转炉炼钢煤气回收系统的分析
转炉煤气回收工艺简述

转炉煤气回收工艺简述伴随冶炼能力提升和技术发展,煤气从冶炼副产品变成富产品。
因为在过程所产生炉气中含量有大量一氧化碳,经过对炉气搜集、储存,又将这些一氧化碳作为燃气应用于生产之中。
高炉炼铁生产出铁水中有大量碳,当转炉温度>1700℃时,有大量碳被氧化,生成一氧化碳和二氧化碳,每一吨铁水可产生100m3一氧化碳,因为设备、技术等方面原因,只有60%-80%一氧化碳被回收。
在转炉炼钢前5分钟里,因为顶吹氧,大量纯氧气和高温铁水接触,在高温和充足氧气情况下,铁水中硅和氧气反应,燃烧生成氧化硅,这个反应有两个作用:一、铁水中大部分硅被氧化,生成钢渣脱离铁水。
二、硅燃烧放出大量热,提升了铁水温度。
(在这5分钟里所产生气体,不能回收)铁水温度升高后,氧气和碳反应生成一氧气化碳和二氧化碳,因为烟道几乎是密封,一氧化碳不会和外界氧气发生反应,所以烟道内一氧化碳保持它原状,铁水液面上气体温度可达成1700多度,高温气体进入一文,二文,然后进入旋流塔,在旋流塔中,高温气体上升,旋流塔上方有转炉浊环水向下喷淋,和煤气中灰尘凝结下落,达成洗涤煤气目标,同时使气体温度下降,40度气体进入一次除尘风机,对于进入一次除尘风机煤气,是用往返收还是放散,在线分析仪能够在一秒钟之内分析出结果,假如当初一氧化碳含量大于等于25%,且氧含量小于2%,那么就可回收,此时PLC自动控制打开旋转水封阀门,再打开三通阀(此时放散阀门被关闭)同时通往煤气柜阀门打开,开始回收煤气。
出了旋转水封煤气顺着管道进入预防回气水封(这里有四道,在正常回收情况下,为了减小对煤气阻力,这个水封没有水,当检修时,为了预防煤气柜内煤气回返,在水封里面注入适量水)再进入防沉降水封,(防沉降水封作用相当于膨胀节,起到管道伸缩作用,在管道变形时,相互不影响,不至于拉裂管道。
)当煤气进入煤气柜后,临时在里面存放,煤气柜容量大小决定了气柜内气体存留时间。
“断续回收,连续使用”是煤气回收基础状态。
转炉煤气回收工艺

转炉煤气回收工艺转炉煤气回收工艺是一种重要的环保技术,可以大量减少工业生产过程中的废气排放,这对于保护环境、减少污染、节约能源具有非常重要的意义。
转炉煤气回收工艺是将高温炼钢废气中的一部分可燃气体重新利用,使其燃烧后产生的热能可以继续用于炼钢工艺中。
这种自给自足的方式在钢铁行业中具有显著的优势,因为钢铁生产需要大量的热能来保持高温状态。
在传统的炼钢工艺中,高温炼钢废气中的大部分热能和可燃气体都是被浪费掉了,直接排放到大气中造成了严重的环境污染。
而采用转炉煤气回收工艺后,这些废气中的可燃气体可以被有效回收利用,从而达到节约能源、减少排放的目的。
转炉煤气回收工艺主要分为两个步骤:收集和利用。
首先,需要在炉膛的废气口处设置一个废气管道,将所有的高温炼钢废气收集起来。
在这个过程中,应该对废气管道进行良好的密封,避免废气的泄漏和外泄,从而确保废气能够稳定地流向后续的工艺流程中。
其次,将收集到的废气送入热风炉或燃烧炉中进行燃烧利用,将废气中的可燃气体转换成热能。
这个过程需要使用一些特殊的设备来控制废气的流量、温度和压力等参数,以确保废气燃烧的效果达到最佳状态。
通过这样的转炉煤气回收工艺,可以大大提高炼钢过程中的能效,降低工业生产过程中的废气排放,从而达到环保减排的目的。
不仅如此,这种技术还可以大幅降低企业的用能成本,减少经营成本,提高企业的经济效益,具有非常积极的社会和经济意义。
总之,转炉煤气回收工艺是一项非常重要的绿色技术,可以促进钢铁产业的可持续发展,实现环保减排、节约能源的目标。
随着环保意识的提高和技术的不断进步,相信这种技术在未来的发展中将会得到更广泛的应用和推广。
转炉煤气的回收与利用

转炉煤气的回收与利用1,转炉煤气的特性;1.转炉煤气是一种无色、无味的有毒气体,发热量为7117.56~8373.64千焦/m,燃点为600~700℃,密度为1.25~1.29㎏/nm⒊煤气中含有50﹪以上的一氧化碳,若发生泄露极易造成人员中毒。
转炉煤气与空气在有限空间内,混合成一定比例后,遇到明火或高温就会发生爆炸。
其在空气中爆炸极限为12.5%~75%。
2. 转炉煤气的三大特性为:易中毒﹑易着火﹑易爆炸。
另外,转炉煤气还具有腐蚀性﹝生成硫酸、碳酸﹞、与尘毒危害等特性。
2,转炉煤气系统使用现状;在采用吹氧冶炼的氧气转炉炼钢过程中,其烟气量、烟气成分和烟气温度随冶炼阶段呈周期性变化。
烟尘中金属铁约占13%,Fe0约占68.4%,特别在吹炼中期CO体积分离高达80%以上,一般情况下,转炉煤气成分中CO的体积分数约达 55%~66%,当CO在60%左右是,其热度可达8MJ/m3,而每吨钢烟尘量一般为10~20㎏∕t。
由此可见,转炉煤气中CO 含量很高,烟尘中铁含量也很高,具有很高的回收利用价值。
1.国内外概况和发展趋势;随着氧气转炉炼钢生产的发展,炼钢工艺的日趋完善,相应的除尘技术也在不断的发展完善。
目前,氧气转炉炼钢的净化回收主要有2种方法,一种是煤气湿法﹙OG法﹚净化回收系统,一种是煤气干法﹙LT法﹚净化回收系统。
日本新日铁和川崎公司于上世纪60年代联合开发研制成功OG法转炉煤气净化回收技术。
OG法系统主要由烟气、冷却、净化、煤气回收和污水处理等部分组成。
其烟气经冷却烟道进入烟气净化系统,烟气净化系统包括2级文氏管、脱水器和水雾分离器,烟气经喷水处理后,除去烟气中的烟尘,带烟尘的污水经分离、浓缩、脱水等处理,污泥送烧结厂作为烧结原料,净化后的煤气被回收利用。
系统全过程采用湿法处理,该技术存在的缺点:一是处理后的煤气含尘量较高,达100㎎/m3以上,要利用此煤气,需在后部设置湿法电除尘器进行精除尘,将其含尘质量浓度降至10㎎/m3 以下;二是系统存在二次污染,其污水需进行处理;三是系统阻损达,所以能耗大,占地面积大,环保治理及管理难度较大。
