改良西门子法生产多晶硅工艺流程
四氯化硅西门子法多晶硅生产工艺

四氯化硅西门子法生产工艺四氯化硅西门子法生产工艺主要是以四氯化硅为原料,使用氢、锌等作为还原剂与四氯化硅发生反应,还原出高纯硅。
SiCl4的分子量为169.90,常温下为无色透明液体,有窒息气味,对皮肤有腐蚀,密度为1.50g/cm3。
熔点−70℃。
沸点57.6℃。
潮湿受气中水解生成硅酸和氯化氢,同时产生白烟。
溶于四氯化碳、四氯化钛、四氯化锡等有机溶剂。
能与水发生激烈的水解作用,也能与醇类起作用。
干燥空气中加热生成氧氯化硅。
与氢及其他还原剂作用生成三氯甲硅烷和其他氯代硅烷,与胺、氨迅速反应生成氮化硅聚合物,与醇反应生成硅酸酯类,与有机金属化合物(如锌、汞、钠)反应生成有机硅烷等。
由于STC原料获取较为便利,在多晶硅发展初期,部分机构和企业研究以SiCl4为原料生产多晶硅,使用Zn、Al、Ca、Mg或H2等还原四氯化硅,制取高纯多晶硅。
(1)锌还原四氯化硅使用锌还原四氯化硅的主要化学反应方式如下,其工艺流程如图所示。
Si+2Cl2=SiCl4SiCl4+2Zn=Si+2ZnCl2ZnCl2=Zn+Cl2此种生产技术是利用Zn还原SiCl4,从而获得高纯多晶硅,生产过程主要分为3步。
1)工业粗硅氯化制备四氯化硅目前,SiCl4的工业制备方法,一般是采用直接氯化法,将工业粗硅在加热条件下直接与氯反应制得SiCl4。
工业上常用不锈钢(或石英)制的氯化炉,将硅铁装入氯化炉,从氯化炉底部通入氯气,加热至200℃~300℃时,就开始反应生成SiCl4,其化学反应为Si+2Cl2=SiCl4生成的SiCl4以气体状态从炉体上部转至冷凝器,冷却为液态后,再流入储料槽。
在生产中,一般将氯化温度控制在450℃~500℃,这样一方面可提高生产率,另一方面可保证质量。
因为温度低时不仅反应速度慢,而且有副产品Si2Cl6、Si3Cl8等生成,影响产品纯度,但若温度过高,硅铁中其他难挥发杂质氯化物也会随SiCl4一起挥发出来,影响SiCl4纯度。
改良西门子法多晶硅生产技术详解

近年来,多晶硅产业之所以迅猛发展,主要受益于改良西门子法技术的进步,具体技术主要体现在化学气相沉积反应器的不断创新,能适应不断扩大生产的需要;冷氢化工艺的发展,使生产过程物料循环回收利用系统进一步完善;系统得到进一步优化,生产体系物料的技术集成不断提高,使工厂能实现更大的生产规模,建设投资和生产成本不断降低。
瓦克公司在一篇50年发展多晶硅生产的纪念性文章中,总结出企业发展的两点关键经验:首先是得益于50多年CVD反应器技术不断进步和创新;其次是生产体系物料的技术集成、综合利用的逐步完善。
1)CVD技术CVD反应炉的生产技术不断创新,生产能力不断扩大,是西门子法生产多晶硅技术得以发展的最重要因素。
钟罩式棒状载体CVD反应器因发源于德国西门子公司而闻名,用于三氯氢硅还原反应的被称为三氯氢硅西门子技术,用于硅烷分解的被称为硅烷西门子技术。
早期德国西门子公司与Wacker公司合作,为西门子公司生产硅整流器研发多晶硅原料,使用硅粉和HCl合成三氯氢硅,提纯后再以氢还原三氯氢硅生成多晶硅,使用石英玻璃CVD反应器。
后期随着材料技术的进步和降本降耗的需要,逐渐发展到金属钟罩炉、不锈钢钟罩炉,还原炉里面的棒数也逐渐从1对棒、3对棒逐渐提升到36对棒以上的大型还原炉。
图为不同年代的主流还原炉年产量情况,从图中可以看出,还原炉产量已从1975年的单炉40吨/年,提升至2015年的500吨/年,48对棒的还原炉年产能更是达到600吨的水平。
多对棒常压还原炉的使用。
进入20世纪70年代,部分企业开始想方设法地提高单炉产量,基于压力安全等方面的考虑,日本多晶硅公司研发了大型常压还原炉,以降低电耗生产能耗。
运行实践证明,多对棒还原炉与少对棒还原炉相比具有明显的节能效果,且相同生产规模的厂房面积减少,与之配套的辅助工艺设备、电气设备、工艺管线和阀门均相应减少,采用多对棒还原炉可以降低建设投资,也可以减少操作人员数量。
其中以三菱公司为代表采用96根硅棒以上的大型常压还原炉为例,炉产量达到5吨/炉,使还原电耗水平由150~200kW·h/kg-Si降到约80kW·h/kg-Si,技术进步较明显。
多晶硅制备方法

多晶硅制备方法嘿,朋友们!今天咱就来聊聊多晶硅制备方法这个有意思的事儿。
你知道吗,多晶硅就像是科技世界里的一块神奇积木,有了它,好多厉害的东西才能被搭建出来呢!那它是怎么来的呢?有一种常见的方法叫改良西门子法。
这就好比是一场精细的烹饪,各种原材料在特定的条件下发生奇妙的反应。
先把氯硅烷这种“食材”准备好,然后通过一系列复杂而又精确的步骤,让硅慢慢沉淀、生长,就像面团发酵一样,最后就得到了我们想要的多晶硅啦。
这过程可不简单,需要高度的控制和技巧,就像大厨做菜要掌握好火候和调味一样,稍有不慎,可能就得不到完美的“菜品”啦。
还有流化床法呢!想象一下,就像是一群小精灵在一个神奇的容器里欢快地跳动,它们相互碰撞、结合,逐渐形成了多晶硅。
这个方法就比较特别啦,它有着自己独特的魅力和挑战。
咱再说说冶金法。
这就像是从一堆矿石中淘出金子一样,通过各种手段把杂质去掉,留下纯净的硅。
是不是很神奇呢?就好像在一堆乱石中找到了闪闪发光的宝石。
每种制备方法都有它的优点和局限性呢。
就像人无完人一样,没有一种方法是绝对完美的呀。
我们得根据不同的需求和情况来选择合适的方法,这可真是个技术活呢!比如说改良西门子法,虽然它能生产出高质量的多晶硅,但是成本可不低呀,这就像是买一件高品质的衣服,价格可能会让你有点小纠结。
