疲劳寿命计算
滚动轴承寿命计算公式
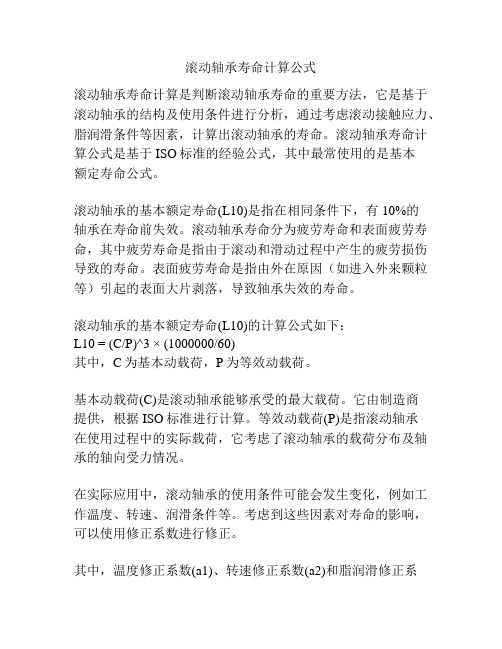
滚动轴承寿命计算公式滚动轴承寿命计算是判断滚动轴承寿命的重要方法,它是基于滚动轴承的结构及使用条件进行分析,通过考虑滚动接触应力、脂润滑条件等因素,计算出滚动轴承的寿命。
滚动轴承寿命计算公式是基于ISO标准的经验公式,其中最常使用的是基本额定寿命公式。
滚动轴承的基本额定寿命(L10)是指在相同条件下,有10%的轴承在寿命前失效。
滚动轴承寿命分为疲劳寿命和表面疲劳寿命,其中疲劳寿命是指由于滚动和滑动过程中产生的疲劳损伤导致的寿命。
表面疲劳寿命是指由外在原因(如进入外来颗粒等)引起的表面大片剥落,导致轴承失效的寿命。
滚动轴承的基本额定寿命(L10)的计算公式如下:L10 = (C/P)^3 × (1000000/60)其中,C为基本动载荷,P为等效动载荷。
基本动载荷(C)是滚动轴承能够承受的最大载荷。
它由制造商提供,根据ISO标准进行计算。
等效动载荷(P)是指滚动轴承在使用过程中的实际载荷,它考虑了滚动轴承的载荷分布及轴承的轴向受力情况。
在实际应用中,滚动轴承的使用条件可能会发生变化,例如工作温度、转速、润滑条件等。
考虑到这些因素对寿命的影响,可以使用修正系数进行修正。
其中,温度修正系数(a1)、转速修正系数(a2)和脂润滑修正系数(a3)是常见的修正系数。
它们表示滚动轴承在不同工况下寿命与基本额定寿命之间的比值。
修正后的寿命(L)可以根据以下公式计算:L = L10 × a1 × a2 × a3同时,还有其他一些公式可以用于计算滚动轴承的寿命,例如基本动载荷的计算公式和等效载荷的计算公式。
这些公式可以根据具体的应用要求和实际情况进行选择和计算。
综上所述,滚动轴承寿命计算公式是根据滚动轴承的结构和使用条件进行分析的重要方法。
通过计算基本额定寿命和修正系数,可以得到滚动轴承的寿命。
计算公式的准确性和合理性对于滚动轴承的设计和选用非常重要,可以提高轴承的使用寿命和可靠性。
机械结构疲劳寿命评估方法

机械结构疲劳寿命评估方法疲劳是指在循环加载下,材料或结构受到变形和应力的影响,最终导致破坏的现象。
在机械工程中,疲劳问题常常是导致机械结构失效的主要原因之一。
因此,评估机械结构的疲劳寿命是非常重要的。
机械结构的疲劳寿命评估方法有许多种,下面我们将介绍几种常用的方法。
1. Wöhler曲线方法Wöhler曲线方法是疲劳寿命评估的经典方法之一。
该方法通过在不同应力幅水平下进行试验,得出应力幅与疲劳寿命的关系曲线。
通过该曲线,可以根据给定应力水平来预测疲劳寿命。
但是,Wöhler曲线方法的缺点是需要进行大量的试验,成本较高,且所得的曲线只适用于特定材料和加载条件下。
2. 快速计算法快速计算法是评估机械结构疲劳寿命的一种便捷方法。
该方法通过使用一些近似公式和简化的计算步骤来估算疲劳寿命。
这些公式和步骤可以减少试验数量和时间。
然而,快速计算法的准确性不如Wöhler曲线方法高,并且只适用于较简单的加载条件和结构。
3. 应力计数法应力计数法是一种常用的疲劳寿命评估方法。
该方法将应力加载历程分解为若干个循环,然后对每个循环的应力幅进行计数。
根据统计分析,可以得出疲劳寿命。
这种方法相对来说比较简单和实用,但是对于复杂的应力加载历程和结构,计数的准确性可能会受到影响。
4. 有限元分析法有限元分析法是一种基于数值计算的评估方法。
该方法通过将机械结构建模为有限元模型,然后通过求解有限元方程来分析结构的应力和变形状态。
通过分析得到的结果,可以评估疲劳寿命。
有限元分析法具有较高的准确性和灵活性,能够适应不同的材料和复杂的加载条件。
但是,该方法需要较高的计算资源和专业知识,适用性有一定限制。
总之,机械结构疲劳寿命评估方法的选择应根据具体情况而定。
不同的方法具有不同的优缺点和适用范围。
在实际应用中,可以根据结构的复杂性、预算和要求准确性等因素进行评估方法的选择。
同时,为了提高评估的准确性,可以采用多种方法的综合应用。
寿命系数kn计算公式
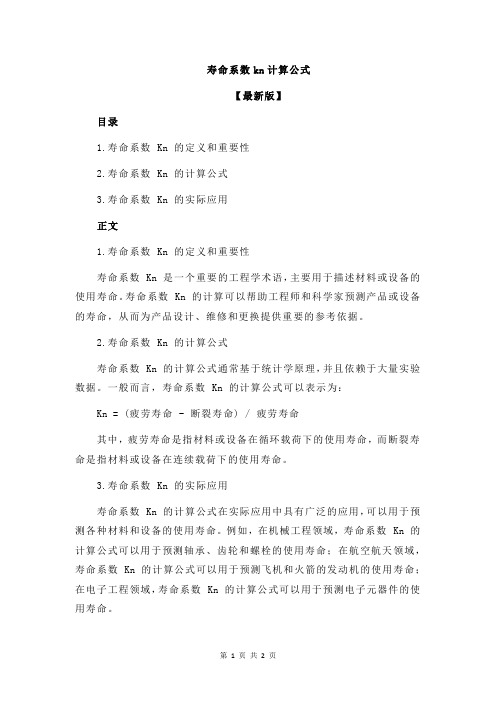
寿命系数kn计算公式
【最新版】
目录
1.寿命系数 Kn 的定义和重要性
2.寿命系数 Kn 的计算公式
3.寿命系数 Kn 的实际应用
正文
1.寿命系数 Kn 的定义和重要性
寿命系数 Kn 是一个重要的工程学术语,主要用于描述材料或设备的使用寿命。
寿命系数 Kn 的计算可以帮助工程师和科学家预测产品或设备的寿命,从而为产品设计、维修和更换提供重要的参考依据。
2.寿命系数 Kn 的计算公式
