液态模锻工艺介绍)
液态模锻的工艺过程

液态模锻的工艺过程
嘿,朋友们!今天咱来聊聊液态模锻这个超有意思的工艺过程呀!
你看啊,液态模锻就像是一场神奇的魔法表演。
想象一下,把滚烫的液态金属当作是调皮的小精灵,它们在模具这个大舞台里尽情地翻滚、跳跃。
首先呢,要准备好模具,这模具就像是给小精灵们准备的家,得舒舒服服的才行。
然后把液态金属小心翼翼地倒进模具里,这时候可别手抖哦,不然小精灵们可就不开心啦!
接着呀,压力这个大力士就上场啦!它用力地挤压着液态金属,让它们紧紧地贴合在模具的每一个角落。
就好像是在给这些小精灵们做按摩,让它们乖乖地按照我们想要的形状来变身。
在这个过程中,液态金属也很努力呢!它们从一开始的自由散漫,慢慢变得听话懂事,逐渐成型。
这难道不像是我们小时候,从调皮捣蛋到慢慢懂事的过程吗?
等压力完成了它的任务,液态模锻的作品就差不多出来啦!这时候就像是揭开一场惊喜的面纱,你永远不知道最后会得到一个多么完美的宝贝。
液态模锻出来的东西啊,那质量可真是杠杠的!强度高,性能好,就像是经过了千锤百炼的勇士。
而且它还能制造出各种复杂形状的东西,这可真是太厉害啦!
你说这液态模锻是不是很神奇?它能把普通的液态金属变成一个个让人惊叹的作品。
这就像是我们的生活,只要我们用心去塑造,就能变得精彩无比!不用什么复杂的步骤,不用什么高深的技术,只要我们有那份热情和耐心,液态模锻就能给我们带来意想不到的收获。
所以啊,大家可别小瞧了这个工艺哦,它可是有着大魔力的呢!。
液态模锻工艺介绍资料
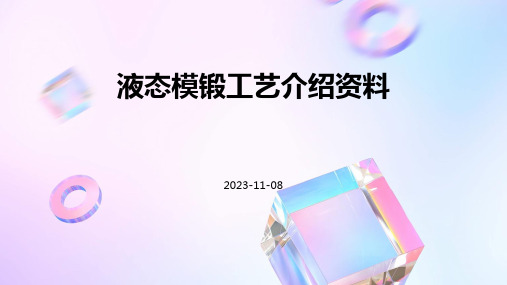
产,以满足不同客户的需求。
技术挑战与难点
模具设计与制造
液态模锻工艺的模具设计与制造是技术难点之一,需要具备高精 度、高强度、高耐热性能等要求。
液态金属流动控制
在液态模锻过程中,液态金属的流动控制是关键技术之一,需要掌 握金属的流动规律和模具填充技巧。
设备投资大
液态模锻工艺需要使用专门的设备 和生产线,相较于传统锻造工艺, 设备投资较大。
液态模锻工艺的改进方向
01
02
03
提高成型精度
通过改进模具设计和制造 工艺,提高液态模锻工艺 的成型精度。
开发新型设备
研发新型的液态模锻设备 和工艺,提高生产效率和 产品质量。
优化生产流程
通过对生产流程进行优化 ,提高生产效率,降低生 产成本。
特点
高生产效率:液态模 锻工艺可以实现批量 生产,提高生产效率 。
制品质量高:液态模 锻工艺可以获得高精 度、高表面质量的金 属制品。
节约材料:液态模锻 工艺采用模具成型, 可以减少材料浪费, 降低成本。
液态模锻工艺的起源与发展
起源
液态模锻工艺起源于20世纪初,最初用于铝合金制品的生产 。
发展
随着科技的不断进步,液态模锻工艺逐渐完善,应用范围也 不断扩大,现在已经成为金属加工领域的重要技术之一。
液态模锻工艺的应用范围
航空航天领域
液态模锻工艺可以用于制造航空航天 领域的铝合金、镁合金等高性能金属 制品。
汽车制造领域
液态模锻工艺可以用于制造汽车车身 、发动机部件等高性能金属制品。
电子通讯领域
液态模锻工艺可以用于制造电子通讯 领域的金属壳体、连接器等精密金属 制品。
液态模锻工艺介绍

h
9
二、液态模锻成形技术的发展概况
液态模锻技术
前苏联1937年
应用于军事及高科技范围 金属构件的制造
该工艺属铸、锻结合工艺,原从事锻压专业的学者称其 为液态模锻,从事铸造专业的人命其名为挤压铸造, 但其内容是一致的
液态金属在模具中经过加压成型,结晶凝固。因而它与铸 锻有着不可分离的“血缘关系”。液态模锻是一种省力、 节能、材料利用率高的先进工艺。液锻件一般很接近工 件最终加工尺寸,质量高,因而为越来越多的国家的学者 和厂家接受和应用。
熔化
浇注
顶出
加压
h
13
四、液态模锻工艺
1、液锻的工艺特点
已凝固金属在压力作用下产生少量塑性变形, 制件轮廓清晰,性能介于锻件和铸件之间
液锻件性能远高于铸件;
整体性能接近锻件,
但能成形较复杂形状的制件,
且省力1/5以上。
h
14
• 金属始终在压力下完成凝固、结晶。好处: 强制补缩,防止出现缩孔缩松 压力直接作用在金属液面上,压力利用率高
相对高度H/a愈大,相对结晶壳就愈长、愈厚, 摩擦阻力愈大,塑性变形时消耗的能量大。
h
52
液态模锻工艺参数
比压力可采用下面的经验公式:
来计算。 铝合金负重轮的比压力p的计算,液锻方式为挤压液锻,
H/a=120/540=0.23,H/a<1时,形状、尺寸影响可忽略不计。
间接液锻时p=K1K2
h
53
液态模锻工艺参数
h1 h2
V收 A0
V液 A0
-合金液体收缩率
V收-合金液收缩的体积
在此过程中,凸模、锻件和模壁间要产生摩擦,消耗
功,当P0为恒定值时,P0在合金液内部产生的压强p不
液态模锻的原理方法和应用