流化床法呢,可能在某些方面表现出色,但也有它自己需要克服的难题。
冶金法呢,相对来说可能成本低一些,但要达到特别高的纯度可能就有点难度啦。
那我们为什么要这么费劲地去研究多晶硅制备方法呢?这还用问吗?多晶硅可是在好多领域都有着重要的作用呀!太阳能电池板,没有多晶硅怎么行?电子设备,也离不开它呀!所以说,掌握了好的制备方法,就等于掌握了开启未来科技大门的钥匙呢!总之呢,多晶硅制备方法是一个充满挑战和机遇的领域。
我们要不断探索、创新,找到更好更高效的方法,让多晶硅为我们的生活带来更多的便利和惊喜。
难道不是吗?让我们一起期待未来多晶硅制备技术的更大突破吧!。
改良西门子法生产多晶硅工艺流程

改良西门子法生产多晶硅工艺流程1. 氢气制备与净化工序在电解槽内经电解脱盐水制得氢气。
电解制得的氢气经过冷却、分离液体后,进入除氧器,在催化剂的作用下,氢气中的微量氧气与氢气反应生成水而被除去。
除氧后的氢气通过一组吸附干燥器而被干燥。
净化干燥后的氢气送入氢气贮罐,然后送往氯化氢合成、三氯氢硅氢还原、四氯化硅氢化工序。
电解制得的氧气经冷却、分离液体后,送入氧气贮罐。
出氧气贮罐的氧气送去装瓶。
气液分离器排放废吸附剂,氢气脱氧器有废脱氧催化剂排放,干燥器有废吸附剂排放,均由供货商回收再利用。
2. 氯化氢合成工序从氢气制备与净化工序来的氢气和从合成气干法分离工序返回的循环氢气分别进入本工序氢气缓冲罐并在罐内混合。
出氢气缓冲罐的氢气引入氯化氢合成炉底部的燃烧枪。
从液氯汽化工序来的氯气经氯气缓冲罐,也引入氯化氢合成炉的底部的燃烧枪。
氢气与氯气的混合气体在燃烧枪出口被点燃,经燃烧反应生成氯化氢气体。
出合成炉的氯化氢气体流经空气冷却器、水冷却器、深冷却器、雾沫分离器后,被送往三氯氢硅合成工序。
为保证安全,本装置设置有一套主要由两台氯化氢降膜吸收器和两套盐酸循环槽、盐酸循环泵组成的氯化氢气体吸收系统,可用水吸收因装置负荷调整或紧急泄放而排出的氯化氢气体。
该系统保持连续运转,可随时接收并吸收装置排出的氯化氢气体。
为保证安全,本工序设置一套主要由废气处理塔、碱液循环槽、碱液循环泵和碱液循环冷却器组成的含氯废气处理系统。
必要时,氯气缓冲罐及管道内的氯气可以送入废气处理塔内,用氢氧化钠水溶液洗涤除去。
该废气处理系统保持连续运转,以保证可以随时接收并处理含氯气体。
3. 三氯氢硅合成工序原料硅粉经吊运,通过硅粉下料斗而被卸入硅粉接收料斗。
硅粉从接收料斗放入下方的中间料斗,经用热氯化氢气置换料斗内的气体并升压至与下方料斗压力平衡后,硅粉被放入下方的硅粉供应料斗。
供应料斗内的硅粉用安装于料斗底部的星型供料机送入三氯氢硅合成炉进料管。
多晶硅的三大生产工艺之比较
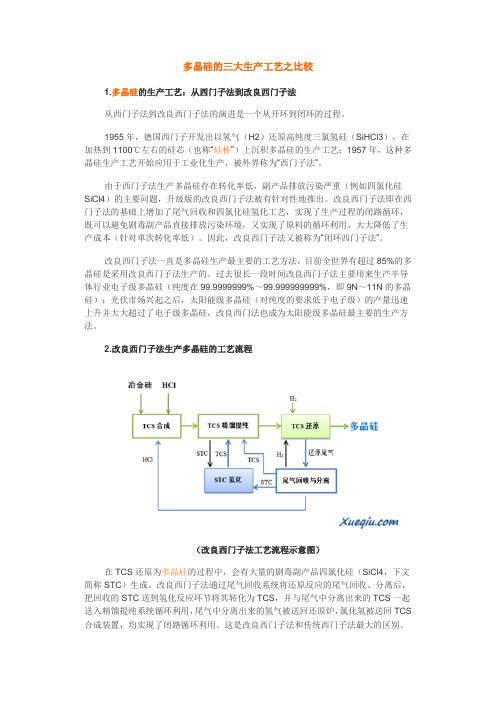
多晶硅的三大生产工艺之比较1.多晶硅的生产工艺:从西门子法到改良西门子法从西门子法到改良西门子法的演进是一个从开环到闭环的过程。
1955年,德国西门子开发出以氢气(H2)还原高纯度三氯氢硅(SiHCl3),在加热到1100℃左右的硅芯(也称“硅棒”)上沉积多晶硅的生产工艺;1957年,这种多晶硅生产工艺开始应用于工业化生产,被外界称为“西门子法”。
由于西门子法生产多晶硅存在转化率低,副产品排放污染严重(例如四氯化硅SiCl4)的主要问题,升级版的改良西门子法被有针对性地推出。
改良西门子法即在西门子法的基础上增加了尾气回收和四氯化硅氢化工艺,实现了生产过程的闭路循环,既可以避免剧毒副产品直接排放污染环境,又实现了原料的循环利用、大大降低了生产成本(针对单次转化率低)。
因此,改良西门子法又被称为“闭环西门子法”。
改良西门子法一直是多晶硅生产最主要的工艺方法,目前全世界有超过85%的多晶硅是采用改良西门子法生产的。
过去很长一段时间改良西门子法主要用来生产半导体行业电子级多晶硅(纯度在99.9999999%~99.999999999%,即9N~11N的多晶硅);光伏市场兴起之后,太阳能级多晶硅(对纯度的要求低于电子级)的产量迅速上升并大大超过了电子级多晶硅,改良西门法也成为太阳能级多晶硅最主要的生产方法。
2.改良西门子法生产多晶硅的工艺流程(改良西门子法工艺流程示意图)在TCS还原为多晶硅的过程中,会有大量的剧毒副产品四氯化硅(SiCl4,下文简称STC)生成。
改良西门子法通过尾气回收系统将还原反应的尾气回收、分离后,把回收的STC送到氢化反应环节将其转化为TCS,并与尾气中分离出来的TCS一起送入精馏提纯系统循环利用,尾气中分离出来的氢气被送回还原炉,氯化氢被送回TCS 合成装置,均实现了闭路循环利用。
这是改良西门子法和传统西门子法最大的区别。
CVD还原反应(将高纯度TCS还原为高纯度多晶硅)是改良西门子法多晶硅生产工艺中能耗最高和最关键的一个环节,CVD工艺的改良是多晶硅生产成本下降的一项重要驱动力。
太阳能级多晶硅生产工艺介绍

流化床法是美国 Boeing 公司研发的多晶硅生产工艺,该方法主要采用硅籽作为 沉积体,再将其与卤硅烷进行反应,进而制造多晶硅。流化床法制造多晶硅需要 用到流化床反应器,具体反应过程如下:将 SiHCl3 和 H2 由底部注入到反应装 置中,在经过加热区和反应区后,可以和装置顶部的硅晶体进行反应,反应条件 需要处在高温环境,同时在气相沉积的作用下,硅晶体将会不断增多,最终可以 形成多晶硅产物。该方法与西门子法相比主要具有以下优势:第一,可以进行连
