双边剪
滚切式双边剪与圆盘剪技术分析
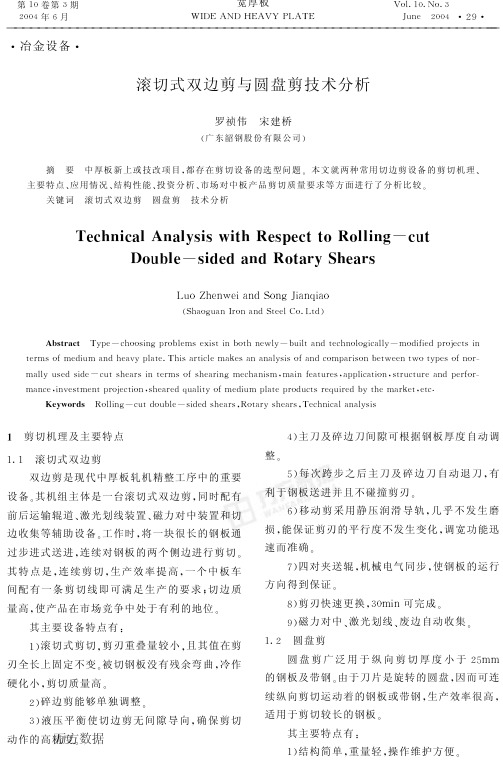
剪使用情况均很理想$特别是柳钢中板厂的投资 %*//万 元 从 意 大 利 购 买 的 二 手 滚 切 式 双 边 剪# 使 用 效 果 很 好$其 主 要 参 数 如 下-剪 切 钢 板 宽 度
故实际 AP3;%C!?@#通过计算 当 ?@B+//MAH#CP!’;/00 当 ?@B%1/MAH#CP%’;’00
< 性能分析比较
双边剪与圆盘剪性能分析比较见表 3$
= 剪切能力比较
’;3 圆盘剪剪切能力 以 一 重 圆 盘 剪 产 品 样 本 为 例#技 术 参 数 见 表
!$ 剪 切 厚 度 为 (2 !(00#剪 切 材 质 强 度 极 限
+//8400!.约 相 当 于 >+/"#最 大 剪 切 力 为 )//78$
根 据 圆 盘 剪 的 剪 切 力 计 算 公 式 计 算 不 同 ?@ 钢板的剪切厚度-
ABC!?@D.3EF3GH6I4D"4.!GH6I" 式中-AJJ 剪切力K
CJJ 剪切钢板厚度K ?@JJ 剪切钢板抗拉强度K DJJ 钢 板 延 伸 率#不 同 钢 种 延 伸 率 不
同 #!/L 钢 为 /;!!#3)M6N为 /;!($ F3JJ 系数#一般取 F3B3;’ IJJ 咬入角#一般为 3/23(O 取 IB3(O#DB/;!($故 AP 3;3!C!?@#考 虑 刃 口 磨 钝 的 影 响#一 般 把 计算的剪切力增大 3(Q2!/Q$
关键词 滚切式双边剪 圆盘剪 技术分析
’()*+,)-./+-.01,12,3*4(15()33646..,+78)93 :69;.(81,<(<-+<463-=0>*(-=1
双边剪剪刃间隙调整问题的研究分析

0 前 言
滚 切式 双边 剪 是 宽厚板 生 产线 上精 整设 备 中 的 核 心设 备 。利 用三 轴 三偏心 运 动原 理进 行滚 切式 双 边 定宽 剪 切 , 集 定 宽剪 切 碎 边 碎 断剪切 和 收集 功 能
2 ) 剪 切 间 隙过小 时 , 剪 切 边 缘 会 出现 二 次 剪 切
面;
5一退 刀 装 置 ; 6一回拉 装 置 ; 7一支 架
图 1 结构 示意
为 了保 证 剪 切 边 缘 的 质 量 ,在 钢 板 剪 切 过 程 中 ,不 同的钢 板厚 度和 强度 需要 选取 不 同的剪 刃 间 隙值 。偏 心轴 、上 刀架 导 向滑架 与退 刀连 杆共 同构
如图 2 所示 。偏心轴通过电机马达带动旋转 , 从 而
Hale Waihona Puke 影 响间 隙调 整精 度 的机构 主要 包括 剪刃 间隙 调
度 高 。具 有剪 切 面平 直 、 光滑 、 无变 形 、 几何 精度 高 、 剪 切速 度 快 等 优 点 , 在 国 内钢 厂 应 用 越 来 越 广 泛 。 由于剪 切 质量 直接 影 响钢 板 断面 的外 观 质 量 , 会 对 产 品的市 场形 象造 成 很 大 的影 响 , 因 此 双边 剪 剪 切 质 量是 反 映双 边剪 使 用 状 况 的重 要 指 标 , 而剪 刃 间 隙是影 响 剪切 质 量 的的 重 要 因素 之 一 。 因此 , 掌握 剪 刃 间 隙调整 的原 理及 方 法对 提 高产 品 的剪切 质 量
接痕 、 塌边 、 压 痕 等缺 陷 , 主 要 是 由于 剪 刃 间 隙 不 合
适造成的, 有 以下 几种 情 况 :
双边剪自动剪切可行性分析

双边剪自动剪切可行性分析发布时间:2022-07-16T03:44:14.693Z 来源:《科学与技术》2022年第5期第3月作者:孙敏覃剑锋[导读] 中厚板的生产线,分为加热区、轧机区、精整区以及成品区孙敏覃剑锋广西柳州钢铁股份有限公司中板厂广西柳州 545002 摘要:中厚板的生产线,分为加热区、轧机区、精整区以及成品区。
精整区包含着冷床,修剪尺寸、垛板等一系列功能,而双边剪的运用,则是精整区的关键。
双边剪的自动剪切,关乎着精整区域片域的自动化程度和升级。
背景:精整区域的自动化升级,目前最大制约为双边剪,双边剪的制约为自动对中,因为对中缘故,目前双边剪必须预留一个操作台,非常制约着自动化的发展,所以,双边剪自动对中迫在眉睫。
