如何消除铸钢件s,p含量高的问题
铸钢件质量分析及质量改进措施
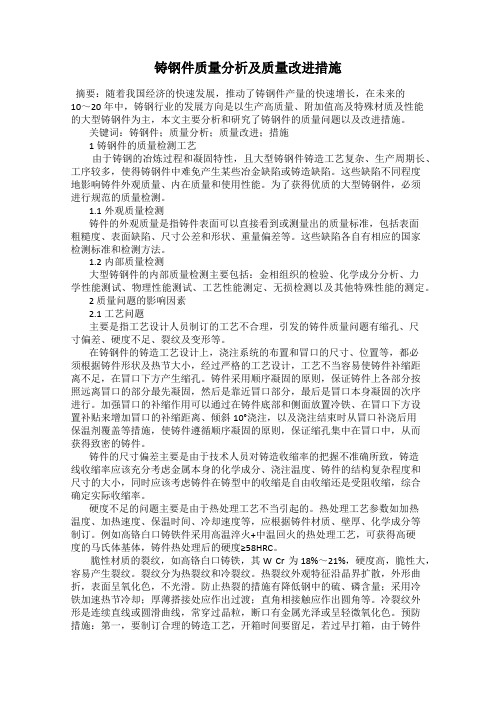
铸钢件质量分析及质量改进措施摘要:随着我国经济的快速发展,推动了铸钢件产量的快速增长,在未来的10~20年中,铸钢行业的发展方向是以生产高质量、附加值高及特殊材质及性能的大型铸钢件为主,本文主要分析和研究了铸钢件的质量问题以及改进措施。
关键词:铸钢件;质量分析;质量改进;措施1铸钢件的质量检测工艺由于铸钢的冶炼过程和凝固特性,且大型铸钢件铸造工艺复杂、生产周期长、工序较多,使得铸钢件中难免产生某些冶金缺陷或铸造缺陷。
这些缺陷不同程度地影响铸件外观质量、内在质量和使用性能。
为了获得优质的大型铸钢件,必须进行规范的质量检测。
1.1外观质量检测铸件的外观质量是指铸件表面可以直接看到或测量出的质量标准,包括表面粗糙度、表面缺陷、尺寸公差和形状、重量偏差等。
这些缺陷各自有相应的国家检测标准和检测方法。
1.2内部质量检测大型铸钢件的内部质量检测主要包括:金相组织的检验、化学成分分析、力学性能测试、物理性能测试、工艺性能测定、无损检测以及其他特殊性能的测定。
2 质量问题的影响因素2.1工艺问题主要是指工艺设计人员制订的工艺不合理,引发的铸件质量问题有缩孔、尺寸偏差、硬度不足、裂纹及变形等。
在铸钢件的铸造工艺设计上,浇注系统的布置和冒口的尺寸、位置等,都必须根据铸件形状及热节大小,经过严格的工艺设计,工艺不当容易使铸件补缩距离不足,在冒口下方产生缩孔。
铸件采用顺序凝固的原则,保证铸件上各部分按照远离冒口的部分最先凝固,然后是靠近冒口部分,最后是冒口本身凝固的次序进行。
加强冒口的补缩作用可以通过在铸件底部和侧面放置冷铁、在冒口下方设置补贴来增加冒口的补缩距离、倾斜10°浇注,以及浇注结束时从冒口补浇后用保温剂覆盖等措施,使铸件遵循顺序凝固的原则,保证缩孔集中在冒口中,从而获得致密的铸件。
铸件的尺寸偏差主要是由于技术人员对铸造收缩率的把握不准确所致,铸造线收缩率应该充分考虑金属本身的化学成分、浇注温度、铸件的结构复杂程度和尺寸的大小,同时应该考虑铸件在铸型中的收缩是自由收缩还是受阻收缩,综合确定实际收缩率。
铸造工艺缺陷及解决措施
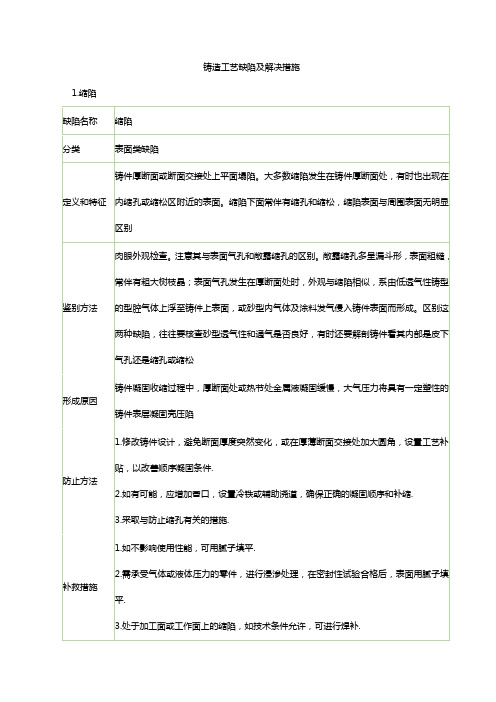
8.铸件开箱落砂太晚,形成固态热粘砂,尤其是厚大铸件和高熔点合金铸件.
9.金属液流动性好、表面张力低。例如,铜合金中磷、铅含量过高,铸钢中磷、硅、锰含量过高.
10.树脂砂型、芯表面未刷涂料或涂料质量差,涂层厚薄不均,浇注时砂粒间树脂膜气化,形成毛细通道,在金属液静压力、蒸气压和表面张力作用下,金属液或金属蒸气渗入毛细通道,形成机械粘砂.
补救措施
概率因子
0.3
缺陷名称
脉纹
分类
多肉类缺陷
定义和特征
鉴别方法
形成原因
涂料过薄或性能不良,型芯开裂后,涂料熔融物填充不良.
防止方法
保证涂料的质量及厚度,在涂料中加入 2 % 氧化铁粉.
