反应精馏技术的关键问题分析
化工行业中的蒸馏工艺技术使用中常见问题

化工行业中的蒸馏工艺技术使用中常见问题在化工行业中,蒸馏是一种常见的分离技术,广泛应用于石油、化工、制药等领域。
然而,在使用蒸馏工艺技术时,常常会遇到一些问题。
本文将针对化工行业中的蒸馏工艺技术使用中常见的问题进行介绍和分析,并提供相应的解决方案。
1. 蒸馏塔内液位控制困难蒸馏塔内的液位控制问题是一种常见的困扰蒸馏工艺操作者的难题。
液位过高会导致液体在干燥塔顶部溢出,从而影响产品质量;液位过低则会造成蒸汽过量与液体接触不足,降低蒸馏效率。
解决方案:液位控制常采用反馈控制的方式,通过修改进料流量、出料流量或底部热油流量来维持合适的液位。
另外,安装液位传感器,并利用自动控制系统实时监测与调整液位,可以提高液位控制的精度与稳定性。
2. 塔底温度异常波动蒸馏塔底部温度异常波动会影响产品的纯度和产量,同时也会增加能源消耗。
解决方案:首先要调整进料流量与热油流量的比例,增加底部的热油流量可以提高塔底温度的稳定性。
其次,对塔底温度进行实时监测,并通过自动控制系统调整进料温度和流量,以平稳地控制塔底温度。
此外,定期检查与维护塔底的加热设备,确保其正常工作,也是保持塔底温度稳定的重要措施。
3. 外循环液回收问题在蒸馏过程中,为了提高塔内的传热效果,通常会采用外循环方式回收部分底部液体,并将其重新注入塔顶。
解决方案:外循环液回收的关键在于回收液的净化与处理。
可采用沉淀、过滤、离心等物理方法进行初步净化,再采用蒸发、萃取、析出等化学方法进一步处理,以去除其中的杂质与不纯物质。
此外,定期检查外循环液回收系统的设备与管道,确保其运行正常,也是确保外循环液质量的重要举措。
4. 塔顶压力控制不准确蒸馏塔顶压力的不准确控制会影响蒸馏塔内液体的沸点,进而影响分离效果和产品纯度。
解决方案:首先,采用反馈控制的方式对塔顶压力进行实时监测,并通过调整蒸汽流量和冷却水流量以维持合适的塔顶压力。
其次,确保塔顶压力传感器的准确性与灵敏度,在使用前进行仔细的校准和调试。
新型精馏技术及其发展趋势
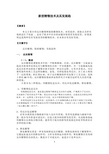
新型精馏技术及其发展趋【摘要】本文主要介绍反应精馏和隔壁精馏技术,对其原理、优缺点及研究现状进行了综述。
总结了技术中存在的问题并展望其发展前景,结果表明这是两种很有发展前景的精馏技术,在未来会有很好发展。
【关键字】反应精馏;隔壁精馏;发展趋势一、反应精馏(一)、概述反应精馏是蒸馏技术中的一个特殊领域。
目前,反应精馏一方面成为提高分离效率而将反应与精馏相结合的一中分离操作,另一方面则成为提高反应收率而借助于精馏分离手段的一种反应过程。
它有许多优点,可以替代某些传统工艺过程如醚化、加氢、芳烃烷基化等反应,在工业上得到了一定的重视。
但长期以来,对于反应精馏的研究仅限于工艺方面,直到上世纪80年代,反应精馏的基础理论性研究才开始引起研究人员的兴趣和重视。
主要分为三种情况:用精馏促进反应,用反应促进精馏,催化精馏。
1、用精馏促进反应用精馏促进反应,就是通过精馏不断移走反应的生成物,产物离开了反应区,从而破坏了原有的化学平衡,使反应向生成产物的方向移动,以提高反应转化率和收率。
在一定程度上变可逆为不可逆,而且可得到很纯的产物。
但采用这种方法必须具备一定的条件:①生成物的沸点必须高于或低于反应物;②在精馏温度下不会导致副反应等不利影响的增加。
目前在工业上主要应用于酯类(如乙酸乙酯)的生产。
2、用反应促进精馏在待分离的混合物溶液中加入反应夹带剂,使其有选择地与溶液中的某一组分发生快速可逆反应,以加大组分间的挥发度差异,从而能容易地用精馏方法将混合物分离。
通常用于组分的挥发度很接近但化学性质存在差异的混合物。
3、催化精馏催化精馏实质是一种非均相催化反应精馏。
将催化剂填充于精馏塔中,它既起加速反应的催化作用,又作为填料起分离作用,催化精馏具有均相反应精馏的全部优点,既适合于可逆反应,也适合于连串反应。
反应精馏的原理可用下图来表示:(二)、反应精馏技术的优点1、选择性高,由于反应产物一旦生成即移出反应区,对于如连串反应之类的复杂反应,可抑制副反应,提高收率。
反应精馏实验实验报告

实验报告:反应精馏实验摘要:本实验旨在通过反应精馏的方法分离和纯化混合物。
通过针对反应精馏实验过程中的变量的调节,我们成功地实现了对混合物的分离和纯化。
本实验采用了硫酸盐的反应,通过反应精馏使得反应物和产物分离,最终得到纯净的产物。
通过对实验中不同变量的观察和分析,我们探讨了对反应精馏实验结果的影响,为进一步研究和应用反应精馏提供了指导。
引言:反应精馏是一种常用的分离和纯化技术,广泛应用于化学、医药等领域。
其基本原理是通过利用不同组分的沸点差异,在特定的条件下将反应物和产物分离和纯化。
在本实验中,我们选取了硫酸盐的反应作为研究对象,通过反应精馏将反应物和产物进行分离和纯化。
材料与方法:1. 反应装置:包括反应釜、冷凝器、接收瓶等。
2. 反应物:硫酸盐。
3. 溶剂:适量的有机溶剂。
4. 加热设备:加热板或电炉。
5. 实验操作:根据实验需求,调整反应物和溶剂的比例,加热设备的温度等。
结果与讨论:在实验过程中,我们观察到随着温度的升高,反应物开始发生反应,产生气体。
通过冷凝器将气体冷凝成液体,并收集于接收瓶中。
通过不同温度下的收集物的分析和比较,我们可以得到不同组分的沸点,从而实现对混合物的分离和纯化。
通过对实验结果的分析,我们发现温度是影响反应精馏实验的关键因素之一。
合适的温度可以促使反应物迅速发生反应,并将产物分离出来。
然而,过高的温度可能导致副反应的发生,影响产物的纯度。
因此,在进行反应精馏实验时,选择适当的温度非常重要。
此外,反应物和溶剂的比例也会对实验结果产生影响。
较高的溶剂浓度可能导致反应物无法充分反应,产生过多的副产品。
相反,过低的溶剂浓度可能使得反应物无法充分溶解,影响反应的进行。
因此,需要根据具体实验情况来选择适当的反应物和溶剂的比例。
结论:通过本实验,我们成功地应用了反应精馏的方法对混合物进行了分离和纯化。
通过对实验过程中变量的调节,如温度和反应物与溶剂的比例,我们得到了纯净的产物。
精馏操作过程中的常见问题及案例分析

