转炉煤气干法(LT)净化回收技术的应用及防爆措施
转炉煤气干法除尘技术

转炉煤气干法除尘技术0引言转炉煤气的除尘技术可以分成干法和湿法两种,其中,干法除尘技术具有降低新水消耗、提高能源回收率,提高能源利用率的作用。
所以,在转炉煤气除尘过程中应用越来越广泛。
在实际应用过程中,由于干法除尘系统设备的技术要求高,过程控制比较复杂,因而会出现一系列的问题。
后来通过对系统的改进,降低了除尘过程中故障的发生,也为系统的改进积累了丰富的经验。
转炉煤气干法除尘技术的顺利应用,对降低能源消耗,提高煤气回收率具有重要意义。
1转炉煤气干法除尘技术概述转炉煤气干法除尘技术中,应用最广泛的是两种方法,分别是鲁齐的LT法和奥钢联的DDS 法。
其中,LT法是由德国的鲁齐和蒂森于20世纪60年代末联合开发的转炉煤气干湿除尘方法。
后来,西门子—奥钢联公司在这个基础上开发了DDS法。
目前,我国国内的公司也开发出了国产干法除尘系统。
转炉煤气干法除尘系统主要包含了煤气冷却系统、除尘系统和回收系统。
在这个过程中,1400T~1600丈的转炉煤气经过活动烟罩、气化冷却烟道回收蒸汽之后,温度降为1000T左右。
然后进人蒸发冷却器进行冷却、粗除尘、增湿调质,最后温度将为150丈~500丈,粉尘浓度由80~150g/m2减小到40~55g/m2。
煤气经过静电除尘器之后,粉尘浓度进一步为10mg/m2。
对于整个系统而言,影响除尘效果的主要有两个器件,分别是蒸发冷却器和静电除尘器。
1.1蒸发冷却器蒸发冷却器顾名思义是利用水蒸气的蒸发冷却原理来工作的。
和湿法除尘技术相比,这种冷却方式极大地降低了冷却所需要的水量,达到节约水的目的。
目前,应用最为广泛的是双流体外混式喷枪,冷却水从喷嘴中心孔喷出,被加热的蒸汽从中心孔的环形间隙喷出,而且在喷嘴口处形成雾化水。
其喷水量是由计算机根据蒸发冷却器的进出口温度流量来控制的,同时,蒸汽可以用氮气来代替,从而达到节水的目的。
1.2静电除尘器静电除尘器是转炉煤气干法除尘系统的核心,它是防止爆炸和控制出口烟气浓度的关键设施。
转炉煤气干法LT净化回收技术的应用及防爆措施

转炉煤气干法LT净化回收技术的应用及防爆措施概述炼钢厂在生产过程中会产生大量的转炉煤气,其中含有大量的有害物质,如一氧化碳、二氧化碳等,对环境造成威胁。
为了减少煤气对环境的影响,炼钢厂引入了转炉煤气干法LT净化回收技术。
技术原理转炉煤气干法LT净化回收技术是一种先将煤气进行除尘、水分脱除等处理后,采用催化剂进行低温净化,在净化完成后再进行回收利用的技术。
该技术的主要原理是:将煤气进行过滤处理,去除其中的杂质和水分,再通过特制的催化剂进行净化处理,使其中的有毒有害物质转化为无害化合物,最后再将净化后得到的煤气进行回收利用。
此种净化方式是比传统的高温净化的方式更加环保,且更加节能。
应用情况转炉煤气干法LT净化回收技术目前已经在国内多家炼钢厂得到了广泛应用,其净化效果得到了良好的验证。
它不仅可以降低污染排放,而且可以提高资源利用率,收益显著。
在使用过程中,需要做好相关的防爆措施,以确保工作安全。
防爆措施作为一种较为安全的净化方式,转炉煤气干法LT净化回收技术在实际使用过程中也需要做好相应的防爆措施。
具体可采取以下措施:1.操作人员必须接受专业的培训,熟练掌握操作技能及相关安全规范。
2.对设备进行定期检查维护,确保设备处于良好的工作状态,减少设备故障以及为防止事故的发生留下隐患。
3.在压力较高的部位加装爆炸防护装置,防止在操作过程中因煤气燃爆出现安全事故。
4.注意防火措施,在操作现场设立消防设施,在操作过程中严格控制火源,尽可能避免火花等潜在火源的出现。
通过加强设备维修保养,并加强操作人员的安全意识,可帮助工作人员避免由于设备故障或操作不当导致的事故发生。
结论转炉煤气干法LT净化回收技术是一种环保且高效的煤气净化方式,已经在国内多家炼钢厂得到了操纵和推广。
在此技术的应用过程中,我们需要加强设备维修保养,注重安全教育培训,在操作现场设立消防设备,注意防火措施等,可实现安全可靠的运转。
虽然转炉煤气干法LT技术已经得到了广泛应用,但我们还需要进行更深入的研究以优化该技术,并进一步推广和应用。
转炉煤气干法净化回收技术

转炉煤气干法(LT)净化回收技术的国产化应用我国现有600多座转炉,年产钢超过4亿吨,节能减排潜力巨大。
目前我国绝大多数转炉的转炉煤气净化采用较为落后的湿法(以下简称老OG)除尘,耗水耗电量大,是钢铁工业节能减排的薄弱环节。
除了老OG除尘之外,近年来我国新建转炉采用了第四代湿法(以下简称新OG法),以及引进的千法(以下简称LT法):使转炉煤气净化技术取得了突破性进展。
在转炉煤气净化技术引进的同时,国内多家设计研究单位进行了吸收开发,目前转炉煤气净化的LT法、新OG法除引进少量关键技术和部件,大量的设备设计、系统设计立足于国内,甚至新OG法基本实现全国产化。
对我国转炉炼钢节能减排、实现负能炼钢起到了积极的推动作用。
但是我们仍清醒看到,转炉煤气净化发展到今天,这些技术包括引进技术都不同程度的存在一些问题、或有值得改之处,这是我国钢铁工业节能减排要追求和持续研究的新目标和新课题。
正是由于目前各种除尘方式的利弊所在,使新建转炉除尘设计选择LT法还是新OG法似乎难以确定。
本文就两种除尘方式进行比较,提出自己的建议。
1.国内外转炉烟气除尘技术的发展和现状当前,转炉烟气净化及煤气回收技术主要有两大类型:即日本的湿法系统(OG法)和德国的干法系统(LT法)。
1.1 湿法系统图1 OG法工艺流程OG法是以双级文氏管为主,抑制空气从转炉炉口流入,使转炉煤气保持不燃烧状态,经过冷却而回收的方法,因此也叫未燃法,又称湿法。
在湿法方面,日本从60年代起开发了OG法,这是世界上普遍采用的流程。
1962年,日本新日铁公司的转炉首次成功地应用该法对转炉烟气进行除尘并回收,合理地利用废气中的化学能和显能及含铁粉尘。
目前己成为世界上最广泛采用的转炉烟气处理方法,在保护环境、回收能源方面发挥了积极作用。
OG法装置主要由烟气冷却系统、烟气净化系统及附属设备组成(见图1)。
在冶炼中生成高一氧化碳浓度且含150~200mg/m3粉尘的煤气,温度达1600℃。
转炉煤气回收的安全措施