难点:英伟轧机轧制的原因,中厚板存在着许多不规则,双边的曲线,重心的偏移,中心线我弯曲,使得对中目前必须靠有经验的师傅进行肉眼对中可行性:轮廓仪系统介绍工艺描述及系统简介在3#冷床出口,距双边剪前最后一组磁力对中3-5米处安装一套轮廓检测系统,系统应用立体视觉测量原理,采用两台线阵CCD 相机作为传感器,配合主动LED光源,和精准标定,可准确计算视场范围内任一点的空间坐标,通过连续拍摄钢板边缘图像,将每帧图像精确合并,再结合辊道编码器测量钢板的实时数据换算出钢板长度,从而最终采集到钢板的完整轮廓图像并计算成工艺需要的数据。
工艺描述具体如下:钢板整体通过轮廓仪,测量出钢板整体轮廓数据。
轮廓仪发送钢板相对辊道位置及钢板姿态参数信息。
控制系统通过轮廓仪的参数信息,自动控制磁力对中装置的动作及横移量;自动控制结束,通过视频监控系统人工确认。
轮廓检测仪采用龙门架安装方式,现场配置光源中继箱和帧同步板,相机通过以太网线直接和仪表计算机系统相连,计算机放置在操作室内。
轮廓成像系统1)系统组成轮廓成像系统由双目相机系统配合主动面阵LED光源构成。
轮廓仪参考结构2)检测原理钢板经过轮廓仪,通过图像拼接得到整个钢板的图像,利用图像处理技术,计算出钢板整体轮廓,从而得出钢板轮廓的凹形侧边与连接测量部分端点间直线的最大距离,也就是所测钢板镰刀弯。
滚切式双边剪与圆盘式双边剪对比分析
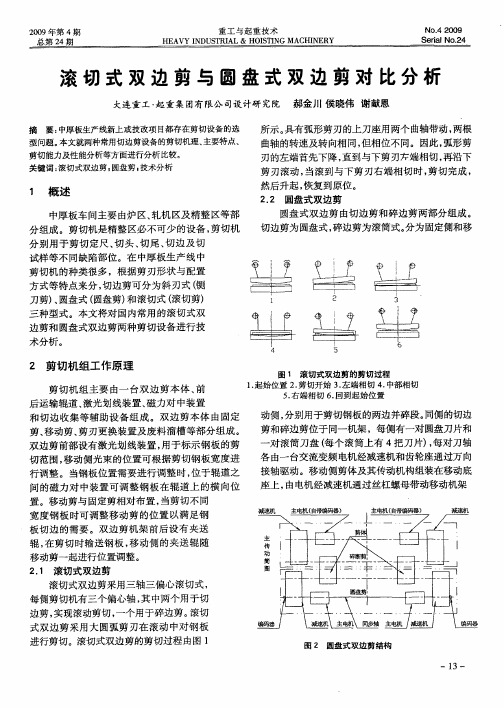
剪切能力及性 能分析等方面进行分析 比较。
关键词 : 滚切 式双边剪 , 圆盘剪 , 技术分析
1 概 述
中厚 板 车 间 主要 由炉 区 、 机 区 及精 整 区等 部 轧 分 组 成 。剪切 机 是精 整 区 必不 可少 的设 备 , 剪切 机
2 1 滚 切式 双边 剪 . 滚切 式双 边剪 采用 三轴 三偏 心 滚切 式 , 每侧 剪切 机有 三个 偏心 轴 , 中两 个用 于切 其
图 : .
—/ : _ 一 _
= l } :『I圆 ! 盘剪厂 ] —
:
一
L
\
I
L.j . H - r I
4
2 剪切机组工作原理
剪 切 机 组 主 要 由一 台双 边 剪 本 体 、 前
后 运 输辊道 、 光 划 线装 置 、 力对 中装置 激 磁 剪 、 动剪、 移 剪刃 更换 装 置 及废 料 溜槽 等 部分 组 成 。
圈 1 滚切式双边剪的剪切过程 1起始位置 2 剪切开始 3 左端相切 4 中部相切 . . . . 5 右端相切 6 回到起始 位置 . .
方 式 等特 点来 分 , 边剪 可 分为 斜 刃 式 ( 切 铡
≥兰车兰;
l
产—亍
2
乒;= 寺
刀剪) 圆盘 式 ( 、 圆盘剪) 和滚切式 ( 滚切剪) 三 种型 式 。本 文 将对 国内 常用 的 滚切 式双 边 剪 和 圆盘 式双 边剪 两种 剪 切 设备 进 行 技
术分 析 。
在底座上移动 , 完成机架开 口度 的调整 , 以便剪切 样 本为例 , 剪切 能力参 数见表 l 其 。 不 同宽度 的钢 板。 圆盘 式双边剪 结构见 图 2 。 滚 切 式双 边 剪 可剪 切 最 大 厚 度为 5rm , 0 a 剪
滚切式双边剪剪刃间隙精度控制的探讨

Kew rs K i a , dut et P ae s eiin y od nf gp A js n, a l lm dv t e m r li ao
0 前言 滚切式 双边 剪 是 中厚 板 剪 切线 的关键 设 备 ,
边 缘 不 均 匀 , 切 接 痕 明显 , 至 出现 台阶 和 缺 剪 甚
轴运 动进行 反 馈控 制 的编码 器 。偏 心 轴 、 刀架 上 导 向滑架 与 退 刀连 杆 共 同构 成 1个 曲柄 摇 杆 机 构 , 过偏 心轴 的角 度 改变 上 刀 架导 向滑 架 的倾 通 斜角 度 , 现剪刃 间隙值 的调整 , 图 1所示 。其 实 如
・
3 4
镑 j 第 2期 8卷 21 02年 4月
宽嬉缀
l DE A—D i tEAVY PLA1
r
i 8. )2 1 N .
