8D报告质量评定要求
8D报告质量评分标准160218

评分细则
0分--基本信息描述错误,或相互矛盾; 1分--问题描述基本清晰,基本符合评审 要求; 2分--问题描述清晰,完全符合评审要 求;
2
D3 应急措施
应急措施的目的是在纠正措施实施前防止对华为及供应商的不良影响进一步扩
大,控制嫌疑物料再次流出,保证华为端产线能够继续生产。因此主要从华为
处→在途→供应商库存→半成品加工现场→现场小库存的物料等快速清查并给
1.问题现象定位:描述导致问题发生的直接原因,例如尺寸超标、LCD异物、 摄像头杂质导致黑点等。 2.根因调查分析:导致直接原因的根因是什么?根因分析方式由供应商自己选 择,要求要有逻辑,不能直接或突然得出根因,从8D报告中能看出其中的逻辑 关系,可以采用鱼骨图、5WHY、SIPOC等工具进行分析,例如摄像头异物导致 整机成像黑点问题,异物到底是什么(通过精密仪器定性分析),异物到底产 生于什么工站还是来料问题(BY产品实现工艺逐一分析并验证),异物为何会 产生,为何制程中有多道清洗工站反而没有清洗干净,是制程条件的问题还是 7分 认为操作的问题,如是制程条件的问题,是标准的问题,还是执行的问题,若 是执行的问题,目前的监控机制又是什么,为何会漏失?等等……;鱼骨图等 分析需要有根因排查表。 3.流出原因分析: 针对问题现象定位后,必须分析为什么会留到华为端?此问 题不良比例是多少,供应商是否可以拦截?是否有此问题现象的拦截检验标 准?有管控标准是否拦截数量或频率不够?拦截频率或数量也足够是否人员能 力问题或态度问题?
序号 8D报告步骤
1
D2 问题/缺陷描述
评审要求
满分
问题描述按照4W1H的模式描述(who,when,where,what,how)用量化的语言详
细清晰地描述问题,如问题发生地点、时间、投入数量、不良数量、不良比例 、不良现象(若条件允许的情况下,提供不良照片和不良样品)、对华为的影
8D报告标准基准(八个步骤)

再发防止对策基准-8D1.0目的为明确产品质量改进的程序和内容,以提高产品质量改进的效率和效果,更好的满足顾客的要求,特制定本办法。
2.0适用范围本办法适用于公司质量改进。
3.0定义3.1现象:通过视觉/嗅觉/听觉/触觉等直觉方式,观察到的不良。
3.2问题:通过品质检查/试验等方法,反馈的与产品或过程基准的偏差。
3.3遏制措施:不良现象反馈的当时当地,采取的紧急措施,防止事态扩大化。
3.4临时措施:针对不良现象采取的措施,防止事态持续化,为永久措施争取时间。
3.5永久措施:针对不良原因采取的措施,预防问题再发生。
3.6体系原因:涉及DFMEA、P-FMEA、图纸、CP(控制计划)、WI(作业指导书)、MP(维护计划)等技术文件的失效/过期/缺失3.7物理原因:产品和产品实现过程所涉及实体的失效/过期/缺失等,包括产品、工装、设备等。
4.0 相关文件《不合格品控制程序》《进料检验控制程序》《信息沟通控制程序》5.0职责5.1品质部:品质工程师负责主导8D报告的填写6.0 作业程序6.1 品质工程师接到下述信息,在PDCA中登录,启动8D。
·客诉(0KM/售后)·1个月后1年内重复出现的过程问题。
6.2按8D的方法及步骤要求,实施行动,并填写对应8D项目,具体填写要求以及工具应用见《8D填写说明+支持资料》)。
6.3向客户提交报告前,必须提交品质部经理确认后提交。
6.4向客户提交报告。
6.5每月底,8D报告作为质量信息登记台帐的附件,提交资料员归档。
6.6 8D编码要求6.6.1规则为车型号+产品分类+年+月+日+流水号 例:R103HSJ201812501①车型号:直接借用客户车型②产品分类:后视镜:HSJ 拉手:LS 灯具:DJ 装饰件:ZSJ 其它:QT③年:4位数字,日历年④月:二位数字,日历月⑤日:二位数字,日历日6.6.28D编码由质量体系管理员统一编码,并登记于《信息跟踪管理台帐》(模版见《不合格品控制程序》附件),与质量信息一起按《信息沟通控制程序》要求传递到相应的品质工程师处,品质工程师在编制8D报告编码时,保持与质量信息登记台帐的8D编码保持一致。
8D报告标准

8D报告方法
什么是8D?
8-D 是一个用于探索原因、解决问题的系统化方法。
什么时候使用8D?
当供应商品质持续超出要求的目标时。
当单一不良现象达到2%,即使总体质量水平满足要求。
供应商制程不良导致品质异常。
供应商未测试的参数导致不良。
第一条:组建团队
选择并记录公司内外的所有成员。
选择团队决策支持人(决策支持人要能排除障碍)。
选择一个组长(组长代表小组向上级负责)。
第二条:描述问题
什么是问题?
