不锈钢连铸生产工艺与设备
不锈钢线材生产工艺
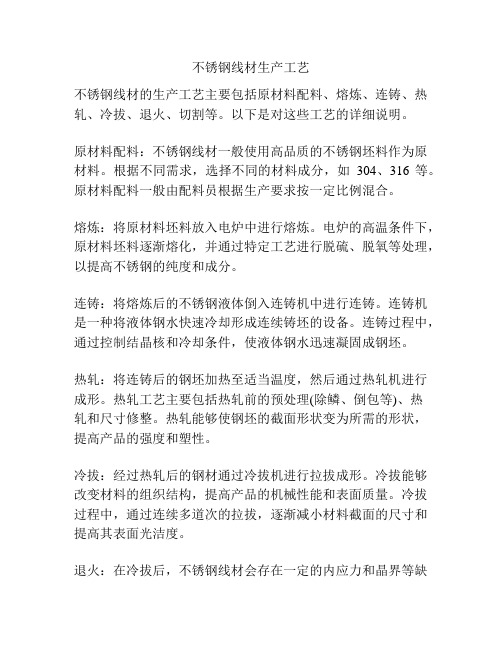
不锈钢线材生产工艺不锈钢线材的生产工艺主要包括原材料配料、熔炼、连铸、热轧、冷拔、退火、切割等。
以下是对这些工艺的详细说明。
原材料配料:不锈钢线材一般使用高品质的不锈钢坯料作为原材料。
根据不同需求,选择不同的材料成分,如304、316等。
原材料配料一般由配料员根据生产要求按一定比例混合。
熔炼:将原材料坯料放入电炉中进行熔炼。
电炉的高温条件下,原材料坯料逐渐熔化,并通过特定工艺进行脱硫、脱氧等处理,以提高不锈钢的纯度和成分。
连铸:将熔炼后的不锈钢液体倒入连铸机中进行连铸。
连铸机是一种将液体钢水快速冷却形成连续铸坯的设备。
连铸过程中,通过控制结晶核和冷却条件,使液体钢水迅速凝固成钢坯。
热轧:将连铸后的钢坯加热至适当温度,然后通过热轧机进行成形。
热轧工艺主要包括热轧前的预处理(除鳞、倒包等)、热轧和尺寸修整。
热轧能够使钢坯的截面形状变为所需的形状,提高产品的强度和塑性。
冷拔:经过热轧后的钢材通过冷拔机进行拉拔成形。
冷拔能够改变材料的组织结构,提高产品的机械性能和表面质量。
冷拔过程中,通过连续多道次的拉拔,逐渐减小材料截面的尺寸和提高其表面光洁度。
退火:在冷拔后,不锈钢线材会存在一定的内应力和晶界等缺陷,为了消除这些缺陷,需要进行退火处理。
退火过程中,将不锈钢线材加热至适当温度,然后慢慢冷却,以恢复其本身的塑性和韧性。
切割:经过退火处理后的不锈钢线材,根据客户要求,通过切割机进行切割。
切割机能够将长线材切断成所需长度的线材,以便进一步加工或使用。
以上是不锈钢线材的生产工艺。
这些工艺保证了不锈钢线材的质量和性能,使其能够广泛应用于建筑、机械、船舶等领域。
连铸工艺设备03连铸坯凝固与传热

29
可见,最大的热阻是来自于坯壳与结晶器 壁之间的气隙。气隙热阻占总热阻84%以 上。因此坯壳的生长决定于气隙形成动力 学,而气隙的大小是决定于坯壳的收缩和 坯壳抵抗钢水鼓胀的能力。结晶器断面气 隙的形成是不均匀的,由于角部是二维传 热,冷却最快收缩最早,产生气隙后向中 心面扩展,结晶器宽面气隙宽度比角部小, 角部坯壳厚度最薄,常常会出现角部裂纹, 甚至造成漏钢。
在液相穴下部液体的流动主要是坯壳的收 缩和晶体下沉所引起的自然对流,或者是 由于铸坯鼓肚所引起的液体流动。
液相穴内液体流动对铸坯结构、夹杂物分 布、溶质元素的偏析和坯壳的生长有重要 作用。
11
四.在连铸机内运行的已凝固坯壳的冷却可看 成是经历“形变热处理”过程
1.从受力的方面看,铸坯承受热应力和机械应 力的作用,使坯壳发生不同程度的变形;
阻,热流下降,导致铜壁温度升高,加速 了水的沸腾。所以,结晶器必须使用软水。 要求其总盐含量≯400mg∕l,硫酸盐≯150 mg∕l,氯化物≯50mg∕l,硅酸盐 ≯40mg∕l,悬浮质点<50mg∕l,质点尺 寸≯0.2mm,碳酸盐硬度≯1~2°Dh, pH 值为7~8。
37
C.结晶器润滑的影响 结晶器润滑可以减小拉坯阻力,并可由于
下过程: ⑴钢水向坯壳的对流传热; ⑵凝固坯壳中的传导传热; ⑶凝固坯壳与结晶器壁传热; ⑷结晶器壁传导传热; ⑸冷却水与结晶器壁的强制对流传热,热量
被通过水缝中高速度流动的冷却水带走。
27
结晶器内钢水热量传给冷却水的总热阻可表示为:
式中
11em1eCu1
h h1 m h0 Cu hW
h—总的传热系数;
一.结晶器内坯壳的形成 1.坯壳表面与铜壁之间的接触状况 ⑴钢液弯月面区; ⑵坯壳与铜壁紧密接触区; ⑶坯壳收缩与铜壁脱开产生的气隙区。
不锈钢热轧和连铸钢坯

不锈钢热轧和连铸钢坯不锈钢是一种耐腐蚀、无磁性的合金材料,广泛应用于许多领域,如建筑、制造业和化工等。
而不锈钢的生产过程中,热轧和连铸钢坯是两种常见的生产工艺。
本文将分别介绍不锈钢热轧和连铸钢坯的特点和应用。
一、不锈钢热轧不锈钢热轧是通过将不锈钢坯料加热至适当温度后,在热轧机上进行轧制,最终得到所需的板材、带材或型材。
热轧工艺可以提高不锈钢的塑性和韧性,使其具有更好的机械性能和表面质量。
热轧工艺的主要特点是温度高、变形大、生产效率高。
在热轧过程中,不锈钢坯料经过预热后,通过多道次的轧制和拉伸,逐渐形成所需的板材或型材。
由于高温下不锈钢的塑性较好,因此可以获得较大的变形,使得板材或型材的尺寸精度和表面质量得到较好的控制。
不锈钢热轧产品广泛应用于建筑、船舶、化工等领域。
例如,不锈钢板材可以用于制作厨具、餐具和装饰材料,不锈钢型材则常用于制造建筑结构和机械零件。
不锈钢热轧产品具有良好的耐腐蚀性能和强度,能够满足各种特殊环境下的使用需求。
二、连铸钢坯连铸是一种将液态金属直接连续铸造成坯料的工艺。
连铸钢坯是通过将熔融的钢液倒入连铸机中,经过冷却和凝固后形成的长方形坯料。
