刻蚀原理及工艺培训
刻蚀培训计划

刻蚀培训计划一、培训概述刻蚀技术是一种在材料表面制造微细结构的加工技术,广泛应用于半导体制造、光电子器件制造、微纳米加工等领域。
随着科技的不断发展,刻蚀技术在相关行业中的需求日益增加。
为了培养专业的刻蚀技术人才,满足行业需求,本次培训计划就专门针对刻蚀技术进行培训,内容包括刻蚀工艺原理、设备操作、安全技术等方面。
二、培训目标1.了解刻蚀技术的基本原理和应用范围。
2.熟练掌握刻蚀工艺过程和设备操作方法。
3.掌握刻蚀技术相关的安全知识和常用故障排除方法。
4.具备一定的刻蚀工程实践能力,能够独立进行一定程度的刻蚀加工。
5.了解国内外刻蚀技术的发展趋势和最新应用领域。
三、培训内容1. 刻蚀技术概述- 刻蚀技术的定义和历史发展- 刻蚀技术的应用范围和发展前景2. 刻蚀工艺原理- 刻蚀过程的基本原理- 刻蚀材料和刻蚀介质的选择- 刻蚀参数对加工效果的影响3. 刻蚀设备操作- 常见刻蚀设备的结构和原理- 刻蚀设备的使用方法和注意事项- 刻蚀设备的日常维护和保养4. 刻蚀工艺实践- 刻蚀样品的准备和加工- 刻蚀工艺中常见问题的解决方法- 刻蚀实验数据的处理和分析5. 刻蚀安全技术- 刻蚀工艺中的安全隐患和预防措施- 突发事件的应急处理和救援措施- 刻蚀设备和材料的安全操作规范6. 刻蚀技术的发展趋势- 国内外刻蚀技术的最新进展- 刻蚀技术在相关领域中的应用案例- 刻蚀技术未来的发展方向和挑战四、培训方法1. 理论讲解:由资深专家讲解刻蚀技术的基本原理和应用知识。
2. 案例分析:通过实际案例分析,让学员了解刻蚀技术在实际应用中的重要性和难点。
3. 实践操作:提供实际的刻蚀设备和材料,让学员亲自操作,掌握刻蚀工艺和设备的操作方法。
4. 网络学习:提供在线学习平台,定期组织学员进行网络学习和交流,分享学习心得和技术经验。
五、培训流程1. 第一阶段:刻蚀技术基础知识培训- 刻蚀技术的基本概念和原理- 刻蚀工艺参数的选择和优化- 刻蚀设备的使用和维护2. 第二阶段:刻蚀工艺实践操作- 刻蚀样品的准备和操作- 常见问题的解决方法和设备操作技巧- 刻蚀实验数据的处理和分析3. 第三阶段:刻蚀安全技术和应急处理- 刻蚀工艺中的安全隐患和预防措施- 突发事件的应急处理和救援措施- 刻蚀设备和材料的安全操作规范4. 第四阶段:刻蚀技术的发展趋势和应用案例- 国内外刻蚀技术的最新进展- 刻蚀技术在相关领域中的应用案例- 刻蚀技术未来的发展方向和挑战六、培训考核1. 理论考核:结合培训内容,进行书面考核,测试学员对刻蚀技术基础知识的掌握程度。
刻蚀工艺培训

二、湿法刻蚀及去PSG原理
2.1 湿法刻蚀原理:利用HNO3和HF的混合液体对扩散后硅片下表面和边缘进行腐 蚀,去除边缘的N型硅,使得硅片的上下表面相互绝缘。
边缘刻蚀原理反应方程式: 3Si + 4HNO3+18HF =3H2 [SiF6] + 4NO2↑ + 8H2O
6
2.2 去PSG原理:
的光生电子会沿着边缘扩散有磷的区域流到PN结的背面,而造成短路
,此短路通道等效于降低并联电阻。������
经过刻蚀工序,硅片边缘带有的磷将会被去除干净,避免PN结短路造成并
联电阻降低。
1.2 去PSG目的
由于在扩散过程中氧的通入,在硅片表面形成一层SiO2,在高温
下POCl3与O2形成的P2O5,部分P原子进入Si取代部分晶格上的Si原子
形成n型半导体,部分则留在了SiO2中形成PSG。
磷硅玻璃的存在使得硅片在空气中表面容易受潮,导致电流的降低 和功率的衰减。
死层的存在大大增加了发射区电子的复合,会导致少子寿命的降低 ,进而降低了Voc和Isc。
磷硅玻璃的存在使得PECVD后产生色差,在PECVD工序将使镀的 SIxNy容易发生脱落,降低电池的转换效率
循环流量:调节循环流量,观察刻蚀效果,一般情况下,循环 流量增加刻蚀线宽增加,反之。
4.2、刻蚀线:可能出现过刻或刻蚀不足的情况,一般不超过 2mm,通过肉眼观察,也可通过冷热探针测量边缘电压来判 断是否刻通。
刻蚀不足:一般首先通过调节参数保证腐蚀深度在工艺 控制范围内即可。
检验方法
冷热探针法
冷热探针法测导电型号
检验原理
热探针和N型半导体接触时,传导电子将流向温度较低的区域, 使得热探针处电子缺少,因而其电势相对于同一材料上的室温 触点而言将是正的。
刻蚀工序培训讲解

后清洗到PECVD的产品时间最长不能超过4小时,时间过长硅片会污染 氧化,从 而影响产品的电性能及效率.
