大型铸钢件冒口设计及其凝固过程模拟
铸造凝固过程数值模拟
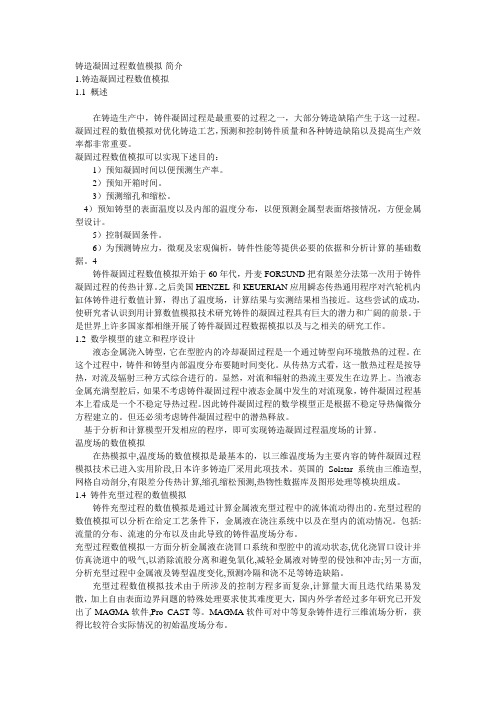
铸造凝固过程数值模拟-简介1.铸造凝固过程数值模拟1.1 概述在铸造生产中,铸件凝固过程是最重要的过程之一,大部分铸造缺陷产生于这一过程。
凝固过程的数值模拟对优化铸造工艺,预测和控制铸件质量和各种铸造缺陷以及提高生产效率都非常重要。
凝固过程数值模拟可以实现下述目的:1)预知凝固时间以便预测生产率。
2)预知开箱时间。
3)预测缩孔和缩松。
4)预知铸型的表面温度以及内部的温度分布,以便预测金属型表面熔接情况,方便金属型设计。
5)控制凝固条件。
6)为预测铸应力,微观及宏观偏析,铸件性能等提供必要的依据和分析计算的基础数据。
4铸件凝固过程数值模拟开始于60年代,丹麦FORSUND把有限差分法第一次用于铸件凝固过程的传热计算。
之后美国HENZEL和KEUERIAN应用瞬态传热通用程序对汽轮机内缸体铸件进行数值计算,得出了温度场,计算结果与实测结果相当接近。
这些尝试的成功,使研究者认识到用计算数值模拟技术研究铸件的凝固过程具有巨大的潜力和广阔的前景。
于是世界上许多国家都相继开展了铸件凝固过程数据模拟以及与之相关的研究工作。
1.2 数学模型的建立和程序设计液态金属浇入铸型,它在型腔内的冷却凝固过程是一个通过铸型向环境散热的过程。
在这个过程中,铸件和铸型内部温度分布要随时间变化。
从传热方式看,这一散热过程是按导热,对流及辐射三种方式综合进行的。
显然,对流和辐射的热流主要发生在边界上。
当液态金属充满型腔后,如果不考虑铸件凝固过程中液态金属中发生的对流现象,铸件凝固过程基本上看成是一个不稳定导热过程。
因此铸件凝固过程的数学模型正是根据不稳定导热偏微分方程建立的。
但还必须考虑铸件凝固过程中的潜热释放。
基于分析和计算模型开发相应的程序,即可实现铸造凝固过程温度场的计算。
温度场的数值模拟在热模拟中,温度场的数值模拟是最基本的,以三维温度场为主要内容的铸件凝固过程模拟技术已进入实用阶段,日本许多铸造厂采用此项技术。
英国的Solstar系统由三维造型,网格自动剖分,有限差分传热计算,缩孔缩松预测,热物性数据库及图形处理等模块组成。
大中型厚壁球铁箱体零件的铸造工艺及数值模拟分析

大中型厚壁球铁箱体零件的铸造工艺及数值模拟分析摘要:厚大球铁铸件在铸造时,常应用无冒口铸造工艺与冷铁配合的方法,能够有效提高冒口补缩能力,消除缩孔、缩松和铁豆等铸造缺陷,保证铸件质量,并且还使树脂砂用量减少,提高了工艺出品率。
而为了提高铸造的合格率,常在进行无冒口铸造时添加较小的补偿冒口。
并基于pro/e与procast对铸造工艺进行改进数值模拟,根据模拟结果对工艺进行改进。
关键词:无冒口;球铁铸件;冷铁1 铸件结构特点箱体结构,内部中空,由多个隔板分隔,上下为两个大平板,上板较大,使用时承载其上的部件,板上有螺纹孔和油槽用于固定和润滑,下板通过螺纹孔与下部固定。
侧壁倾斜并内凹。
在上平板上有四个对称分布,呈工字型的油槽,用于将重物放于其上时的润滑,防止该移动板与其他重物接触时因力量过大而产生磨损。
隔板与外壁相交处散热较难,易产生热节,产生缩松,在工艺设计时应注意应用冷铁等措施改进这些部位的散热。
最大壁厚50mm,最小壁厚30mm,该铸件为大型厚壁铸件,壁厚较均匀且与铸件尺寸相适应。
生产经验表明:具有较大平板的铸件,如机床床身等,会因为结构的刚度差,或由于铸件各表面冷却条件的差别产生的内应力,产生翘曲变形。
该件内腔多处为隔板,能够起到拉肋的作用,因此在一定程度上避免了翘曲变形。
2 无冒口铸造工艺原理球墨铸铁中的碳以球形石墨的形态存在,流动性和线收缩与灰铸铁相近,体收缩及形成内应力倾向较大,易产生缩松和裂纹。
在铁水凝固过程中,具有石墨化膨胀的特点,适宜采用均衡凝固方式,要求砂型的刚度较高,在铸件膨胀时约束铸件,对其产生反作用力,形成自补缩。
自补缩不足的部分可以利用冒口进行补缩,冒口的补缩量和补缩时间均较小,可以有效提高铸件的工艺出品率。
本件为厚大球铁件,适用于无冒口铸造的工艺。
3 铸造工艺设计3.1 分型面与浇注位置的选择采用卧浇卧冷,使合型位置、浇注位置、冷却位置相同。
将零件上部的大平板置于铸型下部。
铸件充型凝固过程数值模拟
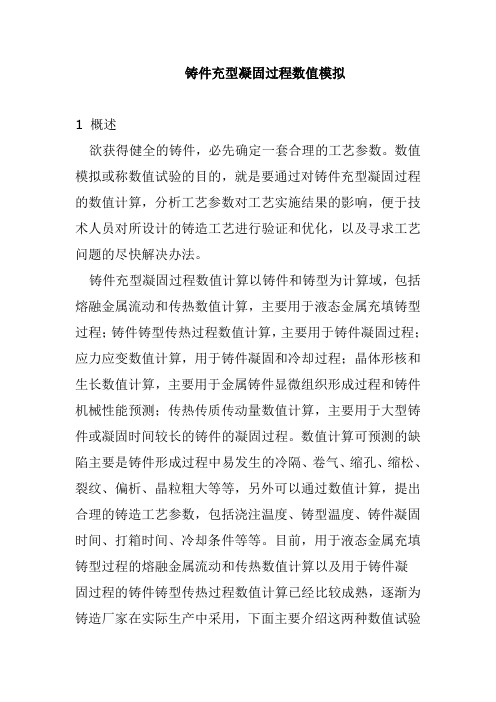
铸件充型凝固过程数值模拟1 概述欲获得健全的铸件,必先确定一套合理的工艺参数。
数值模拟或称数值试验的目的,就是要通过对铸件充型凝固过程的数值计算,分析工艺参数对工艺实施结果的影响,便于技术人员对所设计的铸造工艺进行验证和优化,以及寻求工艺问题的尽快解决办法。
铸件充型凝固过程数值计算以铸件和铸型为计算域,包括熔融金属流动和传热数值计算,主要用于液态金属充填铸型过程;铸件铸型传热过程数值计算,主要用于铸件凝固过程;应力应变数值计算,用于铸件凝固和冷却过程;晶体形核和生长数值计算,主要用于金属铸件显微组织形成过程和铸件机械性能预测;传热传质传动量数值计算,主要用于大型铸件或凝固时间较长的铸件的凝固过程。
数值计算可预测的缺陷主要是铸件形成过程中易发生的冷隔、卷气、缩孔、缩松、裂纹、偏析、晶粒粗大等等,另外可以通过数值计算,提出合理的铸造工艺参数,包括浇注温度、铸型温度、铸件凝固时间、打箱时间、冷却条件等等。
目前,用于液态金属充填铸型过程的熔融金属流动和传热数值计算以及用于铸件凝固过程的铸件铸型传热过程数值计算已经比较成熟,逐渐为铸造厂家在实际生产中采用,下面主要介绍这两种数值试验方法。
1.1 数学模型熔融金属充型与凝固过程为高温流体于复杂几何型腔内作有阻碍和带有自由表面的流动及向铸型和空气的传热过程。
该物理过程遵循质量守恒、动量守恒和能量守恒定律,假设液态金属为常密度不可压缩的粘性流体,并忽略湍流作用,则可以采用连续、动量、体积函数和能量方程组描述这一过程。
质量守恒方程∂ u/∂ x+∂ v/∂ y+∂ w/∂ z= 0 (2-1)动量守恒方程∂(ρ u)/∂ t+u∂(ρ u)/∂ x+v∂(ρ u)/∂ y+w∂(ρ u)/∂z= -∂ p/∂ x+μ(∂2u/∂ x2+∂2v/∂y2+∂ 2w/∂z2)+ρ g x (2-2a)∂(ρ v)/∂ t+u∂(ρ v)/∂ x+v∂(ρ v)/∂ y+w∂(ρ v)/∂z= -∂ p/∂y+μ (∂2u/∂x2+∂2v/∂y2+∂ 2w/∂ z2)+ρg y (2-2b)∂(ρ w)/∂ t+u∂(ρ w)/∂x+v∂(ρ w)/∂ y+w∂(ρ w)/∂ z= -∂ p/∂z+μ (∂2u/∂ x2+∂2v/∂ y2+∂ 2w/∂z2)+ρ g z (2-2c)体积函数方程∂F/∂ t+∂(Fu)/∂ x+∂(Fv)/∂ y +∂(Fw)/∂ z=0 (2-3)能量守恒方程∂(ρc p T)/∂t+∂(ρ c p uT)/∂x+∂(ρ c p vT)/∂ y +∂(ρ c p wT)/∂ z= ∂(λT/∂x)/∂x+∂(λT/∂ y)/∂ y +∂(λT/∂ z)/∂ z+q v (2-4)式中u,v,w —— x,y,z 方向速度分量(m/s);ρ——金属液密度(kg/m3);t ——时间(s);p ——金属液体内压力(Pa);μ ——金属液分子动力粘度(Pa.s);g x, g y, g z —— x,y,z 方向重力加速度(m/s2);F ——体积函数,0≤F≤1;c p ——金属液比定压热容[J/(kg.K)];T ——金属液温度(K);λ ——金属液热导率[W/(m.K)];q——热源项[J/(m3.s)]。