仅供参考[整理] 安全管理文书转炉煤气回收的安全措施日期:__________________单位:__________________第1 页共7 页转炉煤气回收的安全措施1、概述转炉煤气的产生是间歇式的,集中在吹炼期,在吹炼期内的不同时期,其成分也不同,而且与回收设备的操作及煤气的回收条件有关。
每吨钢转炉煤气具有的能量约为100万kJ,回收利用这些能量的方法有燃烧法和未燃法,国外主要发展未燃法以回收煤气。
未燃法有3种净化除尘方法:一是日本的OG除尘法,二是德国克鲁伯公司的最小气量除尘法,三是法国的IC敞口烟道法。
石钢转炉炼钢厂采用的是OG除尘法回收煤气,1998年4月1日正式回收煤气,并在一年多的实践过程中保证了安全可靠运行,回收了资源,降低了生产成本。
煤气具有爆炸、着火、使人中毒三大危险,当回收和使用煤气不当时,就可能发生上述事故。
充分地了解转炉煤气特性,掌握转炉煤气的回收与使用工艺过程,熟悉回收系统设备的功能,避免各类事故的发生和正确处理发生的事故,对于保证人身安全,保护国家财产,减少损失和缩小事故面有很大的意义。
2、转炉煤气的特性转炉未燃法产生的煤气主要成分为一氧化碳及少量的氢,不同的操作工艺回收煤气中的一氧化碳含量也不同,一般为40%~70%。
一氧化碳是无色、有微臭的气体,重度为1.25kg/m3,比空气稍轻。
转炉煤气与空气或氧气(从氧枪中漏出之纯氧)混合,在特定条件下会产生速燃,使设施中的压力突然增高而造成设备损坏和人身事故。
冶金企业常用的煤气为焦炉煤气、高炉煤气、转炉煤气,而转炉煤气的一氧化碳含量远高于焦炉与高炉煤气的一氧化碳含量,且毒性大,回收操作过程不连续,尤其更应引起我们的重视和注意。
第 2 页共 7 页3、回收工艺中的安全保证措施(1)转炉煤气进行回收的前提条件是要保证除尘系统的运行完好,高效率地捕集转炉烟气中的尘粒,使得煤气的质量满足用户需要。
转炉烟气净化除尘与煤气回收设施是一套紧密相连、密切相关的系统。
转炉煤气回收的安全措施

转炉煤气回收的安全措施摘要转炉煤气回收是一项重要的能源回收技术。
但是,它也存在一定的安全隐患,需要采取措施来规范操作和确保安全。
本文将探讨转炉煤气回收的安全措施。
前言随着全球能源消耗量的不断增长,能源回收成为各国政府关注的焦点。
煤气回收是一种常见的能源回收技术,用于将高热量的废气转化成可再利用的能源。
转炉煤气回收是其中的一种技术,主要用于废气热值高的生产工艺中。
然而,由于转炉煤气回收操作涉及高温、高压等危险因素,如果不加以管理和控制,可能会引发安全事故,造成严重的人员伤亡和财产损失。
因此,加强安全措施是确保转炉煤气回收正常运行的必要条件。
知识点转炉煤气回收原理转炉煤气回收技术是一种将转炉煤气进行回收利用的技术。
转炉煤气是一种高温、高压的废气,如果不能得到回收,将会严重浪费资源和能源。
在转炉煤气的回收利用过程中,需要通过特定的方法将其转化为热能或电能,以便进行二次利用。
转炉煤气回收的安全隐患转炉煤气回收操作涉及高温、高压等危险因素,因此存在一定的安全隐患。
其中,较为常见的安全隐患包括:•操作人员不熟练或不规范的操作可能导致煤气泄漏,引发爆炸等危险;•煤气的含氧量和热值易与氧气和空气发生爆炸;•炉体瓦斯按炉套式收集,容易在收集过程中发生瓦斯中毒;•收集后的煤气中含有多种有毒有害物质,如烟气中的苯、酚、重金属、二氧化碳等,需要进行有效的处理和过滤。
转炉煤气回收的安全措施为确保转炉煤气回收的安全运行,需要采取以下措施:1. 操作规范操作规范是保证转炉煤气回收安全的首要条件。
为了避免操作人员疏忽或不规范的操作,需要对其进行培训和考核,保证其掌握正确的操作流程和安全常识。
2. 安全设施为了保护操作人员和设备,需要配置必要的安全设施,如火灾自动报警、自动灭火、安全阀、泄漏报警等设备,以便在发生意外情况时及时发现和处理。
3. 检测监测煤气的含氧量和热值对煤气的安全性有很大影响。
因此,要对煤气进行定期的检测监测。
转炉煤气干法净化回收技术应用及防爆措施

转炉煤气干法净化回收技术应用及防爆措施引言随着工业化进程的加速,煤炭等化石能源的使用量也在不断增加。
然而,煤气作为燃料,在燃烧过程中产生的废气中含有大量的有害物质,对环境和人体健康造成了严重的危害。
因此,净化和回收转炉煤气成为了一项重要的任务。
本文将介绍转炉煤气干法净化回收技术的应用和相关的防爆措施。
转炉煤气干法净化回收技术的原理转炉煤气干法净化回收技术是通过一系列的物理和化学过程,将转炉煤气中的有害物质去除,并回收其中的燃料成分。
主要的净化过程包括吸附、过滤和冷凝等。
吸附过程吸附是将废气中的有害物质吸附到吸附剂表面上的过程。
常用的吸附剂有活性炭和分子筛等。
当煤气通过吸附床时,有害物质会被吸附剂吸附,并在其表面积聚。
吸附剂可以重复使用,只需要定期进行再生处理,将吸附在上面的有害物质去除。
过滤过程过滤是利用滤料的孔隙、表面和作用力等原理,将煤气中的颗粒物、微粒和液滴等固体和液体物质从气体中分离的过程。
常用的过滤材料有陶瓷滤板、玻璃纤维滤料等。
过滤过程可以有效地去除煤气中的颗粒物,提高其净化效果。
冷凝过程冷凝是通过降低煤气温度,使其中的水蒸气和有机物质凝结成液体,从而将其分离出来。
冷凝过程常用的设备有冷却器和冷凝器等。
通过控制冷凝温度和冷凝速度,可以有效地去除煤气中的水分和有机物质。
转炉煤气干法净化回收技术的应用转炉煤气干法净化回收技术在钢铁、化工、电力等行业都有广泛的应用。
钢铁行业在钢铁生产过程中,转炉煤气是一种重要的燃料和能源,同时也是高浓度有害物质的主要来源。
通过应用转炉煤气干法净化回收技术,可以将转炉煤气中的有害物质净化去除,提高环境保护和生产效率。
化工行业在化工生产过程中,转炉煤气是一种重要的燃料和原料。
然而,转炉煤气中含有大量的有机物质和硫化物等有害物质,对生产设备和环境造成了严重的腐蚀和污染。
通过应用转炉煤气干法净化回收技术,可以将转炉煤气中的有害物质净化去除,提高生产安全和产品质量。
转炉煤气回收系统爆炸成因分析和防范措施

转炉煤气回收系统爆炸成因分析和防范措施转炉煤气回收系统是指在转炉炉膛内对产生的烟气进行回收利用的系统。
然而,由于煤气具有易燃易爆的特性,转炉煤气回收系统存在一定的爆炸风险。
为了保障转炉煤气回收系统的安全运行,需要对爆炸成因进行分析,并采取相应的防范措施。
一、爆炸成因分析1.煤气泄漏:在转炉煤气回收系统中,由于管道连接不牢固、管道老化等原因,有可能导致煤气泄漏,进而形成可燃气体的积聚。
2.火源存在:在转炉煤气回收系统周围,可能存在火源,如明火、电火花等,火源接触到煤气,就有可能引发爆炸事故。
