高速机床主轴
高档数控机床高速精密电主 轴关键技术及应用 公告

高档数控机床高速精密电主轴关键技术及应用公告全文共四篇示例,供读者参考第一篇示例:高档数控机床高速精密电主轴关键技术及应用随着科技的不断发展,数控机床作为制造业的重要装备之一,正逐渐成为制造业的主力军。
而高档数控机床的核心部件之一——高速精密电主轴,更是决定了整个机床性能和加工质量的关键部件。
本文将重点介绍高档数控机床高速精密电主轴的关键技术及应用。
一、高速精密电主轴的定义和特点高速精密电主轴是数控机床上用于驱动刀具旋转的核心部件,它直接影响了机床的加工精度、效率和稳定性。
一般来说,高速精密电主轴具有以下几个特点:1. 高速转速:高速精密电主轴的工作转速通常在10000rpm以上,甚至可以达到50000rpm以上。
高转速可以提高加工效率,缩短加工周期。
2. 高精度:高速精密电主轴需要具有极高的旋转精度和稳定性,以保证加工的精度和表面质量。
4. 高功率密度:高速精密电主轴需要具有高功率密度,以满足大功率输出的要求,同时尽可能减小轴体体积和重量。
1. 轴承技术:高速精密电主轴的轴承是其最关键的部件之一,直接影响轴的精度、稳定性和寿命。
目前主要采用陶瓷球轴承、陶瓷滚珠轴承和气体轴承等高速轴承技术。
2. 动平衡技术:高速精密电主轴在旋转时会产生不小的离心力,需要采用动平衡技术来消除不平衡导致的振动和噪音。
3. 冷却技术:高速精密电主轴在高速运转时会产生大量热量,需要采用有效的冷却技术来保持轴的温度稳定,避免发热过高导致零部件热变形。
4. 控制技术:高速精密电主轴需要配备精密的控制系统,以实现精准的转速控制、负载检测和自适应控制等功能。
5. 结构设计:高速精密电主轴的结构设计需要考虑到刚性和轻量化的平衡,同时保证轴体的稳定性和可靠性。
高速精密电主轴广泛应用于汽车、航空航天、铁路、军工等领域,主要用于高精度、高效率的加工。
具体应用包括精密零件加工、高速铣削、高速车削、高速钻孔等领域。
目前国内外一些知名数控机床制造商,如哈斯、西铁城、FANUC 等,都大量采用了高速精密电主轴技术,使其生产的数控机床具有更高的加工精度和效率,受到了市场的广泛认可。
高精高速高效的机床功能部件——电主轴

结构紧凑 、安装方便等优点。
电主 轴 的具 体 优 势体 现 在 以下 几点 :
使用不同精度级别的夹具 ,机床不但可以进行粗加
工 ,也 可 以进 行精 加 工 。
( )电主轴是 高精 主轴技术和高速 电动机的 1
结 合 体 ,使 机 床 省 去 了 齿 轮 和 皮 带 等 机 械 传 动 环
的角加 ( )速度 ,以实现主轴的瞬时升降速与准 减
确起 停 的 功 能 。
平。
高速加 工机床的厂家和关键零部件如高速电主轴和
高 速 数 控 系统 的 厂 家 ,且 均 已具 备 一 定 的 基 础 和 实 力。但针对 这一领域 的技 术特点和 发展现 状 ,
需要国家相关主管部 门出台相关的鼓励政策,进行 引导 ,只有这样 ,中国高速加工机床发展的瓶颈才 能被逐一快速解决 ,才能更快更好的服务于国内汽 车 、航空航天、模具等产业 ,提升这些产业的全球 竞争力。 MW ( 收稿 日期 :2 10 1 ) 0 18 9
节 ,使 机 床布 局 更 为 紧凑 合 理 ,同时 机 床 的噪 声可
以大 大 降低 。
( ) 电主 轴 采 用 高精 度 (4 )的 角接 触 球 2 P级 轴 承 ,使 电主 轴 的 输 出 精 度 最 高 达 到05 l .~ m, P 常规 电主 轴 要 求 主 轴 的 径 向 圆 跳 动 小 于 5Pm ,轴 向 窜 动 小 于 2 m。在 实 际生 产 中 ,根 据 工 况 选 择
的 高 速 电主 轴 相 对 国 内其 他厂 家 ,具 有转 速 高 、 回 转精 度高 、振 动 小 、温 升 小 、输 出扭 力大 ,从 而 得 到很 高 的 加 工效 率 和 加 工精 度 及 表 面加 工 质量 ,达 到 了 国外 同 类 产 品水 平 。另外 ,由于 其健 全 的 研 发 设 计 及验 证 体 系 、高 精 度 的制 造 能 力 成 熟 的 品质 控 制体 系 ,产 品 可 靠性 及 寿 命远 高 于 国 内 同类 产 品 水
数控机床高速电主轴技术要点分析
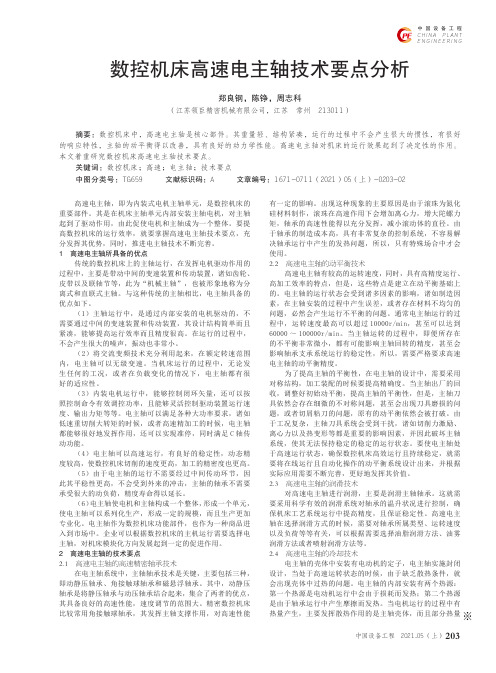
203中国设备工程C h i n a P l a n t E n g i n e e r i ng中国设备工程 2021.05 (上)高速电主轴,即为内装式电机主轴单元,是数控机床的重要部件。
其是在机床主轴单元内部安装主轴电机,对主轴起到了驱动作用,由此促使电机和主轴成为一个整体。
要提高数控机床的运行效率,就要掌握高速电主轴技术要点,充分发挥其优势,同时,推进电主轴技术不断完善。
1 高速电主轴所具备的优点传统的数控机床上的主轴运行,在发挥电机驱动作用的过程中,主要是带动中间的变速装置和传动装置,诸如齿轮、皮带以及联轴节等,此为“机械主轴”,也被形象地称为分离式和直联式主轴。
与这种传统的主轴相比,电主轴具备的优点如下。
(1)主轴运行中,是通过内部安装的电机驱动的,不需要通过中间的变速装置和传动装置,其设计结构简单而且紧凑,能够提高运行效率而且精度很高。
在运行的过程中,不会产生很大的噪声,振动也非常小。
(2)将交流变频技术充分利用起来,在额定转速范围内,电主轴可以无级变速。
当机床运行的过程中,无论发生任何的工况,或者在负载变化的情况下,电主轴都有很好的适应性。
(3)内装电机运行中,能够控制闭环矢量,还可以按照控制命令有效调控功率,且能够灵活控制驱动装置运行速度、输出力矩等等。
电主轴可以满足各种大功率要求,诸如低速重切削大转矩的时候,或者高速精加工的时候,电主轴都能够很好地发挥作用,还可以实现准停,同时满足C 轴传动功能。
(4)电主轴可以高速运行,有良好的稳定性,动态精度较高,使数控机床切削的速度更高,加工的精密度也更高。
(5)由于电主轴的运行不需要经过中间传动环节,因此其平稳性更高,不会受到外来的冲击,主轴的轴承不需要承受很大的动负荷,精度寿命得以延长。
(6)电主轴使电机和主轴构成一个整体,形成一个单元,使电主轴可以系列化生产,形成一定的规模,而且生产更加专业化。
电主轴作为数控机床功能部件,也作为一种商品进入到市场中。
走心机主轴,走心机高速轴

走心机用高速主轴
目前高速主轴在精加工行业得到广泛使用,由于转速高(1000-80000转/分)且转速可调,在各类高精度加工中得到广泛使用,特别适用于用来加工医疗骨钉,螺丝,及小型高精密部件,航空航天业相关部件.
目前可调速高速主轴已经广泛使用在津上,北村,野村,特纳斯,STAR,西铁城等国内外众多厂家的产品上,并已得到用户广泛好评.
