TA15、TB6钛合金切削加工用量和刀具的选择
数控加工中刀具的选择与切削用量的确定

数控加工中刀具的选择与切削用量的确定摘要:现代刀具显著的特点是结构的创新速走加快。
随着计算机应用领域的不断扩大,机械加工也开始运用数拉技术,这时刀具选择与切削用量提出了更高的要求。
本文就扣何确定数控加工中的刀具选择与切削用全进行了探讨。
关键词:数控技术;机械加工;刀具选择一、科学选择数控刀具1、选择数控刀具的原则刀具寿命与切削用量有密切关系。
在制定切削用量时,应首先选择合理的刀具寿命,而合理的刀具寿命则应根据优化的目标而定。
一般分最高生产率刀具寿命和最低成本刀具寿命两种,前者根据单件工时最少的目标确定,后者根据工序成本最低的目标确定。
选择刀具寿命时可考虑如下几点根据刀具复杂程度、制造和磨刀成本来选择。
复杂和精度高的刀具寿命应选得比单刃刀具高些。
对于机夹可转位刀具,由于换刀时间短,为了充分发挥其切削性能,提高生产效率,刀具寿命可选得低些。
对于装刀、换刀和调刀比较复杂的多刀机床、组合机床与自动化加工刀具,刀具寿命应选得高些,尤应保证刀具可靠性。
车间内某一工序的生产率限制了整个车间的生产率的提高时,该工序的刀具寿命要选得低些当某工序单位时间内所分担到的全厂开支较大时,刀具寿命也应选得低些。
大件精加工时,为保证至少完成一次走刀,避免切削时中途换刀,刀具寿命应按零件精度和表面粗糙度来确定。
与普通机床加工方法相比,数控加工对刀具提出了更高的要求,不仅需要刚性好、精度高,而且要求尺寸稳定,耐用度高,断屑和排屑性能好的同时要求安装调整方便,这样来满足数控机床高效率的要求。
数控机床上所选用的刀具常采用适应高速切削的刀具材料(如硬质合金、陶瓷等)并使用可转位刀片。
2、选择数控车削用刀具数控车削车刀常用的一般分成型车刀、仿形车刀、圆弧形车刀三类。
成型车刀也称样板车刀,其加工零件的轮廓形状完全由车刀刀刃的形伏和尺寸决定。
数控车削加工中,常见的成型车刀有小半径圆弧车刀、非矩形车槽刀和螺纹刀等。
在数控加工中,应尽量少用或不用成型车刀。
加工刀具和切削用量的选择

技师评审论文专业:数控车工浅谈数控加工中刀具选择和切削用量的确定姓名:刘胜华班级:074101学号:07指导老师:陈兵单位:江苏省盐城技师学院邮编:2240022010-3-17浅谈数控加工中刀具选择和切削用量的确定【摘要】:在切削加工中不仅要确定刀具的几何参数,还需选择切削用量的参数。
本文从加工零件的形状入手简单的讨论了数控加工中刀具的选择,从零件的加工质量和刀具的耐用度入手简单的讨论了切削用量的选择。
在切削深度A p和进给量F c初步选定后,合理的选择切削速度对切削效率和加工成本也有很大的影响。
【关键词】:数控加工;刀具选择;切削用量等。
无论在普通车床加工还是在数控加工中,刀具选择和切削用量的确定不仅影响加工效率,而且直接影响零件加工精度和表面粗糙度。
现在我们使用的许多机械设计与制造软件都提供自动编程功能,只要选择好所用的刀具、切削用量等有关的加工参数,就可以自动生成程序并传输至数控机床完成其加工。
这与普通车床的加工形成鲜明的对比,也是最大的不同点。
因此,本文在数控编程中必须面对的刀具如何选择和切削如何用量确定问题进行了论述。
一、数控加工常用刀具材料的类型及性能数控加工刀具必须适应数控机床高速旋转、高效率的特点,还需有较好的工艺性、经济性。
工具钢还应具有比较好的热处理工艺性。
在选择刀具材料时,很难找到各方面都很好的,因为材料硬度与韧性之间、综合性能和刀具价格之间都是相互制约的。
㈠、数控刀具的分类有多种方法具体如下。
1、根据结构可分为:整体式、镶嵌式。
2、根据制造刀具所用的材料可分为:高速钢刀具、硬质合金刀具、金刚石刀具、陶瓷刀具等。
3、从切削工艺上可分为:车削刀具、钻削刀具、铣削刀具等。