精馏操作过程中的常见问题及案例分析精馏技术已经过了100多年的发展,成为了目前应用最广泛的一种分离技术,在化学工业、石油化工、精细化工、轻工化工、煤化工、食品工业、医药工业、原子能工业、冶金工业等领域都有广泛的应用。
今天,小7为您总结最简单的精馏操作过程中的常见问题,精馏人,您能秒答吗?精馏塔操作中常见4大问题液泛在精馏操作中,下层塔板上的液体涌至上层塔板,液泛是塔内液体过量的积聚,使液体无法从塔顶向塔底流动,塔的正常操作遭到破坏,这种现象叫做液泛。
1喷射夹带液泛夹带由液体的喷射作用引起,如果蒸汽速度过大,将产生大量雾沫夹带,液体积聚在上层塔板而不是逐板下流。
一般发生在液相负荷较小区域,汽液接触呈喷射状态。
2泡沫夹带液泛在较大液相负荷区,两相接触为泡沫状态。
随汽速增大,板上泡沫层高度增加,夹带量增加。
当汽速达某一液泛速度时,泡沫层面接近上层塔板,夹带急剧增大,引起上层塔板液体积聚,产生液泛。
这种液泛一般只在较小板间距(小于375mm~450mm)时发生,板间距大时,将转变为喷射夹带液泛。
3.降液管满溢液泛由于汽流穿过塔板和板上液层造成的压降,以及液体流经降液管的压降,使得降液管中液面高出板上的液面,又因停留在降液管中的是汽液混合物,液面升得更高。
随汽流增大产生的压降也随之增大;随液流增大,板上液层加厚,将夜光阻力增加,两者均使得降液管中液面上升。
当此液面升到超过上层塔板的溢流堰高度时,液体不在经降液管逐板下流,而是液流倒灌,产生了降液满溢液泛。
4.降液阻塞液泛测量压降是主要的判断液泛主要手段,对塔中汽液相负荷的各段分别测量压降能更灵敏上的判断液泛的发生和发生部位,由于液泛造成塔体中积液,压降随之增大。
液泛现象的判断压降过大或急剧升高测量压降是主要的判断液泛主要手段,对塔中汽液相负荷的各段分别测量压降能更灵敏上的判断液泛的发生和发生部位,由于液泛造成塔体中积液,压降随之增大。
塔底液位下降和波动由于塔中某部位,尤其在进料口下面的部位发生液泛,液体不能畅通溢流,而再沸汽化仍然继续,必然导致塔底液位下降。
反应精馏技术的研究现状及其应用

第 17 卷第 3 期
刘雪暖等: 反应精馏技术的研究现状及其应用
16 5
特定体系的工艺探索、70 年代提出反应精馏 的计算方法、80 年代进行数学模拟和最优化 研究几个发展阶段[ 1] 。
反应精馏具有以下优点[ 2] : 1) 选择性高; 2) 使可逆反应收率提高; 3) 温度易于控制, 避 免出现“热点”问题; 4) 缩短反应时间, 强化设 备生产能力; 5) 能耗低, 操作费用低; 6) 投资 少。由于反应和精馏之间存在着很复杂的相 互影响, 反应精馏过程比单纯的反应和精馏 过程的研究复杂得多, 至今仍未形成完整的 理论体系, 有关反应精馏的理论研究和应用 研究已成为各国专家们的研究热点。
化 学 工 业 与 工 程 CHEMI CAL INDUST RY AND ENGINEERING
专题综述
第 17 卷 第 3 期 Vol. 17 No. 3
反应精馏技术的研究现状及其应用
刘雪暖, 李玉秋
( 石油大学( 华东 ) 炼制系, 山东 东营 257062)
摘要: 本文对反应精馏技术的研究现状及其应用进行了综述。介绍了反应精馏塔及催 化剂, 对催化剂床中传质及流体力学特性、数学模型和反应精馏塔设计方程进行了总 结; 同时介绍了反应精馏技术的应用现状及其可能的应用领域。 关键词: 反应精馏; 催化剂; 数学模型; 传质; 应用 中图分类号: TQ028. 1+ 4 文献标识码: A 文章编号: 1004-9533( 2000) 03-0164-05
N ew t on Raphson+ TDMA
=0
=1
TM
Powell 最小化法
>0
Mod. ma rgule s
反应精馏的模拟与优化

