铁路货车重载车轴热处理工艺开发
高速铁路轴承外圈淬火压床开发设计
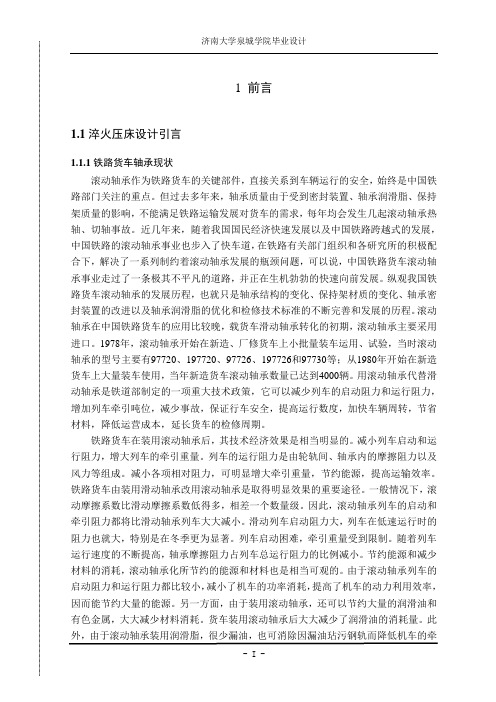
1 前言1.1淬火压床设计引言1.1.1铁路货车轴承现状滚动轴承作为铁路货车的关键部件,直接关系到车辆运行的安全,始终是中国铁路部门关注的重点。
但过去多年来,轴承质量由于受到密封装置、轴承润滑脂、保持架质量的影响,不能满足铁路运输发展对货车的需求,每年均会发生几起滚动轴承热轴、切轴事故。
近几年来,随着我国国民经济快速发展以及中国铁路跨越式的发展,中国铁路的滚动轴承事业也步入了快车道,在铁路有关部门组织和各研究所的积极配合下,解决了一系列制约着滚动轴承发展的瓶颈问题,可以说,中国铁路货车滚动轴承事业走过了一条极其不平凡的道路,并正在生机勃勃的快速向前发展。
纵观我国铁路货车滚动轴承的发展历程,也就只是轴承结构的变化、保持架材质的变化、轴承密封装置的改进以及轴承润滑脂的优化和检修技术标准的不断完善和发展的历程。
滚动轴承在中国铁路货车的应用比较晚,载货车滑动轴承转化的初期,滚动轴承主要采用进口。
1978年,滚动轴承开始在新造、厂修货车上小批量装车运用、试验,当时滚动轴承的型号主要有97720、197720、97726、197726和97730等;从1980年开始在新造货车上大量装车使用,当年新造货车滚动轴承数量已达到4000辆。
用滚动轴承代替滑动轴承是铁道部制定的一项重大技术政策,它可以减少列车的启动阻力和运行阻力,增加列车牵引吨位,减少事故,保证行车安全,提高运行数度,加快车辆周转,节省材料,降低运营成本,延长货车的检修周期。
铁路货车在装用滚动轴承后,其技术经济效果是相当明显的。
减小列车启动和运行阻力,增大列车的牵引重量。
列车的运行阻力是由轮轨间、轴承内的摩擦阻力以及风力等组成。
减小各项相对阻力,可明显增大牵引重量,节约能源,提高运输效率。
铁路货车由装用滑动轴承改用滚动轴承是取得明显效果的重要途径。
一般情况下,滚动摩擦系数比滑动摩擦系数低得多,相差一个数量级。
因此,滚动轴承列车的启动和牵引阻力都将比滑动轴承列车大大减小。
高速重载车轴产品研发及关键制备技术创新
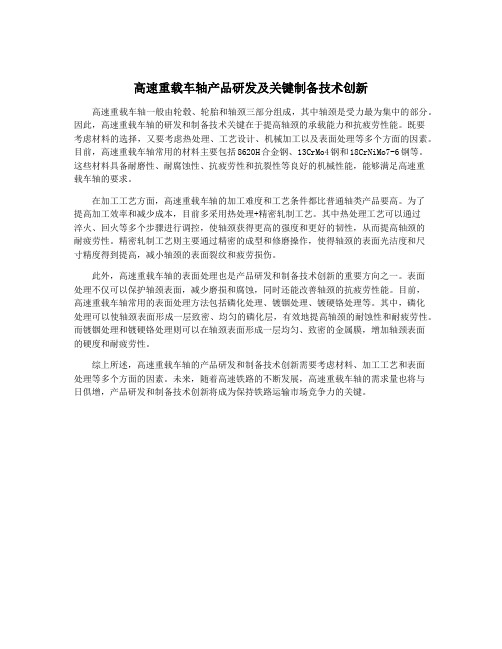
高速重载车轴产品研发及关键制备技术创新高速重载车轴一般由轮毂、轮胎和轴颈三部分组成,其中轴颈是受力最为集中的部分。
因此,高速重载车轴的研发和制备技术关键在于提高轴颈的承载能力和抗疲劳性能。
既要考虑材料的选择,又要考虑热处理、工艺设计、机械加工以及表面处理等多个方面的因素。
目前,高速重载车轴常用的材料主要包括8620H合金钢、13CrMo4钢和18CrNiMo7-6钢等。
这些材料具备耐磨性、耐腐蚀性、抗疲劳性和抗裂性等良好的机械性能,能够满足高速重载车轴的要求。
在加工工艺方面,高速重载车轴的加工难度和工艺条件都比普通轴类产品要高。
为了提高加工效率和减少成本,目前多采用热处理+精密轧制工艺。
其中热处理工艺可以通过淬火、回火等多个步骤进行调控,使轴颈获得更高的强度和更好的韧性,从而提高轴颈的耐疲劳性。
精密轧制工艺则主要通过精密的成型和修磨操作,使得轴颈的表面光洁度和尺寸精度得到提高,减小轴颈的表面裂纹和疲劳损伤。
此外,高速重载车轴的表面处理也是产品研发和制备技术创新的重要方向之一。
表面处理不仅可以保护轴颈表面,减少磨损和腐蚀,同时还能改善轴颈的抗疲劳性能。
目前,高速重载车轴常用的表面处理方法包括磷化处理、镀铟处理、镀硬铬处理等。
其中,磷化处理可以使轴颈表面形成一层致密、均匀的磷化层,有效地提高轴颈的耐蚀性和耐疲劳性。
而镀铟处理和镀硬铬处理则可以在轴颈表面形成一层均匀、致密的金属膜,增加轴颈表面的硬度和耐疲劳性。
综上所述,高速重载车轴的产品研发和制备技术创新需要考虑材料、加工工艺和表面处理等多个方面的因素。
未来,随着高速铁路的不断发展,高速重载车轴的需求量也将与日俱增,产品研发和制备技术创新将成为保持铁路运输市场竞争力的关键。
铁路货车轴承圆锥滚子的热处理工艺

铁路货车轴承圆锥滚子的热处理工艺作者:玄辉李连梅李晓涛来源:《现代经济信息》2013年第13期摘要:通过工艺试验得到了铁路货车轴承352226X2-2RZ、353130B在DRES90/800炉生产线上淬回火的最佳热处理工艺参数。
淬火加热温度和时间的合理匹配可使大尺寸圆锥滚子淬火后得到合适的组织,其热处理后的质量能满足技术条件要求。
