高羟基含量羟基硅油的合成
高羟基含量羟基硅油的合成
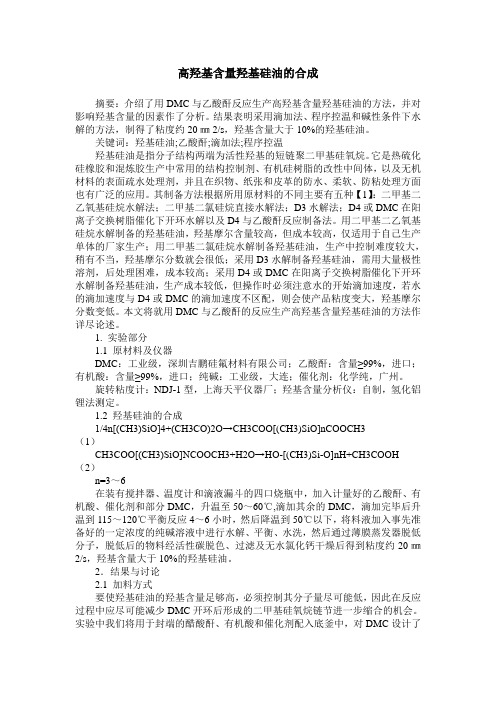
高羟基含量羟基硅油的合成摘要:介绍了用DMC与乙酸酐反应生产高羟基含量羟基硅油的方法,并对影响羟基含量的因素作了分析。
结果表明采用滴加法、程序控温和碱性条件下水解的方法,制得了粘度约20㎜2/s,羟基含量大于10%的羟基硅油。
关键词:羟基硅油;乙酸酐;滴加法;程序控温羟基硅油是指分子结构两端为活性羟基的短链聚二甲基硅氧烷。
它是热硫化硅橡胶和混炼胶生产中常用的结构控制剂、有机硅树脂的改性中间体,以及无机材料的表面疏水处理剂,并且在织物、纸张和皮革的防水、柔软、防粘处理方面也有广泛的应用。
其制备方法根据所用原材料的不同主要有五种【1】:二甲基二乙氧基硅烷水解法;二甲基二氯硅烷直接水解法;D3水解法;D4或DMC在阳离子交换树脂催化下开环水解以及D4与乙酸酐反应制备法。
用二甲基二乙氧基硅烷水解制备的羟基硅油,羟基摩尔含量较高,但成本较高,仅适用于自己生产单体的厂家生产;用二甲基二氯硅烷水解制备羟基硅油,生产中控制难度较大,稍有不当,羟基摩尔分数就会很低;采用D3水解制备羟基硅油,需用大量极性溶剂,后处理困难,成本较高;采用D4或DMC在阳离子交换树脂催化下开环水解制备羟基硅油,生产成本较低,但操作时必须注意水的开始滴加速度,若水的滴加速度与D4或DMC的滴加速度不区配,则会使产品粘度变大,羟基摩尔分数变低。
本文将就用DMC与乙酸酐的反应生产高羟基含量羟基硅油的方法作详尽论述。
1. 实验部分1.1 原材料及仪器DMC:工业级,深圳吉鹏硅氟材料有限公司;乙酸酐:含量≥99%,进口;有机酸:含量≥99%,进口;纯碱:工业级,大连;催化剂:化学纯,广州。
旋转粘度计:NDJ-1型,上海天平仪器厂;羟基含量分析仪:自制,氢化铝锂法测定。
1.2 羟基硅油的合成1/4n[(CH3)SiO]4+(CH3CO)2O→C H3COO[(CH3)SiO]nCOOCH3(1)CH3COO[(CH3)SiO]NCOOCH3+H2O→HO-[(CH3)Si-O]nH+CH3COOH (2)n=3~6在装有搅拌器、温度计和滴液漏斗的四口烧瓶中,加入计量好的乙酸酐、有机酸、催化剂和部分DMC,升温至50~60℃,滴加其余的DMC,滴加完毕后升温到115~120℃平衡反应4~6小时,然后降温到50℃以下,将料液加入事先准备好的一定浓度的纯碱溶液中进行水解、平衡、水洗,然后通过薄膜蒸发器脱低分子,脱低后的物料经活性碳脱色、过滤及无水氯化钙干燥后得到粘度约20㎜2/s,羟基含量大于10%的羟基硅油。
一种小分子羟基硅油的制备方法[发明专利]
![一种小分子羟基硅油的制备方法[发明专利]](https://img.taocdn.com/s3/m/20693cf45ebfc77da26925c52cc58bd6318693ea.png)
[19]中华人民共和国国家知识产权局[12]发明专利申请公布说明书[11]公开号CN 101367940A [43]公开日2009年2月18日[21]申请号200810156229.9[22]申请日2008.09.25[21]申请号200810156229.9[71]申请人江苏宏达新材料股份有限公司地址212200江苏省扬中市明珠广场[72]发明人朱恩俊 朱德洪 王琴芳 祝纪才 [74]专利代理机构南京苏科专利代理有限责任公司代理人孙立冰[51]Int.CI.C08G 77/16 (2006.01)C08G 77/06 (2006.01)C07F 7/18 (2006.01)权利要求书 1 页 说明书 3 页[54]发明名称一种小分子羟基硅油的制备方法[57]摘要本发明涉及有机硅合成领域,具体涉及一种小分子羟基硅油的制备方法。