完整版铸钢件冒口的设计与计算
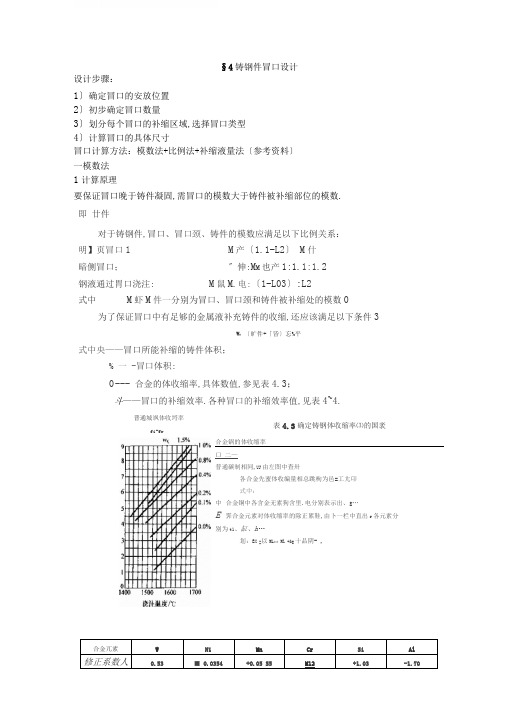
§4铸钢件冒口设计设计步骤:1〕确定冒口的安放位置2〕初步确定冒口数量3〕划分每个冒口的补缩区域,选择冒口类型4〕计算冒口的具体尺寸冒口计算方法:模数法+比例法+补缩液量法〔参考资料〕一模数法1计算原理要保证冒口晚于铸件凝固,需冒口的模数大于铸件被补缩部位的模数.即 廿件对于铸钢件,冒口、冒口颈、铸件的模数应满足以下比例关系:明】页冒口1M 产〔1.1-L2〕 M 什 暗侧冒口;〞伸:M M 也产1:1.1:1.2 钢液通过胃口浇注:M 鼠M.电:〔1-L03〕:L2 式中 M 虾M 件一分别为冒口、冒口颈和铸件被补缩处的模数0为了保证冒口中有足够的金属液补充铸件的收缩,还应该满足以下条件3W V 〔旷件+「皆〕忘%平式中央——冒口所能补缩的铸件体积;% 一 -冒口体积:0 --- 合金的体收缩率,具体数值,参见表4.3;斗——冒口的补缩效率.各种冒口的补缩效率值,见表4~4.表4.3确定铸钢体收缩率⑶的国袤 合金锅的体收缩率 口 二—普通碳制相同,UJ 由左图中查卅各合金先蜜体收编量相总跳枸为邑=工尢卬式中:中 合金铜中各含金无素狗含里.电分别表示出、g …E 霁合金元素对体收缩率的除正累鞋,由卜一栏中直出r 各元素分别为t1、缸、h …划:EX =以ML** Ml +&g 十品阴- ,合金兀素W Ni Mn Cr Si Al 修正系数人0.53 ■ 0.0354 +0.05 S5 M12 +1.03 -1.70 普通城飒体收埒率fi-fr总结:M冒=1.2M件P127式4-5,左边为总收缩量,右边为由冒口补充量2计算步骤1〕计算铸件模数根据铸件需补缩部位,划分补缩区,分别计算铸件的模数.计算方法:公式计算+图表计算—表4-5 〔p128-130〕.2〕计算冒口及胃口颈模数.根据热节的位置,确定胃口的类型,再根据式〔4-2〕或式〔4-3〕、式〔4-4〕. 即可计算出国口及冒口颈模数计算举例;铸钢件在下部法上处放置暗冒口补缩. 如图4-3三所示.求吩和利用表4・5中上形体计算公式,法兰处o=200mm, b—lOOnun*非散热面可得:“*0x20 …M 社=—j ---- ——cm = 3.636cm件2〔10 + 20〕-5因浇口通过冒口,故:1.05Mr = 374 cm 加冒=L2A/件=436 cmS 中左边的冒口颈…W R=〔22X 10X2〔22+10〕]四4一箝补缩铸钢件法兰的目口颈cm- 3.43cm,小于3.74cm,不能满足补缩要求,在铸件热节处将出现缩松口采用右边的冒口颈,必=Q0X 12V[2QO+I2〕]crti=3.75cm,满足了要求.计算M件用L形体计算公式,为什么不用法兰体公式去套呢?〔法兰体高度b无法确定〕图4-33B-B剖面图中200应改为220,因计算M B时用的数值是220;另外, 冒口直径为〔|〕220,其冒口颈宽也应为220.〔A-A剖面图中200改否.〕采用右边的A-A剖面冒口颈满足了要求,A-A剖面冒口颈尺寸怎么得来的呢?不要瞎懵,可列式M仝^=3.74=20X/[2 〔20+X〕],求出X=12.生产中可根据M冒数值查出标准侧冒口,得冒口尺寸〔直径、高等〕,冒口颈尺寸,冒口体积、重量,能补缩的铸件体积及重量〔 M冒结合一查〕.3〕确定铸钢件体收缩率由表4-3求出.例如,ZG270-500的平均W C=0.35%,假设浇注温度为1560℃,可从表4-3 查出=4.7%〔碳钢e V= e C〕.£V如何查出的呢?浇注温度为1560 C; W C=0.40%, ev=5%; W C=0.20%,&V=3.8%;据此列式〔5-3.8〕 / 〔0.4-0.2〕 = 〔5-X〕 / 〔0.4-0.35〕,解出X=4.7 〔插入法,比例法〕4〕确定冒口形状和尺寸查相关表格.5〕确定冒口数目6〕校核冒口的最大补缩水平.二比例法〔热节圆法〕使冒口根部直径大于铸件被补缩处热节圆直径或壁厚, 再以冒口根部直径来确定其他尺寸.D=cd式中D ……冒口根部直径;c ••…比例系数,参见表4-6;〔查表步骤〕d ……铸件被补缩热节处内切圆直径.可用作图法画出图4-34热节圆直件a 〕壁厚均匀b 〕壁面和交查表步骤:1〕选取比例系数c 〔先按铸件结构选择冒口类型,再选比例系数〕2〕确定冒口高度〔根据直径 D 确定〕;3〕确定每个冒口长度或冒口个数〔根据冒口延伸度确定〕.三铸件工艺出品率的校核表4-7说明校核方法.采用普通冒口时,冒口尺寸 可根据表中数值进行验算 和调整,即将冒口重量代入 计算后,假设工艺出品率低于 表中数值,那么冒口尺寸偏 大,可适当减小冒口高度; 假设高于表中数值,那么应加大 冒口尺寸或增加冒口个数.四冒口计算举例 见p133例题.图535 ZG35SiMn 铸钢齿轮铸件1模数法工艺出品率= 铸件重量铸件重量+浇铸系统重 量+冒口重量轮缘与轮辐的交接处为热节,其直径d按作图法得50〔大于轮缘厚40〕;按作图法且考虑热节增大,见P126图4-31,dy=d+〔10~30〕,取d=60 〔见P134比例法〕.轮缘热节处按表4-5应为板与杆的相交体,由图4-35可得a=d=60mm, b=180mm,c=24mm.2比例法〔热节圆法〕作业:如下列图铸钢齿圈坯件ZG25,为一圆环,中径〔|〕920,厚80,高240, 有三种补缩方案:3个6190冒口, 3个6190冒口和3个冷铁,尺寸为:宽100X厚50X高240, 6个6190冒口.按有效补缩距离检验,冒口数目是否足够?。
大型铸钢件冒口设计及其凝固过程模拟
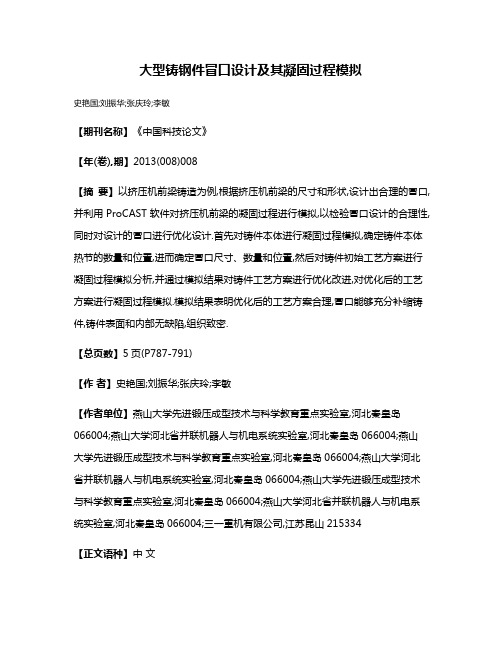
大型铸钢件冒口设计及其凝固过程模拟史艳国;刘振华;张庆玲;李敏【期刊名称】《中国科技论文》【年(卷),期】2013(008)008【摘要】以挤压机前梁铸造为例,根据挤压机前梁的尺寸和形状,设计出合理的冒口,并利用ProCAST软件对挤压机前梁的凝固过程进行模拟,以检验冒口设计的合理性,同时对设计的冒口进行优化设计.首先对铸件本体进行凝固过程模拟,确定铸件本体热节的数量和位置,进而确定冒口尺寸、数量和位置,然后对铸件初始工艺方案进行凝固过程模拟分析,并通过模拟结果对铸件工艺方案进行优化改进,对优化后的工艺方案进行凝固过程模拟.模拟结果表明优化后的工艺方案合理,冒口能够充分补缩铸件,铸件表面和内部无缺陷,组织致密.【总页数】5页(P787-791)【作者】史艳国;刘振华;张庆玲;李敏【作者单位】燕山大学先进锻压成型技术与科学教育重点实验室,河北秦皇岛066004;燕山大学河北省并联机器人与机电系统实验室,河北秦皇岛066004;燕山大学先进锻压成型技术与科学教育重点实验室,河北秦皇岛066004;燕山大学河北省并联机器人与机电系统实验室,河北秦皇岛066004;燕山大学先进锻压成型技术与科学教育重点实验室,河北秦皇岛066004;燕山大学河北省并联机器人与机电系统实验室,河北秦皇岛066004;三一重机有限公司,江苏昆山215334【正文语种】中文【中图分类】TG244+.4【相关文献】1.铸钢件锚的动态顺序凝固浇冒口设计 [J], 李宏兴2.大型铸钢件冒口设计及其凝固过程模拟 [J], 史艳国;刘振华;张庆玲;李敏;3.用比较法设计大型铸钢件冒口 [J], 王永云4.动态模数法在大型铸钢件冒口设计中的应用 [J], 华勤;顾超5.运用均衡凝固理论设计铸钢件曲柄的浇冒口 [J], 焦玉胜;李宏兴因版权原因,仅展示原文概要,查看原文内容请购买。