转炉炼钢煤气回收

“LT”法系统主要是由蒸发冷却塔、静电除尘器、除尘风机、切换站、煤气冷却器等几部分组成。 转炉1500℃的高温烟气经汽化冷却烟道冷却至800~1000℃后,然后进入烟气净化系统。烟气净化系统
由蒸发冷却塔和圆筒型静电除尘器组成,烟气温度通过蒸发冷却器后降至170~200℃,同时通过调质处理, 降低了烟尘的电阻率,收集了粗粉尘。烟气经过这一初步处理后,进入圆筒型静电除尘器,进行进一步净 化,使其含尘质量浓度降至15mg/m3以下,从而达到最佳的除尘效率。
2.2 主要设备及工作原理
汽化冷却烟道:
转炉汽化烟道(也称为余 热锅炉)是转炉炼钢的主要配 套设备之一,该设备在工作时 要最大限度地收集高温烟气, 高温烟气的温度在1400摄氏度1600摄氏度,这些烟气在循环 泵产生的负压作用下,在汽化 烟道内流通,带有火星未燃烧 尽的钢渣进入燃烧室,之后烟 道内的温度在800摄氏度左右, 然后烟气随着烟道出口进入蒸 发冷却塔。
莱钢从2002年底开始酝酿转炉采用干法除尘技术。2003年完成施工图设计和控制系统的软件编程。 2004年7月建成投产, 对3*120t转炉使用了干法除尘,而投产后10天就达到设计能力,并持续稳定地生产。 至今三套“LT”系统均已通过了考核验收。
2) 缺点: (1)系统复杂,从而要求设备、仪表仪器质量高,以满足生 产要求;对施工质量要求也高; (2)要求管理和操作水平高,必须对管理和操作人员进行较 完善的培训,并在实际生产中达到熟练操作和维护;并且要 与炼钢工艺操作紧密配合和协调,杜绝野蛮操作; (3)一次投资高。
“OG”法工艺系统缺点:
由于该系统全过程采用湿法处理,技术存在以下几个缺点: 一是处理后的煤气含尘量较高,高达100mg/m3,要利用此煤气,需进一步净化方能使用; 二是系统存在二次污染,其污水需进行处理; 三是系统阻损大,所以能耗大,占地面积大,环保治理及管理难度较大。
转炉负能炼钢与煤气回收技术范本(2篇)

转炉负能炼钢与煤气回收技术范本炼钢是钢铁生产过程中的关键环节,炼钢负能是指在炼钢过程中产生的废热和废气。
钢铁行业是我国重要的工业部门,但同时也是主要的能源消耗和环境污染源之一。
为了实现钢铁行业的可持续发展,转炉炼钢过程中的废热和废气应得到充分利用和净化。
炼钢转炉是目前钢铁生产中常用的设备之一。
转炉炼钢是利用转炉炉膛中高温燃烧的氧气与铁水进行反应,将铁水中的杂质氧化脱除,从而得到高质量的钢水的一种冶炼方法。
然而,在转炉炼钢过程中,产生了大量的废热和废气,如果不能有效利用和处理,将造成能源的浪费和环境的污染。
炼钢转炉废热的回收利用是一种有效的能源回收利用方式。
转炉炉膛中废气含有大量的热能,通过炉膛的余热锅炉回收废气中的热能,可以用来产生蒸汽或热水,用于工业生产或供暖。
此外,转炉炉膛中的废气中还含有一定浓度的炉尘和有害物质,需要通过除尘器等设备进行净化处理,以减少对大气环境的不良影响。
炼钢转炉煤气回收技术是一种节能减排的重要手段。
在转炉炼钢过程中,炉膛中需要加入大量的燃料,其中包括煤炭。
煤炭的燃烧产生了大量的废气,其中含有大量的热能和有害物质。
通过合理设计煤气回收系统,可以回收废气中的热能,并通过余热锅炉产生蒸汽或热水。
同时,废气中的有害物质也需要通过除尘器等设备进行净化处理,以保护环境和人类健康。
转炉负能炼钢与煤气回收技术的范本是针对以上问题提出的一种解决方案的指导性文件。
以下是其中一些关键技术的范本介绍:1. 转炉废热回收技术范本:转炉炉膛中的废气通过余热锅炉回收技术进行能源回收。
关键技术包括: 余热锅炉的合理设计和选型、废气预处理和净化技术、余热锅炉运行的控制和优化等。
2. 转炉煤气回收技术范本:煤气回收系统设计的关键技术包括: 废气净化和除尘技术、废气热能回收技术、余热锅炉的选型和运行控制等。
融化煤气的回收利用是其中的重要环节之一,其关键技术包括: 融化煤气的净化和回收、融化煤气的利用方式和设备的设计等。
转炉负能炼钢与煤气回收技术
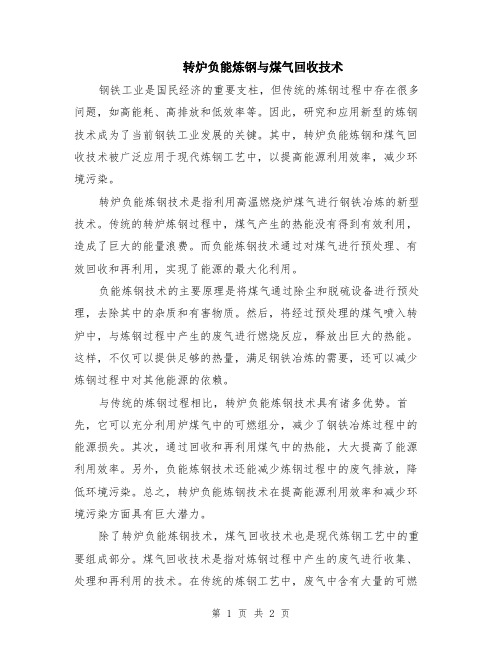
转炉负能炼钢与煤气回收技术钢铁工业是国民经济的重要支柱,但传统的炼钢过程中存在很多问题,如高能耗、高排放和低效率等。
因此,研究和应用新型的炼钢技术成为了当前钢铁工业发展的关键。
其中,转炉负能炼钢和煤气回收技术被广泛应用于现代炼钢工艺中,以提高能源利用效率,减少环境污染。
转炉负能炼钢技术是指利用高温燃烧炉煤气进行钢铁冶炼的新型技术。
传统的转炉炼钢过程中,煤气产生的热能没有得到有效利用,造成了巨大的能量浪费。
而负能炼钢技术通过对煤气进行预处理、有效回收和再利用,实现了能源的最大化利用。
负能炼钢技术的主要原理是将煤气通过除尘和脱硫设备进行预处理,去除其中的杂质和有害物质。
然后,将经过预处理的煤气喷入转炉中,与炼钢过程中产生的废气进行燃烧反应,释放出巨大的热能。
这样,不仅可以提供足够的热量,满足钢铁冶炼的需要,还可以减少炼钢过程中对其他能源的依赖。
与传统的炼钢过程相比,转炉负能炼钢技术具有诸多优势。
首先,它可以充分利用炉煤气中的可燃组分,减少了钢铁冶炼过程中的能源损失。
其次,通过回收和再利用煤气中的热能,大大提高了能源利用效率。
另外,负能炼钢技术还能减少炼钢过程中的废气排放,降低环境污染。
总之,转炉负能炼钢技术在提高能源利用效率和减少环境污染方面具有巨大潜力。
除了转炉负能炼钢技术,煤气回收技术也是现代炼钢工艺中的重要组成部分。
煤气回收技术是指对炼钢过程中产生的废气进行收集、处理和再利用的技术。