使用体积小精度高,转速高的高速主轴能有效节约安装空间,能在极小的安装空间中进行安装并运行,可通过高速主轴的高精度,高转速等特点可以在花极少成本的前提下有效提高走心机加工精度.
目前我们销售的用于走心机上的高速主轴已经在国内众多机床厂家认可并在医疗,精密零件,精密材料工业等方面得到广泛应用.
走心机高速主轴可接并入机床系统进行自动化作业.。
高速电主轴动力学特性分析综述解析
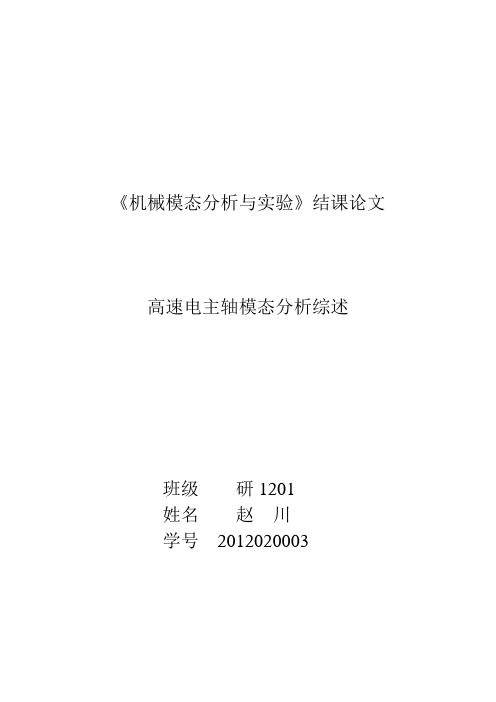
《机械模态分析与实验》结课论文高速电主轴模态分析综述班级研1201姓名赵川学号2012020003高速电主轴模态分析综述前言高速电主轴是高速机床的核心部件, 它将机床主轴与变频电机轴合二为一, 即将主轴电机的定子、转子直接装入主轴组件内部, 也被称为内装式电主轴( Built- in Motor spindle) ,其间不再使用皮带或齿轮传动副。
其具有结构紧凑、重量轻、惯性小、动态特性好等优点, 并改善了机床的动平衡, 避免振动和噪声, 在超高速机床中得到广泛应用。
随着科学技术的发展,高速精密加工技术已广泛应用于高端装备制造各个行业。
高速精密数控机床目前成为现代化制造业的关键生产设备。
提高高速精密数控机床在加工运行过程中精度的可靠性、稳定性和可维护性,对提升企业竞争力越来越重要。
高速精密机床的工作性能,取决于机床的主轴系统。
主轴也是最容易失效的部位之一,主轴系统在加工过程中由于各种原因会引起回转精度劣化和功能丧失,严重影响产品加工精度和质量。
如精密车削的圆度误差30%-70%是主轴的回转误差引起。
加工的精度越高,所占的比例越大。
其动态性能的好坏对机床的切削抗振性、加工精度及表面粗糙度均有很大的影响,是制约数控机床加工精度和使用效率的关键因素。
正文高速加工技术已广泛应用于航空航天、模具及汽车制造等行业。
高速主轴在加工过程中, 由于离心力和陀螺力矩效应, 其动态特性相对静止状态发生很大改变。
若仍然利用静态主轴的动态特性参数进行高速切削稳定性分析, 会带来较大的误差。
因此有必要对高速旋转状态下的主轴进行精确建模, 以达到优化切削参数的目的。
国内电主轴的研究始于20世纪60 年代, 主要用于零件内表面磨削, 这种电主轴的功率低, 刚度小。
且采用无内圈式向心推力球轴承, 限制了高速电主轴的生产社会化和商品化。
20世纪70年代后期至80年代, 随着高速主轴轴承的开发, 研制了高刚度、高速电主轴, 它被广泛应用于各种内圆磨床和各机械制造领域。
机床高速电主轴原理与应用_杨军
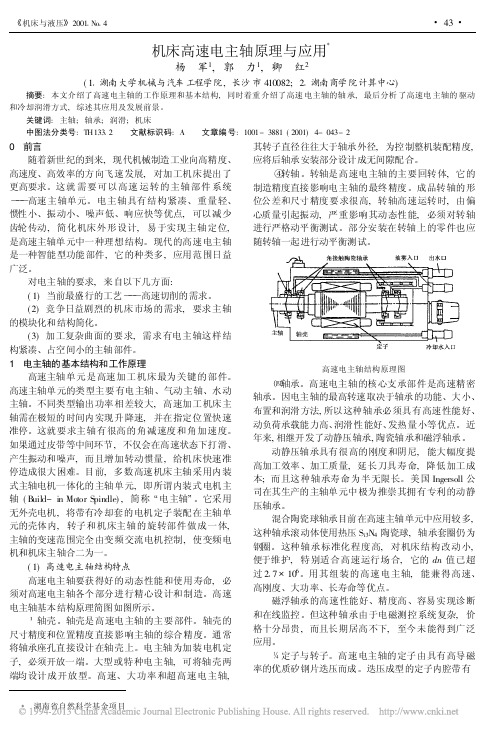
机床高速电主轴原理与应用*杨军1,郭力1,卿红2(11湖南大学机械与汽车工程学院,长沙市410082;21湖南商学院计算中心)摘要:本文介绍了高速电主轴的工作原理和基本结构,同时着重介绍了高速电主轴的轴承,最后分析了高速电主轴的驱动和冷却润滑方式,综述其应用及发展前景。
关键词:主轴;轴承;润滑;机床中图法分类号:TH13312文献标识码:A文章编号:1001-3881(2001)4-043-20前言随着新世纪的到来,现代机械制造工业向高精度、高速度、高效率的方向飞速发展,对加工机床提出了更高要求。
这就需要可以高速运转的主轴部件系统)))高速主轴单元。
电主轴具有结构紧凑、重量轻、惯性小、振动小、噪声低、响应快等优点,可以减少齿轮传动,简化机床外形设计,易于实现主轴定位,是高速主轴单元中一种理想结构。
现代的高速电主轴是一种智能型功能部件,它的种类多,应用范围日益广泛。
对电主轴的要求,来自以下几方面:(1)当前最盛行的工艺)))高速切削的需求。
(2)竞争日益剧烈的机床市场的需求,要求主轴的模块化和结构简化。
(3)加工复杂曲面的要求,需求有电主轴这样结构紧凑、占空间小的主轴部件。
1电主轴的基本结构和工作原理高速主轴单元是高速加工机床最为关键的部件。
高速主轴单元的类型主要有电主轴、气动主轴、水动主轴。
不同类型输出功率相差较大,高速加工机床主轴需在极短的时间内实现升降速,并在指定位置快速准停。
这就要求主轴有很高的角减速度和角加速度。
如果通过皮带等中间环节,不仅会在高速状态下打滑、产生振动和噪声,而且增加转动惯量,给机床快速准停造成很大困难。
目前,多数高速机床主轴采用内装式主轴电机一体化的主轴单元,即所谓内装式电机主轴(B uild-in Motor Spindle),简称/电主轴0。
它采用无外壳电机,将带有冷却套的电机定子装配在主轴单元的壳体内,转子和机床主轴的旋转部件做成一体,主轴的变速范围完全由变频交流电机控制,使变频电机和机床主轴合二为一。
基于数控机床的高速电主轴结构分析
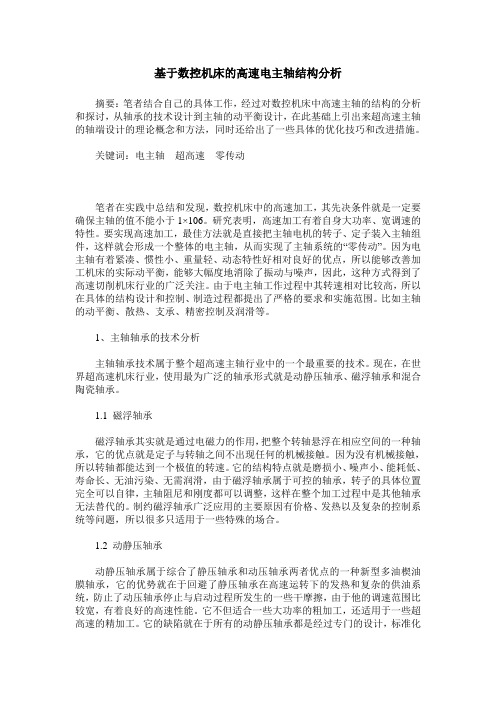
基于数控机床的高速电主轴结构分析摘要:笔者结合自己的具体工作,经过对数控机床中高速主轴的结构的分析和探讨,从轴承的技术设计到主轴的动平衡设计,在此基础上引出来超高速主轴的轴端设计的理论概念和方法,同时还给出了一些具体的优化技巧和改进措施。
关键词:电主轴超高速零传动笔者在实践中总结和发现,数控机床中的高速加工,其先决条件就是一定要确保主轴的值不能小于1×106。
研究表明,高速加工有着自身大功率、宽调速的特性。
要实现高速加工,最佳方法就是直接把主轴电机的转子、定子装入主轴组件,这样就会形成一个整体的电主轴,从而实现了主轴系统的“零传动”。
因为电主轴有着紧凑、惯性小、重量轻、动态特性好相对良好的优点,所以能够改善加工机床的实际动平衡,能够大幅度地消除了振动与噪声,因此,这种方式得到了高速切削机床行业的广泛关注。
由于电主轴工作过程中其转速相对比较高,所以在具体的结构设计和控制、制造过程都提出了严格的要求和实施范围。
比如主轴的动平衡、散热、支承、精密控制及润滑等。
1、主轴轴承的技术分析主轴轴承技术属于整个超高速主轴行业中的一个最重要的技术。
现在,在世界超高速机床行业,使用最为广泛的轴承形式就是动静压轴承、磁浮轴承和混合陶瓷轴承。
1.1 磁浮轴承磁浮轴承其实就是通过电磁力的作用,把整个转轴悬浮在相应空间的一种轴承,它的优点就是定子与转轴之间不出现任何的机械接触。
因为没有机械接触,所以转轴都能达到一个极值的转速。
它的结构特点就是磨损小、噪声小、能耗低、寿命长、无油污染、无需润滑,由于磁浮轴承属于可控的轴承,转子的具体位置完全可以自律,主轴阻尼和刚度都可以调整,这样在整个加工过程中是其他轴承无法替代的。
制约磁浮轴承广泛应用的主要原因有价格、发热以及复杂的控制系统等问题,所以很多只适用于一些特殊的场合。