 ̄ rl 2 2 pi 01
滚 切 式双 边剪 剪 刃 间隙精 度控 制 的探 讨
成利华
( 海交通大学) 上
摘
要
双边剪剪刃 间隙精度是影响双边剪切边质量 的主要原 因之一 , 剪刃间隙精度主要是指 剪刃 间隙
po l s uha isfcet nf gpajs et ag dpo a l lm acr ya e s ecutr esrs r e c s nu in ki a dut n r ea or r li cua w la onem aue bm s i e m n n p aes cs l t h
Ab t a t T e k i a c u a y o o b e—sd mmi g s e ri o eo ek y fco nl e cn h ut g sr c h nf g p a c r c f u l e d i et i r n h a n f h e tr ifu n i gt e c t n s t a s i q ai .T e k i a c u a y rf r t h i e e c ewe n t e k i a et g v l e a d k i a a al l m. u l y h nf g p a c r c e es o t e df r n e b t e h n f g p st n au n nf g p p r l i t e e i e es
精整车间双边剪工工作流程

精整车间双边剪工工作流程咱今天就来唠唠精整车间双边剪工的工作流程呀。
一、上班前的准备。
咱双边剪工,那上班之前可得把自己拾掇好喽。
得穿上合适的工作服,这工作服就像咱的战袍一样,得干净整洁又安全。
鞋子也不能马虎,得是那种防滑又舒服的,毕竟在车间里跑来跑去的,要是不小心摔一跤,那可就惨咯。
到了车间呢,得先去看看双边剪设备,就像去看自己的老朋友一样。
看看它有没有啥不对劲的地方,各个部件是不是都在自己该在的位置上,要是发现哪里有点小问题,就得赶紧报告给相关的负责人,可不能让小毛病变成大麻烦呀。
二、设备启动与检查。
设备要启动的时候,心里还真有点小紧张呢。
就像要开启一场大冒险一样。
按下启动按钮之前,再仔细检查一遍那些关键的部位,比如说刀片啦,是不是锋利又牢固。
这刀片就像咱们的武器,要是钝了或者松了,那可咋干活呀。
还有那些传动装置,就像机器的关节一样,得确保它们都顺滑得很。
等设备启动起来了,就竖起耳朵听听有没有啥奇怪的声音,要是有那种嘎吱嘎吱或者哐当哐当的声音,那肯定是哪里出问题了,就得赶紧停下来检查。
三、材料准备与上料。
接下来就该准备材料啦。
看着那些要被剪的材料,就感觉像是要给它们来个大变身似的。
把材料运到双边剪旁边的时候,可得小心着点,不能磕着碰着了。
上料的时候呢,要把材料摆放得整整齐齐的,就像排兵布阵一样。
要是材料歪歪扭扭的,那剪出来的东西肯定也不标准。
而且上料的速度也得掌握好,不能太快也不能太慢,太快了设备可能处理不过来,太慢了又影响工作效率。
四、正式剪切操作。
开始剪切的时候,那可真是全神贯注的时候啦。
眼睛得死死盯着材料和刀片的接触点,就像老鹰盯着猎物一样。
手也得稳稳地放在操作台上,随时准备调整参数。
这时候的感觉就像是在玩一场很精细的游戏,稍微有点差错就可能前功尽弃。
要根据材料的厚度和要求的尺寸,来调整双边剪的剪切力度和间距。
这可全靠经验和感觉呢,就像厨师做菜的时候放调料一样,多一点少一点都不行。
而且在剪切的过程中,还得时不时地检查一下剪出来的产品质量,要是发现有不合格的,就得马上调整设备,可不能让次品流出去呀。
双边剪板系统及其新技术

双边剪板系统及其新技术中厚板是国民经济中不可缺少的重要材料,例如国防,尖端科学,造船等都需要大量高强度的中厚钢板。
文章在简述了中厚板的基础上,着重说明了我国在双边剪板上的技术和应用。
标签:双边剪板;新技术;实际应用1 我国中厚板的现状及其剪切出现的缺陷1.1 现状近些年我国国内对中厚板的市场需求一直保持高速增长态势,并且由于钢材结构的调整、桥梁建筑的增多、船舶行业、油气输送等其它行业的高速发展,尤其是房地产行业的崛起更是给钢材发展带来不少的机遇。
房地产市场是从事房产、土地的出售、租赁、买卖、抵押等交易活动的场所或领域。
房地产既可以为普通居民服务,又可以建造特别的厂房和办公室来满足各行各业的需求和要求。
因此,房地产是日常生活一部分,它们的稳定和发展更是成为国民经济的一部分。
房地产既是人们避难和休息的场所,又是人们修养和品位的体现,建立和发展从事房产交易的市场是经济运行的要求。
2012年,全国商品房销售面积与销售额均同比增长,而且增幅不断扩大,累计销售面积不断扩大,这样出色的销售量使得中厚板的需求呈现急剧加快的现象。
目前,我国钢材的需求已经变为供不应求的态势。
这就促进了这就使得钢铁和炼钢行业高速发展。
但是,钢铁行业发展的同时,也带来不少的问题和困扰。
需求量多、出口量大、质量成下降趋势。
(1)中厚板的进出口现状我们都知道,第二行业是推动我国经济和社会的重要力量,所以,中厚板成为我国的重要产品也不足为奇。
但是,由于2008年美国次贷危机的爆发,接着是全球金融风暴的爆发,导致全球经济衰退、经济增长速度放缓,再加上全球各国对楼市等行业的宏观调控力度加大,使得整个市场严重缩水,全球产品出现供过于求的现象出现在各个行业,进而导致我国中厚板的出口数量大大减少。
(2)我国中厚板市场发展形势分析钢材工业是国民经济的重要基础之一,尤其是改革开放以后,更是成为经济建设的重要支柱,十二五期间钢材工业的发展被明确提上日程,更是成为产业布局和资源保障的主要布局,这是继钢铁产业调整和振兴产业的另外纲领性文件,2008年以来,钢铁行业陷入低迷,加上产能过剩,钢铁行业的前景令人担忧。
滚切式双边剪剪刃间隙调整的研究

( a g a gHe v lt l, in tn41 1 1 C ia Xin g n a yP aeMi X a ga 1 0 , h n ) l
●◇ ●◇ ●◇ ●◇ ●◇ ●0 ●◇ ●◇ ●◇ ●◇ ●◇ ●0 ●◇ ●◇ ●0 ●◇ ● <> ●◇ ●◇ ●◇ ●◇ ●◇ ●◇ ●◇ ●◇ ●( ) ●0 ●◇ ● 、 >● ◇ 。 ●◇ ●◇ ●◇ ●◇ ●◇ ●◇ ●◇ ●◇ ●
连杆的上下动作 , 使活动导板可以上下移动。齿轮马达 时带动 调整装置显示装置的指针转动 , 可以显示任何时刻 的剪刃间隙大
3 剪刃间隙的调整的常见故障及处理