在传统的炼钢工艺中,废气中含有大量的可燃物质和热能,没有得到有效利用。
而煤气回收技术通过对废气的处理,可以使其达到清洁排放标准,并回收其中的可燃物质和热能。
煤气回收技术的主要原理是通过收集废气,并进行除尘、脱硫等处理,使之达到环保要求。
然后,将处理后的废气中的可燃物质和热能回收利用,提供给炼钢过程中的各项能源需求。
这样,不仅可以减少对其他能源的依赖,还可以减少废气排放,保护环境。
煤气回收技术的应用对钢铁工业的可持续发展具有重要意义。
转炉炼钢煤气回收系统的分析

、
煤气回收系统流程 图 二 、气体分析仪 的作用 三、回收阀组 系统作用 气 体分析在整个煤气 回收系统 中是不可缺少的设备之 一, 回收阀组包 括旁通 阀、三通阀、水封 阀三部分组成 , 在 对
通 过对转炉烟气 的气体分析可 以对其 中的 C 0含量进行检 查, 达 到用户使用标准 , 同时对氧气 的检测可 以使得煤气 能够 安全 使 用。 根 据炼钢工 艺过程 中的检测 , 在氧气含量达到爆 炸极限 范围以下时煤气含量完全 能够符合用户使用标准( 除特 殊情 况 以外,如分析仪检 测出现异 常或工 艺条件改变等 ) ,故氧 气分 析仪是炼钢 煤气 回收气体检测 中的重 中之重 。 当前煤气 回收系统 中氧气分 析仪检测 的设 备主要有取 样 分析和 在线分析 仪两种 。 取样分析仪具有一定 的滞后情况,逐 渐 退出炼钢 煤气 回收检测 的舞 台; 而在线激光分析仪具有相应 时间短 , 分析准确 ,便于维护等特 点,得到广大用户的积极相 应 ,逐渐 占领了气体 分析 的舞 台。 在当前运用 的主要以激光 吸收光谱 ( D L A S ) 技术为主 ,利 用激光能量被气 体分子 “ 选 频” 吸收光谱 的原理来测量气体浓 度 ,由半导体激光器发射出特 定波长的激光 束 ( 仅能被被测气 体吸收) ,穿过被测气体 时,激强度 的衰减与被测气体 的浓度 成一定 的函数关 系 , 因此。 通过测量激光强度衰 L A S ) 技术 利用 激光 能量 被气体分 子“ 选频 ”吸收光谱的原理来测量气体浓度,由半导体激光器
消费 电子
2 0 1 3 年 7月下
C o n s u me r E l e c t r o n i c s Ma g a z i n e 技 术 交 流
转炉炼钢煤气回收系统的分析
转炉负能炼钢与煤气回收技术

转炉负能炼钢与煤气回收技术是一种利用工厂废气中的高温高压煤气进行能源回收的技术。
在传统的转炉炼钢过程中,大量的煤气会产生,并直接排放到大气中,造成能源的巨大浪费和环境的污染。
而通过对煤气进行回收利用,不仅可以减轻环境负荷,还能够降低能源成本,提高能源利用效率。
本文将介绍转炉负能炼钢与煤气回收技术的原理、应用以及存在的问题和挑战。
转炉负能炼钢是一种常用的炼钢工艺,其核心原理是利用煤气在高温高压条件下与炉料中的矿石和还原剂发生燃烧和反应,从而使炉料中的铁和矿石还原成金属铁。
在传统的转炉负能炼钢过程中,煤气是燃烧掉的,只产生热能,而通过煤气回收技术,煤气中的能源可以被有效利用。
煤气中的主要组分是一氧化碳、氢气、甲烷等可燃气体,其热值很高,可以用来发电、供热等方面。
煤气回收技术主要包括废气再利用和废气发电两种方式。
废气再利用是指将煤气作为热源加热转炉内的炉料,提高炉料的温度,加快冶炼过程。
废气发电是指将煤气中的能源转化成电能,通过发电机向企业供电或者并入电网,以实现能源的再利用。
无论是废气再利用还是废气发电,都能够有效减少转炉负能炼钢过程中的能源消耗,提高能源利用效率。
转炉负能炼钢与煤气回收技术在钢铁工业中得到了广泛的应用。
以国内一些大型钢铁企业为例,很多企业在进行转炉炼钢过程中都引进了煤气回收技术。
通过煤气发电,这些企业可以降低电力采购成本,提高能源利用效率;同时,由于燃烧过程中产生的废气不再排放到大气中,大大减少了对环境的污染。
然而,转炉负能炼钢与煤气回收技术也存在一些问题和挑战。
首先,煤气回收技术需要有先进的设备和技术支持,对企业的投入较大,对一些小型钢铁企业而言可能难以承担。
其次,煤气回收技术在实施过程中需要解决一些技术难题,如煤气的净化和处理问题,燃烧稳定性问题等。
此外,由于煤气回收技术的广泛应用,也会带来新的环境问题,如废气的排放标准和处理问题等。
总之,转炉负能炼钢与煤气回收技术是一项具有巨大潜力和发展前景的科技成果。
炼钢厂转炉煤气回收存在问题的解决方案
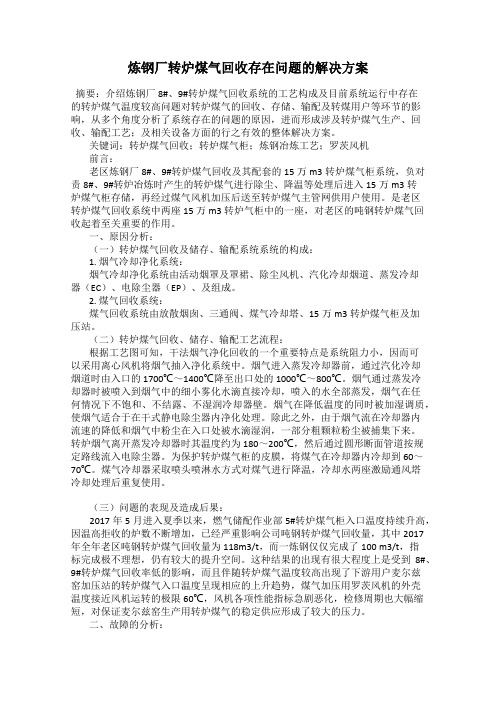
炼钢厂转炉煤气回收存在问题的解决方案摘要:介绍炼钢厂8#、9#转炉煤气回收系统的工艺构成及目前系统运行中存在的转炉煤气温度较高问题对转炉煤气的回收、存储、输配及转煤用户等环节的影响,从多个角度分析了系统存在的问题的原因,进而形成涉及转炉煤气生产、回收、输配工艺;及相关设备方面的行之有效的整体解决方案。
关键词:转炉煤气回收;转炉煤气柜;炼钢冶炼工艺;罗茨风机前言:老区炼钢厂8#、9#转炉煤气回收及其配套的15万m3转炉煤气柜系统,负对责8#、9#转炉冶炼时产生的转炉煤气进行除尘、降温等处理后进入15万m3转炉煤气柜存储,再经过煤气风机加压后送至转炉煤气主管网供用户使用。
是老区转炉煤气回收系统中两座15万m3 转炉气柜中的一座,对老区的吨钢转炉煤气回收起着至关重要的作用。
一、原因分析:(一)转炉煤气回收及储存、输配系统系统的构成:1. 烟气冷却净化系统:烟气冷却净化系统由活动烟罩及罩裙、除尘风机、汽化冷却烟道、蒸发冷却器(EC)、电除尘器(EP)、及组成。
2. 煤气回收系统:煤气回收系统由放散烟囱、三通阀、煤气冷却塔、15万m3转炉煤气柜及加压站。