1.2 动静压轴承动静压轴承属于综合了静压轴承和动压轴承两者优点的一种新型多油楔油膜轴承,它的优势就在于回避了静压轴承在高速运转下的发热和复杂的供油系统,防止了动压轴承停止与启动过程所发生的一些干摩擦,由于他的调速范围比较宽,有着良好的高速性能。
机床高速主轴关键技术的探讨
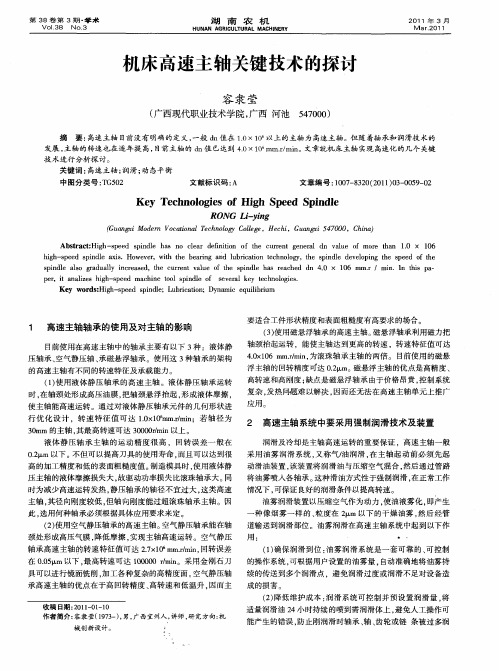
Vo l 8 N o 3 3
湖
南
农
机
201 年 3 月 1
M ar2O11 l
HUNAN AGRI CUL TURAL MACHI NER Y
机 床高速主 轴关键 技术的探讨
容 隶 摘
5 70 ) 4 00
要: 高速 主轴 目前 没有 明确的定义 , 一般 d n值在 1 ×1 . 0 以上的主轴为 高速主轴。但随 着轴承和润滑技术的 0
发展 , 轴的 转速 也在 逐年提 高, 主 目前 主轴的 d 已达到 4 ×1 n1 / n n值 . 0 i . mi。文章就机床主轴 实现 高速化 的几 个关键 0 nr
的高速主轴有不 同的转 速特 征及承载能力 。
40 l6 mnr i, . 0 l.mn 为滚珠轴 承主轴 的两倍 。 目前使用 的磁悬 x / 浮主轴 的回转精度可达 02 m。 . 磁悬浮 主轴 的优 点是 高精度 、
高转速和高刚度 : 缺点是磁悬浮轴承 由于价 格昂贵 , 制系统 控
() 4 隔离污染 物 : 雾系统为 轴承持续 地提供新 鲜 、 油 洁净
的润 滑油 , 在轴承箱 内形 成正压 , 起到 了正压密封 的作用 , 有
效阻挡灰尘进入 , 作面免受 腐蚀气体与杂质 的污染 , 使工 保持
轴承箱 内的清洁 。 ( ) 省润 滑油 :油雾 润滑 系统 预先设 置油 量 。 保持 5节 并 2 4小时持 续润滑 , 出的喷雾 中润滑 油含量微 小 , 比传统 输 相
p r t a a i s h g — p e c i e to p n l f s v r l k y tc n lge . e ,i n l e ih s e d ma h n o l s i d e o e e a e e h o o i s z
机床主轴轴承正确安装方法
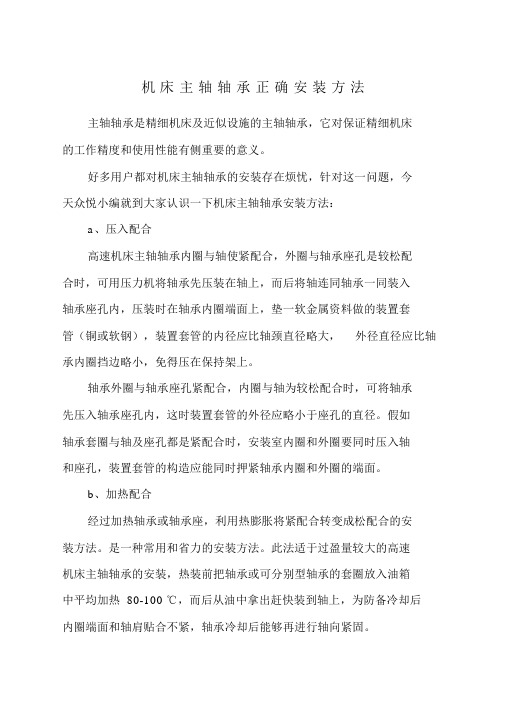
机床主轴轴承正确安装方法主轴轴承是精细机床及近似设施的主轴轴承,它对保证精细机床的工作精度和使用性能有侧重要的意义。
好多用户都对机床主轴轴承的安装存在烦忧,针对这一问题,今天众悦小编就到大家认识一下机床主轴轴承安装方法:a、压入配合高速机床主轴轴承内圈与轴使紧配合,外圈与轴承座孔是较松配合时,可用压力机将轴承先压装在轴上,而后将轴连同轴承一同装入轴承座孔内,压装时在轴承内圈端面上,垫一软金属资料做的装置套管(铜或软钢),装置套管的内径应比轴颈直径略大,外径直径应比轴承内圈挡边略小,免得压在保持架上。
轴承外圈与轴承座孔紧配合,内圈与轴为较松配合时,可将轴承先压入轴承座孔内,这时装置套管的外径应略小于座孔的直径。
假如轴承套圈与轴及座孔都是紧配合时,安装室内圈和外圈要同时压入轴和座孔,装置套管的构造应能同时押紧轴承内圈和外圈的端面。
b、加热配合经过加热轴承或轴承座,利用热膨胀将紧配合转变成松配合的安装方法。
是一种常用和省力的安装方法。
此法适于过盈量较大的高速机床主轴轴承的安装,热装前把轴承或可分别型轴承的套圈放入油箱中平均加热 80-100 ℃,而后从油中拿出赶快装到轴上,为防备冷却后内圈端面和轴肩贴合不紧,轴承冷却后能够再进行轴向紧固。
轴承外圈与轻金属制的轴承座紧配合时,采纳加热轴承座的热装方法,能够防止配合面遇到擦伤。
用油箱加热轴承时,在距箱底必定距离处应有一网栅,或许用钩子吊着轴承,高速机床主轴轴承不可以放到箱底上,以防沉杂质进入轴承内或不平均的加热,油箱中一定有温度计,严格控制油温不得超出 100℃,以防备发生回火效应,使套圈的硬度降低。
别的,在安装过程中也要注意:(1)保持高速机床主轴轴承及其周转洁净即便是眼睛看不到的小灰尘,也会给轴承带来坏影响。
因此,要保持四周洁净,使灰尘不致侵入轴承。
(2)当心慎重地使用在使用中给与轴承激烈冲击,会产生伤痕及压痕,成为事故的原由。
严重的状况下,会裂痕、断裂,因此一定注意。
高速数控机床电主轴热误差机理分析与建模研究

高速数控机床电主轴热误差机理分析与建模研究一、本文概述Overview of this article随着制造业的快速发展,高速数控机床在精密加工领域的应用越来越广泛。
然而,高速数控机床在高速运转过程中,电主轴会产生大量热量,导致热误差问题,严重影响加工精度和效率。
因此,研究高速数控机床电主轴的热误差机理及建模方法,对于提高机床加工精度和稳定性具有重要的理论和实际意义。
With the rapid development of the manufacturing industry, the application of high-speed CNC machine tools in the field of precision machining is becoming increasingly widespread. However, during high-speed operation of CNC machine tools, the electric spindle generates a large amount of heat, leading to thermal error problems and seriously affecting machining accuracy and efficiency. Therefore, studying the thermal error mechanism and modeling method of high-speed CNC machine tool electric spindle has important theoretical and practical significance for improving the machining accuracy andstability of machine tools.本文首先概述了高速数控机床电主轴热误差问题的背景和研究意义,然后介绍了国内外在该领域的研究现状和发展趋势。
数控机床高速电主轴技术及应用

数控机床高速电主轴技术及应用一、高速电主轴的发展历程早在 20 世纪 50 年代,就己出现了用于磨削小孔的高频电主轴,当时的变频器采用的是真空电子管,虽然转速高,但传递的功率小,转矩也小。
随着高速切削发展的需要和功率电子器件、微电子器件和计算机技术的发展,产生了全固态元件的变频器和矢量控制驱动器;加上混合陶瓷球轴承的出现,使得在 20 世纪 80 年代末、90 年代初出现了用于铣削、钻削、加工中心及车削等加工的大功率、大转矩、高转速的电主轴。