关键词:圆锥滚子;热处理;工艺;马氏体:托氏体中图分类号:TG15 文献标识码:A 文章编号:1001-828X(2013)07-0-01352226X2-2RZ、353130B系铁路轴承,滚子尺寸较大,材料均采用GCr15钢,产品技术条件要求高,其在辊底炉上淬火时难度较大,为此进行了淬回火工艺的探索和工艺参数的优化。
一、滚子尺寸及热处理质量要求大型圆锥轴承滚子尺寸见表1,热处理质量要求见表2。
综观表1和表2,根据滚子的尺寸可看出,其相应的热处理质量要求严于JB/T1255-2001。
要达到上述质量要求,热处理工艺是关键,其工艺难点是如何解决热加工中易出现局部托氏体超标及软点现象、组织不合格等问题。
二、加工设备及工艺方案的制订采用热处理辊底炉淬回火生产线对滚子进行处理。
设备自动化程度较高,工艺参数受人为因素影响小。
为了保证产品质量,在淬火过程中采用快速光亮淬火油且油温保持适度,淬火台架在油槽内上下窜动用最快挡,淬火油槽搅拌速度也采用最高挡。
352226X2-2RZ、353130B 轴承滚子在热处理辊底炉生产线的工艺流程为:上料→前清洗→淬火→后清洗→回火。
从淬火加热温度、淬火加热时间、淬火冷却时间等方面进行工艺研究,采用了由少量到批量且分阶段进行工艺调试的方法。
掌握产品加工过程中硬度、组织等一系列质量数据,总结并进行分析,不断改进试验工艺,找出滚子的最佳热处理工艺参数。
三、工艺调试第一阶段:先初步拟订滚子的淬回火工艺进行工艺试验,并根据质量检验结果对所拟订的工艺进行分析。
铁路货车重载车轴热处理工艺开发

铁路货车重载车轴热处理工艺开发【摘要】重载轴LZ45CrV为我公司新材质车轴,通过对铁路货车重载车轴的相关标准要求分析,进行多次试验确定其热处理工艺为:一次正火温度880±10℃,二次正火温度850±10℃,回火温度510±10℃,正火、回火保温时间均为3.5~4小时,空冷。
【关键词】重载车轴晶粒度热处理力学性能1 前言铁路货车重载车轴的材质是LZ45CrV,是27t轴重铁路货车车轴采用的新材质,属低合金钢。
钢坯标准符合《大轴重铁路货车用LZ45CrV车轴钢坯试制技术条件》。
由于在碳素钢的基础上添加Cr、V、Ni、Mo等合金元素,并对杂质和有害元素进行控制,所以具有优良的综合性能。
由于是新材质,目前没有成熟热处理工艺方案借鉴,制定和摸索出合理的热处理工艺方案就成为新材质重载轴工艺开发的关键。
2 LZ45CrV车轴技术标准要求车轴标准符合《大轴重铁路货车用LZ45CrV车轴试制技术条件》规定。
车轴的热处理工艺为两次正火加一次回火,车轴正火前的温度应低于500℃,回火前的温度应低于250℃。
2.1 化学成分钢的化学成分(熔炼分析)应符合表1的规定。
对成品钢坯化学成分进行验证分析时,C、Mn、Si元素与表1规定的成分范围的允许偏差符合表2的规定,其余元素与表1规定的成分范围的允许偏差应符合GB/T222规定。
2.2 力学性能和显微特性经热处理后车轴的拉伸特性和冲击试验特性分别符合表3和表4的指标。
车轴的晶粒度试样应显示为均匀的细晶粒组织,试样在金相显微镜下放大100倍观察。
检验及评定按GB/T6394的规定执行,晶粒度不低于6级。
3 热处理工艺方案初步制定试验采用太钢生产的车轴钢坯,规格260mm×260mm,炉号D1105163,共锻造车轴34根,图1为RE2C型重载轴锻造毛坯图,最大外径尺寸为230mm,长度2400mm,重量680Kg。
针对LZ45CrV钢的基本情况与国内已有比较成熟热处理工艺的40Cr和LZ50钢进行对比分析。
20Mn2车轴钢热处理工艺研究及优化

20Mn2车轴钢热处理工艺研究及优化本文在对某钢铁公司20Mn2整体式半挂车轴调质热处理工艺与组织结构进行生产分析和工艺实验的基础上,对20Mn2车轴钢的相变特性与连续冷却组织转变进行了研究,同时运用有限元数值模拟计算方法,对20Mn2车轴钢的正火冷却条件进行模拟计算和分析,获得20Mn2整体式半挂车轴以正火工艺代替调质处理的条件,以期为车轴的热处理生产提供工艺改进的理论依据。
利用Gleeble3500热模拟实验机,根据膨胀曲线以及组织分析测定了20Mn2车轴钢的热处理相变温度Ac1、Ac3、Ar3、Ar1分别为715℃、849℃、722℃、550℃;奥氏体粗化温度测定结果,粗化温区在980℃~1070℃之间;综合车轴钢相变温度以及奥氏体粗化温度测试结果,20Mn2车轴钢淬火温度应为880~900℃。
