150t炼钢连铸的钢包回转台设计
150t转炉连铸热连轧工程简介
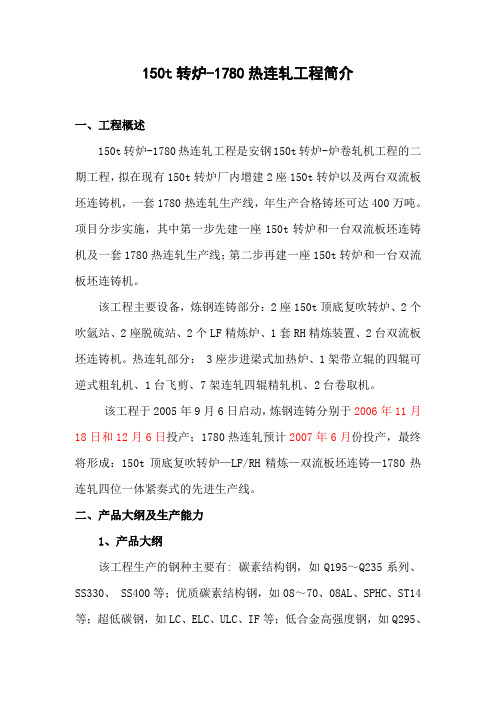
150t转炉-1780热连轧工程简介一、工程概述150t转炉-1780热连轧工程是安钢150t转炉-炉卷轧机工程的二期工程,拟在现有150t转炉厂内增建2座150t转炉以及两台双流板坯连铸机,一套1780热连轧生产线,年生产合格铸坯可达400万吨。
项目分步实施,其中第一步先建一座150t转炉和一台双流板坯连铸机及一套1780热连轧生产线;第二步再建一座150t转炉和一台双流板坯连铸机。
该工程主要设备,炼钢连铸部分:2座150t顶底复吹转炉、2个吹氩站、2座脱硫站、2个LF精炼炉、1套RH精炼装置、2台双流板坯连铸机。
热连轧部分: 3座步进梁式加热炉、1架带立辊的四辊可逆式粗轧机、1台飞剪、7架连轧四辊精轧机、2台卷取机。
该工程于2005年9月6日启动,炼钢连铸分别于2006年11月18日和12月6日投产;1780热连轧预计2007年6月份投产,最终将形成:150t顶底复吹转炉—LF/RH精炼—双流板坯连铸—1780热连轧四位一体紧奏式的先进生产线。
二、产品大纲及生产能力1、产品大纲该工程生产的钢种主要有:碳素结构钢,如Q195~Q235系列、SS330、 SS400等;优质碳素结构钢,如08~70、08AL、SPHC、ST14等;超低碳钢,如LC、ELC、ULC、IF等;低合金高强度钢,如Q295、Q345、Q420、Q460等;专用钢,如集装箱用钢、耐候钢、管线钢、汽车梁及汽车结构用钢、压力容器、锅炉用钢、桥梁用钢等。
该产品大纲结构合理,既有用量大的基础建设用钢,也有汽车、桥梁、集装箱、石油天然气输送管线钢等高附加值的高端产品,丰富了安钢的产品结构,提高了安钢产品的竞争力,为安钢向特大型钢铁强厂发展奠定了基础。
2、设计生产能力及产品规格钢水年产量:368万吨铸坯年产量:360万吨,厚度210 mm、230 mm,宽度800 mm~1650 mm,定尺9 m~11m,少量4.5 m~5.3 m板带年产量:350万吨,厚度 1.2mm~19mm,宽度800mm~1630mm三、该工程所采用的新技术新工艺1、炼钢部分:铁水脱硫技术、副枪及动静态模型控制技术、LF/RH 精炼技术、自动化装备:三级计算机生产管理系统等。
钢包回转台的设计说明书
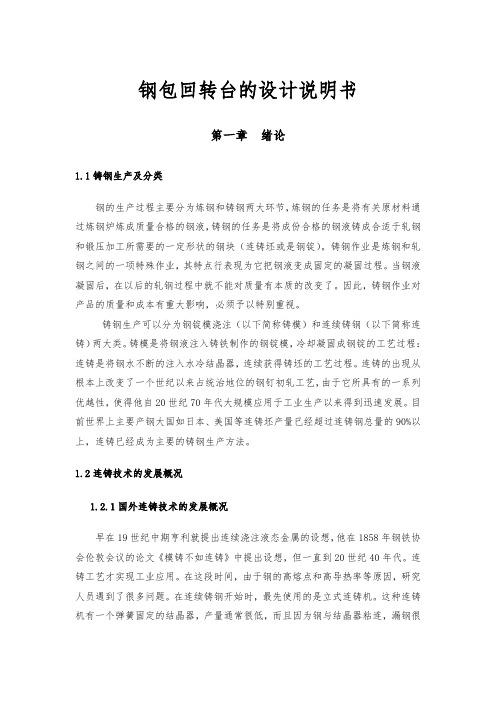
钢包回转台的设计说明书第一章绪论1.1铸钢生产及分类钢的生产过程主要分为炼钢和铸钢两大环节,炼钢的任务是将有关原材料通过炼钢炉炼成质量合格的钢液,铸钢的任务是将成份合格的钢液铸成合适于轧钢和锻压加工所需要的一定形状的钢块(连铸坯或是钢锭)。
铸钢作业是炼钢和轧钢之间的一项特殊作业,其特点行表现为它把钢液变成固定的凝固过程。
当钢液凝固后,在以后的轧钢过程中就不能对质量有本质的改变了。
因此,铸钢作业对产品的质量和成本有重大影响,必须予以特别重视。
铸钢生产可以分为钢锭模浇注(以下简称铸模)和连续铸钢(以下简称连铸)两大类。
铸模是将钢液注入铸铁制作的钢锭模,冷却凝固成钢锭的工艺过程:连铸是将钢水不断的注入水冷结晶器,连续获得铸坯的工艺过程。
连铸的出现从根本上改变了一个世纪以来占统治地位的钢钉初轧工艺,由于它所具有的一系列优越性,使得他自20世纪70年代大规模应用于工业生产以来得到迅速发展。
目前世界上主要产钢大国如日本、美国等连铸坯产量已经超过连铸钢总量的90%以上,连铸已经成为主要的铸钢生产方法。
1.2连铸技术的发展概况1.2.1国外连铸技术的发展概况早在19世纪中期亨利就提出连续浇注液态金属的设想,他在1858年钢铁协会伦敦会议的论文《模铸不如连铸》中提出设想,但一直到20世纪40年代。
连铸工艺才实现工业应用。
在这段时间,由于钢的高熔点和高导热率等原因,研究人员遇到了很多问题。
在连续铸钢开始时,最先使用的是立式连铸机。
这种连铸机有一个弹簧固定的结晶器,产量通常很低,而且因为钢与结晶器粘连,漏钢很常见。
振动结晶器的想法归功于德国人seigfried,他首创了有色金属的连续铸造,与1952年用于德国的钢铁厂的直结晶器立式连铸机上,这是连铸工业化规模的开始。
由于技术的限制多年只应用于小工厂,自1970年开始连铸开始应用于钢铁联合企业来生产板坯。
1.2.2我国连铸技术的发展概况我国是研究和应用连铸技术较早的国家之一,早在20世纪50年代就开始探索性的工作,60年代初进入到连铸技术工业应用阶段。
连铸工程钢包回转台安装

山 西 建 筑
S HANXI ARCH I CTURE TE
V0 . 6No. 0 13 2
J1 2 1 u. 0 0
・11 ・ 1
文 章 编 号 :0 96 2 (0 0 2 .1 10 1 0 —8 5 2 1 )00 1 -2
7 防水 卷材 施 工成 品保 护
防水卷材工程 质量 和完 工后 的成 品保护 密切 相关 。为此 必 须采取有针对性 的措施 , 防止将 已完工 的防水层 破坏成 为渗漏 的
隐 患 。 已铺 贴 好 的 卷 材 防 水 层 , 及 时 采 取 保 护 措 施 , 作 人 员 应 操
工方案 , 工程防水效果应 满足 G 00 —0 8地下 工程 防水 技 该 B 5 182 0
a伸缩缝施工 时未 断开 , . 导致 防水层 撕 裂 ; . 他 部位 由于粘 结 b其
