湿H2S应力腐蚀、NaOH、氢腐蚀环境下压力容器用钢要求
湿硫化氢腐蚀

二级入口气阀固定螺栓的设计材质为3Cr13, 硬度要求HB280-320。断裂固定螺栓含Cr量 5.967%,硬度高达HRC58.6(相当于HV676)。 且1Cr13、2 Cr13、3 Cr13金相组织为马氏 体,对SSCC最敏感,这样高硬度(远高于 HB235)与敏感的马氏体组织的螺栓在瓦斯 HS+H2O的作用下,
11、 胜利炼油厂FCC吸收解吸塔解吸段塔壁氢鼓
泡开裂。(材质A3,1968年投用,1972年发现HB)
12、 胜南京炼油厂FCC吸收解吸塔降液板使用半
年后出现HB,一个周期后HB处开裂。
13、 胜利炼油厂FCC吸收解吸气后冷凝器壳体使 用不到一年出现氢鼓泡、鼓泡开裂和焊缝开裂。 (T=45℃,P=1 Mpa,介质含H2S6%,CN 0.1%及 少量水分,材质为16Mn)。
2、冷高分底(D102)排污水管线大小头开裂。 2001
年3月7日发现开裂,高压水和H2S喷出。由于发现用 时,未发生次生恶性事故。实际运行一年零三个月, 材质为A234/A234M-910 WPB,碳钢锻件,运行介质 为H2S+NH3+H2O,其中H2S含量34284PPm,NH3含 量为19599PPm,温度为45度,压力为15.6MPa.
扩展造成。
9、 1975年四川气田,16Mn螺旋焊管在试压 仅几个小时后即发生两次爆炸。分析结果是, 焊管补焊处产生马氏体过硬组织,未退火处 理,硬度有的高达RC38-42,因而发生应力 腐蚀快速破裂。以后改为退火处理,硬度降
至RC22以下,未再发生问题。
10、 洛阳炼油厂1#催化气体脱硫装置的溶 剂再生塔(1984年投用,上下SM41B+SUS321, 中间A3R),前13个周期(约12年)运行良 好,1996年4月第14周期开工蒸汽试压时发 现中间段开裂泄漏2次。裂纹位置在降液板
湿H2S腐蚀机理

高压分离器试制技术总结新疆塔里木油田指挥部的高压气液分离器,选用的是稀土合金钢新材料07Cr2AlMoRE 钢板和09Gr2AlMoRE锻件进行制造的。
目的是克服设备中的湿硫化氢应力腐蚀和均匀腐蚀问题。
分离器设计压力10MPa,设计温度80℃,介质为含有湿硫化氢和氯离子的天然气,原油及水的混合物,主要用于高含硫油井的气——油——水的分离。
该设备采用一级初分器,一级旋流器,两级丝网结构分离气液,一级隔板分离油水、外型结构为Ф1200x50x8030。
属Ⅲ类压力容器,共6台。
1、材料选择研究表明,H2S浓度对应力腐蚀的影响明显,湿H2S引起的开裂不仅有硫化氢应力腐蚀(SSCC),氢诱导(HIC)和应力导向氢致开裂(SOHIC)及氢鼓泡(HB)等,其破坏敏感度随H2S浓度增加而增加,在饱和湿硫化氢中达最大值。
液体介质中硫化氢浓度对低碳钢而言,当溶液中H2S浓度从2PPm增加到150PPm时,腐蚀速度增加较快,但只要小于50PPm,破坏时间较长,H2S浓度增加到1600PPm时,腐蚀速度迅速下降,当高于1600PPm——2420PPm时腐蚀速度基本不变,这表明高浓度硫化氢腐蚀并不比低浓度硫化氢腐蚀严重;但对于低合金高强度钢,即使很低的硫化氢浓度,仍能引起迅速破坏。
因此在湿化氢腐蚀环境中,选择设备的各受压元件材料将十分重要,尤其是当硫化氢中含有水份时,决定腐蚀程度的是硫化氢分压,而不是硫化氢的浓度,目前国内石化行业将0.00035Mpa(绝)作为控制值,当气体介质中硫化氢分压大于或等于这一控制值时,就应从设计、制造或使用诸方面采取措施和选择新材料以尽量避免和减少碳钢设备的硫化氢腐蚀。
从材料化学成份方面来说,钢中影响硫化氢腐蚀的主要化学元素是锰和硫,锰元素在设备焊接过程中,产生马氏体、贝氏体高强度,低韧性的显微金相组织,表现出极高硬度,这对设备抗SSCC极为不利,硫元素则在钢中形成MnS,FeS非金属夹杂物,致使局部显微组织疏松,在湿硫氢环境下诱发HIC或SOHIC。
