模具制造工艺规程的设计c
模具工艺制造及注塑成型加工流程

对半精加工后的模具进行精细加工 ,包括研磨、抛光等,使模具达到 最终的精度要求。
组装与调试
将各部分模具组装在一起,进行试 模、调整、优化,确保模具能够正 常工作并满足生产要求。
模具制造的设备与工具
数控加工中心
用于模具的铣削、车 削等粗加工和半精加 工。
磨床
用于模具的磨削和精 加工,提高模具的表 面质量和精度。
翘曲
气泡
翘曲是指塑料制品在冷却过 程中出现弯曲、扭曲等现象, 可以通过调整模具温度和注 射压力来改善。
气泡是指在塑料制品内部或 表面出现的气泡状缺陷,可 以通过调整注射速度和注射 压力来改善。
05
注塑成型加工的设备与工具
注塑机的分类与选择
按塑化方式分类 柱塞式注塑机
预塑式注塑机
注塑机的分类与选择
加工过程监控
对加工过程中的关键环节进行监控,确保加 工质量稳定可靠。
成品检验
对最终的模具成品进行全面检验,包括尺寸、 表面质量、精度等。
04
注塑成型加工流程
注塑成型的基本原理
注塑成型是一种塑料加工方法,通过 将热塑性塑料注入模具型腔,在冷却 和固化后获得所需形状的塑料制品。
注塑成型适用于各种塑料材料,如聚 乙烯、聚丙烯、聚氯乙烯等,广泛应 用于汽车、家电、包装、医疗器械等 领域。
模具工艺制造及注塑成型 加工流程
• 模具工艺制造概述 • 模具设计 • 模具制造 • 注塑成型加工流程 • 注塑成型加工的设备与工具 • 模具工艺制造及注塑成型加工的应用
与发展趋势
01
模具工艺制造概述
模具的定义与分类
模具定义
模具是一种用于制造特定形状和尺寸 零件的工具,通过模具成型可得到所 需的产品。
模具制造工艺学课程教学设计

附件1:《模具制造工艺学》课程教学设计方案适用专业:模具设计与制造编制人:侯毅红编制单位:机械工程系编制日期:年月日审核人:崔海花系部主任:师鹏周口科技职业学院教务处制年月日《模具制造工艺学》课程教学设计方案一、《模具制造工艺学》课程整体教学设计方案(一)基本信息课程名称:模具制造工艺学学时:84课程类型:专业课学分:4所属系部:机械工程系授课对象:模具设计与制造专业先修课程:《机械制图》《机械基础》《数控机床与编程技术》《公差配合与技术测量》《冲压工艺与模具设计》《塑料工艺与模具设计》后续课程:模具制造工艺学课程设计制定时间:批准人:课程团队负责人及成员:侯毅红叶艳秋胡桂领(二)课程定位本门课程是模具设计与制造专业的专业课,主要讲授机械加工工艺的基础理论,模具的常规及特种加工方法和装配工艺。
(三)课程设计1、课程目标设计(1)知识与能力目标:①掌握机械加工工艺的基础理论和模具制造工艺的基础知识,熟悉模具的加工工艺及装配工艺。
②具有编制模具制造工艺规程以及分析、解决模具制造中一般工艺技术问题的能力。
③了解模具制造新技术,新工艺及其发展。
(2)情感知识目标:通过对模具制造工艺的学习,具有编制模具制造工艺规程以及分析、解决模具制造中一般工艺技术问题的能力,从中感受学习的快乐与幸福,从快乐中养成一丝不苟的工作态度、良好的职业道德,以及团结协作、不怕困难、勇于创新的精神。
通过对模具制造的实践,加深对涉猎有关的技术、知识、态度、经营、交往的理解,逐渐的热爱模具技术工作,并有为之献身的职业精神,从而形成不断创新、勇攀高峰、立志创业的意识。
(四)课程设计1、课程教学内容设计绪论教学要求:了解我国模具行业的现状与发展趋势;模具制造技术的基本要求及特点;本课程的性质、任务、学习本课程的基本要求。
教学重点:本课程的作用与任务、我国模具行业的现状与发展趋势、模具制造的特点、学习本课程的基本要求。
教学难点:我国模具行业的发展趋势课时安排:本章安排2课时。
模具高级工(A卷及答案)
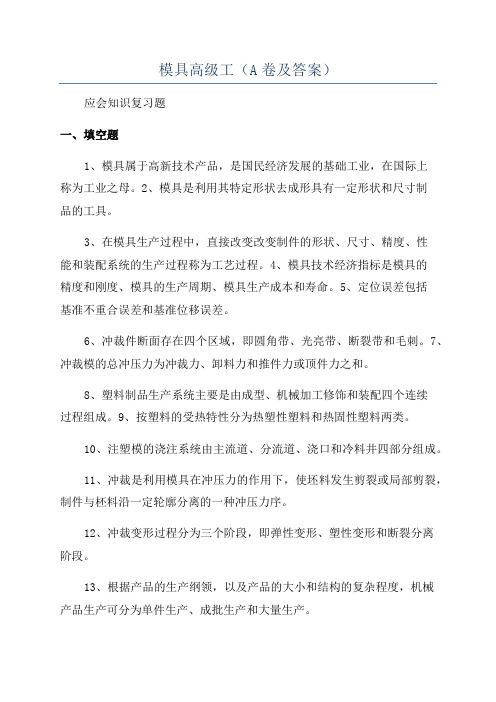
模具高级工(A卷及答案)应会知识复习题一、填空题1、模具属于高新技术产品,是国民经济发展的基础工业,在国际上称为工业之母。
2、模具是利用其特定形状去成形具有一定形状和尺寸制品的工具。
3、在模具生产过程中,直接改变改变制件的形状、尺寸、精度、性能和装配系统的生产过程称为工艺过程。
4、模具技术经济指标是模具的精度和刚度、模具的生产周期、模具生产成本和寿命。
5、定位误差包括基准不重合误差和基准位移误差。
6、冲裁件断面存在四个区域,即圆角带、光亮带、断裂带和毛刺。
7、冲裁模的总冲压力为冲裁力、卸料力和推件力或顶件力之和。
8、塑料制品生产系统主要是由成型、机械加工修饰和装配四个连续过程组成。
9、按塑料的受热特性分为热塑性塑料和热固性塑料两类。
10、注塑模的浇注系统由主流道、分流道、浇口和冷料井四部分组成。
11、冲裁是利用模具在冲压力的作用下,使坯料发生剪裂或局部剪裂,制件与柸料沿一定轮廓分离的一种冲压力序。
12、冲裁变形过程分为三个阶段,即弹性变形、塑性变形和断裂分离阶段。