加的节能,能耗大约在 40kW·h/kg 左右。然而,该方法存在着一定的安全问题, 这是由硅烷的特性决定的,硅烷是一种易燃、易爆的气体,这极大地增加了硅烷 的保存难度,在日常生产过程中不易于管理。产品和晶种相对容易受到污染,存 在超细硅粉问题,工艺和设备成熟度较低。
3. 冶金法
冶金法制备多晶硅主要分为两个步骤:第一,需要采用真空蒸馏、定向凝固等方 式对工业硅进行提纯,去除工业硅中的杂质,使其纯度达到要求。第二,通过等 离子炉清除 C、B 等元素,得到更加纯净的硅元素。通过这种方式制备的多晶硅 具有 P-极性,并且电阻系数较小,因而具有较高的光电转化效果。日本 Kawasaki Steel 企业采用的就是这种制造方式,可以有效地对工业硅进行提纯。此外,上 述方法还可以进行优化,优化过程主要用到了湿法精炼极性处理。通过这种方式 可以对多晶硅进一步进行精炼,与未使用该方法相比,可以将太阳能电池的工作 效率提升到 15%左右。由此可见,多晶硅的纯度非常的重要,通过提高多晶硅 的纯度可以极大地改变多晶硅的物理特性,能够在很大程度上提高太阳能电池的 工作效率。
6. 电解法
电解法采用电解硅酸盐的方式得到纯度较高的硅,在电解装置中,以 C 作为阳 极,反应温度控制在 1000℃,在经过一段时间的电解反应后,Si 单质将会在阴 极上附着,阳极生成 CO2 气体。电解反应对电极材料的要求较高,这是因为在 电解反应中,尤其是温度较高的反应条件下,电极极易发生腐蚀,进而将新的杂 质引入反应体系中,如 B、P 等,对硅的纯度造成影响。以 CaCl2 作为熔盐电解 为例,使用石墨作为阳极,阴极采用特制材料。电解完成后,需要将阴极置于真
多晶硅生产工艺流程
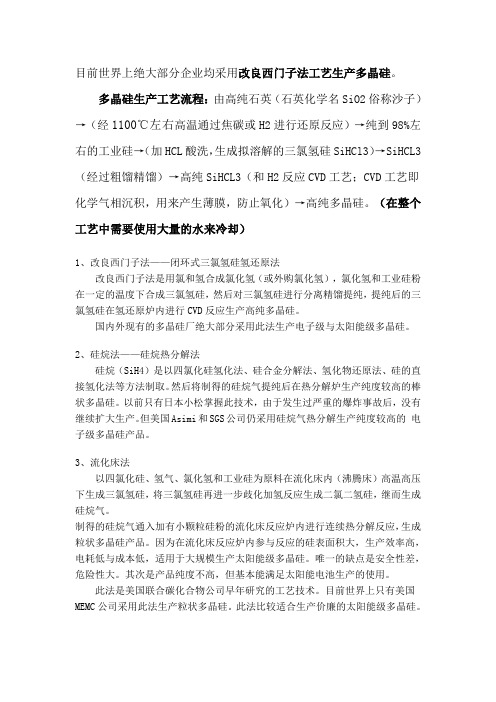
目前世界上绝大部分企业均采用改良西门子法工艺生产多晶硅。
多晶硅生产工艺流程:由高纯石英(石英化学名SiO2俗称沙子)→(经1100℃左右高温通过焦碳或H2进行还原反应)→纯到98%左右的工业硅→(加HCL酸洗,生成拟溶解的三氯氢硅SiHCl3)→SiHCL3(经过粗馏精馏)→高纯SiHCL3(和H2反应CVD工艺;CVD工艺即化学气相沉积,用来产生薄膜,防止氧化)→高纯多晶硅。
(在整个工艺中需要使用大量的水来冷却)1、改良西门子法——闭环式三氯氢硅氢还原法改良西门子法是用氯和氢合成氯化氢(或外购氯化氢),氯化氢和工业硅粉在一定的温度下合成三氯氢硅,然后对三氯氢硅进行分离精馏提纯,提纯后的三氯氢硅在氢还原炉内进行CVD反应生产高纯多晶硅。
国内外现有的多晶硅厂绝大部分采用此法生产电子级与太阳能级多晶硅。
2、硅烷法——硅烷热分解法硅烷(SiH4)是以四氯化硅氢化法、硅合金分解法、氢化物还原法、硅的直接氢化法等方法制取。
然后将制得的硅烷气提纯后在热分解炉生产纯度较高的棒状多晶硅。
以前只有日本小松掌握此技术,由于发生过严重的爆炸事故后,没有继续扩大生产。
但美国Asimi和SGS公司仍采用硅烷气热分解生产纯度较高的电子级多晶硅产品。
3、流化床法以四氯化硅、氢气、氯化氢和工业硅为原料在流化床内(沸腾床)高温高压下生成三氯氢硅,将三氯氢硅再进一步歧化加氢反应生成二氯二氢硅,继而生成硅烷气。
制得的硅烷气通入加有小颗粒硅粉的流化床反应炉内进行连续热分解反应,生成粒状多晶硅产品。
因为在流化床反应炉内参与反应的硅表面积大,生产效率高,电耗低与成本低,适用于大规模生产太阳能级多晶硅。
唯一的缺点是安全性差,危险性大。
其次是产品纯度不高,但基本能满足太阳能电池生产的使用。
此法是美国联合碳化合物公司早年研究的工艺技术。
目前世界上只有美国MEMC公司采用此法生产粒状多晶硅。
此法比较适合生产价廉的太阳能级多晶硅。
4、太阳能级多晶硅新工艺技术除了上述改良西门子法、硅烷热分解法、流化床反应炉法三种方法生产电子级与太阳能级多晶硅以外,还涌现出几种专门生产太阳能级多晶硅新工艺技术。
改良西门子法制备高纯多晶硅料
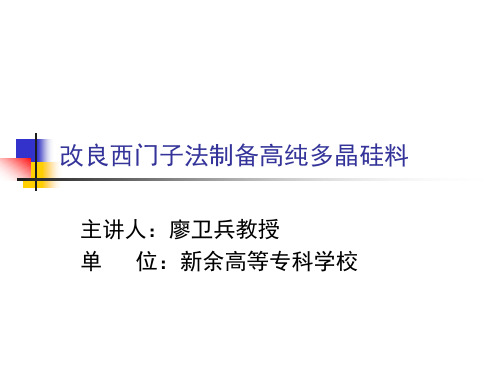
主讲人:廖卫兵教授 单 位:新余高等专科校
纲要
硅的化学提纯 高纯多晶硅硅料主要生产方法 改良西门子法 改良西门子法的关键技术
1.1 硅的化学提纯
对于太阳电池,多晶硅的纯度一般要求在6N (99.9999%)以上。到目前为止,都是利用 化学提纯技术,将冶金级硅(95%—99%)进 一步提纯,得到高纯多晶硅。
所谓硅的化学提纯是将硅用化学方法转化为中 间化合物,再将中间化合物提纯至所需的纯度, 然后再还原成高纯硅。
1.1 硅的化学提纯
硅的化学提纯主要包括三个步骤:
1
中间化合物的 形成。
2
中间化合物的 分离和提纯。
3
中间化合物被 还原或被分解 成高纯硅。
1.2 高纯多晶硅硅料主要生产方法
根据中间化合物的不同,化学提纯多晶硅可分为不同的 技术路线。目前,在工业中广泛应用的技术主要有:
三氯氢硅氢还原法 (西门子法)
硅烷热分解法
四氯化硅氢还原法
经过化学提纯得到的高
纯多晶硅的基硼浓度应 小于0.05ppba,基磷 浓度小于0.15ppba, 碳浓度小于0.1ppma, 金属杂质浓度小于 1.0ppba。
1.3 改良西门子法
三氯氢硅氢还原法于1954年由西门子公司研究成功, 因此又称为西门子法,是广泛采用的高纯多晶硅制备 技术,国际上生产高纯多晶硅的主要大公司都采用该 技术,包括瓦克、海姆洛克和德山。
对环境不产生污染(三氯氢硅和四氯化硅均有腐蚀性)。
知识回顾 Knowledge Review
祝您成功!