用客户可完全理解的述语描述问题。
描述导致问题存在或发生的条件。
如有可能,量化导致问题存在或发生的条件。
第三条:紧急对策
指明紧急对策的人、事、时及方法,同时防止在客户端再发生。
紧急对策应考虑到:成本,交货期
不可因而引起其他形式的不良。
第四条根本原因
描述为何发生,并指出该问题流出的原因。
将根本原因按人、机、料、法、环(4M1E)进行分类
第五条:永久改善措施
描述排除不良根源的人、事、时以及如何使用这些资源。
第六条:效果确认
用量化指标来确认对策落实效果(例如CpK达1.5…
紧急对策不能停,直到永久改善措施被确认生效。
第七条:防止复发
描述能预防问题再发生的内部及外部的文化、系统改善条件;
决策支持人负责将改进建议往上级呈报并推动落实。
第八条:祝贺结案
决策支持人和组长肯定小组成员对解决问题的贡献。
浙江友谊菲诺伞业有限公司
8-D报告
质量部:。
完整的8d报告标准范本

完整的8d报告标准范本8D报告是一种解决问题和改善流程的方法,它由8个步骤组成,每个步骤都有其独特的功能和作用。
接下来,我们将详细介绍完整的8D报告标准范本,希望对您有所帮助。
第一步,建立团队。
在处理问题或改进流程时,首先需要建立一个专门的团队。
这个团队应该由不同领域的专家组成,他们可以提供不同的视角和解决方案,确保问题能够得到全面的分析和解决。
第二步,描述问题。
在这一步中,团队需要准确描述问题的性质和影响。
这包括问题的发生时间、地点、频率,以及对产品质量和客户满意度的影响。
只有准确描述了问题,才能有效地解决它。
第三步,立即采取纠正措施。
一旦问题被发现并描述清楚,就需要立即采取纠正措施,以防止问题再次发生。
这可能包括停产、召回产品、修改工艺流程等措施,以确保问题不会继续影响产品质量。
第四步,确定根本原因。
在这一步中,团队需要对问题进行深入的分析,找出导致问题发生的根本原因。
这可能需要使用一些质量工具,如5W1H分析、鱼骨图、因果分析等,以帮助团队找到问题的根本原因。
第五步,制定长期措施。
一旦确定了问题的根本原因,团队就需要制定长期的措施,以防止问题再次发生。
这可能包括修改工艺流程、更新设备、加强员工培训等措施,以确保问题得到根本性的解决。
第六步,验证效果。
在实施长期措施之后,团队需要验证其效果。
这可能包括进行试验、监控生产过程、收集数据等,以确保问题得到了有效的解决。
第七步,预防措施。
一旦问题得到了解决,团队就需要制定预防措施,以防止类似问题再次发生。
这可能包括更新标准操作程序、加强质量管理体系、改进产品设计等措施,以确保问题得到了有效的预防。
第八步,表彰团队。
最后一步是表彰团队的努力和成就。
这可以通过给予奖励、发表表扬信、举行庆祝会议等方式来表彰团队,鼓励他们在未来继续努力改进流程和解决问题。
总结。
完整的8D报告标准范本包括建立团队、描述问题、立即采取纠正措施、确定根本原因、制定长期措施、验证效果、预防措施和表彰团队这8个步骤。
对供应商8d报告的具体要求

对供应商8d报告的具体要求
供应商8D报告是一种解决问题的方法,也被称为“8步解决问题法”,用
于解决供应商品质问题或其他复杂问题。
下面是供应商8D报告的具体要求:
1. 明确问题:明确地描述供应商产品或服务出现的问题,确保描述准确,不产生歧义。
2. 成立团队:成立一个跨职能的团队,包括供应商、生产商、品质人员等,共同解决这个问题。
