己内酰胺的合成路线及工艺消耗
国内己内酰胺厂家生产工艺
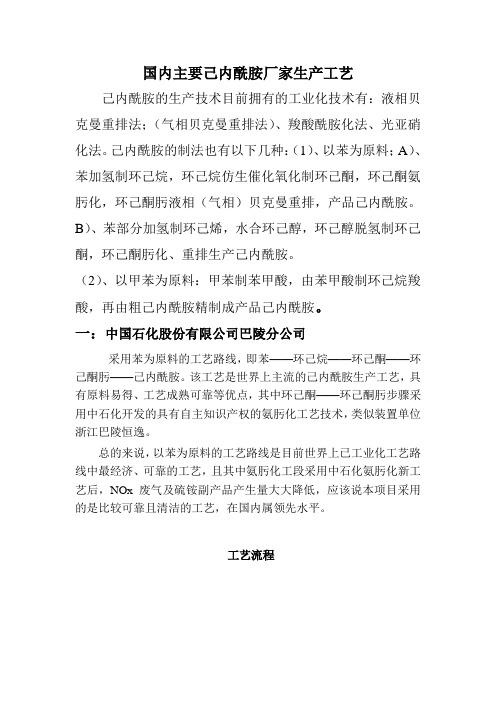
国内主要己内酰胺厂家生产工艺
己内酰胺的生产技术目前拥有的工业化技术有:液相贝克曼重排法;(气相贝克曼重排法)、羧酸酰胺化法、光亚硝化法。
己内酰胺的制法也有以下几种:(1)、以苯为原料;A)、苯加氢制环己烷,环己烷仿生催化氧化制环己酮,环己酮氨肟化,环己酮肟液相(气相)贝克曼重排,产品己内酰胺。
B)、苯部分加氢制环己烯,水合环己醇,环己醇脱氢制环己酮,环己酮肟化、重排生产己内酰胺。
(2)、以甲苯为原料:甲苯制苯甲酸,由苯甲酸制环己烷羧酸,再由粗己内酰胺精制成产品己内酰胺。
一:中国石化股份有限公司巴陵分公司
采用苯为原料的工艺路线,即苯——环己烷——环己酮——环己酮肟——己内酰胺。
该工艺是世界上主流的己内酰胺生产工艺,具有原料易得、工艺成熟可靠等优点,其中环己酮——环己酮肟步骤采用中石化开发的具有自主知识产权的氨肟化工艺技术,类似装置单位浙江巴陵恒逸。
总的来说,以苯为原料的工艺路线是目前世界上已工业化工艺路线中最经济、可靠的工艺,且其中氨肟化工段采用中石化氨肟化新工艺后,NOx废气及硫铵副产品产生量大大降低,应该说本项目采用的是比较可靠且清洁的工艺,在国内属领先水平。
工艺流程
各主体生产装置和辅助生产装置工艺技术路线
二:浙江巴陵恒逸
生产工艺与中国石化股份有限公司巴陵分公司基本相同,都是采用苯为原料的工艺路线,即苯——环己烷——环己酮——环己酮肟——己内酰胺。
三:中石化石家庄炼化
以甲苯为原料制取苯甲酸,经亚硝化反应后生产己内酰胺的苏尼亚工艺过程(意大利SNIA亚硝化法)。
己内酰胺以及生产工艺简介

己内酰胺;ε-己内酰胺;Caprolactam;CPLIUPAC名Azepan-2-oneCAS号105-60-2分子式C6H11NO;NH(CH2)5CO分子量113.18常温下状态白色晶体蒸汽压0.67kPa/122℃闪点125℃熔点68~70℃沸点136~138℃/10mmHg270℃/760mmHg溶解性溶于水,溶于乙醇、乙醚、氯仿等多数有机溶剂相对密度(水=1)1.05(70%水溶液)稳定性稳定由于硫酸铵滞此,减少或消除副产硫酸铵,成为评价当今己内酰胺工业生产经济性的一个重要因素。
肟法:各种肟法的主要生产步骤如下:一、拉西羟胺合成法(由法本公司开发)是用二氧化硫还原亚硝酸铵生成羟胺二磺酸盐(简称二盐),二盐水解生成硫酸羟胺。
硫酸羟胺与环己酮在80~110℃下反应生成环己酮肟(简称肟)和硫酸,然后用25%氨水中和至pH约7,肟和硫酸铵溶液即分层析出。
二、HPO法硫酸铵。
为消酸铵,荷兰国家矿业公司开发了硫酸循环法。
它是将转位产物中的硫酸中和生成为硫酸氢铵,然后用溶剂萃取出己内酰胺。
硫酸氢铵再热解为二氧化硫,二氧化硫转化为发烟硫酸循环使用。
无副产硫酸铵的转位方法还有气相转位法、离子交换树脂法、电渗析分离法等。
己内酰胺精制种己内酰胺生产方法中,均需对己内酰胺进行精制。
一般精制方法有:化学精制(高锰酸钾氧化、催化加氢等)法、萃取法、重结晶法、离子交换树脂法、真空蒸馏法等,为获得高纯度产品,工业上一般是组合几种方法进行联合精制。
一、甲苯法甲苯在钴盐催化剂作用下氧化生成苯甲酸;反应温度160~170℃,压力0.8~1.0MPa,转化率约30%,收率为理论值的92%。
苯甲酸用活性炭载体上的钯催化剂进行液相加氢生成六氢苯甲酸;反应温度170℃,压力1.0~1.7MPa,转化率99%,收率几乎达100%。
在发烟硫酸中,六氢苯甲酸与亚硝酰硫酸反应生成己内酰胺,并用氨水中和;转化率50%,选择性90%。
为减少或消除副产硫酸铵,开发了改良的副产硫酸铵减半法和无副产硫酸铵法。
己内酰胺工艺流程
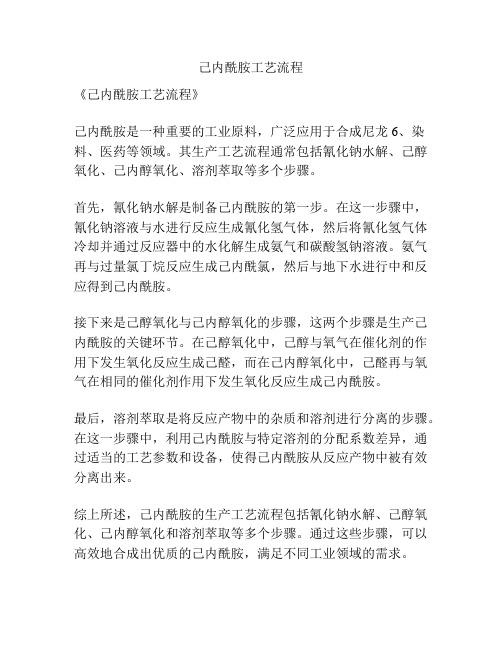
己内酰胺工艺流程
《己内酰胺工艺流程》
己内酰胺是一种重要的工业原料,广泛应用于合成尼龙6、染料、医药等领域。
其生产工艺流程通常包括氰化钠水解、己醇氧化、己内醇氧化、溶剂萃取等多个步骤。
首先,氰化钠水解是制备己内酰胺的第一步。
在这一步骤中,氰化钠溶液与水进行反应生成氰化氢气体,然后将氰化氢气体冷却并通过反应器中的水化解生成氨气和碳酸氢钠溶液。
氨气再与过量氯丁烷反应生成己内酰氯,然后与地下水进行中和反应得到己内酰胺。
接下来是己醇氧化与己内醇氧化的步骤,这两个步骤是生产己内酰胺的关键环节。
在己醇氧化中,己醇与氧气在催化剂的作用下发生氧化反应生成己醛,而在己内醇氧化中,己醛再与氧气在相同的催化剂作用下发生氧化反应生成己内酰胺。
最后,溶剂萃取是将反应产物中的杂质和溶剂进行分离的步骤。
在这一步骤中,利用己内酰胺与特定溶剂的分配系数差异,通过适当的工艺参数和设备,使得己内酰胺从反应产物中被有效分离出来。
综上所述,己内酰胺的生产工艺流程包括氰化钠水解、己醇氧化、己内醇氧化和溶剂萃取等多个步骤。
通过这些步骤,可以高效地合成出优质的己内酰胺,满足不同工业领域的需求。
己内酰胺生产流程及其原理

己内酰胺生产流程及其原理下载温馨提示:该文档是我店铺精心编制而成,希望大家下载以后,能够帮助大家解决实际的问题。
文档下载后可定制随意修改,请根据实际需要进行相应的调整和使用,谢谢!并且,本店铺为大家提供各种各样类型的实用资料,如教育随笔、日记赏析、句子摘抄、古诗大全、经典美文、话题作文、工作总结、词语解析、文案摘录、其他资料等等,如想了解不同资料格式和写法,敬请关注!Download tips: This document is carefully compiled by the editor. I hope that after you download them, they can help yousolve practical problems. The document can be customized and modified after downloading, please adjust and use it according to actual needs, thank you!In addition, our shop provides you with various types of practical materials, such as educational essays, diary appreciation, sentence excerpts, ancient poems, classic articles, topic composition, work summary, word parsing, copy excerpts,other materials and so on, want to know different data formats and writing methods, please pay attention!己内酰胺是一种重要的化工原料,在很多工业领域都有着广泛的应用。