液态模锻的原理方法和应用1. 液态模锻的原理液态模锻是一种先进的金属成形技术,主要利用金属在液态状态下的流动性来实现成形。
其原理主要包括以下几个方面:•金属液态流动性:金属在液态状态下具有较好的流动性,可以在模具内部均匀流动,填充整个模腔。
•压力控制:通过施加一定的液态压力,使金属在模具中流动,并填充模腔。
压力的大小和施加方式对成形质量有重要影响。
•温度控制:液态模锻需要在一定的温度范围内进行,通常要求金属保持在其液态区域内,以保证成形过程的顺利进行。
•冷却控制:液态模锻后,还需要对成形件进行冷却处理,以获得所需的性能和形状。
2. 液态模锻的方法液态模锻的方法有多种,根据实际需求和成形材料的特性选择不同的方法。
下面给出几种常用的液态模锻方法:2.1 直接模锻法直接模锻法是最常用的液态模锻方法之一,其工艺流程简单,适用于各种金属材料。
具体步骤如下:1.预热金属料:将金属料加热至其液态温度以上,使其达到液态状态。
2.填充模具:将液态金属料注入预热好的模具中,使其填充整个模腔。
3.施加压力:在金属料注入模具后,施加一定的液态压力,使金属料在模具内流动并填充模腔。
4.冷却处理:待金属料填充完毕后,进行冷却处理,以获得所需的性能和形状。
2.2 间接模锻法间接模锻法是液态模锻中的另一种常用方法,主要用于形状复杂的零件。
主要步骤如下:1.制备模具:根据所需零件的形状和尺寸,制备相应的模具。
模具可以分为上模和下模两个部分。
2.加热金属料:将金属料加热至其液态温度以上,使其达到液态状态。
3.填充模具:将液态金属料注入上模中,然后合上下模,使金属料填充整个模腔。
4.施加压力:在金属料填充完毕后,施加一定的液态压力,以保证金属料在模具中充分流动,并填充整个模腔。
5.冷却处理:待金属料填充完毕后,进行冷却处理,以获得所需的性能和形状。
2.3 复合模锻法复合模锻法是一种较为复杂的液态模锻方法,主要用于特殊材料或特殊形状的零件。
液态模锻

液态模锻摘要:介绍了液态模锻的概念、特点、分类、研究方法、应用以及国内外的发展状况;同时分别对铝、铜、镁合金的液态模锻成型过程的优缺点进行了分析介绍。
关键词:液态模锻;工艺;应用及发展引言液态模锻是一种介于铸造和模锻之间的金属成形工艺,是使注入模腔的金属在高压下凝固成型,然后施加机械静压力,利用金属铸造凝固成形时易流动和锻造技术使已凝固的封闭硬壳进行塑性变形,使金属在压力下结晶凝固并强制消除因凝固收缩形成的缩孔,以获得无任何铸造缺陷的液锻件[1]。
1液态模锻工艺原理、方法及特点1.1液态模锻工艺原理液态模锻是将一定量的熔融金属液体直接注入金属模膛,随后在机械静压力的作用下,使处于熔融和半熔融的金属液体发生流动并凝固成形,且伴有小量塑性变形,从而获得毛坯或零件。
液态模锻是针对铸造工艺中重力铸造,低压铸造,高压铸造等铸造方法易产生的铸造缺陷,如:疏松,缩孔,气泡等缺点,提出利用提高静压力对模具中的液态或半液态金属进行压力充型和压力下凝固之前,必须建立起工艺所要求的压力,用以避免由于被成形的金属从液态到固态时的体积收缩可能带来的缺陷,液态模锻工艺原理如图液态模锻工艺原理图1.2液态模锻方法1.2.1直接加压法(直接液态模锻)直接加压法液态模锻属于整体加压液态模锻成形方法,一般有两种形式。
(1)平底冲头上直接加压。
当金属液浇入凹模后,平底冲头与凹模形成封闭的型腔,并直接加载到金属液上,很快建立起压力使锻件成形,如图所示:(2)异形冲头直接加压法。
当金属液浇入凹模后,异形冲头与凹模形成封闭型腔在冲头的下行过程中先封闭型腔,并使金属液体流动充满型腔,使锻件成形,如图所示:1.2.2间接加压法。
间接加压法属于局部加压法,是将金属浇入凹模或储液腔后,上模先闭合锁定形成整体型腔,然后通过上冲头挤入金属液,使金属反挤流动充满型腔,使之在压力下凝固成形,如图所示:1.2.3间接挤注法。
间接挤注法是指将浇入到储液腔内的金属液,利用上柱塞或下柱塞,通过浇道挤入到封闭的型腔中获得所需的锻件,如图所示:1.3 液态模锻特点1)机械性能高。
液态模锻
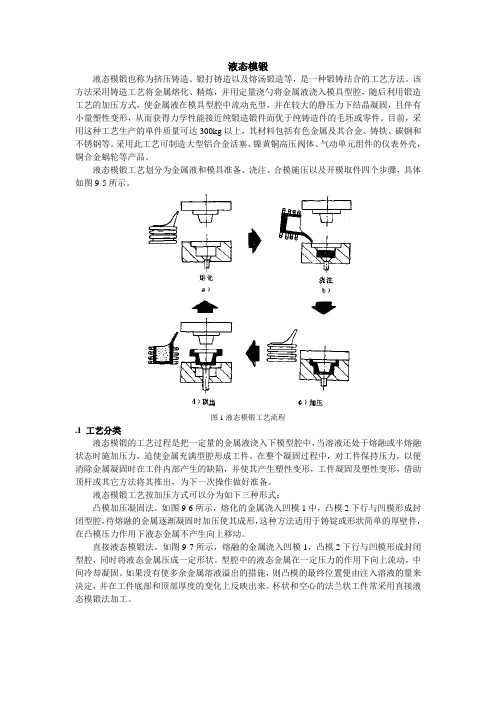
液态模锻液态模锻也称为挤压铸造、锻打铸造以及熔汤锻造等,是一种锻铸结合的工艺方法。
该方法采用铸造工艺将金属熔化、精炼,并用定量浇勺将金属液浇入模具型腔,随后利用锻造工艺的加压方式,使金属液在模具型腔中流动充型,并在较大的静压力下结晶凝固,且伴有小量塑性变形,从而获得力学性能接近纯锻造锻件而优于纯铸造件的毛坯或零件。
目前,采用这种工艺生产的单件质量可达300kg以上,其材料包括有色金属及其合金、铸铁、碳钢和不锈钢等。
采用此工艺可制造大型铝合金活塞、镍黄铜高压阀体、气动单元组件的仪表外壳,铜合金蜗轮等产品。
液态模锻工艺划分为金属液和模具准备、浇注、合模施压以及开模取件四个步骤,具体如图9-5所示。
图1液态模锻工艺流程.1 工艺分类液态模锻的工艺过程是把一定量的金属液浇入下模型腔中,当溶液还处于熔融或半熔融状态时施加压力,迫使金属充满型腔形成工件。
在整个凝固过程中,对工件保持压力,以便消除金属凝固时在工件内部产生的缺陷,并使其产生塑性变形,工件凝固及塑性变形,借助顶杆或其它方法将其推出,为下一次操作做好准备。
液态模锻工艺按加压方式可以分为如下三种形式:凸模加压凝固法。
如图9-6所示,熔化的金属浇入凹模1中,凸模2下行与凹模形成封闭型腔,待熔融的金属逐渐凝固时加压使其成形,这种方法适用于铸锭或形状简单的厚壁件,在凸模压力作用下液态金属不产生向上移动。
直接液态模锻法。
如图9-7所示,熔融的金属浇入凹模1,凸模2下行与凹模形成封闭型腔,同时将液态金属压成一定形状。
型腔中的液态金属在一定压力的作用下向上流动,中间冷却凝固。
如果没有使多余金属溶液溢出的措施,则凸模的最终位置便由注入溶液的量来决定,并在工件底部和顶部厚度的变化上反映出来。
杯状和空心的法兰状工件常采用直接液态模锻法加工。
间接液态模锻法。
如图9-8所示,熔融的金属浇入下模2中,上模1先与下模2组成部分型腔,待凸模3下行时将液态金属挤出形成一定的形状。
液态模锻