致 , 差较 大日 因为 同一 侧有 4个 平行 的滑 动 导板 , 外一 个 相 。 另
小 , 图 1 示 。从 图 1 以看 出 , 滑 动导 板 4下 降 时 , 滑 31剪 刃 间隙平行 度 问题 如 所 可 当右 左 . 动导 板 1 0同时 上 升 , 时上 刀 架 就往 左 移 动 , 刃 间 隙就 增 大 , 这 剪 剪刃 间隙 不平 行 , 要是 剪刃 间 隙 出现入 口与 出 口的间 隙不 主
b e a js et eirdcd Te a u cai dt e m n a r ce o t s po 一 6 l p a ut n a t ue , fir m hn m a eta tp o hs h e r d a g d m no r h le e s n h r e p a e b t f
d ut t v eec dr a l ad terl i s i o ba a a lt hc es nt rcs ajsm n e i n o e f u n h e t nh l eg dpaeti n s i ePo eso e d c t ao pf d p n k h f
滚切式双边剪的控制要求及操作规程
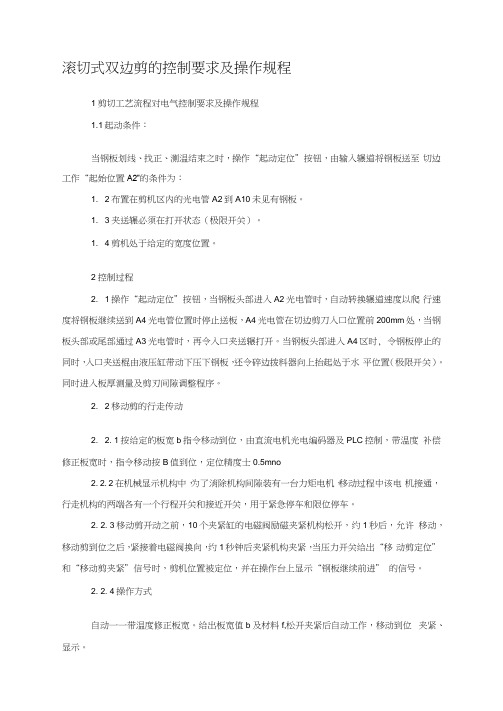
滚切式双边剪的控制要求及操作规程1剪切工艺流程对电气控制要求及操作规程1.1起动条件:当钢板划线、找正、测温结束之时,操作“起动定位”按钮,由输入辗道将钢板送至切边工作“起始位置A2”的条件为:1. 2布置在剪机区内的光电管A2到A10未见有钢板。
1. 3夹送辗必须在打开状态(极限开关)。
1. 4剪机处于给定的宽度位置。
2控制过程2. 1操作“起动定位”按钮,当钢板头部进入A2光电管时,自动转换辗道速度以爬行速度将钢板继续送到A4光电管位置时停止送板,A4光电管在切边剪刀入口位置前200mm 处,当钢板头部或尾部通过A3光电管时,再令入口夹送辗打开。
当钢板头部进入A4区时, 令钢板停止的同时,入口夹送棍由液压缸带动下压下钢板,还令碎边拨料器向上抬起处于水平位置(极限开关)。
同时进入板厚测量及剪刃间隙调整程序。
2. 2移动剪的行走传动2. 2. 1按给定的板宽b指令移动到位,由直流电机光电编码器及PLC控制,带温度补偿修正板宽时,指令移动按B值到位,定位精度士0.5mno2. 2. 2在机械显示机构中,为了消除机构间隙装有一台力矩电机,移动过程中该电机接通,行走机构的两端各有一个行程开关和接近开关,用于紧急停车和限位停车。
2. 2. 3移动剪开动之前,10个夹紧缸的电磁阀励磁夹紧机构松开,约1秒后,允许移动,移动剪到位之后,紧接着电磁阀换向,约1秒钟后夹紧机构夹紧,当压力开关给岀“移动剪定位”和“移动剪夹紧”信号时,剪机位置被定位,并在操作台上显示“钢板继续前进” 的信号。
2. 2. 4操作方式自动一一带温度修正板宽。
给出板宽值b及材料f,松开夹紧后自动工作,移动到位夹紧、显示。
手动一一用于检修、换刀时。
手动按钮夹紧松开、移动启动(快进、慢进、停、慢回、快回)快速100mm/s,慢速12mm/so夹紧定位。
力矩电机通' 断。
2. 2. 5显示:在操作台显示:板宽给定值,实际位置值B,板温。
试析双边剪的结构及影响切口质量的因素

试析双边剪的结构及影响切口质量的因素1 问题提出首秦公司4300mm生产线上的滚切式双边剪是由德国西马克(SMSD)公司设计(三轴三偏心结构),与沈阳重型机械有限责任公司合作制造的,2006年10月份投产,至今投入使用已7年。
剪切质量在同类剪子中可以排在前列,实现完美切口需要在设计、安装、维护、使用各个环节进行控制。
双边剪切完后理论上是两条平行线,但受到的影响因素很多。
根据技术人员对国内同类剪子的考察、了解、研究、分析,影响滚切式双边剪剪切钢板质量的因素归纳起来有两大类:一是两主切边剪刃不平行;二是钢板运输过程中前进轨迹偏离理论轨迹,即“跑偏”,这是众多中厚板厂遇到的最头疼的问题。
针对以上两大类问题,详细分析了具体原因,并且提出了相应的控制措施,希望对今后滚切式双边剪的设计制造、安装调试、使用都具有借鉴和参考价值。
2 滚切式双边剪设计特点简介德国西马克公司设计的滚切式双边剪具有剪切能力大、作业率高等优点。
机械设计中采用了滚切式原理,剪切重叠量很小,剪切角和重叠量沿剪刃长度方向几乎相等,所以被剪切钢板变形小、切口质量好。
设计中采用了多个偏心连杆机构:(1)主驱动三轴三偏心,两个偏心轴驱动主切边剪、一个偏心轴驱动碎边剪;(2)剪刃间隙调整结构,主切边剪和碎断剪剪刃间隙调整全部为偏心结构;(3)退刀结构,设计成三根带有偏心的轴连在一起组成;(4)压脚机构驱动,设计成凸轮结构。
这么多的机械偏心结构组装在一起,并且动作协调,所以对制造、安装的精度要求都非常高。
机械和自动化的完美结合实现了自动调整剪刃间隙、自动送板、自动压紧、自动退刀、自动检测钢板厚度、自动故障检测等。
3 影响切口质量因素及控制措施3.1 主剪刃平行度控制主剪刃平行度的保证是实现切口质量完好的第一要素。
双边剪切边剪剪刃长2080mm,单片剪刃两头距离中心线尺寸公差控制在0.10mm以内(见图1)。
加工制造过程中严格控制零部件尺寸公差,安装过程中每部分都要精确测量,尤其前后机架定位尺寸。
中厚板滚切式双边剪资料

是钢板的切口不光滑, 不够平整, 剪切厚度 1m 8m
以下的钢板往往有“ 错边”即切边的直线度不好) (
的情况发生。
2 夹送辊装置的调整
夹送辊装置在双边剪中的作用是夹紧被剪切 的钢板和输送待剪或剪过的钢板。钢板边部的剪 切要求: 直线度好, 没有任何剪切缺陷, 刀口平整,
上辊
水平状 态
辊缝趋于十 。
每一夹送辊的辊子中心线应与主刀刃线垂 直, 即钢板在辊道上移动方向与主刀刃线平行, 以 保证被剪切钢板移动的直线性 , 3 如图 ,
内偏心套
越 八. 戮
图 2 上下辊相对位置调整示意图
图 3 夹送辊与下主刀相对位置示意图
万方数据
·2 8·
20 年第 4 01 期 22 夹送辊的动作原理 . 钢板在夹送过程中受力情况如图 6 。图 6 中
图 5 夹送辊调整后安装精度示意图
万方数据
宽厚板
2 · 9
改善钢板与夹送辊之间的接触环境可削弱 af ,的
影响 ;
甲 曰白
Hale Waihona Puke 蜘净1 i Q 产生M . )m n Q > 2 . Q 产生MR ) < a Q
十 如
声M ,
、 城M.