己内酰胺流程

己内酰胺流程己内酰胺是一种重要的有机合成中间体,具有广泛的应用价值。
它可以用于合成聚酰胺树脂、润滑剂、塑料助剂等化工产品,也可以作为医药、农药等领域的原料。
己内酰胺的生产工艺一直备受关注,其生产流程的优化和改进对提高生产效率、降低成本具有重要意义。
首先,己内酰胺的生产主要通过氨解己内酰胺酸盐来实现。
具体的生产流程包括以下几个步骤:1. 原料准备,首先需要准备己内酰胺酸盐和氨水作为原料。
己内酰胺酸盐是通过己内酰胺和酸反应得到的中间体,而氨水则是氨气溶解在水中得到的溶液。
2. 反应器装载,将适量的己内酰胺酸盐溶解在水中,加入反应器中。
然后向反应器中通入氨气,控制反应温度和压力。
3. 反应进行,在适当的温度和压力条件下,己内酰胺酸盐和氨水发生氨解反应,生成己内酰胺和相应的盐类产物。
4. 分离提纯,将反应产物进行分离,得到己内酰胺的粗品。
然后通过蒸馏、结晶等工艺对其进行提纯,得到合格的己内酰胺产品。
5. 产品储存,最后,将得到的己内酰胺产品进行包装、标识和储存,待用或出售。
在整个生产流程中,需要特别注意反应条件的控制、产品的分离提纯以及安全生产等环节。
通过优化反应条件、改进分离提纯工艺和加强安全管理,可以提高己内酰胺的生产效率,降低生产成本,保证产品质量。
此外,随着环保意识的提升,己内酰胺的生产过程也需要考虑减少废弃物和减少对环境的影响。
因此,在生产流程中应当注重资源的合理利用和废物的处理,采取节能减排措施,实现清洁生产。
总的来说,己内酰胺的生产流程是一个复杂的化工过程,需要综合考虑反应条件、分离提纯、安全生产和环保等方面的因素。
只有不断优化流程、提高生产技术水平,才能更好地满足市场需求,推动己内酰胺产业的健康发展。
氨肟化法己内酰胺工艺

氨肟化法己内酰胺工艺一、引言氨肟化法己内酰胺工艺是一种生产己内酰胺的重要方法。
己内酰胺作为一种重要的有机合成原料,广泛应用于塑料、纤维、涂料、胶粘剂等领域。
本文将详细介绍氨肟化法己内酰胺工艺的原理、步骤和优势。
二、原理氨肟化法己内酰胺工艺主要通过氨肟与己二酰氯反应生成己内酰胺。
己二酰氯作为己内酰胺的前体,与氨肟反应生成己内酰胺与氯化氢。
氯化氢可以通过回收再利用,实现资源的循环利用。
三、步骤1. 原料准备:准备好己二酰氯和氨肟的化学品,并确保其纯度符合工业标准。
2. 氨肟的加入:将氨肟缓慢加入反应釜中,控制加入速度和温度,避免剧烈反应和温度过高。
3. 己二酰氯的加入:将己二酰氯缓慢加入反应釜中,与氨肟发生反应生成己内酰胺和氯化氢。
4. 反应控制:控制反应物质的投入速度和温度,避免剧烈反应和温度过高,以保证反应的高效进行。
5. 反应结束与分离:反应结束后,将反应液分离得到己内酰胺和氯化氢。
6. 氯化氢回收:通过适当的工艺措施,将氯化氢回收并进行处理,以实现资源的循环利用。
7. 己内酰胺提纯:对得到的己内酰胺进行提纯,去除杂质,提高产品的纯度。
四、优势1. 原料广泛:氨肟化法己内酰胺工艺所需的原料己二酰氯和氨肟在市场上易得,并且价格较为稳定。
2. 反应效率高:氨肟与己二酰氯反应生成己内酰胺的反应速度快,反应效率高。
3. 产品纯度高:通过适当的工艺控制和提纯步骤,可以获得高纯度的己内酰胺产品。
4. 环保可持续:通过回收和处理氯化氢,实现了资源的循环利用,减少了对环境的污染。
5. 工艺成熟稳定:氨肟化法己内酰胺工艺已经在工业生产中得到广泛应用,具有成熟稳定的工艺流程和操作经验。
五、结论氨肟化法己内酰胺工艺是一种高效、环保、成熟稳定的生产己内酰胺的方法。
通过合理控制反应条件和提纯步骤,可以获得高纯度的己内酰胺产品。
该工艺具有原料广泛、反应效率高和环保可持续等优势,对于己内酰胺的生产具有重要意义。
随着科技的进步和工艺的不断优化,相信氨肟化法己内酰胺工艺将在未来得到更广泛的应用。
己内酰胺的生产工艺与技术路线的选择
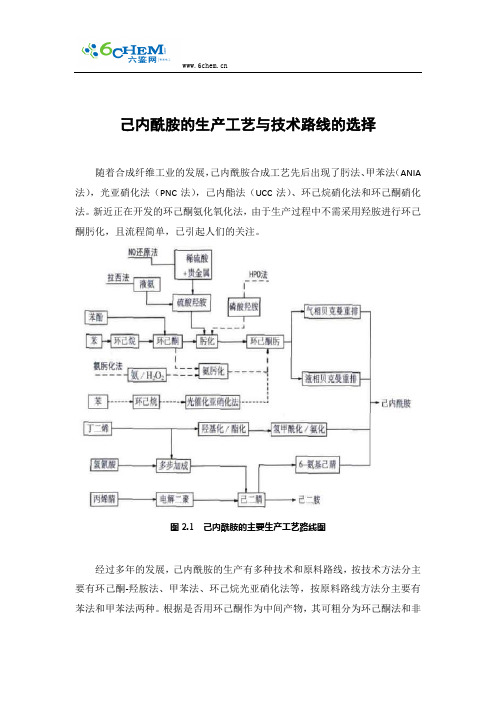
己内酰胺的生产工艺与技术路线的选择随着合成纤维工业的发展,己内酰胺合成工艺先后出现了肟法、甲苯法(ANIA 法),光亚硝化法(PNC法),己内酯法(UCC法)、环己烷硝化法和环己酮硝化法。
新近正在开发的环己酮氨化氧化法,由于生产过程中不需采用羟胺进行环己酮肟化,且流程简单,已引起人们的关注。
图2.1 己内酰胺的主要生产工艺路线图经过多年的发展,己内酰胺的生产有多种技术和原料路线,按技术方法分主要有环己酮-羟胺法、甲苯法、环己烷光亚硝化法等,按原料路线方法分主要有苯法和甲苯法两种。
根据是否用环己酮作为中间产物,其可粗分为环己酮法和非环己酮法。
2.1 环己酮法己内酰胺生产从环己酮合成开始,原料为苯酚或环己烷。
环己烷是优选原料,可生产KA油。
氧化过程通常采用硼酸或钴催化剂。
……2.1.1 环己酮的生产工艺2.1.1.1 苯酚法苯酚法(属苯法)是苯酚在镍催化剂作用下加氢生成环己醇,环己醇再进行提纯脱氢反应生成粗环己酮。
……2.1.1.2 环己烷法环己烷法(属苯法)首先是苯加氢制环己烷,加氢过程分以Ni为催化剂的常压加氢和以Pt为催化剂的加压加氢,然后环己烷氧化制环己醇、…….2.1.1.3 环己烯法环己烯法(属苯法)第一步是苯部分加氢生成环己烯,然后环己烯水合得环己醇,环己醇再进行脱氢反应生成环己酮。
……2.1.2 环己酮肟的生产工艺环己酮肟是生产己内酰胺的重要中间产物,其可以由羟胺与环己酮反应制得,也可以由其它方法制得。