(1)力学成形过程
注入金属模膛内的金属液, 在模壁四周和模底 形成一沿敞口的激冷凝固硬壳。随后合模,冲头端面 与金属液接触处, 迅速形成一硬薄层, 新老硬层组 成一封闭腔, 将待凝固金属液包围在腔内( 如图1a 所示) 。显然, 液态模锻下, 金属液被封闭在一硬 壳内, 没有补缩冒口。金属液凝固所发生的体收缩, 只能靠冲头施力, 迫使外壳产生减缩高度的塑性变 形来补偿, 同时, 金属液承受等静压。即塑性变形 结果, 使金属液获得等静压, 而处于等静压下的金 属液, 才有可能获得在压力下结晶凝固的各种属性, 并迅速使凝固前沿的金属液挤入因凝固收缩所造成 的间隙中, 达到完全补缩的目的。每一循环, 使凝 固前沿向金属液内推进一层, 直至过程结束。
主要工艺因素及控制
金属液质量
压力(加压和充型方式) 速度
时间
工艺流程
主要工艺过程:
原材料配制→熔炼→浇注→加压成型→脱模 →冷却→热处理→检验→入库。
熔化:将一定量的金属放入容器内加热至熔化,金 属量视制件而定。 浇注:金属熔化后稍冷却一会,待达到一定温度后再 浇注。 加压:选择一定的比压值与加压速度进行加压。 顶出:必须设置顶出装置。
液态模锻 Liquid Die Forgin g
思考:
铸件通常都有哪些缺陷?
普通锻造通常出现哪些缺陷?
为什么要提出液态模锻?什么是液态模锻? (视频)
主要内容:
成型原理 工艺流程 成型与凝固的特点 主要工艺因素及控制 工艺方法和分类 工艺对设备的要求 锻件分类与设计要点 模具结构设计 模具材料与热处理 液锻模具用(润滑剂)涂料
其他: 力学性能高 由于半凝固状态的金属液在充足的压力下 凝固结晶组织致密晶 粒 细 小所 得 制 件的力学 性能可以接近或达到模锻件的水平 成形性高 液态金属能均匀地填充模具型腔可生产形状 复杂的薄壁零件 成品率高 液态模锻时 加工温度比铸造时低得多 制件 在模内收缩小 且又受三向压应力的影响不会形成气 孔与显微疏松等缺陷 材料利用率高 与模锻相比 由于没毛边及实心孔所损 耗的金属材料 材料利用率可达 以上与压铸工艺相 比液态模锻工艺不需要设置浇口套喷嘴 浇注系统等 辅助消耗的金属材料占
液态模锻——精选推荐

液态模锻液态模锻摘要:介绍了液态模锻的概念、特点、分类、研究⽅法、应⽤以及国内外的发展状况;同时分别对铝、铜、镁合⾦的液态模锻成型过程的优缺点进⾏了分析介绍。
关键词:液态模锻;⼯艺;应⽤及发展引⾔液态模锻是⼀种介于铸造和模锻之间的⾦属成形⼯艺,是使注⼊模腔的⾦属在⾼压下凝固成型,然后施加机械静压⼒,利⽤⾦属铸造凝固成形时易流动和锻造技术使已凝固的封闭硬壳进⾏塑性变形,使⾦属在压⼒下结晶凝固并强制消除因凝固收缩形成的缩孔,以获得⽆任何铸造缺陷的液锻件[1]。
1液态模锻⼯艺原理、⽅法及特点1.1液态模锻⼯艺原理液态模锻是将⼀定量的熔融⾦属液体直接注⼊⾦属模膛,随后在机械静压⼒的作⽤下,使处于熔融和半熔融的⾦属液体发⽣流动并凝固成形,且伴有⼩量塑性变形,从⽽获得⽑坯或零件。
液态模锻是针对铸造⼯艺中重⼒铸造,低压铸造,⾼压铸造等铸造⽅法易产⽣的铸造缺陷,如:疏松,缩孔,⽓泡等缺点,提出利⽤提⾼静压⼒对模具中的液态或半液态⾦属进⾏压⼒充型和压⼒下凝固之前,必须建⽴起⼯艺所要求的压⼒,⽤以避免由于被成形的⾦属从液态到固态时的体积收缩可能带来的缺陷,液态模锻⼯艺原理如图液态模锻⼯艺原理图1.2液态模锻⽅法1.2.1直接加压法(直接液态模锻)直接加压法液态模锻属于整体加压液态模锻成形⽅法,⼀般有两种形式。
(1)平底冲头上直接加压。
当⾦属液浇⼊凹模后,平底冲头与凹模形成封闭的型腔,并直接加载到⾦属液上,很快建⽴起压⼒使锻件成形,如图所⽰:(2)异形冲头直接加压法。
当⾦属液浇⼊凹模后,异形冲头与凹模形成封闭型腔在冲头的下⾏过程中先封闭型腔,并使⾦属液体流动充满型腔,使锻件成形,如图所⽰:1.2.2间接加压法。
间接加压法属于局部加压法,是将⾦属浇⼊凹模或储液腔后,上模先闭合锁定形成整体型腔,然后通过上冲头挤⼊⾦属液,使⾦属反挤流动充满型腔,使之在压⼒下凝固成形,如图所⽰:1.2.3间接挤注法。
间接挤注法是指将浇⼊到储液腔内的⾦属液,利⽤上柱塞或下柱塞,通过浇道挤⼊到封闭的型腔中获得所需的锻件,如图所⽰:1.3 液态模锻特点1)机械性能⾼。
液态模锻的基本原理和优点