连铸过程中板坯凝固的数值模拟

连铸过程中板坯凝固的数值模拟
QS C PVT
(5-10) 由式(5-9)与式(5-10)等量置换可得
f S C P T / L
(5-11) 此法采用固相率的增加来代替前热的放出,如果 f S 1 ,则表明该领域 V 的 凝固结束。
热焓法
凝固过程金属的焓可定义为
H cdT (1 f s ) L
L ——潜热, J / kg ;
f s ——固相率;
T ——温度, C ;
——时间, s ;
连铸过程中板坯凝固的数值模拟
——导热系数, W /(m K ) ;
x, y ——二维坐标, m 。
对于实用多元和金,要确定固相率和温度的关系,通常可以先采用热分析法 求出凝固开始温度 TL (液相线温度)和结束温度 TS (固相线温度),假定如下: (1)假定为线性分布时
式中, L ——补偿对流换热的等效导热系数;
m ——经验常数,钢液导入区, m 4 ~ 8 ;
S ——静止钢液的导热系数。
热物性参数的数值处理方法
由于导热系数、比热和密度是随温度变化的,其处理方法一般有常数法、线 形函数法和插值法等,在不同的温度区间内用二次曲线拟合的方法得到温度导热系数、温度-比热之间关系的曲线,来确定导热系数、比热值。 对于板坯密度的取值,可在不同相区内取不同的值。 (1) 固相区: S 7.6 10 3 kg / m 3 ;
大型铸钢圆筒件的铸造工艺设计及数值模拟本科毕业论文

摘要材料成型与控制工程专业本科毕业论文大型铸钢圆筒件的铸造工艺设计与数值模拟本科毕业论文(设计)摘要本文运用传统方法完成了对铸钢圆筒件的铸造工艺方案设计,包括分型面、浇注位置的选择、砂芯、各项铸造工艺参数的确定以及浇注系统、冒口、冷铁的设计。
根据铸件体积较大的特点,在铸件两侧设计了用两个内浇道同时对铸件进行浇注的浇注系统;在2个热节处安置冒口,并将冷铁配合使用来实现铸件的定向凝固。
建立了铸件的三维模型,用ViewCast软件模拟了铸钢件圆筒的充型和凝固过程。
模拟结果显示,在铸件靠近内浇道处会产生缩孔缩松缺陷。
根据数值模拟结果并结合理论分析,使用发热材料的方法来改进工艺,经过优化设计,最大程度地消除了铸造缺陷,从而获得了合适的铸造工艺方案。
关键词:铸造工艺;数值模拟;设计优化AbstractAbstractThe casting technological parameters of the Steel casting cylinder, including the parting surface, pouring position, pouting system, riser and chill were defined by using traditional methods in the paper. According to the casting characteristics of big shape, on both sides of the casting is designed with two runner which pouring the casting at the same time; calculating the volume of the riser in the hot spot, and with the use of cold iron to achieve directional solidification sequence of casting. The 3-D model of the casting was build and the simulation software, ViewCast, was employed to analyze the solidification process and filling process of the casting. The simulation result indicates that the shrinkage defects formed department within the sprue .According to the simulation result the original technological parameters, using the method of extending cold iron in the side of the cold iron, in the other side of the cold iron sets the gating system, and with the use of fever materials to the improve process, after several rounds of optimization design, the defects were eliminated to the greatest extent, obtaining the optimal technology program eventually. Keywords:casting process; numerical simulation; design optimization目录目录摘要 (II)Abstract (III)第1章绪论 (1)1.1 铸造成形加工技术的国内外发展 (1)1.1.1 国外发展状况 (1)1.1.2 国内发展情况 (2)1.2 计算机技术在铸造业的应用 (3)1.2.1 铸造模拟软件的概述 (3)1.2.2 计算机模拟的优点 (4)1.3 本文主要研究内容 (6)1.3.1主要研究内容 (6)1.3.2 拟采用的方法 (6)第2章大型铸钢圆筒件的传统工艺方案的设计 (9)2.1 铸件的结构特点及工艺要求 (9)2.1.1 生产条件 (9)2.1.2 主要技术要求 (9)2.2 零件结构的铸造工艺性 (9)2.2.1 铸件质量对零件结构的要求 (9)2.2.2 铸造方法的选择 (10)2.2.3 分型面的选择 (10)2.3 铸造工艺设计参数 (11)2.4 砂芯设计 (13)2.4.1 砂芯形状及分盒面的选择原则 (13)2.4.2 芯头设计 (13)2.4.3 砂芯的固定和定位 (14)2.4.4 芯骨 (14)本科毕业论文(设计)2.5 浇注系统的设计 (14)2.5.1 铸钢件浇注系统类型 (14)2.5.2 浇注系统结构尺寸的设计 (14)2.5.3 浇注系统引入位置的确定 (18)2.6 冒口的设计 (18)2.7 铸钢件冷铁的设计 (19)第3章铸件数值模拟及工艺的优化 (21)3.1 初始方案模拟结果与分析 (21)3.1.1 几何模型的建立 (21)3.1.2 凝固过程模拟及结果分析 (21)3.2 优化方案 (23)3.2.1 工艺改进 (23)3.2.2 凝固过程模拟及结果分析 (24)3.2.3 充型过程模拟结果与分析 (26)结论 (31)参考文献 (33)致谢........................................................................................ 错误!未定义书签。