谢谢观看
反应精馏的模拟与优化
01 引言
目录
02 反应精馏模拟
03 反应精馏优化
04 结论
05 参考内容
引言
反应精馏是一种广泛应用于化学工业中的高效分离技术,通过在精馏过程中 实现化学反应,可以有效地提高产品的纯度和收率,降低能耗和物耗。然而,反 应精馏过程复杂,受到多种因素的影响,因此需要进行细致的模拟和优化。本次 演示将介绍反应精馏的模拟和优化方法,以期为相关领域的研究和实践提供有益 的参考。
(1)机理模型:机理模型是根据化学反应的基本原理,建立反应动力学模 型,结合质量传递、能量传递等基本物理过程,对反应精馏过程进行详细描述。 该模型的优点是精度高,可以用于指导工业实践。但是,机理模型复杂,需要大 量的实验数据支持,建模过程繁琐。
(2)过程模型:过程模型是将反应精馏过程简化为一系列物理量,如温度、 压力、浓度等,通过数学方法对它们进行描述。该模型的优点是简单易懂,可以 快速得到结果。但是,过程模型精度较低,难以用于指导工业实践。
反应精馏过程模拟优化
1、反应精馏过程模拟优化的意 义和目的
反应精馏过程模拟优化的意义在于通过对实际生产过程的模拟和优化,实现 反应精馏过程的高效运行,提高产品质量和产量,降低能源消耗和环境污染。其 目的主要包括:(1)通过对物性参数的优化,提高物系计算的准确性和精度; (2)通过对流程的优化,提高反应精馏过程的分离效果和生产效率;(3)பைடு நூலகம்过 对优化算法的改进,缩短优化时间和提高优化效率。
3、反应精馏过程模拟优化的实 际应用效果
反应精馏过程模拟优化的实际应用效果主要体现在以下几个方面:(1)提 高产品质量和产量,降低能源消耗和环境污染;(2)降低生产成本,提高企业 经济效益;(3)推动化工行业的可持续发展和创新进步。例如,某石化企业利 用ASPEN软件对反应精馏过程进行优化后,提高了柴油产物的质量和产量,同时 降低了能耗和污染物排放量,取得了显著的经济效益和社会效益。
反应精馏技术的研究现状及应用
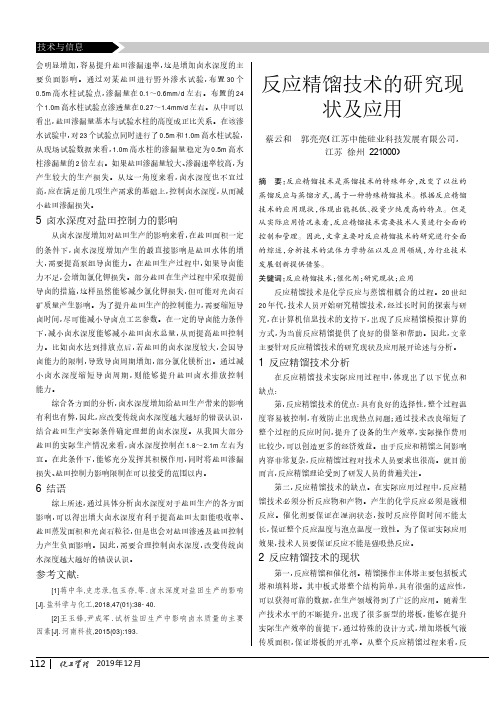
2019年12月会明显增加,容易提升盐田渗漏速率,这是增加卤水深度的主要负面影响。
通过对某盐田进行野外渗水试验,布置30个0.5m 高水柱试验点,渗漏量在0.1~0.6mm/d 左右。
布置的24个1.0m 高水柱试验点渗透量在0.27~1.4mm/d 左右。
从中可以看出,盐田渗漏量基本与试验水柱的高度成正比关系。
在该渗水试验中,对23个试验点同时进行了0.5m 和1.0m 高水柱试验,从现场试验数据来看,1.0m 高水柱的渗漏量稳定为0.5m 高水柱渗漏量的2倍左右。
如果盐田渗漏量较大、渗漏速率较高,为产生较大的生产损失。
从这一角度来看,卤水深度也不宜过高,应在满足前几项生产需求的基础上,控制卤水深度,从而减小盐田渗漏损失。
5卤水深度对盐田控制力的影响从卤水深度增加对盐田生产的影响来看,在盐田面积一定的条件下,卤水深度增加产生的最直接影响是盐田水体的增大,需要提高泵组导卤能力。
在盐田生产过程中,如果导卤能力不足,会增加氯化钾损失。
部分盐田在生产过程中采取提前导卤的措施,这样虽然能够减少氯化钾损失,但可能对光卤石矿质量产生影响。
为了提升盐田生产的控制能力,需要缩短导卤时间,尽可能减小导卤点工艺参数。
在一定的导卤能力条件下,减小卤水深度能够减小盐田卤水总量,从而提高盐田控制力。
比如卤水达到排放点后,若盐田的卤水深度较大,会因导卤能力的限制,导致导卤周期增加,部分氯化镁析出。
通过减小卤水深度缩短导卤周期,则能够提升盐田卤水排放控制能力。
综合各方面的分析,卤水深度增加给盐田生产带来的影响有利也有弊,因此,应改变传统卤水深度越大越好的错误认识,结合盐田生产实际条件确定理想的卤水深度。
从我国大部分盐田的实际生产情况来看,卤水深度控制在1.8~2.1m 左右为宜。
在此条件下,能够充分发挥其积极作用,同时将盐田渗漏损失、盐田控制力影响限制在可以接受的范围以内。
6结语综上所述,通过具体分析卤水深度对于盐田生产的各方面影响,可以得出增大卤水深度有利于提高盐田太阳能吸收率、盐田蒸发面积和光卤石粒径,但是也会对盐田渗透及盐田控制力产生负面影响。
影响精馏塔精馏效果的因素及处理措施