13、根据产品的生产纲领,以及产品的大小和结构的复杂程度,机械产品生产可分为单件生产、成批生产和大量生产。
14、渐开线上任意一点的法线必与其基圆相切。
15、塑料是由从石油生产出来的合成树脂加入增塑剂、稳定剂和填料等物质组成的固件材料。
16、按成型加工方法的不同,塑料模可分为:注塑模、压塑模、挤出模、吹塑模和吸塑模等类型。
17、注塑成型是一个循环过程,完成注塑成型需要经过预塑、注塑阶段和冷却材料三个阶段。
18、注塑模具中完成活动型芯抽出和复位的机构叫做抽芯机构。
19、模具制造过程中的二类工具是指加工模具和装配所用的各种专用工具。
20、电铸工艺是利用金属电镀原理,使母模表面获得一定厚度的金属沉淀层。
21、塑料是以有机高分子化合物为基础,加入若干其他材料制成的固体材料。
22、塑料的密度是三大类主要结构材料中最小,具有较高的比强度。
23、在机械产品的整个生产过程中,直接改变生产对象的形状、尺寸、性能及位置的过程称为工艺过程。
模具制造工艺规程的基础知识选择题

模具制造工艺规程的基础知识选择题、1.轴类零件在一台车床上连续完成车端面、外圆和切断。
此时工序为(A )。
(1-1)A一个 B两个 C三个 D四个2.为完成一定的工序部分,一次装夹工件后,工件与夹具或设备的可动部分所占据的每一位置称为(C)。
(1-1)A、工步B、工序C、工位D、装夹3.简要说明零件加工所经过的工艺路线的卡片是( A )。
(1-1)A机械加工工艺过程卡 B 机械加工工艺卡 C机械加工工序卡4.制订工艺规程的最基本的原始材料是( B )。
(1-1)A装配图 B零件图 C工序图5.单件生产的基本特点是(B )。
(1-1)A产品品种单一 B每种产品仅生产一个或数个别 C经常重复生产6.大量生产的基本特点是(A)。
(1-1)A产品品种单一 B每种产品仅生产一个或数个别 C很少重复生产7.在不同的生产下类型下,同一产品的工艺过程是(C )。
(1-1)A相同的 B 相似的 C 不同的8.模具零件采用锻件锻造的目的可能是:(A)。
(1-2)A、充分发挥材料的力学性能,提高模具零件的加工工艺性和使用寿命B、合理使用加工设备C、保证模具零件的加工精度9.下列不属于平面加工方法的是(D )。
(1-2)A刨削 B磨削 C铣削 D铰削10.装配时用来确定零件或部件在产品中的相对位置所采用的基准,称为(C )基准。
(1-3)A定位 B测量 C装配 D工艺11.测量零件已加工表面的尺寸和位置所使用的基准为( B )基准。
(1-3)A定位 B测量 C装配 D工艺12.选择精基准的原则中讲到的“基准重合”是指( A )。
(1-3)A、选择设计基准作为精基准B、以粗基准作为精基准C、在多数工序中采用同一组精基准定位13.选择定位基准时,粗基准可以使用(A )。
(1-3)A一次 B两次 C多次14.选择精基准的原则中讲到的“基准统一”是指(A )。
(1-3)A 在多数工序中采用同一组精基准定位B 选择加工表面本身作为精基准C选择设计基准作为精基准15.工件的安装方式有多种,其中直接找正法运用于(A)。
模具制造工艺课程设计_指导书参考
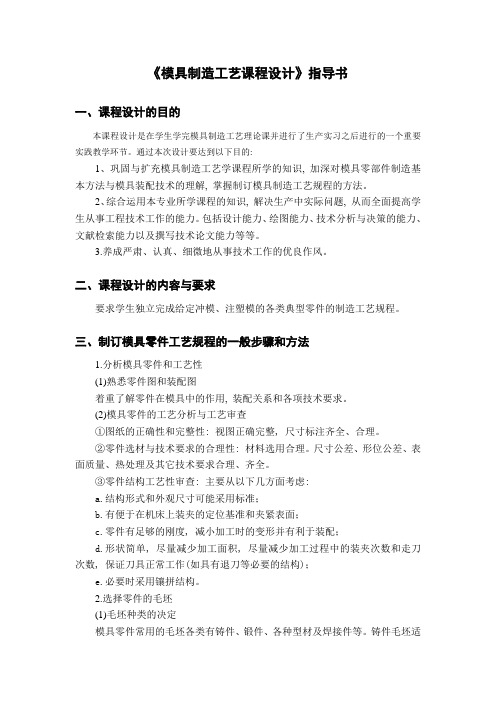
《模具制造工艺课程设计》指导书一、课程设计的目的本课程设计是在学生学完模具制造工艺理论课并进行了生产实习之后进行的一个重要实践教学环节。
通过本次设计要达到以下目的:1、巩固与扩充模具制造工艺学课程所学的知识, 加深对模具零部件制造基本方法与模具装配技术的理解, 掌握制订模具制造工艺规程的方法。
2、综合运用本专业所学课程的知识, 解决生产中实际问题, 从而全面提高学生从事工程技术工作的能力。
包括设计能力、绘图能力、技术分析与决策的能力、文献检索能力以及撰写技术论文能力等等。
3.养成严肃、认真、细微地从事技术工作的优良作风。
二、课程设计的内容与要求要求学生独立完成给定冲模、注塑模的各类典型零件的制造工艺规程。
三、制订模具零件工艺规程的一般步骤和方法1.分析模具零件和工艺性(1)熟悉零件图和装配图着重了解零件在模具中的作用, 装配关系和各项技术要求。
(2)模具零件的工艺分析与工艺审查①图纸的正确性和完整性: 视图正确完整, 尺寸标注齐全、合理。
②零件选材与技术要求的合理性: 材料选用合理。
尺寸公差、形位公差、表面质量、热处理及其它技术要求合理、齐全。
③零件结构工艺性审查: 主要从以下几方面考虑:a.结构形式和外观尺寸可能采用标准;b.有便于在机床上装夹的定位基准和夹紧表面;c.零件有足够的刚度, 减小加工时的变形并有利于装配;d.形状简单, 尽量减少加工面积, 尽量减少加工过程中的装夹次数和走刀次数, 保证刀具正常工作(如具有退刀等必要的结构);e.必要时采用镶拼结构。
2.选择零件的毛坯(1)毛坯种类的决定模具零件常用的毛坯各类有铸件、锻件、各种型材及焊接件等。
铸件毛坯适合于制造形状复杂的零件, 如上、下模座等。