铸铁件冒口设计手册

铸铁件冒口设计手册诸葛胜福士科铸造材料(中国)有限公司铸铁冒口设计手册一、概述冒口是一个个储存金属液的空腔。
其主要作用是在铸件成形过程中提供由于体积变化所需要补偿的金属液,以防止在铸件中出现的收缩类型缺陷(如图1和图2所示),而这些需要补偿的体积变化可能有:图1 各种缩孔图2 缩孔生产图a)和冒口的补缩图b)1—一次缩孔 2—二次缩孔 3—缩松 1—缩孔 2—型腔胀大 3—铸件(虚线以内) 4—显微缩松 5—缩陷(缩凹,外缩孔)(1)铸型的胀大(2)金属的液态收缩(3)金属的凝固收缩补偿这些体积变化所需要的金属液量随着铸型和金属种类的不同而异。
此外,冒口还有排气及浮渣和非金属夹杂物的作用。
铸件制成后,冒口部分(残留在铸件上的凸块)将从铸件上除去。
由此,在保证铸件质量要求的前提下,冒口应尽可能的小些,以节省金属液,提高铸件成品率。
由此冒口的补缩效率越高,冒口将越小,铸件成品率越高、越经济。
FOSECO公司的发热保温冒口具有高达35%的补缩效率;因而,具有极高的成品率和极其优越的经济性。
在金属炉料价格飞涨的情况下,其优越性显得尤其突出。
另外,高品质发热保温冒口,及其稳定可靠的产品质量是获得高品质铸件的重要手段和可靠的质量保证。
二、铸铁的特点铸钢和铸铁都是铁碳合金,它们在凝固收缩过程中有共同之处)如凝固前期均析出初生奥氏体树枝晶,都存在着液态、凝固态和固态下的收缩),但也有不同的特点。
其根本不同之处是铸铁在凝固后期有“奥氏体+石墨”的共晶转变,析出石墨而发生体积膨胀,从而可部分地或全部抵消凝固前期所发生的体积收缩,即,具备有“自补缩的能力”。
因此在铸型刚性足够大时,铸铁件可以不设冒口或采用较小的冒口进行补缩。
灰铸铁在共晶转变过程中析出石墨,并在与枝晶间的液体直接接触的尖端优先长大,其石墨长大时所产生的体积膨胀直接作用在晶间液体上,进行“自补缩”。
对于一般低牌号的灰铁铸件,因碳硅含量高,石墨化比较完全,其体积膨胀量足以补偿凝固时的体收缩,故不需要设置冒口,只放排气口。
大型钢锭凝固过程三维数值模拟

大型钢锭凝固过程三维数值模拟李文胜;沈丙振;周翔;沈厚发;柳百成【摘要】开发了大型钢锭凝固过程三维模拟程序.利用本程序对53 t钢锭的凝固过程进行了模拟,预测的钢锭和锭模中典型测试点的冷却曲线、钢锭完全凝固时间及冒口一次缩孔形状等与商用有限元软件ProCAST的计算结果吻合良好.【期刊名称】《大型铸锻件》【年(卷),期】2010(000)003【总页数】4页(P1-4)【关键词】大型钢锭;凝固;温度场;数值模拟【作者】李文胜;沈丙振;周翔;沈厚发;柳百成【作者单位】清华大学机械工程系,北京100084;中信重工机械股份有限公司,河南471039;中信重工机械股份有限公司,河南471039;清华大学机械工程系,北京100084;清华大学机械工程系,北京100084【正文语种】中文【中图分类】TG156.3随着电力、冶金、石化、船舶等工业领域重大装备中锻件的大型化,使用的钢锭也在向超大型化方向发展。
大型钢锭中通常存在缩孔、缩松等缺陷。
由于实验研究代价高,因此数值模拟成为认识这些缺陷和优化钢锭设计的重要途径[1、2]。
文献中有关钢锭凝固过程传热现象的数学模型多为二维或轴对称模型[1,3~6]。
实际上,钢锭的传热是三维的,目前的计算条件也可以满足大型钢锭三维计算的要求。
最近,文献[7、8]利用商用有限元软件ProCAST[9]对钢锭凝固过程进行了三维模拟。
但是,文献[7]仅对实测的缩孔形状进行了比较,而文献[8]预测的凝固时间与实测差别较大。
显然,模拟结果的准确性及软件的实用性,取决于模型与方法的准确性,同时也取决于材料物性参数、界面换热系数等基本参数是否符合实际。
本文开发了大型钢锭凝固三维模拟程序FT-INGOT,同时通过与ProCAST计算结果的比较与验证,得出了53 t钢锭冷却曲线、凝固时间和一次缩孔形状。
图1 53 t钢锭尺寸与测试点位置的示意图Figure 1 Dimension of 53-ton ingot and locations for temperature comparison1 研究对象本文研究对象为53 t钢锭。
基于距离场的铸钢件冒口设计方法及应用
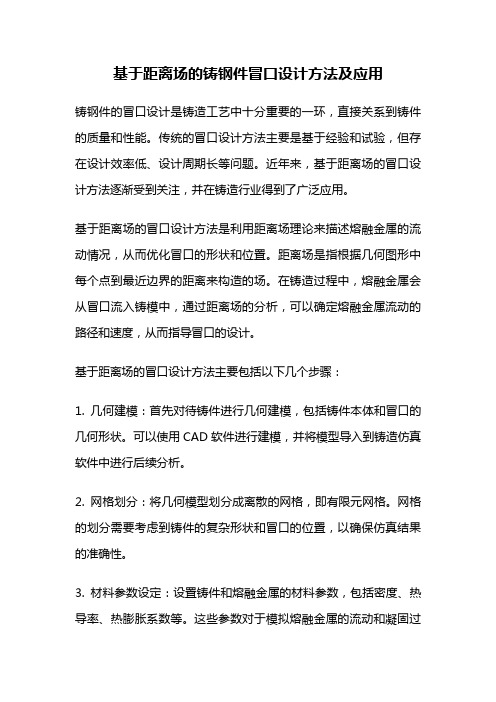
基于距离场的铸钢件冒口设计方法及应用铸钢件的冒口设计是铸造工艺中十分重要的一环,直接关系到铸件的质量和性能。
传统的冒口设计方法主要是基于经验和试验,但存在设计效率低、设计周期长等问题。
近年来,基于距离场的冒口设计方法逐渐受到关注,并在铸造行业得到了广泛应用。
基于距离场的冒口设计方法是利用距离场理论来描述熔融金属的流动情况,从而优化冒口的形状和位置。
距离场是指根据几何图形中每个点到最近边界的距离来构造的场。
在铸造过程中,熔融金属会从冒口流入铸模中,通过距离场的分析,可以确定熔融金属流动的路径和速度,从而指导冒口的设计。
基于距离场的冒口设计方法主要包括以下几个步骤:1. 几何建模:首先对待铸件进行几何建模,包括铸件本体和冒口的几何形状。
可以使用CAD软件进行建模,并将模型导入到铸造仿真软件中进行后续分析。
2. 网格划分:将几何模型划分成离散的网格,即有限元网格。
网格的划分需要考虑到铸件的复杂形状和冒口的位置,以确保仿真结果的准确性。
3. 材料参数设定:设置铸件和熔融金属的材料参数,包括密度、热导率、热膨胀系数等。
这些参数对于模拟熔融金属的流动和凝固过程至关重要。
4. 边界条件设定:设定仿真过程中的边界条件,包括冒口的入口流速、温度等。
这些条件会影响熔融金属的流动和凝固过程,需要根据实际情况进行合理设定。
5. 距离场计算:通过计算每个网格点到几何模型边界的距离,构建距离场。
距离场可以用来表示熔融金属的流动路径和速度,是优化冒口设计的关键。
6. 仿真分析:利用铸造仿真软件进行熔融金属的流动和凝固过程模拟。
通过分析仿真结果,可以评估不同冒口设计方案的可行性和效果。
7. 冒口优化:根据仿真结果,对冒口进行优化。
优化的目标是使熔融金属能够顺利流入铸模,避免产生缺陷,同时尽量减少冒口的体积和对铸件的影响。
基于距离场的冒口设计方法相比传统的经验设计方法具有以下优势:1. 设计效率高:基于距离场的冒口设计方法可以通过计算和仿真快速得到冒口的优化方案,大大缩短了设计周期。
铸造工艺学-冒口设计

顶冒口, M r (1.2 1)MC
2 检验冒口提供足够的金属液够不够
(V V ) V V
c
r
e
r
式中 ε 金属从浇注完到凝固完毕的体收缩率,η 冒口的 补缩效率。η=(补缩体积/冒口体积)。
通常用上式来校核冒口的尺寸够不够。
ε、η对冒口体积的影响
模数的计算
模数:又称为铸 件折算厚度.