刻蚀槽液面的注意事项: 正常情况下液面均处于绿色,如果一旦在流片过程中颜色改变,立 即通知工艺人员。
二、刻蚀工序质量培训
刻蚀工序质量控制点
刻蚀工序的质量控制主要分为来料质量控制和刻蚀后的质量 控制。
每批片子的腐蚀重量和绝缘电阻都要检测。 1.要求每批测量4片。 2.每次放测量片时,把握均衡原则。如第一批把测试片放1.3.5.7道, 下一批则放2.4.6.8道,便于监控设备稳定性和溶液的均匀性。
生产没有充足的片子时,工艺要求: 1.如果有1小时以上的停机,要将刻蚀槽的药液排到tank,减少药液的 挥发。 2.停机后15分钟用水枪冲洗碱槽喷淋及风刀,防止酸碱形成的结晶盐 堵塞喷淋口及风刀。 3.停机1小时以上,要在开启机器生产前半小时用水枪冲洗风刀处的滚 轮,杜绝做出来的片子有滚轮印!
冷热探针法的检测原理 探针和N型半导体接触时,传导电流将流向温度较低的区域,使得热探
针处的电子缺少,因而其电势相对于同一材料上的室温触点而言是正的。同 样原理,P型半导体热探针触电相对于室温触点而言是负的。
万用表操作及判断
•1)确认万用表工作正常,量程置于200mv。
•2 )冷探针连接电压表的正电极,热探针与电压表的负极相连。
上片 清洗1 清洗2 清洗3 下片
碱洗 吹干2
刻蚀槽:用于边缘刻蚀,去除背面及边缘的PN结。 所用溶液为
HF+HNO3+H2SO4,主要工艺参数:
Firstfill volume:270.0L;
Firstfill volume H2SO4 :80.0L;
concentrations of chemical:HF(35g/L)&HNO3 (350g/L);
蚀刻培训讲义
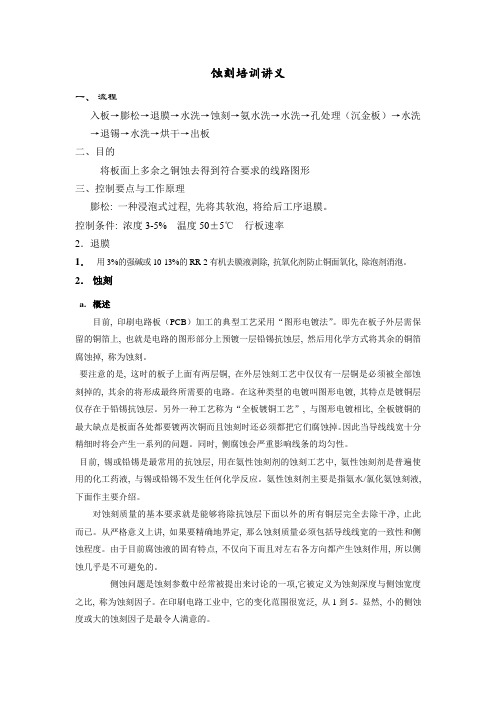
蚀刻培训讲义一、流程入板→膨松→退膜→水洗→蚀刻→氨水洗→水洗→孔处理(沉金板)→水洗→退锡→水洗→烘干→出板二、目的将板面上多余之铜蚀去得到符合要求的线路图形三、控制要点与工作原理膨松: 一种浸泡式过程, 先将其软泡, 将给后工序退膜。
控制条件: 浓度3-5% 温度50±5℃行板速率2.退膜1.用3%的强碱或10-13%的RR-2有机去膜液剥除, 抗氧化剂防止铜面氧化, 除泡剂消泡。
2.蚀刻a.概述目前, 印刷电路板(PCB)加工的典型工艺采用“图形电镀法”。
即先在板子外层需保留的铜箔上, 也就是电路的图形部分上预镀一层铅锡抗蚀层, 然后用化学方式将其余的铜箔腐蚀掉, 称为蚀刻。
要注意的是, 这时的板子上面有两层铜, 在外层蚀刻工艺中仅仅有一层铜是必须被全部蚀刻掉的, 其余的将形成最终所需要的电路。
在这种类型的电镀叫图形电镀, 其特点是镀铜层仅存在于铅锡抗蚀层。
另外一种工艺称为“全板镀铜工艺”, 与图形电镀相比, 全板镀铜的最大缺点是板面各处都要镀两次铜而且蚀刻时还必须都把它们腐蚀掉。
因此当导线线宽十分精细时将会产生一系列的问题。
同时, 侧腐蚀会严重影响线条的均匀性。
目前, 锡或铅锡是最常用的抗蚀层, 用在氨性蚀刻剂的蚀刻工艺中, 氨性蚀刻剂是普遍使用的化工药液, 与锡或铅锡不发生任何化学反应。
氨性蚀刻剂主要是指氨水/氯化氨蚀刻液, 下面作主要介绍。
对蚀刻质量的基本要求就是能够将除抗蚀层下面以外的所有铜层完全去除干净, 止此而已。
从严格意义上讲, 如果要精确地界定, 那么蚀刻质量必须包括导线线宽的一致性和侧蚀程度。
由于目前腐蚀液的固有特点, 不仅向下而且对左右各方向都产生蚀刻作用, 所以侧蚀几乎是不可避免的。
侧蚀问题是蚀刻参数中经常被提出来讨论的一项,它被定义为蚀刻深度与侧蚀宽度之比, 称为蚀刻因子。
在印刷电路工业中, 它的变化范围很宽泛, 从1到5。
显然, 小的侧蚀度或大的蚀刻因子是最令人满意的。
刻蚀工序培训

胶手套以及防护服。并确保该产品附近有安全淋浴及洗眼器。
硝酸 HNO3
特性: 无色透明至淡黄色冒烟液体、有刺激性、挥发性气味。
危害: 其蒸汽有刺激作用,引起眼和上呼吸道刺激症状,如流泪、咽喉刺
激感、呛咳,并伴有头痛、胸闷等。口服引起腹部剧痛,严重者可有胃 穿孔、腹膜炎、喉痉挛、肾损害、休克以及窒息。皮肤接触引起灼伤。 防护措施:
刻蚀原理:
①4HNO3+3Si=3SiO2+4NO+2H2O
②SiO2+6HF=H2[SiF6]+2H2O
去PSG(磷硅玻璃)原理:
SiO2 4HF SiF4 2H2O SiF4 2HF H2[SiF6]
什么是磷硅玻璃
• 在扩散过程中发生如下反应:
5POCL3 600C 3PCL5 P 2O 5 4PCL5 5O 2 800C 2P 2O 5 10CL2 2P 2O 5 5Si 800C 5SiO 2 4P
工艺控制指标
4 方阻上升符合工艺要求
检测方法: • 每批取5片,分别测试刻蚀前
和刻蚀后中心点的方阻并记 录。 • 方阻上升必须小于6。
发现不符合要求的硅片时: • 必须马上停止该台设备的生产; • 正在生产的硅片不能流入下工序; • 通知工艺人员处理。
刻蚀间化学品的种类
• 刻蚀间主要使用的化学的种类有:
•
加强自身建设,增强个人的休养。2020年11月24日 下午4时 18分20.11.2420.11.24
•
追求卓越,让自己更好,向上而生。2020年11月24日星期 二下午4时18分 18秒16:18:1820.11.24
刻蚀培训

尽管很复杂,但刻蚀反应不外分成两步: 硝酸/亚硝酸(HNO2)将硅氧化成二氧化硅(主要是亚 硝酸将硅氧化)。 二氧化硅和氢氟酸反应(快反应),生成四氟化硅和水 (快反应),四氟化硅又和水化合成氟硅酸进入溶液。 硫酸不参与反应,仅仅是增加氢离子浓度,加快反应, 增加溶液黏度(增大溶液与PSG薄层间的界面张力)和 溶液密度。
二、湿 法 刻 蚀
Rena InOxSide 大致构造
刻蚀槽
上
H2SO4/
水 喷
碱洗槽 水 去PSG槽 水
喷
喷
片 HNO3/
淋
NaOH 淋
HF
淋
HF
吹 干
下
风片
刀
1.“一化一水”,硅片每经过一次化学品,都会经过一次水喷淋清洗。 2.除刻蚀槽和第一道水喷淋之间,其它的槽和槽之间都有吹液风刀。 3.除刻蚀槽外,其它化学槽和水槽都是喷淋结构,去PSG氢氟酸槽 是喷淋结构,而且片子进入到溶液内部。 4.最后一道水喷淋(第三道水喷淋)由于要将所有化学品全部洗掉,所 以水压最大。相应的,最后的吹干风刀气压最大。
受PSG影响,对于没有去PSG的单晶片子,正面会有 溶液铺展。 对于铺展上去了的溶液蒸发旺盛,PSG快速消耗氢氟 酸,这些因素造成溶液浓度下降,无法刻蚀硅片;所 以就需要从刻蚀溶液主体来输运酸以保持浓度。 硫酸有时虽会减少铺展,但它会减小氢氟酸、硝酸的 挥发,增加反应速率,有时甚至加深了正面刻蚀。
SiO2+4HF→SiF4↑+2H2O 但是如果HF过量,则SiF4会和HF继续反应,总的反应 式为:
SiO2+6HF→H2[SiF6]+2H2O
操作注意事项
插片务必确认扩散面的方向。 更换氢氟酸必须同时对槽进行彻底清洗。在配制和清 洗时,一定要做好保护措施。 硅片在两个槽中(悬挂在空中)的停留时间不得过长 ,防止硅片被氧化。 甩干的时间不能随便缩短!防止干燥不彻底。 当硅片从氢氟酸槽中提起时,观察其表面是否脱水, 如果脱水,则表明磷硅玻璃已去除干净;如果表面还 沾有水珠,则表明磷硅玻璃未被去除干净。
刻蚀培训

一、干 法 刻 蚀
刻蚀的目的
由于在扩散过程中,即使采用背靠背的单面扩散方式 ,硅片的所有表面(包括边缘)都将不可避免地扩散 上磷。PN结的正面所收集到的光生电子会沿着边缘扩 散有磷的区域流到PN结的背面,而造成短路。此短路 通道等效于降低并联电阻。 经过刻蚀工序,硅片边缘的带有的磷将会被去除干净 ,避免PN结短路造成并联电阻降低。
干法刻蚀原理
等离子体的定义: 随着温度的升高,一般物质依次表现为固体、液体和 气体。它们统称为物质的三态。 如果温度升高到10e4K甚至10e5K,分子间和原子间 的运动十分剧烈,彼此间已难以束缚,原子中的电子 因具有相当大的动能而摆脱原子核对它的束缚,成为 自由电子,原子失去电子变成带正电的离子。这样, 物质就变成了一团由电子和带正电的的离子组成的混 合物。这种混合物叫等离子体。它可以称为物质的第 四态。
刻蚀线
刻蚀线一般是淡淡的一条黑线,正常情况下刻蚀线到边缘的距离控 制在1.5mm以下,最宽不得超过1.5mm。而有时在边缘会有很显眼 的很黑很黑的线或黑区,这些东西就不是刻蚀线了,而是没有洗干 净的酸,此时需要在碱槽手动补碱来解决。如果多次出现这种情况, 必须检查碱洗槽是否堵碱。
湿法刻蚀相对等离子刻蚀的优点
超越工艺——其它
制冷机跳闸与故障 碱喷淋后的吹液风刀堵孔:导致碱液被带出, 频繁出现碱槽液位过低的报警。
谢 谢!