各类常用刀具材料的物理力学能如表1:表1各类常用刀具材料的物理力学性能材料种类相对密度硬度H R C抗弯能力冲击韧度导热率耐热性切削速度大体比值碳素钢7.6-8.160-652.16-----41.87200-2500.32-0.4合金7.5-760-6 2.35----41.8300-0.48-0.6钢.957400高速钢8.0-8.863-71.96-4.40.089-0.5715.7-25590-6902.1-3.2钨钴类14.3-15.389-91.51.08-2.160.02-0.0675-87.9800 3.15-4.76钨钛钴类9.35-13.29-92.50.789-1.20.03-0.0720.9-629004-4.8人造金刚石3.47-3.5610000.21-0.48-----146.54700-80025㈡刀具材料还应具备如下的性能:⑴高硬度刀具材料的硬度应大于工件材料的硬度,常温硬度应在H R C68以上;⑵足够的韧性承受较大切削力、冲击力;⑶高耐磨性刀具材料硬度越高,耐磨性越好;⑷高耐热性刀具材料在高温下保持硬度、耐磨性、强度和韧度的能力;⑸良好的工艺性与经济性二、数控加工中刀具的选择实际生产中,应考虑清楚硬质合金适合车削的材料、高速钢车刀适合车削什么样的材料。
钛合金切削中刀具材料选用及加工工艺介绍

( 4 ) 加工零件两边 U 形弧槽 图 1 所示 U 槽深 约 24mm,宽 18mm,圆弧为 R8,弧形槽弦长 61mm, 为半盲槽,加工后底部弧面及两侧面壁厚为 4mm。 由于是半盲槽,刀具进入切槽后,铣削阻力增大,排 屑不畅,刀具与切屑挤压现象严重,切削过程中有振 动,刀具易崩刃,如继续切削,刀具将在颈部处折 断。加工后的零件表面凹凸不平,表面粗糙度达不到 要求。在选用刀具上,原选用硬质合金立铣刀加工, 由于铣削产生的振动使铣刀崩刃,刀具寿命较短。后 改用超硬铝高速钢铣刀 ( 刀具牌号 W6MO5CrV2AI ) 切槽,取得了较满意的效果。其加工步骤如下:
!" !""! # $
!" 卷 第 !!# 期
专题报导
刀具材料类型 高速钢车刀 硬质合金车刀 端铣刀 硬质合金立铣刀 高速钢立铣刀 高速钢盘铣刀
前角 6O ~ 12O 3O ~ 7O
0O 10O ~ 12O
0O
表! 切削钛合金刀具的几何参数(供参考)
轴向前角 径向前角
5O ~ 8O
- 13O ~ 17O
( 1 ) 影响钛合金切削加工性的因素 钛及钛合 金 的 切 削 加 工 ,从 切 削 的 刀 具 耐 用 度 、加 工 表 面 的 质量及切屑形成和排屑的难易程度等方面来衡量, 钛及钛合金属难加工材料。钛及钛合金的切削加工 性比奥氏体不锈钢还差,退火或固溶处理的钛合金 切削加工性优于高温合金,而经时效处理后的钛合 金切削加工性和高温合金差不多。
TB6钛合金铣削刀具优选测评技术研究与应用

TB6钛合金铣削刀具优选测评技术研究与应用蒋理科;陈文清;陈志同;李勋【摘要】使用相对磨损率快速试验法对TB6切削过程中的刀具磨损进行了评价,得出结论:刀具磨损量在较小切削路程时会达到0.1mm左右,而后随着切削路程达到1000mm会逐渐下降到0.05mm左右,当切削路程继续增加时,磨损量会再次逐步上升.并且对工厂应用过程中不同厂家的刀具进行了评价,得出结论:去除相同体积的TB6时,威迪亚刀具消耗量最小.【期刊名称】《航空制造技术》【年(卷),期】2015(000)019【总页数】5页(P26-29,51)【关键词】刀具磨损;相对磨损率;TB6;刀具优选【作者】蒋理科;陈文清;陈志同;李勋【作者单位】中航工业昌飞河飞机工业(集团)有限责任公司;中航工业昌飞河飞机工业(集团)有限责任公司;北京航空航天大学;北京航空航天大学【正文语种】中文现代先进直升机的升力系统多采用钛合金球柔性桨毂,TB6钛合金(国外牌号为Ti1023)是国内近几年研制并开始工程应用的新材料,该类钛合金属于钛合金材料系列中较难加工的材料,目前国内还没有成熟的高效加工工艺。
其本身的力学性能对切削参数、刀具材料和结构、加工方式有很高的要求,导致切削困难,如果切削参数或刀具选用不合理,容易造成刀具磨损(见图1)及零件表面质量较差(见图2)等情况。
随着公司各型号生产任务日益增加,刀具使用的寿命对加工过程的经济性影响巨大,磨损的刀具还会影响零件加工表面的完整性和零件的加工精度。