压力容器用钢的基本要求

压力容器用钢的基本要求组别:3组员:陈鑫李福安王曦安全可靠性是压力容器最重要的质量特性,并且与其自身的选材有着密切的关系。
为保障压力容器的安全性,压力容器用钢必须满足的基本要求是:压力容器用钢要具有较高的强度,良好的塑性、韧性、制造性能和与介质相容性。
压力容器用钢是否满足要求,可以从以下几个方面进行分析。
一、化学成分钢材的化学成分对其性能和热处理有较大的影响。
对于用于制造压力容器的钢材必须控制其各化学成分的含量。
钢中常见化学元素对钢性能的影响:1、碳(C):钢中含碳量增加,屈服点和抗拉强度升高,但塑性和冲击性降低。
当碳量0.23%超过时,钢的焊接性能变坏,因此用于焊接的低合金结构钢,含碳量一般不超过0.20%。
碳量高还会降低钢的耐大气腐蚀能力,在露天料场的高碳钢就易锈蚀;此外,碳能增加钢的冷脆性和时效敏感性。
压力容器用钢的含碳量一般不应大于0.25%。
2、硅(Si):在炼钢过程中加硅作为还原剂和脱氧剂。
如果钢中含硅量超过0.50-0.60%,硅就算合金元素。
硅能显著提高钢的弹性极限,屈服点和抗拉强度,故广泛用于作弹簧钢。
在调质结构钢中加入 1.0-1.2%的硅,强度可提高15-20%。
硅和钼、钨、铬等结合,有提高抗腐蚀性和抗氧化的作用,可制造耐热钢。
含硅1-4%的低碳钢,具有极高的导磁率,用于电器工业做矽钢片。
硅量增加,会降低钢的焊接性能。
3、锰(Mn):在炼钢过程中,锰是良好的脱氧剂和脱硫剂,一般钢中含锰0.30-0.50%。
在碳素钢中加入0.70%以上时就算“锰钢”,较一般钢量的钢不但有足够的韧性,且有较高的强度和硬度,提高钢的淬性,改善钢的热加工性能,如16Mn钢比A3屈服点高40%。
锰量增高,减弱钢的抗腐蚀能力,降低焊接性能。
4、磷(P):在一般情况下,磷是钢中有害元素,增加钢的冷脆性,使焊接性能变坏,降低塑性,使冷弯性能变坏。
因此通常要求钢中含磷量小于0.045%,优质钢要求更低些。
5、硫(S):硫在通常情况下也是有害元素。
湿H2S应力腐蚀环境设计原则

湿H2S应力腐蚀环境设计原则及技术要求
一.设计原则
1.钢板采用正火板
2.焊接接头系数XXX
3.腐蚀余量不小于3mm
4.A、B类焊接接头检测射线/xx%/II/AB级
5.焊接接头表面检测标准磁粉/xx%/Ⅰ/A,B,D(内表面)
二.技术要求
1.所有与筒体相焊的内构件均应采用连续焊,其角焊缝应打磨圆滑,A、B类焊接接头(内表面)打磨光滑,D类焊接接头应打磨圆滑。
2.公称直径大于等于250mm的法兰(包括人孔)用锻件级别为III级,其余为Ⅱ级,且热处理状态为正火+回火。
3.本设备制造完毕后应进行整体消除应力热处理,热处理温度为620℃%%p20℃,恒温时间不小于(厚度/25)分钟,热处理后焊缝和热影响区的硬度不得大于HB200。
4.与设备相焊的构件应在热处理前焊接完毕,热处理后不得再在设备上施焊,且不允许在接触介质一侧打钢印。
5.厚度大于等于12mm的钢板应按JB/T4730-2005《承压设备无损检测》逐张进行100%超声检测,Ⅱ级合格。
6.人孔筒节应采用XXX(正火)板,且对接接头进行100%射线检测,Ⅱ级合格。
7.本设备存在湿H2S应力腐蚀环境。
8..明细表中所列法兰数量均不包括配对法兰。
金属在h2s环境中抗硫化应力开裂和应力开裂及应力腐蚀开裂的试验方法
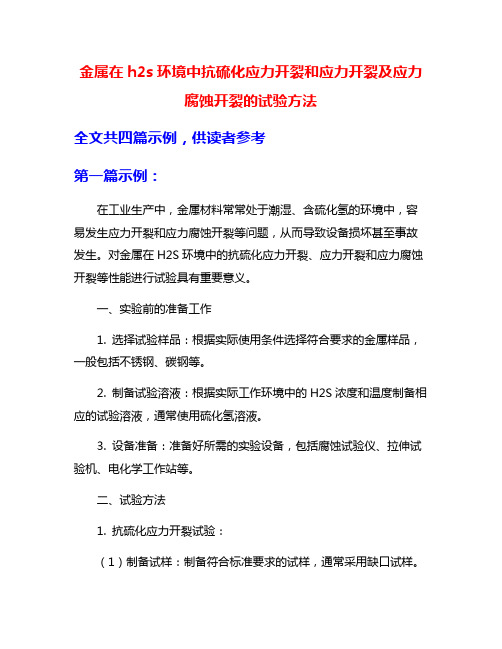
金属在h2s环境中抗硫化应力开裂和应力开裂及应力腐蚀开裂的试验方法全文共四篇示例,供读者参考第一篇示例:在工业生产中,金属材料常常处于潮湿、含硫化氢的环境中,容易发生应力开裂和应力腐蚀开裂等问题,从而导致设备损坏甚至事故发生。
对金属在H2S环境中的抗硫化应力开裂、应力开裂和应力腐蚀开裂等性能进行试验具有重要意义。