1943年,德国法本公司通过环己酮-羟胺合成(现在简称为肟法),……2.1.2.1 拉西法1887年拉西(Raschig)用亚硝酸盐和亚硫酸盐反应经水解制取羟胺获得成功,……2.1.2.2 HPO法磷酸羟胺法(HPO法,属苯法)由荷兰国家矿业(DSM)公司开发,在80年代发展很快。
HPO法是在磷酸盐缓冲溶液中,……2.1.2.3 NO法一氧化氮还原法也称BASF/Polimex-NO还原法(属苯法),是德国BASF公司和波兰Polimex公司开发的工艺。
己内酰胺简介
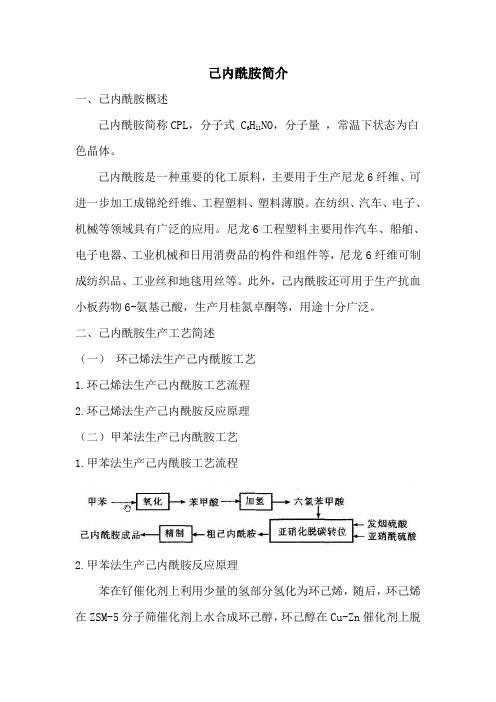
己内酰胺简介一、己内酰胺概述己内酰胺简称CPL,分子式 C6H11NO,分子量,常温下状态为白色晶体。
己内酰胺是一种重要的化工原料,主要用于生产尼龙6纤维、可进一步加工成锦纶纤维、工程塑料、塑料薄膜。
在纺织、汽车、电子、机械等领域具有广泛的应用。
尼龙6工程塑料主要用作汽车、船舶、电子电器、工业机械和日用消费品的构件和组件等,尼龙6纤维可制成纺织品、工业丝和地毯用丝等。
此外,己内酰胺还可用于生产抗血小板药物6-氨基己酸,生产月桂氮卓酮等,用途十分广泛。
二、己内酰胺生产工艺简述(一)环己烯法生产己内酰胺工艺1.环己烯法生产己内酰胺工艺流程2.环己烯法生产己内酰胺反应原理(二)甲苯法生产己内酰胺工艺1.甲苯法生产己内酰胺工艺流程2.甲苯法生产己内酰胺反应原理苯在钌催化剂上利用少量的氢部分氢化为环己烯,随后,环己烯在ZSM-5分子筛催化剂上水合成环己醇,环己醇在Cu-Zn催化剂上脱氢生产环己酮。
与传统工艺一样,环己酮在TS-1分子筛催化剂上与H2O2和氨反应生产环己酮肟,然后重排合成己内酰胺(CPL)。
综合上述两种工艺方案考虑,得到如下结论:1.环己烯法生产己内酰胺工艺特点:有苯不完全加氢制环己烯比环己烷氧化路线少消耗三分之一H2,副产环己烷可用于生产己内酰胺或作为产品出售,实际羰基收率100%。
此工艺流程短,节省资源,不造成三废污染,水循环使用,较空气氧化法安全、清洁,具有极强的竞争力。
2.甲苯法生产己内酰胺工艺特点:生产流程短,但精致步骤繁多,副产硫酸铵多(大约每生产1t己内酰胺副产硫胺)。
三、己内酰胺(CPL)市场(一)国际市场近年来,世界己内酰胺的生产能力稳步增长。
2008年全世界己内酰胺的总生产能力为万t/a,2009年增加到万t/a,同比增长%。
生产能力主要集中在巴斯夫(BASF)、DSM、霍尼韦尔、宇部工业、中国台湾石油发展、中国石油化工集团以及韩国(Capro)等7大公司之中。
2009年这7大公司的生产能力合计达到万t/a,占世界总生产能力的%。
国内己内酰胺生产现状及生产工艺技术经济分析比较
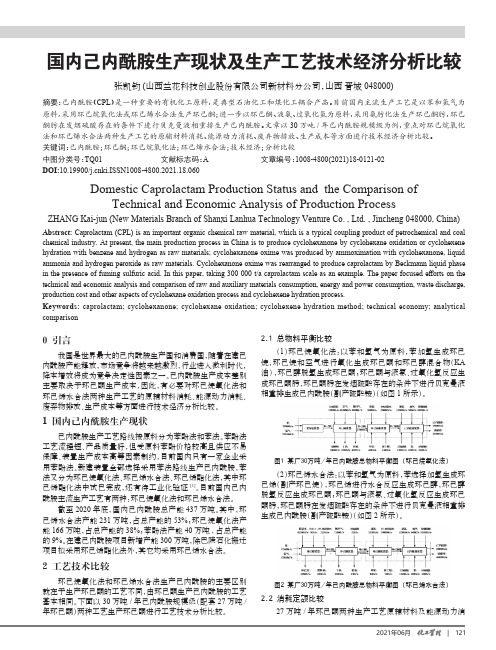
2.1 总物料平衡比较
(1)环己烷氧化法:以苯和氢气为原料,苯加氢生成环己 烷,环己烷和空气进行氧化生成环己酮和环己醇混合物(KA 油),环己醇脱氢生成环己酮;环己酮与液氨、过氧化氢反应生 成环己酮肟,环己酮肟在发烟硫酸存在的条件下进行贝克曼液 相重排生成己内酰胺(副产硫酸铵)(如图 1 所示)。
1 国内己内酰胺生产现状
国内己内酰胺生产现状及生产工艺技术经济分析比较
张凯钧 (山西兰花科技创业股份有限公司新材料分公司,山西 晋城 048000)
摘要:己内酰胺(CPL)是一种重要的有机化工原料,是典型石油化工和煤化工耦合产品。目前国内主流生产工艺是以苯和氢气为
原料,采用环己烷氧化法或环己烯水合法生产环己酮;进一步以环己酮、液氨、过氧化氢为原料,采用氨肟化法生产环己酮肟,环己
己内酰胺生产工艺路线按原料分为苯酚法和苯法。苯酚法 工艺流程短、产品质量好,但受原料苯酚价格较高且供应不易 保障、装置生产成本高等因素制约,目前国内只有一家企业采 用苯酚法。新建装置全部选择采用苯法路线生产己内酰胺,苯 法又分为环己烷氧化法、环己烯水合法、环己烯酯化法,其中环 己烯酯化法中试已完成,还有待工业化验证 [1]。目前国内己内 酰胺主流生产工艺有两种:环己烷氧化法和环己烯水合法。
-0.22 -0.015 -0.002 -0.01
— -6.0
(1)主要原料消耗
环己烷氧化法原料苯只有 75% ~ 80% 转化成环己酮,其 余转化为成分复杂且难以回收利用的副产物,副产物需通过加 碱中和后再焚烧处理,氢气单耗也较环己烯水合法高。
环己烯水合法原料苯 99.5% 转化为环己酮和环己烷,其中 环己酮比例可达到 80% 以上,副产物环己烷纯度高可以作为 产品销售,氢气单耗也较环己烷氧化法低。
己内酰胺生产工艺
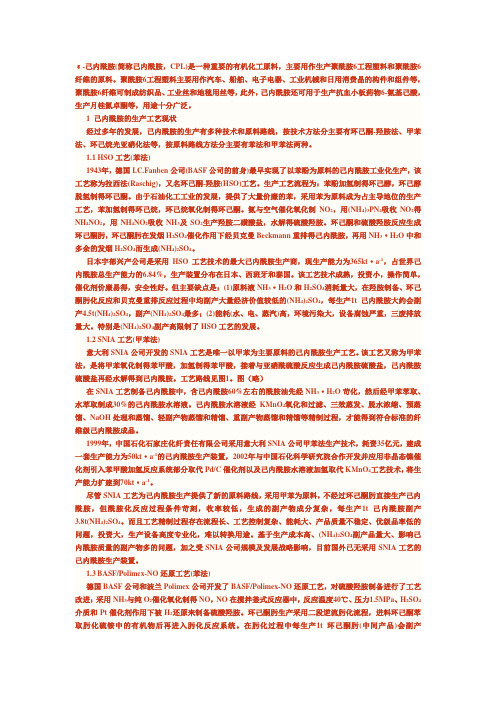
ε-己内酰胺(简称己内酰胺,CPL)是一种重要的有机化工原料,主要用作生产聚酰胺6工程塑料和聚酰胺6纤维的原料。
聚酰胺6工程塑料主要用作汽车、船舶、电子电器、工业机械和日用消费晶的构件和组件等,聚酰胺6纤维可制成纺织品、工业丝和地毯用丝等,此外,己内酰胺还可用于生产抗血小板药物6-氨基己酸,生产月桂氮卓酮等,用途十分广泛。
1 己内酰胺的生产工艺现状经过多年的发展,己内酰胺的生产有多种技术和原料路线,按技术方法分主要有环己酮-羟胺法、甲苯法、环己烷光亚硝化法等,按原料路线方法分主要有苯法和甲苯法两种。
1.1 HSO工艺(苯法)1943年,德国I.C.Fanben公司(BASF公司的前身)最早实现了以苯酚为原料的己内酰胺工业化生产,该工艺称为拉西法(Raschig),又名环己酮-羟胺(HSO)工艺。
生产工艺流程为:苯酚加氢制得环己醇,环己醇脱氢制得环己酮。
由于石油化工工业的发展,提供了大量价廉的苯,采用苯为原料成为占主导地位的生产工艺,苯加氢制得环己烷,环己烷氧化制得环己酮。
氨与空气催化氧化制NO2,用(NH4)3PN4吸收NO2得NH4NO2,用NH4NO2吸收NH3及SO2生产羟胺二磺酸盐,水解得硫酸羟胺。
环己酮和硫酸羟胺反应生成环己酮肟,环己酮肟在发烟H2SO4催化作用下经贝克曼Beckmann重排得己内酰胺,再用NH3·H2O中和多余的发烟H2SO4而生成(NH4)2SO4。
日本宇部兴产公司是采用HSO工艺技术的最大己内酰胺生产商,现生产能力为365kt·a-1,占世界己内酰胺总生产能力的6.84%,生产装置分布在日本、西班牙和泰国。