因此,开发并使用高性能刀具、优化刀具切削用量,确保刀具具有合理的使用寿命是其中最为关键的问题。
图1 刀具损坏Fig.1 Tool failure图2 加工表面粗糙Fig.2 Rough surface为控制TB6钛合金难加工材料关键零件加工表面质量,并提升加工效率,利用经过验证的评价指标对刀具分别进行评价。
文章通过对硬质合金刀具铣削加工TB6钛合金进行刀具优选实验,表面完整性等研究工作,结合公司刀具订单式管理,建立一套以钛合金为代表的难加工材料刀具耐用度评定技术规范,用以指导钛合金加工刀具耐用度的评定,优选出适合加工钛合金TB6的刀具,突破刀具技术经济性综合评价技术难题,为公司钛合金加工刀具采购提供技术支持,并为航空用钛合金材料的切削参数数据库的建立和公司各型号批产奠定坚实基础。
钛合金车削加工刀具和切削用量的研究

钛合金车削加工刀具和切削用量的研究【摘要】刀具材料、刀具的几何角度以及切削用量的选择对于钛合金的车削加工有很大影响。
加工钛合金的刀具必须具备较高的热硬度、耐磨性、良好的韧性、较低的化学活性和较高的导热系数。
【关键词】钛合金;刀具材料;强度;耐磨性1.前言钛合金是继铁、铝之后的第三金属材料,由于钛合金具有无磁性、抗腐蚀性好、热强度高、质量轻等优点,最初它在美国的航空航天领域的应用中占有很重要的地位。
随后世界上许多国家都认识到钛合金材料的重要性,并相继对其进行了研究开发,广泛应用于工业生产、人民的日常生活中。
钛合金在生物医学方面有应用,钛合金在民用领域方面有应用:钛合金在自行车行业、汽车行业及体育行业都有广泛的应用。
钛合金制品应用势头发展迅猛的另一行业是汽车业。
研发直现今,汽车发动机气门、曲轴、连杆、悬簧、消音器和车体等,都用上了钛或钛合金。
2.钛合金的组织和性能根据退火处理后钛合金的金相组织分,钛合金可分为α、(α+β)、β钛合金三类(PCBN高速切削钛合金实验研究)。
(1)α钛合金退火组织为单一α相固溶体的钛合金称为a钛合金。
a钛合金主要以添加含有a稳定元素Al和中性元素,基本上不含或仅含少量的β稳定元素。
广义上的a钛合金包括平衡状态下含有很少β相的近a钛合金。
a钛合金的特点是组织稳定,高温性能好,热稳定性好,是耐热钛合会的基础。
但由于其不能承受热处理强化,因此室温下强度不是很高。
(2)β钛合金从β区淬火后能将高温的β-Ti稳定至室温即得到β钛合金或介β钛合金。
广义上的β钛合金包含平衡状态下不含α相的全β钛合金、具有较少α相的介稳定β钛合金以及具有较多α相的近β钛合金。
由于β钛合金体的心立方晶格结构,滑移系多,易产生塑性变形,高温组织稳定性差。
(3)α+β钛合金α+β钛合金是以α相为基体,添加适当的β稳定元素,一般也称为双相钛合金。
两相钛合金具有较好的综合力学性能,强度高于α钛合金,同时又保留了α钛合金的耐热性,可进行热处理强化,热加工性好。
数控加工中刀具选择与切削用量的确定

数控加工中刀具选择与切削用量的确定刀具的选择和切削用量的确定是数控加工工艺中的重要内容,它不仅影响数控机床的加工效率,而且直接影响加工质量。
CAD/ CAM技术的发展,使得在数控加工中直接利用CAD勺设计数据成为可能。
特别是微机与数控机床的联接,使得设计、工艺规划及编程的整个过程全部在计算机上完成成为可能。
现在,许多CAD/CAM软件包括提供自动编程功能,这些软件一般是在编程界面中提示工艺规划的有关问题,比如,刀具选择、加工路径、切削用量设定等,编程人员只要设置了有关的参数,就可以自动生成NC程序并传输至数控机床完成加工。
因此,数控加工中的刀具选择和切削用量确定是在人机交互状态下完成的,这与普通机床加工形成鲜明的对比,同时也要求编程人员必须掌握刀具选择和切削用量确定的基本原则,在编程时充分考虑数控加工的特点。
本文对数控编程中必须面对的刀具选择和切削用量确定问题进行了分析。
一、数控加工常用刀具的种类及性能数控加工刀具必须适应数控机床高速、高效和自动化程度高的特点,一般应包括通用刀具、通用连接刀柄。
刀柄要联接刀具并装在机床动力头上,因此已逐渐标准化和系列化。
数控刀具的分类有多种方法。
根据刀具结构可分为:①整体式;②镶嵌式。
