铸钢件冒口地设计的要求规范
完整版铸钢件冒口的设计与计算
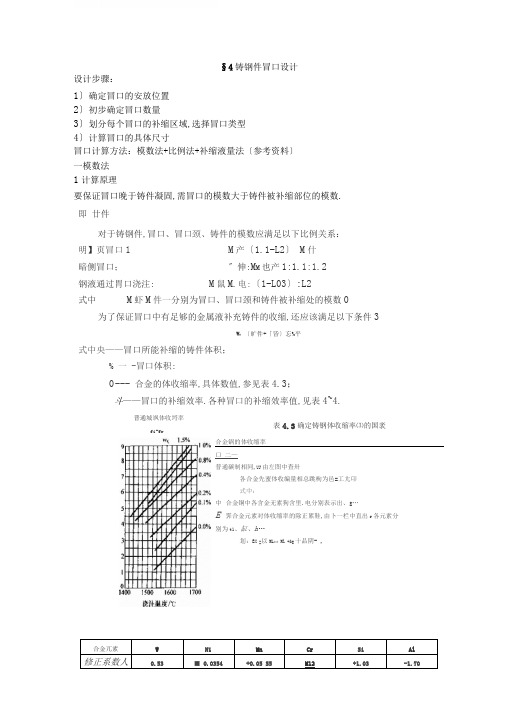
§4铸钢件冒口设计设计步骤:1〕确定冒口的安放位置2〕初步确定冒口数量3〕划分每个冒口的补缩区域,选择冒口类型4〕计算冒口的具体尺寸冒口计算方法:模数法+比例法+补缩液量法〔参考资料〕一模数法1计算原理要保证冒口晚于铸件凝固,需冒口的模数大于铸件被补缩部位的模数.即 廿件对于铸钢件,冒口、冒口颈、铸件的模数应满足以下比例关系:明】页冒口1M 产〔1.1-L2〕 M 什 暗侧冒口;〞伸:M M 也产1:1.1:1.2 钢液通过胃口浇注:M 鼠M.电:〔1-L03〕:L2 式中 M 虾M 件一分别为冒口、冒口颈和铸件被补缩处的模数0为了保证冒口中有足够的金属液补充铸件的收缩,还应该满足以下条件3W V 〔旷件+「皆〕忘%平式中央——冒口所能补缩的铸件体积;% 一 -冒口体积:0 --- 合金的体收缩率,具体数值,参见表4.3;斗——冒口的补缩效率.各种冒口的补缩效率值,见表4~4.表4.3确定铸钢体收缩率⑶的国袤 合金锅的体收缩率 口 二—普通碳制相同,UJ 由左图中查卅各合金先蜜体收编量相总跳枸为邑=工尢卬式中:中 合金铜中各含金无素狗含里.电分别表示出、g …E 霁合金元素对体收缩率的除正累鞋,由卜一栏中直出r 各元素分别为t1、缸、h …划:EX =以ML** Ml +&g 十品阴- ,合金兀素W Ni Mn Cr Si Al 修正系数人0.53 ■ 0.0354 +0.05 S5 M12 +1.03 -1.70 普通城飒体收埒率fi-fr总结:M冒=1.2M件P127式4-5,左边为总收缩量,右边为由冒口补充量2计算步骤1〕计算铸件模数根据铸件需补缩部位,划分补缩区,分别计算铸件的模数.计算方法:公式计算+图表计算—表4-5 〔p128-130〕.2〕计算冒口及胃口颈模数.根据热节的位置,确定胃口的类型,再根据式〔4-2〕或式〔4-3〕、式〔4-4〕. 即可计算出国口及冒口颈模数计算举例;铸钢件在下部法上处放置暗冒口补缩. 如图4-3三所示.求吩和利用表4・5中上形体计算公式,法兰处o=200mm, b—lOOnun*非散热面可得:“*0x20 …M 社=—j ---- ——cm = 3.636cm件2〔10 + 20〕-5因浇口通过冒口,故:1.05Mr = 374 cm 加冒=L2A/件=436 cmS 中左边的冒口颈…W R=〔22X 10X2〔22+10〕]四4一箝补缩铸钢件法兰的目口颈cm- 3.43cm,小于3.74cm,不能满足补缩要求,在铸件热节处将出现缩松口采用右边的冒口颈,必=Q0X 12V[2QO+I2〕]crti=3.75cm,满足了要求.计算M件用L形体计算公式,为什么不用法兰体公式去套呢?〔法兰体高度b无法确定〕图4-33B-B剖面图中200应改为220,因计算M B时用的数值是220;另外, 冒口直径为〔|〕220,其冒口颈宽也应为220.〔A-A剖面图中200改否.〕采用右边的A-A剖面冒口颈满足了要求,A-A剖面冒口颈尺寸怎么得来的呢?不要瞎懵,可列式M仝^=3.74=20X/[2 〔20+X〕],求出X=12.生产中可根据M冒数值查出标准侧冒口,得冒口尺寸〔直径、高等〕,冒口颈尺寸,冒口体积、重量,能补缩的铸件体积及重量〔 M冒结合一查〕.3〕确定铸钢件体收缩率由表4-3求出.例如,ZG270-500的平均W C=0.35%,假设浇注温度为1560℃,可从表4-3 查出=4.7%〔碳钢e V= e C〕.£V如何查出的呢?浇注温度为1560 C; W C=0.40%, ev=5%; W C=0.20%,&V=3.8%;据此列式〔5-3.8〕 / 〔0.4-0.2〕 = 〔5-X〕 / 〔0.4-0.35〕,解出X=4.7 〔插入法,比例法〕4〕确定冒口形状和尺寸查相关表格.5〕确定冒口数目6〕校核冒口的最大补缩水平.二比例法〔热节圆法〕使冒口根部直径大于铸件被补缩处热节圆直径或壁厚, 再以冒口根部直径来确定其他尺寸.D=cd式中D ……冒口根部直径;c ••…比例系数,参见表4-6;〔查表步骤〕d ……铸件被补缩热节处内切圆直径.可用作图法画出图4-34热节圆直件a 〕壁厚均匀b 〕壁面和交查表步骤:1〕选取比例系数c 〔先按铸件结构选择冒口类型,再选比例系数〕2〕确定冒口高度〔根据直径 D 确定〕;3〕确定每个冒口长度或冒口个数〔根据冒口延伸度确定〕.三铸件工艺出品率的校核表4-7说明校核方法.采用普通冒口时,冒口尺寸 可根据表中数值进行验算 和调整,即将冒口重量代入 计算后,假设工艺出品率低于 表中数值,那么冒口尺寸偏 大,可适当减小冒口高度; 假设高于表中数值,那么应加大 冒口尺寸或增加冒口个数.四冒口计算举例 见p133例题.图535 ZG35SiMn 铸钢齿轮铸件1模数法工艺出品率= 铸件重量铸件重量+浇铸系统重 量+冒口重量轮缘与轮辐的交接处为热节,其直径d按作图法得50〔大于轮缘厚40〕;按作图法且考虑热节增大,见P126图4-31,dy=d+〔10~30〕,取d=60 〔见P134比例法〕.轮缘热节处按表4-5应为板与杆的相交体,由图4-35可得a=d=60mm, b=180mm,c=24mm.2比例法〔热节圆法〕作业:如下列图铸钢齿圈坯件ZG25,为一圆环,中径〔|〕920,厚80,高240, 有三种补缩方案:3个6190冒口, 3个6190冒口和3个冷铁,尺寸为:宽100X厚50X高240, 6个6190冒口.按有效补缩距离检验,冒口数目是否足够?。