锻造毛坯适合于制造强度、刚度等力学性能要求高但形状不复杂的零件, 如中、小型凸、凹模等。
型材常用于零件形状与某种型材相近之毛坯。
焊接件多用于某些结构件类型的零件的毛坯。
(2)毛坯尺寸的确定毛坯尺寸应根据模具零件尺寸加上适当的加工余量来确定。
《模具制造学》课程设计说明书

3、拟定零件工艺路线
仅列出工序名称的简明工艺过程称为工艺路线。拟定工艺路线是制定工艺规程的关键步骤。它包括选择定位基准、选择加工方法、划分加工阶段、确定工艺顺序及确定工序分散与集中的程度等。同一零件的加工可有不同的工艺路线,应通过分析对比择优确定。
4、确定所有的机床设备和工艺装备(工艺装备指:刀具、量具、二类工具等)
《模具制造学》
课
程
设
计
说
明
书
专业:材料成型及控制工程
姓名:陈艳青
学号:B11033110
指导老师:贾平
前言
根据《模具制造工艺》的介绍,我们可以大概了解一些模具制造的相关内容。在现代工作生产中,模具是生产各种产品的重要工艺装备,它以其特定的形状通过一定的方式使原材料成形。采用模具生产零部件,具有生产效率高、质量好、成本低、节省能源和原材料等一系列优点,在铸造、锻造、冲压、塑料、橡胶、玻璃、粉末冶金、陶瓷制品等生产行业中的得了广泛的应用,成为当代工业生产的重要手段和工艺发展方向。模具工业对民国经济和社会的发展,起着越来越重要的作用。
本课程设计注重对组员的解决问题能力及组长的协调能力培养。组员必须掌握各类加工所适合的材料,如棒材、板材、锻材等。组长必须深入了解模具个零件及装配情况,根据组员的读图能力、制造工艺设计及装配认识等能力进行分组练习。其中,各组员的情况,如基础掌握程度不同、时间空闲程度不同等,必须合理的安排零件加工的各组人员。组员在加工设计时,必须结合相关内容,检查并查阅资料,与组里的成员相互沟通共同解决相关疑问。
模具制造工艺学题库完整

模具制造工艺学题库一、填空题1、我国模具制造总体上还存在着、、、的弊端,很多精密、复杂、大型模具因为国制造困难,不得不从国外进口。
2、模具制造工艺,就是把模具设计转化为的过程。
3、、、是模具制造的主要技术经济指标。
4、切削加工是利用切削刀具从工件(毛坯)上切去多余的材料,使零件符合图样规定的、、等方面要求的加工过程。
5、切削加工可分为和两部分6、在金属切削加工中,切除多余金属材料时,和之间的相对运动称为切削运动。
7、在切削运动中,被加工的工件上有三个依次变化着的表面:、和。
8、切削用量的三要素包括:、、。
9、普通外圆车刀的组成主要包括和。
10、高速钢按用途不同可以分为和。
11、在加工塑性材料时,在切削速度不高而又能形成带状切屑的情况下,常在前刀面处黏附一块剖面呈三角形的硬块,称为“”。
12、根据切削层金属变性特点和变形程度的不同,切屑可分为四类:、、、。
13、是组成工艺过程的基本单元,也是制定生产计划、进行经济核算的基本单元。
是组成工序的基本单元。
14、化分工序的依据是、的是否变动以及。
15、工件的装夹包括和两个过程。
16、机械产品的加工精度包括:、、。
17、模具加工的精度主要体现在的精度和相关部位的精度。
18、车刀按其用途不同,可分为、、等类型。
20、应采用同一组基准定位加工零件上尽可能多的表面,这就是原则。
21、影响切削力的因素主要包括、、等三个方面。
23、磨削力可以分解为三个相互垂直的力、和。
24、磨削加工时,在磨粒切入金属层的过程中,金属层表面会出现三种不同的变形区,分别是、、。
25、机械制造中常用的毛坯种类有、、和。
26、在金属切削变形过程中,塑性金属材料在刀具的作用下,会沿着与作用力呈45°角的方向产生剪切滑移变形。
27、孔加工中保证加工质量的关键问题是、、和问题。
28、按柄部形状分,麻花钻可分为和。
29、端铣时,根据铣刀与工件的相对位置不同,可分为、和。
30、根据铣削的切削层变化规律不同,周铣可以分为和两种方式。
模具制造工艺考试题库()

模具制造⼯艺考试题库()⼀、单项选择题(本⼤题共15⼩题,每⼩题1分,共15分。
)请将答案填写在题⼲后的括号内。
1、下列⼯件最适合成型磨削加⼯的是 C 。
A、凹模;B、型腔;C、凹模镶块;D、紫铜电极。
2、在不同⽣产类型下,同⼀产品的⼯艺过程是 C 。
A、相同的;B、相似的;C、不同的;3、下列关于数控机床坐标系说法正确的是 A 。
A、⼯件坐标系的⽅向和机床坐标系的⽅向⼀致;B、⼯件坐标系和机床坐标系都是操作者设定的;C、机床坐标系的原点就是⼯件编程的原点。
4、要提⾼电⽕花加⼯的⼯件表⾯质量,应考虑: B 。
A、使脉冲宽度增⼤;B、使电流峰值减⼩;C、增⼤放电间隙。
5、铰孔主要⽤于加⼯ C 。
A、⼤尺⼨孔;B、盲孔和深孔;C、中⼩尺⼨未淬硬的孔;D、中⼩尺⼨已淬硬的孔。
6、对有⾊⾦属零件的外园表⾯加⼯,当精度要求为IT6,Ra=0.4µm时,它的终了加⼯⽅法应该采⽤ A 。
A、精车;B、精磨;C、粗磨;D、研磨。