补救措施
概率因子
0.3
5.未浇满
缺陷名称
未浇满
分类
残缺类缺陷
定义和特征
鉴别方法
形成原因
除了液态金属不足的因素而外浇注工的操作也很重要.
11.对于大型厚壁铸件,适当提早开箱,加快铸件冷却,以防止固态粘砂.
12.采用表面光洁的模样和芯盒.
补救3.电化学清砂,尤其适用于清除铸件深腔和精密铸件的严重粘砂
概率因子
7.抬型/抬箱
缺陷名称
抬型/抬箱
分类
多肉类缺陷
定义和特征
铸件在分型面部位高度增大,并伴有厚大飞翅
鉴别方法
定义和特征
存在于铸件内的严重的空壳状残缺。有时铸件外形虽较完整,但内部金属已漏空,铸件完全呈壳状,铸型底部残留有多余金属
鉴别方法
型漏是铸件内部严重的空壳状残缺,铸件轮廓通常完整。
形成原因
铸钢件质量保证措施
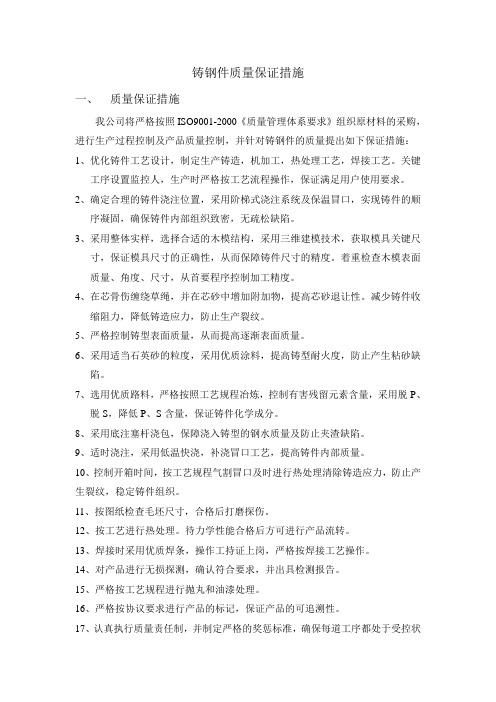
铸钢件质量保证措施一、质量保证措施我公司将严格按照ISO9001-2000《质量管理体系要求》组织原材料的采购,进行生产过程控制及产品质量控制,并针对铸钢件的质量提出如下保证措施:1、优化铸件工艺设计,制定生产铸造,机加工,热处理工艺,焊接工艺。
关键工序设置监控人,生产时严格按工艺流程操作,保证满足用户使用要求。
2、确定合理的铸件浇注位置,采用阶梯式浇注系统及保温冒口,实现铸件的顺序凝固,确保铸件内部组织致密,无疏松缺陷。
3、采用整体实样,选择合适的木模结构,采用三维建模技术,获取模具关键尺寸,保证模具尺寸的正确性,从而保障铸件尺寸的精度。
着重检查木模表面质量、角度、尺寸,从首要程序控制加工精度。
4、在芯骨伤缠绕草绳,并在芯砂中增加附加物,提高芯砂退让性。
减少铸件收缩阻力,降低铸造应力,防止生产裂纹。
5、严格控制铸型表面质量,从而提高逐渐表面质量。
6、采用适当石英砂的粒度,采用优质涂料,提高铸型耐火度,防止产生粘砂缺陷。
7、选用优质路料,严格按照工艺规程冶炼,控制有害残留元素含量,采用脱P、脱S,降低P、S含量,保证铸件化学成分。
8、采用底注塞杆浇包,保障浇入铸型的钢水质量及防止夹渣缺陷。
9、适时浇注,采用低温快浇,补浇冒口工艺,提高铸件内部质量。
10、控制开箱时间,按工艺规程气割冒口及时进行热处理清除铸造应力,防止产生裂纹,稳定铸件组织。
11、按图纸检查毛坯尺寸,合格后打磨探伤。
12、按工艺进行热处理。
待力学性能合格后方可进行产品流转。
13、焊接时采用优质焊条,操作工持证上岗,严格按焊接工艺操作。
14、对产品进行无损探测,确认符合要求,并出具检测报告。
15、严格按工艺规程进行抛丸和油漆处理。
16、严格按协议要求进行产品的标记,保证产品的可追溯性。
17、认真执行质量责任制,并制定严格的奖惩标准,确保每道工序都处于受控状态。
18、我公司派专人见证整个生产过程,必要时请专业监理工程师抽样旁站。
二、铸钢节点生产工艺2.1生产工艺流程:2.2主要工序工艺简述:大型钢结构建筑铸钢节点,属于钢结构建筑中的重要焊接结构件,在保证其正确优异的化学成分基础上,通过一定的热处理工艺来保证其良好的机械性能;同时亦需要有良好的焊接性能及结构外型的美观、精致等特征。
改善铸铁件整体性能的常用热处理方法

改善铸铁件整体性能的常用热处理方法改善铸铁件整体性能常有消除白口退火,提高韧性的球墨铸铁退火,提高球墨铸铁强度的正火、淬火等。
1.消除白口退火普通灰口铸铁或球墨铸件表面或薄壁处在铸造过程中因冷却速度过快出现白口,铸铁件无法切削加工。
为消除白口降低硬度常将这类铸铁件重新加热到共析温度以上(通常880~900℃),并保温1~2h(若铸铁Si含量高,时间可短)进行退火,渗碳体分解为石墨,再将铸铁件缓慢冷却至400℃-500℃出炉空冷。
在温度700-780℃,即共析温度附近不宜冷速太慢,以便渗碳体过多的转变为石墨,降低了铸铁件强度。
2.提高韧性的球墨铸铁退火球墨铸铁在铸造过程中此普通灰口铸铁的白口倾向大,内应力也较大,铸铁件很难得到纯粹的铁素体或珠光体基体,为提高铸铁件的延性或韧性,常将铸铁件重新加热到900-950℃并保温足够时间进行高温退火,再炉冷到600℃出炉变冷。
过程中基体中的渗碳体分解出石墨,自奥氏体中析出石墨,这些石墨集聚于原球状石墨周围,基体全转换为铁素体。
若铸态组织由(铁素体+珠光体)基体,以及球状石墨组成,为提高韧性,只需将珠光体中渗碳体分解转换为铁素体及球状石墨,为此将铸铁件重新加热到700-760℃的共析温度上下经保温后炉冷至600℃出炉变冷。