该工艺技术成熟,投资小,操作简单,催化剂价廉易得,安全性好。
但主要缺点是:(1)原料液NH3·H2O和H2SO4消耗量大,在羟胺制备、环己酮肟化反应和贝克曼重排反应过程中均副产大量经济价值较低的(NH4)2SO4,每生产1t己内酰胺大约会副产4.5t(NH4)2SO4,副产(NH4)2SO4最多;(2)能耗(水、电、蒸汽)高,环境污染大,设备腐蚀严重,三废排放量大。
己内酰胺工艺流程图
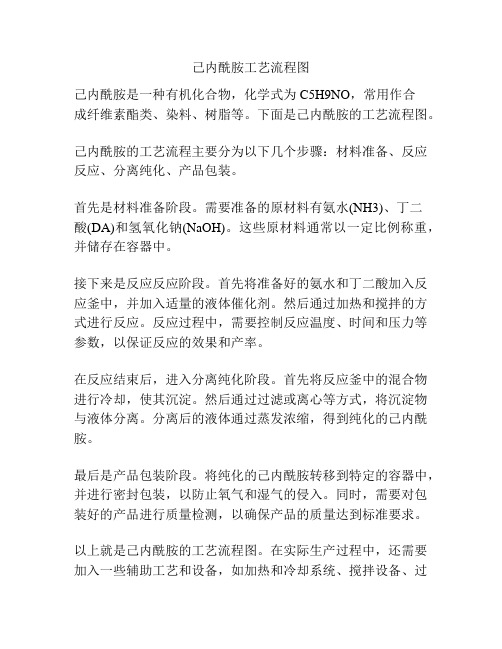
己内酰胺工艺流程图
己内酰胺是一种有机化合物,化学式为C5H9NO,常用作合
成纤维素酯类、染料、树脂等。
下面是己内酰胺的工艺流程图。
己内酰胺的工艺流程主要分为以下几个步骤:材料准备、反应反应、分离纯化、产品包装。
首先是材料准备阶段。
需要准备的原材料有氨水(NH3)、丁二
酸(DA)和氢氧化钠(NaOH)。
这些原材料通常以一定比例称重,并储存在容器中。
接下来是反应反应阶段。
首先将准备好的氨水和丁二酸加入反应釜中,并加入适量的液体催化剂。
然后通过加热和搅拌的方式进行反应。
反应过程中,需要控制反应温度、时间和压力等参数,以保证反应的效果和产率。
在反应结束后,进入分离纯化阶段。
首先将反应釜中的混合物进行冷却,使其沉淀。
然后通过过滤或离心等方式,将沉淀物与液体分离。
分离后的液体通过蒸发浓缩,得到纯化的己内酰胺。
最后是产品包装阶段。
将纯化的己内酰胺转移到特定的容器中,并进行密封包装,以防止氧气和湿气的侵入。
同时,需要对包装好的产品进行质量检测,以确保产品的质量达到标准要求。
以上就是己内酰胺的工艺流程图。
在实际生产过程中,还需要加入一些辅助工艺和设备,如加热和冷却系统、搅拌设备、过
滤和离心设备等,以提高生产效率和产品质量。
另外,还需要严格控制各个环节的操作条件和参数,以确保整个生产过程的安全性和稳定性。
己内酰胺简介

己内酰胺简介一、己内酰胺概述己内酰胺简称CPL,分子式 C6H11NO,分子量 113.18,常温下状态为白色晶体。
己内酰胺是一种重要的化工原料,主要用于生产尼龙6纤维、可进一步加工成锦纶纤维、工程塑料、塑料薄膜。
在纺织、汽车、电子、机械等领域具有广泛的应用。
尼龙6工程塑料主要用作汽车、船舶、电子电器、工业机械和日用消费品的构件和组件等,尼龙6纤维可制成纺织品、工业丝和地毯用丝等。
此外,己内酰胺还可用于生产抗血小板药物6-氨基己酸,生产月桂氮卓酮等,用途十分广泛。
二、己内酰胺生产工艺简述(一)环己烯法生产己内酰胺工艺1.环己烯法生产己内酰胺工艺流程2.环己烯法生产己内酰胺反应原理(二)甲苯法生产己内酰胺工艺1.甲苯法生产己内酰胺工艺流程2.甲苯法生产己内酰胺反应原理苯在钌催化剂上利用少量的氢部分氢化为环己烯,随后,环己烯在ZSM-5分子筛催化剂上水合成环己醇,环己醇在Cu-Zn催化剂上脱氢生产环己酮。
与传统工艺一样,环己酮在TS-1分子筛催化剂上与H2O2和氨反应生产环己酮肟,然后重排合成己内酰胺(CPL)。
综合上述两种工艺方案考虑,得到如下结论:1.环己烯法生产己内酰胺工艺特点:有苯不完全加氢制环己烯比环己烷氧化路线少消耗三分之一H2,副产环己烷可用于生产己内酰胺或作为产品出售,实际羰基收率100%。
此工艺流程短,节省资源,不造成三废污染,水循环使用,较空气氧化法安全、清洁,具有极强的竞争力。
2.甲苯法生产己内酰胺工艺特点:生产流程短,但精致步骤繁多,副产硫酸铵多(大约每生产1t己内酰胺副产3.5t硫胺)。
三、己内酰胺(CPL)市场(一)国际市场近年来,世界己内酰胺的生产能力稳步增长。
2008年全世界己内酰胺的总生产能力为465.0万t/a,2009年增加到475.4万t/a,同比增长2.24%。
生产能力主要集中在巴斯夫(BASF)、DSM、霍尼韦尔、宇部工业、中国台湾石油发展、中国石油化工集团以及韩国(Capro)等7大公司之中。
己内酰胺生产工艺
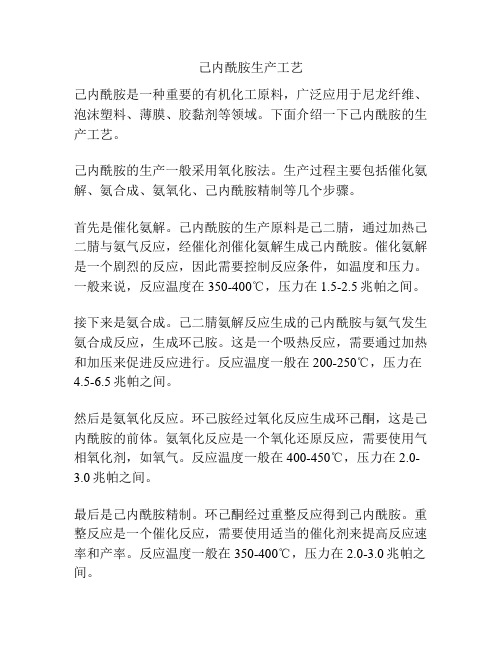
己内酰胺生产工艺己内酰胺是一种重要的有机化工原料,广泛应用于尼龙纤维、泡沫塑料、薄膜、胶黏剂等领域。
下面介绍一下己内酰胺的生产工艺。
己内酰胺的生产一般采用氧化胺法。
生产过程主要包括催化氨解、氨合成、氨氧化、己内酰胺精制等几个步骤。
首先是催化氨解。
己内酰胺的生产原料是己二腈,通过加热己二腈与氨气反应,经催化剂催化氨解生成己内酰胺。
催化氨解是一个剧烈的反应,因此需要控制反应条件,如温度和压力。
一般来说,反应温度在350-400℃,压力在1.5-2.5兆帕之间。
接下来是氨合成。
己二腈氨解反应生成的己内酰胺与氨气发生氨合成反应,生成环己胺。
这是一个吸热反应,需要通过加热和加压来促进反应进行。
反应温度一般在200-250℃,压力在4.5-6.5兆帕之间。
然后是氨氧化反应。
环己胺经过氧化反应生成环己酮,这是己内酰胺的前体。
氨氧化反应是一个氧化还原反应,需要使用气相氧化剂,如氧气。
反应温度一般在400-450℃,压力在2.0-3.0兆帕之间。
最后是己内酰胺精制。
环己酮经过重整反应得到己内酰胺。
重整反应是一个催化反应,需要使用适当的催化剂来提高反应速率和产率。
反应温度一般在350-400℃,压力在2.0-3.0兆帕之间。
己内酰胺生产工艺过程中要注意一些问题。
首先,要控制反应温度和压力,以确保反应的安全性和效果。
其次,需要选择合适的催化剂和氧化剂,以提高反应速率和产率。
此外,还需要合理设计反应装置,以提高反应效果和降低能耗。
己内酰胺是一种重要的化工原料,在工业生产中应用广泛。
通过催化氨解、氨合成、氨氧化和己内酰胺精制等步骤,可实现己内酰胺的大规模生产。
生产过程中需要严格控制反应条件,选择合适的催化剂和氧化剂,并合理设计反应装置,以确保生产的安全性和效率。
己内酰胺的合成路线及工艺消耗

己内酰胺的合成路线及工艺消耗一、己内酰胺生产工艺早在1899年,Gabriel和Meas就通过加热ε-氨基己酸,首次合成了己内酰胺。
但是直到1943年,才由德国I.G.Farben公司实现了己内酰胺的工业化。
当时采用的工艺技术称为拉西法,起始原料为苯酚。