粘结不牢 、 动或基层清理不干净 , 材搭接长度不够 。 松 卷
地下室筏板 防水是 一 门综 合性 、 用性很 强 的工程 技术 , 实 要 求高 、 度大。要提高防水工程 的质 量 , 以材料为基础 , 难 应 以设 计 不牢 、 卷材松 动或 衬垫材料不严 、 有空隙等 ;. c 接槎处 漏水 原因是 为前 提 , 以施工 为关键 , 并加 强维护 。通过实 施筏板 防水专项 施
2 双桥 吊“ 中接 力” 案 的确 定 空 方
3. 回 转 底 座 安 装 2
回转底座 吊装 前要 先在基 础上 进行 坐浆 或研垫 板。如果 采 我们通过综 合分析和充分论 证 , 设计 并制作 了一 个扁担式 吊 坐浆块数量可根据底座重量 和地脚螺栓 初次 紧固力确 具( 以后 可用 于其他工程 )选定 了双桥 吊“ , 空中接力 ” 的吊装方案 用坐浆法 , 定 , 数量不宜过多 , 但 否则会 给后来的底座调整提高一定难度 。坐 ( 回转底座 、 回转体 、 门形 框 架等 均可 采用 这一 方 案 ) 。具体 吊装
连铸钢包回转台安装方案(优.选)

**连铸机钢包回转台安装施工作业设计批准日期审核日期编制日期**公司2002/10/21目录1、编制依据2、工程概况2.1工程内容2.2相关条件2.3工程特点3、安装程序3.1安装流程3.2测量放线3.3底座吊装就位3.4、旋转套筒及旋转臂和其它部件的安装3.5底座找正作业操作要领3.6吊装注意事3.7吊具的强度计算4.工期计划4.1工期网络计划4.2工期控制措施4、质量方针和目标5.1质量方针5.2质量目标5.3质量保证措施5.4质量管理组织5、施工组织6、安全管理7.1安全目标7.2安全措施7.3安全管理组织8.机具及材料9.附图1、编制依据本施工作业设计编制主要依据下列技术资料1)《冶金机械设备安装工程质量检验评定标准》:连续铸钢设备,冶金工业出版社,YB 9244-922)梅钢发放的安装图与转化图3)奥钢联提供的安装说明书4)《冶金机械设备安装工程施工及验收规范》YBJ 202-835)《工程测量规范》GB50026-936)《建筑施工高处作业安全技术规范》JBJ80-917)《建筑工程施工现场供用电安全规范》GB 50194-938)《建筑机械使用安全技术规程》JBJ33-869)《工业设备、管道焊接工程施工及验收规范》GBJ236-822、工程概况2.1工程内容本施工作业设计主要包括下列内容永久基准点和中心标板的埋设;钢包回转台底座的安装与找正;旋转体的安装;两只旋转臂的安装及旋转臂升降装置的安装;旋转驱动装置安装;钢包加盖装置的安装等。
**连铸机的钢包回转台由底座(11.3t)、旋转体(40t)、旋转臂(47.7t)、旋转臂升降装置(16.5t)、上连杆(26.5t)、下连杆(6.4t)、钢包加盖装置、旋转驱动装置等机械部件组成;总重215 .32T。
该钢包回转台位于厂房③线-④线的L列行车轨道梁之下,吊装位置极其困难;其底座基础标高为+10.847m,行车梁隔热板下表面标高为+22.015m。
150t×3转炉精炼及连铸工艺设计 终稿
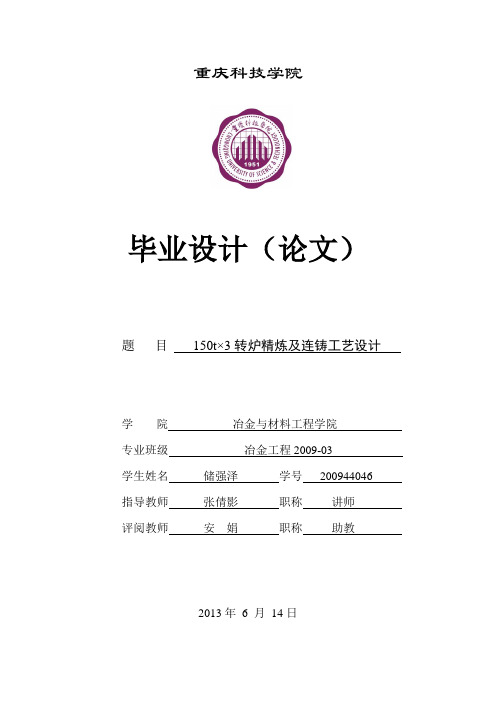
重庆科技学院毕业设计(论文)题目150t×3转炉精炼及连铸工艺设计学院冶金与材料工程学院专业班级冶金工程2009-03学生姓名储强泽学号200944046 指导教师张倩影职称讲师评阅教师安娟职称助教2013年6 月14日注意事项1.设计(论文)的内容包括:1)封面(按教务处制定的标准封面格式制作)2)原创性声明3)中文摘要(300字左右)、关键词4)外文摘要、关键词5)目次页(附件不统一编入)6)论文主体部分:引言(或绪论)、正文、结论7)参考文献8)致谢9)附录(对论文支持必要时)2.论文字数要求:理工类设计(论文)正文字数不少于1万字(不包括图纸、程序清单等),文科类论文正文字数不少于1.2万字。
3.附件包括:任务书、开题报告、外文译文、译文原文(复印件)。
4.文字、图表要求:1)文字通顺,语言流畅,书写字迹工整,打印字体及大小符合要求,无错别字,不准请他人代写2)工程设计类题目的图纸,要求部分用尺规绘制,部分用计算机绘制,所有图纸应符合国家技术标准规范。
图表整洁,布局合理,文字注释必须使用工程字书写,不准用徒手画3)毕业论文须用A4单面打印,论文50页以上的双面打印4)图表应绘制于无格子的页面上5)软件工程类课题应有程序清单,并提供电子文档5.装订顺序1)设计(论文)2)附件:按照任务书、开题报告、外文译文、译文原文(复印件)次序装订3)其它学生毕业设计(论文)原创性声明本人以信誉声明:所呈交的毕业设计(论文)是在导师的指导下进行的设计(研究)工作及取得的成果,设计(论文)中引用他(她)人的文献、数据、图件、资料均已明确标注出,论文中的结论和结果为本人独立完成,不包含他人成果及为获得重庆科技学院或其它教育机构的学位或证书而使用其材料。
与我一同工作的同志对本设计(研究)所做的任何贡献均已在论文中作了明确的说明并表示了谢意。
毕业设计(论文)作者(签字):年月日摘要摘要目前,我国钢铁行业处于低迷期,一些中小型钢铁厂生存艰难,究其原因主要是这些企业能耗高,产品单一,产品科技含量低,缺乏市场竞争力。
方坯连铸线中钢包回转台及中间罐车的制造