连铸工艺具有高效、节能的特点,可以大量生产高质量的钢坯。
连铸钢坯的主要特点是坯料形状规整、组织均匀、表面质量好。
由于连铸工艺中钢液经过冷却和凝固后直接形成坯料,因此可以获得较好的尺寸精度和表面平整度。
同时,连铸工艺还能够控制钢坯的组织和化学成分,使得钢坯具有良好的力学性能和可加工性。
连铸钢坯广泛应用于钢铁工业,是制造钢材的重要工艺环节。
通过连铸工艺可以生产各种规格和材质的钢坯,用于制造建筑结构、机械零件和汽车零部件等。
连铸钢坯具有高强度和良好的可塑性,能够满足不同领域的使用需求。
不锈钢热轧和连铸钢坯是不锈钢生产中常见的工艺。
不锈钢热轧通过高温轧制,可以获得尺寸精度高、表面质量好的产品;连铸钢坯通过连续铸造,可以大量生产高质量的钢坯。
这两种工艺都具有广泛的应用领域,能够满足不同行业对不锈钢产品的需求。
不锈钢方圆坯连铸工艺开发
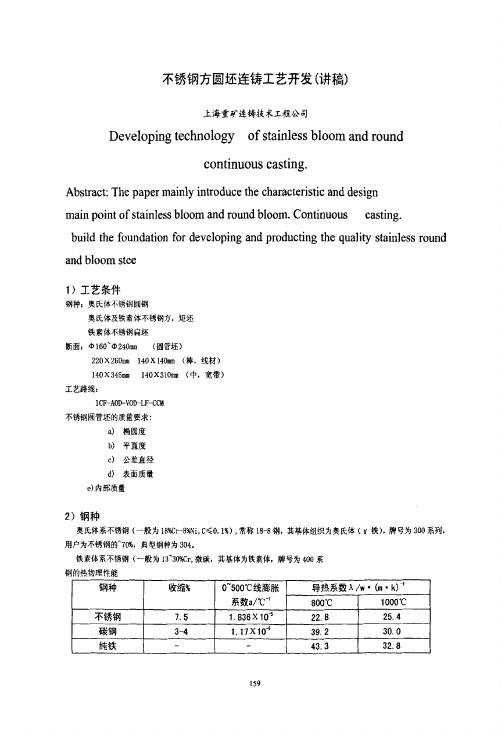
4.)结晶器及铜管的设计
无论是浇铸奥氏体还是铁索体不锈钢我们的目的不在于使热流最大而使其达到最佳,较弱的结晶器冷却可以保证 裂纹及凹陷敏感钢的坯壳非常均匀的生长,他们在凝固时,基本上都经过6一Y的转变,这些钢种的坯壳生长都相当 均匀,在结晶器内其凝固系数在22’25mm・minl 5范围内。
∞
弱
拍幅Βιβλιοθήκη Cu}】:H jⅨ性供【芝控制模以,十作为m,o鍪数雠槲 ?3)
"l十铺“姐W
化学成分 钢种321
断面:220X 260m
C S Cr
Mn B Mo
Si
}P
1i
AI
【Ni
【v
过热度39℃
电流280A
炉号86628 拉速0 65m/m M—E惦
0N
n
流号4 坯号3 频率3Hz
7
4)304不锈钢圜坯
钢种
收缩%
0’500。C线膨胀 系数a/'C叫 1.836X1矿
1.1 7X10{
导热系数^/w・(m・k)一
800℃
22.8 39.2 43.3 1000℃ 25.4 30.0 32.8
不锈钢 碳钢 纯铁
7.5 3—4
159
不锈钢的导热系数比碳钢小,而凝固收缩量比碳素钢大,在二冷区内铸坯的凝固是通过坯壳散热,而坯壳的传热 主要取决于钢的导热系数,不锈钢的凝固速度比较慢,钢的凝固速度与导热系数成正比。 由于钢的导热系数不同,凝固结构也有区别。铁素体不锈钢比奥氏体不锈钢导热系数大20’30%,因而铁素体完全 凝固后形成柱状晶+等轴晶的结构,奥氏体不锈钢的凝固则是贯穿的柱状晶. 高温性能: 1300℃时的抗拉强度
化学成分 钢种:304 断面:o
200 Si Ti ^『 P NI V
太钢2250mm不锈钢热连轧生产线的工艺及设备

1100 Φ700/Φ630 2550
1100 Φ700/Φ630 2550
1100 Φ700/Φ630 2550
支撑辊 辊径 辊身长度
/ mm Φ1600/Φ1440 Φ1600/Φ1440 Φ1600/Φ1440 Φ1600/Φ1440 Φ1600/Φ1440 Φ1600/Φ1440 Φ1600/Φ1440
2 主要工艺及设备
热轧厂由板坯库 、加热炉上料跨 、加热炉 跨 、主轧跨 、钢卷库 、主电室 、磨辊间等组成 , 车间 设 备 总 重 量 33443t , 其 中 , 工 艺 设 备 39908t 。电气设备总功率 155663kW (不含车间 照明及公辅) , 其中主传动电机功率 89000kW 。 211 加热区主要工艺设备
助卷辊
传动功率/ kW 转速/ r·min - 1
3 ×65 AC
1060
传动功率/ kW 1200AC
卷 筒
转速/ r·min - 1
传动比 i
230/ 600
2134/ 5136
公称直径/ mm Φ762
钢卷运输采用运输链和步进梁组合运输方式 , 下运输步进梁直接送往新不锈钢厂冷轧原料库 。
1 概述
太原钢铁 (集团) 有限公司 2250mm 热连轧 项目是太钢新建 150 万 t 不锈钢系统工程的关键 项目 , 并于 2006 年 6 月 30 日轧出第 1 卷钢 。该 项目由 1 条热连轧生产线 、1 条平整生产线和 1 条横切生产线组成 。轧线设计生产规模为 392 万 t/ a , 其 中 碳 钢 19516 万 t/ a , 规 格 为 112 ~ 2514mm ×1000 ~2130mm , 不锈钢 19614 万 t/ a , 规格为 210~2010mm ×1000~2100mm , 最 大卷重 40t 。平整线设计生产规模为 100175 万 t/ a , 其中碳钢 83145 万 t/ a , 不锈钢 17130 万 t/ a 。横切线设计生产规模为 62 万 t/ a , 其中碳钢 32 万 t/ a , 不锈钢 30 万 t/ a 。
《连铸工艺与设备》讲稿1