5Si+6HNO3+30HF=5H2SiF6+2NO2+4NO+10H2O+3H2
尽管很复杂,但刻蚀反应不外分成两步:
硝酸/亚硝酸(HNO2)将硅氧化成二氧化硅(主要是亚
硝酸将硅氧化)。 二氧化硅和氢氟酸反应(快反应),生成四氟化硅和水 (快反应),四氟化硅又和水化合成氟硅酸进入溶液。 硫酸不参与反应,仅仅是增加氢离子浓度,加快反应,
刻蚀培训
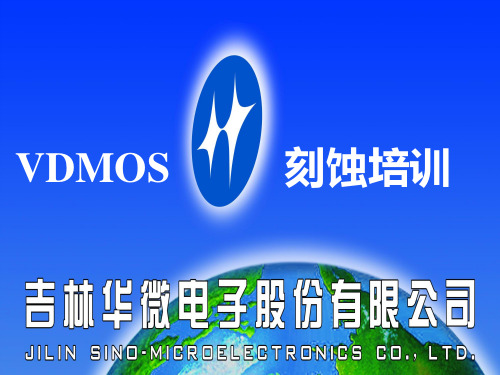
2013-8-9 17
当刻蚀气体被通入刻蚀反应腔中,在射频电场的作用下产生等离子体辉 光放电,反应气体分解成各种中性的化学活性基团,分子、电子、离子; 由于电子和离子的质量不同使得质量较轻的电子能够响应射频电场的变 化而离子却不能,正是这种差异在电极上产生负偏压 Vdc(Negative DC bias) ,离子在负偏压的加速下轰击硅片表面形成反应离子刻蚀;一个持 续的干法刻蚀必须要满足这些条件:在反应腔内有源源不断的自由基团; 硅片必须靠等离子体足够近以便反应基团可以扩散到其表面;反应物应 被硅片表面吸附以持续化学反应;挥发性的生成物应可从硅片表面解吸 附并被抽出反应腔。上面的任一种条件末达到刻蚀过程都会中断。刻蚀 的具体过程可描述为如下六个步骤: 1. 刻蚀物质的产生;射频电源施加在一个充满刻蚀 气体的反应腔上,通 过等离子体辉光放电产生电子、离子、活性反应基团。 2. 刻蚀物质向硅片表面扩散; 3. 刻蚀物质吸附在硅片表面上; 4. 在离子轰击下刻蚀物质和硅片表面被刻蚀材料发生反应; 5. 刻蚀反应副产物在离子轰击下解吸附离开硅片表面; 6. 挥发性刻蚀副产物和其它未参加反应的物质被真空泵抽出反应腔。
2013-8-9 8
SiO2湿法腐蚀
金属湿法腐蚀
金属旋转腐蚀: 设备:SPW-612-A,要改造成6寸的 TEMP:53±1℃ 腐蚀液:H3PO4:HNO3:HAC:H2O=80:5:5:10 工艺程序:
ITEM/STEP N T C V unit RPM sec 喷液 9.6 0 1 600 166 1 3 2 700 5 0 3 800 168 1 4 900 5 0 5 60 5 6
2013-8-9
19
刻蚀间工艺培训2

HF/HNO3体系腐蚀机理特点
大致旳腐蚀机制是先氧化再清除,酸对硅旳腐蚀 速度与晶粒取向无关,所以酸腐蚀又称为各向同性腐 蚀。
在HF-HNO3溶液中旳刻蚀速率是各向同性,(100)面旳刻蚀速 率和(111)面旳腐蚀速率非常接近。
三、滚轴和内槽槽边高度(水平):滚轴高度决定硅片经过刻蚀 槽时旳高度,而内槽槽边高度(水平)决定刻蚀槽液面旳大致 高度,两者旳高度差距只有在合理范围内,硅片才干吸附到刻 蚀液;
四、滚轴水平:滚轴水平,5道轨道内运营旳硅片才干与刻蚀 液水平面平行,只有平行于水平面,硅片吸附刻蚀液才均匀, 也即刻蚀均匀,无过刻或刻不通现象;
SiO2+6HFH2SiF6+2H2O
HF/HNO3体系腐蚀机理
大致旳腐蚀机制是HNO3 (一种氧化剂)腐蚀,在硅片表 面形成了一层SiO2,然后这层SiO2在HF 酸旳作用下清除。
在低HNO3及高HF浓度区,生成SiO2旳能力 弱而清除SiO2旳能力强,反应过程受HNO3氧 化反应控制,所以腐蚀曲线平行于等HNO3 浓度线 。
刻蚀工艺培训
检测