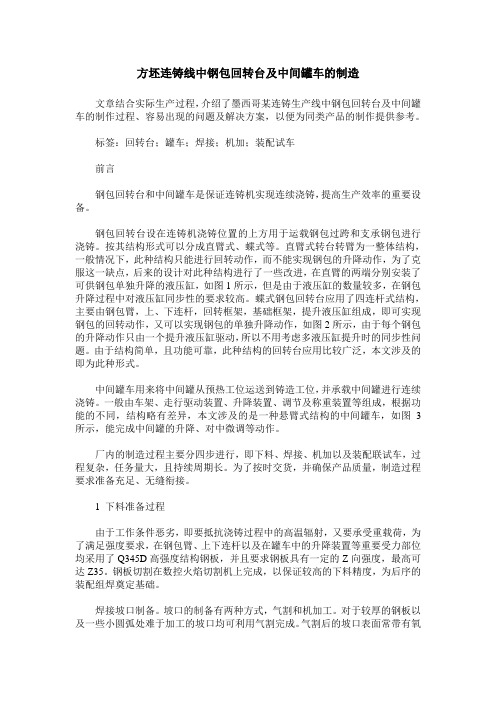
方坯连铸线中钢包回转台及中间罐车的制造文章结合实际生产过程,介绍了墨西哥某连铸生产线中钢包回转台及中间罐车的制作过程、容易出现的问题及解决方案,以便为同类产品的制作提供参考。
标签:回转台;罐车;焊接;机加;装配试车前言钢包回转台和中间罐车是保证连铸机实现连续浇铸,提高生产效率的重要设备。
钢包回转台设在连铸机浇铸位置的上方用于运载钢包过跨和支承钢包进行浇铸。
按其结构形式可以分成直臂式、蝶式等。
直臂式转台转臂为一整体结构,一般情况下,此种结构只能进行回转动作,而不能实现钢包的升降动作,为了克服这一缺点,后来的设计对此种结构进行了一些改进,在直臂的两端分别安装了可供钢包单独升降的液压缸,如图1所示,但是由于液压缸的数量较多,在钢包升降过程中对液压缸同步性的要求较高。
蝶式钢包回转台应用了四连杆式结构,主要由钢包臂,上、下连杆,回转框架,基础框架,提升液压缸组成,即可实现钢包的回转动作,又可以实现钢包的单独升降动作,如图2所示,由于每个钢包的升降动作只由一个提升液压缸驱动,所以不用考虑多液压缸提升时的同步性问题。
由于结构简单,且功能可靠,此种结构的回转台应用比较广泛,本文涉及的即为此种形式。
中间罐车用来将中间罐从预热工位运送到铸造工位,并承载中间罐进行连续浇铸。
一般由车架、走行驱动装置、升降装置、调节及称重装置等组成,根据功能的不同,结构略有差异,本文涉及的是一种悬臂式结构的中间罐车,如图3所示,能完成中间罐的升降、对中微调等动作。
厂内的制造过程主要分四步进行,即下料、焊接、机加以及装配联试车,过程复杂,任务量大,且持续周期长。
为了按时交货,并确保产品质量,制造过程要求准备充足、无缝衔接。
1 下料准备过程由于工作条件恶劣,即要抵抗浇铸过程中的高温辐射,又要承受重载荷,为了满足强度要求,在钢包臂、上下连杆以及在罐车中的升降装置等重要受力部位均采用了Q345D高强度结构钢板,并且要求钢板具有一定的Z向强度,最高可达Z35。
钢包回转台的设计计算

重 工 与 起 重 技 术
HEAVY INDU Srm IAL& HOIS,I1ING MACHINERY
式 中 : 承上面设备 自重 ;
G —A 侧座包 总重量 ; G厂-B侧钢包总 重量 ; K一 座包 冲击 系数 。 (4)径 向载荷
= G ×K  ̄/3 式 中 :
摘 要 :简要介绍 了钢包 回转台的作用、主要技术参数 的确 定及部分机构 的设计计算 。 关键 词 :钢 包 回转 台 ·承 载 能 力 ,回转 ,升 降
1 概 述
钢包 回转 台是连铸机生 产线的大型关键 设备之 一 , 安装在 连铸 车间钢水接受跨 和连铸跨之 间的浇 铸平 台上 ,用于接受炼 钢系统送来 的盛 满钢水 的钢 包 ,将钢包 转至连铸跨的浇注位置进行浇 注。当钢水 浇注 结束后 ,经设备旋转将 空钢包送 回炼钢 跨 ,同时 将 新 的盛 满钢水 的钢包送到 连铸 跨 ,从 而保 证连铸 机 连续浇注生产 。
(3)配 合 150t转 炉 ,回转 半 径参 数 值 通 常 采 用
5300~ 5800mm {
(4)配合 120t转 炉 ,回转半 径 参 数 值 通 常 采 用
5000~ 5500mm 。
3 t/l, ̄和部件设计计算
钢包 回转 台由回转部分 、固定部分 、润滑 系统和 电控系统所组成。
G 座包总 重量 ; 包轴 向冲 击系数 ,取 K=2;
_ 座包径 向冲击系数 ; 当采用插销 式定位时 ,取 = 150/o{ 当采用摩擦 式定位时 ,取 J8= 1 O%。 (5)倾 翻力矩 M =(G ×K-Gb)×R 式 中: 尺一 回转 半径 。 (6)综合 载荷校核 三排 滚柱 回转 支撑轴承综合 载荷 的校 核 ,按照轴 承 生产厂家提供 的各种规 格轴承 载荷 曲线 图进行 ,横 坐 标为轴 向载荷 ,竖坐标为 倾翻力 矩 。分 别将各种 工 况情 况下不 同冲击系数 的计算值 交点列于 曲线 图上 , 所 有点 处于 该规格 轴 承综合 曲线值 下面则 为计 算 校 核 通过 。 3.2 回转 传动计算 (1)回转 体与减速机传动 回转 体与减速机 采用开式齿 轮或齿销 传动 ,开 式 齿 轮和齿销传动 计算详见相 关设 计手册 。 ① 开式齿 轮传动 大齿 轮通常与 回转大轴承外环 连为一 体 ,小齿 轮 则 安装在减速机 输 出轴上 。开 式齿 轮啮合 应采用大侧 隙传动 ,为 方便 减速机 维护 安装 ,通常 在大 齿 轮和小 齿 轮之间加一过 渡齿 轮 。 ② 齿销传动 销 轮通常与 回转体相 连 ,齿轮则安 装在 减速 机输 出轴 上。 当减速机 底座 与 回转 体底座基 础分离 时 ,应 校 核 由 回转 大轴 承综合 间 隙等原 因引起 的齿销 传动 侧隙是否满足使 用要求。 (2)传动功率 确定 回转 台传动功率计算 过程 比较复杂 ,其 中最 大 的 影响因素是 回转大轴 承综合摩擦 系数 ,由于供货 厂家 不 同,其 综合摩擦 系数 变化范 围为 0.o03 ̄o.007。 目 前 ,传动功率确 定大 多根据 以往经验 采用 比照法 ,考 虑回转大 轴承供货厂 家等 因素进行设计 。以下简要介
150吨炉区12机12流连铸机工艺操作规程