冒口设计参考
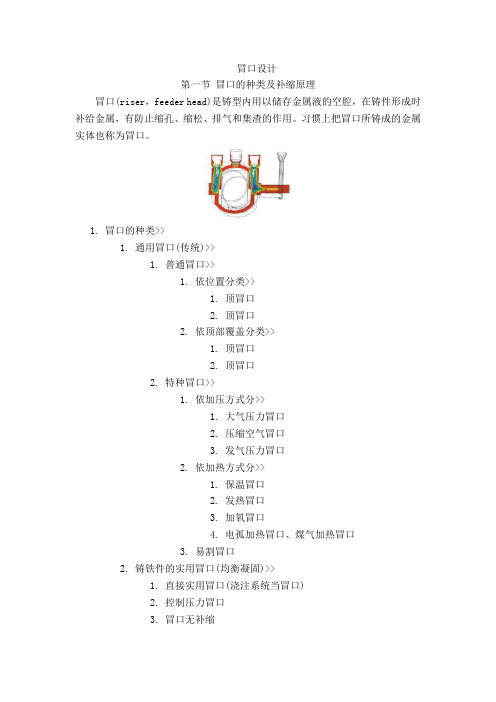
冒口设计第一节冒口的种类及补缩原理冒口(riser,feeder head)是铸型内用以储存金属液的空腔,在铸件形成时补给金属,有防止缩孔、缩松、排气和集渣的作用。
习惯上把冒口所铸成的金属实体也称为冒口。
1.冒口的种类>>1.通用冒口(传统)>>1.普通冒口>>1.依位置分类>>1.顶冒口2.顶冒口2.依顶部覆盖分类>>1.顶冒口2.顶冒口2.特种冒口>>1.依加压方式分>>1.大气压力冒口2.压缩空气冒口3.发气压力冒口2.依加热方式分>>1.保温冒口2.发热冒口3.加氧冒口4.电孤加热冒口、煤气加热冒口3.易割冒口2.铸铁件的实用冒口(均衡凝固)>>1.直接实用冒口(浇注系统当冒口)2.控制压力冒口3.冒口无补缩2.冒口形状冒口的形状有圆柱形、球顶圆柱形、长(腰)圆柱形、球形及扁球形等多种3.通用冒口补缩原理>>1.基本条件>>1.冒口凝固时间大于或等于铸件(被补缩部分)的凝固时间2.有足够的金属液补充铸件的液态收缩和凝固收缩,补偿浇注后型腔扩大的体积3.在凝固期间,冒口和被补缩部位之间存在补缩通道,扩张角向着冒口2.选择冒口位置的原则>>1.冒口应就近设在铸件热节(hotspot)的上方或侧旁2.冒口应尽量设在铸件最高、最厚的部位。
对低处的热节增设补贴或使用冷铁,造成补缩的有利条件3.冒口不应设在铸件重要的、受力大的部位,以防组织粗大降低强度4.冒口位置不要选在铸造应力集中处,应注意减轻对铸件的收缩阻碍,以免引起裂纹5.尽量用一个冒口同时补缩几个热节或铸件6.冒口布置在加工面上,可节约铸件精整工时,零件外观好7.不同高度上的冒口,应用冷铁使各个冒口的补缩范围隔开3.冒口有效补缩距离的确定>>冒口的有效补缩距离为冒口作用区与末端区长度之和,它是确定冒口数目的依据,与铸件结构、合金成分及凝固特性、冷却条件、对铸件质量要求的高低等多种因素有关,简称为冒口补缩距离1.铸钢件冒口的补缩距离有色合金的冒口补缩距离外冷铁的影响补贴(padding)的应用第二节铸钢件冒口的设计与计算铸钢件冒口属于通用冒口,其计算原理适用于实行顺序凝固的一切合金铸件。
铸件冒口设计的原则及方法

图 4 冒口放在两热节之间的工艺对比
放在最后凝固的部位和几何热节处,形成 的接触热节和冒口补缩液流通效应的影 响,会使冒口安放处铸件的凝固时间延长, 相应增加对冒口补缩时间的要求,同时也 对热节处的内在质量产生不利的影响。为 此,文献[4]提出了动态顺序凝固的概念。 动态顺序凝固是指冒口离开热节,放在近 热节处,利用冒口根处形成的接触热节和 冒口补缩液的流通效应,实现铸件各部分 朝向冒口的顺序凝固。其实质是使铸件的 几何热节与设置冒口形成的接触热节相分 离,并控制次热节处所形成的接触热节,使 其凝固模数比几何热节的大,比冒口的小, 将凝固顺序由薄壁→次热节→几何热节→ 几何热节处的接触热节→冒口,改变为薄 壁→几何热节→次热节处的接触热节→冒 口,既避免了接触热节处热量过分集中,又 利用接触热节的热效应,在冒口和几何热 节之间形成补缩通道,保证冒口对几何热 节的补缩。
采用模数法计算出的冒口体积,应该
用补缩液量法进行校核,即冒口体积 V 应 r
满足式(1)。
3.2 热节圆比例法
热节圆比例法是一种经验性方法。采
用作图法或几何公式计算出热节圆直径 T, 然后根据铸件不同截面形状确定例系数α的数值多来源于工程实
科技创新导报 Science and Technology Innovation Herald
101
科技创新导报 2008 NO.27 Science and Technology Innovation Herald
工 程 技 术
图 5 冒口直径与铸件厚度热节圆直径的 关系
使膨胀压力得以控制,避免铸型扩大,一般
铸件凝固过程中,冒口液面不断下降, 体积减少,散热表面积增加,冒口模数动态
变小;铸件获得补缩液体后热量增加,凝固
铸铁件冒口设计.

5 冒口个数(均衡段的个数)
均衡段 冒口位置
均衡段
6 无冒口铸造工艺
无冒口铸造的本质是浇口当冒口
7 浇口当冒口补缩工艺
(1)补缩模型
(2)浇注系统流通效应:金属液流
过、通过直浇道、横浇道、内浇道 时,周围的型砂被加热,凝固时间 延长的热效应。为此,小的浇注系 统模数可以有长的凝固时间。流通 效应系数推荐为: f直浇道流通效应系数=0.70~0.80 f横浇道流通效应系数=0.75~0.85 f内浇道流通效应系数=0.35~0.40
10 铸铁件冒口系列
1989年国家科委成都均衡凝固推广班
谢 谢!