•热探针和N型半导体接触时,传导电 子将流向温度较低旳区域,使得热探 针处电子缺乏,因而其电势相对于同 一材料上旳室温触点而言将是正旳。 •一样道理,P型半导体热探针触点相 对于室温触点而言将是负旳。 •此电势差能够用简朴旳微伏表测量。 •热探针旳构造能够是将小旳热线圈 绕在一种探针旳周围,也能够用小型 旳点烙铁。
简朴设备构造与工艺阐明图示
HF/HNO3体系腐蚀机理
硅在HON3+HF溶液中旳腐蚀速率大,而在纯HNO3或纯HF溶液中旳腐蚀速率很小。
刻蚀相关知识点总结

刻蚀相关知识点总结刻蚀技术主要分为湿法刻蚀和干法刻蚀两种。
湿法刻蚀是在溶液中通过化学反应去除材料表面的工艺,而干法刻蚀是在气相中通过物理或化学反应去除材料表面的工艺。
下面将详细介绍刻蚀的相关知识点。
一、刻蚀的基本原理1. 湿法刻蚀原理湿法刻蚀是利用化学溶液对材料表面进行腐蚀或溶解的工艺。
湿法刻蚀的原理是在溶液中加入具有特定功能的化学试剂,使其与被刻蚀物质发生化学反应,从而去除材料表面的部分物质。
湿法刻蚀通常可以实现较高的刻蚀速率和较好的表面质量,但需要考虑溶液中的成分和温度对环境的影响。
2. 干法刻蚀原理干法刻蚀是利用气相中的等离子体或化学反应对材料表面进行腐蚀或清除的工艺。
干法刻蚀的原理是在高能离子束或化学气体的作用下,使被刻蚀物质表面发生物理或化学反应,从而去除材料表面的部分物质。
干法刻蚀通常可以实现更高的加工精度和更好的表面质量,但需要考虑设备的复杂性和成本的影响。
二、刻蚀的工艺参数1. 刻蚀速率刻蚀速率是刻蚀过程中单位时间内去除的材料厚度,通常以单位时间内去除的厚度为单位。
刻蚀速率的选择需要综合考虑刻蚀材料的性质、刻蚀条件、刻蚀设备和加工要求等因素。
2. 刻蚀选择性刻蚀选择性是指在多种材料叠加或混合结构中选择性地去除某一种材料的能力。
刻蚀选择性的选择需要考虑被刻蚀材料和其它材料之间的化学反应性和物理性质的差异,以实现精确的刻蚀。
3. 刻蚀均匀性刻蚀均匀性是指在整个刻蚀过程中去除材料的厚度分布情况。
刻蚀均匀性的选择需要考虑刻蚀设备和刻蚀条件对被刻蚀物质的影响,以实现均匀的刻蚀。
4. 刻蚀深度控制刻蚀深度控制是指在整个刻蚀过程中去除材料的深度分布情况。
刻蚀深度控制的选择需要综合考虑刻蚀设备和刻蚀条件对被刻蚀物质的影响,以实现精确的刻蚀深度。
5. 刻蚀环境控制刻蚀环境控制是指在整个刻蚀过程中对刻蚀环境(如溶液中的成分、气相中的气体、温度和压力等)的控制。
刻蚀环境控制的选择需要考虑被刻蚀材料的特性和加工的要求,以实现良好的刻蚀效果。
刻蚀原理及工艺培训

刻蚀原理及工艺培训刻蚀是一种常用的微纳加工技术。
它通过在材料表面刻蚀掉一定的材料,以达到加工目的。
刻蚀过程是一个逐渐去除材料的过程,它可以用于制作微型器件、集成电路、MEMS器件、光学元件等。
本篇文章将详细介绍刻蚀的原理以及常见的刻蚀工艺。
刻蚀的原理主要是利用化学反应或物理作用使材料表面的原子在特定条件下发生转变及被移除,从而实现刻蚀过程。
常见的刻蚀方式包括湿法刻蚀和干法刻蚀。
湿法刻蚀是在液体中进行刻蚀,通过浸泡在刻蚀液中的材料表面与刻蚀液中的反应物发生反应,从而溶解或转化材料。
湿法刻蚀的刻蚀速率由刻蚀液中的反应物浓度、刻蚀液中的温度、刻蚀液的搅拌速度等因素决定。
湿法刻蚀可以实现高度的选择性,即只刻蚀特定的材料。
常用的湿法刻蚀液包括酸、碱、氧化剂等。
干法刻蚀是在气相中进行刻蚀,通过将材料表面暴露在气体环境中,利用化学反应或物理作用来去除材料表面的原子。
常用的干法刻蚀技术包括物理刻蚀和化学气相刻蚀。
物理刻蚀是利用离子束轰击材料表面,通过离子与材料表面原子的相互作用来去除材料。
物理刻蚀通常需要一个离子源和一个加速电场。