3.温度过高:由于转炉煤气回收系统内部煤气的温度较高,如果温度过高、无法及时排除,就有可能使煤气自燃并引发爆炸。
4.毒性物质积聚:在转炉煤气回收系统中,如果煤气中含有毒性物质,并且这些物质无法及时排除,就有可能在爆炸时产生有毒烟雾,对人身安全产生威胁。
二、防范措施1.管道维护:定期对转炉煤气回收系统的管道进行维护,检查管道连接是否牢固,是否存在老化、腐蚀等情况,如有问题及时进行修复或更换。
2.煤气泄漏检测:安装煤气泄漏检测装置,及时发现煤气泄漏,参考应急预案进行处理。
另外,对煤气进行层流密封处理,减少泄漏风险。
3.火源防控:确保转炉煤气回收系统周围没有明火存在,并对可能产生电火花的设备进行隔离,使用防爆电器设备。
4.温度控制:安装温度监测装置,对转炉煤气回收系统内部煤气的温度进行实时监测。
一旦温度超过设定范围,及时采取降温措施,如增加冷却介质流量等。
5.毒性物质处理:针对转炉煤气中可能含有的毒性物质,安装相应的过滤装置,将毒性物质排除。
并建立排放标准,确保排放的煤气符合环保要求。
6.紧急预案制定:制定转炉煤气回收系统爆炸事故的紧急预案,明确责任分工和应急处理措施,提前做好人员疏散、扑救和事故报告等工作。
综上所述,转炉煤气回收系统爆炸的成因可能有煤气泄漏、火源存在、温度过高和毒性物质积聚等。
为预防此类事故的发生,需采取管道维护、煤气泄漏检测、火源防控、温度控制、毒性物质处理以及制定紧急预案等多种防范措施,从而保障转炉煤气回收系统的安全运行。
安全技术之转炉煤气回收的安全措施
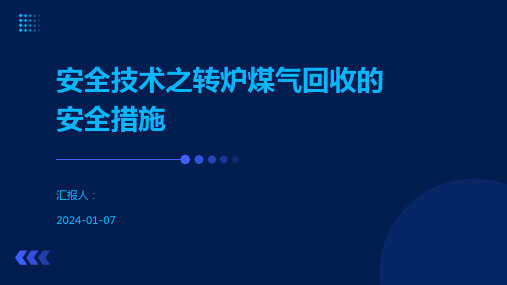
预防火灾和爆炸
01
对转炉煤气回收系统进行严格监控,防止超温、超压等异常情 况。
02
在关键部位设置安全阀、压力表等安全附件,确保系统安全运
行。
建立严格的动火作业管理制度,避免在回收系统中进行违规操
03
作引发火灾和爆炸。
03
安全技术措施
煤气回收设备的维护和检查
01
定期检查
对煤气回收设备进行定期检查, 确保设备处于良好状态,及时发 现并处理潜在问题。
针对不同程度和范围的泄漏,采取相应的应急措 施,如关闭阀门、启动应急电源等,以控制泄漏 。
中毒人员的急救措施
中毒症状:转炉煤气中的一氧化碳是一种无色、无味 的有毒气体,中毒后可能出现头痛、恶心、呕吐、乏
力等症状,严重时可能导致昏迷甚至死亡。
输标02入题
发现中毒人员后应立即将中毒者移至通风处,解开衣 领、腰带等束缚,保持呼吸道通畅,并注意保暖。
数据记录与分析
收集监控和报警数据,进行记录 和分析,以便及时发现和解决潜 在安全隐患。
员工安全培训和防护设备
安全培训
定期开展煤气回收安全培训,提高员工安全意识 和操作技能。
防护设备
为员工配备必要的防护设备,如防毒面具、防护 服等,确保员工在操作过程中的安全。
应急演练
组织煤气泄漏等紧急情况的应急演练,提高员工 应对突发状况的能力。
安全技术之转炉煤气回收的 安全措施
汇报人: 2024-01-07
目录
• 转炉煤气回收概述 • 安全措施的必要性 • 安全技术措施 • 应急处理措施 • 安全管理制度
01
转炉煤气回收概述
转炉煤气的性质
可燃性
01
转炉煤气是一种可燃性气体,具有较高的燃烧热值。
转炉干法除尘系统煤气回收的分析与研究
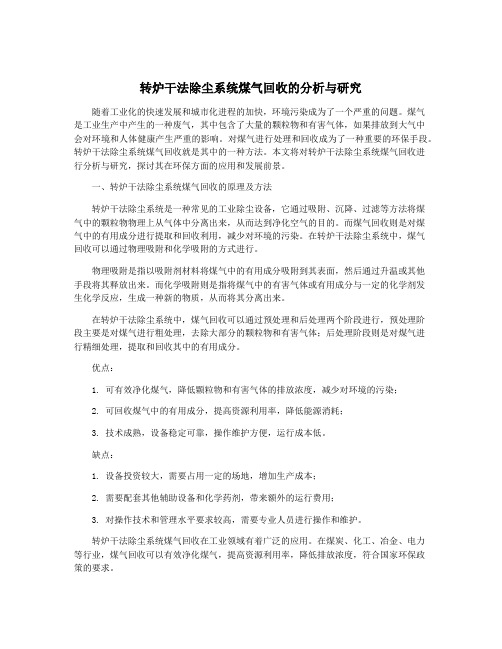
转炉干法除尘系统煤气回收的分析与研究随着工业化的快速发展和城市化进程的加快,环境污染成为了一个严重的问题。
煤气是工业生产中产生的一种废气,其中包含了大量的颗粒物和有害气体,如果排放到大气中会对环境和人体健康产生严重的影响。
对煤气进行处理和回收成为了一种重要的环保手段。
转炉干法除尘系统煤气回收就是其中的一种方法。
本文将对转炉干法除尘系统煤气回收进行分析与研究,探讨其在环保方面的应用和发展前景。
一、转炉干法除尘系统煤气回收的原理及方法转炉干法除尘系统是一种常见的工业除尘设备,它通过吸附、沉降、过滤等方法将煤气中的颗粒物物理上从气体中分离出来,从而达到净化空气的目的。
而煤气回收则是对煤气中的有用成分进行提取和回收利用,减少对环境的污染。
在转炉干法除尘系统中,煤气回收可以通过物理吸附和化学吸附的方式进行。
物理吸附是指以吸附剂材料将煤气中的有用成分吸附到其表面,然后通过升温或其他手段将其释放出来。
而化学吸附则是指将煤气中的有害气体或有用成分与一定的化学剂发生化学反应,生成一种新的物质,从而将其分离出来。
在转炉干法除尘系统中,煤气回收可以通过预处理和后处理两个阶段进行,预处理阶段主要是对煤气进行粗处理,去除大部分的颗粒物和有害气体;后处理阶段则是对煤气进行精细处理,提取和回收其中的有用成分。
优点:1. 可有效净化煤气,降低颗粒物和有害气体的排放浓度,减少对环境的污染;2. 可回收煤气中的有用成分,提高资源利用率,降低能源消耗;3. 技术成熟,设备稳定可靠,操作维护方便,运行成本低。
缺点:1. 设备投资较大,需要占用一定的场地,增加生产成本;2. 需要配套其他辅助设备和化学药剂,带来额外的运行费用;3. 对操作技术和管理水平要求较高,需要专业人员进行操作和维护。
转炉干法除尘系统煤气回收在工业领域有着广泛的应用。
在煤炭、化工、冶金、电力等行业,煤气回收可以有效净化煤气,提高资源利用率,降低排放浓度,符合国家环保政策的要求。
转炉煤气干法(LT)净化回收技术在转炉的应用
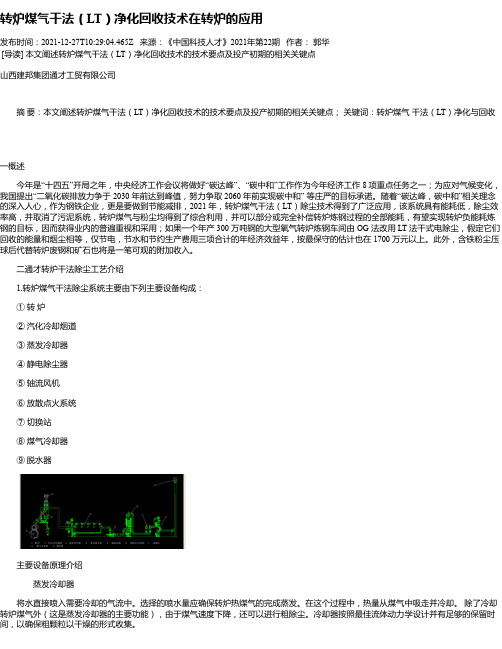
转炉煤气干法(LT)净化回收技术在转炉的应用发布时间:2021-12-27T10:29:04.465Z 来源:《中国科技人才》2021年第22期作者:郭华[导读] 本文阐述转炉煤气干法(LT)净化回收技术的技术要点及投产初期的相关关键点山西建邦集团通才工贸有限公司摘要:本文阐述转炉煤气干法(LT)净化回收技术的技术要点及投产初期的相关关键点;关键词:转炉煤气干法(LT)净化与回收一概述今年是“十四五”开局之年,中央经济工作会议将做好“碳达峰”、“碳中和”工作作为今年经济工作 8 项重点任务之一;为应对气候变化,我国提出“二氧化碳排放力争于 2030 年前达到峰值,努力争取 2060 年前实现碳中和” 等庄严的目标承诺。