3. 实施临时措施:在找到根本原因之前,实施临时的纠正措施,防止问题扩大。
4. 确定并验证问题的根本原因:通过深入调查和分析,确定造成问题的根本原因,并验证这个判断。
5. 制定并实施长期的纠正措施:根据根本原因,制定长期的纠正措施,确保问题不再发生。
6. 验证效果:在实施了纠正措施后,验证效果是否符合预期,问题是否得到解决。
7. 预防措施:如果问题依然存在,制定预防措施,防止问题再次发生。
8. 防止类似问题的再次出现:对解决此问题的方法进行总结和标准化,防止类似问题再次出现。
以上是供应商8D报告的具体要求,供您参考。
如有疑问,建议咨询专业人士获取准确信息。
8D报告的内容及使用说明
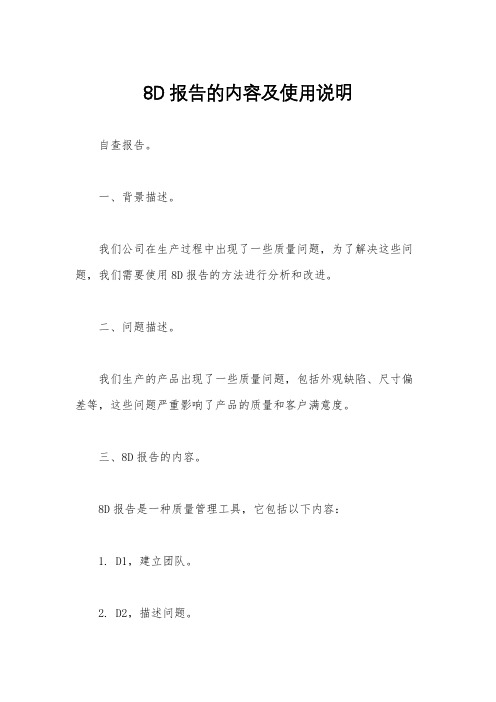
8D报告的内容及使用说明自查报告。
一、背景描述。
我们公司在生产过程中出现了一些质量问题,为了解决这些问题,我们需要使用8D报告的方法进行分析和改进。
二、问题描述。
我们生产的产品出现了一些质量问题,包括外观缺陷、尺寸偏差等,这些问题严重影响了产品的质量和客户满意度。
三、8D报告的内容。
8D报告是一种质量管理工具,它包括以下内容:
1. D1,建立团队。
2. D2,描述问题。
3. D3,立即采取临时措施。
4. D4,找出根本原因。
5. D5,制定长期解决方案。
6. D6,实施长期解决方案。
7. D7,预防措施。
8. D8,确认效果并表彰团队。
四、使用说明。
在使用8D报告的过程中,我们需要按照上述内容逐步进行分析
和改进。
首先建立一个团队,包括相关部门的人员,共同分析和解
决问题。
然后描述问题的具体情况,包括问题的发生时间、地点、
影响等。
接着立即采取临时措施,以减少问题的影响。
然后找出问
题的根本原因,并制定长期解决方案,实施并确认效果。
最后,制
定预防措施,以避免类似问题再次发生,并表彰团队的努力和成果。
五、结论。
通过使用8D报告的方法,我们可以系统地分析和解决质量问题,提高产品质量和客户满意度。
希望全体员工能够认真使用8D报告,
共同改进质量管理工作,为公司的发展做出贡献。
教你如何做8D报告(品质精品)
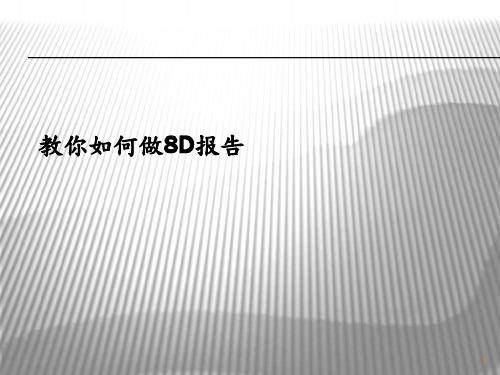
18
也就是我們常說的人, 事, 時, 地, 物
WHAT 什麼事情
WHEN 何時發生 WHO 與誰有關 WHERE 在何處發生
HOW MANY 發生的程度
問題描述
會惡化
是否須緊急處置
19
緊急處置
發生中 Holding
未發生 Sorting
品質問題
已發生
Tracing
20
D2階段 現狀分析(問題細部描述)—收集資料 Fact & Data Finding analysis
24
記錄用查檢表
責任部門
2003年各季LOSS TIME責任分類查檢 表
季度 第一季 第二季 第三季
制 造 1200
1050
890
品保
800
760
780
生管
180
160
100
制工
200
170
185
工程
60
55
78
採購
300
282
300
材倉
50
38
42
合計
2790
2515
2375
合計
3140 2340 440 555 193 882 130 7680
進行真因分析與驗證真因 5、 D5列出選定及驗證永久對策 6、 D6執行永久對策及效果確認 7、 D7防止再發及標準化 8、 D8認知與殘餘潛在問題
4
問題是什么?