质量/环境/职业健康安全体系作业文件编号:XGQEOZ-LG-7.5-52 河北钢铁集团宣化钢铁集团有限责任公司炼钢厂十二机十二流连铸机技术操作规程编制:审核:批准:持有人:分发号:受控状态:2011年1月1日发布 2011年1月1日实施河北钢铁集团宣化钢铁集团有限责任公司炼钢厂更改状态一览表序号版本号更改号更改章节号更改内容修改人日期审核人日期批准人日期生效日期1 1 0 2011.1.1目录1 连铸机工艺流程及主要工艺设备参数、铸坯检验标准2 连铸对钢水的要求3 中间包的准备要求4 主控室技术操作规程5 钢水罐浇钢技术操作规程6 中间罐浇钢技术操作规程7 切割技术操作规程8 出坯技术操作规程9 精整技术操作规程10 附表:冶炼钢种二冷比水量表十二机十二流连铸机技术操作规程1. 连铸机工艺流程及主要工艺设备参数、铸坯检验标准 1.1连铸机工艺流程钢包回转台及钢包 中间罐车及中间罐结 晶 器 二 冷 室拉 矫 机切 前 辊 道火 焰 切 割 机 输 出 辊 道钢包保护浇注铸流保护浇注 切割渣收集车 引锭杆存放 事故冷床 引锭杆导向装置结晶器振动机构、塞棒液面自动控制 双向移钢机步进冷床 热送辊道1.2主要工艺设备参数1.2.1机型 R10/24m 12机12流小方坯连铸机1.2.2流间距 1200mm1.2.3断面 150×150 mm2 165×165 mm21.2.4结晶器长度 900mm1.2.5结晶器振动振幅0±4 mm(可调,需更换偏心套)振频40—300次/min(最高400次/min)1.2.6拉矫机拉速 0.3—4.2m/min1.2.7切割速度~300mm/min 可调1.3铸坯检验标准连铸坯质量应符合连铸坯质量检验标准。
2.连铸对钢水要求2.1钢水成分、温度应达到相关规定要求,连铸温度见钢种制度。
2.2其它要求2.2.1确保钢包清洁,保证红包出钢。
150T板坯连铸机修理工程施工组织设计方案
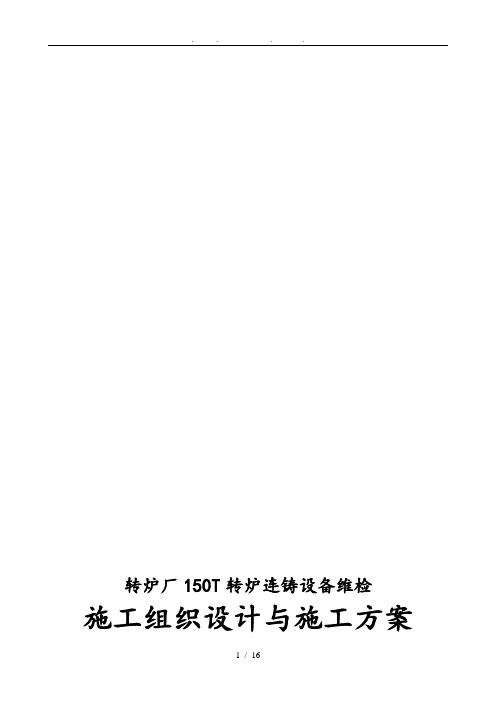
. . . .转炉厂150T转炉连铸设备维检施工组织设计与施工方案2009年02月目录1、工程概况 (3)2、工程质量的目标与保证措施 (3)3、安全施工规 (4)4、施工组织设计 (6)5、施工程序与规 (7)6、维修条件 (8)7、设备维修容与要求(板坯) (8)8、设备维修容与要求(方坯) (12)9、清理埸地、恢复软管、接手、电器线路连接 (15)10、配合热负荷试车 (15)11、投入工程主要施工机械设备表 (16)12、工程配备的主要材料试验、测量、质检仪器设备表 (16)施工组织设计与施工方案1、工程概况1.1工程名称:转炉厂150T转炉连铸设备维检工程1.2工程容:1.2.1 7#、8#板坯连铸机在线所有设备,包含:大包回转台,中间罐车,中间罐烘烤装置,振动,结晶器,弯曲段,扇形段,火焰切割机,脱坯装置,摆动辊道,输送辊道,称重辊道,旋转辊道,翻坯机,冷床推钢机等。
5#方坯7机7流连铸机在线所有设备,包含:大包回转装置,中间罐车,中间罐烘烤装置,结晶器,振动导向段,拉矫机,火焰切割机,输送辊道,翻钢机,过渡冷床,步进冷床,推钢机等。
1.2.2离线对中台、喷号机、输送辊道去毛刺1.2.3二冷风机设备,配水站设备与管道1.2.4电磁搅拌系统1.2.5离线设备、中间包等修复1.2.6区域的过跨车,旋流井,渣钳,夹钳,废钢斗,吊具,葫芦吊等设备1.2.7配合电气、仪表检修需拆装的机械设备(含5KW以上电机的拆装)1.2.8生产事故抢修与恢复。
1.2.9为满足生产而进行的零星整改。
1.2.10设备附属液压系统,干油润滑系统,供油、供气、供水管道,阀门,钢结构等。
1.3工程施工地点:钢铁股份转炉炼钢厂1.4设备安装要求与验收规:铸机设备的安装施工与验收除在各单体设备的技术要求中已注明外,其余遵照以下施工与验收规YBJ201-83 《冶金机械设备安装工程施工与验收规之通用规定》YBJ202-83 《冶金机械设备安装工程施工与验收规之炼2、工程质量的目标与保证措施2.1钢铁股份转炉厂150T转炉连铸设备维检项目,我公司对该工程非常关注和重视。
炼钢厂大包回转台叉型臂设备制造方案

炼钢厂大包回转台叉形臂制作方案单位:编制:审核:批准:一、工程概况大包回转台叉形臂是我公司承揽的非标项目。
本次制作主要部分为1#及2#叉形臂,回转体部分利旧,二钢厂3#连铸机现在所用回转台,叉臂与回转体之间采用高强螺栓连接,新做叉形臂与利旧回转体之间通过焊接连接,新做叉臂在工厂内制作完成,探伤且整体退火后运到机械厂与利旧叉臂进行组对焊接,焊接完成且探伤合格后使用电阻带对最后的对接焊缝进行退火,然后进行整体机加工。
二、方案确定的依据1、回转臂安装图2、重型机械通用技术条件三、工艺流程叉臂:钢板复检→数控下料→加工坡口→钢板煨弯→煨弯处表面渗透检查→组对叉臂箱形结构→焊接18#隔板→焊接四道纵缝内部→外侧清根→焊接四道纵缝外部→四道纵缝探伤→焊接20#隔板→焊接15#件→焊接14#隔板→焊接12#隔板→焊接其它钢板→整形→整体探伤→退火→整体探伤→与利旧回转台组焊→焊缝探伤→电阻带退火→整体机加工四、施工准备1、场地准备清理平台2、人员准备铆工4人焊工4人水焊工2人起重工2人电工1人钳工4人3、机具准备直流电焊机2台水焊工具2套碳弧刨1套角向磨光机4台气保焊工具2套五、技术要求1.下料前应将钢材切割区域表面的铁锈、污物等清除干净,切割后应清除熔渣和飞溅物。
2.气割件允许尺寸偏差长度±1mm。