3.提高球墨铸铁强度的正火球墨铸铁正火的目的是将基体组织转换为细的珠光体组织。
工艺过程是将基体为铁素体及珠光体的球墨铸铁件重新加热到850-900℃温度,原铁素体及珠光体转换为奥氏体,并有部分球状石墨溶解于奥氏体,经保温后空冷奥氏体转变为细珠光体,因此铸件的强度提高。
4.球墨铸铁的淬火并回火处理球墨铸造件作为轴承需要更高的硬度,常将铸铁件淬火并低温回火处理。
工艺是:铸件加热到860-900℃的温度,保温让原基体全部奥氏体化后再在油或熔盐中冷却实现淬火,后经250-350℃加热保温回火,原基体转换为回火马氏体及残留奥氏体组织,原球状石墨形态不变。
如何消除铸钢件s,p含量高的问题
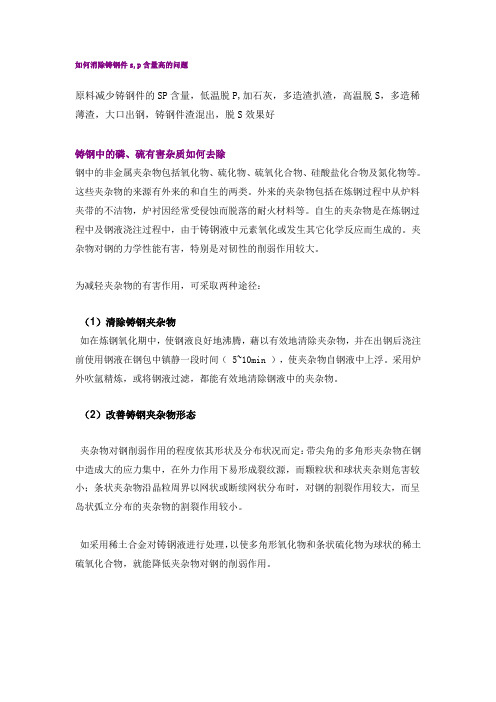
如何消除铸钢件s,p含量高的问题
原料减少铸钢件的SP含量,低温脱P,加石灰,多造渣扒渣,高温脱S,多造稀薄渣,大口出钢,铸钢件渣混出,脱S效果好
铸钢中的磷、硫有害杂质如何去除
钢中的非金属夹杂物包括氧化物、硫化物、硫氧化合物、硅酸盐化合物及氮化物等。
这些夹杂物的来源有外来的和自生的两类。
外来的夹杂物包括在炼钢过程中从炉料夹带的不洁物,炉衬因经常受侵蚀而脱落的耐火材料等。
自生的夹杂物是在炼钢过程中及钢液浇注过程中,由于铸钢液中元素氧化或发生其它化学反应而生成的。
夹杂物对钢的力学性能有害,特别是对韧性的削弱作用较大。
为减轻夹杂物的有害作用,可采取两种途径:
(1)清除铸钢夹杂物
如在炼钢氧化期中,使钢液良好地沸腾,藉以有效地清除夹杂物,并在出钢后浇注前使用钢液在钢包中镇静一段时间( 5~10min ),使夹杂物自钢液中上浮。
采用炉外吹氩精炼,或将钢液过滤,都能有效地清除钢液中的夹杂物。
(2)改善铸钢夹杂物形态
夹杂物对钢削弱作用的程度依其形状及分布状况而定:带尖角的多角形夹杂物在钢中造成大的应力集中,在外力作用下易形成裂纹源,而颗粒状和球状夹杂则危害较小;条状夹杂物沿晶粒周界以网状或断续网状分布时,对钢的割裂作用较大,而呈岛状弧立分布的夹杂物的割裂作用较小。
如采用稀土合金对铸钢液进行处理,以使多角形氧化物和条状硫化物为球状的稀土硫氧化合物,就能降低夹杂物对钢的削弱作用。
铸坯全氧含量偏高的原因调查与解决措施

第4期总第218期冶金丛刊Sum.218 No.42 01 5 年8 月 METALLURGICAL COLLECTIONS August 2 0 15铸坯全氧含量偏高的原因调查与解决措施刘文浩贾黎杰杜亚伟贺瑞飞(安阳钢铁集团有限责任公司,河南安阳455004)摘要针对某钢厂板坯全氧含量偏高进行了炼钢方面与连铸方面相关原因的调查工作。
调查分析结果表明,连 铸中间包挡墙位置设置存在较大的工艺问题,对此进行了针对性的水模拟实验,认为将高墙位置移到距大包长水 口 1 000 mm附近,即A= 1 000 mm$B=485 mm、h=280 mm$H=335 mm,可保证钢水最短停留时间较长的同时中 包死区比率相对较小,促进了夹杂物的充分上浮。
改进后铸坯全氧含量由0.0115%降到了 0.0057%,降低了50. 43 %,效果显著。
关键词全氧含量;铸坯;挡墙;水模拟实验;原因调查;解决措施中图分类号:TF777文献标识码:A文章编号:1671 -3818(2015)04 -0045 -04INVESTIGATION OF REASONS FOR HIGHER TOTALOXYGEN CONTENT IN SLAB AND SOLUTIONSLiu W enhao Jia Lijie Du Yawei H e Ruifei(Anyang Iron and Steel Group Co.,L td.,Anyang455004,Henan)A bstract Investigations of reasons for higher total oxygen content in slab were carried out from steelmaking and continuous casting asjDects in a certain steel mill.The investigation a showed that tlie position setting of tlie retaining wall had a big process problem,and targeted water simulation tests