铸造技术杂志社祝会议圆满成功
提高铸造企业工艺水平和铸件品质
提高中国铸件在国际市场上的竞争力
Qm=
G Mc3
(2)球铁件收缩时间分数
Pc=
1.0 e
(0.65Mc+0.01Qm)
3 冒口体模数MR MR=f1f2f3Mc
f1 ——冒口平衡系数 取f1=1.2
f2 ——收缩模数系数 f2=√Pc f3 ——冒口压力系数 f3=1.1~1.3
4 冒口颈模数MN
MN=fp.f2.f4 Mc
(3)直浇道模数 MZ MZ=f直.f1f2f3Mc
f1 ——冒口平衡系数 取f1=1.2
f2 ——收缩模数系数 f3 ——冒口压力系数 f3=1.1-1.3 f直浇道流通效应系数=0.70-0.80
(4)横浇道模数 Mh
Mh=f横.f2.Mc
f2 ——收缩模数系数 f横浇道流通效应系数=0.75~0.85
(5)内浇道模数Mn Mn=f内f2.f4Mc
重力浇铸冒口设计原则
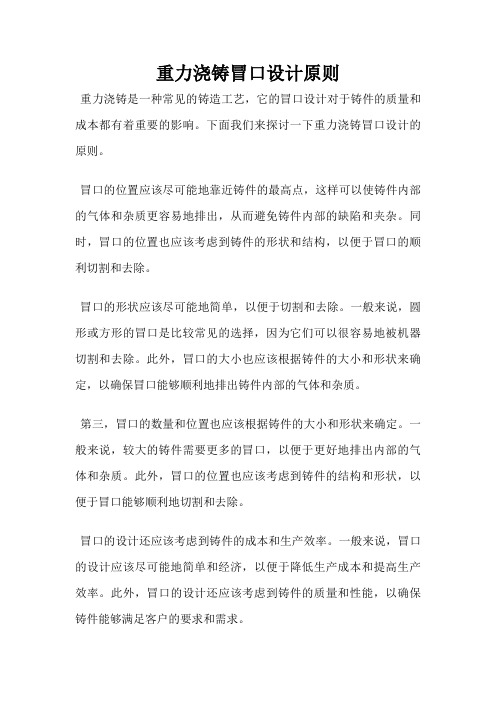
重力浇铸冒口设计原则
重力浇铸是一种常见的铸造工艺,它的冒口设计对于铸件的质量和成本都有着重要的影响。
下面我们来探讨一下重力浇铸冒口设计的原则。
冒口的位置应该尽可能地靠近铸件的最高点,这样可以使铸件内部的气体和杂质更容易地排出,从而避免铸件内部的缺陷和夹杂。
同时,冒口的位置也应该考虑到铸件的形状和结构,以便于冒口的顺利切割和去除。
冒口的形状应该尽可能地简单,以便于切割和去除。
一般来说,圆形或方形的冒口是比较常见的选择,因为它们可以很容易地被机器切割和去除。
此外,冒口的大小也应该根据铸件的大小和形状来确定,以确保冒口能够顺利地排出铸件内部的气体和杂质。
第三,冒口的数量和位置也应该根据铸件的大小和形状来确定。
一般来说,较大的铸件需要更多的冒口,以便于更好地排出内部的气体和杂质。
此外,冒口的位置也应该考虑到铸件的结构和形状,以便于冒口能够顺利地切割和去除。
冒口的设计还应该考虑到铸件的成本和生产效率。
一般来说,冒口的设计应该尽可能地简单和经济,以便于降低生产成本和提高生产效率。
此外,冒口的设计还应该考虑到铸件的质量和性能,以确保铸件能够满足客户的要求和需求。
重力浇铸冒口设计是铸造工艺中非常重要的一环,它的设计原则应该考虑到铸件的形状、结构、大小、成本和生产效率等多个方面。
只有合理地设计冒口,才能够保证铸件的质量和性能,从而满足客户的要求和需求。
冒口

根据国标GB/T5611-1998定义:铸造热节,是指铁水在凝固过程中,铸件内比周围金属凝固缓慢的节点或局部区域。
也可以说是最后冷却凝固的地方。
我们知道,由于结构和铸造参数的原因,在模腔内各点的熔融状态的铁水凝固时间是不相等的,这就会给铸件在凝固后产生热应力,造成铸件变形,裂纹等,同时,由于冷却凝固时间不等,铸件会出现疏松,冷隔,气孔等缺陷。
为避免产生热节,结构上铸件壁厚应尽可能均匀,,以减少模具局部热量集中产生的热疲劳。
铸件的转角处应有适当的铸造圆角,以避免模具上有尖角位导致应力产生,同时在热节处设置冷铁,以加快冷却速度,以及设计合理的横浇道和浇铸速度等工艺参数。
功能不同的冒口,其形式、大小和开设位置均不相同,所以,冒口的设计要考虑铸造合金的性质和铸件的特点。
冒口①对于凝固过程中体积收缩不大的合金(如灰铸铁),或不产生集中缩孔的合金(如锡青铜),冒口的作用主要是排放型腔中的气体和收集液流前沿混有夹杂物或氧化膜的金属液,以减少铸件上的缺陷。
这种冒口多置于内浇口的对面,其尺寸也不必太大,②对于要求控制显微组织的铸件,冒口可以收集液流前沿已冷却的金属液,避免铸件上出现过冷组织。
图2是单体铸造的活塞环,在内浇口的对面设置一个小冒口来收集冷金属,该处就不会因金属过冷而出现白口组织,导致铸件报废。
这类冒口的大小和设置部位,应根据铸件的显微组织要求确定。
③对于凝固期间体积收缩量大而且趋向于形成集中缩孔的合金(如铸钢、锰黄铜及铝青铜等),冒口的主要作用是补偿金属液在型腔中的液态收缩和铸件凝固过程中的收缩,以获得没有缩孔的致密铸件。
铸件在铸型中冷却时,最薄的部位先凝固,其收缩可由附近较厚的部分补偿;较厚部分凝固时,又可由最厚部分得到补偿;最厚部分凝固时,如得不到外来的补偿,该处就会形成大缩孔。
在这种情况下,冒口的作用就是要补偿铸件最后凝固的部分,所以要置于铸件最厚部位的上方或侧面,并且它的凝固要冒口求晚于铸件的最厚部分。
冒口系统设计

冒口系统设计一﹑冒口设计1. 冒口设计的基本原则1)冒口的凝固时间应大于或等于铸件(被补缩部分)的凝固时间。
2)冒口应有足够大的体积,以保证有足够的金属液补充铸件的液态收缩和凝固收缩,补缩浇注后型腔扩大的体积。
3)在铸件整个凝固的过程中,冒口与被补缩部位之间的补缩通道应该畅通,即使扩张角始终向着冒口。
对于结晶温度间隔较宽、易于产生分散性缩松的合金铸件,还需要注意将冒口与浇注系统、冷铁、工艺补贴等配合使用,使铸件在较大的温度梯度下,自远离冒口的末端区逐渐向着冒口方向实现明显的顺序凝固2. 冒口设计的基本内容1)冒口的种类和形状(1)冒口的种类⎧⎧⎧⎪⎪⎪⎨⎪⎪⎪⎪⎪⎨⎩⎪⎪⎪⎧⎪⎪⎨⎪⎪⎩⎩⎪⎧⎧⎪⎪⎪⎪⎨⎪⎪⎪⎪⎪⎨⎩⎪⎪⎪⎧⎪⎪⎪⎪⎪⎪⎪⎨⎨⎪⎪⎪⎪⎪⎪⎩⎪⎪⎪⎪⎪⎪⎪⎪⎪⎪⎪⎩⎩顶冒口依位置分侧冒口贴边冒口普通冒口明冒口依顶部覆盖分暗冒口大气压力冒口依加压方式分压缩空气冒口通用冒口(传统)发气压力冒口保温冒口发热冒口特种冒口依加热方式分加氧冒口电弧加热冒口,煤气加热冒口易割冒口直接实用冒口(浇注系统当铸铁件的实用冒口(均衡凝固)⎧⎪⎪⎪⎪⎪⎪⎪⎪⎪⎪⎪⎪⎪⎪⎨⎪⎪⎪⎪⎪⎪⎪⎪⎪⎪⎪⎧⎪⎪⎨⎪⎪⎪⎩⎩冒口)控制压力冒口冒口无补缩 图1 冒口分类(2)冒口的形状常用的冒口有球形、圆柱形、长方体形、腰圆柱形等。
对于具体铸件,冒口形状的选择主要应考虑以下几方面:a)球形 b)球顶圆柱形 c)圆柱形 d)腰圆柱形(明) e)腰圆柱形(暗)图2 常用的冒口形状①冒口的补缩效果: 冒口的形状不同,补缩效果也不同,常用冒口模数(M)的大小来评定冒口的补缩效果(M=冒口体积/冒口散热面积),在冒口体积相同的情况下,球形冒口的散热面积最小,模数最大,凝固时间最长,补缩效果最好,其它形状冒口的补缩效果,依次为圆柱形,长方体形等。