随着“碳达峰,碳中和”相关理念的深入人心,作为钢铁企业,更是要做到节能减排,2021 年,转炉煤气干法(LT)除尘技术得到了广泛应用,该系统具有能耗低,除尘效率高,并取消了污泥系统,转炉煤气与粉尘均得到了综合利用,并可以部分或完全补偿转炉炼钢过程的全部能耗,有望实现转炉负能耗炼钢的目标,因而获得业内的普遍重视和采用;如果一个年产 300 万吨钢的大型氧气转炉炼钢车间由 OG 法改用 LT 法干式电除尘,假定它们回收的能量和烟尘相等,仅节电,节水和节约生产费用三项合计的年经济效益年,按最保守的估计也在 1700 万元以上。
此外,含铁粉尘压球后代替转炉废钢和矿石也将是一笔可观的附加收入。
二通才转炉干法除尘工艺介绍1.转炉煤气干法除尘系统主要由下列主要设备构成:①转炉②汽化冷却烟道③蒸发冷却器④静电除尘器⑤轴流风机⑥放散点火系统⑦切换站⑧煤气冷却器⑨脱水器主要设备原理介绍蒸发冷却器将水直接喷入需要冷却的气流中。
选择的喷水量应确保转炉热煤气的完成蒸发。
在这个过程中,热量从煤气中吸走并冷却。
除了冷却转炉煤气外(这是蒸发冷却器的主要功能),由于煤气速度下降,还可以进行粗除尘。
冷却器按照最佳流体动力学设计并有足够的保留时间,以确保粗颗粒以干燥的形式收集。
安全技术之转炉煤气回收的安全措施
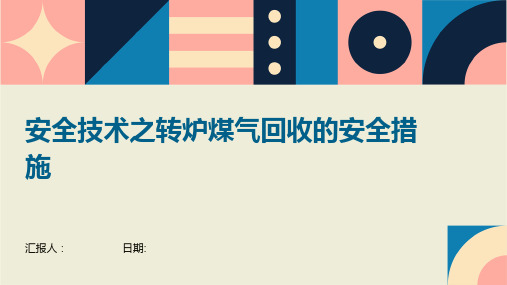
国外钢铁企业在转炉煤气回收方面已经取得了较为显著的成 果,不仅回收利用率高,而且再利用领域广泛。一些企业还 将转炉煤气回收与余热余压利用相结合,实现了能源的高效 利用。
02
转炉煤气回收中的安全风险
煤气泄漏与爆炸风险
泄漏风险
转炉煤气回收系统中,煤气管道、阀 门、法兰等连接部位可能因老化、磨 损、安装不当等原因导致煤气泄漏, 形成安全隐患。
定期对管道进行检查、测 厚、探伤等,及时发现并 处理隐患。
操作人员安全防护措施
个人防护装备
配备防毒面具、防护服、手套等,确保操作人员安全。
安全操作规程
制定详细的安全操作规程,对操作人员进行培训和考核,确保熟练 掌握。
紧急处理措施
制定煤气泄漏、中毒等紧急情况的处理措施,并进行演练,确保操 作人员具备应急处理能力。
爆炸风险
煤气泄漏后与空气混合,在一定条件 下(如明火、静电火花等)可能引发 爆炸,造成设备损坏和人员伤亡。
中毒与窒息风险
中毒风险
转炉煤气中含有大量有毒有害气体(如一氧化碳、硫化氢等),人体长时间吸入 或接触可能导致中毒。
窒息风险
煤气泄漏后,高浓度的一氧化碳等有毒气体会降低空气中氧含量,导致人员窒息 。
安全技术之转炉煤气回收的安全措 施
汇报人:
日期:
• 转炉煤气回收概述 • 转炉煤气回收中的安全风险 • 转炉煤气回收的安全措施 • 紧急情况下的应急处理方案 • 安全管理与培训制度建立 • 结论与展望
01
转炉煤气回收概述
转炉煤气回收定义与重要性
定义
转炉煤气回收是指将钢铁企业转炉生产过程中产生的高温、高压、含有一氧化 碳等有毒有害成分的废气进行收集、处理、再利用的过程。
转炉煤气回收工艺及安全措施
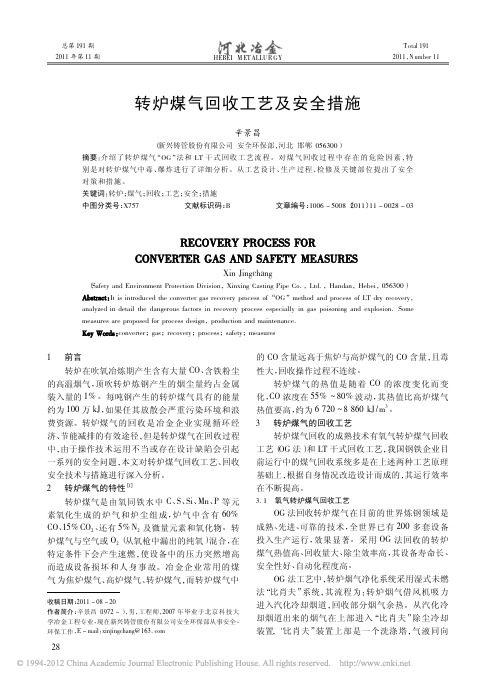
总第191期2011年第11期HEBEI M ETALLU R GYTotal 1912011,N umber 11收稿日期:2011-08-20作者简介:辛景昌(1972-),男,工程师,2007年毕业于北京科技大学冶金工程专业,现在新兴铸管股份有限公司安全环保部从事安全、环保工作,E -mail :xinjingchang@163.com 转炉煤气回收工艺及安全措施辛景昌(新兴铸管股份有限公司安全环保部,河北邯郸056300)摘要:介绍了转炉煤气“OG ”法和LT 干式回收工艺流程。
对煤气回收过程中存在的危险因素,特别是对转炉煤气中毒、爆炸进行了详细分析。
从工艺设计、生产过程、检修及关键部位提出了安全对策和措施。
关键词:转炉;煤气;回收;工艺;安全;措施中图分类号:X757文献标识码:B文章编号:1006-5008(2011)11-0028-03RECOVERY PROCESS FORCONVERTER GAS AND SAFETY MEASURESXin Jingchang(Safety and Environment Protection Division ,Xinxing Casting Pipe Co.,Ltd.,Handan ,Hebei ,056300)Abstract :It is introduced the converter gas recovery process of “OG ”method and process of LT dry recovery ,analyzed in detail the dangerous factors in recovery process especially in gas poisoning and explosion.Some measures are proposed for process design ,production and maintenance.Key Words :converter ;gas ;recovery ;process ;safety ;measures1前言转炉在吹氧冶炼期产生含有大量CO 、含铁粉尘的高温烟气,顶吹转炉炼钢产生的烟尘量约占金属装入量的1%。
转炉煤气净化回收技术及应用

1.1 转炉煤气回收工艺 转炉煤气回收工艺主要有湿法和干法两种。 20 世纪 60 年代,新日铁与川崎股份有限公司共同
开发并成功开发了 OG 转炉煤气净化回收技术,该技术 通常采用双文本技术,主要包括两级文丘里+两级或三 级脱水机。
新 OG 技术采用饱和喷淋塔+环接头洗涤器(RSW 或 AGE),是对传统 OG 方法的技术改进。饱和喷淋塔代 替纸张,环形接头代替可调喉道。
随着国家节能减排政策的实施,国内许多钢铁企业 需要采用新技术、新工艺来实现节能减排的目标。对转 炉炼钢来说,炼钢过程中产生的气体的干法净化和回 收是实现负能量炼钢的有效途径。这一技术的最大特 点就是解决了转炉煤气干法净化与回收系统与转炉炼 钢工艺之间密切相关,互相保证顺利运行的问题。因 此,无论在新建转炉还是对现有转炉煤气净化回收系 统进行改造,采用转炉煤气干法净化回收技术是钢铁 企业的最佳选择。例如,两套 250 t 转炉宝钢 120 t 转 炉三组山东莱芜钢铁公司、重庆三组 180 t 转炉钢铁和 三组 150 t 转炉高锰镍耐磨不锈钢全部采用 LT 除尘方 法和目前运行状态良好。