were conducted.Tests thought tliat if wall location was moved to about 1000 mm(A= 1 000mm$B = 485 mm$h = 280 mm$H = 335 mm)near the long nozzle,longer shortest stay time of moltensteel and relatively smaller dead zone ratio in the tundisli at tlie same time can be guaranteed tp fully promote the inclusion floating.The total oxygen content in slab decreased from 0.0115% to 0. 0057%,reduced by50. 43%after improvement,the effect was remarl^able.Key words Total oxygen content;Slab;Retaining wall;Water simulation test;Reason in Solution0 刖z某钢厂在2014年02月份到08月份,3#板坯连 铸机铸坯出现全氧含量偏高现象,涉及钢种包括该 机组的普碳系列、低合金系列、耐候系列及管线系 列,铸坯全氧含量高于0.0085%,最高达到了0.0130%以上。
常见铸造缺陷的成因与消除

常见铸造缺陷的成因与消除关注我们请点后面铸造工业网昨天任何铸造缺陷都直接影响着企业的经济效益与社会效益。
可惜的是,未有一个铸造厂是没有铸造缺陷的。
现列出几种主要(常见)的铸造缺陷,如气孔,缩孔,夹渣及球化不良等来分析它们产生的原因并提出消除措施,与诸君共议。
一气孔(Gas hole)1、产生原因金属液中的气体未彻底释放出来和铸型内的气体侵入进金属液中,从而滞留在凝固后的铸件之内(图1)。
(1)金属液中的气体来源 g 劣质炉料含泥沙、油垢、锈蚀及湿气等,熔炼中生成大量的O、H、N等气体和渣釉;炉温低;精练不够;浇注温度低,浇注时间长及浇注速度慢、浇包潮湿等。
上述因素,都促使金属液表面过早形成氧化膜而凝固,气体虽然挣扎着向外逃逸但却无法实现。
反映在铸件上则成为向上的“梨形”气泡,梨把朝内。
气孔表面光滑。
通常称这种气孔为“析出性气孔”(图2)。
在薄壁件的表皮下或外观形成密集的小圆孔或针孔(图3)。
(2)型腔内气体来源砂型水分≥4.5%,死灰>12%,透气性差;水玻璃砂未干透(仅吹C O2是不够的);树脂砂的树脂量>1.8%,固化剂量也多;消失模厚大,比重大又未干透,涂料层>2㎜且未干透;粗大砂芯樁的过实,未中空,气体未引出型外;合箱后等待浇注时间>8h,或过夜等,使铸型和砂芯返潮。
(3)工艺设计不合理直浇道粗大,金属液不能很快充满或断流而将气体卷入;内浇口喷射,金属液紊乱;冒口处低位,排气孔少;底注,温度场为上低下高,导致金属液迅速形成氧化膜而快速凝固。
上述(2)、(3)所产生的气体在排气不畅且型内压力大的情况下,气体被卷入或钻入未凝固的金属液内。
通称这种气孔为“侵入性气孔”(图4)。
气孔也似梨状而梨把朝外。
2 消除方法消除金属液中可能产生气体的一切因素;提供气体从金属液内和铸型(砂芯)中容易逸出的机会或条件。
应当着重指出的是,彻底排出金属液中的气体是第一位的!具体做法:选用优质、干净干燥的炉料,提高熔炼温度(灰铁1520℃,铸钢1650℃,不锈钢1680℃),充分精炼脱气与静置,高温且快速浇注,消失模浇注温度比砂铸高50℃,因为泡沫燃烧是一个吸热过程,充型前沿的金属液温降比随后之金属液的温降大得多。
铸钢件常见质量问题及主要影响因素汇总

2.防止缩孔缩松的措施 (1)合适的冒口位置和尺寸 冒口放在铸件厚大部位,最好是上部; 冒口的尺寸要足够大,使得它凝固时间长,铸件全部凝固了,冒口中心 部分还要处于液态; 冒口有足够的液体钢水补充铸件体积收缩的需要。 (2)冒口的补缩距离 钢水在凝固过程中凝固层出现固液共存,影响钢水的流动,补缩受阻, 因此冒口的补缩距离(范围)受到限制。 (3)冒口颈和冒口补贴 冒口与铸件之间的连接部分称冒口颈(边冒口)和冒口补贴(顶冒口), 目的是让冒口中的钢水始终有通道进入铸件,满足铸件的需要,是就要 求冒口颈和冒口补贴有一定的形状尺寸。
(1)铸件设计和工艺上采取措施改变和减少局部热节;