②铸件被补缩部位的结构情祝: 冒口形状的选泽还要考虑铸件被补缩部位的结构形状和造型工艺是否方便。
铸铁件冒口设计手册

铸铁件冒口设计手册诸葛胜福士科铸造材料(中国)有限公司铸铁冒口设计手册一、概述冒口是一个个储存金属液的空腔。
其主要作用是在铸件成形过程中提供由于体积变化所需要补偿的金属液,以防止在铸件中出现的收缩类型缺陷(如图1和图2所示),而这些需要补偿的体积变化可能有:图1 各种缩孔图2 缩孔生产图a)和冒口的补缩图b)1—一次缩孔 2—二次缩孔 3—缩松 1—缩孔 2—型腔胀大 3—铸件(虚线以内) 4—显微缩松 5—缩陷(缩凹,外缩孔)(1)铸型的胀大(2)金属的液态收缩(3)金属的凝固收缩补偿这些体积变化所需要的金属液量随着铸型和金属种类的不同而异。
此外,冒口还有排气及浮渣和非金属夹杂物的作用。
铸件制成后,冒口部分(残留在铸件上的凸块)将从铸件上除去。
由此,在保证铸件质量要求的前提下,冒口应尽可能的小些,以节省金属液,提高铸件成品率。
由此冒口的补缩效率越高,冒口将越小,铸件成品率越高、越经济。
FOSECO公司的发热保温冒口具有高达35%的补缩效率;因而,具有极高的成品率和极其优越的经济性。
在金属炉料价格飞涨的情况下,其优越性显得尤其突出。
另外,高品质发热保温冒口,及其稳定可靠的产品质量是获得高品质铸件的重要手段和可靠的质量保证。
二、铸铁的特点铸钢和铸铁都是铁碳合金,它们在凝固收缩过程中有共同之处)如凝固前期均析出初生奥氏体树枝晶,都存在着液态、凝固态和固态下的收缩),但也有不同的特点。
其根本不同之处是铸铁在凝固后期有“奥氏体+石墨”的共晶转变,析出石墨而发生体积膨胀,从而可部分地或全部抵消凝固前期所发生的体积收缩,即,具备有“自补缩的能力”。
因此在铸型刚性足够大时,铸铁件可以不设冒口或采用较小的冒口进行补缩。
灰铸铁在共晶转变过程中析出石墨,并在与枝晶间的液体直接接触的尖端优先长大,其石墨长大时所产生的体积膨胀直接作用在晶间液体上,进行“自补缩”。
对于一般低牌号的灰铁铸件,因碳硅含量高,石墨化比较完全,其体积膨胀量足以补偿凝固时的体收缩,故不需要设置冒口,只放排气口。
铸钢件冒口的设计与计算-推荐下载

§4 铸钢件冒口设计设计步骤:1)确定冒口的安放位置2)初步确定冒口数量3)划分每个冒口的补缩区域,选择冒口类型4)计算冒口的具体尺寸冒口计算方法:模数法+比例法+补缩液量法(参考资料)一模数法1 计算原理要保证冒口晚于铸件凝固,需冒口的模数大于铸件被补缩部位的模数。
总结:M冒=1.2M件P127式4-5,左边为总收缩量,右边为由冒口补充量。
2 计算步骤1)计算铸件模数根据铸件需补缩部位,划分补缩区,分别计算铸件的模数。
计算方法:公式计算+图表计算-表4-5(p128-130)。
计算M件用L形体计算公式,为什么不用法兰体公式去套呢?(法兰体高度b无法确定)图4-33B-B剖面图中200应改为220,因计算M B时用的数值是220;另外,冒口直径为φ220,其冒口颈宽也应为220。
(A-A剖面图中200改否.)采用右边的A-A剖面冒口颈满足了要求,A-A剖面冒口颈尺寸怎么得来的呢?不要瞎懵,可列式M颈=3.74=20X/[2(20+X)],求出X=12.生产中可根据M冒数值查出标准侧冒口,得冒口尺寸(直径、高等),冒口颈尺寸,冒口体积、重量,能补缩的铸件体积及重量(M冒结合εV查)。
3)确定铸钢件体收缩率由表4-3求出。
例如,已知ZG270-500的平均W C=0.35%,若浇注温度为1560°C,可从表4-3查出εV=4.7%(碳钢εV=εC)。
如何查出的呢?浇注温度为1560°C;W C=0.40%,εV=5%;W C=0.20%,εV=3.8%;据此列式(5-3.8)/(0.4-0.2)=(5-X)/(0.4-0.35),解出X=4.7(插入法,比例法)4)确定冒口形状和尺寸查相关表格。
5)确定冒口数目6)校核冒口的最大补缩能力。
二比例法(热节圆法)见p133例题。
1 模数法轮缘与轮辐的交接处为热节,其直径d按作图法得50(大于轮缘厚40);按作图法且考虑热节增大,见P126图4-31,dy=d+(10~30),取d=60(见P134比例法)。
铸造工艺学冒口设计方案

保温作用:冒口可 以减缓铸件凝固速 度,提高铸件质量
冒口的设计原则
保证补缩量:根据铸件的结 构、尺寸、壁厚等确定冒口 的补缩量
便于操作:冒口的位置应便 于操作,以便于浇注和清理
减少金属消耗:在保证补缩 量的前提下,尽量减少冒口 的金属消耗
避免形成热节:冒口的设计 应避免形成热节,以防止铸 件产生缩孔和缩松等缺陷
计算法
冒口体积计算 冒口直径计算 冒口高度计算 冒口材料选择
实验法
实验目的:确定最 佳冒口尺寸和位置
实验步骤:设计多 种方案,进行实际 铸造实验
实验结果:观察铸 件质量,分析实验 数据
结论:根据实验结 果,确定最佳冒口 设计方案
05 冒口的设计优化
减小冒口体积
优化冒口结构: 采用合理的冒 口结构,如分 片式、组合式 等,以减
冒口的设计原则: 根据铸件的结构、 尺寸、材质等因 素进行设计
冒口的设计方法: 根据铸造工艺学 原理,采用合适 的冒口尺寸、形 状和位置
冒口设计的实际 应用:在铸铁件 生产中,根据实 际情况选择合适 的冒口设计方案, 提高铸件质量和 生产效率
铝合金铸件的冒口设计
口体积
降低冒口高度: 通过减小冒口 高度,减少冒 口体积,同时 保证补缩效果
减小冒口直径: 采用较小的冒 口直径,以减 小冒口体积, 同时保证补缩
效果
改进冒口材料: 采用轻质、高 强度、低热膨 胀系数的材料 制作冒口,以 减小冒口体积
提高冒口补缩效率
确定冒口的位置和数量 选择合适的冒口类型 优化冒口尺寸和形状 控制冒口补缩时间
铸造工艺学冒口设计 方案
,a click to unlimited possibilities
汇报人:
3.4.3及3.4.4 铸钢及铸铁件冒口设计

3.4.3 铸钢件冒口设计与计算
四、铸件模数的计算
1. 正立方体
2. 圆柱体
3. 具有“无限大”尺寸的物
体 4. 圆筒壁 5. 交接立方体
3.4.3 铸钢件冒口设计与计算
四、铸件模数的计算