离子源根据需要选择不同的气体,例如氩气、氙气等。
物理刻蚀可以实现高度的选择性和精度,广泛应用于集成电路制造等领域。
化学气相刻蚀是利用化学反应将材料表面上的原子移除。
常用的化学气相刻蚀技术包括反应离子刻蚀和等离子体刻蚀。
反应离子刻蚀通过离子轰击材料表面,使表面原子与气相中的反应物发生化学反应,从而去除材料。
等离子体刻蚀则是利用等离子体产生的高能反应物与材料反应来刻蚀材料。
化学气相刻蚀具有高速和均匀性的优点,被广泛应用于光学元件、显示器件等领域。
除了刻蚀原理外,刻蚀工艺也是刻蚀技术中非常重要的一环。
刻蚀工艺包括刻蚀装备、刻蚀参数的选择以及刻蚀后的处理等。
刻蚀装备通常包括刻蚀机、进气装置、抽真空装置等。
不同的刻蚀装备适用于不同的刻蚀工艺,例如湿法刻蚀需要具备湿法刻蚀槽、搅拌器等设备,而干法刻蚀需要具备加速电场、离子源等设备。
刻蚀培训ppt课件
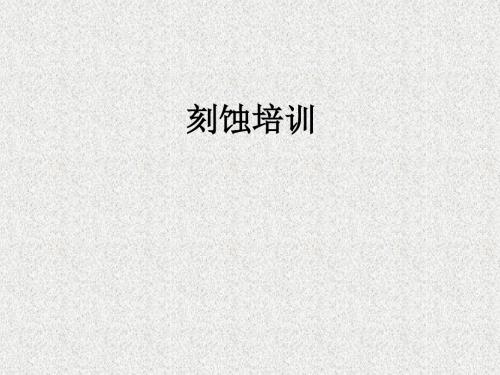
SiO2+6HFH2SiF6+2H2O
HF/HNO3体系腐蚀机理
大致的腐蚀机制是HNO3 (一种氧化剂)腐蚀, 在硅片表面形成了一层SiO2,然后这层SiO2在HF 酸的作用下去除。
• 在低HNO3及高HF浓度区,生成SiO2的能力弱而去除SiO2的能力强, 反应过程受HNO3氧化反应控制,所以腐蚀曲线平行于等HNO3浓度 线。 在低HF高HNO3浓度区,生成SiO2的能力强而去除SiO2的能力弱, 反应过程受HF反应控制,所以腐蚀线平行于HF浓度线。
简单设备结构与工艺说明图示
HF/HNO3体系腐蚀机理
硅在HON3+HF溶液中的腐蚀速率大,而在纯 HNO3或纯HF溶液中的腐蚀速率很小。
1. 在低HNO3及高HF浓度区(图右角区) 等腐蚀曲线平行于等HNO3浓度线 。
2. 在低HF高HNO3浓度区(图左下角区) 等腐蚀线平行于HF浓度线。
图:硅在70%(重量)HNO3+49%(重量)HF混合液中 的腐蚀速率与成分的关系
4
等离子体的应用
5
等离子体的产生
6
等离子体刻蚀原理
• 等离子体刻蚀是采用高频辉光放电反应,使反应气体激活成活性粒子, 如原子或游离基,这些活性粒子扩散到需刻蚀的部位,在那里与被刻 蚀材料进行反应,形成挥发性反应物而被去除。 • 这种腐蚀方法也叫做干法腐蚀。
7
等离子体刻蚀反应
8
• 首先,母体分子CF4在高能量的电子的碰撞作用下分解成多种中性基团 或离子。
e
CF CF , CF , CF, F, C 以及 它们的离
4 3 2
• 其次,这些活性粒子由于扩散或者在电场作用下到达SiO2表面,并在表 面上发生化学反应。
刻蚀工艺培训

上海神舟新能源发展有限公司
去PSG清洗常见工艺问题 PSG清洗常见工艺问题
4. 异常现象:补HF时无法补液。 时无法补液。 时无法补液 补液处的液位传感器故障。 分析原因: CDS补液处的液位传感器故障。 补液处的液位传感器故障 检查供液泵开了没, 解决办法:检查供液泵开了没,如果开了不抽说明管路里 没有液体,查看 储罐是否有液 若没有,则更换桶; 储罐是否有液, 没有液体,查看HF储罐是否有液,若没有,则更换桶;若 溶液, 有HF溶液,则手动补 ,给传感器一个有液信号,并重启 溶液 则手动补HF,给传感器一个有液信号, 设备、电脑,若依旧无法补液说明传感器坏了, 设备、电脑,若依旧无法补液说明传感器坏了,联系设备人 员更换传感器。 员更换传感器。
上海神舟新能源发展有限公司
Thank you!