根据制造刀具所用的材料可分为:①高速钢刀具;②硬质合金刀具;③金刚石刀具;④陶瓷刀具等。
从切削工艺上可分为:①铣削刀具;②钻削刀具;③镗削刀具;④车削刀具等。
刀具材料应具备的性能:(1)高硬度刀具材料的硬度应高于工件的硬度(2)足够的韧性承受切削力、振动和冲击;(3)高耐磨性耐磨性是材料抵抗磨损的能力;(4)高耐热性刀具材料在高温下保持硬度、耐磨性、强度和韧性的能力;(5)良好的工艺性二、数控加工刀具的选择刀具的选择应根据机床的加工能力、工件材料的性能、加工工序、切削用量以及其它相关因素正确选用刀具及刀柄。
刀具选择总的原则是:安装调整方便,刚性好,耐用度和精度高。
在满足加工要求的前提下,尽量选择较短的刀柄,以提高刀具加工的刚性。
钛合金零件切削用量与刀具参数的选择---中华工具网

钛合金零件切削用量与刀具参数的选择- 中华工具网钛合金零件切削用量与刀具参数的选择 主要加工方法钛合金零件的加工余量比较大,有的部位很薄(2~3mm),主要配合表面的尺寸精度、形位公差又较严,因此每项结构件都必须按粗加工→半精加工→精加工的顺序分阶段安排工序。
主要表面分阶段反复加工,减少表面残余应力,防止变形,最后达到设计图的要求。
其主要的加工方法有铣削、车削、磨削、钻削、铰削、攻丝等。
铣削用量及刀具的选择钛合金结构件中大量应用铣削加工,如零件内外型面。
刀具应选择具有高硬度、高抗弯强度和韧性、耐磨性好、热硬性好、工艺性好、散热性好的材料,主要为高速钢W6Mo5Cr4V2Al、W2Mo9Cr4VCo5(M42)和硬质合金YG8、K3O、Y330。
刀具几何参数应以保证刀具强度高、刚性好、锋利为原则,细长比不能过大,并分粗、精加工两种,加工时最好采用顺铣。
铣削刀具参数见表1,常规加工铣削用量见表2。
铣削时必须注入充足的水溶性油质切削液来降低刀具和工件的温度,切削液流量应不小于5L/min,以延长刀具的使用寿命。
在上述常规加工的基础上,为进一步提高铣削加工效率,我们在强力铣加工中心机床上进行了高效铣削试验,获得了较理想的切削用量、刀具和切削液,铣削用量数据见表3。
通过高效铣削与常规对比可以看出,高效铣削加工比常规加工效率提高了2~4倍,零件表面质量也得到较大的提高,加工周期大大缩短,制造成本相应降低。
车削用量及刀具的选择在刀具、切削用量、切削液选择合理的情况下,钛合金车削并不困难,与加工合金钢接近。
但车削钛合金表面氧化皮较为困难,一般在加工前用酸洗方法去掉表面薄层氧化皮,然后车削剩余的氧化皮,车削时切削深度应超过氧化皮深度1~5倍,走刀量可加大,但切削速度应降低。
刀具材料应选择YG类硬质合金材料。
刀具几何参数选择:前角g0=4°~8°,后角a0=12°~18°,主偏角Ø45°~75°,刃倾角l=0°,刀尖圆弧半径r=0.5~1.5mm。
钛合金材料及其加工刀具参数选择
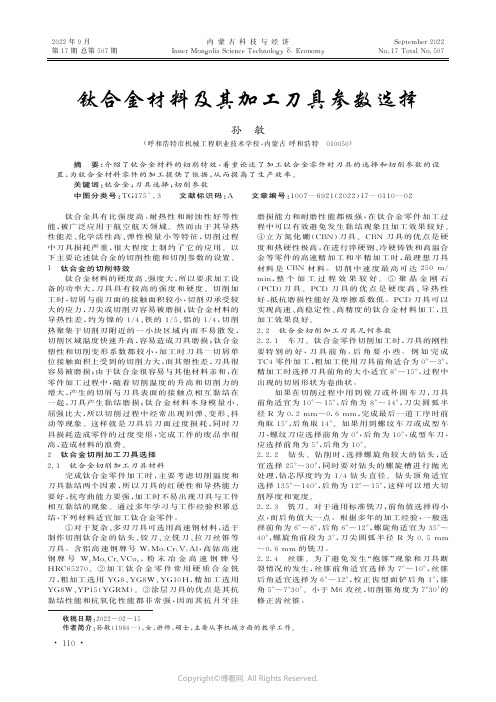
5 mm。
3
削 TC
根据 进 给 量 的 大 小 确 定 切 削 深 度 和 切 削
4 时,
速度,
见表 2,
表内个参数值均是工作中的经验值。
钛合金的切削用量
3.
1
3.
2
车削
用硬质合金 YG8 车 刀 加 工 表 面 被 氧 化 形 成 硬
膜的钛合金毛坯 件 时,粗 加 工 时,切 削 速 度、切 削 深
°~1
0
°,丝 锥
后角适宜选择为 6
°~1
2
°,校 正 齿 型 面 铲 后 角 1
°,锥
收稿日期:
2022-02-15
作者简介:孙敏(
1984—),女,讲师,硕士,主要从事机械方面的教学工作。
· 110 ·
Copyright©博看网. All Rights Reserved.
孙敏 · 钛合金材料及其加工刀具参数选择
1.
5~3
20~24
7~14
8~5
11~22
7~14
0.
08~0.
10
0.
10~0.
13
0.
10~0.
13
0.
06~0.
08
0.
07~0.
1
≤0.
6D
1.
5~6
钛合金工件进行攻丝时,
最 适 合 采 用 跳 牙 丝 锥,
0.
1
44
3
0.
2
30
0.