4. 圆筒壁
5. 交接立方体
6. 冒口颈的模数(riser neck)
铸钢件:Mn>Mc 铸铁件:Mn<Mc
选择圆柱形冒口,由标准冒口表查得冒口尺寸:
D=160mm,H=24mm 校核冒口个数: 估计冒口个数1000/(D+4.5a×2)≈1.6 ≈2 按两个冒口校核长度方向 4.5×50+4×50+4.5×50+2×160=970<1000
增加一个冒口,按三个冒口校核 970+160+4×50=1330>1000 宽度方向校核
4.5×50×2+160=610 >600
校核冒口最大补缩能力:
εv(Vr+Vc)=5%(100×60×5+π(16/2)2 ×24×3)
=2223(cm3)
Vrη=15 %π(16/2)2 ×24×3=2170 (cm3)
增大冒口尺寸,D=180mm
εv(Vr+Vc) = 2415 cm3 <Vrη=2746 cm3
有先有后,相互交错重叠,而铁水是相通的,这时膨胀、 收缩就可以叠加相抵,铸件表现出来的收缩实质上是胀缩 相抵的剩余量。然而就某一点而言,是收缩在前,膨胀在 后,二者是不能相抵的。
3.4.4 铸铁件实用冒口设计
图3-3-24 铸铁件凝固时收缩和膨胀的叠加 曲边三角形ABC—铸件的总收缩 曲边三角形ADC —铸件总膨胀 曲边三角形AB‘P—铸件的表观收缩 AC—铸件凝固时间 AP—铸件表观收缩时间 (冒口作用时间) P—均衡点(收缩量等于膨胀量的时间)
负压实型铸造技术中的铸钢件冒口设计
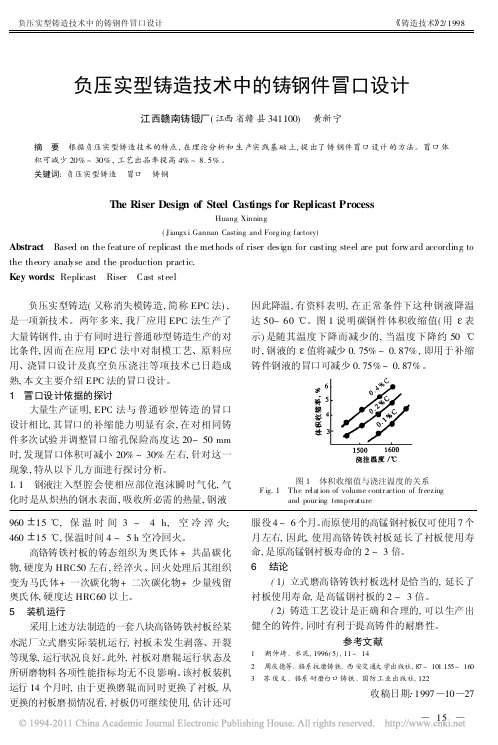
负压实型铸造( 又称消失模铸造, 简称 EPC 法) , 是一项新技术。两年多来, 我厂应用 EPC 法生产了 大量铸钢件, 由于有同时进行普通砂型铸造生产的对 比条件, 因而在应用 EP C 法中对制模工艺、原料应 用、浇冒口设计及真空负压浇注等项技术已日趋成 熟, 本文主要介绍 EPC 法的冒口设计。 1 冒口设计依据的探讨
设置补贴会更好。
2 5 根据冒口散热应最慢的原则, EP C 法冒口形状
应以球形为最好, 但综合考虑通用化标准化及手工制
模难易程度, 生产中一般选圆柱形或椭圆形冒口, 如
图 2 所示。这种形状更易于在砂型铸造方法的基础 上来设计。冒口最好放在铸件的最高位置, 以使其既
能补缩铸件又可起到集渣集气的作用。
图 2 冒口示图 F ig. 2 T he drawing of r iser
3 两个与冒口设计有关的措施 3 1 EPC 法的型腔是由泡沫模形成的, 填充砂是松 散的, 在抽真空形成负压条件下才被紧实。因而对铸 件厚大区采用内冷铁时安放不大方便, 实际操作常采 用干净圆钉插入泡沫模作为激冷内冷铁, 但对大面积 厚大部位效果甚微。另一个方法是采用外冷铁, 由于 放置简单, 放安灵活, 泡沫模型又上了涂料, 因而对外 冷铁表面锈蚀情况也不需作严格要求, 只要与铸件贴 合处形状相同即可, 与普通砂型铸造方法不同的是泡
铸铁件收缩模数法冒口设计
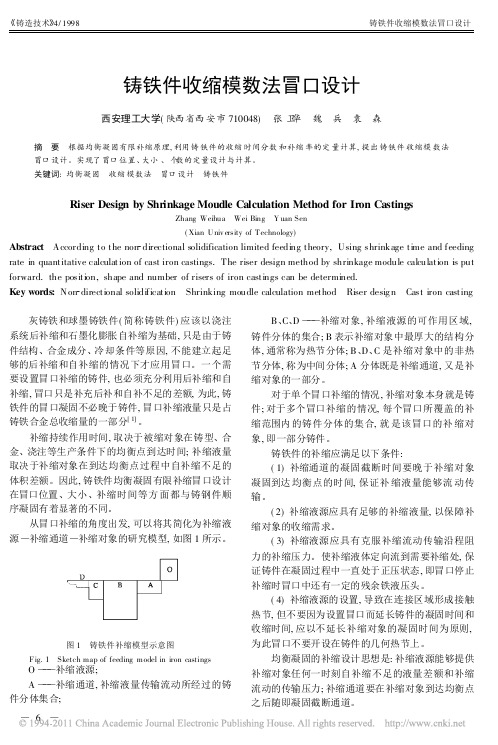
合金的收缩时间、收缩率不同, 铸铁合金的收缩时间、 收缩率是在一定的工艺条件下, 用规定的试样( 一种
特定的铸件) 测定的收缩、补缩特性参数。铸铁件的
补缩持续作用时间与补缩液量与浇注条件、浇冒口设
置位置、铸型冷却特性、铸型硬度等工艺条件及铸件
本身的结构有关, 具有动态特性。
这种动态特性, 按照补缩液源 补缩通道 补
灰铸铁件: P c =
1 e( 0. 5Mc+ 0. 01 qm )
( 4)
Fc =
0. 06
e( 0. 2M + 0. 01q )
c
m
( 5)
球 铁 件: Pc =
1
e( 0. 65M + 0. 01q )
c
m
( 6)
Fc =
0. 08
e( 0. 5M + 0. 01q )
c
m
( 7)
2 收缩模数法补缩设计原理
均衡凝固的补缩设计思想是: 补缩液源能够提供 补缩对象任何一时刻自补缩不足的液量差额和补缩
流动的传输压力; 补缩通道要在补缩对象到达均衡点 之后随即凝固截断通道。
铸造技术 4/ 1998
铸铁件收缩模数法冒口设计
1 铸铁件收缩时间和补缩率动态特性的数学描述
铸铁件的补缩持续作用时间与补缩液量, 与铸铁
f3
Ms
式中 M r Ar Vf Vp
= f 1 f 2 f 3 Mc
( 9)
冒口模数, cm ;
冒口散热表面积, cm2;
补缩液量, cm3;
形成补缩压力的安全液量, cm3;
f 1 补缩液量平衡系数;
f 3 补缩压力系数。
2 4 冒口颈大小的确定 冒口颈作为连接补缩液源 铸件的过渡通道,
铸钢件冒口的设计规范
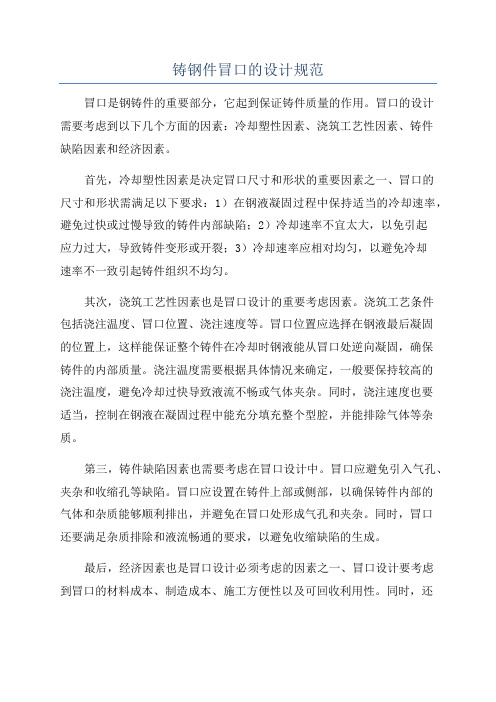
铸钢件冒口的设计规范冒口是钢铸件的重要部分,它起到保证铸件质量的作用。
冒口的设计需要考虑到以下几个方面的因素:冷却塑性因素、浇筑工艺性因素、铸件缺陷因素和经济因素。
首先,冷却塑性因素是决定冒口尺寸和形状的重要因素之一、冒口的尺寸和形状需满足以下要求:1)在钢液凝固过程中保持适当的冷却速率,避免过快或过慢导致的铸件内部缺陷;2)冷却速率不宜太大,以免引起应力过大,导致铸件变形或开裂;3)冷却速率应相对均匀,以避免冷却速率不一致引起铸件组织不均匀。
其次,浇筑工艺性因素也是冒口设计的重要考虑因素。
浇筑工艺条件包括浇注温度、冒口位置、浇注速度等。
冒口位置应选择在钢液最后凝固的位置上,这样能保证整个铸件在冷却时钢液能从冒口处逆向凝固,确保铸件的内部质量。
浇注温度需要根据具体情况来确定,一般要保持较高的浇注温度,避免冷却过快导致液流不畅或气体夹杂。
同时,浇注速度也要适当,控制在钢液在凝固过程中能充分填充整个型腔,并能排除气体等杂质。
第三,铸件缺陷因素也需要考虑在冒口设计中。
冒口应避免引入气孔、夹杂和收缩孔等缺陷。
冒口应设置在铸件上部或侧部,以确保铸件内部的气体和杂质能够顺利排出,并避免在冒口处形成气孔和夹杂。
同时,冒口还要满足杂质排除和液流畅通的要求,以避免收缩缺陷的生成。
最后,经济因素也是冒口设计必须考虑的因素之一、冒口设计要考虑到冒口的材料成本、制造成本、施工方便性以及可回收利用性。