其特征是:以氨水和二甲基二氯硅烷为原料制备而得。
本发明反应温和,室温反应便可。
200810156229.9权 利 要 求 书第1/1页1.一种小分子羟基硅油的制备方法,其特征是:将二甲基二氯硅烷与氨水反应得到。
2.权利要求1的制备方法,其中氨水与二甲基二氯硅烷的重量比为1:1.2~2.0。
3.权利要求2的制备方法,其中氨水与二甲基二氯硅烷的重量比为1:1.5~1.8。
4.权利要求1的制备方法,其中反应温度为0~30℃。
5.权利要求4的制备方法,其中反应温度为10~20℃。
6.权利要求1的制备方法,其中反应p H值为大于7。
7.权利要求6的制备方法,其中反应p H值为8~10。
8.权利要求1的制备方法,其中还包括将所得反应液沉降、洗涤、过滤和干燥。
200810156229.9说 明 书第1/3页一种小分子羟基硅油的制备方法技术领域本发明涉及有机硅合成领域,具体涉及一种一种小分子羟基硅油的制备方法。
背景技术α,ω--双--二甲基羟基硅氧基聚二甲基硅氧烷,简称羟基硅油,它以重复的硅氧键结构为主链,甲基为侧基的羟基封端的线型结构的聚合物,可表示为:小分子羟基硅油是指硅氧键主链比较短(n小于等于10),其粘度一般小于20厘泊。
羟基硅油粘度和羟基含量

羟基硅油是一种有机硅化合物,通常是聚二甲基硅氧烷与羟基取代基(OH)相连而形成的。
其粘度和羟基含量会影响其性质和用途。
羟基硅油粘度:羟基硅油的粘度取决于分子链的长度和化学结构。
粘度较低的羟基硅油在涂抹或涂覆时更容易流动,而粘度较高的羟基硅油可能更适合于在皮肤上形成保护膜。
常用的羟基硅油粘度范围从较薄的流体到较浓稠的凝胶。
羟基含量:羟基含量指的是羟基硅油分子中含有的羟基数量,这对于其在化妆品、护肤品和医疗领域中的应用具有重要意义。
高羟基含量的羟基硅油可能具有更好的保湿性能和润滑性能,对皮肤的滋润效果更显著。
羟基硅油中的羟基基团还可以与水分子相互作用,从而帮助维持肌肤的水分平衡。
粘度和羟基含量通常会影响羟基硅油在化妆品、护肤品和其他产品中的使用效果。
选择适合的羟基硅油取决于所需的特定性质和应用。
不同品牌和制造商可能会提供不同粘度和羟基含量的羟基硅油产品,以满足不同需求。
羟基硅油生产工艺

羟基硅油生产工艺
羟基硅油(Hydroxypropylsilicone oil)是一种常用的特殊有机
硅功能修饰剂,广泛应用于化妆品、医疗领域及工业润滑剂等方面。
下面介绍一种羟基硅油的生产工艺。
首先,制备羟基丙基二氯硅烷。
将丙烯腈和甲醇加入反应釜中,在加热搅拌下进行缩合反应,得到羟基丙腈。
然后,将得到的羟基丙腈与氯化亚砜反应,生成羟基丙基亚砜。
最后,将羟基丙基亚砜与氯化硅烷反应,得到羟基丙基二氯硅烷。
其次,反应合成羟基硅油。
将制得的羟基丙基二氯硅烷与羟基聚二甲基硅氧烷(PDMS)进行缩合反应。
首先,在反应釜中
加入适量的反应溶剂,如二甲苯,然后加入羟基丙基二氯硅烷和催化剂,通入惰性气体,保持反应釜内的惰性气氛。
加热反应,控制反应温度和时间,使羟基丙基二氯硅烷缩合到PDMS 链上,形成羟基硅油。
反应结束后,冷却反应液,过滤得到羟基硅油。
最后,对羟基硅油进行后处理。
将合成得到的羟基硅油进行脱色和洗涤处理。
首先,对羟基硅油进行脱色处理,可以通过活性炭吸附或活性白土吸附等方法进行。
其次,使用溶剂进行洗涤处理,去除其中的杂质。