當現狀與標准或目標有了差距時, 即遇到了問題
過去
現在
目標 未來
5
盤點工厂現存在的問題
VQA進料檢驗單位 合資單位 業務單位 工程單位 制造單位 IPQC FQC QA QE
8D报告的评价标准

华阳通用电子有限公司.8D 报告的评价标准整理: SQA-Springsun 日期:2012年2月13日8D(Eight Disciplines of Problem Solving)是福特公司解决问题的8条基本准则。
是福特公司在20世纪90年代早期引进的技术方法来解决工厂和供应商的问题。
8D是解决问题的一种工具,通常是客户所抱怨的问题要求公司分析,并提出永久解决及改善的方法。
8D是由一个准备步骤和8个步骤组成。
这些步骤用来客观地确定、定义和解决问题,并防止相似问题的再次发生。
解决问题的8个步骤:问题发生成立8D 小组问题描述实施并验证临时性纠正措施确定和验证问题的根本原因选择和验证永久性纠正措施实施和确认永久性纠正措施防止问题再次发生/系统预防性建议表彰小组和个人的贡献D0D1(10分)D2(10分)D3(15分)D4(15分)D5(15分)D6(15分)D7(15分)D8 (5分)8D目标:解决问题,保证品质积累解决问题的经验。
8D准则:针对出现的问题,找出问题产生的根本原因,提出短期、中期、长期的对策,并采取相应的行动,彻底解决问题,杜绝或尽量减少问题重复出现。
8D好处:z可以通过建立小组训练内部合作能力z推进有效的问题解决和预防技术z改进整个质量和生产率z防止相同或类似问题的再发生z提高顾客满意度有效实施8D的质量工具:z控制计划(PC)z潜在失效模式及后果分析(FMEA)z生产件批准程序(PPAP)z统计过程控制(SPC)z试验计划(DOE)8D说明:1)选定了目标,一定要找出其根本原因,针对产生问题的原因,制订短期对策、中期对策、长期对策。
短期对策:是指生产现场怎么办?中期对策:是指即将要生产的怎么办?长期对策:是指如何将问题解决在发生之前?2)必须采取行动,有对策,执行是关键。
有了对策,必须是不折不扣地执行。
3)持之以恒,必须要坚持行动,解决问题必须要达到彻底清楚的目的。
绝不能因为解决了一半而导致问题周而复始,不时复出发生。
8D改善报告作业规范
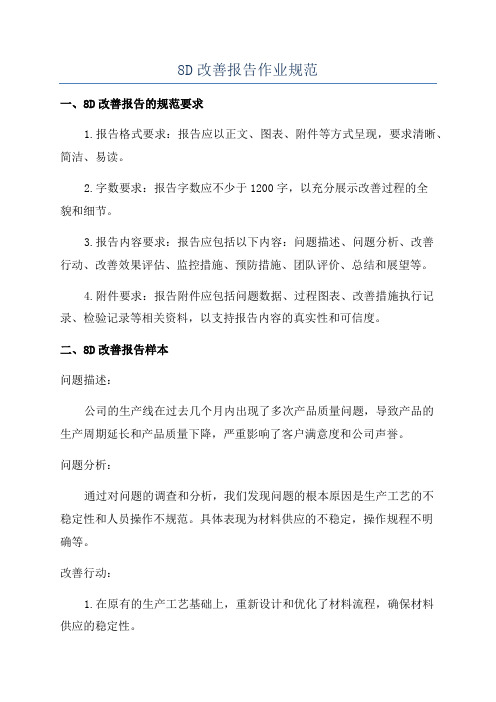
8D改善报告作业规范一、8D改善报告的规范要求1.报告格式要求:报告应以正文、图表、附件等方式呈现,要求清晰、简洁、易读。
2.字数要求:报告字数应不少于1200字,以充分展示改善过程的全貌和细节。
3.报告内容要求:报告应包括以下内容:问题描述、问题分析、改善行动、改善效果评估、监控措施、预防措施、团队评价、总结和展望等。
4.附件要求:报告附件应包括问题数据、过程图表、改善措施执行记录、检验记录等相关资料,以支持报告内容的真实性和可信度。
二、8D改善报告样本问题描述:公司的生产线在过去几个月内出现了多次产品质量问题,导致产品的生产周期延长和产品质量下降,严重影响了客户满意度和公司声誉。
问题分析:通过对问题的调查和分析,我们发现问题的根本原因是生产工艺的不稳定性和人员操作不规范。
具体表现为材料供应的不稳定,操作规程不明确等。
改善行动:1.在原有的生产工艺基础上,重新设计和优化了材料流程,确保材料供应的稳定性。
2.对工序流程进行了再设计,明确了每个操作环节的规范和要求,提高了操作人员的技能水平。
改善效果评估:经过改善行动后,产品质量问题得到了有效控制。
生产周期缩短了20%,产品质量合格率提高了30%以上,客户的投诉率明显下降。
监控措施:为了保持改善效果的持续稳定,我们制定了一系列监控措施。
包括定期检查生产工艺流程,采取纠正措施;对操作人员进行培训和考核,定期评估其技能水平。
预防措施:为了避免类似问题的再次出现,我们制定了一系列预防措施。
包括加强供应商的管理,确保材料供应的稳定性;进行定期的产品质量抽检,发现问题及时纠正。
团队评价:整个改善过程中,团队成员紧密合作,发挥了各个成员的优势,取得了良好的成效。
团队成员之间的沟通和协作能力得到了有效提升。
总结和展望:通过本次的8D改善报告,我们解决了生产线的质量问题,并取得了明显的改善效果。
但我们也意识到,改善是一个持续性的过程,需要不断地监控和预防。
我们将继续改进我们的工艺流程和操作规程,提高产品质量和客户满意度。
质量8D报告模板案例