寿命系数 Kn 的计算公式通常基于统计学原理,并且依赖于大量实验数据。
一般而言,寿命系数 Kn 的计算公式可以表示为:
Kn = (疲劳寿命 - 断裂寿命) / 疲劳寿命
其中,疲劳寿命是指材料或设备在循环载荷下的使用寿命,而断裂寿命是指材料或设备在连续载荷下的使用寿命。
3.寿命系数 Kn 的实际应用
寿命系数 Kn 的计算公式在实际应用中具有广泛的应用,可以用于预测各种材料和设备的使用寿命。
例如,在机械工程领域,寿命系数 Kn 的计算公式可以用于预测轴承、齿轮和螺栓的使用寿命;在航空航天领域,寿命系数 Kn 的计算公式可以用于预测飞机和火箭的发动机的使用寿命;在电子工程领域,寿命系数 Kn 的计算公式可以用于预测电子元器件的使用寿命。
疲劳寿命计算

疲劳分析的数值计算方法及实例第一节引 言零件或构件由于交变载荷的反复作用,在它所承受的交变应力尚未达到静强度设计的许用应力情况下就会在零件或构件的局部位置产生疲劳裂纹并扩展、最后突然断裂。
这种现象称为疲劳破坏。
疲劳裂纹的形成和扩展具有很大的隐蔽性而在疲劳断裂时又具有瞬发性,因此疲劳破坏往往会造成极大的经济损失和灾难性后果。
金属的疲劳破坏形式和机理不同与静载破坏,所以零件疲劳强度的设计计算不能为经典的静强度设计计算所替代,属于动强度设计。
随着机车车辆向高速、大功率和轻量化方向的迅速发展,其疲劳强度及其可靠性的要求也越来越高。
近几年随着我国铁路的不断提速,机车、车辆和道轨等铁路设施的疲劳断裂事故不断发生,越来越引起人们的重视。
疲劳强度设计及其研究正在成为我国高速机车车辆设计制造中的一项不可缺少的和重要的工作。
金属疲劳的研究已有近150年的历史,有相当多的学者和工程技术人员进行了大量的研究,得到了许多关于金属疲劳损伤和断裂的理论及有关经验技术。
但是由于疲劳破坏的影响因素多而复杂并且这些因素互相影响又与构件的实际情况密切相关,使得其应用性成果尚远远不能满足工程设计和生产应用的需要。
据统计,至今有约90%的机械零部件的断裂破坏仍然是由直接于疲劳或者间接疲劳而引起的。
因此,在21世纪的今天,尤其是在高速和大功率化的新产品的开发制造中,其疲劳强度或疲劳寿命的设计十分重要,并且往往需要同时进行相应的试验研究和试验验证。
疲劳断裂是因为在零件或构件表层上的高应力或强度比较低弱的部位区域产生疲劳裂纹,并进一步扩展而造成的。
这些危险部位小到几个毫米甚至几十个微米的范围,零件或构件的几何缺口根部、表面缺陷、切削刀痕、碰磕伤痕及材料的内部缺陷等往往是这种危险部位。
因此,提高构件疲劳强度的基本途径主要有两种。
一种是机械设计的方法,主要有优化或改善缺口形状,改进加工工艺工程和质量等手段将危险点的峰值应力降下来;另一种是材料冶金的方法,即用热处理手段将危险点局部区域的疲劳强度提高,或者是提高冶金质量来减少金属基体中的非金属夹杂等材料缺陷等局部薄弱区域。
钢结构疲劳计算

钢结构疲劳计算
钢结构疲劳计算是指通过一系列的分析和计算,确定钢结构在连续循环加载(如交通载荷、风荷载等)下的疲劳寿命和疲劳极限,从而确保结构的安全性和可靠性。
钢结构疲劳计算主要包括以下几个步骤:
1. 疲劳载荷分析:确定钢结构在实际工况下的受力情况,包括静载荷和动载荷等。
常用的方法有实测、数值模拟和统计分析等。
2. 构件应力分析:基于疲劳载荷分析结果,通过有限元分析或经验公式等方法,计算出各构件的应力情况。
应注意考虑动荷载引起的共振和谐振效应。
3. 疲劳寿命计算:根据Wöhler曲线(疲劳强度与循环次数的关系曲线),将应力历程转化为循环次数,并通过疲劳寿命估算公式计算出构件的疲劳寿命。
4. 疲劳累积损伤计算:针对多次循环载荷的情况,需要进行疲劳累积损伤计算。
常用的方法有矿山方程法、极限状态方程法和累积损伤积分法等。
5. 安全性评估:根据疲劳寿命和疲劳极限计算结果,与设计要求进行比较,评估结构的安全性。
如果结构的疲劳寿命较短,需要采取相应的措施,如加强结构、增加支撑等。
需要注意的是,钢结构疲劳计算是一项较为复杂的工作,需要对结构材料的疲劳性能、荷载特性以及结构形式等进行综合考虑。
因此,在进行钢结构疲劳计算时,应遵循相应的标准规范,采用合适的计算方法,并进行有效的验证和优化。
疲劳寿命计算公式

疲劳寿命计算公式疲劳寿命是指材料在反复加载和卸载的过程中所能承受的最大循环次数,也称为疲劳寿命。
疲劳寿命的计算公式是通过材料的力学性能参数和应力载荷来确定的。
疲劳寿命计算公式的选择取决于应力载荷的类型和作用方向。
下面介绍几种常用的疲劳寿命计算公式。
1.S-N曲线法S-N曲线法是最常用的疲劳寿命计算方法之一、该方法通过实验测定材料在不同应力水平下的疲劳寿命,然后将实验结果绘制成S-N曲线。