同时,还要综合考虑冒口数量、形状和尺寸的合理性,以降低冒口制造的成本,并提高冒口的使用寿命。
总结起来,铸钢件冒口的设计规范应满足冷却塑性因素、浇筑工艺性因素、铸件缺陷因素和经济因素的要求。
冒口设计的合理与否直接影响到铸件的质量和成本,因此在实际工程中需要根据具体情况综合考虑以上各方面因素,合理设计冒口。
铸件冒口设计的原则及方法

1前言
2 0世 纪 3 0年 代 , 名 冶 金 工程 师 N. 著 C v H o 提 出了凝 固模数的概 念 , h on v 在考 虑 了 合 金 、铸型 等热物 理参 数和 浇注 条件 的基 础 上 , 照 铸件 形 体所 决 定 的 热 量 传输 特征 , 按 建 立 了凝 固模 数 与 凝 固 时 间 关 系 的 平 方根 定 律 , 冒 口设 计 提 供 了 科 学 依 据 。6 为 0年 代 , Wld we 完善 并 发展 了 C v r o R. o a r h oi v n 的理论 , 在平 方根 定 律 的 基 础 上 , 立 了 冒 建 口~ 铸 件 间模 数 关 系 式 , 结 出 适 用 于 各 总 种 复 杂铸 件 的 模 数 计 算 方 法 , 冒 口 参 数 把 设 计 定 量 化 。 至 今 , 种 冒 口设 计 方 法 的 各 演 变 和 发 展 , 没 有 脱 离 模数 理 论 体 系 。 还
按照模数理论 , 论铸件 形体如何 , 无 只 n 与 合 金 有 关 的 常数 ; 一 要 模 数 相 同 , 固 时 间 就 大 抵 相 近 。 模 数 凝 冒 I 的体 积 ; Z l 大 , 件 厚 实 , 固时 间 长 ; 之 亦 然 。 根 铸 凝 反 铸件被补缩部分的体积 ; 据 平方 根 定律 ( - ) 冒 口的 凝 固 模 r= M2, 凝 固 收缩 率 ( ) %; C 与 冒 口和 铸 件 的 相 对 冷 却 速 度 有 一 数 , 与铸 件 的凝 固模 数 , 须 满 足 如 下 必 关系: 关 的系数。 取 = %,= . ,=10 式 () 5 a O 1 c . , 5 可以变 为 ≥ 坛 () 2
,
V V= .O一 . +0 5 / , O1 r 1 1 . / 0 0
铸件浇冒口设计原则
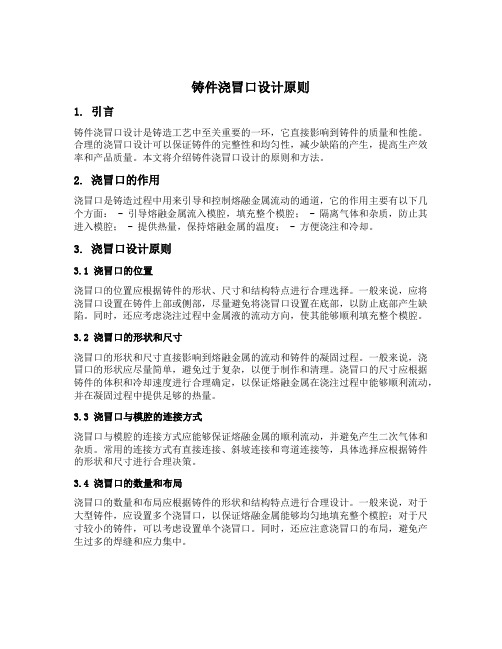
铸件浇冒口设计原则1. 引言铸件浇冒口设计是铸造工艺中至关重要的一环,它直接影响到铸件的质量和性能。
合理的浇冒口设计可以保证铸件的完整性和均匀性,减少缺陷的产生,提高生产效率和产品质量。
本文将介绍铸件浇冒口设计的原则和方法。
2. 浇冒口的作用浇冒口是铸造过程中用来引导和控制熔融金属流动的通道,它的作用主要有以下几个方面: - 引导熔融金属流入模腔,填充整个模腔; - 隔离气体和杂质,防止其进入模腔; - 提供热量,保持熔融金属的温度; - 方便浇注和冷却。
3. 浇冒口设计原则3.1 浇冒口的位置浇冒口的位置应根据铸件的形状、尺寸和结构特点进行合理选择。
一般来说,应将浇冒口设置在铸件上部或侧部,尽量避免将浇冒口设置在底部,以防止底部产生缺陷。
同时,还应考虑浇注过程中金属液的流动方向,使其能够顺利填充整个模腔。
3.2 浇冒口的形状和尺寸浇冒口的形状和尺寸直接影响到熔融金属的流动和铸件的凝固过程。
一般来说,浇冒口的形状应尽量简单,避免过于复杂,以便于制作和清理。
浇冒口的尺寸应根据铸件的体积和冷却速度进行合理确定,以保证熔融金属在浇注过程中能够顺利流动,并在凝固过程中提供足够的热量。
3.3 浇冒口与模腔的连接方式浇冒口与模腔的连接方式应能够保证熔融金属的顺利流动,并避免产生二次气体和杂质。
常用的连接方式有直接连接、斜坡连接和弯道连接等,具体选择应根据铸件的形状和尺寸进行合理决策。
3.4 浇冒口的数量和布局浇冒口的数量和布局应根据铸件的形状和结构特点进行合理设计。
一般来说,对于大型铸件,应设置多个浇冒口,以保证熔融金属能够均匀地填充整个模腔;对于尺寸较小的铸件,可以考虑设置单个浇冒口。
同时,还应注意浇冒口的布局,避免产生过多的焊缝和应力集中。
3.5 浇冒口的排气和除渣在浇注过程中,熔融金属中会存在气体和杂质,因此浇冒口的设计应考虑到排气和除渣的问题。
一般来说,可以在浇冒口附近设置排气孔和除渣孔,以便及时排除气体和杂质,保证铸件的质量。
铸钢件冒口的设计与计算
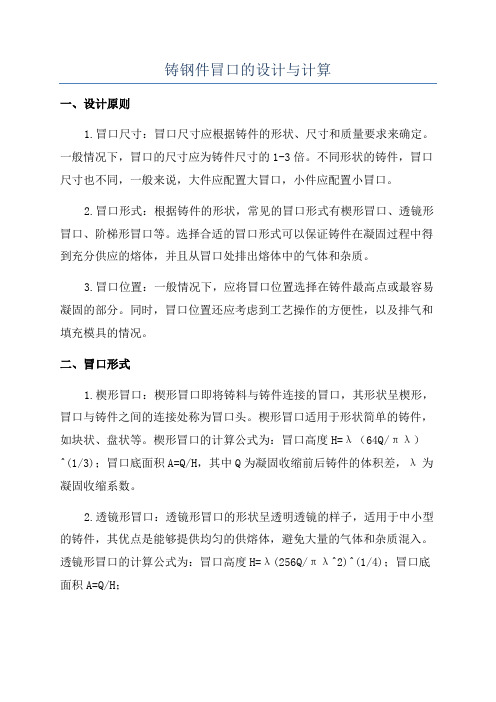
铸钢件冒口的设计与计算一、设计原则1.冒口尺寸:冒口尺寸应根据铸件的形状、尺寸和质量要求来确定。
一般情况下,冒口的尺寸应为铸件尺寸的1-3倍。
不同形状的铸件,冒口尺寸也不同,一般来说,大件应配置大冒口,小件应配置小冒口。
2.冒口形式:根据铸件的形状,常见的冒口形式有楔形冒口、透镜形冒口、阶梯形冒口等。
选择合适的冒口形式可以保证铸件在凝固过程中得到充分供应的熔体,并且从冒口处排出熔体中的气体和杂质。
3.冒口位置:一般情况下,应将冒口位置选择在铸件最高点或最容易凝固的部分。
同时,冒口位置还应考虑到工艺操作的方便性,以及排气和填充模具的情况。
二、冒口形式1.楔形冒口:楔形冒口即将铸料与铸件连接的冒口,其形状呈楔形,冒口与铸件之间的连接处称为冒口头。
楔形冒口适用于形状简单的铸件,如块状、盘状等。
楔形冒口的计算公式为:冒口高度H=λ(64Q/πλ)^(1/3);冒口底面积A=Q/H,其中Q为凝固收缩前后铸件的体积差,λ为凝固收缩系数。
2.透镜形冒口:透镜形冒口的形状呈透明透镜的样子,适用于中小型的铸件,其优点是能够提供均匀的供熔体,避免大量的气体和杂质混入。
透镜形冒口的计算公式为:冒口高度H=λ(256Q/πλ^2)^(1/4);冒口底面积A=Q/H;3.阶梯形冒口:阶梯形冒口由多个楔形冒口组成,适用于尺寸较大、结构复杂的铸件。
阶梯形冒口的计算较为复杂,首先需要计算整个冒口的总高度和底面积,然后根据冒口内各个楔形冒口的高度和底面积之和来确定每个楔形冒口的尺寸。
三、计算方法在进行铸钢件冒口的设计与计算时,一般需要考虑以下几个参数:1.铸件尺寸:包括最大尺寸、最小尺寸、平均尺寸等。
2.凝固收缩率:铸钢件在凝固过程中会产生一定的收缩,该值一般根据实验数据来确定。