M, 为电机的回转力矩, 设计上可调; R为夹送辊半径, 磨损后会减小, 设计上要求
边” 问题。切边不平整、 不光滑及“ 错边” 板显著减
由两侧阀台控制, 液压管路是相对独立的。 实际运行中, 两侧液压缸压力有差别, 相差 1 -2 a MP 。为解决两侧压力差别, 现将两侧液压缸
少, 中板产品的切边质量得到了极大的改善。
4 结束语 韶钢中板厂以滚切式双边剪为主的新剪切
双边剪剪切质量的改进

现代冶金Modern Metallurgy第47卷第5期2019年10月Vol. 47 No. 5Oct. 2019双边剪剪切质量的改进金柏林(南京钢铁股份公司"江苏南京10035)摘要:针对双边剪剪切存在的缺陷,分析影响剪切质量的因素,提出改进措施°关键词:双边剪;剪切缺陷;刀缝间隙;钢板跑偏;剪切力中图分类号:TG333. 2<1引言双边剪是中厚板生产线上的关键设备,根据二级设定值对钢板定宽,剪切钢板的两侧并同时碎边, 采用三轴三偏心式的结构,两根偏心轴用于主刀刃 的滚切,另一根偏心轴用于碎边刀的剪切,钢板剪切 步长"1300 ==,剪切次数1632次/=in,由于采用滚切原理,相同的剪切力,可以剪切强度更大、厚度更厚的钢板(40 mm 厚钢板的抗拉强度达105 MPa,50 mm 厚钢板的抗拉强度达80 MPa )。
在生 产过程中,充分发挥了双边剪节奏快、精度高、故障率低的优良性能,提高了生产效率;同时也存在一些剪切缺陷,影响了产品的外观质量,主要缺陷有:边 部重皮、边部撕裂、边部台阶等&1影响剪切质量的因素分析1.1刀缝间隙刀缝间隙是影响钢板边部剪切质量的主要因素,刀缝间隙包括垂直间隙和侧间隙&1)垂直间隙需保证上、下刀刃的重合量,如果上、下刀刃之间的垂直间隙过大,即重合量过小,上、 下刀刃将不能剪切钢板的全厚度,没有剪切的部分将形成台阶缺陷&上刀刃采用圆弧结构(半径R = 9500 mm ),两根偏心轴利用不同的偏心距和相位差,使得上刀刃沿着下刀刃滚切运动,每一点的剪切角度和重合量随着偏心轴的转动而变化&上主刀架 通过连杆与两根偏心轴相连,连杆上部采用轴瓦,下部采用球铰轴承,都是滑动摩擦,虽然采用了循环稀油润滑,但长时间使用后,将产生很大的磨损和间 隙,上刀架的平衡装置可以消除间隙,减少冲击,同时也改变了上刀刃的位置,减少了重合量;另外,上、下刀刃高度方向的磨损,也将加大垂直间隙,减少 上、下刀刃的重合量&2)上、下刀刃的侧间隙是影响钢板剪切质量的 重要因素,刀刃侧间隙过大,增大了剪切力,影响双边剪的使用寿命,同时影响剪切质量,刀刃在剪切过 程中将钢板向两侧拉而产生撕裂缺陷;刀刃侧间隙太小,会加快刀刃的磨损,同时使钢板边部产生剪切 缺陷,对于15 mm 厚以上的钢板,在剪断瞬间,多余的部分附着在断口面上而产生重皮缺陷;对于10 mm 以下的钢板,在钢板纵边的底部出现扣边缺陷&双边剪按照控制程序里的函数公式计算间隙值,然后通过一偏心轴来自动调整上、下刀刃的侧间隙&侧间隙计算公式Gap = a T +0式中T 为钢板的厚度;!为钢板厚度因子;"为钢板强度因子&!值根据剪切钢板的厚度来取值:a = 0. 1, 4. 5"T "15 mm ;a = 0. 095, 15<T "40 mm ;a = 0. 085, 40<T "50 mm 。
双边剪钢板跑偏原因探讨与调整

双边剪钢板跑偏原因探讨与调整宝钢湛江钢铁4200mm厚板厂产线布置四台剪切机,实现来料钢板长度和宽度上的剪切。
其中双边剪主要实现对来料钢板按规定尺寸进行双边剪切,然双边剪钢板跑偏现象一直是困扰现场生产的难题!文章介绍了夹送辊的机械结构及控制方式并结合双边剪运行的现场实际情况,对中板双边剪运行故障进行分析、总结,针对引起双边剪钢板跑偏的原因进行探讨并对夹送辊的调整做简单讨论。
为日后双边剪的检修、调整提供依据,确保双边剪连续运行的稳定性和可靠性,同时也提高了双边剪剪切成材率。
标签:夹送辊;钢板跑偏;调整;成材率Abstract:Four shearing machines are arranged in the production line of 4200mm thick plate factory of Baosteel Zhanjiang Iron & Steel Co.,Ltd.,in order to realize the shearing in the length and width of the incoming steel plate. The bilateral shear mainly realizes the bilateral shear of the incoming steel plate according to the specific size. However,the phenomenon of the bilateral shear plate deviation has been a difficult problem in the field of production. This paper introduces the mechanical structure and control mode of the clamping roller and analyzes and summarizes the faults of the double-side shear operation of the medium plate in combination with the actual situation of the operation of the two-sided shear,and discusses the causes of the deviation of the bilateral shear steel plate and discusses the adjustment of the clamping roller. It can provide the basis for the maintenance and adjustment of the bilateral shear in the future,ensure the stability and reliability of the continuous operation of the two-sided shear,and at the same time,improve the yield of the two-sided shear.Keywords:pinch roller;steel plate deviation;adjustment;yield前言双边剪机械装置主体部分由西马克设计,采用传统经典的滚切式剪切方案。