M=V/A =体积/散热面积
1 简单几何体 模数的计算
29
2 相交节点的模数计算
a)测量法
测量出热节中心处的凝 固时间和平壁中心处的凝 固时间 ,用下式计算
T M
பைடு நூலகம்
j
2
式中,T--平板壁厚;
j--热节中心处凝固时间;
--平壁中心处凝固时间。
b)一倍厚度法
以相交的地方为基 准,分别向外移动一倍 的板宽的长度,得图中 阴影部分;然后用阴影 部分的模数,作为热节
38
(2)轮毂冒口计算 把轮毂看作长方形断面的杆,用类似的方法计算.该
补缩节点的热节圆直径为50mm.于是50mmˣ1.1=55mm,计算得, Mc=5.5ˣ12.7/2ˣ(5.5+12.7)=1.92cm
Mr=1.2Mc=2.30cm 查标准圆柱形冒口表,当Mr=2.38cm收缩率5%每个冒口能补缩最大 铸件体积为4.2L(质量32kg)时,冒口尺寸Φ120mmˣ180mm (h=1.5d)。可见设置一个冒口已足够。
的材料(如铸铁、石墨或铸钢等)作为冷铁。 12
2 冒口位置的选择原则
① 在热节的上方或侧旁;
② 尽量在铸件最高、最厚部位, 低处热结设补贴或冷铁;
铸件充型凝固过程数值模拟实验报告

哈尔滨工业大学《材料加工过程数值模拟基础》实验课程铸件充型凝固过程数值模拟实验报告姓名:学号:班级:材料科学与工程学院铸件充型凝固过程数值模拟实验报告实验一:铸件凝固过程数值模拟一、实验目的1.学习有限差分法温度场模拟的数学模型和基本思路;2.掌握用AnyCasting 铸造模拟软件进行温度场模拟的方法。
二、实验原理1.有限差分法温度场模拟的基本思路:设计铸造工艺方案→根据定解条件求解能量方程→揭示凝固行为细节→预测凝固缺陷→改进工艺方案,返回第二步循环。
2.有限差分法温度场模拟的数学模型:222222T T T T L C t x y z t三、铸件凝固模拟过程及参数设置1.凝固模拟过程铸件、浇冒口等三维实体造型(输出STL 文件)→网格剖分、纯凝固过程参数设置等前处理→凝固温度场和收缩缺陷计算模拟数据→后处理得到动态的液相凝固、铸件色温图和缩孔缺陷等文件。
2.参数设置铸件材质:AC1B铸型材质:SM20C初始条件:上下模500℃,侧模400℃,升液管700℃。
边界条件:所有界面与空气间的界面传热系数都为10W/(m 2∙K),熔融金属液与模具之间的界面传热系数为4000 W/(m 2∙K),各部分模具间和模具与升液管间界面传热系数都为5000 W/(m 2∙K)。
四、模拟结果图1 冷却时间由于模拟中设置了水冷和空冷条件,所以铸件冷却速度较快。
由图1可知凝固首先发生在铸件表面,铸件的轮辋区厚度较薄,冷却速度比轮辐处冷却快。
内浇口先于轮辐凝固,在内浇口凝固后升液管内铝合金熔液无法对轮毂进行补缩,则在轮毂中最后凝固处容易产生缩松缩孔。
图2 冷却率由冷却率分布情况可知凝固过程中各部分冷却速率不同,可以判断出凝固时内应力较大的区域,在应力较大区域铸件容易产生裂纹缺陷。
由模拟结果中铸件的温度场情况,合理设置工艺参数减少缩松缩孔及裂纹的产生,合理布置冷却水管的分布位置。
实验二:铸件充型过程数值模拟一、实验目的1.学习有限差分法流动场模拟的数学模型和基本思路;2.掌握用AnyCasting 铸造模拟软件进行流动场模拟的方法。
铸钢件冒口的设计示范

铸钢件冒口的设计规范钢水从液态冷却到常温的过程中,体积发生收缩。
在液态和凝固状态下,钢水的体积收缩可导致铸件产生缩孔、缩松。
冒口的作用就是补缩铸件,消除缩孔、缩松缺陷。
另外,冒口还具有出气和集渣的作用。
1、冒口设计的原则和位置1.1冒口设计的原则1.1.1、冒口的凝固时间要大于或等于铸件(或铸件被补缩部分)的凝固时间。
1.1.2、冒口所提供的补缩液量应大于铸件(或铸件被补缩部分)的液态收缩、凝固收缩和型腔扩大量之和。
1.1.3、冒口和铸件需要补缩部分在整个补缩的过程中应存在通道。
1.1.4、冒口体内要有足够的补缩压力,使补缩金属液能够定向流动到补缩对象区域,以克服流动阻力,保证铸件在凝固的过程中一直处于正压状态,既补缩过程终止时,冒口中还有一定的残余金属液高度。
1.1.5、在放置冒口时,尽量不要增大铸件的接触热节。
1.2、冒口位置的设置1.2.1、冒口一般应设置在铸件的最厚、最高部位。
1.2.2、冒口不可设置在阻碍收缩以及铸造应力集中的地方。
1.2.3、要尽量把冒口设置在铸件的加工面或容易清除的部位。
1.2.4、对于厚大件一般采用大冒口集中补缩,对于薄壁件一般采用小冒口分散补缩。
1.2.5、应根据铸件的技术要求、结构和使用情况,合理的设置冒口。
1.2.6、对于清理冒口困难的钢种,如高锰钢、耐热钢铸件的冒口,要少放或不放,非放不可的,也尽量采用易割冒口或缩脖型冒口。
2、设置冒口的步骤与方法冒口的大小、位置及数量对于铸钢件的质量至关重要。
对于大型铸钢件来说,必须把握技术标准及使用情况,充分了解设计意图,分清主次部位,集中解决关键部位的补缩。
以模数法为例,冒口设计的步骤如下:2.1、对于大、中型铸钢件,分型面确定之后,首先要根据铸件的结构划分补缩范围,并计算铸件的模数(或铸件被补缩部分的模数)M铸。
2.2、根据铸件(或铸件被补缩部分)的模数M铸,确定冒口模数M冒。
2.3、计算铸件的体收缩ε。
2.4、确定冒口的具体形状和尺寸。
铸钢件熔模精密铸造凝固过程数值模拟
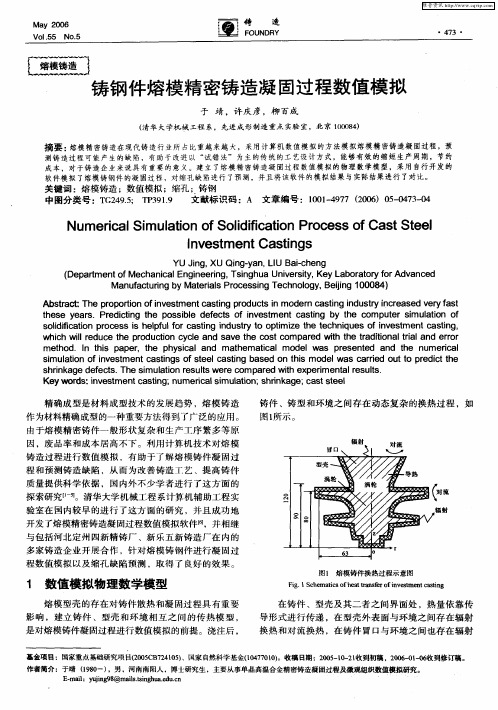
精确 成 型是材 料成 型技术 的发 展趋 势 ,熔模 铸 造 作 为材料精确成 型的一种重要 方法得 到 了广泛 的应用 。 由于熔模 精 密铸件 一般 形状 复杂 和生 产工序 繁 多等原
s r k g ee t . e sm ua in r s l r o p r dwi x e i nale ut . h i a e d f cs Th i lt e ut we e c m a e t e p r n o s h me t s l r s Ke r s iv sm e tc sig n m e ia i ua in s r k g ; a tse I ywo d :n e t n a t ; u n r I m lt ; h i a e c s t e c s o n