3
26
精铣
切削速度
/mm
每齿
进给量
/mm
轴向切深
/mm
30~45
动等现象。这样就 是 刀 具 后 刀 面 过 度 损 耗,同 时 刀
钛合金材料切削加工刀具的选择

钛合金材料切削加工刀具的选择
周泽智
【期刊名称】《机械制造》
【年(卷),期】2001(039)008
【摘要】钛合金材料历来被机械制造技术人员认为是难加工的材料。
作者根据多年的实践,整理出一套加工钛合金材料刀具的几何参数等实际数据,可作为有关人员对钛合金材料切削加工时的参考。
【总页数】3页(P17-19)
【作者】周泽智
【作者单位】南方航空动力机械公司工具厂
【正文语种】中文
【中图分类】TG71
【相关文献】
1.钛合金TC4粗加工刀具优选及切削参数优化 [J], 周超;李勋;陈五一
2.树脂基玻璃纤维复合材料加工刀具和切削参数的选择 [J], 尹垒;黄勇;孔博
3.高速切削加工刀具材料的性能分析及合理化选择 [J], 丁杰;赵杰;张振金
4.钛合金车削加工刀具和切削用量的研究 [J], 游红超;袁芬
5.木质材料CNC数控加工刀具的选择与切削用量确定 [J], 李黎
因版权原因,仅展示原文概要,查看原文内容请购买。
钛合金切削中的刀具选择与切削参数优化

钛合金切削中的刀具选择与切削参数优化钛合金是一种具有优异性能的金属材料,广泛应用于航空、航天、汽车等领域。
然而,由于钛合金的高强度、低导热性和易生成切屑困难等特点,使得它在加工过程中面临着许多挑战。
为了克服这些挑战,合理选择刀具和优化切削参数是至关重要的。
首先,刀具的选择对于钛合金切削至关重要。
钛合金具有较高的热硬度和化学活性,因此能够应对高温和高速切削。
在刀具选择上,硬质合金刀具是首选材料,其具有高硬度、耐磨性和热稳定性。
同时,镀膜刀具也是常用的选择,通过在刀具表面形成TiC、TiN等涂层来提高刀具的磨损抗力。
其次,切削参数的优化也是钛合金切削中必不可少的一环。
刀具的进给速度、切削速度和切削深度等参数的合理选择对于提高加工效率和延长刀具寿命至关重要。
一般而言,钛合金切削的切削速度相对较低,控制在刀具的合理范围内,以避免切削温度过高造成刀具的热退火和变形。
同时,合理选择切削深度和进给速度,以平衡加工效率和切削力之间的关系。
此外,冷却润滑剂的使用也对钛合金切削具有重要影响。
由于钛合金的高热导率和低导热性,加工过程中产生的高温难以迅速散热,容易导致刀具失效和表面质量的下降。
因此,在切削过程中适时地引入冷却润滑剂,可以有效地降低切削温度和摩擦系数,减少刀具磨损,提高切削效率和表面质量。
此外,钛合金的切削还需要注意刀具的刃角和刃口形状的选择。
一般而言,较大的刃角有利于分散切削力,减小切削温度和切削力,从而延长刀具寿命。
而刃口则需要选择合适的刃口形状,以满足不同切削任务的需求,如截削刃口、弧面刃口等。
通过合理选择刃角和刃口形状,可以优化切削过程,提高加工效率和刀具寿命。
另外,切削中的刀具磨损以及破损需要及时监测和处理。
在钛合金切削过程中,由于材料的高硬度、切削力的集中以及高温的影响,刀具的磨损和破损较为常见。
因此,及时监测刀具的磨损和破损情况,及时更换和修复刀具,可以保证加工质量和刀具使用寿命。
总结起来,钛合金切削中刀具的选择与切削参数的优化是提高加工效率和保证加工质量的关键。
钛合金与加工
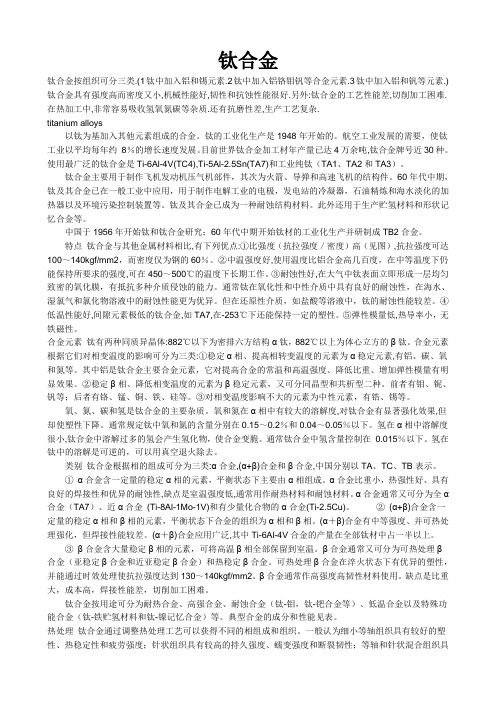
钛合金钛合金按组织可分三类.(1钛中加入铝和锡元素.2钛中加入铝铬钼钒等合金元素.3钛中加入铝和钒等元素.)钛合金具有强度高而密度又小,机械性能好,韧性和抗蚀性能很好.另外:钛合金的工艺性能差,切削加工困难.在热加工中,非常容易吸收氢氧氮碳等杂质.还有抗磨性差,生产工艺复杂.titanium alloys以钛为基加入其他元素组成的合金。
钛的工业化生产是1948年开始的。
航空工业发展的需要,使钛工业以平均每年约8%的增长速度发展。
目前世界钛合金加工材年产量已达4万余吨,钛合金牌号近30种。
使用最广泛的钛合金是Ti-6Al-4V(TC4),Ti-5Al-2.5Sn(TA7)和工业纯钛(TA1、TA2和TA3)。
钛合金主要用于制作飞机发动机压气机部件,其次为火箭、导弹和高速飞机的结构件。