钢铁企业中双边剪设备安装流程设计

静 压 导 轨安 装 及 测量 方 法 图 1
装 80 粱 目 目 吨 担
的, 调整步骤 分三步进 行 : 找 : 挂钢线 ①粗 利用 1 锅 =o 板 5 3l m 8 6 6 2 o 2 2 5 己 5 将中心线进 行初步找正 。 找正后 , 将基板二次灌 2 铜 = 0 一m 703 4 板 5 用千分杆配合经纬仪对平行度 、 直 3 锶 - 0 7 o 4 14 1 板  ̄ 4I 5 66 q o 线度进行找正 , 用标尺和精密水准仪 、 框式水平 蛆 l I 己20 0 S 口 5 装示 图 意 对总平面度找正。 ③反复进行②的过程, 使其达 5 组 1 a 4 1 70 7 0 5 到精度要求 。为了避免温差对静压导轨调整 的 需要 因轴承间 影响 ,尽量每天选择相同时段进行静压导轨 的 内时 , 通过调 整滑板使三者 同心。 故通心轴 的穿人难度较大。 安装完成 安装调整。 以导轨 的上平面位测量基准面 , 安装 配合紧密 ,
{@ 移 动静哪瞄擞一 穆
I② 废 i l 女 #
接钩在扁担梁两端销轴上,扁担梁及吊装见示
电机 驱动齿 轮齿条的传动下 , 沿静压导轨移动 , 从而使移动剪到达所要剪切的钢 板宽度处 。 3. .2静压导轨 的调整 1 静压导轨固定在底板上 ,通过多组可调斜
垫板组 调整标高和水平度 , 并通 过一根导轨定 位。斜 垫板不 浇灌 , 以便调整静 压导轨水平度 、
意图 2 。 3. _ 3 2齿轮箱就位注意事项 移动 浆一 体 姑= 灌 单 阵 由于齿轮箱与机架上部两侧定位均为 十字 3双边剪主要设备安装 键连接 , 齿轮箱与滑板和机架三者通过通心 且 31 . 静压导轨的安装 轴连接 , 齿轮箱就位时 , 轮箱 必须严格 吊 故在 齿 3. .1静压导轨工作原理 1 齿轮箱就位后 , 将通心轴穿人齿 轮箱支撑座 静压导轨通过调整垫块 , 安装在基板上 , 并 平。 与基 础通过地脚螺栓连接 ,静压导轨的上表面 为形成静压的表面 , 压油膜形成时 , 当静 机架在
双边剪夹送辊调整方法
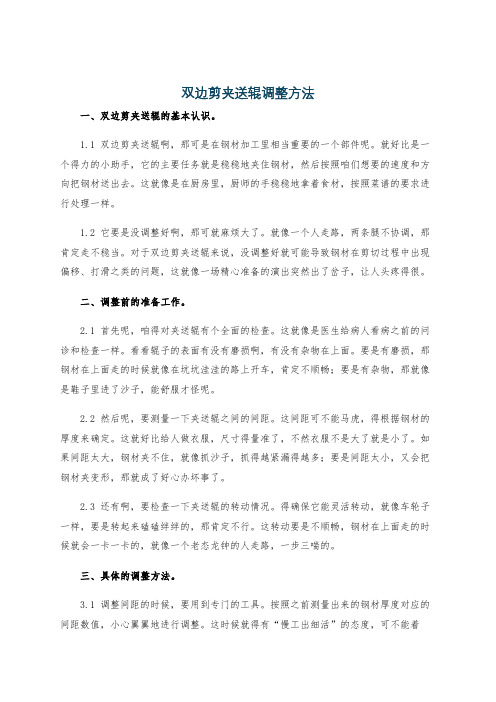
双边剪夹送辊调整方法一、双边剪夹送辊的基本认识。
1.1 双边剪夹送辊啊,那可是在钢材加工里相当重要的一个部件呢。
就好比是一个得力的小助手,它的主要任务就是稳稳地夹住钢材,然后按照咱们想要的速度和方向把钢材送出去。
这就像是在厨房里,厨师的手稳稳地拿着食材,按照菜谱的要求进行处理一样。
1.2 它要是没调整好啊,那可就麻烦大了。
就像一个人走路,两条腿不协调,那肯定走不稳当。
对于双边剪夹送辊来说,没调整好就可能导致钢材在剪切过程中出现偏移、打滑之类的问题,这就像一场精心准备的演出突然出了岔子,让人头疼得很。
二、调整前的准备工作。
2.1 首先呢,咱得对夹送辊有个全面的检查。
这就像是医生给病人看病之前的问诊和检查一样。
看看辊子的表面有没有磨损啊,有没有杂物在上面。
要是有磨损,那钢材在上面走的时候就像在坑坑洼洼的路上开车,肯定不顺畅;要是有杂物,那就像是鞋子里进了沙子,能舒服才怪呢。
2.2 然后呢,要测量一下夹送辊之间的间距。
这间距可不能马虎,得根据钢材的厚度来确定。
这就好比给人做衣服,尺寸得量准了,不然衣服不是大了就是小了。
如果间距太大,钢材夹不住,就像抓沙子,抓得越紧漏得越多;要是间距太小,又会把钢材夹变形,那就成了好心办坏事了。
2.3 还有啊,要检查一下夹送辊的转动情况。
得确保它能灵活转动,就像车轮子一样,要是转起来磕磕绊绊的,那肯定不行。
这转动要是不顺畅,钢材在上面走的时候就会一卡一卡的,就像一个老态龙钟的人走路,一步三喘的。
三、具体的调整方法。
3.1 调整间距的时候,要用到专门的工具。
按照之前测量出来的钢材厚度对应的间距数值,小心翼翼地进行调整。
这时候就得有“慢工出细活”的态度,可不能着急。
就像雕刻家在雕刻作品一样,每一刀都得慎重。
如果不小心调过了头,那就前功尽弃了,又得重新来一遍,这可就太浪费时间和精力了。
3.2 对于夹送辊的平行度也要调整。
这就像盖房子打地基,得让两边一样平才行。
要是不平行,钢材在夹送辊上走的时候就会偏向一边,就像走路走歪了一样。
双边剪安全生产职责

双边剪安全生产职责双边剪安全生产职责安全生产是一个重要的社会问题,涉及到人民群众的生命安全和财产安全。
在任何行业和领域,都应该高度重视安全生产工作,采取一切必要的措施来预防事故的发生,并尽最大努力保护员工和公众的安全。
双边剪本身是一种用于裁剪材料的工具,然而,如果不正确地使用或者没有进行必要的维护和保养,双边剪也可能会产生安全隐患。
因此,不论是使用双边剪的工人还是企业应该都对安全生产负有相应的职责,以确保使用双边剪的安全。
首先,作为使用双边剪的工人,我们应该充分了解和掌握双边剪的使用方法和安全操作规程。
在使用双边剪之前,我们应该接受必要的安全培训,了解如何正确使用双边剪、如何预防事故的发生以及如何处理紧急情况。
我们还应该熟悉双边剪的结构和特点,确保能够正确地选择合适的双边剪来完成任务。
其次,我们在实际操作中应该时刻遵守安全规定和程序。