改良西门子法——为闭环式三氯氢硅氢还原法。在西门 子法工艺的基础上,通过增加还原尾气干法回收系统, 四氯化硅氢化工艺,实现了闭路循环。改良西门子法包 括5个主要环节:三氯氢硅合成,三氯氢硅精馏提纯, 三氯氢硅的氢还原,尾气的回收和四氯化硅的氢化分离;
多晶硅工艺流程
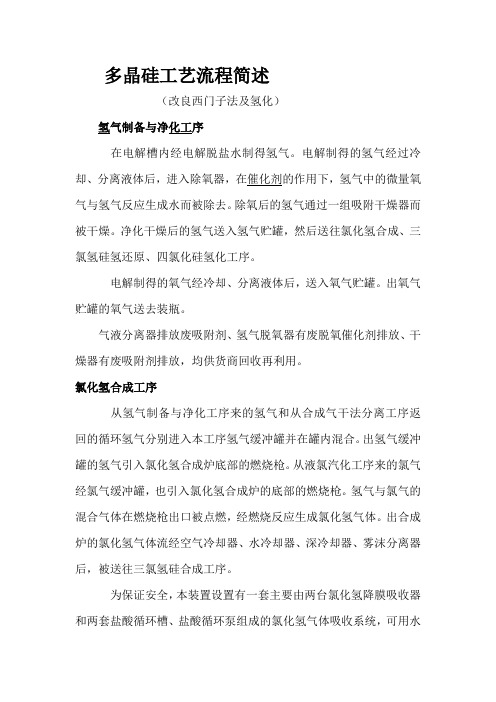
多晶硅工艺流程简述(改良西门子法及氢化)氢气制备与净化工序在电解槽内经电解脱盐水制得氢气。
电解制得的氢气经过冷却、分离液体后,进入除氧器,在催化剂的作用下,氢气中的微量氧气与氢气反应生成水而被除去。
除氧后的氢气通过一组吸附干燥器而被干燥。
净化干燥后的氢气送入氢气贮罐,然后送往氯化氢合成、三氯氢硅氢还原、四氯化硅氢化工序。
电解制得的氧气经冷却、分离液体后,送入氧气贮罐。
出氧气贮罐的氧气送去装瓶。
气液分离器排放废吸附剂、氢气脱氧器有废脱氧催化剂排放、干燥器有废吸附剂排放,均供货商回收再利用。
氯化氢合成工序从氢气制备与净化工序来的氢气和从合成气干法分离工序返回的循环氢气分别进入本工序氢气缓冲罐并在罐内混合。
出氢气缓冲罐的氢气引入氯化氢合成炉底部的燃烧枪。
从液氯汽化工序来的氯气经氯气缓冲罐,也引入氯化氢合成炉的底部的燃烧枪。
氢气与氯气的混合气体在燃烧枪出口被点燃,经燃烧反应生成氯化氢气体。
出合成炉的氯化氢气体流经空气冷却器、水冷却器、深冷却器、雾沫分离器后,被送往三氯氢硅合成工序。
为保证安全,本装置设置有一套主要由两台氯化氢降膜吸收器和两套盐酸循环槽、盐酸循环泵组成的氯化氢气体吸收系统,可用水吸收因装置负荷调整或紧急泄放而排出的氯化氢气体。
该系统保持连续运转,可随时接收并吸收装置排出的氯化氢气体。
为保证安全,本工序设置一套主要由废气处理塔、碱液循环槽、碱液循环泵和碱液循环冷却器组成的含氯废气处理系统。
必要时,氯气缓冲罐及管道内的氯气可以送入废气处理塔内,用氢氧化钠水溶液洗涤除去。
该废气处理系统保持连续运转,以保证可以随时接收并处理含氯气体。
三氯氢硅合成工序原料硅粉经吊运,通过硅粉下料斗而被卸入硅粉接收料斗。
硅粉从接收料斗放入下方的中间料斗,经用热氯化氢气置换料斗内的气体并升压至与下方料斗压力平衡后,硅粉被放入下方的硅粉供应料斗。
供应料斗内的硅粉用安装于料斗底部的星型供料机送入三氯氢硅合成炉进料管。
从氯化氢合成工序来的氯化氢气,与从循环氯化氢缓冲罐送来的循环氯化氢气混合后,引入三氯氢硅合成炉进料管,将从硅粉供应料斗供入管内的硅粉挟带并输送,从底部进入三氯氢硅合成炉。
改良西门子法制备高纯多晶硅

改进西门子法制备高纯多晶硅摘要:本文主要表达了高纯多晶硅的各种制备方法,有三氯氢硅氢复原法、硅烷热分解法、四氯化硅氢复原法、流化床法、物理提纯法等其他制备高纯多晶硅的工艺。
[1]其中重点介绍了现在普遍都使用,技术相对成熟的改进西门子法,包括改进西门子法的制备工艺、三氯氢硅的提纯与尾气处理。
关键词:高纯多晶硅;良西门子法;尾气处理The preparation of high purity poly crystalline silicon modified SiemensAbstract:This paper mainly describes various preparation methods of high purity poly crystalline silicon,hydrogen reduction method,the silicon cross-linked with hydrogen silica thermal decomposition method,silicon tetra chloride hydrogen reduction method,fluidity bed method,physical purification method preparation of high purity poly crystalline silicon and other crafts. Which focus on widely used now,the technology is relatively mature and improved Siemens method,including improved Siemens method of preparation,chemical hydrogen purification of silicon and tail gas treatment.Keywords:high purity poly crystalline silicon;a good method of Siemens;tail gas treatment.绪论近年来,太阳能硅电池、半导体工业和电子信息产业开展迅猛,而多晶硅是这些产业的最根本和主要的功能材料,因此,多晶硅的生产受到了各国企业的重视。
多晶硅的性质、用途、冶炼方法以及工艺流程图
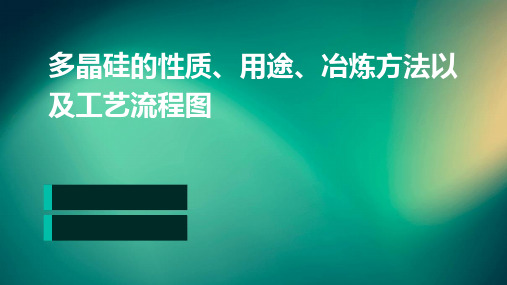
检测与包装
检测
对多晶硅产品进行质量检测,如纯度、晶体质量、表面质量等。
包装
根据客户需求对多晶硅产品进行包装,以确保其在运输和存储过程中的安全和稳定性。
THANKS FOR WATCHING
感谢您的观看
多晶硅的性质、用途、冶炼方法以 及工艺流程图
目录
• 多晶硅的性质 • 多晶硅的用途 • 多晶硅的用途 • 多晶硅的用途 • 多晶硅的冶炼方法 • 多晶硅的工艺流程图
01 多晶硅的性质
物理性质
硬度
多晶硅的硬度较高,属于硬质材料。
导热性
多晶硅的导热性能良好,热膨胀系数较小。
密度
多晶硅的密度为2.32-2.34g/cm³,比单晶 硅略低。
详细描述
化学气相沉积法利用化学反应将原料气体转化为多晶硅。该方法可以在较低温度下进行,结晶质量较好,但生产 成本较高,且对设备要求较高。
04 多晶硅的工艺流程图
原料准备
原料准备
多晶硅的生产需要高纯度 的硅材料作为原料,通常 采用冶金级硅或工业硅作 为起始原料。
硅材料的纯化
为了获得高纯度的硅材料, 需要进行一系列的提纯和 除杂过程,如破碎、酸洗、 碱洗等。
杂质去除
通过精馏过程,可以去除硅原料中 的大部分杂质,如铁、铝、钙等, 从而提高硅的纯度。
化学气相沉积
化学气相沉积原理
化学气相沉积是一种利用化学反应在硅表面形成固态薄膜的方法, 通过控制反应条件,可以在硅表面形成多晶硅层。
反应气体