一、实验前的准备工作1. 选择试验样品:根据实际使用条件选择符合要求的金属样品,一般包括不锈钢、碳钢等。
2. 制备试验溶液:根据实际工作环境中的H2S浓度和温度制备相应的试验溶液,通常使用硫化氢溶液。
3. 设备准备:准备好所需的实验设备,包括腐蚀试验仪、拉伸试验机、电化学工作站等。
二、试验方法1. 抗硫化应力开裂试验:(1)制备试样:制备符合标准要求的试样,通常采用缺口试样。
(2)浸泡试样:将试样浸泡在硫化氢溶液中,在设定的环境参数下进行实验。
(3)观察试样:观察试样在实验过程中的裂纹情况,记录裂纹扩展情况和断裂形态。
(2)加载试样:在设备上加载试样施加一定的拉伸载荷,使试样发生应力开裂。
三、实验结果分析通过以上试验方法可以获得金属在H2S环境中的抗硫化应力开裂、应力开裂和应力腐蚀开裂等性能数据,可以用于评估金属材料在潮湿硫化氢环境下的使用寿命和性能稳定性。
同时可以针对不同金属材料提出相应的改进措施和防护措施,减少事故发生的风险。
金属在H2S环境中的抗硫化应力开裂、应力开裂和应力腐蚀开裂试验方法对于工业生产中金属材料的安全可靠运行具有重要意义,通过科学准确的试验方法,可以有效提高金属材料的抗腐蚀性能,延长设备的使用寿命,确保工业生产的安全稳定进行。
第二篇示例:金属材料在高硫化氢(H2S)环境中容易发生应力开裂、应力腐蚀开裂等问题,这不仅会降低金属的使用寿命,也可能带来严重的安全隐患。
研究金属在H2S环境中的耐受性是非常重要的。
为了评估金属对硫化氢的抗性,常常需要进行应力腐蚀开裂试验和应力开裂试验。
钢制容器在氢氧化钠溶液中的使用限制

钢制容器在氢氧化钠溶液中的使用限制钢材在常温较稀的氢氧化钠溶液中,表面出现坚牢的保护膜,所以在工业生产和贮运低浓度常温氢氧化钠溶液时,用途很广泛。
随着浓度和温度的升高,钢铁的腐蚀迅速增加,温度越高,腐蚀越严重,承受应力的部件就容易发生应力腐蚀破裂—碱脆。
碱脆,又称苛性脆化,是金属材料在碱性溶液中,由于拉应力和腐蚀介质的联合作用而产生的开裂。
钢的碱脆,一般要同时具备3个条件:一是较高浓度的氢氧化钠溶液;二是较高的温度,碱脆的温度范围较宽,但最容易引起碱脆的温度是在溶液的沸点附近;三是拉伸应力,可以是外载荷引起的应力,也可以是残余应力等,或者是几者的联合作用。
设备要避免碱脆,除了应合理设计零件和构件,减少应力集中外,同时要改善腐蚀环境,还应考虑合理选材,避免使用对应力腐蚀敏感的材料。
在各种金属材料中,普通碳钢和低合金钢材料来源广泛,应用较多。
不锈钢材料可用在中、低浓度的氢氧化钠溶液中,但不耐高浓度高温碱液。
碳钢和低合金钢对常温低浓度的烧碱液有良好的耐蚀性,但随浓度和温度的升高,腐蚀速率也在增大,并在拉应力的作用下可能发生碱脆,应用上存在一定限制和范围。
如HG*****-1998中规定,碳钢和低合金钢焊制化工容器,如焊后或冷加工后,不进行消除应力热处理,则在氢氧化钠溶液中的使用温度不得大于附表1的温度。
当氢氧化钠溶液在其与烃类的混合问中体积≥5%时,也应根据氢氧化钠溶液的浓度符合该表的要求,氢氧化钠溶液浓度≤1%或氢氧化钠溶液在其与烃类的混合物中体积﹤5%时,不受限制。
由表1可见,在一定范围内,碳钢和低合金钢可直接使用而不必进行消应力热处理,随着浓度的增加,它所对应的适用温度的有所下降。
(附表1)A区:碳钢不必作应力消除;B区:碳钢焊缝及弯头应作应力消除C区:在此区域内应考虑用镍合金或不锈钢;B区及C区域:镍合金适用于阀门然而,有关资料表明,碳钢或低合金钢材料即使在消除应力热处理后,它们在较高浓度和温度的氢氧化钠溶液中使用还是存在限制。
浅谈基于湿硫化氢应力腐蚀的压力容器设计和制造
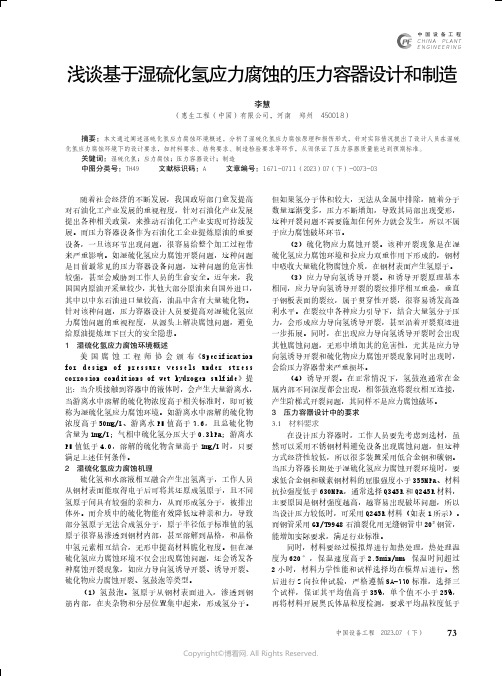
中国设备工程 2023.07 (下)
73
Copyright©博看网. All Rights Reserved.