(二)转炉煤气回收、储存、输配工艺流程:根据工艺图可知,干法烟气净化回收的一个重要特点是系统阻力小,因而可以采用离心风机将烟气抽入净化系统中。
烟气进入蒸发冷却器前,通过汽化冷却烟道时由入口的 1700℃~1400℃降至出口处的 1000℃~800℃。
烟气通过蒸发冷却器时被喷入到烟气中的细小雾化水滴直接冷却,喷入的水全部蒸发,烟气在任何情况下不饱和、不结露、不湿润冷却器壁。
烟气在降低温度的同时被加湿调质,使烟气适合于在干式静电除尘器内净化处理。
除此之外,由于烟气流在冷却器内流速的降低和烟气中粉尘在入口处被水滴湿润,一部分粗颗粒粉尘被捕集下来。
转炉烟气离开蒸发冷却器时其温度约为 180~200℃,然后通过圆形断面管道按规定路线流入电除尘器。
为保护转炉煤气柜的皮膜,将煤气在冷却器内冷却到 60~70℃。
浅析转炉煤气回收的影响因素及提高措施
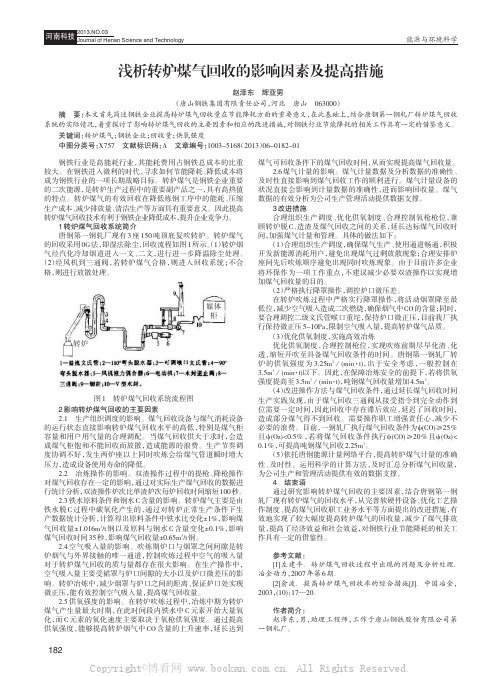
钢铁行业是高能耗行业,其能耗费用占钢铁总成本的比重较大。
在钢铁进入微利的时代,寻求如何节能降耗、降低成本将成为钢铁行业的一项长期战略目标。
转炉煤气是钢铁企业重要的二次能源,是转炉生产过程中的重要副产品之一,具有高热值的特点。
转炉煤气的有效回收在降低炼钢工序中的能耗、压缩生产成本、减少排放量、清洁生产等方面具有重要意义。
因此提高转炉煤气回收技术有利于钢铁企业降低成本,提升企业竞争力。
1转炉煤气回收系统简介唐钢第一钢轧厂现有3座150吨顶底复吹转炉。
转炉煤气的回收采用0G法,即湿法除尘,回收流程如图1所示。
(1)转炉烟气经汽化冷却烟道进入一文、二文,进行进一步降温除尘处理。
(2)经风机到三通阀,若转炉煤气合格,则进入回收系统;不合格,则进行放散处理。
2影响转炉煤气回收的主要因素2.1生产组织调度的影响。
煤气回收设备与煤气消耗设备的运行状态直接影响转炉煤气回收水平的高低,特别是煤气柜容量和用户用气量的合理调配。
当煤气回收供大于求时,会造成煤气柜饱和不能回收而放散,造成能源的浪费。
生产节奏调度协调不好,发生两炉座以上同时吹炼会给煤气管道瞬时增大压力,造成设备使用寿命的降低。
2.2冶炼操作的影响。
双渣操作过程中的提枪、降枪操作对煤气回收存在一定的影响,通过对实际生产煤气回收的数据进行统计分析,双渣操作炉次比单渣炉次每炉回收时间缩短100秒。
2.3铁水原料条件和钢水C含量的影响。
转炉煤气主要是由铁水脱C过程中碳氧化产生的,通过对转炉正常生产条件下生产数据统计分析,计算得出原料条件中铁水比变化±1%,影响煤气回收量±1.016m3/t钢以及原料与钢水C含量变化±0.1%,影响煤气回收时间35秒,影响煤气回收量±0.65m3/t钢。
2.4空气吸入量的影响。
吹炼期炉口与烟罩之间间隙是转炉烟气与外界接触的唯一通道,控制吹炼过程中空气的吸入量对于转炉煤气回收的质与量都存在很大影响。
转炉干法除尘工艺中煤气回收的分析与研究
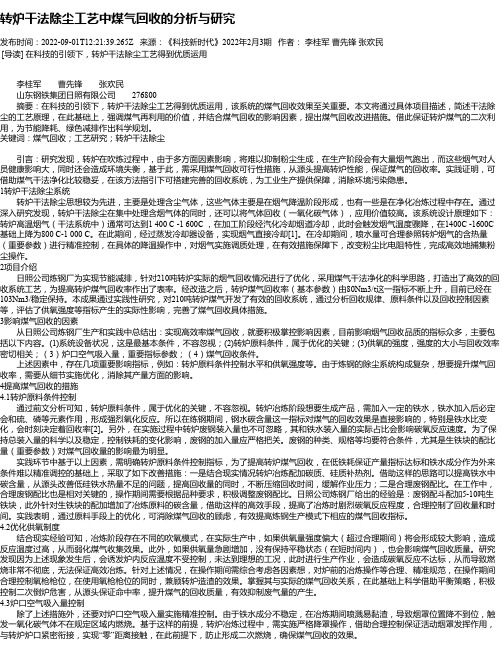
转炉干法除尘工艺中煤气回收的分析与研究发布时间:2022-09-01T12:21:39.265Z 来源:《科技新时代》2022年2月3期作者:李桂军曹先锋张欢民[导读] 在科技的引领下,转炉干法除尘工艺得到优质运用李桂军曹先锋张欢民山东钢铁集团日照有限公司 276800摘要:在科技的引领下,转炉干法除尘工艺得到优质运用,该系统的煤气回收效果至关重要。
本文将通过具体项目描述,简述干法除尘的工艺原理,在此基础上,强调煤气再利用的价值,并结合煤气回收的影响因素,提出煤气回收改进措施。
借此保证转炉煤气的二次利用,为节能降耗、绿色减排作出科学规划。
关键词:煤气回收;工艺研究;转炉干法除尘引言:研究发现,转炉在吹炼过程中,由于多方面因素影响,将难以抑制粉尘生成,在生产阶段会有大量烟气跑出,而这些烟气对人员健康影响大,同时还会造成环境失衡,基于此,需采用煤气回收可行性措施,从源头提高转炉性能,保证煤气的回收率。
实践证明,可借助煤气干法净化比较稳妥,在该方法指引下可搭建完善的回收系统,为工业生产提供保障,消除环境污染隐患。
1转炉干法除尘系统转炉干法除尘思想较为先进,主要是处理含尘气体,这些气体主要是在烟气降温阶段形成,也有一些是在净化冶炼过程中存在。
通过深入研究发现,转炉干法除尘在集中处理含烟气体的同时,还可以将气体回收(一氧化碳气体),应用价值较高。
该系统设计原理如下:转炉高温烟气(干法系统中)通常可达到1 400 C -1 600C ,在加工阶段经汽化冷却烟道冷却,此时会触发烟气温度骤降,在1400C -1600C 基础上降为800 C-1 000 C。
在此期间,经过蒸发冷却器设备,实现烟气直接冷却[1]。
在冷却期间,喷水量可合理参照转炉烟气的含热量(重要参数)进行精准控制,在具体的降温操作中,对烟气实施调质处理,在有效措施保障下,改变粉尘比电阻特性,完成高效地捕集粉尘操作。
2项目介绍日照公司炼钢厂为实现节能减排,针对210吨转炉实际的烟气回收情况进行了优化,采用煤气干法净化的科学思路,打造出了高效的回收系统工艺,为提高转炉煤气回收率作出了表率。
转炉煤气回收和利用技术分析

转炉煤气回收和利用技术分析1. 引言1.1 研究背景煤气回收技术是针对转炉生产过程中排放的煤气进行有效处理和利用的一项重要技术。
煤气含有大量的一氧化碳、烃类物质和其他有害物质,如果排放到大气中会造成严重的环境污染和资源浪费。
研究和推广转炉煤气回收技术具有重要的现实意义。
随着我国钢铁行业的快速发展,煤气回收技术不断得到推广和应用。
在实际生产中,仍然存在技术不成熟、设备老化、能源利用率低等问题。