化学气相沉积过程中需要使用不同的反应气体,如硅烷、氢气等, 这些气体在高温下发生化学反应,形成固态的多晶硅层。
铸锭和切片
将提纯后的多晶硅铸造成锭, 并进行切片加工成所需的规格 和形状。
改良西门子法工艺简介及各工段取样项目介绍
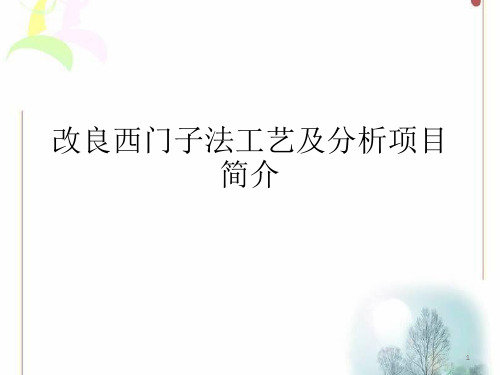
9
CDI回收氯硅烷精馏 回收氯硅烷精馏6~7#塔 # 回收氯硅烷精馏
轻组分 V03A09 CDI回收 回收 V03A16a
6# 精 馏 塔
CDI回收 回收 V03A16b
STC V03A15
7# 精 馏 塔
纯TCS储罐 储罐 V03A14
10
精馏8#~9#塔
8#、 #塔具有不同功能。 #、9#塔具有不同功能。 #、 8#是脱除系统中的轻组分,其产品 回到 #是脱除系统中的轻组分,其产品TCS回到 1#塔重新精馏。 #塔重新精馏。 9#塔是脱除系统中的重组分,其产品是 #塔是脱除系统中的重组分,其产品是STC 回到氢化工段转化成TCS, 在去往6# 回到氢化工段转化成 ,到CDI在去往 #塔。 在去往
改良西门子法工艺及分析项目 简介
1
提纲
• 1、改良西门子法工艺流程 • 2、各工段取样项目简介
2
生产流程图
Si
氢化 制
SiHCl3,SiCl4 STC
TCS精 精 馏
三 氯 废 热 蒸 汽
N2 LSI AP A H2O 气 H2
尾气
氯 H2 H2O 硅 烷
氢 硅
程
气
3
改良西门子法工艺流程
• 1、制H2工段 、 工段
12
还原炉结构图
13
14
改良西门子法工艺流程
• 5、CDI尾气回收 、 尾气回收
尾气的回收就是将尾气中有用成分, 尾气的回收就是将尾气中有用成分,主要 是H2、SiHCl3、SiCl4和HCl等,通过物理和化 、 、 和 等 学的方法使之分离, 学的方法使之分离,经过提纯后再应用于生 产中。在多晶硅生产过程中, 产中。在多晶硅生产过程中,尾气主要来自 于以下两个工序, 氢还原工序, 于以下两个工序,SiHCl3氢还原工序,SiCl4氢 氢还原工序 氢 化工序。 化工序。
改良西门子法制备高纯多晶硅料
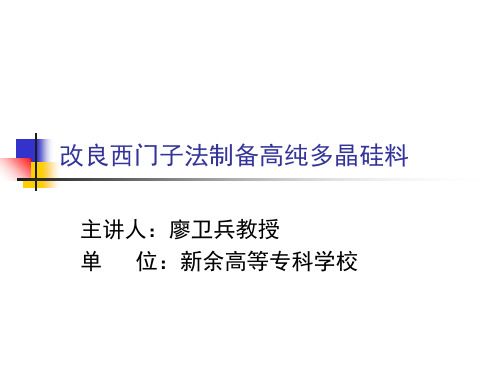
1、反应温度在300℃-400℃之间;
2、氯化氢气体(HCI)必须是干燥无水的;
3、工业硅(
S
)须经过破碎和研磨,达到适合的粒径。
i
1.3 改良西门子法
改良西门子法多晶硅制备工艺原理图
氯气
工业硅
氯化氢合成
硅粉
三氯氢硅合成
氢气 三氯氢硅提纯
氢气 多晶硅 还原
氯化氢气体 三氯氢硅 三氯氢硅
氢化
四氯化硅
硅的化学提纯主要包括三个步骤:
1
中间化合物纯。
3
中间化合物被 还原或被分解 成高纯硅。
1.2 高纯多晶硅硅料主要生产方法
根据中间化合物的不同,化学提纯多晶硅可分为不同的 技术路线。目前,在工业中广泛应用的技术主要有:
三氯氢硅氢还原法 (西门子法)
硅烷热分解法
四氯化硅氢还原法
1.1 硅的化学提纯
对于太阳电池,多晶硅的纯度一般要求在6N (99.9999%)以上。到目前为止,都是利用 化学提纯技术,将冶金级硅(95%—99%)进 一步提纯,得到高纯多晶硅。
所谓硅的化学提纯是将硅用化学方法转化为中 间化合物,再将中间化合物提纯至所需的纯度, 然后再还原成高纯硅。
1.1 硅的化学提纯
经过化学提纯得到的高
纯多晶硅的基硼浓度应 小于0.05ppba,基磷 浓度小于0.15ppba, 碳浓度小于0.1ppma, 金属杂质浓度小于 1.0ppba。
1.3 改良西门子法
三氯氢硅氢还原法于1954年由西门子公司研究成功, 因此又称为西门子法,是广泛采用的高纯多晶硅制备 技术,国际上生产高纯多晶硅的主要大公司都采用该 技术,包括瓦克、海姆洛克和德山。
主要化学反应主要包括以下2个步骤:
西门子法提纯硅的工艺流程

西门子法提纯硅的工艺流程The Siemens process is a widely used method for purifying silicon, a crucial material in the electronics industry. This process involves converting metallurgical grade silicon into pure polysilicon through a series of steps. 西门子法是一种广泛应用的方法,用于提炼硅,这是电子行业中至关重要的材料。
这个过程涉及将冶金级硅转化为纯净的多晶硅,通过一系列的步骤。
The first step in the Siemens process is the reduction of silicon tetrachloride with hydrogen gas at high temperatures. This reaction produces silicon and hydrogen chloride as byproducts. 西门子法的第一步是在高温下用氢气还原四氯化硅。
这个反应会产生硅和氢氯酸作为副产物。
After the reduction step, the produced silicon is further refined through a series of distillation processes to remove impurities. This purification process ensures that the final polysilicon product meets the high purity standards required for semiconductor manufacturing. 在还原步骤之后,通过一系列的蒸馏过程进一步提炼产生的硅,以去除杂质。
多晶硅生产工艺—西门子法
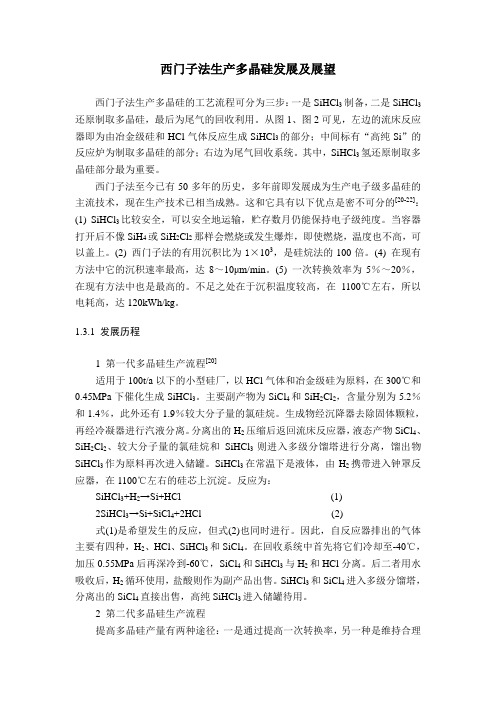
西门子法生产多晶硅发展及展望西门子法生产多晶硅的工艺流程可分为三步:一是SiHCl3制备,二是SiHCl3还原制取多晶硅,最后为尾气的回收利用。
从图1、图2可见,左边的流床反应器即为由冶金级硅和HCl气体反应生成SiHCl3的部分;中间标有“高纯Si”的反应炉为制取多晶硅的部分;右边为尾气回收系统。
其中,SiHCl3氢还原制取多晶硅部分最为重要。
西门子法至今已有50多年的历史,多年前即发展成为生产电子级多晶硅的主流技术,现在生产技术已相当成熟。