60年代中期,钛及其合金已在一般工业中应用,用于制作电解工业的电极,发电站的冷凝器,石油精炼和海水淡化的加热器以及环境污染控制装置等。
钛及其合金已成为一种耐蚀结构材料。
此外还用于生产贮氢材料和形状记忆合金等。
中国于1956年开始钛和钛合金研究;60年代中期开始钛材的工业化生产并研制成TB2合金。
特点钛合金与其他金属材料相比,有下列优点:①比强度(抗拉强度/密度)高(见图),抗拉强度可达100~140kgf/mm2,而密度仅为钢的60%。
②中温强度好,使用温度比铝合金高几百度,在中等温度下仍能保持所要求的强度,可在450~500℃的温度下长期工作。
③耐蚀性好,在大气中钛表面立即形成一层均匀致密的氧化膜,有抵抗多种介质侵蚀的能力。
通常钛在氧化性和中性介质中具有良好的耐蚀性,在海水、湿氯气和氯化物溶液中的耐蚀性能更为优异。
但在还原性介质,如盐酸等溶液中,钛的耐蚀性能较差。
④低温性能好,间隙元素极低的钛合金,如TA7,在-253℃下还能保持一定的塑性。
⑤弹性模量低,热导率小,无铁磁性。
合金元素钛有两种同质异晶体:882℃以下为密排六方结构α钛,882℃以上为体心立方的β钛。
钛合金切削参数选择
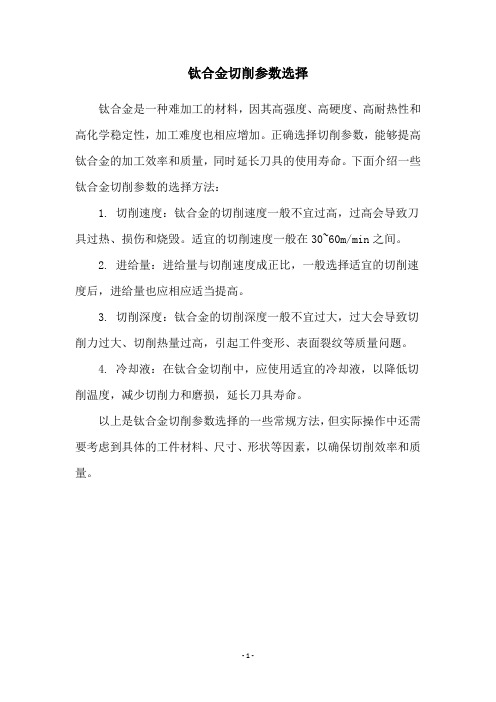
钛合金切削参数选择
钛合金是一种难加工的材料,因其高强度、高硬度、高耐热性和高化学稳定性,加工难度也相应增加。
正确选择切削参数,能够提高钛合金的加工效率和质量,同时延长刀具的使用寿命。
下面介绍一些钛合金切削参数的选择方法:
1. 切削速度:钛合金的切削速度一般不宜过高,过高会导致刀具过热、损伤和烧毁。
适宜的切削速度一般在30~60m/min之间。
2. 进给量:进给量与切削速度成正比,一般选择适宜的切削速度后,进给量也应相应适当提高。
3. 切削深度:钛合金的切削深度一般不宜过大,过大会导致切削力过大、切削热量过高,引起工件变形、表面裂纹等质量问题。
4. 冷却液:在钛合金切削中,应使用适宜的冷却液,以降低切削温度,减少切削力和磨损,延长刀具寿命。
以上是钛合金切削参数选择的一些常规方法,但实际操作中还需要考虑到具体的工件材料、尺寸、形状等因素,以确保切削效率和质量。
- 1 -。
钛合金加工切削参数表

钛合金加工切削参数表【实用版】目录一、引言二、钛合金概述1.钛合金的定义与特点2.钛合金的应用领域三、钛合金加工切削参数表1.切削速度2.进给速度3.刀具直径4.刀具材料四、切削参数对钛合金加工的影响1.切削速度对加工效率和表面粗糙度的影响2.进给速度对加工效率和刀具磨损的影响3.刀具直径对加工精度和切削力的影响4.刀具材料对切削性能和刀具寿命的影响五、选择合适的切削参数1.根据钛合金的特性选择切削参数2.根据加工工艺和设备选择切削参数3.根据加工需求和经济性选择切削参数六、结论正文一、引言随着航空航天、医疗和化工等领域的飞速发展,对钛合金的需求越来越大。
作为一种重要的金属材料,钛合金因其优良的力学性能、良好的抗腐蚀性能和较低的重量而备受青睐。
然而,钛合金的加工难度较大,对切削参数的选择提出了较高要求。
本文旨在介绍钛合金加工切削参数表,以帮助工程师更好地进行钛合金加工。
二、钛合金概述1.钛合金的定义与特点钛合金是指以钛为基础,加入一定比例的铝、钒、钛等元素组成的合金。
钛合金具有优良的力学性能、良好的抗腐蚀性能和较低的重量,广泛应用于航空航天、医疗和化工等领域。
2.钛合金的应用领域钛合金在航空航天领域用于制造飞机发动机、机身结构等部件;在医疗领域,用于制造人工关节、牙科植入物等;在化工领域,用于制造热交换器、反应釜等设备。
三、钛合金加工切削参数表钛合金加工切削参数表主要包括切削速度、进给速度、刀具直径和刀具材料四个方面。
1.切削速度切削速度是指刀具在单位时间内沿刀尖的线速度。
切削速度的选择应根据钛合金的硬度、刀具材料和加工工艺进行调整。
2.进给速度进给速度是指刀具在单位时间内沿刀尖的线性移动速度。
进给速度的选择应根据加工效率、刀具磨损和表面粗糙度进行调整。
3.刀具直径刀具直径的选择应根据加工精度、切削力和刀具寿命进行调整。
直径较小的刀具可获得较高的加工精度,但切削力较小,刀具寿命较短;直径较大的刀具切削力较大,刀具寿命较长,但加工精度较低。
钛合金材料及其加工刀具参数选择

钛合金材料及其加工刀具参数选择
孙敏