液态模锻的基本原理和优点液态模锻是一种利用金属在液态状态下的特殊性能进行塑性变形的加工方法。
与传统的固态锻造或热锻相比,液态模锻具有独特的优点和特点。
液态模锻的基本原理是将金属在其液态区域内进行加热,保持其处于液态状态,然后将其导入模具中进行锻造。
与传统的固态锻造相比,液态模锻的温度较高,材料处于液态状态,因此液态模锻具有以下特点和优点:1. 温度高:在液态模锻过程中,金属被加热到接近或达到其熔点温度。
相对于传统的固态锻造,液态模锻的温度更高,这有助于改善金属的塑性,降低变形阻力,提高变形能力。
2. 无需预制坯料:传统的锻造过程通常需要预制坯料,然后再进行锻造。
而液态模锻可以直接将金属液体导入模具中进行锻造,无需预制坯料,简化了生产工序,提高了生产效率。
3. 成型能力强:液态模锻可以通过调整模具的结构和形状,实现复杂零件的精确成型。
由于液态模锻在金属液体状态下进行,金属流动性好,可以更好地适应模具的形状,实现更复杂的成型。
4. 大幅度节省材料:液态模锻能够有效地减少锻件的加工余量和修整量,降低材料的浪费。
与传统的固态锻造相比,液态模锻可以在更细小的尺寸范围内获得更高的净成形率,提高材料利用率。
5. 减小晶粒尺寸:液态模锻过程中,金属在高温状态下进行塑性变形,可以减小晶粒尺寸,提高材料的强度和塑性。
液态模锻可以获得更小的晶粒尺寸,从而使锻件具有更好的力学性能和高温稳定性。
6. 改善材料性能:液态模锻可以改变材料的组织结构和性能,优化材料的力学性能。
通过精确控制锻造过程中的温度、应变速率和变形程度等参数,可以实现材料微观结构的调控,提高材料的强度、韧性和耐磨性等性能。
液态模锻作为一种高效、精密的金属成形技术,在航空航天、汽车制造、能源领域等许多高端制造领域具有广泛的应用前景和市场需求。
它可以有效地提高锻件的质量和生产效率,降低成本和材料浪费,同时还可以实现对材料性能的优化和提升,满足各种工程和技术要求。
液态模锻工艺流程

液态模锻工艺流程
嘿,朋友们!今天咱来唠唠液态模锻工艺流程这档子事儿。
你说液态模锻啊,就好像是一场奇妙的金属变形大冒险!想象一下,那滚烫的液态金属,就如同充满活力的小精灵,等待着被赋予新的形状和使命。
首先呢,得准备好模具,这模具就像是给小精灵们准备的特别房子,得合适、得精致。
然后把液态金属小心翼翼地倒入模具中,这可不是随随便便倒进去就行的哦,得掌握好火候和速度,不然小精灵们可不乐意呢!
接下来,压力这个大力士就登场啦!它用力地挤压着液态金属,让它们乖乖地按照模具的形状来变身。
这时候啊,就像是在给金属做按摩一样,让它们舒舒服服地变成我们想要的样子。
在这个过程中,可不能有丝毫马虎。
温度要是不合适,那可就糟糕啦,就好比做饭火大了或者小了,那味道能好吗?还有啊,压力要是没控制好,要么压不实,要么压坏了,那不就白折腾啦!
等这一切都完成了,取出来的就是我们期盼已久的成品啦!那可是凝聚了无数心血和技术的宝贝呀。
你看看,液态模锻不就是这么神奇又有趣的过程嘛!
咱再仔细琢磨琢磨,这液态模锻多重要啊!它能让那些普通的金属摇身一变,成为各种厉害的零部件,为我们的生活和工作提供强大的支持。
没有它,好多机器设备都没法好好工作呢!
所以说呀,液态模锻工艺流程可真是个了不起的东西,咱得好好重视它,让它为我们创造更多的价值和惊喜!咱得不断钻研,把这门技术掌握得更精湛,让我们的制造业更上一层楼!怎么样,是不是觉得液态模锻很有意思呀?。
液态模锻工艺介绍资料课件

将选择好的金属材料进行熔炼,得 到适当温度的液态金属。
3. 填充模具
将液态金属倒入预先准备好的模具中。
4. 施加压力
在液态金属冷却和凝固的过程中,通 过专用设备施加高压,使金属在模具 内充分填充并减少缺陷。
5. 冷却和脱模
等待液态金属完全冷却并凝固后, 解除压力,并将产品从模具中取出。
温度控制技术
通过精确控制液态金属和模具的温度,防 止产品出现裂纹、气孔等缺陷。
高压施加技术
通过精确控制施加在液态金属上的压力和 时机,减少产品内部缺陷,提高产品致密 性。
液态模锻工艺中的设备和工具
高压设备
如液压机、机械压力机等,用 于在液态金属凝固过程中施加 高压。
温度控制设备
如冷却水循环系统、温度传感 器等,用于控制液态金属和模 具的温度。
高强度连接技术
液态模锻工艺还可以结合其他工艺,如搅拌摩擦焊等,实现零部件 之间的高强度连接,提高汽车的整体刚度和安全性。
大规模生产效率
液态模锻工艺具备高效、高精度的特点,适用于汽车制造业的大规模 生产,降低生产成本。
液态模锻工艺在航空航天领域的应用
1 2 3
高性能轻质结构件 航空航天领域对材料性能要求极高,液态模锻工 艺可以制造出高性能的轻质结构件,如钛合金机 翼梁、铝合金机身框架等。
复杂构件一次成型 液态模锻工艺可将多个零部件集成为一体,减少 连接件数量,降低构件重量,提高航空航天器的 飞行性能。
精密制造技术 液态模锻工艺可实现高精度、高表面质量的零部 件制造,满足航空航天领域对零部件精度和可靠 性的严格要求。
液态模锻工艺的未来发展趋势和前景
新材料应用拓展
01
随着新材料的不断涌现,液态模锻工艺将适应更多材料的加工
液态模锻操作规程