质量8D报告模板案例一、背景介绍随着市场竞争的加剧,产品质量成为企业生存和发展的关键因素。
为了提高产品质量,企业需要建立一套完善的品质管理体系,并对产品质量问题进行有效的分析和改进。
8D报告作为一种常用的品质问题分析工具,旨在帮助团队系统地识别问题、找出根本原因并制定解决方案。
本文将介绍一个质量8D报告模板案例,帮助您更好地理解和应用8D报告。
二、8D报告概述1. 建立团队:确定团队成员,明确各自职责,确保团队具备解决问题的能力。
2. 描述问题:详细描述问题的症状、影响范围、严重程度等,以便团队成员对问题有清晰的认识。
3. 临时措施:在找到根本原因之前,采取临时措施以减轻问题的影响。
4. 确定并验证根本原因:通过数据分析和团队讨论,找出问题的根本原因,并验证其准确性。
5. 选择并验证永久纠正措施:针对根本原因,制定并验证永久性的纠正措施。
6. 实施并验证永久纠正措施:执行永久性纠正措施,并验证其有效性。
8. 团队认可:确保团队成员对问题解决过程和结果表示认可。
三、质量8D报告模板案例1. 建立团队:项目组成员包括研发、生产、品质、采购等部门,明确各自职责。
2. 描述问题:某产品在客户使用过程中出现故障,导致客户投诉。
故障现象为产品无法启动,影响范围为多个批次。
3. 临时措施:对故障产品进行维修,确保客户正常使用。
4. 确定并验证根本原因:通过分析故障产品,发现故障原因为电源模块设计缺陷,导致电源供应不足。
5. 选择并验证永久纠正措施:对电源模块进行重新设计,确保电源供应充足。
6. 实施并验证永久纠正措施:对新产品进行测试,验证电源模块设计改进的有效性。
7. 预防措施:加强电源模块设计审查,确保设计符合要求。
8. 团队认可:项目组成员对问题解决过程和结果表示认可,认为措施有效。
本文通过一个质量8D报告模板案例,向您介绍了8D报告的八个步骤及其在实际问题解决中的应用。
希望本文能帮助您更好地理解和应用8D报告,提高企业产品质量。
优秀8D评分标准

类似问题改进推广,5分
2 实施培训或经验分享得5分;
奖励对疑难杂症问题解决的改进和
突破,并取得良好效果和成绩,10 加10分
分
备注
分)
完整;25分
很好10分,较好7分,不完整3分,无0分;
4 实施效果显著,无问题重现(10分)
预防与推广 (20分)
其他(加分)
及时关闭,5分
5 各项措施在要求得时间内关闭得5分,否则0分;
相同问题改进推广,15分
1 在本生产线推广改进得5分;在本工厂推广改进得 10分;在全公司推广改进得15分;
原因分析(35
分)
3 问5个为什么,直至根本原因,得15分
多层次展开直至根本原因;27分 4 借鉴分析过去类似问题,得2分
5 缺陷再现,用数据验证原因得10分。
遏制措施有效遏制缺陷,5分; 1 及时有效,无问题重现,得5分
2 永久措施与根本原因对应落实并完整,得5分,缺
一项扣1分;
纠正措施(35 长期措施落实有效;验证跟踪数据 3 验证得相关数据和文件收集、分类、汇总完整,
8D评优标准
评估项
8D完整性(10 分)
评估标准
各栏填写完整,5分
问题描述清晰,4分
评估细则
1 满分5分,空白一栏扣1分 2 按要求填写完整,3栏依次得3、2、1分; 3 附照片,得1分
Hale Waihona Puke 得分8D小组成员构成,1分
4 构成合理、完整,得1分
从人机料法环等方面分析,8分 1分析全面得3分,依次3、2、1分;
8D报告评分标准

7分
4分--问题现象定位清晰,有根因分析和流 出原因分析,但是根因分析或流出原因逻 辑不清晰(只有其中一方面满足评审要 求);
分析需要有根因排查表。 3.流出原因分析: 针对问题现象定位后,必须分析为什么会留到华为端?此问
7分--问题现象定位清晰,有根因分析和流 出原因分析,且根因分析和流出原因逻辑
施与原因分析不一致的状况,或者有原因分析,但是没有对策的状况;
2.制定纠正措施须具有可执行性,不能出现加强检验、加强培训等类似不能落
地的措施,针对一些常规措施还需描述“从什么改善到什么”,例如CCD机从每
天点检一次改善到每班点检一次(因为设备点检对于华为供应商来说都是基本
0分--纠正措施与原因分析不对应;
题不良比例是多少,供应商是否可以拦截?是否有此问题现象的拦截检验标
均清晰完全满足评审要求。
准?有管控标准是否拦截数量或频率不够?拦截频率或数量也足够是否人员能
力问题或态度问题?