深入研究转炉煤气回收技术,提高其技术水平和应用范围,对于促进钢铁行业的可持续发展具有重要意义。
在此背景下,本文旨在对转炉煤气回收和利用技术进行深入分析,探讨其发展历程、分类、应用和优势,为进一步推动煤气回收技术的研究和应用提供参考和借鉴。
通过展望转炉煤气回收技术的前景,挑战和发展建议,为我国钢铁行业的绿色发展贡献力量。
1.2 研究目的研究目的是为了深入探讨转炉煤气回收和利用技术,分析其在钢铁生产过程中的应用情况及潜在优势,进一步推动煤气回收技术在工业领域的发展和应用。
通过系统研究转炉煤气回收技术的概念、历程、分类和应用,可以更全面地了解该技术在减少污染排放、提高资源利用率等方面的作用和价值,为工业生产的可持续发展提供技术支持和理论指导。
通过对转炉煤气回收技术的优势、挑战和前景展望的分析,可以为相关部门和企业制定科学的技术发展战略,提高工业生产的环保水平和经济效益,促进绿色低碳发展。
研究的目的是为了促进转炉煤气回收和利用技术的推广应用,推动工业生产的绿色转型,实现资源循环利用和环境可持续性发展的目标。
1.3 研究意义转炉煤气回收和利用技术的研究意义主要体现在以下几个方面:转炉煤气回收和利用技术是实现资源循环利用和节能减排的重要途径之一。
煤炭是世界上重要的能源资源,而煤气是其中一种重要的副产品。
通过有效的转炉煤气回收和利用技术,可以最大限度地利用煤气资源,减少能源浪费,降低生产成本,实现资源的再生利用。
转炉煤气回收和利用技术对环境保护具有重要意义。
转炉煤气干法净化回收系统

★拨叉振打仿真视频
★拨叉振打现场视频
六、关键技术及创新点
六、关键技术及创新点
六、关键技术及创新点
六、关键技术及创新点
七、系统性能保证
主要指标 煤气回收值 排放指标 排放指标
指标值 铁水冶炼不低于90m3/h(标) 回收煤气含尘浓度≤10mg/m3(标) 放散煤气含尘浓度≤15mg/m3(标)
回收煤气温度指标
≤70℃
八、经典工程实例
莱钢3座120吨转炉工程
太钢2座180吨转炉工程
八、经典工程实例
天铁2座190吨转炉工程
邯钢2座250吨转炉工程
八、经典工程实例
江阴兴澄2座150吨转炉工程
首钢迁安2座210吨转炉工程
八、经典工程实例
的目的,灰尘聚积在蒸发冷却器底部,由链式输送机送至贮灰仓。
三、系统关键设备及功能(电除尘器)
转炉煤气干法电除尘器是整个转炉煤气干法回收与净化系统中最为关键的
设备之一,也是所有电除尘器当中结构最为复杂的,对设计,制造和安装的要求 很高,转炉生产所产生的烟气中含有大量的煤气,为了使电除尘器内烟气具有较 好的空气动力学特性,避免在除尘器内形成煤气和空气的可燃性混合气体,必须 要防止电除尘器内产生回流和死区,最佳的流动方式是以塞状流动通过电除尘器 内部,基于上述观点,将电除尘器断面设计成圆筒型是最理想的,其主要结构及 特点如下: 电除尘器断面为圆形,因此也称为“圆筒型电除尘器”,有良好的动力学特性。 圆形壳体耐压能力达0.3MPa 壳体上安装有减压泄爆装置(泄爆阀),有效保证了除尘系统的安全运行
三、系统关键设备及功能(蒸发冷却器)
蒸发冷却器位于汽化冷却烟道下游,主要用于 烟气降温,烟气调质和预除尘。 主要由冷却器本体,喷雾系统,温度检测系统, 粗灰捕集系统四个系统组成。
浅谈转炉煤气的回收与利用
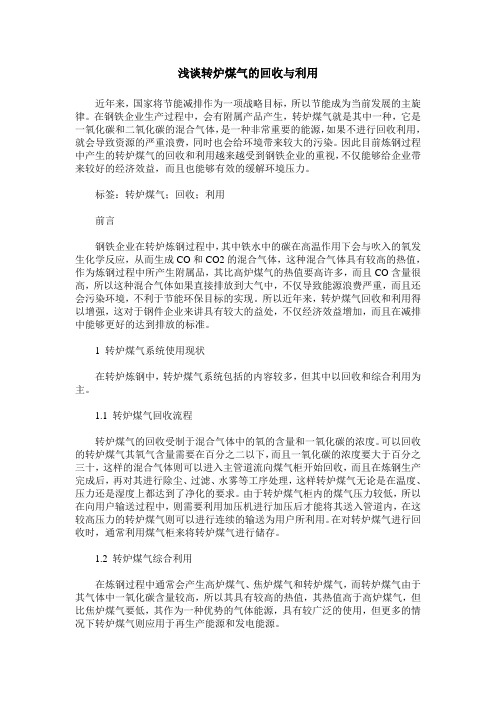
浅谈转炉煤气的回收与利用近年来,国家将节能减排作为一项战略目标,所以节能成为当前发展的主旋律。
在钢铁企业生产过程中,会有附属产品产生,转炉煤气就是其中一种,它是一氧化碳和二氧化碳的混合气体,是一种非常重要的能源,如果不进行回收利用,就会导致资源的严重浪费,同时也会给环境带来较大的污染。
因此目前炼钢过程中产生的转炉煤气的回收和利用越来越受到钢铁企业的重视,不仅能够给企业带来较好的经济效益,而且也能够有效的缓解环境压力。
标签:转炉煤气;回收;利用前言钢铁企业在转炉炼钢过程中,其中铁水中的碳在高温作用下会与吹入的氧发生化学反应,从而生成CO和CO2的混合气体,这种混合气体具有较高的热值,作为炼钢过程中所产生附属品,其比高炉煤气的热值要高许多,而且CO含量很高,所以这种混合气体如果直接排放到大气中,不仅导致能源浪费严重,而且还会污染环境,不利于节能环保目标的实现。
所以近年来,转炉煤气回收和利用得以增强,这对于钢件企业来讲具有较大的益处,不仅经济效益增加,而且在减排中能够更好的达到排放的标准。
1 转炉煤气系统使用现状在转炉炼钢中,转炉煤气系统包括的内容较多,但其中以回收和综合利用为主。
1.1 转炉煤气回收流程转炉煤气的回收受制于混合气体中的氧的含量和一氧化碳的浓度。
可以回收的转炉煤气其氧气含量需要在百分之二以下,而且一氧化碳的浓度要大于百分之三十,这样的混合气体则可以进入主管道流向煤气柜开始回收,而且在炼钢生产完成后,再对其进行除尘、过滤、水雾等工序处理,这样转炉煤气无论是在温度、压力还是湿度上都达到了净化的要求。
由于转炉煤气柜内的煤气压力较低,所以在向用户输送过程中,则需要利用加压机进行加压后才能将其送入管道内,在这较高压力的转炉煤气则可以进行连续的输送为用户所利用。
在对转炉煤气进行回收时,通常利用煤气柜来将转炉煤气进行储存。
1.2 转炉煤气综合利用在炼钢过程中通常会产生高炉煤气、焦炉煤气和转炉煤气,而转炉煤气由于其气体中一氧化碳含量较高,所以其具有较高的热值,其热值高于高炉煤气,但比焦炉煤气要低,其作为一种优势的气体能源,具有较广泛的使用,但更多的情况下转炉煤气则应用于再生产能源和发电能源。
转炉煤气高效回收利用技术