Research and Exploration 研究与探索·工艺流程与应用
6 级,材料非金属杂物不能超过 1.5 级,其门槛值要等 于实际屈服强度的 80%。另外,针对螺旋材料,工作人 员通常选择低强度普通碳素钢和低合金钢,普通碳素钢 采用正火,低合金钢应长时间处于调质状态。并保证焊 接材料中的磷含量、硫含量和母体相互配备,其焊缝熔 敷金属硬度小于 200HBW,焊条要采用低氢型材料,这种 材料中硅元素和锰元素含量较低,埋弧自动焊和焊条电 弧焊所使用的焊接材料锰含量在 1.0% 左右,硅含量为 0.50%。
表 3 湿硫化氢应力腐蚀环境下压力容器用碳素钢和低合金钢选 用原则
H2S 分压 /MPa
化学成分
硬度
强度
其他
Ceq=w(C)+w(Mn)
母材和焊接材
焊接接
/6 ≤ 0.40%,W
料强度相同, 焊接后的
0.00035
头硬度
(SI)≤ 1.0%,
屈服强度小于 构件外层
~ 0.001
超过
禁止焊缝中出现
355MPa,抗拉强 纤维变形
硬度试验
每个开口接管和筒体焊接接头各一组
6 尺寸检查
各部位尺寸
蚀环境下,很容易给压力容器性能带来严重影响。因此, 在设计压力容器时,工作人员要考虑容器材料各方面的 性能,如焊接性能、热处理性能、冷加工性能等,结合 设备操作环节设计运行数据,从而计算出介质对压力容 器选材阶段带来的影响(如表 3 所示)。
细晶粒钢
强度低于 630MPa
氏体熔敷金属
湿硫化氢应力腐蚀环境下压力容器选材的探讨

湿硫化氢应力腐蚀环境下压力容器选材的探讨作者:明勇姚蓉来源:《中国化工贸易·下旬刊》2018年第04期摘要:针对压力容器设备在湿硫化氢环境中所产生的应力腐蚀破坏,结合实际经验,讨论了在不同情况下压力容器用钢的选材要求。
关键词:湿硫化氢;应力腐蚀;压力容器1 湿硫化氢应力腐蚀环境定义湿硫化氢导致压力容器的应力腐蚀破坏是有条件的,只有在应力、材质、腐蚀介质三个因素相匹配的共存区域,才具备产生应力腐蚀的基本条件,偏离三个因素中的任何一个因素,应力腐蚀就不可能产生,此时湿硫化氢气体存在与应力腐蚀全然无关。
化工行业标准中规定必须同时满足下列条件才能形成硫化氢的应力腐蚀环境:①温度小于等于(60+2p)℃;②硫化氢分压大于等于0.00035MPa,即相当于常温在水中的H2S溶解度大于或等于7.7mg/L;③介质中含有液相水或处于水的露点温度以下;④pH2 设计选材时应着重考虑因素湿硫化氢应力腐蚀环境下压力容器设计选材时,需着重考虑湿硫化氢带来的应力腐蚀开裂(SCC)。
一旦发生应力腐蚀开裂,将直接导致压力容器失效、爆炸,后果非常严重。
除此之外,湿硫化氢所引起的开裂形式还有硫化物应力开裂(SSC)、氢鼓包(HB)、氢致裂纹(HIC)以及应力向氢诱发开裂(SOHIC)等。
影响硫化物应力开裂、氢诱发开裂和氢鼓包的因素主要为材料因素和环境因素两大类。
其中材料因素中的硬度(强度)、显微组织和化学成分是主要因素。
3 化学成分影响在合金钢中,一般加入Mn、Cr、Ni等元素来提高淬透性,特别是Ni的作用,一般认为Ni对于合金钢的韧性是有益的,但是含Ni钢上析氢的的过电位低,氢离子易于放电还原,从而促进了氢的析出,因而Ni钢的抗硫化物应力腐蚀的能力较差。
故一般来说,要求碳素钢和低合金钢中Ni含量小于1%或尽可能不含Ni。
钢中影响硫化氢腐蚀的主要元素是Mn和S。
Mn在设备焊接过程中,会产生马氏体及贝氏体高强度、低韧性的显微金相组织,表现出极高硬度,这对设备抗硫化物应力腐蚀极为不利。
湿H2S环境金属材料防腐解析
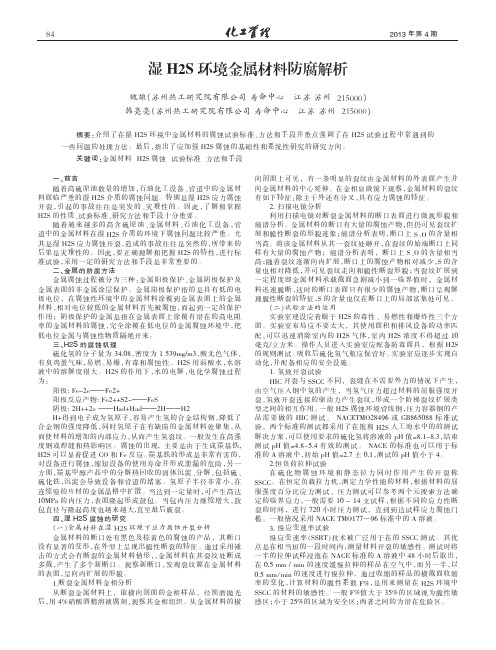
2013年第4期湿H2S环境金属材料防腐解析魏雄(苏州热工研究院有限公司寿命中心江苏苏州215000)韩亮亮(苏州热工研究院有限公司寿命中心江苏苏州215000)摘要:介绍了在湿H2S环境中金属材料的腐蚀试验标准、方法和手段并重点强调了在H2S试验过程中常遇到的一些问题的处理方法。
最后,指出了应加强H2S腐蚀的基础性和系统性研究的研究方向。
关键词:金属材料H2S腐蚀试验标准方法和手段一、前言随着高硫原油数量的增加,石油化工设备、管道中的金属材料面临严重的湿H2S介质的腐蚀问题。
特别是湿H2S应力腐蚀开裂,引起的事故往往是突发的、灾难性的。
因此,了解和掌握H2S的性质、试验标准、研究方法和手段十分重要。
随着越来越多的高含硫原油、金属材料、石油化工设备,管道中的金属材料在湿H2S介质的环境下腐蚀问题比较严重。