利用光学金相显微镜与扫描电镜,结合实验室热处理实验,对20Mn2半挂车轴实际生产中的调质热处理的组织结构、性能以及存在的问题进行了分析,实验结果表明,实际生产的20Mn2车轴调质组织以回火屈氏体和回火索氏体为主,同时存在沿原奥氏体晶界析出的网状铁素体以及羽毛状上贝氏体等组织缺陷;通过增设淬火中间的释放高温蒸汽环节,可以改善车轴调质组织和性能。
热模拟实验结果表明,20Mn2车轴钢连续冷却组织转变规律如下:在冷速为0.5~2℃/s时,转变产物以块状或多边铁素体、准多边铁素体以及珠光体组织为主;冷速达到1℃/s,开始出现少量粒状贝氏体组织,冷速增大到2~5℃/s时,粒状贝氏体含量明显增多,组织逐渐呈现为针状铁素体形态,且铁素体尺寸减小;当冷速达到10~20℃/s时,珠光体组织消失,准多边铁素体数量大大降低,基体以针状铁素体为主,且铁素体晶粒进一步细化,晶粒之间交叉、互成角度,同时开始出现少量的马氏体;冷却速度达到30℃/s时,粒状贝氏体组织中的铁素体板条明显拉长,板条间取向性增强,岛状物由粒状向条状转变,同时板条马氏体数量明显增加;当控制20Mn2车轴钢连续冷却速度在10℃/s~30℃/s时,显微组织主要为大量粒状贝氏体以及少量准多边铁素体和少量板条马氏体组成的混合组织,力学性能测试结果,混合组织的硬度为250-290 HV,产物的硬度达到工厂和国家标准要求。
论述车轴件热处理及加热炉设计

论述车轴件热处理及加热炉设计发表时间:2017-11-02T12:00:13.933Z 来源:《基层建设》2017年第21期作者:秦健荣[导读] 摘要:随着近几年我国经济的迅速发展,科学技术也不断的进步,车轴件也不断的改进,变得更加科学化。
佛山市永力泰车轴有限公司摘要:随着近几年我国经济的迅速发展,科学技术也不断的进步,车轴件也不断的改进,变得更加科学化。
其中车轴件主要的问题是热处理的问题,因为车轴主要是铁道机车辆中非常重要的零件,在整个列车安装和列车运行过程中扮演者非常重要的角色,所以说随着科学技术的发展对交通提出了更高的要求,也就对车辆零部件的要求不断地提高。
车轴件的热处理问题会在一定程度上影响到车辆运行过程中的稳定,而且加热炉是保证获得优质质量车轴的必要条件之一。
关键词:车轴件;热处理;加热炉车轴是铁道机车车辆转向整个的走行部中必不可少的零件,这个零件对于整个机车的运行来讲是比较重要的,而且车轴件的质量也会影响到列车在行车过程中的安全,因此对于车轴件设计要求上比较高,因为在设计上要考虑到力学性能和组织要求。
力学性能和组织要求都能够对车轴件产生较大的影响,最终影响到车辆行驶的安全。
因此,车处理是车轴件形成过程中必不可少的环节,热处理配合适当的加热炉是提高整个车轴件质量,提高行车的安全。
一、车轴件材料力学性能和组织要求1、车轴件材料车轴件主要运用到的材料是优质碳素钢,一般用到的优质碳素钢的型号为JZ45,车辆车轴有的也会使用到LZ50优质碳素钢。
不同的优质碳素钢在车轴使用中要考虑到不同的现实状况,只有将不同现实状况考虑在其中才能够在问题出现时进行的处理。
可见车轴件材料的问题对于车辆还是比较关键的,因此要给予足够的重视。
2、车轴件的力学性能和晶粒度车轴件的力学性能和晶粒度是在车轴件使用过程中的又一大原则,主要是根据铁道行业的标准对机车车轴的力学进行分析和规定,只有车轴件达到力学性能的规定之后才能够投入到使用当中。
铁道车辆车轴锻造及热处理技术
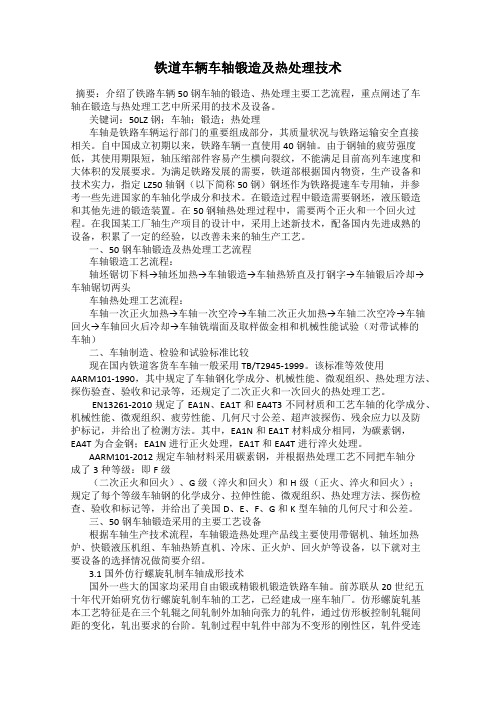
铁道车辆车轴锻造及热处理技术摘要:介绍了铁路车辆50钢车轴的锻造、热处理主要工艺流程,重点阐述了车轴在锻造与热处理工艺中所采用的技术及设备。
关键词:50LZ钢;车轴;锻造;热处理车轴是铁路车辆运行部门的重要组成部分,其质量状况与铁路运输安全直接相关。
自中国成立初期以来,铁路车辆一直使用40钢轴。
由于钢轴的疲劳强度低,其使用期限短,轴压缩部件容易产生横向裂纹,不能满足目前高列车速度和大体积的发展要求。
为满足铁路发展的需要,铁道部根据国内物资,生产设备和技术实力,指定LZ50轴钢(以下简称50钢)钢坯作为铁路提速车专用轴,并参考一些先进国家的车轴化学成分和技术。
在锻造过程中锻造需要钢坯,液压锻造和其他先进的锻造装置。
在50钢轴热处理过程中,需要两个正火和一个回火过程。
在我国某工厂轴生产项目的设计中,采用上述新技术,配备国内先进成熟的设备,积累了一定的经验,以改善未来的轴生产工艺。