国外高速电主轴技术发展较快,中等规格的加工中心的主轴转速目前己普遍达到 10000r/min 甚至更高。
1976 年美国的 Vought 公司首次推出一台超高速铣床,采用了 Bryant 内装式电机主轴系统,最高转速达到了20,OOOr/min,功率为 15KW。
到 90 年代末期,电主轴发展的水平是:转速40,000 r/min,功率 40 KW(即所谓的“40-40 水平”)。
但 2001 年美国Cincinnati 公司为宇航工业生产了 SuperMach 大型高速加工中心,其电主轴最高转速达 60,000 r/min,功率为 80 KW。
目前世界各主要工业国家均有装备优良的专业电主轴生产厂,批量生产一系列用于加工中心和高速数控机床的电主轴。
其中最著名的生产厂家有:瑞士的 FISCHER 公司、IBAG 公司和 STEP-TEC 公司,德国的 GMN 公司和FAG 公司,美国的 PRECISE 公司,意大利的 GAMFIOR 公司和 FOEMAT 公司,日本的 NSK公司和 KOYO公司,以及瑞典的 SKF公司等公司。
高速电主轴生产技术的突破,大大推动了世界高速加工技术的发展与应用。
从 80年代中后期以来,商品化的超高速切削机床不断出现,超高速机床从单一的超高速铣床发展成为超高速车铣床、钻铣床乃至各种加工中心等。
德国、美国、瑞士、英国、法国、日本也相继推出了自己的超高速机床。
高速电主轴解析

谢谢!!
电主轴的电动机技术
• 电主轴将机床主轴与电机合二为一,形成内装式主轴驱动 系统,是机床的核心关键部件之一
高速精密轴承技术
滚动轴承
主要支承类型
磁悬浮轴承
动静压轴承
滚动轴承
(1)传统钢制球轴承 高速运转时将产生巨
大的离心力和陀螺力矩, 使得滚动体与轴承外圈的 接触应力急剧增大,使得 摩擦与温升增加,导致轴 承的运转条件变差,因而 钢制球轴承应用于电主轴 受到了一定限制。
(2)氮化硅陶瓷球轴承
具有转速高、温升低、 等优良特性,可弥补钢制 球轴承的不足,显著提高 电主轴的转速、刚度和寿 命。
磁悬浮轴承
(1)机械磨损小、能耗低、噪声小、寿命长、无需润滑、无油污染等; (2)可控轴承,转子位置能够自律,主轴刚度和阻尼可调; (3)价格昂贵,控制系统复杂,发热问题不易解决;
磁悬浮轴承原理图
动静压轴承
动静压轴承是能在流体静力润滑状态下,又能 在流体动力润滑状态下工作的滑动轴承
动压轴承
静压轴承
热态性能和动态性能的设定
电主轴的润滑
脂润滑
一次性永久润滑
润
滑
的
主
油-雾润滑
具有润滑和冷却
要
双重作用
类
型
油-气润滑
精确润滑、润 滑油利用率高、 轴承发热量小、 无环境污染
油-气润滑设计
高速电主轴及其结构
周李念 20122449 机自实验04班
高速电主轴概述
定义
机床主轴由内装式电动机直 接驱动,从而把机床主传动链 的长度缩短为零,实现了机床 的“零传动”,这种主轴电动 机与机床主轴“合二为一”的 传动结构形式,使主轴部件从 机床的传动系统和整体结构中 相对独立出来的电主轴单元, 俗称为“电主轴”。
主轴知识分享

高速加工技术越来越受到机械制造领域的关注,为了能提高整体加工效率,降低零件加工成本,获得较高加工精度和加工表面完整性,降低能耗、节省制造资源,有效抑制或减小切削振动,就必须使用超高速数控机床.高速电主轴单元作为高速机床的关键部件,其高转速、高精度、高刚性、低噪音、低温升、结构紧凑、易于平衡、安装方便、传动效率高等优点,使它在超高速切削机床上得到广泛的应用。
高速电主轴概述高速电主轴最早是用于磨削机床加工,逐步发展到加工中心电主轴及其他各行业机床主轴.传统的主轴一般是通过传动带、齿轮来进行传动驱动,而电主轴的驱动是将异步电机直接装入主轴内部,通过驱动电源直接驱动主轴进行工作,以实现机床主轴系统的零传动,形成“直接传动主轴”.从而减少中间皮带或者齿轮机械传动等环节,实现了机械与电机一体的主轴单元.电主轴不但减少了中间环节存在的打滑、振动和噪音的因素,也加速了主轴在高速领域的快速发展,成为满足高速切削,实现高速加工的最佳方案.2 高速电主轴的结构设计要求高速电主轴要求具备很高的工作性能,因此对其结构的设计、材质、加工工艺和检验等方面都有非常严格的要求.电主轴设计时,需要确定主轴的总体性能参数、主轴的实际结构(根据轴承形式、配置、驱动方法、润滑、等参数来确定)、主轴轴承的选型确认、轴承的寿命、主轴的刚度、危险速度、轴承游隙(预紧力)、主轴的尺寸(轴径、长度、轴承支距等)和主轴实际安装条件的要求等等因素.2.1 电主轴的转轴要求转轴是高速电主轴的主要零件之一,转轴的材料一般是经过轧制或锻造经切削加工的碳素钢或合金钢.它用来安装各种传动零件,使之绕其轴线转动,传递转矩或回转运动,并通过轴承与主轴机架或机座相联接.转轴带动工件或刀具旋转,完成表面成型运动,承受切削和驱动等载荷的作用.因此,对轴有很高的技术要求,在设计时应满足下列几方面的要求:(1) 节约材料,减轻重量,在特殊情况下选用合适的具有耐腐蚀性和耐高温性的材料;(2) 在结构上要受力合理、尽量避免或减少应力集中现象;(3) 提高足够的强度(静强度和疲劳强度)和刚度的结构措施;(4) 转轴在高速时的振动稳定性及良好的加工工艺性,保证精度要求;(5) 易于各个零件在轴上精确定位、稳固、装配、装拆和调整方便.在一般情况下,转轴结构设计成阶梯形,将内装的电机转子部件与转轴联接在一起形成整体部件,如图 2 所示.该转轴部件最大的优点是前后轴承组件、电机转子部件、平衡环均采用先进的感应加热下套工艺方法进行组装,无键槽的设计工艺方法,不但增加了转轴的刚度,同时,通过平衡环调整转轴整体动平衡量,最大限度地降低了转轴在旋转时由于偏心造成的振动和偏差.2.2 电主轴的电动机技术电主轴将机床主轴与电机合二为一,形成内装式主轴驱动系统,是机床的核心关键部件之一,它不但要实现高速、高精度、高刚度等要求,还必须要实现连续工作时输出的较大转矩力和承受较宽领域的恒功率运转范围.尤其是在转速要求较高且加减速操作频繁的领域,如加工中心、铣镗床、磨床、钻床等领域.交流主轴驱动系统根据电机类型分为感应电机电主轴驱动系统、永磁无刷同步电机主轴驱动系统以及开关磁阻电机主轴驱动系统.由于不同的机床要求不同的主轴输出性能(旋转速度、输出功率、动态刚度、振动抑制等),因此主轴的实际应用于选择需要精密相关[2].目前主要采用感应电机交流主轴驱动系统,主轴功率设计时,电机需满足条件:(1)切削(实际工作)功率的要求;(2)主轴加减速时间所需功率要小于主轴电机的最大输出功率;(3)主轴频繁启动、制动时,需要计算平均功率,该功率要小于主轴电机的连续额定输出功率;(4)在要求时限表面恒线速切削的机床上,切削功率与恒线速所需功率之和应小于电机最大输出功率.