我们应该正确佩戴个人防护用品,如安全帽、护目镜、防护手套等,并确保双边剪的工作区域保持清洁整洁。
我们还应该正确地操作双边剪,不得超负荷使用或者使用损坏的双边剪。
如果发现双边剪出现故障或者不安全的情况,我们应该立即停止使用,并及时报告给相关负责人,以便进行修理或更换。
除了工人的职责之外,企业也应该对双边剪的安全生产负有相应的责任。
首先,企业应该购买符合安全要求的双边剪,并保障双边剪的质量和性能。
在购买双边剪之前,企业应该对供应商进行严格的筛选和审核,确保双边剪符合相关的国家标准和规范。
此外,企业还应该建立完善的双边剪安全管理制度,明确各项工作的责任和要求。
企业应该为工人提供必要的安全培训和技能教育,确保他们能够正确地使用双边剪、预防事故的发生,并能够灵活应对突发情况。
此外,企业还应该定期检查和维护双边剪,确保其安全性能和工作效果。
企业应该建立定期检查的制度,对双边剪的结构、功能和安全装置进行检查,发现问题及时排除。
企业还应该为双边剪设备提供必要的保养和维修,包括更换磨损的刀片、修复损坏的零件等,以保证双边剪的正常工作和安全使用。
- 1、下载文档前请自行甄别文档内容的完整性,平台不提供额外的编辑、内容补充、找答案等附加服务。
- 2、"仅部分预览"的文档,不可在线预览部分如存在完整性等问题,可反馈申请退款(可完整预览的文档不适用该条件!)。
- 3、如文档侵犯您的权益,请联系客服反馈,我们会尽快为您处理(人工客服工作时间:9:00-18:30)。
滚切式双边剪简介1.机器的用途滚切式双边剪安装在中厚板轧钢厂的精整剪切线上,用来剪切经轧制、矫直、冷却、修磨后的单张钢板的两个纵向边部的同时,把切下来的边条横向剪切成一定长度的碎边小块并以收集。
碎边小块不经再次处理,可供装炉炼钢。
2.规格与性能2.1 钢板规格厚度6~50mm宽度成品1500~3300 mm 来料1550~3350 mm长度6000~42000 mm重量来料max 16t2.2 钢板强度极限厚度=50mm时σb≤800Mpa厚度≤40mm时σb≤1200Mpa2.3纵向剪切弯曲度≤1.0mm/10m2.4宽度公差0~2mm2.5两刀切口错位≤0.4mm2.6 剪切次数14~28次/min2.7 剪切步长max 1300mm2.8碎边宽度(单边)max 150mm min 20mm2.9 钢板剪切温度≤200℃以下2.10主刀片长度2200mm2.11主刀片开口度≈150 mm2.12主刀剪切角α1≈4.5°α2≈6°2.13碎边刀剪切角α≈3°2.14主刀后退量 2 mm2.15主刀重叠量 5 mm2.16碎边刀重叠量max 60 mm2.17主刀片左右侧同步方式机械同步2.18剪切力2X6500KN2.19换刀时间≤30 min2.20刀片侧隙调整范围0.4~4 mm2.21移动剪横移距离max 2000 mm2.22移动剪横移速度0~100 mm/s 2.23夹送辊送板速度max 2 m/s2.24夹送辊加速度max 2.5 m/s2 2.25夹送辊直径φ650mm2.26夹送辊开口度150mm2.27夹送辊左右侧同步方式机械同步2.28压料装置开口度150mm2.29主传动电机Z355-6 4台2.30换刀小车移动速度~0.25m/s 电动2.31换刀旋转台转角180°手动2.32压板压力2×16t2.33剪刃材料H132.34夹送辊液压缸压力 4.5~12mm时 4.5Mpa13~40mm时7Mpa41~50mm时9Mpa2.35对板形的要求为了确保剪机运转时不出故障,板材的不平度不得大于下值:板厚8mm时最大45mm板厚40mm时最大30mm板厚50mm时最大20mm板材头部和尾部舌形或燕尾形结构不得大于250mm3.工作原理与结构特点3. 1 工作原理3. 1 .1工作原理见图1(1)切边已经开始,碎边则刚刚开始;(2)碎边结束, 切边在继续;(3)剪切结束后, 切边剪与碎边剪松开板材,板材向前进给。
滚切剪是装有半径为R的弧形上刀片的上刀架,在具有不同相位角和偏心半径的两个曲轴及连杆带动下,并在控制杆的约束下,上刀片沿一个水平基面实现理想的滚动运动中,将钢板的两边剪断。
该基面比水平的固定下刀片略低约5mm,基面与下刀片的高度差即是上下刀片的重叠量,剪切过程中该重叠量保持不变,可通过改变两个曲轴相位角来调整刀片的重叠量,以适应不同厚度钢板的剪切,对于双边剪,视其剪切断面质量,一般不予调整刀片的重叠量。
由连续运转(自控)或断续运转(手控)的主电机,同时带动第三根曲轴,连杆以及装有碎边上刀片的上刀架,并以精确规定的运动规律完成纵向切边和废边的横向剪切。
当切边刀片和碎边刀片抬离下刀片向上张开时,控制夹送辊及辊道,将钢板送进一个确定的剪切步长。
钢板停止运送之时,在三曲轴的带动下完成钢板的切边及废边剪切,这一动作连续不断重复进行,直至切完这一张钢板为止。
3。
2 结构特征一台滚切式双边剪是由一台固定剪和一台移动剪组成,这两台剪机相对地安装在同一底座上。
每台剪机都有切边的纵向剪刀和切废边的碎边剪刀,它们各自由主电机经过齿轮传动装置及三根平行的曲轴带动。
每台剪机的主要组成部分包括:机架、传动装置、刀架及剪刃固定装置、剪刃间隙调整机构、剪刃后退机构、拨料器及压板装置、夹送辊、左右剪同步机构、移动剪横移装置、辊梁及碎边溜槽、快速换刀装置、板厚测量装置、稀油润滑系统、干油润滑系统、液压管路系统等。
滚切式双边剪的各组成部分结构特征如下3。
2。
1 机架固定剪和移动剪的入口及出口侧各有一个铸焊结构的机架,固定剪机架用螺栓固定在两个平行的底座上,移动剪安装在底座及横移装置上。
每台剪机的机架在靠近剪切线的下方与铸钢的下刀台连结在一起,其上部通过安全销用扭力搬手把合,当剪机过载时安全销被拉断,下刀架卸压,以保护设备安全.其下部用螺栓把合在一起。
机架在靠近剪切线的上方用螺栓及斜键与前面板连结在一起。
机架的上方前部装上主减速机箱体,用液压予应力拉杆及螺栓把它们连结成一个刚性的整体。
机架的上方后部与主电机的平台连结成一体。
机架下方后部与换刀装置的横梁连结成一体。