一、50钢车轴锻造及热处理工艺流程车轴锻造工艺流程:轴坯锯切下料→轴坯加热→车轴锻造→车轴热矫直及打钢字→车轴锻后冷却→车轴锯切两头车轴热处理工艺流程:车轴一次正火加热→车轴一次空冷→车轴二次正火加热→车轴二次空冷→车轴回火→车轴回火后冷却→车轴铣端面及取样做金相和机械性能试验(对带试棒的车轴)二、车轴制造、检验和试验标准比较现在国内铁道客货车车轴一般采用TB/T2945-1999。
该标准等效使用AARM101-1990,其中规定了车轴钢化学成分、机械性能、微观组织、热处理方法、探伤验查、验收和记录等,还规定了二次正火和一次回火的热处理工艺。
EN13261-2010规定了EA1N、EA1T和EA4T3不同材质和工艺车轴的化学成分、机械性能、微观组织、疲劳性能、几何尺寸公差、超声波探伤、残余应力以及防护标记,并给出了检测方法。
其中,EA1N和EA1T材料成分相同,为碳素钢,EA4T为合金钢;EA1N进行正火处理,EA1T和EA4T进行淬火处理。
铁路货车轮轴组装工艺改进研究

铁路货车轮轴组装工艺改进研究摘要:随着铁路货车重载、高速的发展需要,对轮轴的制造水平要求越来越高,以进一步提升车辆的运行品质。
铁路货车轮轴主要由车轴、车轮、轴承及前盖后挡等附件组成,车轴与车轮加工后采用过盈配合冷压装装配形成轮对,轴承及附件与轮对装配后成为轮轴。
基于此,本文主要对铁路货车轮轴组装工艺改进进行分析探讨。
关键词:铁路货车;轮轴组装;工艺改进1轮对组装工艺及改进研究轮对组装须符合TB/T1718《铁道车辆轮对组装技术条件》相关要求,目前我国主要铁路货车以准轨为主,设计时速小于120km/h,要求同一轮对的两车轮直径差不大于1mm,同一车轮相互垂直的直径差不大于0.5mm,轮对内侧距离为(1353±2)mm,且轮对内侧距任意三处相差不大于1mm,轮位差不大于3mm。
1.1轮对压装工艺轮对压装工艺设计时,车轴与车轮采用过盈配合,采用自动化压装设备进行压装,其装配过盈量为车轴轮座直径的0.8‰~1.5‰,轮对压装最终压装力根据轮毂孔直径进行计算,轮对压装后,通过轮对尺寸检测及压装位移—压力曲线综合判断车轮车轴的装配质量。
车轴车轮及轮对尺寸检测项目较多,配置有内径外径千分尺、轮径尺、内侧距尺、深度尺、圆弧样板、踏面全形样板、三孔位置度检具、轮位差尺、轮轴偏心检测仪、样板轮对等成套量具检具,用于控制轮对的组装尺寸及组装质量。
轮对压装为特殊过程工序,车轮与车轴的装配质量难以用肉眼观察,需通过压装实物质量与压装曲线综合判断轮对组装质量,其组装尺寸及形位公差满足产品图纸及技术条件相关要求,压装曲线要求光滑并均匀上升,不得有跳动;压装压力曲线长度不小于理论长度的80%;曲线起点陡升时,陡升值不超过98kN;曲线中部不得有下降,平直长度不超过该曲线投影长度的10%;压力曲线末端平直线长度不超过该曲线投影长度的15%;压力曲线开始上升点与终点连成一直线,曲线应全部在此直线之上。
轮对压装曲线可直观判断轮对的装配质量,压装过程中装配不良、损伤拉伤等质量缺陷可通过压装曲线的平直、陡升、降吨、异常凸起等缺陷进行判断,车轮与车轴的压装位移通过位移-压力曲线长度进行判断。
重卡汽车传动轴的加工工艺
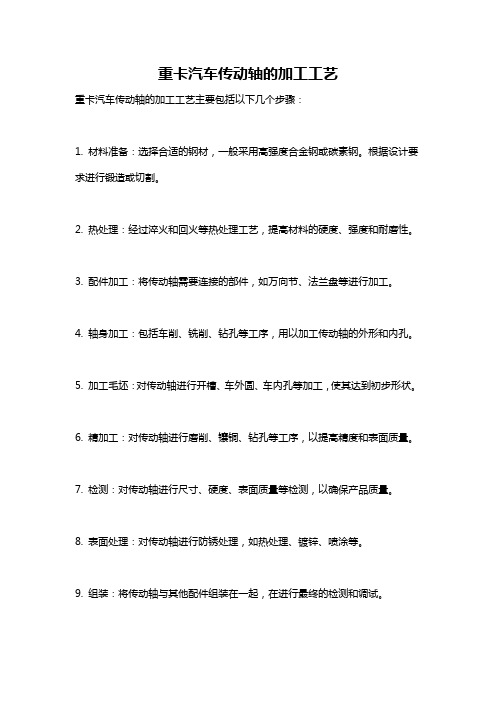
重卡汽车传动轴的加工工艺
重卡汽车传动轴的加工工艺主要包括以下几个步骤:
1. 材料准备:选择合适的钢材,一般采用高强度合金钢或碳素钢。
根据设计要求进行锻造或切割。
2. 热处理:经过淬火和回火等热处理工艺,提高材料的硬度、强度和耐磨性。
3. 配件加工:将传动轴需要连接的部件,如万向节、法兰盘等进行加工。
4. 轴身加工:包括车削、铣削、钻孔等工序,用以加工传动轴的外形和内孔。
5. 加工毛坯:对传动轴进行开槽、车外圆、车内孔等加工,使其达到初步形状。
6. 精加工:对传动轴进行磨削、镶铜、钻孔等工序,以提高精度和表面质量。
7. 检测:对传动轴进行尺寸、硬度、表面质量等检测,以确保产品质量。
8. 表面处理:对传动轴进行防锈处理,如热处理、镀锌、喷涂等。
9. 组装:将传动轴与其他配件组装在一起,在进行最终的检测和调试。
以上是重卡汽车传动轴的一般加工工艺,具体的加工过程和工艺参数会根据产品的具体要求和制造厂商的工艺流程而有所不同。
铁路货车重载车轴热处理工艺
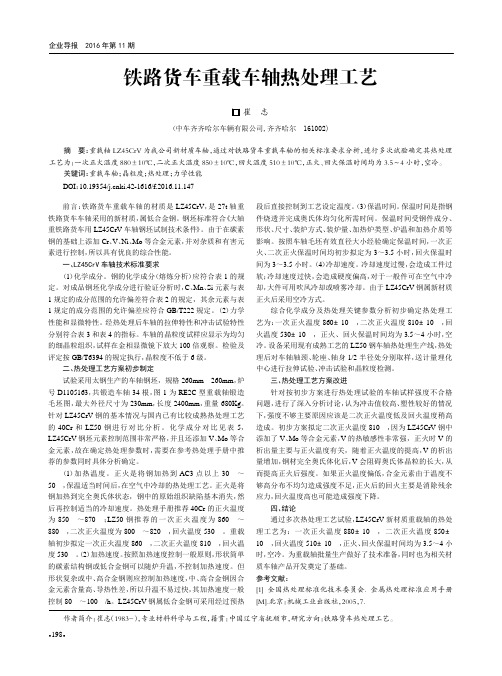