7、下列A C 可超声波切割加⼯。
A、陶瓷B、紫铜C、玻璃D、塑料8、下列A B C D可制作模具电铸成形的原模(母模)。
A、塑料B、⽯膏C、⾦属材料D、环氧树脂9、对塑料模浇⼝套的装配,下列说法正确的有:B C。
A、浇⼝套与定模板采⽤间隙配合B、浇⼝套的压⼊端不允许有导⼊斜度C、常将浇⼝套的压⼊端加⼯成⼩圆⾓D、在浇⼝套的导⼊斜度加⼯时不需留有修磨余量10、分散装配的特点是:AA、适合成批⽣产B、⽣产效率低C、装配周期长D、装配⼯⼈少11、⼯序集中到极限时,把零件加⼯到图样规定的要求的⼯序应该是A 。
A、⼀个;B、⼆个;C、多个。
12、在机械加⼯⼯艺规程中的安装是指 D 。
A、⼑具在机床上的装夹过程;B、⼯件更换机床时所发⽣的装卸⼯作;C、⼯件在机床上装卸所完成的⼯艺过程;D、⼯件在机床上的定位和夹紧过程。
13、零件机械加⼯顺序的安排,⼀般应遵循 A 的原则。
A、先加⼯基准表⾯,后加⼯其它表⾯;B、先加⼯次要表⾯,后加⼯主要表⾯;C、先加⼯孔和型腔,后加⼯平⾯。
《模具制造工艺学》试卷及答案
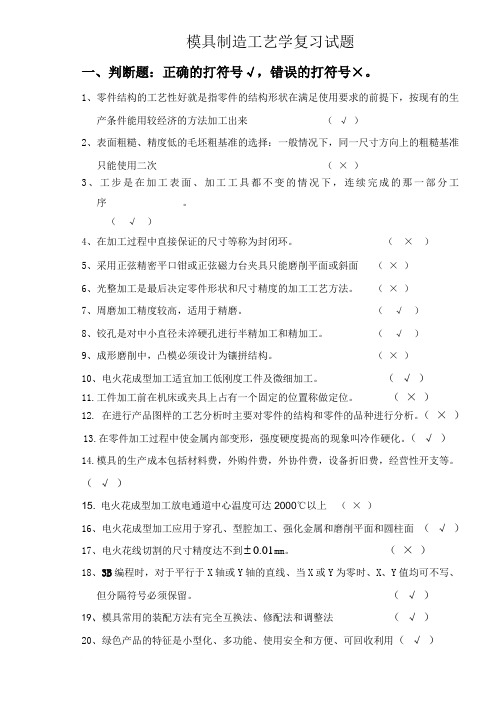
模具制造工艺学复习试题一、判断题:正确的打符号√,错误的打符号×。
1、零件结构的工艺性好就是指零件的结构形状在满足使用要求的前提下,按现有的生产条件能用较经济的方法加工出来 ( √ )2、表面粗糙、精度低的毛坯粗基准的选择:一般情况下,同一尺寸方向上的粗糙基准只能使用二次 ( × )3、工步是在加工表面、加工工具都不变的情况下,连续完成的那一部分工序。
( √ )4、在加工过程中直接保证的尺寸等称为封闭环。
( × )5、采用正弦精密平口钳或正弦磁力台夹具只能磨削平面或斜面 ( × )6、光整加工是最后决定零件形状和尺寸精度的加工工艺方法。
( × )7、周磨加工精度较高,适用于精磨。
( √ )8、铰孔是对中小直径未淬硬孔进行半精加工和精加工。
( √ )9、成形磨削中,凸模必须设计为镶拼结构。
( × )10、电火花成型加工适宜加工低刚度工件及微细加工。
( √ ) 11.工件加工前在机床或夹具上占有一个固定的位置称做定位。
( × )12. 在进行产品图样的工艺分析时主要对零件的结构和零件的品种进行分析。
( × )13.在零件加工过程中使金属内部变形,强度硬度提高的现象叫冷作硬化。
( √ )14.模具的生产成本包括材料费,外购件费,外协件费,设备折旧费,经营性开支等。
( √ )15. 电火花成型加工放电通道中心温度可达2000℃以上 ( × )16、电火花成型加工应用于穿孔、型腔加工、强化金属和磨削平面和圆柱面 ( √ )17、电火花线切割的尺寸精度达不到01.0 mm 。
( × ) 18、3B 编程时,对于平行于X 轴或Y 轴的直线、当X 或Y 为零时、X 、Y 值均可不写、但分隔符号必须保留。
( √ )19、模具常用的装配方法有完全互换法、修配法和调整法 ( √ )20、绿色产品的特征是小型化、多功能、使用安全和方便、可回收利用( √ )二、选择题:1、在不同的生产类型下,同一产品的工艺过程是( C )A、相同的;B、相似的;C、不同的。
模具制造工艺 第2版 项目一 模具制造工艺基础

项目一 模具制造工艺基础
模具机械加工工序卡
项目一 模具制造工艺基础
3、制定模具图纸 审查零件图与装配图 * 审查设计图纸的完整性和正确性 * 审查零件的技术要求 * 审查零件的选材是否恰当 * 审查零件的结构工艺性 2、毛坯的选择 3、拟定工艺路线 4、确定工序具体内容 5、填写工艺文件
项目一 模具制造工艺基础
一、模具加工工艺规程概述
1、工艺过程及其组成 将原材料转变为模具成品的全过程称为模具生产 过程。主要包括: 模具方案策划、结构设计 生产技术准备 模具成型件加工 装配与试模 验收与试用
模具生产过程中直接改变生产对象的形状、尺寸、相对 位置和性质等,使其成为半成品或成品的过程,称为工艺 过程。
项目一 模具制造工艺基础
四、选择加工方法时需要考虑的因素 在选择从粗到精的加工方法及过程时,要综合考
虑多方面的因素,重点考虑以下问题:
(1)被加工零件的结构形状和表面的精度 一般所采用加工方法的经济精度,应保证零件
所要求的加工精度和表面质量。 加工经济精度:是指在正常加工条件下(采用
符合质量标准的设备、工艺装备和标准技术等级的工 人,不延长加工时间)所能保证的加工精度。
加工方法及工序顺序凹模镶套零件的主
要尺寸标注都是以零件的轴心线为基准
的,这使得零件加工时容易与设计基准
进行统一
项目一 模具制造工艺基础
六.安排加工顺序
* 先粗后精 * 基准先行 * 先主后次 * 先面后孔 适当安排热处理(预备热处理和最终热处理) 检验、去毛刺、倒棱、清洗、防锈等辅助工序要 按需设置,不能遗漏。 在确定工序数目时,恰当地决定工序集中与工序 分散问题。
二、模具加工工艺规程及作用:
模具制造工艺学习题集答案(谭海林)

第1章模具制造工艺规程的基础知识一、填空题1.生产类型是指企业(或车间、工段、班组、工作地)生产专业化的分类,包括单件生产、批量生产、大量生产三种类型。
(1-1)2.工艺规程是指规定产品和零件制造工艺过程和操作方法的工艺文件。
(1-1)3.在制订零件的机械加工工艺规程时,必须保证质量、生产率、经济性三个方面的基本要求。
(1-1)4.制订工艺规程的最基本原始资料是零件图。
(1-1)5.工艺过程是指改变生产对象的形状,尺寸、相对位置和性质等,使之成为成品、半成品的生产过程(1-1)6.工序是指一个或一组工人,在一个固定的工作地点(如机床或钳工台等),对同一个或同时对几个工件进行加工所连续完成的那部分工艺过程。
(1-1)7.划分工序的依据是工作地(设备)、加工对象是否变动、加工是否连续完成。
(1-1)8.工序是机械加工工艺过程的基本组成部分。
(1-1)9.安装是工件在机床上正确地定位和夹紧。
(1-1)10.工位是指工件在一次装夹后,工件与夹具或设备的可动部分一起,相对刀具或设备的固定部分所占据的每一个位置。
(1-1)11.铰孔适用于中小尺寸的孔的精加工,而镗孔适用大尺寸的孔的加工。
(1-2)12.铰孔、拉孔适用于直径较小的孔的精加工,淬硬的孔只能用磨削进行加工。
13.模具制造中,通常按照零件结构和工艺过程的相似性,将各种零件大致分为轴类零件、套类零件、盘环类零件、板类零件以及腔类零件等。
(1-2)14.模具零件常用的毛坯主要有锻件、铸件、半成品件、焊接件、各种型材及板料等(1-2)15.铸件毛坯适用于形状复杂的零件,锻件毛坯适用于强度要求较高,而形状比较简单的零件。
(1-2)16.对阶梯式圆凸模,如果各台阶直径相差不大,可直接采用棒料作毛坯,使毛坯准备工作简化(1-2)17.大型凸缘式模柄零件,宜采用锻件作毛坯,以节省材料和减少机械加工的工作量。
(1-2)18.在加工时,为了保证工件相对于机床和刀具之间的正确位置(即将工件定位)所使用的基准称为定位基准。
模具设计与制造试题一及答案
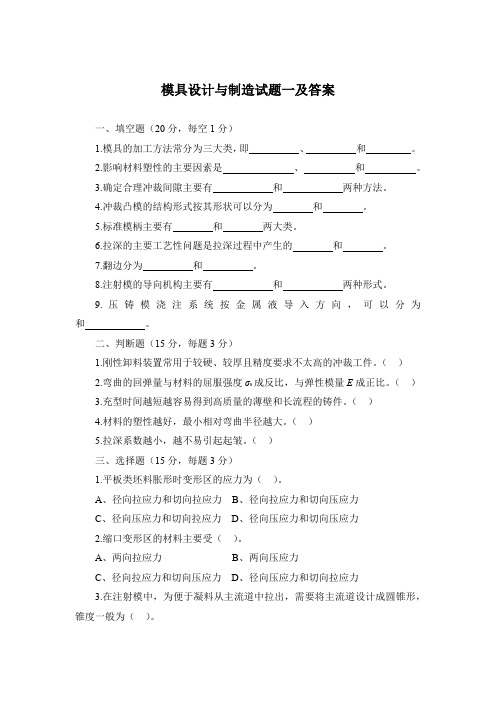
模具设计与制造试题一及答案一、填空题(20分,每空1分)1.模具的加工方法常分为三大类,即、和。
2.影响材料塑性的主要因素是、和。
3.确定合理冲裁间隙主要有和两种方法。
4.冲裁凸模的结构形式按其形状可以分为和。
5.标准模柄主要有和两大类。
6.拉深的主要工艺性问题是拉深过程中产生的和。
7.翻边分为和。
8.注射模的导向机构主要有和两种形式。
9.压铸模浇注系统按金属液导入方向,可以分为和。
二、判断题(15分,每题3分)1.刚性卸料装置常用于较硬、较厚且精度要求不太高的冲裁工件。
()2.弯曲的回弹量与材料的屈服强度σs成反比,与弹性模量E成正比。
()3.充型时间越短越容易得到高质量的薄壁和长流程的铸件。
()4.材料的塑性越好,最小相对弯曲半径越大。
()5.拉深系数越小,越不易引起起皱。
()三、选择题(15分,每题3分)1.平板类坯料胀形时变形区的应力为()。
A、径向拉应力和切向拉应力B、径向拉应力和切向压应力C、径向压应力和切向拉应力D、径向压应力和切向压应力2.缩口变形区的材料主要受()。
A、两向拉应力B、两向压应力C、径向拉应力和切向压应力D、径向压应力和切向拉应力3.在注射模中,为便于凝料从主流道中拉出,需要将主流道设计成圆锥形,锥度一般为()。
A、2°~6°B、6°~10°C、10°~16°D、16°~20°4.在注射成形的每个周期中,将塑件及浇注系统凝料从模具中脱出的机构称为()。
A、导向机构B、顶件机构C、抽芯机构D、推出机构5.压铸过程中,金属熔体从冲头向前快速运动,高速通过内浇口直至充满型腔,此时熔体流动速度称为()。
A、冲头速度B、充型速度C、冲头空压射速度D、熔体速度四、简答题(50分)1.模具设计的基本条件是什么?模具设计的关键技术是什么?(5分)2.模具制造过程一般包括哪几个阶段?(5分)3.什么是排样?排样的分类是什么?(5分)4.影响最小相对弯曲半径的因素主要有哪些?(5分)5.在注射模具中,选用热塑性塑料时,主要考虑哪些工艺特性?(5分)6.注射模浇注系统的设计原则是什么?(5分)7.冲裁过程分为哪三个阶段,每个阶段各有什么特征?(10分)8.压铸模中分型面的选择要点有哪些?(10分)试题一答案一、填空题(20分,每空1分)1.铸造加工、切削加工、特种加工2.材料的化学成分、金相组织、力学性能3.理论确定法、经验确定法4.直通式、台阶式5.刚性、浮动6.起皱、拉裂7.内缘翻边、外缘翻边8.导柱导向、锥面定位9.切向浇口、径向浇口二、判断题(15分,每题3分)1.√2.×3.√4.×5.×三、选择题(15分,每题3分)1.A2. B3.A4.D5.B四、简答题(50分)1.模具设计的基本条件是什么?模具设计的关键技术是什么?(5分)答:模具设计有两个基本条件,即工件的材料、性能、规格和成型设备的种类、性能、规格。