这和它具有以下优点是密不可分的[20-22]:(1) SiHCl3比较安全,可以安全地运输,贮存数月仍能保持电子级纯度。
当容器打开后不像SiH4或SiH2Cl2那样会燃烧或发生爆炸,即使燃烧,温度也不高,可以盖上。
(2) 西门子法的有用沉积比为1×103,是硅烷法的100倍。
(4) 在现有方法中它的沉积速率最高,达8~10μm/min。
(5) 一次转换效率为5%~20%,在现有方法中也是最高的。
不足之处在于沉积温度较高,在1100℃左右,所以电耗高,达120kWh/kg。
1.3.1 发展历程1 第一代多晶硅生产流程[20]适用于100t/a以下的小型硅厂,以HCl气体和冶金级硅为原料,在300℃和0.45MPa下催化生成SiHCl3。
主要副产物为SiCl4和SiH2Cl2,含量分别为5.2%和1.4%,此外还有1.9%较大分子量的氯硅烷。
生成物经沉降器去除固体颗粒,再经冷凝器进行汽液分离。
分离出的H2压缩后返回流床反应器,液态产物SiCl4、SiH2Cl2、较大分子量的氯硅烷和SiHCl3则进入多级分馏塔进行分离,馏出物SiHCl3作为原料再次进入储罐。
SiHCl3在常温下是液体,由H2携带进入钟罩反应器,在1100℃左右的硅芯上沉淀。
反应为:SiHCl3+H2→Si+HCl (1)2SiHCl3→Si+SiCl4+2HCl(2)式(1)是希望发生的反应,但式(2)也同时进行。
三氯氢硅西门子法多晶硅生产工艺详解
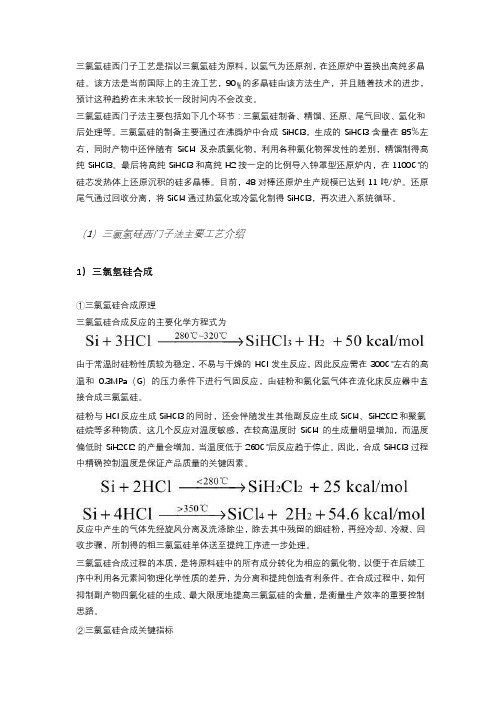
总体而言,国内制取三氯氢硅的技术已相当成熟,尤其在冷氢化技术愈加成熟的今天,很多 多晶硅厂家选择关停三氯氢硅合成工序,三氯氢硅主要由氢化工序提供,不足部分选择外购, 以此降低投资成本。
2)精馏
该项技术是多晶硅生产的关键技术,物料质量尤其是三氯氢硅的质量直接决定了多晶硅的产 品质量。精馏提纯也是工业生产中广泛采用的净化方法之一,设备简单、便于制造、处理量 大、操作方便,同时还具有避免引入其他试剂污染,分离精度可达 ppb 级等众多优点。精 馏主要技术指标如表所示。
(1)三氯氢硅西门子法主要工艺介绍
1)三氯氢硅合成
①三氯氢硅合成原理 三氯氢硅合成反应的主要化学方程式为
由于常温时硅粉性质较为稳定,不易与干燥的 HCl 发生反应,因此反应需在 300℃左右的高 温和 0.3MPa(G)的压力条件下进行气固反应,由硅粉和氯化氢气体在流化床反应器中直 接合成三氯氢硅。 硅粉与 HCl 反应生成 SiHCl3 的同时,还会伴随发生其他副反应生成 SiCl4、SiH2Cl2 和聚氯 硅烷等多种物质。这几个反应对温度敏感,在较高温度时 SiCl4 的生成量明显增加,而温度 偏低时 SiH2Cl2 的产量会增加,当温度低于 260℃后反应趋于停止。因此,合成 SiHCl3 过程 中精确控制温度是保证产品质量的关键因素。
精馏是利用液体混合物中不同组分具有不同的挥发度,液体经过多次部分汽化(加热过程) 和多次部分冷凝(冷凝过程),使混合液各组分得以分离的过程,获得定量的液体和蒸汽, 两者的浓度有较大差异(易挥发组分在汽相中的含量比液相高)。若将其蒸汽和液体分开, 蒸汽进行多次的部分冷凝,最后所得蒸汽含易挥发组分极高。液体进行多次的部分汽化,最 终所得到的液体几乎不含易挥发组分。这种采用多次部分汽化、部分冷凝的方法使高、低沸 点组分进行分离,从而得到预期要求浓度的产品。 在多晶硅生产中,通过精馏技术将三氯氢硅中存在的杂质逐步分离,最终得到高纯度的三氯 氢硅。一般根据物料来源,分成三氯氢硅提纯、高低沸物回收、还原尾气干法回收料分离等 几个部分。以国内多晶硅企业常见的九塔精馏提纯为例(九塔分别以 1#、2#、3#…9#表示)。 ①冷氢化和合成料提纯 首先,采用双塔(1#塔和 2#塔)连续精馏,1#塔除去氯硅烷中二氯二氢硅等低沸点组分, 塔釜液进入 2#塔,塔顶得到较纯的三氯氢硅,塔釜液送入 5#塔进一步回收四氯化硅。 其次,采用连续的二级精馏塔(3#塔、4#塔),对 2#塔顶三氯氢硅进行精提纯,首先进入 3#塔,塔顶去除三氯氢硅中的轻杂质,塔顶液进入 9#塔回收三氯氢硅。塔釜液进入 4#塔, 最终在 4#塔顶得到合格的三氯氢硅,该三氯氢硅的质量可以满足生产太阳能级和电子级多 晶硅的要求。4#塔塔釜得到的含高沸点杂质的釜液被送入 8#塔进一步回收三氯氢硅,避免 物料浪费。 ②还原回收料提纯 采用双塔(6#塔和 7#塔)连续精馏,6#精馏塔塔釜侧线得到纯度 99 的四氯化硅,送到 5# 塔进一步提纯四氯化硅以满足冷氢化要求。塔釜液作为高沸点杂质排放。塔顶液进入 7#精 馏塔塔顶得到合格的三氯氢硅用于还原生产多晶硅,塔釜含高沸点杂质液送入 8#塔进一步 回收三氯氢硅。 ③高沸物分离 4#塔和 7#塔釜液一同送入 8#塔,精馏后塔顶三氯氢硅进入 1#塔进行回收,塔釜高沸物送 去废液处理单元。 ④低沸物分离 1#塔和 3#塔顶得到二氯二氢硅等低沸点馏分一同送入 9#塔,精馏后塔釜三氯氢硅进入 1# 塔进行回收,塔顶气相采出的低沸物送去废液处理单元。
多晶硅制备还原工艺的分析与优化

多晶硅制备还原工艺的分析与优化多晶硅制备还原工艺的分析与优化摘要目前国内多晶企业所采用的生产方法主要是西门子法或改良西门子法,产物为高纯多晶硅,为降低原材料的消耗,提高经济效益,在不影响多晶硅纯度的情况下最大限度提高原材料的转化率。
本文重点介绍了三氯氢硅还原的工艺原理、工艺流程,并对还原反应器提出了相关的优化建议。
关键词:改良西门子法;还原;三氯氢硅;优化Polysilicon preparation reduction process analysisand optimizationAbstractCurrently used by many domestic production of crystal enterprise method is mainly to Siemens method or improved Siemens method, product purity polysilicon, to reduce the consumption of raw materials, improving economic efficiency, are not affected under the condition of polysilicon purity maximizing conversion of raw