另外,还可以按铸坯断面形状分为方坯连铸机、圆坯连铸机、板坯连铸机、异形坯连铸机、方/板坯兼用型连铸机等。
按钢水的静压头可分为高头型、低头型和超低头型连铸机等。
3.1立式连铸机
立式连铸机是20世纪50年代至60年代初的主要机型。立式连铸机,从中间罐到切割装置等主要设备均布置在垂直中心线上,整个机身矗立在车间地平面以上。采用立式连铸机
图0-2 1972年以来我国连铸坯产量和连铸比的增长
1-钢总产量;2-连铸比;3-连铸坯产量
3连铸机的机型及其特点
连铸机的分类方式很多。按结晶器是否移动可以分为两类:
1)固定式结晶器:包括固定振动结晶器的各种连铸机,如立式连铸机、立弯式连铸机、弧形连铸机、椭圆形连铸机、水平式连铸机等。这些机型已成为现代化连铸机的基本机型,如图3所示。
进入20世纪60年代,弧形连铸机的问世,使连铸技术出现了一次飞跃。世界第一台弧形连铸机于1964年4月在奥地利百录厂诞生。同年6月由我国自行设计制造的第1台方坯和板坯兼用弧形连铸机在重钢三厂投入生产。此后不久,在前联邦德国又上马了1台宽板弧形连铸机,并开发应用了浸入式水口和保护渣技术。同年英国谢尔顿厂率先实现全连铸生产,共有4台连铸机11流,主要生产低合金钢和低碳钢,浇注断面为140mm×140mm和432mm×632mm的铸坯。也开发应用了浸入式水口和保护渣技术。1967年由美钢联工程咨询公司设计并在格里厂投产1台采用直结晶器、带液心弯曲的弧形连铸机。同一年在胡金根厂相继投产了2台超低头板坯连铸机,浇注断面为(150~250)mm×(1800~2500)mm的铸坯,该铸机至今仍在运行。
不锈钢生产技术工艺流程
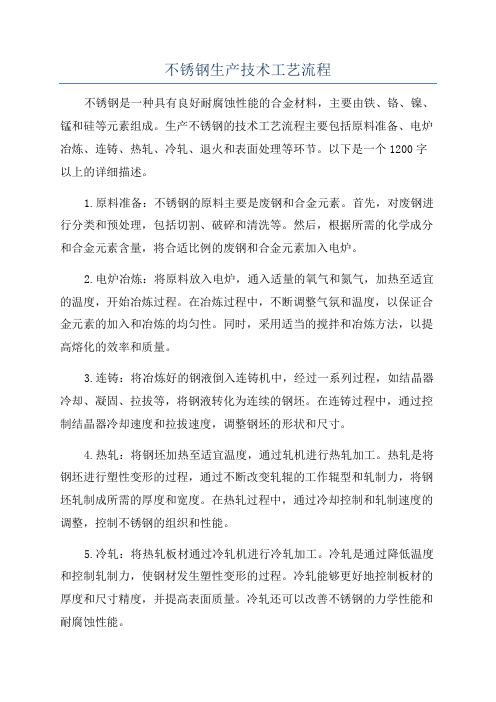
不锈钢生产技术工艺流程不锈钢是一种具有良好耐腐蚀性能的合金材料,主要由铁、铬、镍、锰和硅等元素组成。
生产不锈钢的技术工艺流程主要包括原料准备、电炉冶炼、连铸、热轧、冷轧、退火和表面处理等环节。
以下是一个1200字以上的详细描述。
1.原料准备:不锈钢的原料主要是废钢和合金元素。
首先,对废钢进行分类和预处理,包括切割、破碎和清洗等。
然后,根据所需的化学成分和合金元素含量,将合适比例的废钢和合金元素加入电炉。
2.电炉冶炼:将原料放入电炉,通入适量的氧气和氮气,加热至适宜的温度,开始冶炼过程。
在冶炼过程中,不断调整气氛和温度,以保证合金元素的加入和冶炼的均匀性。
同时,采用适当的搅拌和冶炼方法,以提高熔化的效率和质量。
3.连铸:将冶炼好的钢液倒入连铸机中,经过一系列过程,如结晶器冷却、凝固、拉拔等,将钢液转化为连续的钢坯。
在连铸过程中,通过控制结晶器冷却速度和拉拔速度,调整钢坯的形状和尺寸。
4.热轧:将钢坯加热至适宜温度,通过轧机进行热轧加工。
热轧是将钢坯进行塑性变形的过程,通过不断改变轧辊的工作辊型和轧制力,将钢坯轧制成所需的厚度和宽度。
在热轧过程中,通过冷却控制和轧制速度的调整,控制不锈钢的组织和性能。
5.冷轧:将热轧板材通过冷轧机进行冷轧加工。
冷轧是通过降低温度和控制轧制力,使钢材发生塑性变形的过程。
冷轧能够更好地控制板材的厚度和尺寸精度,并提高表面质量。
冷轧还可以改善不锈钢的力学性能和耐腐蚀性能。
6.退火:对冷轧板材进行退火处理。
退火是通过控制温度和保持时间,将冷轧的板材恢复到较软的状态。
退火可以消除冷轧过程中的应力,提高不锈钢的延展性和塑性,并改善不锈钢的晶粒结构和力学性能。
7.表面处理:最后一道工序是对不锈钢板材进行表面处理。
表面处理能够提高不锈钢的表面光洁度和耐腐蚀性,常见的表面处理方法包括酸洗、电镀、喷涂等。
酸洗是将不锈钢板材浸泡在酸性溶液中,去除不锈钢表面的氧化层和污染物。
电镀是将不锈钢板材放入电镀槽中,通过电解作用在表面镀上一层金属或合金。
不锈钢带的生产(很详细的)
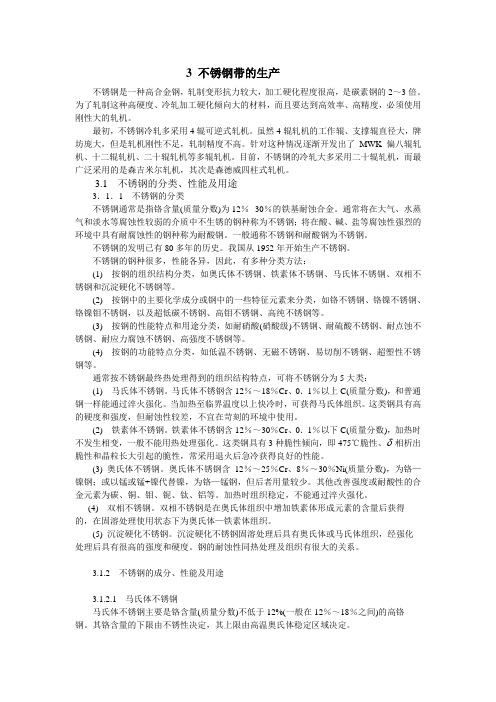
3 不锈钢带的生产不锈钢是一种高合金钢,轧制变形抗力较大,加工硬化程度很高,是碳素钢的2~3倍。
为了轧制这种高硬度、冷轧加工硬化倾向大的材料,而且要达到高效率、高精度,必须使用刚性大的轧机。
最初,不锈钢冷轧多采用4辊可逆式轧机。
虽然4辊轧机的工作辊、支撑辊直径大,牌坊庞大,但是轧机刚性不足,轧制精度不高。
针对这种情况逐渐开发出了MWK偏八辊轧机、十二辊轧机、二十辊轧机等多辊轧机。
目前,不锈钢的冷轧大多采用二十辊轧机,而最广泛采用的是森吉米尔轧机,其次是森德威四柱式轧机。
3.1 不锈钢的分类、性能及用途3.1.1 不锈钢的分类不锈钢通常是指铬含量(质量分数)为12%--30%的铁基耐蚀合金。
通常将在大气、水蒸气和淡水等腐蚀性较弱的介质中不生锈的钢种称为不锈钢;将在酸、碱、盐等腐蚀性强烈的环境中具有耐腐蚀性的钢种称为耐酸钢。
一般通称不锈钢和耐酸钢为不锈钢。