第二次世界大战后,I.G.Farben公司的技术被公开,世界己内酰胺应用得到了快速的发展。
荷兰DSM公司的HPO工艺对拉西法作了重大改进,自上世纪70年代以来在世界上得到了广泛的推广应用,成为己内酰胺生产最重要的工艺技术。
此外,德国巴斯夫公司(BASF)的一氧化氮还原工艺、日本东丽公司的光亚硝化法工艺、美国Allied Singal公司的异丙苯/苯酚工艺、意大利SNIA公司的甲苯法工艺、波兰Polimex/Polservice公司的Capropol工艺也各有特色,在己内酰胺工业生产中得到应用。
传统拉西法:德国I.G.FANBEN公司开发,其关键工艺是环己酮与硫酸羟胺发生肟化反应,生成环己酮肟,环己酮肟在发烟硫酸作用下经贝克曼重排反应生成己内酰胺。
硫酸羟胺是用硫酸中和亚**,生成脱酯硫酸盐,再发生水解反应产生的。
该工艺在羟胺合成、肟化反应、重排反应三道工序都使用硫酸,氨中和后产生大量的副产物硫酸铵,而硫酸铵的经济价值较低。
对传统拉西法的改进,主要着眼于降低硫酸铵的副产量。
Allied异丙苯/苯酚工艺:该工艺主要特点是用异丙苯法生产的苯酚为原料。
苯酚加氢生成环己酮,环己酮与硫酸羟胺经肟化反应生成环己酮肟,环己酮肟在发烟硫酸作用下经贝克曼重排反应生成己内酰胺。
硫酸羟胺是用硫磺、氨、二氧化碳和水经多步工艺生产的,硫酸铵副产量仍然较高。
巴斯夫一氧化氮还原工艺:该工艺的硫酸羟胺是控制氨氧化生成一氧化氮,再在硫酸中用氢气还原而生成的,硫酸铵副产量比传统拉西法少得多。
CAPROPOL工艺:该工艺在环己烷氧化制环己酮环节有一定特点,使用了钯催化剂,降低了氢氧化钠的消耗量和废碱液的生成。
己内酰胺工艺流程
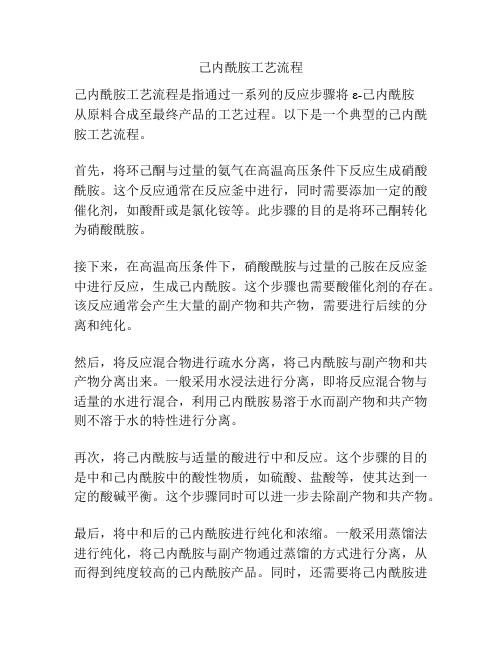
己内酰胺工艺流程己内酰胺工艺流程是指通过一系列的反应步骤将ε-己内酰胺从原料合成至最终产品的工艺过程。
以下是一个典型的己内酰胺工艺流程。
首先,将环己酮与过量的氨气在高温高压条件下反应生成硝酸酰胺。
这个反应通常在反应釜中进行,同时需要添加一定的酸催化剂,如酸酐或是氯化铵等。
此步骤的目的是将环己酮转化为硝酸酰胺。
接下来,在高温高压条件下,硝酸酰胺与过量的己胺在反应釜中进行反应,生成己内酰胺。
这个步骤也需要酸催化剂的存在。
该反应通常会产生大量的副产物和共产物,需要进行后续的分离和纯化。
然后,将反应混合物进行疏水分离,将己内酰胺与副产物和共产物分离出来。
一般采用水浸法进行分离,即将反应混合物与适量的水进行混合,利用己内酰胺易溶于水而副产物和共产物则不溶于水的特性进行分离。
再次,将己内酰胺与适量的酸进行中和反应。
这个步骤的目的是中和己内酰胺中的酸性物质,如硫酸、盐酸等,使其达到一定的酸碱平衡。
这个步骤同时可以进一步去除副产物和共产物。
最后,将中和后的己内酰胺进行纯化和浓缩。
一般采用蒸馏法进行纯化,将己内酰胺与副产物通过蒸馏的方式进行分离,从而得到纯度较高的己内酰胺产品。
同时,还需要将己内酰胺进行浓缩处理,将其水分含量控制在一定的范围内,以达到产品的质量要求。
总结起来,己内酰胺工艺流程主要包括硝酸酰胺的生成、己胺与硝酸酰胺的反应、分离、中和和纯化浓缩等步骤。
每个步骤都需要严格控制反应条件和操作技术,同时还需要对产物进行分析和检测,以确保产品的质量和纯度。
这些步骤互相关联,相互影响,只有在整个工艺流程中各个环节都得到了优化和完善,才能够顺利地生产出高质量的己内酰胺产品。
己内酰胺单位产品能源能耗限额标准
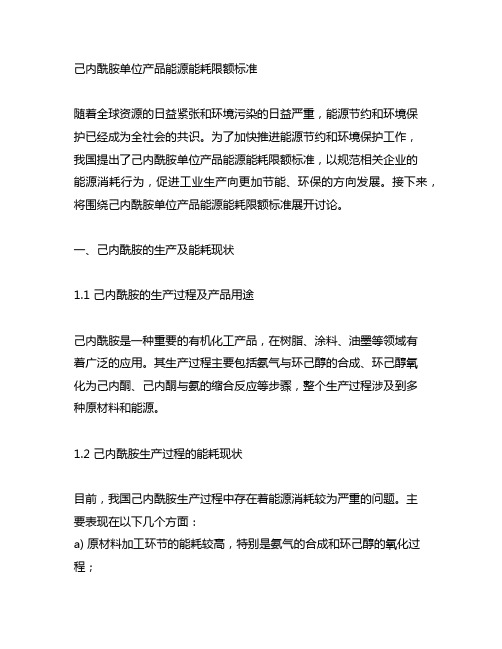
己内酰胺单位产品能源能耗限额标准随着全球资源的日益紧张和环境污染的日益严重,能源节约和环境保护已经成为全社会的共识。
为了加快推进能源节约和环境保护工作,我国提出了己内酰胺单位产品能源能耗限额标准,以规范相关企业的能源消耗行为,促进工业生产向更加节能、环保的方向发展。
接下来,将围绕己内酰胺单位产品能源能耗限额标准展开讨论。
一、己内酰胺的生产及能耗现状1.1 己内酰胺的生产过程及产品用途己内酰胺是一种重要的有机化工产品,在树脂、涂料、油墨等领域有着广泛的应用。
其生产过程主要包括氨气与环己醇的合成、环己醇氧化为己内酮、己内酮与氨的缩合反应等步骤,整个生产过程涉及到多种原材料和能源。
1.2 己内酰胺生产过程的能耗现状目前,我国己内酰胺生产过程中存在着能源消耗较为严重的问题。
主要表现在以下几个方面:a) 原材料加工环节的能耗较高,特别是氨气的合成和环己醇的氧化过程;b) 反应过程中需要消耗大量的热能和电能;c) 产品分离和精制过程中耗能较大。
二、己内酰胺单位产品能源能耗限额标准的制定意义2.1 规范企业能耗行为,促进节能减排通过制定己内酰胺单位产品能源能耗限额标准,可以规范企业的生产行为,促使其在生产过程中更加节约能源、减少污染物排放,从而实现节能减排的目标。
2.2 推动企业技术革新,提高效率限额标准的推行将促使企业加大技术革新力度,采用更加先进的生产工艺和设备,提高生产效率,降低能源消耗,从而提升企业的竞争力。
2.3 塑造良好的生产环境和企业形象依据能源能耗限额标准进行生产,可以降低企业的排放量,改善环境质量,增强企业的社会责任感和公益形象,为企业树立良好的品牌形象。
三、己内酰胺单位产品能源能耗限额标准的内容和要求根据相关法律法规和国家标准,己内酰胺单位产品能源能耗限额标准的内容和要求主要包括以下几个方面:3.1 合理能源消耗指标的确定制定合理的能源消耗指标是己内酰胺单位产品能源能耗限额标准的首要任务。
己内酰胺_实验报告(3篇)

第1篇一、实验目的1. 熟悉己内酰胺的合成方法;2. 掌握己内酰胺的物理、化学性质;3. 了解己内酰胺在工业上的应用。
二、实验原理己内酰胺(C6H11NO)是一种重要的有机化合物,广泛应用于合成尼龙、药物、香料等领域。
本实验采用丁二酸二乙酯与尿素为原料,在酸性条件下进行环合反应,合成己内酰胺。
反应方程式如下:C6H10O4 + 2NH2CONH2 → C6H11NO + 2H2O三、实验仪器与试剂1. 仪器:圆底烧瓶、回流冷凝管、温度计、滴液漏斗、烧杯、抽滤瓶、烘箱等;2. 试剂:丁二酸二乙酯、尿素、浓硫酸、无水乙醇、NaOH、盐酸、氢氧化钠溶液、碘化钾溶液等。