液态模锻操作规程液态模锻是一种先将金属材料加热至其熔点以上,使其处于液态状态下进行模锻加工的工艺。
与传统的固态模锻相比,液态模锻具有成形能力强、能耗低、锻件表面质量好等优点。
下面将介绍液态模锻的操作规程。
一、液态模锻前的准备工作1. 确定模锻材料:根据产品设计要求和性能要求,选择合适的材料进行液态模锻加工。
2. 确定加热设备:根据材料的熔点和加热效果要求,选择适当的加热设备,如电加热炉、气体加热炉等。
3. 准备模具:根据产品的形状和尺寸,制作或选择合适的模具,并保证模具的准确度和加工质量。
二、液态模锻操作步骤及要点1. 加热:将模具和金属材料放入加热设备中,根据材料的特性和加热曲线,控制加热温度和时间,使金属材料达到液态状态。
要点:加热温度要均匀,避免出现过热或不均匀加热的现象,以免影响液态模锻的质量。
2. 模具涂抹材料:在模腔表面涂抹一层锻造液,以提高液态模锻时模具与金属材料的润滑性和热传导性,防止金属材料粘附在模具上。
3. 倒模:将熔融的金属材料倒入模具中,让金属充分填满模腔。
要点:倒模时要控制速度,避免出现气泡和金属温度过高的现象,以免影响液态模锻的质量。
4. 加塞:在加热后的金属液流动结束之前,用适当的方法对模腔进行加塞,以防止金属液突然凝固而引起冲击和变形。
5. 液态模锻:将已加塞的模具放入专用的模锻机中进行液态模锻。
要点:液态模锻的速度要适中,以免造成金属的扭曲和裂纹。
同时,要根据产品的形状和尺寸合理选择模锻机的压力和速度。
6. 冷却:在液态模锻完成后,立即将模具放入冷却设备中进行快速冷却,使金属迅速固化并保持合适的结构和性能。
三、液态模锻后的处理工作1. 清洗:将液态模锻后的锻件在去除表面的铁鳞和模具杂质后,通过酸洗等方法进行表面清洗。
2. 热处理:根据产品的性能要求,进行适当的热处理,以改善锻件的组织和性能。
3. 机械加工:对液态模锻后的锻件进行必要的机械加工,如修整、车削等,以达到产品的精度和表面质量要求。
液态模锻

成形方法:(1)铸造(Casting):强度小,成本低;容易出现气孔、 缩松;(2)锻造(Forging):强度高,导热性好,成本高,用于强 化发动机;(3)液态模锻:兼有前两者特点,切削少,利用率高, 消除铸造缺陷,提高毛坯质量
液态模锻加压方式
1、平冲头加压 (1)、直接加压压头(成型凸模)直接作
连续铸钢
薄板坯连铸连轧
1-中间包; 2-结晶器; 3-液芯压下; 4-除鳞机; 5-预轧机; 6-剪切机; 7-感应加热炉; 8-热卷箱; 9-事故剪; 10-除鳞机; 11-精轧机; 12-层流冷却; 13-卷取机
薄板坯连铸连轧
1-结晶器; 2-挤压辊; 3-轧制辊; 4-感应炉; 5-除鳞区; 6-轧机; 7-冷却区; 8-卷取机
9、若有芯模时,垂直缸应有足够的提升力量;水平缸也应 有足够的压力,以便施压时能使模具保持紧闭状态,防止金 属液挤出。
几种液态模锻设备:
磁性材料液压机
该压机具有调整、半自动两种工作方式: (1) 调整动作主要 用于安装、调整模具。 (2) 半自动工艺动作: 下活塞顶出 →滑块快下→滑块减速下行→合模延时→自动注料→滑块 慢速 压制 (充磁)→滑块低速压制(充磁) → 保 压 → 泄压延 时(退磁) →脱模→ Ⅰ:滑块回程→下活塞退回 →取坯 Ⅱ: 下活塞退回→滑块回程
铜,延时需更长些。 4、保压时间
升压阶段一旦结束,便进入稳定加压,即保压阶段,直至加压结束 (卸压)的时间间隔,为保压时间。
保压时间长短与合金特性和制件大小有关,可按下述情况进行选用: 1)铝合金制件,壁厚在50mm以下,可取0.5s/mm,壁厚在100mm以 上,可取1.0~1.5s/mm; 2)铜合金制件,壁厚在100mm以下,可取1.5s/mm; 3)黑色金属制件,壁厚在100mm以下,可取1.5s/mm。 5、加压速度 加压速度指加压开始时液压机行程速度。加压速度过快,金属液易卷 入气体和金属液飞溅;过慢自由结壳太厚,降低加压效果。 加压速度的大小主要与制件尺寸有关。对于小件,取0.2~0.4m/s; 对于大件取0.1m/s。
液态模锻PPT课件