维普资讯
Ma 0 6 y20
Vo .5 NO. I5 5
铸
F O
造
R Y
・4 73 ・
r・ ・~●●
^●
^_
■ ‘
-
; 熔模铸造 {
■、 ■ '^ ~ _●、 ■ ^, ^ ■ 一 ^ v ■ ‘ _ ’ ■ ,
铸钢件熔模 精密铸造凝 固过程数值模拟
于 靖 ,许 庆彦 ,柳 百成
( 华 大 学机 械 工程 系 ,先 进 成 形 制造 重 点 实验 室 ,北 京 10 8 ) 清 00 4
摘要: 熔模精密铸造在现代铸造行业所 占比重越来越大,采用计算机数值模拟的方法模拟熔模精密铸造凝固过程,预
测铸 造 过 程 可 能 产 生 的缺 陷 , 有助 于 改进 以 “ 错 法” 为 主 的传 统 的工 艺设 计 方 式 ,能 够 有 效 的 缩 短 生 产 周 期 ,节 约 试 成本。对于铸造企业来说具有 重要 的意义。建立 了熔模精 密铸造凝 固过 程数值模 拟的物理 数学模 型,采用 自行开发 的 软 件模 拟 了熔 模 铸 钢 件 的凝 固过 程 ,对 缩 孔缺 陷进 行 了预 测 ,并 且 将该 软件 的模 拟 结 果 与实 际 结果 进 行 了对 比。
河北工业大学科技成果——铸件凝固过程模拟与工艺优化

河北工业大学科技成果——铸件凝固过程模拟与工艺优化项目简介铸件的成形过程是在铸型中完成的,因此它的可控性很差。
随着计算机技术的发展,铸件凝固过程计算机模拟仿真技术随之诞生。
本项目利用计算机对铸件的整个生产工艺流程(工艺设计、配料、熔炼、造型、浇铸、炉前分析等)全过程进行计算机辅助设计和工艺分析,对整个生产系统进行时时监控,对工艺参数进行闭环调整,及时发现生产过程中可能出现的漏洞并采取相应措施予以改进,以生产出高品质的铸件。
本项目是铸造行业的前沿技术,研究利用计算机模拟仿真技术控制铸造工艺过程,铸造出精密铸件。
市场前景在我国大多数企业的铸件产品出品率、成品率及质量都不高,铸件缺陷较多,严重的降低了企业的有效生产效率,从而阻碍了企业发展的脚步。
我们通过对现有铸件的工艺方案的分析,应用先进软件进行三维造型,设计合理的浇注工艺,对凝固过程模拟与优化,从而消除缩孔、缩松与冷隔等缺陷。
该技术适用于所有的铸造企业,能够显著提高逐渐的成品率,为企业创造更多利润,提高企业的竞争力。
规模与投资服务器与高配置计算机,资金需求不超过20万元。
生产设备利用企业现有的铸造设备,以及高配置的计算机以和相关的模拟软件。
效益分析年产10000吨,废品率降低按10%计算,可节约成本200万元。
合作方式合作开发。
铸件凝固过程数值模拟
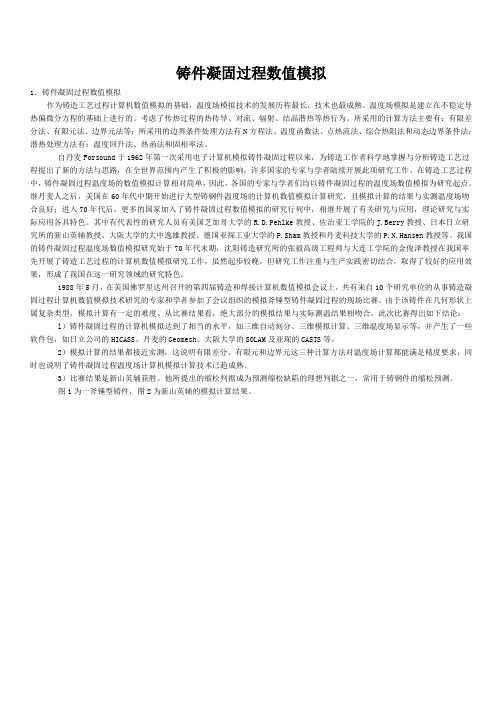
铸件凝固过程数值模拟1.铸件凝固过程数值模拟作为铸造工艺过程计算机数值模拟的基础,温度场模拟技术的发展历程最长,技术也最成熟。
温度场模拟是建立在不稳定导热偏微分方程的基础上进行的。
考虑了传热过程的热传导、对流、辐射、结晶潜热等热行为。
所采用的计算方法主要有:有限差分法、有限元法、边界元法等;所采用的边界条件处理方法有N方程法、温度函数法、点热流法、综合热阻法和动态边界条件法;潜热处理方法有:温度回升法、热函法和固相率法。
自丹麦Forsound于1962年第一次采用电子计算机模拟铸件凝固过程以来,为铸造工作者科学地掌握与分析铸造工艺过程提出了新的方法与思路,在全世界范围内产生了积极的影响,许多国家的专家与学者陆续开展此项研究工作。
在铸造工艺过程中,铸件凝固过程温度场的数值模拟计算相对简单,因此,各国的专家与学者们均以铸件凝固过程的温度场数值模拟为研究起点。
继丹麦人之后,美国在60年代中期开始进行大型铸钢件温度场的计算机数值模拟计算研究,且模拟计算的结果与实测温度场吻合良好;进入70年代后,更多的国家加入了铸件凝固过程数值模拟的研究行列中,相继开展了有关研究与应用,理论研究与实际应用各具特色。
其中有代表性的研究人员有美国芝加哥大学的R.D.Pehlke教授、佐治亚工学院的J.Berry教授、日本日立研究所的新山英辅教授、大阪大学的大中逸雄教授、德国亚探工业大学的P.Sham教授和丹麦科技大学的P.N.Hansen教授等。
我国的铸件凝固过程温度场数值模拟研究始于70年代末期,沈阳铸造研究所的张毅高级工程师与大连工学院的金俊泽教授在我国率先开展了铸造工艺过程的计算机数值模拟研究工作,虽然起步较晚,但研究工作注重与生产实践密切结合,取得了较好的应用效果,形成了我国在这一研究领域的研究特色。
1988年5月,在美国佛罗里达州召开的第四届铸造和焊接计算机数值模拟会议上,共有来自10个研究单位的从事铸造凝固过程计算机数值模拟技术研究的专家和学者参加了会议组织的模拟斧锤型铸件凝固过程的现场比赛。
铸钢件进料口的铸造工艺模拟及改进_米国发
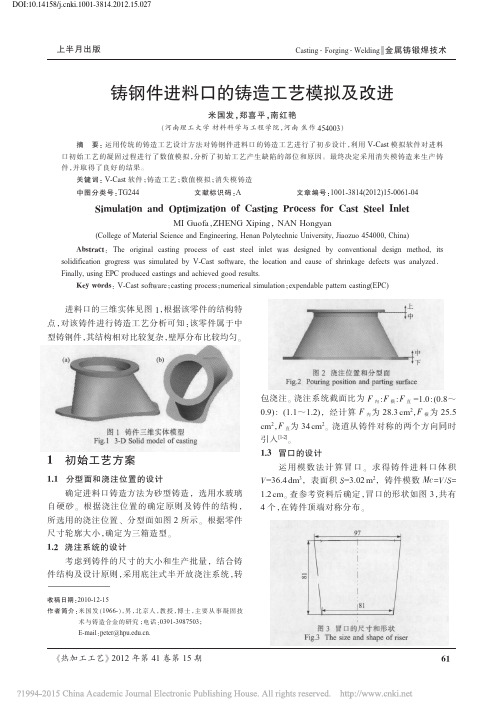
图 12 改进方案缩孔、缩松出现的位置 Fig.12 The positions of shrinkage defects
Key words: V-Cast software;casting process;numerical simulation;expendable pattern casting(EPC)
进料口的三维实体见图 1,根据该零件的结构特 点,对该铸件进行铸造工艺分析可知:该零件属于中 型铸钢件,其结构相对比较复杂,壁厚分布比较均匀。
L1
Ⅳ
570 Ⅳ 210
740 380
ⅤⅠ Ⅲ
Ⅱ
Ⅱ
ⅤⅠ Ⅲ
L1
210
Ⅴ
Ⅴ
(a) 底面
(b) 顶面
图 10 内芯的区域划分 Fig.10 The regional division of inner core
40~50 ℃下烘干,形成铸型内壳。 将带有抽气室的砂箱放在振动台上,底部放入 100
mm 厚度的底砂,其为无粘结剂、不含水的干石英砂,振 动紧实;在上面放置 EPS 模型组,并培砂固定;加入干 砂,同时施以 x、y、z 三个方向振动,振动时间 50s,砂箱表 面用塑料薄膜密封, 用真空泵将砂箱内抽成一定真空, 靠大气压力与铸型内压力之差将砂粒“粘结”在一起,维 持铸型浇注过程不崩散,称之为“负压”定型。 3.5 浇注置换