备注
4
D5 制定纠正措施
5
D6 验证纠正措施
6
D7 预防措施
1.制定的纠正措施应该与D4中的流出原因与产生原因一一对应,切勿出现纠正措
0分--问题现象不能定位或不清晰; 2分--问题现象定位清晰,只有根因分析或 流出原因分析之一;有根因分析和流出原 因分析,但是这两方面逻辑均不清晰(两
整机成像黑点问题,异物到底是什么(通过精密仪器定性分析),异物到底产
方面均不满足评审要求);
生于什么工站还是来料问题(BY产品实现工艺逐一分析并验证),异物为何会 产生,为何制程中有多道清洗工站反而没有清洗干净,是制程条件的问题还是 认为操作的问题,如是制程条件的问题,是标准的问题,还是执行的问题,若 是执行的问题,目前的监控机制又是什么,为何会漏失?等等……;鱼骨图等
8D报告的内容及使用说明
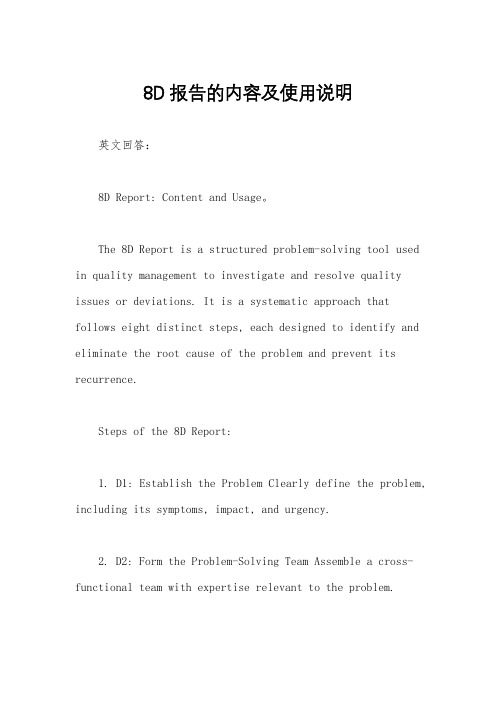
8D报告的内容及使用说明英文回答:8D Report: Content and Usage。
The 8D Report is a structured problem-solving tool used in quality management to investigate and resolve quality issues or deviations. It is a systematic approach that follows eight distinct steps, each designed to identify and eliminate the root cause of the problem and prevent its recurrence.Steps of the 8D Report:1. D1: Establish the Problem Clearly define the problem, including its symptoms, impact, and urgency.2. D2: Form the Problem-Solving Team Assemble a cross-functional team with expertise relevant to the problem.3. D3: Describe the Problem Gather data and observations to understand the problem in detail and its potential causes.4. D4: Implement and Verify Interim Containment Actions Implement temporary measures to prevent the problem from recurring while the root cause is being investigated.5. D5: Identify the Root Cause Use tools like fishbone diagrams, root cause analysis, or failure mode and effects analysis (FMEA) to identify the true underlying cause of the problem.6. D6: Develop and Implement Permanent Corrective Actions Design and implement long-term solutions to eliminate the root cause and prevent the problem from reappearing.7. D7: Verify Effectiveness of Permanent Corrective Actions Monitor the effectiveness of the implemented solutions to ensure the problem has been resolved.8. D8: Prevent Recurrence Implement measures to prevent the problem from reoccurring, such as revising processes, training employees, or updating documentation.Usage of the 8D Report:The 8D Report is a valuable tool for organizations seeking to improve quality and reduce defects. It can be used in various industries and scenarios, including:Manufacturing defects。
8d报告标准步骤