1
整体概述
பைடு நூலகம்
概况一
点击此处输入相关文本内容 点击此处输入相关文本内容
概况二
点击此处输入相关文本内容 点击此处输入相关文本内容
概况三
点击此处输入相关文本内容 点击此处输入相关文本内容
2
3.1、液态模锻概述
液态金属模锻(简称液锻)是一种介于铸、锻之间 无切削工艺。其主要过程是:将一定量的合金液浇 入到模具(液锻模)内,在凸模(压头)的压力作 用下使合金液充填型腔——结晶凝固——压力补 缩——塑性变形。从而获得轮廓清晰,表面光洁, 尺寸精确,性能优良的产品。
5
液锻件无铸造中常见的气孔,缩孔,缩松等缺陷,组织 致密,晶粒细小,性能均匀,可靠性高,能生产一般模 锻方法无法生产的形状相当复杂的零件,其性能可与锻 件相似。液锻件还能用热处理方法进一步提高其力学性 能。液锻件表面粗糙度可达Ral.6~3.2,尺寸精度IT9~ IT11,成品率高达95%以上。 液锻艺过程生产率高,从浇注液态金属到获得液锻件, 每一个工件的生产周期一般小于2分钟,台班产200件以 上。工艺操作易于实现机械化、自动化,可节省劳动力 资源和进一步提高生产率。 节能效果显著,产品成本低,某些液锻件无浇冒口系统, 可节省10%以上的液态金属,因而减少了熔炼所消耗的 能源。液锻件一般不需机械加工或只需少量精加工,因 而节省大量的机械加工工时、机床设备投资及机械加工 电力消耗。产品性能高,重量轻。用于车辆及飞行器上
液态金属模锻工艺适应性广,无论铸造合金材料还 是锻造合金材料均可采用液锻工艺生产。可生产各 种壁厚(壁厚≥1.5mm)及壁厚差大的产品。设备 为通用的万能液压机或液态模锻机,无液锻件生产 时,可作其它工作使用。
正是由于液态金属模锻技术具有如此多的优点, 已引起世界各国的高度重视,一些发达国家都有专 门的从事液锻技术研究、开发、生产基地。
液态模锻
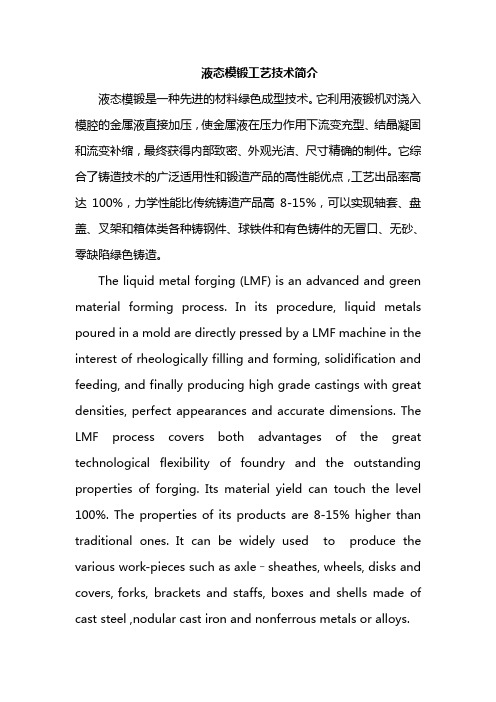
液态模锻工艺技术简介液态模锻是一种先进的材料绿色成型技术。
它利用液锻机对浇入模腔的金属液直接加压,使金属液在压力作用下流变充型、结晶凝固和流变补缩,最终获得内部致密、外观光洁、尺寸精确的制件。
它综合了铸造技术的广泛适用性和锻造产品的高性能优点,工艺出品率高达100%,力学性能比传统铸造产品高8-15%,可以实现轴套、盘盖、叉架和箱体类各种铸钢件、球铁件和有色铸件的无冒口、无砂、零缺陷绿色铸造。
The liquid metal forging (LMF) is an advanced and green material forming process. In its procedure, liquid metals poured in a mold are directly pressed by a LMF machine in the interest of rheologically filling and forming, solidification and feeding, and finally producing high grade castings with great densities, perfect appearances and accurate dimensions. The LMF process covers both advantages of the great technological flexibility of foundry and the outstanding properties of forging. Its material yield can touch the level 100%. The properties of its products are 8-15% higher than traditional ones. It can be widely used to produce the various work-pieces such as axle–sheathes, wheels, disks and covers,forks, brackets and staffs, boxes and shells made of cast steel ,nodular cast iron and nonferrous metals or alloys.图1液态模锻工艺流程图2 各种液态模锻产品示例。
液态模锻技术

液态模锻技术
液态模锻技术是一种先进的金属成形工艺,在金属制造领域具有广泛应用。
该技术主要是利用金属在液态状态下的流动性,通过模具的压力作用来实现金属的塑性变形。
相比于传统的锻造技术,液态模锻技术具有以下优势:
1. 可以制造更加复杂的零部件:液态模锻技术可以制造出更加复杂的零部件,如细节丰富的高精度齿轮、导向轮等,这些零部件不仅具有高精度和高强度,而且能够满足各种复杂工况的要求。
2. 可以提高材料利用率:液态模锻技术可以通过晶粒再结晶控制来实现材料的优化利用,减少废料的产生,提高材料的利用率。
在研发新材料方面,液态模锻技术也能够通过对材料结晶过程的控制来实现材料性能的优化。
3. 可以缩短生产周期:液态模锻技术具有高效、精准和快速的特点,可以在短时间内完成大批量的生产任务,从而缩短生产周期,提高生产效率。
4. 可以降低生产成本:液态模锻技术可以减少模具摩擦和磨损,降低模具成本,同时由于材料利用率的提高和生产周期的缩短,也可以降低生产成本。
液态模锻技术的发展前景非常广阔,有助于推动金属制造业的高质量发展。
- 1 -。
液态模锻工艺介绍资料