模具制造工艺

一:填空题生产过程是将原材料或半成品转化为成品的各有关劳动过程的总和。
工艺过程生产过程中与原材料变为成品直接有关的过程,如毛坏制造、机械加工、热处理和装配等过程。
工序是一个工人(或一组工人)在一个固定的工作地点(如机床或钳工台),对一个(或同进几个)工件所连续完成的哪部分工艺过程。
工步是当加工表面、切削工具和切削用量中的转速与进给量均不变时,所完成的哪部分工序。
工位是工件在机床上占据的每一个加工位置都称为一个工位。
生产纲领是工厂制造产品(或零件)的年产量。
工艺规程是描述产品由毛坯加工成为零件的过程的一种工艺文件。
制定工艺规程的原则是在一定的生产条件下,要使所编制的工艺规程能以最少的劳动量和最低的费用,可靠地加工出符合图样及技术要求的零件。
切削用量是切削时各参数的合称、包括切削速度、进给量、切削深度三要素。
设计基准是在零件图上用以确定其它点、线、面的基准。
工艺基准是指在工艺过程中零件在加工或装配中所采用的基准。
又可分为定位工序基准、定位测量基准和装配测量基准。
定位基准是加工时使工件在机床或夹具中占据正确位置所用的基准。
测量基准是零件检验时,用以测量已加工表面尺寸及位置的基准。
装配基准是装配时用以确定零件在部件或产品中位置的基准。
工件在加工时,安装方法可归纳为直接找正法、单件小批量精度要求很高划线找正法、采用夹具安装法单件小批量生产中的铸件粗加工。
加工阶段通常可划分为粗加工阶段、半精加工半精加工阶段、精加工精加工阶段和光整加工光整加工阶段。
划分加工阶段的好处是:1) 有利于保证零件的加工质量加工精度;2) 有利于毛坯的缺陷合理使用设备;3)便于安排热处理工序加工设备插入热;4)有利于发现毛坯缺陷。
机械加工的精基准选择中,以加工表面设计基准作为定位基准的原则称之为基准重合基准重合原则;使较多的加工表面采用同一个表面为基准的原则称之为基准统一基准统一原则。
工序集中是使每个工序中包括尺可能多的工小内容,工序分散是将工艺路线中的工步内容分散在更多的工序中完成。
模具制造工艺
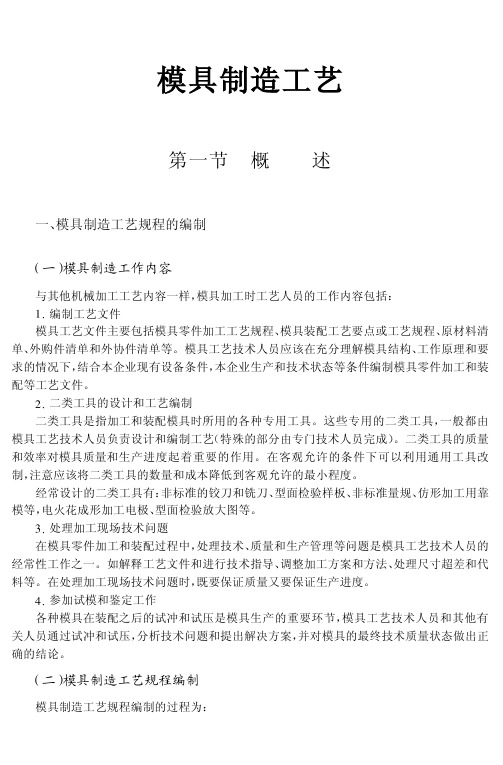
模具制造工艺第一节概述一、模具制造工艺规程的编制(一)模具制造工作内容与其他机械加工工艺内容一样,模具加工时工艺人员的工作内容包括:!"编制工艺文件模具工艺文件主要包括模具零件加工工艺规程、模具装配工艺要点或工艺规程、原材料清单、外购件清单和外协件清单等。
模具工艺技术人员应该在充分理解模具结构、工作原理和要求的情况下,结合本企业现有设备条件,本企业生产和技术状态等条件编制模具零件加工和装配等工艺文件。
#"二类工具的设计和工艺编制二类工具是指加工和装配模具时所用的各种专用工具。
这些专用的二类工具,一般都由模具工艺技术人员负责设计和编制工艺(特殊的部分由专门技术人员完成)。
二类工具的质量和效率对模具质量和生产进度起着重要的作用。
在客观允许的条件下可以利用通用工具改制,注意应该将二类工具的数量和成本降低到客观允许的最小程度。
经常设计的二类工具有:非标准的铰刀和铣刀、型面检验样板、非标准量规、仿形加工用靠模等,电火花成形加工电极、型面检验放大图等。
$"处理加工现场技术问题在模具零件加工和装配过程中,处理技术、质量和生产管理等问题是模具工艺技术人员的经常性工作之一。
如解释工艺文件和进行技术指导、调整加工方案和方法、处理尺寸超差和代料等。
在处理加工现场技术问题时,既要保证质量又要保证生产进度。
%"参加试模和鉴定工作各种模具在装配之后的试冲和试压是模具生产的重要环节,模具工艺技术人员和其他有关人员通过试冲和试压,分析技术问题和提出解决方案,并对模具的最终技术质量状态做出正确的结论。
(二)模具制造工艺规程编制模具制造工艺规程编制的过程为:!"模具工艺性分析在充分理解模具结构、用途、工作原理和技术要求的基础上,分析模具材料、零件形状、尺寸和精度要求等工艺性是否合理,找出加工的技术难点,提出合理加工方案和技术保证措施。
#"确定毛坯形式根据零件的材料类别、零件的作用和要求等确定哪些零件属于自制件、外购件和外协件,分别填写外购件清单和外协件清单。
模具制定工艺规程的具体步骤
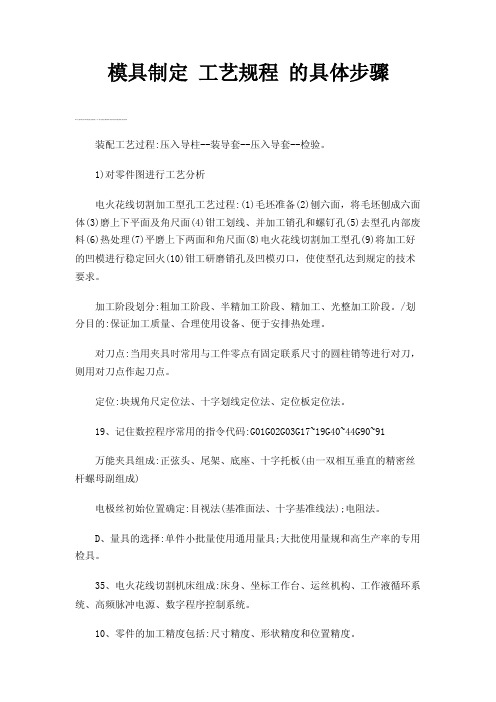
模具制定工艺规程的具体步骤装配工艺过程:压入导柱--装导套--压入导套--检验。
1)对零件图进行工艺分析电火花线切割加工型孔工艺过程:(1)毛坯准备(2)刨六面,将毛坯刨成六面体(3)磨上下平面及角尺面(4)钳工划线、并加工销孔和螺钉孔(5)去型孔内部废料(6)热处理(7)平磨上下两面和角尺面(8)电火花线切割加工型孔(9)将加工好的凹模进行稳定回火(10)钳工研磨销孔及凹模刃口,使使型孔达到规定的技术要求。