影响精馏塔精馏效果的因素及处理措施【摘要】蒸馏是石油工业等化工生产中的一个重要分离操作单元。
本文简要介绍了精馏的工作原理,分析了精馏操作过程中的影响因素,并在此基础上提出了精馏操作的优化方向和目前常用的节能措施。
【关键词】精馏操作原理、影响因素、优化策略、节能措施前言在蒸馏操作过程和设备中,蒸馏塔是最常见的操作形式——蒸馏过程是通过蒸馏塔完成和实现的。
一般来说,蒸馏塔的操作形式可分为两种:间歇蒸馏塔和连续蒸馏塔。
蒸馏塔的顶部不断喷洒液体,液体与从底部进入塔中的上升蒸汽接触并发生化学反应。
分离是通过两者气相中不同的沸点来实现的。
在蒸馏塔中发生反应后,一部分液体将返回蒸馏塔,而另一部分作为最终产物从蒸馏塔中取出。
一、蒸馏操作原理蒸馏是石油工业等化工生产中的一个重要分离操作单元。
通常,混合在一起的液体的分离过程是通过蒸馏实现的。
然而,蒸馏分离过程需要大量的能源,因此如何优化和节约能源具有重要的现实意义。
二、精馏操作过程的影响因素(一)工作压力和温度的影响。
蒸馏操作只能在一定的压力和温度下进行。
在蒸馏操作过程中,蒸馏塔内部的压力不是恒定的,而是随着反应的进行而不断变化,直接导致不同塔板上的气液组成发生变化。
也就是说,蒸馏塔内部的压力变化将直接影响气相中轻组分的含量和浓度。
蒸馏塔内部的温度变化也对蒸馏操作过程产生重大影响。
例如,当材料的温度降低时,它将相应地增加蒸馏塔底部的热负荷,导致蒸馏塔顶部的冷却负荷降低。
蒸馏塔内部的温度变化意味着物质的状态发生了变化,反应条件也发生了改变,这必然会对反应结果产生重大影响。
因此,精馏塔内部温度的控制是影响精馏操作的重要因素之一。
(二)回流比的影响。
回流比可以显著影响蒸馏塔内的蒸馏效果,改变回流比可以控制和调节蒸馏产物的质量。
例如,随着回流比的增加,蒸馏段操作线的斜率也会增加,塔中传质的驱动力也会增大,从而从蒸馏中获得更大的组分。
同时,随着回流比的增加,蒸馏段操作线的斜率也会降低,导致釜内残余液体的组成降低。
精馏塔操作与影响因素分析

精馏塔操作
精馏操作影响因素分析
一、操作压力的影响 精馏塔正常操作应保证在恒压下操作。系统压力的波动对塔的操作将产生影响。 1.影响相平衡关系 压力增加,组分间的相对挥发度降低,平衡线向对角线靠近,分离效率将下降。 2.影响操作温度 温度与气液相的组成有严格的对应关系,生产中常以温度作为衡量塔顶和塔底产品
的增加。 2.进料组成 进料组成的变化将直接影响到产品的质量。进料组成升高,增加了提馏段的
分离负荷,若不及时采取措施,会造成残液中易挥发组分含量增高。同理进料组 成降低,增加了精馏段的分离负荷,会造成馏出液中易挥发组分含量降低。
精馏塔操作
精馏操作影响因素分析
四、采出量的影响与控制 1.塔顶产品采出量 在冷凝器的冷凝负荷不变的情况下,减小塔顶的采出量,会使回流量增加,可
预期的分离效果,应根据温度变化情况采取及时有效的措施。 当回流比等操作条件发生改变时,塔内某些塔板上的温度变化特别明显。即
这些塔板的温度对外界干扰特别敏感,所以将这些塔板称为灵敏板。 所以一般精馏塔至少有三个测温点,塔顶、塔底和灵敏板,而观察的重点是
灵敏板温度变化。
精馏塔操作
精馏操作影响因素分析
三、进料状况的影响 1.进料量 若进料量增加,必然会引起塔内汽、液两相量以及加热剂和冷却剂的消耗量
度以及塔底温度,以便及时作出调整。 6. 在再沸器温度、塔顶温度、塔顶压力、塔压差、回流量等参数趋于稳定后,可基本判定全回流
稳定,可进行连续精馏操作。
精馏塔操作
三、连续精馏操作
1. 全回流稳定后,选择进料板,打开进料泵,调节进料量,进料温度由预热器的加热 功率控制(近泡点进料)。
2. 打开产品采出,采出量要维持回流罐液位恒定(液位低采出量小,液位高采出量可加大)。 3. 在连续精馏进行过程中,确保塔顶压力、塔压差稳定的情况下,及时关注灵敏板的温度、塔顶
影响精馏操作的主要因素及常见问题

影响精馏操作的主要因素1.物料平衡的影响和制约根据精馏塔的总物料衡算可知,对于一定的原料液流量F和组成xF,只要确定了分离程度xD 和xW,馏出液流量D和釜残液流量W也就被确定了。
采出率D/F: D/F=(xF-xW)/(xD-xW)不能任意增减,否则进、出塔的两个组分的量不平衡,必然导致塔内组成变化,操作波动,使操作不能达到预期的分离要求。
在精馏塔的操作中,需维持塔顶和塔底产品的稳定,保持精馏装置的物料平衡是精馏塔稳态操作的必要条件。
通常由塔底液位来控制精馏塔的物料平衡。
2、塔顶回流的影响回流比是影响精馏塔分离效果的主要因素,生产中经常用回流比来调节、控制产品的质量。
当回流比增大时,精馏产品质量提高;当回流比减小时,xD减小而xW增大,使分离效果变差。
回流比增加,使塔内上升蒸汽量及下降液体量均增加,若塔内汽液负荷超过允许值,则可能引起塔板效率下降,此时应减小原料液流量。
调节回流比的方法可有如下几种。
(1)减少塔顶采出量以增大回流比。
(2)塔顶冷凝器为分凝器时,可增加塔顶冷剂的用量,以提高凝液量,增大回流比。
(3)有回流液中间贮槽的强制回流,可暂时加大回流量,以提高回流比,但不得将回流贮槽抽空。
必须注意,在馏出液采出率D/F规定的条件下,籍增加回流比R以提高xD的的方法并非总是有效。
加大操作回流比意味着加大蒸发量与冷凝量,这些数值还将受到塔釜及冷凝器的传热面的限制。
3.进料热状况的影响当进料状况(xF和q)发生变化时,应适当改变进料位置,并及时调节回流比R。
一般精馏塔常设几个进料位置,以适应生产中进料状况,保证在精馏塔的适宜位置进料。
如进料状况改变而进料位置不变,必然引起馏出液和釜残液组成的变化。
进料情况对精馏操作有着重要意义。
常见的进料状况有五种,不同的进料状况,都显著地直接影响提馏段的回流量和塔内的汽液平衡。
精馏塔较为理想的进料状况是泡点进料,它较为经济和最为常用。
对特定的精馏塔,若xF减小,则将使xD和xW均减小,欲保持xD不变,则应增大回流比。
精馏操作的18个问题-精华版