内装式主轴电机结构紧凑,简化了机床的构造.因为转子安装在主轴上,降低了转轴在旋转时由于偏心造成的振动和偏差,而且获得较短的起动时间和制动时间,恒功率调速范围宽、噪声小、维修简单.但是,电机也是一个很大的发热源,要控制电机的温度,安装时最好选用有水冷的水套结构最佳轴承是高速电主轴的重要组成部分,它的类型、配置、精度对电主轴的工作性能、旋转精度有着很大的影响.电主轴一般采用角接触球轴承,主轴在高速旋转时,离心力引起的内圈膨胀、球旋转时离心力会引起内部负荷以及内外圈的温度差等均会使轴承内部的球和内外圈滚道之间的接触应力增大.而且,采用角接触球轴承这样有着接触角的轴承,在旋转中伴随着自转滑动和旋转时的滑动等各种形式的滑动而产生滚动接触,这些滑动随着转速增加而加大,因此接触部分的发热也会变大,特别是采用油脂润滑的轴承,由于润滑油的粘度下降,有时候甚至会出现缺少润滑油膜而烧伤的情况.高速电主轴轴承的选用要根据切削负荷大小、形式和转速的要求,优先选用陶瓷触球轴承.与钢球轴承相比,陶瓷球轴承优点有:(1)钢与陶瓷组成的陶瓷球轴承摩擦性能特好,能降低材料与润滑剂的应力;(2)因密度较低,可降低运转时的离心力;(3)较低的热膨胀系数能有效的降低轴承预压负荷的变化;(4)较高的弹性模数,使轴承的刚性更高.陶瓷球轴承在高速及重载的条件下,可获得高刚度、低温升和长寿命的效果,可以提高主轴的整体精度.2.4 电主轴的预紧力技术电主轴在选用轴承时,需要考虑机床主轴的刚度,固定在主轴上的轴承类似于弹簧的作用,主轴端部承受轴向负荷时,主轴的位移由固定轴承的轴向刚度来决定.当轴前端承受径向负荷时,轴端位移应考虑轴的弯曲变形.单列角接触球轴承接触角愈大,承受轴向载荷的能力愈高,在承受径向载荷时,同时产生轴向力,必须施加反向轴向力,所以,一般成对使用.当需要较大径向刚度时,可使用圆柱滚子轴承与角接触轴承配合安装,轴向负荷由角接触球轴承来承受.通常高速电主轴采用成对双联角接触球轴承组合安装,施加适当的预紧力,安装后有预过盈,消除轴承中间的游隙,因此提高了载荷能力、刚度和旋转精度,同时可以增加轴承的使用寿命,抑制轴的振动和异音,防止假性布氏压痕现象和高速旋转时滚动体的滑动现象产生等[3].机床主轴在工作时,为实现取得较高的刚度,一般对轴承加上预紧力,但是需要注意的是预紧力不可过大,否则将会引起轴承烧伤现象或剥落损坏.主轴的预紧方式一般包括:(1)定位预紧,即组合轴承的轴向相对位置在使用过程中不会改变.(2)定压预紧,即通过圆柱弹簧、蝶形弹簧对轴承施加适当预紧的方法,在使用过程中即使轴承的相对位置发生变化,预紧量也能基本保持恒定.一般情况下,为提高主轴刚度时适合采用定位预紧,高速旋转时适合采用定压预紧的方法.2.5 电主轴的润滑技术高加工精度的机床主轴,不是单纯实现高速旋转,而且要抑制温度上升和减小热变形.一般主轴的润滑方式有:油脂润滑、油雾润滑、喷射润滑和油气润滑.不同类型的电主轴,要根据具体的特性选用适合的润滑方式.一般情况下,油脂润滑用于主轴高速运转比较普遍,但是受到极限转速的影响,填充适量的油脂时才能达到最高数值,油脂的填充量为轴承内部空间体积的10%~20%,填充太多,在进行初期运转时会产生异常发热,导致油脂劣化.在高速旋转时为保持较低的运转温度,可使用供油量少的油雾或油气润滑方式,它可以延长使用寿命、减少摩擦损耗、降低温升,并与密封装置一起保护轴承不受外物的侵入和防止腐蚀.油雾润滑是利用压力使润滑油雾化,再顺着进油通道喷射到轴承的方法;而油气润滑是通过喷嘴定量、定时间歇性的喷射出微量的润滑油,通过混合阀将其压缩空气中润滑油慢慢引出,每套轴承都需要一条单独的油路连续不断的向轴承供油的方法.不同润滑方式特性比较见表电主轴的动平衡技术高速机床的广泛应用,加速了主轴对转速的高要求.转速的提高使机床主轴各零部件在加工制造过程中,首先对材质提出了的较高要求,包括转轴毛胚是否有缺陷、材质是否均匀、形状是否对称及加工装配是否有误差等各个方面.电主轴的动平衡也是装配前的关键环节,动平衡的高低直接影响主轴单元的噪声、振动、发热等性能标.通常在完成零部件加工后,转轴首先需要做单体动平衡试验,使转轴不平衡离心力降到最小值,接着安装上螺母等单体逐步进行动平衡试验,待组装后还要对整机进行动平衡试验,通过数据显示达到理想的动态性能,从而提高主轴整机系统的动态精度,延长轴承及整个主轴系统的寿命.由于转轴上附加的零件偏多,装配前可能无法一一平衡,因此,必要时可做在线动平衡试验.同时,为方便调整电主轴整机的平衡,通常应在转轴前后螺母上预留数个平衡螺孔,以保证转轴在高速运转的平稳性[5].3 高速电主轴的发展国内电主轴研究启蒙阶段为20 世纪60 年代,主要以内圆磨削为主体,多数为仿制技术.到20 世纪70年代到80 年代,随着国内技术的发展,电主轴的广泛应用,我国自行开发研制了高速电主轴,电机的功率也大大提高了30%左右,广泛应用于磨削领域.到20 世纪90 年代以后,数控CNC 技术的研发,大大推动了电主轴在机械领域的应用,铣削加工中心电主轴单元使电主轴越来越多的应用到高速雕铣行业中.21 世纪以来,国内研制电主轴的技术得到快速发展,采用了先进的技术与加工方法,使电主轴具有高转速、高精度、高刚性、低噪音、低温升、结构紧凑、易于平衡、安装方便、传动效率高等优点,生产出适合各个行业领域的电主轴与机械主轴.国外从事高速数控机床电主轴研发与生产的技术较早,著名的企业中尤以GMN 公司、IBAG 公司、Fanuc 公司、Ingersoll 公司、Okuma 公司等几家的技术水平代表了这个领域的世界先进水平.我国电主轴的设计制造技术与国外技术相比,无论是性能、品种和质量还有较大的差距.国外高性能电主轴有以下几个特点:(1)主轴低速输出扭矩大,转速高;(2)采用高速、高刚度陶瓷球轴承和液体动静压轴承,润滑方式采用油气润滑;(3)配套的控制系统,如交流伺服控制技术、自动平衡系统、润滑控制系统、电机冷却系统等方面[6].德国Diebold公司历程1952年:成立Diebold1970年:开始生产刀柄1980年:开始为欧洲知名的机器制造商生产主轴部件1990年:开始生产带装配的主轴单元1997年:开始生产高频主轴2007年:开始生产锥度规2006年:在一个全空调建筑中生产主轴,在洁净室中安装主轴2015年:交付超过20,000个主轴单元2016年:安装温度等级为2的测量室(每米温度+/- 2开尔文)2018年:主轴采用1微米精度的轴承座德国戴博DIEBOLD公司是德国***的刀柄生产商,可生产DIN69893的HSK刀柄,DIN69871A 及B的SK刀柄,MAS-BT刀柄,品种达到5000多个包括液压锁紧和热涨锁紧,其生产的热装设备为客户解决了刀柄的安装问题,同时Diebold公司还生产机床的高频电动主轴和对刀仪设备,如Chrion ,EMAG , Deckel-Maho , Heller等德国知名机床制造商均已***使用了戴博公司的电动主轴。