然后,对羟基硅油进行干燥处理,去除残留的溶剂。
以上就是羟基硅油的一种生产工艺。
在实际生产过程中,需要控制好反应的温度、时间和加料速度等参数,以确保反应得到
高质量的羟基硅油。
此外,还要进行必要的质量监控和检测,以确保产品符合相关的质量标准和要求。
羟基硅油生产工艺

羟基硅油生产工艺以羟基硅油生产工艺为标题,我们来探讨一下羟基硅油的生产过程。
羟基硅油,也被称为硅酮润滑油,是一种具有优异性能的特种润滑油,广泛应用于化工、医药、电子、汽车等领域。
羟基硅油的生产主要通过羟基硅烷的聚合反应来实现。
羟基硅烷是一种含有硅氧键和羟基的有机硅化合物,其化学式为RnSi(OR')4-n,其中R为有机基团,R'为烷基或芳香基团。
在生产过程中,首先将羟基硅烷与溶剂进行混合,并加入催化剂,进行聚合反应。
催化剂通常采用碱性催化剂,如氢氧化钠等。
在聚合反应过程中,羟基硅烷的硅氧键会发生开裂,形成具有不同长度的硅氧链。
这些链可以通过进一步反应进行交联,形成羟基硅油的聚合物。
聚合反应的条件包括温度、压力和反应时间等。
通常情况下,聚合反应在高温下进行,以提高反应速率和产率。
在聚合反应完成后,需要对产物进行后处理。
首先是对反应混合物进行中和处理,以去除残余的催化剂和反应中生成的盐类。
中和处理通常使用酸性溶液进行,如盐酸或硫酸。
接着,需要将产物进行分离和纯化。
这一步骤通常采用蒸馏、结晶、萃取等方法,以去除杂质和提高羟基硅油的纯度。
经过中和处理和纯化后的羟基硅油需要经过稳定化处理。
稳定化处理是为了提高羟基硅油的热稳定性和氧化稳定性。
稳定化处理通常采用添加剂的方式进行,如抗氧化剂、抗磨剂等。
这些添加剂可以提高羟基硅油的使用寿命和性能。
总结起来,羟基硅油的生产工艺包括羟基硅烷的聚合反应、中和处理、分离纯化和稳定化处理等步骤。
通过这些步骤,可以获得具有优异性能的羟基硅油产品。
在实际生产中,还需要考虑工艺参数的优化、设备的选择和维护等因素,以确保生产过程的高效性和产品的质量稳定性。
希望通过本文的介绍,读者对羟基硅油的生产工艺有了更深入的了解。
羟基硅油作为一种重要的特种润滑油,在多个领域发挥着重要作用。
随着技术的不断进步,羟基硅油的生产工艺也在不断改进和创新,以满足市场对产品性能的不断提高的需求。
羟基硅油的制备方法

羟基硅油的制备方法
羟基硅油的制备方法大致分为两种:一种是通过硅烷和水反应合成,另一种是通过二甲基二氯硅烷为原料反应合成。
其中,采用二甲基二氯硅烷为原料的制备方法可分为以下几个步骤:
制备含有氢氧根离子(OH-)的溶液。
通常使用氢氧化钠(NaOH)或者氢氧化钾(KOH)溶解在水中制备。
将二甲基二氯硅烷缓慢滴加到上述溶液中,并同时搅拌。
此时,溶液中的氢氧根离子与二甲基二氯硅烷中的氯离子反应生成羟基硅油分子。
调节溶液的pH值,使其逐渐升高至中性或略高于中性。
这一步骤可以使用盐酸(HCl)等酸性物质进行调节。
通过蒸馏、过滤等方法将得到的羟基硅油纯化。
需要注意的是,在制备羟基硅油的过程中,需要控制反应条件以避免出现不必要的副反应,同时还需要对反应产物进行适当的纯化处理,以获得高纯度和良好品质的羟基硅油产品。
1。
一种羟基硅油的合成方法

一种羟基硅油的合成方法我前几天又试了个新方法合成羟基硅油,总算有点成果了。
说实话这羟基硅油的合成,我一开始也是瞎摸索,走了不少弯路。
我最开始尝试的时候,是按照一些书上的基本理论方法来的。
我想着原料不就是那些嘛,把它们按一定比例混合搅拌就行。
我就搞了些二甲基二氯硅烷和水,觉得这两个反应就能出羟基硅油。