1、影响精馏塔操作的因素有哪些?影响精馏操作的因素有以下几种:(1)回流比的影响;(2)进料状态的影响;(3)进料量大小的影响;(4)进料组成变化的影响;(5)进料温度变化的影响;(6)塔顶冷剂量大小的影响;(7)塔顶采出量大小的影响;(8)塔底采出量大小的影响。
2、进料状态有哪几种,对精馏操作有何影响?进料状态有五种:(1)冷进料。
(2)饱和液。
(3)气液混和物。
(4)饱和气。
(5)过热气。
对于固定进料的某个塔来说,进料状态的改变,将会影响产品质量和损失。
例如:某塔为饱和液进料,当改为冷进料时,料液入塔后在加料板上与提馏段上升的蒸气相遇,即被加热至饱和温度,与此同时,上升蒸汽有一部分被冷凝下来,精馏段塔板数过多,提馏段板数不足,结果会造成釜液中损失增加。
这时在操作上,应适当调整再沸器蒸汽,使塔的回流量达到原来量。
3、进料量的大小对精馏操作有何影响?有两种情况:(l)进料量波动范围不超过塔顶冷凝器和加热釜的负荷范围时,只要调节得当,对顶温和釜温不会有显著变化,而只影响塔内上升蒸汽速度的变化。
(2)进料量变动的范围超过了塔顶冷凝器和加热的负荷范围时,不仅影响塔内上升蒸汽速度的变化,而且会改变塔顶、塔釜温度,致使塔板上的气液平衡组成改变,直接影响塔顶产品的质量和塔釜损失。
总之,进料过大的波动,将会破坏塔内正常的物料平衡和工艺条件,造成了系列的波动。
因此,应平衡进料,细心调节。
4、进料组成的变化对精馏操作有何影响?进料组成的变化直接影响精馏操作,当进料中重组分增加时,精馏段负荷增加,容易造成重组分带到塔顶,使塔顶产品不合格,若进料中轻组分增加,提馏段负菏就会加重,容易造成釜液中轻组份损失加大。
进料组成的变化,还会引起物料平衡和工艺条件的变化。
10、什么是减压精馏?塔顶压力低于大气压的精馏操作过程,叫减压精馏。
减压精馏通常分离沸点较高的混合物或高温下易聚合的混合物。
如乙苯、苯乙烯分离,二乙苯、三乙苯、四乙苯以及沸点更高组份分离都采用减压分离。
精馏操作关键问题的探究

精馏操作关键问题的探究摘要:本文主要介绍了精馏装置工艺和精馏操作步骤及操作过程中的把握的几个主要环节。
关键词:精馏操作平衡精馏操作单元是化工生产过程中最重要的单元过程之一,也是化工企业应用最广泛的单元过程之一。
熟练地掌握其操作方法是化工类专业学生必备的基本技能。
能使学生的工程意识和操作技能得到提高,进一步缩短高职学生入厂后的适应期,真正实现学校与企业的无缝对接。
一、精馏装置简介学院投资几十万元建设精馏实训装置,该实训装置为一种集实训、实训、科研、技能鉴定功能于一体的四位一体多功能化工培训装置,为学生现场操作真实的工业生产装置提供了条件。
1.精馏单元现场装置及工艺在精馏实训装置中,所用设备包括精馏塔、原料泵、回流泵、塔顶产品泵、原料预热器、塔预冷凝器、原料储罐、回流罐、塔釜产品罐、塔顶产品罐、缓冲罐等。
本单元是连续精馏操作过程,原料为18(以下均为质量百分比)的乙醇水溶液,经过精馏塔分离后,得到馏出液纯度为89%的乙醇。
其工艺流程如图所示。
原料液经流量调节器FIC01控制,以4L/h的流量进入预热器E103中,预热至60℃(其温度由温度调节器TIC10控制)后,从精馏塔的第六块塔板(全塔除塔釜外共10块塔板)进料。
塔顶蒸汽经冷凝器E104冷凝为液体后,经缓冲罐V103进入回流冷凝液储罐V104中。
当V104的液位大于回流液位控制上限(其值为150mm,由调节器LIC02控制时,系统自动启动回流泵Pl02,进行塔顶回流。
当塔顶温度小于79℃并且回流冷凝液储罐V104大于回流液位控制上限时,采出泵自动采出,作为塔顶产品经流量计F103计量后进入塔顶产品罐V105中。
塔釜液体的一部分经再沸器E10l加热后送回精馏塔,另一部分作为塔釜产品,经塔底冷却器E102进入塔底产品罐V102中。
,精馏塔塔釜液位由液位调节器LIC01控制,当液位高于规定值380mm时,电动调节阀V Al04自动打开,当液位低于规定值380mm时,电动调节阀V Al04自动关闭。
影响精馏操作的因素有哪些?其实没你想的那么难!

影响精馏操作的因素有哪些?其实没你想的那么难!除了设备问题以外,精馏过程的影响因素主要有以下几个方面:塔的温度和压力(包括塔顶、塔釜和某些具有特殊意义的塔板)、进料状态、进料量、进料组成、进料温度、塔内上升蒸气速度和蒸发釜的加热量、回流量、塔顶冷剂量、塔顶采出量和塔底采出量。
塔的操作就是按照塔顶产品和塔底产品的组成要求来对这几个影响因素进行调节的。
今天七哥就来好好给大家说说这些因素对精馏操作的影响!1、精馏塔操作压力变化对精馏操作的影响塔的设计和操作都是基于一定的压力下进行的,因袭一般的精馏塔总是先要保证压力恒定。
塔压的波动对塔的操作影响是很大的。
塔压的波动将产生如下的影响。
① 影响产品质量和物料平衡改变操作压力,将使每块塔板上的气液相平衡的组成发生改变,塔压升高,则气相中的重组分减少,相应的提高了气相中的轻组分的浓度;液相的轻组分含量增加,同时改变了气液相的比重,使液相增加,气相减少。
总的结果是:塔顶中的轻组分浓度增加,但数量减少;塔釜中的重组分浓度增加,釜液量增加。
同理,压力降低,塔顶馏分的数量增加,轻组分浓度减少;釜液量减少,轻组分浓度减少。
正常操作中应保持恒定的压力,但若操作不正常时,引起塔顶中的重组分浓度增加,则可适当的增加操作压力的办法,使塔顶产品合格,但此时,液相中的轻组分损失增加。
② 改变组分间的相对挥发度压力增大,组分间的相对挥发度降低,分离效果下降,反之亦然。
③ 改变塔的生产能力压力增大,组分的重度增大,塔的处理能力增大。
④ 塔压的波动这将引起温度和组成间对应关系的混乱。
我们在操作中经常以温度作为衡量产品质量的间接标准,但这只是在压力恒定的情况下才是正确的。
当塔压改变时,混合物的露点、泡点都会发生改变,引起全塔的温度分布发生改变,温度和产品质量对应关系也将发生改变。
从以上分析来看,改变操作压力,将改变整个塔的工作状态,因此在正常操作中必须维持塔压恒定,只有在塔的正常操作受到破坏时,才能上述分析,在工艺指标允许的范围内,对塔的压力进行适当的调节。
反应精馏效率影响因素的分析与探讨