企业导报2016年第11期作者简介:崔志(1983-),专业材料科学与工程,籍贯:中国辽宁省抚顺市,研究方向:铁路货车热处理工艺。
DOI :10.19354/ki.42-1616/f.2016.11.147铁路货车重载车轴热处理工艺崔志(中车齐齐哈尔车辆有限公司,齐齐哈尔161002)摘要:重载轴LZ45CrV 为我公司新材质车轴,通过对铁路货车重载车轴的相关标准要求分析,进行多次试验确定其热处理工艺为:一次正火温度880±10℃,二次正火温度850±10℃,回火温度510±10℃,正火、回火保温时间均为3.5~4小时,空冷。
关键词:重载车轴;晶粒度;热处理;力学性能前言:铁路货车重载车轴的材质是LZ45CrV ,是27t 轴重铁路货车车轴采用的新材质,属低合金钢。
钢坯标准符合《大轴重铁路货车用LZ45CrV 车轴钢坯试制技术条件》。
由于在碳素钢的基础上添加Cr 、V 、Ni 、Mo 等合金元素,并对杂质和有害元素进行控制,所以具有优良的综合性能。
一、LZ45CrV 车轴技术标准要求(1)化学成分。
钢的化学成分(熔炼分析)应符合表1的规定。
对成品钢坯化学成分进行验证分析时,C 、Mn 、Si 元素与表1规定的成分范围的允许偏差符合表2的规定,其余元素与表1规定的成分范围的允许偏差应符合GB/T222规定。
(2)力学性能和显微特性。
经热处理后车轴的拉伸特性和冲击试验特性分别符合表3和表4的指标。
车轴的晶粒度试样应显示为均匀的细晶粒组织,试样在金相显微镜下放大100倍观察。
检验及评定按GB/T6394的规定执行,晶粒度不低于6级。
二、热处理工艺方案初步制定试验采用太钢生产的车轴钢坯,规格260mm ×260mm ,炉号D1105163,共锻造车轴34根,图1为RE2C 型重载轴锻造毛坯图,最大外径尺寸为230mm ,长度2400mm ,重量680Kg 。
针对LZ45CrV 钢的基本情况与国内已有比较成熟热处理工艺的40Cr 和LZ50钢进行对比分析。
铁路货车部件铸造材料热处理工艺研究

为了确保产品质量和稳定性,需要采取有效的控制方法。这些方法包括采用 先进的测温设备、建立严格的质量管理体系、进行定期的工艺验证和审核等 。
04
铁路货车部件的铸造和热处理工艺应用
铁路货车部件的铸造工艺
砂型铸造
使用模具和沙子制作铸型,然 后浇注金属液得到铸件。
熔模铸造
通过用熔融的金属或塑料制作模 具,然后浇注金属液得到铸件。
意义
通过研究铸造材料和热处理工艺对铁路货车部件性能的影响 ,有助于优化部件的生产工艺,提高其性能和可靠性,为铁 路运输业的发展提供有力支持。
研究目的和方法
目的
本研究旨在探究不同铸造材料和热处理工艺对铁路货车部件性能的影响,并 优化其生产工艺,以提高部件的性能和可靠性。
方法
本研究采用实验研究方法,通过制备不同铸造材料和热处理工艺的铁路货车 部件样本,测试其性能指标,如强度、硬度、耐磨性等,分析不同工艺对性 能的影响,并优化其生产工艺。
浇注
将熔融的金属注入模具中,冷却后得到所需的 铸件。
3
热处理
通过加热和冷却等工艺,改变铸件的内部结构 ,提高其性能。
铸造材料的性能测试与评估
测试
01
采用各种实验方法,如拉伸试验、冲击试验、硬度试验等,对
铸件的力学性能进行测试。
评估
02
根据测试结果,对铸造材料的性能进行评估,判断其是否满足
设计要求。
压力铸造
在高压下将金属液注入模具,得到 铸件。
铁路货车部件的热处理工艺
01
退火
将金属加热到一定温度,保温一段时间,然后缓慢冷却,以改善材料
的组织和性能。
02
淬火
将金属加热到一定温度,保温一段时间,然后快速冷却,以提高材料
160km/h电力机车车轴热处理工艺开发与优化

160km/h电力机车车轴热处理工艺开发与优化摘要本文通过对160Km/h机车车轴热处理工艺的研究,试验结果表明,原材的基体组织很重要,35CrMoA钢原材料基体组织不理想的情况下可以增加铁素体高温弥散处理来提高后续的调质处理时工件的机械性能,高温回火后快冷处理完全可以满足机车车轴高速重载的要求。
关键词车轴;调质;性能;回火脆性0 引言近年来,公司通过技贸合作的方式,先后成功推出了HXD3、HXD3B、HXN3等一系列和谐型机车,不断提升了公司的生产能力及技术水平,也为公司赢得了大量的客户,同时提高了公司的知名度。
2011年公司为了适应市场的发展需求,也为了公司的发展,确立了自主研制160km/h电力机车的生产规划。
160km/h电力机车是我公司研制的首批准高速客运电力机车,其研制的进度及成功与否直接影响着公司的未来发展。