3.组对前清除部件接触面和沿焊缝边缘每边30~50mm范围内的铁锈及污物。
4.坡口尺寸及形式应按图纸要求进行。
5.使用夹具组装时,不得损伤母材,对残留疤痕应修磨平整。
6.钢板煨弯应采用热煨,加热温度不能超过900℃,以防止材料发生过热过烧,也不能温度过低,产生裂纹。
7.煨弯时应使用胎具定位好材料,防止发生跑偏,造成废品。
8.煨弯后应对煨弯表面进行渗透检查,不允许有裂纹产生。
9.焊工施焊前,应复查焊件接头质量和焊区的处理情况,不符合要求时应进行修正。
10.焊接时不得在焊道以外母材上引弧。
11.角焊缝转角应连续绕角施焊,起落弧点距焊缝端部应大于10mm,且弧坑应填满。
连铸说明书
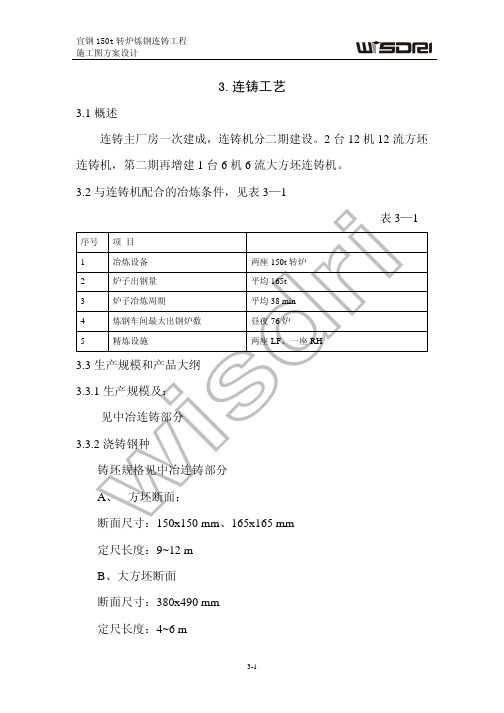
3.连铸工艺3.1概述连铸主厂房一次建成,连铸机分二期建设。
2台12机12流方坯连铸机,第二期再增建1台6机6流大方坯连铸机。
3.2与连铸机配合的冶炼条件,见表3—1表3—1 序号项目1 冶炼设备两座150t转炉2 炉子出钢量平均165t3 炉子冶炼周期平均38 min4 炼钢车间最大出钢炉数昼夜76炉5 精炼设施两座LF、一座RH3.3生产规模和产品大纲3.3.1生产规模及:见中冶连铸部分3.3.2浇铸钢种铸坯规格见中冶连铸部分A、方坯断面:断面尺寸:150x150 mm、165x165 mm定尺长度:9~12 mB、大方坯断面断面尺寸:380x490 mm定尺长度:4~6 m3.4金属平衡从钢水罐钢水到合格坯的金属收得率取98%,此章节详见中冶连铸公司的相关章节3.6连铸车间组成见表3—2表3—2序号 跨间名称厂房尺寸(m ) 吊车配置备注长度 跨度 轨标1浇注跨 348 3334150/80/20t 桥吊x2, 100/20t 桥吊x1 已订货~17 5 t 半门型吊x32 切割跨 348 27 2363/32 t 桥吊x2 32/5t 桥吊x1 已订货3 伸缩缝 348 44 出坯一跨 348 36 16(16+16)t 旋转电磁吊x2 32/5t 桥吊x15 出坯二跨 348 33 13(16+16)t 旋转电磁吊x2 32/5t 桥吊x1连铸全跨 46284m 2 吊车检修葫芦 每跨2台3.7连铸车间工艺布置连铸车间由浇铸跨、切割跨、出坯一跨和出坯二跨组成,与转炉炼钢车间平行布置。
一期上的两台方坯连铸机毗邻布置,浇注平台和主控楼各自独立布置。
在浇铸跨布置两台连铸机的钢包回转台、浇注平台、中间罐车、结晶器、振动装置和拉矫机、引锭杆存放装置等设备。
同时在连铸机平台旁布置有电气室、变压器室、配水室、主机液压站,以及调度室和值班室整体建构筑物。
中间罐维修区,布置在浇铸跨厂房的端头,便于生产管理、原料进出、吊车作业和废耐材运出。
炼钢厂板坯连铸机大包回转台吊装方案
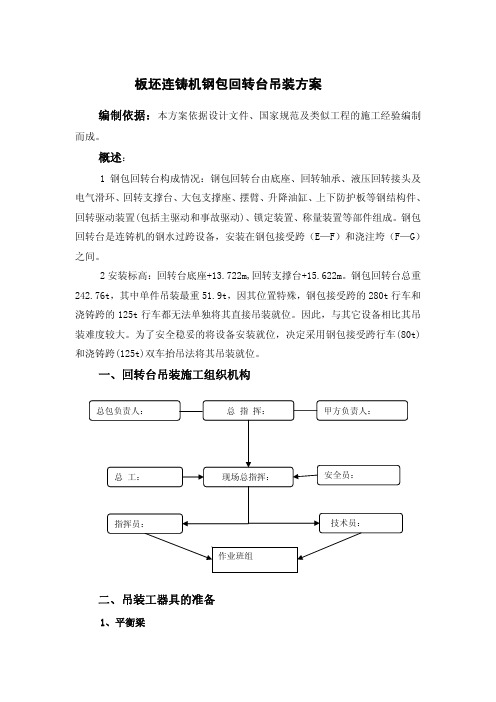
钢丝绳所受作用力 Fˊ<钢丝绳使用拉力 P, 故在大包回转台吊装过程中,钢 丝绳强度是满足需要的。 2、卸扣的强度校核 卸扣所受作用力 W 数值上等于钢丝绳所受拉力 Fˊ=20.004T,其值小于卸扣 允许负荷 50T,因此卸扣的强度是安全的。 3、平衡梁强度校核 平衡梁所用材料为 Q235-B ,该型号钢材在国家标准中规定的许用应力
图 11
其危险截面为矩形,故其所受剪切应力为:
的。
max
F 636.314 KN 70.70 Mpa S 0.06 0.15 M 2
max
[ ] ,符合工程安全需要。
因此,整个平衡梁主要部分的强度是能够满足打包回转台设备的吊装需要
五、吊装作业流程概述
1、钢包回转台底座的吊装 钢包回转台底座重约 18.74t,首先在钢包回转台旁搭设枕木和滚杠的平 台, 用 125t 行车的主钩将钢包回转台底座水平吊移到设有枕木和滚杠的平台上, 用手拉葫芦将底座拉到 F 列吊车梁下, 这时再用 280t 和 125t 行车一起将已制作 好的平衡梁抬放到底座上面,将回转底座和平衡梁用钢丝绳捆好,接着用两跨的 行车同时起吊,吊到一定高度后,两跨行车同时水平位移到钢包底座基础的正上
一、回转台吊装施工组织机构
总包负责人: 总 指 挥: 甲方负责人:
总 工:
现场总指挥:
安全员:
指挥员:
技术员:
作业班组
二、吊装工器具的准备
1、平衡梁
根据已有资料及施工经验,我们拟选用 63C 工字钢、δ=60 钢板、δ=25 钢板、 δ=20 钢板焊接制作平衡梁, 其重量为 12.715T 其基本结构见以下示意图:
连铸钢包回转台安装特殊工艺方案
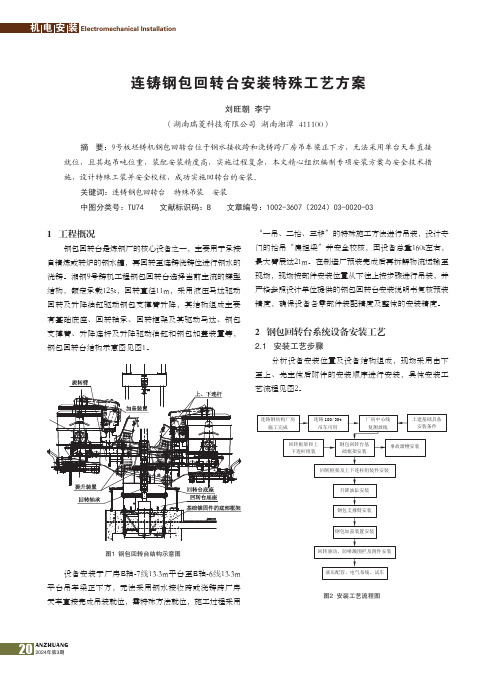
ANZHUANG2024年第3期20刘旺朝 李宁(湖南瑞菱科技有限公司 湖南湘潭 411100)摘 要:9号板坯铸机钢包回转台位于钢水接收跨和浇铸跨厂房吊车梁正下方,无法采用单台天车直接就位,且其起吊吨位重,装配安装精度高,实施过程复杂,本文精心组织编制专项安装方案与安全技术措施,设计特殊工装并安全校核,成功实施回转台的安装。
关键词:连铸钢包回转台 特殊吊装 安装中图分类号:TU74 文献标识码:B 文章编号:1002-3607(2024)03-0020-03连铸钢包回转台安装特殊工艺方案1 工程概况钢包回转台是炼钢厂的核心设备之一,主要用于承接自精炼或转炉的钢水罐,再回转至连铸浇铸位进行钢水的浇铸。