四、实验步骤1. 准备:将丁二酸二乙酯和尿素按照一定比例混合,加入圆底烧瓶中,加入适量的浓硫酸作为催化剂;2. 加热:将混合物加热至回流状态,保持反应温度在150-160℃;3. 回流:持续回流反应2小时,每隔30分钟取样检测反应液的酸碱度;4. 冷却:将反应液冷却至室温,加入适量的氢氧化钠溶液调节pH值至中性;5. 抽滤:将反应液进行抽滤,得到己内酰胺粗品;6. 纯化:将己内酰胺粗品溶解于无水乙醇中,加入适量的碘化钾溶液,观察颜色变化,判断己内酰胺的纯度;7. 蒸发:将纯化后的己内酰胺溶液在烘箱中蒸发,得到己内酰胺晶体;8. 收集:收集己内酰胺晶体,进行称重和干燥。
五、实验结果与讨论1. 实验结果:本实验成功合成了己内酰胺,反应时间为2小时,己内酰胺的纯度达到90%以上;2. 讨论:本实验中,丁二酸二乙酯与尿素的摩尔比为1:1,浓硫酸作为催化剂,反应温度控制在150-160℃。
实验结果表明,本实验方法具有较高的合成效率和己内酰胺的纯度。
六、实验结论1. 本实验采用丁二酸二乙酯与尿素为原料,在酸性条件下合成己内酰胺,反应条件适宜,合成效率高;2. 己内酰胺在合成过程中具有良好的物理、化学性质,适用于多种合成领域;3. 本实验为合成己内酰胺提供了一种简单、高效的方法,具有一定的实际应用价值。
己内酰胺生产工艺
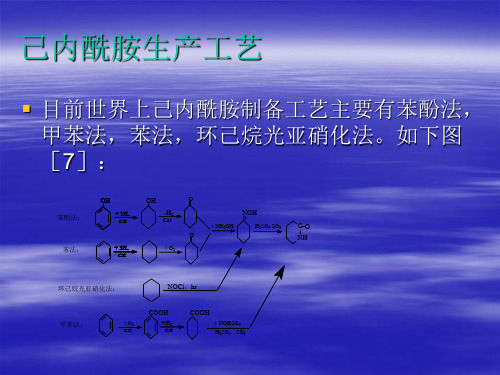
目前世界上己内酰胺制备工艺主要有苯酚法, 甲苯法,苯法,环己烷光亚硝化法。如下图 [7]:
OH 苯酚法:
+ 3H2 Cat
OH -H2
Cat
O
NOH
+NH2OH H2SO4.SO3
C=O NH
O
苯法:
+ 3H2 Cat
+O2
环己烷光亚硝化法:
NOCl,hr
COOH 甲苯法:
+O2
Cat
苯加氢制环己烷工艺有两种,即液相和气相加氢两种。
+3H 2 Cat
苯法制己内酰胺
2.环己烷氧化制环己醇和环己酮: 2.环己烷氧化制环己醇和环己酮:
环己烷氧化主要有催化氧化和无催化氧化。 反应式如下:
= O +O 2 Cat
或无
OH + +H 2O
OOH
苯法制己内酰胺
3.环己醇再脱氢为环己酮: 3.环己醇再脱氢为环己酮:
=NOH.2HCl
+NOCl +HCl
λ
<600nm
(环己酮肟盐酸盐)
环己烷光亚硝化法制己内酰胺
环己酮肟盐酸盐在发烟硫酸的作用下贝克曼重排为己内酰 胺:
C =O NH . H 2SO 4
+2NH 3
C =O NH +(NH 4) 2SO 4
甲苯法制己内酰胺
甲苯法制CPL是由意大利SNIA公司在上世纪六十年代初开发 甲苯法制CPL是由意大利SNIA公司在上世纪六十年代初开发 研制的,并于1962年实现工业化,1968年、1975年分别在 研制的,并于1962年实现工业化,1968年、1975年分别在 意大利的MARFLIDONIA,前苏联乌兹别克的CIRCIK建成8 意大利的MARFLIDONIA,前苏联乌兹别克的CIRCIK建成8 万吨/年工业装置,但目前均已停产。1996年,中国石家庄 万吨/年工业装置,但目前均已停产。1996年,中国石家庄 引进该技术建成5万吨/ 引进该技术建成5万吨/年己内酰胺装置,至今运行良好,并 已扩能至6.5万吨/ 已扩能至6.5万吨/年。该工艺主要有如下步骤: 1.甲苯氧化制苯甲酸 1.甲苯氧化制苯甲酸
简述世界己内酰胺供需以及生产工艺情况
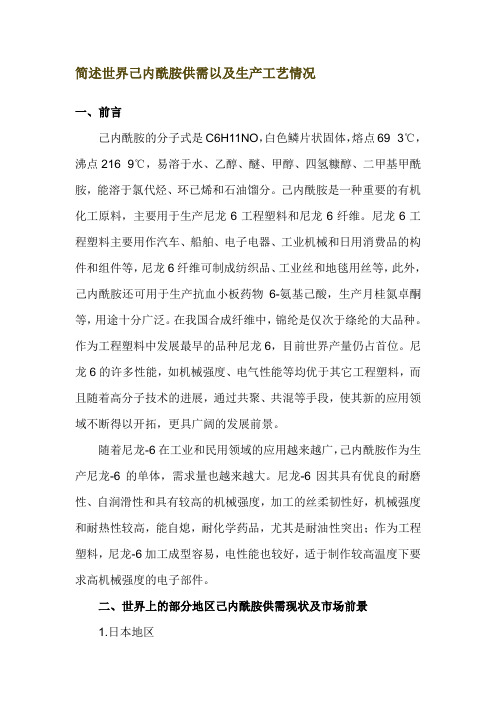
简述世界己内酰胺供需以及生产工艺情况一、前言己内酰胺的分子式是C6H11NO,白色鳞片状固体,熔点69×3℃,沸点216×9℃,易溶于水、乙醇、醚、甲醇、四氢糠醇、二甲基甲酰胺,能溶于氯代烃、环已烯和石油馏分。
己内酰胺是一种重要的有机化工原料,主要用于生产尼龙6工程塑料和尼龙6纤维。
尼龙6工程塑料主要用作汽车、船舶、电子电器、工业机械和日用消费品的构件和组件等,尼龙6纤维可制成纺织品、工业丝和地毯用丝等,此外,己内酰胺还可用于生产抗血小板药物6-氨基己酸,生产月桂氮卓酮等,用途十分广泛。
在我国合成纤维中,锦纶是仅次于绦纶的大品种。
作为工程塑料中发展最早的品种尼龙6,目前世界产量仍占首位。
尼龙6的许多性能,如机械强度、电气性能等均优于其它工程塑料,而且随着高分子技术的进展,通过共聚、共混等手段,使其新的应用领域不断得以开拓,更具广阔的发展前景。
随着尼龙-6在工业和民用领域的应用越来越广,己内酰胺作为生产尼龙-6的单体,需求量也越来越大。
尼龙-6因其具有优良的耐磨性、自润滑性和具有较高的机械强度,加工的丝柔韧性好,机械强度和耐热性较高,能自熄,耐化学药品,尤其是耐油性突出;作为工程塑料,尼龙-6加工成型容易,电性能也较好,适于制作较高温度下要求高机械强度的电子部件。
二、世界上的部分地区己内酰胺供需现状及市场前景1.日本地区2006年,日本己内酰胺的总生产能力为54.2万吨,约占世界总生产能力的11.0%,主要的生产厂家有EMS-UBE 公司(生产能力为1.7万吨/年)、三菱化学公司(生产能力为6.5万吨/年)、本住友化学公司(生产能力为18.0万吨/年)、东丽工业公司(生产能力为10.0万吨/年)以及Ube 工业公司(生产能力为18.0万吨/年)。
2006年,日本己内酰胺的消费量约为24.9万吨,约占世界总消费量的6.2%,其中产量为47.5万吨,净出口量为22.6万吨。
其中尼龙6纤维对己内酰胺的需求量为5.9万吨/年,约占总消费量的23.7%;尼龙6树脂的需求量为17.0万吨/年,约占总消费量的68.3%;其他方面的需求量为2.0万吨,约占总需求量的8.0%。
己内酰胺生产工艺

己内酰胺的三种工业化技术:液相Beckmann 重排法苯 → 环己烷 → 环己酮 → 环己酮肟 →粗己内酰胺 → 产品羧酸酰胺化法甲苯 → 苯甲酸 → 环己烷羧酸 → 粗己内酰胺→产品光亚硝化法苯 → 环己烷 → 粗己内酰胺 → 产品苯甲酸加氢制备亚硝基硫酸己内酰胺 caprolactam (简称CPL )分子式:C 6H 11NO 分子量:133.16结构式:己内酰胺是ε-氨基己酸H 2N(CH 2)5COOH 分子内缩水而成的内酰胺,又称ε-己内酰胺,它一种重要的有机化工原料,是生产尼龙—6纤维(即锦纶)和尼龙—6工程塑料的单体,可生产尼龙塑料、纤维、及L-赖氨酸等下游产品。