高;办理和事务要求不复杂;技能和设备相对老练,在 国内已完全掌握;一次性出资本钱较低。
(2)缺点:耗水耗电量较高,风机故障率较高。气体 粉尘质量浓度较高,为 100 mg/m3。如果降低到 10 mg/ m3,则在气罐与压力站之间增加电除尘器,增加投资成 本。体系阻力大于干体系阻力,能耗较大。与干燥体系 相比,水处理设备每套添加 1500 万元,占地面积较大。 不能从根本上处理二次污染问题。尤其是含六价铬的 废水不能处理,对地下水造成严重污染。 2.2 转炉煤气干法净化回收技术特点
作者简介:蔡伟均(1968-),男,广东梅州人,研究方向:冶金工业煤气回收综合利用。
转炉煤气干法净化回收技术的运用
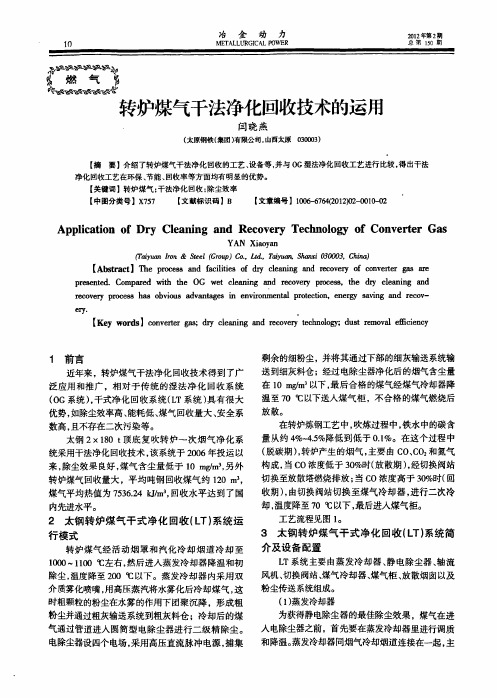
冶金动力2012年第2期10唧A LLU RG I C A L P0w E R总第150期转炉煤气干法净化回收技术的运用闫晓燕(太原钢铁(集团)有限公司.山西太原030003)【摘要】介绍了转炉煤气干法净化回收的工艺、设备等,并与O G湿法净化回收工艺进行比较,得出干法净化回收工艺在环保、节能、回收率等方面均有明显的优势。
【关键词】转炉煤气;干法净化回收;除尘效率【中图分类号】x757【文献标识码】B【文章编号】1006—6764<2012)02—00l㈣2A ppl i cat i蚰of D r y C l eal l i ng and R ecover y Tecl l l l ol o科0f C onV er t er G asY A N X i a oya n闭卫砷埘l胁忍&S纪eZ$,D印J co.,£碰,死f,攸巩‰f∞DDDi C矗讥∞【A bs t r act】The pr oces s趿d f如i l i t i e s of dr y cle肌iI l g and r eco ver y0f conver t er g鹤黜p瑚ent ed.Com pared、^,i t l l山e O G w e t cl e锄i ng锄d r ecov er y pr oces s,ⅡI e dI y cl e明i ng锄d 删ⅪI ve町pr oce ss h勰obvi ou8adv粕t ages洫envi r o如1ent al pr ot ect i on,肌er舒s删ng孤d r e cov—er、r.●【Key w o“Is】convert er g够;dr y cl eani ng锄d r ecov er y t ecl l I l ol o留;dust r e m oval e伍ci ency1前言近年来,转炉煤气干法净化回收技术得到了广泛应用和推广,相对于传统的湿法净化回收系统(O G系统),干式净化回收系统(L T系统)具有很大优势,如除尘效率高、能耗低、煤气回收量大、安全系数高,且不存在二次污染等。
转炉煤气LT法净化技术及在中国的应用

转炉煤⽓LT法净化技术及在中国的应⽤转炉煤⽓LT法净化技术及在中国的应⽤蔡富良(⼴东省韶钢设计院⼴东512123 )摘要: 转炉⼀次烟⽓静电除尘(LT法)是钢铁⾏业节能降耗的重要技术之⼀,钢铁协会贯彻《钢铁产业政策》时将其列为“三⼲三利⽤”等六⼤类先进技术加以重点推⼴。
本⽂介绍了转炉⼀次烟⽓静电除尘(LT法)技术的发展、应⽤,并对LT法及OG法进⾏⽐较,建议国内加快LT法的推⼴,尤其是现使⽤OG法的企业应在条件具备下加快改造,实现节能减排,以降低成本、保护环境。
LT法的采⽤将为钢铁⾏业年节约成本⼏⼗亿元,并可为国家提出的“⼗⼀五”期间单位GDP能耗降低20%做贡献。
关键词:转炉煤⽓静电除尘(LT法)OG法节能降耗⼤⼒推⼴Application of Converter coal gas LT method of purifying technology in ChinaCAI Fu-Liang(Design Institute of Shaoguan Iron& Steel Company, guangdong 512100,China) Abstract: Converter haze electrostatic dust removal (LT method) is one of important techniques in the steel and iron industry to save energy and reduce consumes. It has been listed as it "three dyies, three uses" , one of six kind of advanced techniques, and has been mainly promoted., when the steel and iron association implements "Steel and iron Industry policy" .This article emphasizes on the development of the technology of Converter haze electrostatic dust removal (LT method) ,its application, and the comparison between LT and OG method. It suggests popularizing LT method at all attempts, especially the enterprises using OG method should quicken the speed of rebuilding on providedconditions in order to reduce cost and protect environment. The application of LT method will save the cost of scores of billions for steel and iron industry and reduce 20% energy consume on unit GDP in the period of “eleven-five” layout. Key words: Converter coal gas, electrostatic dust removal(LT method),OG method, energy-saving and consume-reducing, popularize at all attempts,1.前⾔转炉煤⽓⼲式除尘由于采⽤静电除尘器作为净化设施,在净化效果、能耗、占地⾯积、操作运⾏费等⽅⾯都⽐OG法更优越,⽽且没有OG法带来的⽔处理、污泥处理及对环境的⼆次污染,⾼含铁粉尘可直接回收利⽤,在国际上已被认定为今后的发展⽅向,世界各国都陆续采⽤。