湘钢9号铸机工程钢包回转台选择当前主流的蝶型结构,额定承载125t,回转直径11m,采用液压马达驱动“一吊、二抬、三移”的特殊施工方法进行吊装,设计专门的抬吊“扁担梁”并安全校核,因设备总重160t左右,最大臂展达21m。
在制造厂预装完成后再拆解物流运输至现场,现场按部件安装位置从下往上按步骤进行吊装,并严格参照设计单位提供的钢包回转台安装说明书复核预装精度,确保设备各零部件装配精度及整体的安装精度。
2 钢包回转台系统设备安装工艺2.1 安装工艺步骤分析设备安装位置及设备结构组成,现场采用由下至上、先主体后附件的安装顺序进行安装,具体安装工艺流程见图2。
图2 安装工艺流程图设备安装于厂房E轴-7线13.3m平台至E轴-6线13.3m 平台吊车梁正下方,无法采用钢水接收跨或浇铸跨厂房天车直接完成吊装就位,需特殊方法就位,施工过程采用21INSTALLATION2024.32.2 主要部件施工方法及技术措施2.2.1 安装基准设定基础完工后,安装单位和土建单位进行设备基础联合交接验收,确定合格后,根据连铸机的纵横中心线确定安装的基准点,埋设中线标板和标高标板[1]。
确定设备底座标高、中心标记、中心线标记及辅助中心标记,然后进行设备定位。
150连铸机回转台吊装方案
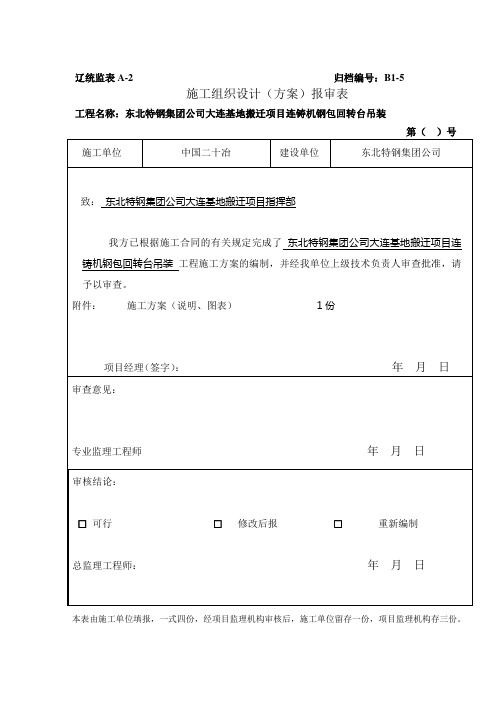
辽统监表A-2 归档编号:B1-5施工组织设计(方案)报审表工程名称:东北特钢集团公司大连基地搬迁项目连铸机钢包回转台吊装本表由施工单位填报,一式四份,经项目监理机构审核后,施工单位留存一份,项目监理机构存三份。
审批页编号:东北特钢集团大连基地环保搬迁工程连铸机钢包回转台吊装方案编制:日期:审核:日期:中国二十冶东北特钢大连基地环保搬迁工程项目部2009年2月24日大钢连铸区钢包回转台回转装置吊装方案一、工程概况大钢连铸机钢包回转台位于D-E跨与E-F跨之间,回转装置主要由回转台、升降液压缸、升降臂及鞍型座组成,回转装置总重70吨。
设备底标高为12米,属高空作业且转台基础空间狭小,存在临边空洞,需要用两台天车抬吊安装。
二、钢包回转台的吊装方法2.1、钢包回转装置的吊装就位采D-E跨内50T天车及E-F 跨内30/100T天车的主钩(100吨)抬吊,两台天车的最小钩距为8米,抬吊用平衡梁详见设计图。
设备的吊点采用1对20T卡环和1对25T卡环和绳扣连接,钢丝绳悬挂于平衡梁上,钢丝绳断面根数为8支,钢丝绳选用1对单根长度为8米直径为φ32的绳扣;平衡梁和天车钩头及天车本体的平衡梁之间采用1对单根长度为6米直径为φ42钢丝绳连接,钢丝绳断面根数为4支;钢丝绳的捆绑方式采用环接方式,两组绳长及平衡梁的垂直高度不超过 6.6m, 钢丝绳和每个平衡梁之间加垫半圆型钢管护角,设备吊装示意图如下所示:2.2、平衡梁设计及强度校核2.2.1、平衡梁设计如附图所示2.2.2、平衡梁及销轴强度校核2.2.2.1、平衡梁抗弯强度校核抗弯截面模量W=(BH3-bh3)/6H=(520×8003-480×7203)/6×800=18.1×106mm3最大弯矩Mmax=FmaxL/4 (受力分析) =700KN×11m/4=1925 KNm构件所受的最弯曲应力σmax=Mmax/W=1925 KNm/18.1×106mm3=106N/ mm2由条件公式可知:当最大弯曲应力σmax≤许用弯曲应力[σw],时满足使用要求许用弯曲应力[σw]= σs/n σs:材料的屈服强度=235 N/ mm2/106N/ mm2=2.2满足使用要求2.2.2.2、平衡梁抗剪强度校核由公式:τmax=(3/2)Nmax/ANmax=700 KN/2= 350KNA=bh=520*800=416000mm2则:τmax=1.26 N/ mm2由条件公式:构件所受最大剪切应力τmax≤[τq] 时满足使用要求许用剪切应力[τq]= 0.6~0.8【σ】材料的许用拉应力【σ】=σs/n σs:材料的屈服强度n=(0.6~0.8)235 /1.26=130满足强度要求2.2.2.3、销轴弯曲强度校核抗弯界面模量:W=0.1D3=0.1×120³mm³=172.8×10³mm³最大弯矩: Mmax=(Fmax/2)(L/2)=350KN×0.3m/4=26.25kNm构件所受最大弯曲应力σmax=Mmax/W=26.25KNm/172.8×10³mm³=152N/ mm2由条件公式可知:当最大弯曲应力σmax≤许用弯曲应力[σw],时满足使用要求许用弯曲应力[σw]= σs/n σs:材料的屈服强度n =235 /152=1.5满足使用要求2.2.2.3、销轴抗剪切力强度校核由公式:τmax= (4/3)(N max/A)N max=Fmax/4=700 KN/4= 175KN得τmax =1.3*175KN/3.14*602=20.1N/mm2由条件公式:构件所受最大剪切应力τmax≤[τq] 时满足使用要求许用剪切应力[τq]= 0.6~0.8【σ】材料的许用拉应力【σ】=σs/n σs:材料的屈服强度则:n= 0.6~0.8【σ】/τmax=7满足强度要求2.3、钢丝绳的选用平衡梁与天车连接的钢丝绳选用直径为(6×37+1)φ42的绳扣,断面根数为4支,安全系数K=5,其许用拉力为P=883/5=176.6KN>175KN (实际拉力),可以使用。
- 1、下载文档前请自行甄别文档内容的完整性,平台不提供额外的编辑、内容补充、找答案等附加服务。