(2)工艺上采取防裂纹,冷铁; (3)提高钢水质量,减少夹杂物; (4)气割、碳刨、焊补采用预热、后热去应力措施。 -20-
人有了知识,就会具备各种分析能力, 明辨是非的能力。 所以我们要勤恳读书,广泛阅读, 古人说“书中自有黄金屋。 ”通过阅读科技书籍,我们能丰富知识, 培养逻辑思维能力; 通过阅读文学作品,我们能提高文学鉴赏水平, 培养文学情趣; 通过阅读报刊,我们能增长见识,扩大自己的知识面。 有许多书籍还能培养我们的道德情操, 给我们巨大的精神力量, 鼓舞我们前进。
-2-
C.炉内的化学成分变化
已化验合格的钢水长时间放在炉内,成分会变化。 D.出钢时钢水成分的变化,某些元素如:Si,Mn, Cr会烧损
E.钢水包对钢水成分的影响
前一包中残余钢水会污染下一包的钢水成分,特别是产生含碳量低的不 锈钢时很明显,碳容易上升,要求浇注后钢水包一定要用氧气吹干净,
不能结包底,结包壁,也不要留有残渣,钢包一定要烘烤好(800℃以
3.防止方法
外来夹渣:一是减少夹杂物的来源,二是浇注前镇静。包
球铁450-10疏松原因和解决方法

球铁450-10疏松相关问题形成的原因有;①凝固温度间隔宽的合金具有体积凝固(糊状凝固)特性,补缩困难,易形成疏松;②浇注温度过低易产生疏松;③合金凝固温度间隔过宽,糊状凝固倾向强,使低熔点成分最后凝固时得不到有效补缩,易形成疏松④合金中杂质和溶解的气体过多,在合金凝固过程中杂质和析出的气体被推向结晶前沿,阻塞补缩通道,使疏松加重;⑤合金中缺少晶粒细化元素,凝固组织晶粒粗大,易阻塞补缩通道,形成疏松;⑥浇注系统、冒口、冷铁、补贴等设置不当,使铸件在凝固时得不到有效补缩;⑦铸件结构不合理,壁厚变化突然,孤立的热节得不到补缩;⑧冒口数量、尺寸、形状、设置部位以及冒口与铸件连接不合理,补缩效果差;⑨内浇道尺寸或位置不当,使铸件不能顺序凝固或在铸件中形成局部热节;⑩合金中易形成低熔点相的杂质元素含量过多,使凝固温度间隔增大。
例如,铸铁中硫、磷含量过多时会在凝固后期形成低熔点共晶,使铸件产生疏松。
防止办法:①改进球墨铸铁件工艺设计,合理设置浇冒口系统、冷铁和补贴,保证铸件在凝固过程中获得有效补缩;②改用补缩效率高的保温冒口、发热冒口、压力冒口和电热冒口;③改进铸件结构设计,减小铸件壁厚差,使铸件壁厚与薄壁部位平滑过渡,尽量避免形成孤立热节。
在铸件的孤立热节等冒口补缩距离达不到的部位,采用内、外冷铁以加快该部位的凝固速度;④对重要铸件,可在计算机数值模拟基础上进行计算机辅助设计,优化铸件结构和铸造工艺;⑤加强合金精炼,净化金属液,减少合金中溶解气体和低熔点杂质的含量,以利于凝固补缩;⑥采用悬浮浇注技术,在浇注过程中往金属液中随流加入晶粒细化剂或微冷铁,加快合金凝固速度并细化晶粒;⑦提高铸型刚度和强度,防止型壁位移和抬型;⑧调整合金成分,进行良好的变质或孕育处理,缩小合金的凝固温度间隔,提高其铸造性能,以利于型内金属液向内浇道和冒口方向顺序凝固,提高浇冒口系统的补缩效果;⑨凝固温度间隔宽的合金铸件,例如球墨铸铁件,宜采用均衡凝固工艺,充分利用凝固时的石墨化膨胀补偿铸铁的液态收缩和凝固收缩;⑩降低球墨铸铁的硫、磷含量和残留镁量,用稀土镁合金处理时,应适当提高碳、硅含量;降低浇注温度和浇注速度,延长浇注时间;点冒口。
铸件缺陷修复
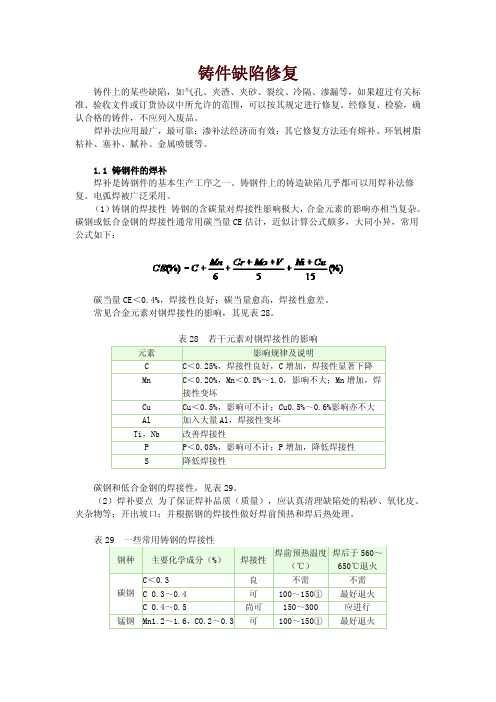
(3)浸渗工艺及设备 浸渗工艺与浸渗方法和浸渗剂有关,通常分为三阶段:前处 理浸渗,后处理在各种浸渗工艺中,硅酸盐真空浸渗最常用。
1)硅酸盐真空浸渗工艺(表 34)
表 34 硅酸盐真空浸渗工艺
阶段
工艺过程及要点
1.脱脂:在有加热装置的脱脂容器中,一般用 60~80℃的碱液
或三氯乙烯蒸汽,去除铸件表面油污。脱脂是关键工序 前处理
尚可 良 可 良 可
尚可 可 可
良
150~300 不需
150~200℃① 不需
100~150①
150~300 100①
100~150①
不需
应进行 不需 最好退火 不需 最好退火
应进行 最好退火 最好退火
不需
注:V 和 Ti 在其正常含量范围内对焊接性的影响可不考虑,Si 含量在 1.0%以下无明显 影响。 ① 形状简单的中小件可不预热。
不需
碳钢 C 0.3~0.4
可 100~150① 最好退火
C 0.4~0.5
尚可 150~300
应进行
锰钢 Mn1.2~1.6,C0.2~0.3 可 100~150① 最好退火