可是啊,我完全没想到它们的反应那么剧烈,一下子就变得乱糟糟的,根本就不是我想要的结果。
就好比你做饭,你觉得把几种食材一股脑儿放进去就好,结果出来一团糊,那可不行。
后来我就意识到,这个反应得控制条件才行。
我给反应容器弄了个冷却装置,就像给热水杯加个冰块让它降温一样。
慢慢把二甲基二氯硅烷滴加到水里,而不是直接混在一起。
我一边滴加一边搅拌,这个搅拌速度我还琢磨了好久呢。
开始的时候我搅拌得特别慢,就感觉它们反应得不充分,出来的产物很奇怪。
后来我加快了速度,但又太快了,感觉就像你搅面糊搅得跟旋风似的,溅得到处都是,反应也失控了。
后来我就慢慢找平衡,找到了一个合适的搅拌速度。
不过在这个过程中,我还不确定这个水解反应需要多长时间是最好的。
有时候反应时间短了呢,感觉很多原料都没反应完。
我试过缩短时间,发现产物里有大量的未反应原料残留。
要是反应时间太长了,又感觉会有一些副反应发生。
我现在还在摸索这个最佳反应时间,不过目前觉得几个小时是比较靠谱的,但不敢确定,还得继续试。
还有啊,反应完了之后怎么提纯这羟基硅油也是个头疼的问题。
我试过用过滤的方法,觉得那些杂质能被滤掉,但是实际操作的时候才发现,这样并不能完全除去杂质。
就像你想把沙子里的小石子筛出来,可是还有好多粉末混在里面。
后来我又试了用蒸馏的方法,这个相对效果要好一些,但我觉得可能还有更高效更好的提纯方式,我还在学习研究呢。
比如说是不是可以用某种特定的溶剂来萃取呢?我不太清楚,也还没试过,但是感觉可以是个方向。
总的来说啊,合成羟基硅油这事儿,真的得一步一步小心翼翼地摸索,每个环节都要试验很久才能找到比较合适的方法。
- 1、下载文档前请自行甄别文档内容的完整性,平台不提供额外的编辑、内容补充、找答案等附加服务。
- 2、"仅部分预览"的文档,不可在线预览部分如存在完整性等问题,可反馈申请退款(可完整预览的文档不适用该条件!)。
- 3、如文档侵犯您的权益,请联系客服反馈,我们会尽快为您处理(人工客服工作时间:9:00-18:30)。
高羟基含量羟基硅油的合成
摘要:介绍了用DMC与乙酸酐反应生产高羟基含量羟基硅油的方法,并对影响羟基含量的因素作了分析。
结果表明采用滴加法、程序控温和碱性条件下水解的方法,制得了粘度约20㎜2/s,羟基含量大于10%的羟基硅油。
关键词:羟基硅油;乙酸酐;滴加法;程序控温
羟基硅油是指分子结构两端为活性羟基的短链聚二甲基硅氧烷。
它是热硫化硅橡胶和混炼胶生产中常用的结构控制剂、有机硅树脂的改性中间体,以及无机材料的表面疏水处理剂,并且在织物、纸张和皮革的防水、柔软、防粘处理方面也有广泛的应用。
其制备方法根据所用原材料的不同主要有五种【1】:二甲基二乙氧基硅烷水解法;二甲基二氯硅烷直接水解法;D3水解法;D4或DMC在阳离子交换树脂催化下开环水解以及D4与乙酸酐反应制备法。
用二甲基二乙氧基硅烷水解制备的羟基硅油,羟基摩尔含量较高,但成本较高,仅适用于自己生产单体的厂家生产;用二甲基二氯硅烷水解制备羟基硅油,生产中控制难度较大,稍有不当,羟基摩尔分数就会很低;采用D3水解制备羟基硅油,需用大量极性溶剂,后处理困难,成本较高;采用D4或DMC在阳离子交换树脂催化下开环水解制备羟基硅油,生产成本较低,但操作时必须注意水的开始滴加速度,若水的滴加速度与D4或DMC的滴加速度不区配,则会使产品粘度变大,羟基摩尔分数变低。
本文将就用DMC与乙酸酐的反应生产高羟基含量羟基硅油的方法作详尽论述。
1. 实验部分
1.1 原材料及仪器
DMC:工业级,深圳吉鹏硅氟材料有限公司;乙酸酐:含量≥99%,进口;有机酸:含量≥99%,进口;纯碱:工业级,大连;催化剂:化学纯,广州。