尤其是湿H2S应力腐蚀开裂,造成的事故往往是突然的,所带来的后果是灾难性的。
因此,要正确理解和把握H2S的特性,进行标准试验,采用一定的研究方法和手段是非常重要的。
二、金属的防腐方法金属腐蚀过程被分为三种:金属阳极保护、金属阴极保护及金属表面的非金属涂层保护。
金属阳极保护指的是具有低的电极电位,在腐蚀性环境中的金属材料涂覆到金属表面上的金属材料,相对电位较低的金属材料首先被腐蚀,而起到一定的保护作用;阴极保护的金属是指在金属表面上涂覆有潜在的高电阻率的金属材料的腐蚀,完全涂覆在低电位的金属腐蚀环境中,把低电位金属与腐蚀性物质隔绝开来。
三、H2S的腐蚀机理硫化氢的分子量为34.08,密度为1539mg/m3,酸无色气体,有臭鸡蛋气味,易燃、易爆,有毒和腐蚀性。
H2S用弱酸水,水溶液中的溶解度很大。
H2S的作用下,水的电解,电化学腐蚀过程为:阳极:Fe-2e———Fe2+阳极反应产物:Fe2++S2-———FeS阴极:2H++2e———Had+Had———2H———H2H+得到电子成为氢原子,容易产生氢的合金结构钢,降低了合金钢的强度降低,同时氢原子在有缺陷的金属材料处聚集,从而使材料的增加的内部应力,从而产生氢裂纹。
压力容器用钢材

压力容器用钢材的选用 在压力容器设计中,正确地选择钢材,对保证容器的使用安全、结构合理和降低制造成本是至关重要的。 一般规定 压力容器用材料的质量及规格,应符合相应的国家标准、行业标准的规定。 压力容器用钢应考虑容器的使用条件(如设计温度、设计压力、介质特性和操作特点等)、材料的焊接性能、容器的制造工艺以及经济合理性。 压力容器专用钢材的磷含量不应大于0.03%,硫含量不应大于0.02%;用于焊接压力容器主要受压元件的碳素钢和低合金钢,其含碳量不应大于0.25%
*
材料的屈服极限、强度极限和弹性模量随温度的升高而降低,如果材料在高温下承受高的应力,则材料的抗蠕变性能是关键性的。
*
耐腐蚀性能 耐腐蚀性能是金属材料抵抗介质腐蚀的能力。压力容器中处理的介质大多数具有腐蚀性的,在设计中必须根据操作介质来选择耐腐蚀材料. 如果腐蚀发生在整个金属表面上,则称为金属的全面腐蚀;如果腐蚀均匀地分布在整个金属表面,则称为均匀腐蚀;如果腐蚀只发生在金属表面的局部区域,其余大部分表面不腐蚀,称之为局部腐蚀。 均匀腐蚀 均匀腐蚀是在整个金属表面均匀地发生腐蚀,这种腐蚀相对其它形式的腐蚀其危害最小。GB150中C2只考虑均匀腐蚀 . C2=KB 其中B—设计寿命(年) K—腐蚀速率(mm/ 年 )
式中各元素的符号代表钢中含量的百分数.
*
一般认为: 当Ceq<0.4%时,钢材的淬硬倾向不大,可焊性优良,焊接时不必预热.
当Ceq=0.4%-0.6%时,钢材的淬硬倾向增大,可焊性有限,焊接时需要预热.控制焊接线能量等工艺措施.
单击此处添加小标题
当Ceq>0.6%时, 淬硬倾向严重,属于较难焊接的钢材,需要采取较高的预热温度和严格的工艺措施.
*
磷(P)--磷可以固溶在钢的铁素体中,降低了钢的延伸率及断面收缩率。磷对钢最有害的影响是降低冲击韧性,随着钢中磷含量的增加,钢发生脆化,最终甚至引起常温脆化。例如:钢中含0.25%的磷(P)其冲击值为零.在一般钢中,随着磷含量增加,其脆性转变温度(NDT)也显著地增加.磷含量不高也容易引起偏析,而且其扩展速度很慢,不易用热处理方法消除偏析.另外,磷和氧亲和力较强,会恶化可焊性和可锻性.所以,磷也是有害杂质, “容规”中对容器用钢中对P含量的限制有明确的规定。 氢—氢原子半径极小,在钢中扩散速度比其它元素大得多,很容易透过晶格.氢可引起钢的1)氢脆;2)韧性下降;3)产生延迟裂纹;4)产生白点;5)焊接时产生凹裂纹等,为了克服这些问题,可采取真空熔炼等办法进行脱氢。另外,焊接时,焊条、焊剂要烘干。焊缝处消氢处理也是有效方法之一。
湿硫化氢环境环境用钢

1、下列环境发生湿H2S腐蚀开裂:(1)含游离水;(2)以下四个条件之一:(i)游离水中H2S溶解量大于50ppmw;(ii)游离水pH值小于4,且有溶解的H2S存在;(iii)游离水pH值大于7.6,水中溶解的HCN大于20ppmw,且有溶解的H2S存在;(iv) H2S在气相中的分压大于0.0003MPa。
2、特别是当设备和管道的介质环境符合以下任何一条时称为湿H2S严重腐蚀环境:(1)液相游离水的pH值大于7.8,且在游离水中的H2S大于2000ppm;(2)液相游离水的pH值小于5,且在游离水中的H2S大于50ppm;(3)液相游离水中存在HCN或氢氰酸化合物,且大于20ppm。