materials.This paper introduces the process of hydrogen silicone reduction trichloramine principle, process flow, and puts forward the relevant to restore the reactor technical advice.Keyword: Modified Siemens Process;deoxidation ;trichlorosilane;optimize目录摘要 (I)Abstract ........................................................................................................................ I I 第一章三氯氢硅还原工艺及其相关物质的介绍 (1)1.1多晶硅还原工艺的简介 (1)1.2三氯氢硅和氢气 (1)1.3多晶硅的基本结构及性质 (3)第二章三氯氢硅氢还原反应基本原理 (4)2.1三氯氢硅氢还原反应原理 (4)2.2 SiHCl3氢还原反应的影响因素 (4)2.2.1 反应温度 (4)2.2.2 反应气体流量 (6)2.2.3 发热体表面积 (6)第三章三氯氢硅氢还原中的主要设备 (8)3.1蒸发器 (8)3.2还原炉 (9)3.3 AEG电柜 (10)第四章三氯氢硅还原工艺的优化 (11)4.1反应器的优化设计 (11)4.1.1钟罩式反应器 (11)4.2热能的综合利用 (12)结论 (14)参考文献..................................................................................... 错误!未定义书签。
- 1、下载文档前请自行甄别文档内容的完整性,平台不提供额外的编辑、内容补充、找答案等附加服务。
- 2、"仅部分预览"的文档,不可在线预览部分如存在完整性等问题,可反馈申请退款(可完整预览的文档不适用该条件!)。
- 3、如文档侵犯您的权益,请联系客服反馈,我们会尽快为您处理(人工客服工作时间:9:00-18:30)。
改良西门子法生产多晶硅工艺流程来源:日晶科技作者:顾斌时间:2010-07-291. 氢气制备与净化工序在电解槽内经电解脱盐水制得氢气。
电解制得的氢气经过冷却、分离液体后,进入除氧器,在催化剂的作用下,氢气中的微量氧气与氢气反应生成水而被除去。
除氧后的氢气通过一组吸附干燥器而被干燥。
净化干燥后的氢气送入氢气贮罐,然后送往氯化氢合成、三氯氢硅氢还原、四氯化硅氢化工序。
电解制得的氧气经冷却、分离液体后,送入氧气贮罐。
出氧气贮罐的氧气送去装瓶。
气液分离器排放废吸附剂,氢气脱氧器有废脱氧催化剂排放,干燥器有废吸附剂排放,均由供货商回收再利用。
2. 氯化氢合成工序从氢气制备与净化工序来的氢气和从合成气干法分离工序返回的循环氢气分别进入本工序氢气缓冲罐并在罐内混合。
出氢气缓冲罐的氢气引入氯化氢合成炉底部的燃烧枪。
从液氯汽化工序来的氯气经氯气缓冲罐,也引入氯化氢合成炉的底部的燃烧枪。
氢气与氯气的混合气体在燃烧枪出口被点燃,经燃烧反应生成氯化氢气体。
出合成炉的氯化氢气体流经空气冷却器、水冷却器、深冷却器、雾沫分离器后,被送往三氯氢硅合成工序。
为保证安全,本装置设置有一套主要由两台氯化氢降膜吸收器和两套盐酸循环槽、盐酸循环泵组成的氯化氢气体吸收系统,可用水吸收因装置负荷调整或紧急泄放而排出的氯化氢气体。
该系统保持连续运转,可随时接收并吸收装置排出的氯化氢气体。
为保证安全,本工序设置一套主要由废气处理塔、碱液循环槽、碱液循环泵和碱液循环冷却器组成的含氯废气处理系统。
必要时,氯气缓冲罐及管道内的氯气可以送入废气处理塔内,用氢氧化钠水溶液洗涤除去。
该废气处理系统保持连续运转,以保证可以随时接收并处理含氯气体。
3. 三氯氢硅合成工序原料硅粉经吊运,通过硅粉下料斗而被卸入硅粉接收料斗。
硅粉从接收料斗放入下方的中间料斗,经用热氯化氢气置换料斗内的气体并升压至与下方料斗压力平衡后,硅粉被放入下方的硅粉供应料斗。
供应料斗内的硅粉用安装于料斗底部的星型供料机送入三氯氢硅合成炉进料管。
从氯化氢合成工序来的氯化氢气,与从循环氯化氢缓冲罐送来的循环氯化氢气混合后,引入三氯氢硅合成炉进料管,将从硅粉供应料斗供入管内的硅粉挟带并输送,从底部进入三氯氢硅合成炉。
在三氯氢硅合成炉内,硅粉与氯化氢气体形成沸腾床并发生反应,生成三氯氢硅,同时生成四氯化硅、二氯二氢硅、金属氯化物、聚氯硅烷、氢气等产物,此混合气体被称作三氯氢硅合成气。
反应大量放热。
合成炉外壁设置有水夹套,通过夹套内水带走热量维持炉壁的温度。
出合成炉顶部挟带有硅粉的合成气,经三级旋风除尘器组成的干法除尘系统除去部分硅粉后,送入湿法除尘系统,被四氯化硅液体洗涤,气体中的部分细小硅尘被洗下;洗涤同时,通入湿氢气与气体接触,气体所含部分金属氧化物发生水解而被除去。
除去了硅粉而被净化的混合气体送往合成气干法分离工序。
4. 合成气干法分离工序从三氯氢硅氢合成工序来的合成气在此工序被分离成氯硅烷液体、氢气和氯化氢气体,分别循环回装置使用。
三氯氢硅合成气流经混合气缓冲罐,然后进入喷淋洗涤塔,被塔顶流下的低温氯硅烷液体洗涤。
气体中的大部份氯硅烷被冷凝并混入洗涤液中。
出塔底的氯硅烷用泵增压,大部分经冷冻降温后循环回塔顶用于气体的洗涤,多余部份的氯硅烷送入氯化氢解析塔。
出喷淋洗涤塔塔顶除去了大部分氯硅烷的气体,用混合气压缩机压缩并经冷冻降温后,送入氯化氢吸收塔,被从氯化氢解析塔底部送来的经冷冻降温的氯硅烷液体洗涤,气体中绝大部分的氯化氢被氯硅烷吸收,气体中残留的大部分氯硅烷也被洗涤冷凝下来。
出塔顶的气体为含有微量氯化氢和氯硅烷的氢气,经一组变温变压吸附器进一步除去氯化氢和氯硅烷后,得到高纯度的氢气。
氢气流经氢气缓冲罐,然后返回氯化氢合成工序参与合成氯化氢的反应。
吸附器再生废气含有氢气、氯化氢和氯硅烷,送往废气处理工序进行处理。
出氯化氢吸收塔底溶解有氯化氢气体的氯硅烷经加热后,与从喷淋洗涤塔底来的多余的氯硅烷汇合,然后送入氯化氢解析塔中部,通过减压蒸馏操作,在塔顶得到提纯的氯化氢气体。
出塔氯化氢气体流经氯化氢缓冲罐,然后送至设置于三氯氢硅合成工序的循环氯化氢缓冲罐;塔底除去了氯化氢而得到再生的氯硅烷液体,大部分经冷却、冷冻降温后,送回氯化氢吸收塔用作吸收剂,多余的氯硅烷液体(即从三氯氢硅合成气中分离出的氯硅烷)经冷却后送往氯硅烷贮存工序的原料氯硅烷贮槽。