为此,公司及车间领导高度重视该项工作,把该项任务作为工作的重中之重。
1 车轴技术要求车轴是高速铁路车辆的承受动载荷的关键零件,受力状态复杂,主要承受弯曲、扭转或弯扭复合载荷,还受到一定的冲击载荷。
因此,车轴用钢应具有良好的强度,特别是弯扭复合疲劳强度及韧性。
车轴材料是决定车轴使用寿命和可靠性的关键之一,因此许多国家都非常重视对车轴材料的开发。
依据国内外车轴用钢标准,车轴材料一般分为两大类,即碳钢和合金钢。
依据欧洲标准,高速铁路采用合金钢车轴,常选用25CrM04、30CrNi3、30CrMoA、34CrNiM06钢等。
由于各国的国情不同,技术观点不同,选用的车轴材料也不尽相同,但都属于含碳量较低的钢种。
车轴用钢的含碳量一般为0.30%~0.45%,再加入适量的合金元素。
Cr、Ni、Mo等是车轴钢的主要合金化元素。
由于该机车的运行速度较高所以车轴也要承载较大的扭矩,机械性能的要求也需要较高。
160km/h电力机车车轴性能要求如下:2 工艺试验根据160km/h客运电力机车车轴技术条件(8U9Z04000JT)要求车轴力学性能试验用试样应取自车轴一端延长体,在车轴端部距表面1/2R处取样。
一种大轴重货运列车用车轴及其热处理工艺和生产工艺
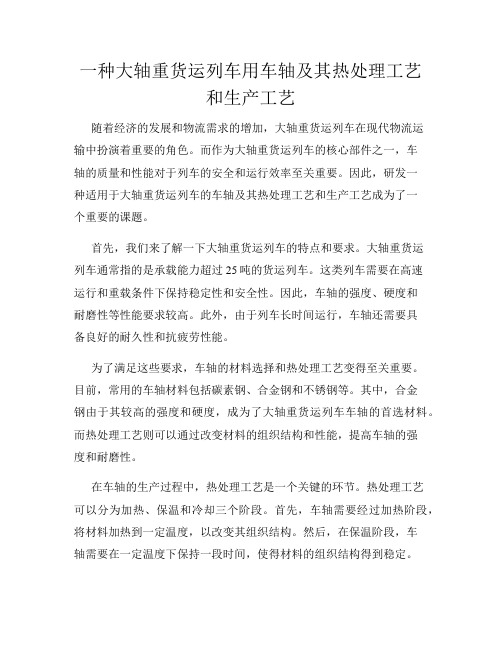
一种大轴重货运列车用车轴及其热处理工艺和生产工艺随着经济的发展和物流需求的增加,大轴重货运列车在现代物流运输中扮演着重要的角色。
而作为大轴重货运列车的核心部件之一,车轴的质量和性能对于列车的安全和运行效率至关重要。
因此,研发一种适用于大轴重货运列车的车轴及其热处理工艺和生产工艺成为了一个重要的课题。
首先,我们来了解一下大轴重货运列车的特点和要求。
大轴重货运列车通常指的是承载能力超过25吨的货运列车。
这类列车需要在高速运行和重载条件下保持稳定性和安全性。
因此,车轴的强度、硬度和耐磨性等性能要求较高。
此外,由于列车长时间运行,车轴还需要具备良好的耐久性和抗疲劳性能。
为了满足这些要求,车轴的材料选择和热处理工艺变得至关重要。
目前,常用的车轴材料包括碳素钢、合金钢和不锈钢等。
其中,合金钢由于其较高的强度和硬度,成为了大轴重货运列车车轴的首选材料。
而热处理工艺则可以通过改变材料的组织结构和性能,提高车轴的强度和耐磨性。
在车轴的生产过程中,热处理工艺是一个关键的环节。
热处理工艺可以分为加热、保温和冷却三个阶段。
首先,车轴需要经过加热阶段,将材料加热到一定温度,以改变其组织结构。
然后,在保温阶段,车轴需要在一定温度下保持一段时间,使得材料的组织结构得到稳定。
最后,在冷却阶段,车轴需要通过控制冷却速度,使得材料的组织结构得到进一步调整和固化。
在大轴重货运列车车轴的热处理工艺中,淬火是一个重要的步骤。
淬火可以通过快速冷却来改变材料的组织结构,提高其硬度和强度。
然而,由于车轴的尺寸较大,传统的水淬方法往往无法满足要求。
因此,研发一种适用于大轴重货运列车车轴的淬火工艺成为了一个挑战。
近年来,一种新型的淬火工艺——高压气体淬火技术逐渐应用于大轴重货运列车车轴的生产中。
高压气体淬火技术通过将车轴置于高压气体环境中,利用气体的冷却效果来实现快速冷却。
相比传统的水淬方法,高压气体淬火技术具有温度均匀、冷却速度可控等优点,可以有效提高车轴的淬火效果和性能。
重型货车贯通轴热处理工艺及质量控制
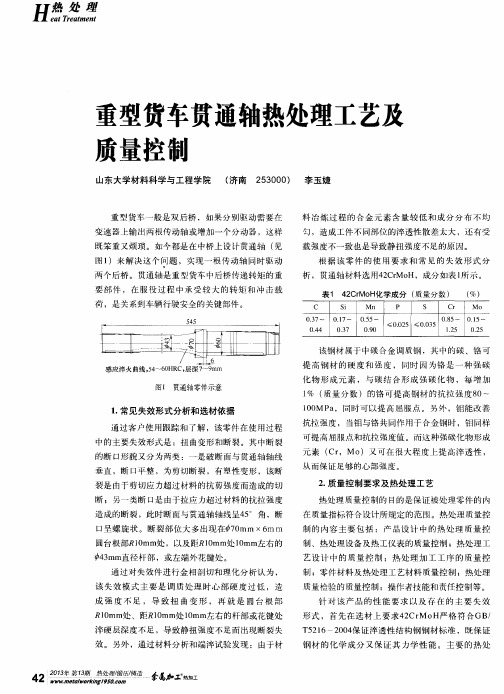
析 ,贯通轴材料选用4 2 C r Mo H,成分如表 1 所示。
表1 4 2 Cr Mo H化学成分 ( 质量分数 )
C S i Mn P S Cr
( %)
M0
0 . 3 7~ 0 . 1 7~ 0 . 5 5~ ≤0. 0 2 5 ≤0. 03 5
图l 贯通轴 零件示意
l % ( 质 量 分 数 )的 铬 可 提 高 钢 材 的抗 拉 强 度 8 0 ~
1 . 常见失效形式分析和选材依 据
通过客户使用跟踪和了解 ,该零件在使用过程 中的主要失效 形式是 :扭 曲变形和断裂 。其 中断裂
的 断 口形 貌 又分 为 两 类 :一 是破 断面 与 贯通 轴 轴 线 垂直 ,断 口平 整 ,为 剪切 断 裂 ,有塑 性 变形 ,该 断 裂 是 由于 剪切 应 力超 过材 料 的 抗 剪 强度 而造 成 的 切 断 ;另一 类 断 口是 由于拉 应 力 超 过材 料 的抗 拉 强 度