转炉煤气高效回收利用技术一、所属行业:钢铁行业二、技术名称:转炉煤气高效回收利用技术三、适用范围:大中小型转炉炼钢企业四、技术内容: 1.技术原理采用电除尘净化转炉运转时的热烟气,并回收煤气,收集的除尘灰,进行热压块后又回到转炉中,作为转炉的冷却剂。
转炉煤气干法烟气除尘处理、煤气回收及可以部分或全部补偿转炉炼钢过程中的能耗。
主要特点是:采用LT干法电除尘净化和除尘灰热压块技术,不消耗水资源,同时降低了除尘风机的电力消耗,除尘灰经热压块后返回转炉用于炼钢,利用流程短且污染物排放少。
结合干法烟气除尘处理将转炉除尘灰回收压块或制成化渣剂(冷固球团) 回用于转炉生产,可提高转炉的产量1%~2%,转炉炼钢指标得到显著改善,煤气及外排烟气粉尘小于10mg/Nm3。
2.关键技术1)蒸发冷却器系统主要技术之一是蒸发冷却器,它精确要求通过雾状喷水直接冷却烟气,并根据烟气含热量精确调节喷水量,所喷的水完全变成蒸汽。
2)圆筒型电除尘器系统3)ID-Fan子午加速轴流风机4)切换站和煤气冷却器5)放散烟囱6)控制系统3.工艺流程见下图所示。
20五、主要技术经济指标: 1)烟气含尘量可以达到≤10mg/m 3;2)煤气含尘浓度低,一般在10mg/m 3以下; 3)吨钢耗电量为6.2kWh/t 。
六、 技术应用情况: 1994年,我国宝钢二炼钢最先引进LT 法回收技术。
此后,山东莱芜钢铁公司、包钢二炼钢等转炉先后也采用了该技术。
七、典型用户及投资效益:包钢薄板坯连铸连轧厂,将现有2×210t 转炉改造为干法除尘系统。
干法除尘运行后,水耗降低了60%,吨钢电耗降低了9kW·h ,平均吨钢多回收煤气多20 m 3 左右,转炉煤气回收处于稳定状态,煤气的热值保证在1800大卡左右,每期的回收量均在18000m 3以上,最大可达到28000m 3,煤气中CO 的含量最大可达到85%,回收煤气的含尘量只有0.2mg/m 3,远低于标准的10 mg/m 3。
转炉负能炼钢与煤气回收技术(三篇)
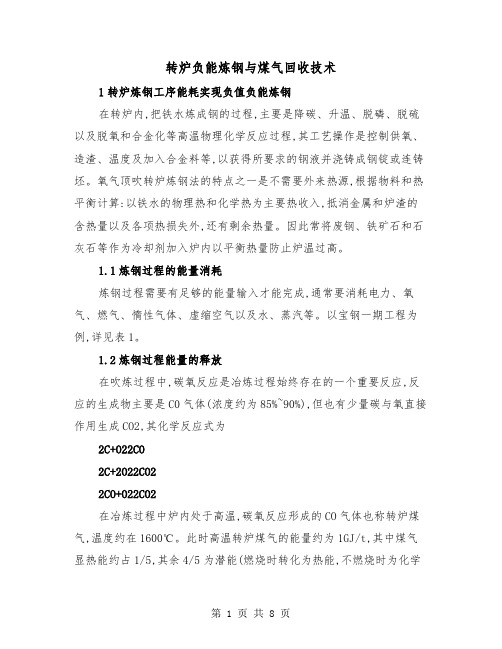
转炉负能炼钢与煤气回收技术1转炉炼钢工序能耗实现负值负能炼钢在转炉内,把铁水炼成钢的过程,主要是降碳、升温、脱磷、脱硫以及脱氧和合金化等高温物理化学反应过程,其工艺操作是控制供氧、造渣、温度及加入合金料等,以获得所要求的钢液并浇铸成钢锭或连铸坯。
氧气顶吹转炉炼钢法的特点之一是不需要外来热源,根据物料和热平衡计算:以铁水的物理热和化学热为主要热收入,抵消金属和炉渣的含热量以及各项热损失外,还有剩余热量。
因此常将废钢、铁矿石和石灰石等作为冷却剂加入炉内以平衡热量防止炉温过高。
1.1炼钢过程的能量消耗炼钢过程需要有足够的能量输入才能完成,通常要消耗电力、氧气、燃气、惰性气体、虚缩空气以及水、蒸汽等。
以宝钢一期工程为例,详见表1。
1.2炼钢过程能量的释放在吹炼过程中,碳氧反应是冶炼过程始终存在的一个重要反应,反应的生成物主要是C0气体(浓度约为85%~90%),但也有少量碳与氧直接作用生成CO2,其化学反应式为2C+O22CO2C+2O22CO22CO+O22CO2在冶炼过程中炉内处于高温,碳氧反应形成的CO气体也称转炉煤气,温度约在1600℃。
此时高温转炉煤气的能量约为1GJ/t,其中煤气显热能约占1/5,其余4/5为潜能(燃烧时转化为热能,不燃烧时为化学能),这就是转炉冶炼过程中释放出的主要能量。
因此,转炉煤气回收利用是炼钢节能降耗的重要途径。
氧气顶吹转炉炼钢过程自台量平衡见图1。
1.3炼钢工序能耗实现负值分析炼钢工序能耗是按生产出每吨合格产品(钢锭或连铸坯)所用的各种能量之和扣除相应回收的能量(标煤)进行计算的。
消耗能量回收能量时,耗能为正值消耗能量-回收能量=0时(称零能炼钢)消耗能量回收能量时,耗能为负值(称负能炼钢)1.4实现负能炼钢是可能的转炉炼钢过程中释放出的能量是以高温煤气为载体,若以热能加以度量分析,具体表现为潜热占83.6%,显热占16.4%,详见图3。
显然,煤气所拥有的能量占总热量中的绝大部分。
转炉煤气回收量的分析与实践

转炉煤气回收量的分析与实践摘要:本文通过物料平衡的方法,计算出转炉煤气回收的极限量,并结合实际生产操作,放宽转炉煤气回收条件,将转炉实际最大回收量与极限量进行对比,并从电能利用方面分析提高转炉煤气回收量的经济性。
关键词:转炉煤气极限回收经济性1 概述随着国家能源政策的进一步加强,钢铁市场竞争的越发剧烈,各钢铁企业在追求钢材品质的同时,更在力争如何降低吨钢能耗,而在整个冶炼工序中,唯一能实现负能冶炼的就是转炉炼钢环节。
转炉煤气回收占整个转炉工序能源回收的80%-90%,是降低炼钢能耗,实现负能炼钢的关键环节,因此,各企业都十分重视转炉煤气回收,尽可能的多回收转炉煤气。
目前,对如何提高转炉煤气回收的研究较多,但对于煤气回收量的潜力有多大的研究较少,从而导致一些企业对吨钢回收量预估不足,后续煤气柜和加压系统配置能力偏低,一旦想提高吨钢煤气回收量则困难重重,设备能力受限,造成能源的浪费;同时也有些企业为了追求吨钢回收量,过大的配置煤气柜容量,以及加压机风量的配置,提高了工程一次投资成本和运行成本,设备能力上也是大马拉小车,造成一定程度的浪费。
本文基于碳平衡原理,建立转炉煤气回收量计算模型,计算了转炉煤气回收量的极限值,同时放宽回收条件,从实际生产中最大限度的提高吨钢回收量,得到生产数据,进而根据实际回收量与极限回收量对比确定转炉煤气回收的潜力,为后续回收设施的选型提供可靠依据。
2 转炉煤气极限回收量计算模型根据冶金反应原理,转炉烟气主要是由原料中碳氧化产生的,含碳原料主要有铁水和炭质发热剂。
原料中的碳以一定的比例氧化成CO、CO,以炉气形式排2出,经炉口处吸入一定的空气形成烟气。
转炉烟气根据回收设备条件和回收技术水平,回收成可利用的能源介质即转炉煤气。