二、设计、制造要求1、设备和管道如选用碳素钢或低合金钢,必须是镇静钢;2、对湿H2S腐蚀环境下的碳素钢或低合金钢制设备和管线,材料的使用状态应是正火、正火+回火或调质状态;3、材料的碳当量CE应不大于0.43(CE=C+Mn/6+(Cr+Mo+V)/5+(Ni+Cu)/15;式中各元素符号是指该元素在钢材中含量百分比);4、在湿H2S严重腐蚀环境下,当材料的抗拉强度大于480MPa时要控制其S含量不大于0.002%,P含量不大于0.008%,Mn含量不大于1.30%,且应进行抗HIC性能试验或恒负荷拉伸试验。
5、在湿H2S环境下,应尽量少选择焊接。
如采取焊接,原则上应进行焊后消除应力热处理,热处理温度应按标准要求取上限。
6、热处理后碳素钢或碳锰钢焊接接头的硬度应不大于HB200,其它低合金钢母材和焊接接头的硬度应不大于HB237;7、热加工成形的碳素钢或低合金钢制管道元件,成形后应进行恢复力学性能热处理,且其硬度不大于HB225;8、冷加工成形的碳素钢或低合金钢制设备和管道元件,当冷变形量大于5%时,成形后应进行消除应力热处理,且其硬度不大于HB200。
但对于冷变形量不大于15%且硬度不大于HB190时,可不进行消除应力热处理;9、接触湿硫化氢环境碳素钢螺栓的硬度应不大于HB200,合金钢螺栓的硬度应不大于HB225;10、铬钼钢制设备和管道热处理后母材和焊接接头的硬度应不大于HB225(1Cr-0.5Mo、1.25Cr-0.5Mo)、HB235(2.25Cr-1Mo、5Cr-1Mo)和HB248(9Cr-1Mo);11、铁素体不锈钢、马氏体不锈钢和奥氏体不锈钢的母材和焊接接头的硬度应不大于HRC22,其中奥氏体不锈钢的碳含量不大于0.10%,且经过固溶处理或稳定化处理;12、双相不锈钢的母材和焊接接头的硬度应不大于HRC28,其铁素体含量应在35-65%的范围内;13、容器内在焊接接头两侧50mm范围内的表面进行防护,可在表面喷锌、喷铝并用非金属涂料封闭的方法;14、不使用承插焊形式的管件;15、结构上应尽量避免应力集中;16、设备壳体或卷制管道用钢板厚度大于12mm时,应按JB/T4730进行超声波检测,符合Ⅱ级要求。
湿硫化氢环境中承压特种设备应力腐蚀研究与防治措施
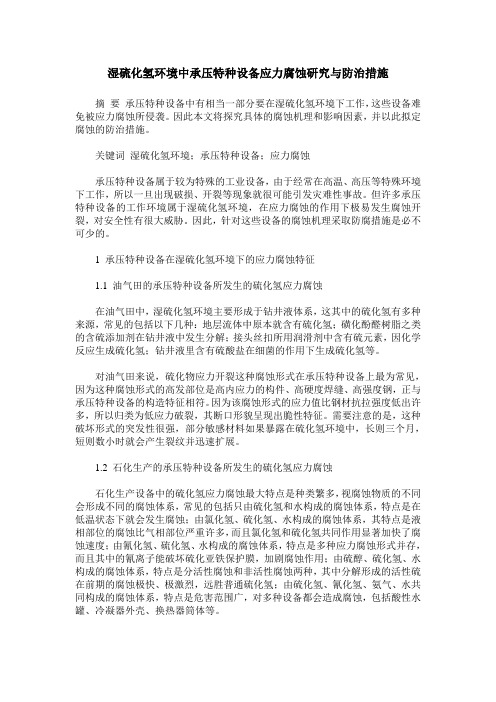
湿硫化氢环境中承压特种设备应力腐蚀研究与防治措施摘要承压特种设备中有相当一部分要在湿硫化氢环境下工作,这些设备难免被应力腐蚀所侵袭。
因此本文将探究具体的腐蚀机理和影响因素,并以此拟定腐蚀的防治措施。
关键词湿硫化氢环境;承压特种设备;应力腐蚀承压特种设备属于较为特殊的工业设备,由于经常在高温、高压等特殊环境下工作,所以一旦出现破损、开裂等现象就很可能引发灾难性事故。
但许多承压特种设备的工作环境属于湿硫化氢环境,在应力腐蚀的作用下极易发生腐蚀开裂,对安全性有很大威胁。
因此,针对这些设备的腐蚀机理采取防腐措施是必不可少的。
1 承压特种设备在湿硫化氢环境下的应力腐蚀特征1.1 油气田的承压特种设备所发生的硫化氢应力腐蚀在油气田中,湿硫化氢环境主要形成于钻井液体系,这其中的硫化氢有多种来源,常见的包括以下几种:地层流体中原本就含有硫化氢;磺化酚醛树脂之类的含硫添加剂在钻井液中发生分解;接头丝扣所用润滑剂中含有硫元素,因化学反应生成硫化氢;钻井液里含有硫酸盐在细菌的作用下生成硫化氢等。
对油气田来说,硫化物应力开裂这种腐蚀形式在承压特种设备上最为常见,因为这种腐蚀形式的高发部位是高内应力的构件、高硬度焊缝、高强度钢,正与承压特种设备的构造特征相符。
因为该腐蚀形式的应力值比钢材抗拉强度低出许多,所以归类为低应力破裂,其断口形貌呈现出脆性特征。
需要注意的是,这种破坏形式的突发性很强,部分敏感材料如果暴露在硫化氢环境中,长则三个月,短则数小时就会产生裂纹并迅速扩展。
1.2 石化生产的承压特种设备所发生的硫化氢应力腐蚀石化生产设备中的硫化氢应力腐蚀最大特点是种类繁多,视腐蚀物质的不同会形成不同的腐蚀体系,常见的包括只由硫化氢和水构成的腐蚀体系,特点是在低温状态下就会发生腐蚀;由氯化氢、硫化氢、水构成的腐蚀体系,其特点是液相部位的腐蚀比气相部位严重许多,而且氯化氢和硫化氢共同作用显著加快了腐蚀速度;由氰化氢、硫化氢、水构成的腐蚀体系,特点是多种应力腐蚀形式并存,而且其中的氰离子能破坏硫化亚铁保护膜,加剧腐蚀作用;由硫醇、硫化氢、水构成的腐蚀体系,特点是分活性腐蚀和非活性腐蚀两种,其中分解形成的活性硫在前期的腐蚀极快、极激烈,远胜普通硫化氢;由硫化氢、氰化氢、氨气、水共同构成的腐蚀体系,特点是危害范围广,对多种设备都会造成腐蚀,包括酸性水罐、冷凝器外壳、换热器筒体等。