口呈 螺旋 状 。 断 裂部 位 大 多 出现 在  ̄ b 7 0 mm × 6 mi n 圆台根 部R1 0 mm处 ,以及 距 l O mm 处l O mm 左 右 的  ̄ b 4 3 m m直 径杆 部 ,或 左 端 外花 键 处 。 通 过 对 失 效件 进 行 金 S N  ̄ ] E 切 和 理 化 分析 认 为 ,
0 . 8 5~ O . 1 5~
O . 4 4 0. 3 7 O Nhomakorabea 9 0
1 . 2 5
O- 2 5
该 钢 材 属于 中碳 合 金 调 质钢 ,其 中的 碳 、铬 可
感应淬火曲线, 5 4  ̄6 0 HR C, 层深 7  ̄9 mm
提 高 钢 材 的 硬 度 和 强 度 ,同 时 因 为 铬 是 一 种 强 碳 化 物 形 成 元 素 ,与 碳 结 合 形 成 强 碳 化 物 ,每 增 加
一种耐寒大轴重货运列车用车轴及其热处理工艺和生产工艺[发明专利]
![一种耐寒大轴重货运列车用车轴及其热处理工艺和生产工艺[发明专利]](https://img.taocdn.com/s3/m/966b38ca192e45361166f530.png)
专利名称:一种耐寒大轴重货运列车用车轴及其热处理工艺和生产工艺
专利类型:发明专利
发明人:张艳,杜松林,陈刚,张磊,戴俊,赵海,于文坛,童乐,汪永阳,阮守丰
申请号:CN202011299583.4
申请日:20201119
公开号:CN112522612A
公开日:
20210319
专利内容由知识产权出版社提供
摘要:本发明公开了一种耐寒大轴重货运列车用车轴及其热处理工艺和生产工艺,所述车轴的化学成分及重量百分比为:C:0.35~0.40%,Si:0.20~0.40%,Mn:0.90~1.20%,Cr:0.70~0.90%,Ni:0.90~1.20%,Mo:0.10~0.20%,Nb:0.025~0.050%,V:0.050~
0.10%,RE:0.002~0.005%,Ca:0.001~
0.005%,P≤0.010%,S≤0.008%,T[O]≤0.0010%,[N]:0.050~0.0070%,Al:0.015~0.035%,其余为Fe和其它不可避免的杂质;其抗拉强度≥700MPa、屈服强度≥400MPa、‑20℃纵向冲击功KU≥80J,‑20℃横向冲击功KU≥60J,‑50℃纵向冲击功KU≥40J,表面光滑试样的疲劳极限R≥380MPa,表面带有缺口试样的疲劳极限R≥280MPa,缺口敏感指数R/R≤1.30,经济型高强高韧及长疲劳寿命的新材质货用列车用大轴重车轴。
申请人:宝武集团马钢轨交材料科技有限公司
地址:243000 安徽省马鞍山市马鞍山经济技术开发区银黄东路700号
国籍:CN
代理机构:芜湖安汇知识产权代理有限公司
代理人:尹婷婷
更多信息请下载全文后查看。
- 1、下载文档前请自行甄别文档内容的完整性,平台不提供额外的编辑、内容补充、找答案等附加服务。
- 2、"仅部分预览"的文档,不可在线预览部分如存在完整性等问题,可反馈申请退款(可完整预览的文档不适用该条件!)。
- 3、如文档侵犯您的权益,请联系客服反馈,我们会尽快为您处理(人工客服工作时间:9:00-18:30)。
铁路货车重载车轴热处理工艺开发
【摘要】重载轴LZ45CrV为我公司新材质车轴,通过对铁路货车重载车轴的相关标准要求分析,进行多次试验确定其热处理工艺为:一次正火温度880±10℃,二次正火温度850±10℃,回火温度510±10℃,正火、回火保温时间均为3.5~4小时,空冷。
【关键词】重载车轴晶粒度热处理力学性能
1 前言
铁路货车重载车轴的材质是LZ45CrV,是27t轴重铁路货车车轴采用的新材质,属低合金钢。
钢坯标准符合《大轴重铁路货车用LZ45CrV车轴钢坯试制技术条件》。
由于在碳素钢的基础上添加Cr、V、Ni、Mo等合金元素,并对杂质和有害元素进行控制,所以具有优良的综合性能。
由于是新材质,目前没有成熟热处理工艺方案借鉴,制定和摸索出合理的热处理工艺方案就成为新材质重载轴工艺开发的关键。
2 LZ45CrV车轴技术标准要求
车轴标准符合《大轴重铁路货车用LZ45CrV车轴试制技术条件》规定。
车轴的热处理工艺为两次正火加一次回火,车轴正火前的温度应低于500℃,回火前的温度应低于250℃。
2.1 化学成分
钢的化学成分(熔炼分析)应符合表1的规定。