3.冒口高度与底面积:根据冒口形式选择相应的计算公式进行计算。
4.填充时间:铸钢件的填充时间一般根据模型铸造实验的经验确定。
以上是关于铸钢件冒口的设计与计算的详细介绍。
- 1、下载文档前请自行甄别文档内容的完整性,平台不提供额外的编辑、内容补充、找答案等附加服务。
- 2、"仅部分预览"的文档,不可在线预览部分如存在完整性等问题,可反馈申请退款(可完整预览的文档不适用该条件!)。
- 3、如文档侵犯您的权益,请联系客服反馈,我们会尽快为您处理(人工客服工作时间:9:00-18:30)。
铸钢件冒口的设计规范钢水从液态冷却到常温的过程中,体积发生收缩。
在液态和凝固状态下,钢水的体积收缩可导致铸件产生缩孔、缩松。
冒口的作用就是补缩铸件,消除缩孔、缩松缺陷。
另外,冒口还具有出气和集渣的作用。
1、冒口设计的原则和位置1.1冒口设计的原则1.1.1、冒口的凝固时间要大于或等于铸件(或铸件被补缩部分)的凝固时间。
1.1.2、冒口所提供的补缩液量应大于铸件(或铸件被补缩部分)的液态收缩、凝固收缩和型腔扩大量之和。
1.1.3、冒口和铸件需要补缩部分在整个补缩的过程中应存在通道。
1.1.4、冒口体内要有足够的补缩压力,使补缩金属液能够定向流动到补缩对象区域,以克服流动阻力,保证铸件在凝固的过程中一直处于正压状态,既补缩过程终止时,冒口中还有一定的残余金属液高度。
1.1.5、在放置冒口时,尽量不要增大铸件的接触热节。
1.2、冒口位置的设置1.2.1、冒口一般应设置在铸件的最厚、最高部位。
1.2.2、冒口不可设置在阻碍收缩以及铸造应力集中的地方。
1.2.3、要尽量把冒口设置在铸件的加工面或容易清除的部位。
1.2.4、对于厚大件一般采用大冒口集中补缩,对于薄壁件一般采用小冒口分散补缩。
1.2.5、应根据铸件的技术要求、结构和使用情况,合理的设置冒口。
1.2.6、对于清理冒口困难的钢种,如高锰钢、耐热钢铸件的冒口,要少放或不放,非放不可的,也尽量采用易割冒口或缩脖型冒口。
2、设置冒口的步骤与方法冒口的大小、位置及数量对于铸钢件的质量至关重要。
对于大型铸钢件来说,必须把握技术标准及使用情况,充分了解设计意图,分清主次部位,集中解决关键部位的补缩。
以模数法为例,冒口设计的步骤如下:2.1、对于大、中型铸钢件,分型面确定之后,首先要根据铸件的结构划分补缩范围,并计算铸件的模数(或铸件被补缩部分的模数)M铸。
2.2、根据铸件(或铸件被补缩部分)的模数M铸,确定冒口模数M冒。
2.3、计算铸件的体收缩ε。
2.4、确定冒口的具体形状和尺寸。
2.5、根据冒口的补缩距离,校核冒口的数量。
2.6、根据铸件结构,为了提高补缩距离,减少冒口的数量,或者使冒口的补缩通道畅通,综合设置内外冷铁及冒口增肉。
2.7、校核冒口的补缩能力,要求ε(V冒+V件)≤V冒η。
3、设计冒口尺寸的方法3.1、模数法在铸件的材料、铸型的性质和浇注条件确定之后,铸件的凝固时间决定于铸件的模数。
模数M=V/A(厘米),V—体积(厘米3);A—散热面积(厘米2)。
随着办公条件的改善,计算机的普及,模数可以用计算机进行计算。
方法是:用SolidWorks软件画出铸件(或铸件被补缩部分)的立体图,计算出铸件的体积和散热面积,然后用公式M=V/A计算模数。
冒口的凝固时间大于铸件的凝固时间,冒口的模数一般是铸件模数的1.1~1.2倍,M冒=1.1~1.2M铸对于厚实铸件,如:圆柱体、块状铸件,用模数法确定的冒口往往偏大,故必须采取一些方法加快铸件的凝固,同时延长冒口的凝固时间。
通常采用以下方法:1、加放内、外冷铁;2、补浇冒口;3、采用保温冒口。
采用以上措施后,M冒=KM铸,K按下表进行选择。
注:对于要求比较高的铸件、探伤件,尽量不放内冷铁。
3.2、热节圆法根据铸件壁厚部位热节圆的大小来确定冒口尺寸的一种方法。
热节圆法主要适用于轮形铸件,一般冒口与热节不连通,需要用滚热节圆的方法确定冒口增肉,然后确定冒口尺寸。
可以用绘图软件画出铸件热节的形状,然后画出热节的内切圆,即为热节圆。
4、钢的体收缩率碳钢的体收缩率εC的大小与碳钢的含碳量和浇注温度有关。
如下图:合金钢的体收缩率比碳钢大,它既与含碳量和浇注温度有关也与合金元素及其含量有关。
合金元素对铸钢体收缩率的影响如下:合金元素W Ni Mn Cr Si Al修正系数Ki -0.53 -0.0354 0.0585 0.12 1.03 1.7合金钢的体收缩率ε=εC+∑KiXi Xi为合金元素的含量注:以上修正系数只适用于低于1600℃时的体收缩。
5、冒口的有效补缩距离冒口区与末端区之和称为冒口补缩距离,超出该距离,在铸件中间区产生轴线缩松。
5.1、板件和杆件的补缩距离通常把断面的宽厚比为5:1以上的称为板型件;断面的宽厚比为5:1以下的称为杆型件。
下图为碳钢(C=0.20~0.30%),板型件的厚度≤175mm、杆型件的厚度≤200mm的冒口有效补缩距离。
在铸件的末端区和冒口之间放外冷铁,冒口有效补缩距离如下:从以上可以看出:(1)冒口对板型件的有效补缩距离大于杆型件的有效补缩距离。
(2)杆型件的末端区长度远大于冒口区长度。
(3)使用外冷铁,可以有效的提高冒口的有效补缩距离。
另外,冒口的有效补缩距离还受以下因素的影响:(1)厚实铸件的凝固区域变宽,冒口的有效补缩距离相对较小。
(2)结晶温度范围较宽的铸钢,冒口的有效补缩距离较小;结晶温度范围较窄的铸钢,冒口的有效补缩距离较大。
例如,含碳量为0.15%的碳素钢比含碳量为0.30%的碳素钢的结晶温度范围较窄,冒口的有效补缩距离较后者大30%。
(3)使用发热冒口,可以增加冒口的有效补缩距离。
5.2、轮型件冒口的有效补缩距离轮型件讲究冒口的延续度。
冒口的延续度为冒口根部长度(沿轮型周向)之和与轮形周长的比率,称为冒口的延续度。
延续度的大小取决于轮缘的厚度与其内在质量的要求程度。
如铣齿齿轮、缸体其延续度适当增加,不重要的且厚壁轮型件可适当减少。
(1)一般小件(φ600mm)不铣齿的轮型件,冒口的延续度取25~35%。
(2)中等高度和大小齿轮和齿圈(铣齿深度不超度4/10轮缘厚度),冒口的延续度取36~40%。