铬钢 镍钢
钼钢 铜钢
Mn1.2~1.6,C0.3~0.4 Cr<1.0,C<0.2 Cr1.5~1.6,C<0.3 Ni<2.0,C<0.2 Ni2.0~3.0,C0.15~ 0.30 Ni>3.0,C0.3~0.4 Mo0.4~0.6,C<0.25 Mo0.4~0.6,C0.25~ 0.35 Cu<2.0,C<0.2
优
优
稍差
差
补洞
良
优
一般 稍差
球墨铸铁 焊接
一般
优
差
差
焊补裂缝 一般
消失模铸件增碳缺陷及其防止措施
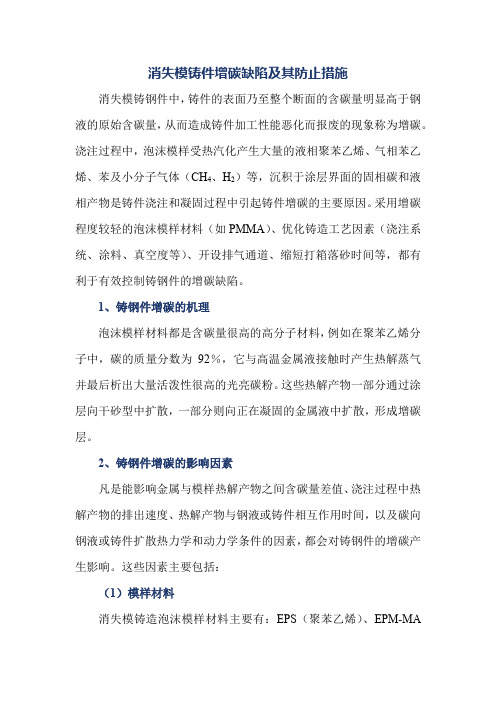
消失模铸件增碳缺陷及其防止措施消失模铸钢件中,铸件的表面乃至整个断面的含碳量明显高于钢液的原始含碳量,从而造成铸件加工性能恶化而报废的现象称为增碳。
浇注过程中,泡沫模样受热汽化产生大量的液相聚苯乙烯、气相苯乙烯、苯及小分子气体(CH4、H2)等,沉积于涂层界面的固相碳和液相产物是铸件浇注和凝固过程中引起铸件增碳的主要原因。
采用增碳程度较轻的泡沫模样材料(如PMMA)、优化铸造工艺因素(浇注系统、涂料、真空度等)、开设排气通道、缩短打箱落砂时间等,都有利于有效控制铸钢件的增碳缺陷。
1、铸钢件增碳的机理泡沫模样材料都是含碳量很高的高分子材料,例如在聚苯乙烯分子中,碳的质量分数为92%,它与高温金属液接触时产生热解蒸气并最后析出大量活泼性很高的光亮碳粉。
这些热解产物一部分通过涂层向干砂型中扩散,一部分则向正在凝固的金属液中扩散,形成增碳层。
2、铸钢件增碳的影响因素凡是能影响金属与模样热解产物之间含碳量差值、浇注过程中热解产物的排出速度、热解产物与钢液或铸件相互作用时间,以及碳向钢液或铸件扩散热力学和动力学条件的因素,都会对铸钢件的增碳产生影响。
这些因素主要包括:(1)模样材料消失模铸造泡沫模样材料主要有:EPS(聚苯乙烯)、EPM-MA(聚甲基丙烯酸甲酯)、STMMA(共聚物,EPS∶EPMMA=3∶7)等。
采用EPS材料时,出现增碳缺陷的可能大;而采用EPMMA材料,可大大减轻铸钢件的增碳缺陷;而STMMA材料综合了EPS和EPMMA的优点,为解决铸钢件增碳和气孔缺陷提供了可能。
用EPS与STMMA模件材料生产铸钢件时的增碳情况对比,如下表所示。
低碳钢消失模铸件增碳情况为了减少铸钢件的增碳,采用EPMMA或STMMA是十分有效的;但EPM-MA发气量大,发气速度也快,浇注时容易产生喷溅、呛火现象,造成气孔等缺陷;而STMMA则要好得多。
因此,STMMA 成为生产铸钢件的首选材料。
除模样材料种类的选择之外,模样的密度也是不可忽视的重要因素。
球铁铸件模型与铁水接触面处S含量的控制

球铁生产中模型与铁水接触面处硫含量的控制对于铸造行业的人员来说,可能都知道,影响铸件特性的因素有很多很多。
通常情况下,要分析解决成品出现的问题,那么要仔细考虑所有的材质成分和与之相关的过程实践。
球铁表面缺陷Taylor & Fenn, 是一个历史长160年,生产各种球铁件和钢材质的铸造厂,最近在生产球铁件泵壳时候,遇到一表面光洁度问题。
造型过程使用的是tolusulphonic acid (TSA) 固化的呋喃自硬砂系统的回收砂,砂芯涂料为甲醇的石墨基涂料。
在铸态状态下,铸件表面良好。
但是,当铸件退火处理时,其表面就会严重恶化。
在1650F(898℃)退火温度下,会有气体释放出来,且会渗入到表面之下,留下麻点。
其中一部分铸件可以通过打磨进行修补,但是其中麻点很严重的就得报废。
进一步观察,技术人员发现,就麻点的数量和严重度来看,并不是均匀分布在整个铸件表面。
另外因为在浇注中它们与散热和浇注时的紊流有关系,所以铸件上箱表面麻点要比下箱较严重。
变化因素在找寻此问题解决答案过程中,技术人员考虑到了一系列的变化因素。
其中包括有:▲球铁中Mg的含量▲浇注温度▲铸件特定截面处的碳当量▲固化砂中的灼减量▲砂芯涂料▲透气孔▲呋喃粘接剂中的水分在这些可变因素考虑基础上,进行了多次试验,结果只是发现冶金品质和铸造工艺都在很好的控制状况下。
但是,麻点问题仍然存在。
再进一步仔细观察热处理后的情况,发现铸件浇口处的麻点不明显。
此时,技术人员考虑到砂型与铁水的接触面,认为是麻点缺陷产生的来源。
第二次试验显示回收使用的呋喃砂中其硫含量高约0.09%,主要是由于使用TSA作为催化剂的原因。
通常情况下,其硫含量要保持在0.03%或以下,以避免Mg和S之间的反应。
对于生产球铁来说,此反应会吸收掉用于生成球墨的Mg,而在铸件表面会留有硫化镁夹杂物。