湿硫化氢环境下压力容器钢板的应力腐蚀机理与材料选择

湿硫化氢环境下压⼒容器钢板的应⼒腐蚀机理与材料选择2019-07-16摘要:钢板材料在湿H2S环境中,如果硬度偏⾼,同时有拉伸应⼒存在,容易导致应⼒腐蚀发⽣,造成严重后果。
⽂章利⽤实验室实验⽅法分析应⼒腐蚀原因,对钢板提出了技术要求来预防湿硫化氢应⼒腐蚀。
关键词:钢板;硬度;湿硫化氢;应⼒腐蚀破裂⽯油化⼯及油⽥采油设备处理的原油中含H2S,随着⾼硫⾼酸原油加⼯量的增加,硫化氢对设备的腐蚀也愈加严重,已成为⽯化⾏业较为突出的问题,特别是湿H2S应⼒腐蚀开裂,所引起的事故往往是突发的、灾难性的。
因此,开展H2S腐蚀的相关研究对于确保⽯化设备的安全运转以及提⾼⽯化⾏业的⽣产效率具有重⼤的理论和实际意义。
1 湿硫化氢环境中的腐蚀分类1.1 在硫化物腐蚀环境和静态拉应⼒同时作⽤下产⽣的开裂称硫化物应⼒腐蚀开裂(SSCC)。
这是酸性环境中破坏性和危害性最⼤的⼀种腐蚀。
1.2 氢致开裂(HIC)与SSCC的驱动⼒不同,HIC不需要像SSCC那样的外⼒,其⽣成裂纹的驱动⼒是靠进⼊钢中的氢产⽣的⽓压,当氢⽓压超过材料屈服强度时便产⽣变形开裂,裂纹间相互扩展连接形成阶梯型开裂(SWC)。
2 实验⽅法的选择与应⽤2.1 A.SSCC实验SSCC⽅法的适⽤性:模拟由外⼒或作应⼒引起的硫化物应⼒腐蚀开裂的实验,可作为压⼒容器等产品的标准检验⽅法,同时可研究H2S对不同材料和不同⼯艺性能的影响。
⼀般情况推荐使⽤美国腐蚀⼯程师协会NACETM0177 标准中的A法,即恒负荷拉伸实验法,实验采⽤饱和的H2S⽔溶液(质量浓度约3250mg/L),配制时应注意使⽤冰⼄酸(冰醋酸),其积体分数为99.5%。
应⼒值和时间的确定:实验过程中,对于施加的应⼒可参考GB/T15970.1-1995标准的⼆元搜索法来确定临界应⼒,实验后的应⼒腐蚀数据采⽤统计⽅法进⾏处理。
不论施加应⼒或试样暴露到腐蚀环境的顺序如何,都以试样暴露到腐蚀环境开始计时。
压力容器用钢的硫化氢应力腐蚀

压力容器用钢的硫化氢应力腐蚀随着压力容器储存介质的范围不断扩大,使压力容器的经济效益一直在不断提高,但是在实际应用过程中,压力容器设备会出现应力腐蚀的情况,通过对现有压力容器应力腐蚀所产生的原因以及性质进行分析,了解压力容器设备的工作条件以及影响因素,提出减缓设备发生应力腐蚀的措施,以及在不同环境下对压力容器用钢的选材要求,从而进一步提高压力容器的经济效益。
标签:压力容器;硫化氢;应力腐蚀高含硫天然气压力容器管道采用的材质为抗硫不锈钢,对这种压力容器的腐蚀缺陷主要表现在为均匀减薄和点蚀,对含有点蚀缺陷的管材进行强度评价,确定其管道缺陷所允许的最大操作压力,做出正确的决策,帮助管道可以继续使用,减少压力容器的运行压力,并进行相应的缺陷修复工作,才可以让压力容器的使用寿命增加,节约相应的维修成本,进而避免管道发生事故。
1压力容器应力腐蚀特征分析目前,我国很多工厂的压力容器设备已经使用很多年,因此在生产过程中往往会发生应力腐蚀开裂的现象。
应力腐蚀开裂的裂纹经常发生在焊缝、熔合以及热影响区,很多研究学者称这些焊缝裂纹为应力腐蚀裂纹。
压力容器设备所使用的材质均为低碳、低合金钢材料。
从压力容器设备所在的环境介质以及温度条件上看,压力容器设备发生应力腐蚀的关键因素为酸露点温度,再生设备表面会形成结露状态,为腐蚀因素创造腐蚀条件。
通过对压力容器设备腐蚀裂纹的部位以及扩展方向来看,裂纹发生的部位大多数为焊缝、熔合或者焊接热影响区域,裂纹会在垂直于焊缝方向进行扩展,所形成的裂纹比较短,其样式多为树枝状分叉。
由此可以说明压力容器设备的应力腐蚀开裂与设备焊接后的金属组织变化以及焊接剩余应力有着直接关系,简单来讲就是设备焊接区为应力腐蚀失效的主要部位,因此应当注重这些部位的腐蚀防护。
2钢在硫化氢环境下的腐蚀机理2.1氢鼓泡钢在HZS水溶液会发生电化学反应,反应出来活性很强的氢会向钢中渗透,在钢材内部形成氢分子,随着氢分子的不断增加,所形成的压力也会不断提高,最终导致夹杂物尖端产生鼓泡,产生氢鼓泡的主要位置为钢中夹杂物与其他炼金不连续处。