(a) t=40 s
(b) t=120 s
(c) t=200 s
(d) t=250 s
(e) t=280 s
负压实型铸造技术中的铸钢件冒口设计
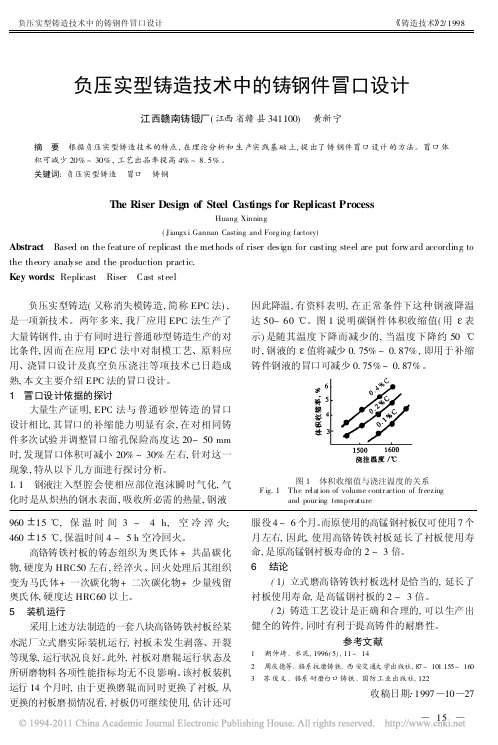
负压实型铸造( 又称消失模铸造, 简称 EPC 法) , 是一项新技术。两年多来, 我厂应用 EPC 法生产了 大量铸钢件, 由于有同时进行普通砂型铸造生产的对 比条件, 因而在应用 EP C 法中对制模工艺、原料应 用、浇冒口设计及真空负压浇注等项技术已日趋成 熟, 本文主要介绍 EPC 法的冒口设计。 1 冒口设计依据的探讨
设置补贴会更好。
2 5 根据冒口散热应最慢的原则, EP C 法冒口形状
应以球形为最好, 但综合考虑通用化标准化及手工制
模难易程度, 生产中一般选圆柱形或椭圆形冒口, 如
图 2 所示。这种形状更易于在砂型铸造方法的基础 上来设计。冒口最好放在铸件的最高位置, 以使其既
能补缩铸件又可起到集渣集气的作用。
图 2 冒口示图 F ig. 2 T he drawing of r iser
3 两个与冒口设计有关的措施 3 1 EPC 法的型腔是由泡沫模形成的, 填充砂是松 散的, 在抽真空形成负压条件下才被紧实。因而对铸 件厚大区采用内冷铁时安放不大方便, 实际操作常采 用干净圆钉插入泡沫模作为激冷内冷铁, 但对大面积 厚大部位效果甚微。另一个方法是采用外冷铁, 由于 放置简单, 放安灵活, 泡沫模型又上了涂料, 因而对外 冷铁表面锈蚀情况也不需作严格要求, 只要与铸件贴 合处形状相同即可, 与普通砂型铸造方法不同的是泡
铸铁件收缩模数法冒口设计
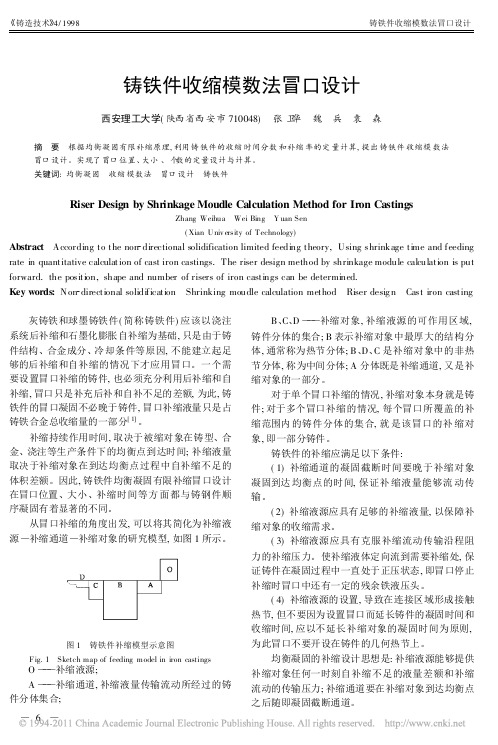
合金的收缩时间、收缩率不同, 铸铁合金的收缩时间、 收缩率是在一定的工艺条件下, 用规定的试样( 一种
特定的铸件) 测定的收缩、补缩特性参数。铸铁件的
补缩持续作用时间与补缩液量与浇注条件、浇冒口设
置位置、铸型冷却特性、铸型硬度等工艺条件及铸件
本身的结构有关, 具有动态特性。
这种动态特性, 按照补缩液源 补缩通道 补
灰铸铁件: P c =
1 e( 0. 5Mc+ 0. 01 qm )
( 4)
Fc =
0. 06
e( 0. 2M + 0. 01q )
c
m
( 5)
球 铁 件: Pc =
1
e( 0. 65M + 0. 01q )
c
m
( 6)
Fc =
0. 08
e( 0. 5M + 0. 01q )
c
m
( 7)
2 收缩模数法补缩设计原理
均衡凝固的补缩设计思想是: 补缩液源能够提供 补缩对象任何一时刻自补缩不足的液量差额和补缩
流动的传输压力; 补缩通道要在补缩对象到达均衡点 之后随即凝固截断通道。
铸造技术 4/ 1998
铸铁件收缩模数法冒口设计
1 铸铁件收缩时间和补缩率动态特性的数学描述
铸铁件的补缩持续作用时间与补缩液量, 与铸铁
f3
Ms
式中 M r Ar Vf Vp
= f 1 f 2 f 3 Mc
( 9)
冒口模数, cm ;
冒口散热表面积, cm2;
补缩液量, cm3;
形成补缩压力的安全液量, cm3;
f 1 补缩液量平衡系数;
f 3 补缩压力系数。
2 4 冒口颈大小的确定 冒口颈作为连接补缩液源 铸件的过渡通道,
大型铸钢件铸造工艺技术
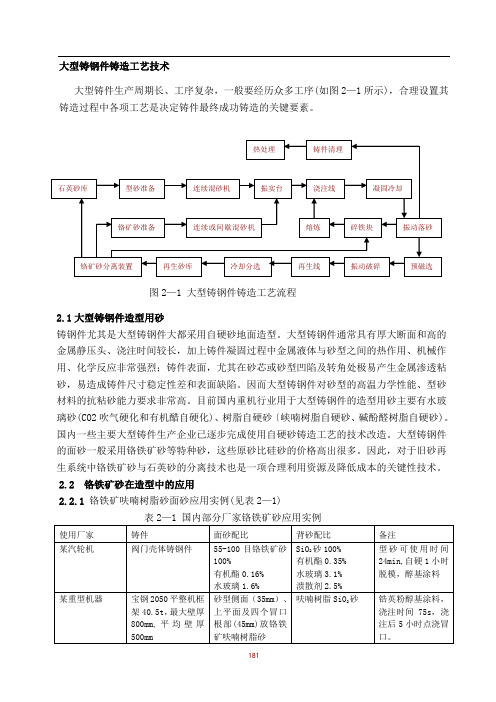
大型铸钢件铸造工艺技术2.1大型铸钢件造型用砂铸钢件尤其是大型铸钢件大都采用自硬砂地面造型。
大型铸钢件通常具有厚大断面和高的金属静压头、浇注时间较长,加上铸件凝固过程中金属液体与砂型之间的热作用、机械作用、化学反应非常强烈;铸件表面,尤其在砂芯或砂型凹陷及转角处极易产生金属渗透粘砂,易造成铸件尺寸稳定性差和表面缺陷。
因而大型铸钢件对砂型的高温力学性能、型砂材料的抗粘砂能力要求非常高。
目前国内重机行业用于大型铸钢件的造型用砂主要有水玻璃砂(CO2吹气硬化和有机醋自硬化)、树脂自硬砂〔峡喃树脂自硬砂、碱酚醛树脂自硬砂)。
国内一些主要大型铸件生产企业已逐步完成使用自硬砂铸造工艺的技术改造。
大型铸钢件的面砂一般采用铬铁矿砂等特种砂,这些原砂比硅砂的价格高出很多。
因此,对于旧砂再生系统中铬铁矿砂与石英砂的分离技术也是一项合理利用资源及降低成本的关键性技术。
2.2 铬铁矿砂在造型中的应用2.2.1铬铁矿呋喃树脂砂面砂应用实例(见表2—1)2.2.2 铬铁矿砂成份及选择铬铁矿砂属于铬尖晶石。
一般以(FeMg )O ·(CrAlFe )2O 3形式存在,其中杂质主要为CaO 、MnO 、SiO 2、TiO 2等金属氧化物和碳酸盐化合物。
铬铁矿砂的比重为(4.4~4.5)kg/cm 3,堆积比重为(2.0~2.7)kg/cm 3,耐火度为2000±25℃,熔融触点2040℃。
铬铁矿砂的选择主要依据需要配制的型(芯)砂后的工艺参数、铸件质量以及旧砂再生回收率的高低来不断摸索确定。
铬铁矿砂的化学成分及质量分数(%)见表2—1。
2.2.2.1 酸耗值我们在采用呋喃树脂砂工艺时其催(固)化剂为磺酸、苯磺酸之类酸性固化剂硬化,要求原砂呈中性,如存在诸如滑石粉的碱性化合物,固化剂的消耗必然要加大,从而砂型固化慢甚至不能硬化。
固对铬铁矿砂的酸耗值要低,因为酸耗值高的(碱性)铬铁矿砂,即使增加再多树脂及固化剂,也不易硬化,即使硬化砂型的最终强度也会很低。
- 1、下载文档前请自行甄别文档内容的完整性,平台不提供额外的编辑、内容补充、找答案等附加服务。
- 2、"仅部分预览"的文档,不可在线预览部分如存在完整性等问题,可反馈申请退款(可完整预览的文档不适用该条件!)。
- 3、如文档侵犯您的权益,请联系客服反馈,我们会尽快为您处理(人工客服工作时间:9:00-18:30)。