上海神舟新能源发展有限公司
1
刻蚀时间:刻蚀时
间越长, 间越长,对硅片造成 损伤影响越大; 损伤影响越大;刻饰 时间过短, 时间过短,导致并联 电阻下降
2
4
3
气体流量:合适的
流量和气体通入的时 间比会很大程度上影 响刻蚀面的侧壁形貌、 响刻蚀面的侧壁形貌、 反应速率等
工艺压力:压力取
决于通气量和泵的抽 速,合理的压力设定 值可以增加对反应速 率的控制、 率的控制、增加反应 气体的有效利用率等
刻蚀工序工艺培训
上海神舟新能源发展有限公司
刻蚀工序简介
刻蚀: 刻蚀:主要负责电池片边缘的刻蚀和扩散后硅片上磷硅玻 璃的清洗。 璃的清洗。 设备(单晶线): ):志圣等离子刻蚀机和捷佳创去磷硅玻璃清 设备(单晶线):志圣等离子刻蚀机和捷佳创去磷硅玻璃清 洗机。 洗机。
等离子刻蚀机
上海神舟新能源发展有限公司
激光刻蚀操作规程培训

激光刻蚀操作规程培训激光刻蚀操作规程培训一、操作概述激光刻蚀是一种常见的微细加工技术,通过高能激光束的蚀刻作用,将材料表面或内部部分物质蒸发或烧蚀,实现对材料进行精细加工的过程。
本次培训旨在向操作人员介绍激光刻蚀的操作规程以及相关注意事项,以确保操作安全和加工效率。
二、操作规程1. 操作前准备- 检查激光刻蚀设备的运行状态,确保各部件正常工作。
- 检查激光刻蚀工作台的环境清洁度,清除杂物和灰尘。
- 穿戴个人防护装备,包括防护眼镜、防护手套等。
2. 材料准备- 准备待加工材料,包括样品或工件。
- 对于需要固定的材料,采用夹具或者其他固定装置进行固定。
3. 参数设置- 根据材料的特性和加工要求,设置合适的激光功率、扫描速度、脉冲频率等参数。
- 注意选择合适的激光工作模式,包括连续激光和脉冲激光。
4. 操作步骤- 打开激光刻蚀设备的电源,启动设备,并进行预热。
- 确认激光刻蚀头的位置和对准,确保激光能够准确照射到待加工材料上。
- 进行试刻,通过调整参数,确定合适的刻蚀效果。
- 进行正式的刻蚀操作,根据需求进行刻蚀加工。
5. 操作注意事项- 操作人员应保持警觉,切勿将手部或其他物体靠近激光束。
- 激光刻蚀过程中,切勿随意更改参数,以免影响刻蚀效果。
- 操作人员应保持通畅的听力和健康状态,避免因激光噪音或辐射引起不适。
6. 刻蚀后处理- 刻蚀完成后,关闭激光刻蚀设备,断开电源。
- 对加工后的材料进行检查,确保刻蚀效果符合要求。
- 清理工作台和设备,保持整洁。
三、操作安全1. 避免直接观察激光刻蚀过程,以免损伤视力。
2. 避免长时间暴露在激光束下,以免皮肤灼伤。
3. 坚守激光刻蚀设备的安全操作规程,严禁随意修改设备结构或参数。
4. 若发生设备故障或异常情况,立即停止操作并向维护人员报告。
四、事故处理1. 如果出现事故,如激光束误伤或设备故障,操作人员应立即停止操作并采取紧急措施。
2. 汇报事故情况,并及时向相关责任人说明情况。
刻蚀

23
4
ICP刻蚀原理及设备
Oxford Plasma lab System 100 ICP 180
温控
真空
能量产生
气路
Wafers经由loadlock后再进出反应腔,确保反 应腔维持在真空下不受粉尘及湿度的影响. 将有毒气体及危险气体与超净室隔离开 24
4
ICP刻蚀原理及设备
•ICP功率: 0-3000W •RF功率:0-1000W •压力范围: 1-100mT •加工范围:6寸 •工艺气体: Cl2,BCl3,HBr,CH4,He,O2, H2,N2
GaAs Via
>2
BCl3/Cl2
PR
>20:1
InP
>2
HBr
SiO2
>10:1
<±3% (1 x <±3% 2”)
28
4
ICP刻蚀原理及设备
GaAs 刻蚀
29
4
ICP刻蚀原理及设备
GaAs 穿孔刻蚀
30
4
ICP刻蚀原理及设备
GaN刻蚀
31
4
ICP刻蚀原理及设备
InP刻蚀
32
4
ICP刻蚀原理及设备
39
刻蚀 1开启 “气体流量显示及控制”这一栏下方的截止阀,并将截止阀上方的开关拨向“阀控”,旋 其右方的旋钮根据需要设定Ar气的气体流量。(一般稳定在4.7Sccm) 2开启 “刻蚀时间显示及控制”在这一栏下方“旋转”与“冷却”按钮,并设定所需要的刻蚀时间。 3开启离子源开关,设定参数如下: 3.1调节“阴极”旋钮,使其上方的阴极电流量程表指示为5.5A-6A。 3.2调节“阳极”旋钮,直至起弧为止。(即阳极电流量程表有指数) 3.3调节“加速”旋钮,使其上方的加速电压量程表指数为180V。 3.4调节“屏栅”旋钮,使“离子能量”显示为所需要的数值。(此时加速电压可能会有 波动,再次适当调节“加速”旋钮和“屏栅”旋钮,使其加速电压和离子能量达到所需要 的数值)。 3.5调节“阴极”和“阳极”旋钮,使得 “离子束流”显示为所需要的数值,同时要保证阳 极电压量程表指示数为45V左右。(因为各电源之间有关联,调节过程需要配合进 行) 3.6调节“中和”旋钮,使得 “中和电流”显示为所需要的数值。(中和电流一般为离子 束流的1.3---1.5倍之间) 4参数设定完毕后,开启 “时控”按钮,此时,载片台上方的挡板移开,刻蚀开始, 如果需要一定的入射角进行刻蚀,可以旋转门板上的手柄,使其载片台旋转至所需 要的角度。 5按所规定的时间刻蚀完毕后,关闭 “时控”按钮,此时,载片台上方的挡板又重新 回到片子的上方了。(注意:如果刻蚀过程中,载片台有一定的角度,则在挡板重 新回到片子上方前一定要将载片台扳到原来的0度,以免挡板与载片台相撞)