这样可以直观地了解材料的疲劳寿命与应力载荷的关系。
根据S-N曲线,可以通过插值或外推的方法来确定特定应力载荷下的疲劳寿命。
2.线性累积损伤法线性累积损伤法是一种基于累积损伤理论的疲劳寿命计算方法。
该方法假设材料在每个循环中都会受到一定的损伤,而疲劳寿命则是所有循环中损伤的累积。
线性累积损伤法通过计算材料在每个循环中的应力载荷和损伤之间的关系,进而推导出疲劳寿命的计算公式。
3.应力幅与寿命关系应力幅与寿命关系是一种常见的疲劳寿命计算方法。
该方法通过实验测定不同应力幅下的疲劳寿命,然后根据实验数据来拟合出应力幅与寿命之间的关系。
这种方法适用于单一应力幅循环下的疲劳寿命计算。
4. Miner线性累积疲劳损伤法Miner线性累积疲劳损伤法是一种基于疲劳损伤的累积理论的疲劳寿命计算方法。
该方法认为材料的疲劳寿命是各个应力循环造成的疲劳损伤之和。
通过计算不同应力循环下的疲劳损伤,然后将其累积起来,可以得到材料的疲劳寿命。
不同的疲劳寿命计算公式适用于不同的应力载荷和材料类型。
在实际工程应用中,需要根据具体情况选择合适的计算方法,并结合实验数据进行验证。
此外,疲劳寿命计算还需要考虑材料的表面处理、应力状态、温度和环境等因素的影响。
疲劳-总寿命法

ε
' f
2N f
c
∆ε
p
/
2是塑性应变幅值,ε
' f
是疲劳延展性常数(对于多
数金属 ≈ ε f-实际的断裂延展性),c是疲劳延展性
常数(许多金属-0.5到-0.7)。
疲劳与断裂
21
疲劳设计法
通常方法
通常来讲,应用哪个方程?(应力寿命或者应变 寿命法)?全更迭中,应变控制载荷。总应变由弹性 和塑性部分组成,即
疲劳与断裂
29
疲劳裂纹的阻滞
子弹射击
因为几乎所有的疲劳和应力腐蚀疲劳发生在一 部分表面,所以子弹射击引起的压缩应力使部分寿 命有可观的增长。产生的典型的残余应力至少是射 击后材料屈服强度的一半。
子弹射击的优点是残留压缩应力和表面冷工作 的结果。
疲劳与断裂
30
疲劳裂纹的阻滞
子弹射击
屈服应力:疲劳裂纹增长、腐蚀疲劳、应力腐 蚀裂化、氢化裂化、腐蚀、磨损和气穴引起的侵蚀 而增加的抗力。
应变寿命法
载荷可由塑性应变幅值 ∆ε p / 2 代替应力幅值σ a
描组成述,。可在以这发些现情如况下下的,线如性果关图系由:log⎜⎜⎝⎛
∆ε
2
p
⎟⎟⎠⎞与
log(2
N
f
)
疲劳与断裂
20
疲劳设计法
应变寿命法
下面的关系式(Coffin-Manson,1955年)描述了
该行为:
( ) ∆ε p 2
=
∆ε = ∆εe + ∆ε p
22 2
Coffin-Manson表达式可用∆ε p / 2表达。∆εe / 2呢?
疲劳与断裂
22
疲劳设计法
疲劳寿命计算公式实例
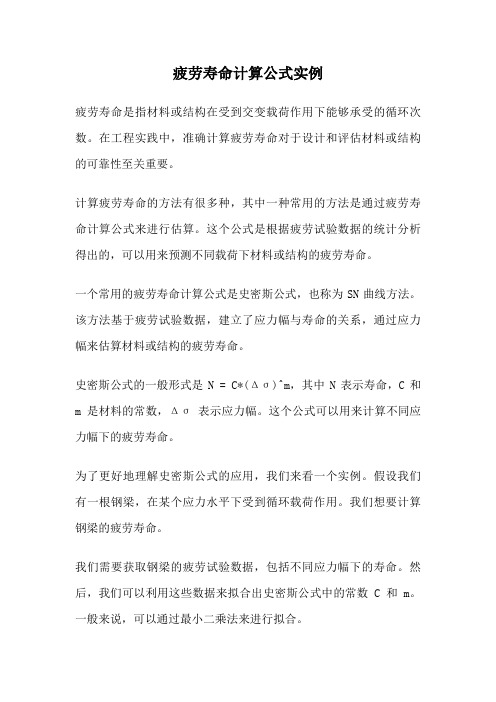
疲劳寿命计算公式实例疲劳寿命是指材料或结构在受到交变载荷作用下能够承受的循环次数。
在工程实践中,准确计算疲劳寿命对于设计和评估材料或结构的可靠性至关重要。
计算疲劳寿命的方法有很多种,其中一种常用的方法是通过疲劳寿命计算公式来进行估算。
这个公式是根据疲劳试验数据的统计分析得出的,可以用来预测不同载荷下材料或结构的疲劳寿命。
一个常用的疲劳寿命计算公式是史密斯公式,也称为SN曲线方法。
该方法基于疲劳试验数据,建立了应力幅与寿命的关系,通过应力幅来估算材料或结构的疲劳寿命。
史密斯公式的一般形式是N = C*(Δσ)^m,其中N表示寿命,C和m是材料的常数,Δσ表示应力幅。
这个公式可以用来计算不同应力幅下的疲劳寿命。
为了更好地理解史密斯公式的应用,我们来看一个实例。
假设我们有一根钢梁,在某个应力水平下受到循环载荷作用。
我们想要计算钢梁的疲劳寿命。
我们需要获取钢梁的疲劳试验数据,包括不同应力幅下的寿命。
然后,我们可以利用这些数据来拟合出史密斯公式中的常数C和m。
一般来说,可以通过最小二乘法来进行拟合。
完成拟合后,我们就可以利用史密斯公式来计算不同应力幅下钢梁的疲劳寿命了。
假设在某个应力幅下,Δσ为100MPa,我们可以代入公式计算出对应的寿命N。
需要注意的是,史密斯公式是一种经验公式,其适用范围有限。
在实际应用中,我们还需要考虑其他因素,如材料的裂纹敏感性、环境条件等。
疲劳寿命的计算还可以使用其他方法,如线性累积损伤法、极限状态法等。
这些方法在不同情况下有不同的适用性,需要根据具体情况选择合适的方法。
总结起来,疲劳寿命的计算是工程实践中一个重要的问题。
通过疲劳寿命计算公式,我们可以预测材料或结构在不同应力幅下的疲劳寿命。
然而,需要注意的是,公式的适用性有限,实际应用时需要综合考虑其他因素。