转炉煤气净化回收技术及应用

196机电技术应用Application of Mechanics-electronics Technology2020年3月下转炉煤气净化回收技术及应用李维花(河钢宣钢一钢轧厂,河北 石家庄 075100)摘 要:我国属于钢铁产业发展较强的大国,各种不同种类的粗钢大部分都是用转炉产出来的。
转炉冶炼钢产品期间会产出许多一氧化碳和氧化铁,这些全是能再次利用的能源。
假如把这些能源资源重新利用,不但能保护环境,而且有利于我国经济的发展。
文章主要分析了国内和国外的转炉煤气净化回收技术和应用,希望给相关工作人员提供一些帮助。
关键词:转炉煤气净化;回收技术;应用中图分类号:X757 文献标志码:A 文章编号:1672-3872(2020)06-0196-01——————————————作者简介: 李维花(1981—),女,河北张家口人,本科,工程师,研究方向:动力。
1 转炉煤气回收技术概述1.1 转炉煤气回收技艺转炉煤气回收技艺包括湿法和干法两类。
转炉煤气的湿法除尘技艺简单来说就是当转炉进行排气工作时,会通过固有的管道,将充满烟气的管道冷却之后,水冷肘,温度大概900益,然后进入文丘里管。
其灭火历程实际也能帮助工艺冷却、去尘等工作的进程。
达到饱和程度的烟气热温大概是70益,再用重力脱水器去除水分,从而减少污水量。
其次是用烟雾在90°弯管脱水机和洗涤器里再除水和去尘。
二冷除尘排水期间,烟气的度数一般使风机限制在50~70益间,灰尘含量减少到0耀100mg/Nm 3。
最终,会排入风机内部,被输送到回收体系中或者通过气动三通双蝶阀将其排出[1-2]。
1.2 干法尘除尘技艺转炉煤气的干法除尘技艺简单说就是转炉烟气经历了汽化冷却之后,再由着烟气管道加入用于蒸发的冷却器里,而蒸发冷却器利用设置在汽化冷却烟气管道末尾的喷枪喷出液体,将烟气温度的700~1000益下降到150~300益,粗大的粉尘造成的烟气能在进入干缸以后再根据细静电原料去除尘土。
转炉煤气净化回收技术规程

转炉煤气净化回收技术规程转炉煤气净化回收技术规程一、前言转炉煤气净化回收技术是一种对炼钢企业的环保方案,削减了污染物的排放,将废气变成为紧要的能源资源。
为了保证技术的牢靠性和运转效率,订立转炉煤气净化回收技术规程便显得尤为紧要。
二、技术应用范围钢厂的炼钢业务一般需要消耗大量的能源和资源,因此排放的二氧化碳、氮氧化物、硫氧化物和烟尘等污染物也很高。
而转炉煤气净化回收技术正好可以解决这一问题,该技术适用于以下领域:1、炉顶煤气净化2、煤气合成3、转炉煤气脱硫脱硝三、技术原理转炉煤气净化回收技术重要通过排气口,将进入大气中的废气进行处理。
实在的原理如下:1、先将转炉废气送至煤气净打扮置2、通过净打扮置将煤气中的二氧化碳、氮氧化物、硫氧化物和烟尘等有害物质进行清除3、清除后的煤气通过管道运至发电机组或者再次压缩后进行加热利用四、技术参数1、净化效率:90%2、最高煤气进口温度:800℃3、煤气出口温度:225℃4、系统压力:0.02-0.1MPa五、安全保障1、进行全面严密的安全风险评估2、对废气处理设备进行全面检查3、定期对煤气管道进行检测4、订立相关的应急预案六、技术进展展望随着市场经济的进展,环保形势持续严峻,转炉煤气净化回收技术将会得到越来越广泛的应用和推广。
同时,随着科技不断进展和技术不断进步,该技术也会不断完善,为环保事业贡献更大的气力。
七、总结转炉煤气净化回收技术在炼钢企业的环保方面发挥了巨大作用,具有很高的社会经济效益。
在技术的应用过程中,必需订立科学合理的技术规程,以确保技术的牢靠性和运转效率。
转炉煤气净化回收技术规程
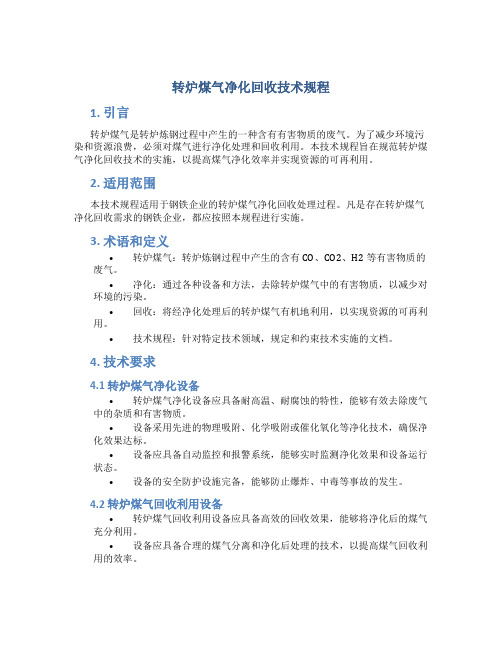
转炉煤气净化回收技术规程1. 引言转炉煤气是转炉炼钢过程中产生的一种含有有害物质的废气。
为了减少环境污染和资源浪费,必须对煤气进行净化处理和回收利用。
本技术规程旨在规范转炉煤气净化回收技术的实施,以提高煤气净化效率并实现资源的可再利用。
2. 适用范围本技术规程适用于钢铁企业的转炉煤气净化回收处理过程。
凡是存在转炉煤气净化回收需求的钢铁企业,都应按照本规程进行实施。
3. 术语和定义•转炉煤气:转炉炼钢过程中产生的含有CO、CO2、H2等有害物质的废气。
•净化:通过各种设备和方法,去除转炉煤气中的有害物质,以减少对环境的污染。
•回收:将经净化处理后的转炉煤气有机地利用,以实现资源的可再利用。
•技术规程:针对特定技术领域,规定和约束技术实施的文档。
4. 技术要求4.1 转炉煤气净化设备•转炉煤气净化设备应具备耐高温、耐腐蚀的特性,能够有效去除废气中的杂质和有害物质。
•设备采用先进的物理吸附、化学吸附或催化氧化等净化技术,确保净化效果达标。
•设备应具备自动监控和报警系统,能够实时监测净化效果和设备运行状态。
•设备的安全防护设施完备,能够防止爆炸、中毒等事故的发生。
4.2 转炉煤气回收利用设备•转炉煤气回收利用设备应具备高效的回收效果,能够将净化后的煤气充分利用。
•设备应具备合理的煤气分离和净化后处理的技术,以提高煤气回收利用的效率。
•设备应具备稳定可靠、操作方便的特点,能够满足钢铁企业的生产需求。
4.3 控制和监测系统•转炉煤气净化回收系统应配备完善的控制和监测系统,能够实现设备的自动化运行和数据实时监测。
•控制系统应具备远程监控和报警功能,能够及时处理意外情况并保证安全生产。
5. 施工和操作要求5.1 设备安装与调试•根据设备厂家提供的安装和调试要求进行操作,并确保设备安装正确、调试完善。
•设备安装完成后,进行必要的质量验收,并办理相关手续。
5.2 操作规程•制定相应的操作规程和操作指导书,明确操作流程和要求。
转炉煤气净化回收技术规程

转炉煤气净化回收技术规程一、概述随着我国钢铁行业的不断发展,转炉煤气的净化回收技术也逐步成熟。