对成品钢坯化学成分进行验证分析时,C、Mn、Si元素与表1规定的成分范围的允许偏差符合表2的规定,其余元素与表1规定的成分范围的允许偏差应符合GB/T222规定。
2.2 力学性能和显微特性
经热处理后车轴的拉伸特性和冲击试验特性分别符合表3和表4的指标。
车轴的晶粒度试样应显示为均匀的细晶粒组织,试样在金相显微镜下放大100倍观察。
检验及评定按GB/T6394的规定执行,晶粒度不低于6级。
3 热处理工艺方案初步制定
试验采用太钢生产的车轴钢坯,规格260mm×260mm,炉号D1105163,共锻造车轴34根,图1为RE2C型重载轴锻造毛坯图,最大外径尺寸为230mm,长度2400mm,重量680Kg。
针对LZ45CrV钢的基本情况与国内已有比较成熟热处理工艺的40Cr和LZ50钢进行对比分析。
化学成分对比见表5,LZ45CrV 钢坯元素控制范围非常严格,并且还添加V、Mo等合金元素,故在确定热处理
参数时,需要在参考热处理手册中推荐的参数同时具体分析确定。
3.1 加热温度
正火是将钢加热到AC3点以上30℃~50℃,保温适当时间后,在空气中冷却的热处理工艺。
正火是将钢加热到完全奥氏体状态,钢中的原始组织缺陷基本消失,然后再控制适当的冷却速度。
热处理手册推荐40Cr的正火温度为850℃~870℃;LZ50钢推荐的一次正火温度为860℃~880℃,二次正火温度为800℃~820℃,回火温度530℃。
重载轴初步拟定一次正火温度860℃,二次正火温度810℃,回火温度530℃。
3.2 加热速度
按照加热速度控制一般原则,形状简单的碳素结构钢或低合金钢可以随炉升温,不控制加热速度。
但形状复杂或中、高合金钢则应控制加热速度,中、高合金钢因合金元素含量高、导热性差,所以升温不易过快,其加热速度一般控制80℃~100℃/h。
LZ45CrV钢属低合金钢可采用经过预热段后直接控制到工艺设定温度。
3.3 保温时间
保温时间是指钢件烧透并完成奥氏体均匀化所需时间。
保温时间受钢件成分、形状、尺寸、装炉方式、装炉量、加热炉类型、炉温和加热介质等影响。
按照车轴毛坯有效直径大小经验确定保温时间,一次正火、二次正火保温时间均初步拟定为3~3.5小时,回火保温时间为3~3.5小时。
3.4 冷却速度
冷却速度过慢,会造成工件过软;冷却速度过快,会造成硬度偏高,对于一般件可在空气中冷却,大件可用吹风冷却或喷雾冷却。
由于LZ45CrV钢属新材质正火后采用空冷方式。
综合化学成分及热处理关键参数分析初步确定热处理工艺为:一次正火温度860±10℃,二次正火温度810±10℃,回火温度530±10℃,正火、回火保温时间均为3.5~4小时,空冷。
设备采用现有成熟工艺的LZ50钢车轴热处理生产线,热处理后对车轴轴颈、轮座、轴身1/2半径处分别取样,送计量理化中心进行拉伸试验、冲击试验和晶粒度检测。
检验结果见表6。
从表中数据可知,目前存在的主要问题是抗拉强度和屈服强度不合格,冲击值较高,晶粒度指标虽然不是很理想,但在标准要求合格范围内。
4 热处理工艺方案改进
针对按初步方案进行热处理试验的车轴试样强度不合格问题,进行了深入分析讨论,认为冲击值较高、塑性较好的情况下,强度不够主要原因应该是二次正
火温度低及回火温度稍高造成。
初步方案拟定二次正火温度810℃,因为LZ45CrV钢中添加了V、Mo等合金元素,V的热敏感性非常强,正火时V的析出量主要与正火温度有关,随着正火温度的提高,V的析出量增加,钢材完全奥氏体化后,V会阻碍奥氏体晶粒的长大,从而提高正火后强度。
如果正火温度偏低,合金元素由于温度不够高分布不均匀造成强度不足,正火后的回火主要是消除残余应力,回火温度高也可能造成强度下降。
按照提高二次正火温度、适当降低回火温度的改进原则,确定改进后的热处理方案为,一次正火温度880±10℃,二次正火温度850±10℃,回火温度510±10℃,正火、回火保温时间均为3.5~4小时,空冷。
按照改进后的热处理工艺方案进行热处理试验,并进行理化检验,检验结果见表7,检测项目全部达到《铁道车辆用LZ45CrV车轴技术条件》要求。
强度、冲击值数据指标分布基本合理,且平均晶粒度达到7级以上。
5 结论
通过多次热处理工艺试验,LZ45CrV新材质重载轴的热处理工艺为:一次正火温度880±10℃,二次正火温度850±10℃,回火温度510±10℃,正火、回火保温时间均为3.5~4小时,空冷。
为重载轴批量生产做好了技术准备,同时也为相关材质车轴产品开发奠定了基础。