保温,用高温显微镜观察组织随时间的变化,就会发现这种变化基本上可分为三个阶段。
回复阶段:显微组织无明显变化,机械性能变化不大,仅有某些物理性能发生了较为显著的变化(电阻),内应力基本消除。
中温回复:其主要机制是位错滑移导致位错重新组合,以及异号位错会聚而互相抵消。
高温回复:高温回复机制为多边化。
5. 动态再结晶和静态再结晶有何区别?解答:再结晶指冷变形金属在再结晶温度以上退火时,由新的无畸变的晶粒取代变形晶粒的过程。
再结晶不是相变过程,它只有组织变化而没有晶体结构的变化。
热变形(再结晶温度以上的变形)过程中发生的再结晶称动态再结晶,热变形后靠金属余温发生的再结晶称静态再结晶。
动态再结晶发生在热变形过程中,即在再结晶温度以上加工。
而静态再结晶是冷变形金属在后期的热处理过程中,如退火..晶粒由于应变储能释放发生再结晶。
第四次课1. 滑移带在分析切削区域塑性变形中的作用?解答:由一组平行的滑移线构成的带。
当晶体在切应力作用下产生滑移时, 在晶体表面形成显微台阶,在显微镜下观察时是一些细线,称滑移线,滑移线常成组出现,形成滑移带。
滑移带是晶体发生塑性变形的重要特征。
材料的塑性变形越严重的区域,滑移带越密,扩展越长,而且常出现表征多重滑移引起的滑移带网。
一个滑移带中有很多滑移层,变形时,滑移带由无到有,由浅到深(滑移层增多,意味着整个滑移带滑移量增加)由短到长(滑移层的滑移量)数目由少到多,可以看出整个形变过程是不连续的。
2. 分析切削过程中位错的特点?解答:1)切削是一种特殊的塑性变形和破坏形式。
•变形速度高103~106 /s,(静载10-3~10-4 /s )——与切削速度和切削层厚度相关•压力非常大1.96×103MPa•位错机理具有与静载条件下不同的规律性。
2)位错运动速度是切削变形速度的函数,即与切削速度和切下层的厚度有关。
3)位错停滞机理与作用应力和位错运动速度有关。
•低速1~10m/s,热激活特征流变应力—(位错-障碍)•高速硬化—(位错-晶格)4)切削温度-塑性变形热+摩擦热•平均温度0.2~0.4Tm,硬化和回复•接触区局部温度0.5~0.6Tm热激活软化5)切削材料-多晶体、杂质、结晶缺陷•影响塑性变形和硬化过程6)位错密度高,生成速度快7)分析切削位错机理最有前途的方法——统计方法——中和结构特征,用平均值描述8)由滑移带的取向、长度和密度来描述金属不同晶粒中滑移面的结晶学取向和塑性变形进行的特征。
3. 切削条件对位错密度有何影响?解答:影响位错运动的重要因素是切削条件, 它与工件材料性能、刀具几何参数及材料、切削用量等有关密切关系。
(1)作用在切削区域的载荷愈小和作用时间愈短,则位错密度和硬化深度愈小。
(2)随切削速度的增加和切削深度的减小,加工表面位错密度和硬化层深度减小。
4. 切削区域中位错结构如何演化?解答:当切削金属以速度V 刀具移动时, 受到切削刃及前刀面的挤压, 在剪切区之前主要受到压应力作用, 其值越接近剪切区时越大。
应变的加剧使晶体内原子排列和缺陷分布大量改组, 产生广泛的位错增列和运动。
此外, 随受压应力的方向逐渐旋转(图3), 其结果使位错发生交截和塞积, 形成位错缠结。
随着压缩变形的增大, 使大量的位错聚集在一起发展成为亚晶胞和网络结构。
另外, 切削过程中切削层受力的不均匀性也会造成变形后位错密度分布不均,形成网络。
5. 如何用位错理论解释切屑形成过程?解答:位错是晶体原子排列的一种线缺陷, 这种金属缺陷大量分布在材料内部, 它们在剪应力作用下能够从晶体中移出晶界表面,在剪切面上产生一个剪切位移, 切削层金属即借这种晶体内部的位错运动而发生剪切滑移现象这种亚细胞和网络结构与剪切过程中形成剪切阵面和层片结构直接有关。
在未产生变形前, 材料中由于压缩变形产生大量位错, 其密度随切削层金属接近刀尖部分而增大。
当材料进入到剪切区后, 这些位错就在切削刃所施加的剪应力作用下, 在材料内部扩展、延伸开来, 由刃前区扩展到切削层中, 产生剪切阵面, 使切削层金属发生塑性变形, 最终形成切屑沿前刀面流出。
6. 如何用位错理论说明工件表面层的特征?解答:(1)已加工表面滑移带密度的改变。
预先硬化层早已具有位错源,有继续运动的能力。
当外加载荷作用在具有位错源的金属上时,旧的位错继续运动——位错遗传效果。
(2)切屑外表面的宏观轮廓B=bn.金属层沿着滑移平面相对滑动,产生台阶。
(3)已加工表面的微观轮廓已加工表面的微观不平度与塑性变形相关a.切屑分离处的塑性变形及裂纹的分叉裂纹表面中位错的发射,在表面形成微观台阶b.后刀面与加工表面的摩擦引起的塑性变形塑性变形产生的位错在表面的露头形成了剪切台阶当外加载荷作用在具有位错源的金属上时,旧的位错继续运动——位错遗传效果。
金属层沿着滑移平面相对滑动,产生台阶。
已加工表面的微观不平度与塑性变形相关:切屑分离处的塑性变形及裂纹的分叉,裂纹表面中位错的发射,在表面形成微观台阶;后刀面与加工表面的摩擦引起的塑性变形,塑性变形产生的位错在表面的露头形成了剪切台阶。