【期刊名称】《内蒙古科技与经济》
【年(卷),期】2022()17
【摘要】介绍了钛合金材料的切削特效,着重论述了加工钛合金零件时刀具的选择和切削参数的设置,为钛合金材料零件的加工提供了依据,从而提高了生产效率。
【总页数】3页(P110-111)
【作者】孙敏
【作者单位】呼和浩特市机械工程职业技术学校
【正文语种】中文
【中图分类】TG175.3
【相关文献】
1.钛合金材料切削加工刀具的选择
2.加工淬硬钢时刀具材料及刀具几何参数选择方法研究
3.不同材料和刀尖圆弧半径刀具加工TC4钛合金的表面质量及刀具磨损行为
4.采用AMBORITE刀具加工硬金属材料时加工参数的选择实例
5.钛合金材料零件加工的刀具参数选择
因版权原因,仅展示原文概要,查看原文内容请购买。
- 1、下载文档前请自行甄别文档内容的完整性,平台不提供额外的编辑、内容补充、找答案等附加服务。
- 2、"仅部分预览"的文档,不可在线预览部分如存在完整性等问题,可反馈申请退款(可完整预览的文档不适用该条件!)。
- 3、如文档侵犯您的权益,请联系客服反馈,我们会尽快为您处理(人工客服工作时间:9:00-18:30)。
TA15 TB6钛合金切削加工用量和刀具的选择
加工的研究是必要的,特别是铳削高效加工的探索尤其显得紧迫和重要。
TA15、TB6钛合金材料主要特征
TA15 a钛合金是a相固熔体组成的单相合金。
该合金室温强度在930MPa以上,耐热性高于纯钛,组织稳定,抗氧化能力强,500〜600 C下仍保持其强度,抗蠕变能力强,但不
能进行热处理强化。
TB6 b钛合金是b相固熔体组成的单相合金。
该合金室温强度在1105MPa以上,但热稳
定性较差,不宜在高温下使用。
TA15、TB6钛合金的切削加工工艺特性
摩擦系数大,导热系数低,刀尖切削温度高。
钛合金热导率仅为钢的1/4、铝的1/14、铜的1/25 ,因而散热慢,不利于热平衡。
切削时产生的切削热都集中在刀尖上,使刀尖温度很高,易使刀尖很快熔化或粘结磨损而变钝。
弹性模量小。
钛合金的弹性模量只有30CrMnSi的56%,这说明零件的刚性差,切削时
易产生弹性变形和振动,不仅影响零件的尺寸精度和表面质量,而且还影响刀具的使用寿命;
同时造成已加工面的弹性恢复较大,刀具后面摩擦增加导致刀具过快磨损。
化学活性大。
在300 C以上时有强烈的吸氢、氧、氮的特性,造成加工表面易产生脆硬的化合物,切屑形成短碎片状,使刀具极易磨损。
钛合金化学亲和力较强,极易与其他金属亲和结合。
在加工中切屑与刀具的粘结现象严重,使刀具的粘结和扩散磨损加大。
TA15、TB6钛合金零件切削用量和刀具参数的选择
主要加工方法
钛合金零件的加工余量比较大,有的部位很薄(2〜3mm),主要配合表面的尺寸精度、
形位公差又较严,因此每项结构件都必须按粗加工T半精加工T精加工的顺序分阶段安排工序。
主要表面分阶段反复加工,减少表面残余应力,防止变形,最后达到设计图的要求。
其主要的加工方法有铳削、车削、磨削、钻削、铰削、攻丝等。
铳削用量及刀具的选择
钛合金结构件中大量应用铳削加工,如零件内外型面。
刀具应选择具有高硬度、高抗弯强度和韧性、耐磨性好、热硬性好、工艺性好、散热性
好的材料,主要为高速钢W6Mo5Cr4V2AJ W2Mo9Cr4VCo5(M42和硬质合金YG8 K3O Y330。
刀具几何参数应以保证刀具强度高、刚性好、锋利为原则,细长比不能过大,并分粗、精加工两种,
加工时最好采用顺铳。
铳削刀具参数见表1,常规加工铳削用量见表2。
铳削时必须注入充足的水溶性油质切削液来降低刀具和工件的温度,切削液流量应不小
于5L/min ,以延长刀具的使用寿命。
在上述常规加工的基础上,为进一步提高铳削加工效率,我们在强力铳加工中心机床上进行了高效铳削试验,获得了较理想的效果。
切削用量、刀具和切削液,铳削用量数据见表
3。
通过高效铳削与常规对比可以看出,高效铳削加工比常规加工效率提高了2〜4倍,零件表面质量也得到较大的提高,加工周期大大缩短,制造成本相应降低。
车削用量及刀具的选择
在刀具、切削用量、切削液选择合理的情况下,钛合金车削并不困难,与加工合金钢接近。
但车削钛合金表面氧化皮较为困难,一般在加工前用酸洗方法去掉表面薄层氧化皮,然后车削剩余的氧化皮,车削时切削深度应超过氧化皮深度1〜5倍,走刀量可加大,但切削