(3)轮缘较高的双辐板、三辐板齿轮,冒口的延续度取38~42%。
(4)高压缸类的受压与有探伤要求件,冒口延续度可取100%。
6、冒口补贴对于致密度要求高的铸件,当冒口的补缩距离达不到时,应在冒口处设置补贴造成向冒口方向的顺序凝固,以增加冒口的补缩距离。
6.1、水平补贴水平补贴可以按下图进行计算6.2、垂直补贴对于壁厚≤100mm碳素钢板状铸件,浇注系统为上注时,铸件的补贴厚度如下图:根据铸钢件的形状、浇注位置和钢种的不同,补贴厚度=K1K2a,K1 为杆状件补贴的补偿系数,K2 为铸件材质和浇注方式的补偿系数。
杆状件补贴的补偿系数K1横断面的宽厚比 4.0:1.0 3.0:1.0 2.0:1.0 1.5:1.0 1.0:1.0补偿系数 1.0 1.25 1.5 1.7 2.0铸件材质和浇注方式的补偿系数K2碳钢及低合金钢高合金钢材质和浇注方式上注底注上注底注补偿系数 1.0 1.25 1.25 1.56厚实铸件的轴线缩松是很难消除的,对于一般铸件,轴线缩松只要不被切削加工所显露,则不影响它的使用性能。
对于压力容器铸件和用于承受疲劳冲击应力的铸件,一般均随其工矿压力、温度、应力状况和铸件壁厚的不同,而分别允许存在射线探伤等级1~3级的轴线缩松。
一般铸钢件的轴线缩松允许4~5级。
据厚度为100~150mm介于杆-板之间的铸钢试验件的试验结果,射线探伤质量等级与补贴斜率存在如下关系:对大型汽轮机缸体、泵体类薄壁型打压、探伤铸件的补缩,根据日本室兰的经验,UT按ASTM标准,RT按ASME标准,对不同补缩斜度的铸件进行无损检测的结果,补缩斜度可按:补缩斜度8%(1:12.5)可达1级补缩斜度6%(1:16.6)可达2级补缩斜度3%(1:33.3)可达3级7、冒口的补缩效率不同类型的冒口的补缩效率η为:另外,冒口覆盖剂也能提高冒口的补缩效率。
好的覆盖剂可以提高冒口的补缩效率5%。
8、保温冒口目前,保温套主要分成:珍珠岩复合型保温套、纤维复合型保温套、空心微珠复合型保温套和陶粒保温套。
后两种可以做较大铸钢件的保温套。
保温套的堆密度一般控制在0.6~0.8g/cm3。
保温套的厚度一般取保温冒口模数的1~1.5倍,保温效果好的取下限。
保温剂的用量约为冒口重量的1.0~1.7%,冒口的上部不见红时,保温效果比较理想。
在此条件下,保温冒口的模数约为普通冒口模数的1.3~1.4倍,补缩效率为25~45。
9、冒口的形状与尺寸按照冒口的保温性能可分为普通冒口和保温冒口;按照冒口的形状可分为圆冒口和矩形冒口;按照冒口是否被砂型所覆盖可分为明冒口和暗冒口。
目前,在我厂铸钢件的生产过程中,直径小于(或等于)1600mm圆冒口,一般采用保温冒口,直径大于1600mm圆冒口,一般采用普通冒口。
为了提高冒口的补缩距离(或延续度),可采用矩形冒口。
在铸件的上部一般采用明冒口,在铸件的下部一般采用暗冒口。
9.1、圆形暗冒口9.2、矩形明冒口矩形明冒口的重量和模数:编号 A BH250 300 350 400 450 500 550 600 700 8001 300 150 96 120 144 170 198 3.7 4.1 4.4 4.6 4.72 350 200 178 212 250 285 326 4.8 5.1 5.3 5.5 5.73 400 250 295 341 392 445 500 5.7 6.0 6.2 6.5 6.74 500 300 500 570 643 722 810 6.8 7.1 7.4 7.6 7.95 600 350 780 880 985 1090 1200 7.9 8.2 8.5 8.7 9.06 700 400 1160 1290 1420 1700 1990 8.9 9.3 9.6 10.0 10.69.3、圆型明冒口圆形明冒口的重量、模数表9.4、保温冒口保温冒口的重量、模数表编号φ高度(H)400 450 500 550 600 700 800 900 1000 1100 1200 1300 1400 15001 400 362 407 452 497 5436.7 6.97.1 7.3 7.52 500 636 707 777 848 9898.0 8.3 8.6 8.8 9.23 600 1221 1424 1628 1730 183110.0 10.5 10.9 11.3 11.54 700 1939 2216 2354 2493 2769 304611.7 12.2 12.6 13.0 13.3 13.55 800 2894 3256 3617 3979 434113.3 13.8 14.3 14.7 15.06 900 4120 4578 5036 5494 5952 640915.0 15.5 16.0 16.4 16.7 17.07 1000 5652 6217 6782 7348 7913 847816.7 17.2 17.6 18.1 18.4 18.8编号φ高度(H)1100 1200 1300 1400 1500 1600 1700 1800 1900 20008 1100 7523 8207 8891 9574 10258 10942 18.3 18.9 19.3 19.7 20.1 20.59 1200 9767 10581 11394 12208 13022 13836 14650 20.0 20.5 21.0 21.4 21.8 22.2 22.510 1300 12417 13373 14328 15283 16238 17193 18149 21.7 22.2 22.7 23.1 23.5 23.9 24.211 1400 15509 16617 17725 18832 19940 2104823.3 23.9 24.3 24.8 25.2 25.6 25.912 1500 19076 20347 21619 22891 24162 25434 25.0 25.5 26.0 26.5 26.9 27.313 1600 23151 24598 26044 27491 28938 26.7 27.2 27.7 28.1 28.69.5、冒口座、冒口圆角冒口与铸件的接触部位要做出圆角,保温冒口的下部要做冒口座。