8d报告标准步骤
8D报告标准步骤是指在处理产品或服务质量问题时,按照8D 方法进行问题分析和解决的一系列步骤。
以下是8D报告的标
准步骤:
1. D1:团队组建
- 识别并组建一个多学科的团队来解决问题。
- 指定一个团队负责人,确保团队有效运作。
2. D2:问题定义
- 描述和定义问题的性质、规模和影响。
- 使用问题陈述工具,如问题描述和问题分类等。
3. D3:紧急措施
- 确定和实施必要的紧急措施,以控制问题的影响范围。
- 评估和调整紧急措施的有效性。
4. D4:根本原因分析
- 使用工具和技术,如鱼骨图、5W1H、5为什么等,来识别
问题的根本原因。
- 采集数据和进行相应的数据分析,以支持根本原因的确定。
5. D5:纠正措施
- 开发和实施根本原因的纠正措施。
- 指定负责人,并确保纠正措施的实施和跟踪。
6. D6:预防措施
- 确定并实施预防措施,以防止同类问题再次发生。
- 进行风险评估,并采取适当的措施降低风险。
7. D7:确认措施效果
- 确认纠正措施和预防措施的效果。
- 评估和验证问题是否已解决,并记录相关数据和结果。
8. D8:固化措施和持续改进
- 确保纠正措施和预防措施已固化到系统和流程中。
- 学习和分享经验,并持续改进质量管理系统。
以上是8D报告的标准步骤,通过按照这些步骤进行分析和解决问题,可以有效地改进产品或服务质量,并避免同类问题再次发生。
8D报告要求说明

8D報告要求說明一﹑客訴/8D報告最重要的是三現﹕現場﹑現時﹑現物﹔1.現物分兩點進行分析﹕a.控制現場﹔b.真因動作發生處。
2.現物是真因線索之一。
二﹑客訴/8D報告的關鍵是驗証﹐有效的驗証是靠對比﹐凡事透過對比才可得到有效的驗証。
三﹑客訴/8D報告的禁忌﹕1.無中生有﹔2.憑空想象﹔3.不可一而多﹔4.教育訓練。
四﹑臨時及長期改善措施是控制問題﹐不讓問題擴大。
五﹑效果比對確認﹕1.源頭管理﹔2.事后管理(臨時手段)。
六﹑驗証方法﹕1.還原驗証(模擬現場)﹔2.實驗比對效果驗証。
七﹑所有的預防需定期檢查﹐而不是隨查。
八﹑預防措施是讓長期措施有效。
為何8D報告中以『問題描述』最為重要:問題描述就是將問題的三現(現場、現物、現實)資料儘可能完整的予以舉証,如此,才能符合態度要客觀的標準,同時,三現資料愈充足,真因就愈容易被正確分析出來。
8D報告三現中:『現實』是指什麼:指記錄;與問題有關的記錄及文件為何『源頭管理』是改善管理問題使成本降低及浪費減少的主要方法﹕在工作上只要源頭正確,自然後續工作就無需再多花成本去彌補源頭的問題與不足,自然會使成本降低及浪費減少。
為何『定期檢查並記錄結果』對長期對策可以達到預防的效果?定期檢查並記錄結果本身就有提醒的作用,如果,再結合控制表的手法,將會使預防的效果更為明顯。
8D報告有效驗証結果是通過什么得來﹕將改善前與改善後的理論值或實驗值做比對為何8D報告中最關鍵的資料是『驗証』:還原驗証法:可証實問題真因的存在性、真實性;失效驗証法:可証實改善方法的有效性、可靠性;由驗証資料中可以得知問題的再發週期性,有助於預防措施的施行。
8D報告的追蹤確認單位指的是那一個單位:品質問題為QA;工作問題為主管單位。
8D報告最重要及最關鍵的資料分別是﹕在內容上最重要的是﹕三現(現場﹑現時﹑現物)在分析上最關鍵的是﹕驗証。
质量8D问题解决标准工作程序与效果评价规范
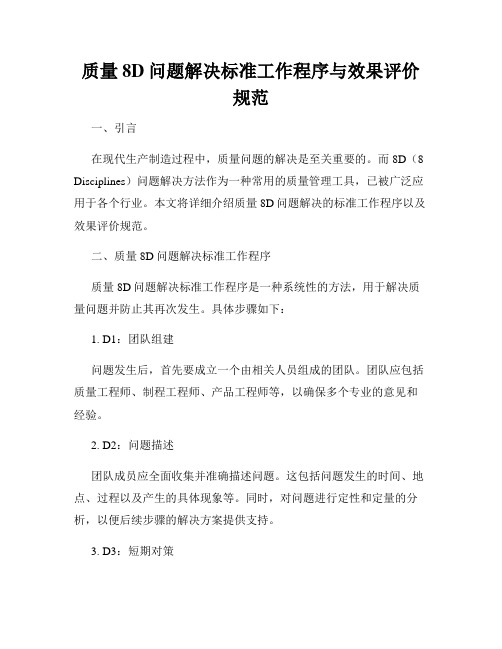
质量8D问题解决标准工作程序与效果评价规范一、引言在现代生产制造过程中,质量问题的解决是至关重要的。
而8D(8 Disciplines)问题解决方法作为一种常用的质量管理工具,已被广泛应用于各个行业。
本文将详细介绍质量8D问题解决的标准工作程序以及效果评价规范。
二、质量8D问题解决标准工作程序质量8D问题解决标准工作程序是一种系统性的方法,用于解决质量问题并防止其再次发生。
具体步骤如下:1. D1:团队组建问题发生后,首先要成立一个由相关人员组成的团队。
团队应包括质量工程师、制程工程师、产品工程师等,以确保多个专业的意见和经验。
2. D2:问题描述团队成员应全面收集并准确描述问题。
这包括问题发生的时间、地点、过程以及产生的具体现象等。
同时,对问题进行定性和定量的分析,以便后续步骤的解决方案提供支持。
3. D3:短期对策在确定问题的具体原因之前,可以通过采取一些短期对策来控制问题的扩散。
这些对策可以包括降低不良品数量、停止不良品流动等。
4. D4:根本原因分析团队应该通过使用5W1H的方法(即什么、为什么、何时、何地、谁、如何)来找出问题的根本原因。
采用鱼骨图、5W1H分析表等工具有助于决定问题根本原因。
5. D5:纠正措施当根本原因确定后,就需要制定纠正措施。
这些措施应着重于解决问题的根本原因,并确保将来不会再次发生类似的问题。
所有纠正措施都应该进行测试和验证。
6. D6:预防措施除了纠正措施外,还应该采取一些预防措施来避免类似的问题再次发生。