北京航空航天大学科技成果——机床高速电主轴的扭矩测量装置
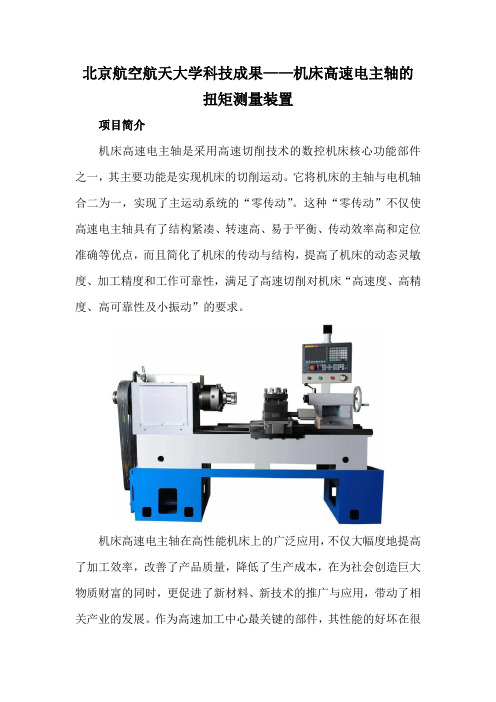
北京航空航天大学科技成果——机床高速电主轴的扭矩测量装置项目简介机床高速电主轴是采用高速切削技术的数控机床核心功能部件之一,其主要功能是实现机床的切削运动。
它将机床的主轴与电机轴合二为一,实现了主运动系统的“零传动”。
这种“零传动”不仅使高速电主轴具有了结构紧凑、转速高、易于平衡、传动效率高和定位准确等优点,而且简化了机床的传动与结构,提高了机床的动态灵敏度、加工精度和工作可靠性,满足了高速切削对机床“高速度、高精度、高可靠性及小振动”的要求。
机床高速电主轴在高性能机床上的广泛应用,不仅大幅度地提高了加工效率,改善了产品质量,降低了生产成本,在为社会创造巨大物质财富的同时,更促进了新材料、新技术的推广与应用,带动了相关产业的发展。
作为高速加工中心最关键的部件,其性能的好坏在很大程度上决定了整台高速机床的加工精度和生产效率,而高速电主轴的可靠性更是体现了整台机床在生产企业的可用性,高速电主轴在高速运转状态下的扭矩输出是高速电主轴的主要性能之一。
因此,需要设计一种扭矩试验装置来测量高速电主轴在高速运转情况下的扭矩输出情况。
目前国内研究机构对高速电主轴扭矩的测量大多是基于独立的电主轴利用测功电机直接加载,并通过扭矩传感器直接测量高速电主轴的输出扭矩和转速,这对同轴度的要求比较高,且很难达到高速的要求。
为解决上述问题,本项目研发了一种用于机床高速电主轴的扭矩测量装置。
技术描述本成果属于测量装置技术领域,具体涉及一种用于机床高速电主轴的扭矩测量装置及测量技术。
用于机床高速电主轴的扭矩测量装置,包括减速器、扭矩转速传感器和电力测功电机,减速器和扭矩转速传感器之间通过第一联轴器相连,以用于传递扭矩,扭矩转速传感器和电力测功电机之间通过第二联轴器相连,以用于扭矩加载,减速器的输入轴上设有第三联轴器,第三联轴器用于将减速器的输入轴与加载杆连接,加载杆能够与机床的电主轴相连。
通过使用本成果的用于机床高速电主轴的扭矩测量装置及测量技术,可以有效的降低机床电主轴的转速并传递转矩,使扭矩的测量更加准确,且易于装配。
机床主轴介绍

机床主轴介绍机床主轴是机床中的关键部件之一,它是用来传递动力给刀具或夹具的重要部件。
在机械加工过程中,主轴的质量和稳定性直接关系到加工效率和产品质量。
本文将对机床主轴进行详细介绍。
一、机床主轴的作用机床主轴是机床上最重要的零件之一,它的作用包括负责传递动力、保持精度和达到平稳的运行状态。
机床主轴的转速和转矩直接关系到加工效率和产品质量。
二、机床主轴的类型1.气动主轴气动主轴是一种能够通过压缩空气来实现高速运动的主轴。
它能够实现高精度、高速度和高精度的加工。
尤其在微细加工领域中,气动主轴被广泛应用。
2.电动主轴电动主轴是广泛应用于各种机床上的主轴,它能够实现高速、高精度和高负荷的加工。
目前,大部分机床的主轴都是电动主轴。
3.水冷主轴水冷主轴是一种能够通过水冷却来降低主轴温度的主轴。
它特别适用于高速度和长时间运转下的加工,比如高速机床、数控机床等。
三、机床主轴的结构机床主轴主要由下列几个组成部分组成:主轴头、轴承、主轴尾、快速换刀机构、电机和卡盘。
其中,轴承便是机床主轴中最核心的部分。
轴承的质量和精度直接关系到整个主轴的质量和精度,因此机床主轴的轴承要用高精度的陶瓷轴承。
四、机床主轴的维护保养为确保机床主轴的正常运行和延长机床使用寿命,机床主轴需要定期维护保养,主要包括轴承更换、润滑油更换等。
五、总结机床主轴是机床中不可或缺的重要部件之一,其质量和稳定性是整个机床的核心部分。
在机械加工中,正确选择合适的主轴能够提高加工效率和产品品质。
机床主轴需要经常维护保养以确保其正常运行和延长机床的使用寿命。
数控机席高速电主轴技术及应用

紧方 式 以及 刀 具动 平 衡 等 。 在 高 速 主 轴 单 元 中 , 由于 机 床 既 要 完 成 粗 加 工 ,又要 完 成 精 加 工 , 因此 对 主 轴 单 元 提 出 了较 高 的静 刚度 和 工作
精 度 的 要 求 。 另外 ,高 速 机 床 主 轴 单 元 的动 态 特 性 也 在 很 大程 度 上 决 定 了机 床 的 加 质 量 和切 削能 力 。 当切 削 过 程 现 较 大 的振 动 时 ,会 使 刀 具 出 现 剧 烈 的 磨 损 或 破 损 , 也 会 增 加 主 轴 轴 承 所 承 受 的 动 载 荷 ,降 低 轴 承 的精 度 和 寿 命 ,影 响加 工 精 度 和 表 面 质 量 。 因此 ,主轴 单元 应 具 有 较 好 的抗 振 性 。高 速 运 转 下 ,主 轴 单 元 的振 动 问 题 是 非 常 突 的 ,采 用 电 主轴 是 最 佳 的 选 择 ,这 是 基 于 以 下 几 点 。
数控 机 床 的 迅 速发 展 也 将 成 为 一 句 空 话 。
高 速 电 主 轴 单 元包 括 动 力 源 、主 轴 、轴 承 和 机 架 四个 主要 部 分 ,是 高 速 机 床 的 核 心 部 件 。这 四个 部 分 构 成 一 个 动 力 学 性 能及 稳定 性 良好 的 系 统 _.在 很 大 程 度 上决 定 了 5 ] 机 床 所 能 达 到 的 切 削 速 度 、加 工 精 度 和 应 用 范 围 。高 速 电 主 轴 单 元 的 性 能 取 决 于 主 轴 的 设 计 方 法 、材 料 、结 构 、轴 承 、润 滑 冷 却 、动 平 衡 、噪 声 等 多 项 相 关 技 术 ,其 中一 些
主轴 技 术 包 括 主 轴 机 械 体 、高 速 主 轴 轴 承 、无 外 壳 主轴 电
高速电主轴
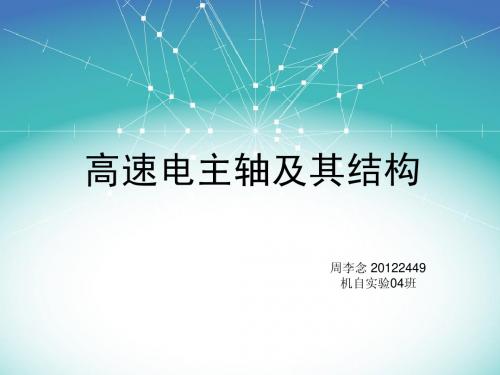
油-气润滑设计
供油部分
供气部分
油气混 合部分
油气分 配部分
原理图
电主轴的冷却
电主轴两个主要的内部热源:内装式电动机的损耗 发热、轴承摩擦发热 冷却系统:针对定转子和轴承的发 热
温升的影响 (1)主轴、工件热变形; (2)导致永磁体的永久退 磁, 直接影响电机性能;
电主轴的动平衡技术
• 动平衡的稳定性决定了机床的加工质量和切削能力。 • 振动过大会出现剧烈的磨耗和破损, 增加主轴承载的动态 负荷, 降低寿命和精度。
谢谢!!