不锈钢的发明已有80多年的历史。
我国从1952年开始生产不锈钢。
不锈钢的钢种很多,性能各异,因此,有多种分类方法:(1) 按钢的组织结构分类,如奥氏体不锈钢、铁素体不锈钢、马氏体不锈钢、双相不锈钢和沉淀硬化不锈钢等。
(2) 按钢中的主要化学成分或钢中的一些特征元素来分类,如铬不锈钢、铬镍不锈钢、铬镍钼不锈钢,以及超低碳不锈钢、高钼不锈钢、高纯不锈钢等。
(3) 按钢的性能特点和用途分类,如耐硝酸(硝酸级)不锈钢、耐硫酸不锈钢、耐点蚀不锈钢、耐应力腐蚀不锈钢、高强度不锈钢等。
(4) 按钢的功能特点分类,如低温不锈钢、无磁不锈钢、易切削不锈钢、超塑性不锈钢等。
通常按不锈钢最终热处理得到的组织结构特点,可将不锈钢分为5大类:(1) 马氏体不锈钢。
马氏体不锈钢含12%~18%Cr、0.1%以上C(质量分数),和普通钢一样能通过淬火强化。
当加热至临界温度以上快冷时,可获得马氏体组织。
这类钢具有高的硬度和强度,但耐蚀性较差,不宜在苛刻的环境中使用。
(2) 铁素体不锈钢。
精炼-连铸主要设备介绍

主要设备构成:LF炉主要由钢包炉体、钢 LF炉主要由钢包炉体、钢
包车(分单工位和双工位)电极加热 系统、吹氩搅拌系统、合金加料系统以 及测温取样系统、高压室、操作室、液 压站(实现电极、炉盖的升降)等部分 组成。
LF炉主要冶金功能及精炼手段 LF炉主要冶金功能及精炼手段 LF炉具有的主要冶金功能有: LF炉具有的主要冶金功能有 炉具有的主要冶金功能有: 钢水升温、 钢水升温、调温及保温功能 强化脱氧、脱硫功能 强化脱氧、 合金微调功能 采用的精炼手段有: 采用的精炼手段有: 吹氩搅拌 埋弧加热 造强还原气氛 造碱性合成渣
三、各种精炼设备介绍: (一)吹氩:分为底吹、顶吹两种方式。
(二)喷粉及喂丝
合金的喂入与喷粉工艺示意图
(三)LF炉 (三)LF炉 钢包处理型处理钢水过程中,因钢水的温降而使 渣及合金成分的调整以及处理时间等都受到限制。 如果用提高初炼炉出钢温度的办法保证渣熔化及 足够的精炼时间,势必加重初炼炉的负担,降低 炉衬寿命,命中率也比较低,不具备工业性连续 生产的条件。 1971年,日本特殊钢公司开发的Ladle Furnace, 1971年,日本特殊钢公司开发的Ladle Furnace, 简称“LF” 简称“LF”、“LF炉”、“LF钢包炉”、“LF钢 LF炉 LF钢包炉” LF钢 包精炼炉” 包精炼炉”、 “钢包炉”、“钢包精炼炉”等。 钢包炉” 钢包精炼炉” 该炉采用碱性合成渣,埋弧加热,吹氩搅拌,在 还原气氛下精炼,钢包炉的原理图见图
6、中间罐预热站及水口烘烤 功能及结构: 中间罐预热站,用浇注平台上,对砌筑好内衬并 经烘烤干燥的中间罐进一步加热升温,使其在大 约90min左右升温至~1100摄氏度。有利于浇注 90min左右升温至~1100摄氏度。有利于浇注 时减少钢水温度损失和提高铸坯质量。 中间罐预热站由支架、电动推杆、助燃风机、蝶 阀、燃气管及烧嘴等主要部件组成。 浸入式水口预热装置放在浇注平台上,每个人中 间罐预热位中间罐底部,采用中间罐预热废气预 热。
不锈钢生产工艺简述
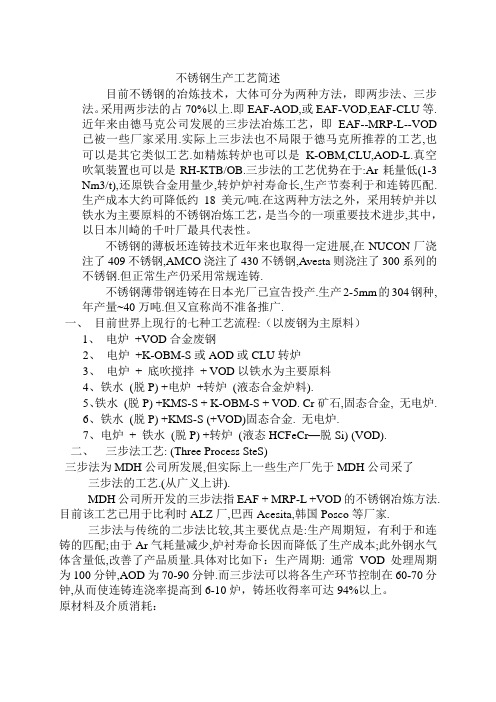
不锈钢生产工艺简述目前不锈钢的冶炼技术,大体可分为两种方法,即两步法、三步法。
采用两步法的占70%以上.即EAF-AOD,或EAF-VOD,EAF-CLU等.近年来由德马克公司发展的三步法冶炼工艺,即EAF--MRP-L--VOD 已被一些厂家采用.实际上三步法也不局限于德马克所推荐的工艺,也可以是其它类似工艺.如精炼转炉也可以是K-OBM,CLU,AOD-L.真空吹氧装置也可以是RH-KTB/OB.三步法的工艺优势在于:Ar耗量低(1-3 Nm3/t),还原铁合金用量少,转炉炉衬寿命长,生产节奏利于和连铸匹配.生产成本大约可降低约18美元/吨.在这两种方法之外,采用转炉并以铁水为主要原料的不锈钢冶炼工艺,是当今的一项重要技术进步,其中,以日本川崎的千叶厂最具代表性。
不锈钢的薄板坯连铸技术近年来也取得一定进展,在NUCON厂浇注了409不锈钢,AMCO浇注了430不锈钢,Avesta则浇注了300系列的不锈钢.但正常生产仍采用常规连铸.不锈钢薄带钢连铸在日本光厂已宣告投产.生产2-5mm的304钢种,年产量~40万吨.但又宣称尚不准备推广.一、目前世界上现行的七种工艺流程:(以废钢为主原料)1、电炉+VOD合金废钢2、电炉+K-OBM-S或AOD或CLU转炉3、电炉+ 底吹搅拌+ VOD以铁水为主要原料4、铁水(脱P) +电炉+转炉(液态合金炉料).5、铁水(脱P) +KMS-S + K-OBM-S + VOD. Cr矿石,固态合金, 无电炉.6、铁水(脱P) +KMS-S (+VOD)固态合金. 