在进行疲劳寿命计算时,我们还可以借鉴其他方法,以提高计算的准确性和可靠性。
轴体机械寿命计算公式
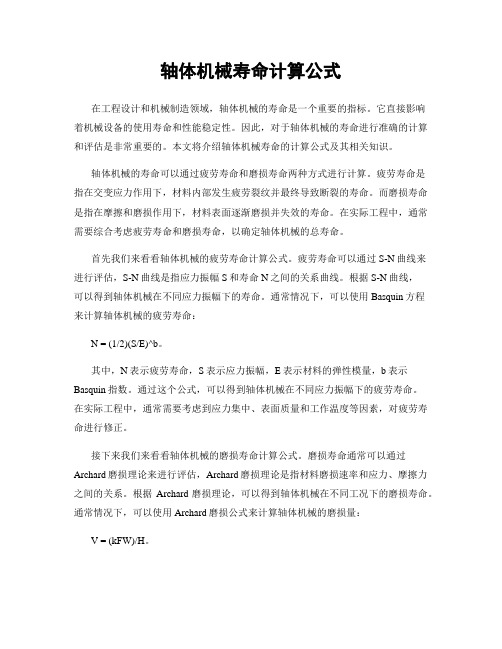
轴体机械寿命计算公式在工程设计和机械制造领域,轴体机械的寿命是一个重要的指标。
它直接影响着机械设备的使用寿命和性能稳定性。
因此,对于轴体机械的寿命进行准确的计算和评估是非常重要的。
本文将介绍轴体机械寿命的计算公式及其相关知识。
轴体机械的寿命可以通过疲劳寿命和磨损寿命两种方式进行计算。
疲劳寿命是指在交变应力作用下,材料内部发生疲劳裂纹并最终导致断裂的寿命。
而磨损寿命是指在摩擦和磨损作用下,材料表面逐渐磨损并失效的寿命。
在实际工程中,通常需要综合考虑疲劳寿命和磨损寿命,以确定轴体机械的总寿命。
首先我们来看看轴体机械的疲劳寿命计算公式。
疲劳寿命可以通过S-N曲线来进行评估,S-N曲线是指应力振幅S和寿命N之间的关系曲线。
根据S-N曲线,可以得到轴体机械在不同应力振幅下的寿命。
通常情况下,可以使用Basquin方程来计算轴体机械的疲劳寿命:N = (1/2)(S/E)^b。
其中,N表示疲劳寿命,S表示应力振幅,E表示材料的弹性模量,b表示Basquin指数。
通过这个公式,可以得到轴体机械在不同应力振幅下的疲劳寿命。
在实际工程中,通常需要考虑到应力集中、表面质量和工作温度等因素,对疲劳寿命进行修正。
接下来我们来看看轴体机械的磨损寿命计算公式。
磨损寿命通常可以通过Archard磨损理论来进行评估,Archard磨损理论是指材料磨损速率和应力、摩擦力之间的关系。
根据Archard磨损理论,可以得到轴体机械在不同工况下的磨损寿命。
通常情况下,可以使用Archard磨损公式来计算轴体机械的磨损量:V = (kFW)/H。
其中,V表示磨损量,k表示磨损系数,F表示摩擦力,W表示工作时间,H 表示材料的硬度。
通过这个公式,可以得到轴体机械在不同工况下的磨损寿命。
在实际工程中,通常需要考虑到润滑情况、表面处理和工作环境等因素,对磨损寿命进行修正。
最后,我们来综合考虑疲劳寿命和磨损寿命,得到轴体机械的总寿命。
一般情况下,可以使用Palmgren-Miner线性累积损伤理论来进行综合评估。
疲劳度 公式
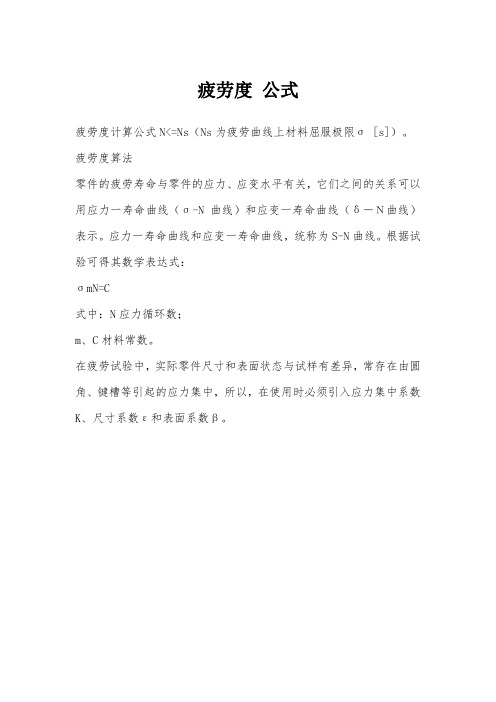
疲劳度公式
疲劳度计算公式N<=Ns(Ns为疲劳曲线上材料屈服极限σ [s])。
疲劳度算法
零件的疲劳寿命与零件的应力、应变水平有关,它们之间的关系可以用应力一寿命曲线(σ-N曲线)和应变一寿命曲线(δ-Ν曲线)表示。
应力一寿命曲线和应变一寿命曲线,统称为S-N曲线。
根据试验可得其数学表达式:
σmN=C
式中:N应力循环数;
m、C材料常数。
在疲劳试验中,实际零件尺寸和表面状态与试样有差异,常存在由圆角、键槽等引起的应力集中,所以,在使用时必须引入应力集中系数K、尺寸系数ε和表面系数β。
疲劳寿命的计算流程
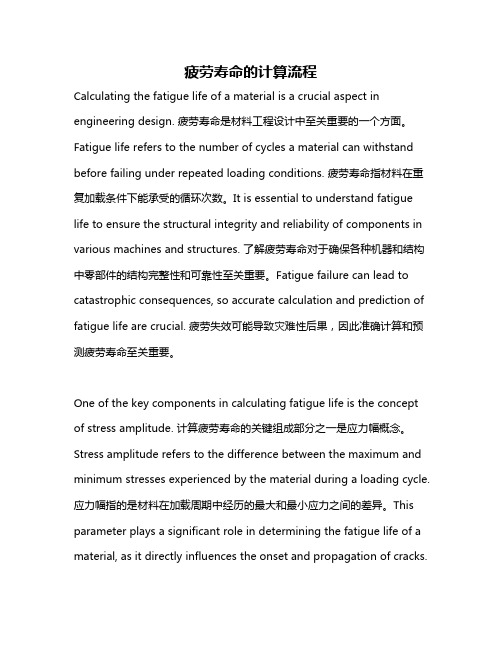
疲劳寿命的计算流程Calculating the fatigue life of a material is a crucial aspect in engineering design. 疲劳寿命是材料工程设计中至关重要的一个方面。
Fatigue life refers to the number of cycles a material can withstand before failing under repeated loading conditions. 疲劳寿命指材料在重复加载条件下能承受的循环次数。
It is essential to understand fatigue life to ensure the structural integrity and reliability of components in various machines and structures. 了解疲劳寿命对于确保各种机器和结构中零部件的结构完整性和可靠性至关重要。
Fatigue failure can lead to catastrophic consequences, so accurate calculation and prediction of fatigue life are crucial. 疲劳失效可能导致灾难性后果,因此准确计算和预测疲劳寿命至关重要。
One of the key components in calculating fatigue life is the concept of stress amplitude. 计算疲劳寿命的关键组成部分之一是应力幅概念。