5. 氯硅烷分离提纯工序在三氯氢硅合成工序生成,经合成气干法分离工序分离出来的氯硅烷液体送入氯硅烷贮存工序的原料氯硅烷贮槽;在三氯氢硅还原工序生成,经还原尾气干法分离工序分离出来的氯硅烷液体送入氯硅烷贮存工序的还原氯硅烷贮槽;在四氯化硅氢化工序生成,经氢化气干法分离工序分离出来的氯硅烷液体送入氯硅烷贮存工序的氢化氯硅烷贮槽。
原料氯硅烷液体、还原氯硅烷液体和氢化氯硅烷液体分别用泵抽出,送入氯硅烷分离提纯工序的不同精馏塔中。
6. 三氯氢硅氢还原工序经氯硅烷分离提纯工序精制的三氯氢硅,送入本工序的三氯氢硅汽化器,被热水加热汽化;从还原尾气干法分离工序返回的循环氢气流经氢气缓冲罐后,也通入汽化器内,与三氯氢硅蒸汽形成一定比例的混合气体。
从三氯氢硅汽化器来的三氯氢硅与氢气的混合气体送入还原炉内。
在还原炉内通电的炽热硅芯/硅棒的表面,三氯氢硅发生氢还原反应,生成硅沉积下来,使硅芯/硅棒的直径逐渐变大,直至达到规定的尺寸。
氢还原反应同时生成二氯二氢硅、四氯化硅、氯化氢和氢气,与未反应的三氯氢硅和氢气一起送出还原炉,经还原尾气冷却器用循环冷却水冷却后,直接送往还原尾气干法分离工序。
还原炉炉筒夹套通入热水,以移除炉内炽热硅芯向炉筒内壁辐射的热量,维持炉筒内壁的温度。
出炉筒夹套的高温热水送往热能回收工序,经废热锅炉生产水蒸汽而降温后,循环回本工序各还原炉夹套使用。
还原炉在装好硅芯后,开车前先用水力射流式真空泵抽真空,再用氮气置换炉内空气,再用氢气置换炉内氮气(氮气排空),然后加热运行,因此开车阶段要向环境空气中排放氮气和少量的真空泵用水(可作为清洁下水排放);在停炉开炉阶段(约5~7天1次),先用氢气将还原炉内含有氯硅烷、氯化氢、氢气的混合气体压入还原尾气干法回收系统进行回收,然后用氮气置换后排空,取出多晶硅产品,移出废石墨电极,视情况进行炉内超纯水洗涤,因此停炉阶段将产生氮气、废石墨和清洗废水。
氮气是无害气体,因此正常情况下还原炉开、停车阶段无有害气体排放。
废石墨由原生产厂回收,清洗废水送项目含氯化物酸碱废水处理系统处理。
7. 还原尾气干法分离工序从三氯氢硅氢还原工序来的还原尾气经此工序被分离成氯硅烷液体、氢气和氯化氢气体,分别循环回装置使用。
还原尾气干法分离的原理和流程与三氯氢硅合成气干法分离工序十分类似。
从变温变压吸附器出口得到的高纯度的氢气,流经氢气缓冲罐后,大部分返回三氯氢硅氢还原工序参与制取多晶硅的反应,多余的氢气送往四氯化硅氢化工序参与四氯化硅的氢化反应;吸附器再生废气送往废气处理工序进行处理;从氯化氢解析塔顶部得到提纯的氯化氢气体,送往放置于三氯氢硅合成工序的循环氯化氢缓冲罐;从氯化氢解析塔底部引出的多余的氯硅烷液体(即从三氯氢硅氢还原尾气中分离出的氯硅烷),送入氯硅烷贮存工序的还原氯硅烷贮槽。
8. 四氯化硅氢化工序经氯硅烷分离提纯工序精制的四氯化硅,送入本工序的四氯化硅汽化器,被热水加热汽化。
从氢气制备与净化工序送来的氢气和从还原尾气干法分离工序来的多余氢气在氢气缓冲罐混合后,也通入汽化器内,与四氯化硅蒸汽形成一定比例的混合气体。
从四氯化硅汽化器来的四氯化硅与氢气的混合气体,送入氢化炉内。
在氢化炉内通电的炽热电极表面附近,发生四氯化硅的氢化反应,生成三氯氢硅,同时生成氯化氢。
出氢化炉的含有三氯氢硅、氯化氢和未反应的四氯化硅、氢气的混合气体,送往氢化气干法分离工序。
氢化炉的炉筒夹套通入热水,以移除炉内炽热电极向炉筒内壁辐射的热量,维持炉筒内壁的温度。
出炉筒夹套的高温热水送往热能回收工序,经废热锅炉生产水蒸汽而降温后,循环回本工序各氢化炉夹套使用。
9. 氢化气干法分离工序从四氯化硅氢化工序来的氢化气经此工序被分离成氯硅烷液体、氢气和氯化氢气体,分别循环回装置使用。
氢化气干法分离的原理和流程与三氯氢硅合成气干法分离工序十分类似。
从变温变压吸附器出口得到的高纯度氢气,流经氢气缓冲罐后,返回四氯化硅氢化工序参与四氯化硅的氢化反应;吸附再生的废气送往废气处理工序进行处理;从氯化氢解析塔顶部得到提纯的氯化氢气体,送往放置于三氯氢硅合成工序的循环氯化氢缓冲罐;从氯化氢解析塔底部引出的多余的氯硅烷液体(即从氢化气中分离出的氯硅烷),送入氯硅烷贮存工序的氢化氯硅烷贮槽。
10. 氯硅烷贮存工序本工序设置以下贮槽:100m3氯硅烷贮槽、100m3工业级三氯氢硅贮槽、100m3工业级四氯化硅贮槽、100 m3氯硅烷紧急排放槽等。
从合成气干法分离工序、还原尾气干法分离工序、氢化气干法分离工序分离得到的氯硅烷液体,分别送入原料、还原、氢化氯硅烷贮槽,然后氯硅烷液体分别作为原料送至氯硅烷分离提纯工序的不同精馏塔。
在氯硅烷分离提纯工序3级精馏塔顶部得到的三氯氢硅、二氯二氢硅的混合液体,在4、5级精馏塔底得到的三氯氢硅液体,及在6、8、10级精馏塔底得到的三氯氢硅液体,送至工业级三氯氢硅贮槽,液体在槽内混合后作为工业级三氯氢硅产品外售。
11. 硅芯制备工序采用区熔炉拉制与切割并用的技术,加工制备还原炉初始生产时需安装于炉内的导电硅芯。
硅芯制备过程中,需要用氢氟酸和硝酸对硅芯进行腐蚀处理,再用超纯水洗净硅芯,然后对硅芯进行干燥。
酸腐蚀处理过程中会有氟化氢和氮氧化物气体逸出至空气中,故用风机通过罩于酸腐蚀处理槽上方的风罩抽吸含氟化氢和氮氧化物的空气,然后将该气体送往废气处理装置进行处理,达标排放。
12. 产品整理工序在还原炉内制得的多晶硅棒被从炉内取下,切断、破碎成块状的多晶硅。
用氢氟酸和硝酸对块状多晶硅进行腐蚀处理,再用超纯水洗净多晶硅块,然后对多晶硅块进行干燥。
酸腐蚀处理过程中会有氟化氢和氮氧化物气体逸出至空气中,故用风机通过罩于酸腐蚀处理槽上方的风罩抽吸含氟化氢和氮氧化物的空气,然后将该气体送往废气处理装置进行处理,达标排放。
经检测达到规定的质量指标的块状多晶硅产品送去包装。
13. 废气及残液处理工序① 含氯化氢工艺废气净化SiHCl3提纯工序排放的废气、还原炉开停车、事故排放废气、氯硅烷及氯化氢储存工序储罐安全泄放气、CDI吸附废气全部用管道送入废气淋洗塔洗涤。
废气经淋洗塔用10%NaOH连续洗涤后,出塔底洗涤液用泵送入工艺废料处理工序,尾气经15m高度排气筒排放。
② 残液处理在精馏塔中排出的、主要含有四氯化硅和聚氯硅烷化合物的釜地残液以及装置停车放净的氯硅烷残液液体送到本工序加以处理,需要处理的液体被送入残液收集槽,然后用氮气将液体压出,送入残液淋洗塔洗涤。