反应精馏效率影响因素的分析与探讨作者:汪海峰来源:《价值工程》2011年第29期Analysis and Discussion on Influencing Factors of Reactive Distillation EfficiencyWang Haifeng(Daqing Refining and Chemical Company,Daqing 163411,China)摘要:近年来人们相继开发了许多新型的反应精馏工艺,以取代传统的化工生产工艺,但目前反应精馏工艺流程的选择仍然靠人们的经验和实验探索。
本文通过对反应精馏效率影响因素的分析与探讨,阐明了反应精馏效率与工艺流程等影响因素的相互关系,为反应精馏工艺的优化提供一定的参考依据。
Abstract: In recent years, people developed many new type of reactive distillation process one after another, which have displaced traditional chemical production process. However, the selection of reactive distillation process flow still depends on people's experience and experiment exploration. The paper analyzed and discussed influencing factors of reactive distillation efficiency, demonstrated correlations of reactive distillation efficiency and process flow providing reference for optimizing reactive distillation process.关键词:反应精馏工艺流程效率Key words: reactive distillation;process flow;efficiency中图分类号:S220.6 文献标识码:A文章编号:1006-4311(2011)29-0073-011反应精馏工艺简介反应精馏(RD,reactive distillation)是将化学反应与精馏分离结合在同一设备中进行的一种耦合过程。
反应精馏工程工艺解决方案

反应精馏工程工艺解决方案一、传统的精馏工程工艺解决方案传统的精馏工程工艺解决方案主要包括托盘塔精馏和填料塔精馏两种。
在托盘塔精馏中,原料混合物通过塔底加热后上升至塔顶,同时冷却剂从塔顶或塔底进入,通过与原料混合物的接触分离出不同组分。
而在填料塔精馏中,塔内装有填料,原料混合物从塔顶或塔底喷入,同时冷却剂从塔顶进入,通过与填料的接触分离出不同组分。
传统的精馏工程工艺解决方案在实际应用中具有较高的可靠性和稳定性,但也存在以下缺点:1. 能耗较高。
2.降低产品纯度。
3. 塔内流体分布不均匀,容易产生结晶和积垢。
4. 塔内气液传质效率低。
因此,传统的精馏工程工艺解决方案在一定程度上影响了工艺的效率和经济性。
二、新型的精馏工程工艺解决方案为了克服传统的精馏工程工艺解决方案的不足,各国研究机构和企业纷纷开展了新型的精馏工程工艺解决方案的研发工作。
这些新型的精馏工程工艺解决方案主要包括:1. 引入新型填料。
例如,开发了一种特殊结构的填料,可提高传质效率,减少能耗。
2. 引入新型塔内结构。
例如,研发了一种新型的塔板结构,具有更好的气液分布性能和传质效率。
3. 引入新型传热方式。
例如,采用超声波传热技术,可提高传热效率,降低能耗。
4. 引入新型控制技术。
例如,采用智能控制技术,可实现精确控制,减少产品纯度波动。
5. 引入新型辅助设备。
例如,采用高效过热器和冷凝器,可提高传质效率,降低能耗。
这些新型的精馏工程工艺解决方案在一定程度上能够解决传统的精馏工程工艺中存在的问题,提高了工艺的效率和经济性,受到广泛关注和应用。
三、精馏工程工艺解决方案的发展趋势随着科学技术的不断进步,精馏工程工艺解决方案也在不断发展和优化。
未来精馏工程工艺解决方案的发展趋势主要有以下几个方面:1. 发展成套技术。
随着工厂规模的扩大,设备和工艺的一体化成套技术将成为未来的发展趋势,以提高效率和降低成本。
2. 发展高效节能技术。
随着节能环保理念的深入人心,高效节能技术将成为未来的发展方向,以降低能源消耗,减少环境污染。
反应精馏技术的关键问题分析_秦建华
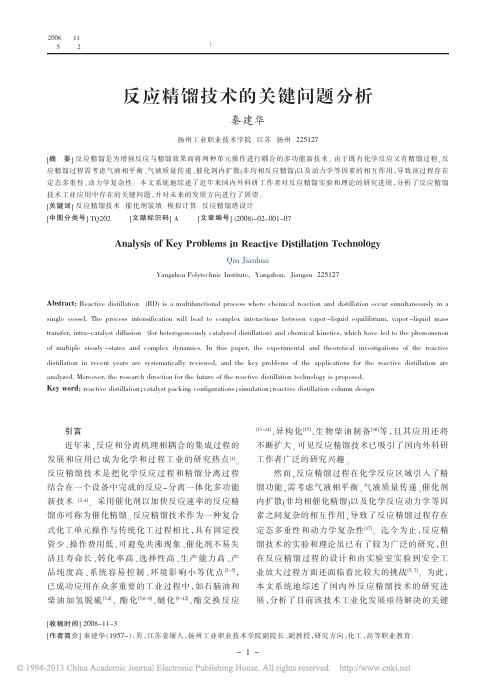
[收稿时间]2008-11-3[作者简介]秦建华(1957-),男,江苏姜堰人,扬州工业职业技术学院副院长、副教授,研究方向:化工,高等职业教育。
引言近年来,反应和分离机理相耦合的集成过程的发展和应用已成为化学和过程工业的研究热点[1]。
反应精馏技术是把化学反应过程和精馏分离过程结合在一个设备中完成的反应-分离一体化多功能新技术[2-4]。
采用催化剂以加快反应速率的反应精馏亦可称为催化精馏。
反应精馏技术作为一种复合式化工单元操作与传统化工过程相比,具有固定投资少、操作费用低、可避免共沸现象、催化剂不易失活且寿命长、转化率高、选择性高、生产能力高、产品纯度高、系统容易控制、环境影响小等优点[2-5],已成功应用在众多重要的工业过程中,如石脑油和柴油加氢脱硫[3,4]、酯化[5,6-8]、醚化[9-12]、酯交换反应[13-14]、异构化[15]、生物柴油制备[16]等,且其应用还将不断扩大。
可见反应精馏技术已吸引了国内外科研工作者广泛的研究兴趣。
然而,反应精馏过程在化学反应区域引入了精馏功能,需考虑气液相平衡、气液质量传递、催化剂内扩散(非均相催化精馏)以及化学反应动力学等因素之间复杂的相互作用,导致了反应精馏过程存在定态多重性和动力学复杂性[17]。
迄今为止,反应精馏技术的实验和理论虽已有了较为广泛的研究,但在反应精馏过程的设计和由实验室实验到安全工业放大过程方面还面临着比较大的挑战[5,7]。
为此,本文系统地综述了国内外反应精馏技术的研究进展,分析了目前该技术工业化发展亟待解决的关键反应精馏技术的关键问题分析秦建华扬州工业职业技术学院江苏扬州225127[摘要]反应精馏是为增强反应与精馏效果而将两种单元操作进行耦合的多功能新技术。
由于既有化学反应又有精馏过程,反应精馏过程需考虑气液相平衡、气液质量传递、催化剂内扩散(非均相反应精馏)以及动力学等因素的相互作用,导致该过程存在定态多重性、动力学复杂性。
精馏原理及故障分析