它常温下为白色晶体或结晶性粉末。
熔点(CH 2)5CONH69~71℃,沸点139℃(12毫米汞柱)、122~124℃(665Pa)、130℃(1599Pa)、165~167℃(2247Pa)。
比重:1.05(70%水溶液),熔化热:121.8J/g ,蒸发热:487.2J/g 。
纯己内酰胺的凝固点为69.2℃,在760mmHg 时沸点为268.5℃,85℃下密度1010kg/m3。
在20℃水中溶解度为100g 水溶解82g 己内酰胺。
受热时起聚合反应,遇火能燃烧。
常温下容易吸湿,有微弱的胺类刺激气味,手触有润滑感,易溶于水、甲醇、乙醇、乙醚、石油烃、环己烯、氯仿和苯等溶剂。
受热时易发生聚合反应。
己内酰胺的制法主要有:①以苯酚为原料,经环己醇、环己酮、环己酮肟而制得;②以环己烷为原料,用空气氧化法或光亚硝化法转化成环己酮肟,经重排CH 3+3/2O 2COOH +H2O Co COOH +3H2Pd/C H COOH 2NH 3+3O 2N 2O 3+3H2O N 2O 3+H 2SO 4+SO 32NOHSO 4Pt/Rh而制得;③以甲苯为原料,用斯尼亚法合成。
此外,也可以糠醛或乙炔为原料合成。
在制造过程中,环己酮(cyclohexanone)是主要的关键性中间原料,此关键性原料可藉由环己烷氢化或苯酚氢化得到,这两种制程相当类似,不同点仅在于触媒的使用和操作条件的不同而已。
- 1、下载文档前请自行甄别文档内容的完整性,平台不提供额外的编辑、内容补充、找答案等附加服务。
- 2、"仅部分预览"的文档,不可在线预览部分如存在完整性等问题,可反馈申请退款(可完整预览的文档不适用该条件!)。
- 3、如文档侵犯您的权益,请联系客服反馈,我们会尽快为您处理(人工客服工作时间:9:00-18:30)。
己内酰胺的合成路线及工艺消耗一、己内酰胺生产工艺早在1899年,Gabriel和Meas就通过加热ε-氨基己酸,首次合成了己内酰胺。
但是直到1943年,才由德国I.G.Farben公司实现了己内酰胺的工业化。
当时采用的工艺技术称为拉西法,起始原料为苯酚。
第二次世界大战后,I.G.Farben公司的技术被公开,世界己内酰胺应用得到了快速的发展。
荷兰DSM公司的HPO工艺对拉西法作了重大改进,自上世纪70年代以来在世界上得到了广泛的推广应用,成为己内酰胺生产最重要的工艺技术。
此外,德国巴斯夫公司(BASF)的一氧化氮还原工艺、日本东丽公司的光亚硝化法工艺、美国Allied Singal公司的异丙苯/苯酚工艺、意大利SNIA公司的甲苯法工艺、波兰Polimex/Polservice公司的Capropol工艺也各有特色,在己内酰胺工业生产中得到应用。
传统拉西法:德国I.G.FANBEN公司开发,其关键工艺是环己酮与硫酸羟胺发生肟化反应,生成环己酮肟,环己酮肟在发烟硫酸作用下经贝克曼重排反应生成己内酰胺。
硫酸羟胺是用硫酸中和亚**,生成脱酯硫酸盐,再发生水解反应产生的。
该工艺在羟胺合成、肟化反应、重排反应三道工序都使用硫酸,氨中和后产生大量的副产物硫酸铵,而硫酸铵的经济价值较低。
对传统拉西法的改进,主要着眼于降低硫酸铵的副产量。
Allied异丙苯/苯酚工艺:该工艺主要特点是用异丙苯法生产的苯酚为原料。
苯酚加氢生成环己酮,环己酮与硫酸羟胺经肟化反应生成环己酮肟,环己酮肟在发烟硫酸作用下经贝克曼重排反应生成己内酰胺。
硫酸羟胺是用硫磺、氨、二氧化碳和水经多步工艺生产的,硫酸铵副产量仍然较高。
巴斯夫一氧化氮还原工艺:该工艺的硫酸羟胺是控制氨氧化生成一氧化氮,再在硫酸中用氢气还原而生成的,硫酸铵副产量比传统拉西法少得多。
CAPROPOL工艺:该工艺在环己烷氧化制环己酮环节有一定特点,使用了钯催化剂,降低了氢氧化钠的消耗量和废碱液的生成。
环己酮与硫酸羟胺经肟化反应生成环己酮肟,环己酮肟在发烟硫酸作用下经贝克曼重排反应生成己内酰胺。
硫酸羟胺是用一氧化氮还原工艺生产的。
DSM-HPO工艺:该工艺的羟胺合成和环己酮肟化两个阶段都是在循环使用的磷酸缓冲液中完成的,不产生硫酸铵。
首先用磷酸缓冲液吸收氨氧化产生的二氧化氮气体,生成硝酸;然后用氢气还原磷酸缓冲液中的硝酸根离子,生成羟胺;富含羟胺的磷酸缓冲液再与环己酮逆流接触,经肟化反应生成环己酮肟。
该工艺的优势在于仅在环己酮肟重排反应阶段使用硫酸,因而大大降低了硫酸铵副产量。
不足之处是设备复杂,分离精制环节多,工艺控制难度大,催化剂较为昂贵。
目前世界上90%以上的己内酰胺都是通过上述几种基于拉西法的工艺生产的。
它们的共同特点是都经过环己酮和环己酮肟这两个中间产物,由环己酮与羟胺反应生成环己酮肟,环己酮肟再在发烟硫酸作用下经贝克曼重排生成己内酰胺。
环己酮主要是环己烷经空气氧化反应生产,小部分来源于苯酚加氢。
东丽光亚硝化工艺:在水银灯照射下,环己烷与亚硝酰氯和氯化氢生成氯化氢肟,再重排生成己内酰胺。
尽管有人认为这项工艺生产己内酰胺的成本最低,但迄今只有日本东丽公司采用该工艺建有两套共170万吨/年的生产装置,且多年来没有扩产的报道。
SNIA甲苯法工艺:该工艺用甲苯氧化生成苯甲酸,苯甲酸加氢生成环己烷羧酸,环己烷羧酸经中和、脱羧及重排生成己内酰胺。
该工艺硫酸铵副产量很高,而且原子经济性不佳,有较大的局限性,在意大利的装置已经停产,仅有我国石家庄化纤有限公司的一套原设计为50万吨/年的装置尚在营运。
二、新工艺的开发应用到目前为止,己内酰胺生产所采用的工艺都是以芳香族化合物或其衍生物为原料的。
近10几年来,国外一些大公司积极研究以非芳香族化合物为原料的工艺路线。
DSM、杜邦(Dupont)及壳牌(Shell)合作推出了一项以丁二烯和一氧化碳为原料生产己内酰胺的工艺,巴斯夫公司也申请了类似的专利。
巴斯夫公司和杜邦公司合作开发的丁二烯/甲烷工艺,在德国建成了1千吨/年的丁二烯/甲烷工艺的工业实验装置。
该工艺用丁二烯、甲烷和氨经多步工艺生产己二腈和己二胺,己二腈单端氰基加氢生产氨基己腈,氨基己腈通过水解和环化生成己内酰胺。
后来Rhodia公司也开发了一项类似工艺,并声称有所改进。