无电炉.7、电炉+ 铁水(脱P) +转炉(液态HCFeCr—脱Si) (VOD).二、三步法工艺: (Three Process SteS)三步法为MDH公司所发展,但实际上一些生产厂先于MDH公司采了三步法的工艺.(从广义上讲).MDH公司所开发的三步法指EAF + MRP-L +VOD的不锈钢冶炼方法.目前该工艺已用于比利时ALZ厂,巴西Acesita,韩国Posco等厂家.三步法与传统的二步法比较,其主要优点是:生产周期短,有利于和连铸的匹配;由于Ar气耗量减少,炉衬寿命长因而降低了生产成本;此外钢水气体含量低,改善了产品质量.具体对比如下:生产周期: 通常VOD处理周期为100分钟,AOD为70-90分钟.而三步法可以将各生产环节控制在60-70分钟,从而使连铸连浇率提高到6-10炉,铸坯收得率可达94%以上。
连铸工艺、设备--09连铸坯质量控制
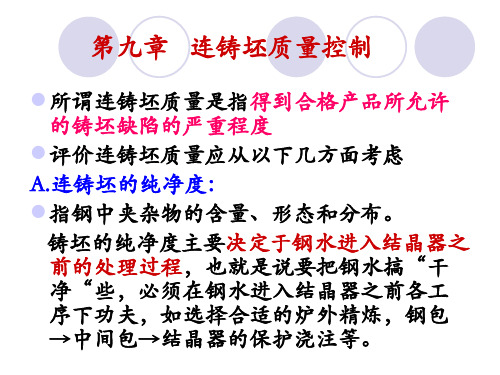
液相穴内夹杂物上浮示意图: a—带垂直段立弯式连铸机; b—弧形连铸机
B.连铸操作对铸坯中夹杂物的影响
连铸操作有正常浇注和非正常浇注两种情况。
在正常浇注下,浇注过程比较稳定,铸坯中 夹杂物多少主要由钢液的纯净度决定。
B.连铸坯的表面质量:
指连铸坯表面是否存在裂纹、夹渣及皮下 气泡等缺陷。
连铸坯的表面缺陷主要决定于钢水在结晶 器的凝固过程。它是与结晶器内坯壳的形 成、结晶器振动、保护渣性能、浸入式水 口设计及钢液面稳定性等因素有关的,必 须严格控制影响表面质量的各参数在合理 的目标值以内,以生产无缺陷的铸坯,这 是热送和直接轧制的前提。
2.钢包精炼。
根据钢种的需要选择合适的精炼处理方法,以均 匀温度、微调成分、降低氧含量、去除气体夹杂 物、改善夹杂物形态等。
3.无氧化浇注技术。
从钢包→中间包用长水口,中间包→结晶器用浸 入式水口(板坯、大方坯)或气体保护(小方 坯),中间包采用覆盖剂,结晶器用保护渣。
4.充分发挥中间包冶金净化器的作用。
C.在操作中,注温和拉速对铸坯中夹杂物也有 一定影响
当钢液温度降低时,夹杂物指数升高;随着 拉速的提高,铸坯中夹杂物有增多的趋势。
D.耐火材料质量对铸坯夹杂物的影响
注连铸过程中由于钢液和耐火材料接触, 钢液中的元素(锰和铝等)会与耐火材料中 的氧化物发生作用生成夹杂物,当其不能上 浮时就遗留在铸坯中。
2.连铸坯中夹杂物的类型和来源
类型:取决于浇注钢种和脱氧方法。在连铸 坯中较常见的夹杂物有Al2O3和以SiO2为主并 含有MnO和CaO的硅酸盐,以及以Al2O3为主 并含有SiO2、CaO 和CaS等的铝酸盐。此外还 有硫化物如FeS、MnS等。
连铸连轧工艺流程
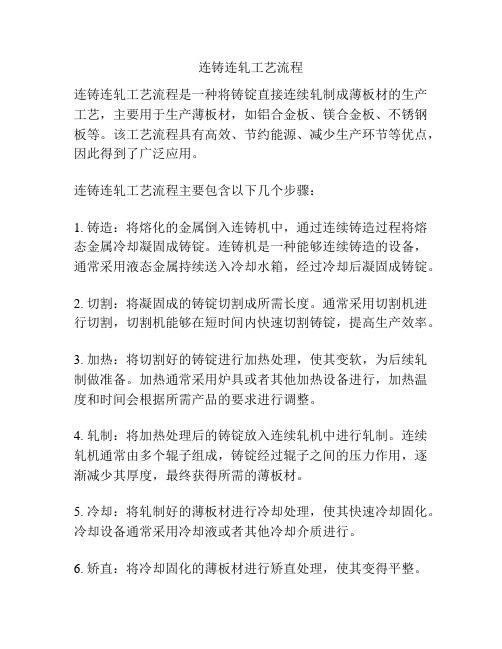
连铸连轧工艺流程连铸连轧工艺流程是一种将铸锭直接连续轧制成薄板材的生产工艺,主要用于生产薄板材,如铝合金板、镁合金板、不锈钢板等。
该工艺流程具有高效、节约能源、减少生产环节等优点,因此得到了广泛应用。
连铸连轧工艺流程主要包含以下几个步骤:1. 铸造:将熔化的金属倒入连铸机中,通过连续铸造过程将熔态金属冷却凝固成铸锭。
连铸机是一种能够连续铸造的设备,通常采用液态金属持续送入冷却水箱,经过冷却后凝固成铸锭。
2. 切割:将凝固成的铸锭切割成所需长度。
通常采用切割机进行切割,切割机能够在短时间内快速切割铸锭,提高生产效率。
3. 加热:将切割好的铸锭进行加热处理,使其变软,为后续轧制做准备。
加热通常采用炉具或者其他加热设备进行,加热温度和时间会根据所需产品的要求进行调整。
4. 轧制:将加热处理后的铸锭放入连续轧机中进行轧制。
连续轧机通常由多个辊子组成,铸锭经过辊子之间的压力作用,逐渐减少其厚度,最终获得所需的薄板材。
5. 冷却:将轧制好的薄板材进行冷却处理,使其快速冷却固化。
冷却设备通常采用冷却液或者其他冷却介质进行。
6. 矫直:将冷却固化的薄板材进行矫直处理,使其变得平整。
矫直设备通常采用滚轴或者其他矫直装置进行。
7. 切割:将矫直好的薄板材进行切割,使其达到所需长度和宽度。
切割设备通常采用切割机进行。
8. 检测:对切割好的薄板材进行质量检测,确保产品达到标准要求。
质量检测通常包括厚度、宽度、表面质量等方面的检查。
9. 包装:将符合要求的产品进行包装,以便进行运输和销售。
常用的包装方式有木箱、塑料袋等。
通过以上步骤,连铸连轧工艺流程能够将原材料快速转化为薄板材,具有生产效率高、产品质量好的特点。
同时,连铸连轧工艺流程还能减少生产环节和能源消耗,有利于环境保护和节能减排。
因此,连铸连轧工艺流程在金属制造和加工行业得到广泛应用。
连铸工艺、设备--01连铸设备及主要工艺参数