漏 液
当上升气量减少过多或者筛孔直径过大时, 由于气流速度过小而托不住筛孔上的液体, 液体从筛孔直接漏入下一塔板,即为分馏 塔漏液。
漏液
汽轮机转速低时如何操作?
谢谢大家
从上表可以看出:虽然填料塔高度增加,但其具有阻力小、分离效率高、塔径小等多项 优点,目前空分装置的上塔和氩塔全部采用规整填料塔,下塔也逐渐开始采用填料塔
空气精馏分离操作中常见故障分析
空气精馏塔操作中常见故障包括:上下塔压 力背离、氧氮气纯度不合格、漏液、液悬、 粗氩冷凝器氮塞以及精氩冷凝器氩固化等
上下塔压力背离原因分析
背离的原因有以下几点: ①主冷液位过高,导致主冷底部静压力过高, 液氧的沸点升高,主冷温差减小 ②液氮侧压力换热效果差 a、液氮液位过高,导致氮侧传热系数降低 b、液氮侧不凝气(氦氖气)没有及时排出, 占居换热面积
液 悬
什么是液悬? 简单的讲,液悬就是分馏塔内液体不能从 上往下流动。 液悬的典型现象: ①阻力周期性波动,液悬开始时阻力逐渐增 大,当增加大到一定值时突然下降。 ②塔底液位与阻力同步波动,当阻力上升时 液位下降,然后突然上升。
用R表示 即回流比增加时: a、对于上塔,塔顶氮气纯度上升,塔底氧气纯度 下降; b、对于下塔,塔顶氮气纯度上升,塔底液空纯度 下降。
精馏设备
化工生产中精馏操作一般都在分馏塔里完成, 按照塔的结构可以分为两大类:筛板塔和 填料塔
分馏塔结构
液氮来自下塔
液空来自下塔
空气来自换热器
液空去上塔塔
降液管(也叫 溢流斗)
③液体表面张力 上升蒸汽离开塔板 时必须克服液体表面张 力
进塔空气量增加塔内阻力增加 回流液增加塔内阻力增加
筛板塔和填料塔的优缺点
影响精馏操作的主要因素及精馏节能技术浅析