Stress amplitude refers to the difference between the maximum and minimum stresses experienced by the material during a loading cycle. 应力幅指的是材料在加载周期中经历的最大和最小应力之间的差异。
等效疲劳寿命计算公式
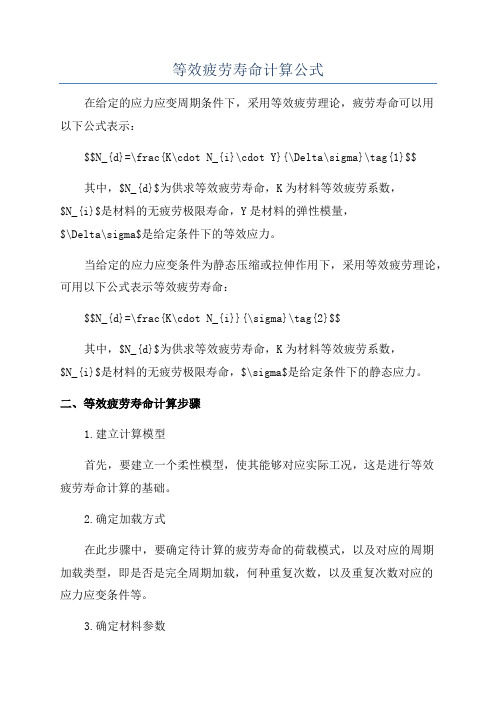
等效疲劳寿命计算公式
在给定的应力应变周期条件下,采用等效疲劳理论,疲劳寿命可以用
以下公式表示:
$$N_{d}=\frac{K\cdot N_{i}\cdot Y}{\Delta\sigma}\tag{1}$$
其中,$N_{d}$为供求等效疲劳寿命,K为材料等效疲劳系数,
$N_{i}$是材料的无疲劳极限寿命,Y是材料的弹性模量,
$\Delta\sigma$是给定条件下的等效应力。
当给定的应力应变条件为静态压缩或拉伸作用下,采用等效疲劳理论,可用以下公式表示等效疲劳寿命:
$$N_{d}=\frac{K\cdot N_{i}}{\sigma}\tag{2}$$
其中,$N_{d}$为供求等效疲劳寿命,K为材料等效疲劳系数,
$N_{i}$是材料的无疲劳极限寿命,$\sigma$是给定条件下的静态应力。
二、等效疲劳寿命计算步骤
1.建立计算模型
首先,要建立一个柔性模型,使其能够对应实际工况,这是进行等效
疲劳寿命计算的基础。
2.确定加载方式
在此步骤中,要确定待计算的疲劳寿命的荷载模式,以及对应的周期
加载类型,即是否是完全周期加载,何种重复次数,以及重复次数对应的
应力应变条件等。
3.确定材料参数
在此步骤中,要确定待计算的疲劳寿命所需的材料参数,如等效疲劳系数K。
叶片疲劳寿命计算简介19页文档
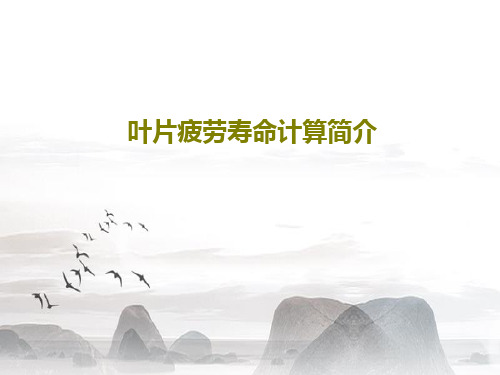
积累损伤
叶片疲劳寿 命
工作进展
•Neuber法验证
➢中心孔板(《结构疲劳寿命分析》,P129-136)
16
工作进展
载荷谱
循环σ-ε曲线
17
工作进展
加载 次数
1 2 3 4 5 6 7 8
局部应力应变计算结果
局部应力 /MPa(书)
263.46 -61.74 402.30
局部应力 局部应变 /MPa(报告) /%(书)
载荷谱
10
疲劳损伤积 累理论
积累损伤
叶片疲劳寿 命
局部应力应变法
• 三大内容:
载荷谱
材料疲劳性 能
循环σ-ε曲 线
材料的ε-N 曲线
疲劳损伤积 累理论
疲劳损伤积 累理论
叶片结构应 力分析
危险部位的 名义应力谱
危险部位的 局部应力应
变谱
积累损伤
叶片几何尺 寸
11
叶片危险部位的 应力应变历程
叶片疲劳寿 命
局部应力应变法
•叶片危险部位的应力应变历程:
叶片结构应 力分析
采用有限元软件进行三维稳态应力分析
气流激振力 工程计算方法或三维流场获得气流激振力
危险部位的 名义应力谱
采用有限元软件进行三维非稳态应力分析 或进行流固耦合分析
危险部位的 局部应力应
变谱
(1)试验方法;(2)弹塑性有限元法; (3)近似计算方法,Neuber法
12
局部应力应变法 • 材料疲劳性能:
循环σ-ε曲 线
13
局部应力应变法 • 材料疲劳性能:
材料的ε-N 曲线
14
工作进展
FEA和CFD
载荷谱
循环σ-ε曲 线
螺栓疲劳寿命计算
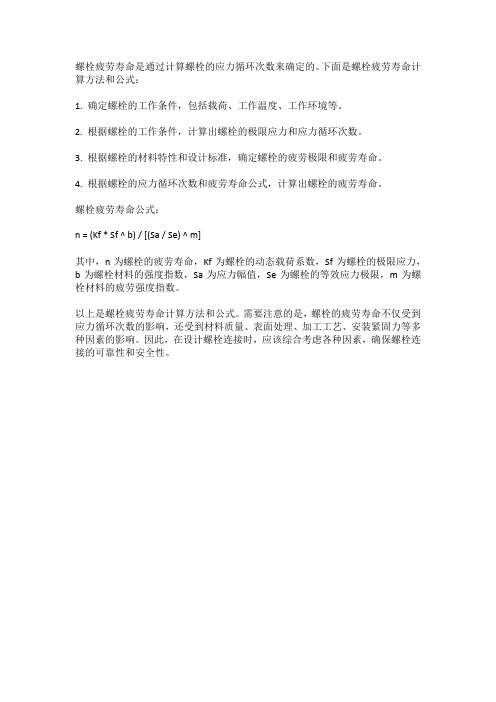
螺栓疲劳寿命是通过计算螺栓的应力循环次数来确定的。
下面是螺栓疲劳寿命计算方法和公式:
1. 确定螺栓的工作条件,包括载荷、工作温度、工作环境等。
2. 根据螺栓的工作条件,计算出螺栓的极限应力和应力循环次数。
3. 根据螺栓的材料特性和设计标准,确定螺栓的疲劳极限和疲劳寿命。
4. 根据螺栓的应力循环次数和疲劳寿命公式,计算出螺栓的疲劳寿命。
螺栓疲劳寿命公式:
n = (Kf * Sf ^ b) / [(Sa / Se) ^ m]
其中,n为螺栓的疲劳寿命,Kf为螺栓的动态载荷系数,Sf为螺栓的极限应力,b为螺栓材料的强度指数,Sa为应力幅值,Se为螺栓的等效应力极限,m为螺栓材料的疲劳强度指数。
以上是螺栓疲劳寿命计算方法和公式。
需要注意的是,螺栓的疲劳寿命不仅受到应力循环次数的影响,还受到材料质量、表面处理、加工工艺、安装紧固力等多种因素的影响。
因此,在设计螺栓连接时,应该综合考虑各种因素,确保螺栓连接的可靠性和安全性。
金属寿命计算

金属寿命计算通常涉及多个因素,包括金属材料的疲劳强度、应力幅值、平均应力等。