加工阶段划分:粗加工阶段、半精加工阶段、精加工、光整加工阶段。
/划分目的:保证加工质量、合理使用设备、便于安排热处理。
对刀点:当用夹具时常用与工件零点有固定联系尺寸的圆柱销等进行对刀,则用对刀点作起刀点。
定位:块规角尺定位法、十字划线定位法、定位板定位法。
19、记住数控程序常用的指令代码:G01G02G03G17~19G40~44G90~91万能夹具组成:正弦头、尾架、底座、十字托板(由一双相互垂直的精密丝杆螺母副组成)电极丝初始位置确定:目视法(基准面法、十字基准线法);电阻法。
D、量具的选择:单件小批量使用通用量具;大批使用量规和高生产率的专用检具。
35、电火花线切割机床组成:床身、坐标工作台、运丝机构、工作液循环系统、高频脉冲电源、数字程序控制系统。
10、零件的加工精度包括:尺寸精度、形状精度和位置精度。
1)对产品装配图和零件图的分析与工艺审查正弦精密平口钳:可用于加工平面、斜面、刚性较大的材料。
加工顺序的安排:先粗后精,先主后次,基准先行,先面后孔。
)3)工序卡片:工序加工过程所必须的工艺资料。
7)数值计算工艺方法:a、单电极平动加工法(先高效低损耗电规准进行粗加工--依次改变电规准,加大平动量--最后使用的电极加工规准小,损耗量小)。
正弦分中夹具主要组成部分:正弦头、尾架、底座。
B、夹具的选择:单件小批量生产应尽量选用通用夹具;大批量使用专用夹具。
34、线切割与成形加工相比的特点:a、不需要制专用电极,电极丝可反复使用,成本低。
模具制造工艺课程设计

模具制造工艺课程设计内容:1、编制图示零件的加工工艺规程要求:(1)进行工艺性分析(2)制订工艺规程2、任选一模具装模图(附图)制订其装配工艺规程(必做)姓名班级学号日期目录一、导柱的加工工艺规程————————————1二、导套的加工工艺规程————————————3三、上模座的加工工艺规程———————————6四、下模座的加工工艺规程———————————8五、凹模的加工工艺规程————————————10六、凹模的加工工艺规程————————————12七、典型凹模的加工工艺规程——————————14八、凹凸模的加工工艺规程———————————16九、凹模的加工工艺规程————————————18十、模具装配图————————————————20一、导柱的加工工艺规程导柱(20钢渗碳58-62HRC)1.导柱的作用导柱是磨具上的导向零件。
与导套配合,起导向和定位作用。
导柱安装在下模座上,导柱与导套滑动配合以保证凸模与凹模工作时有正确的位置,为了保证良好的导向作用,导柱与导套的配合间隙小于凹凸模之间的间隙,导柱与导套的配合间隙一般采用H7/h6,精度要求高时采用H6/h5,导柱与下模座采用H7/r6过盈配合。
为了保证导向精度。
加工时除了使导柱导套精度符合要求外,还应满足配合表面间的同轴度。
即两个外圆表面间的同轴度,以及导套外圆与内孔表面的同轴度。
2.导柱的工艺性分析1)几何形状有同轴不同直径的外圆、倒角、退刀槽组成。
2)技术要求分析⑴导柱配合表面的尺寸和形状精度⑵导柱配合表面间的同轴度⑶导柱配合表面有较高的硬度:HRC50-553)加工表面分析φ32r6:Ra0.4——精磨才能达到要求φ32h6:Ra0.1——圆柱度0.006—研磨才能达到要求φ32h6:精车—半精车—粗磨—精磨—研磨φ32r6:精车—半精车—粗磨—精磨4)毛坯的种类选择构成导柱的基本表面都是回转体表面,材料20钢,可以直接选择适当尺寸的热轧圆钢作为毛坯。
模具主要零件加工工艺规程

模具主要零件加工工艺规程1. 引言模具是工业生产中常用的一种设备,用于制造大批量产品。
模具的主要零件加工工艺规程涉及到模具制造中的关键过程,对于实现模具的高质量和高效率生产至关重要。
2. 模具主要零件加工工艺规程概述模具的主要零件加工工艺规程包括了材料准备、加工工艺流程、加工设备选择、加工工艺参数以及质量控制等内容。
3. 材料准备选择合适的材料对于模具的加工工艺至关重要。
常用的模具材料有钢、铝等。
在材料准备阶段,需要对材料进行质量检查和切割。
3.1 质量检查对于所采购的模具材料,需要进行质量检查,包括外观检查、材料成分分析、硬度测试等。
只有合格的材料才能被用于模具制造。
3.2 切割将材料按照设计要求进行切割,可以采用激光切割、火焰切割等方法。
切割过程中需要注意保持切割精度和避免产生切割热变形。
4. 加工工艺流程加工工艺流程决定了模具的形状和尺寸,对于模具的功能和性能有着重要影响。
加工工艺流程一般包括下面几个步骤:4.1 铣削将切割好的模具材料通过铣削工艺进行加工,以获取所需的形状和尺寸。
铣削工艺可以逐步进行,从粗加工到精加工。
通过钻孔工艺制作模具中的孔洞和螺纹等结构。
钻孔可以使用钻头和铰孔等工具进行。
4.3 攻丝在模具中加入螺纹结构需要进行攻丝。
攻丝可以使用手工攻丝或者机械攻丝。
4.4 磨削通过磨削工艺对模具进行表面处理和修整,以提高模具的光洁度和尺寸精度。