连铸坯形状和尺寸: 小方坯: 70mm × 70mm ~200mm × 200mm 大方坯: 200mm ×200mm ~450mm × 450mm 矩形坯: 150mm × 100mm ~400mm × 630mm 板坯: 150mm × 600mm ~300mm × 2640mm 圆坯: Ф80 ~450mm
AA' A' C ' 0.5D 100 % 100 % 100 % CC ' OC R 0.5D
由于R>>D,故上式可近似写成:
ε=
0 .5 D ×100% R
ε ≤„ε‟ 则: R≥ 0.5 D (m) [ ]
式中 „ε‟:允许延伸率,它主要取决于浇铸钢种、铸 坯温度以及对铸坯表面质量的要求等。对普碳钢和 低合金钢 „ε‟=1.5 ~2.0%
×Vmax )-
2 h ] ∕π
②按铸坯矫直时允许最大延伸率计算铸机半径 原则: 矫直时内弧表面延伸率必须小于允许延伸率 值。 铸坯矫直时,内弧受拉,外弧受压,中心线 未发生变化,断面仍为平面,取C—C’段铸 坯,
铸坯矫直前后的延伸示意图: a—矫直前 b—矫直后
设外弧半径为R,铸坯厚度为D, 则内弧表面延伸率ε:
连铸机的实际作业时间=钢包开浇起至切割 完毕的时间+浇铸准备时间+正常开浇等待 的时间
五.金属收得率 η1=W1∕G1×100% η2 =W2∕W1×100% η = η1η2 = W2∕G1×100% η1—钢水收得率,%; W1—浇铸所得到的全部铸坯量,t; G1—钢水重量,t; η2— 铸坯合格率,% W2— 合格铸坯量,t; η— 金属收得率,%。
L 2
不锈钢管的生产工艺流程
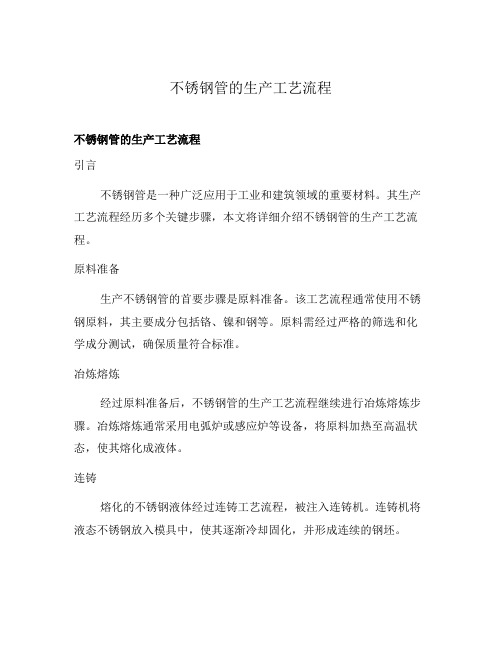
不锈钢管的生产工艺流程不锈钢管的生产工艺流程引言不锈钢管是一种广泛应用于工业和建筑领域的重要材料。
其生产工艺流程经历多个关键步骤,本文将详细介绍不锈钢管的生产工艺流程。
原料准备生产不锈钢管的首要步骤是原料准备。
该工艺流程通常使用不锈钢原料,其主要成分包括铬、镍和钢等。
原料需经过严格的筛选和化学成分测试,确保质量符合标准。
冶炼熔炼经过原料准备后,不锈钢管的生产工艺流程继续进行冶炼熔炼步骤。
冶炼熔炼通常采用电弧炉或感应炉等设备,将原料加热至高温状态,使其熔化成液体。
连铸熔化的不锈钢液体经过连铸工艺流程,被注入连铸机。
连铸机将液态不锈钢放入模具中,使其逐渐冷却固化,并形成连续的钢坯。
经过连铸工艺流程后,连续的钢坯经过预热后进入轧机。
热轧是将钢坯通过连续轧制工艺流程,逐渐减小截面尺寸,形成不锈钢管的重要步骤。
轧辊加工热轧后的不锈钢管需要经过轧辊加工。
该工艺流程使用专业的轧辊设备将热轧后的钢管进行再次轧制和加工,以获得所需的精度和光洁度。
温度控制在整个生产工艺流程中,温度控制是至关重要的环节。
通过合理控制温度,不锈钢管的物理和化学特性得以保持和调节。
酸洗处理为了去除不锈钢表面的氧化物和其他杂质,生产工艺流程中进行酸洗处理。
酸洗处理可使用稀硝酸或稀硫酸等化学溶液,使不锈钢管表面清洁并达到一定的光洁度。
非破坏检测不锈钢管的生产工艺流程中,非破坏检测是必要的环节。
通过采用超声波、X射线等技术,对不锈钢管进行检测,确保其内部和外部质量符合标准。
经过上述步骤的不锈钢管需进行精加工,以获得更高的精度和质量。
精加工包括冷拔、冷轧、锻压等工艺流程,最终得到符合要求的不锈钢管产品。
检验和包装生产工艺流程的最后阶段是对不锈钢管进行检验和包装。
通过对每个批次的不锈钢管进行抽样检测,确保产品质量合格。
随后,对不锈钢管进行包装和标记,以便运输和存储。
结论通过以上的工艺流程,不锈钢管得以生产出高质量、合规格的产品,为工业和建筑等领域提供了重要的材料基础。
转炉及精炼连铸实用工艺流程及排污节点
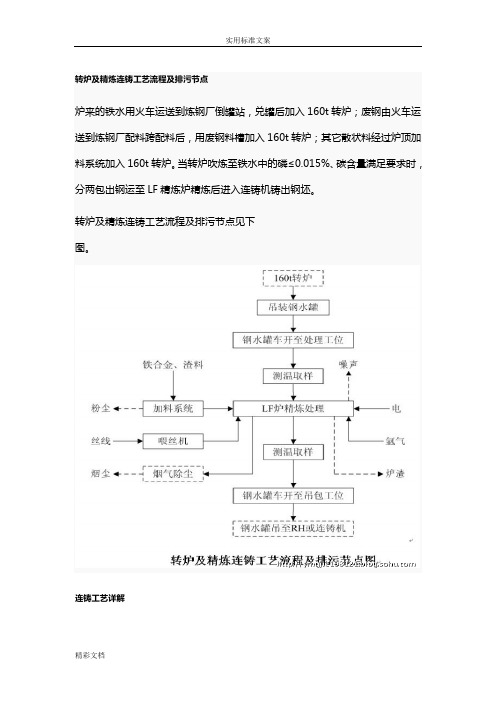
转炉及精炼连铸工艺流程及排污节点炉来的铁水用火车运送到炼钢厂倒罐站,兑罐后加入160t转炉;废钢由火车运送到炼钢厂配料跨配料后,用废钢料槽加入160t转炉;其它散状料经过炉顶加料系统加入160t转炉。
当转炉吹炼至铁水中的磷≤0.015%、碳含量满足要求时,分两包出钢运至LF精炼炉精炼后进入连铸机铸出钢坯。
转炉及精炼连铸工艺流程及排污节点见下图。
连铸工艺详解连铸的生产工艺流程:将装有精炼好钢水的钢包运至回转台,回转台转动到浇注位置后,将钢水注入中间包,中间包再由水口将钢水分配到各个结晶器中去。
结晶器是连铸机的核心设备之一,它使铸件成形并迅速凝固结晶。
拉矫机与结晶振动装置共同作用,将结晶器内的铸件拉出,经冷却、电磁搅拌后,切割成一定长度的板坯。
连铸钢水的准备一、连铸钢水的温度要求:钢水温度过高的危害:①出结晶器坯壳薄,容易漏钢;②耐火材料侵蚀加快,易导致铸流失控,降低浇铸安全性;③增加非金属夹杂,影响板坯内在质量;④铸坯柱状晶发达;⑤中心偏析加重,易产生中心线裂纹。