注意:液锻方式不同,压力损失不同。 一般正挤压液锻较反挤压液锻压力 损失小。 分型面不同,压力损失有差别。
液态模锻工艺基础
(3)间接液锻过程
本质上与1)、2)两种不同,与立式压铸相似,区别在于 设计原则与工艺参数不同。分三个阶段 第一阶段-压力下充型 压力下,一定速度(0.5~15m/s)通过浇道压入型腔,实现 充型。(压铸是以高速,约15~70m/s ) 第二阶段-压力下结晶 合金液在惯性力作用下压紧模壁,散热、迅速结壳。 第三阶段-压力下结晶 压头的压力使合金液产生很大的压强p,在p的作用下合金 液完全凝固。
液态模锻工艺基础
壳层在较大温差下迅速结晶形成,壳体较薄,尚未有枝晶 形成,组织致密、晶粒细小,性能高。 P0/ P(液锻力),仅起 0 压平液面的作用,其在合金液内部产生的压强(比压力) p / 近似为0。 压平后的液面高度
H0
H0 V液
A0
V液 A0
液态模锻工艺基础
第二阶段-压力下结晶 凸模接触液面后,液锻力从P0’~P0,在其内部产生压强p, 使散热进一步加强,结晶进程加快。 结晶过程中形成的微小空隙得到充分的合金液补缩。 压力下结晶,获得组织致密、晶粒细小的组织。 合金液收缩和凝固,液面下降,凸模要下移h1距离。
2.液锻过程压力的作用 压力对合金物理参数的影响 :合金的熔点、导热率、密 度、结晶潜热 (1)对熔点的影响 压力与合金熔点之间有如下的近似关系,
T熔
T熔 ( V 液- V 固) p 100 4186 . 8 Q 熔
Q熔-单位质量金属的熔化潜热,J/kg。
液态模锻工艺基础
液态模锻
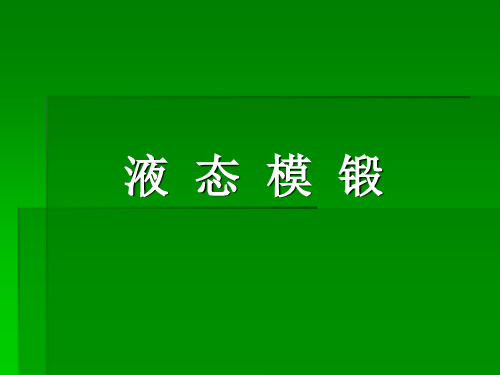
压力铸造示意图
压力铸造零件
②压力铸造时,金属借助浇注系统传递压力,这一 压力虽然较大,但由于浇道较长,其内部金属比铸 件冷却得快,凝固得早,因此液态金属被压入型腔 后,压力不可能始终作用在铸件上直到其完全结晶。 型腔里的金属在压力不够充分的条件下结晶,得不 到补缩的地方会形成缩孔,且晶粒也较粗大。液态 模锻没有浇注系统,当上、下模闭合后,金属便在 充分的压力作用下结晶成形,因而组织致密均一, 晶粒细化。
图1-3 间接液态模 锻法的基本形式 1-上模 2-下模 3-凸模 4-金属熔液 (工件)
因为液压机具有压力和速度均可以控制,操 作容易,施压平稳,不会产生飞溅等现象,可以 保压等特点,所以目前国内液态模锻基本上在液 压机上进行。摩擦压力机的压力和速度较难控制, 且冲击大,无法保压,故很少使用。
凝固以后的组织致密。又因为金属熔液在凝固过程中受
到高压作用,增加了金属的成核率,可以获得细晶粒组
织。此外,由于工件在压力下结晶从而减少或消除了工
件内部疏松、气孔、缩孔等缺陷,又因冷却较快,减少
了化学成分偏析,从而改善了内部组织,达到了改善力
学性能的目的。对于铸铁类的材料,液态模锻还有促进
其石墨球化、细化,改善分布和基体组织等作用。
却不被人们所充分认识。近期,这一工艺正在机械、
舰船、航空、光学仪器和兵器工业等领域迅速扩大
应用。随着工农业生产的飞速发展,已出现和将出
现新的高压金属学理论、新型的专用设备、液态金
属定量浇注装置、联动机构和自动控制等辅助设施,
将会大大提高液态模锻工件的质量和生产率。
1.1 液态模锻的特点与选用
1.1.1 液态模锻的特点
在熔炼合金的同时,要准备好模具。安装凸模和 凹模时必须使它们保持同心,可以通过使凸模和 凹模周围间隙均匀一致来实现。安装调整模具时 应尽可能使其压力中心和液压机柱塞的中心对准, 以避免液压机承受过大的偏心载荷和模具的严重 磨损,利于延长设备和模具寿命使工艺过程顺利 进行。安装时还要考虑工艺过程中操作的方便和 安全。安装完毕后,凸模表面粘着的残留金属层 及润滑剂,必须去除干净,最后用砂纸打光,任 何表面的污垢和粗糙都会严重地影响到工件的表 面质量。例如,在制造玻璃杯铜合金模具时凸模 表面过多的润滑剂会引起工件表面的凹陷等。
液态挤出工艺