磨削可以采用手工磨削或者机械磨削。
4.5 焊接在模具的加工中,需要进行零件的组合和连接,常用的方法是采用焊接。
焊接工艺需要根据模具材料的特性选择适当的焊接材料和焊接方法。
将加工好的模具零件进行组装,形成完整的模具。
组装过程需要严格按照设计要求进行,确保模具的稳定性和可靠性。
5. 加工设备选择加工设备的选择对于模具的加工质量和效率起着重要作用。
常用的加工设备有铣床、车床、钻床、磨床等。
6. 加工工艺参数在模具加工过程中,需要设定合适的加工工艺参数,包括切削速度、进给速度、刀具选用等。
- 1、下载文档前请自行甄别文档内容的完整性,平台不提供额外的编辑、内容补充、找答案等附加服务。
- 2、"仅部分预览"的文档,不可在线预览部分如存在完整性等问题,可反馈申请退款(可完整预览的文档不适用该条件!)。
- 3、如文档侵犯您的权益,请联系客服反馈,我们会尽快为您处理(人工客服工作时间:9:00-18:30)。
复习上次课容
1.毛坯的形式有哪几种?哪些模具零件需要采用锻造件毛坯?
2.何谓设计基准?何谓工艺基准?
1.1.7零件工艺路线的分析和拟定
拟定工艺路线就是制定工艺过程的总体布局,选择各加工表面的加工方法和加工方案,确定加工顺序和整个加工工序数目的过程。
除合理选择定位基准外,主要有以下四方面容:
1、表面加工方法的选择
⑴确保加工表面的加工精度和表面粗糙度要求。
⑵考虑工件材料的性质对加工方法的影响。
⑶考虑生产效率和经济性的要求。
⑷考虑现有设备情况和工人的技能水平。
2、加工阶段的划分
模具的加工一般分为四个阶段:⑴粗加工阶段⑵半精加工阶段⑶精加工阶段⑷光整加工阶段★工艺过程划分阶段的主要原因:⑴保证加工质量。
⑵合理使用设备。
⑶便于安排热处理工序。
⑷及早发现毛坯部缺陷,避免损失。
检验、去毛刺、清洗和防锈等。
检验时主要辅助工序。
检验工序的安排:
①粗加工后精加工前一次。
②一个车间转向另一个车间之前。
③冲压工序加工的前后。
④特种性能的检验(探伤、密封性检测)之前。
⑤零件加工完毕,进入装配或成品库之前。
1.1.8加工余量与工序尺寸的确定㈠、加工余量的概念
1、加工总余量与工序余量
毛坯尺寸与零件设计尺寸之差称为加工总余量。
每一工序切除的金属层厚度称为工序余量。
相互关系:
Z0=Z1+Z2+ +Zn=∑Zi
i=1n
n-机械加工的工序数目
◆工序余量又定义为相邻两工序基本尺寸之差。
一般可分为:单边余量、双边余量。
★非对称结构的加工表面常用单边余量:
Zi=li-1-li
其中:Zi-本道工序的工序余量;
li-本道工序的基本尺寸;
li-1-上道工序的基本尺寸。
★具有对称结构的加工表面常用双边余量:
2Zi=li-1-li
★轴对称旋转体表面常用双边余量:
外圆表面:
圆表面:2Zi=di-1-di2Zi=Di-Di-1
★工序尺寸有公差,加工余量也就有公差,所以,加工余量就有标称余量Zb、最大余量Zmax、最小余量Zmin的概念。
加工余量的公差等于上下两道工序尺寸公差之和。
关系式:Tz= Zmax-Zmin=Tb-Ta
一般情况下,工序尺寸的公差按“入体原则”标注,毛坯尺寸
公差按双向对称偏差形式标注。
2、影响工序余量的因素
⑴毛坯的制造状态影响第一道工序的加工余量;⑵上道工序的尺寸公差Ta影响本道工序的加工余量;⑶上道工序的表面粗糙度和缺陷层的影响;⑷上道工序留下的需要单独考虑的空间误差(ea);⑸本工序的安装误差(εb)
安装误差包括定位误差和夹紧误差。
㈡加工余量的确定
确定方法:计算法、查表法、经验法。
模具生产中常用查表法和经验法。
㈢工序尺寸与公差的确定
在大多数加工中,采用基准重合原则(步骤):
1、确定各加工工序的加工余量;
2、从终加工工序开始(设计尺寸)到第二道工序,依次加
上每道工序的加工余量,求出各工序的基本尺寸(包括毛坯尺寸);
3、确定各工序尺寸的公差(按各加工方法的经济精度);
4、按“入体原则”标注各工序尺寸和公差。
(如例P20)
1.1.9工艺装备的选择
1、设备(机床)选择的注意点:
①零件尺寸与机床规格相适应;
②设备精度与工序要求的加工精度相适应;③设备的生产率与加工零件的生产类型相适应;④根据现场生产情况,合理安排设备负荷。
2、夹具的选择
单件小批量-通用夹具;大批量-专用夹具;夹具精度应与加工精度相适应。
3、刀具的选择
一般采用标准刀具;特殊加工采用复合刀具或专用刀具;刀具的类型、规格、精度与加工要求相适应。
4、量具的选择
单件小批量用通用量具,大批量用专用量具,量具的度必须与加工精度相适应。
小结:
拟定零件加工的工艺路线方案是编制工艺规程的重要步骤,主要从加工方法、加工的阶段和工序的集中还是分散几个方面综合考虑,确定了加工路线,再考虑加工的工序安排,安排工序是必须进行加工余量的分配,确定各工序的尺寸和公差最后根据各工序选择合适的加工机床和工量具。