电主轴关键技术
电主轴的要求
转轴是高速电主轴的主要零件之一, 转轴的材料一般 是经过轧制或锻造经切削加工的碳素钢或合金钢
• 要求: • (1) 耐腐蚀性和耐高温性的材料; • (2) 在结构上要受力合理、尽量避免或减少应力集中现象; • (3) 足够的强度(静强度和疲劳强度)和刚度;
• (4) 高速时的振动稳定性及良好的加工工艺性,保证精度要求;
电主轴
结构原理图
1.前轴承 2.定子 3.冷却水套 4.壳体 5.出水管 6.进气管 7.主轴 8.转子 9.进水管 10.后轴承
高速电主轴的优点
(1) 电主轴由内装式电动机直接驱动,省去了皮带、齿轮联 轴节等中间变速和传动装置,具有结构简单紧凑、效率高、 噪声低、振动小和精度高等特点。 (2)利用交流变频技术,电主轴可以在额定转速范围内实 现无级变速。 (3)电主轴更易于实现高速化,其动态精度和稳定性更好。 (4)由于没有中间传动环节,电主轴工作时运行更加平稳, 其精度寿命更长。 (5)实现电机和主轴的一体化、单元化,促进了机床模块 化和其他技术的发展。
(2)氮化硅陶瓷球轴承 具有转速高、温升低、 等优良特性,可弥补钢制 球轴承的不足,显著提高 电主轴的转速、刚度和寿 命。
对机床主轴增速的好处
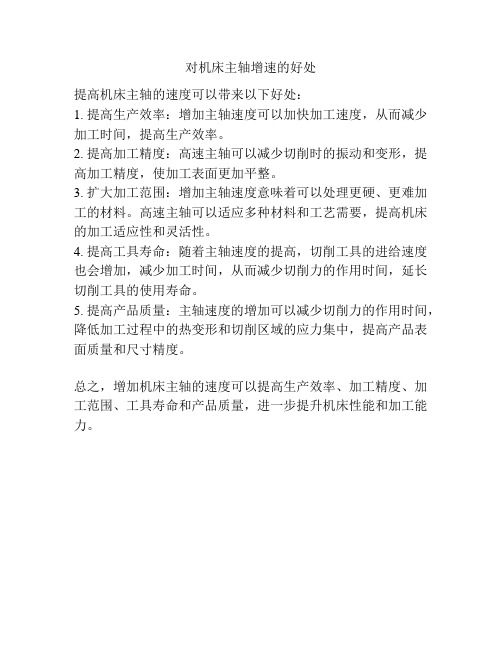
对机床主轴增速的好处
提高机床主轴的速度可以带来以下好处:
1. 提高生产效率:增加主轴速度可以加快加工速度,从而减少加工时间,提高生产效率。
2. 提高加工精度:高速主轴可以减少切削时的振动和变形,提高加工精度,使加工表面更加平整。
3. 扩大加工范围:增加主轴速度意味着可以处理更硬、更难加工的材料。
高速主轴可以适应多种材料和工艺需要,提高机床的加工适应性和灵活性。
4. 提高工具寿命:随着主轴速度的提高,切削工具的进给速度也会增加,减少加工时间,从而减少切削力的作用时间,延长切削工具的使用寿命。
5. 提高产品质量:主轴速度的增加可以减少切削力的作用时间,降低加工过程中的热变形和切削区域的应力集中,提高产品表面质量和尺寸精度。
总之,增加机床主轴的速度可以提高生产效率、加工精度、加工范围、工具寿命和产品质量,进一步提升机床性能和加工能力。
- 1、下载文档前请自行甄别文档内容的完整性,平台不提供额外的编辑、内容补充、找答案等附加服务。
- 2、"仅部分预览"的文档,不可在线预览部分如存在完整性等问题,可反馈申请退款(可完整预览的文档不适用该条件!)。
- 3、如文档侵犯您的权益,请联系客服反馈,我们会尽快为您处理(人工客服工作时间:9:00-18:30)。
高速机床主轴/刀具联结的设计高速加工具有比普通加工大5~10倍的切削速度,其优点是能减少加工时间,达到普通加工需要几道工序才能达到的加工精度和表面质量。
与高速切削有关的主要问题有:刀具材料及设计、高速机床主轴的动平衡、机床的热态动态性能及可靠性等。
而刀具与主轴的联结问题会严重影响高速切削的可靠性及机床主轴的动平衡,已成为限制高速切削的薄弱环节之一。
一、高速切削对刀/轴联结要求高速加工要求确保高速下主轴与刀具联结状态不能发生变化。
但是,高速主轴的前端锥孔由于离心力的作用会膨胀,膨胀量的大小随着旋转半径与转速的增大而增大,标准的7/24实心刀柄膨胀量较小,因此标准锥度联结的刚度会下降,在拉杆拉力的作用下,刀具的轴向位置会发生改变(见图1)。
主轴的膨胀还会引起刀具及夹紧机构质心的偏离,从而影响主轴的动平衡。
要保证这种联结在高速下仍有可靠的接触,需有一个很大的过盈量来抵消高速旋转时主轴轴端的膨胀,如标准40号锥需初始过盈量为15~20μm,再加上消除锥度配合公差带的过盈量(at4级锥度公差带达13μm),因此这个过盈量很大。
这样大的过盈量需拉杆产生很大的拉力,拉杆产生这样大的拉力一般很难实现,对换刀也非常不利,还会使主轴端部膨胀,对主轴前轴承有不良影响。
图 1 在高速离心力作用下主轴扩张图高速加工对动平衡要求非常高,不仅要求主轴组件需精密动平衡(g0.4级以上),而且刀具及装夹机构也需精密动平衡。
但是,传递转矩的键和键槽很容易破坏动平衡,而且,标准的7/24锥柄较长,很难实现全长无间隙配合,一般只要求配合面前段70%以上接触,因此配合面后段会有一定的间隙,该间隙会引起刀具径向跳动,影响结构的动平衡。
键是用来传递转矩和进行角向定位的,为解决键及键槽引起的动平衡问题,可以尝试研究一种刀/轴联结实现在配合处产生很大的摩擦力以传递转矩,并用在刀柄上作标记的方法实现安装的角向定位,达到取消键的目的。
二、标准7/24锥联结的优缺点标准的7/24锥联结有许多优点:因不自锁,可实现快速装卸刀具;刀柄的锥体在拉杆轴向拉力的作用下,紧紧地与主轴的内锥面接触,实心的锥体直接在主轴内锥孔内支承刀具,可以减小刀具的悬伸量;这种联结只有一个尺寸即锥角需加工到很高的精度,所以成本较低而且可靠,多年来应用非常广泛。
但是,7/24联结也有一些缺点;锥度较大,锥柄较长,锥体表面同时要起两个重要的作用,即刀具相对于主轴的精确定位及实现刀具夹紧并提供足够的联结刚度。
由于它不能实现与主轴端面和内锥面同时定位,所以标准的7/24刀/轴锥联结在主轴端面和刀柄法兰端面间有较大的间隙。
在iso标准规定7/24锥度配合中,主轴内锥孔的角度偏差为“-”,刀柄锥体的角度偏差为“+”,以保证配合的前段接触,所以它的径向定位精度往往不够,在配合的后段还会产生间隙,如典型的at4级(iso1947,gb11334-89)锥度规定角度的公差值为13″,这就意味着配合后段的最大径向间隙高达13μm,这个径向间隙会导致刀尖的跳动和破坏结构的动平衡,还会形成以接触前端为支点的条件,当刀具所受的弯矩超过拉杆轴向拉力产生的摩擦力矩时,刀具会以前段接触区为支点摆动。
在切削力作用下,刀具在主轴内锥孔的这种摆动,会加速主轴锥孔前段的磨损,形成喇叭口,引起刀具轴向定位误差。
7/24锥度联结的刚度对锥角的变化和轴向拉力的变化很敏感。
当拉力增大4~8倍时,联结的刚度可提高20%~50%,但是,过大的拉力在频繁的换刀过程中会加速主轴内孔的磨损,使主轴内孔膨胀,影响主轴前轴承的寿命。
另外,如前所述,这种实心刀柄的锥联结在高速旋转时,主轴端部扩张量大于锥柄的扩张量,高速性能差,不适合超高速主轴与刀具的联结。
三、典型高速主轴/刀具联结设计在高速主轴设计中,目前对刀轴联结研究较成功的设计主要两大类型,一是摒弃原有的7/24标准锥度而采用新思路的替代性设计,如德国的hsk系列和美国的km系列刀具锥柄等。
另一种是为降低成本,仍采用现有的7/24锥度而进行改进性设计,这种设计可实现现有主轴结构向高速化的过渡,如美国的wsu系列刀柄。