硫的含量越高,则其反应就会越恶化。
在此状况下,泵壳大部分表面型砂与球铁相互反应,而引起麻点。
钢水成分超标应急处理规定
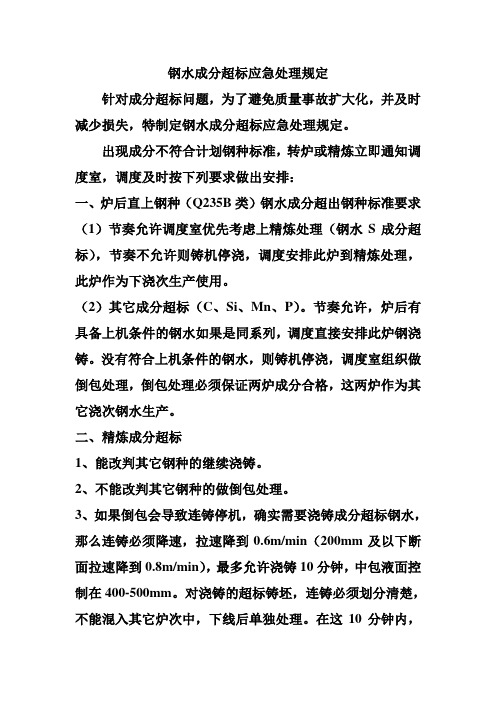
钢水成分超标应急处理规定针对成分超标问题,为了避免质量事故扩大化,并及时减少损失,特制定钢水成分超标应急处理规定。
出现成分不符合计划钢种标准,转炉或精炼立即通知调度室,调度及时按下列要求做出安排:一、炉后直上钢种(Q235B类)钢水成分超出钢种标准要求(1)节奏允许调度室优先考虑上精炼处理(钢水S成分超标),节奏不允许则铸机停浇,调度安排此炉到精炼处理,此炉作为下浇次生产使用。
(2)其它成分超标(C、Si、Mn、P)。
节奏允许,炉后有具备上机条件的钢水如果是同系列,调度直接安排此炉钢浇铸。
没有符合上机条件的钢水,则铸机停浇,调度室组织做倒包处理,倒包处理必须保证两炉成分合格,这两炉作为其它浇次钢水生产。
二、精炼成分超标1、能改判其它钢种的继续浇铸。
2、不能改判其它钢种的做倒包处理。
3、如果倒包会导致连铸停机,确实需要浇铸成分超标钢水,那么连铸必须降速,拉速降到0.6m/min(200mm及以下断面拉速降到0.8m/min),最多允许浇铸10分钟,中包液面控制在400-500mm。
对浇铸的超标铸坯,连铸必须划分清楚,不能混入其它炉次中,下线后单独处理。
在这10分钟内,调度必须抓紧时间,保证合格钢水上铸机。
三、中包取样发现成分超标时,能改判的继续浇铸,不能改判的调度安排下炉钢水5min内上机,连铸继续浇铸。
下炉钢水不具备上机条件,则连铸大包停浇,连铸将剩余中包钢水浇铸完毕后铸机停浇。
大包内剩余钢水返炉或根据现场实际情况决定是否折入其它罐中。
4.试验新钢种成分超标技术室负责处理。
四、奖惩按《产品质量责任划分及考核管理规定》执行。
炼钢厂技术室2012-08-02。
合金中s、p的作用与危害及相关的去除方法

钢的脱硫与脱磷1钢液的脱硫硫是钢中常见元素。
对于大多数钢种而言硫是有害元素。
只有少数钢种硫作为合金元素加入钢中,用来改善钢的切削性能及其他性能。
1.1 硫在钢中存在的形式在铁液中Fe与FeS能无限互溶,FeS在固态铁中的溶解度为0.015%~0.020%。
当钢中含硫量大于0.020%时,冷却后在晶界上以网状FeS和FeS-Fe共晶析出。
FeS-Fe共晶体的熔点为988℃。
FeS还会与FeO形成FeS-FeO共晶体,其熔点为940℃。
在钢中硫与许多合金元素可以形成硫化物或硫氧化物。
这些化合物的熔点和密度列于表1。
镍基合金中硫除了形成上述类型的镍的化合物之外,还会形成碳硫化合物。
表1 钢中硫化物的熔点和密度硫化物或硫氧化物熔点/℃密度/(g/cm3)硫化物或硫氧化物熔点/℃密度/(g/cm3)NiS 797 5.66 NdS 2200 6.24 FeS 1195 4.69 σ-Y2S3 1600 3.87 MnS 1530 4.05 γ-Ce2S3 1890 5.18 ZrS 2150 5.14 γ-La2S3 2150 4.93 TiS 2050 4.05 γ-Pr2S3 1795 5.27 MgS 2000 2.85 γ-Nd2S3 2200 5.49 BaS 2200 4.25 Y2O2S 2120 4.89 CaS 2600 2.80 Ce2O2S 1950 5.99 CeS 2450 5.88 La2O2S 1940 5.77 LaS 2200 5.75 Pr2O2S — 6.16 YS 2060 4.51 Nd2O2S 1990 6.22 PrS 2230 6.071.2 硫在钢中的作用1.2.1 硫的有益作用(1)改善钢的切削性能硫加入钢中形成细小的硫化物夹杂,可以产生应力集中的缺口效应,降低钢的切削抗力。
硫化物夹杂颗粒破坏了钢基体金属的连续性,使切削容易断裂。
此外硫化物夹杂质地柔软,对刀具能起润滑作用,减少了刀具与切削金属间的摩擦力。
造成球墨铸件质量问题及对策

造成球墨铸件质量问题及对策
1、原料质量:采用优质生铁,低磷、低硫。
2、球化率标准:提高球化率标准,达标产品才进入下一道工序。
2、浇铸铸造过程中产生的质量缺陷:夹砂和砂眼,针孔现象,是模具造成的,需要对模具及时修复。
3、球墨铸件退火,消除应力。
退火保持适当的温度,只有在退火良好的情况下,球墨铸件都会有很好的物理性能。