刻蚀原理及工艺培训

维护保养
辉光前必须按下橙色按钮对电子管预热10—15min。 。 辉光前必须按下橙色按钮对电子管预热 辉光结束后须冷却15min后,才可关闭电源。 高频电源实际使用功率不能超过800W。 高频电源地线必须独立接地,不允许与其它设备共用地。 反应管需定期旋转,以便延长其使用寿命。 长期停机时反应室应抽为真空状态,以免被污染。 做完一个循环后,若不立即做下一个循环,应盖上盖子。 每天要清洁反应室,特别是密封部位,否则真空漏气。 非设备人员请勿调节高频部分,有问题通知设备人员。
冷热探针测试注意
确认万用表工作正常,量程置于200mV。 冷探针连接电压表的正电极,热探针与电压表的负极相连。
等离子体刻蚀工艺原理
等离子体刻蚀机是基于真空中的高频激励而产生的辉光 等离子体刻蚀机是基于真空中的高频激励而产生的辉光 真空中的高频激励而产生的 放电将四氟化碳中的氟离子电离出来从而获得化学活性 放电将四氟化碳中的氟离子电离出来从而获得化学活性 微粒与被刻蚀材料起化学反应产生辉发性物质进行刻蚀 的。同时为了保证氟离子的浓度和刻蚀速度必须加入一 氧气生成二氧化碳 定比例的氧气生成二氧化碳。 定比例的氧气生成二氧化碳。 这种腐蚀方法也叫做干蚀法 干蚀法。 这种腐蚀方法也叫做干蚀法。 生产过程中, 中掺入O2,这样有利于提高Si和 生产过程中,在CF4中掺入 ,这样有利于提高 和 中掺入 SiO2的刻蚀速率。 的刻蚀速率。 的刻蚀速率
压力控制系统
压力控制仪 电容式薄膜压力 变送器 电子执行器 蝶阀
高频电源和匹配器技术性能
最大输出功率10~1000W 板极电压200~2700V 板极电流0~500mA 转换效率大于80% 振荡频率13.56MHz 反射功率调配小于5% 连续工作时间小于4h
- 1、下载文档前请自行甄别文档内容的完整性,平台不提供额外的编辑、内容补充、找答案等附加服务。
- 2、"仅部分预览"的文档,不可在线预览部分如存在完整性等问题,可反馈申请退款(可完整预览的文档不适用该条件!)。
- 3、如文档侵犯您的权益,请联系客服反馈,我们会尽快为您处理(人工客服工作时间:9:00-18:30)。
刻蚀机整体结构
反应室 真空系统 送气系统 压力控制系统 高频电源和匹 配器
反应室结构
石英管 上下密封圈 电机旋转台 正常辉光时为 乳白色
真空系统
旋片式真空泵 电磁隔断放气阀 波纹管 碟阀 预抽阀 主抽阀
送气系统
O2、CF4、N2和压缩空气 尾气、稀释、保护氮气 四氟化碳和氧气10:1的器,再打开操作面板的电源按钮开关; 打开工作气体(N2,O2,CF4)手动阀并调整压力在0.2Mpa,压 缩空气手动阀,调节压力0.5Mpa左右; 打开真空泵与射频电源电子管“预热”按钮,预热10—20分钟; 打到“手动”状态,并按下“充气”按钮 ,报警提示开盖; 将硅片按照工艺要求装夹,并小心放入反应室内,盖好密封盖; 打到“自动”状态,并按下“运行”按钮,此时设备按工艺流程自 动运行; 结束时报警提示,关掉“运行”按钮后才能打开上盖,取片。
压力控制系统
压力控制仪 电容式薄膜压力 变送器 电子执行器 蝶阀
高频电源和匹配器技术性能
最大输出功率10~1000W 板极电压200~2700V 板极电流0~500mA 转换效率大于80% 振荡频率13.56MHz 反射功率调配小于5% 连续工作时间小于4h
刻蚀机系统原理
刻蚀工艺流程
预抽开(2-3min) 主抽开同时关预抽(2min) 开CF4和O2同时压力调节(2-3min) 开高频辉光进行刻蚀(12min) 关高频和CF4及 O2 抽真空(0.5min) 通保护N2(2min) 关主抽同时充气(1min) 到大气压蜂鸣开盖
维护保养
辉光前必须按下橙色按钮对电子管预热10—15min。 。 辉光前必须按下橙色按钮对电子管预热 辉光结束后须冷却15min后,才可关闭电源。 高频电源实际使用功率不能超过800W。 高频电源地线必须独立接地,不允许与其它设备共用地。 反应管需定期旋转,以便延长其使用寿命。 长期停机时反应室应抽为真空状态,以免被污染。 做完一个循环后,若不立即做下一个循环,应盖上盖子。 每天要清洁反应室,特别是密封部位,否则真空漏气。 非设备人员请勿调节高频部分,有问题通知设备人员。
冷热探针测试注意
确认万用表工作正常,量程置于200mV。 冷探针连接电压表的正电极,热探针与电压表的负极相连。
等离子体刻蚀工艺原理
等离子体刻蚀机是基于真空中的高频激励而产生的辉光 等离子体刻蚀机是基于真空中的高频激励而产生的辉光 真空中的高频激励而产生的 放电将四氟化碳中的氟离子电离出来从而获得化学活性 放电将四氟化碳中的氟离子电离出来从而获得化学活性 微粒与被刻蚀材料起化学反应产生辉发性物质进行刻蚀 的。同时为了保证氟离子的浓度和刻蚀速度必须加入一 氧气生成二氧化碳 定比例的氧气生成二氧化碳。 定比例的氧气生成二氧化碳。 这种腐蚀方法也叫做干蚀法 干蚀法。 这种腐蚀方法也叫做干蚀法。 生产过程中, 中掺入O2,这样有利于提高Si和 生产过程中,在CF4中掺入 ,这样有利于提高 和 中掺入 SiO2的刻蚀速率。 的刻蚀速率。 的刻蚀速率