影响精馏操作的主要因素及精馏节能技术浅析摘要:精馏过程是化工行业耗能最多的工艺之一,影响精馏效果的因素的是多方面的,主要包括分离物的组成和性质、操作工艺(压力和温度、持液量、流量)和设备(塔内件类型、塔径、塔高)等等,笔者结合多年的实践经验,简要分析了影响精馏操作的主要因素,并就降低精馏过程中的能源损耗提出了自己的见解。
关键词:精馏操作因素节能技术浅析精馏过程是化工行业耗能最多的工艺之一,影响精馏效果的因素的是多方面的,主要包括分离物的组成和性质、操作工艺(压力和温度、持液量、流量)和设备(塔内件类型、塔径、塔高)等等,往往一个因素发生变化时,会牵扯到一些其他因素发生变化,如何提高精馏质量和降低精馏过程中的能源损耗一直是人们研究难点和热点,笔者结合多年的实践经验,简要分析了影响精馏操作的主要因素,并就降低精馏过程中的能源损耗提出了自己的见解,供大家参考。
一、精馏塔的分类和原理简介精馏塔又名蒸馏塔,是一种进行蒸馏的气液塔式接触装置,主要有填料塔和板式塔两种类型,根据操作方式的不同又可以分为间隙精馏塔和连续精馏塔。
整个物料变化过程就是气相物质和液相物质相互作用传质的过程,首先气相从塔底进入塔内,与塔内下降的液相接触,气相中难挥发的物质源源不断的向液相转化,与此同时,液相中容易挥发的物质也会转化到气相中去,随着工序的继续,液相物质在塔底积聚,气相物质流向塔顶,逐步实现气液不同相物质成分的分离。
分离出的气相进入冷凝器,液相组分一部分作为蒸馏的液体取出,另一部分作为回流液继续返回塔顶进入蒸馏塔中。
塔底流出的液体,部分送入再沸器加热蒸发成气相,其它的液体作为釜残液取出。
二、精馏操作的主要影响因素分析1.精馏操作压力的影响精馏过程和塔的设计都是基于一定塔压下进行的,保持塔压的稳定对整个精馏效果有很大的影响,当压力出现波动时,将会对如下几个方面产生影响:(1)改变相组的相对挥发度和塔的生产效率。
如果塔内压力突然增大,液相物质的挥发度将下降,此时无法将液体中不同的物质进行蒸馏分离,同时气相的重度也增加,蒸馏效率会大大减低,直接影响生产效率和产品的质量;(2)破坏产品质量和物料平衡;如果操作压力增加,气相组成成分的浓度将明显升高,重量比也变大,应该挥发出去的气相很可能因为压力过大而液化,混入原有的液相物质中,最终达不到蒸馏分离的效果。
- 1、下载文档前请自行甄别文档内容的完整性,平台不提供额外的编辑、内容补充、找答案等附加服务。
- 2、"仅部分预览"的文档,不可在线预览部分如存在完整性等问题,可反馈申请退款(可完整预览的文档不适用该条件!)。
- 3、如文档侵犯您的权益,请联系客服反馈,我们会尽快为您处理(人工客服工作时间:9:00-18:30)。
3 8 lf g c e c r {{ d h m.oi , l
第3 7卷 总第 2 3期 0
反应精馏技术的关键 问题分析
秦建华
( 州工 业职业技 术学 院 ,江 苏 扬 州 2 5 2 ) 扬 2 7 1
[ 摘 要1 反应精馏是为增强反应与精馏效果而将两种单元操作进行耦合的多功能新技术。因既有化学反应又有精馏过程,反应精馏过程需考
d si ai n n h mia i eis wh c a e o t ep e o n n o li e se d .t tsa d c mp e y a c I h r . h x e i n a a d t e rtc 1 it lt 1 d c e c 1 n t . i hh s1d t h h n me o f l o a k c mut ta y sa e n o pl lx d n mi s n t ewo k t ee p rme t l n h o e ia i v sia in f h e c ie d si ai n i e e t e r a eb e y t maia l e iwe , n ek y p o lms ft ea p iai n r h e c ie d s l t nh v n e t t so t er a t i l t nr c n a sh v e n s se t lyr v e d a d t e r b e h p l t sf er a tv it l i a e g o v tl o y c h o c o o t iao b e n lzd e n a a y e Mo e v r ter s a c i c in f r h tr f h e ci ed si ai n tc n l g sp o o e ro e , h e e rh d r t e f u eo te ra t it lt e h oo y wa r p s d e o o t u v l o
21 平衡 级模 型 .
19 年 ,S rl 究稳 态精馏过程时提 出了平衡级模型 。 83 oe 研 平衡 级模型假设离开任何一 级的蒸汽与液体物流达到热力 学 平衡状态 , 且反应只发生在液相 。 反应精馏 的平衡级模型包括 对体系进行 的物料衡 算、相平衡 、摩尔分数归一、焓平衡方程  ̄ME H以及化 学反应动力学方程( ! [ S I R方程) ,但是 动力 学数据 通 过实验或估计较难获得 ,因此有时可通过化学平衡 方程代 替。 对于慢速反应 ,可用化学平衡方程估算反应可能进行的最 大程度 。
Ke w o d : e ci ed si a in; c tl s p c ig c n g rt n ; sm u ai n ra t ed si ai n c lm n d sg y r s r a t it lt v l o a ay t a k n o f u ai s i l t ; e ci it lto o u e in i o o v l
it s ia o ll d o o l t at n ew e a o・ q i q ibim, a o —q i m s t n frit —a ls df s n( r e rg n o s a l e ne ic t n le mpe i e c o s t e n p r iu e ul r n f i wi a t c xn r i b v l d i u v p r iud a s r se, r c t y t iu i f t o e e u l ct y d l a n a a f o oh e y as
反 应 精 馏作 为反 应 和 分离 相 耦 合 的集 成 过 程 , 发 展 和 应 其 用 已成为化学工业的研究热点 。 反应精馏过程需考虑气液相平 衡、气液质量传递、催化剂 内扩散( 非均相催化精馏) 以及化学 反应动力学等 因素之问复杂 的相互作用 , 导致 了反应精馏过程 存在定态 多重性和动力学复杂性 , 在过程设 计和安全放大方面 还面临着较大的挑战。 章系统地综述国内外反应精馏技 术的 文 研究进 展, 分析 目前该技术工业化发展亟待解决 的关键技 术问 题 ,并对未来的发展方向进行展望 。
展 方国进 行了展 望 。 [ 词】 关键 反应精 馏技 术 ;催 化剂 装填 ;模拟 计算 ;反应 精馏塔 设计 【 中图分类 号]E T 【 标识 码 l 文献 A f 编号]0716(000。0 80 文章 10 .852 1)30 3.2
Anay i ft eK e o 来自 si a tv sil to c l sso h yPr blm n Re ci eDitla i n Te hno o y lg
Qi J n u n i ha a ( a gh uP l e h i Istt Y n z o 2 7 C ia Y n z o oy c nc n tue a g h u2 5 , hn ) t i , 1 2
Ab ta t Re ciedsiain( samutu cin 1po eswh r h mia e cina ddsiaino c rs l n o syi igev se. epo e s sr c: a t itlto RD11 lfn t a rc s eec e c 1ra t n itlt cu i t e u l nasn l es1Th rc s v l i o o l o mu a
虑气 液相 平衡 、气 液质量 传递 、催 化剂 内扩散 ( 非均相反 应精 馏) 以及动 力学等 因素 的相 互作 用 ,导致 该过程 存在 定态 多重性 、动 力学复 杂性 。文 章 系统地 综述 了近 年来 国陡外科 研 工作者 对反 应精 馏实验 和理 论 的研究进 展 ,分析 了反 应精馏 技术 工业 应用 中存在 的 关键 问题 ,并 对未 来的 发