旋转粘度计:NDJ-1型,上海天平仪器厂;羟基含量分析仪:自制,氢化铝锂法测定。
1.2 羟基硅油的合成
1/4n[(CH3)SiO]4+(CH3CO)2O→C H3COO[(CH3)SiO]nCOOCH3
(1)
CH3COO[(CH3)SiO]NCOOCH3+H2O→HO-[(CH3)Si-O]nH+CH3COOH (2)
n=3~6
在装有搅拌器、温度计和滴液漏斗的四口烧瓶中,加入计量好的乙酸酐、有机酸、催化剂和部分DMC,升温至50~60℃,滴加其余的DMC,滴加完毕后升温到115~120℃平衡反应4~6小时,然后降温到50℃以下,将料液加入事先准备好的一定浓度的纯碱溶液中进行水解、平衡、水洗,然后通过薄膜蒸发器脱低分子,脱低后的物料经活性碳脱色、过滤及无水氯化钙干燥后得到粘度约20㎜2/s,羟基含量大于10%的羟基硅油。
2.结果与讨论
2.1 加料方式
要使羟基硅油的羟基含量足够高,必须控制其分子量尽可能低,因此在反应过程中应尽可能减少DMC开环后形成的二甲基硅氧烷链节进一步缩合的机会。
实验中我们将用于封端的醋酸酐、有机酸和催化剂配入底釜中,对DMC设计了
三种加料方式:a. DMC全部加入底釜中;b. 一部分DMC加入底釜中,另一部分DMC以滴加方式加入;c. DMC全部以滴加方式加入。
由表一的实验结果可看出,采用一部分DMC配入底料、另一部分DMC以滴加的方式加入对羟基含量的提高有利。
其原因在于,用于封端的乙酸酐作为底料配入釜中,DMC采取滴加方式加入,则酰氧基始终处于高浓度状态,如(1)所示的反应方程有利于向正反应反应方向进行,阻碍了硅氧链的增长,易于得到低分子量的硅氧链节。
由于所用的催化剂浓硫酸系强酸,加入部分DMC稀释了催化剂浓度,使得乙酸酐在强酸性环境中不至于被碳化,从而影响到羟基含量的提高。
采用DMC全部以滴加方式加料,在四口烧瓶壁上及搅拌棒上可明显观察到因碳化而产生的黑色杂质。
2.2 温度的控制
温度的控制,对于DMC能否很好的开环至关重要。
由于DMC系D3、D4、D5及少量的D6、D7等组成的混合环体,在生产过程中为了使转化率达到最高,应使DMC混合环体中的各组分尽可能发生开环反应,但是DMC各组份开环的活化能不一样,同时考虑乙酸酐在高温环境下的挥发损失,因此我们采取程序控温的办法【2】,即滴加过程在50~60℃,使DMC中的大部分活性高的D3、D4、D5组份先开环,滴加完毕后升温到115~120℃使D6、D7等大环体开环,这样对于提高收率有很大的好处。
实验结果见表1所示。
表1 影响羟基含量和收率的因素
2.3 水解条件的控制
水解条件的控制,对于羟基含量的高低影响很大。
我们设计了两种方案:a. 加自来水,在60~70℃水解,平衡、水洗;b. 加一定浓度的碱水,在60~70℃水解,平衡、水洗。
乙酰氧基的水解反应如(2)所式,在中性或酸性条件下,乙酰氧基的水解比较缓慢,随着水解介质PH值增大,水解速度加快,羟基在碱性条件下是比较稳定的【3】,但PH值不得过高,否则会导致羟基缩合,羟基含量下降。
表1所示的实验结果也证明了这一点。
3. 结论
采用部分DMC滴加,在50~120℃之间程序控温,然后直接在碱水中水解、平衡,后脱低的方法能制得粘度约20㎜2/s,羟基含量大于10%的硅油。
参考文献
1.黄薇.低粘度端羟基硅油的合成.第十一届中国有机硅学术交流会论文集. 208.
2.龚家全.甲基硅油生产工艺改进及异味去除.有机硅材料.2001.15(6):17~18.
3.杜作栋.有机硅化学.化学工业出版社.1990:88.。