转炉煤气是指在转炉冶炼过程中产生的高温排放气体,其中含有大量粉尘、二氧化碳、一氧化碳、氮气和一些有毒物质。
若不加以处理,将造成污染环境,并对员工身体造成威胁。
因此,对转炉煤气进行净化回收是十分必要的。
本文主要介绍转炉煤气净化回收技术规程。
二、技术规程1. 净化措施钢铁生产中使用的转炉煤气净化系统,一般采用除尘、脱硫、脱氮和有害成分的去除等方法。
•除尘:收集转炉煤气中的粉尘,主要运用的为静电除尘和布袋除尘技术。
其中静电除尘是利用电场作用力将粉尘从气体中去除,而布袋除尘则是利用纤维材料将粉尘隔离。
•脱硫:通过加入氢氧化钙或者氢氧化钠使二氧化硫转化为硫酸钙或者硫酸钠,从而达到脱硫的目的。
钙和钠的稳定性较高,可直接投放到生活污水中。
•脱氮:一般应先进行除尘和脱硫,再进行脱氮处理。
常见的脱氮方法有选择非催化脱氮、选择催化脱氮、选择吸附脱氮、选择氧化脱氮等。
•有害成分的去除:对于有害气体的去除一般会运用活性炭吸附,酸碱中和或者催化氧化等技术。
2. 回收操作•二氧化碳回收:二氧化碳是排放量最大的一种气体,可利用化学吸收法、膜分离法、吸附分离法等技术进行回收。
•一氧化碳回收:一氧化碳是一种有毒气体,参加化学反应,主要与氧反应生成二氧化碳。
其回收利用可采用吸附分离、催化氧化等技术。
•余热回收:通过余热回收,可以提高 30%-50%的能源利用率。
采用余烟利用装置,可将余热回收到发电设备或其他技术生产中进行有效利用。
三、安全措施在对转炉煤气进行净化回收过程中,必须严格遵守生产安全标准。
对于易燃、易爆、有毒气体,必须采取必要的安全措施,以防止事故发生。
具体措施如下:•固定化学剂:制定化学剂固定作业方案,将化学剂提前准备好并预置于指定位置,避免因为溅洒、泄漏等原因引发安全事故。
•各项设备检修和维护保养:定期检测转炉煤气净化设备运行状态,及时更换易损件和损坏部件,确保设备正常运行。
- 1、下载文档前请自行甄别文档内容的完整性,平台不提供额外的编辑、内容补充、找答案等附加服务。
- 2、"仅部分预览"的文档,不可在线预览部分如存在完整性等问题,可反馈申请退款(可完整预览的文档不适用该条件!)。
- 3、如文档侵犯您的权益,请联系客服反馈,我们会尽快为您处理(人工客服工作时间:9:00-18:30)。
转炉煤气干法(LT)净化回收技术的应用及防爆措施李建民转炉煤气除尘技术可分为湿法(OG 法)和干法(LT)两种,由于以文氏管喷水除尘为主的湿法除尘技术存在能耗大、污水需二次处理、煤气处理后含尘浓度高等缺点,在全球钢铁行业大力进行节能减排的形势下,转炉煤气干法除尘技术作为一种最佳可行技术得到越来越多的关注,我国已将其纳入《国家重点行业清洁生产技术导向目录》重点推广。
了解国内外转炉煤气干法除尘技术的发展及应用情况,对钢铁企业选择先进的除尘工艺,从而降低吨钢能耗、提高煤气回收率、实现负能炼钢具有重要意义。
一、概述氧气转炉炼钢采用吹氧冶炼,在吹炼过程中,其烟气量烟气成份和烟气温度随冶炼阶段呈周期性变化。
同时在吹炼过程中,会产生大量烟尘和CO气体,特别在吹炼中期CO浓度可达80%以上,一般情况下,转炉煤气成份中CO的含量占55~66%(体积百分比),其烟尘成份中金属铁占13%,FeO占68.4%,Fe2O3占6.8%,当CO含量在60%左右时,其热值可达8000KJ/Nm3,而烟尘量一般为10~20kg/t钢。
从中可以看出,在氧气转炉炼钢中,转炉煤气中CO含量很高,烟尘中铁含量也很高,因此都有很高的回收利用价值。
通过转炉煤气的回收,不仅可以节约大量能源,而且对烟尘加以综合利用,变废为宝,同时又净化了大气环境。
1、国内外概况和发展趋势随着氧气转炉炼钢生产的发展,炼钢工艺的日趋完善,相应的除尘技术也在不断地发展完善。
日本新日铁和川崎公司于60年代联合开发研制成功OG法转炉煤气净化回收技术。
OG法系统主要由烟气冷却、净化、煤气回收和污水处理等部分组成。
其烟气经冷却烟道后进入烟气净化系统,烟气净化系统包括两级文氏管、脱水器和水雾分离器,烟气经喷水处理后,除去烟气中的烟尘,带烟尘的污水经分离、浓缩、脱水等处理,污泥送烧结厂作为烧结原料,净化后的煤气被回收利用。
系统全过程采用湿法处理,该技术存在的缺点:一是处理后的煤气含尘量较高,达100mg/Nm3以上,要利用此煤气,需在后部设置湿法电除尘器进行精除尘将其含尘浓度降至10 mg/Nm3以下;二是系统存在二次污染,其污水需进行处理;三是系统阻损大,所以其能耗大,占地面积大,环保治理及管理难度较大。
鉴于以上情况,德国鲁奇公司和蒂森钢厂在60年代末联合开发了转炉煤气干法(LT 法)净化回收技术。
LT法系统主要由烟气冷却净化回收和粉尘压块三大部分组成,其烟气经冷却烟道使烟气温度由1550°C左右降至800~1000°C,然后进入烟气净化系统。
烟气净化系统由蒸发冷却器和圆筒型电除尘器组成,烟气通过蒸发冷却器使其温度继续降至180~200°C,同时通过调质处理,使烟尘的比电阻降低并收集了粗粉尘,经过初步处理的烟气进入圆筒型电除尘器,经过进一步的净化,使其含尘浓度降至10 mg/Nm3以下,以获得最佳的除尘效果。
由电除尘器和蒸发冷却器收下的粉尘经输送机送到压块站,在回转窑中将粉尘加热到500~600°C,通过压块机采用热压块的方式将粉尘压制成型,成型的粉块可直接用于转炉炼钢。
LT法主要的优点:一是除尘效率高,通过电除尘器可直接将粉尘浓度降至10 mg/Nm3以下;二是该系统全部采用干法处理,不存在二次污染;三是系统阻损小、能耗低,煤气发热值高,回收粉尘可直接利用,节约了能源;四是系统简化,占地面积小。
因此,LT法干法除尘技术比OG法湿法除尘技术有更高的经济效益和环境效益。
由于该系统具有能耗低,除尘效率高,并取消了污泥系统,转炉煤气与粉尘均得到了综合利用,并可以部分或完全补偿转炉炼钢过程的全部能耗,有望实现转炉负能耗炼钢的目标,因而获得世界各国的普遍重视和采用。
到目前为止,转炉煤气干法(LT法)净化回收技术在德国、奥地利、韩国、澳大利亚、法国、卢森堡等国得到应用,与此同时,美、英、日也开始采用该技术,应用总数已达40套以上。
转炉煤气干法(LT法)净化回收技术在国际上已被认定为今后的发展方向。
2、经济效益和社会效益分析由于氧气转炉干式电除尘技术具有独特的优越性,所以被越来越多的国家所采用以取代OG法。
采用干式电除尘技术,不但经济效益明显,且环境效益也佳。