这些措施包括设立相应的工艺控制标准、培训相关人员等。
7. D7:效果验证纠正措施和预防措施实施后,应进行效果验证。
这可以通过对相关工艺和产品进行全面检查、检测和测试来完成。
8. D8:经验总结在解决问题后,团队应该进行经验总结和总结。
这样能够为以后类似问题的解决提供经验参考,并进一步提高质量管理水平。
三、效果评价规范为了评价质量8D问题解决方法的效果,可以采用以下几个方面进行评估:1. 解决时间评估解决问题所花费的时间。
8D报告的内容及使用说明

8D报告的内容及使用说明
自查报告。
一、 8D报告的内容。
1. 问题描述,详细描述问题的性质、严重程度和影响范围。
2. 紧急措施,列出已经采取的紧急措施,以减轻问题带来的影响。
3. 问题分析,对问题进行深入分析,找出问题的根本原因。
4. 制定对策,提出解决问题的具体对策,并列出实施计划。
5. 验证对策,对制定的对策进行验证,确保其有效性。
6. 预防措施,提出预防措施,防止问题再次发生。
7. 根本原因分析,对问题的根本原因进行深入分析,并提出改进措施。
8. 结果验证,对改进措施进行验证,确保问题得到彻底解决。
二、使用说明。
1. 填写清晰,在填写8D报告时,要确保内容清晰明了,包括问题描述、对策制定和实施计划等部分。
2. 严格执行,在执行对策和预防措施时,要严格按照报告中的计划进行,确保问题得到彻底解决。
3. 及时更新,对于已经解决的问题,要及时更新8D报告,记录问题的解决过程和结果验证情况。
4. 持续改进,通过8D报告的使用,可以不断总结经验,提高问题解决的效率和质量,实现持续改进的目标。
综上所述,8D报告是一种非常有效的问题解决工具,通过对问题进行全面分析和对策制定,可以有效地解决各类质量问题。
在使用8D报告时,要注意填写清晰、严格执行、及时更新和持续改进,以确保问题得到彻底解决并实现持续改进的目标。
8D报告质量评分标准
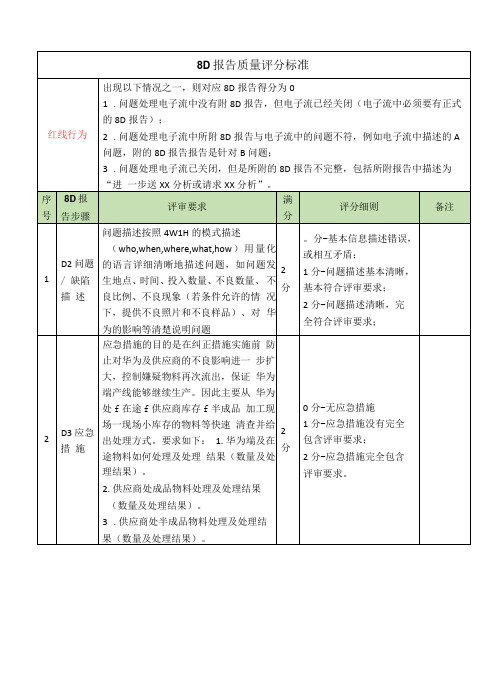
7
分
0分-纠正措施与原因分 析不对应;
2分-纠正措施与原因分 析基本对应(比例超过50%);
5分-纠正措施与原因分 析完全对应,且措施基本 具有可执行性(比例超过80%);
2.供应商处成品物料处理及处理结果 (数量及处理结果)。
3.供应商处半成品物料处理及处理结 果(数量及处理结果)。
2
分
0分-无应急措施
1分-应急措施没有完全 包含评审要求;
2分-应急措施完全包含 评审要求。
3
D4识别问 题根因
7
分
。分-问题现象不能定位 或不清晰;
2分-问题现象定位清晰, 只有根因分析或流出原 因分析之一;有根因分
2
分
。分-基本信息描述错误, 或相互矛盾;
1分-问题描述基本清晰, 基本符合评审要求;
2分-问题描述清晰,完 全符合评审要求;
2
D3应急措 施
应急措施的目的是在纠正措施实施前 防止对华为及供应商的不良影响进一 步扩大,控制嫌疑物料再次流出,保证 华为端产线能够继续生产。因此主要从 华为处f在途f供应商库存f半成品 加工现场一现场小库存的物料等快速 清查并给出处理方式。要求如下:1.华为端及在途物料如何处理及处理 结果(数量及处理结果)。
2.制定纠正措施须具有可执行性,不能 出现加强检验、加强培训等类似不能落 地的措施,针对一些常规措施还需描述 “从什么改善到什么〃,例如CCD机从每 天点检一次改善到每班点检一次(因为 设备点检对于华为供应商来说都是基 本要求,以往就应该做的,所以纠正措 施必须明确以往是什么情况);不合格 纠正措施类型举例:
- 1、下载文档前请自行甄别文档内容的完整性,平台不提供额外的编辑、内容补充、找答案等附加服务。
- 2、"仅部分预览"的文档,不可在线预览部分如存在完整性等问题,可反馈申请退款(可完整预览的文档不适用该条件!)。
- 3、如文档侵犯您的权益,请联系客服反馈,我们会尽快为您处理(人工客服工作时间:9:00-18:30)。
临时措施
备注
G8D-QR代码(如QNM****)- 车型(如CD391)-*******售后问题如下作为参考
ECB/GCR- CD391XXXXXX问题----VIN号命名。
包含发生时间,发生地点,发生数量和批次信息,以及具体现象
D0 针对症状/保护客户整机/整车的发运,或支持CAF的当前生产,如在CAF 临时的跟线100%检查或拒收问题批次零件等
如停止生产或采取100%检查
对应急措施有必要进行评估,并确认应急措施的检出有效性和数量
如工厂经理/或总监
具有Leadship能力的牵头人,能主导整个8D的顺利完成。
包含与问题相关的部门成员
什么零件出了什么问题
根据事实,有数据依据的展示“Is/Is Not”清单,包含What/Where/When/How Big
描述问题发生的时间,受影响的批次,数量,问题的比例及产生问题的模穴或设备等详细量化信息。
附上问题图片
对目前的ICA进行描述,并根据QCM 进行文档化和培训
对ICA经过的验证进行描述,如边界零件/失效零件的有效性验证等。