巴斯夫公司和杜邦公司曾计划于1995年在我国海南省以丁二烯/甲烷工艺建设一套联产15万吨/年己内酰胺、15万吨/年己二胺的大型装置,但该计划一再被推迟,迄今没有实施。
而台湾CPDC公司仍然购买DSM的HPO技术,在2000年建成投产一套12万吨/年的己内酰胺装置。
相形之下,说明以丁二烯为原料的新工艺对传统工艺并没有明显的竞争优势。
在拉西法技术基础发展的己内酰胺生产工艺,在过去30年来一直比较稳定,现在也面临着重大的突破。
环己酮氨肟化工艺、环己酮肟气相重排工艺、环己烷氧化新工艺开始进入工业应用环己酮氨肟化工艺:该工艺将环己酮、氨、过氧化氢置于同一反应器中,一步合成环己酮肟。
与其它工艺相比,具有流程短、环境友好、反应条件温和、设备投资低的优势。
该工艺自上世纪60年代就得到关注,意大利Enichem公司和中国石化都已完成了该工艺的中间试验,并拥有相关专利,其技术可靠性和经济可行性都已达到工业应用水平。
环己酮肟气相重排工艺:该工艺是在固体酸催化剂作用下,环己酮肟在气相重排成己内酰胺,由于不使用硫酸和氨,也就不产生副产物硫酸铵,可以大幅度降低生产成本。
国外多家公司对这项工艺的进行了研究,石油化工科学研究院和中国石化巴陵分公司也在积极开展研究,重点是提高催化剂的转化率、选择性和寿命。
日本住友公司采取流化床反应器,环己酮肟/甲醇/氮气在高温下通过分子筛,转化率为99.3%,己内酰胺的产率为95.3%,研究成果已经达到工业应用水平。
环己烷氧化新工艺:大连化学物理研究所与中国石化巴陵分公司利用自行开发的复合金属氧化物催化剂,研究环己烷非均相催化氧化新工艺生产环己酮,反应温度降低15℃至25℃,环己烷单程转化率提高1倍多,醇酮选择性提高10多个百分点,可显著提高设备效率和生产安全性,大幅度降低物耗、能耗和废液处理量,与目前的环己酮生产工艺相比,竞争优势十分明显。
湖南大学和中国石化巴陵分公司使用仿生催化剂也取得了类似的研究成果。
这项新技术的研究目前已经完成了中间试验。
日本住友公司采用意大利Enichem公司开发的环己酮氨肟化工艺和自行开发的环己酮肟气相重排工艺,于2002年开工建设一套6.5万吨/年的己内酰胺新装置,2003年2月完成施工,2003年4月投产。
中国石化股份有限公司组织石油化工科学研究院和巴陵分公司等科研、生产、设计单位联合开发的己内酰胺成套新工艺,已经取得了重大突破,并具有自主知识产权。
通过环己烷氧化新工艺、环己酮氨肟化工艺、环己酮肟气相重排工艺、己内酰胺精制新工艺的整合,可以较大幅度地降低己内酰胺成本。
现已着手对巴陵分公司己内酰胺生产装置分段实施改造,其中环己酮氨肟化制环己酮肟的改造将于2003年完成。
这套工艺如果能够顺利实现工业化,大幅度降低生产成本,将给己内酰胺以及下游产品带来活力。
目前主要工艺是环己酮与硫酸羟胺发生肟化反应,生成环己酮肟,环己酮肟在发烟硫酸作用下经贝克曼重排反应生成己内酰胺。
DSM-HPO工艺:该工艺的羟胺合成和环己酮肟化两个阶段都是在循环使用的磷酸缓冲液中完成的,不产生硫酸铵。
首先用磷酸缓冲液吸收氨氧化产生的二氧化氮气体,生成硝酸;然后用氢气还原磷酸缓冲液中的硝酸根离子,生成羟胺;富含羟胺的磷酸缓冲液再与环己酮逆流接触,经肟化反应生成环己酮肟。
该工艺的优势在于仅在环己酮肟重排反应阶段使用硫酸,因而大大降低了硫酸铵副产量。
不足之处是设备复杂,分离精制环节多,工艺控制难度大,催化剂较为昂贵。
主要工艺流程:环己酮肟化;环己酮肟液相贝克曼重排;精制3个工艺单元。
二、国内己内酰胺总产能在50万吨左右,浙江恒逸的20万吨/年装置正在建设中。
三、欧洲、美国和日本是传统的己内酰胺生产区域,主要生产厂家有巴斯夫、帝斯曼、霍尼韦尔、日本宇部工业、日本东丽、韩国己内酰胺公司、朗盛化工、住友化学等。
国内只有浙江巨化、巴陵石化、石家庄炼化、南京帝斯曼东方化工有限公司。
四、菏泽市东巨化工股份有限公司10万吨/年己内酰胺工程五、山东方明化工有限公司16万t/a己内酰胺项目拟建项目己内酰胺生产采用环己酮—羟胺肟化法中的HPO法。
HPO法工艺技术先进,原辅材料消耗低,副产硫酸铵少,生产装置安全可靠、易于操作,在国内外被广泛应用。
六、(1)DSM公司和杜邦公司的Altam工艺。
DSM公司和杜邦公司联合开发出基于C4的Altam工艺,新工艺采用丁二烯和一氧化碳(CO)为原料,不会联产硫酸铵,与常规技术相比,可节约费用约30%。
首先是丁二烯与一氧化碳和水或醇反应得到3-戊烯酸/甲酯,3-戊烯酸/甲酯异构化生成4-戊烯酸/甲酯,3-戊烯酸/甲酯和4-戊烯酸/甲酯的羰基合成反应,生成5-甲酰基戊酸/甲酯,5-甲酰基戊酸/甲酯还原胺化成6-氨基己酸/甲酯,6-氨基己酸/甲酯环化生成已内酰胺,当6-氨基己酸/甲酯的转化率为97%-98%时,已内酰胺的选择性为97%-99%。
对于Altam新工艺来说,要提高转化率和目的产物的选择性,关键在于催化剂的筛选和制备及反应条件的选择。
(2)己二腈工艺。
该工艺由巴斯夫与杜邦公司合作开发成功。
丁二烯与氢氰酸反应合成己二腈,已二腈部分加氢生成6-氨基己腈和已二胺的混合物,6-氨基己腈与水反应生成己内酰胺。
考虑到重组分的循环,已内酰胺的总收率约为93%。
该工艺的关键在于己二腈选择性部分加氢,开发成功高性能催化剂,使中间产物和最终产物的转化率和选择性达到高水平。
该工艺的主要优点是采用了价格较为低廉的丁二烯,流程较短,物耗能耗较低,不副产硫酸铵,缺点是HCN酸和腈类毒性较大。
(3)住友化学公司生产工艺。
日本住友化学公司结合意大利埃尼化学公司许可的氨化工艺,开发出生产己内酰胺的新技术。
该新工艺是将一种专用的高硅沸石催化剂FS-1代替硫酸使过氧化氢同氨进行氨氧化直接生产环己酮肟的技术与环己酮肟气相法贝克曼重排反应技术结合起来。
新工艺采用流化床反应器,使用甲醇为辅助反应剂,环已酮肟/甲醇/氮气在350℃、0.10MPa下通过分子筛,环已酮肟转化率为99.3%,环己酮肟和甲醇的空速分别为5.04g/g催化剂.h和8.76g/g催化剂.h,己内酰胺产率为95.3%,唯一的副产物是水,甲醇可以回收和循环使用。
住友化学公司己在日本爱媛建成一套6.7万吨/年己内酰胺生产装置。
该工艺由于不需要羟胺装置,从而降低了投资费用,但过氧化氢费用昂贵,使得必须大规模生产才能显示出其规模经济性和价格优势。