液态挤出工艺
液态挤出工艺(又称挤压铸造或液态模锻)是一种铸锻结合的生产工艺。
其核心是将液态金属直接注入一端封闭的挤压筒内,然后通过挤压机施加压力,使金属在压力下成型并伴有微量塑性变形。
液态挤出工艺可以在一定程度上减少铸件缩孔缺陷,提高工件的组织致密性,并通过热处理极大提高力学性能。
挤压铸造(机)可分为卧式和立式两种类型,同时挤压铸造可分为间接挤压和直接挤压两种工艺。
挤压铸造适用的材料广泛,如铝合金、锌合金、铜合金等。
该工艺适用于汽车、摩托车、高铁、通讯、军工、航空、五金等多个领域。
- 1、下载文档前请自行甄别文档内容的完整性,平台不提供额外的编辑、内容补充、找答案等附加服务。
- 2、"仅部分预览"的文档,不可在线预览部分如存在完整性等问题,可反馈申请退款(可完整预览的文档不适用该条件!)。
- 3、如文档侵犯您的权益,请联系客服反馈,我们会尽快为您处理(人工客服工作时间:9:00-18:30)。
壳层在较大温差下迅速结晶形成,壳体较薄,尚未有枝晶
形成,组织致密、晶粒细小,性能高。 P0/ P(0 液锻力),仅起
压平液面的作用,其在合金液内部产生的压强(比压力) p/
近似为0。
压平后的液面高度
H0
V液H 0
A0
V液 A0
液态模锻工艺基础
P 凸第模二接阶触段液-面压后力,下液结锻晶力从P0’~P0,0/ 在其P0内部产生压强p,
凸
式
冲
头
加
压 凹
式
冲
头
加
压
液态模锻工艺方法选择
壁厚差别大的零件 壁厚均匀的零件 形状复杂的零件
正挤压液锻 反挤压液锻 复合挤压间接液锻
六、液态模锻成形方式选择原则
杯形件 小型,形状复杂
凸式冲头 上端面有凸台并带有内腔和孔
间接液态模锻
复合式冲头
六、液态模锻凹模结构形式
六、液态模锻凹模结构形式
七、液态模锻工艺基础
五、液态模锻分类
1、按金属流动方式
(1)静压液锻
合金液不产生大量的流动,液锻形状主要靠浇注时定 型。压力的作用主要是加速(影响)合金液的凝固并产 生塑性变形。分单、双向静压液锻。
单向液锻 h/d≤5 双向液锻 h/d>5
液态模锻分类 (2)挤压液锻
液锻时,浇入的合金液在凸模作用下迅速流动、充型,接 着在高压下凝固和产生少量的塑性变形 (1)正挤压液锻。 (2)反挤压液锻。(3)复合挤压液锻。
塑性成形方法
优点 塑性成形方法
缺点
零件组织致密,强度、 塑性高
高质量的零件表面和尺 寸精度
不能成形较复杂外形状 的零件
受施压和取件的约束, 只能成形与施压方向一 致,简单形状的内孔, 不能成形零件的侧内孔
相对铸造成型,成本较 高
金属的成形(成型)方法
模锻视频
金属体积成形方法分类
二、液态模锻成形技术的发展概况
液态模锻成形
我国自1958年就开始进 行液态模锻的研究工作
70年代,此项工作发展 得更快些,采用这项工 艺制成了大型铝合金活 塞,镍黄铜高压阀体, 气动单龙组合的仪表外 壳和铜合金蜗轮等产品
60年代中期己用于铝合 金仪表零件等生产
80年代以后,该工艺又得到较大 发展,以钢平法兰为代表的黑色 金属液态模锻技术进入生产应用
液态模锻
一、金属的成形(成型)方法
金属坯料
机械加工 焊焊接接 凝固成形 塑性成形
重力铸造 差压铸造 离心铸造 压力铸造
砂型 金属型 熔模
体积成形
板材成形
锻造 挤压 轧制 粉末
冲压 旋压 电磁 内高压
自由锻
模锻
金属的成形(成型)方法
压力铸造设备及成形示意图
金属的成形(成型)方法
离心铸造设备及成形示意图
领域。
液态模锻成形
液态模锻工艺过程是将液态金属直接浇到模具型 腔,然后在较高压力下使其迅速充满型腔,凝固 并产生少量的塑性变形,从而获得轮廓清晰,表 面光洁,尺寸精确、晶粒细小、组织致密、机械 性能优良的制件。
金属熔炼 模具准备
浇注
液锻
脱模
模具复位,喷涂料
产品
三、液态模锻工艺流程
熔化
浇注
顶出
加压
液态模锻与常规模锻的区别
毛坯与模膛形状基本一致,塑性变形量 小,不会产生锻造流线 适于成形复杂形状,且所需设备吨位大 幅度降低
液态模锻的适用范围
各种金属、非金属、复合材料 有色金属取得广泛应用(尤其铝合金) 特别适合于纤维或颗粒增强复合材料 适用于复杂形状、对力学性能有一定要 求的零件 壁厚不能太薄,也不能太厚(5~50mm)
1.液锻过程
(1)静压液锻过程
分四个阶段: 第一阶段-结壳
液态金属浇入模具后,由于具有一定粘度,液面呈现 凸、凹不平,在静压力作用下迅速压平;合金液在低温 模壁强烈散热作用下沿模壁迅速结晶(凝固),形成外 壳;随时间增长,外壳层不断增厚,固液相间的温差不 断减小,结壳速度逐渐减慢。
液态模锻工艺基础
液态模锻技术
前苏联1937年
应用于军事及高科技范围 金属构件的制造
该工艺属铸、锻结合工艺,原从事锻压专业的学者称其 为液态模锻,从事铸造专业的人命其名为挤压铸造, 但其内容是一致的
液态金属在模具中经过加压成型,结晶凝固。因而它与铸 锻有着不可分离的“血缘关系”。液态模锻是一种省力、 节能、材料利用率高的先进工艺。液锻件一般很接近工 件最终加工尺寸,质量高,因而为越来越多的国家的学者 和厂家接受和应用。
金属的成形(成型)方法
差压铸造设备及成形示意图
铸造成形方法
机械 加工
有切削, 材料有损耗
能够成型较复 杂形状的零件
材料加工工程通常指 金属通过液态流动成型 或通过固态塑性变形获 得近净金属零件的成形 (成型)方法,即铸、 锻、焊,特点少无切削。
成本低
铸造 成形
适用于流动性 好的金属材料
零件内部易产 生缩孔、疏松 等缺陷,一般 不能热处理, 强度、塑性低
与立式压铸相似,不同点:浇道短、截面大 ,充型速度低,保压时间长,能生产壁厚较 大、形状复杂的产品,充型时不会有气体卷 入。
加压前
加压后
平冲头间接加压
液态模锻分类
平
2、按加压冲头形状分
冲 头
类
直
(1)平冲头加压
接
加
压
实心制件
平
冲
头
间
接
加 压
加压前
加压后
平冲头间接加压
通孔制件
液态模锻分类
(2)异形冲头加压
正挤压液锻
反挤压液锻
液态模锻分类
复合挤压液锻 挤压液锻的特点:
在压力下充型的合金液流动好,较易获得轮廓清晰、 表面光洁的制件,初生的树枝晶在流动中破碎形成大量 的晶核,可获得细晶组织,最后在高压下凝固核塑性变 形,产品组织致密,性能高。
液态模Байду номын сангаас分类
(3)间接液态模锻
合金液在压力作用下,通过内浇道压入型腔、充 型、凝固,获得产品的液锻方式,叫间接液锻。
四、液态模锻工艺
1、液锻的工艺特点
已凝固金属在压力作用下产生少量塑性变形, 制件轮廓清晰,性能介于锻件和铸件之间
液锻件性能远高于铸件; 整体性能接近锻件, 但能成形较复杂形状的制件, 且省力1/5以上。
• 金属始终在压力下完成凝固、结晶。好处: 强制补缩,防止出现缩孔缩松
压力直接作用在金属液面上,压力利用率高
使散热进一步加强,结晶进程加快。 结晶过程中形成的微小空隙得到充分的合金液补缩。 压力下结晶,获得组织致密、晶粒细小的组织。 合金液收缩和凝固,液面下降,凸模要下移h1距离。
• 与铸件比无浇道系统和冒口,节材10%以上。 与锻件比无飞边。
• 能成形复杂制件,主要靠流动成形,对模具磨 损小
• 模具工作温度高,成形黑色金属时寿命短
液态模锻与压铸的区别
液态金属注入模腔的方式不同 低速浇入,排气良好 压力传递方式不同 压力直接作用并始终保持 组织性能不同 组织细密,力学性能提高