按物料平衡和热平衡建立转炉煤气回收量计算模型,如下:式中:折算为标准热值后的转炉煤气量,m3/t;3018——CO热值,Kcal/m32000——标准热值,Kcal/m3碳氧化生成的炉气量,m3/t;炭质发热剂生成的炉气量,m3/t;空气吸入系数,即实际空气吸入量与转炉气完全燃烧所需的理论空气量的比值;转炉煤气回收比,即煤气回收量与转炉煤气发生量的比值,%;的分配比。
炼钢厂转炉煤气回收误差操作分析研究

C O,具有 较 高 的 热 值 ,是 一 种 宝 贵 的 可 回 收 资 源… 。转 炉煤 气 的 回收 是 炼 钢 厂 实 现 负 能 炼 钢 关
定 的资产 流失 。
( 【 £ 一 88_ 鲫
键手段 ,同 时剩 余转 炉煤 气 的并 网可 以产 生效
益 。
2 调 查 方 法
煤气 的回收 时 间为 6 mi 0 s n ,本 次 调 查 时 间 总 长 4
煤气 回收操作 。 调查 的相关 统计 数 据见 表 2 。
表 2 误 差 操 作 炉 数 统 计 表
度 为 2 ,所 以每 2 内相 当 于少 回收煤 气 9 1 4h 4h之 .
炉次 。
每炉 次 的煤 气 回收 量 约为 350m ,每天 单纯 0 。
作者简介 :高
恺 (9 3一 ) 18 ,男,20 09年 7 毕业 于青 岛理 工 月
大学环境工程专业。助理】程 师,主要从事循环经济技术工作。 :
1 4
莱钢 科技
表 1 调 查 炉 数 概 况 单 位 :炉
21 0 0年 6月
转 炉 累计 延 迟时 间各 不相 近 ,这说 明转 炉 与转 炉 之
1和 图 2 。
▲
一
▲ .●・ . . ■ .^ ▲ ▲
产“
.
入
▲
‘
一 .
I — - ●
一
■- ●_
一
一
。 一
。 / ‘
■. . .
—
一
.
.
rr
.
。— l “
垒 。c _
o.- occ oo r
D
l Z
转炉炼钢项目7除尘及煤气回收

任务实施
一、除尘及煤气系统的检查操作 (1)观察风机故障信号灯,该灯不亮,表示风机正常;该灯亮,表示风
机有故障。 (2)观察要求送停风按钮、信号灯是否正常。 (3)观察煤气回收信号灯是否显示正常。回收阀开时,放散阀关;回收
氧气顶吹转炉炉气中夹带的烟尘量为金属装入量的0.8%~1.3%,炉气 (标态)含尘量为80~120g/m3。烟气的含尘量一般小于炉气的含尘量,且 随净化过程逐渐降低。顶底复合吹炼转炉的烟尘量一般比顶吹工艺的烟尘量 少。
相关知识
四、烟气净化与回收的工艺流程 烟气→水冷或汽化冷却的活动烟罩和固定烟罩→汽化冷却或废热锅炉式
转炉炼铁操作
项目七 除尘及煤气回收
项目导入
若转炉烟气不经过回收净化处理直接向大气排放,将 会使空气严重污染,危害人的健康,影响动、植物生长, 破坏大自然的生态平衡。国家规定的排放标准为标准态烟 气中CO含量不超过2mg/m3,含尘量不得超过120mg/m3。本 项目叙述未燃法烟气净化与回收系统的流程和主要设备, 煤气回收与放散操作。
• 检查并确认设备完好正常,能及时发现设备故障。 学会正确使用除尘和煤气回收装置。。
学习目标 任务描述
在了解烟气净化回收的方式、烟气与烟尘的特 征的基础上,学习烟气净化与回收的工艺流程及主 要设备。学会检查和正确使用除尘和煤气回收装置。
任务 描述
相关知识
一、烟气净化回收的方式 1.燃烧法
炉气从炉口进入烟罩时,称为烟气,令其与足够的空气混合,使烟气中 的可燃成分CO进行燃烧,形成高温废气,经冷却、净化后通过风机、烟囱排 入大气中去。 2.未燃法
当烟罩就位后将“烟罩”开关恢复“零位”。降罩后自动分析装置开始不断 分析其烟气成分。当自动回收煤气装置收到了3个信号:开氧信号,降罩信号, 烟气成分符合回收要求信号时,会进行自动回收。然后当其中任一条件不符 合设计要求时又会自动放散。主要设计的成分是CO和氧的含量。
- 1、下载文档前请自行甄别文档内容的完整性,平台不提供额外的编辑、内容补充、找答案等附加服务。
- 2、"仅部分预览"的文档,不可在线预览部分如存在完整性等问题,可反馈申请退款(可完整预览的文档不适用该条件!)。
- 3、如文档侵犯您的权益,请联系客服反馈,我们会尽快为您处理(人工客服工作时间:9:00-18:30)。
转炉炼钢煤气回收系统的分析
摘要:副产煤气的全部回收综合利用,是反映钢铁企业能源利用水平及节能降耗水平的关键指标,是实现负能炼钢和降低炼钢工序能耗的关键环节,同时能降低钢厂污染物排放总量,实现节能环保双赢,具有环境效益和经济效益。
本文主要对转炉炼钢煤气回收系统进行了分析。
关键词:炼钢转炉除尘系统回收条件煤气回收量
引言
转炉煤气回收是把炼钢转炉生产过程中的副产品—一氧化碳含量进行回收再利用的生产工艺。
转炉生产时,氧抢顶吹脱碳过程中产生的一氧化碳高含量的烟气在经过冷却、除尘、分析、回收进煤气柜、精(电)除尘、利用(如发电)的全过程统称为转炉煤气回收再利用。
氧气顶吹转炉煤气的生成,主要来自铁水中碳的氧化,其产气量的大小也取决于铁水含碳量的大小,氧气顶吹转炉煤气产气量中,能够回收使用的部分称为实际回收量,回收煤气的炉数与冶炼炉数之比称为煤气回收率,煤气回收量及回收率与操作、技术水平有关。
这项工作的安全可靠性、科学回收性及产能提高性的技术,是转炉煤气回收的关键。
目前,全国很多转炉炼钢厂都实现了煤气的回收,由于该技术在各家企业运用的不同特点和采用的技术、工艺不同,煤气回收最终的产能也有较大的差异,效益也不尽相同。
对转炉炼钢煤气回收工艺分析
转炉煤气回收的成熟技术有氧气转炉煤气回收工艺(OG法) 和LT干式回收工艺,我国钢铁企业目前运行中的煤气回收系统多是在上述两种工艺原理基础上,根据自身情况改造设计而成的,其运行效率在不断提高。