速度应降低。
刀具材料应选择YG类硬质合金材料。
刀具几何参数选择:前角gO=4°〜8°,后角a0=12°〜18°,主偏角?45°〜75°,
刃倾角1=0 °,刀尖圆弧半径r=0.5〜1.5mm。
切削用量的选择:主轴转速n》23Or/min,进给量f >0.10〜0.15mm/r,切削深度
ap=1.5 〜2.0mm。
车削时必须注入充足的水溶性油质切削液来降低刀具和工件的温度,提高刀具的耐用度。
磨削用量及刀具的选择
磨削加工可获得较高精度,但由于钛合金的特有性质决定了钛合金磨削非常困难。
磨削时砂轮磨损严重,容易变钝,磨削比也较低;同时易在表面产生有害的拉应力及严重的表面
烧伤现象,因此应尽量避免磨削加工,以精铳代替。
磨削材料选择:磨削钛合金选用绿碳化硅(TL)、黑碳化硅(TH)两种磨料。
如出现磨削烧伤趋势,应使用人造金刚石或立方氮化硼砂轮,其效果好,但价格昂贵。
砂轮硬度选择较软砂轮R3 ZR1、ZR2,粒度选择46、60为佳,选A类结合剂。
磨削用量选择见表4。
钛合金零件在磨削过程中必须充分冷却,否则零件会变色甚至烧伤。
磨削液除具有冷却、
润滑和冲洗作用外,更重要的还在于能有效地抑制钛与磨料的粘附和化学反应。
表5
表6
表7
表8钻头直径与切削用量的关系
适当增大钻头顶角,顶角范围由118°〜120°增加到135。
〜140°,其目的是增强切削部分并使切削厚度增加,改善钻削效果。
选择合适的螺旋角b, b角增加,前角也增加,切削轻快,易于排屑,扭矩和轴向力也小,见表5。
增大钻心厚度,以提高钻头强度。
钻心厚度一般为:K=(0.45〜0.32)D , D为钻头直径。
增大钻头外缘处后角,可以使横刃锋利,改善切削性能,特别对钻心处的钻削加工有明显改善,外缘处后角选择见表6。
加工成倒锥K,减小棱带同孔壁摩擦,使钻头切削时扭矩减小,提高效率,倒锥度见表
7。
钻削用量见表8。
钛合金进行钻削和攻丝加工时最好不用含氯的冷却液,避免产生有毒物质和引起氢脆。
钻削浅孔时,可用电解切削液;钻削深孔时,可用N32机械油加煤油,也可用硫化切削铰削用量及刀具的选用
钛合金铰孔是最后一道精加工工序,不仅要考虑生产率的问题,更重要的是要保证孔的
加工质量(精度和表面粗糙度)。
为此必须保证刀具质量,合理选择切削用量,注意铰刀与钻铰模的协调和正确的操作技术。
通过钻孔T扩孔(粗铰)T精铰的加工方法,一般都能满足产
品零件规定的要求。
刀具材料一般选用M42高速钢或硬质合金K30b刀具的几何参数为:前角g0=3°〜7 °
后角a0=12°〜18°,主偏角?=5°〜18°,刃倾角1=0 °。
校准部分刃带宽度b=0.05〜0.15mm,过宽容易同钛合金加工表面粘结,过窄容易在铰削时产生振动。
铰刀齿数Z=4〜
8(铰刀直径为?10〜20mm。
我们加工的肋和接头,因加工的两孔跨度较长,同轴度要求较高,为此专门设计了加长钻头和铰刀。
切削用量的选择见表9。
铰削时应不断地注人冷却润滑液以获得较好的表面粗糙度,同时应勤排屑,及时清除铰
刀刃上的切屑末,铰削时要匀速地进退刀。
攻丝用量及刀具参数的选
钛合金攻丝时会产生很大的挤压变形,作用在螺纹齿侧的摩擦力加大,这样不但使加工
出来的螺纹表面粗糙度不好,而且丝锥容易折断。
为了改变这种情况,可以采用跳牙丝锥或改进丝锥结构(加大校正段刀齿的后角或加大倒锥度)的方法,以减少切削扭矩和摩擦扭矩,
增大容屑空间,改善攻丝的切削性能。
另外,钛合金攻丝前的底孔直径一般应大于标准值,而且底孔的表面粗糙度应达到RsK 3.2卩m。
刀具材料和几何参数选橄丝锥材料选用M2AI、M42高速钢。
丝锥几何参数为:前角
g0=5°〜8°,后角a0=8°〜10°,丝锥校堆段齿背圆柱刃带b1=0.1〜0.2mm。
主偏角?6°〜10° (通孔)、?=15°〜20° (不通孔);头锥?=2°〜3°,二锥?=4°〜5°。
切削用量选择:攻丝的切削用量也只有速度(转速)一项可选,钛合金攻丝速度v为3〜6m/min。
攻丝时应及时清除丝锥刃部毛刺、切屑末,以免损伤螺纹;攻丝时要勤退刀。
攻丝时要加适量的冷却润滑液,建议使用蓖麻油或机油,以保证螺纹粗糙度要求。
(注:范文素材和资料部分来自网络,供参考。
只是收取少量整理收集费用,请预览后才下载,期待你的好评与关注)。