1.替代型的设计“曲线耦合”的结构:这种结构由两部分组成,每一部分上面加工有数目相同的螺旋齿,并分别与主轴前端和刀柄固定。
刀具与主轴联结精度较高,联结刚度也较好,装卸刀具需要的轴向移动量很小(5~10mm)。
但对联结用的螺旋齿形精度要求较高,结构的两部分与主轴和刀柄的固定也有较高的要求,另外主轴端部和刀柄需重新设计,换刀时要使两部分齿形精确啮合需较长调整时间,影响换刀速度。
sandvik公司的三棱锥结构:这种刀柄不是圆锥形,而是三棱锥,其棱为圆弧形,锥度为1/20的空心短锥结构[4]。
实现了锥面与端面同时接触定位,三棱结构可实现转矩传递,不再需要传动键,消除了因传动键和键槽引起的动平衡问题。
但三棱锥特别是主轴三棱锥孔加工困难,加工成本高,与现有刀柄不兼容,配合会自锁。
km系列:采用1/10短锥配合,锥柄的长度仅为标准7/24锥柄长度的1/3,由于配合锥度较短,部分解决了端面与锥面同时定位而产生的干涉问题,刀柄设计成中空的结构,在拉杆轴向拉力作用下,短锥可径向收缩,实现端面与锥面同时接触定位。
由于锥度配合部分有较大的过盈量(0.02~0.05mm),所需的加工精度比标准的7/24长锥配合所需的精度低。
与其它类型的空心锥联结相比,相同法兰外径采用的锥柄直径较小,主轴锥孔在高速旋转时的扩张小,高速性能好。
这种系统的主要缺点是,主轴端部需重新设计,与传统的7/24锥联结不兼容;短锥的自锁会使换刀困难;由于锥柄是空心的,所以不能用作刀具的夹紧,夹紧需由刀柄的法兰实现,这样增加了刀具的悬伸量,对于联结刚度有一定的削弱。
由于端面接触定位是以空心短锥和主轴变形为前提实现的,主轴的膨胀会恶化主轴轴承的工作条件,影响轴承的寿命。
hsk刀柄:这种结构是由德国阿亨大学机床研究室(wzl)专为高速机床主轴开发的一种刀轴联结结构,已被din标准化[5]。
hsk短锥刀柄采用1∶10的锥度,它的设计近似于km系列,它的锥体比标准的7/24锥短,锥柄部分采用薄壁结构,锥度配合的过盈量较小,对刀柄和主轴端部关键尺寸的公差带特别严格,由于短锥严格的公差和具有弹性的薄壁,在拉杆轴向拉力的作用下,短锥有一定的收缩,所以刀柄的短锥和端面很容易与主轴相应结合面紧密接触,具有很高的联结精度和刚度。
当主轴高速旋转时,尽管主轴端会产生扩张,短锥的收缩得到部分伸张,仍能与主轴锥孔保持良好的接触,主轴转速对联结刚度影响小。
拉杆通过楔形结构对刀柄施加轴向力(见图2)。
图 2 hsk刀柄与主轴联结结构hsk也有缺点:它与现在的主轴端面结构和刀柄不兼容;制造精度要求较高,结构复杂,成本较高(刀柄的价格是普通标准7/24刀柄的1.5~2倍);锥度配合过盈量较小(是km结构的1/5~1/2),极限转速比km结构低。
2.改进型的设计该类型的联结是以开发出比普通7/24锥联结具有较好精度、刚度和高速性能,同时又能与现存的主轴端部和刀柄兼容为出发点设计出来的。
锥面与端面同时接触定位的wsu-1:这种设计利用了“虚拟锥度”的概念,即以离散的点或线形成一个锥面,与主轴内锥孔面接触(见图3)。
实现这些点线接触的元件是弹性的,因此,当拉杆轴向拉力使刀柄与主轴端面定位接触时,只会使刀柄锥体的这些弹性元件变形,刀柄不变形。
这种方法可使接触锥部获得较大的过盈量,而不需太大的拉力,也不会使主轴膨胀,对接触面的污染不敏感。
图 3 wsu-1刀柄与主轴联结结构wsu-1要求的加工精度与7/24刀柄相同,刀柄的锥部仍采用7/24锥度,但它的直径比相同法兰尺寸的标准刀柄锥度直径要小,锥柄的外表面套有由金属或塑料保持架固定的相同直径的滚珠,由滚珠形成的虚拟锥的直径约比主轴内锥孔直径大5~10μm,在拉杆拉力作用下,滚珠发生弹性变形,刀柄在主轴锥孔内移动直到刀柄法兰与主轴端面接触为止。
滚珠的材料为金属、塑料或者玻璃,但其制造精度要求很高,球面精度和直径的制造精度都在1μm以下,严格的制造精度可以保证虚拟锥与主轴锥孔良好的配合。
虚拟锥与主轴锥孔的接触变形包括滚珠与刀具锥柄、滚珠与主轴锥孔的赫兹变形以及滚珠本身的变形。
这种联结的主要优点有:实现了端面与锥面的同时接触定位,刚度和高速性能好,主轴不会膨胀,对轴承没有影响;接触区变形大,虚拟锥部与主轴锥孔没有间隙,因此刀杆跳动小;拉杆产生的轴向力在接触锥部损失小,因此施加在刀轴接触端面的压力大,接触面摩擦力增大,在某种程度上可用来传递转矩,替代传动键的作用,可取消键,具有良好的动平衡性能。
在拉杆拉力25kn作用下,如接触面摩擦系数为0.35,则50号锥联结可传递的转矩高达360n。
m,大于常规铣削所需的转矩,可取消传动键。
其主要的缺点是:滚珠的加工精度要求很高,否则所形成的虚拟锥与主轴锥孔难以形成良好的配合。
滚珠与锥面接触会产生永久变形,出现压痕,对重复定位精度会有影响。
为了获得良好效果,要求的拉杆拉力较大,建议的拉杆拉力为20~30kn[6]。
kemet公司的absc结构:该结构实现了主轴与刀柄的端面定位,具有很高的轴向联结刚度,主轴的转速对联结的影响很小。
它在结构上仍然采用了7/24的锥度,允许使用标准的7/24刀柄,不同的是,这种结构的专用刀柄中设计有一个内装式的增力器,使用普通的10~15kn 拉杆即可产生较大的轴向拉力,实现刀柄与主轴的端面接触定位。
它的缺点是刀柄的结构复杂,成本较高,而且会使主轴端部膨胀,影响主轴前轴承工作。
改进锥配合的wsu-2结构:对标准的7/24锥配合分析可知,它的主要缺点是配合区特别是配合的后段会出现间隙,引起刚度下降,磨损加剧和跳动等问题,因此只要消除配合后段间隙,这些问题即可解决。
wsu-2就是基于这种考虑,在标准锥柄基础上设计出的一种方案。
如图4所示,刀柄的结构完全与7/24标准锥柄相同,只是在尾部加工有同轴凹槽,凹槽内安装有一列或几列同直径滚珠,滚珠形成的外包络直径约大于刀柄与主轴锥孔配合时可能的间隙直径,滚珠由保持架固定。
刀柄与主轴锥孔配合时,滚珠及其接触区变形,消除配合后段可能出现的间隙,解决了标准锥度联结出现的静态问题。
图 4 wsu-2刀柄设计方案这种方案较好地解决了标准联结的静态问题,对标准7/24锥联结结构改动小,但同轴凹槽的加工精度要求较高,高速时标准7/24锥联结出现的问题仍然存在,因此不适合高速主轴与刀具的联结。
四、结论从以上对现行的标准刀/轴联结和各种改进方案分析可知,刀/轴联结存在的主要问题是联结刚度、精度、动平衡性能、结构的复杂性和制造成本等,为解决这些问题,主要有以下四种方法:(1)对现有结构进行改进,消除联结时联结面间隙,改善标准联结的静态性能;(2)严格规定配合公差,并增大轴向拉力,在不改变标准结构的前提下,实现锥-面同时接触定位;(3)改用小锥度,并采用空心短锥柄结构,实现锥-面同时接触定位;(4)增大配合预过盈量,同时采取措施防止主轴膨胀,改善标准锥柄的高速性能。