氧气转炉煤气回收工艺
OG法回收转炉煤气在目前的世界炼钢领域是成熟"先进"可靠的技术,全世界已有200 多套设备投入生产运行,效果显著。
采用OG法回收的转炉煤气热值高"回收量大"除尘效率高,其设备寿命长"安全性好"自动化程度高。
OG法法工艺中,转炉烟气净化系统采用湿式未燃法‘比肖夫’系统,其流程为: 转炉烟气借风机吸力进入汽化冷却烟道,回收部分烟气余热。
从汽化冷却
烟道出来的烟气在上部进入‘比肖夫’除尘冷却装置,‘比肖夫’装置上部是一个洗涤塔,气液同向而行,进行降温和粗除尘。
然后,气体进入下部的可调文氏管进行精除尘,经除尘后的气体由下部返入筒体进行脱水,然后从中部引出#比肖夫$装置。
经降温除尘的净煤气经风机加压后通过三通切换阀,当烟气中的 CO 及 O含量符合回收要求时,则进入煤气储柜储存,需使用时进行精除尘和加压供用户使用。
在烟气不合格时,通过三通切换阀将烟气送至放散管点火放散。
LT干式回收工艺
LT法是德国鲁奇公司与蒂森公司合作开发的转炉烟气净化"回收"利用的干式工艺,其基本原理是: 当转炉吹炼时,O和C 之间发生反应产生含有高浓度 CO 和烟尘的转炉煤气( 烟气) 。
为了回收利用高热值的转炉煤气和减少污染,需对烟气进行净化,首先将转炉烟气经过废气冷却系统,然后进入蒸发冷却器,喷水蒸发使烟气得到冷却。
由于烟气在蒸发器中得到减速,使烟气中粗颗粒的粉尘沉降下来,通过链式输送机以及闸板阀将粉尘排出。
同时,烟气通过荒煤气管道导入设有4个电场的静电除尘器,在电场作用下使粉尘和雾状颗粒物吸附在收尘极板上,使烟气得到净化。
电除尘器下部的集灰用扇形刮灰器刮到位于其下部的链式输送机中,并送入中间料仓,然后通过气力输送系统再将干灰送到压块系统的集尘料仓中。
切换站由联锁控制,当符合煤气回收条件时,回收侧的钟型阀自动开启,高温净煤气进入煤气冷却器喷淋降温至约73摄氏度,然后送入煤气储柜。
经储柜后的煤气加压机将高洁度转炉煤气( 含尘10 mg/m3以下) 提供给用户使用。
吹炼前期和后期不符合回收要求的煤气,则自动开启放散侧钟型阀,通过放散塔点燃放散,以达到工业炉窑大气污染物的排放标准.
国内常见的回收工艺流程
多数钢铁企业综合考虑目前国内同等型号转炉煤气回收工艺和公司实际情况,煤气净化回收多采用的工艺为: 转炉冶炼过程中的烟尘通过固定烟罩和冷却烟道经二文三脱煤气净化装置"风机"煤气柜及加压站到达用户,实现对煤气净化回收,不合格或不宜回收的煤气经处理后从烟囱达标排放,同时从冷却烟道和烟罩产生的蒸汽通过余热设施回收。
提高转炉煤气回收量的方法
实现转炉煤气回收的各个单位独有自己的煤气回收量增加的办法,总结起来主要有以下几点:控制煤气回收时炉口的空气吸人量,使烟气中的一氧化碳含量尽快达标;在转炉生产时化好初渣对煤气回收的影响也很大,化渣的好坏直接影响到转炉生产的平稳性,也是衡量转炉生产操作水平的主要标志,是转炉煤气量在生产初期平稳上升的重要因素。
转炉生产的稳定对一氧化碳含量的稳定有很大的关系,也是增加煤气回收量的保证。
在转炉钢水脱碳后期,可以适当将提罩时间后延,控制住炉口空气暂不让其进人,就可延长回收时间,从而增加煤气的回收量。
此外,在转炉生产时,风机一般有两个转速:转炉不生产或工序间隙时间是低速运行的,在转炉生产开始到结束期间是高速运行,这是降低转炉工序能耗的重要手段。
在转炉生产后期,可以根据各单位的实际情况摸索风机的第三速度来配合生产,是转炉煤气平稳下降,从而增加转炉煤气的回收量。
从上面的分析来看,这些手段有一个共同的特点,就是为了使转炉生产初期一氧化碳含量尽快达标,因此,在转炉生产后期要延缓一氧化碳含量不达标的时间,延长了回收的时间就增加了煤气回收量。
转炉煤气回收过程中需要注意的事项
转炉煤气回收是通过程序采集一氧化碳含量和氧含量实现自动控制的,绝对不允许手动强行进行回收,造成不合格气体进人煤气柜。
转炉煤气回收虽是通过程序实现自动回收,但每一炉都必须由人工确认,在收到人工确认后才启动回收程序,程序编制时就要求完整。
在人工确认后,旁通阀就进行关闭,关闭过程中阀体阀板密封冲洗水要同时打开,在阀体关闭到位后,冲洗水自动停止。
这样保持密封干净和不产生火花,水冲洗要在现场确认。
冲洗水的水流量要有显示,这就容易检查水冲洗的正常与否。
在烟气成分中的一氧化碳含量和氧含量达标、同时煤气柜条件又允许的情况下,程序设定要首先打开水封逆止阀,然后打开三通阀到回收位置,实现回收;在回收结束时,要先同时打开旁通阀和三通阀,然后关闭水封逆止阀,这是合理的程序。
在煤气回收的整个过程中,前后生产工艺、设备的匹配非常重要,一个环节做不好,将影响整个回收效果。
同时,做好工作联系制度的落实,加压站、煤气柜、除尘净化等岗位要时刻与有关的工序岗位进行联系,预防生产中的突发事情,从
实际的情况来看,转炉煤气回收系统要有比较齐全的应付突发故障的方法和手段,以确保安全回收。
结语
在当今能源缺乏的时代,如何做好现有资源的再利用是我们每一个济钢能源工作者的职责。
转炉煤气回收是一个比较成熟的工艺,但要进一步提升此工艺的安全技术操作水平,提高转炉煤气的回收量和利用率,我们要做的工作还很多,应持续不断地努力。
参考文献:
【1】郭素清. 转炉煤气在酒钢的综合利用[J]. 甘肃冶金. 2009(04)
【2】杜繁志,孙长启,刘宪会,马仁川. 优化加压和输送系统,提高转炉煤气回收量[J]. 冶金动力. 2011(04)
【3】武乐,杨国华. 新型炼钢转炉煤气净化回收系统[J]. 冶金能源. 2009(05)
【4】李建新,姜碧涛,底根顺,翟永臻,赵国英. 转炉煤气回收及综合利用[J]. 中国冶金. 2006(03)。