在金属疲劳计算公式的基本形式中,N表示疲劳寿命,C是一个常数,σf是金属材料的疲劳强度,σa是施加在金属构件上的应力幅值,m是一个与材料性质相关的指数。
这个公式可以用来估计给定应力幅值和材料性质下的金属疲劳寿命。
此外,S-N(Stress-Life)疲劳寿命预测方法是一种反映应力幅值与疲劳寿命之间关系的模型。
Basquin模型是S-N曲线的一种形式,它考虑了应力幅值作为寿命的控制量,并给出了等寿命曲线。
这些曲线可以用来估计在不同平均应力和不同应力幅下的材料寿命。
除了这些基本的疲劳寿命模型,还有许多其他因素也会影响金属的寿命,如微结构、尺寸效应、表面处理以及载荷频率等。
因此,要建立完备的寿命模型是一大难题。
总的来说,金属寿命计算需要综合考虑多种因素,并可能需要借助于专业的软件工具进行复杂的分析和计算。
如果您对这方面有需求,可以进一步咨询相关领域的专家获取更准确的信息。
等效疲劳寿命计算公式

等效疲劳寿命计算公式1、 [公式] (Stre-Life) 疲劳寿命预测方法[公式]寿命估计本质就是反映了应力幅值与疲劳寿命之间的关系,科学家们发现[公式]与[公式]呈幂指数关系:[公式](1)[公式](2)综合(1)(2)可以估计不同平均应力和不同应力幅下的材料寿命。
除了上述影响因素,微结构、尺寸效应、表面处理以及载荷频率等因素对寿命都有影响,因此,如何建立完备的寿命模型一直是一大难题。
2、 [公式] (Strain-Life) 疲劳寿命预测方法2、1、应变控制下材料的行为低周疲劳测试时,局部的应力将超过屈服应力,从而产生塑性区。
对于大多数金属材料,其单调应力应变 [公式] 关系满足Ramberg-Ogood表达式:[公式](3)其中[公式]分别为弹性、塑性应变,[公式]均为材料常数。
由该表达式可见,当材料屈服后,应力与应变呈指数关系,应变微小的变化对应着应力极大的变化,因此多采用应变控制,这也是[公式]方法诞生的主要原因。
[公式](4)其中,[公式]为循环材料常数。
由于是增量表达式,因此需要确定其中一参考点的坐标,才能确定曲线上各点的值。
值得注意的是,由于上述表达式刻画的是整个曲线,即加载和卸载满足相同的表达式。
在稳定迟滞环的基础上,开展应变控制下疲劳寿命的预测。
2、2、疲劳寿命预测模型应变控制下的疲劳寿命预测模型与应力控制相似,只是需要分弹性与塑性两部分,其表达式为:[公式](5)该表达式也被成为Manon-Coffin模型,式中 [公式] 都是与疲劳相关的材料常数。
!注意在应变控制的寿命预测公式中,括号内不再写成[公式] 而是以 [公式] 代替,这是因为如果幅值不是恒定的,常常没有正弦波形如 [公式] 的循环(cycle),因此以转折(reveral)来代替,两个reveral表示一个循环,在式中写作 [公式]。
平均应变同样会对寿命预测产生影响,Morrow做出了如下的修正:[公式](6)总体来说应变控制的疲劳模型与应力控制思路相似,也是以幅值作为主要的控制量,再根据实际情况加以修正。
- 1、下载文档前请自行甄别文档内容的完整性,平台不提供额外的编辑、内容补充、找答案等附加服务。
- 2、"仅部分预览"的文档,不可在线预览部分如存在完整性等问题,可反馈申请退款(可完整预览的文档不适用该条件!)。
- 3、如文档侵犯您的权益,请联系客服反馈,我们会尽快为您处理(人工客服工作时间:9:00-18:30)。
疲劳分析的数值计算方法及实例第一节引 言零件或构件由于交变载荷的反复作用,在它所承受的交变应力尚未达到静强度设计的许用应力情况下就会在零件或构件的局部位置产生疲劳裂纹并扩展、最后突然断裂。
这种现象称为疲劳破坏。
疲劳裂纹的形成和扩展具有很大的隐蔽性而在疲劳断裂时又具有瞬发性,因此疲劳破坏往往会造成极大的经济损失和灾难性后果。
金属的疲劳破坏形式和机理不同与静载破坏,所以零件疲劳强度的设计计算不能为经典的静强度设计计算所替代,属于动强度设计。
随着机车车辆向高速、大功率和轻量化方向的迅速发展,其疲劳强度及其可靠性的要求也越来越高。
近几年随着我国铁路的不断提速,机车、车辆和道轨等铁路设施的疲劳断裂事故不断发生,越来越引起人们的重视。
疲劳强度设计及其研究正在成为我国高速机车车辆设计制造中的一项不可缺少的和重要的工作。
金属疲劳的研究已有近150年的历史,有相当多的学者和工程技术人员进行了大量的研究,得到了许多关于金属疲劳损伤和断裂的理论及有关经验技术。
但是由于疲劳破坏的影响因素多而复杂并且这些因素互相影响又与构件的实际情况密切相关,使得其应用性成果尚远远不能满足工程设计和生产应用的需要。