钢水温度过低的危害:①容易发生水口堵塞,浇铸中断;②连铸表面容易产生结疱、夹渣、裂纹等缺陷;③非金属夹杂不易上浮,影响铸坯内在质量。
二、钢水在钢包中的温度控制:根据冶炼钢种严格控制出钢温度,使其在较窄的范围内变化;其次,要最大限度地减少从出钢、钢包中、钢包运送途中及进入中间包的整个过程中的温降。
实际生产中需采取在钢包内调整钢水温度的措施:1)钢包吹氩调温2)加废钢调温3)在钢包中加热钢水技术4)钢水包的保温中间包钢水温度的控制一、浇铸温度的确定浇铸温度是指中间包内的钢水温度,通常一炉钢水需在中间包内测温3次,即开浇后5mi n、浇铸中期和浇铸结束前5min,而这3次温度的平均值被视为平均浇铸温度。
浇铸温度的确定可由下式表示(也称目标浇铸温度):T=TL+△T 。
二、液相线温度:即开始凝固的温度,就是确定浇铸温度的基础。
推荐一个计算公式:T=1536-{78[%C]+7.6[%Si]+4.9[%Mn]+34[%P]+30[%S]+5.0[%Cu]+3.1[%Ni]+1.3[% Cr]+3.6[%Al]+2.0[%Mo]+2.0[%V]+18[%Ti]}三、钢水过热度的确定钢水过热度主要是根据铸坯的质量要求和浇铸性能来确定。
不锈钢生产技术工艺流程
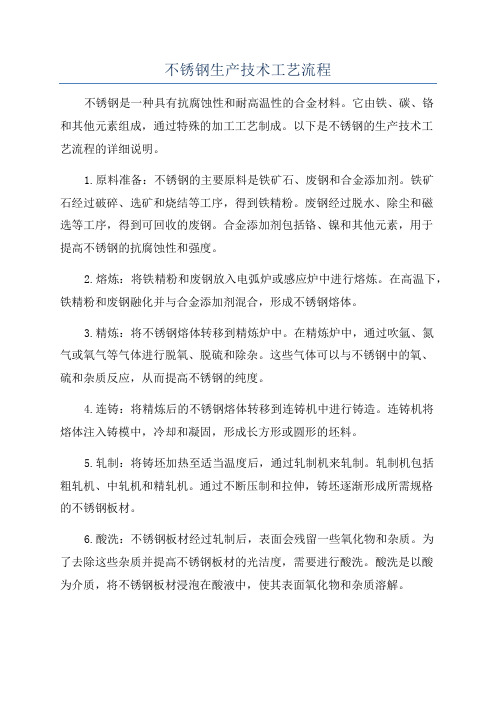
不锈钢生产技术工艺流程不锈钢是一种具有抗腐蚀性和耐高温性的合金材料。
它由铁、碳、铬和其他元素组成,通过特殊的加工工艺制成。
以下是不锈钢的生产技术工艺流程的详细说明。
1.原料准备:不锈钢的主要原料是铁矿石、废钢和合金添加剂。
铁矿石经过破碎、选矿和烧结等工序,得到铁精粉。
废钢经过脱水、除尘和磁选等工序,得到可回收的废钢。
合金添加剂包括铬、镍和其他元素,用于提高不锈钢的抗腐蚀性和强度。
2.熔炼:将铁精粉和废钢放入电弧炉或感应炉中进行熔炼。
在高温下,铁精粉和废钢融化并与合金添加剂混合,形成不锈钢熔体。
3.精炼:将不锈钢熔体转移到精炼炉中。
在精炼炉中,通过吹氩、氮气或氧气等气体进行脱氧、脱硫和除杂。
这些气体可以与不锈钢中的氧、硫和杂质反应,从而提高不锈钢的纯度。
4.连铸:将精炼后的不锈钢熔体转移到连铸机中进行铸造。
连铸机将熔体注入铸模中,冷却和凝固,形成长方形或圆形的坯料。
5.轧制:将铸坯加热至适当温度后,通过轧制机来轧制。
轧制机包括粗轧机、中轧机和精轧机。
通过不断压制和拉伸,铸坯逐渐形成所需规格的不锈钢板材。
6.酸洗:不锈钢板材经过轧制后,表面会残留一些氧化物和杂质。
为了去除这些杂质并提高不锈钢板材的光洁度,需要进行酸洗。
酸洗是以酸为介质,将不锈钢板材浸泡在酸液中,使其表面氧化物和杂质溶解。
7.镀锌:不锈钢板材经过酸洗后,为了提高其耐腐蚀性和耐磨性,可以进行镀锌处理。
镀锌是将不锈钢板材浸泡在含锌溶液中,与锌发生反应形成锌层。
8.表面处理:不锈钢板材经过酸洗和镀锌后,还可以进行一些表面处理,如抛光、刻蚀和喷砂等。
这些处理可以改善不锈钢表面的光洁度和美观度。
9.检测和质量控制:在生产过程中,对不锈钢的各个环节进行严格的检测和质量控制,以确保产品的合格性。
常用的检测方法包括拉伸试验、硬度测试和冲击试验等。
10.包装和运输:经过检测和质量控制后,合格的不锈钢产品将进行包装和运输。
通常采用木箱、钢板和膜包装,以保护产品的完整性。
- 1、下载文档前请自行甄别文档内容的完整性,平台不提供额外的编辑、内容补充、找答案等附加服务。
- 2、"仅部分预览"的文档,不可在线预览部分如存在完整性等问题,可反馈申请退款(可完整预览的文档不适用该条件!)。
- 3、如文档侵犯您的权益,请联系客服反馈,我们会尽快为您处理(人工客服工作时间:9:00-18:30)。
不锈钢连铸生产工艺与设备
不锈钢分公司共建有四台板坯连铸机,其中两台为不锈钢板坯连铸机,两台为碳钢板坯连铸机。
所浇铸的钢水全部来自炼钢厂,生产的合格板坯主要供应1780热轧厂。
5.1 生产规模与连铸坯规格
不锈钢板坯生产规模: 144万t/a
不锈钢连铸坯规格:
厚度: 180、200mm(标准坯)
宽度: 750~1600 mm
定尺长度: 8000~13600mm
短尺长度: 4800~6500mm(热轧能接受的非定尺长度)最大坯重: 30t
5.2 不锈钢连铸板坯的生产工艺
不锈钢连铸板坯的生产工艺流程见图5-1。
电炉
氩氧精炼炉
VOD炼钢3#不锈钢连铸
机
连铸铸坯切割
去毛刺
缓冷喷号机空冷
离线辊道检查堆放横移小车过跨车人工清理上线辊道堆放
铸坯称量连铸
入库热轧1780mm热轧修磨机
图5-1 不锈钢板坯连铸生产工艺流程
不锈钢板坯连铸生产工艺流程简述:
经过精炼的温度、成分均已合格的不锈钢钢水送至钢水接受跨,280/80/20t起重机将盛满钢水的钢包放置到钢包回转台上,连接好钢包滑动水口液压缸和钢包下渣检测装置接线,测量钢水温度后,钢包加盖,钢包回转台旋转180°,把钢包运送到处于浇注位置的中间包小车的上方。