4、成品缺陷修复:在发现在有缺陷产品时,根据情况:可修复进入修复程序,不可修复作为废品处理。
解决球墨铸件出现质量问题的办法:
1、生产技术因素:在不考虑球墨铸件缺陷的前提下,影响球墨铸件性能的主要因素是铁水成分以及基体组织。
铁水成分方面要考虑到各种元素的变化、铸件要求的化学成分,从而合理选择炉料。
同时在熔炼过程中也要注意操作工艺,保证铁水温度以及成分稳定性,避免产品局部浇铸出现质量问题。
2、质量管理因素:在生产质量管理方面,应该加强生产技术人员的培训,提高铸造技术,严格质量把关,对于生产的每一个质量环节加强控制,及时发现问题,解决问题。
并对各个工序作好相应的质量记录报告。
钢液成分不正常情况的处理

钢液成分不正常情况的处理如果配料、装料准确及工艺合理与操作正确,钢液的成分极少出现不正常的情况,但有时因某个环节贻误而造成不正常的情况理应进行妥善的处理,以利于冶炼的经济效益。
钢液成分的不正常情况,这是主要是指钢中的元素含量高出控制规格,又简称超格。
常见的有全熔后,残余元素的超格,如Cr、Ni、Cu、Mo等元素;以及出钢前钢液成分的超格,如C、Si、Mn、Cr、Ni、Mo、W等元素。
前者主要是炉料分选不好,或配料、装料不准而引起的;后者是工艺不合理或操作不当造成的。
炉料自全熔后,由于冶炼方法或工艺规定,有些元素的成分允许高出规格,如C、Si、Mn、P、S等,这些高出的含量可通过后步的操作进行脱除,也有些元素的成分虽然高出规格,但以后却能随着补加大量的铁合金等金属料而降低,如返回法冶炼铬镍不锈钢中的镍等。
类似上述现象,可利用冶炼手段和工艺措施得到满意的解决,因此均属于正常情况。
然而也有些元素,在目前冶炼的条件下根本不能去除,如不氧化元素Ni、Cu等。
还有些元素虽能去除,但受冶炼方法或工艺所限,也很难或不能去除。
类似这些现象均列为不正常的情况。
化学成分不合的钢液是不能用来浇注钢锭(钢坯)或铸件的。
在冶炼过程中,为了避免元素含量的超格,往往采取低控制的操作,然后在出钢前进行适量的补加调整。
初看起来,这种操作似乎水平低,实际上是谨慎、稳妥。
但不能控制得过低,因为过低的含量容易造成出钢前大量补加合金,既降低熔池的温度,又耽误冶炼时间。
目前,钢液成分不正常情况处理的途径主要有:(1)对于能与氧化合的元素,可借用氧化反应来处理;(2)对于不氧化元素主要通过改钢、改技术条件或补加各种铁合金等金属料进行撤算。
钢中的C、Si、Mn、P以至于Cr、W等元素与氧均有不同程度的亲和力,这些元素如在氧化初期超格,可利用正常的氧化反应求得解决。
如果在出钢前超格,即使超出的不多,也会带来严重的后果。
对于这种情况,目前一般是采用重氧化的办法进行处理。
- 1、下载文档前请自行甄别文档内容的完整性,平台不提供额外的编辑、内容补充、找答案等附加服务。
- 2、"仅部分预览"的文档,不可在线预览部分如存在完整性等问题,可反馈申请退款(可完整预览的文档不适用该条件!)。
- 3、如文档侵犯您的权益,请联系客服反馈,我们会尽快为您处理(人工客服工作时间:9:00-18:30)。
如何消除铸钢件s,p含量高的问题
原料减少铸钢件的SP含量,低温脱P,加石灰,多造渣扒渣,高温脱S,多造稀薄渣,大口出钢,铸钢件渣混出,脱S效果好
铸钢中的磷、硫有害杂质如何去除
钢中的非金属夹杂物包括氧化物、硫化物、硫氧化合物、硅酸盐化合物及氮化物等。
这些夹杂物的来源有外来的和自生的两类。
外来的夹杂物包括在炼钢过程中从炉料夹带的不洁物,炉衬因经常受侵蚀而脱落的耐火材料等。
自生的夹杂物是在炼钢过程中及钢液浇注过程中,由于铸钢液中元素氧化或发生其它化学反应而生成的。
夹杂物对钢的力学性能有害,特别是对韧性的削弱作用较大。
为减轻夹杂物的有害作用,可采取两种途径:
(1)清除铸钢夹杂物
如在炼钢氧化期中,使钢液良好地沸腾,藉以有效地清除夹杂物,并在出钢后浇注前使用钢液在钢包中镇静一段时间( 5~10min ),使夹杂物自钢液中上浮。
采用炉外吹氩精炼,或将钢液过滤,都能有效地清除钢液中的夹杂物。
(2)改善铸钢夹杂物形态
夹杂物对钢削弱作用的程度依其形状及分布状况而定:带尖角的多角形夹杂物在钢中造成大的应力集中,在外力作用下易形成裂纹源,而颗粒状和球状夹杂则危害较小;条状夹杂物沿晶粒周界以网状或断续网状分布时,对钢的割裂作用较大,而呈岛状弧立分布的夹杂物的割裂作用较小。
如采用稀土合金对铸钢液进行处理,以使多角形氧化物和条状硫化物为球状的稀土硫氧化合物,就能降低夹杂物对钢的削弱作用。