据统计,至今有约90%的机械零部件的断裂破坏仍然是由直接于疲劳或者间接疲劳而引起的。
因此,在21世纪的今天,尤其是在高速和大功率化的新产品的开发制造中,其疲劳强度或疲劳寿命的设计十分重要,并且往往需要同时进行相应的试验研究和试验验证。
疲劳断裂是因为在零件或构件表层上的高应力或强度比较低弱的部位区域产生疲劳裂纹,并进一步扩展而造成的。
这些危险部位小到几个毫米甚至几十个微米的范围,零件或构件的几何缺口根部、表面缺陷、切削刀痕、碰磕伤痕及材料的内部缺陷等往往是这种危险部位。
因此,提高构件疲劳强度的基本途径主要有两种。
一种是机械设计的方法,主要有优化或改善缺口形状,改进加工工艺工程和质量等手段将危险点的峰值应力降下来;另一种是材料冶金的方法,即用热处理手段将危险点局部区域的疲劳强度提高,或者是提高冶金质量来减少金属基体中的非金属夹杂等材料缺陷等局部薄弱区域。
在解决实际工程问题时,往往需要结合运用以上两种方法进行疲劳强度设计和研究。
合理地利用各种提高疲劳强度的手段,可以有效地提高构件的疲劳强度或延长其疲劳寿命,并起到轻量化的作用。
关于疲劳问题的研究,基本上可分为疲劳裂纹的形成和扩展机理、规律方面的基础性研究和疲劳强度设计以及提高疲劳强度的有效途径等应用性研究。
应用性研究虽然借鉴了基础性研究的成果,但因为它需要考虑更多的实际影响因素,所以它的研究更为复杂和困难。
因此相比之下关于疲劳寿命的预测和疲劳强度设计等应用性研究要少得多,远远落后于实际工程的需求。
过去,疲劳强度设计和寿命预测的研究主要是以试验为基础进行的。
随着计算机应用技术和有限元数值计算理论及其应用的迅速发展,现在又兴起了基于大量试验数据的疲劳强度设计和寿命计算的有限元数值计算方法,有力地推动着零部件疲劳强度设计的研究及应用的发展。
当前,业已发展形成了专用的疲劳分析软件,如MSC/FA TIGUE 等。
此外许多著名的有限元分析软件也嵌套有功能较为齐全的疲劳强度计算模块,如MARC ,ANSYS ,以及I-Deas 中的CAE 等。
这些软件疲劳强度计算模块的细节虽然不尽相同,但是其基本思路与算法大都相似。
本章将阐述疲劳强度设计的基本概念、疲劳强度的主要影响因素、疲劳强度设计的有关理论、基本设计方法等。
最后,还将对疲劳强度分析的实例进行介绍。
第二节 疲劳载荷类型与S-N 曲线:一、疲劳载荷的类型与基本术语使零件或构件发生疲劳破坏的动载荷称为疲劳载荷,可分为为两类。
一类是其大小和正负方向随时间周期性地变化的交变载荷,另一类是大小和正负方向随时间随机变化的随机载荷。
交变载荷又称为循环载荷,是最为简单和基本的疲劳载荷形式。
所研究结构部位因交变载荷引起的应力称为交变应力。
图14-1(a)是一个典型的交变应力-时间的变化历程。
图中循环应力的大小和正负方(拉压)向随着时间的变化而作周期性的变化。
一个周期的应力变化过程称为一个应力循环。
应力循环特点可用循环中的最大应力σmax 、最小应力σmin 和周期T(或频率f=1/T)来描述。
因为最大应力和最小应力的绝对值相等而正负号相反,故称这种交变载荷为对称循环应力。
典型的循环载荷如圆轴类杆件的旋转弯曲、轴向拉压和平板零件的双向弯曲等,都可以在零件的表面或内部产生这样的交变应力。
另外,轴类零件的双向扭转也可以产生类似的交变应力。
图14-1(a) 对称循环交变载荷图14-1(b) 不对称循环交变载荷在疲劳载荷的描述中经常使用应力幅σa 和应力范围△σ(也称为应力振幅、应力幅度)的概念,定义如下。
(14-1)(14-2) 应力幅σa 反映了交变应力在一个应力循环中变化大小的程度,它是使金属构件发生疲a σσσσ2=-=∆min max 2min max a σσσ-=劳破坏的根本原因。
当研究的部位除承受有动载荷外,还有静载分量荷时,动静载荷的共同作用下的应力-时间变化曲线如图14-1(b)所示。
此时的载荷时间-变化曲线相当于把图14-1(a)的对称循环应力曲线向上平移一个了静应力分量。
这种的循环载荷称为不对称循环载荷,并用最小应力与最大应力的比值R 来描述循环应力的不对称程度,R 称为应力比,有时又称为不对称系数,即(14-4)由定义可知,当R =-1时的循环应力即为对称循环应力,当R ≠0时统称不对称循环应力。
其中,R =0时为拉伸脉动应力,R =-∞时为压缩脉动循环。
循环应力中的静载分量通常称为平均应力,用σm 表示,可由下式求出。
(14-5) 静载分量或平均应力对构件的疲劳强度有一定的影响。
压缩平均应力往往提高构件的疲劳强度,而拉伸平均应力往往降低构件的疲劳强度。
因此,在疲劳强度和疲劳寿命的研究中,给定一个循环应力水平时,需要同时给出应力幅σa 和应力比R 、或者同时给出最大应力σmax 和平均应力σm ,也有时直接给出最大应力σmax 和最小应力σmin 来表示循环应力水平。