根据宝钢转炉煤气湿法(OG法)净化回收系统及干法(LT法) 净化回收系统运行的经验,采用干法电除尘技术,每吨钢可节约电1.1度,节水3吨,并可回收10.5公斤含铁75%以上的烟尘和相当于20升左右燃料油的优质煤气.此外,每吨还可节约生产费用2.5元人民币。
我国目前广泛采用的转炉湿式除尘系统(OG法),除宝钢外,一般大、中型转炉除尘吨钢耗电平均为6度,小型转炉除尘耗电平均10~15度。
转炉煤气的回收率很低,转炉除尘的污水处理复杂,污泥均未合理的综合利用。
如果一个年产300万吨钢的大型氧气转炉炼钢车间由OG法改用LT法干式电除尘,假定它们回收的能量和烟尘相等,仅节电,节水和节约生产费用三项合计的年经济效益年,按最保守的估计也在1700万元以上。
其中:节约工业用电: 0.4 x 1.1 x 3000000=900 万元 (每度电按0.4元计) 节约工业用水: 1.0 x 3.0 x 3000000=132 万元 (每吨水按1.0元计)节约生产费用: 2.5 x 3000000=750 万元此外,含铁粉尘压球后代替转炉废钢和矿石也将是一笔可观的附加收入.★如果在我国普遍推行转炉干法电除尘,全年除尘耗电可减少近3亿度。
★若将转炉可回收的煤气与蒸汽都综合起来,折合成标准煤,每吨钢可回收35公斤左右,可望实现低能或无能练钢。
★更值得注意的是干法回收的粉尘,成球后直接返回转炉替代废钢或矿石作为冷却剂,直接回收其金属铁,可增加钢产量180吨/每万吨钢。
★使煤气粉尘排放量大大低于国家环境保护要求,创造一个良好的生产环境和生活环境。
★大大减少了原系统的设备维修费用。
3、转炉煤气干法(LT法)与湿法(OG法)除尘的技术经济指标比较在新建或改造一座炼钢转炉时,其除尘系统选择干法除尘,还是湿法除尘,以下引用德国鲁奇公司两座次150吨转炉为例。
提供干法与湿法除尘的技术经济比较,对设计人员、用户选择除尘方法有一定的参考价值。
(1)基本参数氧气量 42000 Nm3/h 转炉容量 150 t年钢产量 1.3x106 t 冶炼周期性 40~50 min吹氧时间 16~17 min 每天吹炼炉数 30炉原始炉气量 94000 Nm3/h 燃烧系数 0.1烟气量 110000 Nm3/h 出汽化冷却器温度 1000 °C(2)除尘系统相应设备的主要技术数据对比(3)投资比较注:比较内容中投资费用不包括烟罩、汽化冷却烟道、煤气柜与烟气管道。
上述分析表明,干法电除尘系统的初次投资比湿式系统约高10% 。
但由于干式系统具有许多优点,所以其年消耗费用比湿法低22%。
从综合比较表可看出,干法所多花的投资,不到一年半时间即可全部收回,而且随着运行时间的增长,干法除尘的经济效益逐年增加。
二、德晟转炉干法除尘工艺介绍约1550℃的转炉烟气在ID风机的牵引作用下,经过烟气冷却系统(活动烟罩、汽化冷却烟道),使温度降至800℃~1000℃后进入蒸发冷却器。
蒸发冷却器内配备8只双介质雾化冷却喷嘴,对烟气进行降温、调质、粗除尘,烟气温度降低到200℃,同时约40%烟气中的粉尘在蒸发冷却器雾化水的作用下被捕获,形成的粗颗粒粉尘通过链式输送机输入粗灰储灰仓;经冷却、粗除尘和调质后的烟气通过除尘管道进入圆筒形静电除尘器,烟气经静电除尘器除尘后含尘量降至10mg/m3以下。
静电除尘器收集到的除尘灰,经过扇形刮板器、底部链式输送机和细灰输送装置排到细灰仓。
除尘后的烟气再经除尘风机送至切换站,实现煤气放散或回收的快速切换。
为适应转炉烟气的变化,轴流风机采用变频调速,以满足转炉每个冶炼周期各个阶段烟气量的变化。
在切换站前设有气体分析仪,根据气体分析仪检测的一氧化碳浓度来控制切换站,当烟气中氧含量及一氧化碳气体含量达到回收条件时,通过切换站的回收钟阀进入煤气冷却器,经喷淋冷降温到70℃以下后并通过管网送入煤气柜。
热值较低的或氧含量>0.5%的不合格的煤气(或气柜已满)则通过切换站的放散钟阀进入放散烟囱点火放散。
整套系统按照爆炸性气体设计,在电除尘器的进、出口分别设置安全泄压阀,在粗灰系统、细灰系统均设有充氮保护装置;在管路系统、煤气冷却器设有检修氮气吹扫、压缩空气吹扫装置。
1.蒸发冷却器转炉冶炼过程中,含有大量CO的高温烟气经冷却后才能满足干法除尘系统的运行条件。
蒸发冷却器入口的烟气温度为800℃~1000℃,出口温度约为200℃才能达到静电除尘器的条件。
为此,采用了8只双流喷嘴调节最佳水量降温。
双流喷嘴的水量根据进入蒸发冷却器的转炉烟气进、出口温度及流量随时调整。
通入的蒸汽将水雾化成微小的水滴,水滴受烟气加热被蒸发汽化,在汽化过程中吸收烟气的热量,从而降低烟气温度。
蒸发冷却器除了冷却烟气功能外,还可依靠气流的减速以及进口处水滴对烟尘的润湿将粗颗粒的烟尘分离出去,达到除尘的目的。
粉尘聚积在蒸发冷却器底部由链式输送机输出。
蒸发冷却器还有对烟气进行调质的功能。
即在降低气体温度的同时提高烟气含湿量对烟气进行调质,改变烟气粉尘比电阻,有利于在静电除尘器中将粉尘分离出来。
除了烟气冷却和调节以外,占烟气中总粉尘含量约40%的粗灰在蒸发冷却器中进行沉积并被收集。
2.静电除尘器静电除尘器有一个圆筒形的钢板外壳,壳体外表面带有隔热装置,设计有4个独立的电场,平行布置。
与除尘器的外壳相连接的阳极板之间形成通道,需净化的烟气流经这些通道,在集尘电极板框架间装有与高压供电系统连接的电极(阴极),由绝缘支架支撑工作电压67kV,峰值电压111kV,由此产生的电晕,将导致形成带负电荷的气体离子,在放电电极和集尘电极之间的电场作用下,细小的粉尘颗粒由于受到气体离子的作用带上负电,在电场作用下在集尘阳极板上堆集。
积聚在集尘电极上的细颗粒粉尘通过振打脱尘系统,掉落在静电除尘器底部,由扇形刮灰装置收集到电除尘器底部的链式输灰机中。
圆筒形静电除尘器作为转炉一次烟气干法除尘系统的核心设备,其主要技术特点为:①优异的极配形式。
由于转炉煤气的含尘量较高,在进入电除尘器时,一般为55 g/Nm³-80 g/Nm³,而除尘器出口的排放浓度要求小于15m g/Nm³。
这就要求电除尘器具有非常高的除尘效率,而除尘效率高低的主要因素就取决于其极线极板设计的合理性。
除尘器分为4个独立的电场,平行布置。
第三、四个电场均采用ZT24型阳极板,由于烟气温度较高且条件复杂,所以一、二电场阳极板采用了00Cr12材料。
针对4个电场的先后顺序,阴极采用了不同的形式和材质。