- 2、"仅部分预览"的文档,不可在线预览部分如存在完整性等问题,可反馈申请退款(可完整预览的文档不适用该条件!)。
- 3、如文档侵犯您的权益,请联系客服反馈,我们会尽快为您处理(人工客服工作时间:9:00-18:30)。
毕业设计说明书150t 炼钢连铸的钢包回转台设计源设计图纸请联系本人,参见豆丁备注。
毕业生姓名:专业:机械设计制造及其自动化学号:指导教师:所属系(部):机械电子工程系二〇一四年六月摘要钢包回转台是现代炼钢连铸生产中的主要设备之一,其作用是支撑和运载钢包进行浇铸,为实现多炉连浇创造了条件。
钢包回转台是连续铸钢设备中负荷最大、体积最大的焊接件。
它的主要组成部分是回转臂、推力轴承及塔座三部分。
为了安全运转,要求他的各个零部件有足够的强度和刚度。
本设计说明书是以江苏省镔鑫特钢材料有限公司炼钢厂的连铸车间方坯连铸机的钢包回转台为借鉴,以蝶式钢包回转台为形式进行的设计。
主要内容包括:钢包回转台传动方案的设计,回转台的结构尺寸的确定,主要零件的选择、计算与校核;电动机、减速器的选择与计算,以及钢包升降装置、称量装置、加盖装置的设计,此外,还介绍了部分主要零件具体的安装、维修、润滑、操作方法。
关键词:连铸;蝶式钢包回转台;传动方案;回转台结构尺寸。
AbstractThe ladle turret is one of the main casting equipments.Principal affect is supporting ladle and carrying to operation. For continue us casting invent a condition that working with many ladles.The ladle turret is the most load and volume jointing part in the casting equipments. It's making up of revolving arm,thrust-axletree,foundation. For the safety, needing every parts have enough intensity and rigidity.To take a basis of the dishing ladle helicoid dado for the square-circle castings BinXin Steel Iron Works. This direction is involved in many respects including drive scheme device ,Construvtion and size of helicoid dado, main pare parts calibration, motor, reduction gear, aircylinder, and ladle lifting device, locking device, weighing device, cove lifting device, elicit introduced about the concert install, lubrication and operation.Key words: casting equipment,dishing ladle helicoid dado, drive scheme, helicoid dado configurable.目录摘要 (II)Abstract (III)1 绪论 (1)1.1 国内外连铸机术的发展及我国与世界连铸技术的差距 (1)1.2 连铸机的主要设备及分类 (3)1.3 连铸机钢包旋转 (7)1.3.1 钢包旋转台的形式 (7)1.3.2 钢包旋转台的主要结构特点 (8)1.3.3 各类连铸机钢包回转台的特点 (9)1.4 钢包回转台的组成 (11)1.5 钢包回转台的工作特点 (12)2 初步确定方案 (13)2.1 已知条件 (13)2.1.1 设计题目 (13)2.1.2 技术参数及性能 (13)2.2 方案的总体布置形式 (13)2.3 回转台具体部件设计方案的确定 (13)2.3.1 钢包旋转驱动方式 (13)2.3.2 锁紧方式 (14)2.3.3 钢包盖的升降装置 (15)2.3.4 长水口机械手动作方式 (15)2.3.5 钢包升降驱动方案 (15)3 电机的计算与选择 (17)3.1钢包回转功率的计算 (17)3.1.1 基本数据的计算 (17)3.1.2 情况Ⅰ的回转功率计算 (19)3.1.3 情况Ⅱ的回转功率计算 (19)3.1.4 情况Ⅲ的回转功率计算 (20)3.2 电动机和电气马达的选择 (21)3.2.1 电动机的选择: (21)3.2.2马达的选择 (22)3.3 减速器的设计 (22)3.3.1 确定减速器的结构 (22)3.3.2 传动比的计算和分配,计算传动装置的运动和动力参数 (23)3.3.3 齿轮的设计 (24)3.3.4 轴的设计 (30)3.3.5 减速器箱体的结构尺寸 (39)4 回转台主要构件分析 (40)4.1 对回转臂进行分析 (40)4.2 滚柱回转支承 (40)4.2.1 径向滚柱的分析 (41)4.2.2 轴向滚柱的分析 (42)4.3 地脚螺栓设计与计算 (43)4.3.1 选择材料 (43)4.3.2 确定螺栓的基本数据 (43)5 销齿传动的设计与计算 (45)T (45)5.1 销轮轴转矩35.2 选材及许用应力的确定 (45)5.2.1 材料的选择 (45)5.3 销齿直径确定 (46)5.4 校核齿轮弯曲强度 (47)5.5 确定尺寸 (47)6 钢包旋转台的加盖装置的设计 (48)7 称量传感器的形式选择与容量计算 (49)8 地脚螺栓的设计与计算 (50)8.1 选材及尺寸确定 (50)8.2 螺栓工作负荷的确定 (50)9 钢包回转台设备安装、使用和维护 (52)9.1 一些设备的安装 (52)9.1.1 滚柱旋转轴承的使用方法以及安装 (52)9.1.2 提升缸的安装与拆卸 (52)9.2 钢包回转台的使用和维护 (52)总结 (54)参考文献 (55)外文资料 (56)中文翻译 (61)致谢 (65)1 绪论1.1 国内外连铸机术的发展及我国与世界连铸技术的差距把高温钢水连续不断地浇铸成具有一定断面形状和一定尺寸规格铸坯的生产工艺过程叫做连续铸钢。
完成这一过程所需的设备叫连铸成套设备。
浇钢设备、连铸机本体设备、切割区域设备、引锭杆收集及输送设备的机电液一体化构成了连续铸钢核心部位设备,习惯上称为连铸机。
在钢铁厂生产各类钢铁产品过程中,使用钢水凝固成型有两种方法:传统的模铸法和连续铸钢法。
而在二十世纪五十年代在欧美国家出现的连铸技术是一项把钢水直接浇注成形的先进技术。
与传统方法相比,连铸技术具有大幅提高金属收得率和铸坯质量,节约能源等显著优势。
自从20世纪50年代,连续铸钢技术进入工业性应用阶段后,不同类型、不同规格的连铸机及其成套设备应运而生。
20世纪70年代以后,连铸技术发展迅猛,特别是板、方坯连铸机的发展对加速连铸技术替代传统的模铸技术起到了决定性作用。
连铸坯的吨数与总铸坯(锭)的吨数之比叫做连铸比,它是衡量一个国家或一个钢铁企业生产发展水平的重要标志之一,也是连铸设备、工艺、管理以及和连铸有关的各生产环节发展水平的综合体现。
1970年至1980年,世界平均连铸比从4.4%发展到28.4%,中国的连铸比从2.1%发展到6.2%;至1990年,世界和中国的连铸比分别发展到62.8%和22.4%;到2001年,又分别发展到87.6%和92.0%。
2003年,中国连铸比达到95.3%左右,估计世界平均连铸比2003年接近90%。
从统计数字可以看出,中国的连铸技术在近10多年内得到了迅速发展。
世界上有许多连铸技术实力较强的公司,如西马克·德马格、奥钢联、日本JSP公司、达涅利(包括戴维)公司等。
以板坯连铸机为例,西马克·德马格公司从1962年至2001年新设计和改造板坯连铸机共约370台;奥钢联从1959年至2000年新建和改造板坯连铸机共约181台;日本JSP公司截止2001年新建并改造板坯连铸机共约150台;达涅利的戴维公司也设计了10多台连铸机。
2001年末,世界上共有各类投产的板坯连铸机约550台800流(有一些是重复改造的,按估计值未计入)。
截止到2002年底,中国共有551台(1749流)连铸机,其中板、方坯连铸机分别为101台(130流)、429台(1564流),圆坯、异形坯连铸机分别为20台(52流)、1台(3流)。
这些统计中,绝大部分连铸机是立足于中国国内设计制造的。
我国加入WTO后,人才、知识、科技与经济的全球化趋势越来越清晰地展现出来。
由于历史及其他各方面原因,国外先进技术和管理方式显然具有竞争优势。
近几年,我国经济发展较快,冶金企业投放的技改资金比较大,新上项目很多,连续铸钢项目也较多,但连铸机设备和技术大部分还是靠引进。
我国薄板坯连铸连轧已经引进了将近10条生产线;从2000年开始,我国先后全部引进或引进核心部位设备与技术的常规板坯连铸机共有24台27流,还有继续引进的趋势;中薄板坯连铸机、异型坯连铸机全部引进;大方坯连铸机也有引进的倾向。
其原因主要是我国连铸技术与国外先进水平还存在一定差距。
新材料是钢铁工业的永远追求,进入21世纪后,以高新技术为先导的“产业革命”在材料领域出现了一些令人瞩目的新现象,神奇的纳米材料可能孕育着社会经济的巨大变革,新材料是高新技术的基础。
作为连续铸钢,就是要提高无缺陷坯的比率,在连铸工艺、设备和生产操作等多方面下功夫。
连铸产品合格率不仅仅取决于连铸机本身,由于连铸工艺的特殊性,需要进行浇铸的钢种往往对钢水的成分、夹渣、气体含量、温度有一定的要求。
因此,连铸前工序的炉外精炼技术从20世纪80年代受到连铸工艺的重视之后,在90年代已成为必不可少的手段连铸技术发展应关注的问题近终形和传统断面的板坯连铸机各有千秋,很多人把薄板坯、中厚板坯连铸机也称作近终形板坯连铸机。
目前近终形板坯连铸连轧工艺还有较大的发展空间,但这类连铸连轧工艺的发展重点还是扩大产品品种,提高产品质量。
过去曾有人认为,近终形连铸连轧工艺的出现将大量地取代传统断面的板坯连铸机和热连轧机。
然而,由于钢种、产品用途、产品质量的实际情况,传统断面的板坯连铸机不但不会被近终形连铸连轧工艺大量代替,而且还会继续向前发展。
连铸机的高效化改造今后若干年,新增连铸机的势头将会明显减弱,正在生产的连铸机的高效化改造会越来越多。
不论是新建连铸机,还是老连铸机的改造,人们不会单一地追求高拉速、高产量,而综合经济效益、投入与产出的水平将成为连铸机高效化的基本准则。