由以上各式可知,在应力幅、平均应力、应力比、最大应力和最小应力的参数中,只要已知其中的两个便可求出其它。
如当已知σa 、R 时,其它参数便可由下式得到。
(14-6) 或者已知或σa 、σm 时,(14-7)二、材料的S-N 曲线与基本术语一般情况下,材料所承受的循环载荷的应力幅越小,到发生疲劳破断时所经历的应力循环次数越长。
S-N 曲线就是材料所承受的应力幅水平与该应力幅下发生疲劳破坏时所经历的应力循环次数的关系曲线。
S-N 曲线一般是使用标准试样进行疲劳试验获得的。
如图14-2所示,纵坐标表示试样承受的应力幅,有时也表示为最大应力,但二者一般都用σ表示;横坐标表示应力循环次数,常用N f 表示。
为使用方便,在双对数坐标系下S-N 曲线被近似简化成两条直线。
但也有很多情况只对横坐标取对数,此时也常把S-N 曲线近似简化成两条直线。
S-N 曲线中的水平直线部分对应的应力水平就是材料的疲劳极限,其原意为材料经受无max min σσ=R a m a a R R RR R σσσσσσ-+=-=-=1121212min max 2min max m σσσ+=a m a m σσσσσσ-=+=min max图14-2 S-N 疲劳曲线数次应力循环都不发生破坏的应力极限,对钢铁材料此“无限”的定义一般为107次应力循环。
但现代高速疲劳试验机的研究成果表明,即使应力循环次数超过107材料仍然有可能发生疲劳断裂。
不过107次的应力循环次数,对于实际的工程中的疲劳强度设计已经完全能够满足需要。
疲劳极限又称持久极限,对于无缺口的光滑试样,多用σw0表示,而应力比R =-1时的疲劳极限常用σ-1来表示。
某些不锈钢和有色金属的S-N 中没有水平直线部分,此时的疲劳极限都一般定义为108次应力循环下对应的应力幅水平。
疲劳极限是材料抗疲劳能力的重要性能指标,也是进行疲劳强度的无限寿命设计的主要依据。
斜线部分给出了试样承受的应力幅水平与发生疲劳破断时所经历的应力循环次数之间的关系,多用如幂函数的形式表示。
(14-8)式中σ为应力幅或最大应力,N 为达到疲劳破断时的应力循环次数,m ,C 材料常数。
如果给定一个应力循环次数,便可由上式求出或由斜线量出材料在该条件下所能承受的最大应力幅水平。
反之,也可以由一定的工作应力幅求出对应的疲劳寿命。
因为此时试样或材料所能承受的应力幅水平是与给定的应力循环次数相关联的,所以称之为条件疲劳极限,或称为疲劳强度。
斜线部分是零部件疲劳强度的有限寿命设计或疲劳寿命计算的主要依据。
材料或构件到发生疲劳破坏时所经历的应力循环次数称为材料或构件的疲劳寿命,通常它包括疲劳裂纹的萌生寿命与扩展寿命之和。
疲劳裂纹萌生寿命为构件从开始使用到局部区域产生疲劳损伤累积、萌生裂纹时的寿命;裂纹扩展寿命为构件在裂纹萌生后继续使用而导致裂纹扩展达到疲劳破坏时的寿命。
在疲劳强度设计中,疲劳破坏可能被定义为疲劳破断或规定的报废限度。
S-N 曲线又称为应力-寿命曲线,主要用于构件的变形在弹性变形范围内的情形。
一般说来,这种应力状态下的疲劳达到破坏时的循环次数比较高,往往达到106以上,所以这种疲劳又称为高周疲劳。
相对地,达到疲劳破坏的循环次数较低时的疲劳称为低周疲劳,发生低周疲劳时构件在局部位置发生了塑性变形。
近三十年来,对于低周疲劳,基于塑性应变幅εaC N m =σN的疲劳寿命曲线(εa -N)在工程中得到应用。
对于带缺口的零件,其工作载荷变动较大时,在应力集中的局部区域将会发生塑性变形,此时疲劳寿命估算则要求基于应力和基于塑性应变的两种材料疲劳性能曲线。
这种方法目前还不能用于高周疲劳的寿命估算。
第三节、疲劳强度的影响因素通常我们通过手册所获得的S-N 曲线大多是无缺口的标准试样的试验结果。
但是实际零部件的形状、尺寸、表面状态、工作环境和工作载荷的特点都可能大不相同,而这些因素都对零部件的疲劳强度产生很大的影响。
疲劳强度的影响因素可分为力学、冶金学和环境三个方面。
这些因素互相联系影响,使得在疲劳强度设计和疲劳寿命预测时,综合评价这些因素影响变得复杂。
三类因素中,力学因素从根本上讲可归结为应力集中和平均应力的影响;冶金学因素可归纳为冶金质量即材料的纯净度和材料的强度;而环境因素主要有腐蚀介质和高温的影响。
对于铁路车辆零部件大多数的情况是在大气和常温环境下工作的,所以一般情况下应主要考虑力学和冶金学两类因素。
它们包括缺口形状的影响、尺寸的影响、表面状态的影响和平均应力的影响等。
关于这些因素对疲劳极限影响的具体数据相关的经验公式,可查阅有关手册和资料。