钢包下降
至浇注位置,并由长水口夹持装置接上保护套管。
浇注平台上有两辆中间包小车,每辆小车上有一只中间包以实现快速更换。
每辆小车都装有提升和称重装置,每辆小车都可以在浇注位和各自的停车位间往返移动。
每个中间包小车停车位都有一个中间包预热站和一个浸入式水口预热站。
从钢包到中间包的钢流由装在钢包底部的滑动水口控制,钢包底部装有下渣检测装置。
开启钢包滑动水口后,钢水经过钢包到中间包之间的保护套管流入中间包,待中间包内钢水液面上升至一定高度后,投入覆盖渣。
中间包钢流控制系统采用整体内装式浸入式水口和塞棒控制机构,并带有事故切断闸板。
当自动开浇系统启动后,中间包塞棒自动打开,钢水通过浸入式水口流入结晶器。
结晶器内的钢水上升到一定高度后,人工加入保护渣。
在自动开浇系统的作用下,结晶器振动装置和拉坯辊自动启动,在结晶器内已形成坯壳的铸坯在引锭杆的带动下缓缓拉
出结晶器和足辊段,进入铸坯导向段。
结晶器液面自动控制装置不断调节中间包塞棒的开度,使结晶器内的钢液面保持稳定的高度。
结晶器内装有漏钢预报装置,一旦发生坯壳与结晶器铜板的粘连,该装置发出报警信号,人工判断后,手动或自动降低铸机拉速,防止拉漏。
铸坯二冷导向段由直线段、弯曲度、弧形段、矫直段以及水平段等不同的扇形段组成,铸坯在二冷导向段中经过气雾喷淋冷却,坯壳不断加厚直至全凝固。
为使铸坯得到合适的冷却,在扇形段辊子间装有气雾喷嘴,通过二冷动态控制模型的计算和设定,由仪表和阀门系统来控制喷淋冷却的强度,以适应不同钢种和不同拉坯速度的需要。
二冷室为隧道式,其中充满着的二冷水和热铸坯作用产生的大量蒸汽,通过排蒸风机和管道抽出。
所有扇形段辊子都采用分节辊形式,上下框架用四个液压缸连接在一起,必要时可遥控调节铸坯的厚度和锥度。
扇形段可以通过起重机从浇注平台上方吊出更换。
第3个扇形段即第1个弧形段装有铸流电磁搅拌装置
(S-EMS),平时一直通水冷却,当浇铸铁素体不锈钢板坯时,为了消除粗大的柱状晶,增加等轴晶,S-EMS装置通电形成磁场,对板坯液相穴中的钢液进行搅拌。
直线段以下的弯曲段中装有一组小径辊,经过7个弯曲点,将板坯逐渐弯曲到铸机的基本半径。
其后是半径恒定的弧形段,然后铸坯进入半径逐渐增大的矫直段,以保证凝固中的铸坯矫直应力不超过极限值。
经过9个矫直点,铸坯进入到水平段。
在水平段部分应用动态轻压下技术,根据在线模型对铸坯的凝固末端施加一定的压下量,减小铸坯的中心偏析。
开浇前,浇铸平台上的引锭杆小车开到结晶器旁,将引锭杆从上部送入结晶器。
开浇后,引锭杆起牵引铸坯的作用,引锭头前部为爪式结构,可以方便而可靠地脱锭。
引锭杆尾部出了水平扇形段后,由卷扬机系统牵引提升,与拉坯速度同步。
引锭杆与铸坯脱离后被快速提升回到引锭杆小车上,在引锭杆通过浇铸平台的开口处装有保险装置,以确保引锭杆在提升过程中的安全。
铸坯出了最后一个扇形段后,从切前辊道进入装有火焰切割机的切割辊道。
带有铁粉火焰切割机将铸坯切割成预定的长度,铸坯长度由火焰切割机上的长度测量装置测出。
除了正常定尺切割外,火焰切割机还要对铸坯的头部、尾部以及试样进行切割,切割长度优化模型还会对最后一段铸坯进行优化计算,使丢弃的切尾最少。
切成定尺的铸坯经过出坯辊道在去毛刺辊道上由去毛刺机去除两端的毛刺,再由喷号机在铸坯的前端喷上板坯编号。
经过铸坯质量判定模型判定和人工目视检查认定为无缺陷的铸坯通过横移小车、输送辊道和辊道称量直接送到热轧的板坯库。
铸坯质量判定模型判定有缺陷或人工目视检查认定有缺陷需要修磨的铸坯用出坯跨30t板坯夹钳起重机吊运下线到铸坯冷却区堆垛冷却或放入保温坑内缓冷。
冷却到一定温度的铸坯由板坯夹钳起重机送到修磨区进行检查、翻坯,需要修磨的铸坯再吊到修磨机上进行完全修磨或局部修磨。
较小
规模的修磨还可用手持式砂轮机人工修磨。
修磨完毕后经检查已无缺陷的铸坯再用板坯夹钳起重机吊运到输送辊道上经称量送往热轧板坯库。
5.3连铸机主要技术参数
表5-8 板坯连铸机主要技术参数
序号项目单
位
技术参数
1 连铸机机型直弧型
2 基本半径mm 8636
3 弯曲点数7
4 矫直点数9
5 结晶器长度mm 900
6 直线段长度mm 2571
7 机身长度(冶金
长度)
mm 24501
8 台数×流数台/
流
1×1
9 板坯厚度mm 180、200
板坯宽度mm 750~1600 定尺长度m 8~13.6
10 连铸机速度范
围m/mi
n
0.25~2.5
11 连铸机工作拉
速m/mi
n
Max.1.6
12 钢包支承方式钢包回转台
13 中间包钢流控
制
塞棒
14 结晶器调宽在线热调宽
15 结晶器振动装
置共振式板弹簧导向
液压振动
16 切割装置氧气+天然气+铁。