压力容器特殊介质的使用

《压力容器安全技术监察规程》(99版)修订说明及条文解释关于“压力容器选材与介质”的说明原化工行业标准HCJ15—1989《钢制化工容器选用规定》,已于1998年11月修订并由国家石油和化学工业局批准发布,标准号为HG20581—1998。
在HG20581—1998中有专门章节对碳钢和低合金钢焊制容器在NaOH、湿H2S应力腐蚀环境、高温高压氢腐蚀环境以及液氨等四种介质环境中使用时,选材、制造、检验应遵循的要求进行了规定,这些规定的主要内容及措施、指标都是国际上较为一致的,且为各国工程公司或协会(如API、NACE)以文件形式予以肯定的。
现将HG20581中有关章节摘录于下,供参考。
6.7 使用介质的限制6.7.1 NaOH溶液碳钢及低合金钢焊制化工容器如焊后或冷加工后,不进行消除应力热处理,则在NaOH溶液中的使用温度不得大于表17所列的温度。
当NaOH溶液在其与烃类的混合物中体积≥5%时,也应根据NaOH溶液的浓度符合该表要求。
NaOH溶液浓度≤1%或NaOH溶液在其与烃类的混合物中体积<5%时,不受限制。
6.7.2 湿H2S应力腐蚀环境6.7.2.1 腐蚀环境当化工容器接触的介质同时符合下列各项条件时,即湿H2S应力腐蚀环境:a.温度≤(60+2p)℃;p为压力,MPa(表压)b.H2S分压≥0.00035MPa即相当于常温在水中的H2S溶解度≥10-5;c.介质中含有液相水或处于水的露点温度以下;d.pH<9或有氰化物(HCN)存在。
6.7.2.2 材料要求及限制在湿H2S应力腐蚀环境中使用的碳钢及低合金钢应符合下列各条要求;a.材料标准规定的屈服强度σs≤355MPa;b.材料实测的抗拉强度6b≤630MPa;c.材料使用状态应至少为正火+回火、退火、调质状态;d.碳当量限制(当碳当量限制超标时,应加大硬度限制的检测频度);低碳钢和碳锰合金:CE≤0.40,CE=[C]+[Mn]/6低合金钢(包括低温镍钢):CE≤0.45,CE=[C]+[Mn]/6+([Cr]+[Mo]+[V]/5)+([Ni]+[Cu])/15e.对非焊接件或焊后经回火热处理的材料,硬度限制如下:低碳钢HV(10)≤220(单个值)低合金钢HV(10)≤245(单个值)f.壳体用钢板厚度>20mm,应按JB4730进行超声波探伤,符合Ⅱ级要求。
几种化学物质对压力容器的应力腐蚀

几种化学物质对压力容器的应力腐蚀引言(1)应力腐蚀是金属材料在腐蚀性介质和拉伸应力的共同作用下发生的一种破坏形式。
金属发生应力腐蚀时,腐蚀和应力这两个因素相互促进的,一方面腐蚀使金属的有效截面积减小和表面上形成缺口,产生应力集中,如果是晶间腐蚀,则会使金属晶粒之间的结合力降低;另一方面,应力加速了腐蚀的进展,使表面缺口向更深处(或沿晶间)扩展,最终导致断裂。
在应力腐蚀中,如果应力是交变的拉伸应力,这种腐蚀叫做疲劳腐蚀。
在疲劳腐蚀过程中,首先也是在表面形成腐蚀缺口引起应力集中,成为疲劳裂纹的策源点。
在交变拉伸应力的作用下,被破坏的保护膜无法再恢复,沉积在腐蚀坑底部的始终是处在活性状态且构成腐蚀电池的阳极。
这样在腐蚀与交变应力的共同作用下,裂纹不断扩散直至金属材料最后断裂。
压力容器的腐蚀破裂都是应力腐蚀,因为压力容器一般都承受较大的拉伸应力,而它的结构也常常难以避免地有程度不同的应力集中处,如设备的开孔、焊缝等,且容器的工作介质又常常是带腐蚀性的。
液氨对碳钢及低合金钢容器的应力腐蚀(2)液氨的储存和运输大部分用碳钢或低合金钢制压力容器。
近年来国内外多次发生液氨储罐破裂爆炸事故,事故分析表明,很多是由于应力腐蚀造成的。
另外,对未发生事故的液氨球罐进行检查,相继发现了程度不同的数量很多的裂纹,这些裂纹大都分布在长期处于液面下部的南极板与下温带组焊的周向焊缝上。
一般情况下,无水液氨只对钢产生很轻微的均匀腐蚀。
但液氨储罐在充装、排料及检修过程中,容易受空气的污染,空气中的氧和二氧化碳则促进氨对钢的腐蚀,其反应如下:反应中的氨基甲酸氨对碳钢有强烈的腐蚀作用,使钢材表面的钝化膜产生破裂,并在此产生阳极型腐蚀。
由于焊缝处残余应力较高,所以应力腐蚀严重。
许多资料表明,液氨球罐所用的钢材强度越高,产生应力腐蚀裂纹的倾向越大。
此外,容器的工作温度愈高、液氨中氧含量越高,其应力腐蚀也越严重。
采取下列措施有利于防止液氨对储存容器的应力腐蚀:1.焊接时,采取措施尽量消除残余应力。