固过程进行模拟 , 以检验 冒口设计 的合理性 , 同时对设计 的 冒口进行 优化设 计。首先 对铸件本 体进 行凝 固过程模 拟 , 确定铸件 本体 热节 的数量和位置 , 进 而确定 冒口尺寸 、 数量和位置, 然后 对铸 件初 始工艺方案进行凝 固过程模拟 分析 , 并通过模 拟结果对 铸件 工艺方案进行优化 改进 , 对优化后 的工 艺方案进行凝 固过 程模 拟。模 拟结果表 明优化 后的工 艺方案合理 , 冒 口能够充分 补 缩铸 件, 铸件表 面和 内部 无缺 陷, 组 织致 密。 关键词 : 铸造 ; 冒口设计 ; 凝 固过程 ; 计 算机模 拟 中图分 类号 : T G2 4 4 . 4 文献标志码 : A
( 1 .燕山大学先进锻 压成型技 术与科 学教 育重 点实验 室 , 河北秦皇 岛 0 6 6 0 0 4 ;
2 .燕山大学河北省并联机器人与机 电系统 实验 室 , 河 北秦皇 岛 0 6 6 0 0 4 ; 3 .三一重机 有限公 司, 江苏昆山 2 1 5 3 3 4 )
摘 要: 以挤压机 前梁铸造为例 , 根据 挤压 机前梁 的尺寸和形 状 , 设计 出合 理 的 冒口, 并利用 P r o C AS T 软件对 挤压机 前梁 的凝
第 8卷
第 8 期
中 国 科 技 论 文
CHI NA S CI ENC EPAPER
V0 L 8 No . 8
Au g .2 0 1 3
2 0 1 3 年 8 月
大 型 铸 钢 件 冒 口设 计 及 其 凝 固过 程 模 拟
史艳 国 , 刘振 华 , 张庆玲 , 李 敏。
S h i Ya n g u o ,Li u Z h e n h u a ”,Z h a n g Qi n g l i n a n U n i v e r s i t y Ad v a n c e d Fo r g i n g T e c h n o l o g y a n d S c i e n c e Ke y L a b o r a t o r y o f t h e Mi n i s t r y o f E d u c a t i o n
文章编 号 : 2 0 9 5— 2 7 8 3 ( 2 0 1 3 ) o 8 —0 7 8 7 —0 5
De s i g n o f l a r g e s t e e l c a s t i n g r i s e r a nd s i mu l a t i o n o f i t s s o l i d i f i c a t i o n p r o c e s s
Ab s t r a c t :Ta k i n g t h e f o r me r b e a m o f a me t a l e x t r u s i o n ma c h i n e a s a n e x a mp l e ,t h e r e a s o n a b l e r i s e r s we r e d e s i g n e d a c c o r d i n g t O
Me c h a n i c a l a n d El e c t r o n i c En gi n e e r i n g,Qi n h u a n g d a o ,He b e i 0 6 6 0 0 4,Ch i n a;2 .He b e i Pr o v i n c e Ya n s h a n Un i v e r s i t y Pa r a l l e l Ro b o t a n d El e c t r o me c h a n i c a l S ys t e m ab L o r a t o r y,Qi n h u a n g d a o ,He b e i 0 6 6 0 0 4,Ch i n a; 3 .S a n y He a v y Ma c h i n e C o .,Lt d,Ku n s h a n ,J i a n gs u 2 1 5 3 3 4 ,C hi n a)
t h e b e a m s i z e a n d s h a p e ,t h e s o l i d i f i c a t i o n p r o c e s s o f t h e b e a m wa s s i mu l a t e d t o t e s t t h e r a t i o n a l i t y o f t h e r i s e r s u s i n g P r o CAS T s o f t wa r e ,a n d t h e n t h e r i s e r d e s i g n wa s o p t i mi z e d .Af t e r d e t e r mi n i n g t h e d i me n s i o n a n d n u mb e r o f r i s e r s b a s e d o n t h e s o l i d i f i c a —
t i o n r e s u l t s a n d t h e n u mb e r o f h o t s p o t s ,t h e o p t i ma l s a n d mo l d r i s e r wa s o b t a i n e d .Fu r t h e r mo r e ,t h e o r i g i n a l s a n d mo l d p r o g r a m c a n b e o p t i mi z e d t O r e d u c e r i s e r s i z e . Th e c a l c u l a t i o n r e s u l t s s h o w t h a t r i s e r d e s i g n i s r e a s o n a b l e i n i mp r o v i n g t h e f e e d i n g c a s t i n g a n d c a s t i n g s u r f a c e ,a n d o b t a i n i n g l e s s — d e f e c t a n d c o mp a c t i n t e r n a l s t r u c t u r e .