3。
2。
2 传动装置主传动装置由可分的上、中、下主减速机箱体、齿轮、轴及曲轴组成。
箱体由焊接和铸钢件制成,高速轴由滚动轴承支承,低速轴由滑动轴承支承。
固定剪和移动剪的主减速机上的全部齿轮与轴是通过外锥式中间套液压过盈连接,以便于调整曲轴的相位角的同时利于卸装。
主减速机上、中、下箱体用液压予应力拉杆连接在一起。
主电机安装在剪机机架上部的平台上,每台剪机由二台主电机传动。
主电机与主减速机之间由带制动盘的齿型安全联轴器连接,每个联轴器上装有二个安全销,以保护设备免受过载,每个安全联轴器的制动盘处装有一个制动器,当过载断销时由电气控制令其设备运转制动。
固定剪和移动剪的主传动同步是由主减速机上部的花键轴来实现。
当主机断电时,制动器随即将主传动装置制动。
3。
2。
3 剪刃间隙调整机构为了保证剪切质量,对于不同厚度钢板及不同的材质,在剪切前必须调整剪刃间隙。
切边刀片的调隙装置由前面板与上刀架之间镶有自润滑板的4个调整楔,上刀架与主减速机箱体之间镶有自润滑滑板的4个调整楔以及连杆和蜗轮箱组成,每个调整楔都由各自的连杆及蜗轮箱带动,蜗轮箱之间用万向接轴相连,并通过两个锥齿轮箱由一个共同的电磁制动异步电动机驱动。
前侧的每个调整楔由各自装于前面板的两组碟簧压紧机构自始自终压在上刀架上,以保证上刀架的无隙导向。
碎边刀片的调隙装置由装于前面板及主减速机箱体的镶有自润滑滑板的4个调整楔以及杠杆、连杆、蜗轮箱组成,每两个调整杆由各自的杠杆、连杆、蜗轮箱带动,此蜗轮箱与切边刀片调隙,蜗轮箱之间用离合器连接,蜗轮箱的另一端有手调离合器机构。
调整楔的调整是相互反向的,即前侧调整楔下降时后侧调整楔上升,反之亦然,这样可保证刃隙能准确地平行调整,刃隙是可以实现无级调整,刃隙与板材厚度成线性关系。
该设备刃隙最大值可调到4mm,由于安全原因,即为避免咬刀,最小值不得小于0.4mm。
当上刀片重磨时出现小于0.2mm偏差时,可通过刃隙调整来补偿。
刃隙调整可以采取自动及手动方式,自动调整时,由固定剪入口夹送辊上的板厚测量装置测量值转换到它的光电编码器中,再由PLC 控制刃隙调整机构的电机驱动,直到达到与板厚对应的刃隙为止。
手动调整一般用于换刀时的对固定剪和移动剪的刃隙的分别调整。
必须指出,碎边刀片刃隙也可与切边刀片一起自动调整,也可单独手动调整。
固定剪和移动剪各有一套完全相同的剪刃间隙调整机构。
3。
2。
4 剪刃后退机构两个剪机同时切边时,由于水平分力作用使钢板被夹紧在两刀片之间,为了防止将钢板刮伤或在上刀片向上回程时带起钢板,在每次剪切后,即上刀架从下死点位置起向上回程时,上刀片将从被切钢板边缘离开约2mm,并在向下行程开始之前又恢复到原来的剪切位置。
驱动切边刀片的两个曲轴后端分别装有控制凸轮,曲轴转动时靠凸轮曲面将运动传递到双弓形件上的导轮。
双弓形件又通过连杆、杠杆、拉杆系统将运动传递到肘杆,肘杆的后端支承于主减速机箱体上,其前端通过连杆与两个悬挂在减速机箱体上的楔形导向板相连,使其摆动。
剪切过成中楔形导向板处于前面位置上,剪切的水平分力由几乎全部伸展的肘杆及减速机箱体承受,为了避免肘杆处于死点以及过弯曲,肘杆接头在水平位置上方约2mm处被定位。
当肘杆水平接头升高时,带动楔形导向板向后摆动,同时由于前面板上的碟簧压紧机构的压力下,上刀架也随之向后摆动相同距离。
为使楔形导向板精确定位,可调整肘杆上的拉杆或者肘杆支座与减速机箱体之间的调整垫来调整。
此外,通过固定凸轮的张紧圈来准确定位凸轮及换刀装置的起始点。
3。
2。
5 刀架及剪刃固定装置由铸钢制成的上刀架装于前后调整楔之间,并通过装在机架入口侧的弹簧减震控制杆来实现准确滚切所必须的位移控制。
它不仅可以缓减刀片与钢板之间增加的磨擦阻力,还可以弥补由于系统的几何偏差而引起的约3~4mm位移成为可能。
上刀架通过两个连杆与两个曲轴相连结,曲轴一端支承在前面板上,另一端支承在主减速箱体中。
由铸钢制成的上碎边刀架布置成向送板方向大约倾斜5°左右,可避免被切着的废边条夹带,但为了更有效地防止边条被带起。
另外又设置了液压缸带动的刮料器。
通过第三根曲轴及其连杆带动碎边上刀架运动。
切边上刀片与上刀座是用螺栓连结在一起,并一同更换,为了能够快速换刀,上刀座与上刀架之间分别用5个夹紧缸和一个锁紧缸连结在一起。
它们都是碟簧夹紧,液压松开。
切边下刀片与下刀座也是用螺栓连结在一起,并一同更换。
为了快速更换刀片,下刀座与固定的下刀架之间分别用5个夹紧缸和一个锁紧缸连接在一起。
用锁紧缸来定位固定刀座,防止使其发生位置串动。
碎边上刀片与其上刀座之间,碎边下刀片与其下刀座之间用螺栓连结,并一同更换,为了快速更换刀片,刀座与其相应的刀架之间分别用一个夹紧缸和一个锁紧缸连结在一起。
3。
2。
6 碎边拨料器及压板装置为了使第一次切边后自由悬连着的废边条能够顺利通过下碎边剪刀,在上切边刀片的下方,下刀架的内侧装有液压缸带动的碎边拨料器。
在第一次碎边剪切后,由液压缸带动拨料器的导板落下,以让出下一块废边的通路,当导板向下摆到最低位置时,就与碎边溜槽相接,该溜槽位于切边刀片之下并有斜向通道,碎边刀片和出口侧夹送辊之间在斜向方向上有诸部分组成的溜槽,所有碎边通过后都落到剪机下方的碎边运输带上。
为了防止剪切钢板串动或翘头,以提高剪切断面质量及几何精度,每台剪机的第一、二根曲轴中心线处,在前面板上装有二个液压压板装置,剪切前,液压缸将压板推到待剪切的钢板上压紧,剪切后,控制阀将油压卸压,压板稍微抬起以便钢板顺利送进的同时,保证在下次剪切前压板提前压在钢板上。
液压缸的两端采用球接头,压板头的连接采用柱形接头,可以避免冲击活塞杆及压板头。
液压缸的渗漏油将由十字头槽内集中起来并用管子排在外面收集,以防滴漏在钢板上。
3。
2。
7 夹送辊及板厚测量装置为了将钢板准确地快速而断续地送进规定的剪切步长,在固定剪和移动剪的入口及出口侧装有四对夹送辊。
夹送辊悬挂在进料一侧及出料一侧的剪机机架上。
它们总是二对固定,另二对根据板宽变化随移动剪一起移动。